3D Printing Missile Nose Cones with Titanium Alloys
Table des matières
Introduction: The Critical Role of Missile Nose Cones and Additive Manufacturing
In the demanding world of aerospace and defense, components are pushed to the absolute limits of material science and engineering design. Among the most critical of these components is the missile nose cone. Far from being a simple aerodynamic fairing, the nose cone is a sophisticated piece of technology that dictates a missile’s trajectory, protects sensitive internal guidance systems, and must withstand the brutal conditions of high-speed, and potentially hypersonic, flight. Its performance is intrinsically linked to the overall mission success, whether for tactical engagement, strategic deterrence, or space exploration applications. The geometry must be meticulously crafted for optimal aerodynamic efficiency, minimizing drag and ensuring stable flight characteristics across a wide range of speeds and altitudes. Simultaneously, it must possess exceptional structural integrity to endure immense aerodynamic pressures, vibration, and potentially severe thermal loads generated by air friction at supersonic and hypersonic velocities. The materials used must offer a unique combination of strength, stiffness, low density, and often, thermal resistance or specific electromagnetic properties.
Traditionally, manufacturing these complex components involved subtractive methods like multi-axis CNC machining from solid billets or forgings, or sometimes complex fabrication and joining techniques. While effective, these methods often entail significant material waste, long lead times, design constraints imposed by the manufacturing process itself, and high costs, especially for complex geometries or low-volume production runs common in the defense sector. The quest for enhanced performance – higher speeds, greater maneuverability, improved payload capacity – constantly drives engineers to seek lighter, stronger, and more complex designs, often pushing traditional manufacturing to its limits.
Entrer la fabrication additive métallique (AM), commonly known as metal Impression 3D. This transformative technology is rapidly reshaping the landscape of fabrication additive aérospatiale et defense manufacturing. Instead of removing material, AM builds parts layer by layer directly from digital designs, typically using high-energy sources like lasers or electron beams to fuse fine metal powders. This fundamental shift opens up unprecedented possibilities for designing and producing missile nose cones and other critical composants de missiles. AM allows for the creation of highly complex internal and external geometries that are difficult or impossible to achieve through traditional means. This includes features like optimized internal lattice structures for weight reduction without compromising strength, conformal cooling channels for thermal management in hypersonic applications, or integrated mounting points and sensor housings, reducing part count and assembly complexity.
Furthermore, metal AM excels with matériaux avancés like the high-strength alliages de titane (e.g., Ti-6Al-4V) and nickel-based superalloys (e.g., IN718) that are essential for meeting the extreme demands of high-speed flight. These materials are often difficult and expensive to machine conventionally due to their toughness and poor thermal conductivity. AM processes, particularly powder bed fusion techniques, can handle these materials effectively, enabling the production of near-net-shape parts that require less finish machining, thereby conserving expensive material and reducing lead times. Companies specializing in advanced additive manufacturing, such as Met3dp, are at the forefront, providing not only the sophisticated printing equipment but also the high-quality, process-optimized metal powders essential for producing reliable, mission-critical aerospace components. Their expertise in powder metallurgy and printing processes ensures that the resulting parts meet the stringent quality and performance standards demanded by the aerospace and defense industries. The ability to rapidly iterate designs, produce parts on-demand, and potentially even manufacture components closer to the point of need offers significant strategic advantages in terms of supply chain agility and responsiveness, crucial factors in the fast-paced defense sector. As we delve deeper into the specifics of 3D printing missile nose cones, it becomes clear that AM is not just an alternative manufacturing method; it is an enabling technology unlocking new levels of performance and design freedom.
Applications and Demands: Where are 3D Printed Nose Cones Utilized?
The adoption of metal additive manufacturing for missile nose cones spans a diverse range of systèmes de missiles and aerospace vehicles, driven by the unique performance requirements of each application. The demanding operational environments these components face necessitate the advanced materials and design freedoms offered by 3D printing. Procurement managers and aerospace engineers involved in defense procurement et component sourcing are increasingly turning to AM to meet challenges that traditional manufacturing struggles to address efficiently or cost-effectively.
Here’s a breakdown of key application areas and the associated demands:
- Tactical Missiles:
- Exemples : Air-to-air, surface-to-air, anti-tank missiles.
- Demands: These missiles often require high maneuverability, necessitating aerodynamically efficient nose cone designs that minimize drag across various flight regimes. They experience significant G-forces during launch and terminal guidance phases. While thermal loads might be less extreme than hypersonic systems, structural integrity, durability against environmental factors (rain, dust erosion), and sometimes specific radar transparency or signature management characteristics are critical. Cost-effectiveness for potentially higher volume production runs is also a key consideration.
- Avantage AM : Ability to create complex, optimized aerodynamic shapes. Potential for part consolidation (integrating sensor windows or mounting features). Use of durable materials like Ti-6Al-4V offers excellent strength-to-weight. Rapid prototyping allows for quick testing of new aerodynamic profiles.
- Strategic Missiles:
- Exemples : Ballistic missiles (ICBMs, SLBMs).
- Demands: These systems involve extremely high speeds during atmospheric re-entry (for re-entry vehicles often housed within the nose shroud initially) or ascent. Nose cones (or shrouds) must withstand immense aerodynamic forces and, in the case of re-entry vehicles, extreme thermal loads (thousands of degrees Celsius). Precision in manufacturing is paramount for predictable trajectory and targeting accuracy. Weight is always a critical factor, directly impacting range and payload capacity.
- Avantage AM : Enables the use of high-temperature materials like nickel superalloys (IN718) or potentially ceramic matrix composites (via indirect AM routes) or refractory metals for thermal protection. Complex internal structures or cooling channel designs, manufacturable via AM, can aid thermal management. Weight reduction through topology optimization is highly valuable.
- Cruise Missiles:
- Exemples : Long-range subsonic or supersonic land-attack and anti-ship missiles.
- Demands: These missiles fly within the atmosphere for extended durations, often at low altitudes. Nose cones need excellent aerodynamic efficiency for range, structural integrity to withstand sustained flight loads and potential environmental hazards (bird strikes, weather), and potentially incorporate seekers or sensors requiring specific material properties (e.g., radomes). Stealth characteristics (low observable shaping and materials) are often crucial.
- Avantage AM : Facilitates complex, low-observable external geometries. Allows integration of internal structures for sensors and guidance systems. Enables optimization for weight and fuel efficiency, extending range. Materials like Ti-6Al-4V provide a good balance of properties.
- Hypersonic Vehicles:
- Exemples : Hypersonic glide vehicles (HGVs), hypersonic cruise missiles.
- Demands: This is arguably the most demanding application. Operating at speeds exceeding Mach 5, the nose cone (or leading edges) faces extreme aerodynamic heating (potentially reaching plasma temperatures), intense pressures, and requires exceptional geometric precision to maintain stability and control. Materials must possess ultra-high temperature resistance, high strength at temperature, and thermal shock resistance.
- Avantage AM : Metal AM, particularly using materials like IN718 or other advanced superalloys offered by specialist powder suppliers, provides a pathway to manufacture components capable of surviving these conditions. The ability to integrate complex conformal cooling channels directly into the nose cone structure is a game-changer for thermal management, something extremely difficult or impossible with traditional methods. AM allows for rapid iteration of designs needed for this cutting-edge research and development field.
- Sounding Rockets and Research Vehicles:
- Exemples : Vehicles used for atmospheric research, technology demonstrators.
- Demands: Often require custom, low-volume nose cone designs tailored for specific instrumentation payloads and flight profiles. Need to withstand high acceleration and aerodynamic forces during ascent. Cost-effective prototyping and manufacturing are beneficial.
- Avantage AM : Ideal for producing one-off or small batches of complex, customized nose cones quickly and affordably compared to tooling up for traditional manufacturing. Facilitates easy integration of custom sensor ports and mounting features.
Cross-Cutting Demands:
Across all these applications, certain demands are common:
- High Reliability: Failure is not an option in mission-critical defense systems. Parts must meet stringent quality control and validation standards.
- Précision : Aerodynamic performance and sensor integration require tight dimensional tolerances.
- Weight Optimization: Reducing weight improves range, maneuverability, payload capacity, and fuel efficiency.
- Performance des matériaux : Selecting the right material with the required strength, temperature resistance, and other specific properties is crucial.
- Résilience de la chaîne d'approvisionnement : The ability to produce parts on-demand, potentially reducing reliance on complex global supply chains, is strategically important for defense procurement.
Ingénierie aérospatiale teams are leveraging metal 3D printing not just as a replacement technology but as a tool to fundamentally rethink component design. The ability to create shapes driven by performance requirements rather than manufacturing constraints allows for significant leaps in capability, particularly crucial for next-generation systèmes de missiles et véhicules hypersoniques. Partnering with knowledgeable AM service providers and high-quality fournisseurs de poudres métalliques is essential to successfully harness the potential of this technology for these demanding applications.
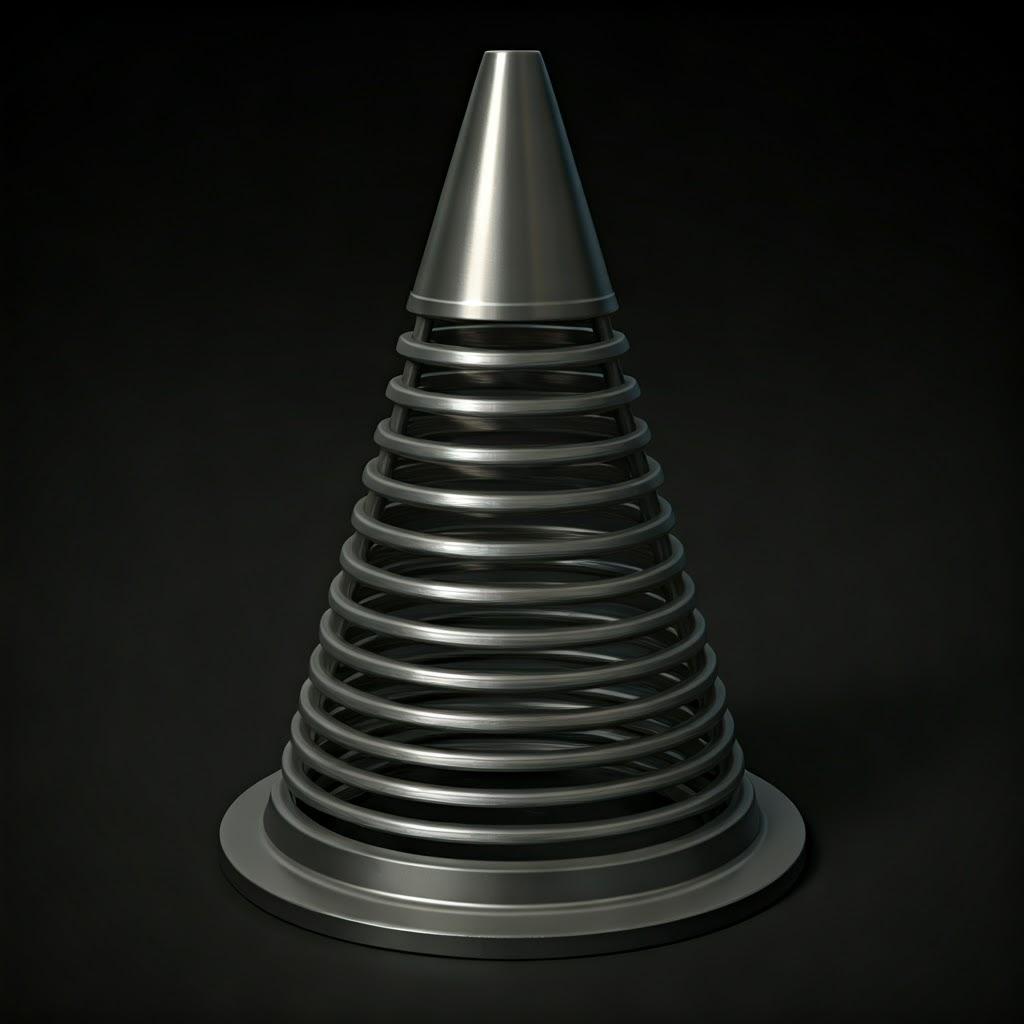
Why Metal 3D Printing for Missile Nose Cones? Unlocking Performance Advantages
The decision to employ impression 3D de métaux for manufacturing missile nose cones stems from a compelling set of advantages that directly address the limitations of traditional vs additive manufacturing methods like machining, forging, or casting, particularly when dealing with the complex requirements of aerospace and defense components. These benefits translate into tangible improvements in performance, development speed, and supply chain efficiency.
1. Unparalleled Design Freedom and Complexity:
- Traditional Limitations: Machining is constrained by tool access, limiting internal features and geometric complexity. Forging requires expensive dies and produces near-net shapes that still need extensive machining, especially for intricate details. Casting can produce complex shapes but often suffers from lower material properties, potential porosity, and may not be suitable for high-performance alloys like Ti-6Al-4V without extensive post-processing like Hot Isostatic Pressing (HIP).
- Avantage AM : Additive manufacturing builds parts layer-by-layer, freeing designers from many traditional constraints. This allows for:
- Highly Optimized Aerodynamic Shapes: Creating complex curves, variable profiles, and sharp leading edges precisely tailored for minimum drag and optimal airflow across different speed regimes (subsonic, supersonic, hypersonic).
- Internal Features: Incorporating internal lattice or honeycomb structures significantly reduces weight while maintaining structural integrity (réduction du poids). Conformal cooling channels can be integrated directly into the structure for thermal management in high-heat applications (hypersonics) – a feat nearly impossible with machining.
- Consolidation partielle : Integrating brackets, mounting points, sensor housings, or even small subsystems directly into the nose cone design reduces the number of individual parts, fasteners, and assembly steps. This simplifies logistics, lowers weight, improves reliability by eliminating joints/interfaces, and streamlines supply chain optimization.
2. Material Efficiency and Reduced Waste:
- Traditional Limitations: Subtractive manufacturing, especially CNC machining from billet, can be extremely wasteful. For expensive aerospace materials like titanium alloys or nickel superalloys, generating large amounts of chips (swarf) represents a significant cost. Forging reduces waste compared to machining billet but still requires significant material removal in finishing stages.
- Avantage AM : AM processes like Laser Powder Bed Fusion (L-PBF) or Selective Electron Beam Melting (SEBM) use only the material necessary to build the part and its supports. Unfused powder can typically be recycled and reused in subsequent builds (with proper quality control), leading to much higher material utilization rates (often >90%). This is a major cost benefit when working with high-value aerospace grade titanium or superalloys sourced from specialized Ti-6Al-4V powder suppliers ou IN718 additive manufacturing specialists.
3. Accelerated Development and Rapid Prototyping:
- Traditional Limitations: Creating tooling (dies for forging, molds for casting) or complex multi-axis machining setups is time-consuming and expensive. Design iterations require significant lead time and cost penalties.
- Avantage AM : AM operates directly from digital CAD files, eliminating the need for part-specific tooling. This enables:
- Prototypage rapide : Engineers can design, print, and test multiple nose cone iterations (e.g., different aerodynamic profiles, internal structures) in a matter of days or weeks, rather than months. This accelerates the development cycle dramatically, allowing for faster validation and refinement.
- Production à la demande : Small batches or even single custom parts can be produced economically without the overhead of traditional tooling setup, ideal for research, development, testing, and evaluation (RDT&E) phases or for producing spares for legacy systems.
4. Enhanced Performance Through Material Capabilities:
- Traditional Limitations: Some advanced alloys preferred for their high strength-to-weight ratio or high-temperature performance (like Ti-6Al-4V and IN718) are notoriously difficult to machine due to their toughness, low thermal conductivity, and work-hardening tendencies. This drives up machining time and cost.
- Avantage AM : Powder bed fusion processes are well-suited for these ‘difficult-to-machine’ materials. While challenges exist within AM itself (e.g., residual stress), the fundamental process of melting and solidification layer by layer is often more manageable than bulk machining for complex geometries in these alloys. Furthermore, AM opens the door to potentially using novel alloy compositions or functionally graded materials (varying material properties within a single part), although this is still an area of active research and development. Companies like Met3dp, with their deep expertise in both advanced metal powders and printing processes like SEBM, can achieve high-density, high-quality parts with mechanical properties comparable, and sometimes superior (in certain aspects like fatigue life due to finer microstructures), to wrought materials after appropriate post-processing.
5. Supply Chain Agility and Resilience:
- Traditional Limitations: Complex aerospace components often rely on specialized suppliers and multi-step manufacturing processes, leading to potentially long and fragile supply chains. Minimum order quantities for forged or cast parts can be prohibitive for low-volume needs.
- Avantage AM : Digital manufacturing enables distributed production. Nose cone designs can be digitally transmitted and printed closer to the point of assembly or need, potentially reducing transportation costs and lead times. The ability to produce parts on-demand mitigates risks associated with supply chain disruptions and reduces the need for large inventories of spares. This aligns well with modern defense procurement strategies focused on agility and responsiveness.
Table: AM vs. Traditional Manufacturing for Missile Nose Cones
Fonctionnalité | Fabrication additive métallique (AM) | Traditional Manufacturing (Machining/Forging/Casting) | Advantage of AM |
---|---|---|---|
Complexité de la conception | High (Complex internal/external features, lattices, channels) | Moderate to Low (Tool access, draft angles limit) | Enables optimized designs, part consolidation, integrated features (cooling) |
Déchets matériels | Low (Powder recycling) | High (Machining) or Moderate (Forging/Casting) | Significant cost savings, especially with expensive aerospace alloys |
Lead Time (Proto) | Short (Days/Weeks) | Long (Weeks/Months – tooling/setup) | Faster design iteration, accelerates development (Prototypage rapide) |
Coût de l'outillage | None (Direct digital manufacturing) | High (Dies, molds, complex fixtures) | Economical for low volumes, prototypes, custom parts |
Réduction du poids | High potential (Topology optimization, internal lattices) | Limited (Primarily by material choice/machining) | Improved missile performance (range, maneuverability) |
Consolidation partielle | High potential (Integrating multiple functions/parts) | Low potential | Reduced assembly time/cost, increased reliability, lighter weight |
Options de matériaux | Excellent for Ti-6Al-4V, IN718, other difficult-to-machine alloys | Can process most materials, but challenges exist | Efficient processing of high-performance alloys essential for nose cones |
Chaîne d'approvisionnement | Agile, distributed potential, on-demand | More rigid, longer lead times, MOQ issues | Improved responsiveness, reduced inventory, enhanced Optimisation de la chaîne d'approvisionnement |
Exporter vers les feuilles
In summary, the compelling additive manufacturing benefits – design freedom, material efficiency, speed, ability to process high-performance materials effectively, and enhanced supply chain flexibility – make metal 3D printing an increasingly indispensable tool for developing and manufacturing next-generation missile nose cones.
Material Focus: Ti-6Al-4V and IN718 for Extreme Environments
The selection of materials for a missile nose cone is paramount, dictated by the extreme aerodynamic forces, high temperatures, structural loads, and specific functional requirements encountered during flight. Among the workhorse materials enabling the use of additive manufacturing in this demanding application, two stand out: Titanium alloy Ti-6Al-4V and Nickel-based superalloy IN718. Both are readily processable via metal AM techniques like Laser Powder Bed Fusion (L-PBF) and Selective Electron Beam Melting (SEBM), and their properties make them suitable, albeit for slightly different operational envelopes. Sourcing high-quality, AM-optimized powders from reputable suppliers is critical for achieving the desired material properties and ensuring part reliability.
Titanium Alloy Ti-6Al-4V (Grade 5): The Aerospace Benchmark
Ti-6Al-4V is arguably the most widely used titanium alloy, particularly in the aerospace industry, and for good reason. It offers an exceptional combination of properties that make it highly attractive for missile nose cones operating in subsonic, supersonic, and potentially lower-end hypersonic regimes.
- Key Properties & Benefits:
- Rapport résistance/poids élevé : This is perhaps its most significant advantage. Titanium is roughly 40% lighter than steel but can achieve comparable strength levels, especially after appropriate heat treatment. This directly translates to lighter missiles, enabling greater range, payload capacity, or maneuverability.
- Excellente résistance à la corrosion : Ti-6Al-4V exhibits outstanding resistance to corrosion in various environments, including saltwater and industrial atmospheres, ensuring durability and longevity.
- Bonne résistance à la fatigue : Critical for components subjected to cyclic loading and vibrations during flight.
- Moderate High-Temperature Capability: It retains good strength up to approximately 315°C (600°F), making it suitable for many supersonic applications. However, its strength begins to decrease significantly at higher temperatures.
- Biocompatibilité : While not relevant for nose cones, this property highlights its inert nature.
- Weldability/Processability: It is readily weldable and can be effectively processed using AM techniques.
- AM Considerations for Ti-6Al-4V:
- Qualité de la poudre : Achieving optimal mechanical properties in AM parts requires high-quality powder with specific characteristics: high sphericity for good flowability and packing density, controlled particle size distribution (PSD), low oxygen and nitrogen content (interstitials can embrittle titanium), and high purity. Reputable Ti-6Al-4V powder suppliers, such as Met3dp which utilizes advanced gas atomization techniques, focus on producing powders meeting these stringent metal powder specifications. Met3dp’s commitment to quality control ensures consistency and reliability batch after batch, crucial for mission-critical aerospace grade titanium des composants.
- Paramètres du processus : Careful optimization of laser/electron beam power, scan speed, layer thickness, and build chamber atmosphere (argon or vacuum) is necessary to achieve fully dense parts with fine microstructures and minimize defects like porosity or lack of fusion.
- Microstructure : As-built AM Ti-6Al-4V typically exhibits fine acicular α’ martensitic structures due to rapid cooling rates. Post-processing heat treatments (like stress relief, annealing, or solution treatment and aging – STA) are essential to transform this microstructure into the desired α+β structure, optimizing strength, ductility, and fatigue life.
- Contrainte résiduelle : Due to large thermal gradients during printing, residual stress can be significant and requires management through optimized scan strategies and mandatory stress relief heat treatments.
Nickel-Based Superalloy IN718: The High-Temperature Champion
When operational temperatures exceed the capabilities of titanium alloys, particularly in hypersonic applications or components near hot engine exhausts, Nickel-based superalloys like Inconel 718 (IN718) become the material of choice.
- Key Properties & Benefits:
- Excellent High-Temperature Strength: IN718 maintains remarkable tensile, creep, and rupture strength at temperatures up to 700°C (1300°F) and retains useful properties even higher. This is due to its precipitation-strengthened austenitic nickel-chromium matrix.
- Good Corrosion and Oxidation Resistance: Performs well in harsh, corrosive, and oxidizing environments encountered at high temperatures.
- High Fatigue Strength: Retains strength under cyclic loading, even at elevated temperatures.
- Good Weldability (for a Superalloy): Compared to some other complex superalloys, IN718 exhibits relatively good weldability, which translates favorably to AM processability.
- AM Considerations for IN718:
- Qualité de la poudre : Similar to Ti-6Al-4V, high-purity, spherical IN718 powder with controlled PSD and low interstitial content is crucial for successful IN718 additive manufacturing. Suppliers specializing in matériaux à haute température for AM understand these requirements.
- Défis liés au processus : IN718 is susceptible to solidification cracking (hot cracking) during welding and AM due to the segregation of certain elements (like Niobium) during rapid solidification. Careful control over process parameters, potentially using specialized scan strategies or machine pre-heating, is needed to mitigate this.
- Traitement thermique : Extensive post-processing heat treatments are mandatory for IN718 to achieve its optimal properties. This typically involves solution annealing followed by a two-step precipitation hardening (aging) treatment to develop the strengthening γ’ and γ” phases. Hot Isostatic Pressing (HIP) is also commonly used to close any internal porosity and further enhance properties.
- Contrainte résiduelle : Significant residual stresses can build up, requiring careful management during the build and appropriate stress relief treatments.
Why Powder Quality Matters – The Met3dp Advantage:
The performance and reliability of an AM missile nose cone are fundamentally linked to the quality of the metal powder used. Issues like inconsistent particle size, irregular shape, internal porosity within powder particles, or contamination can lead to defects in the final part, compromising its mechanical integrity.
This is where the expertise of companies like Met3dp becomes critical. Their investment in industry-leading powder production technologies, such as Vacuum Induction Melting Gas Atomization (VIGA) and Plasma Rotating Electrode Process (PREP), allows them to produce poudres métalliques de haute qualité with characteristics optimized for AM:
- Sphéricité élevée : Ensures excellent powder flowability in the printer and uniform powder bed density.
- Distribution contrôlée de la taille des particules (PSD) : Tailored PSDs for specific AM processes (L-PBF, SEBM) ensure optimal melting behavior and surface finish.
- High Purity & Low Contamination: Strict process controls minimize oxygen, nitrogen, and other contaminants that can degrade material properties.
- Batch Consistency: Rigorous quality control ensures reliable and repeatable performance from the powder.
By partnering with suppliers like Met3dp, who not only provide the printers but also manufacture the specialized Ti-6Al-4V et IN718 powders optimized for their equipment and aerospace applications, engineers and procurement managers can have higher confidence in the quality and performance of their 3D printed missile components.
Table: Ti-6Al-4V vs. IN718 for AM Nose Cones
Propriété | Ti-6Al-4V | IN718 | Primary Consideration for Nose Cones |
---|---|---|---|
Densité | Low (~4.4 g/cm³) | High (~8.2 g/cm³) | Ti-6Al-4V offers significant weight savings. |
Rapport résistance/poids | Excellent | Good (but lower than Ti-6Al-4V at room temp) | Critical advantage for Ti-6Al-4V in weight-sensitive applications. |
Température de service maximale | ~315°C (600°F) | ~700°C (1300°F) | IN718 required for hypersonic or very high-temperature environments. |
Coût | High (but generally lower than IN718) | Très élevé | Material cost is a significant factor; AM helps mitigate via waste reduction. |
AM Processability | Generally good, requires atmosphere control | More challenging (cracking risk), requires care | Both require expertise, IN718 may need more process control. |
Post-traitement | Stress relief, Heat treatment (Anneal/STA) | Stress relief, Solution + Double Aging, often HIP | Both require significant, specific post-processing for optimal properties. |
Typical Application | Supersonic missiles, tactical systems, structure | Hypersonic vehicles, high-heat zones, engine parts | Match material to the specific thermal and structural demands of the missile application. |
Exporter vers les feuilles
Choosing between Ti-6Al-4V and IN718 depends critically on the specific operating environment, particularly the peak temperatures the nose cone will experience. Both materials, when sourced as high-quality powders and processed using optimized AM parameters and appropriate post-processing, offer pathways to manufacturing robust, high-performance missile nose cones that push the boundaries of aerospace technology.
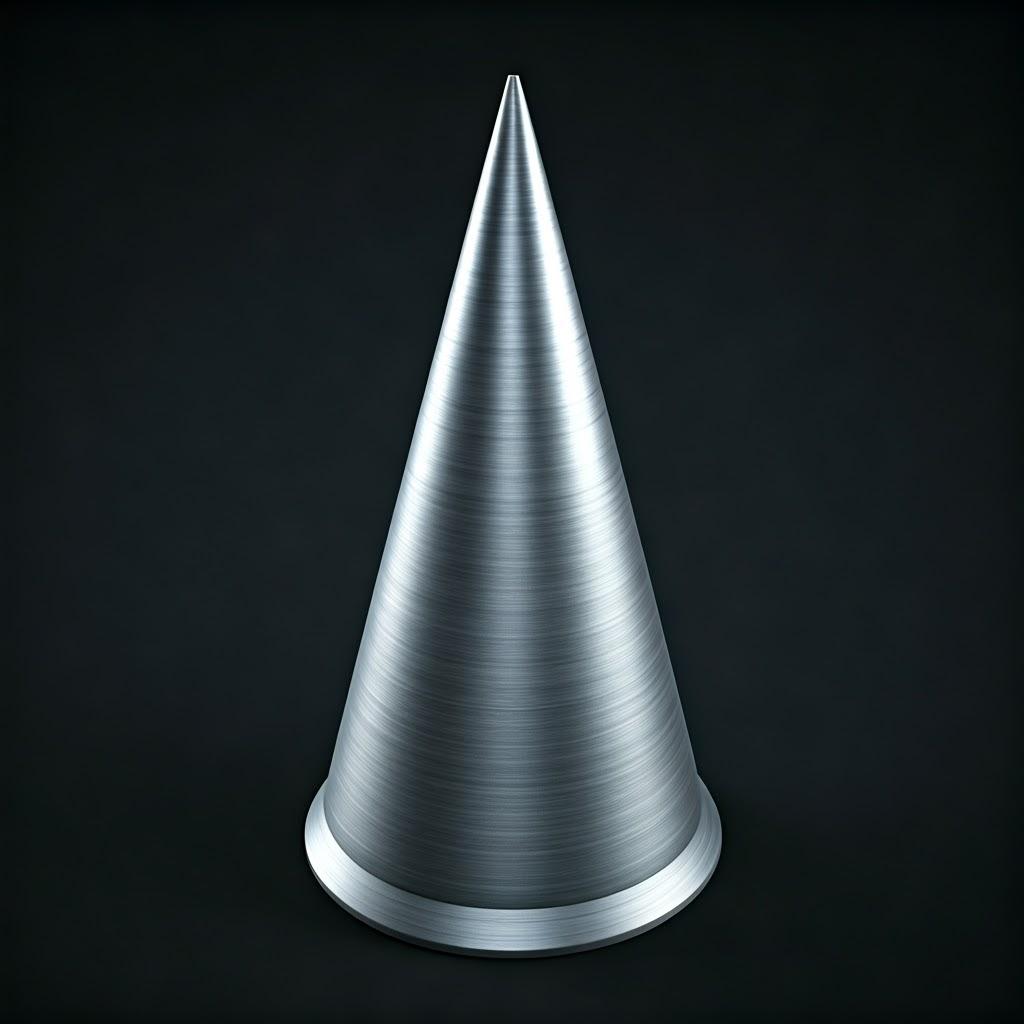
Design for Additive Manufacturing (DfAM): Optimizing Nose Cone Geometry
Simply replicating a design intended for traditional manufacturing onto a metal 3D printer rarely unlocks the full potential of additive manufacturing. To truly harness the benefits of AM for missile nose cones – achieving superior performance, reducing weight, and streamlining production – engineers must embrace Conception pour la fabrication additive (DfAM) principles. DfAM is a paradigm shift, encouraging designers to think in terms of layers, support structures, thermal management during the build, and the unique capabilities of the chosen AM process (like L-PBF or SEBM). Applying DfAM effectively requires a deep understanding of both the component’s functional requirements and the nuances of the additive process.
Key DfAM Principles for Missile Nose Cones:
- Leveraging Geometric Freedom for Performance:
- Aerodynamic Optimization: AM allows for the creation of highly complex, continuously variable curvatures and sharp leading edges tailored for specific flight regimes (subsonic to hypersonic). Computational Fluid Dynamics (CFD) simulations can drive designs that minimize drag and optimize lift characteristics far beyond what’s easily machinable. Features like precisely shaped inlets for air-breathing hypersonic missiles or subtle contours for stealth applications become manufacturable.
- Caractéristiques intégrées : Move beyond simple shapes. Design integrated mounting points for sensors, internal passages for wiring or cooling fluids, antenna elements embedded within the structure (requiring specific material considerations), or complex internal ribbing/stiffening structures precisely placed where needed. This reduces part count, assembly time, and potential points of failure.
- Weight Reduction Strategies:
- Optimisation de la topologie : Utilize software tools that iteratively remove material from low-stress areas while maintaining structural integrity under defined load cases (aerodynamic pressure, G-forces, vibration). This often results in organic, non-intuitive shapes that are significantly lighter than conventionally designed counterparts but equally strong or stiff. AM is uniquely capable of producing these complex, optimized geometries.
- Structures en treillis : Replace solid sections with internal lattice or honeycomb structures. These engineered porous structures provide excellent stiffness-to-weight ratios and can also enhance energy absorption or thermal dissipation. Different lattice cell types (e.g., cubic, octet truss, gyroid) offer varying mechanical and thermal properties, allowing for tailored performance within the nose cone structure. Designing access for powder removal from these internal structures is a critical DfAM consideration.
- Designing for Manufacturability (AM Specifics):
- Support Structure Strategy: While AM offers great freedom, gravity still applies during the build. Overhanging features beyond a certain angle (typically 45° relative to the build plate, but process/material dependent) require support structures to prevent collapse or deformation during printing. Supports add print time, consume material, require post-processing removal (which can be difficult and risk damaging the part), and can affect surface finish. Effective DfAM involves:
- Optimisation de l'orientation : Choosing the optimal build orientation to minimize the volume of required supports.
- Conception d'angles autoportants : Modifying overhangs to be below the critical angle where possible (e.g., using chamfers instead of sharp 90° overhangs).
- Minimizing Internal Supports: Designing internal channels or cavities to be self-supporting (e.g., teardrop or diamond shapes instead of circular horizontal holes) or ensuring clear access paths for support removal.
- Support Design: Utilizing specialized support structures (e.g., tree supports, easily breakable interfaces) offered by AM preparation software to ease removal.
- Wall Thickness and Feature Size: AM processes have limitations on minimum printable wall thickness and feature resolution, which depend on the machine, process (L-PBF often offers finer features than SEBM), and material. Designs must respect these limits (e.g., minimum wall thickness often around 0.4-0.8 mm). Thin walls are also more prone to warping.
- Thermal Management Considerations: Large solid sections or rapid changes in cross-sectional area can lead to differential cooling, increasing residual stress and warpage risk. DfAM might involve adding sacrificial ribs or modifying geometry to promote more uniform thermal distribution during the build.
- Orientation du trou : Horizontally oriented holes often print with poorer circularity and surface finish on the “up-skin” surfaces compared to vertically oriented holes. Design considerations might include orienting critical holes vertically or planning for post-print machining.
- Support Structure Strategy: While AM offers great freedom, gravity still applies during the build. Overhanging features beyond a certain angle (typically 45° relative to the build plate, but process/material dependent) require support structures to prevent collapse or deformation during printing. Supports add print time, consume material, require post-processing removal (which can be difficult and risk damaging the part), and can affect surface finish. Effective DfAM involves:
- Concevoir pour le post-traitement :
- Accès au retrait des supports : Ensure that areas requiring support structures are accessible for manual or tool-based removal after printing. This is especially critical for complex internal channels.
- Tolérances d'usinage : If specific surfaces require tight tolerances or superior finish achievable only by CNC machining, the AM design must include extra stock material (‘machining allowance’) in those areas.
- Accès à l'inspection : Design the part so that critical features can be accessed for inspection tools (e.g., CMM probes, NDT scanners) after manufacturing.
- Considérations relatives au traitement thermique : Very thin or delicate features might be susceptible to distortion during high-temperature heat treatments or HIP cycles. Design choices may need to balance weight reduction against post-processing robustness.
DfAM Workflow & Tools:
Implementing DfAM typically involves:
- CAD Software: Modern CAD packages increasingly incorporate DfAM-specific features.
- Simulation Tools: CFD for aerodynamics, Finite Element Analysis (FEA) for structural loads, Topology Optimization software.
- AM Build Preparation Software: Tools for orienting the part, generating support structures, and simulating the build process to predict potential issues like thermal stress or recoater blade interference.
- Collaboration : Close collaboration between design engineers, materials specialists, and AM process engineers (like the experts at service providers) is crucial for successful DfAM implementation.
By applying these principes de la DfAM, engineers can move beyond simply substituting manufacturing methods and start designing truly additive-native missile nose cones. This approach unlocks superior aerodynamic performance, achieves significant réduction du poids, integrates complex functionalities, and ultimately leverages the unique capabilities of services d'impression 3D en métal to create next-generation aerospace components. Exploring advanced manufacturing options like those offered by Met3dp’s printing methods early in the design phase can significantly influence the final part’s performance and cost-effectiveness.
Achieving Precision: Tolerance, Surface Finish, and Dimensional Accuracy in AM Nose Cones
While additive manufacturing offers remarkable design freedom, achieving the necessary precision for critical aerospace components like missile nose cones requires careful process control and often, post-processing steps. Engineers and procurement managers must understand the typical metal AM tolerances, achievable surface roughness (Ra), and factors influencing stabilité dimensionnelle to set realistic expectations and specify appropriate quality control measures. The precision requirements for a nose cone are driven by aerodynamic performance (smoothness, profile accuracy), interface requirements (mating with the missile body), and potentially sensor integration needs.
Typical Achievable Precision (As-Built):
The precision achievable directly from the AM process depends heavily on the specific technology (L-PBF vs. SEBM), machine calibration, material, part size/geometry, build orientation, and process parameters (layer thickness, beam energy density, scan strategy).
- Précision dimensionnelle :
- Tolérances générales : For well-controlled processes using high-end machines, typical dimensional accuracy for smaller features might be in the range of ±0.1 mm to ±0.2 mm (±0.004″ to ±0.008″). For larger dimensions (e.g., overall length or diameter of the nose cone), tolerances might widen proportionally, often expressed as a percentage of the dimension (e.g., ±0.1% to ±0.2%).
- L-PBF vs. SEBM: L-PBF generally offers slightly better dimensional accuracy and finer feature resolution due to smaller laser spot sizes and finer powder layers compared to the electron beam and powder used in SEBM. However, SEBM, often performed at elevated temperatures, can sometimes result in lower residual stress and less distortion for certain geometries, particularly with Ti-6Al-4V.
- Surface Roughness (Ra):
- As-Built Surfaces: The as-built surface finish of metal AM parts is inherently rougher than machined surfaces due to the layer-by-layer fusion process and partially melted powder particles adhering to the surface.
- Typical Ra Values: As-built Ra values typically range from 6 µm to 25 µm (approx. 240 µin to 1000 µin), depending heavily on:
- Orientation : Upward-facing surfaces and vertical walls tend to be smoother than downward-facing (overhanging) surfaces that required support structures. Angled surfaces have intermediate roughness.
- Épaisseur de la couche : Thinner layers generally lead to smoother surfaces but increase build time.
- Paramètres du processus : Beam power, scan speed, and powder characteristics influence melt pool stability and resulting surface texture.
- Matériau : Different materials can exhibit slightly different surface characteristics.
- Aerodynamic Implications: For supersonic and especially hypersonic applications, surface roughness can significantly impact boundary layer transition and aerodynamic heating. As-built surfaces often require post-processing (polishing, machining) to meet stringent aerodynamic smoothness requirements.
Factors Influencing Precision:
- Machine Calibration & Condition: Regular calibration of the laser/electron beam positioning system, scanner accuracy, and overall machine health is crucial.
- Paramètres du processus : Optimized parameters (beam power, speed, focus, layer thickness, hatch spacing) are essential for stable melting and solidification, minimizing variations.
- Gestion thermique : Controlling temperature gradients during the build (e.g., via build plate heating, chamber temperature control in SEBM) minimizes thermal stress, warping, and distortion, which directly affect dimensional accuracy.
- Qualité de la poudre : Consistent powder particle size distribution and morphology contribute to uniform powder bed density and stable melting, impacting both surface finish and dimensional accuracy. Sourcing powders from quality-focused manufacturers like Met3dp, known for their advanced atomization processes, helps ensure this consistency.
- Structures de soutien : Supports prevent distortion during the build but can leave witness marks upon removal, affecting local surface finish and potentially dimensional accuracy if not removed carefully.
- Géométrie et taille de la pièce : Large or complex parts with varying cross-sections are more prone to thermal distortion than smaller, simpler geometries.
- Post-traitement : Steps like heat treatment or HIP can cause minor dimensional changes (shrinkage or growth), which must be accounted for. Machining is often used to achieve the final, tightest tolerances on critical features.
Quality Control and Verification:
Ensuring that 3D printed nose cones meet stringent aerospace precision manufacturing standards requires robust quality control procedures:
- Contrôle en cours de fabrication : Some advanced AM systems incorporate sensors to monitor melt pool characteristics, layer temperatures, or powder bed quality in real-time, providing early defect detection.
- Inspection dimensionnelle : Coordinate Measuring Machines (CMMs) are commonly used for high-accuracy dimensional verification of the final part against the CAD model. Laser scanners or structured light scanners can provide full-field surface geometry data.
- Mesure de la rugosité de surface : Profilometers are used to quantify surface roughness (Ra, Rz) on critical areas.
- Essais non destructifs (END) : Techniques like X-ray Computed Tomography (CT) scanning can detect internal defects (porosity, inclusions) and verify internal channel geometry without damaging the part.
Achieving High Precision with AM Providers:
Choosing an AM service provider with demonstrated experience in high-precision manufacturing is key. Look for providers who:
- Operate well-maintained, high-quality AM systems.
- Employ rigorous process control and monitoring.
- Have robust Quality Management Systems (QMS), ideally certified to standards like AS9100 relevant for aerospace.
- Possess expertise in the specific materials (Ti-6Al-4V, IN718) and necessary post-processing techniques.
- Offer comprehensive metrology and inspection capabilities (CMM inspection, NDT).
While as-built AM parts may not match the tolerances and finish of precision machining in all aspects, understanding the achievable limits and integrating necessary post-processing allows metal 3D printing to produce missile nose cones meeting the demanding précision dimensionnelle and surface requirements for aerospace applications.
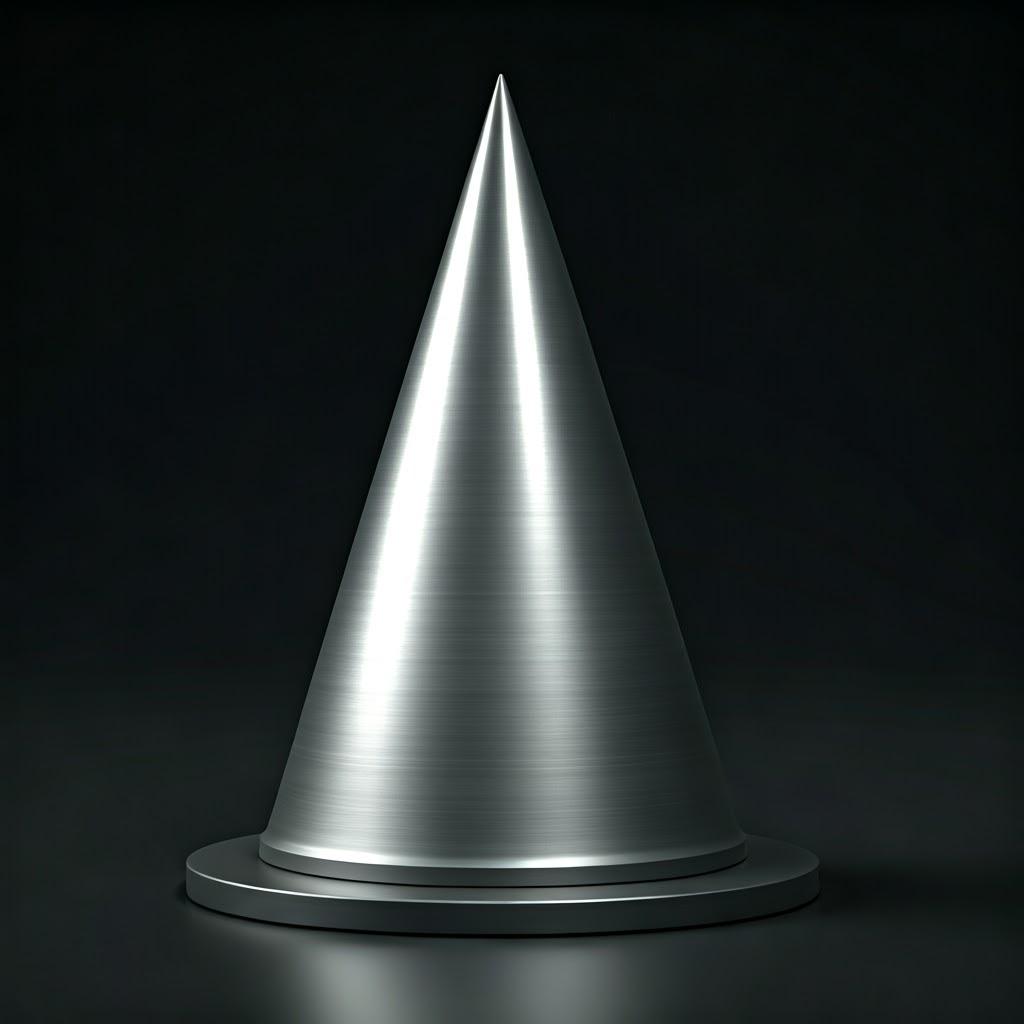
Beyond the Print: Essential Post-Processing for Missile Nose Cones
A common misconception about metal additive manufacturing is that the part coming out of the printer is the final product. For demanding applications like missile nose cones, the “print” is often just the beginning. A series of crucial post-traitement steps are almost always required to transform the as-built component into a functional, reliable, flight-ready part. These steps are essential to relieve internal stresses, optimize material properties, remove temporary structures, achieve final dimensions and surface finish, and ensure overall component integrity and component validation. Neglecting or improperly performing these steps can severely compromise the performance and safety of the final product.
Common Post-Processing Steps for AM Nose Cones:
- Soulagement du stress :
- Objet : The rapid heating and cooling cycles inherent in powder bed fusion AM processes create significant internal residual stresses within the part. These stresses can cause distortion (especially after removal from the build plate), cracking, and negatively impact mechanical properties (particularly fatigue life).
- Processus : The part, often while still attached to the build plate, is heated in a furnace (typically under vacuum or inert atmosphere like argon to prevent oxidation, especially critical for titanium) to a specific temperature below the material’s transformation point, held for a duration, and then slowly cooled. For Ti-6Al-4V, this might be around 600-800°C; for IN718, it might be higher, often integrated with the solution annealing step.
- Importance : This is generally considered a mandatory first step before any significant machining or removal from the build plate to prevent subsequent warping.
- Removal from Build Plate & Support Removal:
- Objet : Separating the printed part(s) from the base plate they were built upon and removing the temporary support structures required during the build.
- Méthodes :
- Build Plate Removal: Often done using wire EDM (Electrical Discharge Machining) or a band saw.
- Suppression du support : Can involve manual breaking/cutting (for well-designed supports), machining (milling), grinding, or sometimes specialized methods like electrochemical machining for inaccessible areas.
- Défis : Support removal can be labor-intensive and risks damaging the part’s surface or delicate features, especially with complex internal supports. DfAM plays a key role in minimizing and simplifying support removal.
- Heat Treatment (Optimizing Microstructure and Properties):
- Objet : To homogenize the microstructure, relieve stress further, and develop the desired mechanical properties (strength, ductility, hardness, fatigue resistance) tailored for the application. As-built AM microstructures are often non-equilibrium and not optimal for performance.
- Process (Material Specific):
- Ti-6Al-4V : Common treatments include:
- Annealing: Heating (e.g., 700-850°C) followed by controlled cooling to improve ductility and toughness.
- Solution Treatment and Aging (STA): Heating to a higher temperature (solutionizing, e.g., ~950°C), rapidly quenching, and then aging at an intermediate temperature (e.g., 500-600°C) to precipitate fine strengthening phases, achieving higher strength. Specific heat treatment aerospace parts standards dictate exact parameters.
- IN718 : Typically requires a multi-step process:
- Recuit de la solution : Heating to dissolve soluble phases (e.g., ~980°C).
- Double Aging: Two-step aging process (e.g., ~720°C followed by ~620°C) to precipitate the primary strengthening phases (γ’ and γ”).
- Ti-6Al-4V : Common treatments include:
- Équipement : Requires precisely controlled vacuum or inert atmosphere furnaces capable of reaching high temperatures and implementing specific cooling rates.
- Pressage isostatique à chaud (HIP) :
- Objet : To eliminate internal porosity (micro-voids) that can sometimes remain after the AM process, thereby improving material density, ductility, fatigue life, and overall structural integrity. Often specified for critical, fatigue-sensitive aerospace components.
- Processus : The part is subjected to high temperature (below melting point) and high-pressure inert gas (typically Argon, ~100 MPa or higher) simultaneously within a specialized HIP vessel. The pressure collapses internal voids, diffusion bonding the material across the void interfaces.
- Considérations : HIP processing titanium and nickel alloys is common practice for demanding applications. It adds cost and time but provides significant improvements in material quality and consistency. Minor dimensional changes can occur.
- Usinage CNC :
- Objet : To achieve final dimensional tolerances on critical features (e.g., mating interfaces with the missile body, sensor mounting surfaces) that are tighter than achievable with AM alone. Also used to improve surface finish in specific areas or create features not easily formed during the AM build.
- Processus : Using multi-axis CNC milling or turning centers to precisely remove material from specific areas identified in the design (requiring machining allowances in the AM part). Machining AM parts, especially Ti-6Al-4V and IN718, requires expertise due to their material properties.
- Importance : Essential for ensuring proper fit, form, and function within the larger missile assembly.
- Surface Finishing Techniques:
- Objet : To improve surface smoothness beyond the as-built or machined state, primarily for aerodynamic reasons (reducing drag, controlling boundary layer transition) or sometimes for applying coatings.
- Méthodes : Abrasive flow machining (AFM), electrochemical polishing, vibro-polishing (tumbling), manual polishing. The choice depends on the required smoothness level, part geometry, and cost.
- Revêtements : For hypersonic applications, specialized thermal barrier coatings (TBCs) or environmental barrier coatings (EBCs) might be applied to the exterior surface for thermal protection and oxidation resistance.
- Nettoyage et inspection :
- Objet : Final cleaning to remove any residues from machining, polishing, or handling. Followed by rigorous final inspection (dimensional, visual, NDT) to ensure the part meets all specifications before acceptance.
Table: Overview of Post-Processing Steps & Purpose
Post-Processing Step | Primary Purpose | Typical Material(s) | Principales considérations |
---|---|---|---|
Soulagement du stress | Reduce internal stresses, prevent distortion | All (esp. Ti-6Al-4V) | Mandatory first step, requires controlled furnace atmosphere |
Suppression du support | Remove temporary build supports | All | Can be labor-intensive, risk of part damage, DfAM is key |
Traitement thermique | Optimize microstructure & mechanical properties (strength, ductility) | All | Material-specific cycles (Anneal, STA, Aging), requires precise control |
Pressage isostatique à chaud | Eliminate internal porosity, improve density, enhance fatigue life | All (common for Aero) | Adds cost/time, improves material consistency, minor dimension changes |
Usinage CNC | Achieve tight tolerances on critical features, improve surface finish | All | Requires machining allowance, expertise in machining AM materials |
Finition de surface | Improve smoothness (aerodynamics), prepare for coating | All | Various methods (polishing, AFM), depends on requirements/geometry |
Cleaning & Inspection | Ensure cleanliness, final verification against specifications | All | Final quality gate, NDT often required for critical parts |
Exporter vers les feuilles
Successfully navigating these intricate post-processing steps requires significant expertise and specialized equipment. Partnering with a full-service metal AM provider who understands the entire workflow, from powder to validated component, is crucial for manufacturing high-quality, flight-worthy missile nose cones.
Navigating Challenges: Overcoming Hurdles in 3D Printing Nose Cones
While metal additive manufacturing offers transformative potential for producing missile nose cones, the process is not without its technical challenges. Successfully implementing AM for such critical components requires acknowledging these potential hurdles and employing robust strategies, advanced technologies, and rigorous process controls to overcome them. Addressing these challenges is key to ensuring part quality, repeatability, and ultimately, mission success.
Défis communs et stratégies d'atténuation :
- Residual Stress and Warpage:
- Défi: The intense, localized heating from the laser or electron beam followed by rapid cooling creates steep thermal gradients within the part during the build. This differential expansion and contraction generates internal stresses. If these stresses exceed the material’s yield strength at temperature, they can cause plastic deformation, leading to warping of the part (especially thin sections or large flat areas) or even cracking.
- Stratégies d'atténuation :
- Stratégies d'analyse optimisées : Using techniques like island scanning (dividing layers into small sections scanned randomly), checkerboard patterns, or optimized scan vector rotation helps distribute heat more evenly and reduce peak stress accumulation.
- Build Plate Heating: Pre-heating the build plate (common in L-PBF, inherent in SEBM which operates at higher background temperatures) reduces the thermal gradient between the fused material and the substrate, lowering stress.
- Intelligent Support Structures: Well-designed supports not only anchor the part but also act as heat sinks, drawing heat away more uniformly.
- Simulation de processus : Software tools can simulate the build process to predict stress accumulation and distortion, allowing for design or parameter adjustments before printing.
- Stress obligatoire après l'impression : As discussed previously, a stress relief heat treatment immediately after printing is crucial to relax internal stresses before part removal or machining. Providers like Met3dp leverage technologies like SEBM, which operates at elevated temperatures, inherently helping to reduce residual stress in materials like Ti-6Al-4V.
- Support Structure Design and Removal:
- Défi: Designing supports that effectively anchor overhangs and dissipate heat without being overly difficult or damaging to remove is a balancing act. Supports in complex internal channels or hard-to-reach areas pose significant removal challenges. Incomplete or damaging removal compromises the part’s geometry and surface finish.
- Stratégies d'atténuation :
- DfAM for Reduced Supports: Orienting the part and modifying designs (using self-supporting angles, changing feature shapes) to minimize the need for supports is the most effective approach.
- Optimized Support Types: Utilizing software features for generating easily removable supports (e.g., with smaller contact points, perforation, specific materials if using multi-material systems though rare in this context).
- Accessibility Planning: Ensuring clear lines of sight and tool access for support removal during the design phase.
- Techniques avancées de suppression : Employing methods like electrochemical machining or carefully controlled CNC machining for stubborn supports, although this adds cost.
- Porosity and Internal Defects:
- Défi: Small voids or pores can form within the printed material due to incomplete melting (lack of fusion), gas entrapment (from dissolved gas in the powder or shielding gas), or powder inconsistencies (e.g., hollow powder particles). Porosity degrades mechanical properties, particularly fatigue strength, acting as crack initiation sites.
- Stratégies d'atténuation :
- Paramètres de processus optimisés : Ensuring sufficient energy density (beam power/speed) to fully melt the material, while avoiding excessive energy that can cause keyholing (vapor depression instability) and associated porosity.
- Contrôle de la qualité des poudres : Using high-quality, dry, spherical powder with low internal gas content is critical. Stringent powder contamination control and handling procedures (e.g., vacuum storage, sieving) are essential. Met3dp’s focus on producing high-purity powders using advanced atomization and handling techniques directly addresses this challenge.
- Atmosphere Control: Maintaining a high-purity inert gas atmosphere (Argon in L-PBF) or high vacuum (SEBM) prevents oxidation and reduces gas pickup.
- Pressage isostatique à chaud (HIP) : As a post-processing step, HIP is highly effective at closing internal gas porosity and lack-of-fusion voids, significantly improving material integrity.
- Essais non destructifs (END) : Using CT scanning to detect and quantify internal porosity in the final part.
- Powder Management and Contamination:
- Défi: Metal powders, especially reactive ones like titanium, are sensitive to contamination (oxygen, nitrogen, moisture, cross-contamination from other materials). Contamination degrades material properties. Ensuring powder traceability and consistent reuse protocols is also critical for quality assurance.
- Stratégies d'atténuation :
- Dedicated Equipment: Using dedicated machines or thorough cleaning protocols when switching between reactive and non-reactive materials.
- Controlled Environment: Handling and storing powders in controlled humidity environments or inert atmospheres.
- Gestion du cycle de vie des poudres : Implementing rigorous procedures for powder sieving, sampling, testing (chemistry, PSD), blending, and tracking usage/reuse cycles to maintain quality and traceability. Companies with integrated powder production, like Met3dp, often have robust internal systems for this.
- Supplier Qualification: Sourcing powder only from reputable suppliers with strong quality certifications.
- Achieving Desired Surface Finish:
- Défi: The inherent layer-wise nature of AM results in a rougher surface finish compared to machining. For aerodynamically sensitive surfaces on a nose cone, this as-built roughness is often unacceptable.
- Stratégies d'atténuation :
- Optimisation des paramètres : Fine-tuning parameters (e.g., contour scans, smaller layer thickness) can improve finish slightly but often at the cost of build time.
- Orientation de la construction : Orienting critical surfaces vertically or as upward-facing planes generally yields better finishes.
- Post-Processing Finishing: Incorporating steps like CNC machining, polishing, or abrasive flow machining specifically targeted at achieving the required Ra values on critical surfaces.
- Process Consistency and Repeatability:
- Défi: Ensuring that parts produced today have the same dimensions, microstructure, and properties as parts produced weeks or months later, potentially on different machines, is crucial for serial production in aerospace. Variations in powder batches, machine calibration drift, or environmental factors can affect consistency.
- Stratégies d'atténuation :
- Des systèmes de gestion de la qualité (QMS) robustes : Implementing comprehensive QMS (e.g., ISO 9001, AS9100) covering all aspects from powder handling to final inspection.
- Procédures normalisées : Using detailed, validated work instructions for machine setup, operation, post-processing, and inspection.
- Regular Machine Calibration and Maintenance: Ensuring all equipment performs within specified parameters.
- Surveillance des processus : Utilizing available in-situ monitoring tools to track build consistency.
- Contrôle statistique des processus (CSP) : Analyzing process data to identify and control sources of variation.
Successfully managing warpage, ensuring effective support removal, controlling powder contamination, mitigating defects through AM process monitoring, and achieving consistent results requires a combination of advanced technology, materials science knowledge, process engineering expertise, and rigorous quality control – all areas where experienced metal AM service providers add significant value.
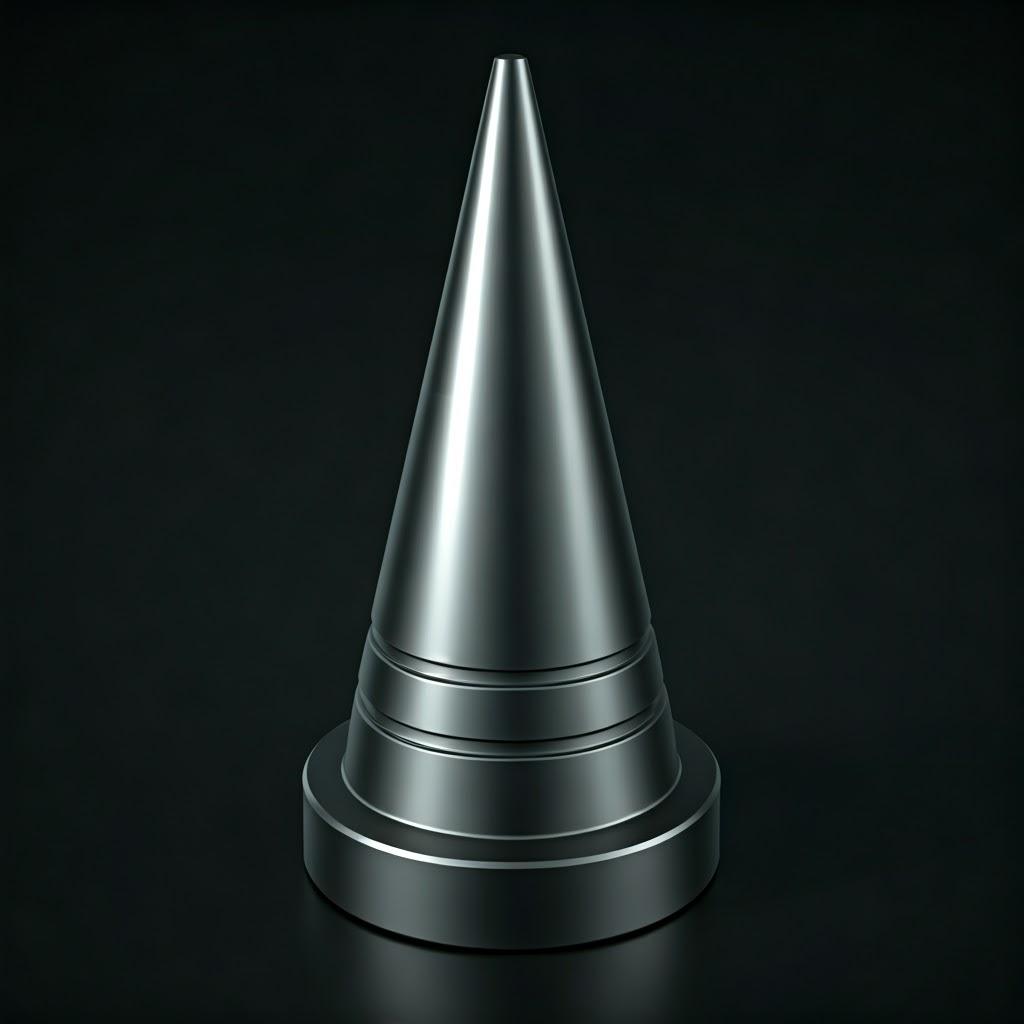
Supplier Selection: Choosing the Right Metal AM Partner for Defense Components
Selecting the appropriate metal 3D printing service provider is arguably one of the most critical decisions when sourcing additively manufactured missile nose cones or other high-consequence defense components. The difference between a capable, quality-focused partner and one lacking the necessary expertise or certifications can significantly impact project success, component reliability, and adherence to stringent aerospace and defense standards. Procurement managers and engineers must conduct thorough due diligence, evaluating potential suppliers against a comprehensive set of criteria.
Key Criteria for Evaluating Metal AM Suppliers:
- Certifications and Compliance: This is often the first gate for aerospace and defense work.
- Certification AS9100 : The internationally recognized Quality Management System (QMS) standard for the aviation, space, and defense industries. Certification to AS9100 demonstrates a supplier’s commitment to rigorous quality processes, traceability, risk management, and continuous improvement tailored to the sector’s demands. Non-negotiable for most flight-critical components.
- ISO 9001 Certification: A foundational QMS standard, indicating robust general quality processes. Often a prerequisite for AS9100.
- ITAR Compliance (International Traffic in Arms Regulations): Crucial for suppliers handling US defense articles or technical data. ITAR mandates strict controls on the export and handling of defense-related items and information. Suppliers involved in US defense projects must be ITAR registered and have stringent security protocols in place to prevent unauthorized access or transfer of controlled data/hardware. Note: For non-US defense projects or components not subject to ITAR, equivalent national export control regulations may apply. When considering international suppliers, understanding their status and capability regarding relevant export controls is vital.
- Accréditation Nadcap : While AS9100 covers the overall QMS, Nadcap provides specific accreditation for special processes like heat treatment, non-destructive testing (NDT), welding, and potentially additive manufacturing itself (though AM accreditation is still evolving). If a supplier performs these critical post-processing steps in-house, Nadcap accreditation provides additional confidence in their process control.
- Expertise technique et expérience :
- Proven Track Record: Look for demonstrated experience in producing components for the aerospace and defense sectors. Case studies, references, and examples of similar projects (within confidentiality limits) are valuable indicators.
- Materials Expertise: Deep understanding of processing the specified materials (e.g., Ti-6Al-4V, IN718), including their metallurgy, AM process interactions, and required post-processing.
- DfAM Capabilities: Does the supplier offer engineering support to help optimize designs for additive manufacturing? Can they provide feedback on manufacturability and suggest design improvements?
- Post-Processing Know-How: Expertise in the full chain of necessary post-processing steps (stress relief, heat treatment, HIP, machining, finishing) is critical, whether performed in-house or managed through qualified subcontractors. Companies like Met3dp, with decades of collective expertise in metal AM, bring significant value here. You can learn more about their background and focus on their Page À propos de nous.
- Equipment, Capabilities, and Capacity:
- Technology Fit: Do they operate the appropriate AM technology (L-PBF, SEBM) for the material and application requirements? SEBM, for instance, might be preferred for reducing residual stress in Ti-6Al-4V.
- Volume de construction : Can their machines accommodate the size of the required nose cone? Availability of large format metal printing capabilities is essential for larger components. Met3dp emphasizes their printers’ industry-leading print volume and accuracy.
- Machine Fleet & Redundancy: Number and age of machines, maintenance schedules. Sufficient capacity to meet lead time requirements and provide redundancy in case of machine downtime.
- In-House vs. Subcontracted Post-Processing: Understand which post-processing steps are performed in-house versus outsourced. In-house capabilities generally offer better control over the entire process chain and potentially shorter lead times. If outsourced, ensure the subcontractors are also appropriately qualified (e.g., Nadcap accredited).
- Metrology and Inspection: Availability of advanced inspection equipment (CMM, scanners, NDT like CT scanning) and trained personnel.
- Material Quality, Handling, and Traceability:
- Powder Sourcing: Do they source powders from reputable, qualified suppliers, or do they manufacture their own powders to exacting standards? Met3dp’s use of advanced gas atomization and PREP technologies for their poudres métalliques de haute qualité provides an advantage in controlling input material quality.
- Powder Management: Rigorous procedures for incoming powder inspection, storage (environmental control), handling (preventing contamination), sieving, blending, and tracking reuse cycles are critical, especially for reactive materials like titanium.
- Full Traceability: Ability to trace a specific part back to the exact powder batch, machine used, build parameters, post-processing steps, and inspection results. This is a fundamental requirement of AS9100.
- Quality Management System (QMS) Implementation:
- Beyond certification, assess the implementation of the QMS. This includes robust process controls, comprehensive documentation practices, effective handling of non-conformances, rigorous calibration schedules, and a culture of quality throughout the organization.
- Security:
- Data Security: Secure methods for transferring and storing sensitive CAD data and project information, compliant with ITAR or other relevant regulations.
- Physical Security: Controls to prevent unauthorized access to facilities and hardware, particularly important for defense projects.
- Communication and Partnership:
- Look for a supplier who acts as a partner, offering proactive communication, technical collaboration, and transparency throughout the manufacturing process. Responsiveness and clear points of contact are important.
Supplier Audit:
For critical components, a physical or virtual supplier audit is highly recommended to verify capabilities, procedures, and certifications firsthand. This allows for a deeper assessment beyond documentation and marketing materials.
Choisir le bon aerospace certified AM supplier is an investment in quality, reliability, and risk mitigation. Thoroughly evaluating AM capabilities, certifications, and quality processes is essential when sourcing components as critical as missile nose cones.
Economic Considerations: Cost Drivers and Lead Times for AM Nose Cones
While metal additive manufacturing enables performance breakthroughs, understanding the metal 3D printing cost analysis and typical AM production lead times est cruciale pour B2B procurement AM decisions and project planning. Compared to traditional manufacturing, the cost structure of AM is different, shifting emphasis from tooling and raw material bulk towards machine time, specialized labor, and sophisticated post-processing.
Key Cost Drivers for AM Missile Nose Cones:
- Coût des matériaux :
- Powder Price: Poudre Ti-6Al-4V and especially Poudre IN718 are expensive raw materials. Cost is typically calculated per kilogram.
- Volume de la pièce : The amount of material directly fused to create the part.
- Support Structure Volume: Material used for supports, which is later removed. Efficient DfAM minimizes this.
- Powder Recycling Rate: The efficiency with which unfused powder can be sieved and reused impacts the effective material cost per part. High recycling rates significantly reduce costs.
- Qualité de la poudre : Higher quality, aerospace-grade powders meeting stringent specifications command premium prices but are necessary for reliable parts.
- AM Machine Time:
- Taux horaire : Metal AM machines represent significant capital investment, leading to relatively high hourly operating rates. Rates vary by machine type, size, and supplier.
- Temps de construction : The total time the machine spends printing the part. This is influenced by:
- Part Height: The primary driver, as printing is layer-by-layer.
- Part Volume/Density: Amount of material to be fused per layer.
- Épaisseur de la couche : Thinner layers improve resolution/finish but significantly increase build time.
- Stratégie de numérisation : Complex scanning patterns for stress reduction can add time.
- Nesting: Printing multiple parts simultaneously in one build can reduce per-part machine time by sharing setup and non-printing phases.
- Coûts de main-d'œuvre :
- Machine Setup & Teardown: Preparing the machine, loading powder, removing the build plate and part.
- Build Monitoring: Skilled technicians often monitor the build process.
- Part Removal & Cleaning: Separating parts from the build plate, initial powder removal (depowdering).
- Suppression du support : Can be highly labor-intensive depending on complexity.
- Main-d'œuvre de post-traitement : Performing heat treatments, machining setups, finishing, inspection. Requires skilled personnel.
- Coûts de post-traitement :
- Soulagement du stress / Traitement thermique : Furnace time, energy consumption, inert gas/vacuum costs.
- Pressage isostatique à chaud (HIP) : Significant cost adder due to specialized equipment and long cycle times. Often charged per cycle or based on volume.
- Usinage CNC : Machine time and skilled labor for finishing critical features.
- Finition de la surface : Polishing, coating application costs.
- Assurance qualité et inspection :
- Métrologie : Time for CMM inspection, scanning.
- Essais non destructifs (END) : Costs associated with CT scanning, ultrasonic testing, etc.
- Documentation & Certification: Effort required to compile traceability documentation and certificates of conformance.
- Design, Engineering & Setup:
- DfAM Effort: Time spent optimizing the design for AM.
- Préparation de la construction : Generating support structures, slicing the model, creating the build file. Can be complex for intricate parts.
- Supplier Overhead and Profit: Standard business costs incorporated into the final price.
Délais d'exécution typiques :
Lead time for an AM nose cone is the sum of several stages and can vary significantly:
- Quoting & Order Processing: Days to a week.
- Design Review & Build Prep: 1-5 days, depending on complexity and need for DfAM adjustments.
- Machine Queue: Highly variable, from days to several weeks, depending on supplier workload and machine availability.
- AM Build Time: Highly variable, from ~12 hours for a small, simple part to over a week (150+ hours) for a large, complex nose cone.
- Post-traitement : Can be the longest phase:
- Cooling & Stress Relief: 1-2 days.
- Support/Part Removal: 0.5-2 days.
- Heat Treatment: 1-3 days (including furnace cycles).
- HIP: 2-4 days (including shipping to/from HIP provider if outsourced).
- Machining: 1-5 days (depending on complexity and setup).
- Finishing/Inspection: 1-3 days.
- Expédition: 1-5 days (domestic), longer internationally.
Total Lead Time: For a complex missile nose cone requiring extensive post-processing, lead times of 4 to 8 weeks from order placement to final delivery are common, though expedited options may exist at a premium cost. Rapid prototyping iterations might be faster if some post-processing steps are omitted.
AM vs. Traditional – Economic Perspective:
While the per-part cost of AM might sometimes be higher than mass-produced traditional parts, a Total Cost of Ownership (TCO) perspective is often more relevant for aerospace components:
- No Tooling Costs: Significant savings for prototypes and low-volume production compared to forging dies or casting molds.
- Réduction des déchets matériels : Higher material utilization saves costs, especially with expensive alloys.
- Faster Development: Reduced lead time for prototypes accelerates R&D and time-to-market/deployment.
- Performance Gains: Weight reduction can translate to significant operational savings (fuel efficiency, range) or enhanced capability over the component’s lifetime.
- Supply Chain Benefits: On-demand production reduces inventory costs and improves responsiveness.
Understanding the specific cost drivers and lead time components allows for better budgeting, planning, and comparison when evaluating impression 3D de métaux against traditional methods for missile nose cone manufacturing.
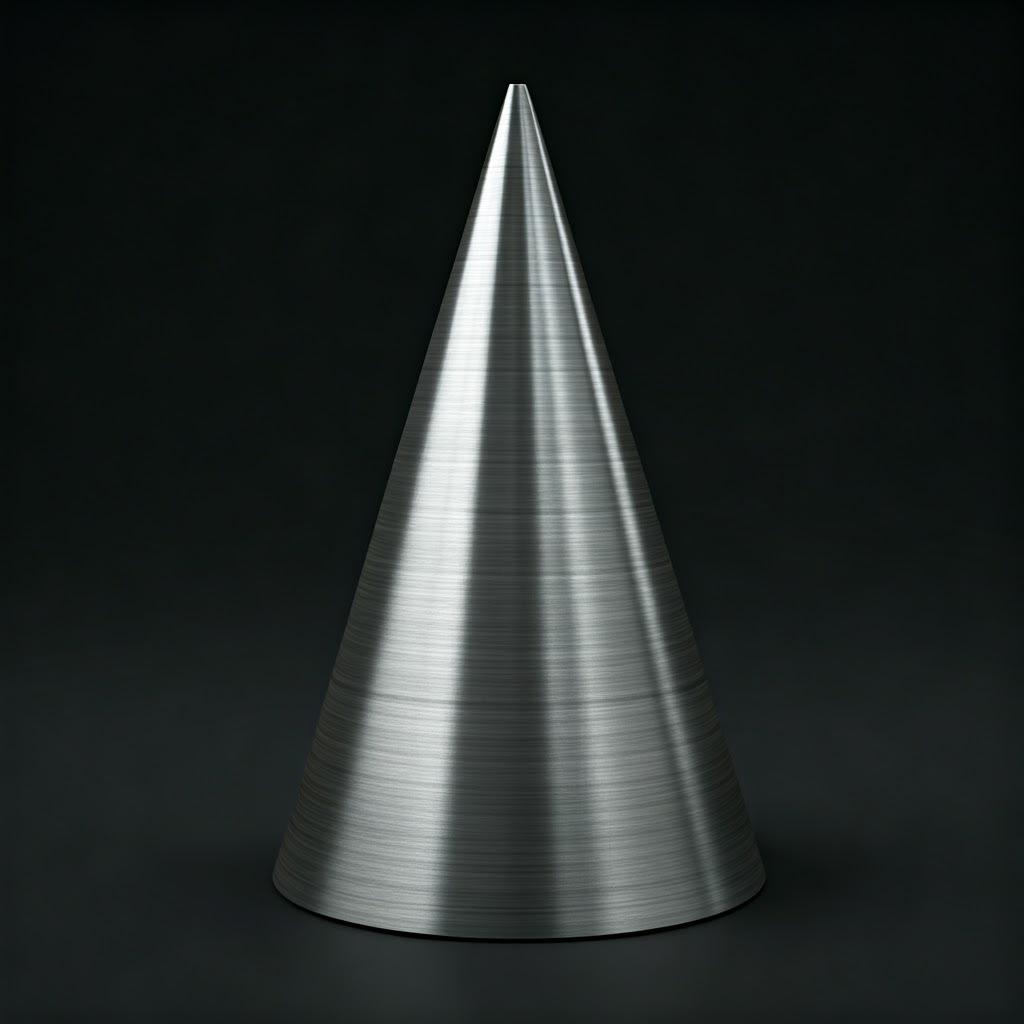
Frequently Asked Questions (FAQ) about 3D Printed Missile Nose Cones
Here are answers to some common questions regarding the additive manufacturing of missile nose cones using materials like Ti-6Al-4V and IN718:
- Q: How do the mechanical properties of AM Ti-6Al-4V and IN718 compare to traditional wrought or cast materials?
- A : When produced using optimized process parameters and subjected to appropriate post-processing (including stress relief, heat treatment, and often HIP), the mechanical properties of AM Ti-6Al-4V and IN718 can be highly comparable, and in some cases superior, to their conventionally manufactured counterparts.
- Static Strength (Tensile, Yield): Typically meets or exceeds minimum specifications for wrought or cast materials after proper heat treatment.
- Ductilité : Can be slightly lower than wrought material in some orientations but generally meets requirements after HIP and heat treatment.
- Résistance à la fatigue : Often a key advantage of AM. The fine microstructures resulting from rapid solidification, combined with porosity elimination via HIP, can lead to fatigue properties equivalent to or even better than wrought materials, especially for Ti-6Al-4V.
- Cohérence : Achieving consistent properties requires rigorous process control and post-processing standardization. Properties can be anisotropic (directionally dependent) in the as-built state but become more isotropic after heat treatment and HIP.
- A : When produced using optimized process parameters and subjected to appropriate post-processing (including stress relief, heat treatment, and often HIP), the mechanical properties of AM Ti-6Al-4V and IN718 can be highly comparable, and in some cases superior, to their conventionally manufactured counterparts.
- Q: What are the typical size limitations for 3D printing missile nose cones?
- A : The maximum size is primarily limited by the build volume of the available metal AM machines. Standard commercial L-PBF machines often have build envelopes around 250x250x300 mm to 400x400x400 mm. Larger format systems are becoming increasingly available, with build volumes reaching up to 800 mm or even 1000 mm (1 meter) in one dimension. Selective Electron Beam Melting (SEBM) machines also offer substantial build volumes. For very large nose cones exceeding the capacity of a single build, options might include printing in sections and joining them via welding (requiring subsequent stress relief and inspection of the weld). Companies investing in industry-leading print volume capabilities, like those highlighted by Met3dp, are better equipped to handle larger aerospace components.
- Q: How is powder quality ensured throughout the AM process and lifecycle?
- A : Maintaining powder quality is critical for part integrity. Robust protocols include:
- Supplier Qualification: Sourcing powder only from reputable manufacturers like Met3dp who provide detailed material certifications documenting chemistry, particle size distribution (PSD), morphology, and flow characteristics. Information on specific Met3dp products, including their powder specifications, is crucial.
- Incoming Inspection: Verifying powder quality upon receipt against specifications.
- Controlled Storage & Handling: Storing powder in sealed containers, often under inert gas or controlled humidity, to prevent contamination (especially oxygen/moisture pickup for reactive metals). Using dedicated tools and equipment.
- Tamisage : Regularly sieving powder before loading into the machine and after a build (for recycled powder) to remove contaminants, agglomerates, or spatters.
- Reuse Strategy: Implementing a documented strategy for powder reuse, often involving blending virgin and recycled powder in controlled ratios and tracking the number of reuse cycles. Periodic chemical and PSD analysis of recycled powder ensures it remains within specification.
- Traceability: Maintaining meticulous records linking specific powder batches to specific builds and parts.
- A : Maintaining powder quality is critical for part integrity. Robust protocols include:
- Q: What level of surface finish (roughness) can be realistically expected on an AM nose cone?
- A : As-built surface roughness (Ra) typically ranges from 6 to 25 µm, depending on the AM process (L-PBF generally smoother than SEBM), material, build orientation (up-skin vs. down-skin vs. vertical walls), and process parameters (e.g., layer thickness). This as-built finish is often too rough for optimal aerodynamic performance. Post-processing is usually required for critical surfaces:
- Usinage CNC : Can achieve Ra values well below 1 µm on specific features.
- Polishing/Finishing: Techniques like abrasive flow machining, electrochemical polishing, or manual polishing can significantly reduce surface roughness across broader areas, potentially achieving Ra values of 1-5 µm or lower depending on the effort and technique. The final achievable finish depends on the target requirements, geometry, and chosen finishing methods.
- A : As-built surface roughness (Ra) typically ranges from 6 to 25 µm, depending on the AM process (L-PBF generally smoother than SEBM), material, build orientation (up-skin vs. down-skin vs. vertical walls), and process parameters (e.g., layer thickness). This as-built finish is often too rough for optimal aerodynamic performance. Post-processing is usually required for critical surfaces:
Conclusion: The Future of Missile Technology Forged with Additive Manufacturing
The journey through the intricacies of 3D printing missile nose cones reveals a clear trajectory: metal additive manufacturing is not just a viable alternative but an essential enabler for the future of aerospace and defense technology. The ability to fabricate complex geometries from high-performance materials like Ti-6Al-4V et IN718 layer by layer unlocks unprecedented opportunities for enhancing missile performance, agility, and survivability.
We’ve seen how AM, guided by rigorous principes de la DfAM, allows engineers to shed the constraints of traditional manufacturing. This freedom translates into aerodynamically superior shapes, integrated functionalities, and significantly lighter components through topology optimization and internal lattice structures – all contributing to missiles that fly faster, farther, and with greater precision. The efficient use of expensive aerospace grade titanium et superalliages de nickel, coupled with the potential for prototypage rapide and on-demand production, fundamentally streamlines development cycles and enhances supply chain optimization within the defense sector.
However, realizing these benefits demands meticulous attention to detail. The importance of qualité des matériaux, sourced from expert fournisseurs de poudres métalliques, cannot be overstated. Precise control over the AM process parameters, coupled with essential post-traitement steps like stress relief, heat treatment, HIP, and precision machining, are non-negotiable for achieving the required dimensional accuracy, surface finish, and mechanical integrity. Navigating potential challenges such as residual stress, support removal, and defect mitigation requires deep process knowledge and robust quality management.
Critically, the success of implementing AM for such demanding applications hinges on collaboration with the right partners. Selecting an experienced fournisseur de services AM en métal with the necessary certifications (AS9100, potentially ITAR where applicable), proven technical expertise, appropriate equipment, stringent quality controls, and a deep understanding of materials like Ti-6Al-4V et IN718 est primordiale.
The future of missile technology will undoubtedly be shaped by continued advancements in digital manufacturing. Metal AM stands at the forefront of this transformation, offering a powerful toolkit to meet the ever-increasing demands for performance and capability. As this technology matures, driven by innovation in machines, materials, and processes, we can expect to see even more sophisticated and capable aerospace systems take flight. Companies like Met3dp, providing comprehensive Met3dp solutions that encompass cutting-edge SEBM printers, advanced metal powders manufactured using state-of-the-art atomization techniques, and deep application development expertise, are pivotal in empowering organizations to harness the full potential of additive manufacturing and forge the next generation of aerospace and defense components. The path forward involves embracing AM not just as a manufacturing method, but as a strategic capability for innovation and competitive advantage.
Partager sur
MET3DP Technology Co. est un fournisseur de premier plan de solutions de fabrication additive dont le siège se trouve à Qingdao, en Chine. Notre société est spécialisée dans les équipements d'impression 3D et les poudres métalliques de haute performance pour les applications industrielles.
Articles connexes
À propos de Met3DP
Mise à jour récente
Notre produit
CONTACTEZ-NOUS
Vous avez des questions ? Envoyez-nous un message dès maintenant ! Nous répondrons à votre demande avec toute une équipe dès réception de votre message.
Obtenir les informations de Metal3DP
Brochure du produit
Obtenir les derniers produits et la liste des prix
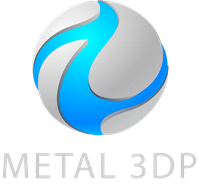
Poudres métalliques pour l'impression 3D et la fabrication additive