Additive Manufacturing of Jet Engine Diffusers: Revolutionizing Aerospace Components
Table des matières
Introduction to Metal 3D Printing of Jet Engine Diffusers
The aerospace industry constantly demands lighter, stronger, and more efficient components. Among these critical parts is the jet engine diffuser, a crucial element in directing airflow and ensuring optimal engine performance. Traditional manufacturing methods for diffusers often involve complex and time-consuming processes, limiting design possibilities and increasing production costs. Metal Impression 3D, also known as metal additive manufacturing, offers a transformative approach to producing these intricate components. This blog post explores the significant advantages of using metal 3D printing for jet engine diffusers, highlighting the materials, design considerations, and benefits for aerospace engineers and procurement managers. At Métal3DP, we are at the forefront of this revolution, providing advanced metal 3D printing solutions that meet the demanding needs of the aerospace sector. Our industry-leading print volume, accuracy, and reliability ensure the production of mission-critical parts with exceptional quality.
What are Jet Engine Diffusers Used For?
Jet engine diffusers play a vital role in the combustion process by slowing down the high-speed air exiting the compressor and increasing its pressure before it enters the combustion chamber. This controlled deceleration is essential for efficient fuel mixing and combustion, ultimately impacting the engine’s thrust and fuel economy. Diffusers are integral to various types of jet engines, including turbofans, turbojets, and turboprops, and their design directly influences the engine’s overall performance characteristics. The complex geometries required for optimal airflow management often pose significant manufacturing challenges with conventional techniques. Metal 3D printing overcomes these limitations, enabling the creation of intricate internal channels and optimized aerodynamic profiles that were previously unattainable. Industries that heavily rely on high-performance jet engines, such as aerospace, defense, and power generation, stand to gain significantly from the advancements in metal 3D printed diffusers.
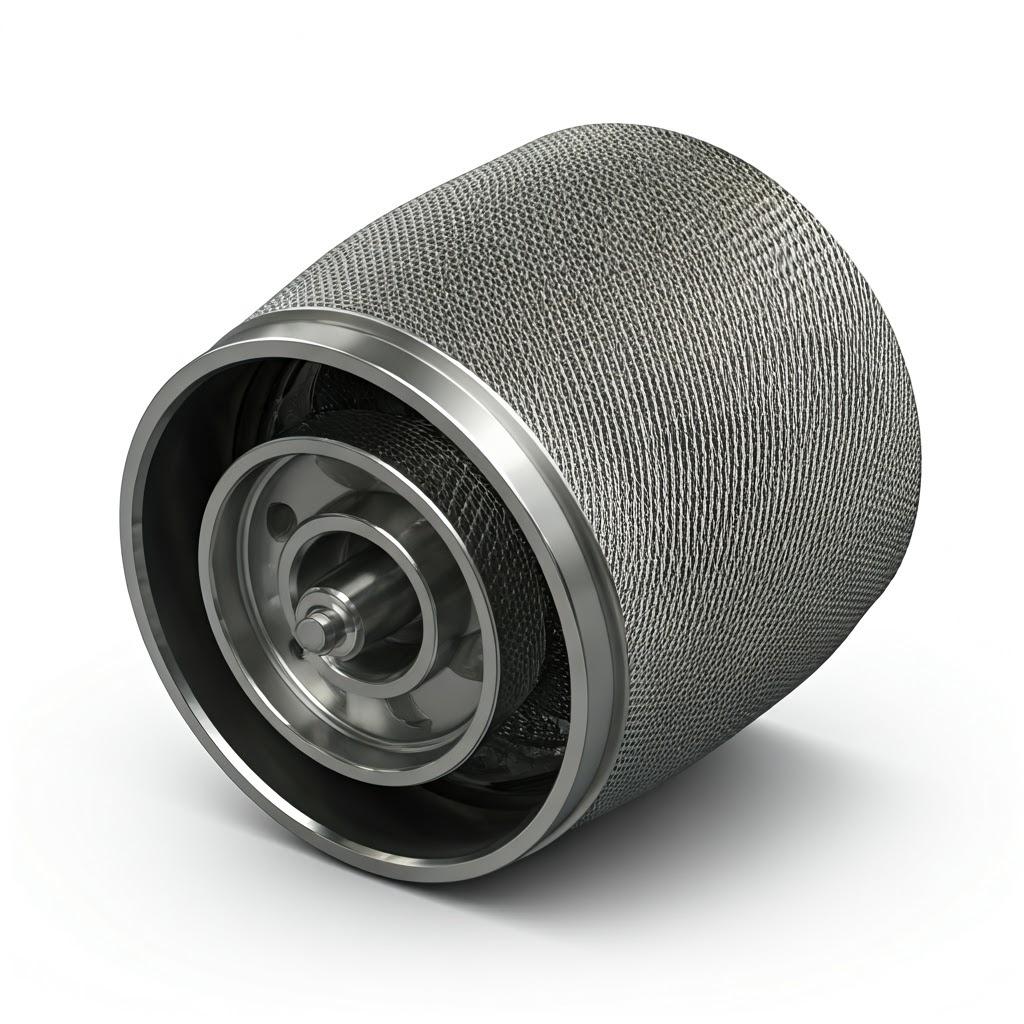
Why Use Metal 3D Printing for Jet Engine Diffusers?
Adopting metal 3D printing for the production of jet engine diffusers offers a multitude of advantages over traditional manufacturing methods:
- Liberté de conception : Additive manufacturing allows for the creation of complex geometries and intricate internal features that are difficult or impossible to achieve with casting, machining, or forging. This design flexibility enables engineers to optimize diffuser aerodynamics for improved engine efficiency and performance.
- Réduction du poids : By enabling topology optimization and the creation of lightweight lattice structures, metal 3D printing can significantly reduce the weight of jet engine diffusers. This is crucial in aerospace, where every kilogram saved translates to lower fuel consumption and increased payload capacity.
- Efficacité matérielle : Additive manufacturing processes build parts layer by layer, minimizing material waste compared to subtractive methods where significant material is removed. This is particularly beneficial when working with expensive, high-performance alloys commonly used in aerospace applications.
- Réduction des délais d'exécution : Traditional manufacturing of complex diffuser components often involves lengthy tooling and setup processes. Metal 3D printing eliminates the need for molds and specialized tooling, drastically reducing lead times and enabling faster prototyping and production cycles.
- Consolidation partielle : Metal 3D printing allows for the consolidation of multiple components into a single, integrated part. This reduces the number of assembly steps, lowers manufacturing costs, and improves the reliability of the final product by eliminating joints and fasteners.
- Customization and Complexity: Each jet engine design may require a specific diffuser geometry. Metal 3D printing offers the ability to produce highly customized diffusers tailored to the exact requirements of the engine, without the high costs associated with custom tooling in traditional manufacturing.
Métal3DP‘s advanced metal 3D printing technology empowers aerospace manufacturers to leverage these advantages, producing high-performance jet engine diffusers with unparalleled efficiency and design complexity. Explore our metal 3D printing services to see how we can support your aerospace manufacturing needs.
Recommended Materials and Why They Matter
The selection of the appropriate metal powder is critical for the performance and durability of 3D printed jet engine diffusers, which must withstand high temperatures, pressures, and corrosive environments. Métal3DP offers a range of high-performance metal powders specifically suited for these demanding applications, including:
- IN738LC: This nickel-based superalloy exhibits exceptional high-temperature strength, creep resistance, and oxidation resistance, making it ideal for hot-section components in jet engines. Its excellent mechanical properties at elevated temperatures ensure the diffuser can maintain its structural integrity under extreme operating conditions. | Property | Value | Significance | | :—————————- | :—————————————- | :—————————————————————————————————————————————– | | High-Temperature Strength | Excellent | Ensures structural integrity at high operating temperatures within the jet engine. | | Creep Resistance | Superior | Prevents deformation under sustained high temperatures and loads, crucial for long-term component reliability. | | Oxidation Resistance | Excellent | Protects the diffuser from degradation due to exposure to high-temperature air and combustion products. | | Corrosion Resistance | Good | Enhances the lifespan of the component by resisting chemical attack from the operating environment. | | Typical Applications | Turbine blades, vanes, combustion liners | Demonstrates the alloy’s suitability for critical hot-section components similar to diffusers. | | Disponibilité de Metal3DP | Yes | Métal3DP offers high-quality IN738LC powder optimized for additive manufacturing processes. |
- René 41 : Another high-performance nickel-based superalloy, Rene 41, offers exceptionally high strength at both room and elevated temperatures, along with excellent oxidation resistance up to 871°C (1600°F). Its superior strength-to-weight ratio makes it an attractive option for aerospace components where weight is a critical factor. | Property | Value | Significance | | :—————————- | :—————————————- | :———————————————————————————————————————————————- | | High Strength | Exceptional | Provides the necessary mechanical properties to withstand the high pressures and stresses within the jet engine. | | Elevated Temperature Strength | Very High | Ensures the diffuser maintains its strength and performance at the high operating temperatures encountered. | | Oxidation Resistance | Outstanding | Protects against high-temperature degradation, ensuring long-term durability in the harsh engine environment. | | Strength-to-Weight Ratio | High | Contributes to the overall weight reduction of the engine, improving fuel efficiency. | | Typical Applications | Turbine blades, wheels, bolting | Indicates its use in critical aerospace components requiring high strength and temperature resistance, similar to jet engine diffusers. | | Disponibilité de Metal3DP | Yes | Métal3DP provides high-quality Rene 41 powder suitable for producing robust and lightweight jet engine diffusers. |
Métal3DP‘s advanced powder making system, utilizing industry-leading gas atomization and PREP technologies, ensures that our metal powders exhibit high sphericity and excellent flowability, crucial for consistent and high-quality 3D printing. Our comprehensive portfolio of high-quality metal powders is optimized for laser and electron beam powder bed fusion, enabling our customers to 3D print dense, high-quality metal parts with superior mechanical properties. Contact Métal3DP to discuss your specific material requirements and explore how our advanced metal powders can enhance the performance of your jet engine diffusers. Sources and related content
Design Considerations for Additive Manufacturing of Jet Engine Diffusers
Optimizing the design of jet engine diffusers for additive manufacturing is crucial to fully leverage the technology’s capabilities and achieve the desired performance characteristics. Unlike traditional manufacturing, metal 3D printing imposes unique design considerations that engineers must take into account:
- Optimisation de la topologie : Additive manufacturing enables the creation of complex, organic shapes derived from structural analysis. Topology optimization software can identify areas of low stress and remove unnecessary material, resulting in lightweight yet strong diffuser designs. This process often leads to non-intuitive geometries that are only possible with 3D printing.
- Structures en treillis : Incorporating lattice structures within the diffuser design can further reduce weight without compromising structural integrity. These intricate, repeating patterns provide stiffness and support while significantly decreasing the overall material volume. The design of the lattice structure (e.g., gyroid, diamond, cubic) can be tailored to meet specific load-bearing requirements.
- Internal Channels and Cooling Features: Metal 3D printing allows for the creation of complex internal channels for cooling or other functional purposes. Integrating cooling pathways directly into the diffuser design can improve thermal management and enhance the component’s lifespan in the high-temperature environment of a jet engine.
- Structures de soutien : During the metal 3D printing process, support structures are often required to prevent warping, sagging, and collapse of overhanging features. Careful consideration of support structure design is essential to minimize material usage, ensure print quality, and facilitate easy removal during post-processing. Design for Additive Manufacturing (DfAM) principles emphasize minimizing the need for supports through strategic part orientation and self-supporting geometries.
- Épaisseur de la paroi et taille de l'élément : The minimum achievable wall thickness and feature size are dictated by the specific metal 3D printing technology and material used. Designers must adhere to these limitations to ensure successful printing and the desired structural integrity. Métal3DP‘s advanced SEBM printers offer high accuracy and the ability to produce fine features, allowing for more intricate and optimized designs.
- Considérations relatives à l'état de surface : The as-printed surface finish of a metal 3D printed part can vary depending on the printing process and parameters. For critical aerodynamic surfaces of a jet engine diffuser, post-processing steps like polishing or machining may be necessary to achieve the required smoothness and airflow characteristics.
By considering these design principles and collaborating with experienced additive manufacturing providers like Métal3DP, aerospace engineers can unlock the full potential of metal 3D printing to create high-performance, lightweight, and complex jet engine diffusers. We offer comprehensive application development services to assist our partners in optimizing their designs for additive manufacturing.
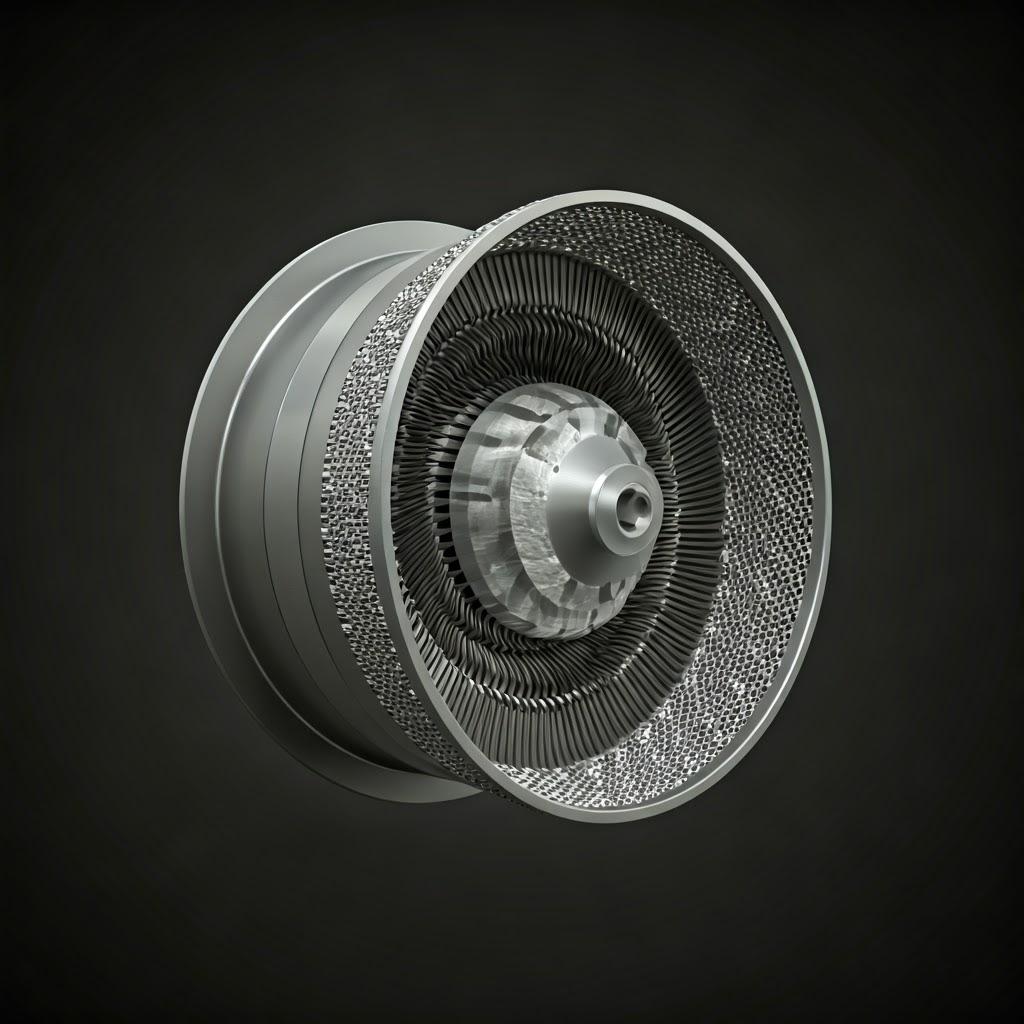
Tolerance, Surface Finish, and Dimensional Accuracy of 3D Printed Diffusers
Achieving the required tolerance, surface finish, and dimensional accuracy is paramount for the functional performance and reliability of jet engine diffusers. Metal 3D printing technologies have made significant strides in these areas:
- Tolérance : The achievable tolerance in metal 3D printing depends on the specific printing technology (e.g., DMLS, SLM, EBM), the material used, and the part geometry. Generally, tolerances in the range of ±0.1 to ±0.05 mm can be achieved for critical dimensions. Métal3DP‘s high-precision SEBM printers are engineered to deliver industry-leading accuracy, ensuring that printed diffusers meet stringent aerospace specifications.
- Finition de la surface : The as-printed surface finish typically ranges from 5 to 20 µm Ra (roughness average) depending on the printing parameters and powder particle size. For aerodynamic surfaces requiring smoother finishes, post-processing techniques such as machining, grinding, polishing, or abrasive flow machining can be employed. The choice of post-processing depends on the specific surface finish requirements and the complexity of the diffuser geometry.
- Précision dimensionnelle : Dimensional accuracy refers to the ability of the 3D printing process to produce parts that closely match the intended CAD model. Factors influencing dimensional accuracy include material shrinkage during solidification, thermal gradients, and the calibration of the printing system. Métal3DP‘s rigorous quality control processes and advanced machine calibration ensure high dimensional accuracy of the printed components.
- Factors Affecting Precision:
- Étalonnage de la machine : Regular calibration of the 3D printer is essential for maintaining accuracy.
- Propriétés du matériau : The thermal expansion and contraction properties of the metal powder can influence the final dimensions.
- Orientation de la construction : The orientation of the part on the build platform can affect dimensional accuracy and surface finish in different areas of the component.
- Slicing Parameters: The parameters used to slice the 3D model into layers can impact the final part dimensions and surface quality.
Métal3DP is committed to delivering metal 3D printed parts with the highest levels of precision. Our expertise in material science and additive manufacturing processes allows us to optimize printing parameters and recommend appropriate post-processing techniques to meet the specific tolerance and surface finish requirements for jet engine diffusers. Learn more about our printing methods and how we ensure the quality of our 3D printed metal parts.
Post-Processing Requirements for Metal 3D Printed Diffusers
While metal 3D printing offers significant advantages in creating complex geometries, post-processing steps are often necessary to achieve the final desired properties and surface finish for jet engine diffusers:
- Suppression du support : Support structures, essential during the printing process, must be carefully removed without damaging the delicate features of the diffuser. Techniques include manual removal, machining, or chemical dissolution, depending on the support material and part geometry.
- Traitement thermique : To relieve internal stresses, optimize mechanical properties (such as hardness and tensile strength), and achieve the desired microstructure of the metal alloy, heat treatment is a crucial post-processing step. Specific heat treatment cycles are tailored to the material and the intended application.
- Finition de la surface : As mentioned earlier, post-processing techniques like CNC machining, grinding, polishing, abrasive flow machining, or shot peening may be required to achieve the desired surface finish for optimal aerodynamic performance and fatigue resistance. The choice of method depends on the required smoothness and the accessibility of the surfaces.
- Inspection et contrôle qualité : Thorough inspection using techniques such as coordinate measuring machines (CMM), non-destructive testing (NDT) like ultrasonic testing or X-ray inspection, and surface roughness measurements are essential to ensure the dimensional accuracy, structural integrity, and surface quality of the printed diffusers meet stringent aerospace standards.
- Revêtement (en option) : Depending on the specific application and environmental conditions, coatings may be applied to enhance corrosion resistance, wear resistance, or thermal barrier properties. Techniques include thermal spraying, electroplating, or specialized ceramic coatings.
Métal3DP provides comprehensive post-processing services to ensure that our 3D printed jet engine diffusers meet the most demanding aerospace requirements. Our expertise in heat treatment, surface finishing, and quality control guarantees the production of high-performance, reliable components.
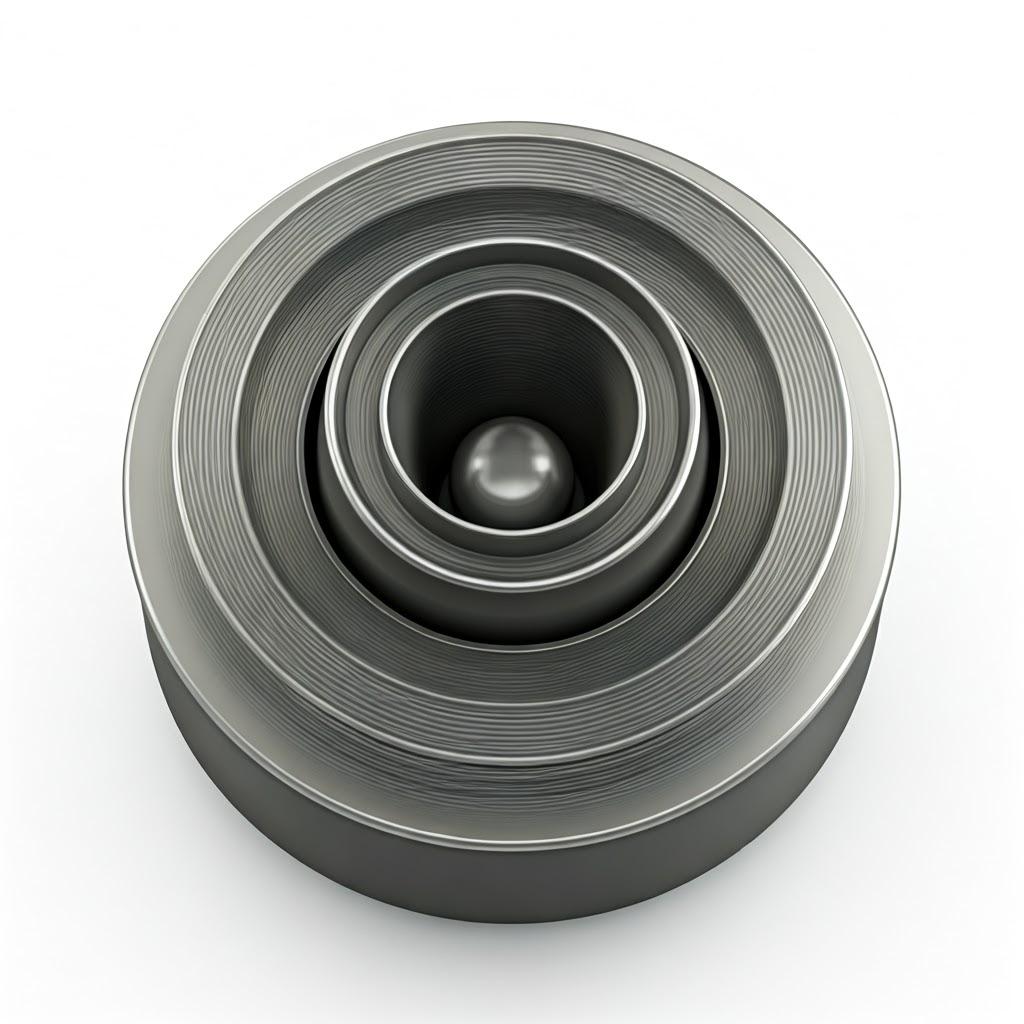
Common Challenges and How to Avoid Them in 3D Printing Diffusers
While metal 3D printing offers numerous advantages, several challenges can arise during the production of complex parts like jet engine diffusers. Understanding these potential issues and implementing appropriate strategies can mitigate them:
- Déformation et distorsion : Thermal stresses during the printing process can lead to warping or distortion of the part, particularly for large or complex geometries.
- Solution : Optimize part orientation on the build platform, employ effective support structures, and carefully control the build chamber temperature. Métal3DP‘s expertise in process parameter optimization minimizes the risk of warping.
- Porosité : Internal voids or pores within the printed part can compromise its mechanical strength and fatigue life.
- Solution : Utilize high-quality metal powders with good flowability, optimize laser or electron beam power and speed, and ensure proper shielding gas flow. Métal3DP‘s advanced powder making system and printing technology minimize porosity.
- Support Structure Removal Damage: Improper removal of support structures can damage delicate features or leave surface imperfections.
- Solution : Design support structures strategically for easy removal, use appropriate removal techniques, and consider dissolvable support materials where applicable.
- Rugosité de la surface : Achieving the required surface finish for aerodynamic performance can be challenging with as-printed parts.
- Solution : Plan for appropriate post-processing techniques such as machining or polishing. Optimize printing parameters to minimize initial surface roughness.
- Dimensional Inaccuracy: Deviations from the intended dimensions can occur due to material shrinkage, thermal effects, or machine calibration issues.
- Solution : Implement rigorous machine calibration procedures, compensate for material shrinkage in the design phase, and control the build environment. Métal3DP‘s commitment to quality ensures high dimensional accuracy.
- Material Property Variability: Inconsistent material properties throughout the printed part can affect its performance.
- Solution : Use high-quality, well-characterized metal powders and optimize the printing process to ensure uniform melting and solidification. Métal3DP‘s stringent quality control measures guarantee consistent material properties.
By proactively addressing these potential challenges through careful design, optimized printing parameters, and appropriate post-processing, aerospace manufacturers can reliably produce high-quality jet engine diffusers using metal 3D printing. Métal3DP‘s extensive experience and technical expertise provide our customers with the solutions and support needed to overcome these challenges.
How to Choose the Right Metal 3D Printing Service Provider for Diffusers
Selecting the right metal 3D printing service provider is crucial for the successful production of high-performance jet engine diffusers. Consider the following factors when evaluating potential suppliers:
- Capacités matérielles : Ensure the provider has experience working with the specific high-temperature alloys required for jet engine applications, such as IN738LC and Rene 41. Verify their expertise in processing these materials to achieve the desired mechanical properties and microstructures. Métal3DP offers a comprehensive portfolio of high-quality metal powders, including those ideal for aerospace applications.
- Technologie et équipement : Inquire about the types of metal 3D printing technologies they employ (e.g., DMLS, SLM, EBM). The choice of technology can impact the achievable part size, complexity, tolerance, and surface finish. Métal3DP utilizes advanced SEBM printers known for their accuracy and reliability in producing large, complex metal parts.
- Quality Assurance and Certifications: Verify if the provider has robust quality management systems and relevant industry certifications, such as AS9100 for aerospace applications. This ensures that their processes meet stringent quality standards for design, manufacturing, and inspection.
- Expertise en matière de conception pour la fabrication additive (DfAM) : A knowledgeable service provider should offer expertise in DfAM principles to help optimize your diffuser design for 3D printing, maximizing its performance and manufacturability. Métal3DP provides comprehensive application development services to assist clients in tailoring their designs for additive manufacturing.
- Capacités de post-traitement : Determine if the provider offers the necessary post-processing services, such as heat treatment, surface finishing, and inspection, required for your specific application. A one-stop-shop for printing and post-processing can streamline the production process. Métal3DP offers a full suite of post-processing services to deliver finished, ready-to-use components.
- Lead Times and Production Capacity: Discuss their typical lead times for similar projects and assess their production capacity to ensure they can meet your volume requirements and timelines.
- Cost Structure and Transparency: Understand their pricing model and ensure transparency in all cost components. Request a detailed quotation that outlines material costs, printing costs, post-processing charges, and any other applicable fees.
- Communication and Support: Evaluate their responsiveness, technical support capabilities, and willingness to collaborate throughout the project lifecycle. A strong communication channel is essential for a successful partnership. Métal3DP is committed to providing excellent customer support and technical assistance.
By carefully evaluating these factors, you can select a metal 3D printing service provider like Métal3DP that can reliably produce high-quality jet engine diffusers that meet your specific performance and quality requirements.
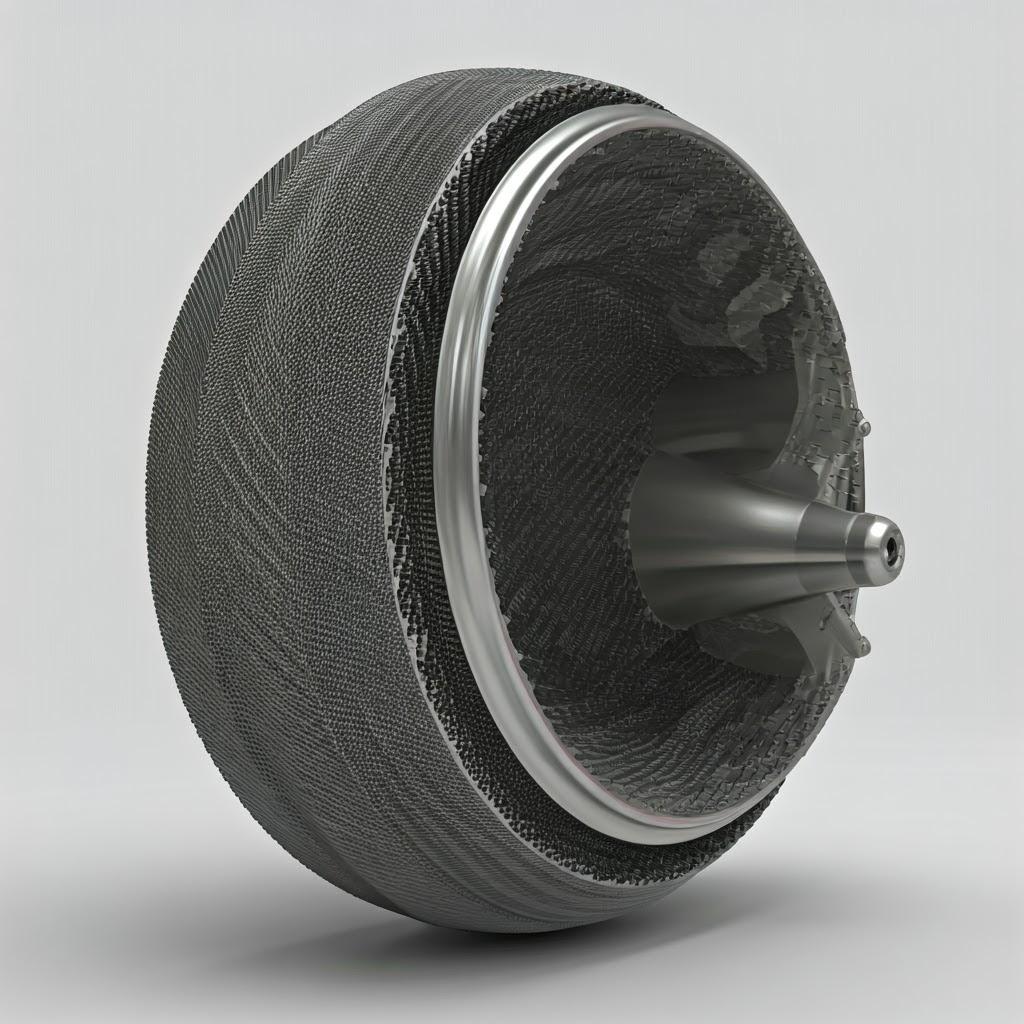
Cost Factors and Lead Time for 3D Printed Diffusers
The cost and lead time for manufacturing jet engine diffusers using metal 3D printing are influenced by several factors:
- Coûts des matériaux : The cost of the metal powder is a significant factor. High-performance alloys like IN738LC and Rene 41 are typically more expensive than standard metals. The volume of material required for the diffuser also directly impacts the cost.
- Temps d'impression : The build time depends on the size and complexity of the diffuser, the layer height used, and the printing technology. Longer build times translate to higher machine operating costs.
- Coûts de post-traitement : The extent of post-processing required (e.g., support removal, heat treatment, machining, coating) significantly affects the overall cost. Complex geometries often necessitate more intricate and time-consuming post-processing.
- Coûts de main-d'œuvre : The labor involved in design optimization, print setup, machine operation, post-processing, and quality inspection contributes to the total cost.
- Machine Depreciation and Overhead: The cost of the 3D printing equipment and the associated operational overhead are factored into the pricing.
- Volume de production : Generally, the cost per part decreases as the production volume increases, due to economies of scale.
Délai de mise en œuvre: The lead time for metal 3D printed diffusers typically includes:
- Design and Optimization: Time spent on designing or optimizing the diffuser for additive manufacturing.
- Temps de construction : The duration of the 3D printing process.
- Temps de post-traitement : The time required for support removal, heat treatment, surface finishing, and other post-processing steps.
- Contrôle de la qualité : The time taken for thorough inspection and quality checks.
- Expédition: The time for packaging and delivery of the finished parts.
Compared to traditional manufacturing, metal 3D printing can offer shorter lead times for complex geometries and low to medium production volumes, as it eliminates the need for tooling. However, the exact cost and lead time will vary depending on the specific design, material, and service provider. Métal3DP provides transparent cost breakdowns and works closely with clients to establish realistic lead times based on their project requirements. Contact us for a detailed cost estimate and lead time assessment for your jet engine diffuser project.
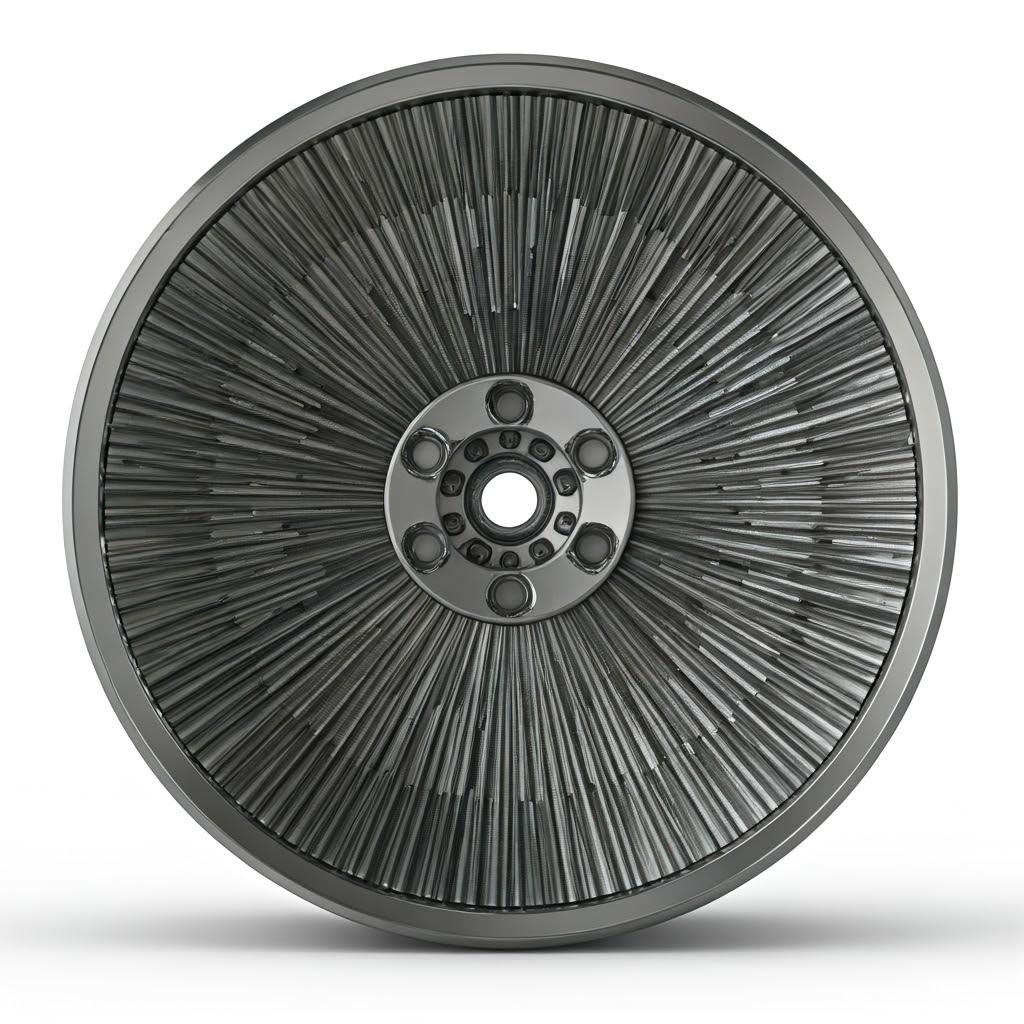
Foire aux questions (FAQ)
- Can metal 3D printed diffusers meet aerospace industry standards? Yes, when produced using high-quality metal powders and adhering to strict quality control processes, metal 3D printed diffusers can meet the demanding standards of the aerospace industry. Materials like IN738LC and Rene 41 are well-suited for high-temperature aerospace applications, and providers like Métal3DP with AS9100 certification ensure rigorous quality management.
- What are the typical size limitations for 3D printed jet engine diffusers? The maximum printable size depends on the build volume of the metal 3D printer. Métal3DP‘s printers offer industry-leading print volumes, enabling the production of relatively large diffuser components. For extremely large parts, segmented printing and subsequent joining techniques can also be considered.
- Is metal 3D printing cost-effective for producing jet engine diffusers? For complex geometries, low to medium production volumes, and customized designs, metal 3D printing can be a cost-effective alternative to traditional manufacturing. It eliminates tooling costs, reduces material waste, and enables design optimization for weight reduction, leading to potential long-term cost savings in fuel efficiency. The cost-effectiveness is highly dependent on the specific application and production volume.
Conclusion: The Future of Jet Engine Diffusers is Additive
Metal 3D printing is revolutionizing the manufacturing of jet engine diffusers, offering unprecedented design freedom, material efficiency, and performance enhancements. The ability to create complex internal geometries, reduce weight through topology optimization and lattice structures, and utilize high-performance alloys like IN738LC and Rene 41 positions additive manufacturing as a key technology for the aerospace industry. Companies like Métal3DP, with our advanced printing technology, high-quality metal powders, and comprehensive post-processing capabilities, are enabling aerospace engineers and procurement managers to realize the full potential of metal 3D printing for mission-critical components. By embracing additive manufacturing, the aerospace industry can achieve lighter, more efficient, and higher-performing jet engines, paving the way for the future of air travel. Contact Métal3DP today to explore how our metal additive manufacturing solutions can power your organization’s aerospace manufacturing goals.
Partager sur
MET3DP Technology Co. est un fournisseur de premier plan de solutions de fabrication additive dont le siège se trouve à Qingdao, en Chine. Notre société est spécialisée dans les équipements d'impression 3D et les poudres métalliques de haute performance pour les applications industrielles.
Articles connexes
À propos de Met3DP
Mise à jour récente
Notre produit
CONTACTEZ-NOUS
Vous avez des questions ? Envoyez-nous un message dès maintenant ! Nous répondrons à votre demande avec toute une équipe dès réception de votre message.
Obtenir les informations de Metal3DP
Brochure du produit
Obtenir les derniers produits et la liste des prix
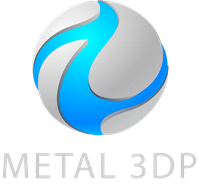
Poudres métalliques pour l'impression 3D et la fabrication additive