Corrosion-Resistant Housings for Hydrophones: Advancing Underwater Acoustic Technology
Table des matières
The exploration and monitoring of underwater environments rely heavily on the performance and longevity of hydrophones. These sensitive acoustic sensors are deployed in diverse and often harsh conditions, demanding robust and reliable protective housings. Traditionally manufactured housings can face limitations in design complexity, material suitability for corrosive environments, and production efficiency. Metal Impression 3D, also known as metal additive manufacturing, offers a transformative approach to creating high-performance, corrosion-resistant housings tailored precisely for demanding underwater applications.
What are Corrosion-Resistant Hydrophone Housings Used For?
Corrosion-resistant hydrophone housings play a crucial role in a wide array of underwater applications across various industries. Their primary function is to protect the delicate hydrophone sensor from the surrounding aquatic environment, ensuring accurate and reliable acoustic data acquisition. Here’s a breakdown of key use cases:
- Oceanographic Research: Scientists and researchers utilize hydrophones housed in corrosion-resistant enclosures to study marine life vocalizations, monitor ocean currents, analyze underwater geological events, and track climate change indicators. These housings must withstand prolonged exposure to saltwater and varying depths.
- Offshore Oil and Gas: In this sector, hydrophones are essential for seismic surveys, equipment monitoring, and environmental compliance. Corrosion-resistant housings are critical due to the harsh offshore conditions and the potential for exposure to hydrocarbons and other corrosive substances.
- Naval and Defense: Underwater surveillance, sonar systems, and communication networks rely on hydrophones with robust housings capable of withstanding extreme pressures and corrosive seawater for extended periods.
- Aquaculture: Monitoring fish populations, feeding patterns, and environmental conditions in aquaculture farms benefits from the use of hydrophones in durable, corrosion-resistant housings that do not introduce contaminants.
- Surveillance de l'environnement : Assessing noise pollution levels in marine environments, monitoring the impact of human activities on aquatic ecosystems, and tracking marine mammal migrations all depend on reliable hydrophone systems with appropriate protective housings.
- ** подводная робототехника (Underwater Robotics):** Remotely Operated Vehicles (ROVs) and Autonomous Underwater Vehicles (AUVs) often integrate hydrophones for navigation, obstacle avoidance, and data collection. Their housings must be compact, lightweight, and exceptionally resistant to corrosion and pressure.
By providing a reliable barrier against the damaging effects of the underwater environment, these housings ensure the continuous and accurate operation of hydrophone systems, enabling critical data collection and informed decision-making across diverse maritime fields.
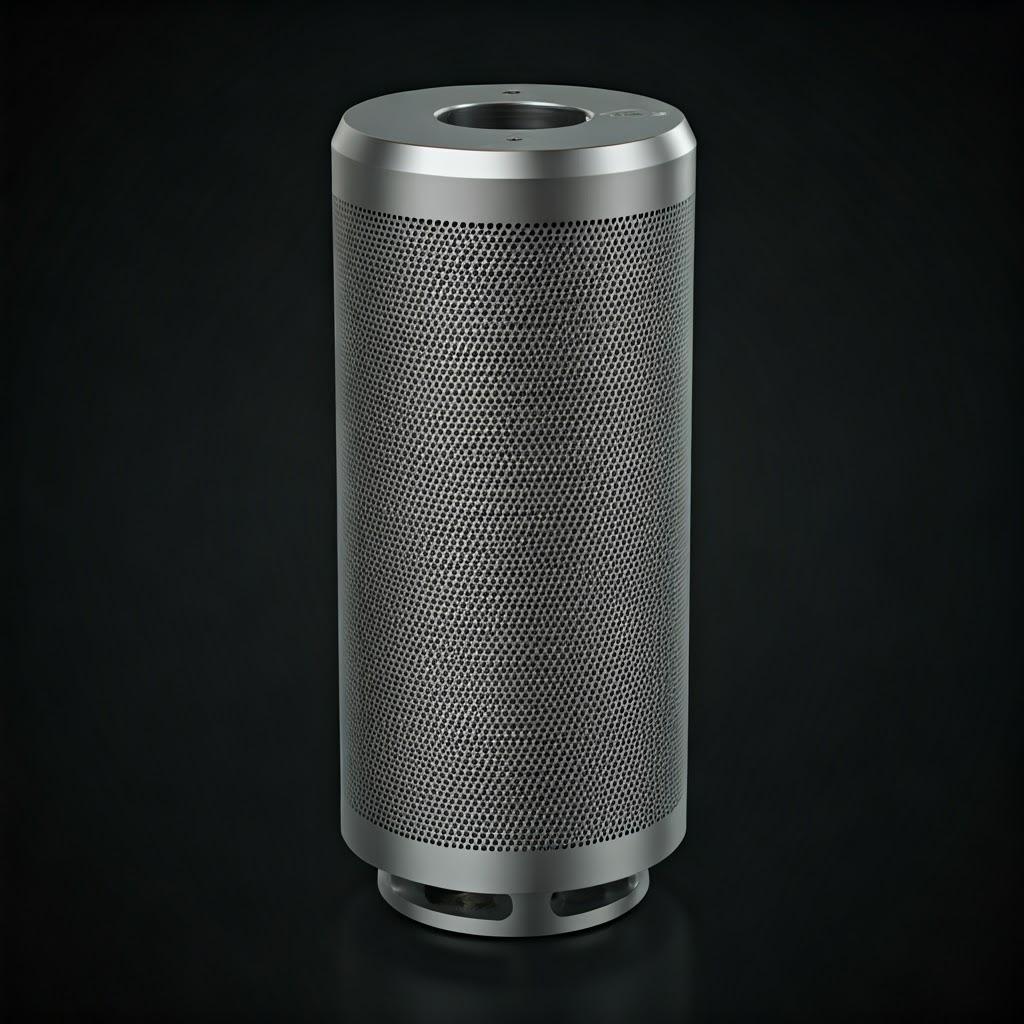
Why Use Metal 3D Printing for Hydrophone Housings?
Opting for metal 3D printing for the fabrication of corrosion-resistant hydrophone housings offers significant advantages over traditional manufacturing methods. These benefits address key challenges related to performance, design flexibility, material selection, and production efficiency:
- Liberté de conception accrue : Additive manufacturing allows for the creation of complex geometries that are difficult or impossible to achieve with conventional techniques like machining or casting. This enables optimized hydrodynamic designs for reduced drag, integrated mounting features, and custom internal structures to accommodate specific hydrophone sensors. Engineers can design housings with intricate baffling or acoustic lensing features directly into the part, improving sensor performance.
- Superior Material Selection for Corrosion Resistance: Metal 3D printing is compatible with a range of high-performance, corrosion-resistant alloys such as 316L stainless steel and CuNi30Mn1Fe (copper-nickel alloy). These materials offer excellent resistance to saltwater corrosion, biofouling, and the harsh conditions encountered in underwater environments. Traditional methods might be limited in the complexity achievable with these specialized alloys. At Métal3DP, we offer a selection of premium metal powders, including those ideal for demanding marine applications. You can explore our range of poudres métalliques de haute qualité pour vos besoins spécifiques.
- Customization and Rapid Prototyping: Metal 3D printing facilitates the rapid creation of prototypes with design iterations that can be quickly tested and refined. This agility is crucial for developing housings tailored to specific hydrophone models and application requirements. Furthermore, additive manufacturing allows for the production of small to medium batches of customized housings cost-effectively, without the need for expensive tooling.
- Efficacité des matériaux et réduction des déchets : Unlike subtractive manufacturing processes that remove material to create a part, metal 3D printing builds the object layer by layer, minimizing material waste. This is particularly beneficial when working with expensive, specialized alloys.
- Integration of Features: Metal 3D printing enables the integration of multiple functionalities into a single part. For example, mounting features, cable glands, and even internal acoustic dampening structures can be directly incorporated into the housing design, reducing the need for additional components and assembly steps.
- Potentiel d'allègement : Through optimized internal lattice structures and topology optimization, metal 3D printed housings can be designed to be lighter than traditionally manufactured counterparts without compromising structural integrity or corrosion resistance. This is particularly important for AUVs and other mobile underwater platforms where weight is a critical factor.
By leveraging the capabilities of metal 3D printing, engineers and procurement managers can obtain high-performance, corrosion-resistant hydrophone housings that meet the demanding requirements of diverse underwater applications, often exceeding the limitations of traditional manufacturing.
Recommended Materials and Why They Matter
The selection of the appropriate metal powder is paramount in ensuring the corrosion resistance, mechanical integrity, and overall performance of 3D printed hydrophone housings. Métal3DP offers a range of high-quality metal powders specifically suited for demanding environments. For underwater hydrophone housings requiring exceptional corrosion resistance, we recommend the following materials:
- Acier inoxydable 316L : This austenitic stainless steel is a widely used material in marine environments due to its excellent resistance to pitting and crevice corrosion in saltwater. The addition of molybdenum enhances its resistance to chloride attack, making it superior to 304 stainless steel in harsh marine conditions. 316L also offers good weldability, formability, and mechanical properties, making it a versatile choice for hydrophone housings. Its biocompatibility also makes it suitable for certain environmental monitoring applications. You can learn more about the applications of metal 3D printing in various industries on our impression 3D de métaux page. | Property | Value | Significance for Hydrophone Housings | | :—————————- | :———————————— | :—————————————————————————————————————————————————————————————————————————– | | Résistance à la corrosion | Excellent in saltwater and chloride environments | Ensures long-term reliability and performance in underwater deployments, minimizing degradation of the housing and protecting the sensitive hydrophone sensor. | | Résistance à la traction | ~550 MPa | Provides the structural integrity needed to withstand hydrostatic pressure at various depths and potential mechanical stresses during deployment and retrieval. | | Limite d'élasticité | ~290 MPa | Indicates the material’s resistance to permanent deformation under load, crucial for maintaining the housing’s shape and protecting the internal components. | | Allongement à la rupture | ~40% | Measures the material’s ductility, allowing it to deform without fracturing under stress, which is important for impact resistance. | | Biocompatibilité | Yes | Important for applications where the housing might interact with marine life or sensitive ecosystems, ensuring no harmful leaching of materials. | | Soudabilité | Good | Facilitates potential post-processing steps or integration with other components. | | Compatibilité avec l'impression 3D | Excellent with Laser Powder Bed Fusion (LPBF) and Direct Metal Laser Sintering (DMLS) | Allows for the creation of complex geometries and fine features essential for optimized hydrodynamic designs and integrated functionalities. Métal3DP‘s advanced printing technology ensures high-density parts with excellent material properties. |
- CuNi30Mn1Fe (Copper-Nickel Alloy): This alloy, typically composed of approximately 70% copper and 30% nickel with additions of manganese and iron, offers exceptional resistance to seawater corrosion and biofouling. Copper naturally inhibits the growth of marine organisms, reducing the need for anti-fouling coatings and maintaining the hydrodynamic efficiency of the housing over extended deployments. CuNi alloys also exhibit good thermal conductivity and moderate strength. | Property | Value | Significance for Hydrophone Housings | | :—————————- | :————————————- | :————————————————————————————————————————————————————————————————————————————————————————————————- | | Résistance à la corrosion | Excellent in seawater, high resistance to biofouling | Minimizes the accumulation of marine organisms, maintaining the hydrodynamic profile and preventing degradation of the housing material, leading to longer service life and reduced maintenance. | | Résistance à la traction | ~450 MPa | Provides sufficient structural integrity for many underwater applications and depths. | | Limite d'élasticité | ~200 MPa | Offers good resistance to permanent deformation under typical operating loads. | | Allongement à la rupture | ~35% | Provides good ductility for impact resistance. | | Résistance à l'encrassement | Excellent | A key advantage in long-term underwater deployments, reducing maintenance requirements and ensuring consistent performance. | | Conductivité thermique | Higher than stainless steel | Can be beneficial for dissipating heat generated by the hydrophone electronics in certain applications. | | Compatibilité avec l'impression 3D | Good with Laser Powder Bed Fusion (LPBF) | Allows for the creation of complex and customized housing designs. Métal3DP‘s expertise in processing copper-based alloys ensures high-quality, corrosion-resistant parts. Our méthodes d'impression are optimized for various materials. |
The choice between 316L and CuNi30Mn1Fe will depend on the specific application requirements, including the severity of the corrosive environment, the need for biofouling resistance, mechanical load considerations, and budget. Consulting with the material science experts at Métal3DP can help you determine the optimal powder for your hydrophone housing needs. We leverage our système avancé de fabrication de poudres to ensure the highest quality and performance of our metal powders.
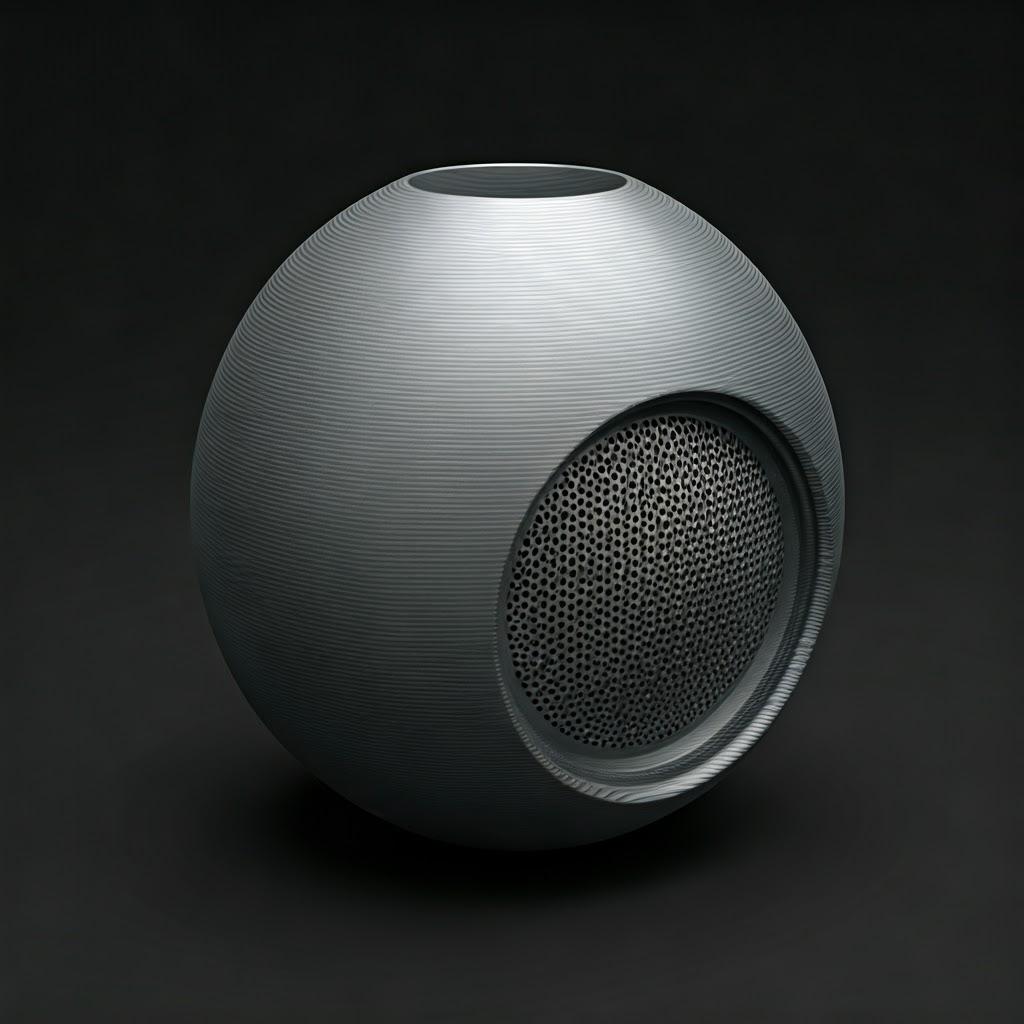
Design Considerations for Additive Manufacturing of Hydrophone Housings
Optimizing the design of hydrophone housings for metal 3D printing is crucial to fully leverage the capabilities of additive manufacturing and ensure the final part meets the required performance specifications. Unlike traditional manufacturing methods with their inherent design constraints, metal 3D printing offers a high degree of design freedom. Here are key considerations for engineers:
- Hydrodynamic Efficiency: For housings deployed on moving platforms like AUVs or in strong currents, minimizing drag is essential. Metal 3D printing allows for the creation of streamlined shapes and complex curves that reduce water resistance. Consider incorporating features like tapered edges or smooth transitions to improve flow.
- Integration of Mounting Features: Design mounting interfaces directly into the housing. This can include threaded holes, flanges with specific bolt patterns, or custom interlocking mechanisms. Integrating these features eliminates the need for secondary machining or assembly of separate components, reducing cost and potential failure points.
- Optimisation de l'épaisseur de la paroi : Utilize Finite Element Analysis (FEA) to determine the optimal wall thickness required to withstand the expected hydrostatic pressure at the maximum deployment depth. Additive manufacturing allows for varying wall thicknesses across the part, placing material where it’s needed most and reducing weight in less stressed areas.
- Internal Cavity Design: The internal cavity must precisely accommodate the hydrophone sensor and any associated electronics. Consider留出足够的空间 (leave enough space) for cable routing and connectors. For housings requiring specific acoustic properties, internal baffling or sound-dampening structures can be designed and 3D printed directly into the part.
- Support Structure Strategy: During the metal 3D printing process, support structures are often necessary to prevent part deformation and ensure proper overhangs. Design the part with consideration for easy support removal to minimize post-processing time and potential surface damage. Orienting the part strategically on the build platform can also reduce the need for extensive supports.
- Minimizing Trapped Powder: Design internal channels and cavities to allow for the effective removal of un-sintered metal powder after the printing process. Trapped powder can be difficult to remove and may compromise the long-term performance of the housing, especially in corrosive environments.
- Feature Size and Resolution: Be mindful of the minimum feature sizes and achievable resolution of the chosen metal 3D printing technology. Small threads, intricate details, and thin walls may require specific process parameters and careful design to ensure they are printed accurately. Consult with Métal3DP‘s experts to understand the capabilities of our equipment and optimize your design accordingly.
- Optimisation de la topologie : Explore the use of topology optimization software to generate designs that maximize strength-to-weight ratio by strategically removing material from less stressed areas. This can lead to lighter and more efficient housings without compromising structural integrity.
By carefully considering these design aspects specific to additive manufacturing, engineers can create high-performance, corrosion-resistant hydrophone housings that are optimized for functionality, weight, and manufacturability.
Tolerance, Surface Finish, and Dimensional Accuracy of 3D Printed Housings
Achieving the required tolerance, surface finish, and dimensional accuracy is critical for the proper functioning and integration of 3D printed hydrophone housings. Metal 3D printing technologies have advanced significantly, offering increasingly precise and high-quality results. Here’s what users can typically expect:
- Précision dimensionnelle : The dimensional accuracy achievable with metal 3D printing depends on several factors, including the chosen printing technology (e.g., Laser Powder Bed Fusion – LPBF, Direct Metal Laser Sintering – DMLS), the material used, the size and complexity of the part, and the optimization of printing parameters. Typically, tolerances in the range of ±0.1 to ±0.05 mm can be achieved on critical dimensions. For highly demanding applications, post-processing steps like CNC machining can further improve dimensional accuracy. Métal3DP‘s printers are known for their industry-leading accuracy and reliability, ensuring that your hydrophone housings meet stringent specifications.
- Finition de la surface : The as-printed surface finish in metal 3D printing is generally rougher compared to machined surfaces, typically ranging from Ra 5-20 µm depending on the powder size and printing parameters. For underwater applications, a smoother surface finish can be beneficial in reducing drag and minimizing biofouling. Post-processing techniques such as media blasting, polishing, or electrochemical polishing can be employed to achieve smoother surface finishes as required.
- Tolerance Considerations in Design: When designing hydrophone housings for metal 3D printing, it’s essential to consider the achievable tolerances and incorporate appropriate clearances and fits for mating parts, such as the hydrophone sensor itself and any sealing components. Specifying critical dimensions with appropriate tolerances on the design drawings is crucial for ensuring proper assembly and functionality.
- Impact of Material Choice: Different metal powders can exhibit variations in achievable tolerance and surface finish. For instance, finer powder particles generally lead to smoother surface finishes and potentially higher accuracy. The thermal conductivity and solidification behavior of the material can also influence the final dimensions and potential for warping.
- Role of Build Orientation and Support Structures: The orientation of the part on the build platform and the placement of support structures can impact both dimensional accuracy and surface finish. Surfaces that are oriented upwards during printing tend to have a better surface finish than downward-facing surfaces that are in contact with support structures. Careful build planning is essential to minimize these effects.
- Quality Control and Inspection: Employing rigorous quality control measures, including dimensional measurements using coordinate measuring machines (CMMs) and surface roughness testing, is crucial to verify that the 3D printed hydrophone housings meet the specified tolerances and surface finish requirements.
By understanding the capabilities and limitations of metal 3D printing in terms of tolerance, surface finish, and dimensional accuracy, engineers can design housings that meet the functional requirements of their underwater applications. When high precision is paramount, consider incorporating post-processing steps to achieve the desired level of accuracy and surface quality.
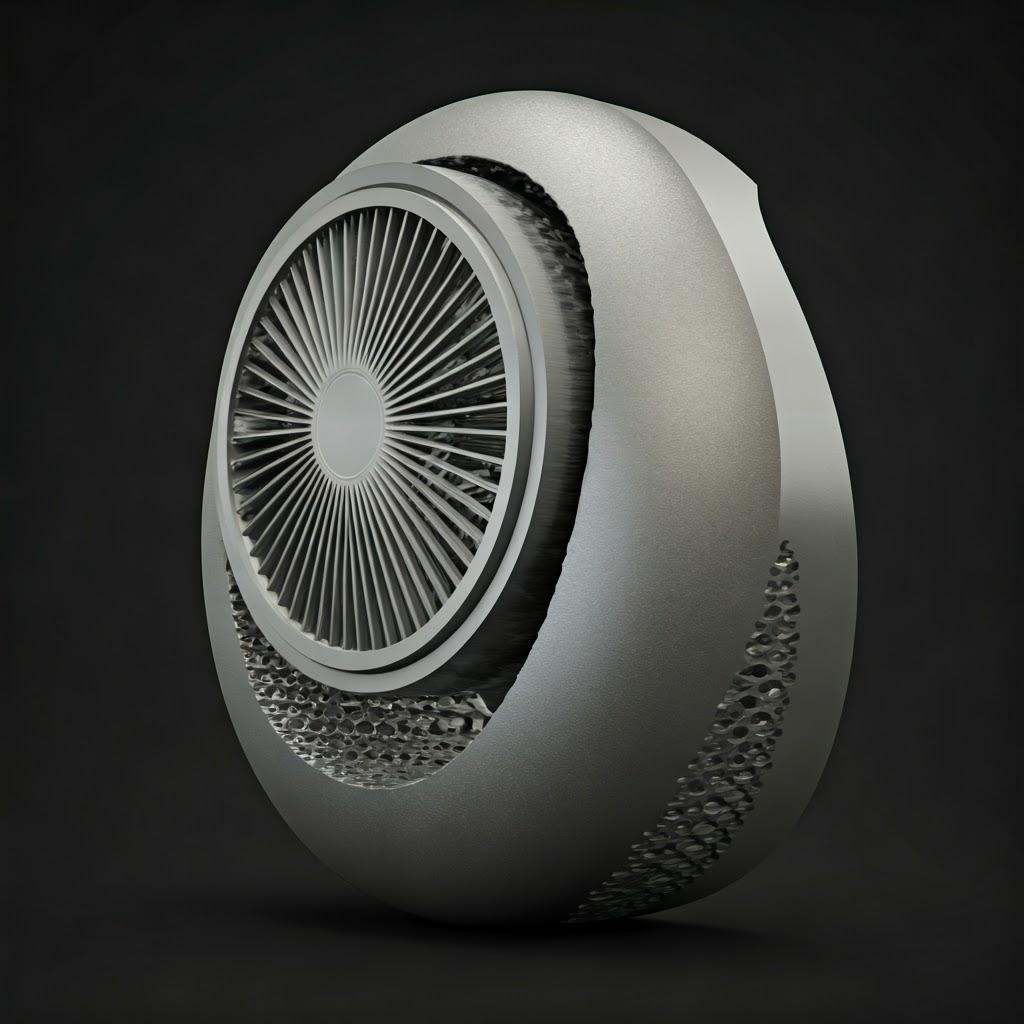
Post-Processing Requirements for 3D Printed Hydrophone Housings
While metal 3D printing offers near-net-shape manufacturing, some post-processing steps are often necessary to achieve the final desired properties, surface finish, and dimensional accuracy of hydrophone housings. The specific post-processing requirements will depend on the application, the material used, and the as-printed quality. Common post-processing steps include:
- Elimination des poudres : After the printing process, un-sintered metal powder needs to be carefully removed from internal channels and external surfaces. This is typically done using compressed air, vacuum systems, or specialized powder removal equipment. For intricate internal geometries, more advanced techniques might be required.
- Retrait de la structure de soutien : If support structures were used during printing, they need to be removed. This can be done manually using cutting tools, or through automated processes like machining or electrochemical dissolution, depending on the material and support type. Careful removal is essential to avoid damaging the part surface.
- Traitement thermique anti-stress : Metal 3D printed parts can have residual stresses due to the rapid heating and cooling cycles during the printing process. Stress relief annealing is often performed to reduce these stresses, improve dimensional stability, and enhance mechanical properties. The specific temperature and duration of the heat treatment will depend on the material.
- Finition de la surface : As mentioned earlier, the as-printed surface finish may not be suitable for all applications. Various surface finishing techniques can be employed to achieve smoother surfaces, including:
- Media Blasting: Using abrasive media to remove surface imperfections and create a more uniform finish.
- Polissage : Mechanical or chemical polishing to achieve a smooth, often reflective surface, which can be beneficial for reducing drag and biofouling.
- Electrochemical Polishing: Using an electrochemical process to smooth the surface by selectively removing material.
- Usinage CNC : For critical dimensions requiring very tight tolerances, CNC machining can be used as a secondary process to achieve the desired accuracy on specific features, such as mounting interfaces or sealing surfaces.
- Coating and Surface Treatment: Depending on the specific underwater environment, additional coatings or surface treatments may be applied to further enhance corrosion resistance or provide anti-fouling properties. Examples include specialized paints, electrochemical coatings, or plasma spraying.
- Contrôle de la qualité : After all post-processing steps are complete, thorough quality inspection is essential to ensure that the hydrophone housings meet the required dimensional accuracy, surface finish, and material properties. This may involve visual inspection, dimensional measurements using CMMs, and non-destructive testing methods like ultrasonic testing or dye penetrant inspection to detect any internal flaws.
Understanding the necessary post-processing steps and their impact on the final part is crucial for budgeting time and costs associated with the production of 3D printed hydrophone housings. Collaborating with an experienced metal 3D printing service provider like Métal3DP, which offers comprehensive post-processing capabilities, can streamline the entire manufacturing process.
Common Challenges and How to Avoid Them in 3D Printing Hydrophone Housings
While metal 3D printing offers numerous advantages, certain challenges can arise during the fabrication of hydrophone housings. Understanding these potential issues and implementing appropriate strategies can help avoid them and ensure the production of high-quality, reliable parts:
- Déformation et distorsion : Thermal stresses during the printing process can lead to warping or distortion of the part, especially for large or complex geometries.
- How to Avoid: Optimize part orientation on the build platform, use appropriate support structures to anchor critical areas, and employ stress relief heat treatment after printing. Careful control of printing parameters and build chamber temperature is also crucial.
- Porosity and Density Issues: Insufficient laser power or improper printing parameters can result in porosity within the printed part, compromising its mechanical strength and corrosion resistance.
- How to Avoid: Work with an experienced metal 3D printing provider like Métal3DP that has expertise in material-specific printing parameters and utilizes high-quality metal powders. Optimize scanning strategies and ensure proper powder bed preparation. Our Système avancé de fabrication de poudres ensures the high density and flowability of our powders, minimizing porosity.
- Support Removal Damage: Removing support structures can sometimes leave surface marks or damage the part, especially on delicate features.
- How to Avoid: Design parts with self-supporting geometries where possible, optimize support structure placement for easy removal, and utilize appropriate removal techniques. Consider using dissolvable support materials if available for the chosen metal.
- Achieving Tight Tolerances: Meeting tight dimensional tolerances can be challenging with as-printed parts, especially for complex geometries.
- How to Avoid: Design with realistic tolerances in mind, consider using hybrid manufacturing approaches that combine 3D printing for near-net-shape fabrication with precision CNC machining for critical features. Ensure proper calibration of the 3D printer and utilize accurate post-processing measurement techniques.
- Rugosité de la surface : The as-printed surface finish may be too rough for certain applications, potentially increasing drag or promoting biofouling.
- How to Avoid: Specify appropriate surface finishing techniques such as polishing or media blasting as part of the post-processing workflow. Optimize printing parameters, such as layer height and powder particle size, to improve the as-printed surface finish.
- Material Compatibility and Corrosion: Choosing the wrong metal powder or improper handling can lead to inadequate corrosion resistance in the intended underwater environment.
- How to Avoid: Select materials specifically designed for marine applications, such as 316L stainless steel or CuNi30Mn1Fe. Consult with material experts at Métal3DP to ensure the chosen powder is compatible with the intended environment. Implement proper powder handling and storage procedures to prevent contamination.
- Cost Management: Metal 3D printing can be more expensive than traditional methods for very high production volumes.
- How to Avoid: Focus on applications where the design flexibility, customization, or performance benefits of metal 3D printing outweigh the initial cost per part. Optimize designs for efficient printing and material usage. Consider the total cost of ownership, including reduced assembly, tooling, and potential for improved performance and longevity.
By anticipating these potential challenges and implementing appropriate design and manufacturing strategies, engineers and procurement managers can successfully leverage metal 3D printing to produce high-quality, corrosion-resistant hydrophone housings that meet the demanding requirements of underwater applications.
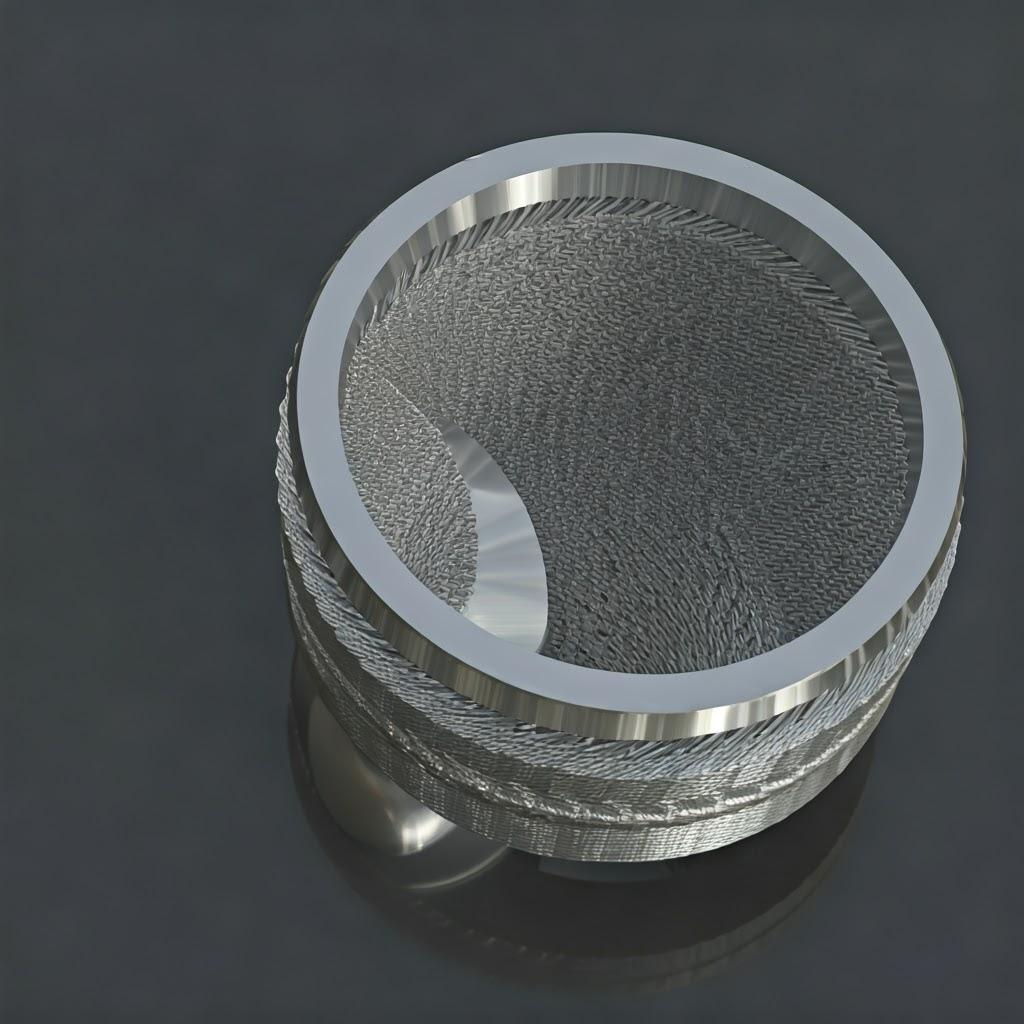
How to Choose the Right Metal 3D Printing Service Provider for Hydrophone Housings
Selecting the right metal 3D printing service provider is crucial for ensuring the successful fabrication of high-quality, corrosion-resistant hydrophone housings that meet your specific requirements. Consider the following factors when evaluating potential suppliers:
- Expertise matérielle : Ensure the provider has extensive experience working with corrosion-resistant alloys like 316L stainless steel and CuNi30Mn1Fe, and possesses a deep understanding of their properties and processing parameters. Métal3DP se spécialise dans poudres métalliques de haute qualité optimized for additive manufacturing, including those ideal for marine environments.
- Technology and Equipment: Inquire about the types of metal 3D printing technologies they utilize (e.g., LPBF, DMLS). Different technologies offer varying levels of precision, surface finish, and build volume. Ensure their equipment is well-maintained and calibrated to deliver consistent results. Our méthodes d'impression leverage industry-leading technology for optimal performance.
- Quality Control and Certifications: Verify that the provider has robust quality control processes in place, including material traceability, in-process monitoring, and post-printing inspection. Look for relevant certifications such as ISO 9001 or industry-specific standards that demonstrate their commitment to quality.
- Design and Engineering Support: A reputable service provider should offer design consultation and engineering support to help optimize your hydrophone housing design for additive manufacturing, considering factors like material selection, build orientation, and support structure strategy. Métal3DP‘s team possesses decades of collective expertise in metal additive manufacturing and application development.
- Post-Processing Capabilities: Ensure the provider offers the necessary post-processing services to meet your requirements, such as powder removal, stress relief heat treatment, surface finishing (e.g., polishing, media blasting), and CNC machining for critical tolerances. A comprehensive suite of services streamlines the manufacturing process.
- Build Volume and Capacity: Confirm that the provider has sufficient build volume to accommodate the size of your hydrophone housings and the capacity to handle your production volumes within your required lead times. Métal3DP‘s printers deliver industry-leading print volume to meet diverse production needs.
- Communication and Customer Service: Evaluate the provider’s responsiveness, communication clarity, and willingness to collaborate throughout the project. A strong partnership based on open communication is essential for a successful outcome.
- Expérience dans le secteur : Prioritize providers with a proven track record of serving industries relevant to your application, such as aerospace, marine, or oil and gas. Their experience in these sectors indicates an understanding of the specific challenges and requirements.
- Cost and Lead Time: Obtain clear and detailed quotes that outline all costs, including printing, materials, and post-processing. Understand the estimated lead time for production and delivery. While cost is a factor, prioritize quality and reliability, especially for critical underwater applications.
By carefully evaluating these factors, you can select a metal 3D printing service provider that can deliver high-performance, corrosion-resistant hydrophone housings that meet your technical and business objectives. Contact Métal3DP to explore how our capabilities can power your organization’s additive manufacturing goals.
Cost Factors and Lead Time for 3D Printed Hydrophone Housings
The cost and lead time for producing corrosion-resistant hydrophone housings using metal 3D printing are influenced by several factors. Understanding these elements can help in budgeting and project planning:
Facteurs de coût :
- Coût des matériaux : The type and quantity of metal powder used significantly impact the overall cost. Corrosion-resistant alloys like 316L and CuNi30Mn1Fe can have higher material costs compared to standard metals. The efficiency of the printing process and the ability to minimize waste also play a role.
- Temps de construction : The duration of the printing process is a key cost driver. Longer build times, influenced by part size, complexity, and layer height, translate to higher machine operating costs.
- Coûts de post-traitement : The extent of post-processing required (e.g., support removal, heat treatment, surface finishing, machining) adds to the overall cost. Complex geometries that require extensive support removal or demanding surface finish requirements will incur higher post-processing expenses.
- Complexité de la conception : Intricate designs that require significant engineering effort for optimization and build preparation can increase upfront costs.
- Volume de production : While metal 3D printing is cost-effective for low to medium volumes and highly customized parts, the cost per part may not be as competitive as traditional methods for very high production runs. However, factors like reduced tooling costs and faster time-to-market can offset this in many cases.
- Service Provider Overhead: The pricing structure of the chosen metal 3D printing service provider, including their operational costs, expertise, and quality control measures, will also influence the final cost.
Facteurs de délai d'exécution :
- Design and Engineering: The time required for design optimization, material selection, and build preparation can impact the overall lead time, especially for complex or novel designs.
- Temps d'impression : The actual printing duration depends on the size and complexity of the housings and the number of parts being printed simultaneously.
- Post-Processing Time: The time needed for various post-processing steps, such as heat treatment, surface finishing, and quality inspection, will add to the total lead time.
- Service Provider Capacity and Scheduling: The current workload and scheduling of the chosen service provider can affect the turnaround time. It’s essential to discuss lead times upfront.
- Shipping and Logistics: The time required for shipping the finished parts to their final destination should also be considered.
It’s important to obtain a detailed quotation from your chosen metal 3D printing service provider that breaks down the costs and provides a realistic estimate of the lead time based on your specific requirements. Discussing your project needs thoroughly with Métal3DP will allow us to provide an accurate assessment of both cost and lead time.
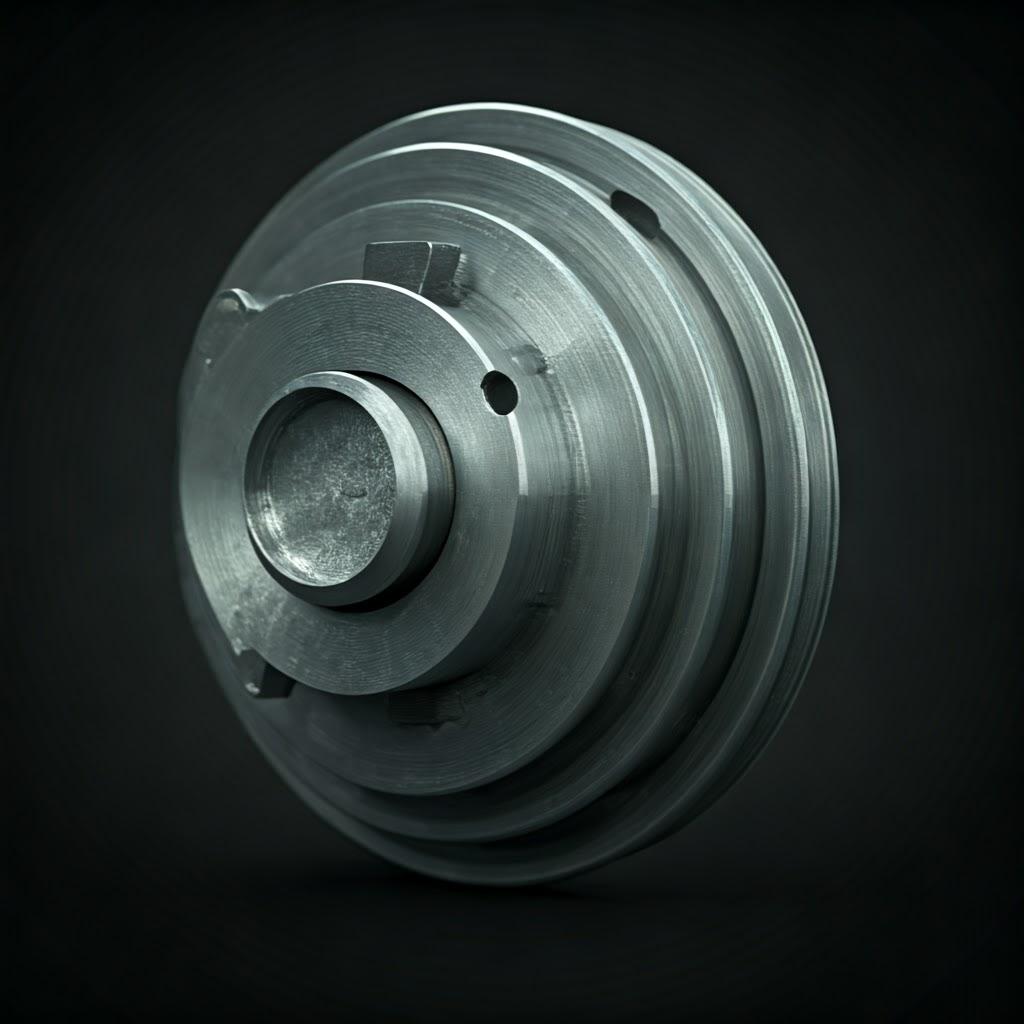
Foire aux questions (FAQ)
- Q: Can metal 3D printed hydrophone housings withstand deep-sea pressures?
- A : Yes, with proper design and material selection. By optimizing wall thickness using FEA and choosing high-strength, corrosion-resistant alloys like 316L, 3D printed housings can be designed to withstand significant hydrostatic pressures encountered in deep-sea environments. The density achieved through Métal3DP‘s printing processes ensures structural integrity.
- Q: Are 3D printed metal housings more susceptible to corrosion than traditionally manufactured ones?
- A : Not necessarily. When the correct corrosion-resistant materials are used and the printing process is optimized to achieve high density and minimize porosity, 3D printed housings can offer comparable or even superior corrosion resistance to traditionally manufactured parts. Post-processing surface treatments can further enhance corrosion protection.
- Q: What is the typical lifespan of a 3D printed metal hydrophone housing in a marine environment?
- A : The lifespan depends on factors such as the material used, the severity of the underwater environment (salinity, temperature, depth), and any post-processing treatments applied. High-quality materials like 316L and CuNi30Mn1Fe, processed by experienced providers like Métal3DP, can offer excellent long-term durability in marine applications. Regular inspection and maintenance are recommended to maximize lifespan.
Conclusion: Embracing Metal 3D Printing for Advanced Underwater Acoustic Solutions
Metal 3D printing is revolutionizing the design and manufacturing of corrosion-resistant hydrophone housings, offering unprecedented design freedom, material versatility, and the potential for enhanced performance in demanding underwater environments. By leveraging the capabilities of additive manufacturing and selecting appropriate materials like 316L stainless steel and CuNi30Mn1Fe, engineers and procurement managers can create customized housings with optimized hydrodynamic properties, integrated features, and exceptional resistance to saltwater corrosion and biofouling.
Choosing an experienced and knowledgeable metal 3D printing service provider like Métal3DP, with expertise in material science, advanced printing technologies, and comprehensive post-processing capabilities, is crucial for realizing the full potential of this transformative manufacturing approach. As underwater exploration and monitoring continue to grow in importance across various industries, metal 3D printing stands as a powerful tool for developing the next generation of robust and reliable acoustic sensing solutions. Contact Métal3DP today to discuss your specific hydrophone housing requirements and embark on a journey towards advanced additive manufacturing solutions.
Partager sur
MET3DP Technology Co. est un fournisseur de premier plan de solutions de fabrication additive dont le siège se trouve à Qingdao, en Chine. Notre société est spécialisée dans les équipements d'impression 3D et les poudres métalliques de haute performance pour les applications industrielles.
Articles connexes
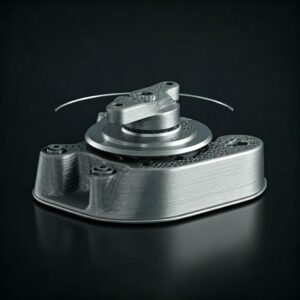
Supports imprimés en 3D pour les capteurs radar automobiles : Précision et performance
Lire la suite "À propos de Met3DP
Mise à jour récente
Notre produit
CONTACTEZ-NOUS
Vous avez des questions ? Envoyez-nous un message dès maintenant ! Nous répondrons à votre demande avec toute une équipe dès réception de votre message.
Obtenir les informations de Metal3DP
Brochure du produit
Obtenir les derniers produits et la liste des prix
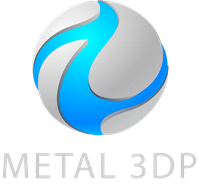
Poudres métalliques pour l'impression 3D et la fabrication additive
PRODUIT
cONTACT INFO
- Ville de Qingdao, Shandong, Chine
- [email protected]
- [email protected]
- +86 19116340731