Panneaux d'accès légers pour l'aérospatiale grâce à l'impression 3D
Table des matières
Révolutionner la conception aérospatiale : Panneaux d'accès légers grâce à l'impression 3D de métal
L'industrie aérospatiale représente le summum des réalisations techniques, repoussant sans cesse les limites de la performance, de l'efficacité et de la sécurité. Dans cet environnement exigeant, chaque composant, aussi petit soit-il en apparence, joue un rôle essentiel. Les panneaux d'accès de l'aérospatiale, bien que souvent négligés par l'observateur occasionnel, sont des éléments fondamentaux de la structure de l'aéronef et des protocoles de maintenance. Ces panneaux constituent des points d'entrée essentiels pour les opérations d'inspection, de maintenance, de réparation et de révision (MRO), et protègent les systèmes complexes logés dans la cellule, les ailes, les moteurs et d'autres sections critiques. Historiquement, ces composants ont été fabriqués à l'aide de méthodes traditionnelles telles que l'usinage CNC à partir de billettes solides ou le formage à partir de feuilles de métal. Bien que fiables, ces techniques présentent souvent des limites, notamment en ce qui concerne le poids, la complexité de la conception et les délais de fabrication, en particulier pour les faibles volumes ou les besoins hautement personnalisés typiques des cycles d'approvisionnement de l'aérospatiale.
Dans la quête incessante d'un meilleur rendement énergétique, d'une capacité de charge utile accrue et d'une réduction de l'impact sur l'environnement, la réduction du poids reste un objectif primordial pour les ingénieurs et les fabricants de l'aérospatiale. Chaque kilogramme économisé se traduit directement par des économies de coûts opérationnels et des gains de performance significatifs sur la durée de vie d'un aéronef. Cet impératif a stimulé l'innovation dans tous les aspects de la conception des aéronefs, depuis les structures composites avancées jusqu'aux systèmes hautement optimisés. Aujourd'hui, une technologie de fabrication transformatrice fait des percées significatives dans la production de composants tels que les panneaux d'accès : la fabrication additive métallique (AM)plus connu sous le nom de impression 3D de métaux. Cette technologie offre un changement de paradigme, en s'éloignant des méthodes soustractives (enlèvement de matière) ou formatives (mise en forme de la matière) pour adopter une approche additive, en construisant des pièces couche par couche directement à partir de dessins numériques, à l'aide de poudres métalliques spécialisées.
Le potentiel de l'AM des métaux dans l'aérospatiale est immense. Elle offre une liberté de conception sans précédent, permettant aux ingénieurs de créer des structures légères et hautement optimisées dont la fabrication était auparavant impossible ou d'un coût prohibitif. Des caractéristiques telles que des canaux internes complexes, des géométries à topologie optimisée qui placent stratégiquement le matériau uniquement là où il est nécessaire, et des fonctionnalités intégrées peuvent être réalisées directement au cours du processus d'impression. Pour les panneaux d'accès, cela se traduit par la possibilité de créer des composants nettement plus légers que leurs équivalents fabriqués traditionnellement, tout en conservant, voire en améliorant, l'intégrité structurelle et les caractéristiques de performance. Cette capacité n'est pas seulement une amélioration progressive ; elle représente un changement fondamental dans la manière dont les composants aérospatiaux peuvent être conceptualisés, conçus et produits.
L'adoption de l'AM des métaux s'accélère dans toute l'industrie, grâce aux progrès de la technologie des machines, de la science des matériaux et du contrôle des processus. Les principaux équipementiers aérospatiaux, les fournisseurs de niveau 1 et les prestataires de services de maintenance et de réparation spécialisés explorent et mettent en œuvre l'AM pour une gamme croissante d'applications, depuis les composants non critiques de la cabine jusqu'aux pièces structurelles critiques pour le vol. Les panneaux d'accès représentent un domaine d'application particulièrement approprié, car ils nécessitent souvent un équilibre entre résistance, rigidité et faible poids, ainsi que des variations géométriques en fonction de leur emplacement et de leur fonction sur l'avion. En outre, la capacité de l'AM à produire des pièces à la demande offre des avantages significatifs pour la gestion des pièces de rechange et la réduction des coûts de stockage, un facteur crucial pour la logistique aérospatiale et les fournisseurs en gros.
Des entreprises comme Met3dp sont à l'avant-garde de cette révolution de la fabrication. Fort de son expertise dans les systèmes avancés d'AM des métaux et dans la production de poudres métalliques de haute performance, Met3dp fournit des solutions complètes adaptées aux exigences du secteur aérospatial. Nos imprimantes SEBM (Selective Electron Beam Melting) à la pointe de l'industrie et nos poudres métalliques de haute qualité atomisées au gaz, y compris les alliages d'aluminium de qualité aérospatiale, permettent la production de pièces denses, fiables et géométriquement complexes telles que les panneaux d'accès légers. En tant que fournisseur et partenaire de confiance, nous collaborons avec les ingénieurs de l'aérospatiale et les responsables des achats pour exploiter tout le potentiel de la fabrication additive, en transformant la conception des composants et en optimisant les flux de travail de fabrication. Cet article de blog traite des spécificités de l'utilisation du métal dans la fabrication additive. Impression 3D pour les panneaux d'accès de l'aérospatiale, en explorant les applications, les avantages, les matériaux, les considérations de conception et les stratégies d'approvisionnement liées à l'adoption de cette technologie de pointe.
Fonctions critiques : À quoi servent les panneaux d'accès pour l'aérospatiale ?
Les panneaux d'accès de l'aérospatiale sont des composants omniprésents mais essentiels que l'on retrouve dans pratiquement tous les types d'aéronefs, qu'il s'agisse de petits avions d'aviation générale ou de drones, d'énormes avions de ligne à fuselage large, de jets militaires à hautes performances ou même d'engins spatiaux. Leur objectif premier est simple mais essentiel : fournir des sections amovibles à l'intérieur du revêtement ou de la structure de l'aéronef qui permettent aux techniciens et aux ingénieurs d'accéder de manière contrôlée aux systèmes et aux compartiments sous-jacents pour effectuer les tâches nécessaires. Sans ces panneaux, les inspections de routine, la maintenance programmée, les réparations imprévues ou les mises à niveau des composants seraient beaucoup plus complexes, prendraient plus de temps et risqueraient d'endommager la structure environnante.
Les fonctions et emplacements spécifiques des panneaux d'accès sont incroyablement variés, reflétant la complexité des systèmes aéronautiques modernes. Il est essentiel de comprendre ces rôles variés pour apprécier les exigences de conception et les avantages potentiels que la fabrication additive peut apporter.
Lieux et fonctions clés :
- Panneaux du fuselage : De nombreux panneaux d'accès sont situés le long du fuselage de l'avion. Ils permettent d'inspecter les éléments structurels (cadres, longerons), les faisceaux de câbles, les conduites hydrauliques, les conduits du système de contrôle environnemental (ECS), les baies avioniques, les soutes à bagages et d'autres systèmes internes. Certains sont de simples orifices d'inspection, tandis que d'autres sont des portes plus grandes permettant l'accès aux équipements.
- Points d'accès à l'aile : Les ailes abritent des systèmes critiques, notamment les réservoirs de carburant, les actionneurs hydrauliques des gouvernes (ailerons, volets, spoilers), le câblage électrique, l'équipement de dégivrage, ainsi que les longerons et les nervures de la structure. Les panneaux d'accès situés sur les surfaces supérieures et inférieures des ailes sont essentiels pour la maintenance du système de carburant, les inspections structurelles (en particulier pour la fatigue et la corrosion) et l'entretien des mécanismes des gouvernes. Les panneaux situés près des pylônes moteurs permettent également d'inspecter les points de fixation.
- Empennage (section de queue) Panneaux : Comme les ailes, les stabilisateurs horizontaux et verticaux contiennent des actionneurs de gouvernes (gouvernes de profondeur, gouvernes de direction), des câblages et des composants structuraux nécessitant une inspection et une maintenance périodiques par le biais de panneaux d'accès dédiés.
- Panneaux de la nacelle du moteur et du pylône : Les moteurs doivent être inspectés et entretenus fréquemment. Les panneaux d'accès situés sur les nacelles (capots des moteurs) et les pylônes (structures fixant les moteurs à l'aile ou au fuselage) permettent aux techniciens d'examiner les composants des moteurs, les groupes auxiliaires de puissance (APU), les systèmes de purge d'air, les systèmes de détection/suppression d'incendie et les supports structuraux. Ces panneaux sont souvent soumis à des températures et des vibrations élevées, ce qui exige une conception et des matériaux robustes.
- Baies du train d'atterrissage : Les compartiments abritant le train d'atterrissage en position rentrée contiennent des systèmes hydrauliques complexes, des mécanismes de rétraction et d'extension, des roues, des freins et des éléments structurels. Les panneaux d'accès à l'intérieur de ces baies sont essentiels pour l'entretien et l'inspection de ces composants soumis à de fortes contraintes.
- Baies avioniques : Les zones concentrées, souvent situées à l'avant du fuselage ou sous le cockpit, abritent les équipements électroniques sensibles (ordinateurs de vol, systèmes de navigation, radios de communication). Les panneaux d'accès permettent le dépannage, la mise à jour des logiciels et le remplacement des unités remplaçables en ligne (LRU). Ils nécessitent souvent des conceptions spécifiques pour le blindage contre les interférences électromagnétiques (EMI).
- Points d'entretien des fluides : Les points d'accès plus petits sont souvent dédiés à l'entretien des réservoirs de fluides hydrauliques, des réservoirs d'huile ou d'autres systèmes de fluides.
Types de panneaux d'accès :
Les panneaux d'accès ne sont pas monolithiques ; leur conception varie considérablement en fonction de leur fonction, de leur emplacement, de leur fréquence d'utilisation et de leurs exigences structurelles :
- Panneaux à dégagement rapide : Conçus pour un accès fréquent, ils utilisent souvent des fixations quart de tour (par exemple, des fixations Dzus), des loquets ou des mécanismes à charnière pour une ouverture et une fermeture rapides sans outils importants. Ils sont courants pour les inspections de routine avant le vol ou les zones de maintenance fréquemment accessibles.
- Panneaux vissés : Fixés à l'aide de vis ou de boulons standard, ils sont généralement utilisés dans les zones nécessitant un accès moins fréquent ou lorsqu'une force de serrage plus élevée est nécessaire pour assurer l'intégrité structurelle ou l'étanchéité.
- Panneaux d'accès structurels : Certains panneaux sont conçus pour supporter des charges structurelles importantes en tant qu'éléments de la cellule. Leurs procédures de dépose et de réinstallation sont critiques et leur conception doit répondre à des exigences strictes en matière de résistance et de rigidité. Ce sont des candidats de choix pour l'optimisation par AM.
- Panneaux scellés : Les panneaux donnant accès à des zones pressurisées, à des réservoirs de carburant ou à des zones sensibles du point de vue de l'environnement nécessitent des joints spécialisés (par exemple, des joints toriques, des joints de forme en place) afin d'éviter les fuites. La planéité et l'état de surface du panneau et de la structure environnante sont essentiels.
- Panneaux ventilés/ouverts : Certains panneaux comportent des évents ou des persiennes pour permettre la circulation de l'air, le refroidissement des composants ou l'égalisation de la pression.
Variations entre les types d'aéronefs :
Les exigences spécifiques relatives aux panneaux d'accès diffèrent également en fonction du profil de mission de l'aéronef :
- Avions de ligne : L'accent est mis sur la durabilité, la fiabilité, la facilité d'entretien pour minimiser les délais d'exécution (les situations d'AOG - Aircraft on Ground - sont extrêmement coûteuses) et la conformité avec les réglementations strictes de l'aviation civile (FAA, EASA). Les économies de poids sont cruciales pour l'efficacité énergétique.
- Avions militaires : L'accent est mis sur la robustesse, les capacités de maintenance rapide sur le terrain, les caractéristiques de faible observabilité (furtivité) le cas échéant (nécessitant des formes et des revêtements spécifiques), la résistance aux environnements d'exploitation difficiles (vibrations, charges G, dommages potentiels au combat) et les exigences de protection balistique potentielle pour certains panneaux.
- Aviation générale : La rentabilité et la simplicité sont souvent des facteurs clés, mais la sécurité et la fiabilité restent primordiales.
- UAVs/Drones : Le poids est souvent très important pour l'endurance et la capacité de la charge utile. La miniaturisation et l'intégration des fonctionnalités sont hautement souhaitables.
- Vaisseaux spatiaux/véhicules de lancement : Des conditions environnementales extrêmes (vide, radiations, cycles thermiques), des exigences de fiabilité très élevées et une extrême légèreté sont nécessaires. L'accès pendant le traitement au sol est essentiel, mais les panneaux doivent résister aux contraintes du lancement.
La variété même et la nature critique de ces composants soulignent pourquoi l'optimisation de leur conception et de leur processus de fabrication est si importante. Pour les responsables des achats et les fournisseurs de composants aérospatiaux, il est essentiel de garantir une source fiable de panneaux d'accès conformes et de haute qualité, tant pour les nouvelles lignes de production d'aéronefs que pour les opérations de maintenance et de réparation en cours dans le monde entier. Les limites de la fabrication traditionnelle pour répondre aux besoins combinés de légèreté, de géométries complexes (en particulier pour intégrer des caractéristiques ou se conformer à des surfaces incurvées) et de disponibilité à la demande ouvrent la voie à l'exploration de solutions avancées telles que l'impression 3D de métal.
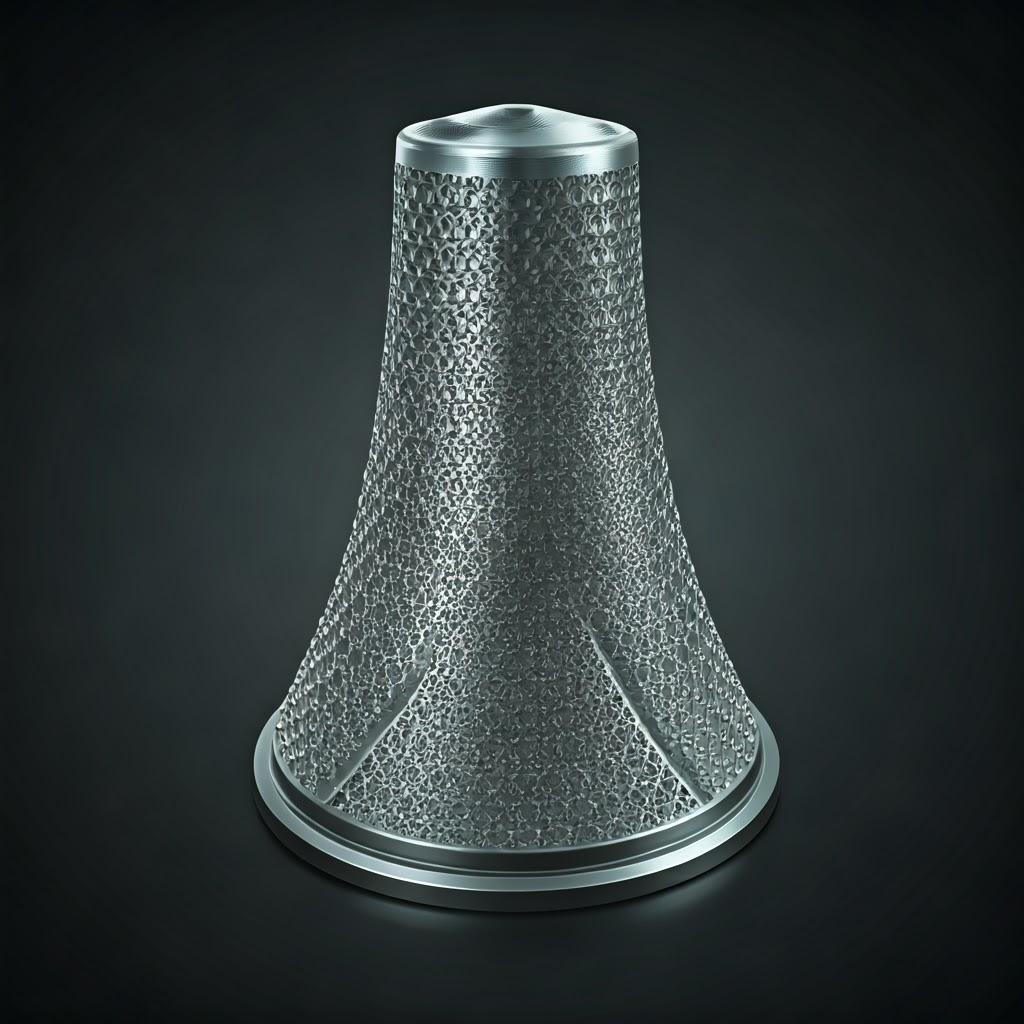
L'avantage additif : Pourquoi utiliser l'impression 3D de métaux pour les panneaux d'accès à l'aérospatiale ?
Si les méthodes de fabrication traditionnelles telles que l'usinage CNC à partir de billettes d'aluminium ou le formage de tôles ont bien servi l'industrie aérospatiale pendant des décennies, elles présentent intrinsèquement des limites que la fabrication additive métallique peut surmonter, offrant des avantages indéniables, en particulier pour les composants tels que les panneaux d'accès. La décision de passer à la fabrication additive est motivée par une combinaison de facteurs visant à améliorer les performances, à réduire les coûts et à rationaliser la chaîne d'approvisionnement. La comparaison de la fabrication additive, en particulier des techniques de fusion sur lit de poudre (PBF) telles que la fusion sélective par laser (SLM) ou la fusion sélective par faisceau d'électrons (SEBM), avec les méthodes conventionnelles révèle pourquoi les fabricants, les concepteurs et les acheteurs en gros de l'aérospatiale adoptent de plus en plus cette technologie.
Comparaison : Fabrication de panneaux d'accès par AM métal contre fabrication traditionnelle
Fonctionnalité | Fabrication additive métallique (PBF) | Traditionnel (usinage CNC) | Traditionnel (Formage de tôles) |
---|---|---|---|
Réduction du poids | Excellent : Permet l'optimisation de la topologie, des structures en treillis, de la conception générative pour des économies de poids significatives (souvent 20-50%+). | Limitée : L'enlèvement de matière est limité par l'accès à l'outil et la forme initiale de la pièce. L'optimisation est moins radicale. | Modéré : Matériau de base léger, mais géométrie limitée par le processus de formage. Optimisation limitée. |
Complexité de la conception | Très élevé : Permet de créer des caractéristiques internes complexes, des formes conformes, des fonctionnalités intégrées (charnières, raidisseurs) impossibles à réaliser autrement. | Modéré : Limité par la géométrie de l'outil, l'axe de déplacement et le besoin potentiel de réglages multiples. Contre-dépouilles difficiles. | Faible : Principalement des formes 2,5D, limitées par les rayons de courbure, la profondeur d'emboutissage et le potentiel de déchirure et de froissement. |
Consolidation partielle | Excellent : Les composants multiples (par exemple, panneau + raidisseurs + supports) peuvent souvent être imprimés comme une seule pièce monolithique. | Pauvre : Nécessite l'assemblage de plusieurs pièces usinées. | Pauvre : Nécessite l'assemblage de pièces formées et d'attaches. |
Utilisation des matériaux | Bon : Utilise la poudre principalement là où c'est nécessaire ; la poudre non utilisée est largement recyclable. Quelques déchets provenant des supports. | Pauvre : Un gaspillage important de matériaux (le ratio achat/vol peut être élevé, par exemple 10:1 ou plus) car les matériaux sont découpés à partir d'un bloc solide. | Bon : Rebut relativement faible si l'imbrication est optimisée, mais des chutes sont tout de même générées. |
Coûts d'outillage | Aucun : La fabrication numérique directe ne nécessite pas d'outillage, de moules ou de matrices spécifiques aux pièces. | Faible-modéré : Nécessite des montages et des outils de coupe. | Haut : Nécessite des matrices, des poinçons et des outils de formage personnalisés et coûteux, en particulier pour les formes complexes. |
Délai d'exécution (Prototype) | Rapide : De quelques jours à quelques semaines, idéal pour l'itération rapide et la validation de la conception. | Modéré : Semaines, en fonction de la complexité et de la disponibilité des machines. | Lent : Mois, en raison de la conception de l'outillage et du temps de fabrication. |
Délai (production) | Modéré : Convient aux volumes faibles à moyens ; la vitesse dépend de la taille/complexité des pièces et du nombre de machines. | Rapide : Bien adapté à la production de gros volumes une fois mis en place. | Rapide : Très efficace pour la production en grand volume de pièces plus simples une fois l'outillage réalisé. |
Aptitude à la personnalisation | Excellent : Chaque impression peut être unique sans changement d'outillage. Idéal pour les variations sur mesure ou en faible volume. | Modéré : Nécessite une reprogrammation et éventuellement de nouveaux appareils. | Pauvre : Nécessite des modifications coûteuses de l'outillage ou de nouveaux outils. |
Exporter vers les feuilles
Principaux avantages élaborés :
- Un allègement sans précédent : Il s'agit sans doute du facteur le plus important pour l'AM dans l'aérospatiale. Les panneaux d'accès, qui doivent être robustes, n'ont souvent pas besoin de l'encombrement inhérent aux pièces usinées à partir d'un stock standard ou des limites géométriques de la tôle.
- Optimisation de la topologie : Des algorithmes logiciels analysent les chemins de charge et les contraintes sur un panneau et enlèvent le matériau des zones non critiques, ce qui permet d'obtenir des structures à l'aspect organique et très efficaces qui répondent aux exigences de performance avec une masse minimale.
- Structures en treillis : L'AM permet d'incorporer des structures internes en treillis (nids d'abeille, mousses stochastiques, gyroïdes) dans le volume du panneau. Ces structures offrent un excellent rapport rigidité/poids et peuvent être adaptées à des conditions de charge spécifiques ou à l'amortissement des vibrations.
- Conception générative : Les ingénieurs définissent les exigences fonctionnelles, les charges et les contraintes, et le logiciel génère de multiples solutions de conception optimisées, trouvant souvent des moyens non intuitifs de réduire le poids tout en atteignant les objectifs de performance.
- Consolidation partielle : Les panneaux d'accès traditionnels sont souvent constitués du panneau lui-même, ainsi que de raidisseurs, de supports, de doublures ou d'éléments de montage séparés qui doivent être fabriqués individuellement puis assemblés (par exemple, par rivetage, collage ou soudage). Cela augmente le nombre de pièces, le temps d'assemblage, le poids (en raison des fixations et des chevauchements) et les points de défaillance potentiels. L'AM des métaux permet aux concepteurs d'intégrer un grand nombre de ces caractéristiques directement dans une seule pièce imprimée monolithique. Cela permet de réduire :
- Coûts de la main-d'œuvre pour l'assemblage
- Complexité de la chaîne d'approvisionnement (moins de pièces à acheter, à suivre et à stocker)
- Poids total
- Points de défaillance potentiels associés aux articulations et aux fixations
- Liberté géométrique : L'AM libère les concepteurs des contraintes imposées par les outils et processus de fabrication traditionnels. Les panneaux d'accès doivent souvent s'adapter aux courbes complexes de la carlingue d'un avion.
- Formes conformes : L'impression permet aux panneaux de s'adapter parfaitement aux surfaces incurvées du fuselage ou des ailes, sans outils de formage coûteux ni installations d'usinage complexes.
- Caractéristiques intégrées : Les charnières, les mécanismes de verrouillage, les fixations imperdables, les canaux de fluides (pour le refroidissement ou l'étanchéité), voire les voies de blindage EMI intégrées, peuvent potentiellement être conçus directement dans la structure du panneau.
- Raidissement complexe : Les nervures et les raidisseurs ne doivent pas nécessairement suivre des lignes droites ou des courbes simples ; ils peuvent avoir une forme organique et être placés exactement là où ils sont nécessaires pour une efficacité maximale.
- Prototypage rapide et itération : Avant de s'engager dans un outillage coûteux (pour le formage) ou de longues séries d'usinage, l'AM permet aux ingénieurs de produire rapidement des prototypes fonctionnels de panneaux d'accès. Ceux-ci peuvent être utilisés pour les contrôles d'ajustement, les essais fonctionnels et la validation de la conception, ce qui permet des itérations et des améliorations rapides de la conception en quelques jours ou semaines, plutôt qu'en quelques mois.
- Élimination de l'outillage : La création de moules ou de matrices pour le formage de la tôle, ou de montages complexes pour l'usinage CNC multi-axes, représente un investissement initial important en termes de coût et de temps. Pour les volumes relativement faibles de nombreux panneaux d'accès spécifiques à l'aérospatiale (en particulier pour certains modèles d'avions ou pièces de rechange), le coût de l'outillage peut être prohibitif. L'AM des métaux est un processus sans outillage ; la complexité est gérée par la machine directement à partir du fichier numérique, ce qui le rend économiquement viable pour la production de volumes faibles à moyens et pour les conceptions hautement personnalisées.
- Fabrication à la demande et MRO : Les avions peuvent avoir une durée de vie de plusieurs dizaines d'années, ce qui nécessite un approvisionnement à long terme en pièces détachées. Le maintien d'importants stocks physiques de panneaux d'accès pour chaque variante de chaque modèle d'avion est coûteux et inefficace. L'AM des métaux permet une approche d'"inventaire numérique". Les dessins des panneaux sont stockés sous forme numérique et les pièces peuvent être imprimées à la demande lorsque les fournisseurs de services de maintenance et de réparation ou les compagnies aériennes en ont besoin. Cela permet de réduire considérablement les coûts d'entreposage, de minimiser les déchets liés aux stocks obsolètes et de raccourcir considérablement les délais de livraison des pièces de rechange essentielles, ce qui permet de remettre les avions en service plus rapidement. Cette capacité transforme la chaîne d'approvisionnement MRO de l'aérospatiale, ce qui profite à la fois aux fournisseurs MRO et aux distributeurs en gros qui les soutiennent.
Bien que l'AM des métaux présente de nombreux avantages, il est essentiel de s'associer à un fournisseur expérimenté tel que Met3dp. Notre expertise en matière d'optimisation des paramètres de processus, de science des matériaux et de post-traitement garantit que les avantages de l'AM - en particulier l'allègement et les géométries complexes - sont pleinement exploités tout en respectant les normes strictes de qualité et de performance de l'industrie aérospatiale. Nous tirons parti des technologies d'impression avancées pour fournir des composants qui redéfinissent ce qui est possible en matière de conception et de fabrication aérospatiales.
Questions de matériaux : Poudres métalliques recommandées pour les panneaux d'accès imprimés en 3D
Le choix du bon matériau est primordial dans l'ingénierie aérospatiale, car il a un impact direct sur les performances, la sécurité et la durée de vie des composants. Pour les panneaux d'accès métalliques imprimés en 3D, le choix de l'alliage de poudre dicte des propriétés cruciales telles que le rapport résistance/poids, la résistance à la fatigue, la résistance à la corrosion, la stabilité thermique et la soudabilité/réparabilité. Bien que divers alliages puissent être traités par fabrication additive, deux alliages à base d'aluminium se distinguent en tant que candidats principaux pour les panneaux d'accès légers de l'aérospatiale en raison de l'excellent équilibre de leurs propriétés et de leur utilisation établie dans l'industrie : AlSi10Mg et Scalmalloy® (alliage d'aluminium).
La compréhension des caractéristiques de ces matériaux est essentielle pour les ingénieurs qui conçoivent les panneaux et pour les responsables des achats qui s'approvisionnent auprès de fournisseurs qualifiés dans le domaine de l'AM des métaux.
1. AlSi10Mg :
- Description : AlSi10Mg est un alliage d'aluminium très répandu contenant du silicium et du magnésium. Il est connu pour sa bonne résistance, ses excellentes propriétés thermiques, sa résistance à la corrosion et, notamment, son excellente aptitude à la transformation dans les systèmes de fusion laser sur lit de poudre (LPBF/SLM). Il s'agit essentiellement d'une composition d'alliage coulé adaptée à la fabrication additive.
- Propriétés clés et pertinence aérospatiale :
- Faible densité : Environ 2,67 g/cm3, ce qui contribue de manière significative aux efforts d'allègement.
- Bonne résistance et dureté (après traitement thermique) : Bien que modéré à l'état brut, l'AlSi10Mg réagit très bien aux traitements thermiques (typiquement T6 : mise en solution et vieillissement artificiel). Après un cycle T6, il peut atteindre des limites d'élasticité d'environ 230-270 MPa et des résistances ultimes à la traction de 330-430 MPa, associées à une bonne dureté. Cette résistance est suffisante pour de nombreux panneaux d'accès semi-structurels ou non structurels.
- Excellente imprimabilité : C'est l'un des alliages d'aluminium les plus faciles à traiter par LPBF, avec des jeux de paramètres bien compris qui permettent d'obtenir des pièces à haute densité (>99,8%) avec une bonne finition de surface (par rapport à d'autres métaux AM). Cette fiabilité est cruciale pour une fabrication cohérente.
- Bonne résistance à la corrosion : Convient aux environnements d'exploitation typiques de l'aérospatiale.
- Conductivité thermique : Possède une bonne conductivité thermique, ce qui peut être bénéfique si le panneau se trouve à proximité de sources de chaleur.
- Considérations :
- Ductilité/fatigue : Comparé aux alliages d'aluminium corroyés ou aux alliages AM spécialisés comme le Scalmalloy®, l'AlSi10Mg présente généralement une ductilité (allongement à la rupture souvent 3-10% post-T6) et une résistance à la fatigue plus faibles. Cela le rend moins adapté aux panneaux soumis à des charges cycliques très élevées ou à des impacts potentiels, à moins qu'il ne soit conçu avec des facteurs de sécurité appropriés.
- Limites de température : Ses propriétés mécaniques ont tendance à se dégrader de manière significative à des températures élevées (supérieures à ~150-200°C), ce qui limite son utilisation dans des zones à haute température telles que les nacelles de moteur sans une gestion thermique minutieuse.
- Applications : Idéal pour les panneaux d'accès statiques ou modérément chargés, les couvercles d'inspection, les supports, les boîtiers et les composants pour lesquels la légèreté et la facilité de fabrication sont des objectifs primordiaux, et les exigences en matière de fatigue ne sont pas extrêmes. Utilisé couramment dans les fuselages, les ailes (structure non primaire) et les boîtiers de systèmes.
2. Scalmalloy® :
- Description : Scalmalloy® est un alliage aluminium-magnésium-scandium haute performance breveté, spécialement conçu pour la fabrication additive par APWORKS GmbH. L'ajout de scandium crée de fins précipités qui améliorent considérablement les propriétés mécaniques de l'alliage par rapport aux alliages Al-Si traditionnels.
- Propriétés clés et pertinence aérospatiale :
- Faible densité : Similaire aux autres alliages d'aluminium (~2,67g/cm3), ce qui maintient l'avantage de la légèreté.
- Rapport force/poids exceptionnel : C'est la caractéristique déterminante du Scalmalloy®. Il offre une limite d'élasticité (jusqu'à 450-500 MPa) et une résistance ultime à la traction (jusqu'à 500-540 MPa) nettement plus élevées que l'AlSi10Mg, approchant la résistance de certains alliages d'aluminium traditionnels à haute résistance de la série 7xxx, mais avec de meilleures caractéristiques de soudabilité inhérentes à l'AM.
- Excellente ductilité et durée de vie à la fatigue : Contrairement à de nombreux alliages d'aluminium à haute résistance, le Scalmalloy® conserve une bonne ductilité (allongement typiquement >12%) et présente une performance en fatigue nettement améliorée par rapport à l'AlSi10Mg. Il convient donc aux composants et structures soumis à des charges dynamiques et nécessitant une tolérance élevée aux dommages.
- Bonne résistance à la corrosion et bonne soudabilité : Offre des performances robustes dans les environnements aérospatiaux typiques.
- Grande robustesse du processus : Conçu pour l'AM, il est généralement bien traité dans les systèmes LPBF, ce qui permet d'obtenir des pièces de haute densité.
- Considérations :
- Coût : Le scandium est un élément d'alliage coûteux, ce qui rend la poudre Scalmalloy® beaucoup plus chère que l'AlSi10Mg.
- Disponibilité : Bien qu'elle soit de plus en plus courante, sa chaîne d'approvisionnement pourrait être moins répandue que celle de l'omniprésent AlSi10Mg. Nécessite des fournisseurs agréés.
- Traitement thermique : Nécessite des cycles de traitement thermique spécifiques optimisés pour l'alliage afin d'atteindre ses propriétés maximales.
- Applications : Convient parfaitement aux applications aérospatiales exigeantes pour lesquelles un rapport résistance/poids maximal, une résistance élevée à la fatigue et l'intégrité structurelle sont essentiels. Il s'agit notamment de panneaux d'accès porteurs, de supports structurels remplaçant des composants usinés, de composants soumis à des vibrations importantes ou à des charges cycliques, et d'applications critiques en termes de performances où le coût plus élevé du matériau est justifié par les gains de performance.
Comparaison des propriétés des matériaux (valeurs typiques après traitement thermique optimisé) :
Propriété | AlSi10Mg (état T6) | Scalmalloy® (condition optimisée) | Unité | Importance pour l'aérospatiale |
---|---|---|---|---|
Densité | ~2.67 | ~2.67 | g/cm³ | Fondamental pour l'allègement |
Limite d'élasticité (Rp0.2) | 230 – 270 | 450 – 500 | MPa | Résistance à la déformation permanente sous charge |
Résistance ultime à la traction (Rm) | 330 – 430 | 500 – 540 | MPa | Contrainte maximale avant rupture |
Allongement à la rupture (A) | 3 – 10 | > 12 | % | Ductilité ; capacité à se déformer avant de se fracturer |
Module d'élasticité (E) | ~70 | ~70 | GPa | Rigidité ; résistance à la déformation élastique |
Résistance à la fatigue | Modéré | Haut | (variable) | Résistance à la rupture sous charge cyclique |
Température de service maximale | ~150 – 200 | ~200 – 250 | °C | Limite de température pour la conservation des propriétés mécaniques |
Imprimabilité (LPBF) | Excellent | Très bon | – | Facilité et fiabilité du processus d'AM |
Coût relatif | Plus bas | Plus élevé | – | Coût de l'approvisionnement en matériaux |
Exporter vers les feuilles
Le rôle de Met3dp dans l'excellence matérielle :
Le choix du bon alliage n'est qu'une partie de l'équation. La qualité de la poudre métallique elle-même est essentielle pour obtenir les propriétés mécaniques souhaitées et garantir des pièces sans défaut. Met3dp utilise les technologies de pointe en matière d'atomisation de gaz et de procédé d'électrodes rotatives à plasma (PREP) pour produire de l'aluminium. poudres métalliques de haute qualité optimisé pour les processus AM tels que LPBF et SEBM.
- Sphéricité et fluidité élevées : Nos techniques d'atomisation avancées, avec des buses et des flux de gaz uniques, permettent d'obtenir des poudres métalliques à haute sphéricité et d'une excellente fluidité. Cela garantit une stratification uniforme du lit de poudre dans l'imprimante 3D, ce qui est essentiel pour obtenir une densité élevée des pièces et des propriétés matérielles cohérentes.
- Distribution contrôlée de la taille des particules (PSD) : Nous contrôlons soigneusement le PSD pour répondre aux exigences spécifiques des différentes machines et applications AM, en optimisant la densité d'empaquetage et le comportement de fusion.
- Faibles niveaux d'impureté : Un contrôle rigoureux de la qualité minimise les niveaux d'oxygène et d'autres impuretés, qui peuvent avoir un impact négatif sur les propriétés mécaniques et la résistance à la fatigue du composant final.
- Portefeuille de matériaux : Tout en se concentrant sur les alliages tels que TiNi, TiTa, TiAl, CoCrMo, les aciers inoxydables et les superalliages, Met3dp possède la capacité et l'expertise nécessaires pour produire des alliages d'aluminium de qualité aérospatiale tels que AlSi10Mg répondant aux spécifications rigoureuses de l'industrie. Notre équipe travaille en étroite collaboration avec les clients de l'aérospatiale pour s'assurer que la poudre fournie répond aux exigences exactes de leurs applications de panneaux d'accès.
En combinant des capacités avancées de fabrication de poudres avec un équipement d'impression de pointe et une connaissance approfondie des applications, Met3dp permet aux entreprises aérospatiales d'adopter en toute confiance l'AM des métaux pour des composants exigeants tels que les panneaux d'accès légers, en tirant parti des meilleurs matériaux pour une performance et une fiabilité optimales. Le choix entre AlSi10Mg et Scalmalloy® dépend en fin de compte d'une analyse détaillée des exigences structurelles du panneau spécifique, de l'environnement d'exploitation, du spectre de charge de fatigue et des objectifs de coût.
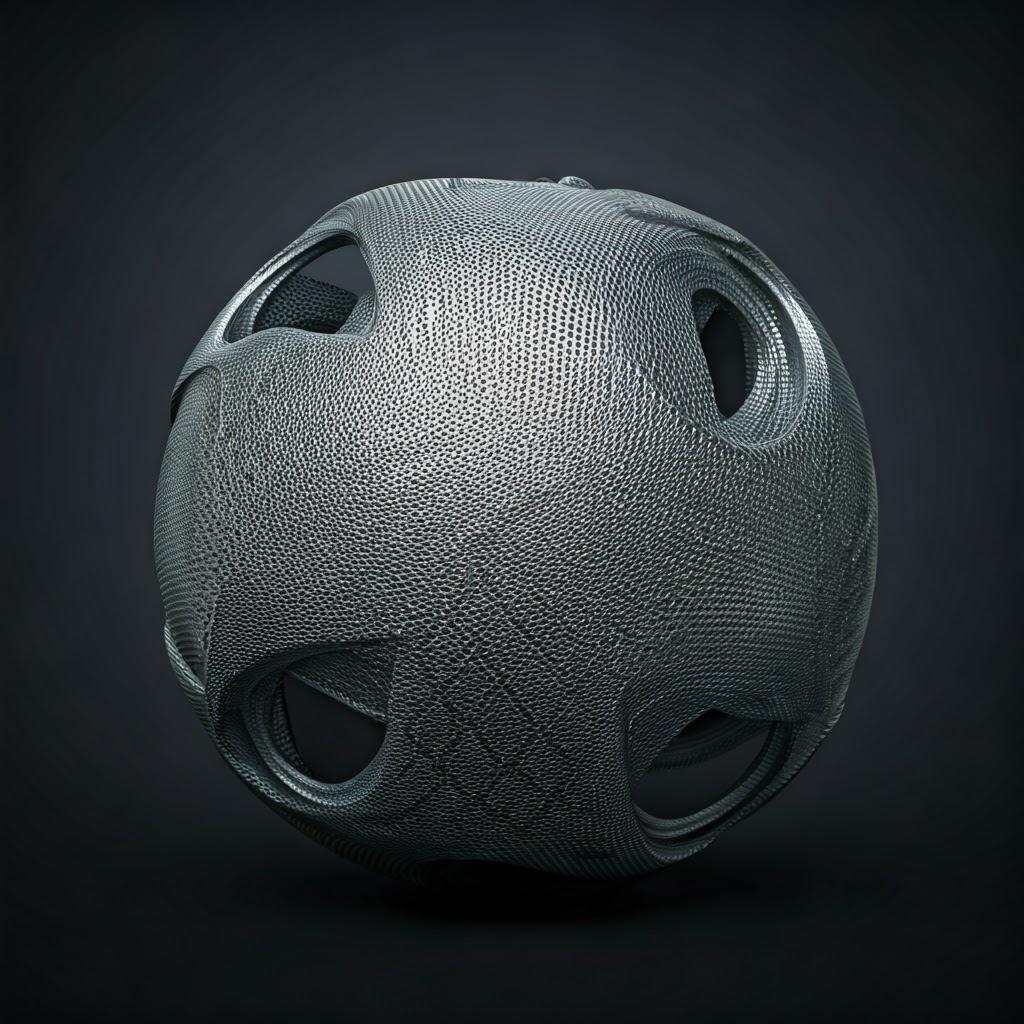
Conception pour la fabrication additive (DfAM) : Optimisation des panneaux d'accès pour l'impression 3D
La simple reproduction d'une conception destinée à la fabrication traditionnelle (comme l'usinage CNC ou le formage de tôle) à l'aide de la fabrication additive permet rarement d'exploiter tout le potentiel de la technologie. Pour véritablement exploiter les avantages de l'impression 3D de métal pour les panneaux d'accès de l'aérospatiale - en particulier pour obtenir un allègement significatif, une intégration fonctionnelle et des améliorations de performance - les ingénieurs doivent adopter les principes suivants Conception pour la fabrication additive (DfAM) principes. La DfAM est une méthodologie qui consiste à concevoir des pièces en tenant compte des capacités et des contraintes du processus d'AM choisi, des matériaux et des étapes de post-traitement. Pour les composants aérospatiaux, cela signifie qu'il faut aller au-delà de la conception conventionnelle et tirer parti de la liberté géométrique unique offerte par la fabrication couche par couche.
L'application de la méthode DfAM aux panels d'accès implique plusieurs stratégies clés :
- Optimisation de la topologie : C'est souvent le point de départ d'un allègement radical.
- Processus : Les ingénieurs définissent l'espace de conception (le volume maximal admissible pour le panneau), spécifient les cas de charge (forces, pressions, vibrations que le panneau subira en service), définissent les contraintes (points de montage, zones d'exclusion, épaisseur minimale) et fixent les objectifs de performance (par exemple, la déflexion maximale admissible, les limites de contrainte). Un logiciel spécialisé élimine ensuite de manière itérative le matériau des zones soumises à de faibles contraintes, laissant derrière lui une structure porteuse optimisée.
- Résultat : Le résultat est souvent une structure organique, semblable à un os, qui répond à toutes les exigences de performance avec le minimum de masse possible. Pour un panneau d'accès, cela peut signifier un matériau solide autour des bords pour l'étanchéité et la fixation, des sections plus épaisses là où les charges sont les plus élevées (par exemple, près des loquets ou des charnières), et une structure hautement optimisée, potentiellement semblable à une toile, dans le corps principal du panneau.
- Bénéfice : Réduit considérablement le poids (souvent 20-50% ou plus par rapport à un panneau plein) tout en garantissant l'intégrité structurelle.
- Structures en treillis et stratégies de remplissage : Là où l'optimisation de la topologie pourrait supprimer de grandes sections de matériau, les structures en treillis peuvent remplacer les volumes solides par des géométries internes légères, mais rigides.
- Les types: Il existe différents types de treillis (nid d'abeille, cubique, treillis octogonal, gyroïde, mousses stochastiques), chacun offrant des propriétés mécaniques différentes (rigidité, absorption d'énergie, conductivité thermique).
- Application : Pour un panneau d'accès, un remplissage en treillis pourrait être utilisé entre les peaux supérieures et inférieures solides pour créer une structure sandwich légère. Cela augmente considérablement la rigidité en flexion du panneau avec une pénalité de poids minimale par rapport à un panneau solide de la même épaisseur. Des densités ou des types de treillis différents pourraient même être utilisés dans différentes régions d'un même panneau en fonction des contraintes locales.
- Bénéfice : Il offre un excellent rapport rigidité/poids, un potentiel d'amortissement des vibrations et peut être intégré de manière transparente dans le processus de fabrication par AM.
- Conception générative : En poussant l'optimisation un peu plus loin, les outils de conception générative permettent aux ingénieurs de saisir des exigences fonctionnelles de haut niveau, des choix de matériaux, des méthodes de fabrication (y compris des contraintes liées à l'AM) et des objectifs de performance. Le logiciel génère et évalue alors de manière autonome des centaines ou des milliers de solutions de conception potentielles, ce qui permet souvent d'obtenir des formes innovantes et non intuitives qui répondent aux critères. Cela peut s'avérer particulièrement utile pour les panneaux d'accès complexes avec de multiples fonctions intégrées ou des conditions de charge difficiles.
- Stratégie de minimisation et d'orientation de la structure de soutien : Les procédés d'AM métal comme la fusion sur lit de poudre (PBF), y compris la PBF au laser (LPBF/SLM) et la PBF par faisceau d'électrons (EBPF/SEBM), nécessitent généralement des structures de support pour ancrer la pièce à la plaque de construction, soutenir les caractéristiques en surplomb et gérer les contraintes thermiques au cours de la construction. Ces supports consomment des matériaux supplémentaires, augmentent le temps de construction et doivent être retirés lors du post-traitement, ce qui augmente les coûts de main-d'œuvre et peut affecter la finition de la surface. Une DfAM efficace vise à réduire au minimum la dépendance à l'égard des supports.
- Angles autoportants : La conception d'éléments avec des angles de surplomb généralement supérieurs à 45 degrés (par rapport à la plaque de construction) permet souvent de les imprimer sans support. Les panneaux d'accès doivent être orientés dans la chambre de construction de manière à maximiser le nombre de surfaces autoportantes.
- Conception de l'article : La modification des porte-à-faux horizontaux aigus pour y inclure des chanfreins ou des congés peut éliminer la nécessité d'utiliser des supports dans ces zones.
- Orientation de la construction : L'orientation du panneau a un impact significatif sur les exigences en matière de support, le temps de construction, la qualité de la surface (en particulier les surfaces orientées vers le bas) et potentiellement les propriétés mécaniques en raison de l'anisotropie. Le choix de l'orientation optimale est une étape critique de la DfAM, qui implique souvent des compromis. Par exemple, l'impression d'un panneau à plat peut minimiser la hauteur de construction (et le temps) mais maximiser les besoins de support pour la face inférieure, alors que l'impression verticale peut réduire le support mais augmenter le temps de construction et potentiellement introduire des problèmes d'anisotropie. Les outils de simulation peuvent aider à prédire le résultat des différentes orientations.
- Soutien intégré : Parfois, les supports peuvent être conçus comme des éléments fonctionnels qui font partie du composant final, éliminant ainsi l'étape du retrait.
- Intégration des fonctionnalités et consolidation des pièces : Comme indiqué précédemment, l'AM permet de combiner plusieurs pièces traditionnellement séparées en un seul composant imprimé. La DfAM pour les panneaux d'accès implique une recherche active de ces opportunités :
- Raidisseurs intégrés : Les nervures et les éléments de raidissement peuvent être conçus directement dans le panneau, se conformant parfaitement aux chemins de charge optimisés, plutôt que d'être des éléments distincts rivetés ou collés.
- Points de fixation intégrés : Les bossages pour les inserts filetés, les brides de montage ou même les caractéristiques qui fonctionnent avec des attaches rapides spécifiques peuvent être incorporés directement.
- Caractéristiques des charnières et des loquets : De simples charnières ou des éléments préliminaires pour les mécanismes de verrouillage peuvent être imprimés dans le cadre du panneau, ce qui réduit la complexité de l'assemblage.
- Rainures d'étanchéité : Les rainures pour les joints toriques ou les joints de forme en place peuvent être imprimées directement dans le bord du panneau avec une grande précision.
- Concevoir pour le post-traitement : Le DfAM doit également prendre en compte les étapes de fabrication en aval.
- Soutenir l'accessibilité : Si les supports sont inévitables, ils doivent être conçus de manière à pouvoir être physiquement atteints et retirés sans endommager la pièce. Les canaux internes nécessitant un support peuvent être particulièrement difficiles à réaliser.
- Tolérances d'usinage : Si certaines surfaces nécessitent une grande précision ou des finitions spécifiques qui ne peuvent être obtenues que par usinage CNC (par exemple, les faces d'étanchéité, les interfaces de montage), un matériau supplémentaire ("stock d'usinage" ou "décalage") doit être ajouté à ces caractéristiques dans le fichier de conception AM afin de permettre l'enlèvement de matière lors de l'usinage.
- Accès à l'inspection : Les caractéristiques doivent être conçues de manière à permettre les inspections nécessaires, qu'elles soient visuelles, dimensionnelles (accès aux sondes CMM) ou non destructives (par exemple, en veillant à ce que les caractéristiques ne créent pas d'angles morts pour les rayons X).
La mise en œuvre réussie de la méthode DfAM requiert non seulement une expertise en matière de principes de conception, mais aussi une compréhension approfondie des spécificités de l'environnement dans lequel elle s'inscrit. méthodes d'impression 3D en métal Le processus de fabrication doit tenir compte des caractéristiques du matériau utilisé, du comportement du matériau choisi et de l'ensemble du processus de bout en bout. En s'associant avec un fournisseur de services AM expérimenté tel que Met3dp peut s'avérer inestimable. Nos équipes d'ingénieurs possèdent des connaissances approfondies en matière d'AMD, spécifiques aux applications aérospatiales et à nos technologies d'impression avancées (y compris LPBF et SEBM). Nous collaborons étroitement avec les équipes de conception de nos clients, en leur offrant des conseils et des analyses pour optimiser la conception des panneaux d'accès afin d'obtenir une légèreté, des performances et une fabricabilité maximales, en veillant à ce que les avantages théoriques de l'AM se traduisent par des résultats tangibles.
La précision définie : Tolérance, finition de surface et précision dimensionnelle dans les panneaux d'accès AM
Alors que la fabrication additive offre une liberté de conception inégalée, les composants produits pour l'industrie aérospatiale doivent respecter des exigences strictes en matière de précision dimensionnelle, de tolérances et d'état de surface. Les panneaux d'accès, en particulier ceux qui font partie de la peau aérodynamique, assurent l'étanchéité ou sont en interface avec d'autres structures et mécanismes de verrouillage, nécessitent un contrôle précis de leur géométrie et de leurs caractéristiques de surface. Pour les ingénieurs concepteurs et les responsables des achats qui évaluent les fournisseurs potentiels, il est essentiel de comprendre les niveaux de précision qu'il est possible d'atteindre avec des procédés d'AM métalliques tels que la fusion sur lit de poudre (PBF).
Précision dimensionnelle et tolérances :
- Tolérances générales : En règle générale, les procédés PBF en métal permettent d'obtenir des précisions dimensionnelles comparables à celles du moulage à la cire perdue. Les tolérances standard réalisables se situent souvent dans la fourchette de la norme ISO 2768-m (moyenne) ou parfois ISO 2768-f (fine) pour les dimensions globales des pièces. Cela se traduit généralement par des tolérances d'environ ±0,1 mm à ±0,3 mm pour les petites pièces (jusqu'à ~100 mm) et potentiellement ±0,5 mm ou plus pour les dimensions plus importantes, en fonction de la géométrie spécifique, du matériau et de l'étalonnage de la machine.
- Facteurs influençant la précision : Plusieurs facteurs contribuent à la précision dimensionnelle finale d'une pièce métallique imprimée :
- Étalonnage de la machine : Il est essentiel de calibrer régulièrement le système de balayage du faisceau laser/électronique de l'imprimante, le mécanisme de recouvrement des poudres et le nivellement de la plate-forme de construction.
- Paramètres du processus : L'épaisseur de la couche, la puissance du faisceau, la vitesse de balayage et l'espacement des trappes ont un impact significatif sur la dynamique du bain de fusion, le retrait et les dimensions finales. L'optimisation des paramètres est essentielle.
- Effets thermiques : Les contraintes résiduelles accumulées au cours des cycles de chauffage et de refroidissement peuvent provoquer des déformations et des distorsions, ce qui affecte la précision, en particulier dans le cas de pièces complexes ou de grande taille. Une gestion thermique efficace (par exemple, le chauffage de la plaque de construction dans le SEBM) et une réduction des contraintes après le traitement sont essentielles.
- Propriétés du matériau : Les différents alliages présentent des taux de retrait et une conductivité thermique variables, ce qui influe sur les dimensions finales.
- Géométrie et orientation des pièces : Les grandes surfaces planes sont plus susceptibles de se déformer que les structures complexes. L'orientation affecte l'historique thermique et l'emplacement des supports, ce qui a un impact sur la précision.
- Stratégie de soutien : Les supports permettent d'ancrer la pièce et d'éviter les déformations, mais leur retrait peut parfois affecter les dimensions ou la qualité de la surface aux points de contact.
- Obtenir des tolérances plus strictes : Pour les caractéristiques critiques telles que les trous de montage, les surfaces d'accouplement ou les rainures d'étanchéité qui nécessitent des tolérances plus serrées que la capacité standard du processus PBF (par exemple, ±0,05 mm ou moins), l'usinage CNC post-processus est généralement utilisé. Le processus DfAM doit en tenir compte en prévoyant un stock d'usinage suffisant sur ces caractéristiques spécifiques dans le modèle 3D.
Finition de la surface (rugosité) :
- Rugosité de la surface telle que construite : L'état de surface des pièces métalliques obtenues par AM est intrinsèquement plus rugueux que les surfaces usinées. Cela est dû au processus couche par couche et aux particules de poudre partiellement fondues qui adhèrent à la surface. Les valeurs typiques de rugosité de surface (Ra) pour les processus PBF sont comprises entre :
- Surfaces orientées vers le haut : Généralement plus lisse, souvent Ra 6-15 µm.
- Parois latérales (surfaces verticales) : Montrer les lignes de la couche, typiquement Ra 10-20 µm. La valeur exacte dépend de l'épaisseur de la couche et de son orientation par rapport à la direction de construction (effet de marche d'escalier sur les surfaces angulaires).
- Surfaces orientées vers le bas (soutenues) : Tendent à être les plus rugueuses, souvent Ra 15-30 µm ou plus, en raison du contact avec des structures de support ou de la poudre partiellement frittée.
- Amélioration de l'état de surface : Pour de nombreux panneaux d'accès, la finition telle qu'elle a été réalisée peut être acceptable, en particulier pour les surfaces internes non critiques. Cependant, pour les surfaces aérodynamiques externes, les surfaces d'étanchéité ou les zones nécessitant une amélioration de la résistance à la fatigue ou de l'esthétique, un post-traitement est nécessaire. Les méthodes les plus courantes sont les suivantes :
- Sablage et grenaillage : Améliore l'uniformité, élimine les poudres non adhérentes, confère une finition mate et peut induire des contraintes de compression bénéfiques pour la durée de vie en fatigue. Il permet d'obtenir des valeurs Ra généralement comprises entre 5 et 10 µm.
- Finition par culbutage et vibration : Utilise un média abrasif dans un tambour rotatif ou vibrant pour lisser les surfaces et ébavurer les arêtes. Efficace pour les lots de petites pièces, il permet d'obtenir un Ra ~1-5 µm.
- Usinage CNC : Permet d'obtenir le meilleur état de surface et la meilleure précision pour des caractéristiques spécifiques, en atteignant facilement un Ra < 1,6 µm ou même moins (finitions miroir avec polissage).
- Polissage (manuel ou automatisé) : Permet d'obtenir des finitions très lisses, semblables à des miroirs (Ra < 0,4 µm), lorsque cela est nécessaire pour des applications spécifiques (par exemple, optique ou écoulement des fluides).
- Spécification : Les exigences en matière de finition de surface doivent être clairement spécifiées sur les dessins techniques en utilisant les notations standard Ra ou Rz pour les différentes surfaces du panneau d'accès.
Métrologie et contrôle de la qualité :
Vérifier que les panneaux d'accès imprimés en 3D répondent aux exigences spécifiées en matière de dimensions et de finition de surface est un élément essentiel du processus d'assurance qualité dans l'aérospatiale.
- Machines à mesurer tridimensionnelles (MMT) : Fournit des mesures ponctuelles de haute précision pour vérifier les dimensions critiques, l'emplacement des trous, la planéité et les repères de dimensionnement et de tolérancement géométriques (GD&T). Nécessite un palpage physique.
- Balayage laser 3D/balayage par lumière structurée : Méthodes sans contact qui capturent des millions de points pour créer une carte numérique en 3D de toute la surface de la pièce. Cela permet de comparer la pièce au modèle CAO d'origine (analyse des écarts), de vérifier la forme générale et les courbures complexes, et d'effectuer des contrôles GD&T. De plus en plus utilisé pour les pièces AM complexes.
- Les testeurs de rugosité de surface (profilomètres) : Instruments à stylet de contact utilisés pour mesurer les valeurs Ra ou Rz sur des surfaces spécifiques.
- Tomodensitométrie (CT) : Il peut être utilisé non seulement pour la détection des défauts internes (voir la section Défis), mais aussi pour l'analyse dimensionnelle, en particulier pour les caractéristiques internes complexes qui sont inaccessibles aux sondes ou aux scanners des MMT.
L'engagement de Met3dp en faveur de la précision :
Au Met3dpNous comprenons que la précision n'est pas négociable dans l'aérospatiale. Notre investissement dans des systèmes d'AM métalliques de pointe, notamment des imprimantes LPBF à haute résolution et des imprimantes SEBM robustes, combiné à un contrôle rigoureux des processus et à des routines d'étalonnage, nous permet de produire des pièces d'une grande précision dimensionnelle et d'une grande homogénéité. Nous travaillons en étroite collaboration avec nos clients pour définir les tolérances et les finitions réalisables, en recommandant des étapes de post-traitement appropriées, telles que l'usinage CNC, lorsque des caractéristiques spécifiques nécessitent une très grande précision. Notre système de gestion de la qualité intègre des techniques de métrologie avancées pour garantir que chaque panneau d'accès livré répond aux spécifications rigoureuses exigées par l'industrie aérospatiale. La collaboration avec un partenaire compétent comme Met3dp garantit que les exigences de précision sont satisfaites de manière efficace et fiable.
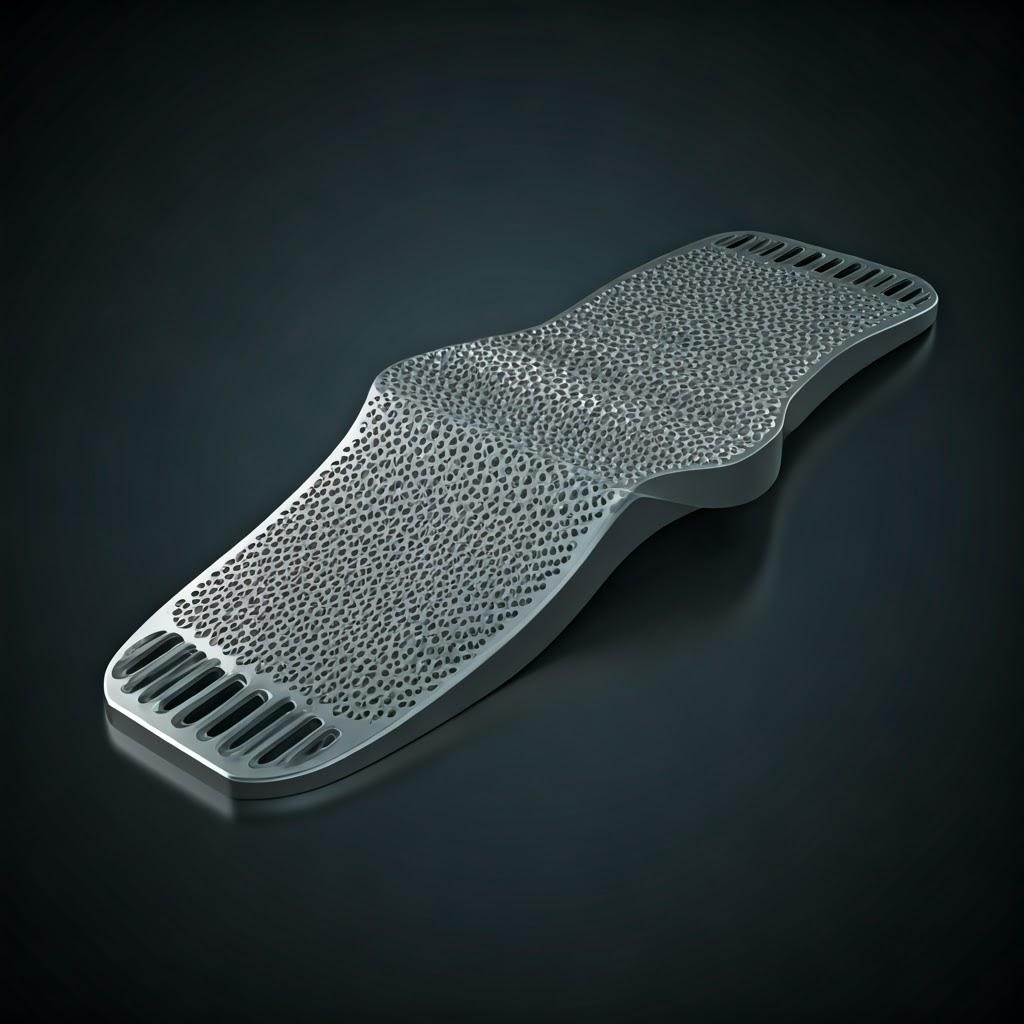
Au-delà de la construction : Exigences de post-traitement pour les panneaux aérospatiaux imprimés en 3D
Le parcours d'un panneau d'accès aérospatial en métal imprimé en 3D ne s'arrête pas lorsque l'imprimante s'arrête. La pièce "telle que construite", fraîchement sortie de la machine, nécessite une série d'étapes essentielles de post-traitement pour la transformer en un composant fonctionnel, prêt pour le vol. Ces étapes sont essentielles pour obtenir les propriétés mécaniques, la précision dimensionnelle, l'état de surface et la qualité globale requises pour les applications aérospatiales. Il est essentiel de comprendre ce flux de travail pour planifier les délais et les coûts de production.
La chaîne de post-traitement typique d'un panneau d'accès en métal AM (en particulier en utilisant le PBF avec des alliages d'aluminium comme AlSi10Mg ou Scalmalloy®) comprend les éléments suivants :
- Traitement thermique antistress (facultatif mais recommandé) :
- Objet : Les cycles de chauffage et de refroidissement rapides inhérents aux procédés PBF créent des contraintes résiduelles importantes dans la pièce imprimée. Ces contraintes peuvent entraîner un gauchissement ou une déformation, en particulier après que la pièce a été retirée de la plaque de construction rigide, et peuvent avoir un impact négatif sur les propriétés mécaniques. La réduction des contraintes consiste à chauffer la pièce (encore attachée à la plaque de construction) à une température modérée (inférieure à la température de vieillissement) pendant une durée déterminée, suivie d'un refroidissement lent.
- Bénéfice : Réduit les contraintes internes, améliore la stabilité dimensionnelle pour les étapes suivantes et minimise le risque de fissuration. Le cycle spécifique dépend de l'alliage et de la géométrie de la pièce.
- Retrait de la pièce de la plaque de construction :
- Méthode : Les pièces sont généralement imprimées sur une plaque métallique épaisse. Elles doivent être soigneusement séparées. Les méthodes les plus courantes sont les suivantes :
- Usinage par électroérosion à fil (EDM) : Offre une coupe précise et de faible force, minimisant les contraintes sur la pièce. Idéal pour les géométries délicates ou complexes.
- Sciage à ruban : Une méthode plus rapide et plus rentable pour les géométries plus simples, mais qui nécessite une manipulation soigneuse pour éviter d'endommager la pièce.
- Considération : La surface où la pièce a été fixée à la plaque (et toute structure de support reliée à la plaque) devra être finie ultérieurement.
- Méthode : Les pièces sont généralement imprimées sur une plaque métallique épaisse. Elles doivent être soigneusement séparées. Les méthodes les plus courantes sont les suivantes :
- Retrait de la structure de soutien :
- Objet : Retirer les structures de support temporaires générées pendant le processus d'impression.
- Méthodes : Il s'agit souvent d'un processus manuel ou semi-automatisé, qui peut impliquer.. :
- Outils à main : Casser les supports accessibles à l'aide de pinces, de cutters ou de meules. Nécessite de l'habileté pour éviter d'endommager la surface de la pièce.
- Usinage (fraisage/meulage) : Utilisé pour les supports plus robustes ou lorsqu'une finition de surface spécifique est requise aux points d'interface du support ("marques témoins").
- EDM : Peut parfois être utilisé pour des supports internes ou difficiles d'accès.
- Défis : Peut nécessiter beaucoup de travail, en particulier pour les treillis ou les éléments internes complexes. Les supports mal conçus peuvent être difficiles, voire impossibles à retirer complètement. Le DfAM joue un rôle clé dans la minimisation et l'optimisation des supports pour faciliter le retrait.
- Recuit de mise en solution et traitement thermique de vieillissement (par exemple, T6 pour les alliages d'aluminium) :
- Objet : Il s'agit d'une étape critique pour développer les propriétés mécaniques finales souhaitées (résistance, dureté, ductilité) des alliages d'aluminium tels que AlSi10Mg et Scalmalloy®.
- Recuit de la solution : Chauffer la pièce à une température élevée (par exemple, ~500-540°C pour les alliages d'aluminium) pour dissoudre les éléments d'alliage en une solution solide.
- Trempe : Refroidissement rapide de la pièce (généralement dans de l'eau ou un polymère) pour piéger les éléments en solution.
- Vieillissement artificiel : Réchauffer la pièce à une température plus basse (par exemple, ~150-180°C) pendant une période prolongée, permettant la précipitation contrôlée des phases de renforcement dans la matrice d'aluminium.
- Contrôle : Il faut des fours contrôlés avec précision, avec un chauffage uniforme et des atmosphères appropriées (par exemple, gaz inerte ou vide) pour éviter l'oxydation. Les paramètres de trempe sont également essentiels pour minimiser les déformations.
- Résultat : Transforme le matériau d'un état relativement mou à un état de haute résistance adapté à l'utilisation aérospatiale. Les cycles T6 spécifiques varient en fonction de l'alliage et de l'équilibre des propriétés souhaité.
- Objet : Il s'agit d'une étape critique pour développer les propriétés mécaniques finales souhaitées (résistance, dureté, ductilité) des alliages d'aluminium tels que AlSi10Mg et Scalmalloy®.
- Usinage (caractéristiques critiques) :
- Objet : Pour obtenir des tolérances serrées, des finitions de surface spécifiques ou des caractéristiques géométriques qui ne peuvent pas être produites avec précision par le seul processus d'AM.
- Applications : Communs pour les surfaces d'étanchéité des panneaux d'accès, les trous de montage nécessitant des diamètres et des emplacements précis, les interfaces avec les loquets ou les charnières, et la garantie de la planéité générale si nécessaire.
- Processus : Il s'agit généralement d'un fraisage ou d'un tournage CNC à 3 ou 5 axes. Nécessite une conception minutieuse de l'outillage pour maintenir la géométrie souvent complexe de la pièce AM en toute sécurité et sans distorsion. Le DfAM garantit qu'il reste suffisamment de matière pour ces opérations.
- Finition de la surface :
- Objet : Pour obtenir la texture de surface souhaitée, éliminer les imperfections mineures, améliorer la résistance à la fatigue ou préparer la surface pour les revêtements ultérieurs.
- Méthodes (détaillées dans la section précédente) :
- Grenaillage de billes / grenaillage de précontrainte
- Tambourinage / Finition vibratoire
- Polissage
- Sélection : La méthode dépend des exigences relatives aux surfaces spécifiques du panneau (par exemple, surface aérodynamique externe par rapport à la surface interne non critique).
- Nettoyage et inspection :
- Objet : Nettoyage approfondi de la pièce pour éliminer les fluides d'usinage, les produits de sablage ou les contaminants. Suivi d'un contrôle dimensionnel final (CMM, scanning) et d'un contrôle non destructif (CND).
- CND pour l'aérospatiale : Elle est essentielle pour garantir l'intégrité interne et détecter les défauts tels que la porosité ou les fissures introduites lors de l'impression ou du post-traitement. Les méthodes les plus courantes sont les suivantes :
- Inspection visuelle (VT) : Contrôle de base des défauts de surface.
- Contrôle par ressuage (LPI/FPI) : Détecte les fissures superficielles.
- Examen radiographique (rayons X) / tomographie assistée par ordinateur (TAO) : Indispensable pour détecter les vides internes, la porosité, les inclusions et vérifier les géométries internes complexes. La tomodensitométrie permet d'obtenir une vue 3D complète des structures internes.
- Contrôle par ultrasons (UT) : Peut détecter des défauts sous la surface.
- Revêtement / Peinture :
- Objet : Pour assurer une protection contre la corrosion, améliorer la résistance à l'usure, répondre à des exigences spécifiques en matière de conductivité de surface ou appliquer les schémas de peinture requis dans l'aérospatiale.
- Revêtements aérospatiaux courants pour l'aluminium :
- Anodisation (par exemple, anodisation à l'acide sulfurique - Type II, anodisation dure - Type III) : Offre une excellente résistance à la corrosion et à l'usure.
- Revêtement de conversion chimique (par exemple, à base d'alodine, de chromate ou de non-chromate) : Offre une résistance à la corrosion et sert d'excellente base d'apprêt.
- Apprêt et couche de finition : Application d'apprêts et de peintures spécialisés pour l'aérospatiale pour la protection finale et la livrée.
La complexité de cette chaîne de post-traitement souligne la nécessité d'une solution de fabrication complète. Il ne suffit pas d'avoir une imprimante 3D. Les fournisseurs de composants aérospatiaux doivent posséder ou avoir des partenariats solides pour le traitement thermique, l'usinage de précision, la finition de surface, les essais non destructifs et les capacités de revêtement, le tout géré dans le cadre d'un système de qualité robuste tel que l'AS9100. Met3dp comprend cet écosystème. Bien que nos principaux atouts résident dans les technologies de pointe, nous n'en sommes pas à notre coup d'essai. Équipement AM et production de poudresDans le cadre de notre programme d'impression 3D, nous proposons des solutions complètes, en gérant l'ensemble du flux de travail, de l'optimisation de la conception à l'inspection finale et à la finition, afin de garantir que les panneaux d'accès imprimés en 3D livrés à nos clients de l'aérospatiale sont prêts à l'intégration.
Relever les défis : Problèmes courants liés à l'impression 3D Panneaux d'accès et solutions
Si la fabrication additive métallique offre un potentiel de transformation pour les panneaux d'accès de l'aérospatiale, elle n'est pas dépourvue de défis techniques. Produire avec succès des composants AM fiables et de haute qualité nécessite une compréhension approfondie de la physique du processus, de la science des matériaux et des pièges potentiels. La connaissance de ces problèmes courants et la mise en œuvre de stratégies d'atténuation efficaces sont essentielles à la fois pour le fournisseur de services de fabrication additive et pour l'utilisateur final.
Défis communs et solutions :
- Déformation et distorsion :
- Enjeu : Les gradients de température importants au cours du processus PBF (fusion et solidification rapides) entraînent l'accumulation de contraintes résiduelles internes. Ces contraintes peuvent entraîner le gauchissement ou la déformation du panneau d'accès, surtout s'il est grand et relativement mince, pendant la construction ou après son retrait de la plaque de construction.
- Les causes : Gradients thermiques élevés, ancrage insuffisant des pièces, stratégies de balayage inappropriées, grandes sections transversales.
- Solutions :
- Simulation de processus : L'utilisation de logiciels de simulation (par exemple, l'analyse par éléments finis - FEA) pour prédire le comportement thermique et l'accumulation de contraintes avant l'impression, ce qui permet d'ajuster l'orientation ou la stratégie de support.
- Structures de soutien optimisées : Des supports stratégiquement placés ancrent efficacement la pièce et aident à dissiper la chaleur.
- Construire des plaques chauffantes (en particulier dans le cadre du SEBM) : Le maintien d'une température élevée dans la chambre de construction réduit les gradients thermiques.
- Stratégies d'analyse optimisées : L'utilisation de schémas de balayage laser/électronique spécifiques (par exemple, balayage d'îlots, schémas en damier) peut contribuer à répartir la chaleur de manière plus homogène et à réduire les contraintes.
- DfAM : Concevoir des pièces avec des caractéristiques qui réduisent intrinsèquement la concentration des contraintes (par exemple, éviter les grands plans plats, utiliser des structures nervurées).
- Traitement thermique anti-stress : Il est essentiel d'effectuer cette étape avant de retirer la pièce de la plaque de construction.
- Gestion du stress résiduel :
- Enjeu : Même si un gauchissement important est évité, des contraintes résiduelles élevées peuvent rester bloquées dans la pièce. Ces contraintes peuvent réduire la durée de vie en fatigue, provoquer des fissures lors du traitement ultérieur (par exemple, l'usinage) ou entraîner une instabilité dimensionnelle à long terme.
- Les causes : Identique à la déformation (gradients thermiques).
- Solutions :
- Soulagement obligatoire du stress : La mise en œuvre d'un cycle de traitement thermique de détente approprié n'est pas négociable pour la plupart des pièces AM de l'aérospatiale.
- Optimisation des paramètres du processus : Les paramètres de réglage fin tels que la puissance du faisceau, la vitesse et l'épaisseur de la couche peuvent influencer l'état de contrainte résiduelle.
- Détente après la construction : Des techniques telles que le grenaillage de précontrainte peuvent introduire des contraintes résiduelles de compression bénéfiques sur la surface, contrebalançant les contraintes de traction préjudiciables.
- Difficultés liées au retrait de l'aide :
- Enjeu : Bien que nécessaires, les structures de support peuvent être difficiles et longues à enlever, en particulier dans le cas de géométries internes complexes (comme les structures en treillis) ou de caractéristiques délicates. Un retrait incorrect peut endommager la surface de la pièce ou laisser des traces indésirables.
- Les causes : Faible DfAM (supports inaccessibles), structures de support trop denses ou trop fortes, canaux internes complexes.
- Solutions :
- Focus DfAM : Concevoir un support minimal, utiliser des angles autoportants et veiller à ce que les supports soient accessibles. Des outils logiciels peuvent aider à créer des supports facilement amovibles (par exemple, des interfaces perforées ou coniques).
- Paramètres de soutien optimisés : Utiliser des structures de support suffisamment denses pour fonctionner, mais optimisées pour faciliter le retrait (par exemple, densité plus faible, couches d'interface spécifiques).
- Techniques avancées de suppression : Utiliser des méthodes telles que l'usinage électrochimique ou l'usinage par flux abrasif pour les supports internes, bien que ces méthodes augmentent les coûts et la complexité.
- Techniciens qualifiés : Demander à des techniciens expérimentés d'effectuer la suppression manuelle avec soin.
- Porosité :
- Enjeu : De petits vides ou pores peuvent se former dans le matériau imprimé. Des niveaux élevés de porosité peuvent dégrader de manière significative les propriétés mécaniques, en particulier la résistance à la fatigue et la résistance à la rupture, ce qui est inacceptable pour les composants aérospatiaux.
- Les causes :
- Porosité du gaz : Argon piégé (dans les IAA) ou gaz atmosphériques si le blindage est inadéquat. Peut également provenir de gaz dissous dans la poudre de départ.
- Porosité de manque de fusion : Apport d'énergie insuffisant entraînant une fusion incomplète entre les couches ou les pistes de balayage adjacentes, ce qui crée des vides de forme irrégulière.
- Porosité du trou de serrure : Densité d'énergie excessive provoquant la vaporisation du métal, ce qui conduit à des bassins de fusion instables et à l'emprisonnement de gaz lors de l'effondrement.
- Questions relatives à la qualité de la poudre : Mauvaise morphologie de la poudre, pores de gaz internes dans les particules de poudre ou contamination.
- Solutions :
- Contrôle strict des paramètres : Développer et contrôler rigoureusement les paramètres validés du processus (puissance, vitesse, épaisseur de la couche, flux de gaz) pour le matériau et la machine spécifiques.
- Poudre de haute qualité : Utilisation de poudres métalliques sphériques de haute pureté avec une distribution granulométrique contrôlée et une faible teneur en gaz interne. Les Les procédés avancés d'atomisation des gaz et de PREP sont conçus pour produire des poudres qui minimisent ces risques.
- Stratégies d'analyse optimisées : Assurer un chevauchement suffisant entre les pistes de balayage et les couches.
- Contrôle de l'atmosphère inerte : Maintien d'un environnement de gaz inerte de haute pureté (argon ou azote dans l'IAA) ou d'un vide poussé (dans le SEBM).
- Essais non destructifs (END) : L'utilisation de la tomodensitométrie ou de l'UT à haute sensibilité pour détecter et quantifier la porosité interne est essentielle pour l'assurance qualité dans l'aérospatiale. Le pressage isostatique à chaud (HIP) peut parfois être utilisé comme post-processus pour fermer les pores internes, mais il ajoute au coût et à la complexité.
- Défauts de surface :
- Enjeu : Imperfections de la surface de la pièce au-delà de la rugosité générale, telles que poudre partiellement frittée, formation de crasses, "escalier" sur les surfaces angulaires, ou marques de témoins provenant des supports.
- Les causes : Instabilités du processus, éclaboussures de poudre, orientation sous-optimale, interactions avec le support.
- Solutions :
- Optimisation des paramètres : Réglage précis des paramètres pour minimiser les éclaboussures et assurer une fusion stable.
- Orientation optimisée : Choisir des orientations de construction qui minimisent les marches d'escalier sur les surfaces critiques.
- Débit de gaz de protection efficace : Pour éliminer les éclaboussures et les fumées de la zone de construction (LPBF).
- Post-traitement : Les techniques de finition de surface (sablage, usinage, polissage) sont souvent nécessaires pour éliminer ou atténuer ces défauts.
- Obstacles à la qualification et à la certification :
- Enjeu : L'industrie aérospatiale est soumise à des normes de qualité et de certification extrêmement strictes (par exemple, AS9100). La qualification d'un nouveau procédé de fabrication tel que l'AM, de matériaux spécifiques, de machines et d'étapes de post-traitement nécessite des efforts, des essais et une documentation considérables pour démontrer la stabilité du procédé, la répétabilité et l'équivalence ou la supériorité des performances de la pièce par rapport aux méthodes traditionnelles.
- Solutions :
- Système de gestion de la qualité (SGQ) robuste : Mise en œuvre et respect de la norme AS9100 ou d'une norme équivalente.
- Validation des processus : Essais rigoureux (caractérisation des matériaux, essais mécaniques, essais non destructifs) pour établir les capacités du processus et créer un ensemble de données statistiquement significatif.
- Traçabilité des matériaux : Maintenir une traçabilité complète des lots de poudre, de la source à la pièce finale en passant par la production.
- Contrôle de la configuration : Contrôle strict des paramètres de la machine, des versions du logiciel et des procédures de post-traitement.
- Partenariat avec des fournisseurs expérimentés : La collaboration avec des fournisseurs de services d'AM tels que Met3dp, qui ont l'expérience des processus de qualification aérospatiale et possèdent les certifications et l'expertise nécessaires, est cruciale pour atténuer les risques et accélérer l'adoption.
Pour relever ces défis avec succès, il faut combiner une technologie de pointe, des connaissances en science des matériaux, un contrôle rigoureux des processus, une assurance qualité complète et un personnel qualifié. En abordant ces problèmes potentiels de manière proactive par le biais d'une conception soignée, d'une simulation, d'une optimisation des processus et d'un partenariat avec des fournisseurs compétents, les avantages significatifs de l'AM des métaux pour les panneaux d'accès de l'aérospatiale peuvent être obtenus de manière fiable.
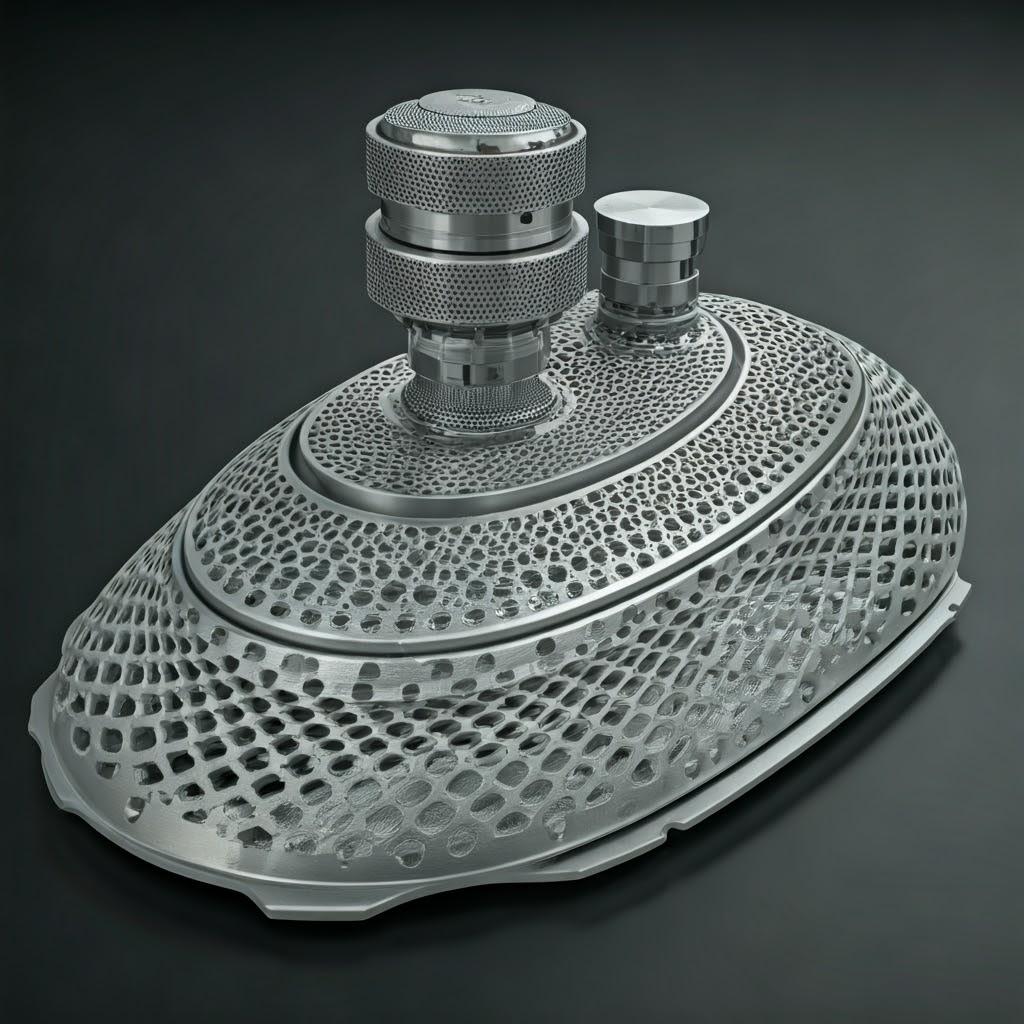
Succès en matière d'approvisionnement : Comment choisir le bon fournisseur de services d'impression 3D de métaux pour les composants aérospatiaux ?
Le choix du bon partenaire de fabrication est toujours critique dans l'industrie aérospatiale, où la qualité, la fiabilité et la traçabilité sont primordiales. Lors de l'approvisionnement en composants métalliques imprimés en 3D, tels que les panneaux d'accès, le choix d'un fournisseur de services de fabrication additive (AM) compétent et certifié est sans doute encore plus crucial en raison de la nouveauté relative de la technologie et de l'expertise spécialisée requise. Un mauvais choix peut entraîner des retards dans les projets, des dépassements de coûts, une qualité médiocre des composants et des risques potentiels pour la navigabilité. Les responsables des achats et les équipes d'ingénieurs doivent faire preuve d'une grande diligence et évaluer les fournisseurs potentiels en fonction d'un ensemble de critères rigoureux adaptés aux exigences de l'aérospatiale.
Critères clés pour l'évaluation des fournisseurs d'AM métal pour les panneaux d'accès dans l'aérospatiale :
- Certification aérospatiale (AS9100) :
- Exigence : Ce point n'est pas négociable. Les fournisseurs potentiels DOIVENT être en possession d'une certification AS9100 (ou équivalente, comme EN9100). Cette norme internationalement reconnue s'appuie sur la norme ISO 9001 mais comprend des exigences spécifiques pour les systèmes de gestion de la qualité dans les secteurs de l'aviation, de l'espace et de la défense.
- Importance : La norme AS9100 démontre l'engagement d'un fournisseur en faveur d'un contrôle rigoureux de la qualité, de la gestion des processus, de la traçabilité, de la gestion des risques et de l'amélioration continue, autant d'éléments essentiels à la production de composants aptes au vol. La vérification de la validité et de la portée du certificat est cruciale.
- Expérience et antécédents démontrés dans le domaine de l'aérospatiale :
- Exigence : Ne vous contentez pas du certificat. Le fournisseur a-t-il une expérience avérée de la production de composants, notamment par AM métallique, pour d'autres clients de l'aérospatiale ? Peut-il fournir des études de cas ou des références pertinentes (dans le respect des limites de confidentialité) ?
- Importance : L'expérience indique une bonne connaissance des attentes en matière de performances aérospatiales, des exigences en matière de documentation (par exemple, les rapports d'inspection du premier article - FAIR), des spécifications des matériaux (normes AMS) et de la culture générale de l'industrie en matière de précision et de sécurité. Une expérience spécifique des panneaux d'accès ou de composants structurels/semi-structurels similaires est un atout.
- Capacités et technologies des machines :
- Exigence : Le fournisseur possède-t-il la technologie AM appropriée (par exemple, fusion laser sur lit de poudre - LPBF/SLM, fusion sur lit de poudre par faisceau d'électrons - EBPF/SEBM) adaptée au matériau choisi (AlSi10Mg, Scalmalloy®) et aux exigences de la pièce ? Évaluez leur parc de machines : modèles spécifiques, dimensions de l'enveloppe de fabrication (peuvent-elles s'adapter aux dimensions de vos panneaux ?), état de la machine, programmes de maintenance et capacités de surveillance du processus (par exemple, surveillance du bain de fusion).
- Importance : Les différentes machines ont des atouts différents. Le SEBM, par exemple, fonctionne à des températures plus élevées, ce qui peut réduire les contraintes résiduelles pour certains alliages, mais les caractéristiques de l'état de surface peuvent être différentes de celles du LPBF. Assurez-vous que leur technologie correspond à vos besoins en matière de précision, d'état de surface et de choix des matériaux.
- Expertise et manipulation des matériaux :
- Exigence : Une connaissance approfondie des matériaux spécifiés (AlSi10Mg, Scalmalloy®) est essentielle. Comment s'approvisionnent-ils en poudres métalliques, comment les testent-ils, comment les manipulent-ils, comment les stockent-ils et comment les recyclent-ils ? Disposent-ils de procédures solides pour prévenir la contamination croisée entre les différents alliages ? Peut-il fournir des certifications de matériaux et démontrer la traçabilité de chaque lot de poudre utilisé ? Ont-ils l'expérience des cycles de traitement thermique requis pour ces alliages spécifiques ?
- Importance : Les propriétés des matériaux sont intrinsèquement liées à la qualité de la poudre et aux procédures de manipulation. Un mauvais stockage (par exemple, absorption d'humidité), une contamination ou une réutilisation incorrecte peuvent compromettre l'intégrité de la pièce finale. L'expertise en matière de traitement thermique après impression est essentielle pour obtenir les propriétés mécaniques spécifiées.
- Système de gestion de la qualité (SGQ) robuste :
- Exigence : Au-delà de la norme AS9100, examinez les procédures spécifiques de leur système de gestion de la qualité. Comment gère-t-elle le contrôle des processus (validation des paramètres, surveillance) ? Quelles sont leurs procédures de gestion des non-conformités, d'actions correctives et de documentation ? Comment assure-t-elle la répétabilité d'une fabrication à l'autre ?
- Importance : Un système de gestion de la qualité solide garantit que les pièces seront produites de manière cohérente et conforme aux spécifications, à chaque fois. Cela inclut le contrôle de la configuration des fichiers numériques, des paramètres de processus et des réglages des machines.
- Soutien technique (DfAM & Simulation) :
- Exigence : Le fournisseur offre-t-il une assistance technique, en particulier une expertise en matière de conception pour la fabrication additive (DfAM) ? Peut-il aider à optimiser la conception du panneau d'accès en termes d'allègement, de minimisation du support et de fabricabilité ? Utilise-t-il des outils de simulation de processus pour prévoir et atténuer les problèmes potentiels tels que la distorsion ?
- Importance : Un fournisseur agissant comme un véritable partenaire peut apporter une valeur ajoutée significative en aidant à affiner les conceptions pour l'AM, ce qui peut conduire à de meilleures performances, à des coûts plus bas et à une production plus rapide. Cette approche collaborative est souvent essentielle pour maximiser les avantages de l'AM.
- Capacités de post-traitement internes ou en partenariat :
- Exigence : Évaluez leurs capacités pour l'ensemble du flux de travail nécessaire : détente, enlèvement des pièces/supports, traitement thermique (avec des fours calibrés de qualité aérospatiale), usinage CNC, finition de surface, contrôle non destructif et revêtement. Ces opérations sont-elles effectuées en interne ou gérées par des sous-traitants qualifiés ? En cas de sous-traitance, comment le fournisseur gère-t-il la qualité et la traçabilité tout au long de la chaîne d'approvisionnement ?
- Importance : Les capacités internes permettent souvent de mieux contrôler les délais et l'intégration de la qualité. Toutefois, des partenariats bien gérés peuvent également s'avérer efficaces. Il est essentiel de comprendre l'ensemble du flux de travail et de savoir qui exécute chaque étape.
- Ressources en matière d'inspection et d'essais non destructifs (END) :
- Exigence : Possèdent-ils l'équipement métrologique nécessaire (MMT, scanners 3D, profilomètres de surface) et le personnel CND qualifié (par exemple, inspecteurs certifiés de niveau II/III) pour les méthodes applicables à l'AM (en particulier la tomodensitométrie pour les défauts internes, le FPI pour les fissures superficielles) ?
- Importance : Une inspection et des essais non destructifs appropriés ne sont pas négociables pour valider la qualité des pièces et garantir la conformité aux normes aérospatiales.
- Capacité, évolutivité et fiabilité des délais :
- Exigence : Le fournisseur peut-il prendre en charge les volumes de production requis (prototypes, production initiale à faible cadence, production en série) ? Dispose-t-il d'une capacité de production suffisante et d'une main-d'œuvre disponible ? Quels sont ses antécédents en matière de respect des délais de livraison ?
- Importance : Cela leur permet de respecter les délais de votre projet et d'augmenter éventuellement la production si nécessaire. La fiabilité des délais de livraison est essentielle pour la planification des projets.
- Communication et gestion de projet :
- Exigence : Quel est le degré de réactivité et de transparence du fournisseur ? Fournit-il des canaux de communication clairs et un support de gestion de projet dédié ?
- Importance : Une bonne communication est essentielle pour résoudre les questions techniques, gérer les changements et assurer le bon déroulement du projet, de la commande à la livraison.
Met3dp, votre partenaire pour la gestion de l'aérospatiale :
Met3dp est stratégiquement positionné pour répondre à ces critères exigeants. En tant que fournisseur de premier plan de solutions de fabrication additive, nous sommes en mesure de fournir des informations plus détaillées sur l'utilisation de la technologie de fabrication additive. à propos de nousnous offrons :
- Technologie avancée : Imprimantes SEBM et LPBF à la pointe de l'industrie, capables de traiter des alliages aérospatiaux tels que l'AlSi10Mg avec une grande précision et une grande fiabilité.
- Excellence matérielle : Production en interne de poudres métalliques sphériques de haute qualité à l'aide de technologies avancées d'atomisation de gaz et de PREP, garantissant une charge d'alimentation optimale pour les applications exigeantes. La manipulation rigoureuse des poudres et les protocoles de traçabilité sont des pratiques courantes.
- Des solutions globales : Tout en nous spécialisant dans les équipements et les poudres, nous nous associons à nos clients pour leur fournir des solutions de bout en bout, y compris l'assistance DfAM, l'optimisation des processus et la coordination des étapes nécessaires de post-traitement et d'assurance qualité par le biais d'un réseau de partenaires qualifiés, le cas échéant.
- Pleins feux sur l'aérospatiale : Des décennies d'expertise collective dans le domaine de l'AM des métaux appliquées à des secteurs difficiles, notamment l'aérospatiale, nous permettent de comprendre et de répondre aux besoins spécifiques de l'industrie en matière de qualité, de performance et de documentation.
- Approche collaborative : Nous travaillons en étroite collaboration avec les équipes d'ingénierie et d'approvisionnement de nos clients afin de garantir la réussite de la mise en œuvre de la technologie AM, en optimisant les conceptions et les processus pour obtenir les meilleurs résultats possibles.
Choisir le bon fournisseur est une décision stratégique. En évaluant soigneusement les partenaires potentiels en fonction de ces critères, les entreprises aérospatiales peuvent en toute confiance tirer parti de l'impression 3D métallique pour produire des panneaux d'accès innovants, légers et très performants, et s'assurer un avantage concurrentiel dans un secteur de la fabrication en évolution rapide.
Comprendre l'investissement : Facteurs de coût et délais d'exécution pour les panneaux d'accès imprimés en 3D
Si les avantages techniques de l'impression 3D de métaux pour les panneaux d'accès de l'aérospatiale sont convaincants, il est essentiel de comprendre les coûts et les délais de production associés pour établir le budget du projet, prendre des décisions d'achat et justifier l'ensemble de l'analyse de rentabilité. Les coûts et les délais sont influencés par une interaction complexe de facteurs liés à la conception de la pièce, au choix du matériau, aux spécificités du processus, au niveau de qualité requis et au volume de la commande.
Principaux facteurs de coûts pour les panneaux d'accès métalliques imprimés en 3D :
- Coût des matériaux :
- Type de poudre : Le coût de base de la poudre métallique influe considérablement sur le prix. Les alliages à haute performance comme le Scalmalloy® sont nettement plus chers que l'AlSi10Mg standard en raison du coût des éléments d'alliage comme le Scandium.
- Volume de la pièce et volume du support : La quantité totale de poudre consommée est directement liée au volume de la pièce finale plus le volume des structures de support nécessaires. Une DfAM efficace qui minimise le volume de la pièce (par l'optimisation de la topologie, les treillis) et les structures de support réduit directement le coût des matériaux.
- Taux de recyclage/rafraîchissement de la poudre : Bien que la poudre inutilisée soit largement recyclable, il est généralement nécessaire de la mélanger à de la poudre vierge (rafraîchissement) pour maintenir des propriétés optimales sur plusieurs constructions, ce qui ajoute un petit coût indirect.
- Temps machine (temps de construction) :
- Préparation de la construction : Temps nécessaire au chargement du fichier numérique, au réglage des paramètres de construction, à la préparation de la plate-forme de construction et au chargement de la poudre.
- Temps d'impression : C'est souvent le facteur qui contribue le plus au coût de la machine. Il est principalement dû à la hauteur de la construction (nombre de couches) et le volume la quantité de matériau fritté/fondu dans chaque couche (liée à la surface de la section transversale et à la vitesse de balayage). Les géométries complexes avec des caractéristiques compliquées ou des structures de support étendues peuvent augmenter le temps de balayage par couche.
- Temps de refroidissement : Temps nécessaire pour que la chambre de construction et les pièces refroidissent suffisamment avant d'être retirées, ce qui est particulièrement important pour des processus tels que le SEBM fonctionnant à des températures élevées.
- Machine Taux horaire : Les prestataires de services tiennent compte de l'amortissement des machines, de la maintenance, de la consommation d'énergie, des frais généraux et des licences logicielles dans un taux d'exploitation horaire pour leur équipement AM.
- Coûts de main-d'œuvre :
- Technicien Temps : Une main-d'œuvre qualifiée est nécessaire pour l'installation et le fonctionnement des machines, la surveillance, la manipulation des poudres, l'enlèvement des pièces, l'enlèvement des supports, la finition des surfaces, l'inspection et l'emballage. L'enlèvement du support, en particulier, peut nécessiter beaucoup de travail pour les pièces complexes.
- Ingénierie/CAM Temps : Temps consacré par les ingénieurs ou les spécialistes de la FAO à la préparation de la construction, à l'optimisation de l'orientation, à la génération de supports et à la simulation de processus, en particulier pour les conceptions nouvelles ou complexes.
- Coûts de post-traitement :
- Soulagement du stress et traitement par la chaleur : Coûts associés à la durée du four, à la consommation d'énergie et à toute atmosphère contrôlée requise (gaz inerte, vide).
- Usinage : Les coûts dépendent de la complexité des opérations d'usinage requises, du nombre de caractéristiques à usiner, des tolérances requises, du temps de travail de la machine CNC et du temps de programmation/réglage.
- Finition de la surface : Les coûts varient considérablement en fonction de la méthode (le sablage est relativement bon marché, le polissage en plusieurs étapes est coûteux) et de la surface à traiter.
- Revêtement/peinture : Les coûts dépendent du type de revêtement, de la préparation de la surface nécessaire et de la complexité du masquage requis.
- Coûts de l'assurance qualité et de l'inspection :
- Métrologie : Temps et ressources pour les mesures CMM, la numérisation 3D et l'analyse des données.
- NDT : Coûts associés à l'exécution et à l'interprétation des résultats des essais non destructifs (FPI, rayons X, tomodensitométrie). La tomodensitométrie, bien qu'elle fournisse des données internes inestimables, est généralement la méthode de CND la plus coûteuse.
- Documentation : Le temps passé à préparer la documentation requise, telle que les certifications de matériaux, les certificats de conformité et les rapports d'inspection du premier article (FAIR).
- Volume de commande :
- Economies d'échelle : Comme la plupart des processus de fabrication, l'AM bénéficie d'économies d'échelle, mais peut-être différemment de la production de masse traditionnelle. L'impression de plusieurs copies d'un panneau en une seule fois ("imbrication") permet d'utiliser plus efficacement le temps machine et de répartir les coûts de configuration sur un plus grand nombre de pièces. Des volumes de commande globaux plus élevés peuvent permettre d'optimiser le processus et de réduire éventuellement le prix par pièce. Toutefois, les principaux facteurs de coût (matériaux, temps de machine par pièce) restent significatifs.
Facteurs de délai d'exécution :
Le délai d'exécution désigne le temps total écoulé entre la passation d'une commande et la réception des pièces finies. Pour les panneaux d'accès AM en métal, il comprend plusieurs étapes :
- Devis et confirmation de commande : Examen initial du fichier CAO, consultation du DfAM (si nécessaire), calcul des coûts et placement formel de la commande (peut prendre plusieurs jours).
- Ingénierie et préparation de la construction : Vérifications finales de la conception, planification de l'agencement (imbrication de plusieurs pièces), génération de supports, création de fichiers de tranches et programmation des machines (peut prendre de 1 à 5 jours en fonction de la complexité et de la file d'attente).
- Impression : Le temps réel que la pièce passe dans la machine AM. Cela peut aller de quelques heures pour un petit panneau simple à plusieurs jours, voire plus d'une semaine, pour de très grandes pièces complexes ou une plaque complète de composants imbriqués.
- Refroidissement et dépoussiérage : Laisser refroidir la construction et retirer avec précaution les pièces du lit de poudre (généralement des heures à une journée).
- Post-traitement : Ce délai peut représenter une part importante du délai global.
- Soulagement du stress/traitement thermique : 1-3 jours (y compris le temps de chauffage et de refroidissement).
- Retrait de la pièce/du support : De quelques heures à plusieurs jours, en fonction de la complexité.
- Usinage : De quelques jours à quelques semaines, en fonction de la complexité et de la disponibilité des machines.
- Finition/enduction : De quelques jours à quelques semaines, en fonction du processus et des délais de livraison des fournisseurs.
- Assurance qualité et inspection : Effectuer des contrôles dimensionnels et des essais non destructifs (peut prendre de 1 à 5 jours en fonction des besoins).
- Expédition: Temps de transport jusqu'au lieu de résidence du client.
Délais d'exécution typiques :
- Prototypes (1-5 unités) : Souvent de 1 à 4 semaines, en fonction de la complexité et des étapes de post-traitement nécessaires. Les services de prototypage rapide peuvent offrir des délais plus courts pour les pièces plus simples avec un post-traitement minimal.
- Production à faible volume (10-100 unités) : Généralement 4 à 8 semaines, ce qui permet d'optimiser l'imbrication, le post-traitement des lots et les contrôles de qualité approfondis.
- Volumes supérieurs : Les délais d'exécution doivent être soigneusement planifiés et dépendent fortement de la capacité du fournisseur et des exigences spécifiques en matière de pièces et de processus.
Conclusion sur les coûts et les délais :
Bien qu'ayant potentiellement un par partie En comparaison avec les méthodes traditionnelles pour des conceptions très simples ou des volumes extrêmement élevés, l'AM des métaux devient très compétitif en termes de coûts et souvent avantageux pour les panneaux d'accès qui se caractérisent par.. :
- Haute complexité : Là où l'usinage nécessiterait de multiples réglages ou un enlèvement de matière important.
- Potentiel d'allègement important : Lorsque la valeur des économies de poids (efficacité énergétique, performances) l'emporte sur le coût potentiellement plus élevé des composants.
- Consolidation partielle : L'élimination des étapes d'assemblage permet d'économiser beaucoup de main-d'œuvre et de réduire les frais généraux de la chaîne d'approvisionnement.
- Volumes faibles à moyens : Lorsque le coût élevé de l'outillage traditionnel (par exemple, pour le formage) est évité.
- Besoins en matière de prototypage rapide : Lorsque la rapidité est essentielle pour la validation de la conception.
- Pièces détachées à la demande : Lorsque le coût de détention des stocks physiques est élevé.
L'obtention de devis précis de la part de fournisseurs qualifiés comme Met3dp, sur la base de conceptions mûres et d'exigences clairement définies, est le meilleur moyen d'évaluer les coûts et les délais spécifiques de votre projet de panneau d'accès pour l'aérospatiale.
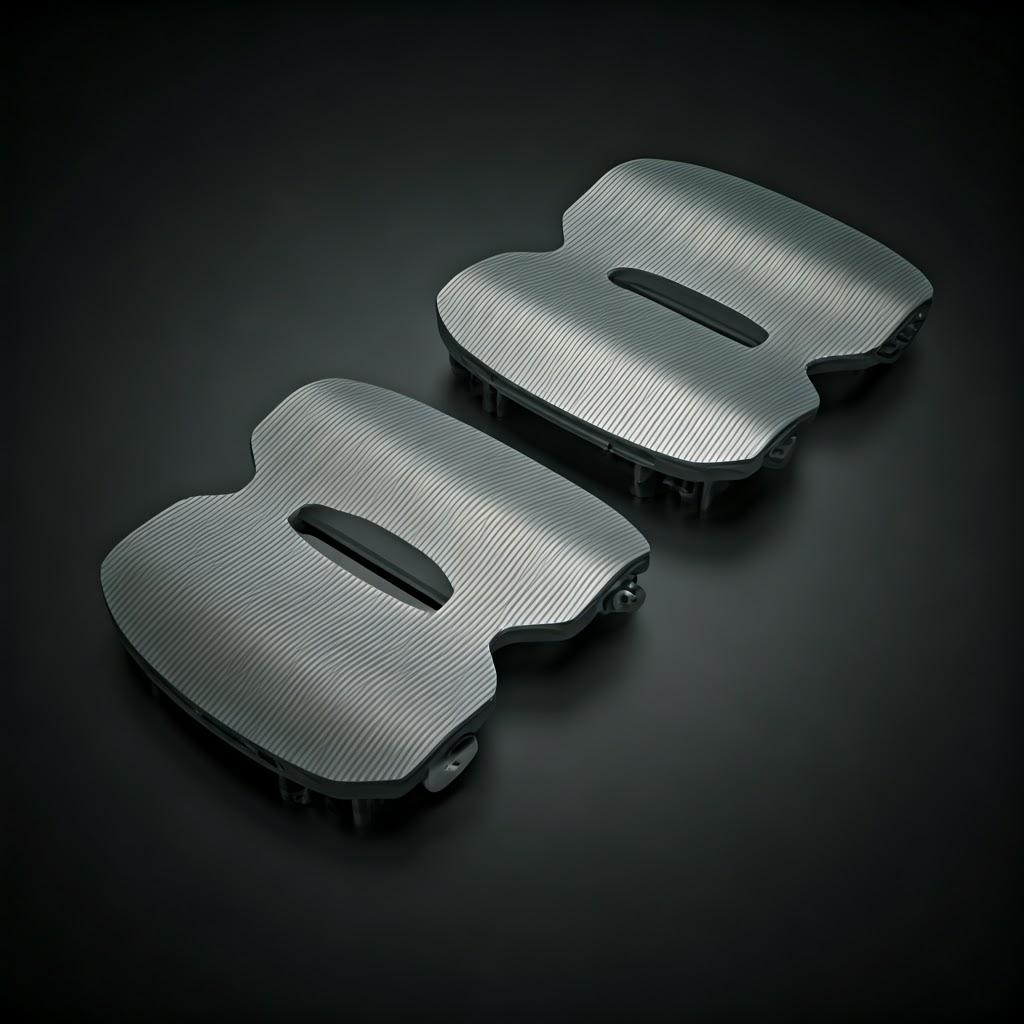
Foire aux questions (FAQ) sur les panneaux d'accès à l'aérospatiale imprimés en 3D
Alors que la fabrication additive métallique est de plus en plus adoptée dans le secteur aérospatial, les ingénieurs, les concepteurs et les professionnels de l'approvisionnement se posent souvent des questions sur son application à des composants tels que les panneaux d'accès. Voici les réponses aux questions les plus fréquentes :
1. Les panneaux d'accès métalliques imprimés en 3D sont-ils aussi solides et fiables que les panneaux usinés ou formés de manière traditionnelle ?
- Répondre: Oui, à condition qu'ils soient conçus, fabriqués et post-traités correctement en utilisant des matériaux appropriés et des processus validés. La clé consiste à obtenir une densité totale du matériau (généralement >99,8%) et à développer la microstructure requise par traitement thermique.
- La force : Avec des alliages comme le Scalmalloy®, les composants imprimés en 3D peuvent atteindre des rapports résistance/poids supérieurs à ceux de nombreux alliages d'aluminium corroyés traditionnels utilisés pour les panneaux d'accès. Pour l'AlSi10Mg, le traitement thermique post-T6 permet d'obtenir des résistances adaptées à de nombreux panneaux modérément chargés, comparables à celles des pièces en aluminium moulé.
- Fatigue : La résistance à la fatigue dépend fortement du choix du matériau, des paramètres du processus (qui influencent la population de défauts comme la porosité), de la finition de la surface (les finitions plus lisses améliorent généralement la résistance à la fatigue) et de l'état des contraintes résiduelles. Le Scalmalloy® offre une résistance à la fatigue nettement supérieure à celle de l'AlSi10Mg. Les post-traitements tels que le grenaillage de précontrainte peuvent encore améliorer la résistance à la fatigue en induisant des contraintes de compression en surface. Un contrôle non destructif minutieux (comme la tomodensitométrie) est essentiel pour s'assurer que la qualité interne répond aux exigences en matière de résistance à la fatigue.
- Fiabilité : La fiabilité découle du contrôle des processus et de l'assurance qualité. Un partenariat avec un fournisseur certifié AS9100 qui utilise des processus validés, des poudres de haute qualité, des contrôles non destructifs rigoureux et une documentation complète garantit que les panneaux imprimés répondent aux normes de fiabilité exigeantes de l'aérospatiale. Lorsqu'elles sont réalisées correctement, les pièces obtenues par AM peuvent être tout aussi fiables, voire plus, que les pièces traditionnelles, en particulier lorsque la consolidation des pièces élimine les points de défaillance potentiels au niveau des joints.
2. Quel est le processus de certification des panneaux d'accès imprimés en 3D pour le vol ?
- Répondre: La certification de toute pièce d'avion, quelle que soit la méthode de fabrication, est un processus rigoureux régi par les autorités aéronautiques (FAA, EASA, etc.). Pour les pièces AM, le processus consiste à démontrer l'équivalence ou la supériorité par rapport aux pièces certifiées existantes ou à qualifier la nouvelle combinaison pièce/processus. Les étapes clés sont généralement les suivantes
- Plan de qualification : Définir le champ d'application, les exigences, les matériaux, les processus de fabrication (y compris les spécificités de la machine AM, les paramètres, le post-traitement), les protocoles d'essai et les critères d'acceptation.
- Caractérisation des matériaux : Essais approfondis du matériau AM choisi (par exemple, AlSi10Mg ou Scalmalloy® traité par la méthode AM spécifique) pour établir des valeurs admissibles de conception statistiquement significatives (par exemple, valeurs de base A ou de base B pour la résistance, la fatigue, etc.) ). Cela implique souvent de tester de nombreux coupons fabriqués dans des conditions variables.
- Spécification du processus : Verrouiller et documenter chaque paramètre critique du processus - de la manipulation des poudres et de la configuration de la machine aux paramètres d'impression (puissance du laser, vitesse, épaisseur de la couche, etc.) et à toutes les étapes de post-traitement (cycles de traitement thermique, configurations d'usinage, procédures de finition).
- Validation des pièces : Fabrication de plusieurs pièces conformes en utilisant la spécification de processus verrouillée et en les soumettant à des essais approfondis, y compris la vérification dimensionnelle, les essais non destructifs, les essais de charge statique, les essais de fatigue et éventuellement les essais environnementaux, afin de prouver qu'elles répondent à toutes les exigences en matière de performance.
- Documentation et audits : Compilation de l'ensemble des données, des rapports (y compris FAIR) et de la documentation relative aux processus en vue de leur examen par l'autorité de certification ou le maître d'œuvre. Les audits de l'installation de fabrication et des processus sont standard.
- Travailler avec des experts : Ce processus est complexe et nécessite un investissement important. La collaboration avec des fournisseurs d'AM expérimentés comme Met3dp, qui comprennent les exigences de qualification aérospatiale, peut rationaliser l'effort.
3. Quel est le coût de l'impression 3D par rapport aux méthodes traditionnelles (usinage CNC, formage de tôle) pour les panneaux d'accès ?
- Répondre: Il n'y a pas de réponse simple ; cela dépend fortement de la complexité, de la taille, du matériau et du volume de la pièce.
- Panneaux simples et à grand volume : Pour les panneaux très simples produits en grandes quantités, le formage traditionnel de la tôle (une fois l'outillage amorti) ou l'usinage CNC à grande vitesse d'un matériau standard resteront probablement moins chers par pièce.
- Panneaux complexes, de volume faible à moyen : L'AM des métaux devient très compétitive en termes de coûts, voire moins chère, lorsque.. :
- La géométrie des panneaux est très complexe (par exemple, topologie optimisée, formes conformes, caractéristiques intégrées), ce qui rend l'usinage difficile et long ou nécessite des outils de formage coûteux.
- L'allègement est important et la valeur du poids économisé pendant la durée de vie de l'aéronef justifie un coût initial plus élevé.
- La consolidation des pièces élimine les multiples pièces traditionnelles et les étapes d'assemblage.
- Les volumes sont faibles à moyens, ce qui permet d'éviter des coûts d'outillage élevés pour le formage.
- Le prototypage rapide ou la production de pièces de rechange à la demande sont nécessaires, en tirant parti de la rapidité de l'AM et de son absence d'outils.
- Point d'équilibre : Le seuil de rentabilité dépend de ces facteurs. Une analyse approfondie des coûts comparant l'AM aux méthodes traditionnelles pour la conception spécifique du panneau d'accès et le scénario de production est nécessaire. N'oubliez pas d'inclure dans la comparaison l'outillage, l'assemblage et les économies de poids potentielles.
4. Quel matériau (AlSi10Mg ou Scalmalloy®) convient le mieux à mon application spécifique de panneau d'accès ?
- Répondre: Le choix dépend des exigences de performance et du budget :
- Choisissez AlSi10Mg si :
- Le panneau est non structurel ou semi-structurel avec des exigences de charge modérées.
- La charge de fatigue n'est pas le principal facteur de conception.
- Les températures de fonctionnement restent inférieures à ~150°C.
- Le rapport coût-efficacité est une priorité majeure.
- Une bonne imprimabilité et des paramètres de processus établis sont souhaités.
- Choisissez Scalmalloy® si :
- Le panneau est structurellement critique ou supporte des charges importantes.
- La résistance à la fatigue et la tolérance aux dommages doivent être élevées.
- Il est essentiel que le rapport résistance/poids soit le plus élevé possible.
- Le coût plus élevé des matériaux est justifié par des gains de performance ou des économies de poids.
- Les températures de fonctionnement peuvent légèrement dépasser celles qui conviennent à AlSi10Mg (jusqu'à ~200-250°C).
- Consultation : Discuter des cas de charge spécifiques, de l'environnement opérationnel et des objectifs de performance avec les experts en matériaux d'un fournisseur d'AM tel que Met3dp peut aider à faire la sélection optimale.
- Choisissez AlSi10Mg si :
5. Quel niveau de détail et de complexité géométrique peut-on atteindre de manière réaliste pour les panneaux d'accès grâce à l'impression 3D de métal ?
- Répondre: L'AM des métaux, en particulier le PBF, offre une très grande liberté géométrique.
- Taille minimale des fonctionnalités : En fonction de la machine et des paramètres, les dimensions minimales des caractéristiques imprimables (par exemple, l'épaisseur de la paroi, le diamètre du trou) sont généralement de l'ordre de 0,4 à 0,8 mm. Les parois minces et non soutenues inférieures à 0,5-1,0 mm peuvent poser des problèmes en raison des contraintes thermiques et de la manipulation.
- La complexité : Des géométries extrêmement complexes, y compris des canaux internes (pour le refroidissement, le câblage ou l'allègement), des structures en treillis complexes, des formes conformes correspondant à des surfaces courbes et des formes hautement optimisées sur le plan topologique, sont facilement réalisables. Des caractéristiques telles que des charnières intégrées, des bossages et des raidisseurs peuvent être construites directement.
- Limites : Les limitations pratiques comprennent la nécessité de structures de soutien pour les surplombs à faible angle (<45 degrés) et la difficulté d'enlever les supports des canaux internes très longs et étroits. La finition des surfaces orientées vers le bas ou soutenues sera plus rugueuse que celle des autres zones, à moins qu'elle ne soit traitée ultérieurement. Les principes de la DfAM sont essentiels pour tirer parti de la complexité tout en garantissant la fabricabilité. En discutant de l'intention de conception avec un expert en AM, il est possible de clarifier ce qui est faisable et la meilleure façon d'obtenir des caractéristiques complexes de manière fiable.
Conclusion : Améliorer les composants aérospatiaux grâce à la fabrication additive avancée
La quête incessante de l'industrie aérospatiale pour des avions plus légers, plus résistants et plus efficaces a trouvé un allié de poids dans la fabrication additive métallique. Comme nous l'avons exploré tout au long de cette discussion, l'application de l'impression 3D de métaux à des composants tels que les panneaux d'accès offre une série d'avantages convaincants qui répondent directement aux principaux défis de l'industrie. Dépassant les contraintes de la fabrication traditionnelle, l'AM ouvre une nouvelle dimension de possibilités de conception, permettant la création de composants optimisés pour la performance et la fabricabilité d'une manière jusqu'alors inimaginable.
Les principales conclusions sont claires : l'impression 3D de métal permet aux ingénieurs aéronautiques de concevoir des panneaux d'accès qui sont nettement plus légers que les panneaux d'origine. plus léger grâce à des techniques sophistiquées telles que l'optimisation topologique et les structures en treillis internes, ce qui contribue directement aux économies de carburant et à l'augmentation de la capacité de charge utile. Il permet des économies de carburant et une augmentation de la capacité de charge utile sans précédent. liberté de conceptionLe système d'information sur la santé permet de créer des formes complexes et conformes, et le système d'information sur la santé permet de créer des formes complexes et conformes. consolidation de plusieurs pièces en un seul composant monolithique, réduisant ainsi le temps d'assemblage, le poids et les points de défaillance potentiels. En outre, les nature sans outil de l'AM rationalise le prototypage, accélère l'itération de la conception et révolutionne la chaîne d'approvisionnement MRO grâce à la production à la demande de pièces détachées, minimisant ainsi les coûts d'inventaire et le temps d'immobilisation des avions.
Toutefois, pour bénéficier de ces avantages, il ne suffit pas d'avoir accès à une imprimante 3D. Le succès dépend d'une approche holistique englobant :
- Dessein intelligent (DfAM) : Repenser la conception des composants pour exploiter spécifiquement les capacités de l'AM tout en tenant compte de ses contraintes.
- Sélection stratégique des matériaux : Choix de la poudre métallique optimale (comme AlSi10Mg ou le Scalmalloy® haute performance) sur la base d'une analyse rigoureuse des exigences de performance et des conditions d'exploitation.
- Post-traitement contrôlé : Mise en œuvre d'étapes essentielles telles que le traitement thermique, l'usinage et la finition pour obtenir les propriétés mécaniques, la précision dimensionnelle et les caractéristiques de surface requises.
- Une assurance qualité rigoureuse : Respecter les normes aérospatiales strictes (AS9100) grâce à un contrôle complet des processus, à la traçabilité des matériaux et à des essais non destructifs.
La complexité de la science des matériaux, de l'optimisation des processus et de la gestion de la qualité nécessite une collaboration avec un partenaire compétent et expérimenté. Le choix d'un fournisseur de services d'AM des métaux est une décision cruciale qui a un impact direct sur la réussite du projet. Les fournisseurs doivent non seulement posséder la technologie et les certifications adéquates, mais aussi une expertise approfondie des applications aérospatiales, des matériaux, de la DfAM et de l'ensemble du processus de fabrication de bout en bout.
Met3dp est prêt à devenir ce partenaire stratégique. En produisant des poudres métalliques spécialisées de haute qualité à l'aide de techniques d'atomisation de pointe et en exploitant des systèmes de fabrication additive à la pointe de l'industrie, nous fournissons les éléments de base nécessaires à la réussite. L'expertise collective de notre équipe en matière de fabrication additive métallique, associée à notre engagement en faveur de la qualité et de la collaboration, nous permet d'aider les entreprises aérospatiales à exploiter efficacement cette technologie transformatrice. Nous travaillons avec vos ingénieurs et vos équipes d'approvisionnement pour optimiser les conceptions, sélectionner les bons matériaux, gérer le processus de fabrication et livrer des composants prêts à voler qui répondent aux normes les plus strictes en matière de performance et de fiabilité.
L'avenir de la fabrication aérospatiale est de plus en plus numérique et additif. L'impression 3D de métaux n'est pas seulement un outil de prototypage ; c'est une technologie de production viable, à valeur ajoutée, capable d'apporter des avantages tangibles à des composants tels que les panneaux d'accès et au-delà. En adoptant l'AM et en s'associant à des fournisseurs compétents, les entreprises aérospatiales peuvent accélérer l'innovation, améliorer les performances des aéronefs et s'assurer un avantage concurrentiel dans le ciel de demain.
Prêt à découvrir comment la fabrication additive métallique peut révolutionner vos composants aérospatiaux ? Contactez Met3dp aujourd'hui pour discuter de vos besoins spécifiques et découvrir comment nos poudres et nos solutions d'impression avancées peuvent contribuer à la réalisation des objectifs de fabrication additive de votre entreprise.
Partager sur
MET3DP Technology Co. est un fournisseur de premier plan de solutions de fabrication additive dont le siège se trouve à Qingdao, en Chine. Notre société est spécialisée dans les équipements d'impression 3D et les poudres métalliques de haute performance pour les applications industrielles.
Articles connexes
À propos de Met3DP
Mise à jour récente
Notre produit
CONTACTEZ-NOUS
Vous avez des questions ? Envoyez-nous un message dès maintenant ! Nous répondrons à votre demande avec toute une équipe dès réception de votre message.
Obtenir les informations de Metal3DP
Brochure du produit
Obtenir les derniers produits et la liste des prix
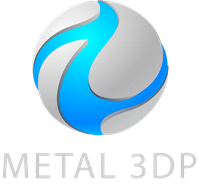
Poudres métalliques pour l'impression 3D et la fabrication additive