Supports de connexion imprimés en 3D pour les ailes d'avion
Table des matières
Introduction : Le rôle critique des supports de connexion des ailettes dans l'aviation moderne
Regardez de près l'extrémité de l'aile de presque tous les avions de ligne ou jets d'affaires modernes et vous verrez probablement une extension angulaire distinctive vers le haut (ou parfois vers le bas et vers le haut) : l'ailette (winglet). Bien qu'apparemment petites par rapport à l'ensemble de l'avion, les winglets jouent un rôle crucial dans l'amélioration de l'efficacité aérodynamique en réduisant la traînée induite par la portance. Cela se traduit directement par des économies de carburant significatives, une autonomie accrue et une réduction des émissions - des objectifs essentiels dans l'industrie aéronautique d'aujourd'hui. Mais comment ces surfaces aérodynamiques vitales sont-elles solidement fixées à la structure de l'aile principale, supportant d'immenses forces aérodynamiques, des vibrations et des fluctuations de température, vol après vol ? La réponse se trouve dans le support de connexion des winglets.
Ces supports sont des héros méconnus de l'ingénierie aérospatiale - des composants structurels critiques conçus pour transférer des charges complexes de manière fiable entre l'ailette et le caisson de l'aile. Ils doivent être exceptionnellement solides, rigides, résistants à la fatigue et, surtout, légers. Chaque kilogramme économisé sur un composant d'aéronef contribue à améliorer les performances et l'économie opérationnelle. Jusqu'à présent, la fabrication de ces composants complexes et porteurs faisait appel à des méthodes traditionnelles telles que l'usinage à partir de blocs de métal solides (souvent du titane ou de l'aluminium à haute résistance) ou le moulage. Toutefois, ces méthodes sont limitées en termes de complexité géométrique, peuvent entraîner un gaspillage important de matériaux (mauvais rapport achat-vol) et impliquent souvent de longs délais pour l'itération de la conception et la production.
C'est là que le changement de paradigme en faveur de la fabrication avancée, et plus particulièrement de l'industrie de l'automobile, se fait sentir. la fabrication additive métallique (AM)ou Impression 3DL'AM est en train d'avoir un impact profond. L'AM des métaux permet de produire des structures légères très complexes, à la topologie optimisée, dont la fabrication était auparavant impossible ou d'un coût prohibitif. Pour des composants tels que les supports de connexion des winglets, cette technologie permet d'atteindre de nouveaux niveaux de performance et d'efficacité. Des entreprises comme Met3dpspécialisée dans les solutions d'impression 3D de métaux industriels, y compris les solutions avancées d'impression 3D de métaux. impression 3D de métaux Les systèmes d'AMC et les poudres de haute performance sont à l'avant-garde de cette transformation, fournissant les outils et les matériaux nécessaires à la réalisation des conceptions aérospatiales de la prochaine génération. Cet article se penche sur les spécificités de l'utilisation de l'AM des métaux pour produire des supports de connexion d'ailettes aérospatiales, en explorant les applications, les avantages, les matériaux, les considérations de conception et les aspects de la chaîne d'approvisionnement pertinents pour les ingénieurs et les responsables de l'approvisionnement dans le secteur de l'aviation.
Comprendre la fonctionnalité des supports de Winglet : Cas d'utilisation et demande de l'industrie
Les supports de connexion des winglets sont bien plus que de simples fixations ; ce sont des éléments structurels sophistiqués conçus pour résister à un environnement opérationnel exigeant. Leur fonction première est de fournir une interface sûre et robuste entre le winglet et la structure primaire de l'aile, en veillant à ce que les charges aérodynamiques générées par le winglet soient efficacement transférées et réparties dans le caisson de l'aile sans compromettre l'intégrité structurelle.
Exigences fonctionnelles clés :
- Transfert de charge : Les supports doivent supporter des charges aérodynamiques importantes (moments de flexion, forces de cisaillement) générées par le winglet, en particulier pendant les manœuvres, les turbulences et les différentes phases de vol.
- Résistance à la fatigue : En raison de la nature cyclique des charges aérodynamiques et des vibrations de l'avion, les supports doivent présenter une résistance à la fatigue exceptionnelle pour répondre aux exigences rigoureuses de sécurité et de longévité de l'aérospatiale (souvent des dizaines de milliers de cycles de vol).
- Rigidité et stabilité : Ils doivent conserver une stabilité dimensionnelle et offrir une rigidité suffisante pour garantir que le winglet reste correctement positionné par rapport à l'aile afin d'obtenir des performances aérodynamiques optimales.
- Résistance à l'environnement : Les supports sont exposés aux variations de température (du sol à la haute altitude), à l'humidité, aux liquides de dégivrage et aux impacts potentiels, ce qui nécessite des matériaux présentant une excellente résistance à la corrosion et à l'environnement.
- Minimisation du poids : Comme pour tous les composants aérospatiaux, il est essentiel de réduire le poids pour maximiser le rendement énergétique et la capacité de charge.
Applications pour tous les types d'aéronefs :
La demande de supports de connexion d'ailettes efficaces s'étend à divers segments de l'industrie aéronautique :
- Avions de ligne : Les gros avions de transport de passagers (Boeing 737 MAX, famille Airbus A320neo, A350, 787) sont largement tributaires d'ailettes avancées pour réduire la consommation de carburant sur les itinéraires moyen et long-courriers. Les supports doivent supporter des charges importantes de manière fiable pendant des décennies. L'approvisionnement de ces composants implique des processus de qualification rigoureux, ce qui permet d'assurer la fiabilité des composants. fournisseurs de composants aérospatiaux cruciale.
- Jets d'affaires : Les performances et l'autonomie sont des arguments de vente essentiels pour les avions d'affaires. Les winglets optimisés y contribuent de manière significative, et leurs supports de connexion doivent répondre à des normes de performance élevées tout en respectant des objectifs de poids stricts. Les constructeurs recherchent souvent des partenaires capables de produire des supports personnalisés et performants.
- Véhicules aériens sans pilote (UAV) : L'efficacité aérodynamique est essentielle, en particulier pour les drones de grande taille et de longue durée utilisés pour la surveillance ou le transport de marchandises. Les supports légers conçus sur mesure grâce à la technologie AM peuvent être avantageux.
- Maintenance, réparation et révision (MRO) : Le secteur de la maintenance, de la réparation et de l'entretien représente une opportunité importante. L'AM peut être utilisée pour produire des supports de remplacement, en intégrant éventuellement des améliorations de conception, parfois dans des délais plus courts que l'approvisionnement en pièces de rechange fabriquées traditionnellement, en particulier pour les modèles d'aéronefs plus anciens. Solutions MRO pour l'aviation les fournisseurs explorent de plus en plus l'AM pour les pièces détachées.
La recherche incessante d'une meilleure efficacité énergétique, motivée à la fois par les pressions économiques (coût du carburant) et les réglementations environnementales (réduction des émissions), garantit une demande élevée et continue pour la technologie avancée des winglets et, par conséquent, pour les supports à haute performance qui les fixent. Achats dans le secteur aérospatial Les équipes de la Commission sont constamment à la recherche de techniques de fabrication innovantes et de produits fiables. fabricants de supports pour avions qui peuvent fournir des composants répondant à ces exigences en constante évolution.
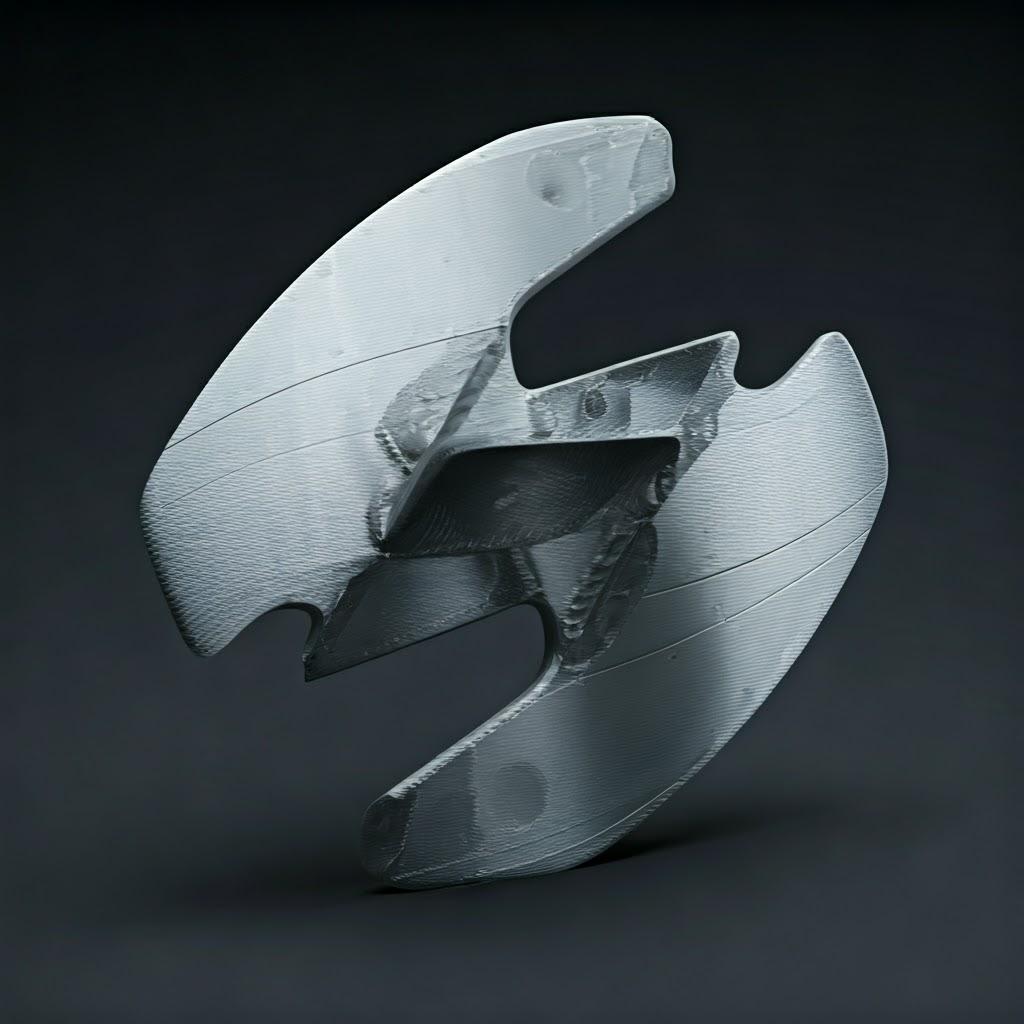
Pourquoi choisir l'impression 3D métal pour les supports de connexion de Winglet ?
Alors que les méthodes de fabrication traditionnelles telles que l'usinage CNC et le moulage à la cire perdue ont bien servi l'industrie aérospatiale pendant des décennies, la fabrication additive métallique offre des avantages indéniables, en particulier pour les composants structurels complexes tels que les supports de connexion des ailettes. Les limites des procédés soustractifs (usinage) et formatifs (moulage) conduisent souvent à des compromis en matière de conception, de poids et de délais que la fabrication additive peut surmonter.
Limites des méthodes traditionnelles :
- Usinage CNC :
- Haute Déchets de matériaux : Il part d'une billette solide d'un matériau coûteux (comme le titane) et en retire de grandes quantités, ce qui conduit à de mauvais ratios "buy-to-fly" (le rapport entre le poids de la matière première achetée et le poids de la pièce finale). Des ratios de 10:1, voire 20:1, ne sont pas rares.
- Contraintes géométriques : Il est difficile et fastidieux de créer des caractéristiques internes complexes, des parois minces ou des formes très organiques. Les limitations d'accès aux outils restreignent les possibilités de conception.
- Temps d'usinage longs : Les pièces complexes nécessitent des réglages multiples et un usinage important, ce qui augmente les délais et les coûts.
- Moulage à la cire perdue :
- Coûts d'outillage et délais d'exécution : Nécessite un investissement initial important et du temps pour créer des moules, ce qui le rend moins adapté à la production de faibles volumes ou au prototypage rapide.
- Défauts potentiels : Susceptibles de présenter des porosités internes ou des incohérences qui peuvent nécessiter une inspection approfondie et des retouches.
- Limites de la conception : Bien qu'il soit meilleur que l'usinage pour certaines formes complexes, le moulage présente encore des limites en ce qui concerne les structures internes complexes ou les caractéristiques très fines.
Avantages de la fabrication additive de métaux (fusion sur lit de poudre - PBF) :
L'AM des métaux, en particulier les processus tels que la fusion laser sur lit de poudre (L-PBF) et la fusion par faisceau d'électrons (EBM), permet de fabriquer des pièces couche par couche directement à partir de poudre métallique, offrant ainsi des avantages transformateurs pour les supports d'ailettes :
- Une réduction de poids sans précédent :
- Optimisation de la topologie : L'AM permet d'utiliser des outils logiciels avancés pour optimiser la géométrie de la pièce en fonction des trajectoires de charge. Le matériau n'est placé que là où il est structurellement nécessaire, ce qui permet d'éliminer la masse inutile tout en maintenant, voire en augmentant, la résistance et la rigidité de la pièce. Cela permet d'améliorer considérablement le rapport entre l'achat et le vol.
- Structures en treillis : L'incorporation de structures internes en treillis ou cellulaires permet de réduire encore le poids de manière significative tout en maintenant l'intégrité structurelle, ce qui est impossible avec les méthodes traditionnelles.
- Consolidation partielle :
- Un support complexe traditionnellement constitué de plusieurs pièces usinées ou moulées, boulonnées ou soudées ensemble, peut souvent être redessiné et imprimé comme un seul composant monolithique. Cela permet de réduire le nombre de pièces, d'éliminer les fixations (points de défaillance potentiels), de simplifier l'assemblage, de réduire le poids et d'améliorer l'intégrité structurelle globale.
- Liberté de conception accrue :
- L'AM élimine de nombreuses contraintes géométriques imposées par la fabrication traditionnelle. Les ingénieurs peuvent concevoir des formes organiques très complexes avec des canaux internes (par exemple, pour le refroidissement ou le câblage), des contours lisses et des caractéristiques parfaitement adaptées à l'application spécifique sans se soucier de l'accès à l'outil ou des angles de dépouille du moule. Cette liberté permet d'atteindre des niveaux de performance plus élevés.
- Réduction des délais d'exécution (prototypage et faible volume) :
- Pour les prototypes initiaux, les itérations de conception et les productions de faible volume, l'AM peut être beaucoup plus rapide que les méthodes traditionnelles qui nécessitent un outillage ou des installations d'usinage importantes. Les modifications de conception peuvent être mises en œuvre et testées rapidement.
- Efficacité matérielle :
- L'AM est un processus additif, qui n'utilise principalement que le matériau nécessaire à la pièce et aux structures de soutien. La poudre non fondue peut souvent être recyclée, ce qui permet une bien meilleure utilisation des matériaux par rapport à l'usinage soustractif.
Pour tirer parti de ces avantages, il faut disposer de l'expertise et de l'équipement adéquat. Met3dp fournit volume d'impression, précision et fiabilité à la pointe de l'industrie avec ses systèmes PBF avancés, ce qui rend possible et efficace la production de composants aérospatiaux essentiels à la mission, tels que les supports d'ailettes. En explorant les possibilités de la L'AM des métaux au service de l'aérospatiale peut conduire à des avantages concurrentiels significatifs dans la conception et la fabrication des avions.
Pleins feux sur les matériaux : Ti-6Al-4V et Scalmalloy® pour des supports haute performance
Le choix du matériau est primordial pour les composants aérospatiaux, en particulier pour les structures porteuses telles que les supports de connexion d'ailettes fonctionnant dans des conditions exigeantes. Les processus de fabrication additive nécessitent des poudres métalliques spécialisées et, pour cette application, deux matériaux se distinguent : L'alliage de titane Ti-6Al-4V et l'alliage d'aluminium haute performance Scalmalloy®. La qualité et la consistance de la poudre ont un impact direct sur les propriétés mécaniques et la fiabilité de la pièce finale.
Importance des poudres métalliques de haute qualité :
Le succès de l'AM des métaux dépend fortement des caractéristiques de la matière première de la poudre métallique. Les principales caractéristiques sont les suivantes
- Sphéricité : Les particules hautement sphériques assurent une bonne fluidité de la poudre et une bonne densité d'empilement dans le lit de poudre, ce qui permet d'obtenir une fusion plus uniforme et des pièces finales plus denses avec moins de vides.
- Distribution de la taille des particules (PSD) : Un PSD contrôlé est crucial pour un comportement de fusion cohérent et pour obtenir la finition de surface et la résolution souhaitées.
- La pureté : De faibles niveaux d'impuretés et de contaminants (comme l'oxygène et l'azote, en particulier pour le titane) sont essentiels pour obtenir des propriétés mécaniques optimales et prévenir les défauts.
- Fluidité : Un flux de poudre constant garantit l'étalement de couches uniformes sur la plate-forme de fabrication, ce qui est essentiel pour la stabilité du processus et la qualité des pièces.
Utilisation de Met3dp des technologies de pointe en matière d'atomisation des gaz et de traitement par électrodes rotatives à plasma (PREP) pour produire des poudres métalliques répondant à ces exigences strictes. Les poudres système avancé de fabrication de poudresGrâce à la conception unique de la buse et du flux de gaz, on obtient des poudres d'une grande sphéricité, d'un PSD contrôlé et d'une excellente fluidité, ce qui les rend idéales pour les applications aérospatiales les plus exigeantes. L'accès à un fournisseur de poudres métalliques pour l'aérospatiale L'utilisation de matériaux comme Met3dp est cruciale pour obtenir des résultats cohérents et de haute qualité. Vous pouvez explorer leur gamme d'alliages innovants et de matériaux standard sur leur site web. page produit.
1. Alliage de titane Ti-6Al-4V (grade 5) :
Le Ti-6Al-4V est sans doute l'alliage de titane le plus utilisé dans l'aérospatiale, et ce pour de bonnes raisons. Il offre une excellente combinaison de propriétés hautement souhaitables pour les composants structurels :
- Rapport résistance/poids élevé : Il offre une résistance comparable à celle de nombreux aciers, mais avec une densité nettement inférieure, ce qui est crucial pour la réduction du poids.
- Excellente résistance à la corrosion : Forme une couche d'oxyde passive stable, offrant une résistance exceptionnelle à la corrosion dans divers environnements aérospatiaux, y compris l'exposition au carburéacteur et aux fluides de dégivrage.
- Bonne résistance à la fatigue : Il se comporte bien dans les conditions de charge cyclique typiques des structures aéronautiques.
- Capacité à haute température : Conserve une bonne résistance à des températures modérément élevées (jusqu'à environ 315°C ou 600°F).
- Biocompatibilité : Bien qu'il ne soit pas pertinent pour les ailettes, sa biocompatibilité le rend également utilisable pour les implants médicaux.
- Base de données établie : Des décennies d'utilisation signifient que ses propriétés et son comportement (y compris dans l'AM) sont bien compris et documentés, ce qui simplifie les processus de certification.
Pour les supports d'ailettes, le Ti-6Al-4V offre la solidité, la résistance à la fatigue et la stabilité environnementale nécessaires dans un ensemble relativement léger. Il s'agit d'un choix courant pour les supports produits à la fois par usinage traditionnel et par fabrication additive.
2. Scalmalloy® :
Scalmalloy® est un alliage aluminium-magnésium-scandium haute performance spécialement développé pour la fabrication additive. Il repousse les limites de ce qui est possible avec les alliages d'aluminium :
- Une force exceptionnelle : Offre une résistance à la traction et une limite d'élasticité nettement plus élevées que les alliages d'aluminium traditionnels pour l'aérospatiale (comme AlSi10Mg), approchant la résistance de certains alliages de titane, mais avec une densité plus faible.
- Excellente ductilité et durée de vie à la fatigue : Contrairement à certains alliages d'aluminium à haute résistance, le Scalmalloy® conserve une bonne ductilité et présente d'excellentes propriétés de fatigue, ce qui le rend adapté aux composants soumis à des charges dynamiques.
- Optimisé pour l'AM : Sa composition est conçue pour une bonne aptitude au traitement par fusion laser sur lit de poudre (L-PBF), ce qui permet de créer des composants complexes et sans fissures.
- Soudabilité : Peut être soudé, ce qui peut être avantageux pour le post-traitement ou l'intégration dans des assemblages plus importants.
- Léger : Comme il s'agit d'un alliage d'aluminium, il offre un potentiel de gain de poids significatif par rapport aux composants en titane ou en acier.
Pour les supports d'ailettes où la minimisation du poids est la priorité absolue tout en exigeant une très grande solidité et résistance à la fatigue, le Scalmalloy® constitue une alternative convaincante au Ti-6Al-4V. Son développement met en évidence le potentiel des matériaux spécifiquement conçus pour exploiter les capacités uniques de la fabrication additive.
Comparaison des propriétés des matériaux (valeurs typiques pour l'AM) :
Propriété | Ti-6Al-4V (sans contrainte et HIP) | Scalmalloy® (traité thermiquement) | Unité | Notes |
---|---|---|---|---|
Densité | ~4.43 | ~2.67 | g/cm³ | Scalmalloy® est nettement plus léger. |
Résistance ultime à la traction | > 930 | > 520 | MPa | Le Ti-6Al-4V est globalement plus résistant. |
Limite d'élasticité (0.2%) | > 860 | > 480 | MPa | Le Ti-6Al-4V a une limite d'élasticité plus élevée. |
Allongement à la rupture | > 10 | > 13 | % | Le Scalmalloy® présente une ductilité légèrement supérieure. |
Module d'élasticité | ~114 | ~70 | GPa | Le Ti-6Al-4V est plus rigide. |
Résistance à la fatigue (R=-1) | ~500 (@ 10⁷ cycles) | ~250 (@ 10⁷ cycles) | MPa | Ti-6Al-4V généralement plus élevé, mais variable. |
Temp. de fonctionnement max. | ~315 | ~150 | °C | Ti-6Al-4V meilleur pour les températures plus élevées. |
Exporter vers les feuilles
Remarque : les propriétés sont approximatives et dépendent fortement des paramètres spécifiques du processus AM, de l'orientation de la construction et du post-traitement (traitement thermique, HIP). Il convient de toujours se référer aux fiches techniques des fournisseurs pour connaître les valeurs spécifiques.
Choix entre Ti-6Al-4V et Scalmalloy® :
Le choix dépend des exigences spécifiques de la conception :
- Choisir Ti-6Al-4V quand : Une résistance maximale, une résistance à des températures plus élevées et l'exploitation des données de qualification aérospatiales existantes sont primordiales.
- Choisir Scalmalloy® (alliage d'aluminium) quand : Le poids minimum absolu est le principal critère, et son rapport résistance/poids exceptionnel (supérieur au Ti-6Al-4V à cet égard) et sa bonne résistance à la fatigue répondent aux exigences opérationnelles.
Ces deux matériaux, lorsqu'ils sont traités à l'aide de poudres de haute qualité provenant de fournisseurs experts tels que Met3dp et fabriqués sur des systèmes AM fiables, permettent de créer des supports de connexion d'ailettes de qualité supérieure qui repoussent les limites de la performance et de l'efficacité des aéronefs.
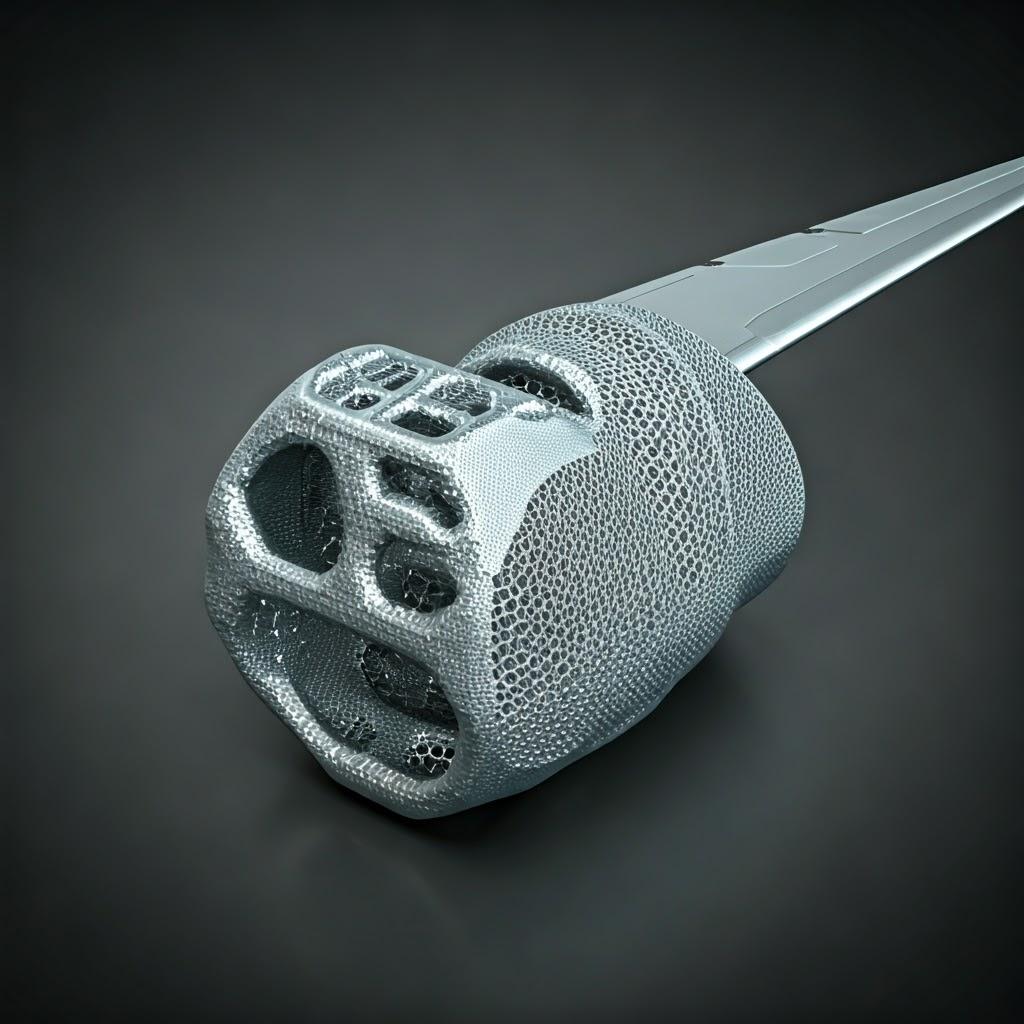
Principes de conception pour la fabrication additive (DfAM) pour une performance optimale des supports
L'un des changements les plus importants à opérer lors de l'adoption de la fabrication additive métallique est la prise en compte de la technologie de fabrication additive. Conception pour la fabrication additive (DfAM). La simple reproduction sur une imprimante 3D d'une conception initialement prévue pour l'usinage CNC ou le moulage aboutira probablement à une pièce sous-optimale qui n'exploitera pas les principaux avantages de l'AM. La DfAM est une méthodologie, un changement d'état d'esprit, qui intègre les capacités et les contraintes du processus de fabrication directement dans la phase de conception afin de maximiser le potentiel de la technologie AM pour des composants tels que les supports de connexion des winglets. L'application des principes de la DfAM est cruciale pour atteindre les objectifs de réduction de poids, d'amélioration des performances et de rentabilité.
Stratégies DfAM clés pour les supports Winglet :
- Optimisation de la topologie : Il s'agit peut-être de la technique DfAM la plus efficace pour les composants structurels. À l'aide de logiciels spécialisés (par exemple, des outils d'optimisation basés sur l'analyse par éléments finis), les ingénieurs définissent l'espace de conception, les cas de charge (forces aérodynamiques, vibrations), les contraintes (points d'attache, zones d'exclusion) et les objectifs de performance (minimiser le poids, maximiser la rigidité). Le logiciel élimine ensuite de manière itérative la matière des zones soumises à de faibles contraintes, ce qui permet d'obtenir des structures très efficaces, souvent d'apparence organique, qui placent la matière précisément là où elle est nécessaire pour supporter la charge. Cela peut conduire à des économies de poids considérables (30-60% ou plus) par rapport aux supports conçus de manière traditionnelle.
- Conception générative : En poussant l'optimisation un peu plus loin, les algorithmes de conception générative explorent simultanément plusieurs possibilités de conception sur la base d'un ensemble défini de règles, de contraintes et d'objectifs. Cela permet de découvrir de nouvelles solutions de conception très performantes qu'un concepteur humain n'aurait peut-être pas imaginées, repoussant ainsi les limites de la légèreté et de la performance.
- Consolidation partielle : Analyser les assemblages de supports existants. Est-il possible de redessiner et d'imprimer plusieurs composants (par exemple, un corps principal, des brides séparées, des fixations) sous la forme d'une seule pièce intégrée ? Cette stratégie DfAM réduit le nombre de pièces, élimine les joints et les fixations (points de défaillance potentiels), simplifie les processus d'assemblage en aval et réduit intrinsèquement le poids.
- Minimisation de la structure de soutien : Les procédés PBF pour le métal nécessitent généralement des structures de support pour les caractéristiques en surplomb (généralement des angles inférieurs à 45° par rapport au plan de construction horizontal) afin d'éviter l'effondrement et d'ancrer la pièce à la plaque de construction. Ces supports consomment des matériaux supplémentaires, allongent le temps d'impression et nécessitent un retrait manuel ou usiné lors du post-traitement, ce qui augmente les coûts et la complexité. Le DfAM se concentre sur :
- Conception d'angles autoportants : Orienter les surfaces et les caractéristiques de manière à dépasser l'angle de surplomb critique chaque fois que cela est possible.
- Optimiser l'orientation de la construction : Sélection de l'orientation d'impression qui minimise naturellement le besoin de supports, en tenant compte d'autres facteurs tels que l'état de surface et les propriétés mécaniques (qui peuvent être anisotropes).
- Utilisation de caractéristiques sacrificielles : Conception d'éléments destinés à être usinés ultérieurement et qui servent également de supports lors de l'impression.
- Structures de treillis internes : Au lieu de sections solides, des structures internes en treillis ou cellulaires (par exemple, des gyroïdes, des nids d'abeille) peuvent être incorporées dans la conception du support. Ces structures réduisent considérablement le poids et la consommation de matériaux tout en offrant un soutien structurel adapté, une absorption d'énergie ou des propriétés d'amortissement des vibrations. Ce niveau de complexité interne est unique à l'AM.
- Règles de conception des fonctionnalités : Tenir compte des limites spécifiques du processus d'AM :
- Épaisseur minimale de la paroi : La conception de parois inférieures à un certain seuil (dépendant du processus et du matériau, souvent autour de 0,4-0,8 mm) peut entraîner des échecs d'impression ou une mauvaise définition des caractéristiques.
- Orientation du trou : Les trous horizontaux nécessitent souvent des structures de soutien ou peuvent être imprimés avec de légers écarts par rapport à une circularité parfaite, contrairement aux trous verticaux. La conception de formes en losange ou en goutte d'eau pour les trous horizontaux peut les rendre autoportants.
- Gestion thermique : Prendre en compte la dissipation de la chaleur pendant le processus de construction afin de minimiser les contraintes résiduelles et le gauchissement potentiel, en particulier pour les sections larges ou denses.
Le rôle de la simulation : La DfAM est fortement tributaire des outils de simulation. L'analyse par éléments finis (FEA) valide les performances structurelles des conceptions optimisées sur le plan topologique dans les conditions de charge prévues. La simulation thermique permet de prévoir et d'atténuer les déformations et les contraintes résiduelles au cours du processus d'impression. Les outils de simulation du processus d'impression peuvent aider à optimiser l'orientation de la construction et les stratégies de support avant d'engager des matériaux coûteux et du temps machine. Mettre en œuvre efficacement DfAM aérospatiale nécessitent une expertise à la fois dans les principes de conception et dans les nuances du processus d'AM choisi.
Atteindre la précision : Tolérance, état de surface et précision dimensionnelle
Les ingénieurs et les responsables des achats qui abandonnent la fabrication traditionnelle doivent avoir des attentes réalistes en ce qui concerne la précision qu'il est possible d'obtenir avec la fabrication additive métallique. Si la fabrication additive offre une incroyable liberté de conception, elle diffère intrinsèquement de la précision de l'ordre du micron souvent associée à l'usinage CNC multi-axes dans son état "tel que construit". Cependant, la compréhension des capacités et l'incorporation des post-traitements nécessaires permettent aux composants AM, tels que les supports d'ailettes, de répondre aux exigences rigoureuses de l'aérospatiale.
Tolérances typiques :
La tolérance dimensionnelle réalisable dépend fortement du processus d'AM spécifique (L-PBF ou EBM), du matériau imprimé, de la taille et de la complexité de la pièce, de son orientation sur la plaque de construction et de l'étalonnage de la machine.
- Fusion laser sur lit de poudre (L-PBF) : Offre généralement une plus grande précision et une résolution plus fine des caractéristiques en raison de la taille plus petite du bain de fusion. Les tolérances typiques peuvent aller de ±0,1 mm à ±0,2 mm pour les petites caractéristiques, pouvant aller jusqu'à ±0,1-0,2% pour les dimensions plus importantes.
- Fusion par faisceau d'électrons (EBM) : Elle fonctionne souvent à des températures plus élevées et utilise un faisceau plus large, ce qui peut conduire à une précision légèrement inférieure à celle de la L-PBF, de l'ordre de ±0,2 mm à ±0,4 mm ou ±0,2-0,5% pour les dimensions plus importantes. Cependant, l'EBM excelle avec certains matériaux (comme le Ti-6Al-4V) et nécessite souvent moins de structure de support en raison de l'environnement du lit de poudre chaud. Explorer différentes méthodes d'impression pour comprendre leurs capacités spécifiques.
Il est essentiel de noter que les caractéristiques critiques nécessitant des tolérances plus serrées (par exemple, les surfaces d'accouplement, les interfaces de roulement, les trous de fixation) sur un support d'ailette sont généralement obtenues par des opérations de post-usinage plutôt qu'en s'appuyant uniquement sur la tolérance AM telle qu'elle a été construite.
Finition de la surface (rugosité) :
L'état de surface des pièces métalliques obtenues par AM est généralement plus rugueux que les surfaces usinées en raison du processus couche par couche et des particules de poudre partiellement fondues qui adhèrent aux surfaces.
- Tel que construit Ra : Les valeurs de rugosité de surface (Ra) varient généralement de 6 µm à 25 µm (240 µin à 1000 µin), en fonction du procédé, du matériau, de l'orientation (surfaces orientées vers le haut ou vers le bas ou parois latérales) et des paramètres utilisés. Les pièces EBM ont souvent tendance à être plus rugueuses que les pièces L-PBF.
- Ra. post-traité : Diverses étapes de post-traitement, telles que le microbillage, le tambourinage, la gravure chimique, l'électropolissage ou l'usinage CNC, permettent d'améliorer sensiblement l'état de surface. L'usinage permet d'obtenir des valeurs Ra inférieures à 1 µm (40 µin) lorsque cela est nécessaire.
Facteurs influençant la précision dimensionnelle :
- Étalonnage de la machine : Un étalonnage régulier et précis du système AM est essentiel.
- Propriétés du matériau : La dilatation thermique et la conductivité influent sur le retrait et la contrainte.
- Paramètres du processus : La puissance du laser/du faisceau, la vitesse de balayage, l'épaisseur de la couche, l'espacement des hachures sont autant d'éléments qui influencent la dynamique du bain de fusion et la précision qui en résulte.
- Contraintes thermiques : Un chauffage et un refroidissement irréguliers provoquent des tensions internes qui peuvent entraîner des déformations et des distorsions.
- Géométrie et orientation des pièces : Les grandes surfaces planes ou les surplombs non soutenus sont plus susceptibles de dévier.
- Stratégie de soutien : Des supports bien conçus sont essentiels pour ancrer la pièce et gérer les contraintes thermiques.
Systèmes de gestion de la qualité (QMS) : Obtenir une précision dimensionnelle constante et respecter exigences en matière de finition de surface dans l'aérospatiale s'appuie fortement sur un contrôle qualité rigoureux tout au long du processus - de la gestion des poudres et de la configuration de la machine au contrôle du processus et à la vérification après traitement. Les fournisseurs de services d'AM réputés tels que Met3dp appliquent des protocoles QMS rigoureux (souvent alignés sur des normes telles que AS9100 pour l'aérospatiale) afin de garantir la répétabilité et la conformité. S'appuyer sur des fournisseurs ayant volume d'impression, précision et fiabilité à la pointe de l'industrie est essentiel pour les composants critiques.
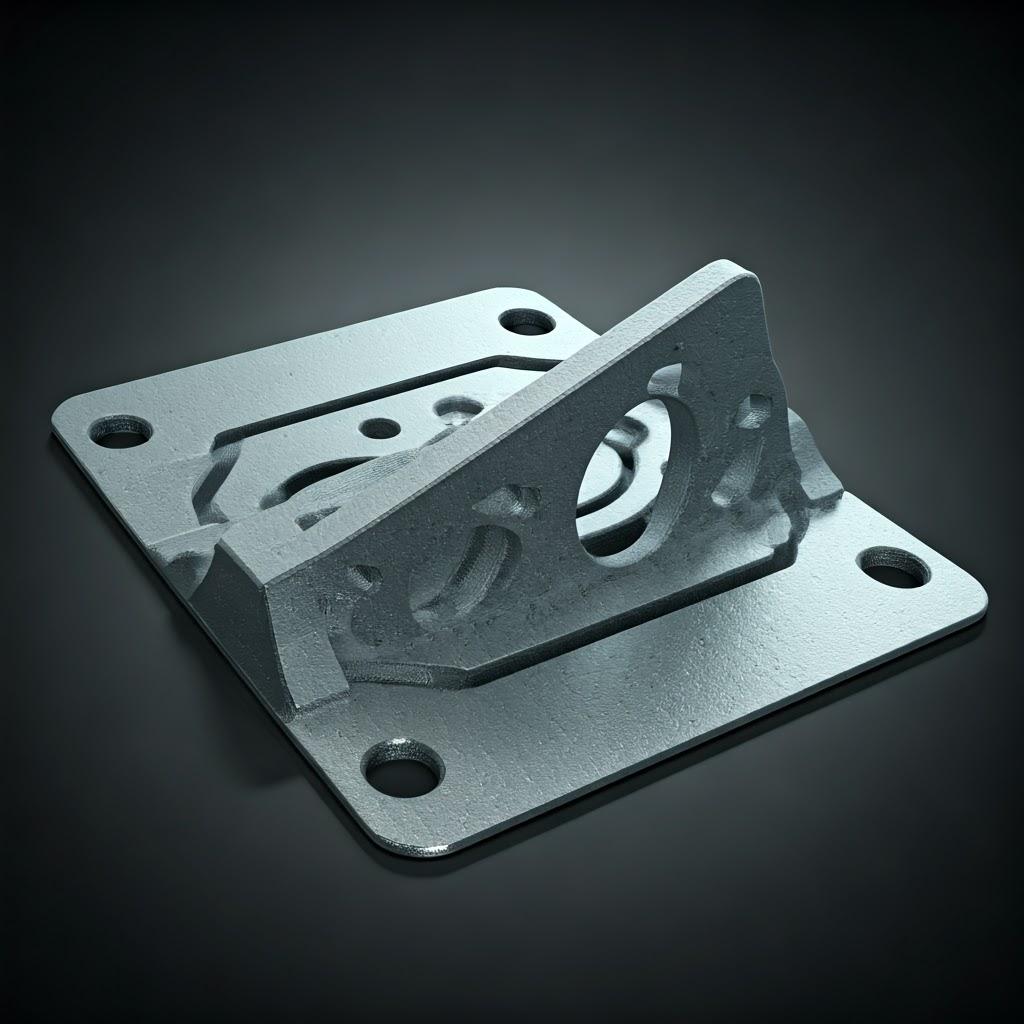
Étapes essentielles du post-traitement des supports de qualité aérospatiale
Un support d'aile métallique imprimé en 3D, tel qu'il sort de la plaque de construction, n'est pas encore prêt pour le vol. Une série d'étapes cruciales de post-traitement sont nécessaires pour réduire les contraintes internes, supprimer les structures de soutien, atteindre les tolérances dimensionnelles et la finition de surface nécessaires, et s'assurer que le composant répond aux propriétés mécaniques exigeantes et aux normes de sécurité de l'industrie aérospatiale. Ces étapes font partie intégrante du processus de fabrication et doivent être prises en compte lors de l'évaluation des délais et des coûts.
Flux de travail commun de post-traitement :
- Elimination des poudres : Tout d'abord, l'excès de poudre métallique doit être méticuleusement éliminé de la pièce achevée, en particulier des canaux internes ou des caractéristiques complexes. Cette opération est souvent réalisée par brossage, aspiration ou microbillage dans un environnement contrôlé pour permettre le recyclage de la poudre.
- Soulagement du stress : Il s'agit généralement du premier traitement thermique appliqué, souvent alors que la pièce est encore attachée à la plaque de construction. L'accumulation de gradients thermiques au cours du processus d'impression par couches crée des contraintes internes importantes. Un cycle de traitement thermique de détente (la température et la durée spécifiques dépendent du matériau) réduit ces contraintes, minimisant le risque de déformation ou de fissuration lorsque la pièce est retirée de la plaque de construction.
- Retrait de la plaque de construction : Les pièces sont généralement découpées ou détachées de la plaque de construction à l'aide de méthodes telles que l'électroérosion à fil (Electrical Discharge Machining), le sciage à ruban ou l'usinage.
- Retrait de la structure de soutien : Cette étape peut être l'une des plus laborieuses, en fonction de la complexité et de l'emplacement des supports. Les méthodes utilisées sont les suivantes :
- Suppression manuelle : Casser ou découper les supports facilement accessibles.
- Usinage : Utilisation du fraisage ou du meulage CNC pour enlever les supports, en particulier près des surfaces critiques.
- EDM : Pour les aides dans les zones difficiles d'accès. Une GPAO soigneuse au départ peut réduire considérablement la complexité de cette étape.
- Traitement thermique (recuit de mise en solution, vieillissement, etc.) : Au-delà du détensionnement, d'autres traitements thermiques sont souvent nécessaires pour obtenir la microstructure finale et les propriétés mécaniques souhaitées (par exemple, résistance, ductilité, dureté) spécifiées pour l'application aérospatiale. Les cycles exacts dépendent de l'alliage (le Ti-6Al-4V et le Scalmalloy® ont des traitements spécifiques prescrits).
- Pressage isostatique à chaud (HIP) : Ce processus est souvent obligatoire pour les de qualité aérospatiale les composants AM en métal, en particulier les pièces en titane. Le HIP consiste à soumettre la pièce simultanément à une température élevée (inférieure au point de fusion) et à une pression élevée de gaz inerte (généralement de l'argon). Cette combinaison ferme efficacement la micro-porosité interne (pores de gaz ou vides de fusion) qui peut être présente après l'impression, améliorant de manière significative la résistance à la fatigue, la ductilité et la ténacité - des propriétés essentielles pour la sécurité et la fiabilité de l'aérospatiale.
- Usinage CNC : Pour obtenir des tolérances serrées sur les interfaces critiques (par exemple, les surfaces en contact avec la structure de l'aile ou le longeron de l'aile), les trous de fixation et les emplacements des roulements, il est nécessaire d'appliquer des tolérances de précision à l'ensemble de la structure de l'aile. Usinage CNC des pièces imprimées en 3D est essentielle. Cela permet de garantir un ajustement et un fonctionnement corrects au sein de l'ensemble de l'aéronef.
- Finition de la surface : Selon les besoins, d'autres étapes de finition peuvent être réalisées :
- Sablage et grenaillage : Le grenaillage de précontrainte peut induire des contraintes résiduelles de compression afin d'améliorer la durée de vie en fatigue.
- Finition par culbutage et vibration : Lisse les surfaces et ébavure les bords, en particulier pour les petites pièces.
- Polissage : Pour obtenir des surfaces très lisses lorsque c'est nécessaire, bien que moins courant pour les supports purement structurels, à moins qu'ils ne soient nécessaires pour l'inspection.
- Essais non destructifs (END) : Une inspection rigoureuse n'est pas négociable pour les pièces critiques pour le vol. CND pour la fabrication additive garantit que la pièce est exempte de défauts critiques et qu'elle répond aux spécifications dimensionnelles. Les méthodes les plus courantes sont les suivantes :
- Tomodensitométrie (CT) : Fournit une vue en 3D de la structure interne pour détecter la porosité, les inclusions ou les déviations géométriques internes.
- Contrôle par ressuage fluorescent (FPI) : Détecte les fissures superficielles.
- Contrôle par ultrasons (UT) : Peut détecter des défauts sous la surface.
- Inspection dimensionnelle : Utilisation de machines à mesurer tridimensionnelles (MMT) ou de scanners 3D pour vérifier les dimensions critiques par rapport aux spécifications de conception.
Le partenariat avec un fournisseur de services de gestion de l'AM qui offre ces services complets de gestion de l'AM. métal AM post-traitement aérospatiale en interne ou par l'intermédiaire de partenaires certifiés est essentielle pour rationaliser la chaîne d'approvisionnement et garantir la qualité et la conformité des pièces.
Défis de l'impression 3D des bracelets d'aile et stratégies d'atténuation
Si la fabrication additive métallique offre des avantages significatifs pour la production de composants tels que les supports de connexion des winglets de l'aérospatiale, elle n'est pas exempte de défis. Il est essentiel de comprendre ces obstacles potentiels et les stratégies employées par les fournisseurs expérimentés en matière de fabrication additive pour les surmonter afin de les adopter avec succès, en particulier lorsqu'il s'agit de commandes en vrac de bracelets pour l'aérospatiale ou des applications critiques.
Défis communs et techniques d'atténuation :
- Contraintes résiduelles et déformation :
- Défi: Les cycles de chauffage et de refroidissement rapides inhérents aux procédés PBF créent des gradients thermiques qui entraînent des contraintes internes. Ces contraintes peuvent entraîner le gauchissement ou la déformation des pièces pendant l'impression ou après leur retrait de la plaque de construction, ce qui affecte la précision des dimensions.
- Atténuation :
- Simulation : Utilisation de logiciels de simulation thermique pour prévoir l'accumulation de contraintes et optimiser l'orientation de la construction et les structures de soutien.
- Stratégies d'analyse optimisées : L'utilisation de modèles spécifiques de balayage laser/de faisceaux (par exemple, balayage d'îlots, balayage de secteurs) pour répartir la chaleur de manière plus uniforme.
- Structures de soutien robustes : Concevoir des supports non seulement pour les surplombs, mais aussi pour ancrer efficacement la pièce et servir de puits de chaleur.
- Chauffage de la plate-forme (EBM/quelques L-PBF) : Le maintien d'une température élevée dans la chambre de construction réduit les gradients thermiques.
- Stress obligatoire après l'impression : Appliquer le cycle thermique approprié immédiatement après la construction.
- Porosité :
- Défi: De petits vides internes peuvent se former en raison de gaz piégés (porosité gazeuse) ou d'une fusion incomplète entre les couches/pistes de balayage (porosité par manque de fusion). La porosité peut dégrader de manière significative les propriétés mécaniques, en particulier la résistance à la fatigue.
- Atténuation :
- Paramètres de processus optimisés : Contrôle précis de la puissance du laser/du faisceau, de la vitesse de balayage, de l'épaisseur de la couche et du débit de gaz (en L-PBF) adapté au matériau spécifique.
- Poudre de haute qualité : Utilisation d'une poudre à faible teneur en gaz piégés, à PSD contrôlé et à bonne fluidité (un point fort de la production avancée de poudres de Met3dp).
- Contrôle de l'atmosphère inerte : Maintien d'un environnement de gaz inerte de haute pureté (argon ou azote) dans la chambre de construction pour éviter l'oxydation et la contamination.
- Pressage isostatique à chaud (HIP) : La méthode la plus efficace pour fermer les pores internes après l'impression, souvent nécessaire pour les pièces critiques de l'aérospatiale.
- Difficultés liées au retrait de la structure de soutien :
- Défi: Les supports dans des canaux internes complexes ou des géométries compliquées peuvent être extrêmement difficiles, voire impossibles à retirer complètement sans endommager la pièce.
- Atténuation :
- DfAM : Donner la priorité aux conceptions autoportantes et optimiser l'orientation pour minimiser le recours aux supports dans les zones inaccessibles.
- Outils/techniques de retrait spécialisés : En utilisant l'électroérosion, le décapage chimique (pour certains matériaux) ou un enlèvement manuel/usiné minutieux.
- Conception pour l'accès : Veiller à ce que les voies d'évacuation soient prises en compte lors de la phase de conception.
- Contamination et gestion des poudres :
- Défi: La contamination des poudres métalliques (par exemple, contamination croisée entre alliages, absorption excessive d'oxygène) peut compromettre les propriétés des matériaux et la qualité de l'impression. La gestion et le recyclage des poudres nécessitent des procédures rigoureuses.
- Atténuation :
- Protocoles stricts de manipulation des poudres : Équipements dédiés aux différents matériaux, manipulation sous atmosphère contrôlée, stockage approprié.
- Conditionnement et tamisage des poudres : Tamiser régulièrement la poudre pour éliminer les particules surdimensionnées ou les contaminants et garantir une DSP constante avant réutilisation.
- Essais de contrôle de la qualité : Tester régulièrement les propriétés des poudres (chimie, PSD, fluidité).
- Cohérence et reproductibilité (production en vrac) :
- Défi: Veiller à ce que chaque pièce produite, en particulier dans les grands lots (fournisseur d'impression 3D de grands volumes de métaux ), répond exactement aux mêmes spécifications et normes de qualité.
- Atténuation :
- Des systèmes de gestion de la qualité (QMS) robustes : Mise en œuvre et respect des normes aérospatiales telles que la norme AS9100.
- Surveillance des processus : Surveillance in situ des paramètres clés du processus (par exemple, les caractéristiques du bain de fusion, la température) pendant la construction.
- Étalonnage et maintenance des machines : Maintenance préventive régulière et étalonnage des systèmes AM.
- Procédures normalisées : Des flux de travail documentés pour chaque étape, de la conception au post-traitement et à l'inspection.
- Contrôle statistique des processus (CSP) : Analyser les données du processus afin d'en assurer la stabilité et d'identifier les déviations potentielles.
Pour relever ces défis avec succès, il faut disposer d'une expertise approfondie en matière de science des matériaux, d'ingénierie des procédés, de DfAM et de contrôle de la qualité. C'est là que le partenariat avec un fournisseur d'AM bien établi et bien informé comme Met3dp devient inestimable. Avec des décennies d'expertise collective et une approche verticalement intégrée comprenant des imprimantes SEBM avancées, des poudres métalliques de haute qualité produites en interne et des services complets de développement d'applications, Met3dp est bien équipé pour s'attaquer aux complexités de la production de composants aérospatiaux exigeants. L'accent mis sur précision et fiabilité permet d'atténuer les risques et de garantir la livraison de supports de connexion de winglets de haute qualité et aptes au vol. Pour en savoir plus sur leur approche dédiée, consultez leur site Web. À propos de nous page.
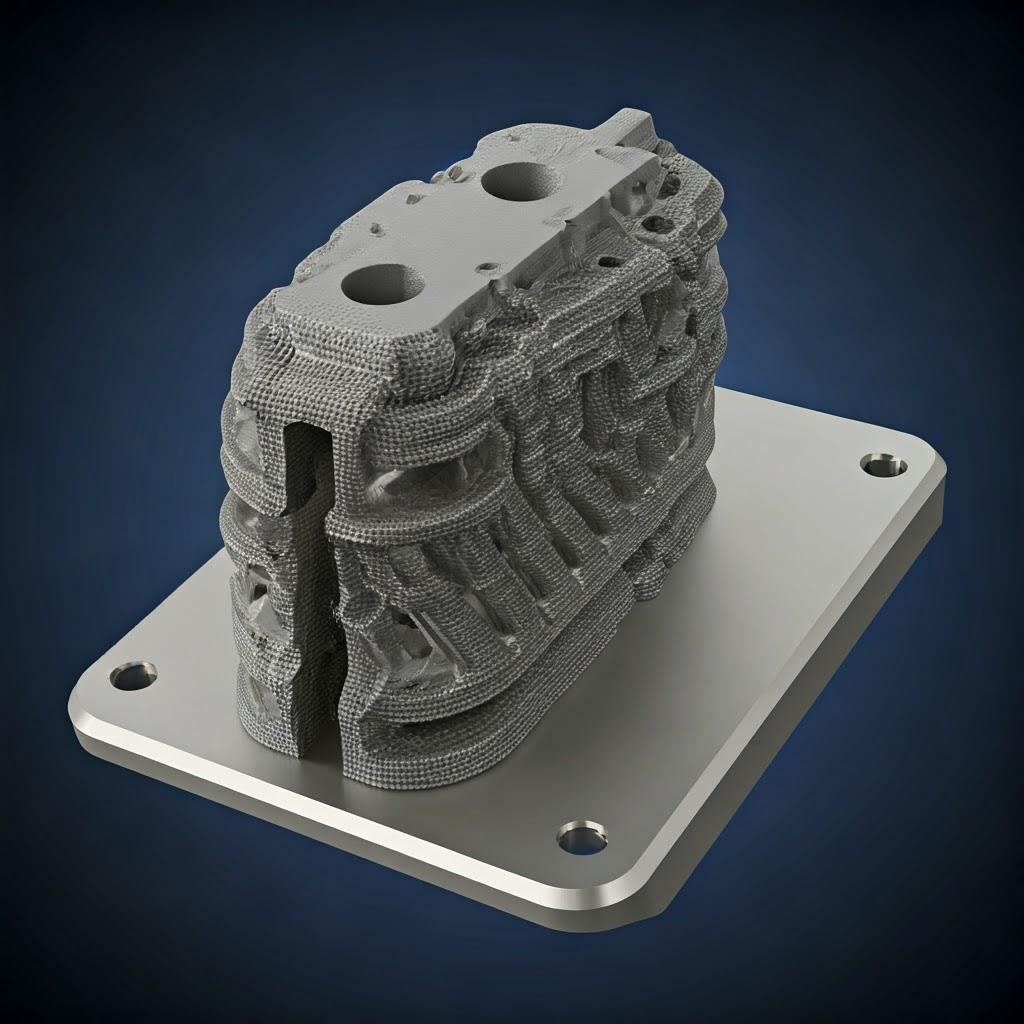
Choisir le bon fournisseur de services d'impression 3D de métaux pour les composants aérospatiaux
Le choix du bon partenaire de fabrication est sans doute l'une des décisions les plus critiques lors de l'approvisionnement en composants métalliques imprimés en 3D pour des applications aérospatiales telles que les supports de connexion d'ailettes. Les exigences uniques de l'industrie aérospatiale - réglementations de sécurité strictes, processus de qualification complexes et nécessité d'une fiabilité absolue - signifient que tous les fournisseurs de services d'impression 3D ne se valent pas. Les ingénieurs et les responsables des achats doivent procéder à des évaluation des fournisseurs d'AM dans l'aérospatiale sur la base d'un ensemble de critères définis.
Critères clés pour l'évaluation des fournisseurs :
- Certifications aérospatiales : Ce point n'est pas négociable. Recherchez des prestataires détenant des certifications pertinentes, principalement :
- AS9100 : Norme internationalement reconnue de système de gestion de la qualité pour les industries de l'aviation, de l'espace et de la défense. La conformité démontre un engagement en faveur de la qualité, de la traçabilité, de la gestion des risques et de l'amélioration continue, spécifiques aux exigences de l'aérospatiale.
- ISO 9001 : Une certification de base du système de gestion de la qualité.
- Accréditation Nadcap : Accréditation spécifique pour les processus spéciaux tels que le traitement thermique, les essais non destructifs (END), le soudage et les essais de matériaux, garantissant que ces étapes critiques répondent aux normes de l'industrie.
- Expertise et traçabilité des matériaux : Le fournisseur doit avoir une expérience avérée dans le traitement des alliages spécifiques requis (par exemple, Ti-6Al-4V, Scalmalloy®). Renseignez-vous :
- Approvisionnement en poudre : Ont-ils des fournisseurs fiables ou produisent-ils la poudre en interne ?
- Contrôle de la qualité des poudres : Quelles sont les procédures d'essai, de manipulation, de stockage et de recyclage des poudres afin d'éviter toute contamination et de garantir l'homogénéité ?
- Traçabilité complète des matériaux : Peut-on remonter jusqu'à l'origine du lot de poudre utilisé pour chaque pièce spécifique ? La capacité de Met3dp à produire ses propres poudres métalliques de haute qualité offre un avantage certain en matière de traçabilité et de contrôle de la qualité.
- Expérience confirmée dans le domaine de l'aérospatiale : Recherchez des preuves que le fournisseur a produit avec succès des composants (idéalement structurels ou critiques pour le vol) pour d'autres clients de l'aérospatiale (équipementiers, fournisseurs de niveau 1). Des études de cas, des exemples de projets (dans les limites de la NDA) et des références peuvent valider leur expérience et leur capacité à naviguer dans les voies de qualification aérospatiale.
- Capacités de l'équipement :
- Utilise-t-il la technologie AM appropriée (L-PBF, EBM) pour le matériau et la conception de votre support ?
- Leurs machines sont-elles bien entretenues et calibrées ?
- Disposent-ils d'un volume de fabrication suffisant pour la taille de vos pièces et d'une capacité machine adéquate pour répondre aux besoins de la production potentielle (commandes en vrac de bracelets pour l'aérospatiale) et les délais d'exécution ?
- Soutien technique et ingénierie : Un partenaire de valeur est plus qu'un simple bureau d'impression. Recherchez des fournisseurs offrant :
- Expertise du DfAM : Capacité à donner des conseils sur l'optimisation de la conception pour la fabrication additive.
- Capacités de simulation : Aide à la validation des conceptions et à la prévision des résultats d'impression.
- Développement de procédés : Volonté de collaborer à l'optimisation des paramètres pour des applications spécifiques.
- Post-traitement intégré : Le fournisseur offre-t-il une suite complète d'étapes de post-traitement nécessaires (détente, HIP, usinage, NDT, finition) en interne ou par l'intermédiaire d'un réseau de partenaires certifiés et étroitement gérés ? La gestion de plusieurs fournisseurs augmente la complexité et les risques.
- Système de gestion de la qualité (SGQ) robuste : Au-delà des certifications, examinez leurs procédures de qualité spécifiques :
- Surveillance et contrôle en cours de processus.
- Protocoles d'inspection rigoureux (dimensionnels, CND).
- Contrôle de la documentation et tenue de registres.
- Gestion de la configuration.
- Fiabilité de la chaîne d'approvisionnement et communication : Évaluer leur réactivité, la clarté de leur communication, leurs capacités de gestion de projet et leur aptitude à fournir des services fiables et de qualité. délai de fabrication additive et respecter les délais de livraison.
Choisir un fournisseur comme Met3dpqui combine des décennies d'expertise collective dans la fabrication additive métallique avec des solutions intégrées verticalement couvrant Imprimantes SEBM, poudres métalliques avancées et services de développement d'applicationsLes entreprises de l'Union européenne peuvent rationaliser de manière significative le processus de sélection. L'accent qu'ils mettent sur la fourniture de services de volume d'impression, précision et fiabilité à la pointe de l'industrie vise spécifiquement les pièces critiques dans des domaines exigeants tels que l'aérospatiale.
Analyse des coûts et estimation des délais pour les supports d'ailettes imprimés en 3D
Il est essentiel de comprendre les facteurs de coût et les délais typiques associés aux supports d'ailettes métalliques imprimés en 3D pour planifier un projet, établir un budget et comparer la technologie AM aux méthodes de fabrication traditionnelles du point de vue du coût total de possession. Pour obtenir des informations détaillées sur les devis en gros pour l'impression 3D Il est nécessaire d'obtenir des devis spécifiques à un projet ou à une entreprise, mais la connaissance des facteurs d'influence aide à les évaluer.
Facteurs de coûts primaires :
- Coût des matériaux : Les poudres métalliques de qualité aérospatiale comme le Ti-6Al-4V et le Scalmalloy® sont des matières premières intrinsèquement coûteuses par rapport aux alliages techniques standard. La masse totale de la pièce finale, plus tout matériau utilisé pour les structures de support, a un impact direct sur le coût.
- Volume de la pièce et hauteur de construction : Les pièces plus grandes ou plus hautes consomment plus de temps machine. Les machines d'AM représentent un investissement important, et leur temps de fonctionnement (taux d'heures machine) est un élément de coût majeur. L'imbrication efficace de plusieurs pièces sur une seule plaque de fabrication peut contribuer à réduire les coûts du temps machine par pièce pour les lots plus importants.
- Temps de construction : Déterminé par le nombre de couches (hauteur de la pièce / épaisseur de la couche) et le temps nécessaire pour scanner chaque couche (complexité, surface de la section transversale). Des machines plus rapides ou des processus tels que l'EBM (pour certaines applications) peuvent offrir des avantages en termes de temps.
- Complexité des pièces : Les conceptions très complexes peuvent nécessiter des structures de support plus complexes ou des temps de balayage plus longs par couche. Cependant, c'est souvent dans le domaine de la complexité que l'AM se distingue, en permettant la consolidation des pièces, ce qui peut compenser l'augmentation des coûts d'impression par des économies d'assemblage.
- Structures de soutien : Le volume de matériau utilisé pour les supports et, plus important encore, le temps de travail et/ou d'usinage nécessaire à leur enlèvement contribuent au coût global. Les efforts déployés par le DfAM pour minimiser les supports sont payants à cet égard.
- Exigences en matière de post-traitement : Cela peut représenter une part importante du coût final.
- Traitements thermiques (allègement des contraintes, traitement thermique, HIP) : Nécessite un équipement de four spécialisé et du temps ; le HIP est particulièrement énergivore et ajoute un coût important, mais il est souvent essentiel pour les pièces critiques du point de vue de la fatigue.
- Usinage : L'usinage CNC de précision des caractéristiques critiques augmente les coûts en fonction de la complexité et du temps.
- CND et inspection : Les inspections requises (tomodensitométrie, FPI, CMM) augmentent les coûts liés à l'équipement, au temps et à l'expertise.
- Finition : Les coûts dépendent de la méthode utilisée et de la qualité de surface requise.
- Quantité : Comme pour la plupart des processus de fabrication, les économies d'échelle s'appliquent. Les coûts de mise en place (préparation de la pièce, réglage de la machine, réglage du post-traitement) sont amortis sur de plus grandes quantités. Les remises sur les volumes de poudre et l'optimisation de l'utilisation de la plaque de fabrication peuvent réduire les coûts par pièce pour les produits suivants commandes en vrac de bracelets pour l'aérospatiale.
- Qualification et certification : Les coûts associés au développement d'un processus certifié et à la qualification de la pièce spécifique pour le vol peuvent être importants, en particulier pour l'adoption initiale.
Estimation du délai d'exécution :
Le total délai de fabrication additive De l'approbation finale de la conception à la livraison d'un support d'ailette prêt à voler, il y a plusieurs étapes :
- Préparation de la construction : Préparation des dossiers, planification de l'agencement, réglage des machines (quelques heures par jour).
- Impression : Le délai peut aller de quelques heures pour les petits supports à plusieurs jours pour les grandes pièces complexes ou les plaques de construction complètes (en fonction de la hauteur et du volume).
- Refroidissement et élimination de la poudre : Heures.
- Soulagement du stress : En général, plusieurs heures à une journée (y compris la durée du four).
- Retrait de la pièce/du support : De quelques heures à quelques jours, en fonction de la complexité et de la méthode.
- Traitement thermique/HIP : Cela peut prendre plusieurs jours, y compris les cycles de chauffage et de refroidissement.
- Usinage : Très variable en fonction des besoins (de quelques heures à quelques jours).
- Finition : Des heures aux jours.
- CND et inspection : De quelques heures à quelques jours, en fonction des méthodes et des rapports.
- Expédition: Variable.
Délais d'exécution typiques :
- Prototypes (forme/adaptation) : De quelques jours à 1 ou 2 semaines (souvent sans traitement ultérieur, comme le HIP ou les essais non destructifs approfondis).
- Prototypes testés sur le plan fonctionnel : 2-4 semaines (y compris les traitements thermiques essentiels et une partie de l'usinage/NDT).
- Pièces de production qualifiées : 4-10+ semaines, dépendant fortement de l'étendue du post-traitement, des contrôles non destructifs rigoureux, des exigences en matière de documentation et de la taille du lot.
Il est essentiel de travailler en étroite collaboration avec le fournisseur d'AM choisi pour obtenir des estimations précises et personnalisées des coûts et des délais en fonction de vos exigences spécifiques en matière de conception, de matériaux, de quantité et de qualification.
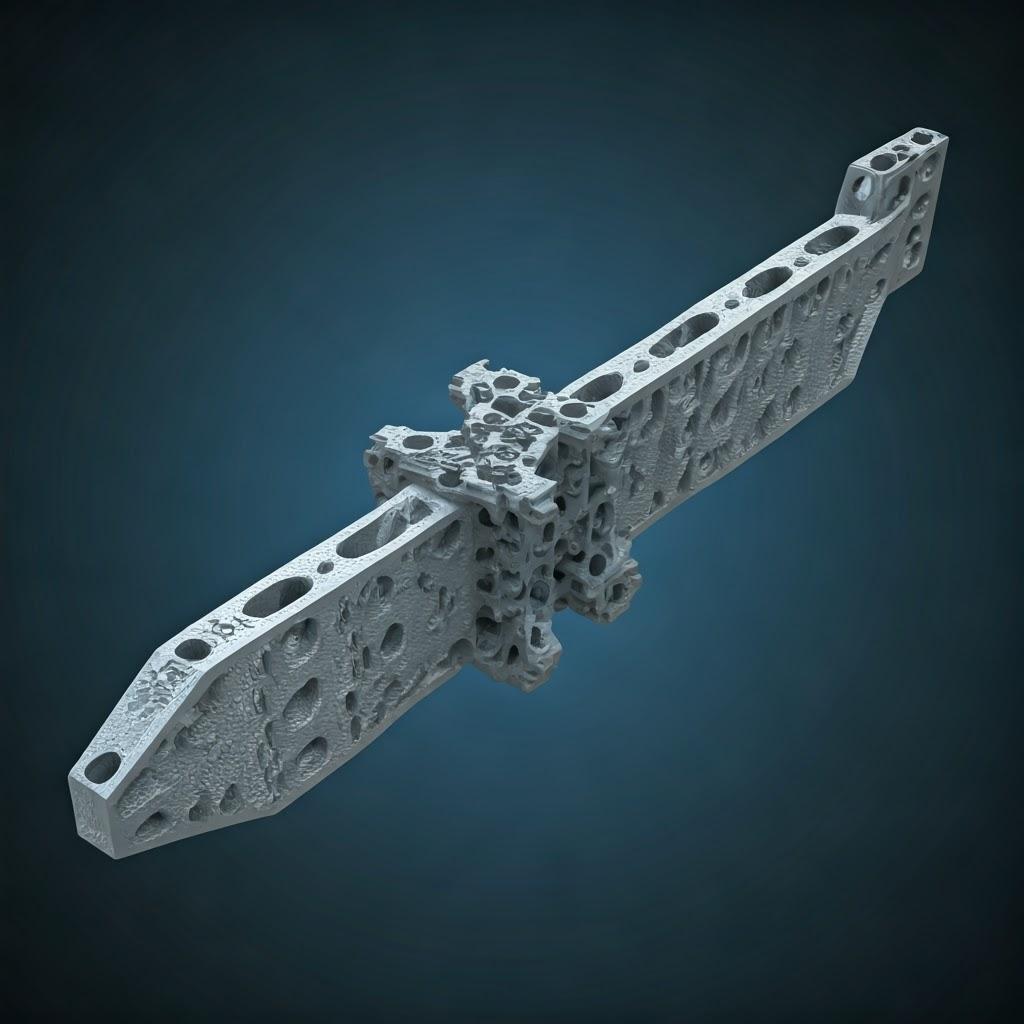
Foire aux questions (FAQ) sur les supports d'ailettes imprimés en 3D
Voici les réponses à quelques questions courantes concernant l'utilisation de la fabrication additive métallique pour les supports de connexion des winglets dans l'aérospatiale :
Q1 : Les supports métalliques imprimés en 3D sont-ils certifiés pour le vol ?
- A : Oui, absolument. La certification de vol n'est pas accordée à la technologie d'impression 3D elle-même, mais plutôt à un système d'impression 3D spécifique et hautement contrôlé. processus de fabrication. Il s'agit notamment du modèle spécifique de machine d'AM, du lot de matériaux qualifiés (par exemple, la poudre Ti-6Al-4V répondant aux spécifications aérospatiales), des paramètres validés de la machine, des étapes définies de post-traitement (y compris la détente, le HIP, le traitement thermique, l'usinage) et de l'adhésion à un système de gestion de la qualité certifié (comme l'AS9100). Les pièces produites de manière cohérente grâce à ce processus rigoureusement contrôlé et certifié, et vérifiées par des contrôles non destructifs et dimensionnels approfondis, peuvent être certifiées pour des applications de vol. Plusieurs avions qui volent aujourd'hui intègrent des composants structurels imprimés en 3D.
Q2 : Quelle est la durée de vie des supports AM par rapport aux supports usinés ?
- A : Lorsqu'ils sont produits en utilisant des paramètres optimisés, des poudres de haute qualité et un post-traitement approprié (en particulier HIP pour la fermeture des porosités), la durée de vie en fatigue des composants AM Ti-6Al-4V peut atteindre ou dépasser celle des composants moulés et s'approcher des propriétés des composants corroyés/usinés. Pour le Scalmalloy®, le traitement AM peut donner des propriétés de fatigue supérieures à celles de nombreux alliages d'aluminium conventionnels à haute résistance. En outre, la DfAM permet des conceptions qui minimisent spécifiquement les concentrations de contraintes, ce qui peut conduire à une amélioration des performances en fatigue par rapport aux conceptions traditionnellement contraintes. Les performances doivent toujours être validées par des essais rigoureux spécifiques à l'application.
Q3 : Quelle est l'amélioration typique du ratio achat-vol avec les supports AM ?
- A : Il s'agit là de l'un des principaux avantages de l'AM. L'usinage traditionnel de supports aérospatiaux à partir de billettes, en particulier de titane, peut présenter des ratios achat/vol de 10:1, 15:1, voire plus (ce qui signifie que 10 à 15 kg de matière première sont achetés pour chaque kilogramme de la pièce finale). Avec l'AM, qui utilise les matériaux de manière additive et permet l'optimisation de la topologie, le rapport achat/vol peut souvent être réduit de manière spectaculaire à des chiffres comme 2:1 ou 3:1, ce qui représente des économies substantielles de matières premières coûteuses et un impact environnemental réduit.
Q4 : Est-il possible d'imprimer directement en 3D des modèles de bracelets existants ?
- A : Bien que cela soit techniquement possible, ce n'est généralement pas recommandé. L'impression directe d'une conception optimisée pour l'usinage ou le moulage ne permet généralement pas de tirer parti des principaux avantages de l'AM (comme la réduction du poids grâce à l'optimisation de la topologie ou à la consolidation des pièces). Il peut également être difficile d'imprimer efficacement en raison de caractéristiques qui ne conviennent pas à l'AM (par exemple, de grands porte-à-faux). Pour exploiter tout le potentiel de l'AM, il est vivement conseillé de revoir la conception du support en appliquant les principes de la DfAM.
Q5 : Quelles sont les méthodes de contrôle non destructif utilisées pour qualifier les pièces aérospatiales AM ?
- A : Une combinaison de méthodes de contrôle non destructif est généralement employée pour garantir l'intégrité des composants aérospatiaux AM critiques. La tomodensitométrie (CT) est très utile pour détecter les défauts internes tels que la porosité ou les inclusions et pour vérifier les géométries internes. Le contrôle par ressuage fluorescent (FPI) est couramment utilisé pour détecter les fissures superficielles. Le contrôle par ultrasons (UT) permet de détecter les défauts sous la surface. En outre, une inspection dimensionnelle rigoureuse à l'aide de machines à mesurer tridimensionnelles (MMT) ou de scanners laser 3D permet de vérifier la conformité aux spécifications de conception. Le plan spécifique de contrôle non destructif est adapté à la criticité et à la conception de la pièce.
Conclusion : Adoption de la fabrication additive pour les supports d'ailettes d'aéronefs de nouvelle génération
La recherche incessante par l'industrie aérospatiale de meilleures performances, d'une plus grande efficacité énergétique et d'une réduction de l'impact sur l'environnement exige une innovation continue en matière de conception et de fabrication. La fabrication additive métallique s'est imposée sans équivoque comme un outil puissant pour atteindre ces objectifs, en particulier pour les composants structurels complexes tels que les supports de connexion des ailettes.
En exploitant les capacités des processus d'AM tels que le L-PBF et l'EBM, combinés à des matériaux avancés tels que le Ti-6Al-4V standard pour l'aérospatiale et le Scalmalloy® haute performance, les ingénieurs peuvent désormais concevoir et produire des supports nettement plus légers, potentiellement plus résistants, et présentant des géométries optimisées pour la fonction plutôt que contraintes par les limites de fabrication traditionnelles. La possibilité de consolider les pièces, de réduire le gaspillage de matériaux (en améliorant les ratios d'achat et de vol) et d'accélérer les cycles d'itération de la conception renforce encore les arguments en faveur de l'adoption de l'AM.
Bien que les défis liés au contrôle des processus, à la complexité du post-traitement et aux voies de qualification existent, ils sont relevés avec succès grâce aux progrès de la technologie, de la science des matériaux, des outils de simulation et à la mise en place de systèmes de gestion de la qualité et de normes industrielles solides. La clé réside dans le partenariat avec des entreprises expérimentées et compétentes. fournisseurs de services d'impression 3D métal qui possèdent les certifications nécessaires, l'expertise en matière de matériaux, les capacités technologiques et l'attention rigoureuse portée à la qualité exigée par le secteur aérospatial.
L'avenir de la fabrication aérospatiale verra sans aucun doute l'adoption croissante de la fabrication additive pour les applications structurelles, dépassant les prototypes et les pièces non critiques pour passer à la production en série de composants critiques pour le vol. Les supports de connexion des ailettes représentent une application idéale où les avantages de la fabrication additive - réduction du poids, amélioration des performances et liberté de conception - apportent une valeur tangible.
Pour les ingénieurs aérospatiaux et les responsables des achats qui cherchent à explorer le potentiel de l'AM des métaux pour les supports d'ailettes ou d'autres applications exigeantes, c'est maintenant qu'il faut s'engager. La collaboration avec un partenaire compétent peut aider à surmonter les difficultés et à exploiter le potentiel de transformation de cette technologie.
Prêt à révolutionner vos composants aérospatiaux ? Découvrez les solutions de pointe en matière de fabrication additive métallique avec Met3dp. Visitez le site https://met3dp.com/ pour en savoir plus sur nos imprimantes SEBM avancées, nos poudres métalliques haute performance et nos services complets de développement d'applications adaptés à l'industrie aérospatiale. Contactez-nous dès aujourd'hui pour savoir comment Solutions aérospatiales Met3dp peut contribuer à la réalisation des objectifs de votre organisation en matière de fabrication additive et vous aider à construire l'avenir de l'aviation.
Partager sur
MET3DP Technology Co. est un fournisseur de premier plan de solutions de fabrication additive dont le siège se trouve à Qingdao, en Chine. Notre société est spécialisée dans les équipements d'impression 3D et les poudres métalliques de haute performance pour les applications industrielles.
Articles connexes
À propos de Met3DP
Mise à jour récente
Notre produit
CONTACTEZ-NOUS
Vous avez des questions ? Envoyez-nous un message dès maintenant ! Nous répondrons à votre demande avec toute une équipe dès réception de votre message.
Obtenir les informations de Metal3DP
Brochure du produit
Obtenir les derniers produits et la liste des prix
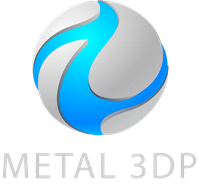
Poudres métalliques pour l'impression 3D et la fabrication additive