3D Printed Cooling Plates for Electric Vehicles: Revolutionizing Thermal Management with Additive Manufacturing
Table des matières
Introduction: Powering the EV Revolution with Advanced Cooling
The electric vehicle (EV) market is accelerating at an unprecedented pace, driven by technological advancements, environmental concerns, and shifting consumer preferences. Central to the performance, longevity, and safety of EVs is effective thermal management. Batteries, electric motors, and power electronics generate significant heat during operation, and controlling these temperatures is paramount. Traditional cooling solutions often struggle to meet the increasingly demanding requirements of modern EV architectures. This is where métal Impression 3D, also known as additive manufacturing (AM), emerges as a transformative technology. By enabling the creation of highly complex and efficient 3D printed cooling plates, AM is revolutionizing how manufacturers approach thermal management challenges in the automotive sector.
EV cooling plates, often referred to as cold plates, are essential heat exchangers designed to absorb and dissipate heat from critical components. They typically circulate a coolant through internal channels, transferring thermal energy away from heat sources like battery cells or power modules. As EV batteries become more energy-dense and charging speeds increase, the need for sophisticated EV thermal management solutions becomes critical. Inefficiencies in cooling can lead to reduced battery lifespan, compromised performance, safety risks (thermal runaway), and slower charging capabilities.
Conventional manufacturing methods for cooling plates, such as brazing multiple stamped or machined components, casting, or extensive CNC machining, often face limitations. These methods can restrict design complexity, particularly for internal channel geometries, potentially leading to suboptimal thermal performance, heavier components, and multiple potential failure points at joints or seals. The quest for higher performance, lighter weight, and more compact designs necessitates a new approach.
Additive manufacturing offers a paradigm shift. It allows engineers to design cooling plates with intricate internal structures, such as complex lattice networks, biomimetic channels, or passages that conform precisely to the shape of the components being cooled. This geometric freedom translates directly into significantly enhanced heat transfer efficiency, reduced pressure drop, and optimized coolant flow – benefits unattainable with traditional processes. Furthermore, AM enables part consolidation, rapid prototyping, and the use of advanced materials specifically chosen for thermal performance and low weight. For procurement managers and engineers in the automotive industry seeking high-performance cooling plates and reliable EV component suppliers, understanding the capabilities of metal AM is becoming increasingly vital.
Met3dp stands at the forefront of this technological wave. As a leading provider of industrial metal additive manufacturing solutions, Met3dp specializes in both advanced 3D printing equipment and the high-performance metal powders essential for producing mission-critical parts. With industry-leading print volume, accuracy, and reliability, our systems are tailored for demanding applications in aerospace, medical, automotive, and industrial manufacturing. Our expertise in powder metallurgy, utilizing cutting-edge gas atomization and Plasma Rotating Electrode Process (PREP) technologies, ensures the production of superior quality spherical metal powders like AlSi10Mg, ideal for manufacturing lightweight and thermally efficient EV cooling plates. Partnering with Met3dp provides access to comprehensive solutions, empowering companies to leverage the full potential of fabrication additive automobile for next-generation EV development. This post will delve into the specifics of 3D printed EV cooling plates, exploring their applications, the advantages of using AM, recommended materials, design considerations, and more, providing a comprehensive guide for businesses looking to source or implement these advanced components. We aim to be your trusted wholesale cooling plate manufacturing partner.
What are EV Cooling Plates Used For? Applications and Critical Functions
EV cooling plates are specialized heat exchangers meticulously designed to manage the thermal loads generated by various key components within an electric vehicle’s ecosystem. Their primary role is to maintain these components within their optimal operating temperature ranges, ensuring efficiency, reliability, safety, and longevity. The transition to electrification places immense pressure on thermal management systems, making advanced cooling plates indispensable.
The core functions and applications include:
- Battery Thermal Management System (BTMS): This is arguably the most critical application.
- Fonction : EV batteries generate significant heat during both charging and discharging cycles, especially under high power demand (acceleration) or fast charging conditions. Cooling plates are integrated into battery packs, often placed between battery modules or beneath cells, to absorb this heat and transfer it to the vehicle’s coolant loop.
- Importance : Maintaining battery temperatures within a narrow optimal range (typically 20-40°C) is crucial for:
- Performance : Prevents overheating, which can limit power output and acceleration.
- Lifespan: Reduces degradation mechanisms accelerated by high temperatures, extending battery service life.
- La sécurité : Mitigates the risk of thermal runaway, a dangerous condition where excessive heat triggers uncontrolled exothermic reactions within cells.
- Charging Speed: Allows for faster charging rates by effectively dissipating the generated heat.
- Les types: Designs vary from simple serpentine channels to complex micro-channel or lattice structures, depending on the required cooling capacity and packaging constraints.
- Electric Motor Cooling:
- Fonction : High-performance electric motors, particularly permanent magnet synchronous motors (PMSM) common in EVs, generate substantial heat in the stator windings and rotor due to electrical resistance (Joule heating) and magnetic losses. Cooling plates, often integrated into the motor housing (as cooling jackets) or placed in direct contact with heat-generating elements, remove this heat.
- Importance : Prevents motor overheating, which can lead to demagnetization of permanent magnets, insulation breakdown, reduced efficiency, and decreased power output. Effective cooling allows motors to operate at higher power densities and sustain peak performance for longer periods.
- Trend: As motors become more powerful and compact, the need for advanced cooling solutions like intricately channeled 3D printed plates increases.
- Power Electronics Cooling:
- Fonction : Power electronic components, such as inverters (DC-to-AC conversion for the motor), converters (DC-to-DC for auxiliary systems), and onboard chargers, handle large amounts of electrical power and consequently generate significant heat due to switching losses and conduction losses. Cooling plates are used as heat sinks, often with direct mounting interfaces for power modules (e.g., IGBTs, SiC MOSFETs).
- Importance : These semiconductor devices are highly sensitive to temperature. Overheating can drastically reduce their lifespan, impair performance, and lead to component failure, potentially disabling the vehicle. Efficient cooling ensures reliable operation and enables higher power density designs, making the power electronics units smaller and lighter.
- Défi: Power electronics often have very high heat flux densities, requiring cooling solutions with exceptionally high thermal conductivity and optimized fluid flow paths, areas where 3D printing excels.
- Other Potential Applications:
- Integrated Thermal Systems: AM allows for the potential integration of cooling channels directly into structural components or housings, further consolidating parts and improving thermal pathways.
- High-Performance Computing (HPC) / Control Units: Advanced driver-assistance systems (ADAS) and central computing units in modern vehicles also generate heat that may require dedicated cooling solutions, potentially utilizing compact 3D printed cold plates.
- Beyond Automotive: While the focus here is EVs, similar 3D printed cooling plates find applications in other demanding sectors requiring advanced thermal management, such as high-power industrial electronics, aerospace systems, medical devices (e.g., laser cooling), and data center cooling.
Industries desservies :
- Primary: Automotive (Electric Vehicles, Hybrid Electric Vehicles, Plug-in Hybrid Electric Vehicles)
- Secondary: Electric Mobility (E-Buses, Electric Trucks, Electric Motorcycles), Motorsport (Electric Racing Series), Aerospace (Electric Aircraft Components), Industrial Electronics, High-Performance Computing.
Procurement managers and engineering teams sourcing automotive cooling solutions or looking for electric vehicle component manufacturers must recognize the critical role these plates play. They are not merely passive components but active enablers of EV performance and reliability. The ability to customize designs for specific vehicle architectures, battery chemistries, or power levels makes flexible manufacturing techniques like Impression 3D de métaux particularly attractive. Met3dp collaborates closely with automotive clients to develop and manufacture cooling plates optimized for their unique thermal challenges, leveraging our deep understanding of both additive manufacturing processes and material science to deliver effective EV powertrain cooling and BTMS solutions.
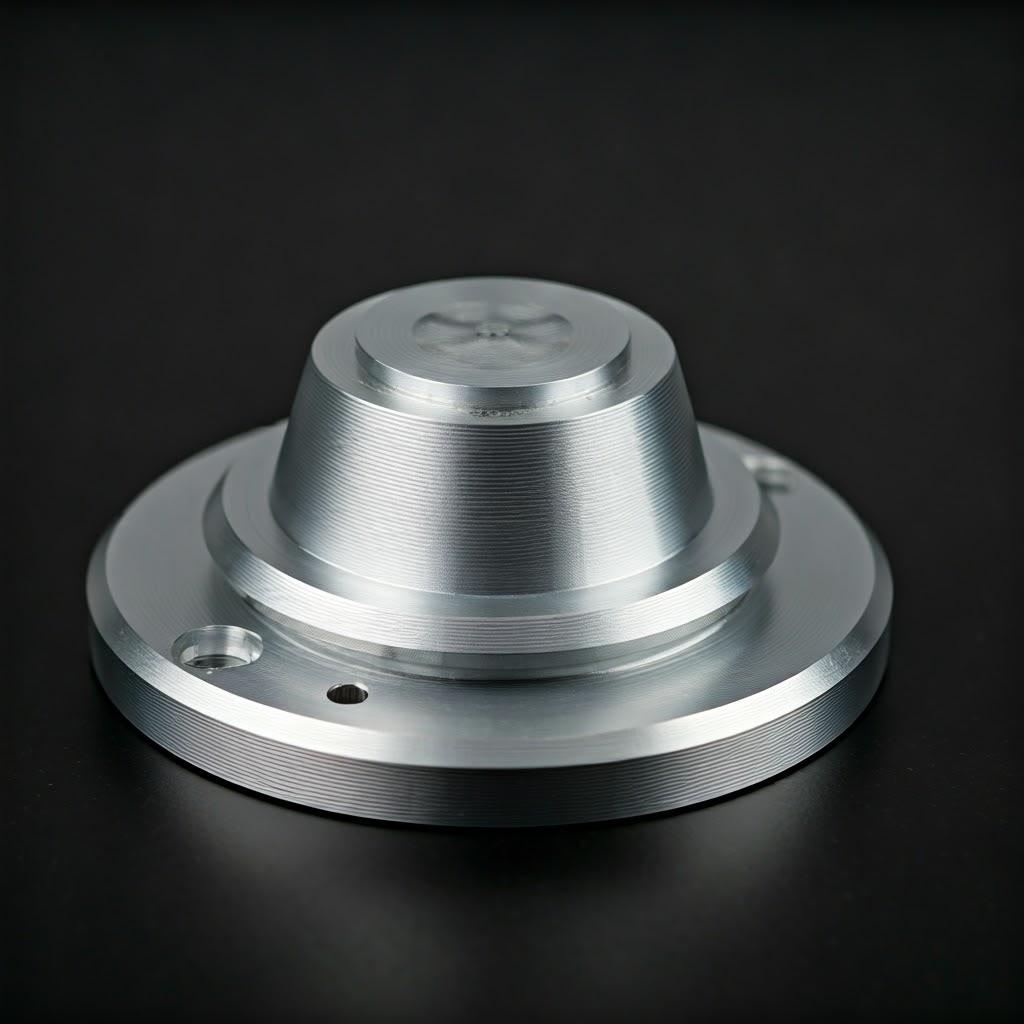
Why Use Metal 3D Printing for EV Cooling Plates? Unlocking Performance and Design Freedom
While traditional manufacturing methods have served the industry for decades, they inherently limit the potential for truly optimized thermal management components. Metal additive manufacturing fundamentally changes the design and production paradigm for EV cooling plates, offering a compelling suite of advantages that directly address the challenges of modern electric vehicles. Engineers and manufacturers are increasingly turning to AM to gain a competitive edge through superior performance, reduced weight, and faster development cycles.
Here’s a breakdown of the key benefits of using metal AM for EV cooling plates:
- Unprecedented Design Freedom and Complexity:
- Intricate Internal Channels: AM’s layer-by-layer process allows the creation of highly complex internal geometries that are impossible or prohibitively expensive to produce using traditional methods. This includes:
- Thin-walled structures: Reducing material usage and weight.
- Lattice or Gyroid Structures: Maximizing surface area within a given volume, significantly enhancing heat transfer between the plate material and the coolant.
- Conformal Channels: Designing coolant passages that precisely follow the contours of the heat source (e.g., battery cells, power modules), minimizing thermal resistance and improving cooling uniformity.
- Biomimetic Designs: Mimicking natural structures (like veins in a leaf) to optimize fluid flow, reduce pressure drop, and enhance thermal efficiency.
- Impact: This geometric freedom empowers designers to create cooling plates that are not just functional but highly optimized for specific thermal loads, flow rates, and packaging constraints.
- Intricate Internal Channels: AM’s layer-by-layer process allows the creation of highly complex internal geometries that are impossible or prohibitively expensive to produce using traditional methods. This includes:
- Enhanced Thermal Performance:
- Increased Heat Transfer: The complex internal structures enabled by AM dramatically increase the surface area available for heat exchange, leading to significantly higher heat transfer coefficients compared to simple serpentine or drilled channels found in traditional designs.
- Improved Flow Distribution: Optimized channel designs ensure more uniform coolant flow distribution across the plate, eliminating hot spots and improving overall cooling effectiveness.
- Reduced Thermal Resistance: Conformal channels minimize the distance heat needs to travel from the source to the coolant, lowering thermal resistance and improving responsiveness.
- Result: 3D printed cooling plates can often achieve superior cooling capacity within the same or smaller volume compared to conventional counterparts, critical for managing heat in power-dense EV components.
- Consolidation partielle :
- Reduced Assembly Complexity: Traditionally, cooling plates might consist of multiple pieces (e.g., two plates with channels machined, then brazed together, plus inlet/outlet fittings). AM allows these complex assemblies to be printed as a single, monolithic part.
- Avantages :
- Fewer Potential Leak Points: Eliminates joints and seals associated with brazing or gaskets, improving long-term reliability.
- Simplified Supply Chain & Assembly: Reduces part count, inventory management, and assembly time/cost.
- Intégrité structurelle améliorée : Monolithic parts can offer better structural performance compared to assemblies.
- Allègement :
- Efficacité matérielle : AM uses material only where needed. Complex internal structures like lattices inherently reduce material volume while maintaining performance.
- Optimized Topologies: Design software can perform topology optimization, removing material from non-critical areas while maintaining structural integrity and thermal performance, leading to significant weight savings.
- Material Choice: AM enables the use of lightweight, high-performance materials like Aluminum alloys (e.g., AlSi10Mg) which offer excellent thermal properties at low density.
- Impact: Reducing component weight is crucial in EVs to improve range, handling, and overall vehicle efficiency.
- Rapid Prototyping and Accelerated Development:
- Fast Iteration: AM allows designers to quickly move from a CAD model to a physical prototype. Multiple design variations can be printed and tested in a fraction of the time required for traditional tooling and manufacturing setups.
- Reduced Time-to-Market: This rapid iteration capability significantly accelerates the development cycle for new EV models or component upgrades.
- Personnalisation et production à la demande :
- Tailored Solutions: Cooling plates can be easily customized for specific battery module sizes, motor housings, power electronic layouts, or unique packaging requirements without the need for expensive tooling changes.
- Low-Volume Viability: AM is cost-effective for producing small batches or highly customized parts, ideal for niche EV applications, prototypes, or aftermarket performance upgrades.
- Advanced Material Utilization:
- High-Performance Alloys: AM processes can effectively utilize advanced metal alloys, including high-thermal-conductivity copper alloys (like CuCrZr) or specialized aluminum grades optimized for thermal applications, which might be difficult to process conventionally.
Comparison: Metal AM vs. Traditional Manufacturing for Cooling Plates
Fonctionnalité | Fabrication additive métallique (AM) | Traditional Methods (Brazing, Casting, Machining) |
---|---|---|
Complexité de la conception | Extremely High (Complex internal channels, lattices) | Limited (Simple channels, requires assembly) |
Performance thermique | Potentially Superior (Optimized geometry, high SA) | Good to Very Good (Design limitations) |
Consolidation partielle | Excellent (Monolithic parts possible) | Poor (Requires assembly of multiple parts) |
Allègement | Excellent (optimisation topologique, treillis) | Moderate (Limited by process constraints) |
Lead Time (Proto) | Rapide | Slow (Tooling often required) |
Lead Time (Prod) | Moderate (Scalability improving) | Fast (For established high-volume processes) |
Personnalisation | High / Easy | Low / Expensive (Requires tooling changes) |
Déchets matériels | Low (Near-net shape) | Moderate to High (Machining, casting runners) |
Initial Cost (Low Vol) | Lower (No tooling) | Higher (Tooling cost dominates) |
Cost (High Vol) | Potentially Higher (Process speed/cost) | Lower (Economies of scale) |
Fiabilité | Potentially Higher (No joints/seals) | Dependent on assembly quality |
Exporter vers les feuilles
Leveraging Met3dp’s Expertise:
Achieving these additive manufacturing benefits requires not only advanced design capabilities but also robust and reliable printing processes and high-quality materials. About Met3dp – our company provides precisely that. Met3dp’s range of Selective Electron Beam Melting (SEBM) and Laser Powder Bed Fusion (LPBF) printers are engineered for precision and repeatability, essential for producing the intricate features of high-performance cooling plates. Our systems deliver industry-leading build volumes, allowing for the production of larger plates or batch manufacturing of smaller units. Furthermore, our deep understanding of process parameters for materials like AlSi10Mg ensures that the resulting parts possess the desired density, mechanical integrity, and thermal properties. By partnering with Met3dp, automotive companies and suppliers gain access to state-of-the-art technology and expertise, enabling them to harness the full potential of AM for creating lighter, more efficient, and highly reliable custom cooling solutions for the demanding EV market. We act as a dedicated metal AM automotive supplier, ready to assist from design optimization through to serial production.
Recommended Materials and Why They Matter: AlSi10Mg and CuCrZr
The choice of material is fundamental to the performance, weight, durability, and cost of a 3D printed EV cooling plate. Additive manufacturing offers flexibility, but selecting the right metal powder is critical. For thermal management applications like EV cooling plates, the primary considerations are thermal conductivity, density (weight), mechanical strength, corrosion resistance, printability, and cost. Two materials stand out for their suitability: AlSi10Mg (an aluminum alloy) and CuCrZr (a copper alloy).
1. AlSi10Mg (Aluminum-Silicon-Magnesium Alloy): The Versatile Workhorse
- Description : AlSi10Mg is one of the most widely used aluminum alloys in additive manufacturing. It’s essentially a casting alloy adapted for powder bed fusion processes (LPBF and SEBM). The silicon content improves fluidity during melting and solidification, while magnesium enhances strength through precipitation hardening (often achieved via heat treatment).
- Propriétés principales :
- Bonne conductivité thermique : Typically around 120-180 W/m·K depending on the print parameters and post-processing (heat treatment state). While not as high as pure aluminum or copper, it’s sufficient for many EV cooling applications.
- Faible densité : Approximately 2.67 g/cm³. This is a major advantage for lightweighting, crucial in EVs for maximizing range and efficiency.
- Excellente imprimabilité : Processes well in both laser and electron beam systems, allowing for fine features and complex geometries with good surface finish and density (typically >99.5%).
- Good Mechanical Properties: Offers a favorable strength-to-weight ratio, especially after appropriate heat treatment (e.g., T6). Tensile strength can range from 250 MPa (as-built) to over 400 MPa (heat-treated).
- Bonne résistance à la corrosion : Forms a passive oxide layer, providing adequate protection in typical automotive coolant environments.
- Rapport coût-efficacité : Relatively abundant raw materials and well-established printing parameters make it one of the more economical metal AM powders.
- Benefits for EV Cooling Plates:
- Champion des poids légers : Its low density makes it ideal for reducing overall vehicle weight.
- Balanced Performance: Offers a good combination of thermal conductivity, mechanical strength, and manufacturability at a reasonable cost.
- Flexibilité de la conception : Its excellent printability allows designers to fully leverage the geometric freedom of AM for complex channels and features.
- Industry Standard: Widely characterized and understood within the AM industry, with established process parameters and post-processing protocols.
- Applications : Battery cooling plates, power electronics cooling (where heat loads are moderate), motor housing cooling jackets, general-purpose thermal management components where weight is a primary driver.
2. CuCrZr (Copper-Chromium-Zirconium Alloy): The High-Performance Heat Mover
- Description : CuCrZr is a precipitation-hardenable copper alloy known for its exceptional combination of high thermal and electrical conductivity, good mechanical strength (especially at elevated temperatures), and resistance to softening. The small additions of chromium and zirconium allow for strengthening via heat treatment without significantly compromising copper’s inherent conductivity.
- Propriétés principales :
- Excellente conductivité thermique : Typically >300 W/m·K after proper heat treatment and aging, significantly higher than aluminum alloys and approaching that of pure copper. This allows for extremely efficient heat dissipation.
- Conductivité électrique élevée : Also exhibits high electrical conductivity, although less critical for purely thermal applications.
- Good High-Temperature Strength: Retains strength better at elevated temperatures compared to pure copper or many aluminum alloys.
- Moderate Density: Around 8.8-8.9 g/cm³. Significantly denser and heavier than AlSi10Mg.
- Challenging Printability: Copper alloys are notoriously difficult to process via laser-based AM due to their high reflectivity and thermal conductivity, which can lead to process instabilities and defects. Specialized equipment (e.g., green or blue lasers) or Electron Beam Melting (EBM), which is less sensitive to reflectivity, are often preferred. Achieving high density requires careful parameter optimization.
- Coût plus élevé : Copper feedstock is more expensive than aluminum, and the challenging printing process can add to the overall component cost.
- Benefits for EV Cooling Plates:
- Maximum Heat Dissipation: Its superior thermal conductivity makes it the material of choice for applications with very high heat flux densities or where minimizing temperature gradients is critical.
- Performance à haute température : Suitable for components operating closer to heat sources or in more demanding thermal environments.
- Applications : Direct cooling of high-power density components (e.g., SiC/GaN power modules), performance electric motor cooling, applications where thermal performance is the absolute priority over weight or cost.
Material Properties Comparison (Typical Values – Can Vary Significantly with AM Process & Post-Processing)
Propriété | AlSi10Mg (Heat Treated) | CuCrZr (Heat Treated) | Pure Copper (Annealed) | 6061 Aluminum (T6) | Unités | Notes |
---|---|---|---|---|---|---|
Conductivité thermique | ~150 – 180 | >300 | ~390 | ~167 | W/m·K | CuCrZr offers a massive advantage here. |
Densité | ~2.67 | ~8.85 | ~8.96 | ~2.70 | g/cm³ | AlSi10Mg is significantly lighter. |
Limite d'élasticité | ~250 – 300+ | ~400 – 500+ | ~70 | ~276 | MPa | Both AM alloys offer good strength after heat treatment. |
Résistance ultime à la traction | ~400 – 450+ | ~450 – 550+ | ~220 | ~310 | MPa | |
Relative Printability (LPBF) | Excellent | Défi | Very Challenging | Bon | – | EBM can be better for Copper. |
Coût relatif | Plus bas | Plus élevé | Haut | Faible | – | Considers powder and processing complexity. |
Résistance à la corrosion | Bon | Bon | Fair (Can tarnish) | Très bon | – | Specific coolant compatibility needs checking. |
Exporter vers les feuilles
The Importance of Powder Quality – Met3dp’s Advantage:
The theoretical properties of an alloy are only achievable in a 3D printed part if the starting material – the metal powder – is of exceptional quality. This is where Met3dp’s expertise becomes critical.
- Production avancée de poudres : Met3dp utilizes industry-leading atomisation du gaz and Plasma Rotating Electrode Process (PREP) technologies. Our gas atomization systems employ unique nozzle designs and controlled gas flow to produce poudres métalliques sphériques avec:
- High Sphericity & Good Flowability: Essential for uniform powder bed spreading, leading to consistent melting and high part density (>99.5%). Poor flowability can cause voids and defects.
- Distribution contrôlée de la taille des particules (PSD) : Optimized PSD ensures good packing density and resolution capabilities.
- Low Oxygen & Impurity Content: Minimizes contaminants that can compromise material properties and lead to defects during printing.
- Optimized Powders: We manufacture high-quality AlSi10Mg powder specifically optimized for laser and electron beam powder bed fusion processes. While CuCrZr presents unique challenges, Met3dp’s R&D capabilities and advanced powder manufacturing systems position us to work with clients on developing or sourcing high-performance copper alloy powders tailored for thermal applications. Our extensive Produits portfolio, including materials like Ti alloys, CoCrMo, stainless steels, and superalloys, demonstrates our broad capability in handling diverse and demanding materials.
- Assurance qualité : Rigorous quality control measures ensure batch-to-batch consistency, crucial for reliable production of automotive grade metal powder.
Selection Criteria:
Choosing between AlSi10Mg and CuCrZr (or other potential alloys) involves a trade-off analysis:
- Thermal Load: How much heat needs to be dissipated? Very high heat flux points towards CuCrZr.
- Weight Target: Is minimizing weight paramount? AlSi10Mg is the clear choice.
- Température de fonctionnement : Will the component see high temperatures? CuCrZr offers better strength retention.
- Packaging Space: Can a slightly larger AlSi10Mg plate achieve the required cooling, or is space so tight that only the higher conductivity of CuCrZr will suffice?
- Budget : AlSi10Mg is generally more cost-effective.
- Production Volume & Supplier Capability: Ensure the chosen fournisseur de poudre métallique and AM service provider have proven capabilities with the selected material.
In summary, AlSi10Mg provides an excellent balance for many EV cooling applications, leveraging the lightweighting and design freedom of AM effectively. CuCrZr represents the peak performance option for the most thermally demanding scenarios, albeit with weight, cost, and manufacturing complexity considerations. Met3dp provides not only the advanced printing systems but also the high-quality, optimized metal powder for 3D printing required to successfully manufacture reliable and efficient cooling plates from these materials, ensuring our clients can meet the stringent demands of the EV industry.
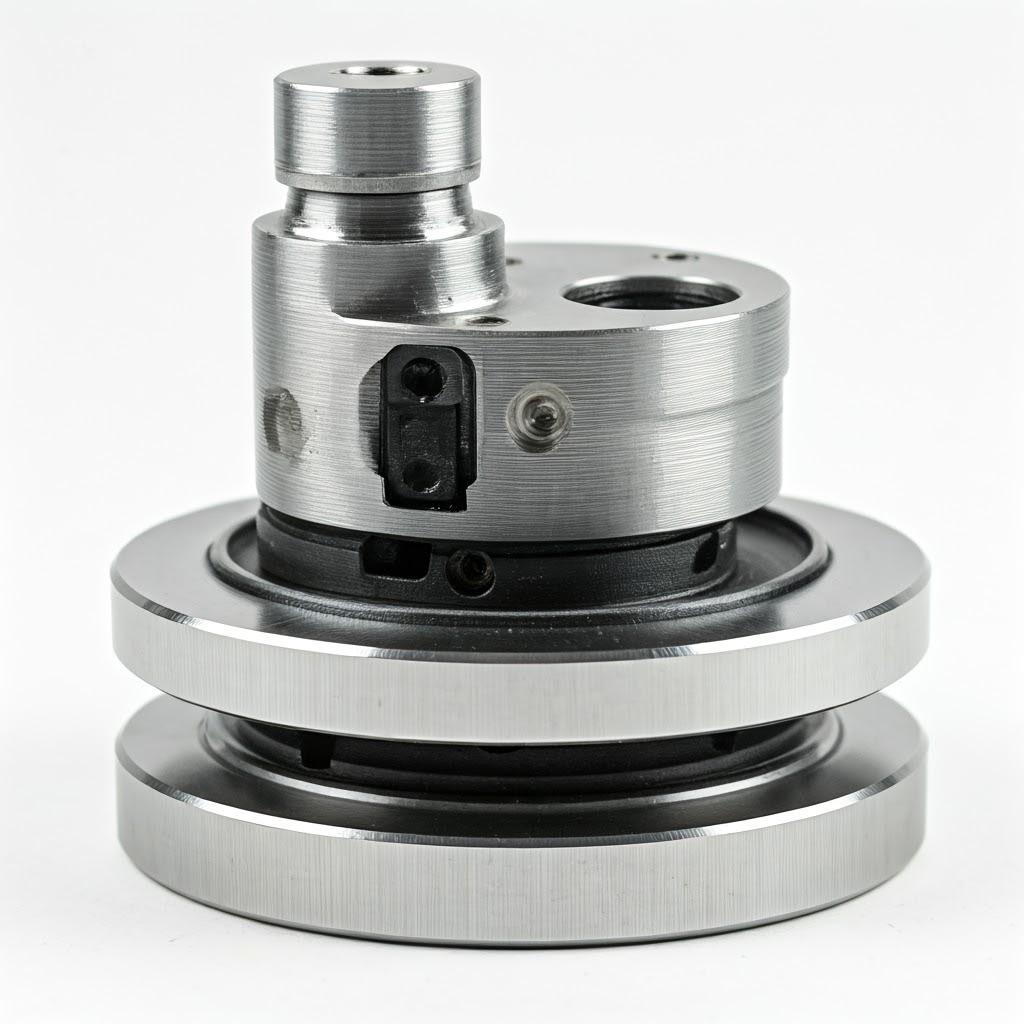
Design Considerations for Additive Manufacturing (DfAM): Thinking in Layers
Transitioning from traditional manufacturing paradigms to additive manufacturing requires more than just converting a standard CAD model into an STL file. To truly harness the power of metal 3D printing for components like EV cooling plates, engineers must embrace Conception pour la fabrication additive (DfAM). DfAM is a methodology that involves designing parts specifically optimized for the unique capabilities and constraints of AM processes. Failing to consider DfAM principles early can lead to print failures, suboptimal performance, increased post-processing efforts, and higher costs. Conversely, mastering DfAM unlocks the potential for creating truly innovative and high-performance topology optimization cooling plates and other thermally efficient components.
Key DfAM Principles for 3D Printed Cooling Plates:
- Leveraging Geometric Freedom for Thermal Performance:
- Optimizing Internal Channels: This is where AM shines for cooling plates.
- Flow Path Design: Avoid sharp 90-degree bends which increase pressure drop and create stagnant flow zones. Use smooth, sweeping curves. Vary channel cross-sections strategically to accelerate or decelerate flow, influencing local heat transfer coefficients.
- Épaisseur de la paroi : AM allows for very thin walls (down to ~0.3-0.5 mm, depending on the process and material), reducing weight and thermal resistance. However, minimum thicknesses must be respected for structural integrity and printability.
- Heat Transfer Enhancement Features: Incorporate features like small pins, fins, dimples, or integrated lattice/gyroid structures within channels. These act as turbulators, disrupting the boundary layer and significantly boosting local heat transfer, albeit often at the cost of increased pressure drop. DfAM allows for precise placement of these features only where needed.
- Complex Networks: Design branching or manifold structures to distribute coolant effectively across large surface areas, ensuring uniform cooling.
- Conformal Cooling: Instead of flat plates with serpentine channels, design cooling passages that precisely follow the 3D contours of the components being cooled (e.g., cylindrical battery cells, curved motor stators, complex power module layouts). This minimizes the thermal path, reduces temperature gradients, and maximizes contact area, leading to highly efficient and uniform cooling. This is exceptionally difficult or impossible with traditional methods but straightforward with AM.
- Caractéristiques intégrées : Consolidate parts by designing features directly into the cooling plate:
- Mounting Bosses/Brackets: Eliminate separate fasteners and assembly steps.
- Fluid Connectors: Integrate threaded ports or customized interfaces for fluid lines directly into the print.
- Sensor Ports: Design housings for temperature or pressure sensors at critical locations within the cooling circuit.
- Cable Routing Channels: Integrate channels or clips for managing nearby wiring harnesses.
- Optimizing Internal Channels: This is where AM shines for cooling plates.
- Accommodating AM Process Constraints:
- Structures de soutien : Metal powder bed fusion requires support structures for features that overhang the build plate at angles typically less than 45 degrees from the horizontal. Internal channels also often require support unless designed carefully.
- Minimization Strategy: Orient the part on the build plate to minimize the amount of overhangs requiring support. Design features with self-supporting angles (>45 degrees) wherever possible. Use diamond, teardrop, or keyhole shapes for horizontal internal channels to make them self-supporting.
- Accessibilité : If supports are unavoidable (especially internal ones), ensure they are accessible for removal during post-processing. Design access ports or split the design into sections if necessary, though this negates some part consolidation benefits. Support removal can affect the internal surface finish.
- Impact: Supports add print time, consume material, and require significant post-processing effort for removal. Minimizing them through smart design is crucial.
- Minimum Feature Sizes: There are limits to the fineness of details AM can produce.
- Épaisseur de la paroi : As mentioned, minimum achievable wall thicknesses exist (e.g., ~0.3-0.5 mm). Designing below this can lead to incomplete features or print failures.
- Hole/Channel Diameter: Very small channels (<0.5-1.0 mm) can be challenging to print reliably and, more importantly, difficult to clear of unfused powder.
- Met3dp Capabilities: Met3dp’s advanced printers offer high resolution, but designers should consult Met3dp’s specific guidelines for minimum feature sizes achievable with their equipment (both LPBF and SEBM) and chosen materials.
- Residual Stress and Warpage: The rapid heating and cooling inherent in PBF processes create internal stresses within the part. These stresses can cause distortion (warpage) during printing or after removal from the build plate.
- Stratégies d'atténuation :
- Orientation : Orienting the part to minimize large, flat surfaces parallel to the build plate and reduce the height can help.
- Thermal Anchoring: Using robust support structures helps anchor the part.
- Design Features: Add sacrificial ribs or structures to stiffen the part during printing (removed later). Use generous radii on corners instead of sharp edges, which act as stress concentrators. Break large volumes into thinner sections if possible.
- Contrôle des processus : Utilizing appropriate process parameters and potentially build plate heating (common in SEBM and some LPBF systems) helps reduce thermal gradients.
- Stratégies d'atténuation :
- Elimination des poudres : Unfused powder must be removed from the finished part, especially from internal channels.
- Design for Evacuation: Include sufficiently large drain/access holes (ideally > 1-2 mm diameter) at low points and strategic locations in internal channel networks to allow powder to escape easily via gravity, vibration, and airflow. Avoid complex internal cavities with no exit path. Smooth internal transitions also aid powder flow.
- Structures de soutien : Metal powder bed fusion requires support structures for features that overhang the build plate at angles typically less than 45 degrees from the horizontal. Internal channels also often require support unless designed carefully.
- Utilizing Advanced Software Tools:
- CAD: Modern CAD software increasingly incorporates DfAM-specific features.
- Simulation :
- Computational Fluid Dynamics (CFD): Essential for simulating coolant flow and heat transfer within complex internal channel designs before printing. Allows optimization of geometry for thermal performance and pressure drop.
- Finite Element Analysis (FEA): Used to predict stress concentrations, deformation under load, and potential residual stress issues.
- Simulation de processus : Specialized software can simulate the AM build process itself to predict potential issues like warpage or support failures.
- Optimisation de la topologie : Algorithms automatically remove material from non-critical areas of a design based on defined load cases, constraints (e.g., keep fluid channels intact), and objectives (e.g., minimize weight, maximize stiffness), resulting in highly efficient, often organic-looking structures ideal for lightweighting.
Collaboration is Key: Effective DfAM often requires close collaboration between the part designer and the AM service provider. Met3dp’s team possesses deep expertise in various Méthodes d'impression (LPBF, SEBM) and materials. Consulting with our application engineers early in the design process can help identify potential printability issues, optimize the design for performance and cost-effectiveness, and ensure the final part meets all specifications. This collaborative approach streamlines the development process and maximizes the benefits of choosing additive manufacturing.
Tolerance, Surface Finish, and Dimensional Accuracy: Understanding As-Built Quality
Engineers accustomed to the tight tolerances and smooth finishes of CNC machining need to adjust their expectations when working with metal additive manufacturing. While AM offers unparalleled geometric freedom, the nature of layer-by-layer fusion results in different characteristics regarding precision and surface texture. Understanding these aspects is crucial for designing parts appropriately and planning necessary post-processing steps. Procurement managers sourcing precision metal printing services should clarify achievable specifications with their suppliers.
Tolérances typiques :
- General Dimensions: As-built metal PBF parts can typically achieve tolerances conforming to ISO 2768-m (medium) or sometimes ISO 2768-f (fine) for overall dimensions. This might translate to ±0.1 mm to ±0.5 mm, depending on the specific dimension, part size, material, and machine calibration.
- Factors Influencing Tolerance:
- Taille de la pièce : Larger parts tend to exhibit greater absolute deviation due to accumulated thermal effects and potential warpage.
- Orientation : The orientation of a feature relative to the build direction affects its achievable tolerance.
- Matériau : Different materials have varying shrinkage factors and thermal behaviors.
- Machine Calibration & Process Control: Well-maintained and calibrated machines with tightly controlled parameters yield better accuracy. Met3dp places a strong emphasis on machine calibration and process stability to ensure consistent and accurate builds.
- Effets thermiques : Residual stress and minor warping can impact final dimensions.
- Critical Tolerances: For features requiring tighter tolerances (e.g., mating surfaces, sealing grooves, bearing fits), post-process CNC machining is almost always necessary. AM is used to create the near-net shape, and machining provides the final precision.
Finition de la surface (rugosité) :
- As-Built Roughness (Ra): The surface finish of AM parts is inherently rougher than machined surfaces due to the partially melted powder particles adhering to the surface and the layer-wise construction.
- Top Surfaces: Generally the smoothest, often Ra 5-10 µm.
- Parois verticales : Moderate roughness, typically Ra 8-15 µm.
- Up-Facing Angled Surfaces: Show characteristic “stair-stepping” artifacts, where the layer edges are visible. Roughness depends on the angle.
- Down-Facing/Supported Surfaces: Usually the roughest surfaces (Ra 15-25 µm or more), as they are formed on top of support structures or loosely sintered powder. Support contact points leave witness marks that need removal.
- Canaux internes : The roughness of internal channels is particularly important for cooling plates. It’s influenced by the channel diameter, orientation, and whether supports were used. Rougher internal surfaces can:
- Increase Pressure Drop: Higher friction losses for the coolant flow.
- Potentially Enhance Heat Transfer: Increased turbulence near the wall can sometimes slightly improve heat transfer, but this effect is complex and often secondary to the negative impact on pressure drop.
- Affect Cleanliness: Rough surfaces can be harder to clean thoroughly and may trap debris or powder.
- Amélioration de l'état de surface : As-built finishes are often sufficient for non-critical surfaces, but functional requirements (sealing, low friction, fatigue life) typically necessitate post-processing like abrasive blasting, tumbling, polishing, or machining (detailed in the next section). Met3dp focuses on optimizing print parameters to achieve the best possible as-built surface quality within the process limits.
Précision dimensionnelle :
- Achieving Accuracy: Beyond tolerances on specific features, overall dimensional accuracy depends on managing thermal effects during the build.
- Shrinkage Compensation: AM software typically applies scaling factors to the CAD model to compensate for material shrinkage during cooling, but perfect prediction is difficult.
- Warpage Control: As discussed in DfAM, controlling residual stress through orientation, supports, and process parameters is vital for maintaining geometric fidelity.
- Étalonnage : Regular machine calibration ensures the laser or electron beam is accurately positioned and delivering the correct energy.
- Met3dp’s Approach: We employ rigorous process monitoring and control, combined with meticulous machine maintenance and calibration routines, to maximize the dimensional accuracy of printed parts. Our experience allows us to anticipate and mitigate potential deviations for various geometries and materials.
Inspection and Metrology:
- Verifying Complex Parts: Given the intricate internal geometries possible with AM, traditional measurement techniques may not suffice.
- Machines à mesurer tridimensionnelles (MMT) : Used for precise measurement of external features and accessible internal points.
- Optical Scanning (3D Scanning): Captures the overall geometry of the part for comparison against the original CAD model, useful for verifying complex shapes and identifying warpage.
- Tomodensitométrie (CT) : Increasingly essential for non-destructively inspecting the integrity of internal channels, verifying wall thicknesses, detecting internal defects (like porosity or trapped powder), and measuring internal features that are otherwise inaccessible. This is particularly critical for validating metal 3D printing quality control in cooling plates.
In essence, while metal AM provides incredible design freedom, engineers must design with realistic expectations of as-built tolerances and finishes, planning for necessary post-processing steps where high precision or smooth surfaces are required. Working with an experienced provider like Met3dp ensures that the process capabilities are well understood and appropriately applied.
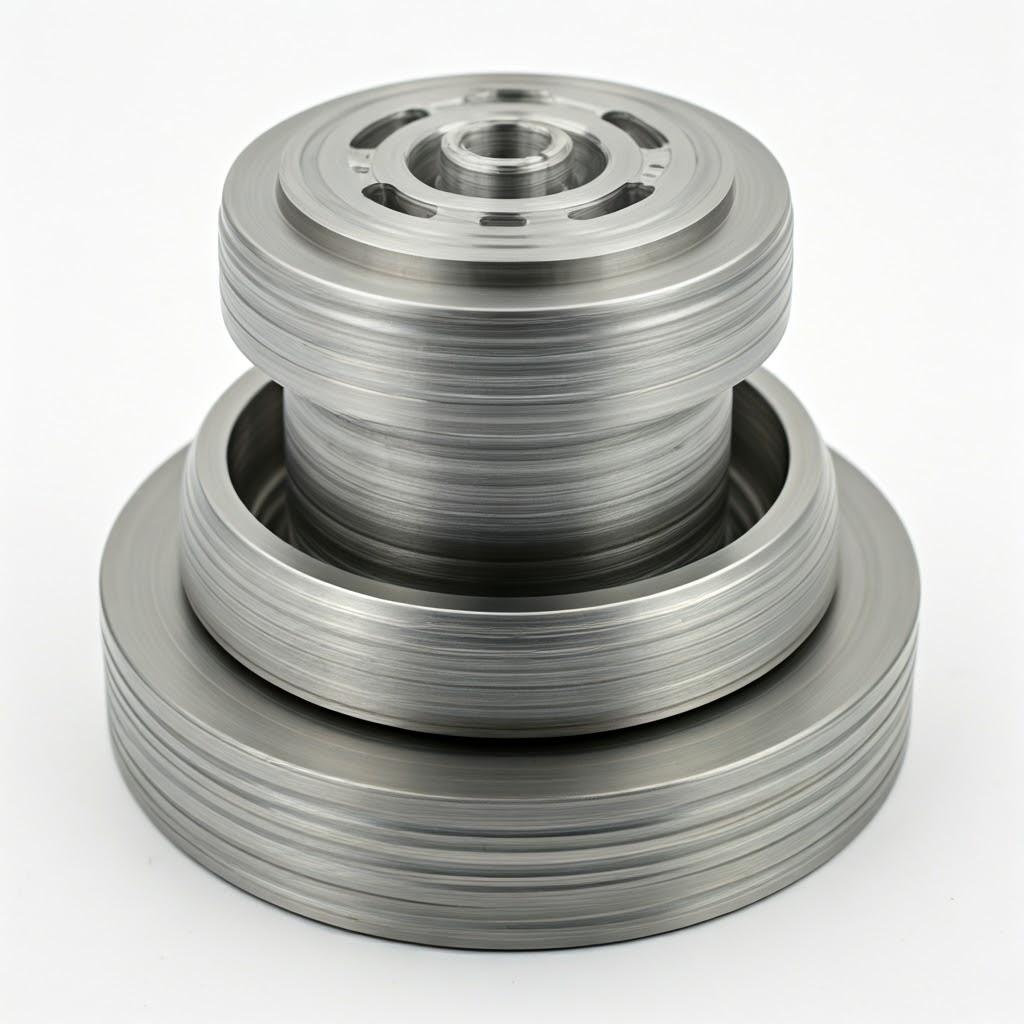
Post-Processing Requirements: From Printer to Performance
A common misconception about metal 3D printing is that parts emerge from the machine ready for immediate use. In reality, especially for demanding functional components like EV cooling plates, the printing process is often just the first major step. A series of post-processing metal AM steps are typically required to transform the as-built part into a finished component that meets performance, safety, and reliability specifications. These steps add to the overall cost and lead time but are essential for achieving the desired material properties, dimensional accuracy, surface finish, and cleanliness. Understanding this metal 3D printing workflow is vital for accurate project planning and costing.
Typical Post-Processing Workflow for Metal AM EV Cooling Plates:
- Soulagement du stress / Traitement thermique :
- Objet : This is arguably the most critical post-processing step for PBF parts. The rapid heating/cooling cycles during printing induce significant residual stresses. Heat treatment is necessary to:
- Relieve Internal Stresses: Reduces the risk of distortion or cracking after removal from the build plate or during subsequent machining/use.
- Homogenize Microstructure: Improves consistency throughout the part.
- Achieve Target Material Properties: Develops the desired microstructure and mechanical properties (strength, ductility, hardness) through processes like precipitation hardening (aging). For example, AlSi10Mg often undergoes a T6 heat treatment (solutionizing + artificial aging) to maximize strength. CuCrZr requires specific solutionizing and aging cycles to optimize its conductivity and strength.
- Procédure : Performed in a controlled atmosphere furnace according to material-specific protocols (temperature, time, cooling rate). Parts are often heat-treated while still attached to the build plate to minimize warpage.
- Met3dp Guidance: Met3dp provides recommended heat treatment AlSi10Mg and other material protocols based on extensive testing and experience, ensuring optimal properties are achieved.
- Objet : This is arguably the most critical post-processing step for PBF parts. The rapid heating/cooling cycles during printing induce significant residual stresses. Heat treatment is necessary to:
- Retrait de la pièce de la plaque de construction :
- Méthode : Once cooled after heat treatment (if done on the plate), the part(s) must be separated from the build plate. This is typically done using:
- Usinage par électroérosion à fil (EDM) : Precise, creates a clean cut, minimal mechanical stress. Often preferred for delicate or complex parts.
- Band Saw: Faster and potentially cheaper, but less precise and induces more mechanical stress. Requires careful handling.
- Méthode : Once cooled after heat treatment (if done on the plate), the part(s) must be separated from the build plate. This is typically done using:
- Retrait de la structure de soutien :
- Méthode : Supports must be removed carefully to avoid damaging the part surface.
- Suppression manuelle : Breaking or cutting away accessible supports using hand tools (pliers, cutters, grinders). Labor-intensive and skill-dependent.
- Usinage (fraisage/meulage) : Used for more robust supports or where a smoother surface finish is required at the contact points.
- EDM : Can be used for delicate or hard-to-reach supports.
- Défis : Removing internal supports from complex channels without damaging the channel walls can be extremely difficult or impossible if not designed for access (see DfAM). This is a major consideration against using extensive internal supports.
- Méthode : Supports must be removed carefully to avoid damaging the part surface.
- Powder Removal (Depowdering):
- Objet : Ensuring all unfused metal powder is removed from the part, especially from internal channels and complex features. Trapped powder can impede coolant flow, add weight, become dislodged later causing contamination, and prevent effective heat treatment or surface finishing.
- Méthodes :
- Compressed Air / Manual Blowing: For loose powder on external surfaces and accessible channels.
- Vibration / Tumbling: Helps shake powder loose from internal cavities.
- Bead Blasting: Can help dislodge powder while also starting the surface finishing process.
- Ultrasonic Cleaning: Uses cavitation in a liquid bath to dislodge trapped powder.
- Chemical Flushing/Etching: In some cases, specific chemical solutions can help dissolve or flush out powder, but material compatibility is critical.
- Verification: CT scanning is often the best way to confirm complete powder removal from complex internal networks.
- Finition de la surface :
- Objet : To improve the as-built surface roughness, remove support witness marks, achieve specific aesthetic requirements, or prepare surfaces for sealing or subsequent operations.
- Méthodes :
- Abrasive Blasting (Bead, Sand, Grit): Cleans the surface, removes oxides, creates a uniform matte finish. Different media provide different textures.
- Tumbling / Mass Finishing (Vibratory Finishing): Parts are tumbled with abrasive media to deburr edges and achieve a smoother, more uniform finish, primarily on external surfaces.
- Manual Grinding/Polishing: Skilled labor using various tools to achieve smooth, mirror-like finishes on specific areas (e.g., sealing faces).
- Automated Polishing: Robotic or specialized equipment for more consistent polishing.
- Électropolissage : An electrochemical process that removes a thin layer of material, smoothing surfaces, including complex geometries and potentially internal channels if electrolyte flow can be managed. Excellent for cleanliness and corrosion resistance.
- Abrasive Flow Machining (AFM) / Extrude Hone: A specialized process where an abrasive-laden polymer is forced through internal channels under pressure. Effective for polishing internal channels and improving their surface finish, reducing pressure drop.
- Usinage CNC :
- Objet : To achieve tight tolerances, specific flatness, parallelism, or surface finish requirements on critical features that cannot be met by the as-built AM process.
- Applications : Machining mating flanges, creating O-ring grooves or sealing faces, drilling and tapping precise connection ports, ensuring flatness of mounting surfaces.
- Near-Net Shape: AM is used to create the complex overall geometry (the near-net shape), minimizing the material that needs to be removed by machining, thus saving time and reducing waste compared to machining from a solid block. Requires careful planning of machining allowances in the DfAM phase.
- Nettoyage et inspection :
- Nettoyage : Final cleaning steps to remove any residues from machining coolants, polishing compounds, or handling.
- Inspection : Final verification of dimensions (CMM, scanning), internal integrity (CT scanning), surface finish, and leak testing (pressure testing the coolant channels) to ensure the cooling plate meets all specifications before shipment or assembly.
- Optional Coating/Plating:
- Objet : Enhance corrosion resistance (e.g., anodizing for aluminum parts exposed to certain coolants or environments), improve wear resistance, or provide specific surface properties. Less common for the primary cooling function inside channels but may be applied externally.
Typical Post-Processing Flowchart (Example):
Code snippet
graph TD
A[Print Completion] --> B(Stress Relief / Heat Treatment);
B --> C(Part Removal from Build Plate);
C --> D(Support Structure Removal);
D --> E(Bulk Powder Removal);
E --> F{Surface Finish Required?};
F -- Yes --> G[Abrasive Blasting / Tumbling];
F -- No --> H[Fine Powder Removal / Cleaning];
G --> H;
H --> I{Tight Tolerances Required?};
I -- Yes --> J(CNC Machining);
I -- No --> K[Final Cleaning];
J --> K;
K --> L(Final Inspection - Dimensional, CT, Leak Test);
L --> M[Finished Part];
subgraph Optional Steps
P1(Polishing / AFM for Internal Channels)
P2(Coating / Plating)
end
H --> P1;
P1 --> I;
K --> P2;
P2 --> L;
Impact on Cost and Lead Time: It’s crucial for procurement teams and project managers to recognize that post-processing often constitutes a significant portion (sometimes >50%) of the final part cost and lead time. Each step adds time and requires specific equipment and expertise.
Met3dp’s Comprehensive Approach: While Met3dp’s core expertise lies in advanced printing systems and high-quality powders, we understand the critical role of post-processing. We provide detailed guidance on best practices for the materials we offer and can connect clients with qualified partners for specialized post-processing services like heat treatment, precision machining, AFM, or CT scanning, ensuring a seamless workflow from design to finished, functional EV cooling plate.
Common Challenges in Metal AM for Cooling Plates and How to Avoid Them
Metal additive manufacturing is a sophisticated process, and like any advanced manufacturing technique, it presents potential challenges. Producing high-quality, reliable EV cooling plates requires careful control over design, materials, printing, and post-processing. Awareness of common pitfalls allows engineers, operators, and fournisseurs de services d'impression 3D métal to implement proactive mitigation strategies, ensuring successful outcomes.
Here are some common challenges and how to avoid them:
1. Print Failures:
- Défi:Warping / Build Plate Detachment: Significant distortion of the part during printing, potentially causing it to lift off the build plate or collide with the powder recoater mechanism.
- Cause : Accumulation of residual thermal stress exceeding the strength of the supports or the part itself.
- Avoidance Strategies:
- DfAM : Optimize part orientation (minimize cross-sectional area parallel to plate, reduce height), add sacrificial stiffening features, use large corner radii.
- Stratégie de soutien : Use strong, well-designed supports, potentially thermally engineered supports.
- Paramètres du processus : Utilize optimized parameters (scan strategy, layer thickness), employ build plate heating if available (standard on Met3dp’s SEBM systems, available on some LPBF).
- Soulagement du stress : Perform intermediate stress relief cycles for very large/complex builds if necessary (though this adds significant time/cost). Perform final stress relief before support removal.
- Défi:Cracking (Solidification/Liquation Cracking): Formation of cracks within the part during printing or cooling.
- Cause : High thermal stresses, unsuitable material chemistry (high impurity levels), inappropriate process parameters leading to unfavorable grain structures. Some alloys are more susceptible than others.
- Avoidance Strategies:
- Qualité du matériel: Use high-quality, AM-optimized powder with low impurities and controlled chemistry, such as those produced by Met3dp’s advanced atomization processes.
- Contrôle des processus : Employ validated process parameters specific to the material. Preheating the build environment (inherent in SEBM, possible in LPBF) significantly reduces thermal gradients and cracking risk.
- Conception : Avoid sharp internal corners which act as stress risers.
- Traitement thermique : Proper stress relief and homogenization heat treatments are crucial.
- Défi:Recoater Collision / Delamination: The recoater blade/roller crashing into a warped part or improperly fused section, potentially damaging the machine and stopping the build. Delamination refers to poor bonding between layers.
- Cause : Warpage (see above), incorrect powder dosing leading to uneven layers, insufficient energy input causing poor layer bonding.
- Avoidance Strategies: Mitigate warpage, ensure correct powder flow and recoating parameters, use validated melt parameters, maintain a clean build environment free of contamination. Met3dp’s printers incorporate monitoring systems to help detect potential issues early.
2. Part Quality Issues:
- Défi:Porosity (Gas / Keyhole / Lack-of-Fusion): Small voids within the printed material.
- Cause : Trapped gas within the powder or shielding gas (gas porosity), excessive energy density vaporizing material (keyhole porosity), or insufficient energy density leading to incomplete melting/fusion between powder particles or layers (lack-of-fusion).
- Impact: Reduces density, compromises mechanical properties (especially fatigue strength), acts as crack initiation sites, can potentially create leak paths in cooling channels.
- Avoidance Strategies:
- Qualité de la poudre : Use high-quality, dry powder with low dissolved gas content (Met3dp powders are produced under controlled conditions to minimize this). Store powder correctly.
- Paramètres du processus : Optimize laser/beam power, scan speed, hatch spacing, and layer thickness to achieve a stable melt pool. Avoid parameters known to cause keyhole or lack-of-fusion defects.
- Shielding Gas: Ensure high-purity, stable flow of inert shielding gas (Argon or Nitrogen for LPBF) or high vacuum (SEBM).
- Post-traitement : Hot Isostatic Pressing (HIP) can close internal pores (except surface-connected ones) but adds significant cost and lead time. Typically avoided unless absolutely necessary for critical applications. Met3dp focuses on achieving >99.5% density via optimized printing, minimizing the need for HIP.
- Défi:Poor Surface Finish: Excessive roughness, particularly on down-facing surfaces or where supports were attached.
- Cause : Nature of the PBF process, stair-stepping effect, support interaction.
- Avoidance Strategies: Optimize part orientation, use appropriate support settings (e.g., smaller contact points where possible), design self-supporting angles, plan for necessary surface finishing post-processing steps (blasting, tumbling, polishing, AFM).
- Défi:Inaccurate Dimensions / Geometric Deviations: Part dimensions falling outside specified tolerances.
- Cause : Thermal shrinkage, warpage, process variability, machine calibration drift.
- Avoidance Strategies: Apply appropriate shrinkage compensation factors, use DfAM to minimize warpage, ensure regular machine calibration and maintenance, use simulation tools to predict deviation, design machining allowances for critical features.
3. Post-Processing Difficulties:
- Défi:Support Removal Issues: Difficulty removing supports completely, especially from intricate internal channels, potentially damaging the part.
- Cause : Inaccessible support structures, overly robust supports, unsuitable removal method.
- Avoidance Strategies:
- DfAM : Design for minimal supports, prioritize self-supporting features, ensure accessibility for any required supports, use optimized support types (e.g., conical, tree-like, block supports that break away more easily).
- Planification des processus : Choose the right removal method (manual, machining, EDM) based on support location, material, and part delicacy. Consider dissolvable or chemically etchable support materials if available/compatible, though less common in metal AM.
- Défi:Trapped Powder: Inability to remove all unfused powder from complex internal passages.
- Cause : Narrow or convoluted channels, lack of adequate drain/access holes, ineffective cleaning methods.
- Impact: Impedes flow, adds weight, potential for contamination.
- Avoidance Strategies: DfAM is critical – design sufficiently large escape holes (>1-2mm), avoid dead-end cavities, smooth internal transitions. Utilize effective depowdering techniques (vibration, compressed air, potentially ultrasonic or chemical methods). Verify removal using inspection methods like CT scanning or borescope inspection.
4. Material Property Variability:
- Défi: Inconsistent mechanical (strength, ductility) or thermal properties within a part or between builds.
- Cause : Variations in powder quality (batch-to-batch), fluctuations in process parameters (laser/beam power, atmosphere), inconsistent heat treatment cycles.
- Avoidance Strategies:
- Qualified Suppliers: Source powder from reputable suppliers like Met3dp who provide consistent, high-quality, batch-traceable material with Certificates of Analysis.
- Contrôle des processus : Utilize machines with robust process monitoring and control. Adhere strictly to validated process parameters.
- Heat Treatment Control: Ensure heat treatment is performed in calibrated furnaces using precise, repeatable cycles.
- Quality Testing: Implement rigorous mechanical testing (tensile tests on witness coupons printed alongside parts) and material analysis to verify properties.
Risk Mitigation Summary Table:
Défi | Cause(s) principale(s) | Principales stratégies d'atténuation |
---|---|---|
Warping / Detachment | Contrainte résiduelle | DfAM (Orientation, Features), Supports, Process Control (Heating), Stress Relief |
Craquage | Stress, Material, Parameters | Quality Powder (Met3dp), Optimized Parameters, Pre-Heat, DfAM (Corners), Heat Treatment |
Porosité | Gas, Parameters (Energy Density) | Quality Powder, Optimized Parameters, Gas/Vacuum Control, (HIP if critical) |
Mauvais état de surface | Process Nature, Supports | DfAM (Orientation, Self-Supporting), Support Settings, Post-Processing (Blasting, Polishing, AFM) |
Dimensional Inaccuracy | Shrinkage, Warping, Calibration | Compensation Factors, DfAM, Calibration, Simulation, Machining Allowances |
Difficult Support Removal | Design (Accessibility), Support Type | DfAM (Minimize, Access), Optimized Supports, Appropriate Removal Method |
Trapped Powder | Design (Channels, Holes), Cleaning Method | DfAM (Drain Holes >1-2mm, Avoid Dead Ends), Effective Depowdering, CT Verification |
Variabilité des propriétés | Powder Inconsistency, Process/Heat Treat Variation | Qualified Powder Supplier (Met3dp), Process Control & Monitoring, Controlled Heat Treatment, Quality Testing (Coupons) |
Exporter vers les feuilles
The Value of Expertise: Successfully navigating these challenges requires deep expertise in materials science, process physics, DfAM, and quality control. Partnering with an experienced metal additive manufacturing provider like Met3dp significantly de-risks the adoption of AM technology. Our team works closely with clients to optimize designs, select appropriate materials from our high-quality powder portfolio, implement robust printing processes on our industry-leading equipment, and ensure effective post-processing and quality assurance, ultimately delivering reliable, high-performance EV cooling plates.
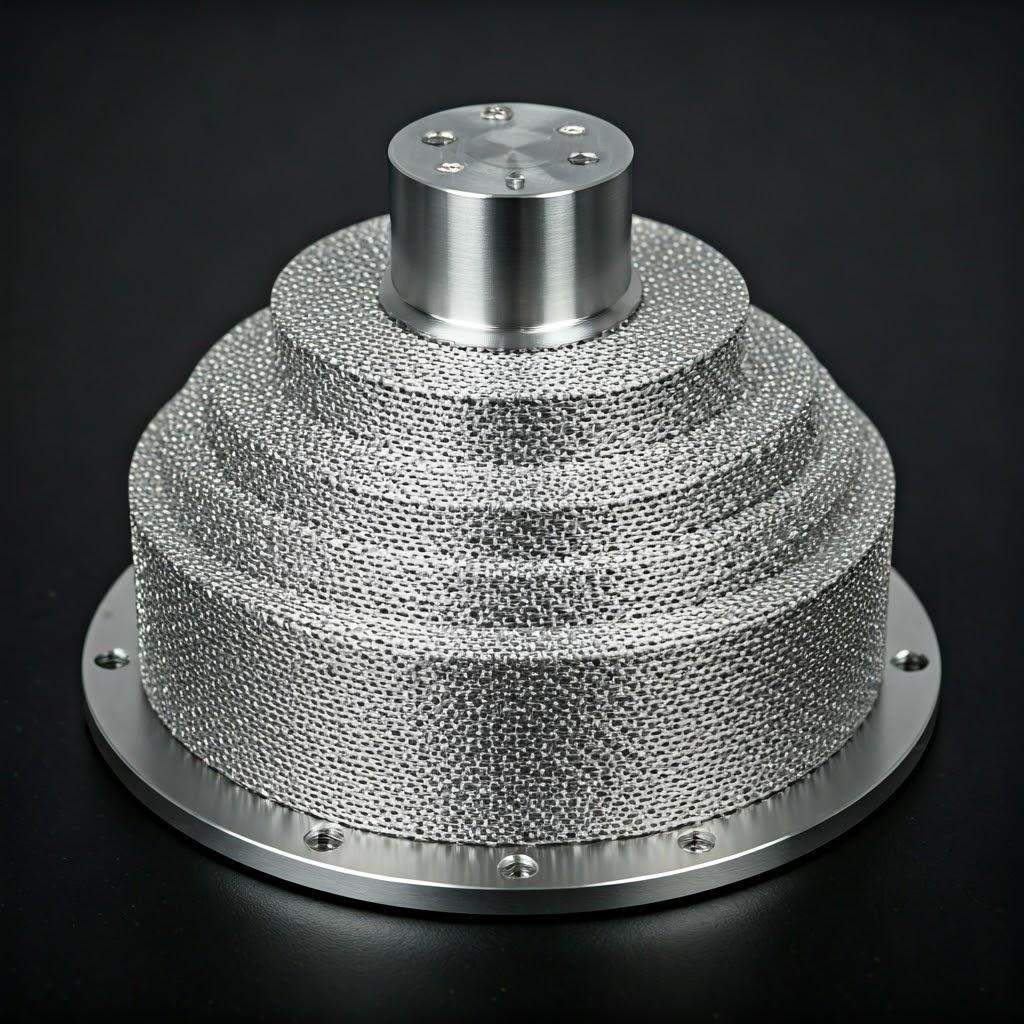
How to Choose the Right Metal 3D Printing Service Provider: Partnering for Success
Selecting a manufacturing partner is a critical decision, especially when dealing with advanced technologies like metal additive manufacturing and essential components such as EV cooling plates. The right metal AM supplier is more than just a vendor; they are a collaborator who can significantly impact the quality, performance, cost, and time-to-market of your product. Choosing based solely on the lowest quoted price can often lead to unforeseen challenges, delays, and potentially subpar components. A thorough evaluation process is necessary to identify a provider with the technical prowess, quality commitment, and supportive capabilities required for success.
Key Evaluation Criteria for Selecting Your Metal AM Partner:
- Technical Expertise and Proven Experience:
- Application Focus: Do they have demonstrable experience in producing parts similar to yours (e.g., heat exchangers, fluid manifolds, automotive components)? Have they worked extensively with the required materials (AlSi10Mg, CuCrZr)? Ask for case studies, sample parts, or references relevant to EV thermal management solutions.
- Process Knowledge: Deep understanding of the chosen AM process (LPBF, SEBM), including parameter optimization for specific materials and geometries.
- Problem-Solving: Can they troubleshoot potential issues during design, printing, or post-processing?
- Met3dp Advantage: Met3dp brings decades of collective expertise specifically in metal additive manufacturing, working across demanding sectors like automotive, aerospace, and medical. Our application engineers have deep knowledge of thermal management challenges.
- Equipment and Technology:
- Capacités de la machine : Do they operate modern, industrial-grade AM systems? Consider the build volume (can it accommodate your part size or desired batch quantity?), beam type (laser vs. electron beam, relevant for materials like copper), monitoring capabilities (melt pool monitoring, atmosphere control), and overall reliability.
- Maintenance & Calibration: Are their machines regularly maintained and calibrated to ensure consistent performance and accuracy?
- Met3dp Advantage: Met3dp designs and manufactures its own industry-leading print volume, accuracy and reliability printers (both SEBM and LPBF options), ensuring state-of-the-art capabilities and meticulous maintenance protocols.
- Material Capabilities and Powder Quality Control:
- Alloy Portfolio: Do they offer the specific alloys you need (AlSi10Mg, CuCrZr, etc.)? Can they source or develop custom alloys if required?
- Powder Source & Quality: This is crucial. Where do they source their metal powders? Do they have rigorous incoming quality checks? Or, ideally, do they produce their own powder with tight quality control? Ask about sphericity, particle size distribution (PSD), flowability, and purity (oxygen levels). Request material certifications.
- Met3dp Advantage: Met3dp uniquely controls the entire material value chain by producing its own poudres métalliques de haute qualité using advanced gas atomization and PREP technologies. This ensures optimized powder characteristics (high sphericity, controlled PSD, low impurities) crucial for printing dense, high-performance parts. We provide full material traceability and certification.
- Système de gestion de la qualité (SGQ) et certifications :
- Formal QMS: Do they operate under a recognized QMS like ISO 9001? While automotive-specific IATF 16949 certification is still emerging for AM providers, related certifications (like AS9100 for aerospace) indicate a strong quality culture.
- Contrôle des processus : What procedures are in place for monitoring build processes, documenting parameters, and ensuring repeatability?
- Capacités d'inspection : Do they have necessary metrology equipment (CMM, scanners) and NDT capabilities (e.g., CT scanning partnerships) for part validation?
- Met3dp Advantage: Met3dp is committed to rigorous quality control throughout the powder production and printing processes, adhering to stringent internal standards and working towards relevant industry certifications.
- Design Support and DfAM Expertise:
- Collaboration : Are they willing and able to collaborate early in the design phase? Can they provide constructive feedback on your design for manufacturability, performance optimization, and cost reduction using DfAM principles?
- Engineering Resources: Do they have experienced application engineers who understand both design principles and the nuances of the AM process?
- Met3dp Advantage: Met3dp offers comprehensive services de développement d'applications, partnering with clients to optimize designs specifically for additive manufacturing, ensuring functional requirements are met efficiently.
- Post-Processing Capabilities and Network:
- In-House vs. Outsourced: Which essential post-processing steps (stress relief/heat treatment, support removal, machining, surface finishing, inspection) can they perform in-house? For outsourced steps, do they have a network of qualified and trusted partners?
- Workflow Management: How do they manage the entire workflow, including logistics and quality control for outsourced processes?
- Met3dp Advantage: We provide expert guidance on all necessary post-processing steps and manage a seamless workflow, leveraging both in-house capabilities and strong partnerships to deliver finished components.
- Capacity, Scalability, and Lead Times:
- Current Capacity: How many machines do they operate? What is their typical utilization rate and queue time?
- Évolutivité : Can they handle an increase in volume if your project moves from prototype to series production?
- Quoted vs. Actual Lead Times: What are their standard lead times for parts like yours? Ask about their on-time delivery performance record. Transparency regarding potential delays is important.
- Cost and Pricing Structure:
- Transparence : Is the quoting process clear and detailed? Does it break down costs for material, printing, supports, and various post-processing options? Beware of quotes that seem too low – they may omit necessary steps or compromise on quality.
- Competitiveness: Is the pricing fair and competitive for the level of quality, service, and expertise offered? Discuss potential for wholesale additive manufacturing pricing for larger or recurring orders.
- Customer Service and Communication:
- Réactivité : How quickly do they respond to inquiries and requests for quotes?
- Communication: Are they proactive in providing updates during the manufacturing process? Is there a dedicated point of contact?
- Collaboration : Do they foster a collaborative relationship, working with you to solve problems and achieve the best outcome?
Supplier Evaluation Checklist Summary:
Critères | Questions clés | Why Met3dp Excels |
---|---|---|
Expertise & Experience | Relevant application/material track record? Case studies? Problem-solving skills? | Decades of collective AM expertise; Focus on demanding industries (Automotive). |
Equipment & Technology | Modern, industrial machines? Build volume? Monitoring? Maintenance? | Designs & builds own industry-leading SEBM/LPBF printers; High reliability. |
Material Capability/Quality | Offers needed alloys? Powder source & QC? Certifications? | In-house advanced powder production (Gas Atomization/PREP); Strict QC; Full traceability. |
Quality System & Certs | ISO 9001 / relevant certs? Process control? Inspection methods? | Strong internal QMS; Commitment to quality; Advanced inspection guidance. |
Design Support (DfAM) | DfAM feedback offered? Experienced application engineers? | Comprehensive application development services; Collaborative design optimization. |
Post-traitement | In-house capabilities? Qualified partner network? Workflow management? | Expert guidance; Manages seamless workflow with trusted partners. |
Capacity & Scalability | Handles required volume (proto/series)? Ability to scale? | Scalable solutions with efficient, large-volume printers. |
Délai de livraison et de livraison | Realistic quotes? On-time performance record? Transparency? | Focus on efficient workflow and clear communication. |
Cost & Pricing | Transparent quoting? Competitive value? Wholesale options? | Fair pricing reflecting high quality and comprehensive service; Volume tiers available. |
Service & Communication | Responsive? Proactive updates? Collaborative approach? | Dedicated customer support; Partnership approach. |
Exporter vers les feuilles
Choisir le bon additive manufacturing partner is an investment in the success of your project. By carefully evaluating potential suppliers against these criteria, you can identify a partner like Met3dp that possesses the technology, expertise, quality commitment, and collaborative spirit needed to successfully produce high-performance 3D printed EV cooling plates.
Cost Factors and Lead Time: Managing Expectations in Metal AM
Understanding the cost structure and typical lead times associated with metal additive manufacturing is crucial for project planning, budgeting, and managing stakeholder expectations. Unlike traditional manufacturing methods where tooling costs dominate low volumes and piece prices drop significantly at high volumes, metal 3D printing cost is driven by a different set of factors, primarily related to material consumption, machine time, and labor-intensive post-processing. Lead times are also influenced by multiple stages beyond just the physical printing.
Key Cost Drivers for 3D Printed EV Cooling Plates:
- Material Type and Cost:
- Powder Price: The base cost of the metal powder feedstock varies significantly. Standard alloys like AlSi10Mg are relatively cost-effective, while high-performance copper alloys like CuCrZr are substantially more expensive due to raw material costs and specialized atomization processes. Exotic or customized alloys will command premium pricing.
- Recycling/Waste: While PBF processes allow for recycling of unfused powder, there are still losses and degradation over time, which factors into the effective material cost.
- Material Consumption (Part Volume + Supports):
- Volume de la pièce : The actual geometric volume of the final part directly impacts the amount of powder fused. Larger parts cost more. DfAM techniques like topology optimization can significantly reduce volume and thus cost.
- Structures de soutien : Supports required for overhangs and internal features are printed using the same expensive material as the part itself. Designs requiring extensive supports will have significantly higher material consumption and cost. Minimizing supports through DfAM is key.
- Print Time (Machine Utilization):
- Build Height: This is often the primary driver of print time. Each layer adds time, so taller parts take longer, regardless of their volume per layer. Printing parts flatter (if possible without compromising function or requiring excessive supports) can sometimes reduce print time.
- Scan Area/Volume: The amount of area the laser or electron beam needs to scan per layer also influences time. Densely packed build plates with multiple parts can optimize machine time per part.
- Machine Taux horaire : Service providers factor in the depreciation, maintenance, energy consumption, and operational costs of their expensive industrial AM systems into an hourly rate.
- Met3dp Efficiency: Met3dp’s printers, with their industry-leading print volume, allow for efficient nesting of multiple parts or production of large single components, optimizing machine utilization.
- Design Complexity & Print Strategy:
- While AM excels at complexity, extremely intricate features might require slower scan speeds or specific strategies to ensure accuracy and quality, potentially slightly increasing print time. However, the primary impact of complexity is usually on support requirements and post-processing effort, rather than the print itself.
- Support Structure Requirements & Removal:
- As mentioned, supports consume material and add print time. Critically, support removal is often a manual, labor-intensive process, especially for internal or hard-to-reach supports. This labor significantly adds to the final cost.
- Exigences en matière de post-traitement :
- This is frequently one of the largest contributors to the final cost per part AM. Each step adds cost:
- Traitement thermique : Requires furnace time, energy, and controlled atmospheres.
- Usinage : Skilled labor and CNC machine time for achieving tight tolerances or specific finishes.
- Finition de la surface : Labor and consumables for blasting, tumbling, polishing; specialized processes like AFM are particularly costly.
- Inspection : Labor, equipment time (CMM, CT scanning), and potential destructive testing costs.
- This is frequently one of the largest contributors to the final cost per part AM. Each step adds cost:
- Travail :
- Includes skilled technicians for machine setup, build monitoring, depowdering, support removal, finishing, inspection, and quality assurance.
- Quality Assurance & Certification:
- Costs associated with material testing, process documentation, witness coupon testing, final inspection reports, and maintaining quality certifications.
- Volume de commande :
- Economies of scale exist in AM, but they are different from traditional manufacturing. Setup costs (build preparation) are amortized over more parts in larger batches. Machine utilization can be optimized with fully nested build plates. Post-processing might be streamlined for batches. Price per part generally decreases with volume, enabling discussions about wholesale cooling plate pricing, but don’t expect the dramatic drops seen with high-volume casting or stamping after tooling amortization.
Facteurs influençant les délais :
Lead time in metal AM is the cumulative time taken for all steps in the workflow:
- Quoting & Design Review (1-3 days): Initial communication, file check, DfAM review/feedback, quote generation.
- File Preparation & Scheduling (1-2 days): Generating support structures, slicing the model, creating the build file, scheduling the job in the machine queue.
- Machine Queue Time (Variable: Days to Weeks): Waiting for an appropriate machine to become available. This can be a significant variable depending on the service provider’s workload.
- Print Time (Hours to Days): The actual time the part spends printing layer by layer. Can range from ~8-12 hours for small, simple parts to 50-100+ hours for large, complex builds.
- Cooling Time (Several Hours to Overnight): Allowing the build plate and parts to cool down slowly and safely within the machine or build chamber, often under an inert atmosphere.
- Post-Processing (Variable: Days to Weeks): This often takes the longest.
- Stress Relief/Heat Treatment: Furnace cycles can take 8-24+ hours, plus cooling time.
- Part/Support Removal, Depowdering, Basic Finishing: 1-2 days typically.
- Machining: Depends on complexity and machine shop scheduling (can add several days).
- Advanced Finishing/Inspection: AFM, extensive polishing, CT scanning can add multiple days depending on vendor lead times if outsourced.
- Final Inspection & Shipping (1-3 days): Final QA checks, packaging, and transit time.
Typical Lead Time Range: For a moderately complex EV cooling plate made from AlSi10Mg requiring heat treatment and some finish machining, expect lead times ranging from 1 to 4 weeks from order confirmation, heavily dependent on machine availability and post-processing complexity. High-complexity parts, CuCrZr material (requiring more specialized handling/parameters), or extensive post-processing can extend this further. Rush services may be available at a premium cost.
Getting Accurate Quotes and Lead Times: To receive the most accurate cost and lead time estimate, provide potential suppliers with a comprehensive data package:
- 3D CAD Model (STEP format preferred)
- Clear material specification (e.g., AlSi10Mg, CuCrZr)
- Detailed drawing indicating critical dimensions, tolerances (using GD&T), and surface finish requirements. Clearly mark surfaces needing machining.
- Required heat treatment condition (e.g., T6 state for AlSi10Mg).
- Required quantity (for prototype or batch production).
- Any specific inspection or testing requirements (e.g., pressure leak test specifications, requirement for CT scan verification).
By understanding these cost and lead time drivers, and by providing detailed information to experienced providers like Met3dp, you can effectively plan your projects and leverage the benefits of metal AM for your EV cooling applications. Feel free to reach out via our Met3dp Contact page to discuss your specific requirements.
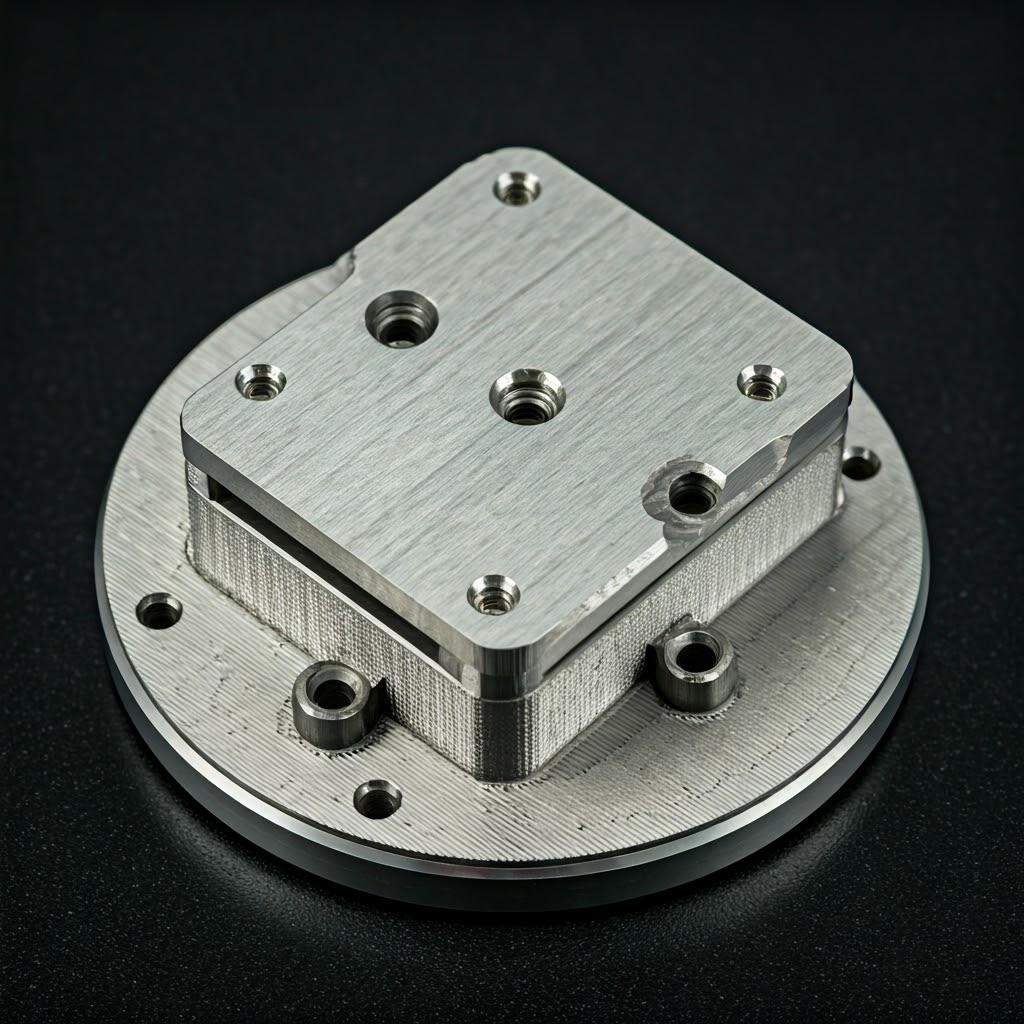
Foire aux questions (FAQ)
Here are answers to some common questions engineers and procurement managers have about using metal 3D printing for EV cooling plates:
Q1: How does the thermal performance of 3D printed AlSi10Mg cooling plates compare to traditional brazed aluminum plates?
A : 3D printed AlSi10Mg cooling plates peut offer significantly superior thermal performance compared to traditional designs (like simple serpentine channels in brazed plates). The key advantage lies in AM’s ability to create highly complex internal geometries (lattices, gyroids, conformal channels) that maximize the surface area for heat transfer and optimize coolant flow paths. Depending on the level of design optimization achieved through DfAM and validated with CFD simulation, performance improvements (e.g., reduced thermal resistance, higher heat dissipation capacity for a given flow rate and size) could potentially range from 20% to over 50% in some cases. However, achieving these gains requires specific expertise in DfAM for thermal management. A simple translation of a traditional design into AM will likely yield little benefit.
Q2: Is 3D printed CuCrZr durable enough for automotive coolant environments and operating conditions?
A : Yes, CuCrZr (Copper-Chromium-Zirconium) is generally considered durable and suitable for typical automotive coolant environments (e.g., water-ethylene glycol mixtures). It exhibits good corrosion resistance, superior to pure copper in many cases. Furthermore, its excellent strength, especially at elevated temperatures compared to aluminum alloys, ensures mechanical integrity under demanding operating conditions found in high-performance EV powertrains. As with any material selection, specific coolant chemistry and operating temperature extremes should be considered, but CuCrZr is a robust choice for high-heat-flux cooling applications demanding longevity.
Q3: Can metal 3D printing be used for serial production of EV cooling plates, or is it primarily for prototypes?
A : Metal 3D printing is increasingly viable and actively used for serial production of components, including EV cooling plates, not just prototypes. While traditionally viewed as a prototyping technology, advancements in machine speed, reliability, size, and process automation have significantly improved its competitiveness. AM is particularly well-suited for serial production in scenarios involving: * High Design Complexity: Where the performance benefits of complex AM designs outweigh potential per-part cost differences. * Moderate Volumes: Where the production quantities don’t justify the high investment in traditional tooling (e.g., complex casting molds or stamping dies). * Personnalisation : Where cooling plates need to be adapted for different vehicle variants or battery configurations. * Consolidation partielle : Where printing a single complex part replaces a multi-component assembly, simplifying the supply chain. Met3dp’s reliable, large-volume printers are designed for both prototype and series production runs. A thorough cost-benefit analysis comparing AM to optimized traditional methods is recommended based on specific volume requirements and design complexity.
Q4: What level of cleanliness can be achieved inside the complex internal channels of a 3D printed cooling plate?
A : Achieving high levels of internal cleanliness is possible but requires dedicated and rigorous post-processing steps beyond simple powder dumping and blowing. Standard methods include high-pressure air/liquid flushing and ultrasonic cleaning. For stringent requirements, advanced techniques like Abrasive Flow Machining (AFM) can polish internal channels and remove adhered particles. Verification is key, often involving borescope inspection, microscopic analysis of flushed fluids for particle counts, or even CT scanning to ensure no powder residue or contaminants remain that could affect coolant flow or downstream components. Define cleanliness requirements early and discuss appropriate cleaning and verification methods with your AM provider.
Q5: What information do I need to provide to get an accurate quote for a 3D printed cooling plate?
A : To receive a timely and accurate quote, provide your potential AM supplier with as much detail as possible, typically including: * Modèle CAO 3D : Preferably in a neutral format like STEP. * Spécification du matériau : Clearly state the desired alloy (e.g., AlSi10Mg, CuCrZr). * Technical Drawing: Include critical dimensions, tolerances (using GD&T), and required surface finishes (Ra values) for specific features, especially mating/sealing surfaces. * Traitement thermique : Specify the required condition (e.g., As-Built, Stress Relieved, T6 condition). * Quantité : Number of parts required (for prototypes or batch sizes). * Testing & Inspection: Detail any mandatory testing (e.g., pressure leak testing requirements – pressure, duration, medium) or inspection needs (e.g., CT scan verification of internal channels). * Delivery Deadline: If applicable. The more complete the information, the faster and more accurately the supplier can assess feasibility, cost, and lead time.
Conclusion: Accelerating EV Innovation with Additive Manufacturing
The relentless drive for higher performance, longer range, faster charging, and enhanced safety in electric vehicles places immense pressure on thermal management systems. Traditional manufacturing methods for critical components like cooling plates are increasingly hitting limitations in delivering the complex, lightweight, and highly efficient solutions required. Metal additive manufacturing has emerged as a powerful enabler, offering unprecedented design freedom to revolutionize how EV cooling plates are conceived and produced.
As we’ve explored, utilizing metal AM allows engineers to:
- Design highly complex internal geometries (lattices, conformal channels) impossible with conventional methods, drastically improving heat transfer efficiency.
- Achieve significant lightweighting through topology optimization and the use of materials like AlSi10Mg, contributing to better vehicle range and dynamics.
- Consolidate multiple components into a single printed part, reducing assembly complexity, potential leak points, and simplifying the supply chain.
- Prototyper et itérer rapidement on designs, accelerating development cycles.
- Customize solutions for specific vehicle architectures and thermal challenges.
However, unlocking these benefits requires navigating the nuances of Design for Additive Manufacturing (DfAM), careful material selection (balancing performance needs of AlSi10Mg vs. CuCrZr, for example), meticulous post-processing, and robust quality control. Success hinges not only on understanding the technology but also on partnering with the right manufacturing provider.
Met3dp stands as a leader in the metal additive manufacturing landscape, uniquely positioned to support the automotive industry’s transition towards advanced thermal management solutions. We offer a comprehensive ecosystem:
- Industry-leading SEBM and LPBF printing systems delivering accuracy, reliability, and volume production capabilities.
- In-house manufacturing of high-quality, optimized metal powders, including AlSi10Mg, leveraging advanced atomization techniques for superior consistency and performance.
- Deep technical expertise and application development support to help you optimize designs and navigate the complexities of AM.
- A commitment to quality throughout the entire process, from powder to finished part.
Whether you are developing prototypes for next-generation EVs or seeking a reliable partner for series production of advanced cooling components, Met3dp provides the technology, materials, and expertise to turn your concepts into reality. We are dedicated to empowering innovation in the EV sector and beyond.
Contactez Met3dp aujourd'hui to discuss your specific EV cooling plate requirements and discover how our cutting-edge additive manufacturing solutions can help you achieve your thermal management goals and accelerate your journey towards electrification.
Partager sur
MET3DP Technology Co. est un fournisseur de premier plan de solutions de fabrication additive dont le siège se trouve à Qingdao, en Chine. Notre société est spécialisée dans les équipements d'impression 3D et les poudres métalliques de haute performance pour les applications industrielles.
Articles connexes
À propos de Met3DP
Mise à jour récente
Notre produit
CONTACTEZ-NOUS
Vous avez des questions ? Envoyez-nous un message dès maintenant ! Nous répondrons à votre demande avec toute une équipe dès réception de votre message.
Obtenir les informations de Metal3DP
Brochure du produit
Obtenir les derniers produits et la liste des prix
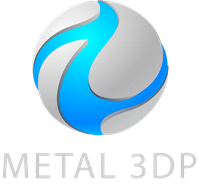
Poudres métalliques pour l'impression 3D et la fabrication additive