Impression 3D Inconel
Table des matières
L'Inconel désigne une famille de superalliages à base de nickel et de chrome connus pour leur résistance à la chaleur, à la corrosion et à la pression. L'impression 3D de l'Inconel permet d'améliorer la liberté de conception et les propriétés mécaniques par rapport aux approches de fabrication conventionnelles pour des industries telles que l'aérospatiale, l'énergie et l'automobile.
Vue d'ensemble Impression 3d inconel
Les superalliages d'Inconel sont des matériaux à base de nickel et de chrome renforcés par des ajouts de fer, de niobium, de molybdène et d'autres éléments. Leur résistance remarquable à la température, à la corrosion et à la fatigue fait de l'Inconel un matériau adapté aux applications exigeantes.
L'impression 3D utilisant des techniques de fusion sur lit de poudre offre de nouvelles possibilités pour fabriquer des pièces complexes en Inconel avec des grains plus fins et une résistance supérieure à celle des méthodes traditionnelles. Les principaux avantages sont les suivants :
- Fabrication de géométries complexes et légères
- Amélioration du comportement à la traction et à la fatigue
- Une plus grande précision et une plus grande souplesse de conception
- Des délais plus courts et des volumes plus faibles
- Capacité à créer des structures de treillis optimisées
- Combinaison de matériaux dissemblables en une seule pièce
Malgré ces avantages, des problèmes tels que les contraintes résiduelles, les risques de porosité et le post-traitement doivent être résolus pour obtenir des composants en Inconel imprimés de qualité.
Globalement, la fabrication additive ouvre la voie à des applications innovantes de l'Inconel dans les échangeurs de chaleur, le matériel de combustion, les composants aérospatiaux, les implants biomédicaux et d'autres créneaux nécessitant une durabilité dans des environnements extrêmes.
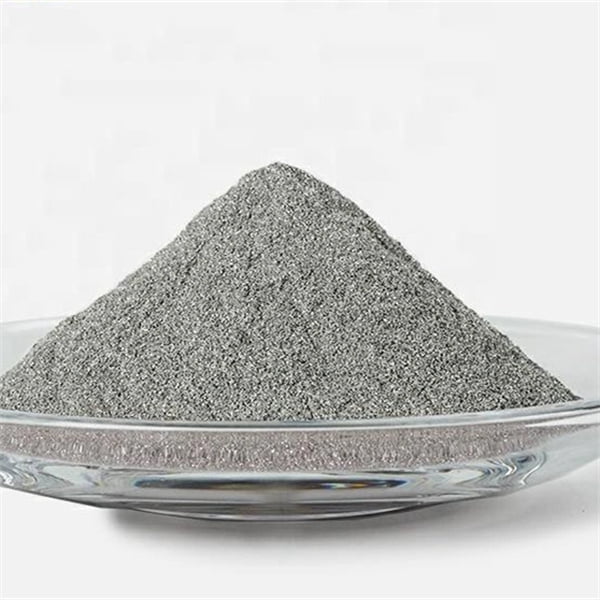
Composition Impression 3d inconel
Inconel est une vaste marque de superalliages désignant plus de deux douzaines de matériaux à base de nickel durcis par précipitation et conçus pour des applications exigeantes en termes de chaleur, de corrosion et de pression.
Leur teneur élevée en nickel forme une structure cristalline austénitique FCC qui assure le renforcement de la solution solide. Des éléments ajoutés comme le chrome, le fer, le niobium, le molybdène, l'aluminium et le titane facilitent le durcissement par précipitation et améliorent les performances mécaniques.
Gammes de composition typiques :
Élément | Composition (poids %) |
---|---|
Nickel (Ni) | 50-80% |
Chrome (Cr) | 10-25% |
Fer (Fe) | 0-50% |
Niobium (Nb) | 0-5% |
Molybdène (Mo) | 0-9% |
Aluminium (Al) | 0-6% |
Cobalt (Co) | 0-2% |
Titane (Ti) | 0-5% |
Tungstène (W) | 0-7% |
Carbone (C) | 0-0.2% |
Certaines nuances d'Inconel ont des gammes d'alliage plus étroites, destinées à des applications de niche. Par exemple :
Inconel 625
- 58% Ni
- 20-23% Cr
- 8-10% Mo
- 3-4% Nb
- 0-5% Fe
Inconel 718
- 50-55% Ni
- 17-21% Cr
- 4,75-5,5% Nb
- 2,8-3,3% Mo
- 0-1% Al
Effets des principaux éléments d'alliage :
- Nickel - Élément dominant assurant la résistance à la corrosion et la ductilité
- Chrome - Résistance à l'oxydation et dureté grâce à la formation d'oxydes de chrome
- Niobium - La formation de carbure est cruciale pour le renforcement par précipitation
- Molybdène - Renforcement de la solution solide
- Fer - Contribue au durcissement de la solution solide
- Aluminium + Titane - Forme des précipités gamma prime pour renforcer considérablement les alliages.
Impression 3d inconel Propriétés
Les matériaux Inconel offrent une combinaison exceptionnelle de résistance à la chaleur, de performance à la corrosion, de haute résistance et de durée de vie en fatigue exceptionnelle, bien au-delà des aciers inoxydables standard. Cela les rend aptes à répondre à des exigences extrêmes malgré leur coût plus élevé.
Propriétés physiques
- Densité - Fourchette de 7,9 à 8,5 g/cm3
- Point de fusion - 1300-1450°C en fonction de la composition exacte
- Résistivité électrique - Fourchette de 70-94 μΩ-cm
- Conductivité thermique - Plus faible à 10-20 W/m-K
- Coefficient de dilatation thermique - Environ 13-16 (μm/m)/°C
Propriétés mécaniques
- Résistance à la traction - 500-1500 MPa
- Limite d'élasticité - 240-1200 MPa
- Élongation – 10-55%
- Dureté - Rockwell B 80-150
- Module d'élasticité - 150-210 GPa
- Ténacité à la rupture - 100-300 MPa-m^1/2^
Limites de performance
- Température de service maximale - 650-1100°C
- Résistance à l'oxydation - Jusqu'à 900-1100°C dans l'air
- Résistance à la corrosion aqueuse - Large éventail de supports
- Résistance à la sulfuration - En continu 500-900°C
Résistance à la fatigue
L'un des principaux avantages de l'Inconel est sa remarquable résistance à la fatigue, même en cas de cycles de déformation thermique et mécanique. Par exemple, l'Inconel 718 offre des durées de vie impressionnantes de plus de 100 000 heures à des températures avoisinant les 700°C.
Méthodes de fabrication additive
L'Inconel peut être imprimé en 3D à l'aide de techniques de fusion sur lit de poudre, où un laser ou un faisceau d'électrons fusionne des couches successives de poudre métallique sur la base de sections de modèles numériques. Cela permet d'obtenir des géométries complexes d'Inconel impossibles à réaliser par des méthodes soustractives.
Les deux principales technologies utilisées sont les suivantes :
Fusion laser sur lit de poudre (L-PBF)
Également connu sous le nom de frittage laser direct des métaux (DMLS), un laser haute puissance balaie les lits de poudre pour faire fondre sélectivement les zones correspondant à la section transversale de la pièce, en liant les particules entre elles lors de la solidification rapide.
Fusion en lit de poudre par faisceau d'électrons (E-PBF)
Un faisceau d'électrons fournit la source d'énergie à haute densité pour fusionner les couches de poudre en fonction de la géométrie du modèle CAO. L'environnement de fabrication est sous vide, ce qui élimine les problèmes de diffusion du faisceau.
Le L-PBF est plus accessible et plus rapide, tandis que le E-PBF permet de mieux traiter les matériaux hautement réfléchissants tels que les alliages d'aluminium ou de cuivre. Les deux méthodes permettent de mélanger les alliages au sein d'un même composant imprimé.
Considérations relatives au processus
Les défis propres à l'AM de l'Inconel comprennent des contraintes thermiques élevées entraînant des fissures et des distorsions, des contraintes résiduelles intrinsèques limitant les géométries, la rugosité imprimée nécessitant une finition, la complexité du développement des paramètres par rapport aux aciers, et le manque de données de conception.
Une optimisation minutieuse de la stratégie de balayage, de la température, de la puissance du faisceau, de l'espacement des trappes, des caractéristiques de la poudre, de la gestion thermique et du post-traitement est nécessaire pour atteindre les performances mécaniques souhaitées.
Impression 3d inconel Notes imprimables
Les variantes d'Inconel corroyé les plus courantes sont l'Inconel 625 et l'Inconel 718, qui représentent plus de 75% d'utilisation, suivies par l'Inconel 800, l'Inconel 686 et des nuances spéciales pour des applications de niche.
Inconel 625
Cet alliage de nickel, chrome et molybdène offre une grande résistance, une excellente brasabilité et une bonne résistance à la corrosion, même à des températures extrêmes allant jusqu'à 980°C. Il est utilisé pour les pots de combustion, les soupapes de moteur, les échangeurs de chaleur et le matériel de traitement chimique.
Inconel 718
Acier au nickel de qualité aérospatiale présentant une limite d'élasticité exceptionnelle allant jusqu'à 1 200 MPa et capable de conserver ses propriétés en cas d'utilisation prolongée à 650°C. Sa résistance élevée, sa ténacité et sa résistance à la fatigue en font le superalliage de référence pour les équipements de vol tels que les pales et les disques de turbines.
Inconel 800
Alliage fer-nickel-chrome offrant une résistance exceptionnelle à la cémentation et à l'oxydation jusqu'à 1150°C. Utilisé dans les tubes de surchauffe, les équipements de traitement thermique, les chauffages au feu, etc.
Inconel 686
Modification de l'Inconel 625 conçue pour améliorer la résistance à la corrosion intergranulaire et aux piqûres grâce à l'ajout de tungstène et de molybdène. Utilisé dans les systèmes de désulfuration des gaz de combustion et les générateurs de vapeur nucléaires.
Classes personnalisées
La R&D pour les applications à haute valeur ajoutée mélange l'Inconel avec des carbures, des alliages à haute entropie ou d'autres particules pour augmenter encore les propriétés telles que la résistance au fluage, à la fatigue, à l'abrasion ou à la corrosion.
Impression 3d inconel Performance mécanique
En général, l'Inconel fabriqué additivement présente un meilleur comportement à la traction et à la fatigue par rapport à ses homologues moulés ou corroyés.
Par exemple, l'Inconel 718 imprimé en 3D présente des résistances à la rupture et à la traction supérieures de plus de 30% par rapport au matériau traité de manière conventionnelle, tout en conservant une ductilité appréciable supérieure à 10% d'allongement.
Propriétés mécaniques typiques des qualités d'Inconel imprimées courantes
Alliage | Résistance ultime à la traction (MPa) | Limite d'élasticité (MPa) | Élongation (%) |
---|---|---|---|
Inconel 625 | 860-980 | 500-690 | 40-55 |
Inconel 718 | 1250-1300 | 1050-1160 | 12-25 |
Inconel 800 | 450-760 | 240-550 | 30-60 |
L'augmentation de la résistance provient d'un affinement significatif des grains jusqu'à 5-10 microns pour l'Inconel imprimé (au lieu de la taille moyenne des grains ASTM >50 microns pour le corroyage). Ce renforcement Hall-Petch, combiné à des phases intermétalliques conservées, explique les capacités mécaniques accrues.
Des microstructures et textures de type solidifié directionnel adaptées aux conditions de charge prévues peuvent encore améliorer les performances. D'autre part, des défauts tels que la porosité ou la fissuration dus à des paramètres d'impression inappropriés ont un impact négatif sur les propriétés.
Impression 3d inconel Applications
L'impression 3D étend l'utilisation de l'Inconel à des applications plus critiques en termes de performances, nécessitant des formes complexes, des délais d'exécution rapides ou des alliages personnalisés, tout en complétant les techniques soustractives conventionnelles pour des composants plus simples ne repoussant pas les limites des matériaux.
Aérospatiale
Les pièces de propulsion de fusées, les aubes de turbines, les tuyères de carburant et les chemises de combustion fabriquées de manière additive sont plus performantes que les superalliages traités traditionnellement dans des conditions de flux de chaleur et de pression extrêmes. Des canaux de refroidissement optimisés et des assemblages consolidés plus légers ont également été réalisés.
Pétrole et gaz
Les têtes de puits, les outils de forage, les trépans et les tubages bénéficient d'une meilleure résistance à l'usure et à la corrosion grâce aux composants en Inconel imprimés et solidifiés dans le sens de la marche, avec des géométries et des capteurs intégrés difficiles à fabriquer autrement.
Production d'électricité
Les tubes des échangeurs de chaleur, les serpentins des surchauffeurs et les composants de la section chaude des turbines à gaz ont une durée de vie de 2 à 4 fois supérieure grâce à des compositions d'Inconel adaptées et à des canaux conformes complexes qui refroidissent les zones critiques.
Automobile
Le mélange de grades d'Inconel différents permet à des culasses uniques intégrant des fonctions de collecteur d'échappement de supporter des températures supérieures à 850°C sans fondre ni se fissurer, tout en optimisant les flux de liquide de refroidissement.
Applications émergentes
Les implants médicaux et dentaires sur mesure, les réacteurs microfluidiques et les dissipateurs thermiques, les électrodes pour l'électrolyse et les applications aérospatiales de niche tirent particulièrement profit de la flexibilité de l'AM de l'Inconel.
Fournisseurs mondiaux et prix
Une série de fabricants sous contrat, d'imprimeurs sur métal, de bureaux d'impression, de vendeurs de poudres, d'entreprises de logiciels et de finisseurs de pièces soutiennent la production de composants en Inconel imprimés dans le monde entier. Les prix varient en fonction de facteurs tels que le volume de la commande, les exigences en matière de tolérance, le délai d'exécution et les exigences de qualité.
Entreprise | Siège social |
---|---|
Renishaw | ROYAUME-UNI |
GE Additive | ÉTATS-UNIS |
Systèmes 3D | ÉTATS-UNIS |
EOS | Allemagne |
Velo3D | ÉTATS-UNIS |
Additif pour charpentier | ÉTATS-UNIS |
Protolabs | ÉTATS-UNIS |
Matérialiser | Belgique |
Höganäs | Suède |
Aubert & Duval | France |
Estimation du coût des pièces :
Les pièces imprimées en Inconel vont de $50-500 par pouce cube en fonction de la complexité, des taux d'utilisation des consommables, des difficultés de traitement par rapport aux alliages conventionnels tels que l'acier ou le titane, et de la qualité de finition requise. Les engagements portant sur des volumes importants améliorent considérablement les économies d'échelle.
Normes et spécifications
Le développement des paramètres d'impression guidé par les normes de traitement de l'Inconel corroyé existantes permet de faire correspondre la composition et les attentes mécaniques de base :
Standard | Organisation | Années d'études couvertes |
---|---|---|
AMS 5662 | SAE | Inconel 625 |
AMS 5663 | SAE | Inconel 718 |
AMS 2875 | SAE | Inconel X-750 |
Toutefois, les normes spécifiques à l'AM couvrant la conception, la qualification, les essais, la certification, la manipulation des poudres et d'autres considérations relatives à l'Inconel imprimé sont encore en cours d'évolution :
- ASTM F3055 - Spécification standard pour la fabrication additive d'alliage de nickel (UNS N06625) par fusion en lit de poudre
- ASTM F3056 - Spécification standard pour la fabrication additive d'alliage de nickel (UNS N07718) par fusion en lit de poudre
- ASME BPVC Section IX - Qualifications pour le soudage, le brasage et la fusion
- AWS D20.1 - Fabrication de composants métalliques par fabrication additive
L'utilisation de qualités corroyées établies comme matière première tout en contrôlant la variabilité du processus d'impression par rapport à ces spécifications garantit la constance des propriétés de l'Inconel imprimé.
Avantages et inconvénients de la fabrication additive de l'Inconel
Avantages | Inconvénients |
---|---|
- Résistance et durabilité accrues | - Coût élevé des imprimantes et des matériaux d'entrée |
- Caractéristiques internes complexes telles que les treillis | - Taille limitée en fonction des enveloppes de l'imprimante |
- Temps de fabrication plus courts | - Débit inférieur à celui du moulage/forgeage |
- Alliages et microstructures sur mesure | - Un post-traitement important est souvent nécessaire |
- Canaux de refroidissement conformes | - Propriétés anisotropes par dépôt de couches |
- Pièces légères à topologie optimisée | - Risques de tension résiduelle et de distorsion |
- Consolidation des pièces en composants uniques | - Défis en matière de qualification et de certification |
- Amélioration de la flexibilité de la chaîne d'approvisionnement | - Quelques propriétés mécaniques : réduction et corroyage |
- Réduction des délais et des stocks | - Précautions pour la manipulation des poudres en vrac |
- La liberté de conception au-delà des méthodes soustractives |
En général, l'équilibre entre les capacités de l'imprimante, les exigences de l'application et les coûts détermine les itinéraires optimaux pour la fabrication de composants en Inconel.
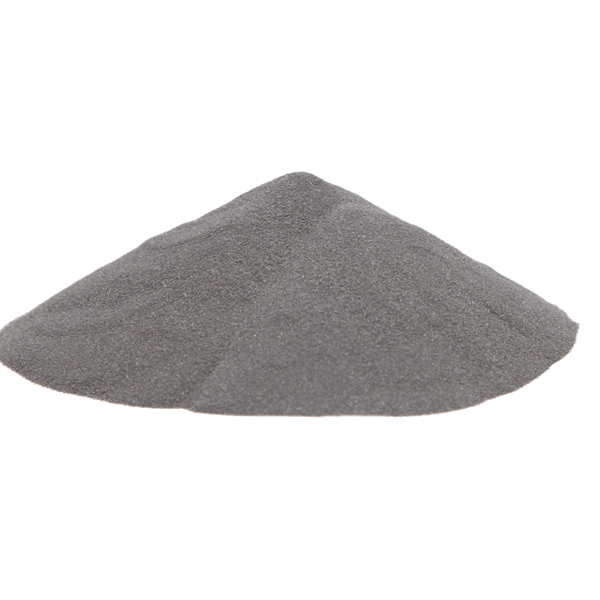
FAQ
Q : Quelles sont les meilleures pratiques pour améliorer la qualité des pièces en Inconel imprimées en 3D ?
R : L'optimisation des paramètres, la gestion des poudres, les variations de la stratégie de balayage, les cycles thermiques adaptés, les traitements thermiques et HIP, la finition de surface, les tomographies et les essais de validation mécanique complets permettent de surmonter les difficultés du processus additif et de garantir l'intégrité de l'Inconel imprimé pendant tout le cycle de vie opérationnel.
Q : Quel procédé d'impression permet d'obtenir de meilleures pièces en Inconel - laser ou fusion sur lit de poudre par faisceau d'électrons ?
R : Les deux méthodes permettent d'obtenir des composants en Inconel de pleine densité, mais le laser gère mieux la finition de la surface tandis que le faisceau d'électrons permet d'obtenir des caractéristiques de rapport d'aspect plus élevé, bien qu'à des vitesses plus lentes. Les performances dépendent également des capacités spécifiques de l'équipement, telles que la puissance du faisceau, la taille du point, la trajectoire de la trame, la taille de la chambre et la précision.
Q : Comment la durée de vie de l'Inconel imprimé se compare-t-elle à celle des composants fabriqués de manière traditionnelle ?
R : Dans des conditions de fatigue à cycle élevé, l'Inconel fabriqué de manière additive atteint ou dépasse généralement les alliages coulés et corroyés. Par exemple, l'Inconel 718 a une durée de vie 6 à 8 fois supérieure à celle des alliages coulés. Mais dans des conditions complexes de fatigue thermo-mécanique, les défauts contrôlent les défaillances permettant des durées de vie plus courtes ou plus longues en fonction du niveau d'optimisation par rapport à d'autres procédés.
Q : Est-il possible d'imprimer en 3D des alliages d'Inconel personnalisés au-delà des qualités courantes telles que 625 et 718 ?
R : Oui, la R&D développe souvent des mélanges de poudres spéciales augmentant les propriétés telles que la rigidité, la résistance, la ductilité, la performance à l'usure, le comportement à haute température et la résistance à la corrosion par l'ajout contrôlé d'éléments tels que le tungstène, le tantale, le cobalt, l'aluminium, le carbone et d'autres dans le cadre des paramètres de la famille Inconel.
Q : Quels sont les développements qui permettront d'accroître l'utilisation des composants Inconel fabriqués de manière additive ?
R : Des équipements plus rapides réduisant les coûts de production, une fabrication hybride combinant l'AM et les techniques soustractives en un seul système, une surveillance avancée en cours de processus et un contrôle en boucle fermée pour minimiser les défauts, des options d'alliage élargies, des données de conception plus complètes et des normes de qualification rigoureuses ciblant spécifiquement l'Inconel imprimé sont autant d'éléments qui favoriseront l'adoption de cette technologie.
Partager sur
MET3DP Technology Co. est un fournisseur de premier plan de solutions de fabrication additive dont le siège se trouve à Qingdao, en Chine. Notre société est spécialisée dans les équipements d'impression 3D et les poudres métalliques de haute performance pour les applications industrielles.
Articles connexes
À propos de Met3DP
Mise à jour récente
Notre produit
CONTACTEZ-NOUS
Vous avez des questions ? Envoyez-nous un message dès maintenant ! Nous répondrons à votre demande avec toute une équipe dès réception de votre message.
Obtenir les informations de Metal3DP
Brochure du produit
Obtenir les derniers produits et la liste des prix
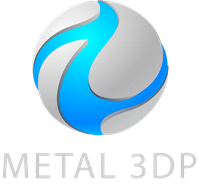
Poudres métalliques pour l'impression 3D et la fabrication additive