3D Printing Sealing Rings for Aerospace Engines
Table des matières
Introduction: Revolutionizing Aerospace Sealing with Metal Additive Manufacturing
The aerospace industry operates at the cutting edge of engineering, demanding components that deliver uncompromising performance, reliability, and safety under some of the most extreme conditions imaginable. Within the intricate heart of jet engines and auxiliary power units (APUs), seemingly simple components like sealing rings play a mission-critical role. These rings are the unsung heroes responsible for containing high-pressure fluids and gases, preventing leaks, maintaining operational efficiency, and ultimately ensuring flight safety. Traditionally manufactured through complex machining or casting processes, the production of high-performance aerospace sealing rings is often time-consuming and constrained by design limitations. However, a paradigm shift is underway, driven by the advancements in la fabrication additive métallique (AM), commonly known as metal L'impression 3D. This technology is not just an alternative production method; it’s a transformative force enabling the creation of aerospace sealing rings with enhanced performance, optimized designs, and significantly reduced lead times.
Metal AM allows engineers to break free from the constraints of traditional manufacturing. Complex geometries, internal channels for cooling or lubrication, and topology-optimized structures that were once impossible or prohibitively expensive to produce can now be realized directly from digital models. This capability is particularly impactful for sealing rings, where intricate designs can lead to improved sealing efficiency, reduced weight, and better integration with surrounding components. For industries where every gram saved translates to fuel efficiency and every incremental performance boost matters, the potential offered by AM is immense. Furthermore, the ability to rapidly iterate designs and produce functional prototypes or even end-use parts accelerates development cycles and strengthens the supply chain for critical composants du moteur.
En tant que chef de file solutions de fabrication additive, Met3dp is at the forefront of this technological evolution. Headquartered in Qingdao, China, Met3dp specializes in providing state-of-the-art impression 3D de métaux equipment, particularly Selective Electron Beam Melting (SEBM) systems, and high-performance metal powders tailored for demanding industrial applications. Our deep expertise in materials science and AM processes enables us to partner with aerospace manufacturers, suppliers, and MRO (Maintenance, Repair, and Overhaul) providers to unlock the full potential of metal AM for components like high-performance seals. We understand the rigorous demands of the aerospace sector and are committed to delivering solutions that meet the highest standards of quality, reliability, and performance, facilitating the transition towards next-generation aerospace manufacturing. This article delves into the specifics of using metal 3D printing for aerospace sealing rings, exploring their function, the advantages of AM, suitable materials like IN625 and 17-4PH, design considerations, and how to partner effectively for success.
The Critical Function of Sealing Rings in Aerospace Engines
Aerospace engines, whether powering commercial airliners, military jets, or spacecraft, are marvels of engineering that operate under conditions of extreme stress. Temperatures can swing from cryogenic lows to well above 1000∘C, pressures can reach hundreds of atmospheres, and components are constantly subjected to intense vibrations, G-forces, and potentially corrosive environments created by combustion byproducts and lubricants. Within this hostile environment, sealing rings perform several indispensable functions vital for safe and efficient operation. Primarily, they act as barriers, preventing the leakage of fluids (like fuel or oil) and gases (like compressed air or hot combustion gases) between different sections of the engine or between moving and stationary parts.
Consider the main sections of a typical jet engine: the fan, compressor, combustor, turbine, and exhaust nozzle. Maintaining precise pressure differentials between these sections is crucial for optimal thermodynamic efficiency. Aerospace engine seals, strategically placed throughout the engine architecture, ensure this separation.
- Compressor Seals: In the compressor stages, seals prevent high-pressure air from leaking back towards lower-pressure stages, ensuring maximum air is delivered to the combustor. This directly impacts engine thrust and fuel efficiency.
- Turbine Seals: In the turbine section, seals must withstand extremely high temperatures while preventing hot combustion gases from bypassing the turbine blades. Leakage here reduces the energy extracted by the turbine, decreasing power output and efficiency. They also prevent hot gases from reaching cooler engine sections or bearings, which could cause catastrophic damage. Common types include labyrinth seals, brush seals, and ring seals, many of which can benefit from AM’s design flexibility.
- Bearing Compartment Seals: These seals are critical for containing lubricating oil within bearing compartments and preventing its leakage into hot gas paths (which poses a fire risk) or contamination by external elements. They must operate reliably across a wide range of temperatures and pressures.
- Accessory Gearbox Seals: Seals within the gearbox prevent oil leaks and contamination, ensuring the reliable operation of engine accessories like fuel pumps, generators, and hydraulic pumps.
- Fuel System Seals: Sealing rings within fuel lines, pumps, and injectors prevent fuel leaks, which are a major safety hazard. They must be compatible with jet fuel and withstand system pressures.
Failure of any of these seals can lead to a cascade of problems, including:
- Reduced engine performance (lower thrust, higher fuel consumption)
- Increased operating temperatures, potentially exceeding material limits
- Oil or fuel leaks, creating fire hazards
- Damage to adjacent components due to escaping hot gases or lack of lubrication
- In severe cases, engine shutdown or catastrophic failure.
Therefore, the materials, design, and manufacturing quality of these sealing rings are subject to the highest scrutiny. They must maintain their integrity, shape, and sealing capability despite thermal cycling, high pressures, rotational speeds, and vibrations. The increasing performance demands of modern engines (higher temperatures, pressures, and efficiency targets) continually push the limits of traditional materials and manufacturing methods, creating a strong case for innovative solutions like metal additive manufacturing. As a key aerospace component supplier through our advanced powders and printing technology, Met3dp understands these critical requirements and provides the materials and processes necessary to produce next-generation sealing solutions. The complexity and performance requirements make these components ideal candidates for the advanced capabilities offered by metal AM.
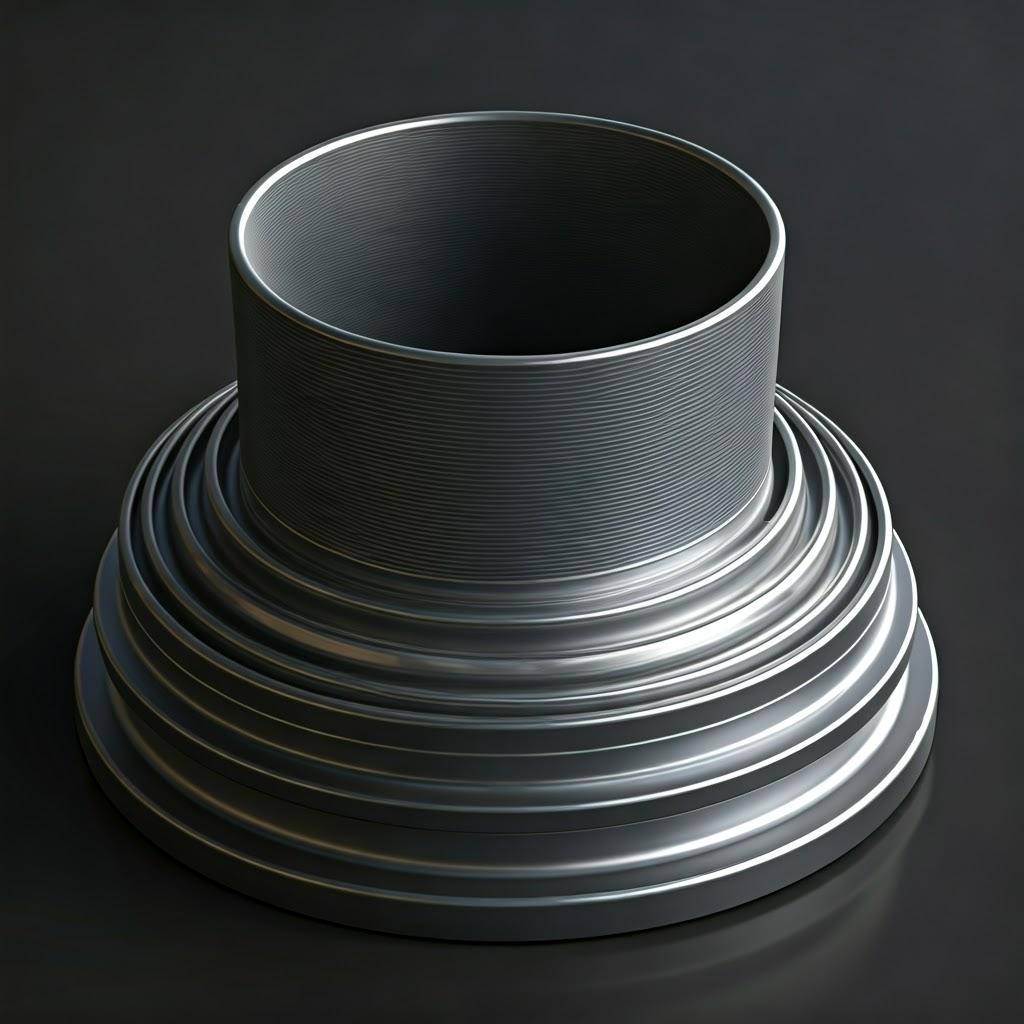
Why Choose Metal 3D Printing for Aerospace Sealing Rings?
While traditional manufacturing methods like precision machining from bar stock or forgings, and investment casting, have long served the aerospace industry, they come with inherent limitations, especially when dealing with complex geometries or high-performance alloys. Metal additive manufacturing, particularly powder bed fusion (PBF) techniques like Selective Laser Melting (SLM), Direct Metal Laser Sintering (DMLS), and Selective Electron Beam Melting (SEBM), offers compelling advantages for producing aerospace sealing rings, addressing many traditional challenges and unlocking new possibilities.
Key Advantages of Metal AM for Aerospace Seals:
- Liberté de conception et complexité :
- Défis avec les méthodes traditionnelles : Machining intricate internal features, complex curves, or thin walls needed for optimal sealing performance can be difficult, costly, or impossible. Casting may struggle with fine details and internal complexity.
- Avantage AM : AM builds parts layer by layer directly from a 3D CAD model, enabling the creation of highly complex geometries without the constraints of tooling or subtractive processes. This allows for:
- Optimisation de la topologie : Algorithms can design the lightest possible ring that still meets all structural and sealing requirements, removing material only where it’s not needed.
- Conformal Features: Cooling channels or lubrication pathways that follow the contours of the ring can be integrated directly into the design, improving thermal management or durability.
- Consolidation partielle : Multiple components of a seal assembly could potentially be combined into a single, complex 3D printed part, reducing assembly time, weight, and potential leak paths.
- Rapid Prototyping and Development:
- Défis avec les méthodes traditionnelles : Creating prototypes often requires dedicated tooling (for casting) or extensive machining setup, leading to long lead times (weeks or months) and high costs for each design iteration.
- Avantage AM : AM allows engineers to quickly produce functional prototypes directly from digital files, often within days. This accelerates design validation, testing, and iteration cycles, allowing for faster development of optimized sealing solutions. Met3dp’s capabilities enable rapid turnaround for such critical rapid prototyping aerospace besoins.
- Efficacité des matériaux et réduction des déchets :
- Défis avec les méthodes traditionnelles : Subtractive manufacturing (machining) starts with a larger block of material and removes excess, often generating significant (and expensive) scrap, especially with high-value aerospace alloys like Inconel.
- Avantage AM : AM is an additive process, using only the material necessary to build the part and its supports. While some powder is non-recyclable support or waste, the buy-to-fly ratio (ratio of raw material weight to final part weight) is often significantly better than machining, reducing material costs and waste, contributing to supply chain optimization.
- Enhanced Performance Potential:
- Défis avec les méthodes traditionnelles : Designs are often compromises based on manufacturing limitations rather than purely performance needs.
- Avantage AM : The design freedom allows engineers to focus purely on optimizing the seal’s function. This might involve creating specific surface textures for better sealing, integrating features for reduced vibration, or using graded materials (though less common for seals currently). The fine microstructures achievable with rapid solidification in AM processes like SEBM, offered by Met3dp, can also lead to superior mechanical properties compared to cast equivalents.
- Suitability for High-Performance Materials:
- Défis avec les méthodes traditionnelles : High-performance alloys like Nickel-based superalloys (e.g., IN625) can be difficult and expensive to machine due to their high strength and work-hardening characteristics.
- Avantage AM : Metal AM processes are well-suited for processing these advanced alloys. While challenges exist (e.g., managing residual stress), specialized equipment and process control, like Met3dp’s SEBM technology and optimized powder parameters, allow for the successful printing of these materials into dense, high-integrity parts.
- On-Demand and Distributed Manufacturing:
- Défis avec les méthodes traditionnelles : Relies on centralized foundries or machine shops, potentially long supply chains, and significant tooling investments.
- Avantage AM : Enables a more distributed manufacturing model. Parts can potentially be printed closer to the point of need, reducing logistics costs and lead times. Digital inventories replace physical ones, allowing for on-demand production of spare parts, critical for MRO operations.
Comparison Table: Traditional vs. Metal AM for Sealing Rings
Fonctionnalité | Traditional Manufacturing (Machining/Casting) | Fabrication additive métallique (PBF) | Advantage AM Offers for Seals |
---|---|---|---|
Complexité de la conception | Limited by tooling, machining access, casting constraints | High degree of freedom, complex internal features possible | Optimized shapes, integrated features, part consolidation |
Vitesse de prototypage | Slow (weeks/months), high cost per iteration | Fast (days), lower cost per iteration | Accelerated development & validation |
Déchets matériels | High (machining), moderate (casting) | Lower (significant reduction vs. machining) | Reduced cost for expensive alloys, more sustainable |
Délai d'exécution | Longer, especially for complex parts or low volumes | Shorter, particularly for prototypes and complex/low-volume production | Faster time-to-market, improved MRO response |
Outillage | Required (molds, fixtures), high upfront cost | Tool-less manufacturing | Economical for low volumes & customized parts |
Performance | Limited by manufacturability constraints | Potential for enhanced performance via optimized design & microstructure | Lighter weight, better thermal management, potentially higher strength |
Utilisation des matériaux | Suitable for standard alloys, challenging for some superalloys | Excellent for high-performance & difficult-to-machine alloys | Enables use of optimal materials like IN625 |
Exporter vers les feuilles
By leveraging these advantages, metal AM aerospace applications are rapidly expanding, and sealing rings represent a prime opportunity for manufacturers seeking enhanced performance, efficiency, and supply chain agility. Choosing AM is not just about adopting a new manufacturing technique; it’s about embracing a new philosophy for designing and producing critical aerospace parts production.
Material Focus: IN625 and 17-4PH for Demanding Sealing Applications
The selection of the right material is paramount for aerospace sealing rings, given the extreme operating conditions they endure. The material must possess a unique combination of high temperature strength, corrosion resistance, fatigue strength, creep resistance, and thermal stability. Two alloys that consistently meet these demanding requirements and are readily processable via metal additive manufacturing are the Nickel-based superalloy Inconel 625 (IN625) and the precipitation-hardening stainless steel 17-4PH. Both are offered as high-quality, spherical powders by leading fournisseurs de poudres métalliques like Met3dp, optimized for PBF processes.
Inconel 625 (IN625 / Alloy 625): The High-Temperature Workhorse
IN625 is a Nickel-Chromium-Molybdenum-Niobium alloy renowned for its exceptional combination of properties, making it a staple in aerospace, chemical processing, and marine applications.
- Key Properties & Benefits for Sealing Rings:
- Excellent High-Temperature Strength: IN625 retains significant strength and toughness at elevated temperatures (up to 815∘C / 1500∘F and even higher for short excursions), crucial for seals operating near combustors or turbines. Its strength derives from the solid solution stiffening effect of Molybdenum and Niobium within the Nickel-Chromium matrix.
- Résistance exceptionnelle à la corrosion : It exhibits superb resistance to a wide range of corrosive media, including oxidation, carburization, pitting, and crevice corrosion, essential for longevity in harsh engine environments exposed to combustion gases and potential contaminants. The high Chromium and Molybdenum content are key contributors.
- Superb Fatigue and Creep Strength: Resists degradation under cyclic loading (fatigue) and continuous stress at high temperatures (creep), vital for ensuring long-term sealing integrity under operational loads and vibrations.
- Good Fabricability and Weldability: Although traditionally challenging to machine, IN625 is well-suited for additive manufacturing processes. Met3dp provides IN625 3D printing powder specifically characterized for optimal flowability and consistent melting behavior in PBF systems.
- Stabilité thermique : Maintains its microstructure and properties after prolonged exposure to high temperatures.
- Why Use AM for IN625 Seals? AM allows for the creation of complex IN625 seal geometries that maximize performance while minimizing weight. It overcomes the machinability challenges associated with this tough alloy, making intricate designs feasible and reducing material waste compared to subtractive methods. Post-processing, including heat treatments like solution annealing and aging (or HIP), is crucial to achieve the desired final properties in AM IN625 parts.
17-4PH Stainless Steel: High Strength and Good Corrosion Resistance
17-4PH is a Chromium-Nickel-Copper precipitation-hardening martensitic stainless steel. It offers an excellent combination of high strength, hardness, good corrosion resistance (comparable to 304 stainless steel in many environments), and good toughness, particularly in lower-temperature sealing applications within the engine or in auxiliary systems.
- Key Properties & Benefits for Sealing Rings:
- Résistance et dureté élevées : Through simple heat treatment (solution treatment followed by aging), 17-4PH can achieve very high tensile strength and hardness, providing excellent wear resistance for dynamic sealing applications. Different heat treatment conditions (e.g., H900, H1025, H1075, H1150) allow tailoring of properties (strength vs. toughness).
- Bonne résistance à la corrosion : Offers significantly better corrosion resistance than standard martensitic stainless steels (like 400 series), suitable for many aerospace environments, although not typically as resistant as IN625 in the most aggressive high-temperature, corrosive conditions.
- Good Fatigue Life: Exhibits good resistance to fatigue failure under cyclic loading.
- Excellent Processability via AM: 17-4PH stainless steel AM is a well-established process. The material generally prints well, achieving high densities. Met3dp offers 17-4PH powder optimized for PBF, ensuring consistency crucial for aerospace applications.
- Rapport coût-efficacité : Generally less expensive than Nickel-based superalloys like IN625, making it a viable option for seals where the extreme temperature and corrosion resistance of IN625 are not strictly necessary.
- Why Use AM for 17-4PH Seals? AM enables the production of complex 17-4PH sealing rings with optimized geometries. The ability to precisely control the heat treatment post-printing allows fine-tuning of the mechanical properties to meet specific application requirements (e.g., maximizing hardness for wear resistance or optimizing toughness for fatigue life).
Met3dp’s Powder Expertise:
The quality of the final 3D printed part begins with the quality of the metal powder. Met3dp employs industry-leading powder production technologies, including vacuum gas atomization (VIGA) and Plasma Rotating Electrode Process (PREP), to manufacture high-quality aerospace materials poudres.
- Atomisation par gaz : Utilizes inert gas jets to break up a stream of molten alloy, creating fine, spherical droplets that solidify rapidly. This process yields powders with:
- Sphéricité élevée : Ensures excellent powder flowability and uniform spreading in the PBF machine’s recoater system.
- Low Satellite Content: Minimizes irregularly shaped particles, leading to higher packing density and more uniform melting.
- Distribution contrôlée de la taille des particules (PSD) : Tailored PSD for specific AM processes (SLM, SEBM) ensures optimal layer thickness and melt pool stability.
- PREP: Uses a rapidly rotating electrode of the target material, which melts at the tip due to plasma heating. Centrifugal force ejects molten droplets that solidify in flight into highly spherical powders with very high purity and minimal internal porosity or satellites. This is often preferred for the most demanding applications, particularly for reactive materials.
Our commitment to quality ensures that Met3dp powders, including IN625 and 17-4PH, possess the characteristics necessary for producing dense, defect-free, high-performance aerospace components like sealing rings. We provide comprehensive material certifications and data sheets detailing powder chemistry, PSD, morphology, and flow characteristics, giving engineers and procurement managers confidence in the material integrity.
Material Selection Table:
Fonctionnalité | IN625 | Acier inoxydable 17-4PH | Selection Guidance |
---|---|---|---|
Temp. de fonctionnement max. | Very High (~815°C+, application dependent) | Moderate (~315°C – 480°C, condition dependent) | Choose IN625 for turbine/combustor proximity; 17-4PH for cooler sections/auxiliary. |
Résistance à la corrosion | Excellent (wide range, high temp) | Good (general atmospheric, mild chemicals) | IN625 for highly corrosive environments (combustion gases); 17-4PH often sufficient. |
Strength @ Room Temp. | Haut | Very High (tunable via heat treatment) | 17-4PH can achieve higher hardness/strength if needed for wear. |
Strength @ High Temp. | Excellent | Moderate (strength drops significantly >315°C) | IN625 clearly superior for high-temp mechanical loads. |
Fatigue/Creep Resistance | Excellent | Good / Moderate | IN625 preferred for components under high cyclic/static load at temperature. |
Coût | Haut | Modéré | Use 17-4PH where its properties suffice to manage costs. |
AM Processability | Good (requires careful control) | Excellent | Both are well-suited for AM with appropriate parameters and expertise. |
Exporter vers les feuilles
Choosing between IN625 and 17-4PH depends heavily on the specific location and operational requirements of the sealing ring within the aerospace application. Partnering with an experienced AM provider like Met3dp, with deep material science knowledge, can help navigate these choices and ensure the optimal material is selected and processed correctly for mission-critical components. Sources and related content
Design Optimization for Additively Manufactured Sealing Rings
Transitioning from traditional manufacturing methods to additive manufacturing for aerospace sealing rings isn’t simply about replicating the existing design using a 3D printer. To truly harness the power of AM and achieve superior performance, weight reduction, and cost-effectiveness, engineers must embrace Conception pour la fabrication additive (DfAM) principles. DfAM is a methodology that involves designing parts specifically to leverage the unique capabilities and address the constraints of AM processes. For critical components like sealing rings, optimizing the design for AM can significantly impact printability, material properties, post-processing requirements, and overall functionality.
Key DfAM Considerations for Aerospace Sealing Rings:
- Leveraging Geometric Complexity:
- Optimized Cross-Sections: Traditional seals often have simple rectangular or O-ring cross-sections due to machining limitations. AM allows for complex, non-uniform cross-sections tailored to specific stress distributions or flow dynamics, potentially improving sealing efficiency or reducing contact pressure variations.
- Internal Features: Consider integrating features like internal channels for cooling in very high-temperature applications, or lubricant pathways for dynamic seals. These are extremely difficult or impossible to create conventionally but feasible with AM.
- Conception conforme : Design the seal to conform perfectly to mating surfaces, potentially simplifying assembly or improving sealing contact.
- Optimisation de la topologie et allègement :
- While sealing rings are often relatively small, weight savings are always critical in aerospace. Optimisation de la topologie software can be used to remove material from non-critical areas of the seal’s body (away from the sealing interface), maintaining structural integrity while reducing mass. This is particularly relevant for larger diameter seals or seal housings.
- Structures en treillis : In some cases, internal lattice structures could potentially replace solid sections to significantly reduce weight, although their application in primary sealing surfaces needs careful evaluation regarding permeability and cleanability. They might be more applicable in structural elements supporting the seal.
- Minimizing and Optimizing Support Structures:
- Défi: Metal PBF processes require support structures for overhanging features (typically angles below 45 degrees relative to the build plate) and to anchor the part, managing thermal stresses. Supports consume material, add print time, and require removal in post-processing, which can be challenging and time-consuming, especially for internal features.
- DfAM Solutions:
- Print Orientation: Carefully select the build orientation to minimize the number and extent of overhangs requiring support. Consider how orientation affects surface finish on critical sealing faces and potential anisotropy (directional variation in properties).
- Angles autoportants : Design overhangs to be self-supporting (typically >45 degrees) wherever possible.
- Designing for Access: If internal supports are unavoidable (e.g., for internal channels), design access ports or features that allow for easier removal (machining, chemical etching, abrasive flow machining).
- Chamfers and Fillets: Replace sharp horizontal overhangs with chamfers or fillets that gradually transition, reducing the need for supports.
- Wall Thickness and Feature Size:
- Taille minimale des fonctionnalités : Understand the minimum printable wall thickness and feature resolution of the specific AM process and machine (e.g., Met3dp’s SEBM systems). Avoid designing features that are too thin to be reliably produced. Typical minimum wall thicknesses for PBF are often in the range of 0.4 – 1.0 mm, depending on the material and machine.
- Uniform Wall Thickness: Aim for relatively uniform wall thicknesses where possible to promote even heating and cooling during the build, reducing residual stress and potential warping.
- Concevoir pour le post-traitement :
- Tolérances d'usinage : Identify critical surfaces (e.g., sealing faces, mating diameters) that will require post-machining to achieve final tolerances and surface finish. Add sufficient sacrificial stock material (machining allowance) to these areas in the CAD model (typically 0.5 – 2.0 mm).
- Fixturing: Consider how the part will be held for post-processing steps like machining or inspection. Incorporate datum features or surfaces into the design to facilitate accurate fixturing.
- Surface Finish Considerations: Understand that upward-facing and downward-facing surfaces will have different as-printed roughness. Orient the part so that critical surfaces are either vertical or upward-facing if possible, or ensure sufficient stock is left for machining downward-facing critical surfaces.
- Stress Concentration Reduction:
- Use generous fillets and radii at corners and transitions to reduce stress concentrations, improving fatigue life. AM allows for smooth, organic transitions that are often easier to implement than with traditional machining.
DfAM Workflow Integration:
Effective DfAM requires close collaboration between design engineers, materials scientists, and AM process specialists. Utilizing simulation tools for thermal and stress analysis during the design phase can help predict potential issues like warping or hot spots and allow for design adjustments before printing. Partnering with an experienced AM service provider like Met3dp, which offers engineering support alongside manufacturing, can provide invaluable insights into optimizing designs for their specific méthodes d'impression and materials, ensuring a successful outcome for demanding aerospace sealing ring applications. Investing time in DfAM upfront significantly reduces risks, minimizes post-processing challenges, and maximizes the benefits of adopting additive manufacturing.
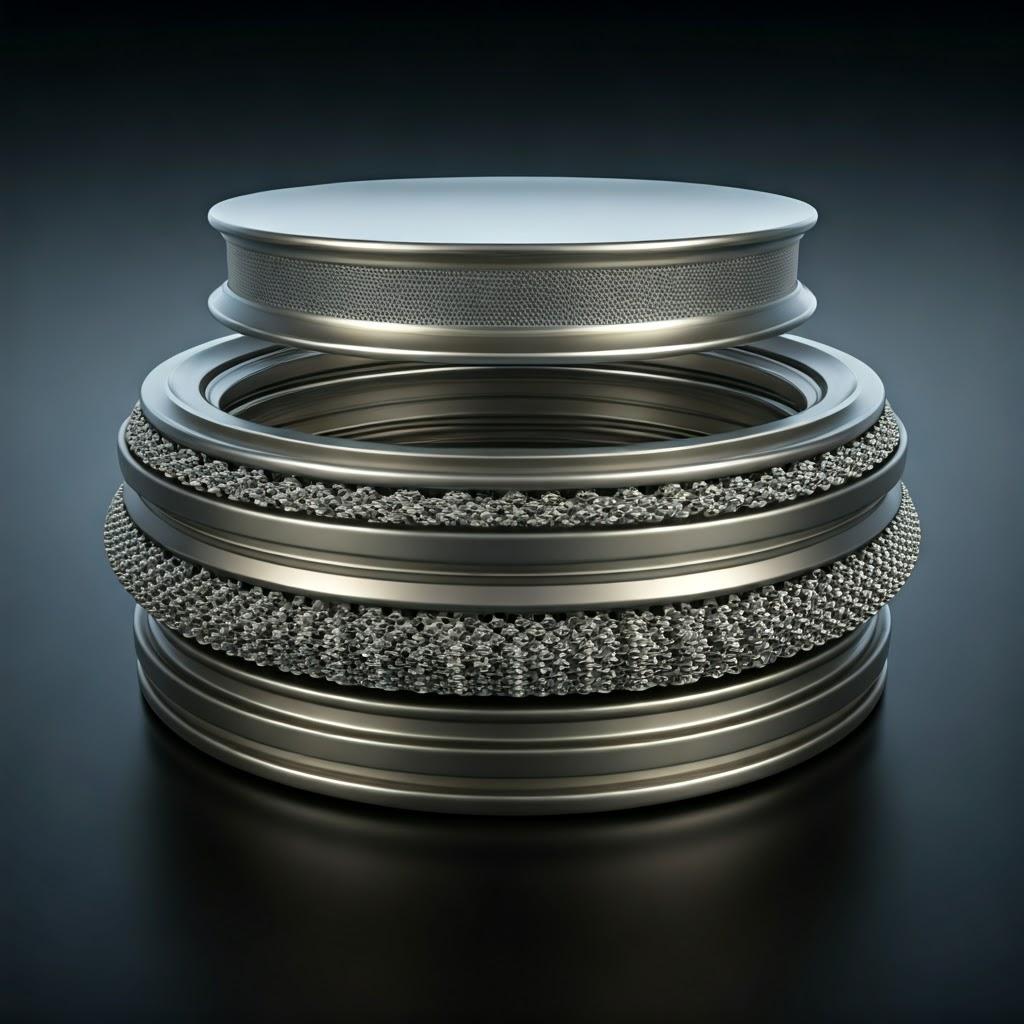
Atteindre la précision : Tolérance, état de surface et précision dimensionnelle
For aerospace components, particularly sealing rings where precise dimensions and smooth surfaces are critical for function, understanding the achievable levels of precision with metal additive manufacturing is essential. While AM offers incredible design freedom, it inherently produces parts with different tolerance ranges and surface characteristics compared to traditional high-precision machining. Managing expectations and planning for necessary post-processing are key.
Typical Tolerances in Metal PBF:
Metal Powder Bed Fusion (PBF) processes like SLM and SEBM, such as those utilized by Met3dp, offer some of the best dimensional accuracy within the AM landscape. However, several factors influence the final tolerances:
- Étalonnage de la machine : The accuracy of the laser/electron beam positioning, layer thickness control, and thermal management systems.
- Paramètres du processus : Settings like beam power, scan speed, layer height, and hatch spacing affect melt pool stability and solidification, influencing shrinkage and accuracy.
- Propriétés du matériau : Different alloys exhibit varying degrees of shrinkage and thermal stress during processing.
- Part Geometry and Size: Larger parts and complex geometries are more susceptible to thermal distortion.
- Orientation de la construction : The orientation affects how thermal stresses accumulate and can influence dimensional accuracy along different axes.
- Post-traitement : Heat treatments (stress relief, HIP) can cause slight dimensional changes, which must be accounted for.
As a general guideline, typical as-printed dimensional tolerances for optimized metal PBF processes are often in the range of:
- ±0.1 mm to ±0.2 mm for smaller features (e.g., up to 25-50 mm)
- ±0.2% to ±0.5% for larger dimensions.
Crucially, these as-printed tolerances are often insufficient for the critical sealing surfaces or mating diameters of aerospace sealing rings. These features typically require much tighter tolerances, often in the range of ±0.01 mm to ±0.05 mm or even tighter, which necessitates post-machining.
Finition de la surface (rugosité) :
Surface finish, typically quantified by the arithmetic average roughness (Ra), is another critical characteristic, especially for dynamic seals or surfaces requiring a specific contact profile.
- As-Printed Surface Finish: The surface finish of AM parts is inherently rougher than machined surfaces due to the layer-by-layer process and partially melted powder particles adhering to the surface.
- Side Walls (Vertical): Often exhibit layer lines, with Ra values typically ranging from 6 $\mu$m to 15 $\mu$m.
- Upward-Facing Surfaces: Generally smoother, potentially Ra 5 $\mu$m to 10 $\mu$m.
- Downward-Facing Surfaces (Supported): Tend to be the roughest due to contact with support structures, often Ra 15 $\mu$m to 25 $\mu$m or more. The removal of supports also impacts the finish.
- Post-Processed Surface Finish: To achieve the smooth surfaces required for effective sealing (often Ra<1.6 $\mu$m, and sometimes much lower, e.g., Ra<0.8 $\mu$m or Ra<0.4 $\mu$m), post-processing is essential.
- Machining (Turning, Grinding): Can achieve very fine finishes (Ra<0.8 $\mu$m).
- Polissage : Can further improve surface finish to mirror-like levels (Ra<0.1 $\mu$m) if required.
- Mass Finishing (Tumbling, Vibratory Finishing): Can improve general surface smoothness and remove loose particles but offers less control over specific surfaces.
- Usinage par flux abrasif (AFM) : Can polish internal channels and complex surfaces.
Dimensional Accuracy Management:
Achieving the final required dimensional accuracy aerospace components demand involves a multi-faceted approach:
- Accurate AM Process Control: Utilizing high-quality equipment like Met3dp’s printers, optimized process parameters developed through rigorous testing, and high-quality, consistent metal powders (like Met3dp’s gas atomized or PREP powders) are foundational.
- DfAM Implementation: Designing the part with AM constraints and post-processing in mind (e.g., adding machining stock).
- Strategic Post-Processing: Implementing precise machining and finishing operations targeting critical features.
- Un contrôle de qualité rigoureux : Employing advanced metrology techniques (CMM, 3D scanning) to verify dimensions at multiple stages – post-print, post-heat treatment, and final inspection.
Table: Precision Expectations for AM Sealing Rings
Fonctionnalité | As-Printed State (Typical PBF) | Post-Processed State (Targeted) | Key Enabling Factor |
---|---|---|---|
General Tolerance | ±0.1 mm – ±0.5% | Defined by Design Specification | AM Process Control |
Critical Tolerance | Often insufficient | ±0.01 mm – ±0.05 mm (or tighter) | Usinage CNC |
Surface Finish (Ra) | 5 $\mu$m – 25+ $\mu$m | <1.6 $\mu$m (often <0.8 $\mu$m or lower) | Machining / Polishing |
Dimensional Control | Good baseline | High, meeting aerospace standards | Integrated QA & Metrology |
Exporter vers les feuilles
By understanding these achievable levels of precision and integrating post-processing into the manufacturing plan, companies can confidently utilize metal AM to produce aerospace sealing rings that meet the stringent quality control additive manufacturing demands of the industry. Partnering with a provider like Met3dp, who understands the entire workflow from powder to finished part, ensures that precision requirements are addressed effectively.
Essential Post-Processing Steps for Aerospace Sealing Rings
Additive manufacturing is often highlighted for its ability to create complex parts in a single process step, but for demanding applications like aerospace sealing rings, the “printing” is just one part of the journey. Metal AM post-processing is a critical sequence of steps required to transform the as-printed part into a functional component that meets stringent material property, dimensional tolerance, and surface finish requirements. Omitting or improperly executing these steps can compromise the integrity and performance of the seal.
Typical Post-Processing Workflow for AM Aerospace Seals:
- Soulagement du stress :
- Objet : The rapid heating and cooling cycles inherent in PBF processes create significant residual stresses within the printed part. These stresses can cause distortion or cracking, especially after removal from the build plate. A thermal stress relief cycle (typically performed while the part is still attached to the build plate in a controlled atmosphere furnace) reduces these internal stresses.
- Méthode : Heating the part to a specific temperature (below the material’s aging or annealing temperature) and holding it for a set duration, followed by slow cooling. Parameters vary significantly based on the alloy (IN625 vs. 17-4PH) and part geometry.
- Retrait de la pièce de la plaque de construction :
- Objet : Separating the printed sealing ring(s) from the base plate they were built upon.
- Méthode : Typically done using wire EDM (Electrical Discharge Machining) or a bandsaw. Care must be taken to avoid damaging the parts.
- Retrait de la structure de soutien :
- Objet : Removing the temporary support structures required during the build process.
- Méthode : Can be a combination of manual removal (breaking or cutting easily accessible supports), CNC machining, grinding, or sometimes specialized techniques like electrochemical machining for difficult-to-reach areas. This can be one of the most labor-intensive steps, highlighting the importance of DfAM to minimize supports.
- Heat Treatment (Crucial for Properties):
- Objet : To homogenize the microstructure, eliminate internal voids (porosity), and achieve the final desired mechanical properties (strength, hardness, ductility, toughness, creep resistance) specified for the aerospace application.
- Methods for Aerospace Seals:
- Pressage isostatique à chaud (HIP) : This is often considered essential for critical aerospace components. Parts are subjected to high temperature (below melting point) and high inert gas pressure (e.g., Argon) simultaneously. This process effectively closes internal porosity and diffusion bonds the material, leading to near 100% density and improved fatigue life and mechanical properties.
- Recuit de la solution : Heats the material to a high temperature to dissolve precipitates and homogenize the structure, followed by rapid cooling.
- Aging (Precipitation Hardening): A lower temperature heat treatment used for alloys like 17-4PH (and sometimes IN625 depending on spec) to form strengthening precipitates within the metal matrix, significantly increasing hardness and strength. The specific aging cycle (e.g., H900, H1075 for 17-4PH) is chosen to achieve the target property balance.
- Atmosphere Control: Heat treatments are performed in vacuum or controlled inert atmospheres to prevent oxidation.
- Machining (Critical Dimensions and Surfaces):
- Objet : To achieve the tight dimensional tolerances and smooth surface finishes required for sealing faces, mating diameters, and other critical features, which cannot typically be met by the as-printed or heat-treated part alone.
- Méthode : Usinage CNC (turning for round seals, milling for features, grinding for very high precision/finish) is used to precisely remove the sacrificial stock material left during the DfAM stage.
- Finition de la surface :
- Objet : To further improve the surface finish beyond machining, enhance wear resistance, or apply specific surface characteristics.
- Méthodes : Polishing (manual or automated), lapping, electropolishing, application of specialized coatings (e.g., wear-resistant or low-friction coatings) if required by the design specification.
- Nettoyage et inspection :
- Objet : Removing any machining fluids, debris, or contaminants, followed by rigorous inspection to ensure the part meets all specifications.
- Méthodes : Ultrasonic cleaning, visual inspection, dimensional inspection (CMM, optical scanning), surface roughness measurement, Non-Destructive Testing (NDT) such as Fluorescent Penetrant Inspection (FPI) to detect surface cracks, and potentially Computed Tomography (CT scanning) or ultrasonic testing to verify internal integrity and density post-HIP.
Importance for Aerospace:
Each of these steps requires careful control, documentation, and validation, especially for heat treatment aerospace alloys and final inspection. Aerospace regulations demand full traceability and process control throughout the entire manufacturing workflow, including all post-processing stages. Partnering with an AM provider like Met3dp, equipped with both advanced printing technology and comprehensive, quality-controlled post-processing capabilities (either in-house or through certified partners), is essential for delivering flight-ready aerospace sealing rings. The integration of these steps is fundamental to realizing the benefits of AM for critical parts production.
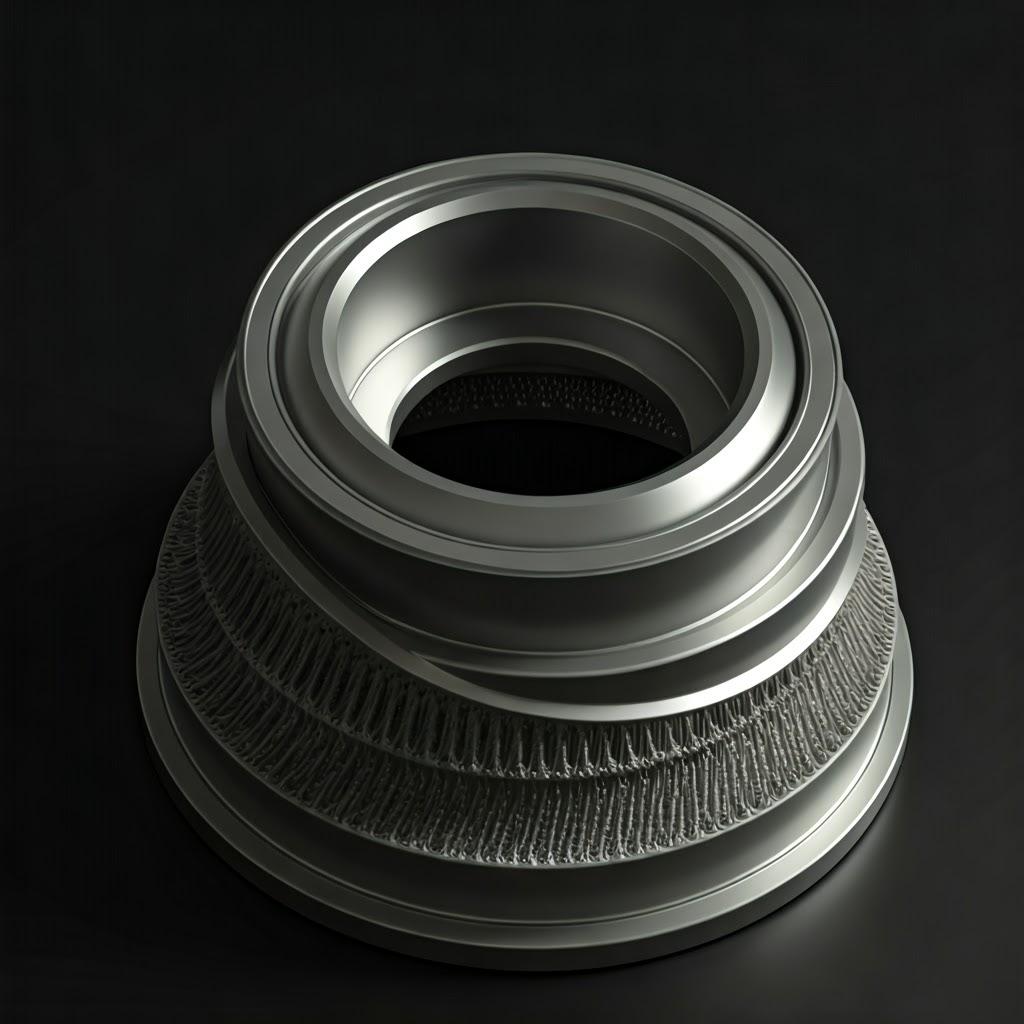
Navigating Common Challenges in 3D Printing Aerospace Seals (and Solutions)
While metal additive manufacturing offers significant advantages for producing aerospace sealing rings, it’s not without its challenges. Understanding these potential hurdles and implementing strategies to mitigate them is crucial for consistent, high-quality production. Many challenges can be addressed through a combination of robust DfAM, optimized process parameters, meticulous post-processing, and collaboration with experienced AM partners.
Défis communs et stratégies d'atténuation :
- Contraintes résiduelles et déformation :
- Défi: The intense localized heating and rapid cooling during PBF induce stresses in the part. If not managed, these stresses can cause the part to warp during the build, detach from supports, or distort after removal from the build plate. Thin-walled or large, flat structures like rings are particularly susceptible.
- Solutions :
- DfAM : Design features to minimize large flat areas parallel to the build plate; use ribs or topology optimization to add stiffness without significant weight increase.
- Structures de soutien optimisées : Strategic placement of supports to anchor the part securely and conduct heat away.
- Optimisation des paramètres du processus : Tuning scan strategies (e.g., island scanning, altering scan vector rotation between layers), beam power, and speed to manage the thermal gradient. Met3dp utilizes advanced process control in its SEBM systems, which often involve higher build chamber temperatures, inherently reducing residual stress compared to some SLM processes.
- Traitement thermique anti-stress : Performing this step before part removal is critical.
- Porosité :
- Défi: Small voids or pores can form within the printed material due to trapped gas (e.g., from powder) or incomplete fusion between layers or scan tracks (Lack of Fusion – LoF). Porosity degrades mechanical properties, particularly fatigue life, and can act as leak paths, unacceptable for seals.
- Solutions :
- Poudre de haute qualité : Using powders with low internal gas porosity, controlled particle size distribution, and good flowability, such as those produced by Met3dp’s advanced atomization techniques. Proper powder handling and storage are also key to prevent moisture absorption.
- Paramètres de processus optimisés : Ensuring sufficient energy density (beam power, speed, hatch spacing) to fully melt the powder and promote good overlap between melt pools, without overheating which can cause keyhole porosity.
- Pressage isostatique à chaud (HIP) : This post-processing step is highly effective at closing internal gas porosity and LoF voids, achieving near-full density essential for aerospace parts.
- Difficultés liées au retrait de la structure de soutien :
- Défi: Supports in complex internal geometries or made from tough materials like IN625 can be very difficult and time-consuming to remove without damaging the part. Incomplete removal can impede function or act as crack initiation sites.
- Solutions :
- DfAM : Prioritize designs that minimize or eliminate the need for internal supports. Design supports for easier access and break-off points.
- Specialized Removal Techniques: Utilize CNC machining, wire EDM, or potentially non-conventional methods like electrochemical machining or abrasive flow machining where appropriate.
- Material Choice (Supports): Some systems allow for different support materials or strategies that are easier to remove, although this is less common in PBF.
- Cracking:
- Défi: Some alloys, particularly certain high-strength Nickel alloys or non-weldable grades, can be susceptible to cracking during printing (solidification cracking) or heat treatment due to thermal stresses or microstructural issues.
- Solutions :
- Sélection des matériaux : Choose alloys known to have good AM processability (IN625 and 17-4PH are generally considered processable with proper control).
- Contrôle des processus : Utilize pre-heating of the build chamber (common in SEBM, reducing thermal gradients), optimize scan strategies, and control cooling rates.
- Post-Weld Heat Treatment Procedures: Carefully developed heat treatment cycles are essential to relieve stress without inducing cracking.
- Surface Finish and Dimensional Accuracy:
- Défi: Achieving the required smooth surfaces and tight tolerances directly from the printer is generally not possible for critical sealing features.
- Solutions :
- Acknowledge Need for Post-Processing: Integrate machining and finishing steps into the production plan from the outset.
- DfAM : Add machining stock strategically.
- Optimisation des processus : Optimize parameters and orientation for the best possible as-printed surface finish on less critical areas to minimize subsequent finishing work.
- Quality Assurance and Consistency:
- Défi: Ensuring that every part produced meets the stringent aerospace requirements, batch after batch. This involves controlling the entire process chain.
- Solutions :
- Système de gestion de la qualité (SGQ) robuste : Implementing systems like AS9100.
- Surveillance des processus : In-situ monitoring of the build process (melt pool monitoring, thermal imaging) can help detect anomalies in real-time.
- Gestion du cycle de vie des poudres : Strict control over powder sourcing, testing, storage, use, and recycling.
- Comprehensive NDT and Metrology: Consistent application of inspection methods to verify part integrity and dimensional accuracy.
Overcoming these metal AM challenges requires a deep understanding of materials science, process physics, and quality control. Success in producing mission-critical components like aerospace sealing rings via AM relies heavily on the expertise and capabilities of the manufacturing partner. Companies like Met3dp, with their focus on advanced SEBM technology, high-quality powder production, and a comprehensive understanding of the entire additive workflow, are well-positioned to help clients navigate these complexities and achieve reliable, high-performance results.
Selecting the Right Metal 3D Printing Service Partner for Aerospace Components
Choosing the right manufacturing partner is always critical, but for aerospace components produced via additive manufacturing, the stakes are exceptionally high. The complexity of the technology, the demanding nature of the materials, and the stringent regulatory requirements necessitate partnering with a metal 3D printing service provider that possesses specialized expertise, robust processes, and the right certifications. Making the wrong choice can lead to project delays, budget overruns, subpar part quality, and even safety risks. For procurement managers and engineers sourcing AM services for parts like sealing rings, here’s a checklist of crucial criteria for evaluating AM suppliers:
- Certification aérospatiale (AS9100) :
- Why it Matters: AS9100 is the internationally recognized Quality Management System (QMS) standard for the aerospace industry. Certification demonstrates a provider’s commitment to quality, traceability, risk management, and continuous improvement, specifically tailored to aerospace requirements. It is often a non-negotiable prerequisite for suppliers manufacturing flight-critical hardware.
- Action: Verify the provider holds a current AS9100 certification (or equivalent, e.g., EN 9100). Inquire about the scope of their certification – does it cover the specific AM processes and materials you require?
- Proven Material Expertise:
- Why it Matters: Successfully printing high-performance aerospace alloys like IN625 and 17-4PH requires deep materials science knowledge and process parameter optimization. The provider should have demonstrable experience processing these specific materials, including understanding their behavior during printing and necessary post-processing like heat treatment and HIP.
- Action: Ask for evidence of experience with IN625, 17-4PH, or other relevant aerospace alloys. Inquire about their material qualification processes, powder handling procedures, and access to material testing facilities. Met3dp, for instance, not only uses but also manufactures high-quality metal powders, giving us intrinsic material expertise AM. Learn more à propos de nous and our integrated approach.
- Advanced Equipment and Technology:
- Why it Matters: The quality and capability of the AM machines directly impact part quality, consistency, and achievable tolerances. Look for providers using industrial-grade equipment from reputable manufacturers, ideally suited for the specific material and application (e.g., SEBM for certain reactive or high-temperature alloys, SLM for others).
- Action: Inquire about the specific printer models used, their maintenance schedules, and calibration procedures. Providers like Met3dp invest in cutting-edge technology, including our own range of SEBM printers known for their reliability and suitability for challenging materials.
- Système de gestion de la qualité (SGQ) robuste :
- Why it Matters: Beyond AS9100, the provider should have comprehensive internal processes for quality control throughout the entire workflow – from powder acceptance testing to final part inspection. This includes process monitoring, non-destructive testing (NDT) capabilities, metrology equipment, and documented procedures.
- Action: Understand their quality control workflow. Ask about their NDT capabilities (FPI, CT scanning, ultrasonics), metrology equipment (CMM, 3D scanners), and how they ensure process repeatability and traceability.
- Ingénierie et soutien du DfAM :
- Why it Matters: The ideal partner acts as more than just a print bureau. They should offer engineering support to help optimize designs for additive manufacturing (DfAM), advise on material selection, and troubleshoot potential manufacturing challenges. This collaborative approach maximizes the benefits of AM.
- Action: Evaluate their engineering team’s experience and willingness to collaborate on design optimization. Do they offer simulation services (thermal, stress)?
- Capacités complètes de post-traitement :
- Why it Matters: As discussed, post-processing is integral for aerospace AM parts. The provider should have established, quality-controlled processes for stress relief, heat treatment (including access to NADCAP-certified HIP if required), support removal, precision machining, and surface finishing, either in-house or through certified partners.
- Action: Verify their post-processing capabilities and quality controls. Understand how they manage the supply chain if external partners are used for steps like HIP or specialized machining.
- Capacité, évolutivité et fiabilité des délais :
- Why it Matters: Ensure the provider has the capacity to meet your volume requirements (from prototypes to potential series production) and a track record of delivering on time. Unreliable lead times can severely disrupt aerospace development and production schedules.
- Action: Discuss their current capacity, typical lead times for similar projects, and how they manage production scheduling. Ask for references or case studies demonstrating their ability to scale.
- Supply Chain Security and IP Protection:
- Why it Matters: Aerospace projects often involve sensitive intellectual property (IP) and require secure supply chains.
- Action: Inquire about their data security measures, NDAs, and procedures for protecting client IP. Understand their material sourcing practices and supply chain resilience.
Table: Key Supplier Evaluation Criteria
Criterion | Importance | Que rechercher | Met3dp Alignment |
---|---|---|---|
Certification AS9100 | Mandatory (Often) | Current certificate, relevant scope | Committed to highest industry standards (Inquire for current status) |
Material Expertise (IN625/17-4PH) | Critique | Proven experience, qualification data, powder control | Deep expertise as powder manufacturer & AM system provider |
Equipment & Technology | Haut | Industrial-grade PBF (SLM/SEBM), proper maintenance | Advanced SEBM printers, ongoing R&D |
Robust QMS | Critique | Traceability, process control, NDT, metrology | Comprehensive quality procedures embedded |
Engineering/DfAM Support | Haut | Collaborative approach, simulation capability | Experienced engineering team available for consultation |
Post-Processing Network | Critique | Controlled processes (Heat Treat, HIP, Machining) | Integrated approach with trusted partners for specialized needs |
Capacity & Reliability | Haut | Ability to meet volume/timeline, proven track record | Scalable solutions, focus on reliable delivery |
Security & IP Protection | Haut | Secure data handling, NDAs, trusted supply chain | Strong commitment to client confidentiality and data security |
Exporter vers les feuilles
Choisir le bon fournisseur de fabrication additive aérospatiale is a strategic decision. Thorough vetting against these criteria will help ensure a successful partnership and the reliable production of high-quality, flight-worthy sealing rings.
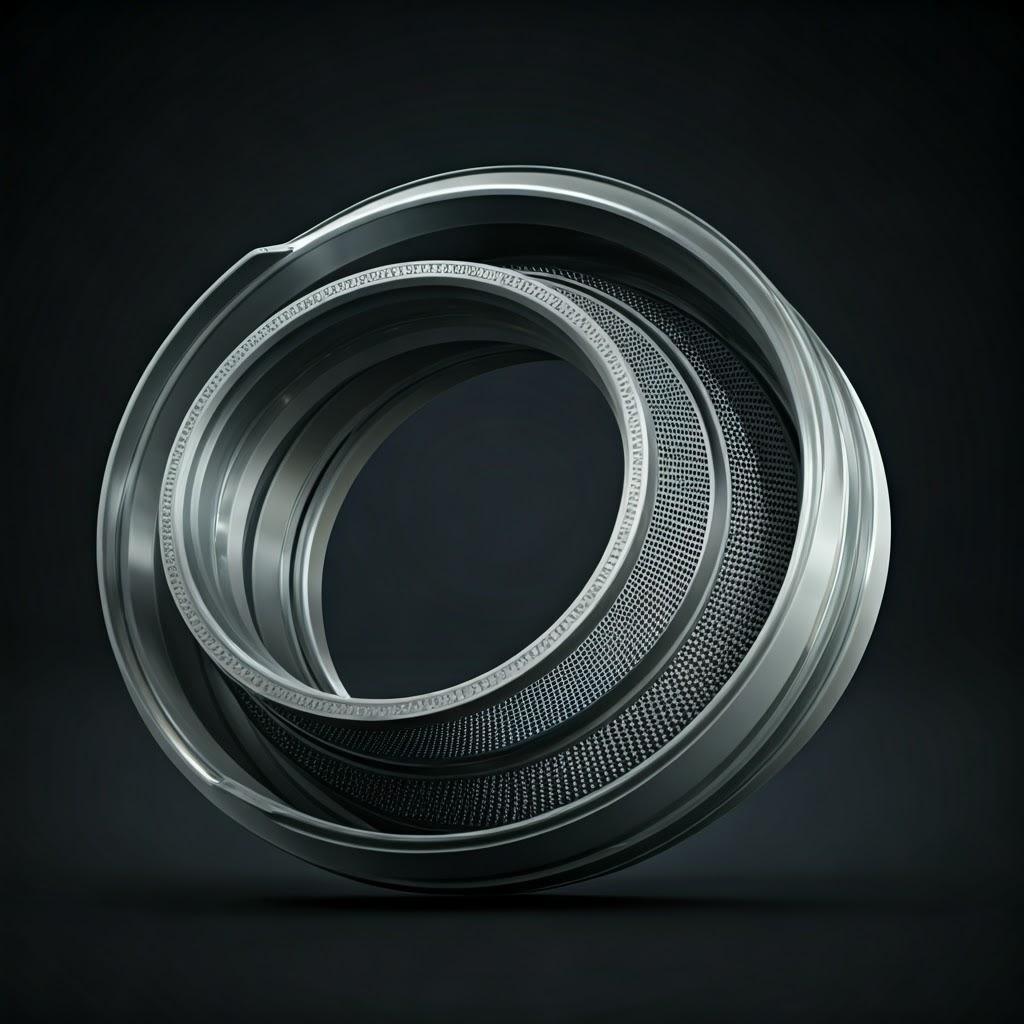
Understanding Cost Drivers and Lead Times for AM Sealing Rings
One of the key considerations for engineers and procurement managers evaluating additive manufacturing is understanding the associated costs and expected timelines. While AM offers significant advantages in speed for prototyping and design freedom, the metal 3D printing cost analysis and lead time estimation require understanding several influencing factors. Pricing isn’t just about the material volume; it’s a complex interplay of process parameters, part complexity, and post-processing requirements.
Key Cost Drivers for AM Sealing Rings:
- Material Type and Consumption:
- Alloy Choice: High-performance aerospace alloys like IN625 are significantly more expensive than materials like 17-4PH stainless steel or tool steels. The raw powder cost is a major factor.
- Part Volume & Weight: The actual amount of material used to print the part directly impacts cost.
- Structures de soutien : Material used for supports adds to consumption and cost. Efficient DfAM aims to minimize this.
- Powder Recycling/Waste: While much unused powder can be recycled, there are limits and associated costs for testing and requalification.
- Part Complexity and Size:
- Geometric Complexity: Highly intricate designs may require more complex support structures, potentially longer print times due to intricate scanning paths, and more challenging post-processing (support removal, finishing).
- Taille de la pièce : Larger parts occupy more space on the build plate, consume more material, and require longer print times.
- Print Time (Machine Utilization):
- Build Height: The primary driver of print time is the number of layers (part height). Taller parts take longer.
- Build Volume Occupation: How many parts can be nested efficiently onto a single build plate affects machine utilization cost per part. Printing multiple copies simultaneously is generally more cost-effective per piece than printing singles.
- Stratégie et paramètres de numérisation : Optimized parameters balance speed and quality, influencing overall print duration.
- Post-Processing Intensity:
- Traitement thermique : Standard stress relief is routine, but required cycles like HIP add significant cost due to specialized equipment and longer processing times. Specific aging cycles for 17-4PH also add time and cost.
- Suppression du support : Complex or internal supports require more manual labor or specialized machining, increasing cost.
- Machining Requirements: The extent of precision machining needed for tolerances and surface finish is a major cost factor. More surfaces requiring tight tolerances mean higher machining costs.
- Finition de la surface : Polishing, coating, or other surface treatments add costs based on the level required.
- Assurance qualité et inspection :
- Level of NDT: Basic visual and dimensional checks are standard. More rigorous NDT (FPI, CT scanning, ultrasonic testing) required for critical aerospace components adds significant cost.
- Documentation : Comprehensive documentation packages required for aerospace traceability add administrative overhead.
- Volume de commande :
- Prototyping vs. Production: One-off prototypes typically have a higher per-part cost due to setup and programming overhead.
- Remises sur volume : For larger batch sizes or devis en gros pour l'impression 3D, per-part costs generally decrease due to efficiencies in build nesting, setup amortization, and potential automation in post-processing.
Délais d'exécution typiques :
Aerospace component lead time using AM can be significantly shorter than traditional methods, especially for prototypes and complex parts, but it’s not instantaneous.
- Prototypage : For a typical sealing ring prototype (depending on size, complexity, material):
- Design Review & Print Prep: 1 à 3 jours
- Impression : 1-5 days (highly dependent on height and quantity)
- Basic Post-Processing (Stress Relief, Removal, Basic Finish): 2 à 5 jours
- Total Prototype Lead Time: Often ranges from 1 à 3 semaines.
- Production Orders (Low-to-Medium Volume):
- Includes full heat treatment (HIP), extensive machining, rigorous NDT, and documentation.
- Total Production Lead Time: Can range from 4 to 10 weeks or more, depending heavily on quantity, complexity, post-processing requirements, and supplier capacity.
Facteurs influençant les délais :
- Supplier backlog and machine availability.
- Complexity of DfAM review and optimization.
- Print time (build height, nesting efficiency).
- Scheduling of specialized post-processing (especially HIP, which often involves batching).
- Complexity of machining and finishing operations.
- Rigor of the QA inspection process.
Obtaining accurate cost and lead time estimates requires submitting a detailed RFQ (Request for Quote) including 3D CAD models, material specifications, tolerance requirements, post-processing needs, required certifications, and desired quantity. Met3dp offers a range of advanced printers and high-quality powders, showcased on our produit page, enabling efficient production. We work closely with clients to provide realistic quotes and optimize the manufacturing plan for cost-effectiveness and timely delivery.
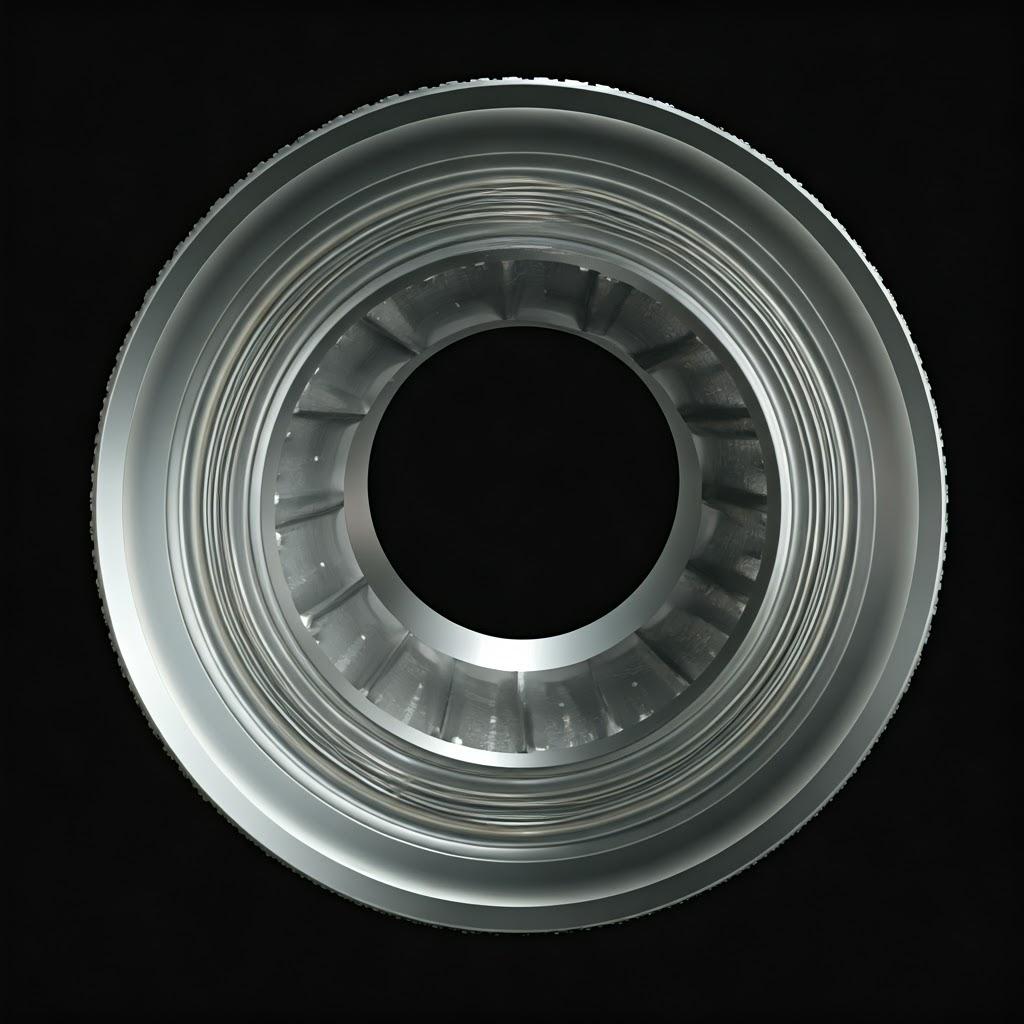
Frequently Asked Questions (FAQ) about 3D Printed Aerospace Sealing Rings
As metal additive manufacturing becomes more prevalent in aerospace, engineers and procurement managers often have specific questions about its application for components like sealing rings. Here are answers to some common inquiries:
- Can 3D printed sealing rings meet stringent aerospace certification requirements?
- Répondre: Yes, absolutely. Achieving certification for 3D printed seal certification relies on demonstrating a stable, repeatable, and controlled manufacturing process coupled with rigorous testing and validation. This involves:
- Qualification des matériaux : Using aerospace-grade powders (like IN625 or 17-4PH from qualified sources like Met3dp) with certified chemistry and properties.
- Contrôle des processus : Utilizing qualified AM machines with locked-down, validated process parameters.
- Post-Processing Validation: Ensuring heat treatments (like HIP) and machining are performed according to certified procedures (e.g., NADCAP for special processes).
- Rigorous Testing: Performing extensive mechanical testing (tensile, fatigue, creep), NDT, and dimensional inspection on witness coupons and final parts to verify they meet or exceed the design specifications and relevant aerospace standards (e.g., SAE AMS specs).
- Quality Management System: Operating under an AS9100 certified QMS ensures traceability and process adherence.
- While qualification requires significant effort and investment, many 3D printed metal parts are already flying in critical aerospace applications, proving its viability.
- Répondre: Yes, absolutely. Achieving certification for 3D printed seal certification relies on demonstrating a stable, repeatable, and controlled manufacturing process coupled with rigorous testing and validation. This involves:
- How does the cost of AM sealing rings compare to traditionally manufactured ones?
- Répondre: Le cost of 3D printed aerospace parts compared to traditional methods (machining, casting) is nuanced and depends heavily on several factors:
- La complexité : For highly complex geometries that are difficult or impossible to machine/cast, AM can be significantly cheaper, even at low volumes, by avoiding complex tooling or multi-axis machining setups.
- Volume : For very simple geometries produced in high volumes, traditional methods like stamping or high-speed machining may still be more cost-effective per part. However, AM’s cost curve is flattening, making it competitive for increasingly larger batch sizes of moderately complex parts.
- Matériau : For expensive materials like IN625, AM’s better material utilization (buy-to-fly ratio) compared to machining can lead to substantial raw material cost savings.
- Lead Time Value: If speed-to-market or rapid prototyping is critical, the value derived from AM’s shorter lead times can outweigh a potentially higher per-part cost.
- Performance Benefits: If AM enables a lighter or better-performing seal (e.g., through topology optimization or integrated cooling), the total cost of ownership (considering fuel savings or improved engine life) might favor the AM part even if its initial production cost is higher.
- General Guideline: AM excels in cost-effectiveness for complex, low-to-medium volume parts, parts made from expensive/difficult-to-machine alloys, and situations where rapid iteration or lead time is critical. A direct cost comparison should always be made based on specific part geometry, material, and volume requirements.
- Répondre: Le cost of 3D printed aerospace parts compared to traditional methods (machining, casting) is nuanced and depends heavily on several factors:
- What are the typical lead times for prototype and production orders of 3D printed seals?
- Répondre: As outlined previously:
- Prototypes : Typically range from 1 à 3 semaines. This speed allows for rapid design iteration and functional testing early in the development cycle.
- Production Orders: Lead times are longer due to the inclusion of full heat treatment cycles (like HIP), extensive precision machining, rigorous NDT, and comprehensive documentation packages required for aerospace certification. Typical lead times can range from 4 to 10 weeks or more, depending on the order quantity, part complexity, specific post-processing required, and the supplier’s capacity.
- While production lead times are longer than prototype lead times, they are often still competitive with or faster than traditional manufacturing routes involving casting tooling creation or complex forging and machining sequences, especially for low-to-medium volumes.
- Répondre: As outlined previously:
- How is material traceability ensured for 3D printed aerospace parts?
- Répondre: Material traceability is fundamental in aerospace and is rigorously maintained in AM through:
- Powder Batch Tracking: Each batch of metal powder received from a qualified supplier (like Met3dp) comes with a unique certificate of analysis detailing its chemistry and physical properties. This batch number is tracked throughout its lifecycle.
- Build Job Documentation: Each print job logs which powder batch(es) were used, the specific parts printed, machine parameters employed, and operator details.
- Part Serialization: Each individual aerospace part is typically assigned a unique serial number, often marked directly on the part (e.g., via laser engraving).
- Linked Records: The QMS links the part serial number back to the specific build job, the powder batch used, machine logs, post-processing records (heat treatment charts, machining reports), and NDT results.
- This comprehensive tracking, mandated by standards like AS9100, ensures full “cradle-to-grave” traceability for every critical component.
- Répondre: Material traceability is fundamental in aerospace and is rigorously maintained in AM through:
Ces AM aerospace FAQs highlight some key considerations for adopting this technology. Partnering with a knowledgeable provider like Met3dp ensures these aspects are managed effectively, providing confidence in the quality and reliability of 3D printed aerospace components.
Conclusion: The Future of Aerospace Sealing is Additive
The demanding environment within aerospace engines requires sealing solutions that push the boundaries of material science and manufacturing capability. Aerospace sealing rings, though often small, are critical components where failure is not an option. While traditional manufacturing methods have served the industry well, metal additive manufacturing represents a significant leap forward, offering unparalleled advantages in design freedom, material utilization, lead time reduction, and the potential for enhanced performance.
As we’ve explored, metal AM enables the creation of sealing rings with optimized geometries, tailored cross-sections, and potentially integrated features like cooling channels, which are difficult or impossible to achieve conventionally. The ability to work effectively with high-performance materials like IN625 et Acier inoxydable 17-4PH, overcoming traditional machinability challenges and reducing waste, makes AM particularly suitable for these demanding applications. Furthermore, the technology accelerates development cycles through rapid prototyping and offers a pathway to more agile and resilient supply chains via on-demand production and digital inventories.
However, realizing these benefits requires navigating the intricacies of DfAM, understanding achievable precision, implementing rigorous post-processing steps (especially heat treatment like HIP and precision machining), and overcoming potential challenges like residual stress and porosity. Success hinges on meticulous process control, deep material expertise, and robust quality assurance – all hallmarks of a competent fournisseur de fabrication additive aérospatiale.
Le future of aerospace manufacturing is undeniably intertwined with additive technologies. For components like sealing rings, AM is not just a novelty but a viable, competitive, and often superior production method capable of meeting the stringent requirements of the industry.
Met3dp stands ready to partner with aerospace engineers and procurement managers looking to leverage the power of metal AM. As a company providing comprehensive Solutions aérospatiales Met3dp, encompassing our own advanced SEBM printers, high-quality gas atomized and PREP metal powders, and extensive application expertise, we offer an integrated approach to producing critical components. We are committed to quality, innovation, and collaboration, helping our clients navigate the complexities of AM and achieve success in producing next-generation sealing rings and other vital aerospace parts.
Ready to explore how metal 3D printing can revolutionize your aerospace sealing applications? Contactez Met3dp aujourd'hui to discuss your project requirements with our expert team and discover how our capabilities can power your organization’s additive manufacturing goals.
Partager sur
MET3DP Technology Co. est un fournisseur de premier plan de solutions de fabrication additive dont le siège se trouve à Qingdao, en Chine. Notre société est spécialisée dans les équipements d'impression 3D et les poudres métalliques de haute performance pour les applications industrielles.
Articles connexes
À propos de Met3DP
Mise à jour récente
Notre produit
CONTACTEZ-NOUS
Vous avez des questions ? Envoyez-nous un message dès maintenant ! Nous répondrons à votre demande avec toute une équipe dès réception de votre message.
Obtenir les informations de Metal3DP
Brochure du produit
Obtenir les derniers produits et la liste des prix
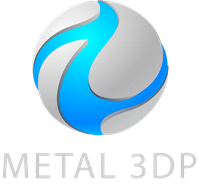
Poudres métalliques pour l'impression 3D et la fabrication additive