Automotive Hinges 3D Printed for Strength and Weight Savings
Table des matières
Revolutionizing Automotive Design: High-Performance Hinges via Metal 3D Printing
The automotive industry is in a constant state of evolution, driven by relentless pressure to enhance performance, improve fuel efficiency (or battery range in electric vehicles), and meet increasingly stringent safety and environmental regulations. Central to achieving these goals is the concept of lightweighting – reducing the overall mass of a vehicle without compromising structural integrity or safety. Every kilogram saved translates into tangible benefits, whether it’s quicker acceleration, sharper handling, extended range, or reduced emissions. While large components like the chassis and body panels receive significant attention, the cumulative weight savings potential of smaller, often overlooked components like hinges is substantial, particularly in high-performance, luxury, and electric vehicle (EV) segments where innovation and optimization are paramount.
High-performance automotive hinges are far more than simple pivots; they are critical structural components responsible for the reliable and safe operation of doors, hoods, trunks (tailgates), and increasingly, complex moving elements like active aerodynamic wings or deployable spoilers. These components must withstand significant static and dynamic loads throughout the vehicle’s lifespan, endure countless opening and closing cycles, resist environmental factors like corrosion, and operate smoothly and precisely every single time. In performance vehicles, hinge failure can be catastrophic, impacting not only convenience but potentially safety and vehicle dynamics. For luxury vehicles, the feel and sound of a hinge contribute significantly to the perception of quality. In EVs, minimizing the weight of every component, including hinges, is crucial for maximizing battery range – a key purchasing factor for consumers.
Traditionally, automotive hinges have been manufactured using methods like stamping, casting, or forging, typically using steel or conventional aluminum alloys. While robust and cost-effective for mass production, these methods often result in parts that are heavier than necessary and impose significant limitations on design complexity. Tooling costs for stamping and forging are substantial, making them less suitable for lower volume or custom applications. Casting can offer more geometric freedom but may suffer from lower strength properties or porosity issues unless carefully controlled. Machining from billet offers precision and strength but generates significant material waste and can be time-consuming.
Enter metal additive manufacturing (AM), commonly known as metal Impression 3D. This transformative technology builds parts layer by layer directly from a digital model using high-performance metal powders. For high-performance automotive hinges, metal AM offers a paradigm shift, unlocking possibilities previously unattainable with conventional manufacturing. It allows engineers to break free from the design constraints imposed by traditional methods, enabling the creation of highly optimized, lightweight structures with intricate geometries tailored precisely to their functional requirements. Technologies like Selective Laser Melting (SLM) and Direct Metal Laser Sintering (DMLS), forms of Laser Powder Bed Fusion (L-PBF), utilize powerful lasers to fuse fine metal powders, layer by microscopic layer, producing dense, high-strength metal parts. This capability is particularly relevant for creating automotive hinges that meet the demanding requirements of performance vehicles, motorsport applications, EVs, and luxury automobiles. The ability to consolidate multiple components into a single printed part, optimize structures using topology optimization, and rapidly prototype and iterate designs makes impression 3D de métaux an increasingly attractive solution for forward-thinking automotive engineers and procurement managers seeking a competitive edge through advanced manufacturing. Companies specializing in additive manufacturing solutions, like Met3dp, provide the necessary equipment, high-quality materials, and expertise to leverage this technology effectively for producing robust, lightweight, and innovative automotive components, including next-generation hinges.
Key Applications & Functions: Where 3D Printed Hinges Excel in Automotive
The application scope for 3D printed high-performance automotive hinges extends far beyond the standard door hinge, touching numerous areas where strength, weight, precision, and design complexity are critical factors. Additive manufacturing allows for tailored solutions that meet specific, often demanding, functional requirements across various vehicle segments.
- Door Hinges: This is perhaps the most obvious application, but AM offers significant advantages even here.
- Standard Doors: Lightweighting standard door hinges contributes significantly to overall vehicle mass reduction, especially when multiplied by four or more doors. Optimized designs can maintain or even increase strength while shedding weight. This is crucial for improving fuel economy in internal combustion engine (ICE) vehicles and extending range in EVs.
- Specialty Doors (Gullwing, Scissor, Suicide Doors): These complex mechanisms often require intricate kinematics, high strength to support potentially heavier doors, and unique packaging solutions. AM allows for the creation of bespoke hinge systems with complex geometries that integrate smoothly into the vehicle’s body structure, something difficult or impossible to achieve with standard off-the-shelf or traditionally manufactured hinges. The ability to create organic, load-path-optimized shapes is a major benefit. Custom car builders and low-volume luxury/performance manufacturers find AM particularly valuable here.
- Hood (Bonnet) Hinges: Hoods, especially on performance cars or trucks, can be large and relatively heavy. Their hinges must support this weight securely, allow for easy opening and closing, and often incorporate safety latch mechanisms. 3D printing allows for the creation of strong yet lightweight hood hinges, potentially integrating features like spring-assist mechanisms or soft-close functionalities within the hinge body itself through clever design. Reducing weight at the front of the vehicle also contributes positively to handling dynamics.
- Trunk/Tailgate Hinges: Similar to hoods, trunks and tailgates require robust hinges. In SUVs and hatchbacks, powered tailgates add complexity, requiring hinges that can withstand the forces exerted by actuators while remaining lightweight. AM enables the design of compact, strong hinges optimized for packaging within tight spaces and capable of integrating mounting points for struts and actuators. For performance vehicles, lightweighting the rear contributes to better weight distribution.
- Glove Compartment & Center Console Hinges: While less load-bearing, hinges in these areas contribute to the perceived quality of a vehicle’s interior. AM can produce hinges with complex kinematics for smooth, damped motion, potentially using advanced materials or integrated features not possible with simple stamped metal or plastic hinges, enhancing the luxury feel.
- Folding Seat Hinges: Particularly in MPVs, SUVs, and vans, folding seat mechanisms involve complex hinges and latches that must be both strong and reliable for safety and convenience. AM allows for part consolidation, reducing the number of individual components in a seat folding mechanism, thereby decreasing weight, assembly time, and potential points of failure. Strength and durability are paramount here.
- Active Aerodynamic Elements: This is a rapidly growing area in performance vehicles. Hinges and actuators for active spoilers, rear wings, front splitters, or cooling flaps must be lightweight, strong, and capable of precise, rapid movement under significant aerodynamic loads. Metal AM is ideally suited for creating the complex, aerodynamically efficient, and highly stressed hinge components required for these systems. Topology optimization can ensure maximum stiffness and strength with minimal weight.
Functional Requirements & Benefiting Industries:
Regardless of the specific application, 3D printed automotive hinges must meet stringent functional requirements:
- Load-Bearing Capacity: Must withstand static weight and dynamic forces during operation and potential impact scenarios. FEA (Finite Element Analysis) is crucial during the design phase.
- Durability & Fatigue Life: Must endure tens of thousands, if not hundreds of thousands, of cycles without failure or excessive wear. Material choice (like A7075) and post-processing (heat treatment) are critical.
- Résistance à la corrosion : Exposure to moisture, road salt, and varying temperatures necessitates good corrosion resistance. Material selection (AlSi10Mg offers good resistance) and surface treatments (anodizing, coatings) are important.
- Smooth & Precise Operation: Hinge kinematics must be accurate to ensure proper alignment of doors/panels, good sealing, and a quality feel. Tolerances and surface finish are key.
- Packaging & Integration: Hinges often need to fit within tight spaces and integrate seamlessly with surrounding body structures and mechanisms. AM’s design freedom is a major advantage here.
The industries and players who stand to benefit significantly from adopting 3D printed hinges include:
- Original Equipment Manufacturers (OEMs): Especially those focused on performance, luxury, and electric vehicles, seeking lightweighting, differentiation, and advanced features.
- Tier 1 Suppliers: Companies designing and supplying complete module assemblies (like doors, seats, closures) can leverage AM to offer innovative, value-added solutions to OEMs.
- Motorsport Teams: Where weight reduction and rapid development of custom, high-strength components offer a direct competitive advantage.
- Custom Car Builders & Tuners: Enabling the creation of unique, high-quality hinge solutions for bespoke vehicle projects.
- Aftermarket Performance Parts Suppliers: Offering lightweight, high-strength hinge upgrades for popular vehicle models.
- Specialty Vehicle Manufacturers: Producers of armored vehicles, recreational vehicles, or industrial vehicles where custom, durable hinge solutions may be required.
By partnering with knowledgeable metal AM service providers and leveraging advanced materials, these industry players can effectively utilize 3D printing to produce superior automotive hinge components. Procurement managers seeking reliable custom automotive hinge suppliers ou automotive component distributors specializing in advanced manufacturing should explore vendors with proven expertise in metal 3D printing services for automotive des applications.
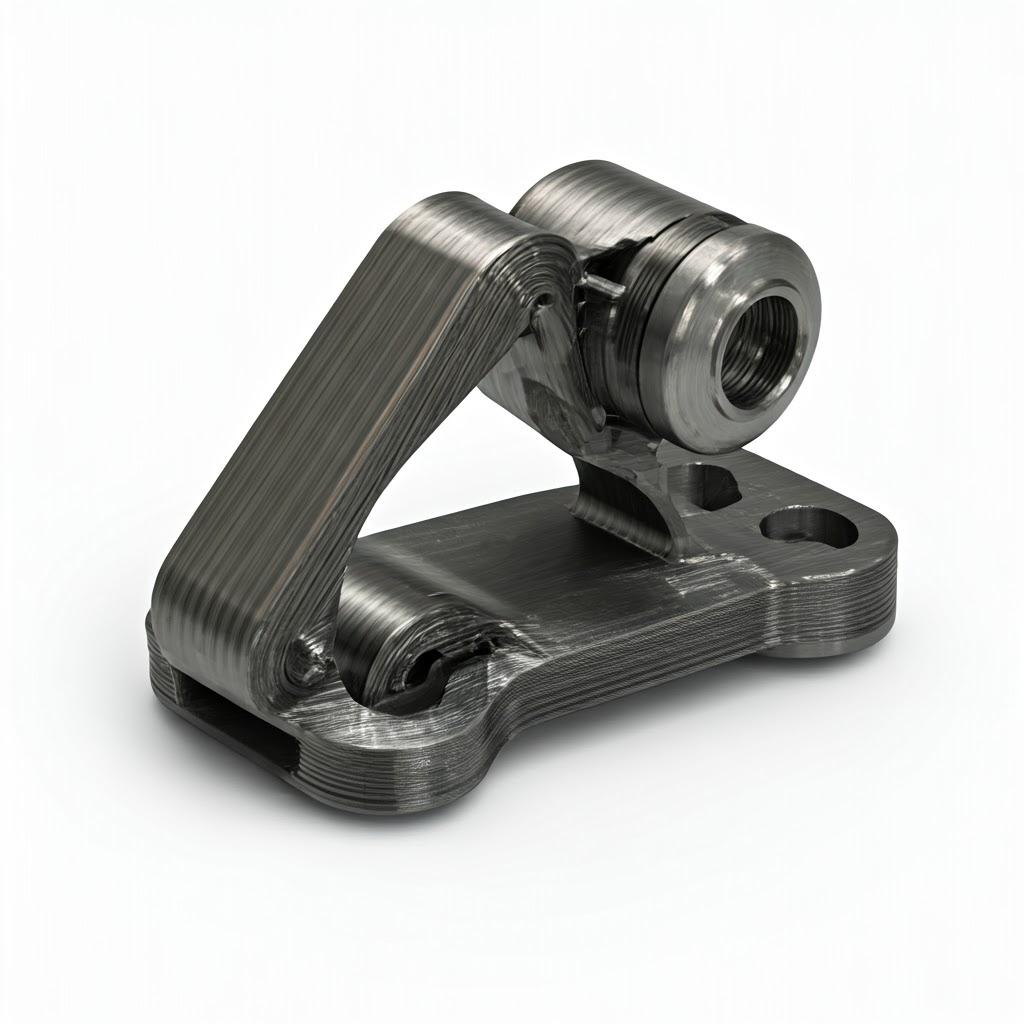
The Additive Advantage: Why Choose Metal 3D Printing for Automotive Hinges?
While traditional manufacturing methods have served the automotive industry well for decades, they present inherent limitations, particularly when producing high-performance hinges where complexity, customization, and weight are critical. Metal additive manufacturing (AM) offers a compelling suite of advantages that directly address these limitations, positioning it as a superior choice for next-generation hinge development and production in many scenarios.
Comparison with Traditional Methods:
- Stamping: Excellent for high-volume production of relatively simple, sheet-metal-based hinge parts. However, it requires extremely expensive tooling (dies), offers limited geometric complexity (primarily 2.5D shapes), and is ill-suited for low-to-medium volumes or design iterations due to tooling costs and lead times. Material choice is also somewhat restricted.
- Casting : Allows for more complex shapes than stamping and can be cost-effective at moderate volumes. However, achieving high strength often requires specific alloys and processes, porosity can be a concern affecting structural integrity, and secondary machining is usually required for precision features. Tooling (molds) still represents a significant upfront investment and lead time. Achieving the thin walls and intricate details possible with AM can be challenging.
- Forgeage : Produces parts with excellent strength and fatigue properties due to the grain structure refinement. However, forging is typically limited to simpler geometries compared to casting or AM, requires expensive tooling, and often necessitates significant post-machining, leading to material waste. Best suited for high-load, simpler hinge components in very high volumes.
- CNC Machining (from Billet): Offers high precision and excellent material properties (starting from solid stock). However, it generates substantial material waste (buy-to-fly ratio can be poor), can be slow for complex geometries, and becomes expensive for intricate parts or large production runs due to machine time and tool wear.
Advantages of Metal Additive Manufacturing for Hinges:
Metal AM, particularly L-PBF processes like SLM/DMLS, overcomes many of these hurdles:
- Liberté de conception inégalée : This is arguably the most significant advantage. AM builds parts layer by layer, freeing designers from the constraints of molds, dies, or tool access. This enables:
- Géométries complexes : Creation of intricate internal structures, conformal channels (e.g., for lubrication or integrated wiring), and organic shapes impossible to produce conventionally.
- Optimisation de la topologie : Using software to analyze load paths and remove material from non-critical areas, resulting in hinges that are significantly lighter (often 30-60% weight reduction) while maintaining or even increasing stiffness and strength precisely where needed.
- Structures en treillis : Incorporating internal lattice structures further reduces weight and material usage while providing tailored structural support.
- Réduction significative du poids : Directly linked to design freedom, AM excels at creating lightweight structures. Topology optimization and lattice structures allow for radical reductions in mass compared to solid parts produced by casting, forging, or machining, directly contributing to vehicle efficiency and performance goals.
- Consolidation partielle : Complex hinge assemblies often consist of multiple individual components (brackets, arms, pins, mounts) that need to be manufactured separately and then assembled. AM allows designers to consolidate several functions into a single, monolithic printed part. This reduces part count, simplifies assembly, minimizes tolerance stack-up issues, lowers assembly labor costs, and eliminates potential failure points at joints or fasteners.
- Prototypage rapide et itération : Creating physical prototypes of new hinge designs is significantly faster with AM compared to waiting for traditional tooling. Engineers can design, print, test, and refine hinge prototypes in days rather than weeks or months. This accelerates the development cycle, allows for more design exploration, and reduces the risk associated with committing to expensive tooling too early. This agility is invaluable for rapid prototyping automotive hinges.
- Material Efficiency (Near-Net Shape): AM processes like L-PBF typically use only the material needed to build the part and its supports, resulting in significantly less waste compared to subtractive manufacturing (CNC machining). While powder recycling is essential, the buy-to-fly ratio is generally much better, making it more sustainable and cost-effective for expensive alloys.
- Viable On-Demand & Low-Volume Production: The elimination of physical tooling makes AM economically viable for producing small batches of specialized hinges, custom designs for bespoke vehicles, or aftermarket parts. Manufacturers can produce hinges on-demand, reducing inventory costs and enabling mass customization strategies. This is ideal for low-volume automotive hinge manufacturing.
- Tool-less Manufacturing: AM requires no part-specific tooling (molds, dies). Designs go directly from CAD to the machine, drastically reducing lead times for the first parts and eliminating tooling costs, which can range from thousands to hundreds of thousands of dollars for traditional methods.
While AM might not replace traditional methods for every hinge in every vehicle (especially standard hinges in high-volume, cost-sensitive models), its advantages make it the clear choice for applications demanding maximum performance, minimal weight, complex functionality, or rapid customization. The additive manufacturing automotive benefits are particularly pronounced in the context of high-performance hinges, enabling designs and performance levels previously unachievable. Businesses looking for on-demand automotive parts production ou metal AM vs casting comparisons for complex components will find compelling reasons to explore additive solutions.
Material Focus: A7075 & AlSi10Mg Aluminum Alloys for Demanding Hinge Applications
The performance of a 3D printed automotive hinge is fundamentally dictated by the material used. While various metals can be processed using additive manufacturing, aluminum alloys are frequently chosen for automotive applications due to their excellent balance of low density, good mechanical properties, and corrosion resistance. For high-performance hinges requiring superior strength or a balance of properties, two alloys stand out in the realm of Laser Powder Bed Fusion (L-PBF): A7075 (an aluminum-zinc alloy) and AlSi10Mg (an aluminum-silicon-magnesium alloy). Selecting the right material is critical and depends heavily on the specific load requirements, operating environment, and performance targets for the hinge.
A7075 Aluminum Alloy:
A7075 is renowned in the aerospace and high-performance automotive industries for its exceptional strength-to-weight ratio, often comparable to that of some steels but at roughly one-third the density. It’s an aluminum alloy primarily alloyed with zinc, along with smaller amounts of magnesium and copper.
- Propriétés principales :
- Haute résistance : Exhibits very high yield and ultimate tensile strength, especially after appropriate heat treatment (typically T6 condition). This makes it suitable for hinges subjected to significant static and dynamic loads.
- Bonne résistance à la fatigue : Resists failure under cyclic loading, crucial for components like door or hood hinges that undergo repeated opening and closing cycles.
- Bonne usinabilité : Can be machined to achieve tight tolerances on critical surfaces after printing.
- Lower Corrosion Resistance (compared to other Al alloys): More susceptible to corrosion, especially stress corrosion cracking, if not properly protected (e.g., via anodizing or painting).
- Soudabilité : Generally considered poor for welding.
- Typical Automotive Uses (Traditional & AM): High-stress structural components, suspension parts, chassis elements, and applications where maximum strength with minimum weight is paramount. In AM, it’s targeted for load-bearing hinges in motorsport, performance vehicles, or safety-critical applications.
- Considerations for AM Processing: Printing A7075 via L-PBF can be challenging due to its susceptibility to hot cracking during the rapid heating and cooling cycles inherent in the process. Achieving dense, crack-free parts requires carefully controlled process parameters, specialized machine capabilities, and often specific powder characteristics. Post-print heat treatment (solutionizing, quenching, and aging – T6 temper) is essential to develop its full strength potential. Finding an A7075 3D printing service with proven experience in processing this alloy is crucial.
AlSi10Mg Aluminum Alloy:
AlSi10Mg is one of the most widely used aluminum alloys in metal additive manufacturing, particularly L-PBF. It’s essentially a casting alloy composition adapted for AM, known for its excellent printability and balanced properties.
- Propriétés principales :
- Good Strength & Hardness: Offers a good combination of strength and hardness, suitable for many structural automotive applications, though typically lower strength than optimally heat-treated A7075.
- Excellente imprimabilité : Relatively easy to process via L-PBF, less prone to cracking than high-strength alloys like A7075, allowing for reliable production of complex geometries.
- Bonne résistance à la corrosion : Offers better inherent corrosion resistance than A7075.
- Good Thermal Properties: Suitable for applications experiencing moderate temperature changes.
- Bonne soudabilité : Can be welded more readily than A7075.
- Common AM Applications: Widely used for engine components (pistons, blocks – though less common for hinges), heat exchangers, housings, brackets, and general structural components where a balance of printability, strength, and weight is needed. It’s a workhorse alloy for many AlSi10Mg automotive parts suppliers.
- Considerations for AM Processing: While easier to print than A7075, achieving optimal mechanical properties still requires careful parameter control and typically involves post-print heat treatment (stress relief and/or aging, similar to T6 but tailored for the Si content) to maximize strength and ductility.
Comparative Analysis for Hinge Applications:
Fonctionnalité | A7075 | AlSi10Mg | Considerations for Hinges |
---|---|---|---|
La force | Very High (post T6 treatment) | Good to High (post heat treatment) | Choose A7075 for maximum load-bearing capacity or extreme fatigue requirements. AlSi10Mg is sufficient for many standard/moderate load hinges. |
Poids | Faible densité | Low Density (Slightly lower than A7075) | Both offer significant weight savings over steel. AlSi10Mg has a slight edge in density. |
Imprimabilité | Challenging (requires expertise) | Excellent (well-established process) | AlSi10Mg generally allows for easier, potentially faster, and more reliable printing. |
Corrosion Resist. | Moderate (requires protection) | Bon | AlSi10Mg may require less aggressive surface treatment for corrosion protection. |
Résistance à la fatigue | Bon | Moderate to Good | A7075 typically offers better fatigue performance under high stress cycles. |
Coût | Higher (powder & processing complexity) | Modéré | AlSi10Mg is often more cost-effective due to easier processing and wider availability. |
Post-traitement | T6 Heat Treatment essential for strength | Heat Treatment recommended for properties | Both require similar steps (support removal, machining), but A7075 heat treatment is critical. |
Exporter vers les feuilles
The Importance of Powder Quality:
Regardless of the alloy chosen, the quality of the metal powder used in the L-PBF process is paramount to achieving high-quality, reliable hinges. The powder particles must be:
- Sphérique : Ensures good powder flowability within the printer’s recoating mechanism and dense packing on the powder bed, leading to consistent melting and reduced porosity.
- Distribution contrôlée de la taille des particules (PSD) : A specific PSD is required for optimal packing density and melting behavior with a given set of laser parameters.
- Haute pureté : Free from contaminants that could compromise the mechanical properties or introduce defects in the final part.
- Low Moisture and Oxygen Content: Prevents oxidation and porosity during the high-temperature printing process.
This is where specialized metal 3D printing powder suppliers play a critical role. Companies like Met3dp, utilizing advanced powder production techniques such as des technologies de pointe en matière d'atomisation des gaz et de traitement par électrodes rotatives à plasma (PREP), are essential partners. Met3dp’s capability to research and manufacture high-quality, spherical metallic powders, including aluminum alloys optimized for AM, ensures that manufacturers have access to the consistent, high-performance materials needed to reliably produce demanding components like automotive hinges. Their focus on unique nozzle and gas flow designs in gas atomization results in powders with the high sphericity and flowability crucial for successful L-PBF printing of alloys like A7075 and AlSi10Mg. Partnering with a provider like Met3dp, who controls both the powder manufacturing and potentially the printing process, offers a significant advantage in ensuring end-to-end quality and performance for critical automotive applications. Procurement managers evaluating an aluminum alloys AM strategy should prioritize suppliers with demonstrable expertise in powder metallurgy and processing.
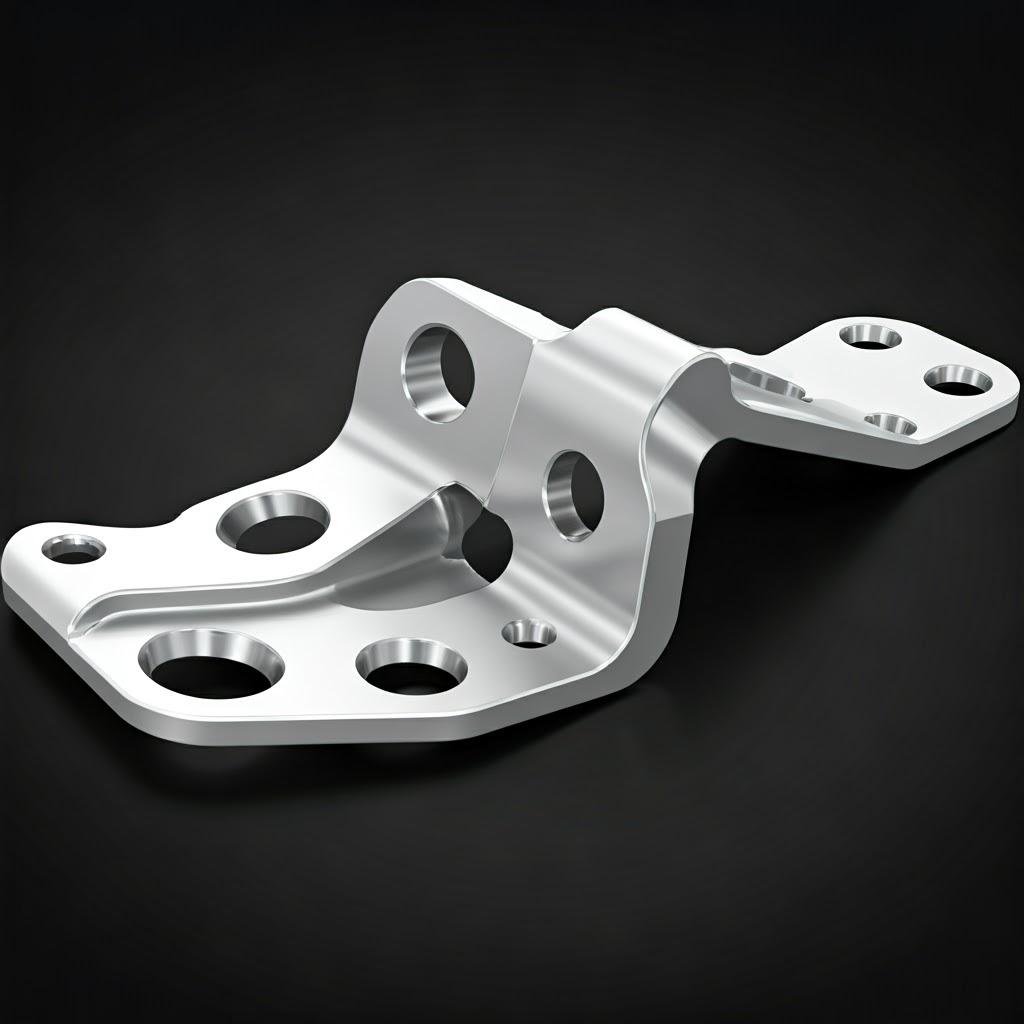
Design for Additive Manufacturing (DfAM): Optimizing Hinges for 3D Printing Success
One of the most profound shifts enabled by metal additive manufacturing (AM) is the liberation from traditional design constraints. However, simply taking a hinge design intended for casting or machining and sending it to a 3D printer rarely unlocks the full potential of AM. To truly harness the benefits of strength-to-weight optimization, part consolidation, and enhanced functionality, engineers must embrace Conception pour la fabrication additive (DfAM) principles. DfAM is not merely about making a part printable; it’s about fundamentally rethinking the design to leverage the unique capabilities of layer-by-layer fabrication. For high-performance automotive hinges, applying DfAM is not just beneficial – it’s essential for achieving competitive advantages in weight, performance, and cost-effectiveness.
Failing to apply DfAM principles can lead to suboptimal results: parts that require excessive support structures (increasing print time, material consumption, and post-processing effort), unachieved weight-saving potential, higher internal stresses leading to potential failure, or even print failures altogether. Conversely, a well-executed DfAM strategy, often developed in collaboration with experienced AM service providers, ensures that the final hinge component is lighter, stronger, more functional, and cost-effective to produce via AM.
Key DfAM Principles for Automotive Hinges:
- Optimisation de la topologie : This is a cornerstone of lightweighting in AM. Topology optimization software uses Finite Element Analysis (FEA) to simulate the loads and stresses a hinge will experience during its operational life (e.g., supporting door weight, enduring closing forces). Based on these simulations, the software intelligently removes material from areas that do not contribute significantly to the part’s structural integrity, leaving behind an organic, load-path-optimized structure.
- Processus : Define design space, loads, constraints (e.g., mounting points, pivot locations, keep-out zones), and optimization goals (e.g., minimize mass, maximize stiffness).
- Software Examples: Altair OptiStruct, ANSYS Discovery, Dassault Systèmes SOLIDWORKS Simulation/CATIA Generative Design, Autodesk Fusion 360 Generative Design, nTopology.
- Benefits for Hinges: Significant weight reduction (often 30-60% or more compared to a solid design) while maintaining or exceeding original strength/stiffness requirements. Creates highly efficient structures perfectly tailored to their specific load case. Essential for lightweight hinge design.
- Considérations : Optimized shapes can be complex and may require smoothing or interpretation for manufacturability, even with AM. Ensuring load cases accurately reflect real-world conditions is critical.
- Lattice Structures & Infill Strategies: Beyond optimizing the overall shape, DfAM allows for the incorporation of internal lattice structures within the solid shell of the hinge. These repeating geometric patterns (e.g., strut-based like cubic or octet-truss, or surface-based like gyroids or other Triply Periodic Minimal Surfaces – TPMS) replace solid material, drastically reducing weight and material consumption while providing tailored structural support and potentially other benefits like energy absorption or vibration damping.
- Les types: Varying densities and cell types can be used in different regions of the hinge based on local stress levels.
- Avantages : Further weight reduction beyond topology optimization alone, potential for enhanced impact absorption (relevant for crashworthiness), improved thermal management if designed correctly.
- Défis : Ensuring printability of fine lattice struts, effective removal of trapped powder from internal cavities (crucial!), potential stress concentrations at node points if not designed carefully. Requires specialized software capabilities (e.g., nTopology, Materialise 3-matic).
- Épaisseur minimale de la paroi et dimensions de l'élément : AM processes have limitations on the minimum size of features they can reliably produce. This is influenced by the laser spot size, powder particle size, and melt pool dynamics. For L-PBF processes used with aluminum alloys like A7075 and AlSi10Mg, minimum printable wall thicknesses are typically in the range of 0.4 mm to 0.8 mm, though thicker walls are generally recommended for structural integrity. Small features like pivot pins or fine details must respect these limitations. Designing walls or features that are too thin can lead to incomplete formation, warping, or failure during printing or use.
- Hinge Relevance: Critical for designing thin reinforcing ribs, lightweight arms, or small integrated features within the hinge assembly.
- Designing for Minimal Support Structures: L-PBF processes require support structures for overhangs (surfaces angled less than ~45 degrees from the horizontal build plate) and to anchor the part to the build plate, manage thermal stress, and prevent warping. However, support structures add print time, consume material, require significant post-processing effort for removal, and can negatively impact the surface finish where they attach. Effective DfAM aims to minimizing support structures AM par:
- Orientation Strategy: Orienting the hinge on the build plate to maximize self-supporting angles. Complex hinges might require careful analysis to find the optimal orientation balancing support needs, print time, and surface quality requirements.
- Designing Self-Supporting Features: Incorporating chamfers or fillets instead of sharp horizontal overhangs where possible. Using diamond or teardrop shapes for horizontal holes instead of simple circles can make them self-supporting.
- Support Optimization Software: Using build preparation software to generate efficient support structures (e.g., tree supports, block supports with optimized interfaces) that are easier to remove.
- Consolidation partielle : As mentioned previously, AM’s ability to create complex geometries allows multiple components of a traditional hinge assembly (e.g., hinge body, mounting bracket, reinforcing plates, spring perch) to be redesigned and printed as a single, monolithic piece.
- Avantages : Reduced part count, simplified assembly, lower inventory needs, elimination of fasteners/joints (potential failure points), improved structural integrity, often reduced overall weight.
- Example: Designing a door hinge where the body structure, the mounting flange for the A-pillar, and the mounting points for a gas strut are all integrated into one printed component.
- Considering Kinematics and Clearance: Hinges are dynamic components. DfAM must account for the movement of the hinge parts relative to each other and the surrounding vehicle structure.
- Pivot Design: Designing pivot points (bores, pins) with appropriate clearances to allow smooth movement without binding, considering the achievable tolerances of the AM process and any planned post-machining steps.
- Mating Surfaces: Ensuring sufficient clearance between moving parts throughout the range of motion.
- Simulation : Using CAD tools to simulate the hinge’s kinematic motion to check for interferences or undesirable movement patterns early in the design phase.
Collaboration and Software:
Effective DfAM often involves an iterative process using a suite of software tools – starting with CAD for initial geometry, moving to FEA and topology optimization for structural efficiency, potentially using specialized lattice design tools, and finally employing build preparation software (e.g., Materialise Magics, Autodesk Netfabb) to orient the part, generate supports, and slice the model for the printer. Collaboration between the automotive design engineers and the AM service provider is highly recommended. Providers like Met3dp, with expertise across materials, solutions de fabrication additive, and DfAM, can offer invaluable input during the design phase to ensure the hinge is optimized for successful and efficient production, leveraging their deep understanding of process capabilities and material behavior. Their experience can help avoid common pitfalls and maximize the benefits achievable through DfAM aluminum parts.
Achieving Precision: Tolerance, Surface Finish, and Dimensional Accuracy in 3D Printed Hinges
While metal AM offers incredible design freedom, achieving the necessary precision for functional components like automotive hinges requires a thorough understanding of the process’s capabilities regarding tolerances, surface finish, and overall dimensional accuracy. Hinges rely on precise alignment and clearances for smooth, reliable operation and proper sealing of doors or panels. Understanding what L-PBF processes can deliver, and how various factors influence the outcome, is crucial for setting realistic expectations and planning necessary post-processing steps.
Tolerances in Metal AM:
Unlike traditional CNC machining, which can readily achieve tolerances in the tens of microns, as-printed metal AM parts generally have looser tolerances. While specific standards are still evolving, a common reference point is often adapted from general machining tolerances (like ISO 2768-m or -f), but dedicated AM standards like ISO/ASTM 52902 provide better guidance on geometric dimensioning and tolerancing (GD&T) for additive parts.
- Typical Achievable Tolerances (L-PBF, A7075/AlSi10Mg):
- For smaller features (e.g., up to 100 mm): Typically in the range of +/- 0.1 mm to +/- 0.3 mm.
- For larger dimensions: Often expressed as a percentage, e.g., +/- 0.1% to 0.2% of the nominal dimension.
- Remarque : These are general guidelines. Achievable tolerances are highly dependent on the factors listed below. Tighter tolerances often require post-machining.
Facteurs influençant la précision dimensionnelle :
Achieving consistent dimensional accuracy additive manufacturing is complex, influenced by numerous interacting factors:
- Étalonnage de la machine : The accuracy of the laser scanning system, the flatness and leveling of the build plate, and the precise control over the Z-axis (layer height) are fundamental. Regular calibration and maintenance are essential. Met3dp emphasizes the accuracy and reliability of their printers, which is crucial for consistent results.
- Paramètres du processus : Settings like laser power, scan speed, hatch spacing, and layer thickness directly impact the size and stability of the melt pool, affecting shrinkage, residual stress, and final part dimensions. Optimized parameter sets specific to the material (A7075 vs. AlSi10Mg behave differently) and machine are critical.
- Propriétés du matériau : Each alloy has unique thermal properties (conductivity, expansion coefficient) and shrinkage behavior during solidification and cooling. These must be accounted for in process planning, sometimes requiring scaling adjustments in the build preparation software.
- Part Geometry and Orientation:
- Thermal Mass: Large, solid sections retain heat differently than thin walls, leading to differential shrinkage and potential distortion.
- Orientation: The orientation on the build plate affects heat distribution, support requirements, and how shrinkage accumulates across layers.
- Surplombs : Areas built on supports often exhibit slightly different dimensional behavior and surface characteristics.
- Stratégie de soutien : The type, density, and location of support structures influence heat dissipation and anchoring, affecting stress buildup and potential distortion during and after printing.
- Contraintes thermiques : The rapid heating and cooling inherent in Fusion laser sur lit de poudre generate internal stresses. If not managed properly (through parameters, supports, stress relief), these stresses can cause warping during the build or distortion after removal from the build plate.
- Post-traitement :
- Traitement thermique : Stress relief and aging cycles can cause slight dimensional changes (shrinkage or growth) that need to be anticipated. Quenching (especially for A7075 T6) can introduce distortion if not carefully controlled (e.g., using fixtures).
- Machining/Finishing: Any material removal step will obviously change dimensions and must be precisely controlled to meet final tolerance requirements.
Surface Finish (Roughness – Ra):
The surface finish of as-printed metal AM parts is inherently rougher than machined surfaces due to the layer-by-layer process and partially melted powder particles adhering to the surface. Surface roughness is typically measured as Ra (average roughness).
- As-Printed Ra Values (L-PBF): Generally range from 5 µm to 25 µm Ra.
- Factors Influencing Ra:
- Surface Orientation: Vertical walls tend to be smoother than top (up-skin) surfaces. Bottom (down-skin) surfaces that rested on supports are typically the roughest due to support contact points.
- Épaisseur de la couche : Thinner layers generally produce slightly smoother surfaces.
- Paramètres du processus : Laser power, scan speed, and powder characteristics influence surface melt behavior.
- Impact on Hinges: High roughness, especially on pivot surfaces or mating faces, can cause excessive friction, wear, and prevent smooth operation. Rough surfaces can also be initiation sites for fatigue cracks and may compromise sealing.
- Amélioration de l'état de surface : Post-processing steps like bead blasting, tumbling, polishing, or CNC machining are typically required to achieve smoother finishes (often < 1 µm Ra is possible with machining/polishing) on critical hinge surfaces.
Importance of Precision for Hinges:
For an automotive hinge, dimensional accuracy and appropriate surface finish are not just aesthetic concerns; they are critical for function and safety:
- Pivot Alignment: Accurate positioning and sizing of pivot bores and pins ensure smooth rotation without binding or excessive play.
- Clearances: Correct gaps between moving parts prevent interference and allow for lubrication or thermal expansion.
- Mounting Interfaces: Precise location and flatness of mounting surfaces ensure the hinge aligns correctly with the vehicle body (A-pillar, door frame, etc.), enabling proper door/panel closure, sealing, and load distribution.
- Sealing: Smooth mating surfaces may be required if the hinge forms part of a weather seal.
Métrologie et contrôle de la qualité :
Ensuring hinges meet specified tolerances requires robust metrology. Coordinate Measuring Machines (CMMs) provide high-accuracy point measurements, while non-contact 3D scanning (laser or structured light) captures the full part geometry, allowing comparison to the original CAD model (scan-to-CAD). Surface roughness testers quantify the finish. Implementing a rigorous Quality Management System (QMS), encompassing process monitoring, material traceability, and final inspection, is essential for suppliers of critical automotive component precision parts like hinges. Reputable service providers will have established procedures for CMM inspection AM parts and other necessary quality checks.
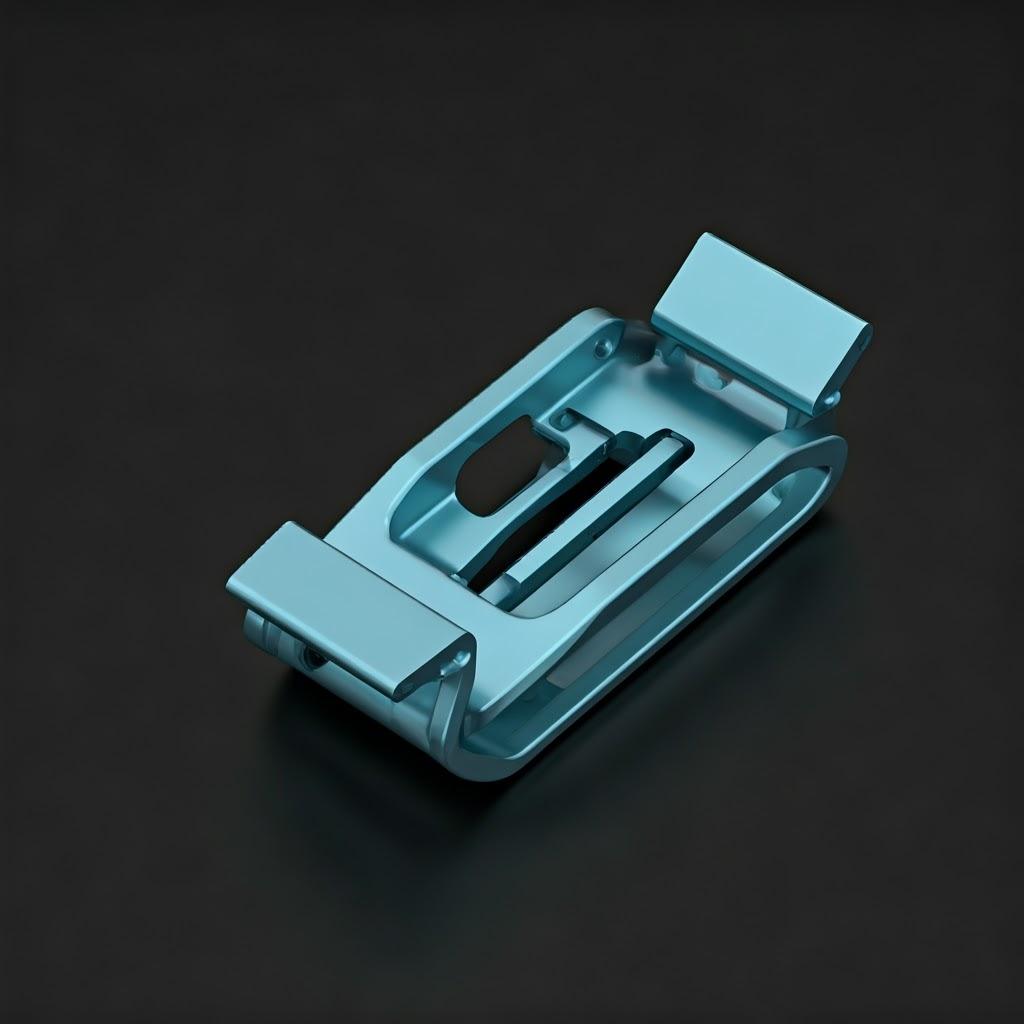
Beyond Printing: Essential Post-Processing Steps for Automotive Hinges
A common misconception about metal 3D printing is that the part emerging from the printer is the final product. In reality, for demanding applications like high-performance automotive hinges made from A7075 or AlSi10Mg, the printing stage is just one part of a multi-step manufacturing workflow. Post-processing is not optional; it’s a critical sequence of operations required to transform the raw printed part into a functional, reliable, and durable component that meets engineering specifications. These steps are essential to relieve stress, achieve desired material properties, remove temporary structures, attain required tolerances and surface finishes, and ensure long-term performance through treatments like anodizing aluminum hinges.
The specific post-processing steps required depend on the material, design complexity, and application requirements, but a typical workflow for L-PBF aluminum hinges includes:
- Soulagement du stress / Traitement thermique : This is often the first crucial step after printing, sometimes performed while the part is still attached to the build plate.
- Objet : The rapid heating/cooling cycles during L-PBF create significant internal stresses within the printed part. These stresses can cause distortion upon removal from the build plate or even lead to cracking later in the part’s life if not relieved. Heat treatment also homogenizes the microstructure and develops the final desired mechanical properties (strength, ductility, hardness).
- Process for AlSi10Mg:
- Soulagement du stress : Typically involves heating to around 300°C for approximately 2 hours, followed by slow cooling. This reduces internal stresses with minimal impact on hardness.
- Solution Annealing & Aging (T6-like): For higher strength, parts may undergo solution treatment at higher temperatures (~500-540°C), followed by quenching and artificial aging (~150-170°C for several hours). Specific parameters depend on the desired balance of strength and ductility.
- Process for A7075: Achieving the high strength A7075 is known for absolutely requires a T6 heat treatment:
- Traitement des solutions : Heating to ~470-490°C for a specific duration to dissolve alloying elements into the aluminum matrix.
- Trempe : Rapid cooling (typically in water) to lock the elements in solution. This step can induce significant distortion if not carefully managed (e.g., controlled quenching rate, potential use of fixtures for complex geometries).
- Vieillissement artificiel : Heating to a lower temperature (~120°C) for an extended period (e.g., 24 hours) to precipitate strengthening phases.
- Atmosphere: Heat treatments are typically performed in inert gas (argon, nitrogen) or vacuum furnaces to prevent oxidation.
- Retrait de la pièce de la plaque de construction : Once cooled (and potentially stress-relieved), the printed hinge needs to be separated from the metal build plate it was fused to. This is commonly done using:
- Wire Electrical Discharge Machining (Wire EDM): Precise method, good for complex interfaces.
- Band Sawing: Faster but less precise, suitable for simpler geometries.
- Retrait de la structure de soutien : The supports generated during printing must be removed. This is often a labor-intensive process.
- Méthodes : Manual breaking/cutting with hand tools (for accessible supports), CNC machining (for precise removal or hard-to-reach areas), sometimes electrochemical machining or abrasive flow machining for internal channels.
- Défis : Can leave witness marks or rough surfaces requiring further finishing. Removing supports from delicate features or complex internal geometries (like lattices) requires careful planning and execution. Effective support removal metal AM techniques are key to efficient post-processing.
- Finition de la surface : As-printed surfaces are typically rough and may have partially sintered particles. Various techniques are used to achieve the desired finish for aesthetics, friction reduction, or preparation for coating.
- Cleaning: Thorough removal of loose or trapped powder, often using compressed air, brushing, or ultrasonic cleaning, especially critical for internal channels or lattice structures.
- Abrasive Blasting (Bead, Sand, Grit): Propelling abrasive media at the surface to remove loose particles, create a uniform matte texture, and slightly improve fatigue properties through compressive stress introduction. Choice of media affects the final finish.
- Tambourinage / Finition vibratoire : Placing parts in a tumbler with abrasive media to deburr edges, smooth surfaces, and achieve a consistent finish, particularly effective for batches of smaller components.
- Polissage : Using progressively finer abrasives (manual or automated) to achieve very smooth, mirror-like finishes (Ra < 1 µm) where required for low friction (pivots) or high aesthetic value.
- Anodizing: An electrochemical process specific to aluminum and its alloys. It grows a controlled oxide layer on the surface, significantly improving corrosion resistance (vital for A7075) and wear resistance. Type II anodizing offers good protection and can be dyed various colors. Type III (hardcoat) anodizing creates a much thicker, harder layer for extreme wear resistance but can slightly impact fatigue life.
- Painting/Powder Coating: Applying organic coatings for aesthetic color choices or additional layers of environmental protection over anodizing or a conversion coating.
- Usinage CNC : Even with optimized AM processes, achieving the tightest tolerances (e.g., for pivot bores, bearing seats, critical mounting faces) often requires secondary CNC machining AM components.
- Objet : To machine critical features to final dimensions and tolerances that exceed the as-printed capability. Creating precise threads, O-ring grooves, or ensuring flatness/parallelism of mating surfaces.
- Considérations : Requires accurate fixturing of the potentially complex AM part. Machining allowances must be considered during the DfAM phase.
- Inspection and Quality Control (QC): Final verification that the hinge meets all specifications.
- Méthodes : Dimensional checks (CMM, 3D scanning), surface finish measurement, visual inspection, material property verification (if test coupons were printed alongside), potentially NDT (e.g., CT scanning for internal defect detection in critical parts).
Impact on Cost, Lead Time & Properties:
Each post-processing step adds cost (labor, machine time, consumables) and extends the overall lead time. Complex finishing requirements or tight tolerances necessitating extensive machining significantly impact the final piece price. Heat treatment, while essential for properties, requires furnace time and careful handling. Therefore, optimizing the design (DfAM) to minimize complex support structures and reduce the need for extensive machining is crucial for cost-effective production. Partnering with a service provider like Met3dp, which offers a comprehensive suite of in-house post-processing additive manufacturing capabilities alongside printing, can streamline the workflow, improve quality control, and potentially reduce overall lead times compared to managing multiple vendors. Understanding the interplay between design, printing, and post-processing is key for procurement managers evaluating surface finishing automotive parts suppliers.
Navigating Challenges: Common Issues in 3D Printing Hinges and Mitigation Strategies
While metal additive manufacturing offers immense potential for producing high-performance automotive hinges, it’s not without its challenges. Understanding these potential issues and the strategies to mitigate them is crucial for successfully implementing AM technology. Automotive engineers and procurement managers should be aware of these complexities when specifying parts and selecting manufacturing partners. The production of reliable A7075 and AlSi10Mg hinges via L-PBF requires careful control over numerous variables.
Common Challenges and How to Avoid Them:
- Déformation et distorsion :
- Cause : Uneven heating and cooling during the layer-by-layer process leads to the buildup of internal thermal stresses. When the part is released from the build plate’s anchoring effect, these stresses can cause it to warp or distort, deviating from the intended geometry. This is a significant metal AM challenges automotive issue.
- Atténuation :
- Optimized Part Orientation: Placing the part on the build plate to minimize large, flat surfaces parallel to the plate and reduce thermal gradients.
- Structures de soutien robustes : Properly designed supports anchor the part securely and help conduct heat away, reducing stress accumulation.
- Build Plate Heating: Preheating the build plate reduces the temperature differential between the solidified material and the new layer, lessening stress.
- Simulation de processus : Using software to predict thermal behavior and potential distortion before printing, allowing for adjustments to orientation or supports.
- Stratégies d'analyse optimisées : Using specific laser scanning patterns (e.g., island scanning, checkerboard patterns) to distribute heat more evenly.
- Immediate Stress Relief: Performing a stress relief heat treatment cycle immediately after printing, sometimes before removal from the build plate.
- Contrainte résiduelle :
- Cause : Similar to warping, residual stresses are inherent due to the rapid thermal cycles. Even if they don’t cause immediate distortion, high residual stresses can negatively impact the hinge’s fatigue life, fracture toughness, and susceptibility to stress corrosion cracking (especially in alloys like A7075).
- Atténuation :
- Effective Stress Relief Heat Treatment: Absolutely essential. The parameters must be carefully chosen based on the alloy and desired final properties.
- Optimized Process Parameters & Scan Strategies: As mentioned for warping control.
- Pressage isostatique à chaud (HIP) : A post-processing step involving high temperature and high pressure (using an inert gas like Argon). HIP can significantly reduce internal porosity and residual stresses, improving mechanical properties, but adds cost and lead time. It’s often considered for critical, high-fatigue applications.
- Porosité :
- Cause : Small voids or pores within the printed material. Can be caused by gas trapped within the powder or melt pool (gas porosity) or by incomplete melting and fusion between layers or scan tracks (lack-of-fusion porosity). Poor quality powder (high gas content, irregular shapes) or non-optimized process parameters (incorrect laser power/speed, poor beam focus) are common culprits.
- Impact: Porosity acts as stress concentrators, significantly reducing the hinge’s tensile strength, ductility, and especially fatigue life. It can be a critical failure point.
- Atténuation :
- Poudre de haute qualité : Using powder with controlled sphericity, PSD, and low gas content (like those produced using advanced atomization by Met3dp) is fundamental for porosity control additive manufacturing.
- Paramètres de processus optimisés : Extensive process development to define parameters that ensure full melting and fusion.
- Contrôle de l'atmosphère inerte : Maintaining a high-purity inert gas environment (Argon or Nitrogen) in the build chamber to minimize oxidation and gas pickup.
- HIP: Can effectively close internal pores (though not those open to the surface).
- Surveillance des processus : Advanced systems can monitor the melt pool during printing to detect potential anomalies.
- Support Removal Difficulty & Surface Quality:
- Cause : Supports, while necessary, can be difficult and time-consuming to remove, especially from complex internal geometries (lattices, channels) or delicate features. Removal processes can damage the part or leave rough witness marks.
- Atténuation :
- Focus DfAM : Designing the hinge to be self-supporting as much as possible, minimizing reliance on supports. Orienting the part strategically.
- Conception optimisée du support : Using build preparation software to generate supports that are strong enough during the build but easier to remove (e.g., specific interface layers, perforation points).
- Planification de l'accès : Designing access holes or channels if internal supports are unavoidable and require manual removal or flushing.
- Techniques avancées de suppression : Utilizing CNC machining, electrochemical polishing, or abrasive flow machining where appropriate.
- Achieving Consistent Material Properties:
- Cause : Slight variations in local thermal history, powder characteristics, or process parameters can lead to inconsistencies in microstructure and mechanical properties within a single part or between different builds.
- Atténuation :
- Strict Process Control: Maintaining tight control over all parameters (laser power, speed, layer thickness, gas flow, temperature).
- Étalonnage et maintenance des machines : Ensuring the AM system performs consistently.
- Powder Quality Management: Using powder from qualified suppliers with consistent batch-to-batch characteristics. Implementing powder handling and recycling protocols to prevent degradation or contamination.
- Standardized Post-Processing: Applying consistent heat treatment and finishing procedures to all parts.
- Witness Coupons: Printing standardized test coupons alongside the actual parts in each build for subsequent mechanical testing to verify properties.
- Cracking (Especially with High-Strength Alloys like A7075):
- Cause : Alloys like A7075 have a wide freezing range and are susceptible to solidification cracking or hot tearing during the rapid cooling phase in L-PBF. The high thermal stresses exacerbate this tendency. Hot cracking A7075 AM is a known challenge.
- Atténuation :
- Specialized Process Parameters: Requires highly optimized, often proprietary, parameter sets developed specifically for processing this challenging alloy (e.g., specific preheating, laser power modulation, scan strategies).
- Powder Chemistry Control: While standard grades are used, minor variations or specifically adapted powder compositions might offer slight improvements (less common).
- Expertise : Successfully printing A7075 reliably demands significant process expertise and experience. Partnering with a provider like Met3dp, with deep materials science knowledge and advanced equipment, is crucial when working with such alloys.
Overcoming these challenges requires a combination of advanced technology, material science expertise, rigorous process control, and a DfAM mindset. Relying on experienced partners with industry-leading print volume, accuracy and reliability, like Met3dp, significantly increases the likelihood of successfully producing robust, high-performance 3D printed automotive hinges while mitigating 3D printing defects. Their focus on poudres métalliques de haute qualité and comprehensive quality control metal AM procedures provides a strong foundation for tackling these inherent process complexities.
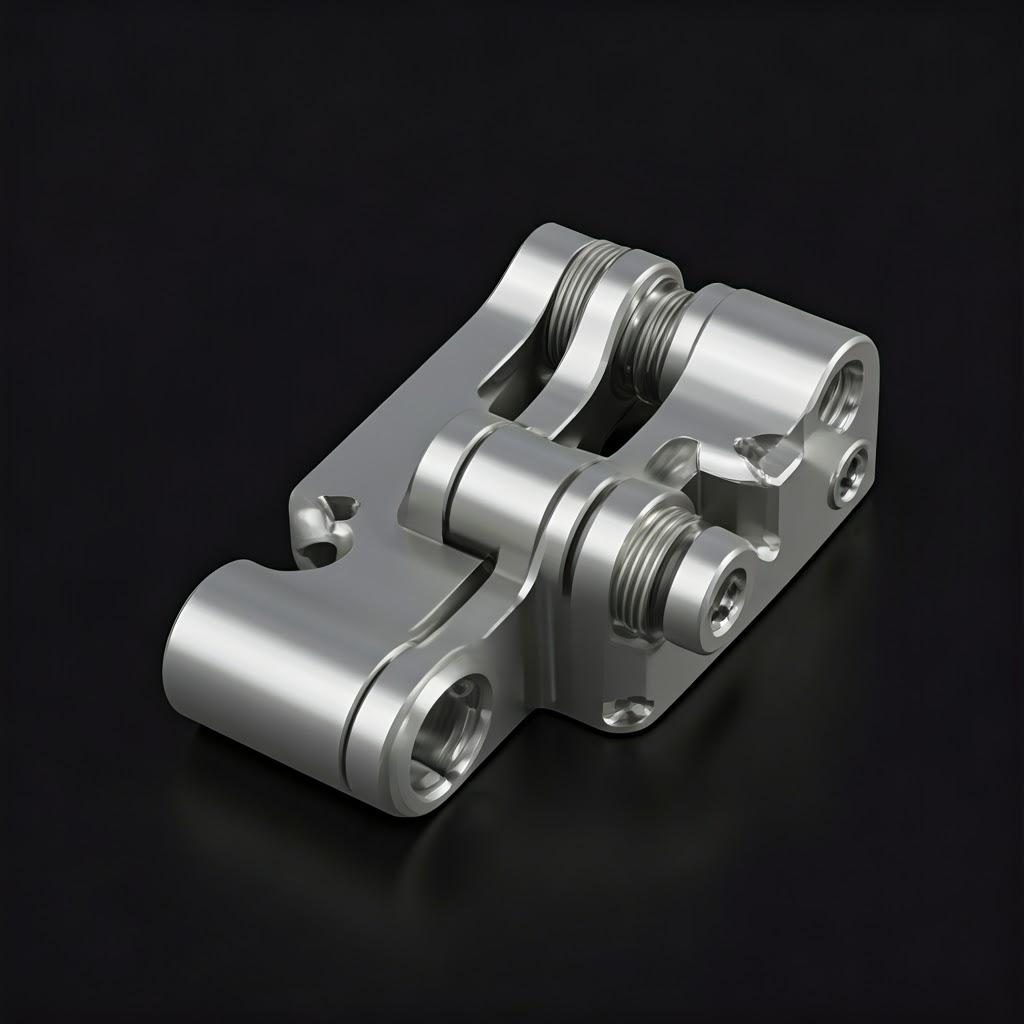
Partner Selection: Choosing the Right Metal 3D Printing Service Provider for Automotive Hinges
Successfully leveraging metal additive manufacturing for critical components like high-performance automotive hinges goes beyond simply having access to a 3D printer. The quality, reliability, and performance of the final part are intrinsically linked to the expertise, capabilities, and quality systems of the manufacturing partner you choose. Selecting the right metal 3D printing service provider automotive specialists trust is arguably one of the most crucial decisions in the adoption process. It’s not just about finding a vendor who can print metal; it’s about finding a strategic partner who understands the nuances of the technology, the materials, and the demanding requirements of the automotive industry.
Making the wrong choice can lead to suboptimal parts, delays, budget overruns, and ultimately, a negative perception of AM technology itself. Conversely, partnering with a capable and experienced provider ensures access to state-of-the-art technology, materials expertise, process control, and the collaborative support needed to truly optimize hinge designs and achieve desired outcomes. For engineers and procurement managers evaluating potential suppliers, especially those seeking services d'impression 3D en gros or a long-term automotive component supplier, a rigorous evaluation process based on key criteria is essential.
Criteria for Evaluating Metal AM Service Providers:
- Material and Process Expertise (A7075 & AlSi10Mg L-PBF):
- Does the provider have documented experience successfully printing the specific aluminum alloy required (A7075 and/or AlSi10Mg) using Laser Powder Bed Fusion (L-PBF/SLM/DMLS)?
- Can they demonstrate expertise in developing and controlling process parameters for these alloys to achieve dense, low-porosity parts with consistent mechanical properties?
- Do they understand the specific challenges associated with each alloy (e.g., hot cracking in A7075) and have proven mitigation strategies?
- Ask for material datasheets based on their actual printed and post-processed results, not just generic powder specs. Request case studies or sample parts demonstrating their capabilities with these specific materials.
- Industry Experience (Automotive Focus):
- Does the provider have experience working with automotive OEMs, Tier 1 suppliers, or motorsport teams?
- Are they familiar with automotive quality expectations, documentation requirements (even if not fully IATF 16949 certified), and common applications?
- Experience in adjacent demanding industries like aerospace (AS9100 certification is a strong plus) often indicates mature processes and rigorous quality control applicable to automotive needs.
- Certifications and Quality Management System (QMS):
- ISO 9001 : This certification for Quality Management Systems is a fundamental requirement, indicating standardized processes for consistency and quality.
- AS9100 (Aerospace): While specific to aerospace, this certification signifies a very high level of QMS maturity, process control, and traceability, often exceeding standard ISO 9001 requirements. Highly desirable for critical components.
- IATF 16949 Awareness: While full certification is rare for pure AM service bureaus, demonstrating awareness and alignment with automotive QMS principles is beneficial.
- Un système de gestion de la qualité robuste : Regardless of specific certifications, inquire about their QMS details: How do they ensure material traceability (tracking powder batches from source to final part)? How are processes documented and controlled? What are their equipment calibration and maintenance procedures? How is operator training managed?
- Machine Fleet and Technology Capabilities:
- What types and brands of L-PBF machines do they operate? Are they well-maintained and calibrated?
- What is their build volume capacity? Can they accommodate the size of the hinges required, potentially in batches? Look for providers mentioning industry-leading print volume, accuracy and reliability.
- Do their machines incorporate advanced features like in-situ process monitoring (e.g., melt pool monitoring) for enhanced quality control?
- What is their overall production capacity and redundancy? Can they handle fluctuating demand or urgent orders?
- Capacités internes de post-traitement :
- Does the provider offer a comprehensive range of post-processing services relevant to aluminum hinges under one roof? This includes:
- Stress relief and critical heat treatment (especially T6 for A7075) with calibrated furnaces.
- Efficient support removal techniques.
- CNC machining for tight tolerances on critical features.
- Various surface finishing options (blasting, tumbling, polishing, anodizing aluminum hinges).
- Metrology and inspection equipment (CMM, 3D scanning, surface profilometry).
- Having these capabilities in-house streamlines the workflow, ensures better process control, potentially reduces lead times, and simplifies supply chain management compared to coordinating multiple vendors. Look for providers advertising solutions complètes.
- Does the provider offer a comprehensive range of post-processing services relevant to aluminum hinges under one roof? This includes:
- Design Support and DfAM Expertise:
- Does the provider offer Design for Additive Manufacturing (DfAM) consultation?
- Can their engineers collaborate with your design team to optimize the hinge design for lightweighting, part consolidation, minimal supports, and overall manufacturability via AM?
- This collaborative approach is often key to maximizing the benefits of the technology.
- Track Record, Reputation, and Communication:
- Ask for client references or testimonials, particularly within the automotive or related industries.
- Evaluate their communication responsiveness, transparency, and project management approach. Are they easy to work with? Do they provide clear quotes and regular updates?
- Consider their stability and longevity in the rapidly evolving AM market.
Finding and Selecting Your Partner:
Potential suppliers can be found through online manufacturing directories (ensure they specialize in metal AM), industry trade shows (like Formnext), professional networks, and recommendations. It’s important to differentiate between brokers (who subcontract work), small workshops (who may have limited capacity or expertise), and established, vertically integrated providers.
For companies seeking a reliable, expert partner for demanding applications like high-performance automotive hinges, Met3dp stands out. Headquartered in Qingdao, China, Met3dp specializes in additive manufacturing solutions, encompassing both state-of-the-art 3D printing equipment and the production of high-performance metal powders. Their focus on delivering industry-leading print volume, accuracy, and reliability makes their systems ideal for mission-critical parts in automotive, aerospace, and medical fields. Crucially, Met3dp employs advanced powder manufacturing technologies like gas atomization and PREP, ensuring the poudres métalliques de haute qualité (including optimized A7075 and AlSi10Mg) necessary for superior part quality. With decades of collective expertise, Met3dp provides comprehensive solutions spanning printers, advanced materials, and application development services, positioning them as a knowledgeable partner capable of guiding clients through the entire process, from design optimization to finished part. Their partnership approach focuses on enabling organizations to implement 3D printing effectively and accelerate their digital manufacturing transformations, making them an ideal choice when choosing AM supplier for critical automotive components.
Understanding Investment: Cost Factors and Lead Times for 3D Printed Automotive Hinges
One of the most frequent questions regarding metal additive manufacturing concerns its cost-effectiveness compared to traditional methods. While AM eliminates the often substantial upfront investment in tooling (molds, dies), the cost structure for producing parts is different, driven primarily by material consumption, machine time, and post-processing labor. Understanding the key cost drivers and typical lead times is essential for budgeting, project planning, and making informed decisions about when and where to apply AM for automotive hinges.
Breakdown of Cost Drivers:
La finale 3D printed hinge price is influenced by a combination of factors:
Cost Driver | Description & Impact | How to Mitigate/Optimize |
---|---|---|
Coût matériel | Cost per kilogram of the chosen powder (e.g., A7075 is typically more expensive than AlSi10Mg). Total volume of the part and its support structures directly dictates material usage. | Apply topology optimization and lattice structures (DfAM) to minimize part volume. Select the most cost-effective material that meets requirements. |
Le temps des machines | Billed per hour of machine operation. Influenced by part volume/height (more layers = more time), complexity, and chosen print parameters (e.g., finer layers increase time). | Optimize part orientation for Z-height. Maximize parts per build plate (nesting) to share setup/cooldown time. Avoid unnecessarily fine parameters. |
Labor Costs | Includes machine setup/teardown, powder handling, extensive post-processing (support removal, finishing, machining), and quality inspection. Can be a significant cost component. | Design for minimal supports (DfAM). Specify only necessary tolerances/finishes to reduce machining/polishing. Automate post-processing where possible. |
Complexité des pièces | Intricate geometries may require slower print speeds or more complex support strategies, increasing both machine time and post-processing labor (especially support removal). | Simplify design where possible without sacrificing function (DfAM). Design internal channels/lattices for accessibility (powder/support removal). |
Tolerances & Finish | Requiring very tight tolerances necessitates extensive CNC machining. High-level surface finishes (e.g., polishing) are labor-intensive. | Specify tolerances/finishes only as tight as functionally required. Leverage as-printed surfaces where acceptable. |
Quantité commandée | Setup costs are amortized over more parts in larger batches. Build plates can be optimized for higher density. Potential volume discounts on powder or processing may apply. | Consolidate demand where possible. Discuss volume breaks with suppliers offering services d'impression 3D en gros. |
Post-Processing Steps | Each step (heat treatment, blasting, machining, anodizing) adds cost (equipment time, labor, consumables). Complex multi-step processes increase overall cost. | Minimize required steps through smart design (DfAM). Choose integrated suppliers to reduce logistical overhead. |
Assurance qualité | The level of required inspection (visual, basic dimensional, CMM, NDT like CT scanning) adds labor and equipment time. | Define critical-to-quality features requiring higher inspection levels, use standard checks elsewhere. |
Exporter vers les feuilles
Estimating Costs:
Obtaining an accurate cost estimation AM parts requires submitting a detailed RFQ (Request for Quote) to potential suppliers, including:
- Final 3D CAD model (STEP format preferred).
- Material specification (A7075 or AlSi10Mg).
- Required tolerances (clearly indicated on drawings using GD&T).
- Surface finish requirements for different features.
- Post-processing requirements (heat treatment temper, anodizing type, etc.).
- Quantity required (including potential future volumes).
- Testing and inspection requirements.
Reputable providers like Met3dp can provide detailed quotes based on this information. Be wary of instant online quotes for complex metal parts, as they often don’t capture the full scope of post-processing and quality requirements.
Lead Times for 3D Printed Hinges:
Le délai de fabrication additive also differs from traditional methods, particularly regarding the absence of tooling lead time.
- Prototypes : For single parts or very small batches with minimal post-processing, lead times can be relatively short, often ranging from a few days to 1-2 weeks, depending on machine availability and part complexity. This enables rapid design iteration.
- Production à faible volume : For series production (tens to hundreds of parts), lead times are typically longer, often in the range of 2 to 6 weeks or more. This is due to:
- Scheduling parts into the machine queue.
- Longer print times for full build plates.
- Batch processing for steps like heat treatment and surface finishing.
- More extensive post-processing (machining, finishing) required for production parts.
- Rigorous quality assurance procedures.
- Factors Influencing Lead Time:
- Current Machine Queue: How busy the service provider is.
- Print Time: Determined by part size, complexity, and quantity.
- Post-Processing Complexity: The number and duration of required steps (heat treatment cycles, machining time, finishing processes).
- Quality Assurance Requirements: Time needed for thorough inspection and documentation.
- Shipping Logistics.
Clear communication with the supplier regarding required delivery dates is essential during the quoting and ordering process. Understanding the interplay between cost drivers and lead time factors helps manage expectations for low-volume automotive manufacturing cost and timelines when using metal AM.
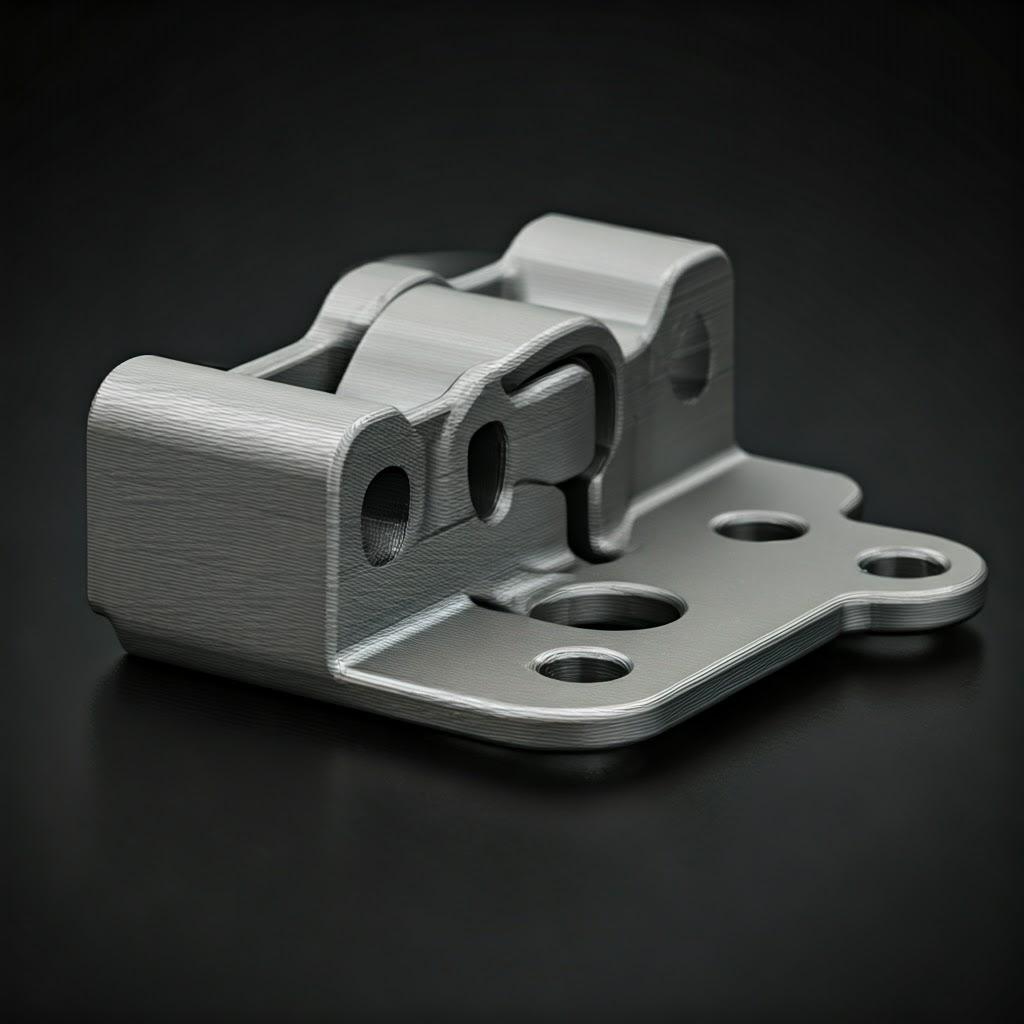
Frequently Asked Questions (FAQ) about 3D Printed Automotive Hinges
As metal additive manufacturing becomes more prevalent in the automotive sector, engineers, designers, and procurement managers often have questions about its capabilities and suitability for components like hinges. Here are answers to some frequently asked questions:
Q1: Are 3D printed aluminum hinges (A7075 / AlSi10Mg) strong enough for automotive doors/hoods?
A : Yes, absolutely, when designed, manufactured, and processed correctly.
- A7075: When printed properly and heat-treated to a T6 temper, A7075 exhibits exceptionally high strength, often comparable or superior to commonly used automotive steels but at significantly lower weight. Its yield strength can exceed 500 MPa. This makes it suitable for highly loaded hinges on doors, hoods, and tailgates, especially in performance applications.
- AlSi10Mg : While generally not as strong as peak-aged A7075, heat-treated AlSi10Mg offers good strength (yield strength typically 250-300+ MPa) and hardness, sufficient for many standard hinge applications, brackets, and housings, with the added benefit of better printability and corrosion resistance.
- Key Factors: Achieving this strength relies heavily on:
- Proper DfAM: Ensuring the design distributes loads effectively.
- Optimized Printing: Achieving high density (>99.7%) and minimizing internal defects like porosity.
- Correct Heat Treatment: Essential to develop the alloy’s full mechanical properties (especially T6 for A7075).
- Contrôle de la qualité : Verifying material properties and part integrity. The 3D printed hinge strength is therefore highly dependent on material choice and meticulous process control.
Q2: How does the cost of a 3D printed hinge compare to a traditionally manufactured one?
A : The direct cost comparison AM vs traditional methods depends heavily on volume, complexity, and the specific traditional method.
- High Volume (e.g., >10,000 parts/year): For simple hinges, traditional methods like stamping or casting are almost always cheaper per part due to economies of scale, despite high initial tooling costs.
- Low to Medium Volume (e.g., <1,000 – 5,000 parts/year): AM becomes much more competitive. The elimination of tooling costs (which can run into tens or hundreds of thousands of dollars) can make AM cheaper overall, especially for complex designs.
- La complexité : For highly complex or topology-optimized hinges that are difficult or impossible to cast or machine, AM might be the seulement feasible manufacturing method, making direct cost comparison less relevant.
- Total Value Proposition: It’s crucial to consider factors beyond the per-part price:
- No Tooling Cost: Significant savings and faster time-to-first-part.
- Weight Savings: Translates to fuel/range efficiency or improved performance, adding value over the vehicle’s lifetime.
- Consolidation partielle : Reduces assembly costs and potential failure points.
- Liberté de conception : Enables performance or features not possible otherwise.
- Production à la demande : Reduces inventory holding costs. Therefore, while the sticker price per AM part might sometimes be higher, its overall value and cost-effectiveness, particularly for lower volumes and high-performance applications, can be superior.
Q3: What is the typical lifespan or durability of a 3D printed automotive hinge?
A : Le durability additive manufacturing parts like hinges can achieve is designed to meet or exceed typical automotive requirements when engineered correctly.
- Fatigue Life: This is critical for hinges undergoing cyclic loading. A7075-T6 offers good fatigue strength. Proper design (avoiding stress concentrations), high-density printing (minimizing porosity), and appropriate surface finishing are crucial. Hinges can be designed and validated (through simulation and physical testing) to endure hundreds of thousands or even millions of cycles required by automotive standards.
- Résistance à l'usure : Pivot points are subject to wear. Material choice (hardness) and surface treatments (e.g., Type III hardcoat anodizing for aluminum) significantly enhance wear resistance. Proper lubrication strategies, potentially enabled by integrated channels via AM, also contribute.
- Résistance à la corrosion : Essential for longevity. AlSi10Mg offers good inherent resistance. A7075 requires protective coatings like anodizing or paint, especially in harsh environments.
- Overall: A well-designed, properly manufactured, and appropriately post-processed metal AM hinge using A7075 or AlSi10Mg can be expected to last the typical lifespan of a vehicle. Validation testing under realistic load and environmental conditions is standard practice for critical components.
Q4: Can existing hinge designs (made for casting/machining) be directly 3D printed?
A : While technically possible to print a geometry designed for another process, it is highly inadvisable and misses the primary benefits of AM.
- Suboptimal Design: Designs optimized for casting (e.g., draft angles, uniform wall thickness) or machining (e.g., accessibility for cutting tools) are not optimized for AM’s layer-based approach. Direct printing often results in excessive weight, unnecessary support structures, and suboptimal performance.
- DfAM Necessity: To leverage AM’s advantages (lightweighting, complexity, consolidation), the hinge must be redesigned using DfAM necessity principles. This involves topology optimization, potentially lattice structures, designing for self-supporting angles, and integrating features.
- Collaboration : Working with AM experts during the redesign phase is crucial to ensure the part is optimized for printability, performance, and cost-effectiveness using AM.
Q5: What quality control measures ensure the reliability of 3D printed hinges?
A : Ensuring the reliability of critical AM components requires a multi-faceted quality control metal 3D printing strategy implemented by the service provider:
- Material Control: Strict incoming inspection of metal powder (chemistry, PSD, morphology, flowability), controlled storage, batch traceability throughout the process.
- Process Validation & Monitoring: Validated print parameters for each material/machine combination, real-time monitoring of key process variables (laser power, oxygen levels, melt pool characteristics where available), documented procedures.
- Post-Print Inspection: Thorough cleaning and visual inspection, precise dimensional verification using CMM or 3D scanning against the CAD model and GD&T specifications.
- Material Property Verification: Regular printing and testing of witness coupons alongside parts (tensile tests, hardness tests) to verify that the process is achieving the expected mechanical properties.
- Essais non destructifs (END) : For highly critical hinges, CT (Computed Tomography) scanning or X-ray can be used to inspect internal structures for porosity or lack-of-fusion defects without destroying the part.
- Un système de gestion de la qualité robuste : All procedures should be governed by a comprehensive Quality Management System (e.g., ISO 9001, AS9100).
Conclusion: Driving the Future of Automotive Components with 3D Printed Hinges
The journey through the intricacies of designing, manufacturing, and implementing high-performance automotive hinges using metal additive manufacturing reveals a technology poised to reshape automotive component production. Metal AM, particularly utilizing advanced aluminum alloys like A7075 and AlSi10Mg through Laser Powder Bed Fusion, offers a compelling pathway beyond the limitations of traditional methods. It empowers engineers to achieve an unparalleled synergy of strength, lightweighting, and design complexity, critical attributes in the relentless pursuit of enhanced vehicle performance, efficiency, and innovation, especially within the demanding EV, performance, and luxury segments.
We’ve explored how DfAM principles unlock radical optimisation de la topologie et consolidation partielle, leading to hinges that are significantly lighter yet just as strong, if not stronger, than their conventional counterparts. We’ve seen how alloys like A7075 deliver steel-like strength for high-load applications, while AlSi10Mg provides a robust and printable solution for a wide range of uses. The ability to rapidly prototype and produce low volumes without tooling investment accelerates development cycles and enables customization previously unimaginable.
However, realizing this potential demands meticulous attention to detail throughout the entire workflow – from expert DfAM and precise process control during printing to critical post-processing steps like heat treatment, machining, and surface finishing. Navigating challenges such as residual stress, porosity, and achieving tight tolerances requires deep expertise and robust quality management. This underscores the importance of selecting the right manufacturing partner – one with proven experience, advanced capabilities, and a commitment to quality.
Le future automotive manufacturing landscape will increasingly feature metal AM, not as a niche prototyping tool, but as a viable solution for series production of complex, high-value components. The innovation automotive components like hinges are undergoing, driven by AM, contributes directly to advancements in vehicle dynamics, range extension, and novel functionalities. As the technology matures and costs continue to evolve, the metal AM adoption automotive industry is set to accelerate further.
For automotive engineers and procurement managers facing challenges with weight reduction, component performance, or seeking faster development for complex assemblies, metal additive manufacturing presents a powerful solution. If you are ready to explore how 3D printed hinges or other components can elevate your next vehicle project, partnering with a leader in the field is paramount.
Met3dp, with its foundation in both advanced metal powder production and cutting-edge printing systems, represents such a leader. Offering comprehensive Met3dp solutions that span materials science, reliable printing equipment, and application development expertise, they are ideally positioned to help your organization leverage the transformative power of additive manufacturing. We encourage you to contact metal 3D printing supplier Met3dp to discuss your specific application needs and discover how their capabilities can drive your digital manufacturing transformation forward.
Partager sur
MET3DP Technology Co. est un fournisseur de premier plan de solutions de fabrication additive dont le siège se trouve à Qingdao, en Chine. Notre société est spécialisée dans les équipements d'impression 3D et les poudres métalliques de haute performance pour les applications industrielles.
Articles connexes
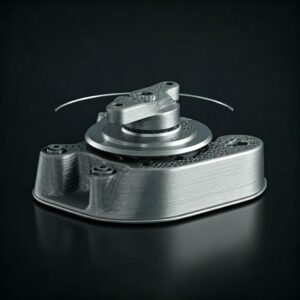
Supports imprimés en 3D pour les capteurs radar automobiles : Précision et performance
Lire la suite "À propos de Met3DP
Mise à jour récente
Notre produit
CONTACTEZ-NOUS
Vous avez des questions ? Envoyez-nous un message dès maintenant ! Nous répondrons à votre demande avec toute une équipe dès réception de votre message.
Obtenir les informations de Metal3DP
Brochure du produit
Obtenir les derniers produits et la liste des prix
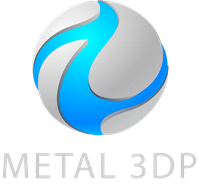
Poudres métalliques pour l'impression 3D et la fabrication additive
PRODUIT
cONTACT INFO
- Ville de Qingdao, Shandong, Chine
- [email protected]
- [email protected]
- +86 19116340731