3D Printing Drone Arms with Aluminum Alloys
Table des matières
Introduction: Revolutionizing Drone Performance with 3D Printed Aluminum Arms
The drone industry, encompassing Unmanned Aerial Vehicles (UAVs) and Unmanned Aircraft Systems (UAS), is experiencing explosive growth, transforming sectors from cinematography and logistics to agriculture and defense. At the heart of every high-performance drone lies a critical structural component: the drone arm. These arms extend from the main body, providing mounting points for motors, propellers, and often housing intricate wiring and sensors. Their design directly impacts flight stability, maneuverability, payload capacity, and overall endurance. As drone applications become increasingly sophisticated and demanding, traditional manufacturing methods often struggle to keep pace with the need for lighter, stronger, and more complex arm designs. This is where the transformative power of fabrication additive métallique, commonly known as metal Impression 3D, enters the picture, particularly utilizing advanced aluminum alloys like AlSi10Mg and the high-performance Scalmalloy®.
Historically, drone arms were predominantly crafted using methods like CNC machining from billet aluminum or carbon fiber composites, or sometimes injection molding for mass-market consumer drones. While effective, these methods present limitations. CNC machining, although precise, can be subtractive and generate significant material waste, especially when creating complex, weight-optimized geometries. Carbon fiber composites offer excellent stiffness-to-weight ratios but can be labor-intensive to manufacture, difficult to repair, and may involve complex tooling for intricate shapes. Injection molding requires expensive molds, making it unsuitable for low-to-medium volume production or customized designs. The quest for enhanced performance – longer flight times, heavier payloads, increased durability, and greater design integration – necessitates a manufacturing paradigm shift.
Metal 3D printing offers a compelling solution, enabling the production of drone arms with unprecedented levels of design freedom and structural efficiency. By building parts layer by layer directly from digital models, AM eliminates many constraints imposed by traditional techniques. Engineers can now leverage powerful tools like topology optimization and generative design to create organically shaped, skeletal drone arms that place material only where it’s structurally required. This results in significant weight reduction without compromising strength or stiffness – a critical factor influencing battery life and payload capability. Imagine drone arms with internal lattice structures, optimized cooling channels for motors, or integrated mounting points for sensors, all produced as a single, monolithic part. This level of integration reduces assembly complexity, minimizes potential failure points, and streamlines the supply chain for drone component suppliers and manufacturers.
The choice of material is paramount, and aluminum alloys have long been favored in aerospace applications due to their favorable strength-to-weight ratio and corrosion resistance. Metal AM brings two exceptional aluminum-based candidates to the forefront for drone arm production:
- AlSi10Mg : A widely adopted aluminum-silicon-magnesium alloy known for its excellent printability, good mechanical properties, thermal conductivity, and corrosion resistance. It represents a robust and cost-effective solution for a broad range of drone applications.
- Scalmalloy®: A patented high-performance aluminum-magnesium-scandium-zirconium alloy specifically developed for additive manufacturing. It boasts mechanical properties comparable to high-strength aluminum alloys (like 7000 series) and even approaches those of some titanium grades, offering exceptional strength, ductility, and fatigue resistance. This makes it ideal for the most demanding UAV manufacturing solutions, particularly in aerospace, defense, and high-performance racing drones where maximizing strength while minimizing weight is critical.
Des entreprises comme Met3dp are at the vanguard of this manufacturing revolution. Headquartered in Qingdao, China, Met3dp specializes in providing comprehensive additive manufacturing solutions, encompassing industry-leading metal 3D printing equipment and a diverse portfolio of high-performance metal powders. With deep expertise collective expertise in metal AM, Met3dp leverages advanced powder production techniques like gas atomization and Plasma Rotating Electrode Process (PREP) to ensure the highest quality spherical metal powders – the foundation for printing dense, reliable, high-performance drone arms. Their commitment to “industry-leading print volume, accuracy and reliability” makes them a trusted partner for businesses seeking to implement cutting-edge aerospace-grade aluminum printing for mission-critical drone components. By embracing metal AM with advanced aluminum alloys, drone manufacturers and suppliers can unlock new levels of performance, innovation, and market competitiveness.
Key Applications and Industries Driving Demand for Advanced Drone Arms
The proliferation of drones across various industries is fueling an insatiable demand for components that push the boundaries of performance, reliability, and efficiency. 3D printed aluminum drone arms, offering bespoke designs, lightweight strength, and rapid production capabilities, are uniquely positioned to meet the diverse and often stringent requirements of these burgeoning sectors. Understanding these applications highlights why advanced manufacturing techniques and materials like AlSi10Mg and Scalmalloy® are becoming indispensable for industrial drone components et commercial UAV parts wholesale suppliers.
Here’s a breakdown of key industries and their specific needs for advanced drone arms:
1. Aerospace & Defense:
- Applications : Intelligence, Surveillance, and Reconnaissance (ISR), border patrol, target acquisition, tactical support, drone swarms, communication relays.
- Arm Requirements: Extreme durability and resilience for harsh operating conditions, high strength-to-weight ratio for extended flight times (loitering capability) and significant payload capacity (advanced sensors, communication equipment, munitions), low observability characteristics (potentially integrated into arm design), resistance to vibration and fatigue, high reliability for mission-critical operations. Scalmalloy® is often preferred here due to its superior strength and fatigue life.
- Avantage AM : Ability to create highly optimized, lightweight yet robust structures, integrate complex sensor housings or wiring channels directly into the arm, rapid prototyping of mission-specific designs, on-demand production of spare parts in remote locations.
2. Agriculture (Precision Farming):
- Applications : Crop monitoring (NDVI imaging), field mapping, pest detection, targeted spraying/seeding, livestock monitoring.
- Arm Requirements: Stability for carrying sensitive cameras and sensors, durability for operation in dusty or damp environments, sufficient payload capacity for spray tanks or sensor packages, cost-effectiveness for wider adoption. AlSi10Mg often provides an excellent balance of performance and cost.
- Avantage AM : Customization for specific sensor or equipment mounts, optimized designs for vibration damping ensuring clear imagery, potential for integrated fluid channels for spraying applications, faster development cycles for new agricultural drone models.
3. Cinematography & Photography:
- Applications : Aerial filming for movies, commercials, documentaries, real estate photography, event coverage.
- Arm Requirements: Exceptional stability and vibration damping to ensure smooth, cinematic footage, ability to carry high-end camera gimbals and lenses (significant payload), potentially aesthetic design considerations, quiet operation (design influencing airflow).
- Avantage AM : Highly customized arm geometries optimized for specific camera/gimbal setups, integrated vibration damping features using complex internal structures (lattices), lightweighting to maximize flight time during shoots, rapid creation of specialized rigs.
4. Logistics & Delivery:
- Applications : Last-mile package delivery, medical supply transport (blood, vaccines), inter-site logistics within large facilities.
- Arm Requirements: High payload capacity relative to drone size, robustness for frequent take-offs and landings, potentially integrated locking mechanisms or package interfaces, aerodynamic efficiency for speed and range, reliability for safe operation in populated areas. Both AlSi10Mg and Scalmalloy® can be viable depending on the payload and range requirements.
- Avantage AM : Design optimization for maximum payload efficiency, integration of complex mounting or delivery mechanisms, ability to rapidly iterate designs based on operational feedback, potential for part consolidation reducing weight and assembly time.
5. Infrastructure Inspection:
- Applications : Inspecting bridges, wind turbines, power lines, pipelines, railways, building facades, cell towers.
- Arm Requirements: Stability in potentially windy conditions, ability to carry high-resolution cameras, thermal imagers, or LiDAR scanners, maneuverability to navigate complex structures, durability for industrial environments.
- Avantage AM : Custom arm lengths and configurations for specific inspection tasks, integration of sensor mounts providing optimal viewing angles, robust designs capable of withstanding environmental factors, rapid replacement part availability reducing downtime for critical inspection services.
6. Emergency Services & Public Safety:
- Applications : Search and rescue (SAR), disaster assessment, situational awareness during fires or incidents, crowd monitoring, accident reconstruction.
- Arm Requirements: Reliability in adverse conditions (smoke, rain), ability to carry thermal cameras, spotlights, or communication devices, rapid deployment capability, robustness.
- Avantage AM : Ruggedized designs tailored for specific emergency equipment, lightweighting for portability and longer operation times in critical situations, fast production for urgent needs or replacing damaged units.
Across all these sectors, the ability to source high-quality, reliable components is crucial. Drone arm suppliers et custom drone manufacturing services leveraging metal AM can offer significant advantages over traditional supply chains. They can provide rapid prototyping services, cater to low-volume orders for specialized drones, and scale production for larger contracts. The use of high-quality powders, such as those produced by Met3dp using their advanced atomization techniques, ensures the material integrity required for these demanding applications. As drone technology continues to evolve, the complexity and performance requirements for components like drone arms will only increase, further solidifying the role of metal additive manufacturing as a key enabling technology.
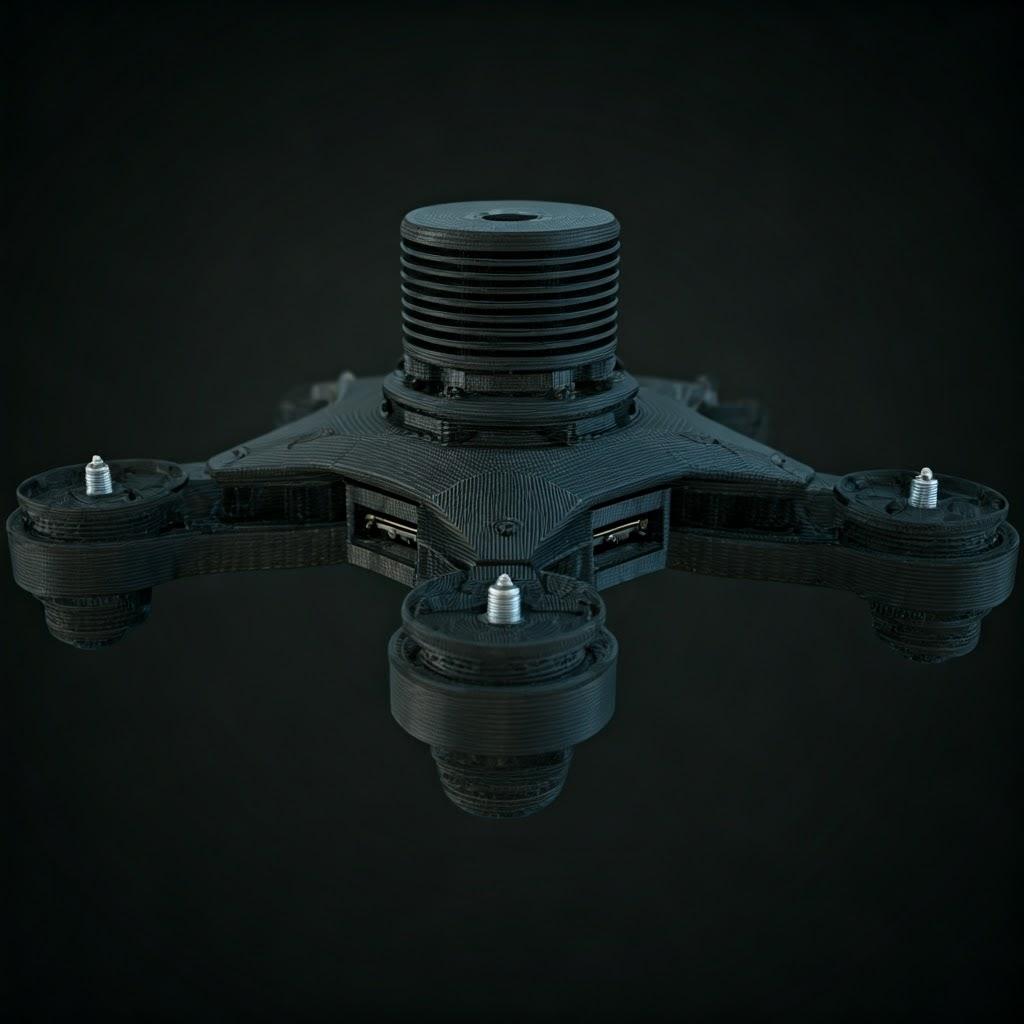
Why Choose Metal Additive Manufacturing for Drone Arm Production?
The decision to adopt metal additive manufacturing (AM) for producing drone arms isn’t just about embracing a novel technology; it’s a strategic choice driven by tangible engineering and business advantages, particularly when compared to traditional manufacturing methods. For drone manufacturers, drone component suppliers, and procurement managers evaluating production pathways, understanding these benefits is crucial for optimizing performance, cost, and time-to-market. Metal AM, especially using Powder Bed Fusion (PBF) technologies like Selective Laser Melting (SLM) or Direct Metal Laser Sintering (DMLS), offers a paradigm shift for creating complex, lightweight, and high-performance aluminum drone arms.
Let’s compare metal AM with conventional methods like CNC machining and injection molding for drone arm production:
Comparison: Metal AM vs. Traditional Methods for Drone Arms
Fonctionnalité | Metal AM (e.g., SLM/DMLS) | CNC Machining (Aluminum Billet) | Injection Molding (Glass-filled Nylon/Polymer) |
---|---|---|---|
Liberté de conception | Très élevé : Enables complex geometries, internal channels, lattice structures, topology optimization. | Modéré : Limited by tool access, difficult for deep pockets or internal features. Generates waste (subtractive). | High (Shape): Complex external shapes possible. Internal complexity limited by mold design. Requires draft angles. |
Allègement | Excellent : Ideal for topology optimization and lattice structures, placing material only where needed. | Bon : Can remove material, but optimization limited by process constraints. Often results in ‘over-engineered’ solid parts. | Good (Material): Polymers are inherently light, but may require thicker sections for strength. |
Matériau | High-performance metals (AlSi10Mg, Scalmalloy®, Titanium, etc.) | Standard wrought/billet alloys (e.g., 6061, 7075 Aluminum) | Thermoplastics (Nylon, ABS, Polycarbonate – often glass-filled for stiffness) |
Strength/Stiffness | High to Very High: Especially with Scalmalloy®. Near-net shape properties can rival wrought materials with proper processing. | Haut : Dependent on alloy (e.g., 7075 is very strong). Well-understood material properties. | Low to Moderate: Significantly lower than metals, even when fiber-reinforced. |
Vitesse de prototypage | Very Fast: Direct from CAD, no tooling needed. Ideal for rapid iteration. | Modéré : Requires programming and setup, but no hard tooling. | Very Slow: Requires expensive mold design and fabrication (weeks/months). |
Volume de production | Ideal for Low-to-Medium: Cost-effective for prototypes, custom parts, and series production up to thousands. | Suitable for Low-to-High: Economical from single parts to large runs, but cost per part less sensitive to volume than molding. | Ideal for High Volume: Lowest cost per part at very high volumes (>10,000s) due to tooling amortization. Very expensive for low volumes. |
Personnalisation | Excellent : Each part can be unique with no extra cost. | Possible: Requires reprogramming for each variation. | Very Poor: Requires new mold or inserts for modifications. |
Coût de l'outillage | Aucun | Faible : Cutting tools, fixtures. | Très élevé : Injection molds are complex and costly. |
Déchets matériels | Faible : Unfused powder is recyclable. Supports generate minimal waste. | Haut : Subtractive process removes significant material. | Faible : Minimal waste (runners/sprues). |
Lead Time (Initial) | Short: Days to weeks. | Modéré : Days to weeks. | Very Long: Weeks to months (mold production). |
Consolidation partielle | Excellent : Multiple components can be integrated into one print. | Limitée : Assembly of multiple machined parts often required. | Bon : Can integrate features, but limited by mold complexity. |
Exporter vers les feuilles
Key Advantages of Metal AM for Drone Arms:
- Liberté de conception inégalée : This is arguably the most significant advantage. AM liberates designers from the constraints of traditional manufacturing.
- Optimisation de la topologie : Software algorithms sculpt the arm, removing material from low-stress areas while maintaining structural integrity, leading to drastically lighter parts impossible to machine conventionally.
- Structures en treillis : Internal lattices can provide excellent stiffness and vibration damping with minimal weight.
- Canaux internes : Cooling channels for motors or conduits for wiring can be seamlessly integrated within the arm’s structure.
- Consolidation partielle : Motor mounts, landing gear interfaces, sensor brackets, and the arm structure itself can potentially be printed as a single, complex component. This reduces part count, assembly time, weight, and potential points of failure – a huge benefit for rapid prototyping UAV components and final production.
- Significant Lightweighting: For drones, every gram saved translates to longer flight times or increased payload capacity. Metal AM, combined with topology optimization and materials like AlSi10Mg or the exceptionally light-yet-strong Scalmalloy®, enables the creation of drone arms with superior strength-to-weight ratios compared to traditionally manufactured counterparts.
- Prototypage rapide et itération : Need to test a new arm design or integrate a different sensor? With AM, revised CAD models can be printed and tested within days, dramatically accelerating the development cycle compared to waiting weeks or months for new tooling or complex machining setups. This agility is crucial in the fast-evolving drone market.
- Personnalisation et production à la demande : AM is economically viable for producing small batches or even single, unique drone arms. This is ideal for specialized drone applications, replacement parts (digital inventory), or offering customized solutions to clients without incurring massive tooling costs. Custom drone arm manufacturing becomes highly feasible.
- Supply Chain Efficiency: Printing parts on demand reduces the need for large inventories. It also allows for decentralized manufacturing, potentially printing parts closer to the point of need. This enhances supply chain resilience, a critical factor for industries like defense and logistics.
- Matériaux haute performance : AM allows the use of advanced alloys like Scalmalloy®, specifically designed for the layer-by-layer process, unlocking performance levels that might be difficult or impossible to achieve with standard billet materials used in CNC machining. Companies like Met3dp, with their expertise in both standard and advanced alloy powders and matching méthodes d'impression, ensure that the full potential of these materials is realized. Their advanced powder manufacturing systems guarantee the high sphericity and flowability needed for consistent, high-quality prints.
While CNC machining remains excellent for precision features and high-strength requirements where AM might need post-machining, and injection molding reigns supreme for mass-market, low-cost polymer parts, metal additive manufacturing occupies a vital space for high-performance, complex, customized, and rapidly developed drone arms. It provides engineers and drone component suppliers with the tools to innovate beyond traditional limitations, directly addressing the core challenges of modern UAV design.
Material Spotlight: AlSi10Mg and Scalmalloy® for High-Performance Drone Arms
The choice of material is fundamental to the performance, durability, and weight of a drone arm. While various materials can be used in additive manufacturing, aluminum alloys stand out for their combination of low density, good mechanical properties, and processability. Within the aluminum family, two materials have gained significant traction for 3D printed drone components: the workhorse AlSi10Mg and the high-performance Scalmalloy®. Understanding their distinct characteristics is key for engineers and AlSi10Mg drone parts suppliers ou Scalmalloy drone arm manufacturing specialists when selecting the optimal material for a specific application.
AlSi10Mg: The Reliable Workhorse
- Composition : Primarily Aluminum (Al), with significant additions of Silicon (Si, typically around 9-11%) and Magnesium (Mg, typically 0.2-0.45%). The silicon content improves the alloy’s fluidity and castability, which translates well to the melting and solidification process in Powder Bed Fusion AM. Magnesium contributes to strength through precipitation hardening during heat treatment.
- Key Properties (As-Printed & Heat Treated):
- Densité : Approximately 2.67 g/cm³ (Lightweight)
- Bon rapport résistance/poids : Offers a solid balance suitable for many applications.
- Excellente conductivité thermique : Beneficial for dissipating heat from motors mounted on the arms.
- Bonne résistance à la corrosion : Suitable for outdoor use and various environmental conditions.
- Soudabilité : Can be welded if needed, although AM often enables part consolidation.
- Excellente imprimabilité : Well-understood parameters, processes relatively easily in SLM/DMLS systems, making it widely available and cost-effective.
- Benefits for Drone Arms:
- Léger : Contributes directly to longer flight times and higher payload capacity.
- Rentable : Generally less expensive than high-performance alloys like Scalmalloy® or Titanium, making it suitable for a wide range of commercial and industrial drones.
- Good All-Around Performance: Provides sufficient strength and stiffness for many drone sizes and operational requirements.
- Mature Process: Printing parameters and post-processing (like heat treatment for T6 condition) are well-established, leading to reliable and repeatable results.
- Met3dp’s Capability: Met3dp’s expertise in producing high-quality gas atomized powders ensures optimal AlSi10Mg powder characteristics – high sphericity, low satellites, controlled particle size distribution, and good flowability. This translates to denser prints, better mechanical properties, and process reliability, making them a dependable supplier for standard aluminum alloy printing needs. Their focus on poudres métalliques de haute qualité is foundational to achieving excellent results with AlSi10Mg.
Scalmalloy®: The High-Performance Champion
- Composition : An aluminum alloy containing Magnesium (Mg), Scandium (Sc), and Zirconium (Zr). Developed by APWorks (an Airbus subsidiary), it’s specifically designed for the rigors of additive manufacturing. The Scandium addition creates fine precipitates that significantly increase strength and resistance to recrystallization at elevated temperatures.
- Key Properties (As-Printed & Heat Treated):
- Densité : Approximately 2.67 g/cm³ (Similar to AlSi10Mg, remarkably light for its strength)
- Rapport force/poids exceptionnel : Yield strength and ultimate tensile strength can approach or exceed those of some high-strength 7000 series aluminum alloys and even Grade 5 Titanium (Ti6Al4V) in certain conditions, but at a lower density.
- Excellent Ductility & Toughness: Unlike some very high-strength aluminum alloys, Scalmalloy® retains good elongation, making it less brittle and more resistant to impacts.
- High Fatigue Strength: Critically important for drone arms subject to constant vibration from motors and aerodynamic forces.
- Bonne résistance à la corrosion : Suitable for demanding environments.
- Stable at Moderately Elevated Temperatures: Retains properties better than conventional aluminum alloys at higher temperatures.
- Benefits for Drone Arms:
- Maximum Performance: Enables the lightest possible arm designs for a given strength requirement, pushing the boundaries of flight endurance and payload capacity.
- Extreme Durability: Ideal for drones operating in harsh conditions, high-G maneuvers (racing drones), or carrying heavy/sensitive payloads where structural integrity and fatigue resistance are paramount.
- Design Optimization Potential: Its high strength allows for even thinner walls and more aggressive topology optimization compared to AlSi10Mg.
- Met3dp’s Capability: Processing advanced alloys like Scalmalloy® requires precise control over printing parameters and powder quality. Met3dp’s investment in advanced powder production (Gas Atomization, PREP) and potentially advanced printing systems like Electron Beam Melting (SEBM), alongside Laser Powder Bed Fusion, demonstrates their capacity to handle these demanding materials. Offering Scalmalloy® showcases their position as a provider of cutting-edge aerospace aluminum powder distributor solutions and manufacturing capabilities for the most challenging applications.
Comparison Table: AlSi10Mg vs. Scalmalloy® (Typical Heat-Treated Properties)
Propriété | AlSi10Mg (état T6) | Scalmalloy® (traité thermiquement) | Unité | Significance for Drone Arms |
---|---|---|---|---|
Densité | ~2.67 | ~2.67 | g/cm³ | Both are lightweight; Scalmalloy® offers more strength per gram. |
Yield Strength (Rp0.2) | ~230 – 280 | ~450 – 520 | MPa | Higher value means more force before permanent deformation. |
Résistance ultime à la traction | ~330 – 430 | ~500 – 580 | MPa | Higher value means more force before fracture. |
Allongement à la rupture | ~6 – 10 | ~10 – 16 | % | Higher value indicates better ductility (less brittle). |
Résistance à la fatigue | Modéré | Très élevé | (variable) | Crucial for resisting vibrations from motors/propellers. |
Temp. de fonctionnement max. | ~150 | ~200 – 250 | °C | Scalmalloy® retains strength better at higher temperatures. |
Printability / Cost | Easier / Lower | More Demanding / Higher | – | Process maturity vs. performance trade-off. |
Typical Application | General Purpose, Industrial, Commercial Drones | Aerospace, Defense, High-Performance, Heavy-Payload Drones | – | Matches material capability to performance needs. |
Exporter vers les feuilles
Choosing the Right Material:
The selection between AlSi10Mg and Scalmalloy® depends heavily on the specific requirements of the drone and its application:
- Choisir AlSi10Mg quand :
- Cost-effectiveness is a primary driver.
- Good all-around performance is sufficient.
- Thermal dissipation is important.
- The drone operates under moderate load and environmental conditions.
- Choisir Scalmalloy® (alliage d'aluminium) quand :
- Maximum strength-to-weight ratio is critical (longest flight time, highest payload).
- High fatigue resistance is required due to vibration or high cycle loading.
- The drone operates in demanding environments or under extreme stress.
- The budget accommodates a higher-performance (and higher-cost) material.
Partnering with an experienced metal AM provider like Met3dp, who understands the nuances of processing both materials and can advise on the best choice based on design requirements and application specifics, is crucial for success. Their comprehensive solutions, spanning high-quality powders to advanced printing and application development, ensure that drone manufacturers can fully leverage the potential of these advanced aluminum alloys.
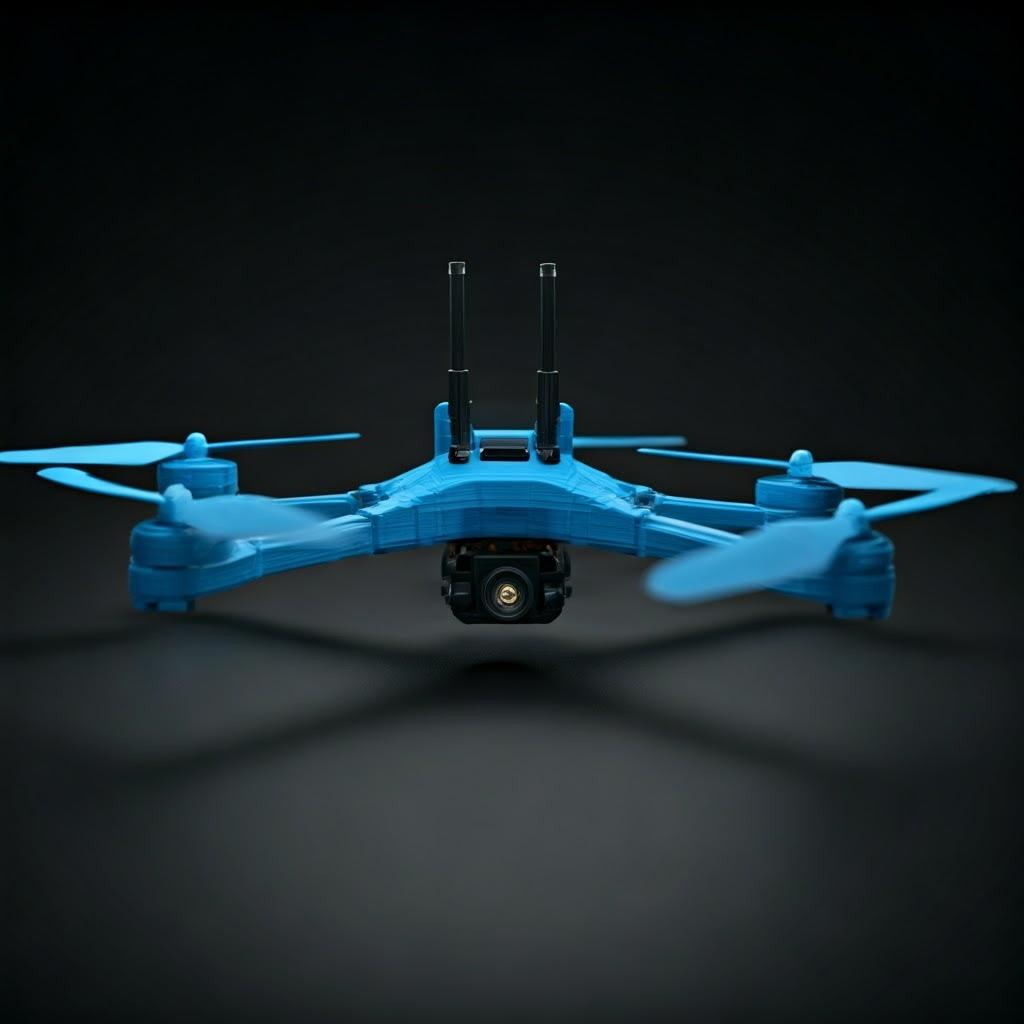
Design Considerations for Optimizing 3D Printed Drone Arms (DfAM)
Transitioning from traditional manufacturing to metal additive manufacturing (AM) for drone arms requires more than simply converting an existing CAD file. To truly harness the power of AM and achieve the desired benefits of lightweighting, strength, and functionality, engineers must embrace Design for Additive Manufacturing (DfAM) principles. DfAM is a mindset and a set of methodologies focused on designing parts specifically for the layer-by-layer building process, leveraging its unique capabilities while mitigating its constraints. Applying DfAM to drone arms, especially when using advanced aluminum alloys like AlSi10Mg or Scalmalloy®, can lead to significant performance gains and cost efficiencies, critical for DfAM drone components and staying competitive.
Here are key DfAM considerations for optimizing 3D printed drone arms:
1. Topology Optimization:
- Concept: This is perhaps the most impactful DfAM tool for drone arms. Using specialized software (e.g., nTopology, Altair Inspire, Ansys Discovery, Autodesk Fusion 360 Generative Design), engineers define load cases (motor thrust, landing impacts, aerodynamic forces), constraints (mounting points, keep-out zones), and optimization goals (minimize weight, maximize stiffness). The software then iteratively removes material from areas experiencing low stress, resulting in highly organic, load-path-optimized structures.
- Benefit for Drone Arms: Creates the lightest possible arm that still meets all structural requirements. The resulting skeletal or bio-inspired forms are often impossible or prohibitively expensive to produce using traditional subtractive methods like CNC machining. This directly translates to longer flight times and/or higher payload capacity.
- Implementation: Requires a good understanding of the expected forces acting on the arm during its operational lifecycle. The output often needs some smoothing or refinement for printability and aesthetics. Partnering with an AM service provider like Met3dp, which may offer About Met3dp design support or has experience with topology-optimized parts, can be highly beneficial.
2. Lattice Structures:
- Concept: Instead of solid infill, internal volumes can be filled with engineered lattice structures (e.g., honeycomb, gyroid, strut-based lattices). These periodic, repeating unit cells offer high stiffness and strength at significantly reduced weight compared to solid material. Different lattice types offer varying properties (e.g., isotropic vs. anisotropic stiffness, energy absorption).
- Benefit for Drone Arms: Further lightweighting beyond just external shape optimization. Can provide excellent vibration damping characteristics, crucial for stabilizing cameras or sensitive electronics. Can also improve buckling resistance in thin-walled structures.
- Implementation: Requires software capable of generating complex lattice geometries. Careful consideration must be given to cell size, beam thickness, and ensuring powder can be removed from internal cavities after printing (escape holes are essential). Scalmalloy®’s high strength often allows for thinner lattice struts, maximizing weight savings.
3. Part Consolidation:
- Concept: Leveraging AM’s ability to create complex geometries, multiple components that were previously manufactured separately and then assembled can be redesigned and printed as a single, monolithic part.
- Benefit for Drone Arms:
- Reduced Part Count: Simplifies inventory management and supply chains for UAV part suppliers.
- Eliminated Assembly Labor: Saves time and cost during drone construction.
- Reduced Weight: Eliminates fasteners (screws, bolts, rivets) and potentially overlapping material at joints.
- Increased Reliability: Fewer interfaces mean fewer potential points of failure (e.g., loosening screws due to vibration).
- Exemples : Integrating the motor mount, arm structure, parts of the landing gear attachment, and wiring channels into one printed piece.
- Implementation: Requires careful redesign considering the functions of all consolidated parts. Access for maintenance or component replacement needs to be considered if previously separate parts are now integrated.
4. Feature Integration:
- Concept: Adding functional features directly into the AM design that would be difficult or impossible otherwise.
- Benefit for Drone Arms:
- Internal Wiring Channels: Smooth, conformal channels protect wiring from damage and snagging, improving aerodynamics and aesthetics.
- Integrated Cooling Channels: Air or fluid channels can be designed around motor mounts to improve thermal management, allowing motors to run more efficiently or preventing overheating during demanding flights.
- Embedded Sensor Mounts: Precisely positioned and shaped mounting points for specific sensors (GPS, LiDAR, cameras).
- Vibration Damping Features: Designing specific geometries or incorporating lattice structures to absorb or isolate motor vibrations.
- Implementation: Requires careful CAD modeling. Internal channels need escape holes for powder removal. Wall thicknesses around features must ensure structural integrity.
5. Designing for Support Structures:
- Concept: Metal Powder Bed Fusion typically requires support structures for overhangs (usually features angled less than 45° from the build plate) and to anchor the part to the build plate, preventing warping. DfAM aims to minimize the need for these supports or make them easier to remove.
- Benefit for Drone Arms: Reduces print time, material consumption, and post-processing effort (support removal can be labor-intensive). Improves surface finish on down-facing surfaces.
- Implementation:
- Orientation : Selecting the optimal build orientation to minimize steep overhangs.
- Angles autoportants : Designing overhangs with angles greater than 45° where possible.
- Chamfers/Fillets: Replacing sharp horizontal overhangs with angled or curved transitions.
- Support Design: If supports are unavoidable, design them for minimal contact area (e.g., conical supports) and easy access for removal tools. Consider soluble or easily breakable support materials/structures if available.
6. Wall Thickness and Minimum Feature Size:
- Concept: AM processes have limitations on the minimum wall thickness and feature size they can reliably produce.
- Benefit for Drone Arms: Ensures structural integrity and printability. Avoids features that are too thin to resolve or handle post-processing.
- Implementation: Adhere to the guidelines provided by the AM machine manufacturer or service provider (e.g., Met3dp). Typical minimum wall thicknesses for aluminum PBF are around 0.4-0.8 mm, but designing slightly thicker (e.g., >1 mm) is often safer for structural parts like drone arms. Consider stress concentrations at thin sections.
7. Anisotropy Considerations:
- Concept: Due to the layer-by-layer build process, mechanical properties (especially strength and ductility) can sometimes vary slightly depending on the build direction (X, Y vs. Z).
- Benefit for Drone Arms: Ensures performance consistency and reliability by aligning the strongest build direction with the primary load paths.
- Implementation: Understand the anisotropic characteristics of the chosen material (AlSi10Mg or Scalmalloy®) as processed by the specific machine/parameters. Orient the drone arm in the build chamber to optimize properties for expected loads (e.g., building the arm vertically might maximize strength along its length). Post-processing like heat treatment can help homogenize properties.
By thoughtfully applying these DfAM principles, engineers can move beyond simply replicating existing drone arm designs and instead create truly optimized components that leverage the full potential of metal additive manufacturing. This collaborative approach, often involving close communication between the designer and the AM service provider, is key to achieving superior directives de conception de la fabrication additive results for demanding applications.
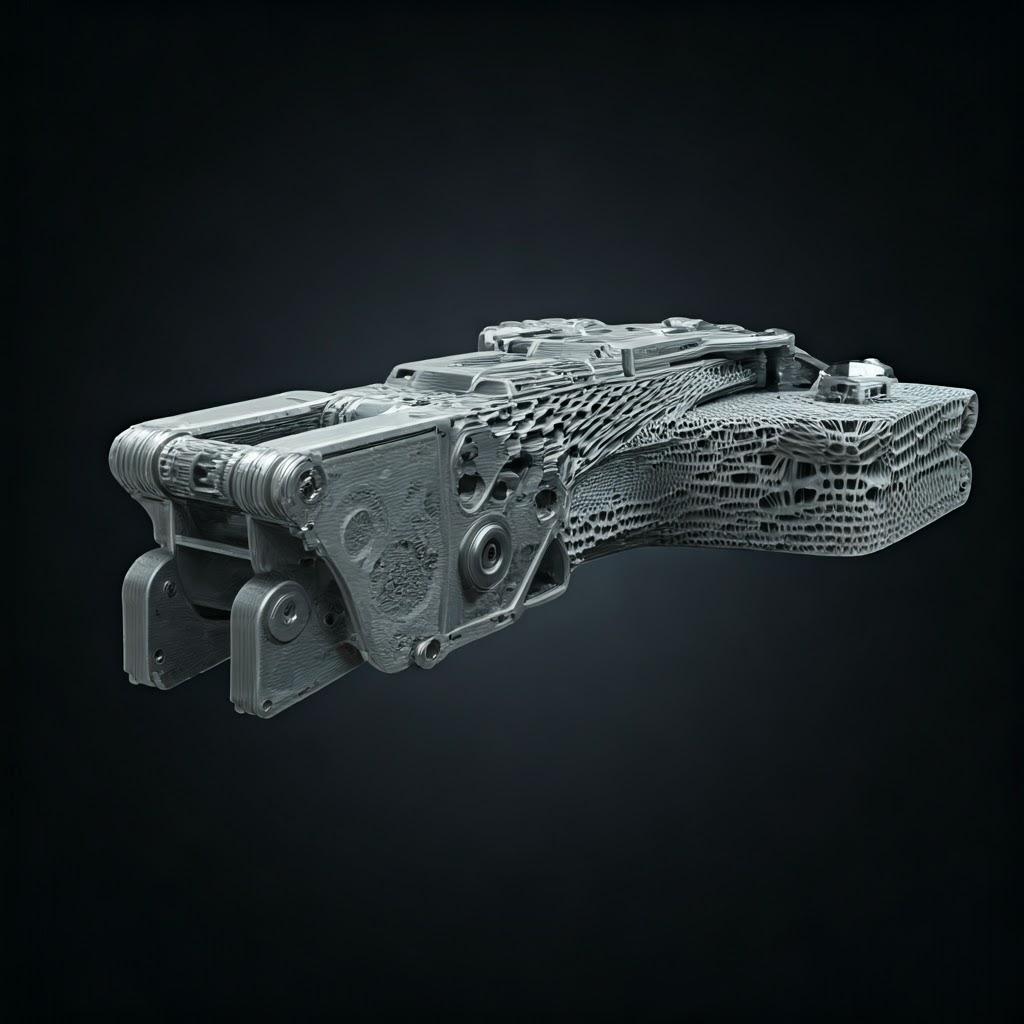
Precision Matters: Tolerance, Surface Finish, and Dimensional Accuracy in AM Drone Arms
While metal additive manufacturing offers unparalleled design freedom, stakeholders – particularly engineers and procurement managers dealing with precision drone component manufacturing – need a clear understanding of the achievable levels of precision. Tolerance, surface finish, and overall dimensional accuracy are critical factors influencing the fit, function, and assembly of 3D printed drone arms. While AM parts may not always match the ultra-tight tolerances of precision CNC machining straight off the printer, advanced systems and proper process control yield highly accurate components suitable for demanding applications, often supplemented by targeted post-processing.
1. Tolerance:
- Définition : Tolerance refers to the permissible limit or limits of variation in a physical dimension of a part.
- Achievable Levels: For metal Powder Bed Fusion (PBF) processes like SLM/DMLS used for aluminum alloys, typical achievable tolerances generally fall within the range of ±0,1 mm à ±0,3 mm (or ±0.004″ to ±0.012″) for smaller dimensions, and potentially ±0.1% to ±0.2% for larger dimensions. However, this is highly dependent on several factors:
- Part Size and Complexity: Larger parts or those with complex geometries are more susceptible to thermal distortion, potentially affecting tolerances.
- Matériau : Different alloys exhibit varying shrinkage and stress behaviors during printing (though AlSi10Mg and Scalmalloy® behave reasonably well).
- Étalonnage de la machine : Accuracy relies heavily on well-maintained and precisely calibrated AM systems, highlighting the importance of choosing a quality provider like Met3dp, known for “industry-leading print volume, accuracy and reliability.”
- Contraintes thermiques : Residual stresses built up during printing can cause minor warping or deviation.
- Stratégie de soutien : How the part is supported can influence its final dimensional accuracy.
- Orientation de la construction : Orientation can affect how thermal stresses accumulate.
- Meeting Tight Tolerances: For critical features requiring tolerances tighter than standard AM capabilities (e.g., bearing bores, motor mounting interfaces, press-fit locations), l'usinage CNC post-processus is typically employed. AM creates the near-net shape, and machining delivers the final precision exactly where needed. This hybrid approach combines the design freedom of AM with the precision of subtractive manufacturing.
2. Surface Finish (Roughness):
- Définition : Surface finish describes the texture of a surface, often quantified by the arithmetic average roughness (Ra).
- As-Printed Finish: The surface finish of PBF parts is inherently rougher than machined surfaces due to the partially melted powder particles adhering to the surface and the layer stepping effect.
- Typical Ra Values (Aluminum PBF): Generally range from 6 µm to 15 µm (240 µin to 600 µin) depending on orientation and parameters.
- Orientation Dependence: Surfaces parallel to the build plate (top surfaces) tend to be smoother, while vertical walls are moderately rough. Overhanging or down-facing surfaces supported by structures are typically the roughest, showing witness marks after support removal.
- Internal Surfaces: Internal channels or lattice structures will have a rougher, as-printed finish unless specifically targeted by post-processing (which can be difficult).
- Amélioration de l'état de surface : Several post-processing techniques can significantly improve the surface finish:
- Bead Blasting / Sandblasting: Creates a uniform, matte finish, removing loose powder. Ra values might improve slightly or become more consistent (e.g., 5-10 µm Ra).
- Tambourinage / Finition vibratoire : Uses abrasive media in a vibrating or rotating drum to smooth surfaces and edges. Can achieve smoother finishes (e.g., 1-5 µm Ra) but may slightly round sharp edges.
- Polissage : Can achieve very smooth, even mirror-like finishes (Ra < 0.8 µm or better) but is typically reserved for specific functional requirements or aesthetics due to cost and labor.
- Usinage CNC : Provides the smoothest and most controlled surface finish on specific features.
3. Dimensional Accuracy:
- Définition : Dimensional accuracy refers to how closely the final manufactured part conforms to the dimensions specified in the original CAD model. It encompasses both tolerance (feature size) and form (shape, flatness, concentricity, etc.).
- Ensuring Accuracy: Achieving high dimensional accuracy requires a holistic approach:
- Precise Machine Operation: Using high-quality, well-calibrated machines with closed-loop control systems.
- Paramètres d'impression optimisés : Fine-tuned laser power, scan speed, layer thickness, and hatch patterns specific to the material (AlSi10Mg or Scalmalloy®).
- Effective Thermal Management: Strategies to minimize thermal gradients and residual stress during the build (e.g., build plate heating, optimized scan strategies).
- Careful Post-Processing: Stress relief heat treatment is crucial to relieve internal stresses that could cause distortion after removal from the build plate. Support removal must be done carefully.
- Quality Control (QC) & Inspection: Rigorous inspection is vital. This can range from caliper/micrometer measurements for basic checks to advanced 3D scanning comparing the final part geometry against the original CAD model (creating color maps of deviations) and Coordinate Measuring Machines (CMM) for highly precise measurements of critical features. For high-integrity parts, Non-Destructive Testing (NDT) like CT scanning might be used to check for internal defects or porosity.
- Met3dp’s Commitment: A provider like Met3dp, emphasizing accuracy and reliability and equipped with advanced systems (potentially including SEBM printers known for lower residual stress, alongside laser systems) and comprehensive solutions, likely incorporates robust process control and QC measures to ensure high dimensional accuracy for demanding applications like tolérances d'impression 3D des métaux réalisables critical drone components.
In summary, while metal AM may require post-machining for features demanding sub-0.1 mm tolerances, its inherent accuracy is sufficient for many aspects of a drone arm’s geometry. Understanding the typical surface finish aluminum AM capabilities and planning for necessary post-processing and rigorous dimensional accuracy UAV parts inspection are key to successfully integrating 3D printed aluminum arms into high-performance drone assemblies.
Essential Post-Processing Steps for Aluminum Drone Arms
Producing a drone arm using metal additive manufacturing, whether with AlSi10Mg or Scalmalloy®, doesn’t end when the printer stops. The “green” part, fresh off the build plate, requires several crucial post-processing steps to achieve the desired mechanical properties, dimensional accuracy, surface finish, and overall functionality. These steps are an integral part of the AM workflow and must be factored into production planning, cost estimation, and lead time calculations for post-processing metal AM parts. Neglecting or improperly executing these steps can compromise the performance and reliability of the final component.
Here’s a breakdown of common and essential post-processing steps for 3D printed aluminum alloy drone arms:
1. Stress Relief / Heat Treatment:
- Objet : This is arguably the most critical post-processing step for metal PBF parts. The rapid heating and cooling cycles during printing induce significant residual stresses within the material. If not relieved, these stresses can cause warping or distortion when the part is cut from the build plate, and can negatively impact mechanical properties, particularly fatigue life. Heat treatment also optimizes the microstructure to achieve the desired strength, ductility, and hardness (e.g., reaching a T6 condition for AlSi10Mg).
- Processus : Typically involves heating the part (often while still attached to the build plate) in a controlled atmosphere furnace to a specific temperature, holding it there for a set duration (soaking), and then cooling it at a controlled rate. Specific cycles vary based on the alloy:
- AlSi10Mg : Often requires a solution treatment followed by artificial aging (e.g., solutionizing around 500-540°C, quenching, then aging around 150-170°C for several hours to achieve T6 properties). Stress relief might be a simpler cycle at lower temperatures (e.g., 250-300°C for a few hours) primarily to reduce distortion potential before removal from the plate.
- Scalmalloy®: Also requires specific heat treatment cycles (often involving aging) to develop its exceptional strength properties. Consult material supplier or experienced AM provider for optimal parameters.
- Importance : Essential for dimensional stability and achieving the target mechanical specifications listed in datasheets. Heat treatment AlSi10Mg and Scalmalloy® is standard practice for structural components.
2. Removal from Build Plate:
- Objet : Separating the printed drone arm(s) from the metal build plate they were fused to during printing.
- Processus : Typically done using Wire EDM (Electrical Discharge Machining) or a band saw. Wire EDM offers higher precision and potentially a smoother cut surface but is slower. Bandsawing is faster but less precise. Care must be taken to avoid damaging the parts.
3. Retrait des structures de support :
- Objet : Removing the temporary structures printed to support overhangs and anchor the part.
- Processus : Can range from manual breaking and cutting (using pliers, grinders, hand tools) to more automated methods. This can be labor-intensive and requires skill to avoid damaging the part surface. Designing supports for easy removal (DfAM principle) significantly simplifies this step. Witness marks or burrs left after support removal often need further finishing.
4. Cleaning / Powder Removal:
- Objet : Removing any trapped or partially sintered powder, especially from internal channels, lattice structures, or complex features.
- Processus : Typically involves compressed air blowing and potentially bead blasting or ultrasonic cleaning baths. Ensuring all powder is removed is crucial, as trapped powder can add weight and potentially compromise performance or cause issues in downstream processes. Escape holes designed into the part are vital for accessing internal cavities.
5. Finition de surface :
- Objet : Improving the surface texture for aesthetics, reducing friction, enhancing fatigue life (by removing surface imperfections), or preparing the surface for coating.
- Common Techniques for Drone Arms:
- Bead Blasting / Sandblasting: Most common method. Provides a uniform, non-directional matte finish. Effective at cleaning surfaces and removing minor imperfections. Different media types (glass beads, aluminum oxide) produce different finishes.
- Tambourinage / Finition vibratoire : Good for smoothing surfaces and deburring edges on multiple parts simultaneously. Can achieve lower Ra values than blasting but may slightly round sharp corners.
- Manual Grinding/Sanding: Used locally to remove support witness marks or smooth specific areas.
- Polissage : Generally overkill for drone arms unless specific aesthetic or functional requirements exist.
- Selection Criteria: Depends on the desired finish, cost, volume, and part geometry. Surface finishing drone components is often essential for a professional look and feel.
6. CNC Machining (If Required):
- Objet : Achieving very tight tolerances (typically < ±0.1 mm) on critical features, creating specific surface finishes, or generating features difficult to print accurately (e.g., precise bores, flat mating surfaces, tapped threads).
- Processus : The 3D printed part is fixtured in a CNC mill or lathe, and specific features are machined to final specifications. This hybrid AM + Machining approach is common for high-precision components.
- Considérations : Requires careful planning for workholding/fixturing the potentially complex AM part. Sufficient stock material must be included in the AM design on features intended for machining. CNC machining 3D printed aluminum requires expertise in handling near-net-shape parts.
7. Inspection and Quality Control (QC):
- Objet : Verifying that the finished drone arm meets all dimensional, material, and functional specifications.
- Processus : Includes visual inspection, dimensional checks (calipers, CMM, 3D scanning), material property verification (e.g., hardness testing), and potentially NDT (e.g., dye penetrant testing for surface cracks, CT scanning for internal defects) depending on the criticality of the component.
- Importance : Ensures reliability and safety, especially for aerospace, defense, or delivery drone applications.
8. Optional Coating/Anodizing:
- Objet : Enhancing corrosion resistance (especially in marine or harsh environments), improving wear resistance, providing electrical insulation, or adding color.
- Processus : Standard surface treatment processes like anodizing (Type II or Type III hardcoat for aluminum), chromate conversion coating, painting, or powder coating can be applied to finished aluminum AM parts.
- Considérations : Surface preparation (cleaning, potentially etching) is critical for good coating adhesion.
Successfully navigating these post-processing steps requires expertise and the right equipment. Partnering with a full-service metal AM provider like Met3dp, offering comprehensive solutions that may include or manage these critical finishing operations, ensures that the final 3D printed drone arms deliver on their performance promises.
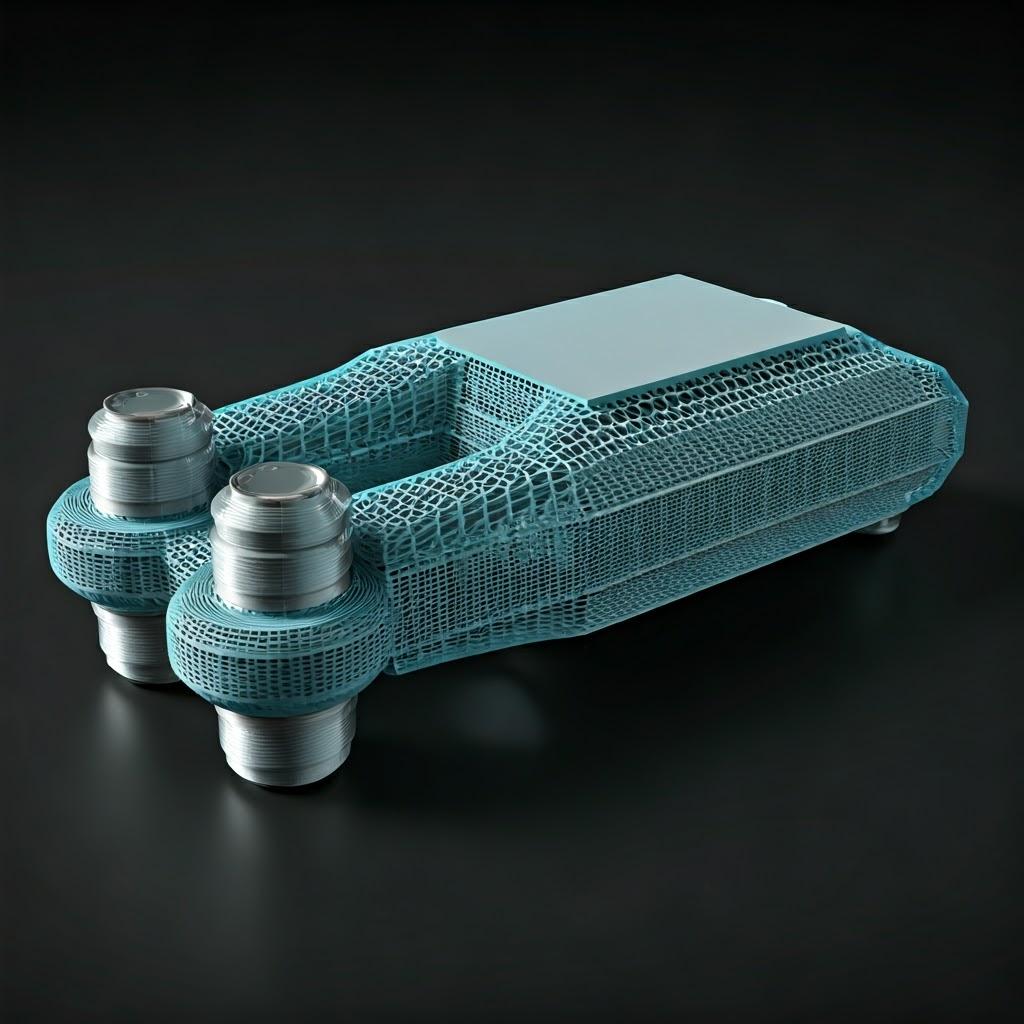
Navigating Common Challenges in 3D Printing Drone Arms (and Expert Solutions)
While metal additive manufacturing unlocks incredible potential for drone arm design and production, it’s not without its challenges. Understanding potential issues and knowing how to mitigate them is crucial for achieving consistent, high-quality results. Experience, robust process control, and high-quality materials are key to overcoming these hurdles. Here are some common challenges encountered when 3D printing aluminum drone arms and expert solutions, often employed by experienced providers like Met3dp:
1. Warping and Distortion:
- Défi: Parts curling up or distorting during the build or after removal from the build plate. This is caused by residual stresses resulting from the extreme thermal gradients inherent in the PBF process. Aluminum alloys, with their relatively high thermal expansion and conductivity, can be particularly susceptible.
- Solutions :
- Optimized Support Strategy: Using robust supports, strategically placed not just for overhangs but also to anchor the part firmly to the build plate and act as heat sinks. Experienced engineers design supports to counteract predicted stress patterns.
- Orientation de la construction : Orienting the part to minimize large, flat surfaces parallel to the build plate and to balance thermal mass distribution.
- Optimized Scan Strategy: Using specific laser scan patterns (e.g., island scanning, sectoring) to distribute heat more evenly and reduce localized stress buildup.
- Build Plate Heating: Maintaining an elevated temperature on the build plate reduces the thermal gradient between the molten pool and the surrounding material.
- Immediate Stress Relief: Performing a stress relief heat treatment cycle before removing the part from the build plate is often the most effective way to relax internal stresses and prevent distortion upon release. This is a standard procedure for preventing warping AM.
2. Support Removal Difficulty and Surface Quality:
- Défi: Supports can be difficult and time-consuming to remove, especially from complex internal geometries or delicate features. Removal can leave witness marks or rough surfaces on the part.
- Solutions :
- DfAM for Supports: Designing parts to be self-supporting (angles >45°) wherever possible. Using fillets instead of sharp overhangs.
- Conception optimisée du support : Using easily removable support types (e.g., thin-walled structures, conical points, patterned supports) with minimal contact area. Planning access paths for removal tools.
- Material Choice (If Applicable): Some systems allow for different support materials, although less common in metal PBF.
- Techniques de post-traitement : Utilizing appropriate tools (manual, rotary, EDM) for removal and then employing bead blasting, tumbling, or localized grinding/polishing to smooth areas where supports were attached.
3. Porosity:
- Défi: Small voids or pores can form within the printed material due to trapped gas (e.g., argon shield gas), incomplete fusion between layers/tracks, or keyholing (vapor depression instability). Porosity can reduce density and negatively impact mechanical properties, especially fatigue life.
- Solutions :
- Poudre de haute qualité : En utilisant metal spherical powders with high sphericity, low satellite content, controlled particle size distribution (PSD), and low moisture/gas content is critical. Met3dp’s advanced gas atomization and PREP technologies are designed to produce such high-quality powders, minimizing gas-related porosity.
- Paramètres d'impression optimisés : Fine-tuning laser power, scan speed, hatch spacing, and layer thickness to ensure complete melting and fusion without excessive energy input causing keyholing. Parameter development is key for achieving >99.5% density.
- Proper Gas Flow: Ensuring optimal flow of inert shield gas (Argon) within the build chamber to remove spatter and fumes effectively without disrupting the melt pool.
- Pressage isostatique à chaud (HIP) : For critical applications requiring maximum density and fatigue performance, HIP can be used as a post-processing step. It involves applying high temperature and high isostatic pressure to collapse internal voids, achieving near 100% density. This adds cost but significantly improves properties, crucial for reducing porosity aluminum printing.
4. Surface Roughness:
- Défi: As-printed surfaces, especially down-facing (supported) surfaces and vertical walls showing layer lines, can be rougher than desired for aesthetics or function.
- Solutions :
- Orientation de la construction : Prioritizing critical surfaces to be oriented upwards or vertically if possible.
- Paramètres optimisés : Using smaller layer thicknesses can improve vertical wall finish but increases build time. Contour scanning can improve edge definition.
- Post-traitement : Employing bead blasting, tumbling, polishing, or machining as described earlier to achieve the desired surface finish specification.
5. Achieving Tight Tolerances:
- Défi: Standard AM processes may not achieve the very tight tolerances required for certain features (e.g., bearing fits, motor shafts).
- Solutions :
- Hybrid Approach: Designing the part for AM to get the complex geometry and near-net shape, then using CNC machining for critical features requiring high precision. Leave adequate machining stock (e.g., 0.5-1.0 mm) on these features in the AM design.
- Process Calibration: Working with a provider who maintains meticulously calibrated machines and has robust quality control procedures.
6. Cost and Lead Time:
- Défi: Metal AM can sometimes have a higher perceived cost per part compared to traditional methods, especially for simpler designs in high volumes. Lead times depend on machine availability and post-processing complexity.
- Solutions :
- Leverage DfAM: Maximize benefits like lightweighting and part consolidation to justify the cost through improved performance or reduced assembly costs.
- Optimize Design: Minimize build height and volume where possible, reduce support needs.
- Nesting: Printing multiple parts simultaneously in one build to improve machine utilization.
- Choose the Right Partner: Experienced providers like Met3dp often have streamlined workflows, optimized parameters, and efficient post-processing chains to offer competitive metal 3D printing cost estimation and reliable lead times. Clear communication on requirements helps optimize the quote.
Successfully addressing these AM challenges drone parts requires a combination of design expertise (DfAM), material science knowledge, process control, high-quality materials and equipment, and diligent post-processing. Partnering with a knowledgeable and well-equipped metal AM service provider significantly mitigates these risks and ensures the production of high-quality, reliable 3D printed drone arms.
Selecting the Right Metal AM Partner: A Guide for Drone Manufacturers and Suppliers
Choosing a partner for metal additive manufacturing (AM) is a critical decision that significantly impacts the quality, cost, and reliability of your 3D printed drone arms. With the increasing adoption of AM, numerous service providers have emerged, but their capabilities, expertise, and quality standards can vary widely. For drone manufacturers, Original Equipment Manufacturers (OEMs), and wholesale drone component manufacturing suppliers seeking consistent results with materials like AlSi10Mg or the demanding Scalmalloy®, a thorough evaluation process is essential. Selecting the right AM service bureau goes beyond just finding the lowest quote; it involves assessing technical prowess, quality systems, material expertise, and overall capability alignment with your project’s needs.
Here’s a guide with key criteria to help you evaluate and choose the ideal metal AM partner:
1. Proven Expertise & Experience:
- Historique : Does the provider have demonstrable experience printing parts similar to drone arms in geometry and complexity? Have they successfully worked with the specific aluminum alloys you require (AlSi10Mg, Scalmalloy®)?
- Secteur d'activité : Do they understand the specific requirements and challenges of your industry (e.g., aerospace, defense, industrial)? Experience in regulated industries often indicates robust processes.
- Case Studies & References: Ask for examples of past projects, case studies, or client testimonials relevant to your application. Can they demonstrate successful outcomes for choosing AM supplier drone parts?
- Technical Depth: Assess the knowledge of their engineering team regarding DfAM, material science, process optimization, and post-processing specific to aluminum alloys.
2. Material Capabilities & Quality Control:
- Validated Materials: Do they offer the specific alloys you need (AlSi10Mg, Scalmalloy®) with validated and optimized printing parameters?
- Qualité de la poudre : This is crucial. Inquire about their powder sourcing and quality control procedures. Do they manage powder handling (storage, sieving, recycling) meticulously to prevent contamination and ensure consistency? Providers like Met3dp, who manufacture their own poudres métalliques de haute qualité using advanced techniques like gas atomization and PREP, have a distinct advantage in controlling this critical input variable. They ensure high sphericity, good flowability, and controlled particle size distribution, directly impacting print quality and final part properties.
- Test des matériaux : Do they perform material testing (e.g., tensile tests on witness coupons printed alongside parts) to verify that the mechanical properties meet specifications?
3. Equipment & Technology:
- Parc de machines : Do they operate state-of-the-art PBF machines (SLM/DMLS or potentially SEBM for specific benefits) suitable for aluminum alloys? Consider machine brands known for reliability and accuracy.
- Volume de construction : Ensure their machines have adequate build volume for your drone arm size and potential batch production needs. Met3dp highlights their “industry-leading print volume,” suggesting capacity for various part sizes and quantities.
- Surveillance des processus : Do their machines incorporate in-situ process monitoring capabilities (e.g., melt pool monitoring)? This can provide valuable data for quality assurance.
- Maintenance & Calibration: Are machines regularly maintained and calibrated to ensure consistent accuracy and performance?
4. Quality Management System & Certifications:
- QMS: Does the provider operate under a robust Quality Management System (QMS)?
- Certifications : Look for relevant certifications that demonstrate a commitment to quality and process control. Common ones include:
- ISO 9001 : General standard for quality management systems.
- AS9100 : Specific QMS for the aerospace industry (highly relevant if your drones target this sector). This certification implies rigorous traceability, process control, and documentation.
- Traceability: Can they provide full material and process traceability, linking the final part back to the specific powder batch, machine, build parameters, and post-processing steps? This is critical for certified metal AM bureau operations, especially in aerospace and defense.
5. Post-Processing Capabilities:
- In-House vs. Outsourced: Determine which post-processing steps (stress relief/heat treatment, support removal, machining, surface finishing, inspection) are handled in-house versus managed through trusted partners. In-house capabilities often allow for better control over lead times and quality.
- Expertise : Do they possess the necessary expertise and equipment for critical steps like heat treatment specific to AlSi10Mg and Scalmalloy®, precision CNC machining for tight tolerances, and various surface finishing techniques? Met3dp’s positioning as a provider of “comprehensive solutions” suggests they address the full workflow, either internally or through qualified partners.
6. Design Support & DfAM Expertise:
- Collaboration : Are they willing and able to collaborate on design optimization (DfAM)? Can they provide feedback on your designs to improve printability, reduce cost, or enhance performance?
- Software & Tools: Do they utilize relevant software for build preparation, simulation (predicting stress/distortion), and potentially topology optimization or lattice generation?
7. Lead Times, Capacity & Communication:
- Quoting Transparency: Is their quoting process clear and detailed, breaking down costs?
- Realistic Lead Times: Do they provide realistic lead times for prototyping and production volumes, considering all necessary steps?
- Capacity: Do they have sufficient machine capacity to handle your projected volumes without significant delays?
- Communication: Is their team responsive, communicative, and easy to work with? Good communication is vital for resolving issues quickly and ensuring project success.
Evaluation Checklist Summary:
Critères | Key Question | Ideal Partner Attributes (e.g., Met3dp) |
---|---|---|
Expertise & Experience | Proven track record with aluminum drone arms / relevant industry? | Demonstrable success, deep AM knowledge, industry understanding. |
Capacité matérielle | Offers & understands AlSi10Mg/Scalmalloy®? Controls powder quality? | Validated parameters, high-quality powder (in-house production is a plus). |
Equipment & Technology | State-of-the-art PBF machines? Adequate build volume? Process monitoring? | Modern, calibrated fleet, sufficient capacity (industry-leading volume). |
Quality System/Certs | ISO 9001? AS9100 (if needed)? Traceability? | Certified QMS, rigorous process control, full traceability. |
Post-traitement | Handles heat treatment, machining, finishing effectively (in-house or managed)? | Comprehensive capabilities, expertise in required finishing steps. |
Design Support (DfAM) | Offers design feedback / optimization collaboration? | Collaborative approach, DfAM expertise, relevant software tools. |
Lead Time, Capacity, Comm. | Realistic timelines? Sufficient capacity? Transparent quoting? Responsive? | Reliable lead times, scalable capacity, clear communication. |
Exporter vers les feuilles
By systematically evaluating potential partners against these criteria, drone manufacturers and suppliers can confidently select a metal AM provider like Met3dp that not only meets their technical requirements but also aligns with their quality standards and business objectives, ensuring the successful production of high-performance 3D printed aluminum drone arms.
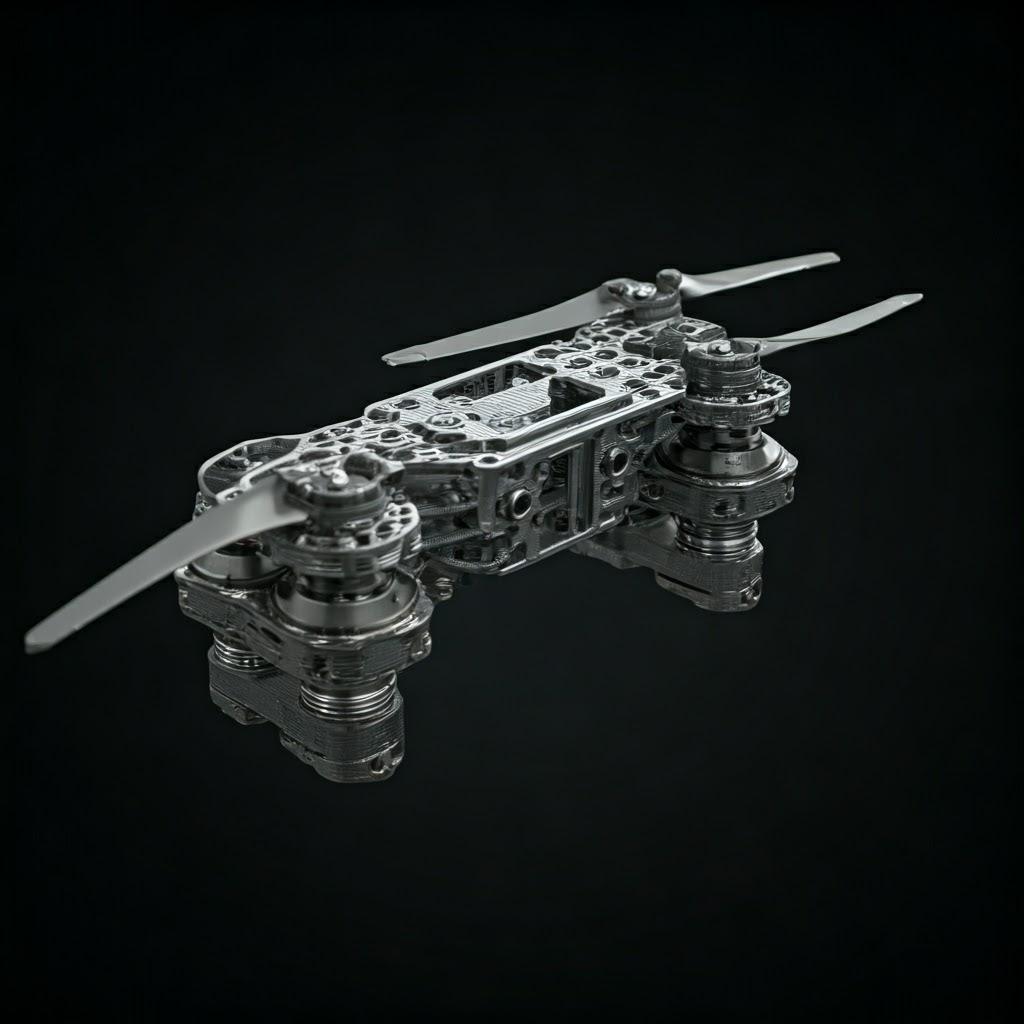
Understanding Cost Factors and Lead Times for Wholesale Drone Arm Production
Transitioning to metal additive manufacturing for drone arm production, especially at wholesale volumes, requires a clear understanding of the associated cost drivers and expected lead times. While AM offers compelling advantages in design freedom and customization, its cost structure differs from traditional methods like injection molding or high-volume CNC machining. Transparency from your AM partner regarding metal 3D printing cost estimation et AM lead time estimation is crucial for accurate budgeting, planning, and evaluating the total cost of ownership.
Key Cost Factors in Metal AM for Drone Arms:
- Material Type & Consumption:
- Alloy Choice: The raw material cost is a significant factor. High-performance alloys like Scalmalloy® (alliage d'aluminium) are inherently more expensive than standard alloys like AlSi10Mg due to the cost of alloying elements (like Scandium) and potentially more complex powder production. Scalmalloy printing costs will reflect this premium.
- Volume de la pièce : The actual volume of the final drone arm directly impacts the amount of powder consumed. Efficient design (topology optimization, lattices) reduces volume and thus material cost.
- Support Structure Volume: Supports also consume material. Minimizing support requirements through DfAM directly reduces cost.
- Powder Recycling & Efficiency: The efficiency of the provider’s powder recycling process impacts overall material cost. High reuse rates (with proper quality control) lower effective material costs.
- Machine Time (Print Time):
- Build Height: This is often the primary driver of print time in PBF. Taller parts take longer to print, regardless of volume per layer. Orienting parts to minimize Z-height can reduce time.
- Part Volume & Density: Larger or denser parts require more laser scanning time per layer.
- Number of Parts per Build (Nesting): Printing multiple drone arms simultaneously in one build maximizes machine utilization. The setup time is amortized over more parts, and the total build time is often determined by the tallest part(s). Effective nesting is key for wholesale drone arm production.
- Épaisseur de la couche : Thinner layers provide better surface finish and resolution but significantly increase the number of layers and thus print time. Thicker layers are faster but rougher.
- Machine Operating Costs: Includes depreciation, energy consumption, inert gas usage, maintenance, and skilled operator labor. These are factored into the hourly machine rate charged by the service provider.
- Coûts de main-d'œuvre :
- Préparation de la construction : CAD file processing, orientation optimization, support structure generation, and slicing require skilled technician time.
- Machine Operation: Setup, monitoring the build process, and removal of the build plate.
- Post-traitement : This can be a significant labor component, including stress relief, part removal, support removal (often manual), cleaning, surface finishing, machining (if required), and inspection. The complexity of the part and support structures heavily influences this cost.
- Exigences en matière de post-traitement :
- Traitement thermique : Furnace time, energy, and potentially specialized atmospheres add cost.
- Usinage CNC : Costs depend on the complexity of the features being machined, the number of setups required, and the machining time.
- Finition de la surface : Costs vary significantly depending on the method (blasting is relatively inexpensive, multi-step polishing is expensive) and the required surface quality (Ra value).
- Inspection : The level of QC required (visual, dimensional, NDT) impacts labor and equipment costs. AS9100 requirements typically mandate more rigorous inspection.
- Complexité de la conception :
- While AM handles complexity well without the tooling penalties of traditional methods, highly intricate designs might require more complex support structures, potentially increasing print time and post-processing labor for support removal. However, complexity enabling part consolidation can lead to net cost savings by reducing assembly labor and fastener costs.
- Volume de commande :
- Unlike injection molding where tooling amortization dominates low-volume costs, AM costs scale more linearly. However, there are still economies of scale. Larger batch sizes allow for better machine utilization (nesting), potentially dedicated post-processing setups, and amortization of setup/programming costs over more units. Expect additive manufacturing pricing drone parts to decrease per unit on larger wholesale orders, but perhaps less dramatically than with molding.
Understanding Lead Times:
Lead time in metal AM is the total time from order placement to part delivery and includes several stages:
- Pré-traitement : Order review, CAD preparation, build simulation, scheduling (can range from hours to days).
- Impression : Actual machine time (can range from hours for small parts to several days for large/complex builds or full plates). Queue time for machine availability must also be considered.
- Cool Down: Allowing the build chamber and parts to cool sufficiently before removal.
- Post-traitement : This is often the longest and most variable part of the lead time.
- Heat Treatment: Furnace cycles take hours or days.
- Part/Support Removal & Cleaning: Hours to days depending on complexity and batch size.
- Machining: Days, depending on complexity and machine shop scheduling.
- Surface Finishing: Hours to days.
- Inspection & QC: Hours to days.
- Expédition: Transit time to the customer.
Délais d'exécution typiques :
- Prototypes (1-10 units): Often 5-15 business days, depending on complexity and required post-processing.
- Low Volume Production (10-100 units): Typically 2-6 weeks.
- Medium/Wholesale Volumes (100s-1000s units): Can range from several weeks to a few months, highly dependent on capacity, part complexity, and optimizing the workflow for series production.
Key Takeaways for B2B Buyers:
- Get Detailed Quotes: Ensure quotes break down costs (material, print time, post-processing) for transparency. Provide clear specifications (material, tolerances, finish, inspection requirements) to get accurate quotes.
- Discuss Lead Times: Understand the timeline for each stage and work with your provider to meet deadlines. Factor in potential queue times.
- Optimize for AM: Leverage DfAM principles to reduce material usage, minimize supports, and potentially consolidate parts – this is the best way to control aluminum 3D printing quote costs.
- Partner Early: Engage with experienced AM providers like Met3dp early in the design process. Their expertise can help optimize your drone arm design for cost-effective and efficient production, ensuring reliable lead times for your supply chain. Their integrated approach, from powder to finished part, facilitates streamlined project management.
By understanding these cost and lead time dynamics, businesses can make informed decisions about implementing metal AM for drone arm production and build strong partnerships with capable suppliers.
Frequently Asked Questions (FAQ) about 3D Printing Drone Arms
Here are answers to some common questions engineers, designers, and procurement managers have about using metal additive manufacturing for drone arms with aluminum alloys:
1. How strong are 3D printed aluminum drone arms compared to traditionally manufactured ones (e.g., CNC machined 6061 or 7075)?
- Répondre: The strength can be comparable or even superior, depending on the alloy, design, and processing.
- AlSi10Mg (Heat Treated): Typically exhibits properties similar to cast aluminum alloys. While generally not as strong as high-strength wrought alloys like 7075-T6 machined from billet, its strength-to-weight ratio combined with design optimization (topology optimization) via AM can result in lighter arms with equivalent or better overall performance for many applications.
- Scalmalloy® (Heat Treated): This alloy is specifically designed for AM and offers exceptional mechanical properties, often exceeding those of standard wrought aluminum alloys like 6061-T6 and approaching or matching 7075-T6 or even some titanium grades in terms of specific strength (strength divided by density). When properly designed and processed, Scalmalloy® arms can be significantly lighter et stronger than conventionally machined aluminum arms.
- Key Factor: Proper heat treatment is crucial for both alloys to achieve their optimal strength. Additionally, AM allows for placing material strategically only where needed, maximizing structural efficiency beyond what’s easily achievable with subtractive methods.
2. What is the typical minimum order quantity (MOQ) and is metal AM suitable for large-scale production of drone arms?
- Répondre: One of the major advantages of metal AM is its flexibility regarding volume.
- MOQ: Typically, there is no minimum order quantity. AM service providers can economically produce single prototypes, very small batches (e.g., for custom drones or R&D), or replacement parts on demand. This eliminates the need for expensive tooling associated with methods like injection molding.
- Large-Scale Production: Metal AM is increasingly viable for series production, moving beyond just prototyping. While perhaps not competing with injection molding for hundreds of thousands of simple polymer parts, it is competitive for low-to-medium volumes (tens to thousands) of complex, high-performance metal components like drone arms. Efficiency gains come from nesting multiple parts per build, optimized workflows, and reduced assembly needs due to part consolidation. Companies like Met3dp, with industry-leading print volumes and comprehensive solutions, are equipped to handle series production requirements for wholesale drone component suppliers.
3. Can complex internal features, like wiring channels or cooling passages, be effectively created in 3D printed aluminum drone arms?
- Répondre: Yes, absolutely. This is a key strength of additive manufacturing.
- Canaux internes : AM can create smooth, complex, and organically shaped internal channels directly within the arm structure during the printing process. These can be designed to perfectly route wiring, protect it from damage, and improve aerodynamics. Integrated cooling channels can also be designed around heat sources like motors.
- Considérations relatives à la conception : The primary considerations are ensuring the channels are large enough for their intended purpose (wiring passage, fluid/air flow) and designing effective “escape holes” or access points to allow for the removal of all unfused powder from these internal cavities during post-processing. This is a standard practice in DfAM, and experienced providers can advise on optimal design strategies.
4. Are 3D printed aluminum arms durable enough for demanding applications like industrial inspection or defense UAVs?
- Répondre: Yes, when the right material is chosen and processed correctly.
- Sélection des matériaux : For demanding applications requiring high fatigue strength, impact resistance, and durability in harsh environments, Scalmalloy® (alliage d'aluminium) is often the preferred choice due to its exceptional mechanical properties. AlSi10Mg provides good durability for many industrial and commercial applications.
- Contrôle des processus : Ensuring high density (>99.5%), proper heat treatment to optimize properties (strength, ductility, fatigue resistance), and appropriate surface finishing are critical for durability.
- Assurance qualité : Rigorous inspection (including potentially NDT for critical components) verifies the integrity of the printed part. Partnering with a quality-focused provider like Met3dp, experienced with applications in aerospace, medical, and industrial fields, ensures that parts meet the stringent requirements for demanding use cases. Their advanced powders and printing systems contribute directly to producing dense, high-quality metal parts with superior mechanical properties suitable for mission-critical components.
Conclusion: Elevating Drone Capabilities with Met3dp’s Additive Manufacturing Solutions
The drone industry’s relentless pursuit of higher performance, greater efficiency, and expanded capabilities demands innovation at every level, particularly in structural components like drone arms. Metal additive manufacturing has unequivocally emerged as a transformative technology, enabling the creation of arms that are lighter, stronger, and more complex than ever before possible with traditional methods. By leveraging the design freedom of AM with advanced aluminum alloys – the versatile AlSi10Mg for a wide range of applications and the exceptional high-performance Scalmalloy® (alliage d'aluminium) for the most demanding scenarios – drone manufacturers and suppliers can unlock significant competitive advantages.
Throughout this exploration, we’ve seen how metal AM addresses key challenges in drone design: achieving radical lightweighting through topology optimization and lattice structures, enhancing functionality via part consolidation and feature integration, and accelerating development cycles through rapid prototyping and iteration. We’ve also navigated the critical considerations of DfAM principles, achievable precision, essential post-processing steps, and common manufacturing challenges, emphasizing that success requires expertise, robust processes, and high-quality materials.
Selecting the right manufacturing partner is paramount to realizing the full potential of this technology. The ideal partner possesses not only state-of-the-art equipment but also deep material science knowledge, rigorous quality control systems (evidenced by certifications like ISO 9001 or AS9100), comprehensive post-processing capabilities, and a collaborative approach to design optimization.
C'est ici Metal3DP Technology Co., LTD (Met3dp) stands out. As a leading provider of additive manufacturing solutions headquartered in Qingdao, China, Met3dp offers a unique combination of capabilities tailored to the needs of demanding industries like aerospace, automotive, medical, and industrial manufacturing. Their specialization in both advanced 3D printing equipment (delivering industry-leading volume, accuracy, and reliability) and the production of high-performance metal powders via cutting-edge gas atomization and PREP technologies ensures quality control from the very source material.
Met3dp’s portfolio, including innovative alloys and standard materials like AlSi10Mg, coupled with their decades of collective expertise, allows them to provide comprehensive solutions spanning printers, powders, and application development services. Whether you are developing next-generation tactical UAVs requiring the extreme strength-to-weight ratio of Scalmalloy®, designing industrial inspection drones needing durable and reliable AlSi10Mg arms, or looking for a wholesale supplier of optimized drone components, Met3dp has the technology and expertise to support your goals. They partner with organizations to implement 3D printing effectively, accelerating digital manufacturing transformations.
Elevate your drone designs beyond conventional limitations. Embrace the power of metal additive manufacturing to create lighter, stronger, and more capable drone arms.
Ready to explore how metal AM can revolutionize your next drone project?
Contactez Met3dp aujourd'hui to discuss your specific requirements for 3D printed drone arms using AlSi10Mg, Scalmalloy®, or other advanced alloys. Let their expertise in cutting-edge systems and high-quality powders power your organization’s additive manufacturing goals and help you achieve new heights in drone performance.
Partager sur
MET3DP Technology Co. est un fournisseur de premier plan de solutions de fabrication additive dont le siège se trouve à Qingdao, en Chine. Notre société est spécialisée dans les équipements d'impression 3D et les poudres métalliques de haute performance pour les applications industrielles.
Articles connexes
À propos de Met3DP
Mise à jour récente
Notre produit
CONTACTEZ-NOUS
Vous avez des questions ? Envoyez-nous un message dès maintenant ! Nous répondrons à votre demande avec toute une équipe dès réception de votre message.
Obtenir les informations de Metal3DP
Brochure du produit
Obtenir les derniers produits et la liste des prix
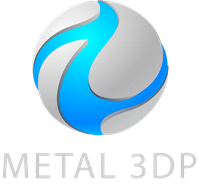
Poudres métalliques pour l'impression 3D et la fabrication additive