Custom Heat Transfer Components 3D Printed in Copper Alloys
Table des matières
Introduction: The Critical Role of Custom Heat Transfer Components in Modern Systems
In an era defined by relentless technological advancement, miniaturization, and escalating power densities, effective thermal management is no longer just a desirable feature—it’s an absolute necessity. From high-performance computing clusters generating immense heat to intricate aerospace systems operating in extreme environments, the ability to efficiently dissipate thermal energy is paramount to reliability, performance, and safety. At the heart of these thermal management solutions lie heat transfer components – devices meticulously designed to move heat from a source to a sink, often utilizing fluids or ambient air. However, standard, off-the-shelf components frequently fall short when faced with the unique constraints and demanding performance requirements of cutting-edge applications. This is where Custom Heat Transfer Components become indispensable.
Customization allows engineers to tailor thermal solutions precisely to the application’s specific geometry, thermal load, flow conditions, and operating environment. Whether it’s a uniquely shaped cold plate for cooling densely packed electronics, a compact heat exchanger integrated into a complex automotive powertrain, or a specialized thermal component for a medical device, the ability to design and manufacture bespoke solutions offers significant advantages. Traditional manufacturing methods like CNC machining, casting, or brazing assemblies have long been used to create these components. While effective, these methods often impose limitations on geometric complexity, integration possibilities, and lead times, particularly for intricate designs or low-volume production runs.
L'avènement de la Fabrication additive métallique (AM), commonly known as metal Impression 3D, has fundamentally changed the landscape for designing and producing custom heat transfer components. Specifically, the ability to 3D print with high-conductivity copper alloys like pure Copper (Cu) and Copper-Chromium-Zirconium (CuCrZr) opens up unprecedented possibilities. Metal AM allows for the creation of highly complex internal channel structures, conformal cooling paths that precisely follow the contours of heat sources, and integrated, monolithic designs that minimize thermal resistance and potential leak points. This technology empowers designers to break free from the constraints of traditional manufacturing, enabling the creation of heat transfer components optimized for maximum performance, minimal size and weight, and enhanced reliability.
For procurement managers and engineers in sectors like aerospace, automotive, high-performance computing, energy, medical devices, and industrial manufacturing, understanding the potential of 3D printed copper heat transfer components is crucial. It represents a paradigm shift in thermal management, offering solutions that were previously unattainable. Companies specializing in advanced manufacturing technologies, like Met3dp, are at the forefront of this revolution. With deep expertise in impression 3D de métaux processes and advanced powder metallurgy, Met3dp provides the capabilities needed to turn complex thermal challenges into high-performance, reliable hardware. Our state-of-the-art gas atomization and PREP technologies ensure the production of high-sphericity, high-purity copper alloy powders, forming the foundation for superior 3D printed components.
This article delves into the world of custom heat transfer components manufactured using metal 3D printing, focusing on the benefits and applications of copper alloys. We will explore the use cases, the distinct advantages offered by AM, the properties of recommended copper powders, critical design considerations, achievable precision, post-processing requirements, potential challenges, supplier selection criteria, cost factors, and answer frequently asked questions. Our goal is to provide engineers, designers, and procurement professionals with a comprehensive understanding of how this technology can be leveraged to solve their most demanding thermal management problems.
Diverse Applications: Where Are Custom Heat Transfer Components Utilized?
The need for efficient and tailored thermal management spans a vast array of industries and applications. Custom heat transfer components, particularly those leveraging the design freedom of metal 3D printing and the excellent conductivity of copper alloys, find critical roles in numerous high-stakes environments. Their ability to be precisely shaped, incorporate complex internal features, and handle significant heat loads makes them invaluable where standard solutions prove inadequate.
Here’s a breakdown of key application areas:
1. Aerospace and Defense:
- Avionics Cooling: Modern aircraft and spacecraft contain densely packed electronic systems generating substantial heat. Custom 3D printed cold plates and heat exchangers with conformal cooling channels can efficiently cool processors, FPGAs, power amplifiers, and other critical components within tight space constraints. Lightweighting, achieved through topology optimization and lattice structures (enabled by AM), is also a major benefit.
- Composants du moteur : Components within jet engines or rocket propulsion systems, such as turbine blades, combustion chambers, or nozzle extensions, often require intricate internal cooling channels to withstand extreme temperatures. 3D printing allows for the creation of these complex cooling networks directly within the part, improving durability and performance. Copper alloys offer the high conductivity needed for rapid heat extraction.
- Satellite Thermal Control: Maintaining optimal operating temperatures for sensitive instruments and electronics in the vacuum of space is critical. Custom heat pipes, radiators, and thermal straps, potentially manufactured using AM for complex geometries and integration, play a vital role.
- Directed Energy Systems: High-power lasers and microwave systems generate significant waste heat that must be managed precisely. Custom copper alloy heat sinks and cooling manifolds manufactured via AM can provide the necessary thermal performance in compact form factors.
2. Automotive Industry:
- Electric Vehicle (EV) Battery Cooling: Maintaining optimal battery temperatures is crucial for EV performance, longevity, and safety. 3D printed copper alloy cold plates with complex, optimized channel designs can provide highly efficient and uniform cooling for battery modules, especially in high-performance vehicles or fast-charging scenarios.
- Power Electronics Cooling: Inverters, converters, and onboard chargers in EVs and hybrid vehicles generate significant heat. Custom, compact heat sinks and liquid cooling plates, potentially integrating multiple functions, can be realized through AM.
- Engine Components (Internal Combustion & Hybrid): While EVs are growing, internal combustion engines still require sophisticated cooling. Custom components like oil coolers, intercoolers, or even cylinder heads with optimized coolant passages can benefit from the design freedom of AM for improved efficiency and performance.
- Motorsport: Racing applications demand maximum performance and minimal weight. 3D printed copper heat exchangers, oil coolers, and brake cooling components offer bespoke solutions optimized for specific vehicle architectures and extreme operating conditions.
3. High-Performance Computing (HPC) and Data Centers:
- CPU/GPU Cooling: Processors in servers, workstations, and supercomputers are major heat sources. Custom liquid cooling cold plates made from high-conductivity copper, featuring micro-channel designs optimized by AM, can dramatically improve cooling efficiency compared to standard heat sinks, enabling higher clock speeds and denser server racks.
- Direct Liquid Cooling (DLC): As power densities increase, direct liquid cooling solutions are becoming more common. 3D printing enables the creation of custom manifolds, distribution units, and complex cold plates integrated directly onto server blades or components.
- Immersion Cooling: While less common, 3D printing can be used to create custom fixtures, flow directors, or even enhanced surfaces for components used within immersion cooling tanks.
4. Medical Devices:
- Laser and Imaging Equipment: Medical lasers (surgical, dermatological) and diagnostic imaging systems (MRI, CT scanners) often have components that generate significant heat. Custom miniature heat exchangers or cold plates made with biocompatible coatings over copper can ensure stable operating temperatures for sensitive detectors or power sources.
- Surgical Tools: Some advanced surgical tools might incorporate cooling mechanisms to prevent overheating during procedures. AM allows for the integration of micro-cooling channels directly into the tool’s structure.
- Patient Temperature Management: Devices used for therapeutic hypothermia or patient warming might utilize custom heat exchange elements tailored to specific body parts or applications.
5. Industrial Manufacturing and Energy:
- Process Equipment: Chemical reactors, plastic injection molds, and other industrial machinery often require precise temperature control. 3D printed conformal cooling channels within molds or custom heat exchangers can significantly reduce cycle times and improve part quality.
- Production d'électricité : Components in turbines, generators, and power plant cooling systems can benefit from optimized heat transfer designs enabled by AM, improving efficiency and reliability.
- Welding and Laser Processing: Torches and heads used in high-power welding or cutting operations require efficient cooling. Custom copper alloy cooling elements can extend consumable life and improve process stability.
- Renewable Energy: Components within concentrated solar power systems or geothermal energy extraction might require specialized heat transfer components adaptable to unique geometries.
6. Consumer Electronics (High-End):
- Gaming PCs and Laptops: Enthusiast-grade computing often pushes thermal limits. Custom liquid cooling loops featuring 3D printed copper cold plates or distribution blocks offer superior performance and aesthetic customization.
- High-Power LEDs: Specialized lighting applications requiring high-power LEDs need efficient thermal dissipation. Custom copper heat sinks with optimized fin structures can be developed using AM.
Summary Table: Key Applications for Custom 3D Printed Copper Heat Transfer Components
Secteur industriel | Applications spécifiques | Key Benefits Enabled by AM & Copper Alloys |
---|---|---|
Aérospatiale et défense | Avionics cooling, Engine components (turbine blades, combustors), Satellite thermal control, Directed energy systems | High thermal conductivity, Complex geometries, Lightweighting, Part consolidation |
Automobile | EV battery cooling, Power electronics (inverters, chargers), Engine/Transmission cooling, Motorsport components | High thermal conductivity, Conformal channels, Compactness, Customization |
HPC & Data Centers | CPU/GPU liquid cooling, Direct Liquid Cooling manifolds, Server cooling solutions | Maximum thermal performance, Micro-channel designs, High heat flux handling |
Dispositifs médicaux | Laser/Imaging equipment cooling, Surgical tool cooling, Patient temperature management systems | Miniaturization, Biocompatibility (with coating), Geometric complexity |
Industrial & Energy | Process equipment (mold cooling), Power generation components, Welding/Laser head cooling, Renewable energy systems | Improved efficiency, Reduced cycle times, Durability, Complex flow paths |
Électronique grand public | High-end PC/Laptop liquid cooling, High-power LED cooling | Superior thermal performance, Design customization, Aesthetics |
Exporter vers les feuilles
The breadth of these applications underscores the universal challenge of thermal management and the transformative potential of combining advanced materials like copper alloys with the design freedom of metal 3D printing. For businesses needing bespoke thermal solutions, partnering with an experienced additive manufacturing provider like Met3dp ensures access to high-quality materials and process expertise required for these demanding applications.
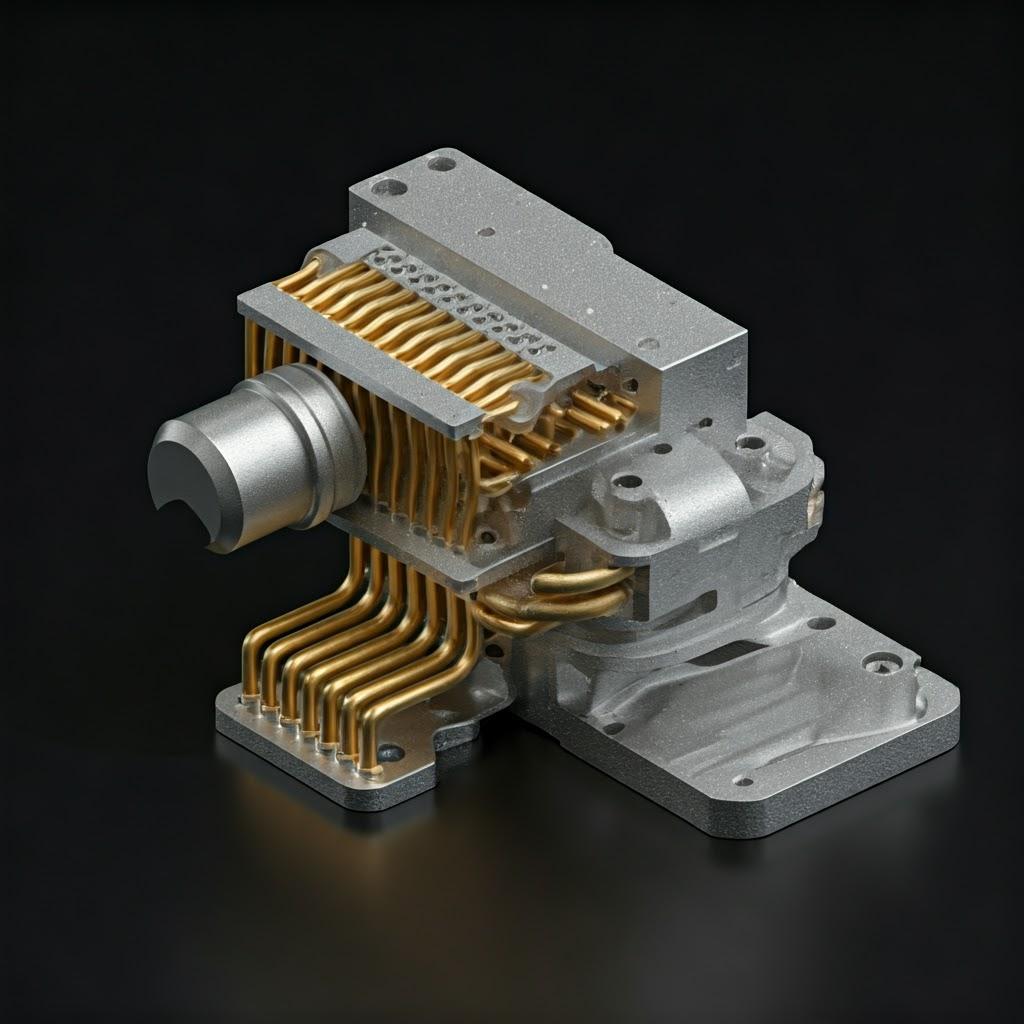
Unlocking Performance: Why Use Metal 3D Printing for Custom Heat Transfer Components?
While traditional manufacturing methods have served the industry well, metal additive manufacturing (AM) offers a compelling suite of advantages specifically beneficial for creating high-performance, custom heat transfer components, especially when using copper alloys. These benefits stem from the layer-by-layer fabrication process, which liberates designers from many constraints inherent in subtractive (machining) or formative (casting, stamping) techniques.
Procurement managers and engineers evaluating manufacturing options for thermal solutions should consider the following key advantages of metal AM:
1. Unparalleled Geometric Complexity:
- Intricate Internal Channels: AM excels at creating complex, freeform internal channels and flow paths within a monolithic part. This allows designers to route coolant precisely where it’s needed most, closely following the contours of heat-generating surfaces (conformal cooling). This minimizes thermal resistance and improves heat transfer efficiency dramatically compared to drilled or milled channels.
- Optimized Flow Paths: Fluid dynamics simulations (CFD) can be used to design highly optimized channel shapes that minimize pressure drop while maximizing heat transfer surface area. AM can accurately reproduce these complex geometries, including varying cross-sections, turbulators, and manifolds, which are often impossible or prohibitively expensive to machine.
- Lattice Structures and TPMS: AM enables the integration of lightweight, high-surface-area lattice structures or Triply Periodic Minimal Surfaces (TPMS) within heat transfer components. These structures can enhance convective heat transfer by promoting turbulence and increasing the wetted surface area, while also reducing overall component weight – a critical factor in aerospace and automotive applications.
2. Part Consolidation:
- Reduced Assembly Complexity: Traditional heat exchangers often involve multiple components (fins, tubes, manifolds, plates) that must be manufactured separately and then joined together (e.g., brazing, welding). Each joint represents a potential leak point and adds thermal resistance. Metal AM allows for the consolidation of these multiple parts into a single, monolithic component.
- Improved Reliability: Eliminating joints significantly enhances the component’s structural integrity and leak-proof reliability, which is crucial in high-pressure or critical applications.
- Simplified Supply Chain: Consolidating parts simplifies procurement, inventory management, and assembly processes.
3. Rapid Prototyping and Iteration:
- Accelerated Design Cycles: AM enables the rapid production of functional prototypes directly from CAD data. Engineers can quickly test different design variations (e.g., channel layouts, fin structures) and iterate towards an optimal solution much faster than with traditional methods that often require dedicated tooling.
- Reduced Tooling Costs: For low-to-medium volume production or highly customized parts, AM eliminates the need for expensive molds, dies, or fixtures associated with casting or stamping, making custom designs economically viable.
4. Enhanced Thermal Performance:
- Conformal Cooling: As mentioned, the ability to create cooling channels that conform precisely to the shape of the heat source maximizes contact area and minimizes the distance heat must travel, leading to significantly lower operating temperatures.
- Optimized Surface Area: Complex geometries like micro-channels, pin fins, and lattice structures maximize the surface area available for heat exchange within a given volume, boosting thermal performance.
- Material Proximity: High-conductivity copper can be placed exactly where needed, directly adjacent to heat sources, without the geometric limitations of machining from a solid block.
5. Material Efficiency and Waste Reduction:
- Near-Net Shape Manufacturing: AM is an additive process, building parts layer by layer, typically using only the material required for the final component plus necessary supports. This contrasts sharply with subtractive machining, where significant amounts of expensive raw material (especially copper) can be machined away as waste.
- Durabilité : Reduced material waste contributes to more sustainable manufacturing practices. Powder recyclability in processes like Laser Powder Bed Fusion (LPBF) further enhances material efficiency.
6. Lightweighting:
- Optimisation de la topologie : Software tools can optimize a part’s geometry to use material only where structurally necessary while meeting performance requirements. AM can fabricate these highly organic, optimized shapes, leading to significant weight reductions compared to traditionally manufactured parts.
- Internal Lattices: Incorporating internal lattice structures provides structural support while drastically reducing material usage and weight, ideal for weight-sensitive applications like aerospace and automotive.
Comparison: Metal AM vs. Traditional Manufacturing for Heat Transfer Components
Fonctionnalité | Fabrication additive métallique (AM) | Traditional Machining (CNC) | Traditional Casting/Brazing |
---|---|---|---|
Complexité géométrique | Very High (complex internal channels, lattices, freeform shapes) | Moderate (limited by tool access, straight channels) | Moderate (limited by mold design, draft angles) |
Canaux internes | Conformal, optimized shapes, micro-features possible | Typically straight, drilled/milled, access limitations | Possible but limited complexity, requires complex cores |
Consolidation partielle | High (multiple parts easily integrated into one) | Low (components made separately) | Moderate (brazing/welding required for assemblies) |
Vitesse de prototypage | Fast (direct from CAD, no tooling) | Moderate (requires programming, setup) | Slow (requires mold/pattern creation) |
Coût de l'outillage | None (tool-less manufacturing) | Low (standard tools) to High (custom fixtures) | High (mold/die costs) |
Déchets matériels | Low (near-net shape, powder recycling) | High (subtractive process) | Moderate (runners, gates) |
Exporter vers les feuilles
- Lead Time (Custom) | Short to Moderate | Moderate | Long (tooling lead time) |
- Optimal Volume | Prototypes, Low-to-Medium Volume, High Customization | Prototypes, Medium-to-High Volume | High Volume |
- Performance thermique | Potentially Highest (due to design freedom, conformal cooling) | Good, but limited by geometry | Good, but limited by geometry and joint resistance |
While metal AM offers significant advantages, it’s important to note that it may not always be the optimal choice for every application. High-volume production of simple designs might still favor traditional methods from a cost perspective. However, for applications demanding maximum thermal performance, miniaturization, complex geometries, or customization, metal 3D printing, particularly with copper alloys, presents a compelling value proposition. Companies like Met3dp leverage advanced méthodes d'impression like Selective Electron Beam Melting (SEBM) and Laser Powder Bed Fusion (LPBF), tailored for materials like copper, to realize these benefits for their clients.
Material Matters: Recommended Copper Alloys (CuCrZr, Cu) for 3D Printing High-Performance Heat Transfer Parts
The effectiveness of any heat transfer component hinges critically on the material’s properties, primarily its thermal conductivity. Copper stands out as one of the best thermal conductors among common engineering metals. However, pure copper presents challenges in metal 3D printing due to its high reflectivity and conductivity, which can interfere with laser or electron beam absorption and lead to process instabilities. Furthermore, pure copper is relatively soft and has lower mechanical strength.
To balance printability, mechanical properties, and thermal performance, specific copper alloys have emerged as preferred choices for additive manufacturing of heat transfer components. Met3dp, leveraging its expertise in advanced powder manufacturing via gas atomization and Plasma Rotating Electrode Process (PREP), produces high-quality, spherical powders ideal for AM processes. The two primary recommended copper materials are:
1. Pure Copper (Cu):
- Propriétés : Pure copper offers the highest thermal conductivity (approaching 400 W/m·K) and excellent electrical conductivity. It is highly ductile and corrosion-resistant in many environments.
- Challenges in AM: Its high reflectivity to infrared lasers used in LPBF makes stable processing difficult, often requiring green or blue lasers or specialized process parameters. High thermal conductivity can also lead to rapid heat dissipation away from the melt pool, potentially causing incomplete fusion or requiring high energy input. It is also relatively soft (low yield strength and hardness).
- AM Suitability: Despite challenges, advancements in machine technology (e.g., higher power lasers, optimized beam parameters, green lasers) and powder quality have made 3D printing of pure copper increasingly feasible, especially for applications where maximum thermal performance is the absolute priority and mechanical strength requirements are secondary. Electron Beam Melting (EBM/SEBM) can sometimes handle reflective materials like copper more readily than LPBF due to better energy absorption.
- Applications : Ideal for extreme heat flux applications like high-performance computing cold plates, specialized scientific equipment, and certain types of electrical conductors where some geometric complexity is needed.
2. Copper-Chromium-Zirconium Alloy (CuCrZr / C18150):
- Propriétés : CuCrZr is a precipitation-strengthened copper alloy. It strikes an excellent balance between high thermal conductivity (typically 300-340 W/m·K, lower than pure Cu but still excellent), good mechanical strength (significantly higher yield strength and hardness than pure Cu, especially after heat treatment), and good resistance to softening at elevated temperatures (up to around 500°C).
- Advantages in AM: CuCrZr generally offers better printability compared to pure copper in standard LPBF systems due to slightly lower reflectivity and conductivity, allowing for more stable melt pools and consistent layer fusion. Its higher strength makes it more suitable for components that experience mechanical stress or require structural integrity in addition to heat transfer.
- Traitement thermique : Post-print heat treatment (solution annealing followed by aging) is typically required to achieve the optimal combination of strength and conductivity in CuCrZr parts.
- Applications : Widely used for demanding applications requiring both excellent thermal management and good mechanical properties. Examples include:
- Rocket engine combustion chambers and nozzles
- High-performance heat exchangers and cold plates in aerospace and automotive
- Welding electrodes
- Induction heating coils
- Components for plastic injection molding requiring conformal cooling
- Heat sinks subjected to vibration or structural loads
Why Powder Quality Matters (Met3dp’s Advantage):
The success of 3D printing copper or its alloys heavily relies on the quality of the metal powder feedstock. Key powder characteristics include:
- Sphéricité : Highly spherical powder particles ensure good flowability, which is crucial for uniformly spreading thin layers in the powder bed fusion process. Poor flowability can lead to defects like porosity.
- Distribution de la taille des particules (PSD) : A controlled PSD ensures good packing density in the powder bed, contributing to fully dense final parts with predictable properties.
- La pureté : High purity and low oxygen content are essential. Impurities and oxides can degrade thermal and mechanical properties and negatively impact printability. Oxygen, in particular, can cause embrittlement.
- Internal Porosity: Powder particles themselves should be dense, without internal voids, to ensure the final printed part achieves maximum density.
Met3dp employs industry-leading powder production technologies like Vacuum Induction Melting Gas Atomization (VIGA) et le Procédé d'électrodes rotatives à plasma (PREP).
- Atomisation par gaz : This process uses high-pressure inert gas jets to break up a stream of molten metal into fine droplets, which solidify into spherical powder particles. Our unique nozzle and gas flow designs optimize for high sphericity and good flowability.
- PREP: This method uses a plasma torch to melt the tip of a rotating electrode made of the desired alloy. Centrifugal force ejects molten droplets that solidify in an inert atmosphere, yielding highly spherical powders with exceptional purity and minimal satellite particles.
By meticulously controlling these processes, Met3dp ensures its copper and CuCrZr powders possess the high sphericity, controlled PSD, high purity, and low internal porosity required for successful, high-quality metal additive manufacturing, enabling customers to reliably produce dense, high-performance heat transfer components.
Comparaison des propriétés des matériaux (valeurs typiques pour l'AM) :
Propriété | Pure Copper (Cu) – As Built | CuCrZr (C18150) – Heat Treated | Unités | Notes |
---|---|---|---|---|
Conductivité thermique | ~380 – 395 | ~300 – 340 | W/(m-K) | Cu offers maximum conductivity. CuCrZr is still excellent. |
Electrical Cond. | ~95 – 100 | ~80 – 85 | % IACS | Follows thermal conductivity trend. |
Limite d'élasticité (0.2%) | ~70 – 100 | ~350 – 450 | MPa | CuCrZr is significantly stronger, especially after heat treatment. |
Résistance à la traction | ~200 – 240 | ~450 – 550 | MPa | CuCrZr exhibits much higher ultimate strength. |
Dureté | ~40 – 60 | ~130 – 170 | HT | CuCrZr is considerably harder. |
Allongement à la rupture | ~30 – 50 | ~10 – 20 | % | Pure Cu is more ductile. |
Densité | 8.96 | 8.89 | g/cm³ | Similar densities. |
Point de fusion | 1084 | ~1080 | °C | Similar melting points. |
Max Service Temp. | Low (softens easily) | ~500 | °C | CuCrZr retains strength better at elevated temperatures. |
Imprimabilité (LPBF) | Défi | Modéré | – | Requires optimized parameters/machines for Cu; CuCrZr is generally easier. |
Exporter vers les feuilles
Choosing Between Cu and CuCrZr:
The choice between pure Copper and CuCrZr depends heavily on the specific application requirements:
- Choose Pure Copper (Cu) if:
- Absolute maximum thermal or electrical conductivity is the primary driver.
- Mechanical strength and resistance to softening at high temperatures are less critical.
- The AM service provider has demonstrated capability and optimized processes for pure copper printing.
- Choose CuCrZr if:
- A combination of very high thermal conductivity et good mechanical strength/hardness is required.
- The component will operate at elevated temperatures where pure copper would soften.
- Improved printability and process stability are desired compared to pure copper.
- The component needs to withstand mechanical loads, pressure, or vibrations.
By understanding the unique properties and trade-offs of these materials, and partnering with a supplier like Met3dp that offers high-quality powders and processing expertise, engineers and procurement managers can confidently select the optimal copper alloy for their 3D printed custom heat transfer components.
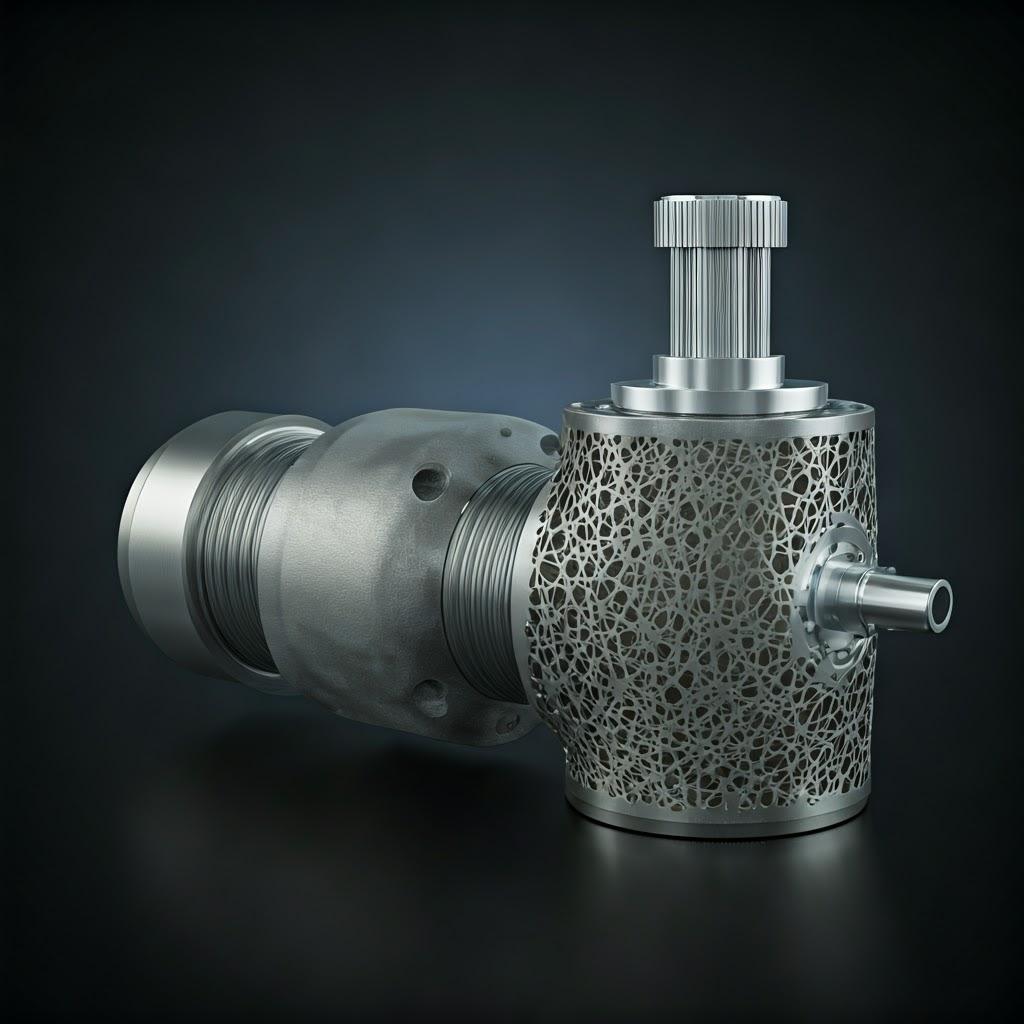
Design for Additive Manufacturing (DfAM): Optimizing Heat Exchangers and Cold Plates for 3D Printing
Simply replicating a traditionally designed heat transfer component using metal 3D printing often fails to leverage the technology’s true potential and can even lead to manufacturing challenges. To fully exploit the advantages of additive manufacturing (AM) for copper and CuCrZr heat exchangers, cold plates, and other thermal components, engineers must adopt a Conception pour la fabrication additive (DfAM) approach. DfAM involves rethinking component design from the ground up, considering both the unique capabilities and the specific constraints of the chosen AM process (like Laser Powder Bed Fusion – LPBF or Selective Electron Beam Melting – SEBM). Applying DfAM principles is crucial for optimizing thermal performance, minimizing weight, reducing manufacturing costs and lead times, and ensuring component reliability.
For engineers and procurement teams sourcing custom heat transfer solutions, understanding DfAM is key to collaborating effectively with AM service providers like Met3dp. Here are critical DfAM considerations for 3D printed copper heat transfer components:
1. Leveraging Geometric Freedom for Thermal Performance:
- Canaux de refroidissement conformes : This is arguably the most significant advantage. Design channels that precisely follow the contours of the heat source or the external shape of the component. This minimizes the conduction path length and maximizes the heat transfer area where it’s most needed, drastically outperforming straight, drilled channels.
- Complex Internal Geometries: Design intricate channel paths, manifolds, and flow distributors integrated directly into the component. Utilize computational fluid dynamics (CFD) simulations early in the design phase to optimize channel cross-sections (circular, rectangular, tear-drop), incorporate turbulators (features that disrupt laminar flow to enhance heat transfer), and balance flow distribution across parallel channels to prevent hot spots and minimize pressure drop.
- Micro-channel Heat Sinks: AM can create extremely fine features, enabling the design of micro-channel cold plates (channels with hydraulic diameters typically less than 1 mm). These offer exceptionally high surface area-to-volume ratios, ideal for dissipating very high heat fluxes, common in power electronics and laser diodes. Careful consideration must be given to pressure drop and potential clogging.
- Triply Periodic Minimal Surfaces (TPMS) and Lattices: Integrate TPMS structures (like Gyroid, Schwarz-P) or lattice structures within fluid channels or as extended surfaces (fins). These complex, mathematically defined surfaces offer very high surface area-to-volume ratios and can significantly enhance convective heat transfer coefficients by promoting mixing and turbulence. They also provide structural support while minimizing weight. Selecting the appropriate unit cell type, size, and strut/wall thickness is critical for balancing thermal performance, pressure drop, and manufacturability.
2. Designing for Manufacturability (Process Constraints):
- Angles autoportants : Powder bed fusion processes require support structures for overhanging features typically below a certain angle (often around 45 degrees from the horizontal build plane). Design internal channels and external features with self-supporting angles wherever possible to minimize the need for supports, which can be difficult and costly to remove, especially from internal channels. Using diamond, teardrop, or keyhole channel cross-sections can facilitate self-support.
- Épaisseur minimale de la paroi : AM processes have limitations on the minimum producible wall thickness, influenced by the material, laser/electron beam spot size, and powder characteristics. For copper alloys, this might typically be in the range of 0.3 mm to 0.5 mm, although thinner walls may be possible with careful process control. Ensure designs respect these limits to prevent incomplete formation or failure. Thin walls in heat exchangers maximize thermal transfer but must also withstand operating pressures.
- Support Structure Strategy: When supports are unavoidable, design the component to facilitate their removal. Provide access points for tools or chemical etching if needed. Minimize supports on critical surfaces or within complex internal channels. Sometimes, breakaway support designs or specific materials (in multi-material systems, though less common for copper) can help. Close collaboration with the AM provider, like Met3dp, is essential for optimizing support strategy.
- Elimination des poudres : Trapped powder within intricate internal channels is a significant concern. Design incorporates features that facilitate powder removal after printing, such as appropriately sized inlet/outlet ports, smooth internal transitions, and avoiding dead-end cavities. Consider vibration, compressed air, or fluid flushing during post-processing. Include inspection ports if feasible.
- Orientation Optimization: The orientation of the part on the build plate significantly impacts surface finish, the need for supports, residual stress accumulation, and potentially anisotropic material properties. Design parts with consideration for the optimal build orientation, often involving trade-offs between these factors.
- Feature Resolution: Understand the minimum feature size (e.g., hole diameter, slot width) achievable with the chosen process and material. Avoid features smaller than this resolution limit.
3. Part Consolidation and Integration:
- Think beyond single components. Can multiple parts of a thermal management system (e.g., cold plate, manifold, mounting bracket) be combined into a single, monolithic 3D printed part? This reduces assembly time, weight, potential leak points, and inventory complexity.
- Integrate mounting features, sensor ports, or fluid connectors directly into the 3D printed design.
4. Lightweighting Strategies:
- Optimisation de la topologie : Use software tools to optimize the material distribution within a component based on structural loads and thermal performance requirements. This often results in organic-looking shapes that place material only where needed, drastically reducing weight while maintaining or even improving performance. This is highly valuable in aerospace and automotive sectors.
- Lattice Infill: Replace solid sections of the component (where high conductivity isn’t paramount) with internal lattice structures to reduce mass while maintaining stiffness.
5. Designing for Post-Processing:
- If specific surfaces require high precision or smooth finishes (e.g., mating surfaces, sealing faces), add extra stock material in the design to allow for post-print CNC machining.
- Consider how heat treatments (like aging for CuCrZr) might affect dimensional stability and incorporate allowances if necessary.
- Ensure the design allows for inspection access, such as leak testing ports or line-of-sight for visual or endoscopic inspection of internal channels.
DfAM Principles Summary Table:
Principe du DfAM | Key Considerations for Copper Heat Transfer Components | Benefit(s) |
---|---|---|
Leverage Geometry | Conformal channels, optimized flow paths (CFD-driven), micro-channels, TPMS/lattices | Maximized thermal performance, reduced pressure drop, higher heat flux capability |
Self-Supporting Design | Optimize overhang angles (>45°), use specific channel shapes (diamond, teardrop) | Reduced support needs, easier post-processing, lower cost |
Wall Thickness/Features | Respect minimum manufacturable wall thickness and feature size | Ensures part integrity, prevents print failures |
Support Strategy | Design for access, minimize internal supports, collaborate with AM provider | Facilitates removal, reduces risk of damage, lowers cost |
Retrait des poudres | Include access ports, design smooth transitions, avoid dead-end cavities | Ensures channel clearance, prevents contamination, guarantees performance |
Build Orientation | Consider impact on supports, surface finish, anisotropy, residual stress | Optimizes print success, cost, and final part properties |
Consolidation partielle | Integrate multiple functions/parts (manifolds, brackets) into one monolithic design | Reduced assembly, weight, leak points; simplified logistics |
Allègement | Utilize topology optimization and lattice structures/infill | Significant weight reduction (aerospace, automotive), material savings |
Design for Post-Pro | Add machining stock, consider heat treatment effects, design for inspection access | Ensures final specifications are met (tolerance, finish), facilitates QA |
Exporter vers les feuilles
Successfully implementing DfAM requires a collaborative approach between the design engineers and the additive manufacturing experts. Providers like Met3dp offer DfAM consultation, leveraging their deep understanding of copper AM processes and materials to help clients optimize their heat transfer component designs for production, ensuring they harness the full potential of metal 3D printing technology.
Precision and Performance: Achievable Tolerances, Surface Finish, and Thermal Efficiency
While metal 3D printing unlocks unparalleled design freedom, potential users, especially procurement managers and engineers focused on quality control, need realistic expectations regarding the achievable precision, surface characteristics, and resulting thermal performance of additively manufactured copper components. These factors are intrinsically linked and influenced by the AM process (LPBF, SEBM), machine calibration, process parameters, material (Cu vs. CuCrZr), part geometry, and post-processing steps.
1. Dimensional Accuracy and Tolerances:
- Typical Achievable Tolerances: As a general guideline, for well-controlled LPBF or SEBM processes printing copper alloys, typical dimensional accuracy might fall within the range of ±0.1 mm to ±0.2 mm for smaller features (e.g., up to 50-100 mm), and potentially ±0.1% to ±0.2% of the nominal dimension for larger parts. However, this can vary significantly.
- Facteurs influençant la précision :
- Étalonnage de la machine : Regular calibration of the scanner system, laser/electron beam focus, and build platform leveling is crucial.
- Paramètres du processus : Laser/beam power, scan speed, layer thickness, and hatch strategy directly impact melt pool dynamics and solidification, affecting shrinkage and final dimensions. Optimized parameters for copper are essential.
- Effets thermiques : Copper’s high thermal conductivity can lead to significant heat buildup and dissipation challenges during the build, potentially causing warping or distortion, especially in large or complex parts. Build strategy (scan pattern, support placement) plays a role in mitigating this.
- Géométrie de la pièce : Large flat surfaces, thin unsupported walls, and sharp transitions can be more prone to deviation.
- Orientation: Dimensions along the Z-axis (build direction) may have slightly different accuracy compared to the X-Y plane.
- Obtenir des tolérances plus strictes : For critical features requiring tolerances tighter than the standard AM process capability (e.g., sealing surfaces, bearing interfaces, alignment features), it’s common practice to design the part with extra material (“machining stock” or “offset”) in those areas and use post-print CNC machining to achieve the required precision. Tolerances of ±0.01 mm to ±0.05 mm are readily achievable with machining.
- Normes : While universal AM tolerance standards are still evolving, referencing general standards like ISO 2768 (medium or fine class for non-critical features) or defining specific Geometric Dimensioning and Tolerancing (GD&T) callouts on drawings based on achievable AM capabilities (often discussed with the provider) is recommended.
2. Surface Finish (Roughness):
- Rugosité de la surface telle que construite : Powder bed fusion processes inherently produce parts with a noticeable surface roughness due to the partially melted powder particles adhering to the surface and the layer-wise building process.
- Top Surfaces: Generally smoother, often Ra 5-15 µm.
- Vertical Walls (X-Y Plane): Typically exhibit roughness related to layer lines, often Ra 8-20 µm.
- Upward-Facing Sloped/Curved Surfaces: Similar to vertical walls or slightly rougher.
- Downward-Facing (Overhanging/Supported) Surfaces: Tend to be the roughest due to contact with support structures or the “stair-stepping” effect, potentially Ra 15-30 µm or higher.
- Impact on Performance:
- Fluid Flow: Rough internal channel surfaces increase turbulence near the wall and can significantly increase pressure drop compared to smooth, machined channels, especially in micro-channels. This needs to be accounted for in hydraulic design (pump sizing). However, increased turbulence can sometimes slightly enhance convective heat transfer, creating a trade-off.
- Thermal Contact Resistance: Rough mating surfaces create fewer actual contact points, trapping air or interface fluid in the valleys. This increases thermal resistance at interfaces (e.g., between a cold plate and the component being cooled), reducing overall heat transfer efficiency. Improving surface finish on critical contact areas is often necessary.
- Amélioration de l'état de surface : Various post-processing techniques can significantly improve the as-built surface finish:
- Abrasive Blasting (Bead/Sand Blasting): Provides a uniform matte finish, removes loose powder, but typically only slightly improves Ra values (e.g., to Ra 5-10 µm).
- Tumbling/Mass Finishing: Can smooth external surfaces and edges, particularly for smaller parts (e.g., achieving Ra 1-5 µm).
- Usinage CNC : Offers the best control for achieving smooth, precise surfaces on specific features (Ra < 1 µm possible).
- Polissage (manuel ou automatisé) : Can achieve very smooth, mirror-like finishes (Ra << 1 µm) but is often labor-intensive.
- Électropolissage : An electrochemical process that preferentially removes material from peaks, resulting in a very smooth, clean surface (Ra < 1 µm possible), often suitable for internal channels if flow can be established.
3. Thermal Efficiency and Validation:
- Intrinsic Material Properties: The primary factor determining potential thermal performance is the bulk thermal conductivity of the 3D printed and post-processed copper alloy. Achieving near-full density (>99.5%) during printing is crucial, as porosity significantly degrades conductivity. Met3dp focuses on high-quality powders and optimized processes to maximize density. Heat treatment (especially for CuCrZr) is also critical for optimizing conductivity.
- Impact of Design: As discussed under DfAM, the complex geometries enabled by AM (conformal channels, TPMS, micro-features) allow for designs that maximize heat transfer area and minimize thermal resistance, leading to potentially higher thermal efficiency than traditionally manufactured parts of the same volume or weight.
- Surface Roughness Effects: While rough internal surfaces might slightly enhance turbulence, the increased pressure drop and potential impact on thermal boundary layer development must be considered. Smooth surfaces are generally preferred for minimizing pressure loss. Smooth contact surfaces are critical for reducing interface resistance.
- Validation: Predicting the exact thermal performance of complex AM designs can be challenging.
- CFD Simulation: Used extensively during design to estimate fluid flow and heat transfer characteristics.
- Experimental Testing: Building and testing functional prototypes under realistic operating conditions (measuring temperatures, flow rates, pressure drops) is the ultimate validation method. Thermal imaging can help identify hot spots.
- Material Property Testing: Verifying the thermal conductivity and mechanical properties of printed samples through laboratory testing ensures the material meets specifications.
Summary Table: Precision and Surface Finish
Paramètres | Typical As-Built (LPBF/SEBM Copper) | Post-Processed (Examples) | Principales considérations |
---|---|---|---|
Dimensional Acc. | ±0.1 to ±0.2 mm or ±0.1-0.2% | Machining: ±0.01 to ±0.05 mm | Machine capability, thermal effects, geometry, orientation. Use machining for critical dims. |
Rugosité de la surface (Ra) | 5-30+ µm (varies by orientation) | Machining/Polishing: <1 µm possible | Impacts fluid dynamics (pressure drop) and thermal contact resistance. |
Achievable Density | >99.5% (with optimized process) | N/A (inherent to printing) | Crucial for thermal conductivity and mechanical properties. |
Exporter vers les feuilles
By understanding these achievable characteristics and planning for necessary post-processing steps like machining, engineers can confidently design and procure 3D printed copper heat transfer components that meet demanding performance and quality requirements. Consulting with experienced providers like Met3dp helps set realistic expectations and develop appropriate finishing and validation strategies.
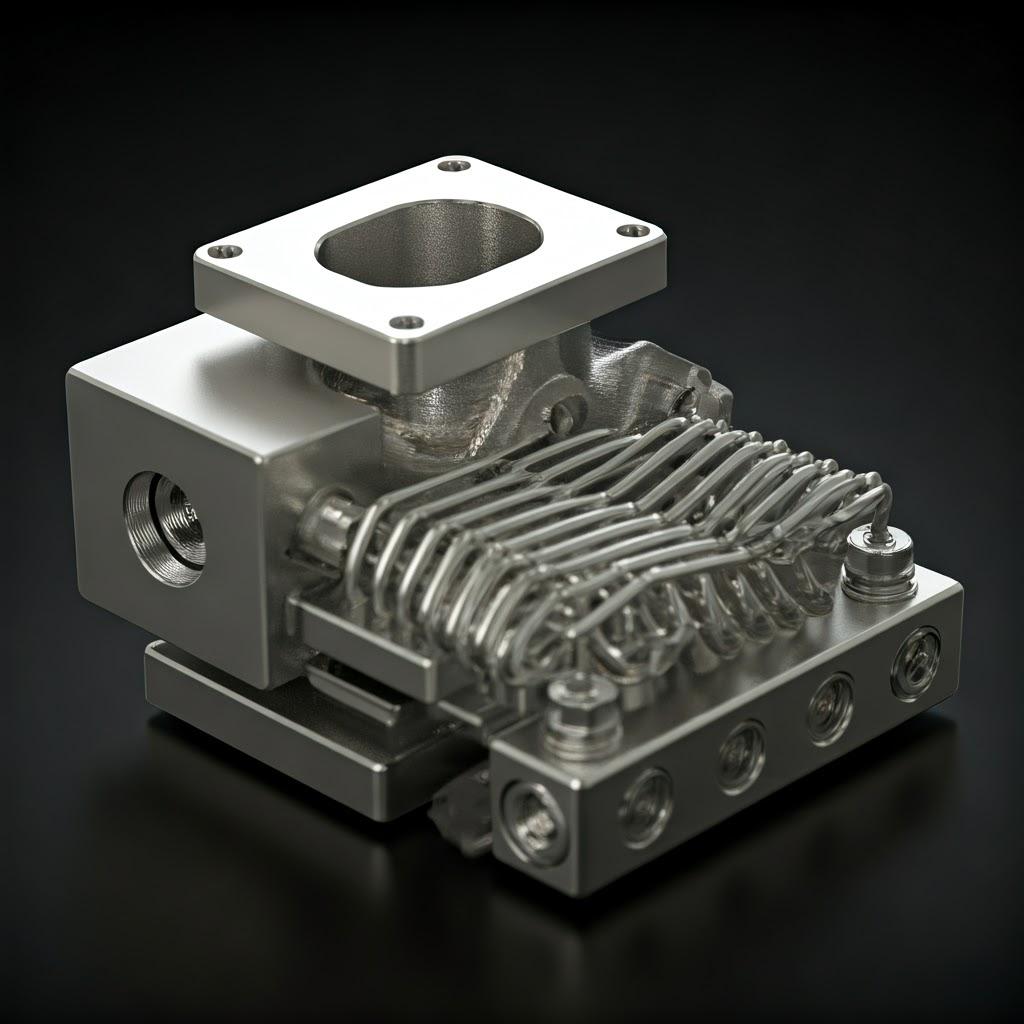
Beyond the Print: Essential Post-Processing Steps for 3D Printed Copper Components
Producing a part on a metal 3D printer is rarely the final step in the manufacturing workflow, especially for demanding applications like heat transfer components made from copper alloys. A series of post-processing steps are typically required to transform the as-built part into a functional, reliable component that meets all engineering specifications. These steps are crucial for relieving stress, achieving desired material properties, removing temporary structures, ensuring cleanliness, attaining required tolerances and surface finishes, and verifying quality. Procurement managers should factor these steps into project timelines and costs when sourcing AM parts.
Here’s a breakdown of common and essential post-processing stages for 3D printed copper and CuCrZr components:
1. Stress Relief:
- Objet : The rapid heating and cooling cycles inherent in powder bed fusion processes create significant residual stresses within the printed part. These stresses can cause distortion during or after removal from the build plate, reduce fatigue life, and potentially lead to cracking. Stress relief heat treatment, typically performed while the part is still attached to the build plate, is often the first step.
- Processus : Involves heating the part in a controlled atmosphere furnace (inert gas like Argon or Nitrogen, or vacuum to prevent oxidation) to a specific temperature (below the aging temperature for CuCrZr), holding it for a period, and then slowly cooling it down. Exact parameters depend on the alloy and part geometry.
2. Removal from Build Plate:
- Processus : Once stress-relieved (if necessary), the part needs to be separated from the metal build plate it was printed on. This is typically done using wire Electrical Discharge Machining (EDM), sawing, or sometimes milling/grinding. Care must be taken to avoid damaging the part.
3. Heat Treatment (Solution Annealing and Aging for CuCrZr):
- Objet : For precipitation-hardening alloys like CuCrZr (C18150), heat treatment is essential to develop the desired high strength and optimize thermal/electrical conductivity. Pure copper typically doesn’t require this strengthening heat treatment but may benefit from annealing for maximum conductivity or ductility if needed.
- Process (CuCrZr):
- Recuit de la solution : Heating the part to a high temperature (e.g., ~950-1000°C) to dissolve the chromium and zirconium precipitates into the copper matrix, followed by rapid quenching (usually in water). This creates a supersaturated solid solution.
- Aging (Precipitation Hardening): Reheating the quenched part to a lower temperature (e.g., ~450-500°C) and holding it for a specific duration (typically several hours). This allows fine precipitates of Cr and Zr to form within the copper matrix, obstructing dislocation movement and significantly increasing hardness and strength. This process also slightly lowers conductivity compared to the pure state but provides the best balance for many applications.
- Atmosphere Control: These treatments must be performed in a controlled atmosphere (vacuum or inert gas) to prevent oxidation, which would degrade surface quality and potentially material properties.
4. Support Structure Removal:
- Objet : Support structures are necessary during printing for overhangs and complex features but must be removed afterward.
- Challenges with Copper: Copper’s ductility and toughness can make support removal more challenging than with harder alloys. Supports tend to deform rather than break cleanly. The high thermal conductivity can also lead to stronger bonding between the support and the part.
- Méthodes :
- Suppression manuelle : Using pliers, grinders, chisels, etc. Labor-intensive and requires skill to avoid damaging the part surface. Often the primary method for accessible supports.
- Usinage CNC : Can be used to precisely remove supports from accessible areas or create access points.
- EDM : Sometimes used for intricate or hard-to-reach supports.
- Chemical Etching: Less common for copper supports but potentially feasible with specific chemistries in controlled environments.
- Design Impact: DfAM plays a huge role here – designing for minimal, accessible supports is crucial.
5. Powder Removal (Depowdering):
- Objet : Removing all unfused powder particles, especially from internal channels and complex cavities, is critical for the functionality of heat transfer components. Trapped powder can obstruct flow, reduce thermal performance, and act as contamination.
- Méthodes : Compressed air blowing, vibration tables, ultrasonic cleaning baths, fluid flushing. Access ports designed into the part are essential. For highly complex internal networks, extensive effort may be required. Verification (e.g., endoscopy, CT scanning) might be necessary.
6. Surface Finishing:
- Objet : To achieve the required surface roughness for fluid dynamics (managing pressure drop), thermal contact resistance (at interfaces), or aesthetics.
- Methods (as detailed previously): Abrasive blasting, tumbling, machining, manual/automated polishing, electropolishing. The choice depends on the specific requirements (Ra value, location) and component geometry. Machining is common for critical interfaces.
7. CNC Machining for Critical Tolerances:
- Objet : As mentioned, achieving high precision on specific features often requires post-print machining.
- Processus : Using milling, turning, or grinding operations to bring features like sealing surfaces, mounting holes, fluid ports, or contact pads to their final dimensions and tolerances specified in the engineering drawing.
8. Cleaning and Inspection:
- Cleaning: Thorough cleaning to remove any residual powder, machining fluids, or contaminants before final inspection and assembly.
- Inspection (Quality Assurance):
- Inspection dimensionnelle : Using calipers, micrometers, Coordinate Measuring Machines (CMMs), or 3D scanners to verify dimensions and GD&T callouts.
- Surface Finish Measurement: Using profilometers.
- Essais non destructifs (END) :
- Visual/Endoscopic Inspection: For external surfaces and accessible internal channels.
- Tomodensitométrie (CT) : Increasingly used to inspect internal geometries, check for trapped powder, and detect internal defects like porosity or cracks non-destructively.
- Pressure/Leak Testing: Essential for heat exchangers and fluid-carrying components to ensure integrity under operating pressure. Dye penetrant testing can also find surface-breaking defects.
- Material Property Verification: Testing samples printed alongside the main part to confirm density, hardness, tensile properties, or thermal conductivity meet specifications.
Intégration des flux de travail :
These post-processing steps require careful planning and often specialized equipment and expertise. Companies like Met3dp, while specializing in printing and powder production, understand the importance of this downstream chain. Through robust internal processes or partnerships with qualified finishing and inspection providers, they can help ensure that the final component delivered meets all requirements. Discussing post-processing needs early in the engagement is crucial for accurate quoting and project planning.
Navigating Complexity: Overcoming Common Challenges in 3D Printing Copper Heat Transfer Parts
Additive manufacturing of copper and its alloys, particularly for intricate heat transfer components, presents unique challenges stemming from the material’s inherent physical properties and the complexities of the powder bed fusion process. Awareness of these potential hurdles allows engineers, procurement teams, and AM providers to proactively implement mitigation strategies, ensuring successful outcomes and reliable parts.
1. Process Stability and Parameter Optimization:
- Défi: Copper’s high reflectivity to infrared wavelengths (used in most standard LPBF machines) and high thermal conductivity make it difficult to achieve stable, consistent melting. The laser energy can be reflected rather than absorbed, and the absorbed heat dissipates very quickly. This can lead to insufficient melting, melt pool instability, balling (formation of spherical droplets instead of a continuous track), and high porosity.
- Atténuation :
- Optimized Laser Parameters: Using higher laser power, specific pulse shaping, adjusted scan speeds, and optimized hatch strategies tailored for copper.
- Advanced Laser Types: Employing green lasers (around 515 nm wavelength), which have significantly higher absorption rates in copper compared to infrared lasers, leading to more stable processing.
- Electron Beam Melting (SEBM): EBM uses an electron beam, which couples energy more effectively with reflective materials like copper compared to infrared lasers. The process also occurs at elevated temperatures in a vacuum, reducing thermal gradients and residual stress. Met3dp’s expertise may include SEBM capabilities suitable for such materials.
- Qualité de la poudre : Using high-quality powder with appropriate morphology and surface characteristics can slightly improve absorption.
- Surveillance des processus : In-situ monitoring tools (melt pool monitoring, thermal imaging) can help track stability and potentially allow for real-time adjustments.
2. Porosity:
- Défi: Achieving near-full density (>99.5%, ideally >99.9%) is critical for thermal conductivity and mechanical integrity. Porosity can arise from incomplete fusion (due to process instability), gas entrapment (from dissolved gases in the powder or shielding gas), or keyholing (vapor depression collapse at excessive energy densities).
- Atténuation :
- Optimisation des paramètres : Finding the right balance of laser power, scan speed, hatch spacing, and layer thickness is crucial to create a stable melt pool that fully fuses the powder without excessive vaporization. Extensive process development is required.
- Poudre de haute qualité : Using powder with low internal gas porosity and low oxygen content minimizes potential gas sources. Met3dp’s advanced atomization techniques (VIGA, PREP) are designed to produce such high-quality powders.
- Controlled Atmosphere: Maintaining a high-purity inert gas atmosphere (Argon, Nitrogen) or vacuum (in SEBM) minimizes oxidation and interaction with atmospheric gases.
- Pressage isostatique à chaud (HIP) : A post-processing step where the part is subjected to high temperature and high isostatic pressure. HIP can effectively close internal pores (if not surface-connected), significantly increasing density. However, it adds cost and lead time.
3. Cracking:
- Défi: High thermal gradients during printing can lead to significant residual stress. In combination with material properties or impurities, this stress can sometimes cause cracking, either during the build (hot cracking) or afterward (cold cracking). Alloys can sometimes be more susceptible than pure copper.
- Atténuation :
- Gestion thermique : Using build plate heating (common in LPBF, inherent in SEBM) reduces thermal gradients. Optimized scan strategies (e.g., island scanning, rotating layers) can distribute heat more evenly.
- Soulagement du stress : Performing stress relief heat treatment immediately after printing, often before support removal, is critical.
- Parameter Control: Avoiding excessive energy input that could lead to localized overheating and stress.
- Design Optimization (DfAM): Avoiding sharp internal corners, using fillets/radii, and managing large changes in cross-section can reduce stress concentrations.
4. Residual Stress and Warping:
- Défi: Even if cracking doesn’t occur, residual stresses can cause significant warping or distortion, especially after the part is removed from the build plate or during support removal. This impacts dimensional accuracy. Large, flat sections or asymmetric designs are particularly prone.
- Atténuation :
- Structures de soutien robustes : Using well-designed support structures to anchor the part firmly to the build plate during printing.
- Build Plate Heating: Reduces temperature differences.
- Optimized Scan Strategy: Distributes heat input to minimize localized stress buildup.
- Traitement thermique anti-stress : Essential for relaxing stresses before dimensional changes occur.
- Considérations relatives à la conception : Symmetry, gradual thickness changes, and potentially adding sacrificial stiffening features (removed later) can help.
5. Support Structure Removal:
- Défi: As mentioned in post-processing, copper’s ductility makes supports difficult to remove cleanly without damaging the part surface. Internal supports are particularly problematic.
- Atténuation :
- DfAM for Self-Support: Prioritize designing parts to be self-supporting as much as possible.
- Conception optimisée du support : Using supports with lower density, specific interface layers designed for easier separation, or strategically placed large structures that are easier to access and machine off. Collaboration with the AM provider is key.
- Appropriate Removal Techniques: Combining manual, machining, and potentially EDM methods based on accessibility and required surface finish.
6. Powder Handling and Oxidation:
- Défi: Fine copper powder is susceptible to oxidation when exposed to air, especially at elevated temperatures or high humidity. Oxides can negatively impact printability (affecting laser absorption, flowability) and final part properties (reduced conductivity, potential embrittlement). Handling requires care to avoid contamination.
- Atténuation :
- Inert Atmosphere Handling: Storing and handling powder under inert gas (Argon, Nitrogen) as much as possible.
- Controlled Environment: Maintaining low humidity in powder handling areas.
- Gestion du cycle de vie des poudres : Tracking powder usage, recycling protocols (sieving, potential rejuvenation), and testing to ensure quality is maintained over time. Met3dp’s integrated powder production and printing services ensure tight control over powder quality.
7. Ensuring Consistent Material Properties and Performance:
- Défi: Minor variations in powder batches, machine calibration, or process parameters can potentially lead to variations in density, microstructure, mechanical properties, and thermal conductivity between builds or even within a single large part.
- Atténuation :
- Un contrôle de qualité rigoureux : Strict control over incoming powder quality, regular machine maintenance and calibration, and standardized, validated process parameters.
- Surveillance des processus : Using in-situ monitoring to detect deviations during the build.
- Test des matériaux : Regularly printing and testing witness coupons alongside production parts to verify material properties meet specifications.
- Performance Validation: Functional testing of final components (thermal cycling, pressure testing, flow testing) to confirm performance.
Overcoming these challenges requires a combination of advanced machine capabilities, high-quality materials, optimized process parameters developed through rigorous experimentation, robust quality control procedures, and skilled engineering and operational expertise. Partnering with a knowledgeable and experienced metal AM provider like Met3dp, which possesses deep expertise specifically in materials like copper and related impression 3D de métaux technologies, significantly increases the likelihood of success for complex heat transfer applications.

Choosing Your Partner: Selecting the Right Metal AM Service Provider for Copper Components
The success of your custom heat transfer project heavily relies not only on the design and material but also on the capabilities and expertise of your chosen additive manufacturing (AM) service provider. Printing copper alloys presents unique challenges, as discussed previously, making supplier selection even more critical than for more common AM materials like stainless steel or titanium. For procurement managers and engineering teams evaluating potential partners, a thorough assessment based on specific criteria is essential.
Here’s what to look for when selecting a metal AM service provider for your copper or CuCrZr heat transfer components:
1. Demonstrated Expertise in Copper Alloy Printing:
- Historique : Does the provider have proven experience specifically with 3D printing pure copper and/or CuCrZr? Ask for case studies, sample parts, or data demonstrating their success with these materials. Copper requires specialized knowledge beyond standard AM practices.
- Understanding of Challenges: Are they knowledgeable about the challenges (reflectivity, conductivity, porosity, stress) and the mitigation strategies required for copper? Can they discuss parameter optimization, thermal management, and quality control specific to these materials?
- Application Knowledge: Do they understand the unique demands of heat transfer applications? Can they offer insights related to thermal performance, fluid dynamics, and relevant industry standards?
2. Appropriate Equipment and Technology:
- Capacités de la machine : Do they operate machines suitable for copper? This might include:
- LPBF systems equipped with high-power infrared lasers and optimized parameters specifically developed for copper.
- LPBF systems using green lasers (highly advantageous for pure copper due to better absorption).
- Selective Electron Beam Melting (SEBM) systems, which often handle reflective, high-conductivity materials well.
- Machine Maintenance and Calibration: Ensure they have rigorous procedures for machine maintenance and calibration to guarantee consistency and accuracy.
3. Material Quality and Handling Expertise:
- Powder Sourcing and Quality Control: Do they source high-quality copper/CuCrZr powders specifically designed for AM? What are their quality control procedures for incoming powder (e.g., verifying sphericity, PSD, purity, flowability)? Providers like Met3dp, who manufacture their own poudres métalliques à haute performance using advanced methods like PREP and gas atomization, offer significant advantages in controlling material quality from the source.
- Powder Handling Procedures: Do they have established protocols for storing, handling, loading, and recycling copper powders under controlled atmospheres to prevent oxidation and contamination?
4. Comprehensive Post-Processing Capabilities:
- In-House vs. Outsourced: Does the provider offer essential post-processing steps in-house (stress relief, heat treatment for CuCrZr, support removal, basic finishing), or do they manage a network of trusted partners?
- Specialized Services: Can they facilitate or perform required CNC machining for critical tolerances, advanced surface finishing (polishing, electropolishing), HIP (if needed), and rigorous cleaning procedures? Having integrated post-processing simplifies the supply chain and ensures accountability.
5. Robust Quality Management System and Certifications:
- Certifications de qualité : Are they certified to relevant quality standards, such as ISO 9001 (General Quality Management)? For specific industries, certifications like AS9100 (Aerospace) or ISO 13485 (Medical Devices) might be required or highly desirable, demonstrating a commitment to stringent quality protocols. Met3dp prides itself on industry-leading quality standards, reflected in our operations and customer partnerships. You can learn more about our company’s commitment on our Page À propos de nous.
- Process Control and Documentation: Do they have documented procedures for process control, traceability (from powder batch to final part), inspection, and non-conformance handling?
6. Engineering and DfAM Support:
- Approche collaborative : Are they willing to collaborate closely with your design team? Do they offer Design for Additive Manufacturing (DfAM) consultation to help optimize your heat transfer component for printability, performance, and cost-effectiveness? This upfront collaboration is invaluable.
- Expertise technique : Does their team include materials scientists, AM process engineers, and manufacturing specialists who can provide expert guidance?
7. Capacity, Lead Time, and Communication:
- Capacité de production : Can they accommodate your required production volume, whether it’s prototypes or small-to-medium series production, within reasonable timelines?
- Realistic Lead Times: Do they provide clear and realistic lead time estimates that account for printing, post-processing, and quality assurance steps?
- Communication and Transparency: Do they maintain open communication throughout the project lifecycle? Are they transparent about potential challenges and their mitigation plans?
Evaluation Checklist for Potential Copper AM Providers:
Critères | Key Questions to Ask | Why It Matters for Copper Heat Transfer |
---|---|---|
Copper Expertise | Can you show examples/data of successful Cu/CuCrZr prints? How do you manage copper’s reflectivity/conductivity? | Specific process knowledge is essential for quality & density. |
Equipement | What machines do you use for copper? (LPBF-IR, LPBF-Green, SEBM?) How are they calibrated? | Ensures stable processing & consistent results. |
Material Quality & Handling | Where do you source powder? What’s your QC? How do you prevent oxidation/contamination? | High-quality, well-handled powder is fundamental for good prints & properties. |
Post-traitement | What steps are done in-house (heat treat, machining, finishing)? How do you manage outsourced services? | Ensures parts meet final specs (properties, tolerance, finish); simplifies logistics. |
Quality System/Certs | Are you ISO 9001 / AS9100 / ISO 13485 certified? Can we review your QC procedures? | Demonstrates commitment to quality, process control, and traceability. |
Soutien technique | Do you offer DfAM consultation? What level of technical support is available? | Optimizes design for AM, improves performance, potentially reduces cost. |
Capacity & Lead Time | What is your capacity for copper printing? What are typical lead times for prototypes/series? | Ensures project timelines can be met. |
Communication & Transparency | Who is the point of contact? How are project updates provided? How are issues handled? | Facilitates smooth project execution & problem-solving. |
Exporter vers les feuilles
Choosing the right partner is an investment in the success of your project. By carefully evaluating potential providers against these criteria, you can identify a supplier, like Met3dp, with the necessary expertise, technology, and quality focus to reliably deliver high-performance, custom 3D printed copper heat transfer components.
Understanding Investment: Cost Analysis and Lead Time Estimation for Custom 3D Printed Heat Transfer Parts
Additive manufacturing of custom copper components represents a significant technological capability, but it also involves specific cost structures and lead time considerations that differ from traditional manufacturing. Understanding these factors is crucial for budgeting, project planning, and making informed decisions about adopting AM for thermal management solutions.
Cost Factors for 3D Printed Copper Components:
The final price of a 3D printed copper or CuCrZr part is influenced by a combination of factors:
- Coût des matériaux :
- Powder Price: High-purity, spherical copper and CuCrZr powders suitable for AM are significantly more expensive than raw materials used in traditional machining (like bar stock) or casting. Powder cost is often a major component of the final price.
- Material Consumption: The total volume of the part, including any necessary support structures, directly determines the amount of powder consumed.
- Temps machine (temps de construction) :
- Printing Speed: Printing copper alloys can sometimes be slower than printing other metals due to the need for specific parameters to manage reflectivity and conductivity, potentially requiring more machine time per part.
- Part Volume & Height: Larger volume parts or taller parts naturally take longer to print layer by layer.
- Machine Occupancy: The total time the part occupies the AM machine, including setup, printing, and cooldown, contributes to the cost based on the machine’s hourly operating rate.
- Part Complexity and Geometry:
- Design Intricacy: Highly complex geometries with intricate internal channels or fine features may require slower printing speeds or more complex support strategies, potentially increasing build time and post-processing effort.
- Structures de soutien : The volume and complexity of required support structures impact both material consumption and the labor/time needed for their removal. DfAM efforts to minimize supports directly reduce cost.
- Exigences en matière de post-traitement :
- Traitement thermique : Stress relief and particularly the solution annealing and aging required for CuCrZr involve furnace time, energy consumption, and potentially specialized atmosphere control, adding cost.
- Suppression du support : Labor-intensive manual removal or specialized machining/EDM for supports adds significant cost, especially for complex internal supports.
- Usinage : CNC machining for tight tolerances or specific surface finishes adds cost based on machine time and programming effort.
- Finition de la surface : Polishing, electropolishing, or coating require additional labor, equipment, and consumables.
- HIP (Hot Isostatic Pressing): If required for maximum density or fatigue life improvement, HIP is a specialized and relatively expensive process.
- Assurance qualité et inspection :
- Inspection Level: The extent of required inspection (dimensional checks, surface roughness measurement, NDT like CT scanning, leak testing, material property verification) impacts labor and equipment costs. More stringent requirements naturally increase the price.
- Travail et expertise :
- Skilled Operators & Engineers: Operating AM machines, optimizing parameters for copper, managing post-processing, and performing quality checks require skilled personnel, contributing to overhead costs.
- DfAM Consultation: While potentially adding upfront cost, expert DfAM support can lead to significant downstream savings in material, print time, and post-processing.
- Volume de commande :
- Economies d'échelle : While AM is suited for customization, some economies of scale can be realized for small-to-medium batches. Setup costs are amortized over more parts, and nesting multiple parts efficiently on a build plate can optimize machine usage. Bulk powder purchasing might offer slight material cost reductions. However, the cost reduction per part is typically less dramatic than in high-volume traditional methods like casting.
Estimation du délai d'exécution :
Lead time is the total time from order placement to final part delivery. For custom 3D printed copper parts, it comprises several stages:
- Pre-Processing/Preparation:
- Order Review & DfAM: Initial design review, potential DfAM adjustments, quote finalization. (1-5 days)
- Préparation de la construction : Job scheduling, slicing the CAD model, generating support structures, planning the build layout (nesting parts). (1-3 days)
- Printing (Build Time):
- Machine Queue: Wait time until a suitable machine is available. Can vary significantly based on provider workload. (Days to weeks)
- Active Printing: Actual time the machine spends building the part(s). Highly dependent on part size, complexity, and quantity. (Hours to several days or even weeks for very large/complex builds)
- Post-traitement :
- Cooldown & Depowdering: Allowing the build chamber to cool, removing the build plate, initial powder removal. (Hours to 1 day)
- Stress Relief/Heat Treatment: Furnace time, including heating, soaking, and cooling cycles. (1-3 days, depending on requirements)
- Part Removal & Support Removal: Cutting from build plate, removing supports. (Hours to days, depending on complexity)
- Machining/Finishing: Time required for CNC operations, polishing, etc. (Days, depending on extent)
- Inspection : Time for dimensional checks, NDT, testing. (Hours to days)
- Expédition: Transit time to the customer’s location. (Days)
Typical Lead Time Ranges (Estimates):
- Prototypes (1-5 parts): Often 1 to 4 weeks, depending heavily on complexity, post-processing, and machine availability.
- Small Series Production (10-100 parts): Potentially 3 to 8 weeks or more, influenced by batch optimization, parallel processing capabilities, and the extent of post-processing.
Key Takeaways on Cost and Lead Time:
- Custom Quoting is Essential: Due to the many influencing factors, accurate cost and lead time estimates require submitting specific CAD data and requirements to the AM service provider for a custom quote.
- DfAM is Crucial for Cost Optimization: Investing time in optimizing the design for additive manufacturing can yield significant savings by reducing material use, print time, and post-processing effort.
- Compare Total Cost of Ownership: While the per-part cost might seem higher than some traditional methods initially, consider the benefits of improved performance, part consolidation, reduced assembly, and faster design iteration, which can lower the total cost of ownership for the overall system.
- Factor Post-Processing: Ensure all necessary post-processing steps are included in quotes and lead time estimates.
Engaging with a provider like Met3dp early in the design process allows for a clearer understanding of cost drivers and lead time expectations, enabling better project planning and budgeting for your custom copper heat transfer components.
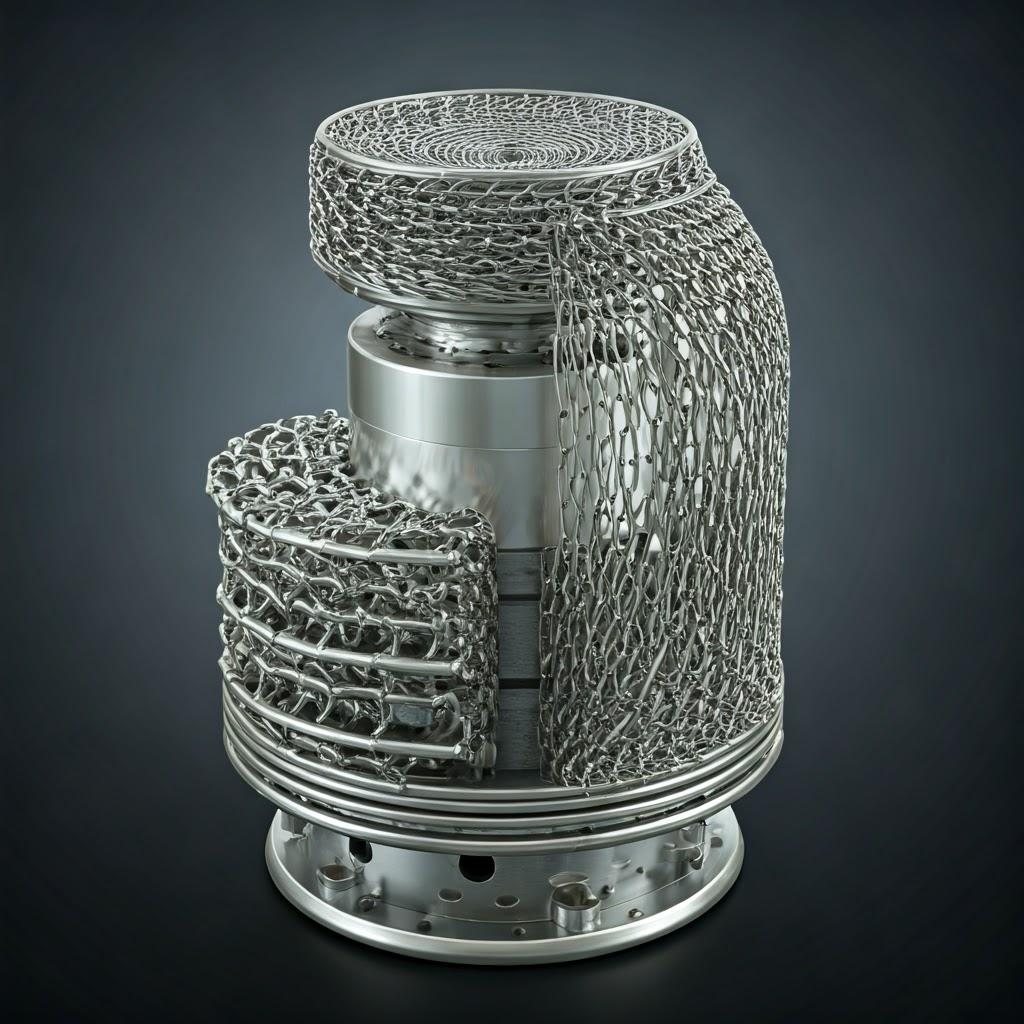
Frequently Asked Questions (FAQ) about 3D Printed Copper Heat Transfer Components
Here are answers to some common questions engineers and procurement managers have about utilizing metal 3D printing for copper and CuCrZr heat transfer components:
1. What is the maximum size part you can typically print in copper or CuCrZr?
The maximum printable size depends directly on the build volume of the specific AM machine used by the service provider. Common build volumes for industrial metal AM systems (LPBF and SEBM) suitable for copper range from medium-sized platforms (e.g., around 250 x 250 x 300 mm) to larger systems (e.g., 400 x 400 x 400 mm or even larger in some cases, though less common for copper-optimized machines). It’s important to note that printing very large copper parts can exacerbate challenges related to thermal management and residual stress. For components exceeding the build volume of a single machine, options might include printing in sections and joining them via post-process welding or brazing (though this negates some benefits of part consolidation) or consulting with providers who operate larger-format machines validated for copper alloys. Always confirm the specific maximum build dimensions with your chosen provider, such as Met3dp.
2. How does the thermal performance of a 3D printed copper/CuCrZr component compare to one machined from solid copper?
Assuming the 3D printed part achieves near-full density (>99.5%) and undergoes appropriate post-processing (like heat treatment for CuCrZr), the intrinsic thermal conductivity of the AM material itself can approach that of wrought or machined copper/CuCrZr. For pure copper, expect AM thermal conductivity around 380-395 W/m·K, very close to the wrought value (~400 W/m·K). For heat-treated CuCrZr, AM conductivity is typically 300-340 W/m·K, comparable to wrought C18150.
Toutefois, le overall thermal performance of the component often exceeds that of a traditionally machined equivalent of the same size/weight. This is because AM allows for significantly more optimized designs:
- Conformal cooling channels: Maximize heat extraction at the source.
- Complex internal structures (lattices, TPMS): Dramatically increase surface area for convection.
- Thin walls: Reduce conduction resistance.
- Consolidation partielle : Eliminates thermal resistance at joints.
Therefore, while the base material conductivity is similar, the design freedom enabled by AM often allows for superior system-level thermal performance compared to geometry-constrained machined parts. Validation through simulation (CFD) and physical testing is recommended to quantify the performance gain for a specific design.
3. Is 3D printed copper suitable for high-vacuum or ultra-high-vacuum (UHV) applications?
Yes, potentially, but with careful consideration. Key factors for vacuum compatibility include:
- Outgassing: Materials used in vacuum must have low outgassing rates to avoid contaminating the environment. Achieving full density (>99.9%) in the 3D printed copper part is critical, as internal porosity can trap gases that slowly outgas. Post-processing steps like Hot Isostatic Pressing (HIP) can help close internal voids. Thorough cleaning procedures are also essential to remove surface contaminants and residues from printing or post-processing.
- Pureté du matériau : Using high-purity copper powder feedstock is important. Impurities can increase outgassing.
- Surface Condition: Smooth surfaces generally have lower outgassing rates than rough surfaces. Post-print surface treatments like electropolishing might be beneficial.
- Trapped Volumes: The design must avoid trapped volumes or virtual leaks (e.g., unvented internal cavities), which AM can sometimes create if not designed carefully. CT scanning can help verify internal integrity.
With proper process control, high-density printing, appropriate cleaning, and potentially HIP, 3D printed copper (especially pure copper) can be made suitable for high-vacuum applications. For UHV, requirements are even stricter, and thorough testing and qualification specific to the application are necessary. Consultation with AM providers experienced in parts for vacuum environments is advised.
4. What are typical surface roughness (Ra) values for internal channels in 3D printed copper heat exchangers? Can they be smoothed?
As-built surface roughness inside channels depends on orientation but is typically higher than external surfaces, often in the Ra 10-30 µm range or potentially more for downward-facing surfaces relying on supports. This roughness increases pressure drop compared to smooth channels. Improving the internal surface finish is challenging but possible:
- Usinage par flux abrasif (AFM) : Flows an abrasive putty through the channels under pressure to smooth surfaces. Effective but requires specialized equipment.
- Électropolissage : Can smooth internal channels significantly (potentially < 1 µm Ra) if the electrolyte can be effectively flowed through the entire network. Design must allow for electrical contact and flow.
- Chemical Polishing: Similar concept using chemical etchants. Process selection depends on channel size, complexity, and the required level of smoothness. Discussing internal finish requirements and feasible post-processing options with your AM provider during the design phase is important.
Conclusion: Revolutionizing Thermal Management with Additively Manufactured Copper Components
The relentless push for higher performance, increased power density, and component miniaturization across industries from aerospace to computing places unprecedented demands on thermal management systems. Custom heat transfer components are essential for meeting these challenges, and metal additive manufacturing with high-conductivity copper alloys like pure Cu and CuCrZr represents a truly transformative technology in this domain.
As we’ve explored, metal 3D printing unshackles designers from the constraints of traditional manufacturing, enabling the creation of components with unparalleled geometric complexity. This freedom allows for:
- Highly optimized designs: Conformal cooling channels, intricate internal flow paths, micro-features, and integrated lattice structures maximize thermal performance within minimal volume and weight.
- Consolidation partielle : Reducing assembly complexity, improving reliability by eliminating joints, and streamlining supply chains.
- Rapid innovation: Facilitating quick design iterations and the production of bespoke solutions tailored to specific application needs.
While challenges related to copper’s printability, post-processing, and cost exist, advancements in AM technology, materials science, and process expertise are continuously overcoming these hurdles. High-quality powders, sophisticated machine capabilities (including green lasers and SEBM), optimized process parameters, and robust post-processing techniques are making 3D printed copper components increasingly reliable and accessible.
The key to successfully leveraging this technology lies in a holistic approach: employing DfAM principles, understanding material properties and trade-offs, planning for necessary post-processing, and, crucially, selecting the right manufacturing partner. An experienced provider like Met3dp brings together expertise in advanced powder manufacturing, state-of-the-art printing technologies, rigorous quality control, and collaborative engineering support. Our comprehensive solutions, spanning from high-sphericity Cu and CuCrZr powders produced via VIGA and PREP to expert printing services and application development, empower organizations to tackle their most demanding thermal management problems.
Whether you are developing next-generation electronics cooling solutions, optimizing aerospace engine components, enhancing EV battery thermal management, or improving industrial process efficiency, 3D printed copper heat transfer components offer a powerful pathway to achieving breakthrough performance.
Ready to explore how additive manufacturing can revolutionize your thermal management strategy?
Contact Met3dp today to discuss your project requirements with our experts. Let us show you how our cutting-edge systems, advanced metal powders, and deep application knowledge can power your organization’s additive manufacturing goals and help you achieve unparalleled thermal performance. Visit us at https://met3dp.com/ pour en savoir plus.
Partager sur
MET3DP Technology Co. est un fournisseur de premier plan de solutions de fabrication additive dont le siège se trouve à Qingdao, en Chine. Notre société est spécialisée dans les équipements d'impression 3D et les poudres métalliques de haute performance pour les applications industrielles.
Articles connexes
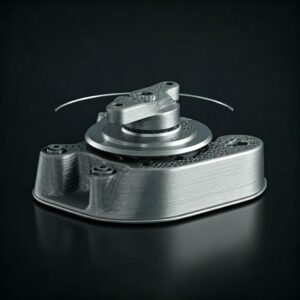
Supports imprimés en 3D pour les capteurs radar automobiles : Précision et performance
Lire la suite "À propos de Met3DP
Mise à jour récente
Notre produit
CONTACTEZ-NOUS
Vous avez des questions ? Envoyez-nous un message dès maintenant ! Nous répondrons à votre demande avec toute une équipe dès réception de votre message.
Obtenir les informations de Metal3DP
Brochure du produit
Obtenir les derniers produits et la liste des prix
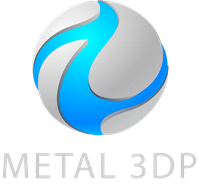
Poudres métalliques pour l'impression 3D et la fabrication additive
PRODUIT
cONTACT INFO
- Ville de Qingdao, Shandong, Chine
- [email protected]
- [email protected]
- +86 19116340731