CuSn3P7 alliage de cuivre soudage
Table des matières
Avez-vous déjà été confronté à un projet exigeant une soudure en alliage de cuivre à la fois très résistante et semblable à une brasure ? Ne cherchez pas plus loin que CuSn3P7cuSn3P7 est un alliage de bronze phosphoreux qui fait fureur dans le monde du soudage. Mais qu'est-ce qui rend le CuSn3P7 si spécial et comment se situe-t-il par rapport aux autres options de soudage ? Attachez votre ceinture, car nous sommes sur le point de plonger dans le monde fascinant du soudage des alliages de cuivre CuSn3P7 !
la puissance du CuSn3P7
CuSn3P7, également connu sous le nom de CDA 725 ou CWB2, est un alliage cuivre-étain-phosphore spécifiquement formulé pour les applications de soudage. Sa composition unique, composée d'environ 9,0 % d'étain (Sn) et de 7,0 % de phosphore (P) en poids, lui confère un mélange remarquable de propriétés. Imaginez un alliage de cuivre ayant la résistance et la maniabilité de l'acier, mais la fluidité et les caractéristiques de brasage de la soudure à l'argent. C’est l’essence du CuSn3P7 !
Voici un tableau résumant les principaux détails du soudage de l'alliage de cuivre CuSn3P7 :
Fonctionnalité | Description |
---|---|
Composition de l'alliage | Cu (base), 9,0% Sn, 7,0% P |
Gamme de points de fusion | 621°C – ; 800°C (1150°F – ; 1472°F) |
Processus de soudage | Soudage à l'arc en tungstène (GTAW), soudage par faisceau laser (LBW) |
Solidité des articulations | Élevée, comparable à certains aciers |
Caractéristiques du brasage | Excellent écoulement et action capillaire |
Résistance à la corrosion | Modéré, similaire au cuivre |
Comme vous pouvez le constater, le CuSn3P7 constitue une proposition convaincante pour les soudeurs à la recherche d'une solution d'assemblage polyvalente et robuste. Mais comment cela se traduit-il dans les applications du monde réel ? Explorons-le !
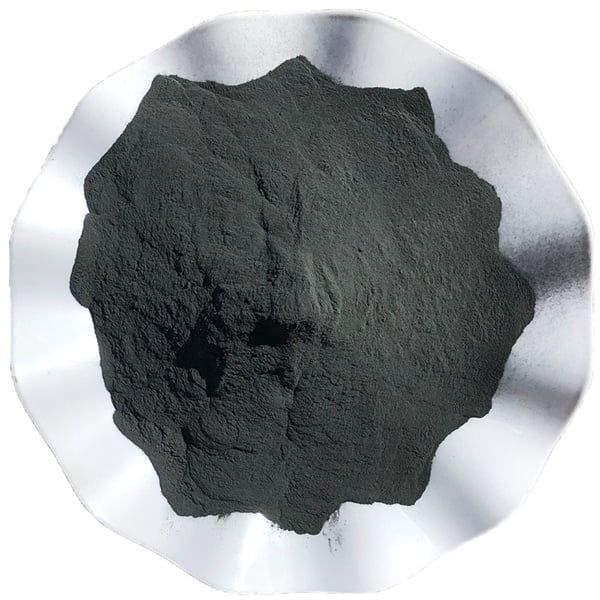
le potentiel de CuSn3P7
Le CuSn3P7 se distingue dans diverses applications où une résistance élevée, une bonne conductivité électrique et des propriétés de brasage sont recherchées. En voici quelques exemples :
- Échangeurs de chaleur : Le CuSn3P7 excelle dans l'assemblage des tubes et des feuilles de cuivre utilisés dans les échangeurs de chaleur en raison de son excellente conductivité thermique et de sa capacité à résister à des températures élevées.
- Composants électriques : La bonne conductivité électrique du CuSn3P7 permet de souder des barres omnibus, des connecteurs et d'autres composants électriques.
- Applications automobiles : Des radiateurs aux systèmes d'échappement, le CuSn3P7 est utilisé dans les applications automobiles en raison de sa capacité à supporter les cycles thermiques et les vibrations.
- Plomberie et réfrigération : La bonne usinabilité de l'alliage et sa résistance à la fissuration par brasage le rendent idéal pour l'assemblage de tuyaux et de raccords en cuivre dans les systèmes de plomberie et de réfrigération.
- Assemblage de métaux dissemblables : Le CuSn3P7 agit comme un pont entre des métaux dissemblables tels que le cuivre et l'acier, offrant un joint solide et fiable.
Ce n'est qu'un aperçu du vaste potentiel du CuSn3P7. Sa combinaison unique de propriétés en fait un outil précieux pour les soudeurs de diverses industries.
Poudres métalliques pour le soudage du CuSn3P7
Alors que les techniques de soudage traditionnelles dominent l'assemblage du CuSn3P7, la fabrication additive métallique (MAM) gagne du terrain. C'est ici qu'entre en jeu une gamme variée de poudres métalliques, chacune offrant des avantages distincts :
1. AMPCos 725 : Cette poudre de cuivre-étain-phosphore atomisée au gaz présente une excellente fluidité et densité de tassement, idéale pour les applications de soudage par faisceau laser.
2. Höganäs AM CuSn7P3 : Cette poudre atomisée à l'eau constitue une option rentable pour le soudage du CuSn3P7, offrant une bonne imprimabilité et de bonnes propriétés mécaniques.
3. Sandvik Osprey CuSn7P3 : Cette poudre de haute pureté, atomisée au gaz, garantit des performances constantes et une porosité minimale dans les soudures CuSn3P7 produites par MAM.
4. LPW CuSn7P7 : Cette poudre optimisée pour le laser, développée par LPW Technology, présente des caractéristiques d'absorption laser supérieures pour un soudage par faisceau laser efficace et précis du CuSn3P7.
5. Solutions SLM CuSn7P3 : Conçue pour les procédés de fusion sélective par laser (SLM), cette poudre de SLM Solutions garantit un écoulement optimal de la poudre et minimise les éclaboussures lors de la fabrication additive de CuSn3P7.
6. Elementum Specialty Materials CuSn7P3 : Ce fabricant réputé propose une option de poudre CuSn3P7 fiable avec une composition chimique et une distribution granulométrique cohérentes.
7. Fabrication additive Carpenter CP7: Cette poudre donne la priorité à la haute résistance et à la résistance aux fissures, ce qui la rend appropriée pour les soudures CuSn3P7 dans les applications exigeantes.
8. Poeton CuSn7P3: Cette poudre, qui permet d'obtenir une microstructure fine et uniforme, confère des propriétés mécaniques supérieures aux composants CuSn3P7 fabriqués par MAM.
9. Voxeljet CuSn7: Optimisée pour la fabrication additive par jet de liant, cette poudre permet d'obtenir des géométries complexes de pièces en CuSn3P7 avec une bonne précision dimensionnelle.
Choisir la bonne poudre métallique :
Le choix de la poudre métallique idéale dépend de plusieurs facteurs. Prenez en compte l'application spécifique, les propriétés de soudure souhaitées, le procédé MAM choisi et les contraintes budgétaires. Voici un aperçu de ces facteurs pour vous aider à prendre votre décision :
- Compatibilité des processus : Veillez à ce que la poudre corresponde à la technologie MAM choisie (fusion par faisceau laser, projection de liant, etc.).
- Taille et distribution des particules : Une distribution granulométrique bien définie favorise une fluidité optimale et minimise les problèmes tels que les éclaboussures pendant le processus de soudage.
- Composition chimique : Optez pour des poudres dont la composition précise correspond à l'alliage CuSn3P7 souhaité pour obtenir des propriétés de soudage prévisibles.
- Fluidité : Les poudres ayant une excellente fluidité garantissent un processus de dépôt homogène et régulier pendant le MAM.
- Sphéricité : Les particules sphériques se tassent généralement mieux et permettent d'obtenir des soudures plus denses avec une meilleure résistance mécanique.
N'oubliez pas qu'il est essentiel de consulter des fournisseurs de poudres métalliques et des fabricants d'équipements MAM réputés pour identifier la poudre la mieux adaptée à votre projet spécifique de soudage du CuSn3P7.
Spécifications, tailles, qualités et normes
Spécifications :
CuSn3P7 le soudage respecte généralement les spécifications suivantes :
- ASTM B189 : Standard Specification for wrought copper and copper-alloy sheet for building construction (Spécification standard pour les feuilles de cuivre et d'alliage de cuivre corroyées pour la construction de bâtiments).
- AWS A5.7 : Spécification pour les métaux d'apport pour le brasage. (Bien que le CuSn3P7 relève de la classification du brasage, ses propriétés vont au-delà du brasage traditionnel)
Tailles et qualités :
Les poudres métalliques pour le soudage du CuSn3P7 sont généralement disponibles dans différentes gammes de tailles de particules, adaptées aux différents procédés MAM. Les gammes de tailles les plus courantes sont les suivantes :
- 15-45 microns (µm)
- 25-50 µm
- 45-100 µm
La désignation spécifique de la qualité des poudres CuSn3P7 peut varier selon le fabricant. Toutefois, la composition chimique respecte généralement la valeur nominale de 9 % de Sn et de 7 % de P en poids.
Normes :
À l'heure actuelle, il n'existe pas de norme unique et universellement reconnue pour les poudres métalliques CuSn3P7 utilisées dans la MAM. Cependant, les fabricants adhèrent souvent aux normes industrielles pour les poudres de fabrication additive métallique, telles que :
- ASTM F3049 : Spécification standard pour les poudres métalliques utilisées dans les processus de fabrication additive.
- ISO/ASTM 52900 : Fabrication additive - Poudres métalliques - Spécification et qualification des poudres pour la fusion par faisceau laser.
Ces normes fournissent des lignes directrices pour les caractéristiques des poudres telles que la composition chimique, la distribution de la taille des particules, la fluidité et la densité apparente.
Fournisseurs et prix
Plusieurs fournisseurs de poudres métalliques réputés proposent des poudres CuSn3P7 pour les applications MAM. En voici quelques exemples notables :
- AMPCos
- Höganäs
- Sandvik Osprey
- Technologie LPW
- Solutions SLM
- Matériaux de spécialité Elementum
- XKEM Orchidée
- Fabrication additive Carpenter
- Poeton
- Voxeljet
Le prix des poudres métalliques CuSn3P7 peut varier en fonction du fournisseur, de la quantité de poudre, de la taille des particules et des certifications souhaitées. En général, il faut s'attendre à un coût plus élevé que celui des consommables de soudage traditionnels en raison de la nature spécialisée de la poudre et du processus MAM lui-même.
Trouver le bon fournisseur implique :
- Recherche de la réputation et de l'expérience des fournisseurs de poudres CuSn3P7.
- Obtenir des devis et comparer les prix en fonction de vos besoins spécifiques.
- Se renseigner sur les certifications disponibles et les procédures de contrôle de la qualité.
- S'assurer que le fournisseur offre une assistance technique pour le dépannage et l'orientation de l'application.
En évaluant soigneusement ces facteurs, vous pouvez vous assurer d'une source fiable de poudre métallique CuSn3P7 pour vos projets MAM.
Avantages et limites : Peser le pour et le contre
Avantages du soudage de l'alliage de cuivre CuSn3P7 :
- Haute résistance : Les soudures en CuSn3P7 présentent une résistance impressionnante, rivalisant avec certains aciers dans certaines applications.
- Excellentes caractéristiques de brasage : L'alliage présente une fluidité et une capillarité supérieures, ce qui permet d'obtenir des joints solides et étanches.
- Bonne conductivité électrique : Le CuSn3P7 conserve un degré significatif de conductivité électrique, ce qui le rend approprié pour l'assemblage de composants électriques.
- Assemblage de métaux dissemblables : Le CuSn3P7 agit comme un pont entre des métaux dissemblables tels que le cuivre et l'acier, offrant un joint robuste.
- Facilité de mise en œuvre : L'alliage présente une bonne aptitude au façonnage, ce qui permet de l'usiner ou de le former après soudage si nécessaire.
- Résistance à la corrosion : Sans être exceptionnel, le CuSn3P7 offre une résistance modérée à la corrosion, similaire à celle du cuivre, et convient à divers environnements.
- Compatibilité avec le soudage laser : Le CuSn3P7 excelle dans le soudage par faisceau laser (LBW) en raison de ses bonnes caractéristiques d'absorption du laser.
Limites du soudage de l'alliage de cuivre CuSn3P7 :
- Coût : Par rapport aux consommables de soudage traditionnels, les poudres métalliques CuSn3P7 et les procédés MAM peuvent être plus coûteux.
- Applications limitées : En raison de ses propriétés spécifiques, le CuSn3P7 n'est pas forcément le choix idéal pour toutes les applications. Une sélection rigoureuse du matériau est cruciale.
- Complexité des processus : La fabrication additive de métaux nécessite un équipement et une expertise spécialisés par rapport aux techniques de soudage conventionnelles.
- Contrôle de la porosité : La gestion de la porosité dans les soudures CuSn3P7 produites par MAM nécessite une optimisation du processus et un contrôle des paramètres appropriés.
- Fumée : Pendant le LBW de CuSn3P7, des fumées peuvent apparaître en raison de la présence de phosphore. Une ventilation adéquate est essentielle.
Prendre une décision en connaissance de cause :
Il est essentiel de comprendre ces avantages et ces limites pour déterminer si CuSn3P7 le soudage d'alliages de cuivre est la solution la plus adaptée à votre projet. Avant de prendre une décision, tenez compte de facteurs tels que la résistance requise du joint, la compatibilité avec les métaux de base, les contraintes budgétaires et l'expertise disponible.
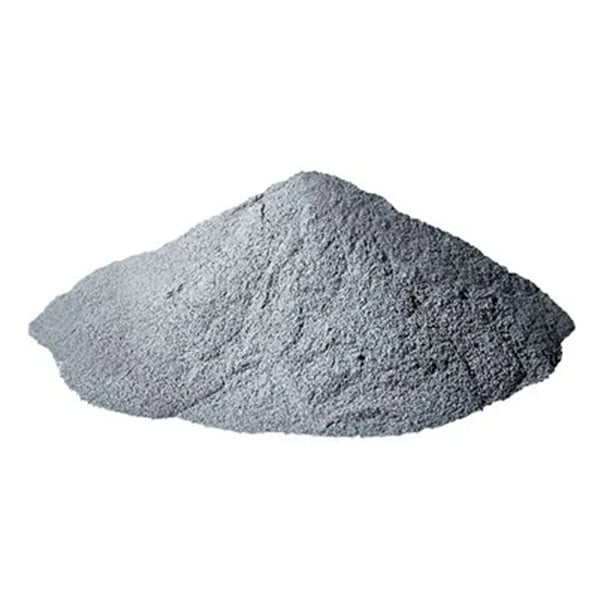
FAQ
Voici quelques questions fréquemment posées sur le soudage de l'alliage de cuivre CuSn3P7, auxquelles il est répondu de manière claire et informative :
Q : Quelles sont les principales différences entre le soudage du CuSn3P7 et le brasage traditionnel ?
R : Bien que le CuSn3P7 présente des caractéristiques similaires à celles du brasage avec un excellent écoulement, il offre une résistance des joints nettement supérieure à celle des charges de brasage traditionnelles. Les soudures en CuSn3P7 conviennent donc mieux aux applications exigeant des connexions à la fois solides et étanches.
Q : Le CuSn3P7 peut-il être utilisé pour souder d'autres métaux que le cuivre ?
R : Le CuSn3P7 trouve des applications dans l'assemblage de métaux dissemblables, en particulier entre le cuivre et l'acier. Toutefois, sa compatibilité avec d'autres métaux peut nécessiter des essais et des qualifications pour garantir des résultats optimaux.
Q : Quelles sont les précautions à prendre lors du soudage du CuSn3P7 ?
R : Comme pour tout processus de soudage, il est essentiel de porter un équipement de protection individuelle (EPI) approprié, notamment un casque de soudage, des gants et un appareil respiratoire (en particulier pendant le soudage à l'arc en raison des fumées potentielles). Veillez à ce qu'une ventilation adéquate soit en place pour évacuer les fumées de soudage.
Q : Le CuSn3P7 est-il une nouvelle technologie de soudage ?
R : Si le CuSn3P7 existe depuis un certain temps, son application dans la fabrication additive métallique est relativement récente. À mesure que la technologie MAM continue d'évoluer, le CuSn3P7 devrait trouver des applications encore plus larges dans diverses industries.
Q : Où puis-je en savoir plus sur le soudage de l'alliage de cuivre CuSn3P7 ?
R : Plusieurs sources peuvent fournir des informations complémentaires sur le soudage du CuSn3P7. Les fournisseurs de poudres métalliques réputés proposent souvent des fiches techniques et des guides d'application spécifiques à leurs poudres CuSn3P7. En outre, les associations industrielles et les instituts de recherche peuvent publier des articles ou des études sur ce sujet.
Partager sur
MET3DP Technology Co. est un fournisseur de premier plan de solutions de fabrication additive dont le siège se trouve à Qingdao, en Chine. Notre société est spécialisée dans les équipements d'impression 3D et les poudres métalliques de haute performance pour les applications industrielles.
Articles connexes
À propos de Met3DP
Mise à jour récente
Notre produit
CONTACTEZ-NOUS
Vous avez des questions ? Envoyez-nous un message dès maintenant ! Nous répondrons à votre demande avec toute une équipe dès réception de votre message.
Obtenir les informations de Metal3DP
Brochure du produit
Obtenir les derniers produits et la liste des prix
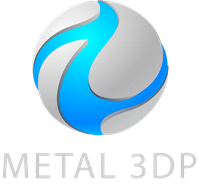
Poudres métalliques pour l'impression 3D et la fabrication additive