Complex Wing Ribs via Metal 3D Printing
Table des matières
Introduction: Revolutionizing Aerospace Structures with Metal 3D Printed Wing Ribs
The aerospace industry stands at the forefront of technological advancement, constantly pushing the boundaries of performance, efficiency, and safety. Central to this pursuit is the relentless optimization of aircraft structures, where every gram saved and every performance enhancement translates into significant operational benefits. Within the intricate framework of an aircraft wing, the aerospace wing rib plays a critical, albeit often unseen, role. These structural components are fundamental to maintaining the wing’s aerodynamic profile, distributing loads, and supporting various systems. Traditionally, manufacturing these complex parts involved subtractive methods like CNC machining, often leading to significant material waste and design limitations. However, the advent of métal Impression 3Dégalement connu sous le nom de la fabrication additive (AM), is triggering a paradigm shift in how complex structures d'aéronefs like wing ribs are designed and produced.
Metal AM technologies, particularly Powder Bed Fusion (PBF) methods like Selective Laser Melting (SLM) and Electron Beam Melting (EBM), offer unprecedented design freedom. This allows engineers to create highly optimized, lightweight wing ribs with intricate internal structures and geometries previously impossible or prohibitively expensive to manufacture. This capability for fabrication avancée unlocks significant potential for weight reduction, part consolidation, improved structural integrity, and accelerated development cycles – all critical factors in the competitive aerospace landscape. For procurement managers and engineers seeking reliable aerospace components suppliers, understanding the capabilities and nuances of metal AM is becoming increasingly vital.
The benefits extend beyond mere component fabrication. Additive manufacturing facilitates rapid prototyping, enabling faster design iteration and validation. It allows for the creation of bespoke components tailored to specific mission requirements and supports the consolidation of multiple parts into a single, integrated structure, reducing assembly time and potential failure points. As the aerospace industry embraces digital manufacturing, metal AM emerges as a cornerstone technology, enabling the production of next-generation aircraft components. Companies specializing in this field, offering both cutting-edge equipment and high-performance materials, are crucial partners in this evolution. For instance, Met3dp, a leader in metal additive manufacturing solutions, provides comprehensive services encompassing advanced printers and optimized poudres métalliques tailored for demanding aerospace applications, empowering manufacturers to leverage the full potential of this transformative technology. Partnering with experienced Met3dp solutions providers ensures access to the expertise needed to navigate the complexities of AM adoption, from material selection to process validation. The journey towards lighter, stronger, and more efficient aircraft is being reshaped, one additively manufactured layer at a time.
The Crucial Role of Wing Ribs in Aircraft Design and Performance
Within the sophisticated architecture of an aircraft wing, wing ribs serve as essential structural elements, performing several critical functions that are indispensable for safe and efficient flight. Understanding the wing rib function is key to appreciating why optimizing their design and manufacturing process through technologies like metal 3D printing is so impactful for ingénierie aérospatiale et globalement conception des aéronefs.
Primarily, wing ribs define and maintain the crucial airfoil shape of the wing. This aerodynamic profile is meticulously designed to generate lift efficiently while minimizing drag. The ribs act as formers, running chordwise (from the leading edge to the trailing edge) and providing attachment points for the wing skin (or covering). By rigidly holding the skin in the correct contour, ribs ensure the wing maintains its intended aerodynamic performance across various flight conditions and load scenarios. Any deviation from this shape can compromise lift generation, increase drag, and potentially affect the aircraft’s stability and control.
Secondly, wing ribs play a vital role in load distribution. They transfer aerodynamic forces (lift and drag) and inertial loads (from the wing’s mass and fuel) from the wing skin to the main structural members of the wing – the spars. Spars typically run spanwise (from root to tip) and bear the primary bending loads. Ribs distribute these loads evenly, preventing stress concentrations in the skin and ensuring the structural integrity of the entire wing assembly. They also resist torsional loads, helping the wing maintain its shape under twisting forces. This load-bearing and distributing function makes the structural integrity of each rib paramount.
Furthermore, wing ribs contribute significantly to the overall stiffness and stability of the wing structure. They compartmentalize the wing, preventing buckling of the skin under compression loads and enhancing the wing’s resistance to flutter – a dangerous aeroelastic instability. The spacing and design of the ribs are carefully calculated by aerospace engineers to ensure adequate structural support without adding unnecessary weight.
Beyond their primary structural roles, wing ribs often serve secondary, yet essential, functions:
- System Integration: They provide mounting points and pathways for various aircraft systems housed within the wing, such as fuel lines, hydraulic pipes, electrical wiring, and control mechanisms (like flap and aileron actuators). Openings (often called cutouts) within the ribs allow these systems to pass through.
- Fuel Tank Boundaries: In many aircraft designs (“wet wings”), the wing itself serves as a fuel tank. Ribs, often sealed, form the chordwise boundaries of these integral fuel tanks, requiring high precision and integrity to prevent leaks.
- Access and Maintenance: Some ribs incorporate access panels or hatches, allowing technicians to inspect and maintain the internal wing structure and systems.
Given these multifaceted and critical functions, the design and manufacture of wing ribs demand precision, reliability, and optimal structural efficiency. Traditional manufacturing methods often involve machining ribs from solid blocks of metal (billets), leading to substantial material waste (buy-to-fly ratio) and limitations on geometric complexity. This is where the search for advanced manufacturing techniques and reliable aerospace components suppliers becomes crucial for aerospace OEMs and their partners. The ability of metal AM to create complex, lightweight, and functionally integrated ribs offers a compelling alternative, promising enhanced performance and manufacturing efficiency for these vital composants aérospatiaux.
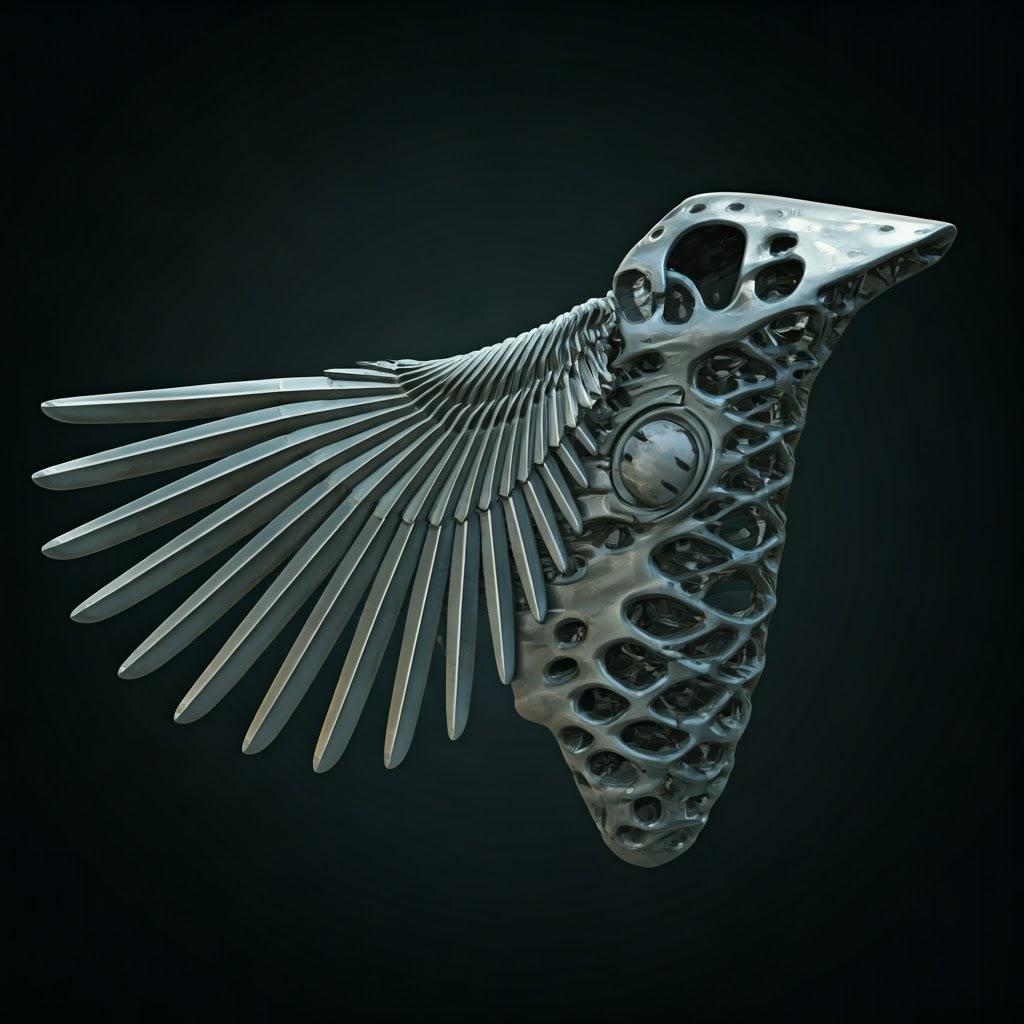
Why Metal Additive Manufacturing is Taking Flight for Wing Rib Production
The transition from traditional manufacturing methods, primarily subtractive machining, to la fabrication additive métallique (AM) for producing components like aerospace wing ribs is driven by a confluence of compelling advantages. These benefits directly address key challenges faced by the aerospace industry, including weight reduction, design complexity, production speed, and cost-efficiency, particularly for low-to-medium volume, high-complexity parts. Understanding the advantages of metal 3D printing clarifies why this technology is rapidly gaining traction among aerospace engineers and aerospace procurement specialists.
One of the most significant drivers is lightweighting aerospace structures. Metal AM enables sophisticated design techniques like topology optimization and the integration of intricate lattice structures.
- Optimisation de la topologie : Algorithms determine the most efficient material distribution within a defined design space, subject to specific load conditions and constraints. This removes material from non-critical areas, resulting in organic-looking, highly optimized structures that maintain or even enhance strength while drastically reducing weight compared to traditionally designed counterparts.
- Structures en treillis : AM allows for the creation of internal lattices (e.g., gyroids, honeycombs) within the rib structure. These cellular designs provide excellent stiffness and strength at very low densities, further contributing to weight savings without compromising structural integrity.
Weight reduction directly translates to lower fuel consumption, increased payload capacity, and improved overall aircraft performance – key metrics in the aerospace sector.
Secondly, metal AM excels at handling complex geometry manufacturing. Traditional methods struggle with internal channels, complex curvatures, and highly intricate features, often requiring multiple setups, specialized tooling, or assembly of several smaller parts. Additive manufacturing builds parts layer-by-layer directly from a digital model, making geometric complexity almost ‘free’. This allows engineers to design wing ribs with:
- Optimized internal stiffeners and truss-like structures.
- Integrated mounting points and brackets for systems.
- Conformal cooling channels or fluid passages if required.
- Smoother aerodynamic transitions.
This capability also enables significant consolidation partielle. A complex wing rib assembly previously made from multiple machined components fastened together can potentially be redesigned and printed as a single, monolithic part. This reduces:
- Assembly time and labor costs.
- Part count and inventory management complexity.
- Potential points of failure (fasteners, joints).
- Overall weight associated with fasteners and overlapping material.
Another crucial advantage is lead time reduction, particularly for prototyping, tooling, and low-volume production. Traditional manufacturing often involves long lead times associated with creating custom tooling (jigs, fixtures) or extensive programming and setup for CNC machines. Metal AM is a digital process; once the design file is ready, printing can often commence relatively quickly. This accelerates the design iteration cycle, allowing engineers to test and validate new rib designs much faster. For producing spare parts or components for older aircraft where original tooling may no longer exist, AM offers an efficient on-demand solution.
Comparaison traditional vs additive manufacturing aerospace highlights the material efficiency of AM. Subtractive machining starts with a large block of material and removes excess, often resulting in buy-to-fly ratios (weight of raw material purchased vs. weight of the final part) of 10:1 or even higher for complex aerospace parts. While AM is not waste-free (support structures, some powder loss), it is fundamentally an additive process, using material primarily where needed. This significantly improves material utilization, especially with expensive aerospace-grade alloys.
Furthermore, the layer-by-layer approach allows for the possibility of creating functionally graded materials or embedding sensors directly within the component during the build process, opening doors for future innovations in smart structures.
Companies like Met3dp are instrumental in facilitating this transition by providing robust impression 3D de métaux technologies and high-quality powders necessary to meet the stringent demands of the aerospace industry. Their expertise ensures that manufacturers can reliably leverage these AM advantages for critical components like wing ribs.
Table: Metal AM vs. Traditional Machining for Wing Ribs
Fonctionnalité | Metal Additive Manufacturing (e.g., PBF) | Usinage CNC traditionnel | Impact sur l'aérospatiale |
---|---|---|---|
Liberté de conception | High (complex geometries, internal features, lattices) | Limited (constrained by tool access & process) | Enables topology optimization, lightweighting, part consolidation |
Réduction du poids | Significant potential via optimization & lattices | Limited by design constraints | Lower fuel burn, increased payload/range |
Consolidation partielle | High potential (integrating multiple parts into one) | Low (often requires assembly of sub-components) | Reduced assembly time, fewer failure points, lower weight |
Utilisation des matériaux | Generally high (additive process) | Generally low (subtractive process, high waste) | Reduced raw material cost, more sustainable, especially for expensive alloys |
Lead Time (New Part) | Potentially shorter (no hard tooling, direct digital manufacturing) | Longer (tooling design/fabrication, programming) | Faster prototyping, quicker time-to-market, efficient low-volume production |
Coûts d'outillage | Minimal to none (digital process) | Significant (jigs, fixtures) | Lower barrier to entry for custom/complex parts, economical for low volumes |
Taille minimale de l'objet | Limited by process resolution (laser/beam spot size, powder) | High precision possible | Requires design considerations for AM process limitations |
Surface Finish (As-Built) | Typically rougher | Typically smoother | Often requires post-processing (machining, polishing) for critical surfaces |
Initial Setup Cost | High machine investment | Moderate to high machine investment | Cost-benefit analysis depends on volume, complexity, and strategic goals |
Ideal Complexity | Haut | Faible à modéré | AM excels where complexity adds functional value (e.g., optimized wing ribs) |
Exporter vers les feuilles
Material Matters: Selecting High-Performance Powders like Scalmalloy® and AlSi10Mg
The success of manufacturing aerospace wing ribs using metal 3D printing hinges critically on the selection of the right material. Aerospace applications demand materials with exceptional specific strength (strength-to-weight ratio), good fatigue performance, corrosion resistance, and consistent properties under varying operational temperatures. For complex, lightweight structures like optimized wing ribs, two aluminum alloys stand out in the additive manufacturing landscape: Scalmalloy® (alliage d'aluminium) et AlSi10Mg. Choosing the appropriate metal powder properties is paramount, and sourcing from a reliable aerospace materials supplier like Met3dp ensures the quality and consistency required for flight-critical components.
Scalmalloy®: The High-Performance Contender
Scalmalloy® is a high-performance aluminum-magnesium-scandium alloy specifically developed for additive manufacturing. It offers properties that often surpass those of traditional high-strength aluminum alloys, making it highly attractive for demanding aerospace applications.
- Propriétés principales :
- Exceptional Specific Strength: Scalmalloy® boasts a very high yield and ultimate tensile strength, especially after appropriate heat treatment, combined with low density. This results in a superior strength-to-weight ratio compared to many conventional aluminum alloys like AlSi10Mg or even some titanium alloys in specific applications.
- Excellent Ductility and Toughness: Unlike some high-strength materials that can be brittle, Scalmalloy® maintains good ductility, which is crucial for damage tolerance in aerospace structures.
- Bonne soudabilité : This is advantageous for potential post-processing or assembly operations, although AM often aims for part consolidation.
- Natural Corrosion Resistance: Like other aluminum alloys, it forms a protective oxide layer.
- Good Dynamic Performance: Exhibits favorable fatigue strength, essential for components subjected to cyclic loading, like wing structures.
- Microstructure Stability: Scandium additions help create a fine-grained microstructure that is stable even at moderately elevated temperatures.
- Benefits for Wing Ribs: Its high strength allows for designing even thinner, lighter ribs through topology optimization without compromising structural integrity. The combination of strength and ductility provides a safety margin against unexpected loads or impacts. Its suitability for AM processes like SLM enables the creation of highly complex, optimized rib geometries.
AlSi10Mg: The Established Workhorse
AlSi10Mg is a more traditional aluminum casting alloy that has become one of the most widely used and well-characterized materials in metal additive manufacturing, particularly Laser Powder Bed Fusion (LPBF).
- Propriétés principales :
- Bon rapport résistance/poids : While generally not as high as Scalmalloy®, AlSi10Mg still offers a good balance of strength and low density, making it suitable for many aerospace applications where weight saving is important.
- Excellente imprimabilité : It is known for its relatively straightforward processing using LPBF systems, resulting in dense parts with good dimensional accuracy.
- Good Thermal Properties: Possesses good thermal conductivity.
- Résistance à la corrosion : Offers adequate corrosion resistance for many environments.
- Well-Understood Properties: Extensive research and application data are available for AlSi10Mg processed via AM, providing confidence in its performance characteristics.
- Benefits for Wing Ribs: AlSi10Mg provides a cost-effective solution for wing ribs where the absolute maximum performance of Scalmalloy® might not be required. Its widespread availability, established process parameters, and lower cost make it an attractive option for many components. It allows for significant lightweighting and complexity compared to traditional manufacturing, even if not reaching the peak performance levels of Scalmalloy®.
Why Powder Quality Matters & Met3dp’s Role
The performance of the final 3D printed part is directly linked to the quality of the metal powder used. Factors like particle size distribution (PSD), morphology (sphericity), flowability, and chemical purity are critical for achieving dense, defect-free components with predictable mechanical properties.
- Distribution de la taille des particules (PSD) : Affects powder bed density and melting behavior. An optimized PSD ensures uniform layers and consistent melting.
- Morphology & Flowability: Spherical powder particles flow easily and pack densely, leading to uniform powder layers and reducing the risk of voids or defects in the final part.
- La pureté : Contaminants can drastically degrade mechanical properties, particularly fatigue life and fracture toughness, which are critical in aerospace.
This is where partnering with a specialized provider like Met3dp becomes crucial. Met3dp utilizes advanced powder making systems, including industry-leading gas atomization and Plasma Rotating Electrode Process (PREP) technologies. Their gas atomization employs unique nozzle designs to produce poudres métalliques de haute qualité with the high sphericity, optimized PSD, and excellent flowability required for demanding AM processes. Their commitment to quality control ensures the chemical purity and batch-to-batch consistency necessary for aerospace applications. By offering rigorously tested and optimized powders like AlSi10Mg and potentially facilitating access to specialized alloys like Scalmalloy®, Met3dp provides the foundational materials needed to reliably produce high-performance, 3D printed wing ribs.
Table: Comparison of Scalmalloy® and AlSi10Mg for AM Wing Ribs
Propriété | Scalmalloy® (alliage d'aluminium) | AlSi10Mg | Considerations for Wing Ribs |
---|---|---|---|
Force spécifique | Très élevé | Bon à élevé | Scalmalloy® allows for maximum lightweighting potential. |
Ductility/Toughness | Excellent | Modéré | Scalmalloy® offers better damage tolerance. |
Résistance à la fatigue | Très bon | Bon | Critical for cyclic wing loads; Scalmalloy® generally preferred for high-cycle fatigue applications. |
Imprimabilité (LPBF) | Good (requires optimized parameters) | Excellent (well-established parameters) | AlSi10Mg may offer easier processing and wider parameter windows. |
Traitement thermique | Required for optimal properties | Often used (T6) to improve strength/ductility | Post-processing step needed for both to achieve desired final properties. |
Max Service Temp. | Higher than AlSi10Mg | Plus bas | Scalmalloy® maintains properties better at slightly elevated temperatures. |
Coût | Plus élevé | Plus bas | Cost-benefit analysis needed based on performance requirements vs. budget. |
Availability/Maturity | Newer, specialized | Widely available, mature process | AlSi10Mg has more extensive public data and broader supplier base, though specialized suppliers like Met3dp are key for both. |
Application idéale | Highest performance, max weight saving critical | Cost-sensitive, good performance required | Choice depends on specific aircraft program requirements, budget, and performance targets. |
Exporter vers les feuilles
Selecting between Scalmalloy® and AlSi10Mg involves balancing performance requirements, manufacturing complexity, and cost. Both materials, when sourced as high-quality powders from reputable suppliers like Met3dp and processed using optimized AM parameters, enable the production of complex, lightweight, and structurally sound aerospace wing ribs, pushing the boundaries of aircraft design and efficiency.
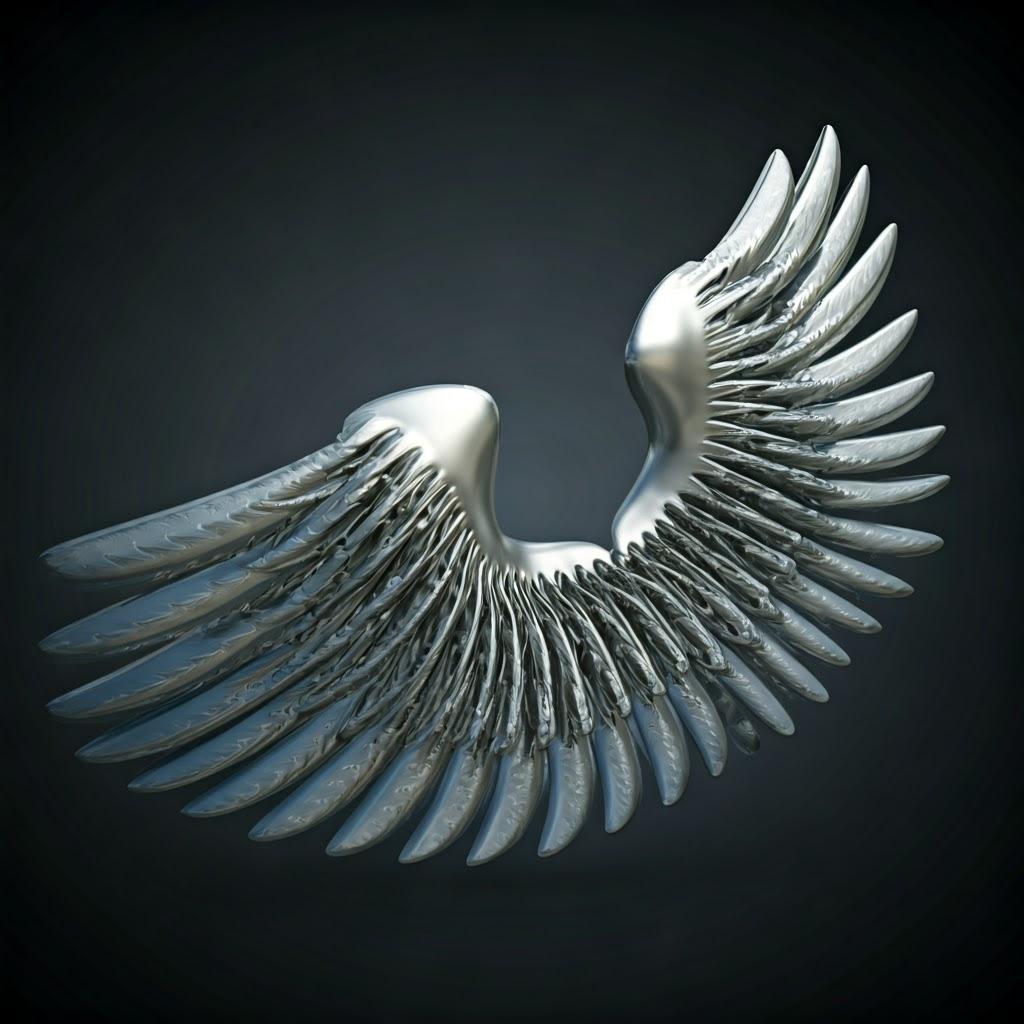
Design for Additive Manufacturing (DfAM): Optimizing Wing Ribs for 3D Printing Success
Simply replicating a traditionally designed wing rib using additive manufacturing often fails to capture the true potential of the technology. To fully leverage the benefits of metal 3D printing – particularly lightweighting, part consolidation, and enhanced performance – engineers must embrace Conception pour la fabrication additive (DfAM) principles. DfAM aérospatiale is not just about making a part printable; it’s a holistic approach that rethinks component design from the ground up, considering the unique capabilities and constraints of the AM process. For complex components like topology optimization wing ribs, applying DfAM is crucial for achieving optimal outcomes.
Key DfAM considerations for metal 3D printed wing ribs include:
- Leveraging Topology Optimization and Generative Design:
- These computational tools are central to lightweighting. Starting with a defined design space (the maximum allowable volume for the rib) and specifying load cases, boundary conditions, and performance targets (e.g., stiffness, stress limits), algorithms intelligently distribute material only where it’s structurally necessary.
- This often results in highly organic, load-path-optimized structures that bear little resemblance to traditionally designed parts but offer superior structural efficiency. Software tools can generate multiple design options, allowing engineers to select the best compromise between weight, performance, and manufacturability.
- Integrating Lattice Structures:
- For internal volumes or sections requiring stiffness without high load-bearing capacity, lattice structures aircraft designs (e.g., gyroids, octet truss, honeycomb) can be integrated. These periodic cellular structures offer excellent stiffness-to-weight ratios and can also enhance energy absorption or facilitate fluid flow if needed.
- DfAM involves selecting the appropriate lattice type, cell size, and strut thickness based on structural requirements and AM process resolution limits. Hybrid designs combining solid load-bearing sections with lattice infill are common for wing ribs.
- Managing Overhangs and Support Structures:
- Powder Bed Fusion processes require support structures for features overhanging the build platform beyond a certain critical angle (typically around 45 degrees relative to the build plate). Supports prevent sagging, warping due to thermal stress, and ensure features are securely anchored during the build.
- Effective DfAM aims for support structure minimization. This involves:
- Angles autoportants : Designing features with angles below the critical threshold where possible.
- Feature Orientation: Orienting parts on the build plate to minimize the extent and complexity of down-facing surfaces.
- Bridging: Designing short horizontal spans that can bridge gaps without support (process-dependent).
- Designing for Removal: Ensuring supports are accessible for easy and non-damaging removal during post-processing. Internal supports in complex rib geometries can be particularly challenging.
- Build Orientation Strategy:
- The orientation of the wing rib on the build platform significantly impacts several factors:
- Structures de soutien : As mentioned, orientation dictates support needs.
- Finition de la surface : Upward-facing and vertical surfaces generally have better finish than downward-facing surfaces supported by structures.
- Précision dimensionnelle : Thermal gradients and shrinkage can vary with orientation.
- Propriétés mécaniques : Due to the layer-wise build process, metal AM parts can exhibit some degree of anisotropy (properties varying with direction). Orientation relative to critical load paths should be considered.
- Build Time & Cost: Taller builds generally take longer. Nesting multiple parts efficiently within the build volume is also key.
- A careful build orientation strategy balances these factors to achieve the desired part quality and economics.
- The orientation of the wing rib on the build platform significantly impacts several factors:
- Minimum Feature Size and Wall Thickness:
- AM processes have limitations on the minimum size of features (holes, slots, struts) and the minimum wall thickness they can reliably produce. This depends on the machine, laser/electron beam spot size, powder characteristics, and process parameters.
- Designers must ensure all features adhere to these minimums (e.g., typically >0.4-0.5 mm for thin walls in LPBF). Failing to do so can result in incomplete features or structural weaknesses.
- Concevoir pour le post-traitement :
- DfAM extends beyond the printing phase. Consideration must be given to downstream processes:
- Support Removal Access: Ensuring tools can reach supports.
- Tolérances d'usinage : Adding extra material (stock) to surfaces requiring high precision or specific finishes that will be achieved via CNC machining after printing.
- Traitement thermique : Designing features that won’t excessively warp or distort during thermal stress relief or heat treatment cycles.
- Accès à l'inspection : Ensuring critical features can be accessed for non-destructive testing (NDT).
- DfAM extends beyond the printing phase. Consideration must be given to downstream processes:
By integrating these design for metal AM principles early in the design cycle, engineers can unlock the full potential of the technology, creating wing ribs that are not only manufacturable but also significantly lighter, stronger, and more functionally integrated than their traditional counterparts. Partnering with experienced AM service providers who understand DfAM nuances is essential for successful implementation.
Achieving Precision: Understanding Tolerance, Surface Finish, and Accuracy in Metal AM
While metal additive manufacturing offers unparalleled design freedom, it’s crucial for engineers and procurement managers to have realistic expectations regarding the achievable metal 3D printing tolerances, surface finish additive manufacturinget dans l'ensemble dimensional accuracy aerospace parts. These factors are critical for ensuring proper fit, assembly, and aerodynamic performance of components like wing ribs. The precision achievable depends heavily on the specific AM process (e.g., LPBF, EBM), machine calibration, material (Scalmalloy®, AlSi10Mg), part geometry, build strategy, and post-processing steps.
Dimensional Tolerances:
- As-Built Tolerances: Parts produced via metal Powder Bed Fusion (PBF) typically have as-built dimensional tolerances that are looser than conventional high-precision machining. General tolerances often fall within the range of ISO 2768 medium (m) or coarse (c) classes.
- For smaller features (e.g., < 100 mm), tolerances might be in the range of ±0.1 mm to ±0.3 mm.
- For larger dimensions, tolerances might scale up, potentially reaching ±0.5 mm or more over several hundred millimeters, depending on thermal management during the build.
- Factors Influencing Tolerances: Thermal expansion/contraction during the layer-wise melting and solidification process is a primary factor. Residual stresses can cause warping, and variations in powder layering or energy delivery can also impact accuracy. Machine calibration and thermal control systems play a huge role.
- Obtenir des tolérances plus strictes : For critical features, mating surfaces, or interfaces requiring tighter tolerances than achievable “as-built,” post-process machining is typically required. DfAM practices incorporate machining allowances on these specific surfaces.
Finition de la surface (rugosité) :
- As-Built Surface Roughness (Ra): The surface finish of as-built metal AM parts is inherently rougher than machined surfaces. The roughness depends on:
- Taille des particules : Larger powder particles generally lead to rougher surfaces.
- Épaisseur de la couche : Thicker layers tend to increase roughness.
- Surface Orientation:
- Surfaces orientées vers le haut : Generally smoother.
- Vertical walls: Moderate roughness, often showing layer lines.
- Downward-facing (supported) surfaces: Typically the roughest due to contact with support structures. Roughness values (Ra) can range widely, often from 5 µm to 25 µm or more, depending on these factors.
- Amélioration de l'état de surface : Post-processing is essential for achieving smooth surfaces required for aerodynamic efficiency or sealing. Common methods include:
- Abrasive blasting (bead blasting, sandblasting) for a uniform matte finish.
- Tumbling or vibro-polishing for bulk finishing.
- Manual polishing for specific areas.
- CNC machining for critical surfaces requiring high smoothness and precision.
- Electrochemical polishing.
Précision dimensionnelle :
- This refers to how closely the final part conforms to the original CAD model dimensions. It’s influenced by all the factors affecting tolerances and surface finish, plus:
- CAD Model Quality: Ensuring the digital model is accurate and appropriately formatted (e.g., STL resolution).
- Simulation de processus : Advanced simulation tools can predict thermal distortion and shrinkage, allowing for compensation in the build file to improve final accuracy.
- Machine Quality & Calibration: The precision and reliability of the impression 3D de métaux system itself are fundamental. High-quality machines with robust calibration routines, like those emphasized by leading providers such as Met3dp, are essential for achieving consistent and accurate results, particularly for demanding aerospace components. Met3dp’s focus on industry-leading print accuracy ensures parts meet stringent specifications.
Table: Typical Precision Levels in Metal PBF (Al Alloys)
Paramètres | As-Built Typical Range | Achievable with Post-Processing | Notes |
---|---|---|---|
Tolérance dimensionnelle | ±0.1 mm to ±0.5 mm+ | Down to ±0.01 mm or better | Depends on size, geometry, feature. Machining required for tightest tolerances. |
Rugosité de la surface (Ra) | 5 µm – 25 µm+ | Down to < 0.8 µm or better | Depends on orientation. Polishing/machining needed for smooth finishes. |
Min. Wall Thickness | ~0.4 – 0.5 mm | N/A | Process/machine dependent. |
Min. Hole Diameter | ~0.5 – 1.0 mm | Drilled/reamed to spec | Small holes may need post-drilling. |
Exporter vers les feuilles
Understanding these achievable precision levels is crucial for quality control metal AM. Engineers must design accordingly, specifying post-processing steps where necessary and collaborating closely with their AM service provider to ensure the final wing rib meets all functional and assembly requirements. Relying on providers with calibrated, high-accuracy equipment and robust quality management systems is key to success in aerospace applications.
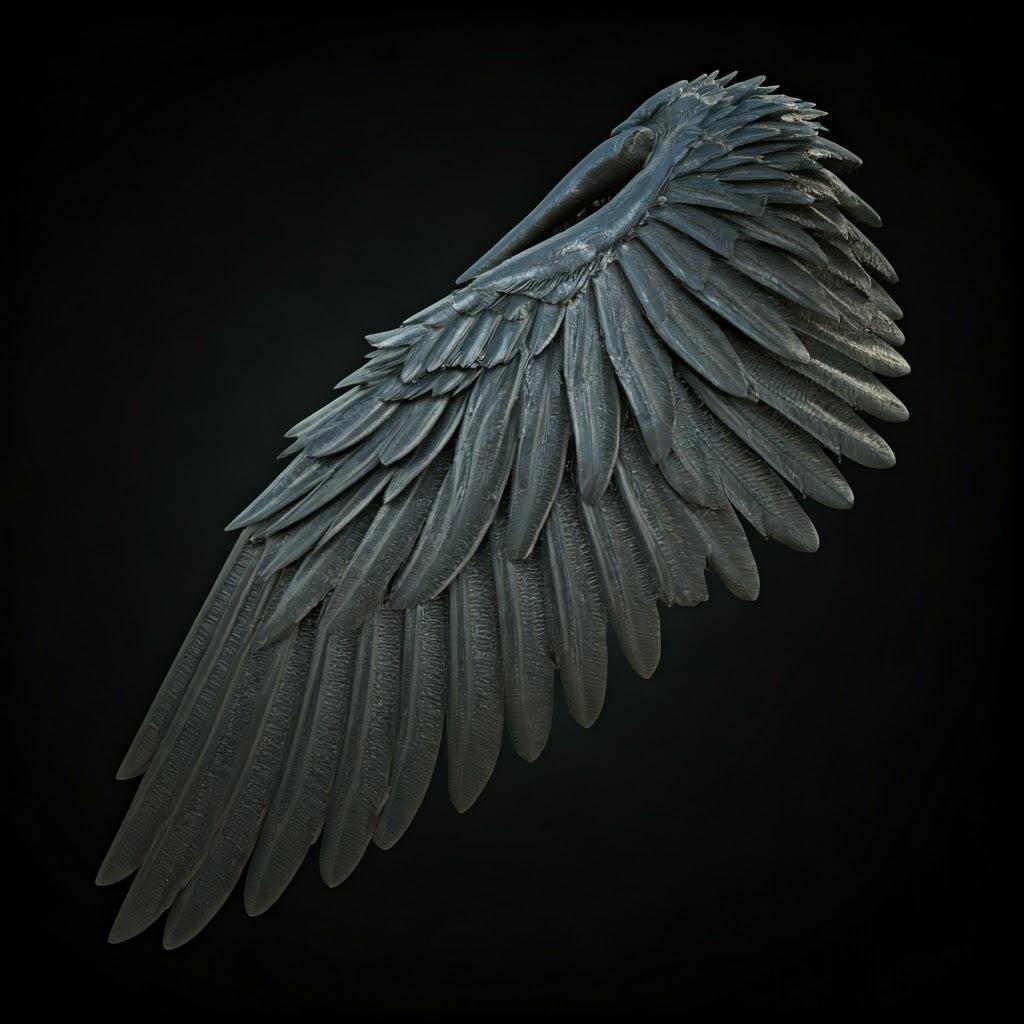
Beyond the Build: Essential Post-Processing for Aerospace-Grade Wing Ribs
Producing an aerospace wing rib doesn’t end when the 3D printer stops. The “as-built” part, fresh from the powder bed, requires a series of crucial post-processing metal 3D printing steps to transform it into a flight-ready component that meets the stringent safety, performance, and quality standards of the aerospace industry. These steps are integral to the manufacturing workflow and must be planned for from the outset, often influencing design choices (DfAM).
Common post-processing stages for metal AM wing ribs (Scalmalloy®, AlSi10Mg) include:
- Elimination des poudres :
- The first step after retrieving the build plate from the machine is removing the surrounding loose powder. This is typically done within a controlled environment to contain the powder (which can be reactive) and enable its recycling.
- Care must be taken to remove powder from internal channels and complex features of the wing rib, often using compressed air/gas jets and careful brushing or vacuuming. Depowdering intricate lattice structures can be challenging.
- Stress Relief (Thermal):
- The rapid heating and cooling cycles inherent in PBF processes induce significant residual stresses within the printed part. These stresses can cause distortion upon removal from the build plate or compromise the part’s mechanical performance and fatigue life.
- A heat treatment aerospace parts cycle, typically performed while the part is still attached to the build plate, is used to relieve these internal stresses. The specific temperature and duration depend on the alloy (e.g., typically around 300°C for AlSi10Mg).
- Retrait de la pièce de la plaque de construction :
- Once stress-relieved, the wing rib(s) are separated from the build plate. This is commonly done using wire Electrical Discharge Machining (EDM) or a bandsaw. Care must be taken to avoid damaging the parts.
- Retrait de la structure de soutien :
- The support structures, essential during the build, must now be removed. This can be one of the most labor-intensive and delicate post-processing steps, especially for complex geometries like optimized wing ribs with internal features.
- Methods include:
- Manual removal (breaking or cutting).
- Machining (milling).
- EDM for difficult-to-reach supports.
- Careful design (DfAM) can make supports easier to access and remove. The removal process can leave witness marks or rough surfaces that may require further finishing.
- Heat Treatment (Solution Annealing, Aging, HIP):
- Beyond stress relief, further heat treatments are often necessary to achieve the desired final microstructure and mechanical properties (strength, ductility, fatigue resistance) for aerospace applications.
- Solution Annealing & Age Hardening (e.g., T6 condition): Common for alloys like AlSi10Mg and Scalmalloy® to significantly increase strength. Specific temperature cycles dissolve alloying elements into the matrix, followed by controlled precipitation hardening.
- Pressage isostatique à chaud (HIP) : This is a crucial step for many flight-critical composants aérospatiaux. Les HIP process involves applying high temperature and high inert gas pressure (e.g., Argon) simultaneously. This effectively closes internal voids or microscopic porosity that might remain after printing, leading to:
- Increased density (near 100%).
- Improved fatigue life and fracture toughness.
- Reduced scatter in mechanical properties.
- Enhanced overall structural integrity. HIP is often considered mandatory for Class 1 aerospace parts.
- Beyond stress relief, further heat treatments are often necessary to achieve the desired final microstructure and mechanical properties (strength, ductility, fatigue resistance) for aerospace applications.
- Finish Machining (CNC):
- As discussed previously, CNC machining AM parts is frequently required to achieve tight tolerances on mating surfaces, critical interfaces (e.g., spar or skin attachment points), hole diameters, and to attain very smooth surface finishes where needed for aerodynamic or sealing purposes. Machining is performed after heat treatments to ensure final dimensional accuracy.
- Surface Finishing & Cleaning:
- Depending on requirements, further surface finishing aerospace components may be applied:
- Abrasive blasting (bead, sand) for a uniform matte finish and cleaning.
- Tumbling/Vibratory finishing for deburring and smoothing edges.
- Polishing for very smooth surfaces.
- Anodizing (for aluminum alloys) to improve corrosion resistance and wear properties.
- Painting or application of specialized aerospace coatings.
- Thorough cleaning is essential before any coating or final assembly.
- Depending on requirements, further surface finishing aerospace components may be applied:
- Inspection and Quality Assurance (QA):
- Rigorous inspection is non-negotiable in aerospace. This involves:
- Dimensional verification (CMM, 3D scanning).
- Surface roughness measurement.
- Non-Destructive Testing (NDT) such as X-ray or CT scanning to detect internal defects (porosity, cracks), and fluorescent penetrant inspection (FPI) for surface flaws.
- Material testing (e.g., tensile tests on witness coupons printed alongside the parts).
- Full documentation and traceability according to aerospace standards (e.g., AS9100) are required.
- Rigorous inspection is non-negotiable in aerospace. This involves:
Each of these l'assurance qualité steps adds time and cost but is essential for ensuring the reliability and safety of 3D printed aerospace wing ribs. Partnering with an AM service provider experienced in these comprehensive post-processing workflows is critical.
Navigating Potential Hurdles: Common Challenges in Printing Wing Ribs and Their Solutions
While metal additive manufacturing offers transformative potential for producing complex aerospace wing ribs, the technology is not without its challenges. Understanding these potential metal AM challenges and implementing effective mitigation strategies is key to achieving consistent, high-quality results. Aerospace manufacturers must be aware of these hurdles and work with experienced partners, like Met3dp, who possess the process simulation aerospace les capacités et les Met3dp expertise to overcome them.
Here are some common challenges encountered when 3D printing complex components like wing ribs using PBF, along with solutions:
- Residual Stress, Distortion, and Warping:
- Défi: The intense, localized heating and rapid cooling inherent in PBF processes create significant thermal gradients, leading to internal stresses within the part. These stresses can cause warping distortion 3D printing, parts detaching from the build plate, or cracking, especially in large or complex geometries like wing ribs.
- Solutions :
- Simulation thermique : En utilisant process simulation aerospace software before printing helps predict stress accumulation and distortion patterns. Build parameters and support strategies can be adjusted based on simulation results.
- Optimized Build Parameters: Fine-tuning laser/beam power, scan speed, and scan strategy (e.g., island scanning) can help manage thermal gradients.
- Structures de soutien robustes : Well-designed supports anchor the part securely and help dissipate heat.
- Traitement thermique anti-stress : Performing this step (often before removing the part from the build plate) is crucial for relaxing internal stresses.
- Optimized Part Orientation: Positioning the part to minimize large flat surfaces parallel to the build plate or long unsupported spans can reduce stress effects.
- Support Structure Design and Removal:
- Défi: Designing effective supports that are strong enough during the build but easy to remove afterward is a balancing act. For support removal complex parts like topology-optimized ribs with intricate internal channels or lattices, accessing and removing supports without damaging the part can be extremely difficult and time-consuming. Incomplete support removal can compromise performance or block internal passages.
- Solutions :
- DfAM for Support Minimization: Designing self-supporting angles and features where possible.
- Conception optimisée du support : Using specialized support structures (e.g., tree supports, block supports with perforation) designed for easier removal. Software tools can automate optimized support generation.
- Strategic Orientation: Orienting the part to minimize internal supports or place them in accessible locations.
- Techniques avancées de suppression : Utilizing methods like multi-axis CNC machining or EDM for hard-to-reach supports.
- Porosity Control and Densification:
- Défi: Achieving full density (>99.5%, often >99.9% for aerospace) is critical for mechanical performance, particularly fatigue life. Porosity (small internal voids) can arise from various factors, including trapped gas during atomization, incomplete melting due to incorrect parameters, keyholing (vapor depression instability), or poor powder quality/packing.
- Solutions :
- Paramètres de processus optimisés : Rigorous development and validation of parameters (power, speed, layer thickness, hatch spacing) specific to the material and machine. Met3dp’s focus on optimized méthodes d'impression ensures robust parameter sets.
- Poudre de haute qualité : Using powder with controlled particle size distribution, high sphericity, good flowability, and low internal gas porosity (like those produced by Met3dp’s advanced atomization) is fundamental.
- Controlled Build Environment: Maintaining proper inert gas atmosphere (e.g., Argon, Nitrogen) and flow to remove process byproducts (soot, spatter).
- Pressage isostatique à chaud (HIP) : As a post-processing step, HIP is highly effective at closing residual gas porosity and improving density.
- Surface Finish and Feature Resolution:
- Défi: Achieving the required surface smoothness, especially on down-facing surfaces or intricate features, can be difficult directly from the printer. Minimum feature sizes are limited by the process physics.
- Solutions :
- Optimisation des paramètres : Fine-tuning parameters can improve surface finish to some extent.
- Orientation Strategy: Prioritizing critical surfaces for optimal orientation (up-facing or vertical).
- Post-traitement : Employing machining, polishing, or other surface finishing techniques is usually necessary for critical areas.
- DfAM : Ensuring designs respect the minimum feature size limitations of the chosen process and machine.
- Material Property Consistency and Validation:
- Défi: Ensuring that the mechanical properties (strength, ductility, fatigue life) are consistent throughout the part and from build to build is vital for aerospace certification. Properties can be influenced by minor variations in parameters, powder batches, or machine calibration.
- Solutions :
- Contrôle de processus robuste : Implementing strict quality control over powder handling, machine calibration, and process parameters.
- Caractérisation des matériaux : Extensive testing of material properties using witness coupons printed alongside parts in each build.
- Normalisation : Adhering to established aerospace standards for AM processes and materials (e.g., AMS specs, AS9100 quality systems).
- Partnering with Experts: Working with experienced AM providers like Met3dp who have established quality systems and deep material science knowledge.
Successfully navigating these common metal AM defects and challenges requires a combination of advanced technology, process expertise, rigorous quality control, and smart design strategies (DfAM). Addressing these proactively ensures the reliable production of high-integrity, mission-critical components like aerospace wing ribs.
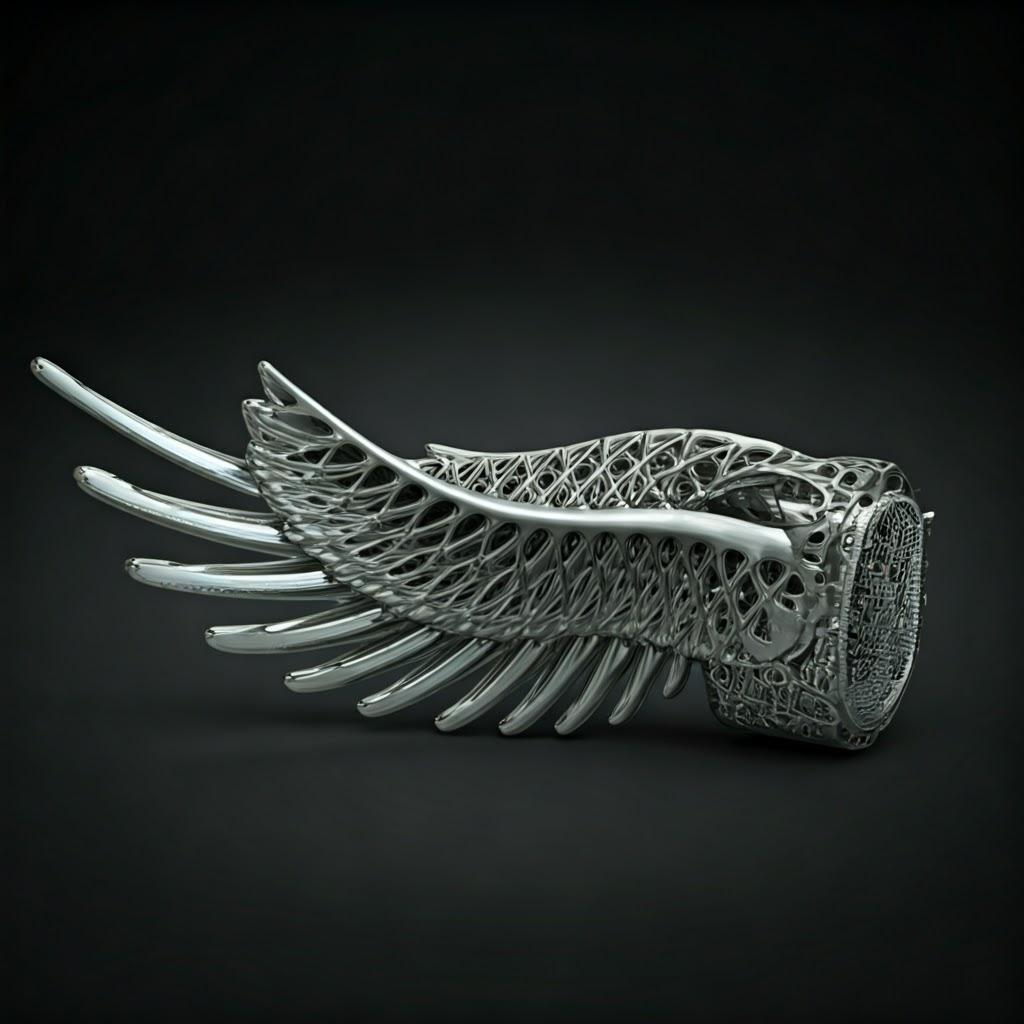
Choosing Your Partner: Selecting the Right Metal 3D Printing Service Provider for Aerospace
Choisir le bon metal 3D printing service provider is as critical as the technology itself, especially when dealing with flight-critical components like aerospace wing ribs. The provider acts as a crucial partner, bringing expertise, certified processes, and reliable execution to the table. For procurement managers and engineers in the aerospace sector, evaluating potential aerospace additive manufacturing suppliers requires a rigorous assessment based on several key criteria:
- Aerospace Certifications and Quality Management System (QMS):
- Mandatory: Rechercher AS9100 certified 3D printing capabilities. AS9100 is the internationally recognized QMS standard for the aerospace industry. Certification demonstrates a commitment to rigorous quality control, traceability, risk management, and continuous improvement processes essential for flight-critical components.
- Verify Scope: Ensure the provider’s certification scope explicitly covers the relevant AM processes (e.g., LPBF), materials (Scalmalloy®, AlSi10Mg), and post-processing steps you require.
- Proven Aerospace Experience and Material Expertise:
- Historique : Does the provider have demonstrable experience manufacturing parts for aerospace applications, particularly structural components? Case studies, references, and examples of past projects are valuable indicators.
- Material Specialization: Expertise in processing the specific alloys required (Scalmalloy®, AlSi10Mg) is crucial. This includes validated parameter sets, understanding material behavior during printing and heat treatment, and managing powder quality. Companies like Met3dp, specializing in both advanced metal powders and printing systems, often possess deep material science knowledge vital for aerospace success.
- Equipment Capabilities and Capacity:
- Technology Match: Ensure they operate the appropriate AM technology (e.g., LPBF for these alloys) with machines known for accuracy and reliability.
- Volume de construction : Does their equipment have the necessary build envelope size to accommodate the dimensions of your wing rib design?
- Machine Maintenance & Calibration: Rigorous maintenance schedules and calibration routines are essential for consistent output.
- Capacity: Can they meet your required production volumes and lead times? Assess their machine availability and overall throughput.
- Powder Quality Control and Traceability:
- Source and Handling: How do they source, test, handle, and store metal powders? Strict controls are needed to prevent contamination and ensure batch-to-batch consistency. Full traceability from powder batch to final part is an aerospace requirement.
- Recycling Strategy: Understand their procedures for powder recycling and rejuvenation to ensure quality is maintained. Met3dp’s foundation in producing high-quality spherical metal powders provides inherent strength in this area.
- Comprehensive Post-Processing Capabilities:
- In-House vs. Outsourced: Does the provider offer the necessary post-processing steps (stress relief, HIP, heat treatment, precision machining, NDT, surface finishing) in-house or through qualified partners? In-house capabilities often streamline the workflow and improve quality control.
- Expertise : Verify their expertise in critical processes like HIP and aerospace-grade NDT.
- Ingénierie et soutien du DfAM :
- Collaboration : Can their engineering team collaborate effectively on Design for Additive Manufacturing (DfAM)? Expertise in topology optimization, support strategy, and process simulation adds significant value, helping optimize designs for printability and performance.
- Transparency and Communication:
- Une communication claire : Look for open communication channels, clear quoting processes, and regular project updates.
- Reporting: Ensure they provide comprehensive quality documentation, including material certifications, process logs, inspection reports, and certificates of conformity.
Table: Key Evaluation Criteria for Aerospace AM Suppliers
Criterion | Why It Matters for Wing Ribs | Questions to Ask |
---|---|---|
Certification AS9100 | Ensures aerospace-level quality, traceability, risk management. Non-negotiable. | Is your certification current? Does its scope cover LPBF with Al/Scalmalloy®? Can you provide the certificate? |
Aerospace Experience | Demonstrates understanding of industry requirements, standards, and component criticality. | Can you share examples/case studies of similar structural aerospace parts you’ve produced? |
Expertise matérielle | Guarantees correct processing, heat treatment, and predictable properties for chosen alloy. | What is your experience with Scalmalloy®/AlSi10Mg? How do you validate process parameters? |
Equipment & Capacity | Ensures parts fit, print reliably, and meet delivery schedules. | What machines do you use? What’s the build volume? What’s your current capacity/typical lead time? |
Powder Control | Critical for part density, mechanical properties, and preventing defects. Traceability needed. | How do you qualify incoming powder? What are your handling and recycling procedures? How is traceability ensured? |
Post-traitement | Essential for achieving final properties, tolerances, and surface finish. HIP often required. | Which post-processing steps are done in-house? Are your sub-contractors AS9100 certified? |
DfAM/Engineering Support | Optimizes design for AM benefits (weight, performance) and manufacturability. | Can your team assist with DfAM? Do you offer simulation services (thermal, topology)? |
QMS & Documentation | Provides objective evidence of quality and conformity required for certification. | Can you provide a sample quality documentation package (CoC, material certs, inspection reports)? |
Exporter vers les feuilles
Choosing the right partner involves careful due diligence. Look for a provider who not only possesses the technical capabilities and certifications but also demonstrates a collaborative approach and a deep understanding of the demanding requirements of the aerospace industry. A supplier like Met3dp, with its dual expertise in advanced materials and printing systems, represents the type of integrated capability valuable for complex aerospace projects.
Demystifying Costs and Timelines for 3D Printed Wing Ribs
Comprendre la metal 3D printing cost factors and typical additive manufacturing lead times is essential for project planning and budgeting when considering AM for aerospace wing ribs. While AM can offer long-term savings through lightweighting and part consolidation, the initial component cost can differ significantly from traditional methods. Transparency from the AM service provider is key to managing expectations.
Key Cost Factors:
- Coût des matériaux :
- Type de poudre : High-performance alloys like Scalmalloy® are significantly more expensive than standard materials like AlSi10Mg or traditional aluminum billets.
- Powder Consumption: The total volume of the part, including support structures, directly impacts the amount of powder consumed. While unused powder can often be recycled, there are costs associated with sieving, testing, and handling.
- Le temps des machines :
- Temps de construction : This is often the most significant cost driver. It depends on:
- Part Volume & Height: Larger and taller parts take longer to print.
- La complexité : Highly complex geometries may require slower scan speeds or intricate support structures, increasing time.
- Nesting Efficiency: How many parts can be printed simultaneously in one build affects the amortization of setup time.
- Machine Depreciation & Operating Costs: These are factored into the hourly rate charged for machine usage.
- Temps de construction : This is often the most significant cost driver. It depends on:
- Coûts de main-d'œuvre :
- Pre-Processing: CAD file preparation, build setup, simulation (if applicable).
- Post-traitement : This can be substantial and includes:
- Depowdering (manual effort, especially for complex parts).
- Stress Relief (furnace time, energy).
- Part Removal from Build Plate (labor, consumables like wire EDM).
- Support Removal (often highly manual).
- Heat Treatment / HIP (furnace time, energy, gas consumption).
- CNC Machining (programming, setup, machine time).
- Surface Finishing (manual polishing, blasting).
- Inspection (NDT, CMM – skilled labor, equipment time).
- Support Structure Volume: Supports consume material and add to print time and post-processing labor for removal. Efficient DfAM minimizes this cost.
- Required Post-Processing Steps: Each step adds cost. HIP, extensive CNC machining, and rigorous NDT are significant cost additions often required for aerospace.
- Quality Assurance & Certification: The level of inspection, testing, and documentation required by aerospace standards adds overhead and direct costs.
- Quantité : Setup costs (build preparation, machine setup) are amortized over the number of parts in a build. Very low quantities (e.g., single prototypes) will have a higher per-part cost than small production runs where multiple parts can be nested.
Délais d'exécution typiques :
Le délai de fabrication additive for a finished aerospace wing rib is typically measured in weeks, not days, due to the multi-stage process involved.
- Quoting & Design Finalization: Days to a week.
- Build Preparation & Scheduling: Days to a week (depending on machine availability).
- Impression : Hours to several days, depending on size, complexity, and nesting.
- Post-traitement : This often takes the longest portion of the lead time.
- Stress relief, cooling, part removal: 1-2 days.
- Support removal: Hours to days (highly variable).
- Heat Treatment / HIP: Can take several days, including furnace cycles and potential batching requirements with external providers.
- CNC Machining: Days to weeks, depending on complexity and shop scheduling.
- Surface Finishing & Inspection: Days.
- Expédition: Days.
Overall: For a complex, fully post-processed and inspected aerospace wing rib, a typical lead time might range from 3 à 8 semaines, sometimes longer depending on HIP/machining backlogs and inspection requirements. Clear communication with the service provider is essential to establish realistic timelines early in the project.
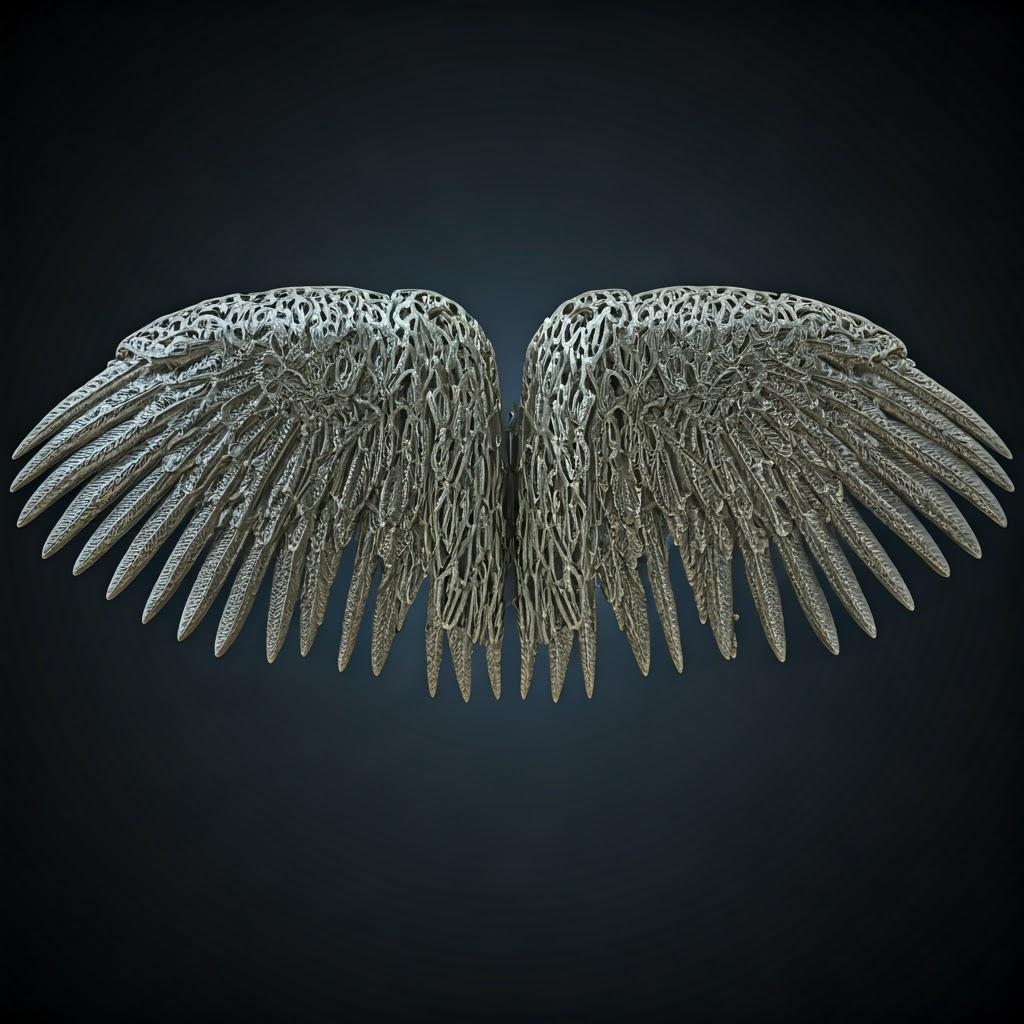
Frequently Asked Questions (FAQ) about Metal 3D Printed Wing Ribs
Here are answers to some common questions regarding the use of metal additive manufacturing for aerospace wing ribs:
- Q1: What are the typical weight savings achieved with AM wing ribs compared to machined ones?
- A : Significant weight savings are a primary driver for using AM. By leveraging topology optimization and advanced DfAM techniques, weight reductions of 20% à 50% ou plus are often achievable compared to conventionally designed and machined wing ribs, while maintaining or improving structural performance. The exact savings depend heavily on the initial design, the degree of optimization applied, and the chosen material (e.g., high specific strength Scalmalloy® enables greater savings).
- Q2: How does the fatigue life of AM Scalmalloy® or AlSi10Mg compare to traditional wrought alloys?
- A : This is a critical consideration for aerospace. As-built AM parts can have lower fatigue life than wrought counterparts due to surface finish and potential micro-porosity. However, with optimized process parameters, mandatory Hot Isostatic Pressing (HIP) to eliminate porosity, and appropriate surface finishing (e.g., machining critical areas), the fatigue performance of AM Scalmalloy® and AlSi10Mg can meet or potentially exceed the requirements for many aerospace applications, sometimes even surpassing cast components. Extensive testing and validation according to aerospace protocols are essential for qualifying parts for fatigue-critical applications.
- Q3: Are 3D printed wing ribs flight-certified?
- A : Certification is a complex process in aerospace. A part isn’t automatically “certified” simply because it was 3D printed. Rather, the manufacturing process (including printing, post-processing, inspection), the material, and the specific part design must be rigorously qualified and certified according to standards set by aviation authorities like the FAA (Federal Aviation Administration) or EASA (European Union Aviation Safety Agency). This 1 involves demonstrating process control, repeatability, material property consistency, and extensive structural testing (static, fatigue, damage tolerance). Achieving flight certification typically requires close collaboration between the design organization, the AM manufacturer (operating under AS9100), and regulatory bodies. Partnering with experienced providers familiar with aerospace qualification pathways is crucial. 1. solvely.ai solvely.ai
- Q4: What information is needed to get an accurate quote for a 3D printed wing rib?
- A : To provide an accurate quote, an AM service provider typically needs:
- Modèle CAO 3D : A well-defined model in a standard format (e.g., STEP, STL).
- Material Specification: Clearly stated alloy (e.g., Scalmalloy®, AlSi10Mg) and any specific material standards.
- Tolerances and Surface Finish: Indication of critical tolerances and required surface finishes on specific features (often via a 2D drawing accompanying the 3D model).
- Exigences en matière de post-traitement : Specification of necessary steps (e.g., Stress Relief, HIP, Heat Treatment condition like T6, specific machining operations, surface treatments).
- Quantité : Number of parts required (affects setup cost amortization).
- Inspection & Certification Level: Required NDT, level of documentation, and any specific aerospace certification requirements.
- A : To provide an accurate quote, an AM service provider typically needs:
Conclusion: The Future of Flight is Additively Manufactured – Partnering for Success
The journey of an aerospace wing rib from digital design to flight-ready component showcases the transformative power of metal additive manufacturing. Technologies like Powder Bed Fusion, coupled with high-performance materials such as Scalmalloy® and AlSi10Mg, unlock unprecedented opportunities for the future aerospace manufacturing landscape. The ability to create highly complex, topology-optimized, and lightweight structures offers tangible benefits: reduced aircraft weight, lower fuel consumption, increased payload capacity, and potentially shorter development cycles through rapid prototyping and part consolidation.
However, realizing these benefits requires more than just access to a 3D printer. It demands a holistic approach encompassing rigorous Design for Additive Manufacturing (DfAM) principles, meticulous process control during printing, comprehensive post-processing steps like heat treatment and HIP, and stringent quality assurance protocols adhering to aerospace standards like AS9100. Navigating the challenges of residual stress, support removal, and achieving consistent material properties is paramount.
Success in leveraging AM for critical components like wing ribs hinges on collaboration and expertise. Choosing the right manufacturing partner – one with proven aerospace experience, deep material knowledge, robust quality systems, and comprehensive capabilities spanning the entire workflow from design support to final inspection – is essential. Companies like Met3dp, with their integrated focus on producing high-quality metal powders and providing advanced additive manufacturing solutions, represent the type of partner needed to navigate this complex but rewarding technological frontier.
As the aerospace industry continues its drive towards greater efficiency, performance, and sustainability, metal additive manufacturing will undoubtedly play an increasingly vital role. By embracing AM and forging strong partnerships with capable suppliers, aerospace companies can accelerate innovation and contribute to the ongoing digital manufacturing transformation, shaping the future of flight one optimized layer at a time.
Partager sur
MET3DP Technology Co. est un fournisseur de premier plan de solutions de fabrication additive dont le siège se trouve à Qingdao, en Chine. Notre société est spécialisée dans les équipements d'impression 3D et les poudres métalliques de haute performance pour les applications industrielles.
Articles connexes
À propos de Met3DP
Mise à jour récente
Notre produit
CONTACTEZ-NOUS
Vous avez des questions ? Envoyez-nous un message dès maintenant ! Nous répondrons à votre demande avec toute une équipe dès réception de votre message.
Obtenir les informations de Metal3DP
Brochure du produit
Obtenir les derniers produits et la liste des prix
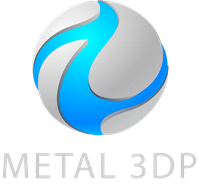
Poudres métalliques pour l'impression 3D et la fabrication additive