Lightweight Structural Panels in Aerospace Applications
Table des matières
Introduction: The Imperative for Lightweighting in Aerospace Structural Panels
The aerospace industry operates at the pinnacle of engineering, where performance, safety, and efficiency are paramount. Every component, from the smallest fastener to the largest wing assembly, is meticulously designed and manufactured to meet incredibly demanding standards. Among the most critical elements are structural panels – components that form the skin, skeleton, and internal framework of aircraft, spacecraft, satellites, and launch vehicles. These panels must withstand significant mechanical loads, extreme temperatures, vibration, and environmental factors while contributing minimally to the overall weight of the structure.
Why is weight such an obsession in aerospace? The answer lies in fundamental physics and economics. Every kilogram saved on an aircraft’s structure translates directly into tangible benefits:
- Improved Fuel Efficiency: Lighter aircraft require less thrust to achieve and maintain flight, leading to significant reductions in fuel consumption over the vehicle’s operational lifespan. This lowers operating costs and reduces environmental impact.
- Increased Payload Capacity: Reducing the structural weight allows for carrying more passengers, cargo, or mission-specific equipment (like sensors, communication arrays, or scientific instruments on satellites).
- Amélioration des performances : Lighter structures enable better maneuverability, higher speeds, longer range, and greater altitude capabilities. For spacecraft, reduced mass lowers launch costs dramatically, as escaping Earth’s gravity is energy-intensive.
- Optimized Design Cycles: Lighter components can sometimes simplify supporting structures, leading to a cascading weight-saving effect throughout the entire vehicle design.
Traditionally, aerospace engineers achieved lightweighting through material selection (using aluminum alloys, titanium alloys, composites) and complex, often subtractive, manufacturing processes like CNC machining, which carves parts from solid blocks, resulting in significant material waste (poor buy-to-fly ratio). While effective, these methods face limitations when dealing with highly complex geometries designed for optimal load distribution and minimal mass – designs often inspired by nature’s efficiency, featuring intricate internal lattices or smoothly varying thicknesses.
C'est ici Fabrication additive métallique (AM), commonly known as metal Impression 3D, emerges as a disruptive and transformative technology. Unlike traditional subtractive methods, AM builds parts layer by layer directly from digital models using high-performance metal powders. This additive approach fundamentally changes the design and manufacturing paradigm for components like structural panels. It unlocks the potential for:
- Liberté de conception sans précédent : Creating complex, topology-optimized shapes that were previously impossible or prohibitively expensive to manufacture.
- Réduction significative du poids : Producing panels with internal lattice structures or optimized geometries that maintain strength while drastically cutting mass.
- Consolidation partielle : Combining multiple traditionally separate components into a single, integrated 3D printed part, reducing assembly time, weight from fasteners, and potential points of failure.
- Réduction des déchets matériels : Using only the material necessary to build the part, significantly improving the buy-to-fly ratio compared to machining.
- Faster Prototyping and Iteration: Enabling rapid production of design variations for testing and validation.
Des entreprises comme Met3dp are at the forefront of this revolution, providing not only industry-leading metal 3D printing systems known for their large build volumes, accuracy, and reliability but also developing and manufacturing the high-performance, spherical metal powders essential for printing dense, high-quality aerospace components. With expertise spanning printers, advanced materials like aluminum alloys (AlSi10Mg), Scalmalloy®, titanium alloys, and superalloys, and comprehensive application support, Met3dp empowers aerospace manufacturers to leverage the full potential of AM for critical applications like lightweight structural panels. This post will delve into the applications, benefits, materials, design considerations, and practical aspects of using metal 3D printing to produce the next generation of aerospace structural panels.
Applications: Where are 3D Printed Structural Panels Revolutionizing Aerospace?
The potential applications for metal 3D printed structural panels span the entire aerospace sector, from commercial airliners and military aircraft to satellites and deep-space exploration vehicles. The ability of AM to create lightweight, complex, and highly optimized structures makes it particularly suitable for components where weight savings directly impact mission success and operational cost. Procurement managers and aerospace engineers are increasingly specifying AM for panels in various critical areas, seeking reliable fournisseurs de composants aérospatiaux capable of delivering qualified parts.
Here’s a breakdown of key application areas where AM is making significant inroads:
1. Fuselage and Airframe Components:
- Optimized Skin Panels: While large, primary skin panels are often still made from sheet metal or composites, AM is ideal for smaller, complex panels, especially those with integrated features like stiffeners, mounting points, or access hatches. Topology optimization can create panels that efficiently transfer loads around cutouts (like windows or doors) with minimal weight.
- Bulkheads and Frames: These internal structures bear significant loads. AM allows for the creation of organically shaped, topology-optimized bulkheads and frame sections that are significantly lighter than traditionally machined or assembled counterparts. Part consolidation can reduce part count and assembly complexity dramatically.
- Fairings and Aerodynamic Surfaces: Panels requiring complex curvatures and smooth transitions for aerodynamic efficiency can be readily produced with AM, often integrating internal stiffening structures without the need for secondary bonding or fastening.
2. Wing Structures:
- Ribs and Spar Sections: These internal wing components provide structural integrity. Metal AM enables the design of highly optimized ribs with internal lattice structures, offering exceptional stiffness and strength at reduced weight compared to conventionally machined ribs. Specific sections of spars requiring complex geometry or integration points can also benefit.
- Leading/Trailing Edge Panels: Panels forming the aerodynamic edges of wings, especially those incorporating features for de-icing systems or control surface attachments, can be manufactured effectively using AM.
- Flap and Slat Components: Structural elements within these high-lift devices often require complex shapes and internal mechanisms, making them suitable candidates for AM-driven design optimization and part consolidation.
3. Engine and Nacelle Components:
- Heat Shields and Thermal Barriers: Panels designed to protect surrounding structures from engine heat can be 3D printed using high-temperature alloys (though aluminum alloys like Scalmalloy® have uses in cooler nacelle sections). AM allows for integrated cooling channels or complex surface features to enhance thermal management.
- Acoustic Liners: Panels designed to absorb engine noise often feature complex honeycomb or lattice structures. AM provides a means to create highly effective, integrated acoustic dampening panels.
- Access Panels and Brackets: Smaller structural panels providing access for maintenance or supporting engine components can be lightweighted and optimized using AM.
4. Satellite and Spacecraft Structures:
- Bus Structures: The primary structure of a satellite, the bus, houses all critical subsystems. AM allows for the creation of incredibly lightweight yet stiff panels and frames, often incorporating mounting points for electronics, antennas, and propulsion systems directly into the printed structure. Every gram saved significantly reduces launch costs.
- Antenna Reflectors and Support Structures: Large, complex reflector shapes or the intricate trusses supporting them can be manufactured using AM, achieving required stiffness and thermal stability with minimal mass.
- Optical Benches and Instrument Mounts: Panels requiring extreme stability and precise alignment for sensitive optical instruments benefit from AM’s ability to create monolithic, optimized structures. Materials like Scalmalloy® offer excellent stability.
5. Interior Cabin Elements:
- Bulkheads and Dividers: Non-primary structural panels within the cabin can be lightweighted using AM, contributing to overall fuel savings.
- Overhead Bin Structures: Supporting structures for luggage compartments can be redesigned using topology optimization and AM for weight reduction.
- Galley and Lavatory Components: Structural elements within these modules can be optimized for space and weight using AM.
Benefits Across Applications:
Domaine d'application | Key Benefits of Metal AM | Target B2B Focus |
---|---|---|
Fuselage & Airframe | Topology optimization, part consolidation, reduced assembly time, improved load distribution around cutouts. | Aircraft OEM requirements, Tier 1 suppliers |
Wing Structures | Lightweight lattice structures, high stiffness-to-weight ratio, complex aerodynamic shapes, integrated features. | Wing manufacturers, Aerospace structural engineers |
Engine & Nacelle | High-temperature capability (other alloys), integrated cooling/acoustic features, complex geometries, part consolidation. | Engine manufacturers, Nacelle system integrators |
Satellite & Spacecraft | Extreme weight reduction (launch cost savings), high stiffness, integrated mounting, thermal stability. | Satellite manufacturers, Space systems manufacturing |
Interior Cabin Elements | Weight reduction, design flexibility for optimized space usage. | Cabin interior suppliers, Aircraft completion centers |
Exporter vers les feuilles
L'adoption de impression 3D de métaux for these structural panels is driven by the clear performance and economic advantages it offers. As the technology matures and qualification processes become more standardized, we expect to see even wider implementation across the aerospace industry, demanding reliable structural panel procurement routes and experienced manufacturing partners like Met3dp.
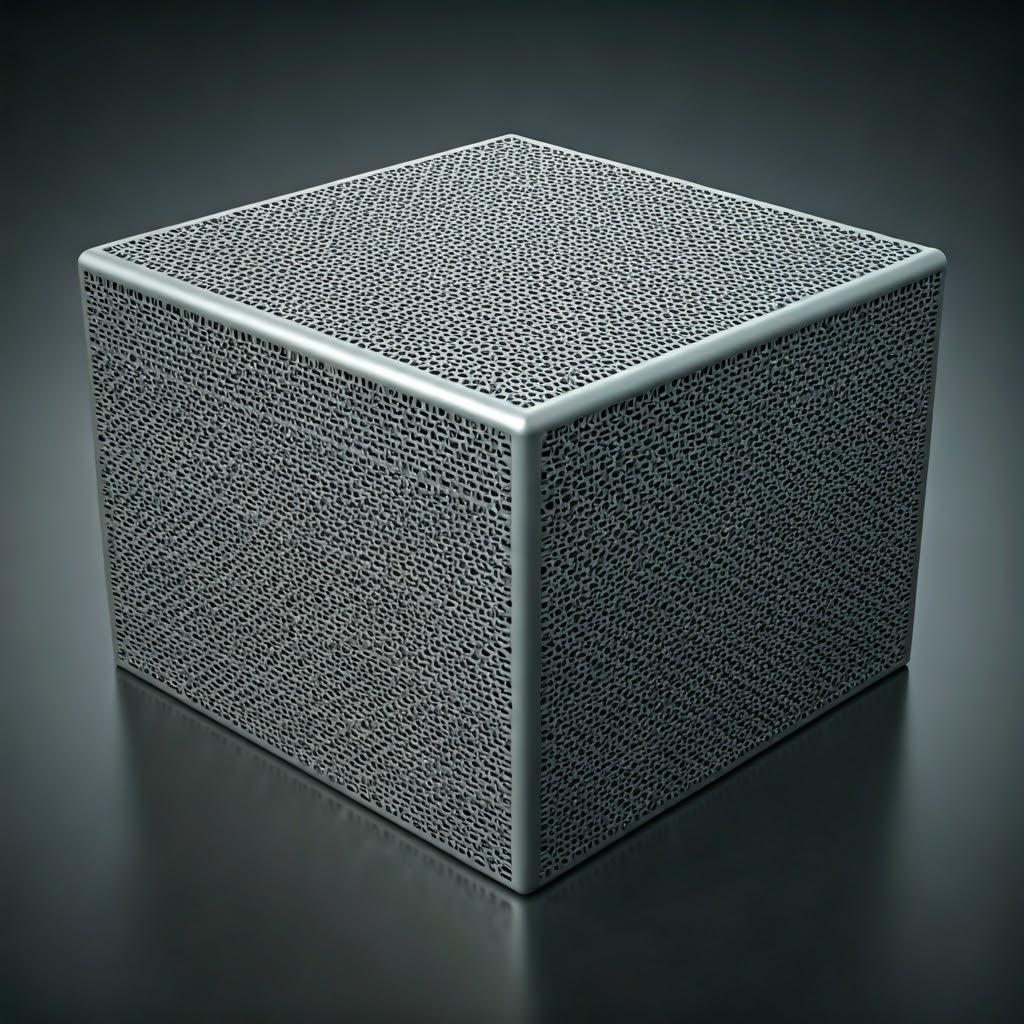
Why Metal 3D Printing for Aerospace Structural Panels? Unlocking Performance Gains
The decision to adopt metal additive manufacturing (AM) for aerospace structural panels isn’t merely about embracing a novel technology; it’s a strategic choice driven by tangible performance enhancements and manufacturing efficiencies that traditional methods often struggle to match. While conventional techniques like CNC machining, sheet metal forming, casting, and multi-part assembly have served the industry well, metal AM offers a unique combination of advantages perfectly suited to the demands of modern aerospace design, particularly the relentless pursuit of lightweighting and performance optimization.
Let’s compare AM with traditional methods for structural panel fabrication:
Traditional Methods vs. Metal AM:
Fonctionnalité | Traditional Methods (CNC, Forming, Assembly) | Metal Additive Manufacturing (LPBF, EBM) | Impact sur l'aérospatiale |
---|---|---|---|
Liberté de conception | Constrained by tool access, mold requirements, bending limitations, assembly needs. | Near-limitless geometric complexity; enables organic shapes, internal lattices, conformal channels. | Allows topology optimization for ideal load paths, leading to maximum strength-to-weight ratio. |
Déchets matériels | High, especially for CNC machining (subtractive); significant scrap generated. | Low (additive); uses primarily only the material needed for the part & supports. Powder is recyclable. | Improved buy-to-fly ratio, reduced raw material costs, more sustainable manufacturing. |
Consolidation partielle | Often requires multiple components joined by fasteners, welds, or adhesives. | Can combine multiple functionalities into a single, monolithic part. | Reduced part count, weight savings (fewer fasteners), simplified assembly, fewer potential failure points. |
Délai d'exécution (Prototype) | Can be long due to tooling fabrication, multiple process steps, setup times. | Very short; parts printed directly from CAD data, ideal for rapid iteration. | Faster design validation, quicker development cycles, accelerated innovation. |
Délai (production) | Can be efficient for high volumes once tooling is established. | Potentially slower per-part build time, but minimal tooling lead time; multiple parts per build possible. | Flexibility for low-to-mid volume production runs, on-demand manufacturing, reduced tooling investment. |
Complexity Cost | Cost increases significantly with geometric complexity. | Cost is less sensitive to complexity, more dependent on volume/height and material usage. | Enables highly complex, optimized designs without prohibitive manufacturing cost penalties. |
Caractéristiques internes | Difficult or impossible to create complex internal channels or voids. | Readily achievable (e.g., internal cooling channels, lightweight lattice structures). | Enhanced functionality (thermal management), maximum lightweighting potential via internal optimization. |
Exporter vers les feuilles
Key Advantages of Metal AM for Structural Panels:
- Topology Optimization and Generative Design: This is arguably the most significant advantage. Engineers can define load cases, constraints, and design space, and specialized software algorithms generate the most efficient material distribution to meet performance requirements with minimum weight. The resulting organic, often bone-like structures are perfectly suited for AM production, leading to weight savings of 30-60% or more in some structural components compared to traditionally designed counterparts. This directly translates to the fuel efficiency and payload benefits discussed earlier.
- Consolidation partielle : Consider a traditional panel assembly involving a skin, multiple stiffeners, brackets, and dozens of fasteners. AM allows designers to potentially integrate all these elements into a single, complex printed part. This drastically reduces:
- Poids : Eliminates the need for fasteners (rivets, bolts) and overlapping material at joints.
- Assembly Time & Cost: Simplifies the manufacturing workflow significantly.
- Potential Failure Points: Reduces the number of joints, which can be sources of fatigue or corrosion.
- Prototypage rapide et itération de la conception : Aerospace design involves rigorous testing and validation. AM allows engineers to quickly produce different design iterations of a structural panel for physical testing (fit checks, load tests). Minor design modifications can be implemented in CAD and a new version printed in days, compared to weeks or months for modifying traditional tooling. This accelerates the development cycle and allows for more refined optimization. Impression 3D de métaux services streamline this iterative process.
- Reduced Material Waste (Buy-to-Fly Ratio): Aerospace alloys are expensive. Machining a complex panel from a solid billet can result in over 90% of the initial material being removed as chips (a buy-to-fly ratio of 10:1 or worse). AM, being additive, uses material far more efficiently. While some support structures are needed and some powder is non-recycled, the buy-to-fly ratio is often significantly better, typically ranging from 1.5:1 to 3:1, leading to substantial raw material cost savings.
- Manufacturing of Complex Internal Structures: AM excels at creating features that are impossible with other methods. For structural panels, this includes:
- Structures de treillis internes : Replacing solid sections with engineered lattices (e.g., gyroids, octet trusses) provides excellent stiffness and strength at a fraction of the weight.
- Canaux de refroidissement conformes : For panels near heat sources, internal channels following the part’s contour can be integrated for highly efficient thermal management.
- Variable Density: Material density can be varied across the panel, placing more material only where stresses are highest.
- Bespoke and Customized Designs: AM is ideal for low-volume, high-value components common in aerospace, especially in satellite and specialty aircraft manufacturing. It allows for the creation of unique panel designs tailored to specific mission requirements without the high setup costs associated with traditional tooling. This facilitates the production sought by aerospace parts wholesale buyers looking for specialized, optimized components.
While AM offers compelling advantages, it’s crucial to partner with experienced providers. Met3dp’s industry-leading printers, renowned for their accuracy and reliability, are essential for producing mission-critical aerospace parts that meet stringent dimensional and quality requirements. Their expertise ensures that the potential benefits of AM for structural panels are fully realized.
Material Focus: AlSi10Mg and Scalmalloy® for High-Performance Panels
The choice of material is fundamental to the performance of any aerospace component, especially load-bearing structural panels. While metal additive manufacturing supports a wide range of alloys, two aluminum-based powders stand out for their combination of lightweight properties, mechanical performance, and suitability for AM processes like Laser Powder Bed Fusion (LPBF), also known as Selective Laser Melting (SLM): AlSi10Mg et Scalmalloy® (alliage d'aluminium). Aerospace procurement managers and engineers frequently specify these materials when seeking metal powder suppliers aerospace solutions.
1. AlSi10Mg: The Workhorse Aluminum Alloy
AlSi10Mg is one of the most widely used aluminum alloys in additive manufacturing. It’s essentially an aluminum casting alloy adapted for powder bed fusion processes. Its popularity stems from a good balance of properties, excellent processability, and relatively lower cost compared to more specialized alloys.
- Composition : Primarily Aluminum (Al), with Silicon (Si) around 9-11% and Magnesium (Mg) around 0.2-0.45%. Silicon improves fluidity and reduces solidification shrinkage during printing (akin to castability), while Magnesium provides precipitation hardening capabilities through heat treatment.
- Key Properties (As-Built and Heat-Treated):
- Léger : Density around 2.67 g/cm³.
- Bon rapport résistance/poids : While not as strong as high-strength aerospace aluminum alloys (like 7000 series) or Scalmalloy®, heat-treated AlSi10Mg offers respectable mechanical properties suitable for many moderately loaded structural panels. Typical yield strength can reach 230-290 MPa, and ultimate tensile strength 330-430 MPa, depending on heat treatment and build orientation.
- Good Thermal Conductivity: Useful for applications requiring some heat dissipation.
- Excellente imprimabilité : Processes well in LPBF systems, allowing for fine features and relatively high build speeds. Good weldability characteristics contribute to layer fusion.
- Résistance à la corrosion : Generally good, can be further enhanced with surface treatments like anodizing.
- Aerospace Applications: Often used for secondary structural components, brackets, housings, ducting, heat exchangers, and panels where moderate strength is sufficient and the benefits of AM (complexity, consolidation) are primary drivers. Ideal for prototypes due to ease of printing and cost-effectiveness.
- Considérations relatives à la transformation :
- Traitement thermique : Typically requires stress relief post-build to reduce internal stresses. A T6 heat treatment (solutionizing and artificial aging) is often applied to achieve optimal mechanical properties through precipitation hardening.
- Anisotropie : Like many AM materials, properties can vary slightly depending on the build direction (XYZ). This must be considered during design and testing.
- Hot Tearing: Susceptibility needs to be managed through optimized process parameters (laser power, scan speed, layer thickness).
Table: Typical Properties of LPBF AlSi10Mg (Heat Treated – T6)
Propriété | Valeur typique | Unité | Notes |
---|---|---|---|
Densité | ~2.67 | g/cm³ | Léger |
Yield Strength (Rp0.2) | 230 – 290 | MPa | Varies with process parameters & orientation |
Résistance ultime à la traction | 330 – 430 | MPa | Varies with process parameters & orientation |
Allongement à la rupture | 3 – 10 | % | ductilité inférieure à celle des alliages corroyés |
Module d'élasticité | ~70 | GPa | |
Dureté | 100 – 120 | HT | Dureté Vickers |
Température de service maximale | ~150 – 200 | °C | Strength decreases significantly above this |
Exporter vers les feuilles
2. Scalmalloy®: High-Performance AM Aluminum Alloy
Scalmalloy® is a patented high-performance aluminum-magnesium-scandium alloy (Al-Mg-Sc) specifically designed and optimized for the demands of additive manufacturing by APWorks, an Airbus subsidiary. It bridges the gap between traditional aluminum alloys and higher-strength materials like titanium, offering exceptional properties for demanding aerospace applications.
- Composition : Aluminum alloyed with Magnesium, Scandium (Sc), and Zirconium (Zr). The Scandium and Zirconium additions are key to its unique properties, forming stable nano-precipitates during heat treatment that significantly strengthen the alloy and enhance its thermal stability.
- Propriétés principales :
- Rapport force/poids exceptionnel : Significantly higher specific strength than AlSi10Mg and comparable to some titanium alloys. Yield strength can exceed 450-500 MPa, with ultimate tensile strength over 500-550 MPa after appropriate heat treatment.
- High Ductility: Unlike many high-strength aluminum alloys, Scalmalloy® retains good ductility (typically >10-12% elongation), making it more damage-tolerant.
- Excellent Dynamic Loading Performance: High fatigue strength, crucial for components subjected to cyclic loads in aerospace.
- Bonne résistance à la corrosion : Similar or better than standard Al-Mg alloys.
- Haute stabilité thermique : Retains strength at higher temperatures compared to AlSi10Mg and conventional high-strength aluminum alloys (e.g., 7075). Service temperatures can potentially reach up to 250°C.
- Designed for AM: Optimized for LPBF, exhibiting good processability and allowing for complex geometries.
- Aerospace Applications: Ideal for primary and secondary structural components requiring high strength, low weight, and good fatigue performance. Applications include highly loaded brackets, suspension components, airframe structures, optimized satellite components, heat exchangers, and performance-critical structural panels. It’s often chosen when AlSi10Mg lacks sufficient strength or thermal stability.
- Considérations relatives à la transformation :
- Traitement thermique : Requires specific multi-stage heat treatments to achieve its optimal microstructure and high-strength properties.
- Coût : Generally more expensive than AlSi10Mg due to the Scandium content and licensing.
- Optimisation des paramètres : Requires well-tuned LPBF process parameters for optimal density and properties.
Table: Typical Properties of LPBF Scalmalloy® (Heat Treated)
Propriété | Valeur typique | Unité | Notes |
---|---|---|---|
Densité | ~2.67 | g/cm³ | Similar to AlSi10Mg |
Yield Strength (Rp0.2) | 450 – 520 | MPa | Significantly higher than AlSi10Mg |
Résistance ultime à la traction | 500 – 580 | MPa | Approaching some Titanium grades |
Allongement à la rupture | > 10 – 15 | % | Excellent ductility for its strength class |
Module d'élasticité | ~70 | GPa | Similar to other Aluminum alloys |
Dureté | ~150 | HT | Dureté Vickers |
Température de service maximale | ~200 – 250 | °C | Higher thermal stability than AlSi10Mg/7xxx Al |
Exporter vers les feuilles
Why These Materials Matter for Aerospace Panels:
- AlSi10Mg : Offers a cost-effective solution for moderately loaded panels, complex geometries requiring AM’s design freedom, and rapid prototyping. Its good printability makes it reliable for complex internal features like lattices in panels where stiffness is key but loads are not extreme.
- Scalmalloy®: Provides a significant step up in performance, enabling the replacement of heavier materials (like titanium or steel in some cases) or traditionally manufactured high-strength aluminum parts with lighter, topology-optimized AM designs. Its fatigue resistance and ductility are critical for panels experiencing cyclic loading and requiring high damage tolerance.
Le rôle de Met3dp dans l'excellence matérielle :
The performance of any AM part is critically dependent on the quality of the metal powder used. Met3dp leverages des technologies de pointe en matière d'atomisation des gaz et de traitement par électrodes rotatives à plasma (PREP) to produce high-quality, spherical metal powders, including aluminum alloys like AlSi10Mg. Key characteristics of Met3dp powders include:
- Sphéricité élevée : Ensures good powder flowability in the printer, leading to uniform layer spreading and consistent melt pool behavior.
- Low Porosity: Minimizes internal gas pores within the powder particles, contributing to denser final parts.
- Distribution contrôlée de la taille des particules (PSD) : Optimized PSD for specific AM processes (like LPBF) ensures good packing density and predictable melting.
- Haute pureté : Minimizing contaminants that could compromise the mechanical properties of the final printed panel.
By controlling the powder manufacturing process using advanced techniques, Met3dp ensures that the AlSi10Mg and other powders (potentially including advanced aluminum alloys or custom compositions) supplied meet the stringent requirements of the aerospace industry, enabling customers to reliably print dense, high-quality structural panels with superior and consistent mechanical properties. Their commitment extends from poudres métalliques de haute qualité to the advanced SEBM and LPBF printers designed to process them effectively.
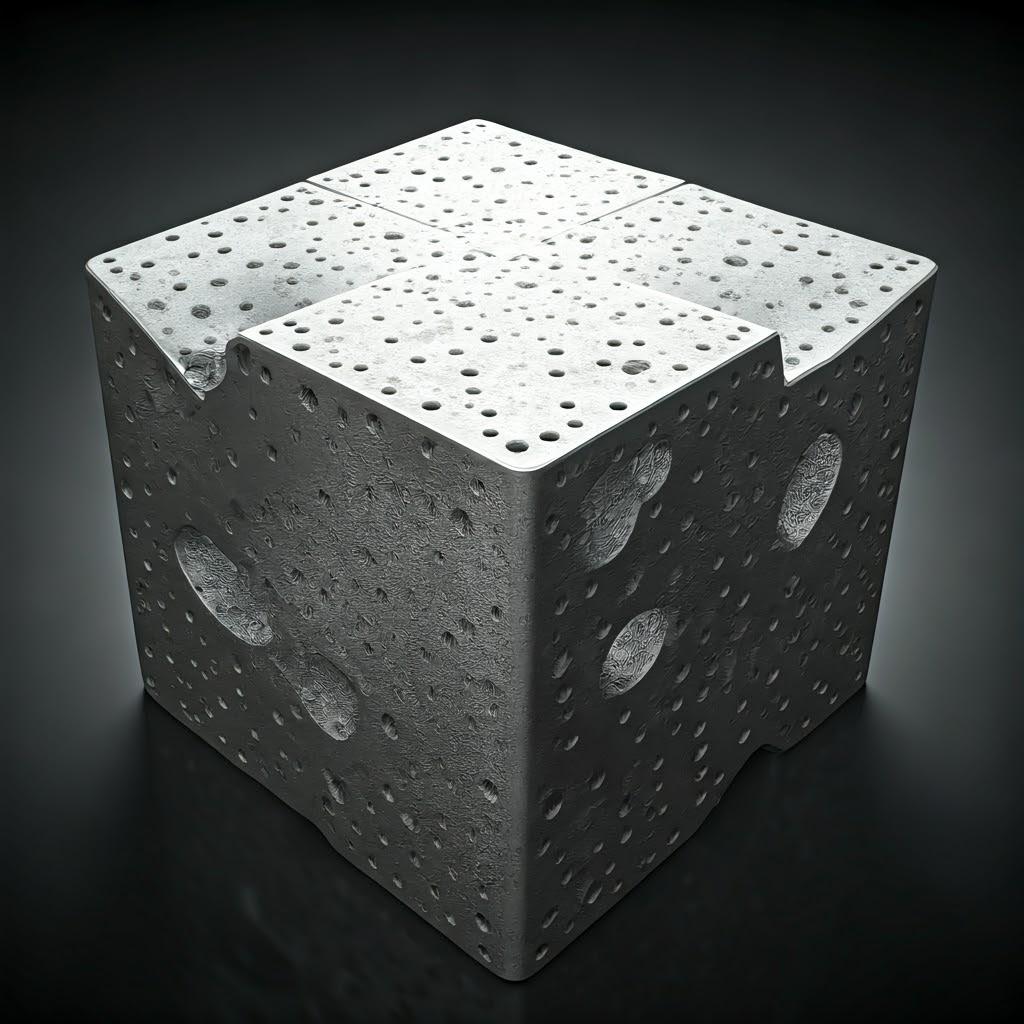
Design for Additive Manufacturing (DfAM): Optimizing Structural Panel Geometry
Simply replicating a traditionally designed structural panel using metal additive manufacturing often fails to capture the true potential of the technology. To unlock the significant weight savings, performance enhancements, and manufacturing efficiencies discussed earlier, engineers must embrace Conception pour la fabrication additive (DfAM) principles. DfAM is not just a set of rules; it’s a different way of thinking about component design, leveraging the unique capabilities of layer-by-layer fabrication while accounting for its constraints. For aerospace structural panels, applying DfAM is crucial for maximizing the strength-to-weight ratio, ensuring printability, and minimizing post-processing efforts. Successful implementation requires close collaboration between design engineers and additive manufacturing aerospace experts.
Key DfAM Principles for Aerospace Structural Panels:
- Topology Optimization and Generative Design:
- Concept: These computational tools are foundational to lightweighting structural panels. Starting with the design space (the maximum allowable volume for the panel), defined load cases (tension, compression, shear, vibration), constraints (mounting points, keep-out zones), and performance targets (stiffness, stress limits), algorithms iteratively remove material from non-critical areas.
- Optimisation de la topologie : Typically results in an organic, freeform structure representing the most efficient load path. This raw output often requires some interpretation and smoothing for manufacturability.
- Conception générative : Explores multiple design solutions simultaneously based on the defined parameters, often presenting several manufacturable options with different aesthetics or performance trade-offs.
- Panel Application: Ideal for creating panels with optimized internal ribbing, complex cutouts reinforced efficiently, or replacing solid sections with highly efficient, load-bearing structures. The resulting designs often look biomimetic, resembling bone structures or plant growth patterns.
- Logiciel : Tools like Altair Inspire, Autodesk Fusion 360 (Generative Design), Ansys Discovery, nTopology, and Siemens NX have powerful modules for these tasks.
- Structures en treillis :
- Concept: Replacing solid material within a panel’s volume with engineered, repeating unit cells (lattices) can dramatically reduce weight while maintaining significant structural integrity, particularly stiffness and buckling resistance. They also offer benefits like energy absorption and thermal management.
- Les types:
- Strut-Based Lattices: Composed of interconnected beams (e.g., cubic, octet-truss, diamond). Offer good stiffness and strength but can be challenging regarding self-supporting angles.
- Surface-Based Lattices (TPMS): Triply Periodic Minimal Surfaces (e.g., Gyroid, Schwarz-P, Diamond). Offer smooth, curved surfaces, are often self-supporting, provide excellent stiffness-to-weight ratios, and have good energy absorption properties. Increasingly popular for AM panels.
- Panel Application: Used to infill thicker panel sections, create sandwich panel cores without bonding, or design panels specifically for vibration damping or heat dissipation. Variable density lattices allow tailoring mechanical properties across the panel.
- Considérations : Lattice density, cell size, strut/wall thickness, and junction design are critical parameters influencing performance and printability (especially powder removal from complex internal structures). Software like nTopology excels in complex lattice generation and control.
- Minimizing and Optimizing Support Structures:
- Défi: Metal AM processes like LPBF require support structures for overhanging features (typically angles below 45 degrees from the build plate) and to anchor the part, preventing warping due to thermal stresses. Supports consume extra material, add print time, and require removal in post-processing, which can be labor-intensive and potentially damage the part surface.
- DfAM Strategies:
- Orientation Optimization: Choosing the optimal build orientation is critical. This involves balancing the need for supports against factors like surface finish requirements (upward-facing vs. downward-facing surfaces), residual stress accumulation, build time, and anisotropy of material properties. Simulation tools can help predict stress and distortion for different orientations.
- Conception d'angles autoportants : Where possible, modify overhangs to be above the critical angle (often ~45 degrees, but material and parameter dependent). Using chamfers or fillets instead of sharp horizontal overhangs can eliminate the need for supports in many cases.
- Canaux internes : Design internal channels with diamond or teardrop cross-sections to make them self-supporting.
- Support Reduction Features: Incorporate features that make support removal easier (e.g., notches at the support-part interface). Minimize supports on critical or hard-to-reach surfaces.
- Intégration des fonctionnalités et consolidation des pièces :
- Concept: Leverage AM’s complexity-for-free nature to combine multiple functions into a single panel.
- Exemples :
- Integrate stiffening ribs directly into the panel skin.
- Print mounting bosses, brackets, or connector housings as integral features.
- Incorporate hinges or snap-fit features (though material properties must be suitable).
- Embed channels for wiring, cooling fluids, or sensors directly within the panel structure.
- Avantages : Reduces part count, eliminates fasteners and assembly steps, decreases weight, and improves structural integrity by removing joints.
- Wall Thickness and Feature Size:
- Épaisseur minimale de la paroi : There are practical limits to how thin a feature can be reliably printed due to laser spot size, powder particle size, and thermal stability. For AlSi10Mg and Scalmalloy® using LPBF, minimum printable wall thicknesses are typically in the range of 0.3 mm to 0.8 mm, but achieving desired mechanical properties might require thicker walls (e.g., 1 mm or more). Thin, tall walls are particularly prone to distortion.
- Taille minimale des fonctionnalités : Small holes, pins, or intricate details also have limitations based on the process resolution.
- Considération : Design panels with wall thicknesses appropriate for the process and structural requirements, avoiding excessively thin unsupported sections.
- Stress Concentration Avoidance:
- Concept: Sharp internal corners or abrupt changes in geometry can act as stress concentrators, potentially leading to fatigue failure under cyclic loading – a critical concern in aerospace.
- DfAM Strategy: Use generous fillets and smooth transitions between sections of different thicknesses or orientations to distribute stress more evenly. Topology optimization naturally tends to produce designs with smooth, stress-reducing contours.
Table: DfAM Strategies for Aerospace Panels & Their Impact
DfAM Strategy | Primary Goal(s) | Key Benefit(s) | Considérations |
---|---|---|---|
Optimisation de la topologie | Maximize Stiffness/Strength-to-Weight Ratio | Significant weight reduction (30%+), optimal load path design | Requires specialized software, output may need refinement |
Generative Design | Explore multiple optimized design solutions | Rapid ideation, diverse manufacturable options, weight savings | Computationally intensive, requires clear objective definition |
Lattice Structures (TPMS/Strut) | Reduce density, add functionality (damping, thermal) | Extreme lightweighting, tunable properties, multi-functional panels | Printability (powder removal), performance simulation complexity |
Orientation Optimization | Minimize supports, manage stress, optimize surface | Reduced post-processing, lower cost, better surface quality, improved accuracy | Trade-offs between different factors, requires process knowledge |
Self-Supporting Features | Eliminate need for supports | Drastically reduced post-processing time/cost, less material waste | Geometric limitations (critical angle), may slightly increase weight |
Consolidation partielle | Reduce part count, simplify assembly | Lower weight (no fasteners), reduced assembly cost, increased reliability | Increased print complexity, NDT challenges for internal features |
Intégration des fonctionnalités | Add functionality without assembly | Weight/cost savings, enhanced performance (e.g., integrated cooling) | Design complexity, potential printability challenges |
Filleting/Smooth Transitions | Reduce stress concentrations | Improved fatigue life, increased durability | May slightly increase volume/weight compared to sharp corners |
Exporter vers les feuilles
Successfully applying these DfAM principles requires not just software tools but also a deep understanding of the chosen AM process (like LPBF or EBM offered by Met3dp), the specific material behavior (AlSi10Mg vs. Scalmalloy®), and the post-processing steps involved. Collaboration between designers and AM specialists from the concept phase onwards is paramount for creating truly optimized and manufacturable lightweight aerospace structural panels.
Atteindre la précision : Tolérance, état de surface et précision dimensionnelle
While metal additive manufacturing unlocks incredible design freedom, aerospace applications demand high levels of precision. Structural panels often interface with other components, requiring specific tolerances for assembly, and their surfaces may need particular characteristics for aerodynamic performance, sealing, or subsequent coating processes. Understanding the achievable levels of tolerance, surface finish, and dimensional accuracy with metal AM processes like Laser Powder Bed Fusion (LPBF) – and the factors influencing them – is critical for engineers and structural panel procurement managers.
Tolerances:
- Définition : Tolerance refers to the permissible range of variation in a dimension of a part.
- Typical AM Capabilities: For LPBF processes using materials like AlSi10Mg and Scalmalloy®, typical achievable tolerances are often cited as:
- Smaller parts (e.g., < 100-150 mm): +/- 0.1 mm to +/- 0.2 mm
- Larger parts (e.g., > 150 mm): +/- 0.1% to +/- 0.2% of the nominal dimension.
- Important Caveats:
- These are general guidelines. Actual achievable tolerances depend heavily on part geometry, size, orientation, material, machine calibration, and process parameters.
- Tighter tolerances (+/- 0.05 mm or better) usually require secondary CNC machining operations on critical features after printing.
- Tolerances can vary between different features on the same part (e.g., a hole diameter vs. overall panel length).
- DfAM Implication: Design critical interfaces or features requiring very tight tolerances with sufficient extra material (‘machining stock’) to allow for post-print CNC finishing. Avoid specifying unnecessarily tight tolerances on non-critical features, as this increases manufacturing cost and complexity.
Finition de la surface (rugosité) :
- Définition : Surface finish describes the texture of a part’s surface, often quantified by average roughness (Ra).
- As-Built Surface Finish: LPBF parts inherently have a degree of surface roughness due to the layer-wise nature of the process and partially melted powder particles adhering to the surface.
- Top Surfaces: Generally smoother, often Ra 5-15 µm.
- Vertical Walls: Moderate roughness, often Ra 10-20 µm.
- Down-Facing/Supported Surfaces: Tend to be roughest due to support structure contact or the nature of overhang formation, potentially Ra 15-30 µm or more. Curved surfaces also show stair-stepping effects depending on orientation.
- Impact of Parameters: Layer thickness, laser power, scan speed, and powder particle size all influence the as-built Ra. Finer powders and thinner layers generally yield smoother surfaces but increase build time.
- Post-Processing for Improvement: If the as-built finish is insufficient (e.g., for aerodynamic smoothness, sealing surfaces, or aesthetics), various post-processing steps are employed:
- Abrasive Blasting (Bead/Sand Blasting): Provides a uniform matte finish, removes loose powder, typically Ra 5-15 µm.
- Finition par culbutage et vibration : Uses media to smooth surfaces and edges, effective for batches of smaller parts, can achieve Ra < 5 µm.
- Usinage CNC : Provides the best control over surface finish on specific features, capable of Ra < 1 µm.
- Polissage (manuel ou automatisé) : Can achieve very smooth, mirror-like finishes (Ra << 1 µm) but is often labor-intensive.
- Électropolissage : An electrochemical process that can smooth surfaces, particularly effective on certain materials.
Table: Surface Finish (Ra) Comparison for Metal AM Panels
Surface Condition | Typical Ra Range (µm) | Notes |
---|---|---|
As-Built (Top Surface) | 5 – 15 | Smoothest as-built condition |
As-Built (Vertical Walls) | 10 – 20 | Influenced by layer thickness, parameters |
As-Built (Down-Facing) | 15 – 30+ | Roughest due to supports/overhangs; variable |
Abrasive Blasted | 5 – 15 | Uniform matte finish, good baseline |
Tumbled/Vibratory | 1 – 6 | Good for batch processing, edge radiusing |
CNC Machined | < 0.1 – 3 | Highly controlled, specific features only, geometry-dependent |
Polished | < 0.05 – 0.5 | Very smooth, labor-intensive, requires accessible surfaces |
Exporter vers les feuilles
Précision dimensionnelle :
- Définition : How closely the final part conforms to the nominal dimensions specified in the CAD model.
- Facteurs influençant la précision :
- Thermal Stresses and Warpage: Temperature gradients during printing cause expansion and contraction, leading to internal stresses. If not managed, these stresses can cause significant distortion (warping), especially in large, flat panels or parts with varying thicknesses. Supports and optimized scan strategies are crucial for mitigation.
- Material Shrinkage: Metals shrink upon solidification and cooling. This is generally compensated for in the slicing software, but non-uniform shrinkage can still affect accuracy.
- Stratégie de soutien : Inadequate or poorly placed supports can allow the part to warp during the build or break free, leading to dimensional errors or build failure.
- Étalonnage de la machine : Accurate laser positioning, stable energy output, and precise Z-axis movement are essential. Regular calibration and maintenance of printers, like the high-precision systems offered by Met3dp, are vital.
- Paramètres du processus : Laser power, scan speed, hatch spacing, and layer thickness affect the melt pool size and stability, influencing dimensional accuracy. Optimized parameter sets are crucial.
- Qualité de la poudre : Consistent powder characteristics (sphericity, PSD, flowability), such as those produced by Met3dp’s advanced atomization processes, contribute to stable melting and predictable shrinkage.
- Post-traitement : Stress relief heat treatments can cause minor dimensional changes. Machining operations improve accuracy on specific features but rely on the overall printed part being dimensionally sound enough for proper fixturing.
- Quality Control and Metrology: Due to the criticality of aerospace components, rigorous inspection is required.
- Coordinate Measuring Machines (CMMs): Provide high-accuracy point measurements for verifying critical dimensions and tolerances.
- Balayage laser 3D/balayage par lumière structurée : Capture the full 3D geometry of the panel, allowing comparison to the original CAD model (Geometric Dimensioning and Tolerancing – GD&T analysis) and visualization of deviations. Useful for complex, freeform shapes.
Achieving the required precision for aerospace structural panels using metal AM is a holistic process. It starts with DfAM, requires precise process control during printing on reliable machines using high-quality powder, often necessitates carefully planned post-processing steps, and mandates thorough metrology and quality verification. Partnering with an experienced AM provider like Met3dp, with expertise across the entire workflow from powder to finished part, is key to meeting stringent aerospace requirements.
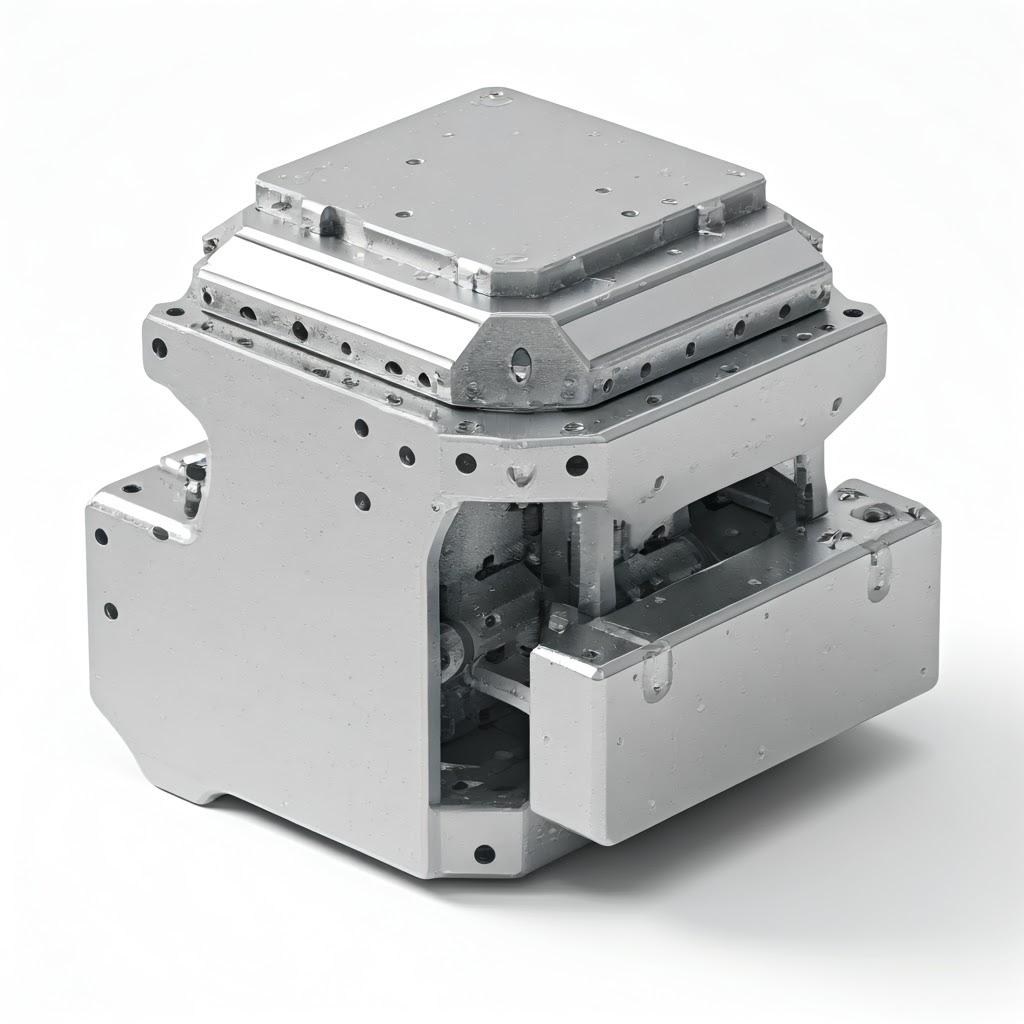
Beyond the Print: Essential Post-Processing for Aerospace Panels
Producing a geometrically accurate structural panel directly from the metal 3D printer is only part of the manufacturing journey, especially for demanding aerospace applications. The “as-built” part, while potentially complex and lightweight, rarely possesses the final material properties, surface characteristics, or dimensional tolerances required for flight-critical hardware. A series of carefully controlled post-processing metal 3D printing steps are typically necessary to transform the printed component into a functional, certified aerospace panel. Neglecting or improperly executing these steps can compromise the integrity and performance of the final product.
Common Post-Processing Steps for AM Aerospace Panels (AlSi10Mg, Scalmalloy®):
- Soulagement du stress / Traitement thermique :
- Why: This is arguably the most critical post-processing step for metal AM parts. The rapid heating and cooling cycles during layer-wise fusion create significant internal residual stresses within the printed component. These stresses can:
- Cause warping or distortion after the part is removed from the build plate or during subsequent machining.
- Reduce the part’s fatigue life and fracture toughness.
- Lead to premature failure under load. Furthermore, for precipitation-hardenable alloys like AlSi10Mg and Scalmalloy®, heat treatment is essential to develop the desired microstructure and achieve the target mechanical properties (strength, ductility, hardness).
- Processus :
- Soulagement du stress : Typically performed while the part is still attached to the build plate (if possible) or immediately after removal. Involves heating the part to a specific temperature below the aging temperature (e.g., 200-300°C for these aluminum alloys), holding it for a period, and then slowly cooling it. This allows internal stresses to relax without significantly altering the microstructure.
- Solutionizing & Aging (e.g., T6 treatment for AlSi10Mg, specific cycles for Scalmalloy®): Involves heating to a higher temperature to dissolve alloying elements into the aluminum matrix (solutionizing), rapidly quenching (cooling), and then heating to a lower temperature for an extended period (aging) to precipitate strengthening phases. The exact temperatures and times are critical and alloy-specific.
- Considérations : Heat treatment must be performed in accurately controlled furnaces (often vacuum or inert atmosphere to prevent oxidation). The process can cause minor dimensional changes (sagging or distortion if not properly supported) which must be accounted for.
- Why: This is arguably the most critical post-processing step for metal AM parts. The rapid heating and cooling cycles during layer-wise fusion create significant internal residual stresses within the printed component. These stresses can:
- Retrait de la structure de soutien :
- Why: Supports are necessary during the build but must be removed to reveal the final part geometry.
- Méthodes :
- Suppression manuelle : Breaking or cutting away supports using hand tools (pliers, saws, grinders). Labor-intensive and requires skill to avoid damaging the part surface. Most common for accessible supports.
- Machining (CNC or Wire EDM): Used for supports in critical areas, to achieve a cleaner separation surface, or when supports are difficult to reach manually. Wire EDM is particularly useful for intricate internal supports if access allows.
- Considérations : DfAM plays a huge role here – designing supports for easy access and removal saves significant time and cost. The removal process can leave witness marks or rough patches on the surface that may require further finishing.
- Usinage CNC :
- Why: Used to achieve tighter tolerances, specific surface finishes, or critical geometric features that cannot be accurately produced by the AM process alone.
- Applications for Panels:
- Machining mating surfaces or interfaces that connect to other structures.
- Creating precisely located holes or bores.
- Achieving very flat surfaces.
- Finishing features to tight GD&T specifications.
- Considérations : Requires careful fixture design to hold the potentially complex AM part securely without distortion. Sufficient machining stock must be included in the DfAM phase on features designated for machining. Combining AM’s ability to create the near-net shape with CNC’s precision finishing is often the most cost-effective approach for complex, high-accuracy panels.
- Traitements de surface :
- Why: To improve surface properties like roughness, fatigue life, corrosion resistance, wear resistance, or prepare the surface for bonding or painting.
- Common Treatments for Aluminum Alloy Panels:
- Abrasive Blasting/Shot Peening: As mentioned earlier, blasting cleans and provides a uniform finish. Shot peening uses small spherical media to bombard the surface, inducing compressive residual stresses which significantly improve fatigue life – often a requirement for aerospace panels.
- Tumbling/Mass Finishing: Smooths surfaces and deburrs edges.
- Anodizing: An electrochemical process that creates a hard, corrosion-resistant aluminum oxide layer on the surface. Can also be dyed for color-coding or cosmetic purposes. Common for aerospace aluminum parts.
- Conversion Coating (e.g., Alodine/Chromate Conversion): Provides corrosion resistance and serves as an excellent primer for paint adhesion. Health and environmental regulations are phasing out hexavalent chromium coatings in favor of trivalent chromium or non-chrome alternatives.
- Painting/Powder Coating: For final surface protection, camouflage, or thermal control. Proper surface preparation (cleaning, priming/conversion coating) is crucial for adhesion.
- Considérations : The choice of surface treatment depends on the specific application requirements (environmental exposure, loading conditions, interfacing materials). Some treatments may have dimensional implications or temperature limitations.
- Essais non destructifs (END) :
- Why: Absolutely essential for aerospace components to ensure internal and external integrity without damaging the part. NDT verifies that the panel is free from critical defects like cracks, porosity, or lack-of-fusion defects that could compromise its structural performance.
- Common NDT Methods for AM Panels:
- Inspection visuelle (VT) : Basic inspection for surface defects, warping, or gross anomalies.
- Dye Penetrant Inspection (PT): Reveals surface-breaking cracks or porosity.
- Tomodensitométrie (CT) : Uses X-rays to create a 3D map of the part’s internal structure, capable of detecting internal voids, porosity clusters, inclusions, and geometric deviations. Increasingly crucial for qualifying critical AM parts.
- Contrôle par ultrasons (UT) : Uses sound waves to detect subsurface flaws. Can be challenging on complex AM geometries.
- Eddy Current Testing (ET): Useful for detecting surface and near-surface flaws in conductive materials.
- Considérations : NDT requirements are typically dictated by aerospace standards (e.g., ASTM, MIL standards) and customer specifications. The complexity of AM parts, especially those with internal lattices, can make NDT interpretation challenging, requiring specialized techniques and trained inspectors.
The post-processing sequence must be carefully planned, often starting with stress relief and ending with final surface treatments and NDT. Each step adds time and cost but is indispensable for delivering airworthy structural panels that meet the rigorous safety and performance standards of the aerospace industry. Companies specializing in aerospace AM suppliers must possess robust capabilities and quality control throughout this entire workflow.
Navigating Challenges: Ensuring Success in Panel Production
While metal additive manufacturing offers transformative potential for lightweight aerospace structural panels, it’s not without its challenges. Achieving consistent, high-quality results that meet stringent aerospace specifications requires a deep understanding of the process, potential pitfalls, and effective mitigation strategies. Engineers and procurement managers should be aware of these common challenges when considering AM for panel production. Successfully navigating them often involves a combination of robust DfAM, optimized méthodes d'impression, rigorous process control, and meticulous post-processing.
Défis communs et stratégies d'atténuation :
- Warping, Distortion, and Residual Stress:
- Défi: The intense, localized heating from the laser or electron beam followed by rapid cooling creates steep thermal gradients within the part during the build. This leads to expansion and contraction, generating significant internal residual stresses. For large, relatively thin structures like panels, or parts with varying thicknesses, these stresses can cause significant warping during the build (pulling away from supports), after removal from the build plate, or during post-processing (e.g., machining).
- Mitigation Strategies:
- Simulation : Use process simulation software (e.g., Ansys Additive Suite, Simufact Additive, Netfabb) to predict thermal behavior and residual stress distribution for a given design and orientation. This allows for optimization before printing.
- Optimized Build Orientation: Choose an orientation that minimizes large flat areas parallel to the build plate and balances thermal mass distribution.
- Structures de soutien robustes : Design supports not just for overhangs but also to act as heat sinks and anchors against thermal stresses. Simulation can help optimize support placement and type.
- Stratégies d'analyse optimisées : Techniques like island/checkerboard scanning (breaking large layers into smaller sections scanned in a specific order) or varying scan vectors between layers help distribute heat more evenly and reduce long-range stress build-up.
- Process Parameter Control: Fine-tuning laser power, scan speed, and layer thickness affects the melt pool size and cooling rate, influencing stress.
- Traitement thermique anti-stress : Essential post-processing step, often performed before support removal, to relax internal stresses.
- Contrôle de la porosité :
- Défi: Pores are small voids within the printed material that can act as stress concentrators and significantly degrade mechanical properties, particularly fatigue life. Porosity can arise from two main sources:
- Porosité du gaz : Trapped gas (e.g., Argon shielding gas, dissolved gases in the powder) within the melt pool that gets frozen in during solidification. Often spherical.
- Lack-of-Fusion (LoF) Porosity: Insufficient energy input or improper melt pool overlap leads to incomplete melting and bonding between powder particles or layers. Often irregular in shape and more detrimental to properties.
- Mitigation Strategies:
- Poudre de haute qualité : Use powder with low internal gas porosity, controlled particle size distribution, good flowability, and minimal moisture content. Met3dp’s focus on advanced gas atomization and PREP technologies directly addresses this, producing powder with high sphericity and purity.
- Paramètres de processus optimisés : Develop and lock down parameters (laser power, speed, hatch spacing, layer thickness) that ensure complete melting and proper overlap for full densification (>99.5%, often >99.9% is achievable). Parameter development requires extensive testing and characterization.
- Proper Shielding Gas Flow: Ensure laminar, consistent flow of inert gas (Argon or Nitrogen) to remove process byproducts (spatter, fume) without disturbing the melt pool or powder bed.
- Machine Maintenance: Regular calibration and maintenance ensure consistent energy delivery and beam quality.
- NDT (CT Scanning): Crucial for detecting and characterizing internal porosity in critical parts.
- Défi: Pores are small voids within the printed material that can act as stress concentrators and significantly degrade mechanical properties, particularly fatigue life. Porosity can arise from two main sources:
- Difficultés liées au retrait de l'aide :
- Défi: Removing supports, especially complex internal supports within lattice structures or intricate channels, can be extremely difficult, time-consuming, and risks damaging the final part surface. Inaccessible powder trapped within complex internal voids can also be an issue.
- Mitigation Strategies:
- DfAM : Design for minimal support use (self-supporting angles, optimal orientation). Design supports for accessibility and easy removal (e.g., using specialized support types with weaker interfaces). Design features to allow trapped powder to escape (drainage holes).
- Optimisation des processus : Some support types (e.g., thin-walled or tree supports) are easier to remove than solid block supports.
- Techniques avancées de suppression : Consider Wire EDM or chemical etching for specific challenging support removal tasks (material compatibility permitting).
- Careful Manual Removal: Requires skilled technicians and appropriate tools.
- Powder Handling, Safety, and Recyclability:
- Défi: Fine metal powders, especially reactive ones like aluminum or titanium, can pose respiratory and fire/explosion hazards if not handled correctly. Maintaining powder quality through recycling is also crucial for cost-effectiveness and consistency but requires careful management to avoid contamination or degradation.
- Mitigation Strategies:
- Protocoles de sécurité : Implement strict procedures for powder handling, storage, loading/unloading, and disposal, including appropriate Personal Protective Equipment (PPE), grounding, inert atmosphere handling where necessary, and ATEX-rated equipment if required.
- Powder Management Systems: Use automated or semi-automated systems for sieving, blending, and transporting powder to minimize operator exposure and maintain powder quality.
- Recycling Strategy: Define clear protocols for powder reuse, including sieving to remove oversized particles/spatter, tracking batch history, potentially blending virgin and used powder, and periodic testing to ensure recycled powder still meets specifications (chemistry, PSD, flowability). Limits on the number of reuse cycles are often implemented.
- Achieving Consistent Material Properties:
- Défi: Ensuring that the mechanical properties (strength, ductility, fatigue life) are consistent across a large panel, from batch to batch, and meet aerospace specifications requires tight control over the entire process chain. Variations in powder quality, machine calibration, process parameters, or heat treatment can lead to inconsistent properties.
- Mitigation Strategies:
- Système de gestion de la qualité (SGQ) robuste : Implement a certified QMS (like AS9100 for aerospace) covering all aspects from powder procurement to final inspection.
- Surveillance des processus : Utilize in-situ monitoring tools (melt pool monitoring, thermal imaging) where available to detect process deviations in real-time.
- Procédures normalisées : Lock down validated process parameters, heat treatment cycles, and post-processing steps.
- Regular Testing: Conduct regular material testing (tensile tests, microstructure analysis) on witness coupons printed alongside parts to verify properties for each build or batch.
- Partnering with Experts: Work with experienced AM service providers like Met3dp who have demonstrated expertise in process control, materials science, and quality assurance for demanding industries. Met3dp’s integrated approach, combining high-reliability printers with their own meticulously produced powders, provides a strong foundation for achieving consistent results.
Overcoming these challenges is essential for the successful adoption of metal AM for aerospace structural panels. It requires investment in technology, process development, quality control, and skilled personnel, highlighting the importance of selecting a capable and experienced manufacturing partner.
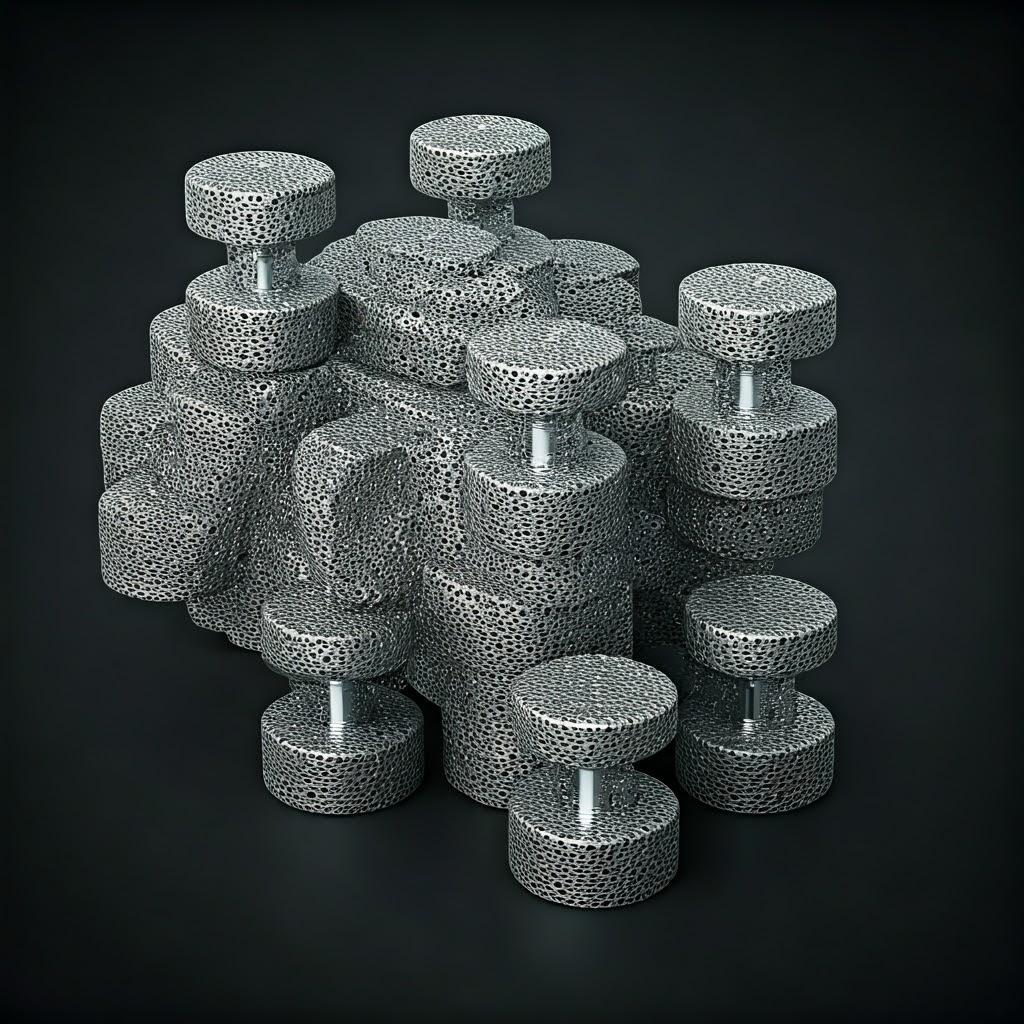
Selecting Your Partner: Choosing the Right Metal AM Service Provider
The successful implementation of metal additive manufacturing for critical components like aerospace structural panels hinges significantly on the capabilities and expertise of your chosen manufacturing partner. While the technology itself offers immense potential, realizing its benefits – lightweighting, complex geometries, part consolidation, and performance gains – requires a provider with deep technical knowledge, robust processes, stringent quality control, and a proven track record in demanding industries. Selecting the right metal 3D printing service provider aerospace specialist is a critical step for engineers and procurement managers.
Here are key criteria to evaluate when choosing a partner for producing your AlSi10Mg or Scalmalloy® structural panels:
- Certifications et conformité aérospatiales :
- AS9100 : This is the internationally recognized Quality Management System (QMS) standard for the Aviation, Space, and Defense industries. Certification to AS9100 (or equivalent standards like EN 9100) is often non-negotiable for flight hardware. It demonstrates a commitment to quality, traceability, risk management, and continuous improvement specific to aerospace requirements.
- NADCAP: National Aerospace and Defense Contractors Accreditation Program. While AS9100 covers the overall QMS, NADCAP provides specific accreditations for special processes like heat treatment, welding, non-destructive testing (NDT), and chemical processing (like anodizing or conversion coating). If your chosen provider performs these critical post-processing steps in-house, NADCAP accreditation adds significant confidence.
- ISO 9001 : A fundamental QMS standard, but generally insufficient on its own for critical aerospace work.
- OEM Qualifications: Specific aircraft or engine manufacturers may have their own qualification requirements for suppliers.
- Technical Expertise and Engineering Support:
- DfAM Capability: Does the provider offer expert support in Design for Additive Manufacturing? Can they assist your team in topology optimization, lattice structure design, support strategy optimization, and adapting designs specifically for AM to maximize benefits and ensure printability?
- Materials Science Knowledge: Deep understanding of the chosen materials (AlSi10Mg, Scalmalloy®) is crucial. This includes knowledge of their behavior during printing, optimal heat treatment cycles for desired properties, and potential failure modes.
- Simulation de processus : Do they utilize process simulation tools to predict and mitigate residual stress, distortion, and potential build failures before printing begins?
- Process Parameter Development: Have they developed and validated robust, optimized printing parameters specifically for the alloys and machines they use?
- Machine Capabilities and Capacity:
- Technologie: Do they operate the appropriate AM technology (primarily LPBF for these aluminum alloys)?
- Volume de construction : Can their machines accommodate the size of your structural panels? For very large panels, inquire about capabilities for printing in sections and potential joining methods (though single-piece printing is often preferred). Met3dp, for instance, offers printers with industry-leading print volume, accuracy, and reliability, suitable for large, mission-critical parts.
- Parc de machines : How many suitable machines do they have? This impacts capacity, redundancy (backup if a machine is down), and potentially lead times for larger or urgent orders.
- Maintenance & Calibration: What are their procedures for machine maintenance and calibration to ensure consistent performance?
- Material Portfolio and Powder Management:
- Alloy Availability: Do they consistently stock and have validated processes for AlSi10Mg and/or Scalmalloy®?
- Contrôle de la qualité des poudres : What are their procedures for incoming powder inspection, handling, storage, and recycling? How do they ensure powder traceability and prevent cross-contamination? Partnering with a provider like Met3dp, which manufactures its own poudres métalliques de haute qualité using advanced atomization techniques, can provide an added layer of quality assurance and material consistency.
- Parameter Sets: Do they have proven, locked-down parameter sets specifically for these alloys on their machines to achieve optimal density and mechanical properties?
- Integrated Post-Processing Capabilities:
- Champ d'application : What post-processing steps can they perform in-house (stress relief/heat treatment, support removal, CNC machining, surface finishing, NDT)? Having integrated capabilities streamlines the workflow, reduces lead times, simplifies logistics, and improves quality control compared to managing multiple subcontractors.
- Expertise : Do they have the necessary equipment (e.g., calibrated vacuum furnaces, multi-axis CNC machines, NDT equipment) and skilled personnel for these critical steps? If outsourcing, do they have qualified, trusted partners?
- Quality Management System (QMS) and Traceability:
- Robustness: Beyond certifications, evaluate the depth of their QMS. How do they ensure process control, document procedures, manage non-conformances, and handle corrective actions?
- Traceability: Can they provide full traceability from raw powder batch to the final shipped part, including all process parameters, post-processing steps, and inspection results? This is mandatory for aerospace components.
- Métrologie : What inspection equipment do they possess (CMMs, 3D scanners, standard metrology tools)? What are their calibration procedures?
- Track Record and Experience:
- Aerospace Experience: Have they successfully produced similar structural components or other critical parts for the aerospace industry? Can they provide (non-confidential) case studies or references?
- Material Experience: Specific experience with AlSi10Mg and Scalmalloy® is highly desirable.
- Collaboration and Communication:
- Responsiveness: Are they easy to communicate with? Do they provide timely responses to inquiries and technical questions?
- Project Management: Do they have clear processes for project management, updates, and handling potential issues?
- Partnership Approach: Do they act as a true partner, willing to collaborate on design challenges and process optimization, rather than just a print-to-spec service?
Met3dp as Your Partner:
Met3dp embodies many of these critical attributes. As a company specializing in both metal 3D printing equipment and high-performance metal powders, they possess a unique, vertically integrated perspective. Their decades of collective expertise in metal additive manufacturing translate into comprehensive solutions. Key strengths include:
- Advanced Printers: Offering systems known for industry-leading volume, accuracy, and reliability, crucial for demanding aerospace panels.
- Poudres de haute qualité : Employing leading gas atomization and PREP technologies to manufacture powders like AlSi10Mg with high sphericity, purity, and flowability, ensuring consistent printing results.
- Integrated Solutions: Providing support that spans equipment, materials, and application development services, fostering a true partnership approach.
- Commitment to Quality: Focusing on delivering dense, high-quality metal parts with superior mechanical properties suitable for mission-critical applications.
Choosing the right partner is an investment in the success of your project. Thoroughly vetting potential providers against these criteria will significantly increase the likelihood of receiving high-quality, reliable, and optimized aerospace structural panels.
Understanding Investment: Cost Factors and Lead Times for AM Panels
While metal additive manufacturing enables the production of highly optimized, lightweight structural panels, understanding the associated costs and typical lead times is crucial for project planning, budgeting, and comparing AM against traditional manufacturing routes. The cost structure and timing for AM differ significantly from conventional methods, influenced by factors unique to layer-by-layer fabrication and its necessary ancillary processes. Procurement managers seeking bulk metal 3D printing quote options need to understand these drivers.
Key Cost Drivers for AM Structural Panels:
- Coût des matériaux :
- Powder Price: The cost per kilogram of the metal powder is a primary factor. High-performance alloys like Scalmalloy® are significantly more expensive than AlSi10Mg due to alloying elements like Scandium and potentially licensing fees.
- Material Consumed: This includes the volume of the part itself plus the volume of support structures required. Efficient DfAM (minimizing supports, using topology optimization) directly reduces material consumption.
- Powder Recycling Efficiency: The ability to safely reuse unsintered powder affects the overall material cost per part. Good powder management and recycling protocols help amortize powder costs.
- Le temps des machines :
- Temps de construction : This is often the most significant cost component for the printing step itself. Build time is primarily driven by the hauteur of the build (number of layers), not just the volume. Laser scanning time per layer (dependent on part cross-sectional area and scan strategy) also contributes.
- Machine Depreciation & Operating Costs: The capital cost of industrial metal AM systems, maintenance, consumables (filters, inert gas), and energy consumption are factored into the hourly machine rate.
- Nesting Efficiency: Printing multiple panels or parts simultaneously in one build (nesting) utilizes the build volume more efficiently and can reduce the effective machine time cost per part.
- Coûts de main-d'œuvre :
- Setup & Teardown: Preparing the build file, setting up the machine, loading powder, removing the build plate and parts.
- Build Monitoring: While often automated, some level of monitoring may be required.
- Post-Processing Labor: This can be substantial. Includes manual support removal, part cleaning, operation of post-processing equipment (furnaces, CNCs, finishing tools), inspection, and documentation. The complexity of the part and support structures heavily influences this cost.
- Engineering and Design Costs (NRE):
- DfAM & Optimization: Time spent by engineers redesigning or optimizing the panel for AM, performing topology optimization, or running simulations.
- Planification des processus : Developing the build strategy, support structures, and post-processing plan.
- Initial Qualification: For critical aerospace parts, initial process validation and testing can involve significant NRE costs.
- Amortization: These non-recurring engineering costs are typically amortized over the production volume. Higher volumes lead to lower NRE cost per part.
- Coûts de post-traitement :
- Traitement thermique : Furnace time, energy consumption, inert gas/vacuum usage.
- Usinage : CNC machine time, tooling costs, programming time, fixture costs.
- Finition de la surface : Cost of materials (blasting media, chemicals) and labor/machine time for processes like shot peening, anodizing, painting.
- NDT : Equipment usage (especially CT scanning, which can be expensive) and expert analysis time.
- Assurance qualité et inspection :
- Métrologie : Time for CMM measurements, 3D scanning, and data analysis.
- Documentation : Creating compliance reports, material certifications, traceability records.
Factors Influencing Lead Times:
Lead time in AM is the total time from order placement (or file submission) to final part delivery. It’s often less dependent on complex tooling than traditional methods but highly dependent on machine availability and the extensive post-processing required for aerospace components.
- Conception et préparation : DfAM optimization, simulation, support generation, and build file slicing. Can range from hours to days or weeks depending on complexity and engineering resources.
- Queue Time: Waiting for an available machine with the correct material loaded. Can vary significantly based on the service provider’s workload (days to weeks).
- Print Time: Directly related to build height and volume. Large or complex panels can take multiple days to print continuously (24/7 operation).
- Cooling and Depowdering: Allowing the build chamber and part to cool sufficiently before removal, followed by careful removal of bulk unsintered powder. (Hours)
- Post-traitement : Often the longest portion of the lead time:
- Stress Relief/Heat Treatment: Can take 1-3 days including furnace cycles and controlled cooling.
- Support Removal & Machining: Highly variable based on complexity (days to weeks).
- Finition de la surface : Variable based on process (days).
- CND et inspection : Scheduling, performing tests, and analyzing results (days to weeks).
- Expédition: Logistics time.
Délais d'exécution typiques : For a moderately complex aerospace structural panel requiring full post-processing and qualification, lead times can range from 2 to 8 weeks, or potentially longer for very large/complex parts or during periods of high demand. While AM excels at rapid prototyping (where minimal post-processing might suffice), production lead times for qualified aerospace parts are substantial due to the necessary downstream steps.
Comparison Snapshot:
Aspect | Metal AM (LPBF – AlSi10Mg/Scalmalloy) | Traditional (e.g., CNC Machining from Billet) |
---|---|---|
Coût de l'outillage | Very Low / None | High (for complex fixtures, potentially molds) |
NRE Cost | Moderate to High (DfAM, Simulation, Qualification) | Moderate (Programming, fixture design) |
Coût matériel | Moderate (Efficient Use but powder cost, supports) | High (Inefficient use – high scrap rate) |
Per-Part Cost (Low Vol) | Often Lower (due to no tooling) | High (Tooling amortization) |
Per-Part Cost (High Vol) | Potentially Higher (longer cycle time) | Lower (Efficient machining cycles) |
Délai d'exécution (Prototype) | Very Fast (Days) | Slow (Weeks – tooling/setup) |
Délai (production) | Moderate to Long (2-8+ weeks due to post-processing) | Moderate (Once setup, faster cycle times) |
Complexité | Handles high complexity well, cost less sensitive | Cost increases significantly with complexity |
Exporter vers les feuilles
Understanding these cost and lead time dynamics allows for better decision-making when evaluating AM for structural panels, ensuring realistic project planning and budgeting.
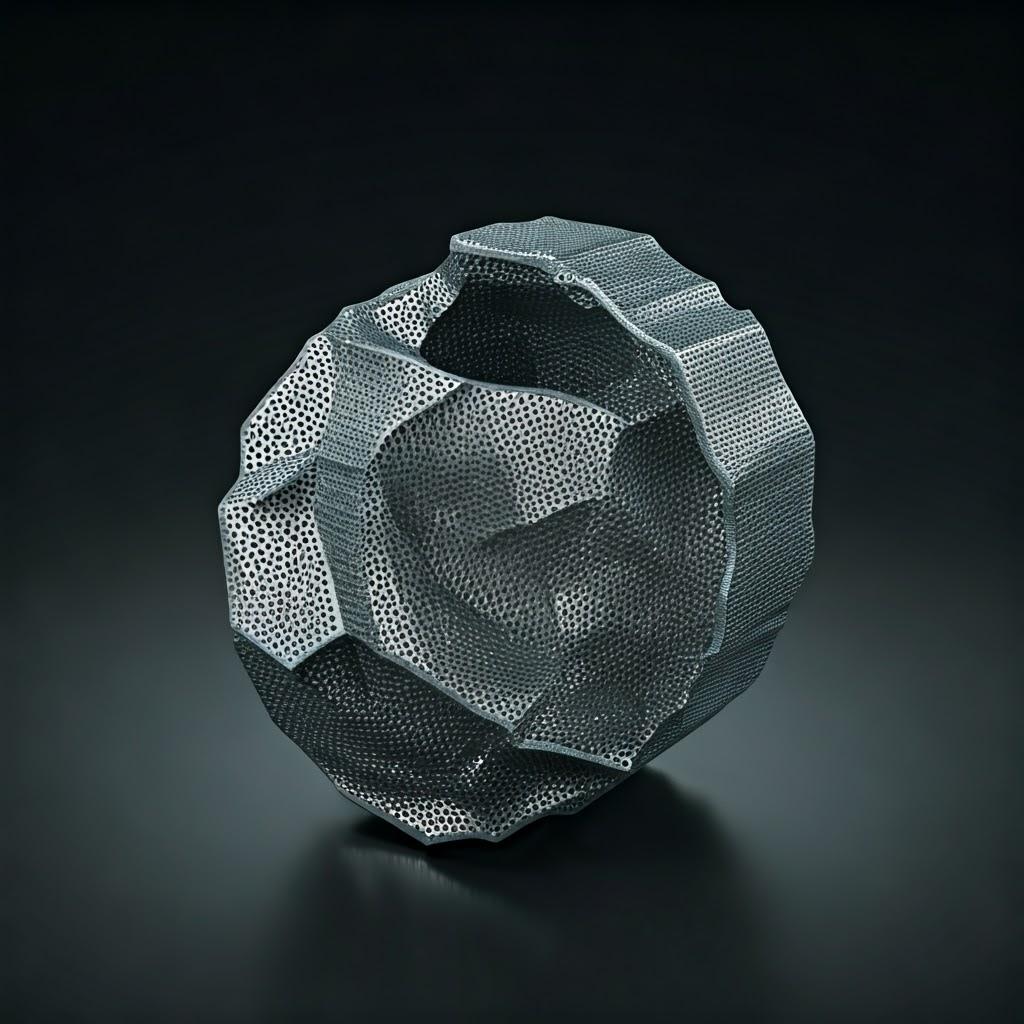
Foire aux questions (FAQ)
Here are some common questions engineers and procurement managers have about using metal additive manufacturing for aerospace structural panels made from AlSi10Mg or Scalmalloy®:
- Q1: How does the strength of 3D printed AlSi10Mg or Scalmalloy® panels compare to traditionally manufactured aluminum panels?
- A1 : It depends on the specific alloys being compared.
- AlSi10Mg (LPBF, Heat Treated): Typically exhibits strength comparable to mid-range aluminum casting alloys but generally lower strength and ductility than common wrought aerospace alloys like 6061-T6 or 7075-T6. However, the ability to create optimized geometries via AM can result in a final component that is lighter for the same performance, even if the base material properties are slightly lower.
- Scalmalloy® (LPBF, Heat Treated): Offers significantly higher strength than AlSi10Mg and traditional aluminum alloys like 6061 or even 7075 in some aspects (especially specific strength and performance at slightly elevated temperatures). Its strength can approach that of some titanium alloys while being much lighter. Its combination of high strength and good ductility is a key advantage over many conventional high-strength aluminum options. For demanding panels, Scalmalloy® allows AM parts to meet or exceed the performance of traditionally manufactured high-strength aluminum components, often at a lower weight due to design optimization.
- A1 : It depends on the specific alloys being compared.
- Q2: What are the typical size limitations for 3D printing large aerospace structural panels?
- A2 : Size limitations are dictated by the build volume of the metal AM machines. Typical large-format LPBF machines might have build envelopes around 400 x 400 x 400 mm up to 800 x 500 x 500 mm, with some newer systems pushing even larger dimensions (e.g., towards 1 meter in X/Y). Companies like Met3dp focus on providing systems with industry-leading print volumes. For panels exceeding the build volume of available machines, options include printing the panel in sections and joining them using methods like welding or specialized fasteners, though this adds complexity and potential weak points. Design considerations (like orientation) can also influence the maximum printable size within a given build chamber.
- Q3: Can existing panel designs, originally made for CNC machining or sheet metal, be directly 3D printed?
- A3 : While it’s technically possible to print a design originally intended for traditional manufacturing, doing so typically fails to leverage the key advantages of AM and may even result in a suboptimal or difficult-to-print part. Designs intended for machining often feature simple geometries, thick sections, and assume tool access constraints that are irrelevant in AM. To gain the primary benefits of AM (lightweighting through topology optimization/lattices, part consolidation), redesigning the panel using Design for Additive Manufacturing (DfAM) principles is highly recommended, and often necessary, to achieve significant weight savings and performance improvements. Direct printing might be feasible for legacy part replacement where redesign isn’t an option, but expect minimal performance gains.
- Q4: What quality certifications are most essential for aerospace AM suppliers like Met3dp?
- A4 : The most critical certification is AS9100 (or EN 9100 / JISQ 9100), the specific Quality Management System standard for the aerospace industry. It ensures rigorous processes for quality, traceability, risk management, and continuous improvement. Additionally, NADCAP accreditation for special processes (like heat treatment, NDT, chemical processing) performed by the supplier provides further assurance of process control and compliance for those specific operations. While ISO 9001 is a foundational QMS standard, AS9100 is the expected baseline for suppliers manufacturing flight-critical hardware. Met3dp’s commitment to industry-leading reliability and quality aligns with the principles underlying these essential certifications.
Conclusion: Elevating Aerospace Structures with Metal Additive Manufacturing
The quest for lighter, stronger, and more efficient aerospace structures is relentless. Metal additive manufacturing has decisively moved beyond prototyping to become a powerful production technology capable of meeting this challenge head-on, particularly for components like structural panels. By leveraging the unique capabilities of AM processes like Laser Powder Bed Fusion, aerospace engineers can now design and produce panels in advanced materials like AlSi10Mg and the high-performance Scalmalloy® (alliage d'aluminium) alloy, achieving results previously unattainable with conventional methods.
The key advantages are clear and compelling:
- Un allègement sans précédent : Through topology optimization and internal lattice structures, AM enables drastic weight reductions in structural panels without compromising strength or stiffness, directly enhancing fuel efficiency, payload capacity, and overall vehicle performance.
- Geometric Complexity: AM thrives on complexity, allowing the creation of intricate, organic shapes that efficiently distribute loads and integrate multiple functions.
- Consolidation partielle : Combining multiple brackets, stiffeners, and skin sections into a single, monolithic printed panel reduces part count, eliminates fasteners, simplifies assembly, and enhances reliability.
- Efficacité matérielle : Significantly improved buy-to-fly ratios compared to subtractive machining reduce waste of expensive aerospace alloys.
However, realizing this potential requires navigating the intricacies of Design for Additive Manufacturing (DfAM), precise process control, essential post-processing steps (like heat treatment, machining, and NDT), and careful material management. Overcoming challenges related to residual stress, porosity, and dimensional accuracy demands expertise and robust quality systems.
The choice of materials like AlSi10Mg provides a reliable, cost-effective solution for moderately loaded panels, while Scalmalloy® pushes the performance envelope, offering exceptional strength-to-weight ratios and fatigue properties for the most demanding applications.
Successfully integrating AM into the production of aerospace structural panels relies heavily on collaboration with a knowledgeable and capable partner. Companies like Met3dp stand at the forefront, offering a synergistic combination of industry-leading AM systems known for their volume and reliability, advanced powder manufacturing capabilities ensuring material quality, and deep collective expertise in metal additive manufacturing. Their comprehensive solutions empower aerospace manufacturers to harness the full transformative power of AM.
Whether you are exploring AM for the first time or seeking a reliable partner for serial production of lightweight structural panels, the future of aerospace manufacturing is undeniably additive.
Ready to explore how metal additive manufacturing can revolutionize your aerospace structural components? Contact Met3dp today to discuss your specific requirements and discover how our advanced printers, high-performance powders, and expert services can help you achieve your lightweighting and performance goals.
Partager sur
MET3DP Technology Co. est un fournisseur de premier plan de solutions de fabrication additive dont le siège se trouve à Qingdao, en Chine. Notre société est spécialisée dans les équipements d'impression 3D et les poudres métalliques de haute performance pour les applications industrielles.
Articles connexes
À propos de Met3DP
Mise à jour récente
Notre produit
CONTACTEZ-NOUS
Vous avez des questions ? Envoyez-nous un message dès maintenant ! Nous répondrons à votre demande avec toute une équipe dès réception de votre message.
Obtenir les informations de Metal3DP
Brochure du produit
Obtenir les derniers produits et la liste des prix
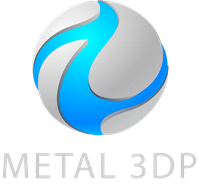
Poudres métalliques pour l'impression 3D et la fabrication additive