3D Printed Ducts for Turbo Cooling Applications
Table des matières
Introduction: Revolutionizing Turbo Cooling with Metal Additive Manufacturing
In the relentless pursuit of automotive performance, efficiency, and reliability, turbocharging has become a cornerstone technology. By forcing more air into the engine’s cylinders, turbochargers enable smaller, lighter engines to produce significantly more power and torque, leading to improved fuel economy and reduced emissions compared to larger naturally aspirated counterparts. However, this power boost comes with a significant challenge: heat. The very act of compressing intake air and exposure to hot exhaust gases used to drive the turbine generates substantial thermal loads that must be meticulously managed. This is where turbo cooling ducts play a critical, often underappreciated, role. These components are essential conduits, directing airflow or coolant to vital areas of the turbocharger and surrounding systems, ensuring optimal operating temperatures and preventing catastrophic failures.
Traditionally, manufacturing these intricate ducts has relied on methods like casting, stamping, welding, and brazing multiple pieces together. While effective to a point, these conventional techniques often impose significant limitations. Complex internal geometries needed for truly optimized airflow or coolant paths can be difficult or impossible to achieve. Tooling costs for casting or stamping can be prohibitive, especially for low-to-medium volume production runs typical in performance aftermarket, motorsport, or specialized vehicle segments. Fabricated assemblies introduce potential leak points at joints, add weight, and increase assembly complexity. Furthermore, material choices might be restricted by the manufacturing process itself, limiting the potential for using advanced alloys perfectly suited for the demanding high-temperature, high-pressure environment of a modern engine bay.
Entrer fabrication additive métallique, more commonly known as metal Impression 3D. This transformative technology is rapidly reshaping the landscape of automotive component design and production, offering unprecedented solutions to the challenges faced in manufacturing parts like turbo cooling ducts. Metal AM builds parts layer by layer directly from a 3D CAD model using high-energy sources like lasers or electron beams to fuse fine metallic powders. This additive approach fundamentally flips the manufacturing paradigm, enabling the creation of highly complex, optimized, and lightweight structures that were previously unimaginable.
For turbo cooling ducts, the implications are profound. Metal AM unlocks:
- Une liberté de conception inégalée : Engineers can design ducts with organic curves, variable wall thicknesses, and intricate internal features precisely optimized for fluid dynamics (airflow or coolant flow), maximizing cooling efficiency within tightly packaged engine compartments.
- Significant Lightweighting: Through topology optimization and the ability to create thin-walled yet strong structures, AM allows for substantial weight reduction compared to cast or fabricated ducts, contributing to overall vehicle performance and fuel efficiency.
- Prototypage rapide et itération : New duct designs can be printed and tested in a matter of days, drastically accelerating the development cycle and allowing for data-driven design improvements without the lengthy delays and high costs associated with traditional tooling modifications.
- Consolidation partielle : Features like mounting brackets, flanges, or sensor bosses can be directly integrated into the duct design, reducing part count, eliminating assembly steps, minimizing potential leak paths, and improving overall system robustness.
- Advanced Material Options: Metal AM readily processes high-performance alloys crucial for demanding turbo applications, such as lightweight Aluminum alloys (like AlSi10Mg) for weight-sensitive areas or Nickel superalloys (like IN625) capable of withstanding extreme temperatures near the turbine housing.
This technology is not just for concept cars or high-end racing anymore. Metal AM is proving its value across a spectrum of automotive applications, including performance tuning, professional motorsport series, heavy-duty truck engines requiring extreme durability, and specialized industrial vehicles. As a leading provider of metal AM solutions, including advanced printing systems and high-quality metal powders, Met3dp is at the forefront of enabling these innovations. Companies seeking additive manufacturing automotive solutions or robust turbocharger component manufacturing capabilities are increasingly turning to metal 3D printing service providers. This article delves into the specifics of utilizing metal AM for turbo cooling ducts, exploring their function, the advantages of this production method, recommended materials like AlSi10Mg and IN625, design considerations, and how to partner with the right solutions d'impression 3D de métaux expert.
The Function and Importance of Turbo Cooling Ducts in Automotive Systems
To fully appreciate the value proposition of 3D printed turbo cooling ducts, it’s essential to understand the intense environment in which they operate and their critical role in maintaining engine health and performance. A turbocharger utilizes exhaust gases, often exceeding 900°C (1650°F), to spin a turbine wheel. This turbine is connected via a shaft to a compressor wheel, which draws in ambient air and compresses it before sending it to the engine’s intake manifold. This compression process significantly increases the air’s density, allowing more oxygen into the cylinders and thus enabling the combustion of more fuel, resulting in greater power output. However, compressing air inherently heats it up (adiabatic heating), and the turbocharger unit itself absorbs immense heat from the exhaust gases passing through the turbine housing and the friction generated by components spinning at incredibly high speeds (often exceeding 150,000 RPM).
Without effective cooling, this combined heat load poses serious risks:
- Reduced Engine Performance: Hot compressed air (charge air) is less dense than cool compressed air. Lower density means less oxygen per unit volume entering the cylinders, which limits the potential power gain from turbocharging. Intercoolers are used to cool the charge air, but the turbocharger unit itself must also be kept within optimal temperature limits. Overheated turbo components can radiate heat, further increasing intake air temperatures post-compressor. Efficient ducting ensures cooling mediums reach the right places to mitigate this.
- Component Degradation and Failure: The turbocharger’s bearings, seals, and housings are susceptible to damage from excessive heat. The lubricating oil flowing through the center housing rotating assembly (CHRA) can break down or ‘coke’ at high temperatures, leading to bearing seizure – a common and catastrophic failure mode. Turbine housings can crack due to thermal stress cycling. Compressor wheels can lose efficiency or even deform. Cooling ducts directing air or engine coolant to the CHRA are vital for preventing these issues and ensuring the turbocharger’s longevity.
- Increased Emissions: Higher operating temperatures can negatively impact combustion efficiency and potentially lead to the formation of unwanted emissions like NOx. Maintaining stable and controlled operating temperatures, facilitated by effective cooling, contributes to cleaner engine operation.
- Reduced Engine Lifespan: Chronic overheating stresses not only the turbocharger but also surrounding engine components, potentially leading to premature wear and tear on gaskets, hoses, sensors, and wiring harnesses located within the hot engine bay environment.
Turbo cooling ducts are designed to combat these issues by precisely delivering a cooling medium – either ambient air or engine coolant – to specific high-temperature zones.
- Air Cooling Ducts: Often simpler in design, these ducts capture cooler air (e.g., from the front of the vehicle or a dedicated scoop) and direct it over the turbocharger housing, particularly the CHRA or sometimes the compressor housing, to facilitate convective cooling. Their effectiveness depends on airflow velocity and the surface area exposed.
- Liquid Cooling Ducts (Coolant Lines): Many modern turbochargers feature integrated coolant passages within the CHRA. Specialized ducts or lines connect these passages to the engine’s main cooling system. Engine coolant actively circulates through the turbo’s core, providing much more effective heat transfer than air cooling alone, especially crucial for preventing heat soak after engine shutdown (which can cause oil coking). These ducts must handle coolant pressure and temperature reliably.
The design and placement of these ducts are critical, particularly given the extremely crowded nature of modern engine bays. They must navigate around other components, withstand constant vibrations, resist high temperatures (especially ducts near the turbine housing), and maintain their structural integrity over the vehicle’s lifetime.
Applications Across Vehicle Types:
- Performance Cars & Aftermarket Tuning: Maximizing boost pressure for ultimate power output generates extreme heat. Custom, optimized cooling ducts (often 3D printed) are essential for reliability and sustained performance during spirited driving or track use. Space is often at a premium, making the design freedom of AM invaluable. Performance vehicle components suppliers are increasingly leveraging AM for these niches.
- Commercial Trucks & Heavy-Duty Engines: While peak power might be less of a focus, reliability and longevity under continuous, heavy loads are paramount. Efficient engine thermal management directly impacts operating costs and uptime. Turbochargers in these applications run for thousands of hours, demanding robust cooling solutions. AM can provide durable, optimized ducts for heavy-duty engine cooling.
- Motorsport: Racing applications push components to their absolute limits. Turbo cooling is non-negotiable for finishing a race. Teams require lightweight, highly efficient, and often bespoke cooling duct solutions that can be rapidly iterated and replaced. Motorsport engineering heavily relies on technologies like AM for competitive advantage.
The inherent challenges of designing effective ducts within these constraints – tight packaging, vibration, extreme temperatures, pressure containment (for liquid cooling), and the need for aerodynamic efficiency (for airflow) – make conventional manufacturing methods struggle. This is precisely where the advantages of metal 3D printing become most apparent, offering engineers the tools to overcome these hurdles and deliver superior automotive cooling systems.
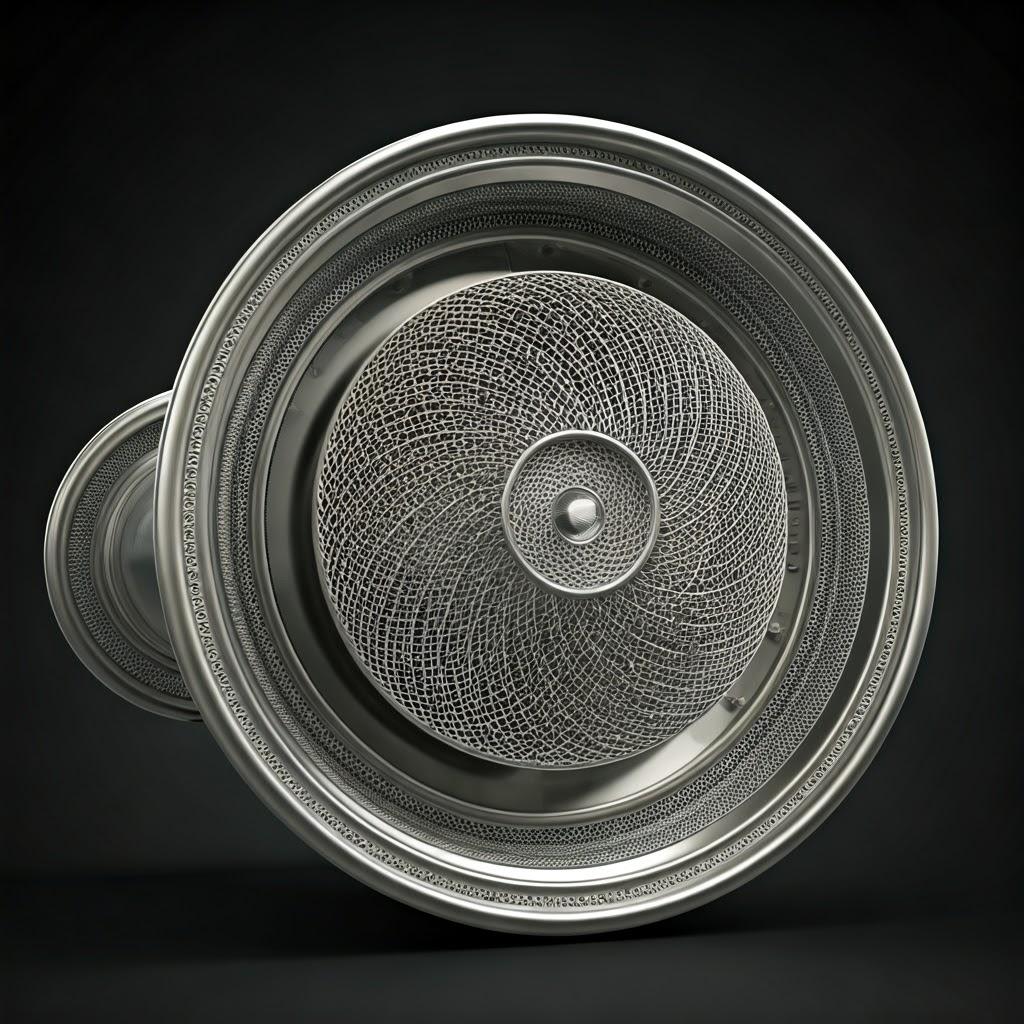
Why Choose Metal 3D Printing for Automotive Turbo Cooling Ducts?
The decision to adopt metal additive manufacturing for components like turbo cooling ducts stems from a clear set of advantages over traditional production methods. While casting, fabrication, and machining have served the industry well for decades, they present inherent limitations that metal AM effectively overcomes, particularly when dealing with complex geometries, demanding performance requirements, and the need for rapid innovation often found in automotive engineering solutions. Let’s compare these methods and highlight the specific benefits AM brings to duct manufacturing.
Traditional Manufacturing Methods vs. Metal AM:
Fonctionnalité | Casting (e.g., Investment, Sand) | Fabrication (Welding/Brazing) | Machining (Subtractive) | Metal AM (Additive) |
---|---|---|---|---|
Complexité de la conception | Moderate (Limited internal features) | Low-Moderate (Joins limit geometry) | Low (Difficult internal features) | Très élevé (Complex internals possible) |
Coût de l'outillage | Haut | Low-Moderate | Low (Fixturing) | Very Low / None |
Lead Time (Proto) | Weeks / Months | Days / Weeks | Days / Weeks | Jours |
Déchets matériels | Modéré | Faible | Haut | Faible (Powder is recyclable) |
Consolidation partielle | Limitée | Very Limited | Not Applicable | Haut (Integrate multiple features) |
Allègement | Moderate (Wall thickness limits) | Modéré | Limitée | Excellent (Topology opt., thin walls) |
Ideal Volume | Haut | Low – Medium | Low – High | Low – Medium (Increasingly higher) |
Options de matériaux | Good (Specific casting alloys) | Good (Weldable alloys) | Très bon | Good & Expanding (Specialized powders) |
Exporter vers les feuilles
Key Advantages of Metal AM for Turbo Cooling Ducts:
- Unmatched Design Freedom & Optimization: This is arguably the most significant advantage. AM liberates designers from the constraints of draft angles (casting), bend radii (fabrication), or tool access (machining). For a turbo cooling duct, this translates to:
- Fluid Dynamically Optimized Paths: Ducts can feature smooth, organic curves and precisely shaped internal passages designed using Computational Fluid Dynamics (CFD) analysis to maximize airflow or coolant velocity, minimize pressure drop, and ensure the cooling medium reaches the most critical hot spots effectively. This level of optimization is often impossible with traditional methods.
- Variable Wall Thickness: Material can be added only where structurally needed, allowing for thin walls in low-stress areas to save weight and thicker sections near mounting points or high-pressure zones for strength.
- Caractéristiques internes du complexe : Features like internal baffles, turbulators to enhance heat transfer, or complex manifolds can be directly integrated within the duct structure.
- Potentiel d'allègement important : In automotive applications, weight reduction is constantly pursued for better performance, handling, and fuel economy. Metal AM enables lightweighting through:
- Optimisation de la topologie : Software algorithms determine the most efficient load paths, removing unnecessary material while maintaining structural integrity. This can lead to organic-looking, highly efficient designs.
- Thin-Walled Structures: AM processes can reliably produce parts with thinner walls than often achievable with casting, directly reducing mass.
- Material Choice: Using lightweight alloys like AlSi10Mg where temperature requirements permit. Potential weight savings of 30-60% compared to traditionally manufactured equivalents are commonly reported for topology-optimized AM components, making AM a key enabler for composants automobiles légers.
- Accelerated Development Cycles (Rapid Prototyping): Bringing new engine designs or performance upgrades to market quickly is a competitive advantage. Metal AM drastically shortens the prototyping phase for components like cooling ducts.
- Tooling Elimination: Designs go directly from CAD to physical part without the need to create expensive and time-consuming molds or dies.
- Fast Iteration: A new duct design can be printed, tested (e.g., fitment check, flow bench testing), and revised within days. This allows engineers to quickly validate concepts, compare different design iterations, and arrive at an optimal solution much faster than traditional methods allow. This makes AM ideal for services de prototypage rapide.
- Consolidation partielle : Complex assemblies are prone to tolerance stack-up issues, require additional assembly labor, and introduce potential failure points (e.g., welds, gaskets). Metal AM allows designers to consolidate multiple components into a single, monolithic part.
- Example: A turbo cooling duct assembly might traditionally consist of a formed tube, a machined flange, and a welded mounting bracket. With AM, these can all be integrated into one printed component.
- Avantages : Reduced part count, simplified inventory management (for automotive component manufacturing), lower assembly time and cost, improved reliability (fewer joints/seals), and often reduced weight.
- Tailored Material Selection: Metal AM offers access to a growing portfolio of advanced metal powders specifically engineered for demanding applications. As discussed previously, engineers can select:
- AlSi10Mg : For lightweight, moderate temperature applications.
- IN625: For extreme heat and corrosion resistance.
- Other Alloys: Depending on specific needs, other options like Titanium alloys (for extreme lightweighting and good strength) or specialized steels might be considered. Reputable providers like Met3dp offer expertise in processing these materials, ensuring optimal properties in the final part. This material flexibility allows for function-specific solutions.
- Economical Low-to-Medium Volume Production: While traditional methods like casting excel at high volumes due to amortization of tooling costs, AM shines in scenarios requiring customization or lower quantities.
- No Tooling Investment: Makes it cost-effective for producing tens, hundreds, or even thousands of parts where tooling would be prohibitively expensive.
- Fabrication à la demande : Parts can be printed as needed, reducing inventory holding costs and enabling faster response to fluctuating demand – a key aspect of supply chain optimization automotive.
- Ideal for: Motorsport, performance aftermarket parts, classic car restorations, specialized vehicles, and bridge production while high-volume tooling is being prepared.
By leveraging these advantages, automotive engineers and procurement managers can achieve superior thermal management solutions, enhance vehicle performance, shorten development timelines, and potentially reduce overall system costs when considering the entire lifecycle. Partnering with an experienced automotive additive manufacturing partner is key to unlocking the full potential of this technology for components like turbo cooling ducts.
Recommended Materials for 3D Printed Turbo Ducts: AlSi10Mg and IN625
Choosing the right material is paramount to the success of any engineering component, and 3D printed turbo cooling ducts are no exception. The material must withstand the specific thermal, chemical, and mechanical loads of its operating environment while meeting performance, weight, and cost targets. Metal additive manufacturing offers a versatile palette of materials, but for the demanding world of turbocharger systems, two alloys stand out as primary candidates: AlSi10Mg (an aluminum alloy) and IN625 (a nickel superalloy). Understanding their distinct properties and ideal use cases is crucial for engineers and automotive grade metal powder suppliers alike.
AlSi10Mg: The Lightweight Choice for Moderate Temperatures
AlSi10Mg is a widely used aluminum alloy in additive manufacturing, essentially the AM equivalent of common casting alloys like A360. Its popularity stems from a combination of good mechanical properties, excellent printability, relatively low cost, and significantly low density.
- Propriétés principales :
- Densité : Approximately 2.67 g/cm³. This is roughly one-third the density of steel or nickel alloys, making it ideal for lightweighting efforts.
- Conductivité thermique : Relatively high (around 130-150 W/mK). This allows ducts made from AlSi10Mg to potentially aid in dissipating heat, although its lower melting point limits its use in the hottest areas.
- La force : Offers good strength and hardness, especially after a T6 heat treatment (solutionizing and artificial aging). Typical tensile strength can reach 300-450 MPa, suitable for many structural and flow-directing applications.
- Imprimabilité : Exhibits excellent behavior during Laser Powder Bed Fusion (L-PBF), the most common AM process for this alloy. It solidifies well with good dimensional accuracy and surface finish achievable.
- Résistance à la corrosion : Generally good, sufficient for typical engine bay environments, although direct contact with certain coolants over long periods should be considered.
- Maximum Service Temperature: This is the primary limitation. AlSi10Mg significantly loses strength above 150-200°C (300-390°F), making it unsuitable for components directly exposed to hot exhaust gases or the turbine housing.
- Ideal Applications for Turbo Cooling Ducts:
- Compressor intake and outlet ducting.
- Intercooler piping connections.
- Air ducts directing ambient air towards the CHRA (if positioned away from the turbine side).
- Coolant lines in moderate temperature zones.
- Applications where minimizing weight is the primary driver (motorsport, performance tuning).
- Rapid prototyping to validate geometry and fitment before committing to a more expensive high-temperature alloy if needed.
- AM Considerations: While printable, achieving optimal mechanical properties usually requires a post-print T6 heat treatment cycle. Support structures are often needed but are generally easier to remove than with tougher alloys. Its reflective nature requires careful laser parameter tuning during printing.
IN625 (Inconel 625): The High-Temperature Heavyweight Champion
When extreme heat, corrosive environments, and high mechanical stress converge, Nickel-based superalloys like IN625 (often referred to by its trade name Inconel® 625) become the material of choice. It’s renowned for its ability to maintain excellent strength and resist oxidation and corrosion at highly elevated temperatures.
- Propriétés principales :
- Densité : Significantly higher than aluminum, at approximately 8.44 g/cm³. This weight penalty must be justified by performance requirements.
- Conductivité thermique : Relatively low (around 10 W/mK). It acts more as an insulator than a conductor, which can be beneficial in preventing heat transfer to surrounding components but means it doesn’t help dissipate heat from the turbo itself as effectively as aluminum might.
- Résistance à haute température : This is IN625’s defining characteristic. It retains significant tensile and creep strength at temperatures exceeding 800°C (1470°F) and can withstand short excursions even higher, making it ideal for exhaust-side components.
- Corrosion & Oxidation Resistance: Exceptional resistance to a wide range of corrosive media, including exhaust gases, acids, and saltwater, thanks to its high Nickel and Chromium content, plus Molybdenum and Niobium.
- Résistance à la fatigue : Exhibits excellent resistance to mechanical and thermal fatigue, critical in the high-vibration, cyclic-temperature environment of a turbocharger system.
- Imprimabilité : Generally considered good for a superalloy, but more challenging than AlSi10Mg. It requires precise control over process parameters (laser power, speed, layer thickness) to minimize internal stresses and prevent cracking during the L-PBF process. Expertise is crucial for successful IN625 additive manufacturing.
- Ideal Applications for Turbo Cooling Ducts:
- Ducting directly connected to or situated very near the turbine housing or exhaust manifold.
- Wastegate components and associated plumbing.
- EGR (Exhaust Gas Recirculation) system components exposed to hot exhaust.
- Any ducting where operating temperatures consistently exceed 200°C.
- Demanding motorsport applications where maximum durability under extreme heat is required.
- Heavy-duty diesel applications needing long service life in harsh conditions.
- AM Considerations: Prone to significant residual stress accumulation during printing, necessitating careful post-print stress relief heat treatments. Support structures are often required and can be difficult to remove due to the material’s toughness. Hot Isostatic Pressing (HIP) may be employed after printing to eliminate any internal porosity and further enhance mechanical properties. Machining features to final tolerance after printing is common but requires appropriate tooling due to IN625’s work-hardening nature.
Material Comparison Summary:
Propriété | AlSi10Mg | IN625 | Unité | Notes |
---|---|---|---|---|
Densité | ~2.67 | ~8.44 | g/cm³ | IN625 is ~3.16x heavier |
Conductivité thermique | ~130-150 | ~10 | W/mK | AlSi10Mg dissipates heat much better |
Max. Service Temp. (Approx) | < 200 (°C) / < 390 (°F) | > 800 (°C) / > 1470 (°F) | °C / °F | Defines primary application difference |
Tensile Strength (RT, Typical) | 300-450 (T6) | 800-1000+ (Annealed/Aged) | MPa | IN625 much stronger, especially at high temps |
Printability (L-PBF) | Excellent | Good (Requires Expertise) | – | IN625 needs tighter process control |
Résistance à la corrosion | Bon | Excellent | – | IN625 superior in harsh/hot environments |
Relative Cost (Powder) | Plus bas | Haut | – | IN625 powder can be 5-10x+ costlier |
Besoins en post-traitement | Heat Treat (T6) Typical | Stress Relief, Poss. HIP/Machining Common | – | IN625 generally requires more post-processing |
Exporter vers les feuilles
The Importance of Powder Quality – Met3dp’s Contribution
Regardless of the alloy chosen, the quality of the metal powder used is fundamental to achieving dense, defect-free parts with predictable mechanical properties. Issues like inconsistent particle size distribution, irregular particle shape (low sphericity), internal porosity within powder particles, or contamination can lead to printing failures, poor surface finish, and compromised part performance.
This is where specialized powder manufacturers play a critical role. Met3dp, utilizing industry-leading powder production technologies like Vacuum Gas Atomization (VIGA) and Plasma Rotating Electrode Process (PREP), focuses on producing poudres métalliques de haute qualité with characteristics optimized for additive manufacturing:
- Sphéricité élevée : Ensures excellent powder flowability in the printer, leading to uniform powder bed density and consistent melting.
- Low Porosity: Minimizes trapped gases within the powder, reducing the risk of porosity in the final part.
- Distribution contrôlée de la taille des particules (PSD) : Tailored PSDs for specific AM processes (like L-PBF) ensure optimal packing density and melting behavior.
- Haute pureté : Strict control over raw materials and processing minimizes contaminants that could degrade material properties.
By partnering with providers like Met3dp who control the quality from the source powder onwards, engineers and procurement managers can have higher confidence in the reliability and performance of their 3D printed turbo cooling ducts, whether they are lightweight AlSi10Mg components or robust, heat-resistant IN625 parts designed for the most demanding high-temperature metal alloy applications. Selecting the appropriate material and ensuring its quality are the foundational steps for leveraging the full potential of nickel alloy 3D printing or aluminum AM in automotive thermal management.
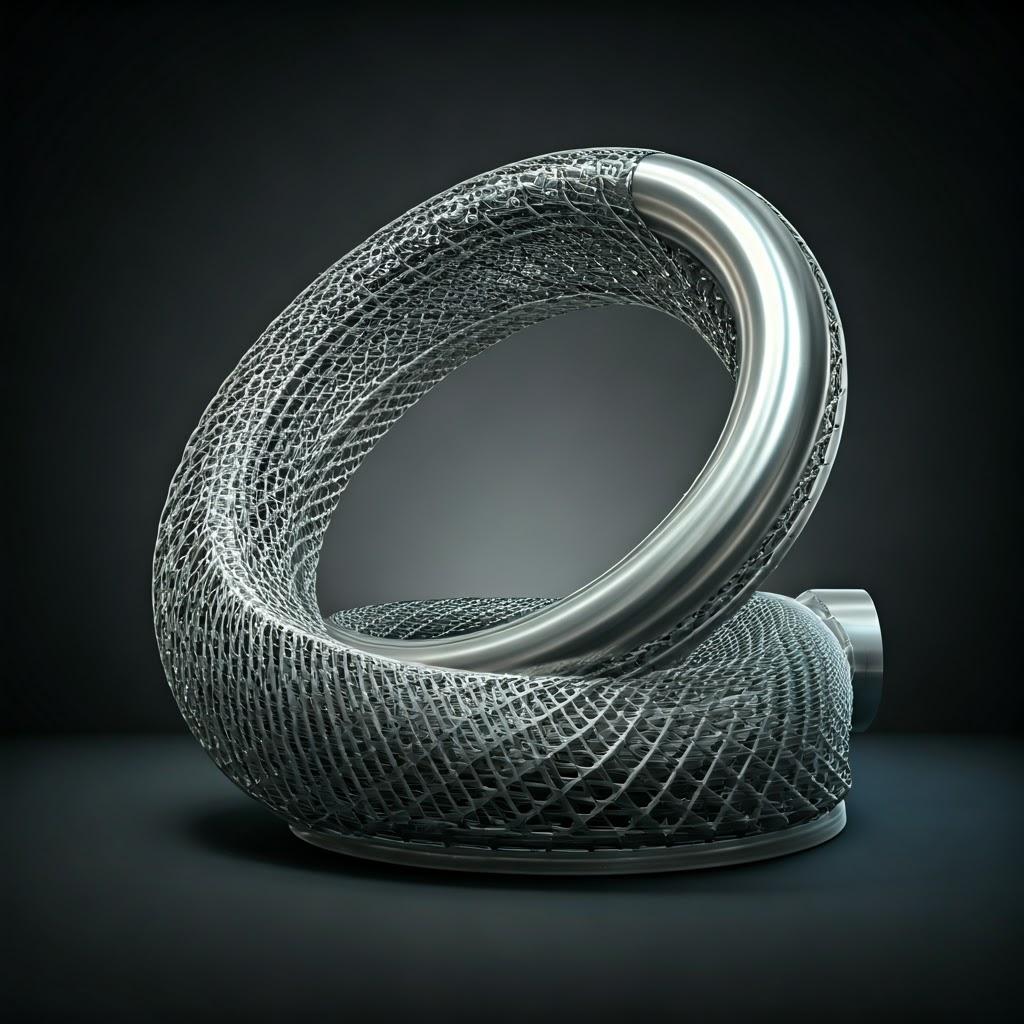
Design for Additive Manufacturing (DfAM): Optimizing Turbo Cooling Ducts
Simply taking a duct design intended for casting or fabrication and sending it to a metal 3D printer rarely yields optimal results. To truly harness the power of fabrication additive, engineers must embrace Conception pour la fabrication additive (DfAM). DfAM is not just about ensuring a part peut be printed; it’s a fundamental shift in mindset focused on leveraging the unique capabilities of layer-by-layer construction to create parts with superior performance, reduced weight, and integrated functionality – outcomes often unattainable with traditional methods. For automotive turbo cooling ducts, applying DfAM principles is crucial for maximizing cooling efficiency, minimizing weight, and ensuring manufacturability.
Key DfAM Principles for Turbo Cooling Ducts:
- Geometry Optimization for Fluid Flow: The primary function of a cooling duct is to transport air or coolant efficiently. DfAM enables designs that excel at this:
- Smooth, Sweeping Bends: Unlike fabricated ducts often limited to sharp, mitered joints, AM allows for long-radius, smooth curves. This minimizes flow separation and turbulence, reducing pressure drop and ensuring the cooling medium retains its velocity and reaches the target area effectively. Computational Fluid Dynamics (CFD) simulation becomes a powerful tool here, allowing designers to virtually test and refine internal geometries before printing.
- Optimized Cross-Sections: Duct cross-sections can be varied along the length – transitioning smoothly from circular to elliptical or other complex shapes to navigate tight spaces while maintaining the required flow area. Internal features like guide vanes or specific textures (possible with AM) could potentially be incorporated to further direct flow or enhance heat transfer, though complexity adds cost.
- Bell-Mouth Entries/Exits: Smoothly radiused entries and exits can further reduce pressure losses compared to abrupt openings.
- Strategic Wall Thickness: Traditional methods often require uniform wall thickness due to manufacturing constraints. AM allows for precision control:
- Minimum Achievable Thickness: L-PBF processes can often achieve walls as thin as 0.4-0.5 mm, though practical limits depend on the material, unsupported span, and handling requirements. This allows for direct weight savings.
- Variable Thickness: Using Finite Element Analysis (FEA) to identify stress concentrations, designers can selectively thicken walls only in high-stress areas (e.g., near mounting points, tight bends) while keeping other areas thin and light. Gradual transitions in thickness are essential to avoid stress risers.
- Targeted Reinforcement: Ribbing or localized thickening can be precisely added to enhance stiffness where needed without adding bulk to the entire structure.
- Support Structure Minimization and Management: Metal AM processes require support structures for overhanging features (typically those angled less than 45° from the horizontal build plane) and to anchor the part to the build plate, preventing warping. Supports consume extra material, add print time, and require removal effort (a significant cost driver). DfAM focuses on minimizing their necessity and impact:
- Angles autoportants : Designing features to inherently avoid shallow overhangs (aiming for >45°).
- Strategic Part Orientation: Orienting the duct on the build platform to minimize the surface area requiring supports. For a tube-like structure, printing vertically might minimize internal supports but increase build height/time, while printing horizontally might require extensive internal supports. Trade-offs must be carefully considered.
- Designing for Support Removal: If internal supports are unavoidable, incorporating access ports or designing channels with shapes (like diamonds or teardrops instead of circles) that facilitate easier support removal and powder cleaning is crucial. Sometimes supports can be designed to be intentionally weaker for easier break-off.
- Topology Optimization for Lightweighting: This advanced DfAM technique uses software algorithms to sculpt the most efficient structure based on defined loads, constraints, and performance targets (e.g., stiffness, flow rate).
- Processus : The designer defines the ‘design space’ (maximum allowable volume), connection points (flanges, mounts), load cases (vibration, pressure), and optimization goals (minimize mass, maximize stiffness). The software then iteratively removes material from non-critical areas.
- Result: Often yields highly organic, lattice-like, or bone-like structures that are unintuitive but structurally very efficient, achieving significant weight reduction (30-60% or more) while meeting performance requirements. This is highly valuable for automotive component optimization, especially in motorsport and performance vehicles. Leading topology optimization services utilize software like Altair Inspire, nTopology, or features within major CAD platforms.
- Consolidation partielle : A key strength of AM is its ability to create complex, monolithic parts that replace multi-component assemblies.
- Integration: For turbo ducts, this means integrating mounting brackets, vibration dampers, heat shields, sensor bosses (for temperature or pressure sensors), and flanges directly into the duct’s 3D printed structure.
- Avantages : Fewer parts to procure and inventory, reduced assembly time and labor, elimination of potential leak paths at joints or gasket interfaces, often lower overall weight, and improved structural integrity. This aligns perfectly with goals for efficient automotive component manufacturing.
- Surface Finish Considerations in Design: AM parts inherently have a rougher surface finish than machined parts, especially on down-facing surfaces and where supports attach. Internal surfaces of ducts are particularly important for flow.
- Impact: Rough internal surfaces can increase friction, potentially leading to higher pressure drop and reduced flow efficiency.
- Mitigation through Design: Designing smooth internal curves helps. Avoiding sharp internal corners where powder might accumulate is also beneficial. If extremely smooth internal surfaces are required, the design might need to incorporate features that allow access for post-processing methods like abrasive flow machining or electrochemical polishing.
Collaboration is Key: Effective DfAM requires a deep understanding of the specific AM process (e.g., L-PBF), material behavior (AlSi10Mg vs. IN625), and machine capabilities. Close collaboration between the component designer and the DfAM expert consultation team at the AM service provider, like Met3dp, is crucial. Met3dp’s engineers can provide invaluable feedback on printability, support strategy, orientation, and potential design modifications to optimize for cost, quality, and performance, ensuring the final product fully leverages the benefits of generative design automotive principles and metal AM technology.
Achievable Tolerances, Surface Finish, and Dimensional Accuracy
While metal additive manufacturing offers incredible design freedom, it’s essential for engineers and procurement managers to have realistic expectations regarding the achievable precision directly off the printer. Metal AM parts are built layer by layer through a complex thermal process, which inherently introduces sources of variation that affect tolerances, surface finish, and overall dimensional accuracy. Understanding these factors is key to designing functional parts and specifying appropriate quality control measures.
Tolérances typiques :
The achievable tolerances for metal AM processes like Laser Powder Bed Fusion (L-PBF), commonly used for AlSi10Mg and IN625, depend on several factors, including the specific machine, its calibration state, the material being printed, part size and geometry, and build orientation. As a general guideline, typical achievable tolerances before post-machining are often cited as:
- General Dimensions: +/- 0.1 mm to +/- 0.3 mm for smaller features (e.g., up to 50-100 mm).
- Larger Dimensions: +/- 0.1% to 0.2% of the nominal dimension for larger parts.
It’s crucial to note that these are general estimates. Complex geometries, significant thermal gradients during the build (especially with high-thermal-expansion materials or large parts), and the effectiveness of support structures can all impact these values. Furthermore, post-print stress relief heat treatments, while necessary for material properties, can sometimes cause minor, albeit predictable, distortion.
Factors Influencing Tolerances and Accuracy:
- Effets thermiques : Repeated heating and cooling layer by layer induces internal stresses. As the part cools, shrinkage occurs, and residual stresses can cause warping or distortion if not properly managed through build strategy (orientation, supports) and post-processing (stress relief). Materials like IN625, with high thermal expansion and processed at high temperatures, are more prone to these effects than AlSi10Mg.
- Machine Accuracy & Calibration: The precision of the laser or electron beam positioning system, the layer recoating mechanism, and overall machine calibration directly impact achievable accuracy. Regular maintenance and calibration by the service provider are vital.
- Caractéristiques de la poudre : Particle size distribution and morphology can influence the melt pool stability and the resulting part density and surface finish, indirectly affecting dimensional control. Met3dp’s focus on high-quality, consistent powder contributes positively here.
- Géométrie et orientation des pièces : Large flat surfaces can be prone to warping. Tall, thin features might distort. The orientation on the build plate affects not only support requirements but also how thermal stresses accumulate and potentially distort the part.
- Structures de soutien : Supports act as anchors and heat sinks. Inadequate support can lead to sagging, warping, and dimensional deviation. However, support removal can also slightly affect surface dimensions where they were attached.
Surface Finish (Roughness – Ra):
The surface finish of as-printed metal AM parts is inherently rougher than that achieved by machining or polishing. The roughness depends significantly on the surface’s orientation relative to the build direction and whether supports were present.
- Vertical Walls: Tend to have a relatively consistent finish, often in the range of 8-15 µm Ra.
- Up-facing Surfaces (Top Surfaces): Generally smoother, potentially 6-12 µm Ra, as they are formed by the top layer of melted powder.
- Down-facing Surfaces (Overhangs): Typically the roughest, often >15-20 µm Ra, as they are formed on top of loosely sintered or support material. The angle of the overhang influences roughness.
- Supported Surfaces: Show witness marks or scarring where support structures were attached and removed, requiring further finishing.
- Canaux internes : Often exhibit roughness similar to down-facing surfaces unless printed vertically. This roughness can increase friction losses for fluid flow in ducts.
Amélioration de l'état de surface : Post-processing steps like bead blasting, tumbling, or media finishing can provide a more uniform matte finish and slightly reduce Ra values. However, for significantly smoother surfaces (< 3 µm Ra, or even < 1 µm Ra), secondary operations like CNC machining, grinding, or polishing (manual, automated, or electrochemical) are necessary.
Dimensional Accuracy vs. Critical Features:
It’s important to distinguish between the general tolerances of the entire part and the specific, tighter tolerances required for critical features. For a turbo cooling duct, these might include:
- Flange flatness and bolt hole positions for sealing against the turbo or engine block.
- Internal diameters of connection ports for hoses or pipes.
- Overall length or specific mounting point locations.
While the overall form of the duct might be acceptable with standard AM tolerances, these critical interface features often require post-machining to achieve the necessary precision (e.g., +/- 0.05 mm or tighter). Good DfAM practice involves designing parts with extra ‘machining stock’ (e.g., 0.5-1.0 mm) on these critical surfaces specifically for post-machining operations.
Métrologie et contrôle de la qualité :
Reputable metal 3D printing service bureaus employ various metrology tools to ensure parts meet specifications:
- 3D Laser Scanning: Captures the overall geometry of the part quickly, allowing comparison to the original CAD model for verifying form and detecting significant deviations or warping.
- Machines à mesurer tridimensionnelles (MMT) : Provides high-accuracy point measurements for verifying critical dimensions, flatness, parallelism, and position of features.
- Other Methods: Profile projectors, gauges, and specialized inspection fixtures may also be used.
A robust Quality Management System (QMS), such as ISO 9001 or AS9100 (common in aerospace and increasingly adopted by high-end automotive suppliers), ensures processes are controlled, documented, and repeatable. Procurement managers should inquire about the provider’s QMS and quality control 3D printing procedures, including material traceability, process monitoring, and final inspection reports. Met3dp emphasizes quality throughout its process, from powder production to final part inspection, providing confidence for automotive parts inspection services.
Managing Expectations: Clear communication is vital. Engineering drawings or annotated 3D models should explicitly define critical dimensions, required tolerances, and surface finish requirements for specific features. Understanding the inherent capabilities and limitations of the AM process allows for realistic specifications and helps avoid unnecessary costs associated with overly tight tolerances on non-critical features. Early discussion with the AM provider about metal AM metrology capabilities and tolerance expectations is highly recommended.
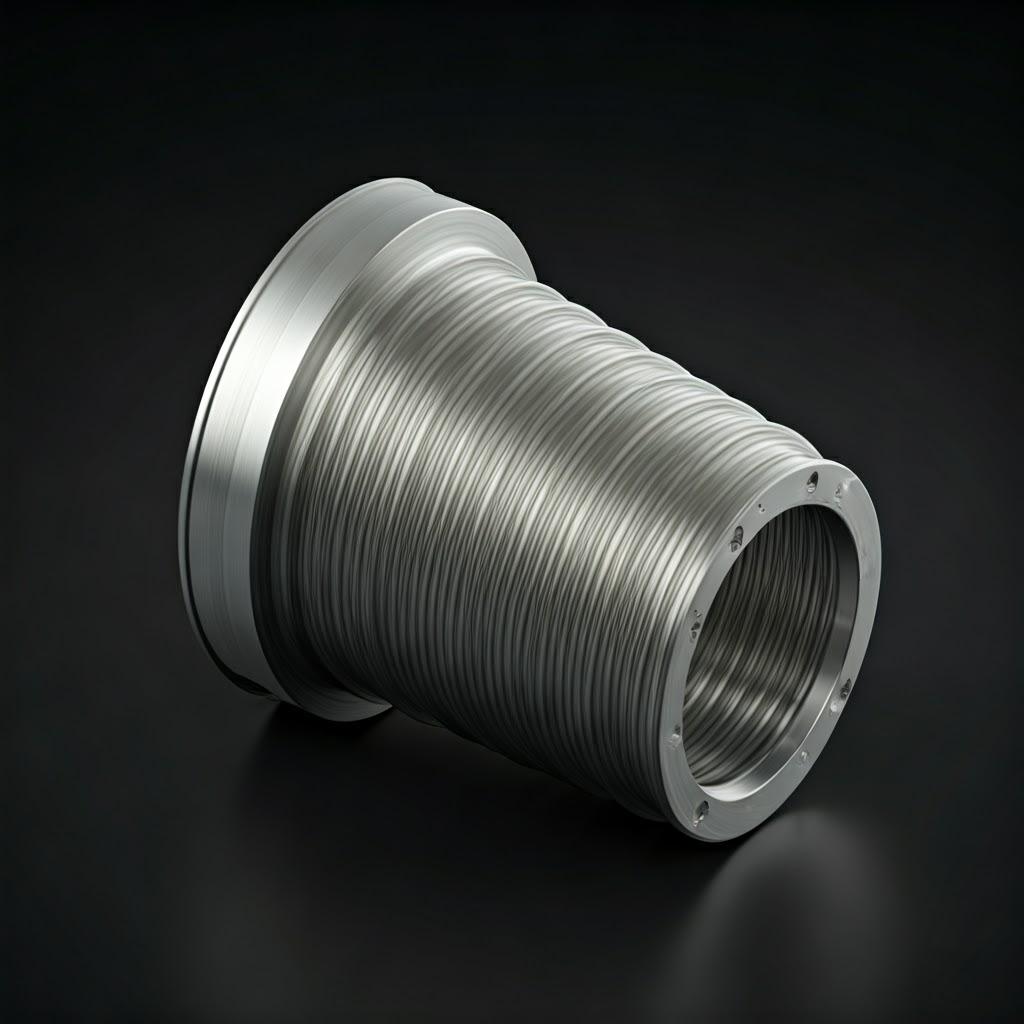
Essential Post-Processing Steps for 3D Printed Turbo Cooling Ducts
A common misconception about metal additive manufacturing is that parts emerge from the printer ready for immediate use. In reality, especially for demanding functional components like automotive turbo cooling ducts, the printing process is just one step in a larger workflow. Post-processing encompasses a series of crucial operations performed after the build is complete to remove supports, relieve stress, achieve desired material properties, meet tolerance and surface finish requirements, and ensure the part is clean and reliable for its intended application. These steps add to the final cost and lead time but are non-negotiable for producing high-quality, end-use parts.
Common Post-Processing Workflow for Metal AM Ducts:
- Soulagement du stress / Traitement thermique : This is arguably the most critical post-processing step, particularly for alloys prone to high residual stress like IN625, but also highly recommended for optimizing AlSi10Mg properties.
- Objet : The rapid heating and cooling cycles during layer-wise printing build significant internal stresses within the part. If not relieved, these stresses can cause distortion during or after printing, cracking (especially in brittle materials or complex geometries), and unpredictable mechanical behavior. Heat treatment also refines the material’s microstructure, achieving the desired hardness, strength, ductility, and fatigue life specified for the alloy (e.g., T6 condition for AlSi10Mg, annealing or aging for IN625).
- Processus : Parts are heated in a controlled atmosphere furnace (to prevent oxidation) to specific temperatures for a defined duration, followed by controlled cooling. Cycles vary significantly depending on the alloy and desired properties. For example, AlSi10Mg T6 typically involves solutionizing around 530°C, quenching, and then artificial aging around 160°C. IN625 might undergo stress relief/annealing at much higher temperatures (e.g., 870°C to 1150°C). Reliable heat treatment services familiar with AM materials are essential.
- Retrait de la pièce de la plaque de construction : The printed part(s) are securely fused to the metal build plate during the AM process. Separation is typically achieved using:
- Usinage par électroérosion à fil (EDM) : Precise method that cuts through the base of the supports or the part itself with minimal force.
- Sciage à ruban : Faster but less precise method, requiring careful handling.
- Retrait de la structure de soutien : This can be one of the most labor-intensive and challenging steps, especially for complex internal geometries or tough materials like IN625.
- Méthodes : Supports are often designed with weakened interfaces for easier removal. Manual removal involves breaking, cutting, or grinding. CNC machining or EDM might be required for hard-to-reach areas or robust supports.
- Impact: The difficulty of support removal directly impacts cost and lead time. Effective DfAM focusing on minimizing supports is highly beneficial here. Support removal AM is a specialized skill.
- Finition de la surface : As-printed surfaces are typically rough and may have partially sintered particles. Various techniques are used to achieve the required finish:
- Media Blasting (Bead/Sand Blasting): The most common initial step. Propels abrasive media against the surface to remove loose powder, create a uniform matte finish, and slightly smooth the surface. Essential for cleaning.
- Tambourinage / Finition vibratoire : Parts are placed in a tub with media that vibrates or tumbles, causing friction that smooths surfaces and deburrs edges. Suitable for batches of smaller, robust parts.
- Machining/Grinding: Used on specific surfaces requiring high smoothness (low Ra) or precise flatness/form, such as sealing faces.
- Polishing (Manual, Automated, Electrochemical): For achieving mirror-like finishes (<1 µm Ra). Electrochemical polishing is particularly effective for smoothing complex internal passages in ducts, improving flow characteristics. These are specialized surface finishing additive manufacturing techniques.
- Usinage CNC : As discussed under tolerances, critical features on AM parts often require final machining to meet tight dimensional requirements.
- Applications : Machining flange faces flat, ensuring precise bolt hole diameters and locations, achieving accurate internal diameters for hose connections, cutting threads.
- Considération : Parts must be designed with sufficient material stock in areas requiring machining. Fixturing complex AM geometries for machining can also be challenging. Access to skilled CNC machining 3D printed parts services is important.
- Leak Testing: Absolutely essential for any duct designed to carry coolant or pressurized air.
- Méthodes : Common techniques include pressurizing the duct with air and submerging it in water to look for bubbles, or using pressure decay testing where the duct is pressurized, sealed, and monitored for any pressure drop over time.
- Nettoyage : Thorough removal of all residual powder is critical, especially from intricate internal channels of cooling ducts. Trapped powder could dislodge during operation, potentially damaging the turbocharger or other downstream engine components.
- Méthodes : Compressed air blow-off, ultrasonic cleaning baths, high-pressure fluid flushing. Design features like drain holes (part of DfAM) can aid cleaning.
- Pressage isostatique à chaud (HIP) : A specialized process primarily used for fatigue-critical or high-performance applications, particularly with materials like IN625 or Titanium alloys.
- Processus : Parts are subjected to high temperature (below melting point) and high isostatic gas pressure (typically Argon) simultaneously.
- Avantages : Effectively closes internal microporosity (gas pores, lack-of-fusion voids) that can act as crack initiation sites, significantly improving fatigue life, ductility, and impact strength. Results in a near-100% dense part.
- Considérations : Adds significant cost and lead time. Usually reserved for the most demanding applications. Requires specialized HIP processing services.
- Optional Coatings: Depending on the application, coatings may be applied:
- Thermal Barrier Coatings (TBCs): Ceramic coatings applied (often via plasma spray) to hot-side IN625 ducts to reduce heat transfer to surrounding components and keep exhaust energy high. Common in thermal barrier coating automotive des applications.
- Anti-Corrosion Coatings: While AlSi10Mg and IN625 have good inherent resistance, specific coolant chemistries or environmental factors might warrant additional protection.
The specific sequence and combination of these post-processing steps depend heavily on the chosen material (AlSi10Mg vs. IN625), the complexity of the duct design, and the performance requirements defined by the application. It’s crucial for procurement teams and engineers to discuss these requirements upfront with their automotive parts finishing supplier or AM service provider to understand the implications for final part properties, cost, and delivery time.
Common Challenges in 3D Printing Turbo Ducts and Mitigation Strategies
While metal additive manufacturing unlocks incredible potential for creating optimized turbo cooling ducts, it’s a sophisticated process with inherent complexities. Achieving consistent, high-quality results requires expertise, careful process control, and proactive strategies to mitigate potential challenges. Understanding these common issues and their solutions is vital for both designers and manufacturers.
1. Warping and Distortion:
- Défi: The significant temperature gradients during printing cause expansion and contraction, leading to internal stresses. As layers build, these stresses can cause the part, especially thin-walled or asymmetric duct geometries, to warp or distort, deviating from the intended shape.
- Atténuation :
- Strategic Orientation: Positioning the part on the build plate to minimize large flat areas parallel to the plate and balance thermal mass distribution.
- Structures de soutien robustes : Supports act as anchors to the rigid build plate and help dissipate heat, counteracting warping forces. Support design requires expertise.
- Optimized Scan Strategy: The pattern and speed of the laser/electron beam can influence stress buildup. Experienced providers use optimized strategies.
- Effective Stress Relief: Performing a proper stress relief heat treatment immediately after printing, often before removing the part from the build plate, is crucial to relax internal stresses before they cause significant distortion.
2. Residual Stress Management:
- Défi: Even if warping is controlled, significant residual stresses can remain locked within the printed part. These stresses can lead to premature failure under load (especially fatigue), cause distortion during post-machining when material is removed, or even lead to cracking during printing or cooldown, particularly in stress-sensitive materials like IN625.
- Atténuation :
- Optimisation des paramètres du processus : Fine-tuning laser power, scan speed, layer thickness, and pre-heating (if applicable) to minimize stress accumulation. Requires deep material and process knowledge.
- Simulation thermique : Advanced simulation software can predict stress hotspots based on the design and build parameters, allowing for design modifications (e.g., adding fillets, adjusting thickness) or optimized support strategies before printing.
- Soulagement obligatoire du stress : As mentioned, appropriate heat treatment is non-negotiable for managing residual stress in functional metal AM parts. Residual stress mitigation AM is a primary goal of post-processing.
3. Porosity Control:
- Défi: Small voids or pores can form within the printed material due to trapped gas (from powder or shielding atmosphere) or incomplete fusion between layers/scan tracks (lack-of-fusion). Porosity reduces density, degrades mechanical properties (especially fatigue strength), and can act as crack initiation sites.
- Atténuation :
- Poudre de haute qualité : Using powder with low internal gas porosity, high sphericity, and controlled particle size distribution is fundamental. Met3dp’s advanced atomization techniques directly address this, ensuring low-porosity Met3dp metal powders.
- Optimized Print Parameters: Ensuring sufficient energy density from the laser/beam to fully melt the powder particles and allow any trapped gas to escape the melt pool.
- Machine Environment Control: Maintaining high purity of the inert shielding gas (Argon or Nitrogen) in the build chamber to prevent oxidation and contamination.
- Pressage isostatique à chaud (HIP) : For critical applications where even microporosity is unacceptable, HIP post-processing effectively closes internal voids, achieving near-full density. Porosity control 3D printing is vital for part integrity.
4. Support Removal Difficulty (Especially Internal):
- Défi: Complex duct designs often feature intricate internal channels requiring support structures that are extremely difficult or impossible to access and remove after printing. This adds significant labor cost and time, and incomplete removal can impede flow or detach later.
- Atténuation :
- DfAM is Critical: Designing self-supporting internal channel shapes (e.g., teardrop, diamond), minimizing overhangs below the self-supporting angle (~45°), and incorporating access ports specifically for support removal and inspection. Support structure optimization est essentiel.
- Specialized Removal Techniques: Utilizing tools like long-reach grinders, micro-EDM, or potentially chemical etching (material dependent) for inaccessible supports.
- Material Choice for Supports: Some systems allow for different support materials or strategies that make removal easier.
5. Powder Removal from Internal Channels:
- Défi: Similar to support removal, ensuring all loose or semi-sintered powder is removed from complex internal passages of a duct is critical but challenging. Trapped powder poses a significant contamination risk to the turbocharger and engine.
- Atténuation :
- DfAM for Cleanability: Designing smooth internal passages without sharp corners or dead zones where powder can get trapped. Including sufficient drain/access holes at low points in the design.
- Rigorous Cleaning Protocols: Employing multi-step cleaning processes involving compressed air, vibration tables, flushing with cleaning solutions, and potentially ultrasonic cleaning. Verification (e.g., borescope inspection) may be needed. Challenges with internal channel 3D printing require meticulous post-processing.
6. Achieving Desired Internal Surface Finish:
- Défi: The inherent roughness of internal AM surfaces can negatively impact fluid flow (increased pressure drop, turbulence). Achieving a smooth internal finish comparable to conventionally manufactured tubes is difficult without targeted post-processing.
- Atténuation :
- Orientation & Parameters: Printing channels vertically generally yields smoother walls than horizontal orientation. Specific parameter sets might slightly improve finish but often compromise speed or other properties.
- Targeted Post-Processing: Techniques like Abrasive Flow Machining (AFM), where abrasive putty is forced through the channel, or Electrochemical Polishing (ECP) can significantly smooth internal surfaces but add cost and complexity.
Collaboration and Expertise:
Successfully navigating these additive manufacturing challenges automotive applications present requires a deep pool of expertise spanning materials science, AM process physics, DfAM, simulation, and post-processing. This is why partnering with an experienced and well-equipped service provider like Met3dp is crucial. Their team can provide guidance from the initial design phase, leveraging simulation tools, optimizing build strategies, and implementing robust process controls and post-processing steps to mitigate risks and ensure the production of high-quality, reliable turbo cooling ducts. Proactive metal AM troubleshooting and collaborative problem-solving are hallmarks of a valuable AM partner.
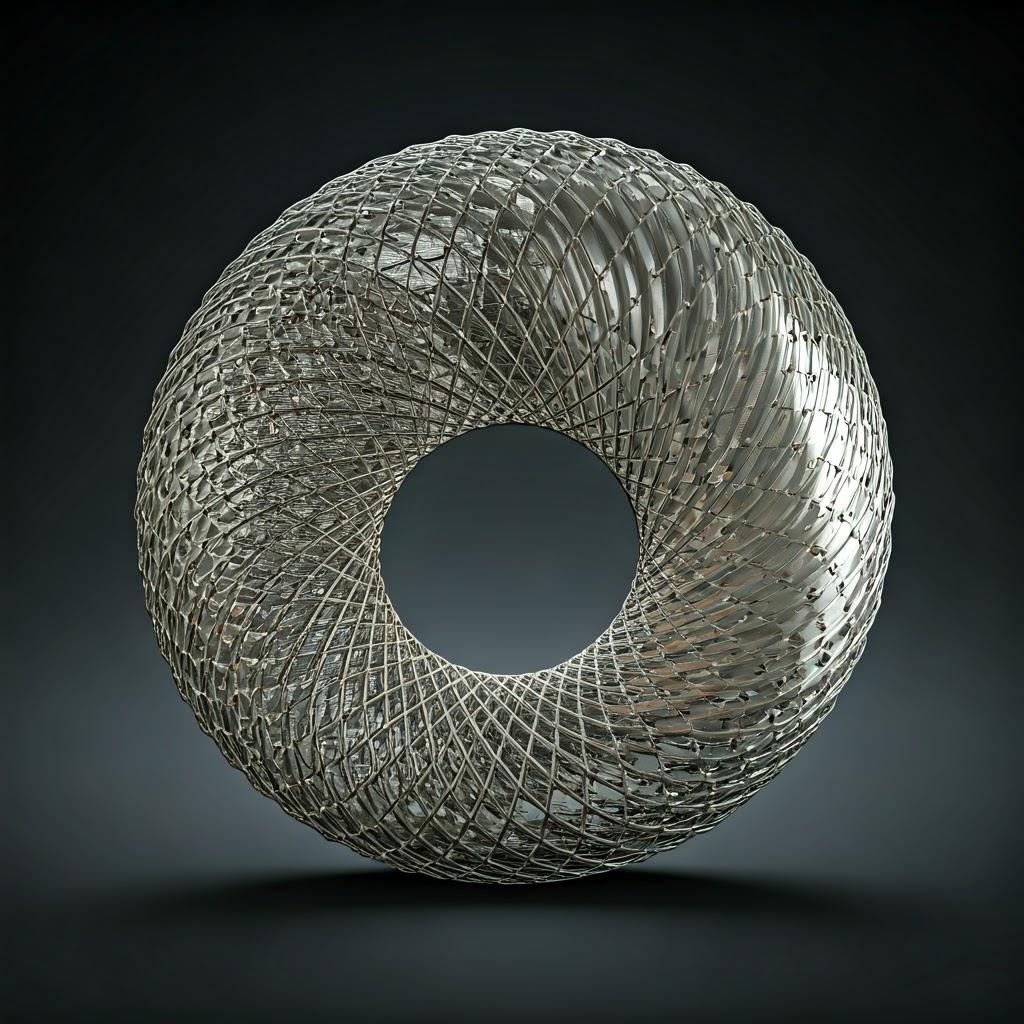
Selecting the Right Metal 3D Printing Service Provider for Automotive Ducts
Choosing a manufacturing partner is always a critical decision, but it takes on heightened importance when dealing with advanced technologies like metal additive manufacturing and demanding components like automotive turbo cooling ducts. The success of your project – achieving the desired performance, quality, cost, and timeline – hinges significantly on the capabilities and expertise of your chosen service provider. They are not just a vendor; they are a crucial collaborator who can guide you through material selection, design optimization, process intricacies, and quality assurance. For engineers and procurement managers navigating the additive manufacturing supplier evaluation process, focusing on the right criteria is essential.
Key Criteria for Evaluating Metal AM Service Providers:
- Technical Expertise & Proven Experience: Look beyond generic claims. Does the provider have demonstrable experience in the fabrication additive automobile sector? Can they showcase successful projects involving similar components (ducting, thermal management parts)? Crucially, do they have deep expertise in processing the specific materials required – lightweight AlSi10Mg and challenging high-temperature IN625? Ask for case studies, references, and evidence of their team’s DfAM (Design for Additive Manufacturing) proficiency. Experience translates into optimized designs, efficient processing, and proactive problem-solving.
- Machine Capabilities & Technology: The quality and type of AM equipment directly impact part quality, consistency, and throughput. Inquire about:
- Technologie: Primarily Laser Powder Bed Fusion (L-PBF or SLM) for AlSi10Mg and IN625. Do they operate well-maintained machines from reputable manufacturers?
- Volume de construction : Ensure their machines can accommodate the full size of your duct design.
- Fonctionnalités avancées : Do they utilize multi-laser systems (which can significantly reduce build times for larger parts or batches), in-situ monitoring capabilities, or controlled atmosphere management?
- Material Quality Assurance & Sourcing: Garbage in, garbage out applies emphatically to AM powders. Understand the provider’s approach to materials:
- Sourcing: Do they source powder from reputable, certified suppliers, or do they produce powder in-house?
- Contrôle de la qualité : What are their procedures for incoming powder inspection (e.g., chemistry, particle size distribution, morphology, flowability)? How do they handle, store, and track powder batches to ensure traceability and prevent contamination/degradation?
- Met3dp Advantage: This is where a company like Met3dp, a fournisseur leader de solutions de fabrication additive with its own advanced powder production facilities utilizing Gas Atomization and PREP technologies, offers a distinct advantage. Their integrated approach ensures control over powder quality from the very beginning, translating to higher confidence in the final printed part’s integrity and properties.
- Systèmes de gestion de la qualité (QMS) : Formal certifications demonstrate a commitment to process control, repeatability, and continuous improvement.
- ISO 9001 : A baseline expectation for quality management.
- AS9100 : The aerospace standard, indicating a higher level of process rigor, traceability, and risk management often beneficial for demanding automotive applications requiring certified metal 3D printing.
- IATF 16949: While less common for pure AM service bureaus, certification to this automotive standard would indicate a strong focus and understanding of automotive supply chain requirements. Ask about their specific quality control procedures, inspection capabilities, and documentation practices.
- Comprehensive Post-Processing Capabilities: As detailed earlier, post-processing is extensive for metal AM parts. A provider with broad in-house capabilities (stress relief, heat treatment, support removal, CNC machining, surface finishing, leak testing, HIP if needed) offers significant advantages:
- Streamlined Workflow: Reduces logistical complexity and potential delays associated with shipping parts between different subcontractors.
- Better Control: Ensures consistent quality and process management throughout the entire workflow.
- Potentially Faster Turnaround: Eliminates hand-off times between different suppliers.
- Engineering & Consultation Support: The ideal automotive AM partner acts as an extension of your engineering team. Evaluate their willingness and ability to provide:
- DfAM Expertise: Reviewing designs for printability, suggesting optimizations for performance, weight reduction, and cost savings.
- Material Selection Guidance: Advising on the best alloy based on application requirements.
- Simulation Services: Offering FEA (stress analysis) or CFD (flow analysis) to validate designs virtually.
- Capacity, Lead Time & Communication: Can the provider handle your required volume within your project timeline? Assess their:
- Capacité de production : Do they have sufficient machines and personnel? How do they manage scheduling and prioritize jobs?
- Délais d'exécution typiques : What are their realistic turnaround times for parts of similar complexity and material?
- Responsiveness & Transparency: Are they easy to communicate with? Do they provide clear updates and proactively address potential issues? This is critical for procurement teams managing timelines.
- Cost Structure & Transparency: While cost is always a factor, the cheapest option may not provide the necessary quality or expertise. Look for:
- Clear Quoting: Itemized quotes showing the breakdown of costs (material, machine time, setup, post-processing steps) are preferred.
- Value Proposition: Consider the total value offered, including engineering support, quality assurance, and reliability, not just the price per part.
- Willingness to Optimize: Are they open to discussing design changes or process adjustments to help manage costs where feasible?
Selecting a provider like Met3dp, with decades of collective expertise in metal additive manufacturing, encompassing both state-of-the-art SEBM (Selective Electron Beam Melting – though L-PBF is more typical for these specific alloys) and L-PBF printers and advanced metal powders, offers a robust foundation. Their focus on comprehensive solutions and a partnership approach helps organizations effectively implement AM and accelerate their manufacturing transformations. When seeking to find metal AM provider that meets stringent metal AM quality standards, thorough evaluation against these criteria is paramount.
Understanding Cost Factors and Lead Times for 3D Printed Turbo Ducts
For procurement managers and project engineers, understanding the primary drivers of cost and lead time for metal additive manufacturing is crucial for budgeting, planning, and supplier negotiation. The cost structure of AM differs significantly from traditional manufacturing – high initial tooling costs are eliminated, but the per-part cost is often driven more by material consumption and machine time. Lead times, while generally faster for prototyping, can vary considerably based on part complexity and post-processing requirements.
Key Cost Drivers for 3D Printed Ducts:
- Coût des matériaux :
- Type de poudre : This is a major differentiator. Nickel superalloys like IN625 are substantially more expensive per kilogram than aluminum alloys like AlSi10Mg (often 5-10x or more). Titanium alloys would fall somewhere in between or higher.
- Volume du matériau : The total amount of powder consumed, which includes not only the final part volume but also the volume required for support structures. Efficient design (topology optimization, thin walls) and optimized support strategies directly reduce material consumption.
- Recyclage : While unused powder can often be sieved and reused, there are limits and costs associated with recycling and requalification, which factor into the overall material cost applied by the service provider.
- Temps machine (temps de construction) : Often the largest single component of the cost for complex parts. It’s influenced by:
- Part Volume: Larger parts simply require more material to be melted, layer by layer.
- Part Height (Z-Height): Each layer adds a fixed recoating time, regardless of the area being printed in that layer. Taller parts inherently take longer. This is why nesting multiple parts efficiently across the build plate is important for reducing cost per part in batches.
- Complexity & Scan Strategy: Intricate features might require slower laser scan speeds for accuracy. The chosen scan strategy (e.g., pattern, laser parameters) affects both speed and final part properties/stress levels.
- Machine Technology: Multi-laser machines can significantly reduce build times compared to single-laser systems by processing multiple areas simultaneously.
- Coûts de main-d'œuvre : Skilled labor is required throughout the AM workflow:
- Setup/Teardown: Preparing the build file, setting up the machine, removing the completed build, initial cleaning.
- Post-traitement : Support removal (can be very time-consuming), surface finishing, heat treatment operation, CNC machining setup and operation, inspection. The more manual steps required, the higher the labor cost.
- Structures de soutien : Supports impact cost in multiple ways:
- Material Used: They consume powder.
- Additional Print Time: The machine has to print them.
- Effort d'enlèvement : This is often a significant labor cost, especially for internal supports or tough materials like IN625. Metal AM cost drivers are heavily influenced by support strategy.
- Exigences en matière de post-traitement : Each additional step adds cost:
- Traitement thermique : Furnace time, energy consumption, labor.
- Usinage : Machine time (often slower for tough AM materials), tooling, programming, labor.
- Finition : Labor and consumables for blasting, tumbling, polishing.
- HIP: Significant cost due to specialized equipment and long cycle times.
- Testing/Inspection: Equipment usage and technician time for leak testing, CMM reports, etc.
- Assurance qualité et inspection : The level of documentation and inspection required (e.g., basic dimensional check vs. full CMM report with material certifications) affects labor time and cost.
- Volume de commande : While AM avoids tooling costs, some economies of scale exist:
- Setup Amortization: The fixed costs of setup are spread over more parts.
- Build Plate Utilization: Printing multiple parts in a single build (nesting) is more efficient than printing them one at a time.
- Optimisation des processus : For larger batches, processes can sometimes be streamlined. Wholesale 3D printing pricing reflects these efficiencies, but the cost reduction per part typically diminishes faster than with traditional high-volume methods. Accurate metal 3D printing cost analysis requires considering all these factors.
Lead Time Components and Influences:
The total time from order placement to receiving finished parts (délai de fabrication additive) involves several stages:
- Devis et confirmation de commande : Typically 1-5 business days, depending on complexity and supplier responsiveness.
- Pre-Production (File Prep): Checking the CAD file, generating support structures, slicing the model into layers, and planning the build layout (nesting). Usually 1-2 days.
- Impression : Highly variable, from a few hours for a small prototype to multiple days (even a week+) for large, complex parts or a full build plate of parts.
- Cooldown & Depowdering: Allowing the build chamber and parts to cool safely, then removing the parts and bulk powder. Several hours to a day.
- Post-traitement : This is often the most variable stage.
- Stress Relief/Heat Treatment: Typically 1-3 days (including furnace time and cooling).
- Support Removal & Basic Finishing (e.g., Blasting): 1-2 days.
- CNC Machining: Can add several days to over a week, depending on complexity and machine availability.
- Other steps (HIP, Polishing, Testing): Each adds further time.
- Quality Control & Shipping: Final inspection, documentation, packaging. Usually 1-2 days.
Total Estimated Lead Time: Can range broadly:
- Simple Prototypes (minimal post-pro): ~ 5-10 business days
- Functional Parts (standard post-pro): ~ 2-4 weeks
- Complex Parts (extensive post-pro, IN625, HIP): ~ 4-8 weeks or longer
Key Influences on Lead Time: Part size/complexity, material choice (IN625 often requires longer print times and more post-pro), the number and intensity of post-processing steps, order quantity, and the service provider’s current workload and capacity.
Tips for Procurement & Engineers:
- Engage Early: Discuss requirements with potential suppliers during the design phase for realistic automotive parts quoting and lead time estimates.
- Provide Clear Specifications: Submit complete CAD data and drawings clearly identifying critical dimensions, tolerances, surface finishes, and required certifications.
- Optimize Design (DfAM): Collaborate with the supplier to minimize supports, reduce volume where possible, and design for manufacturability to positively impact both cost and 3D printing turnaround time.
- Prioritize Requirements: Clearly distinguish between essential requirements and ‘nice-to-haves’ regarding tolerances, finishes, or inspection levels to avoid unnecessary cost and delay. Understanding the trade-offs involved in rapid manufacturing cost versus features is key.
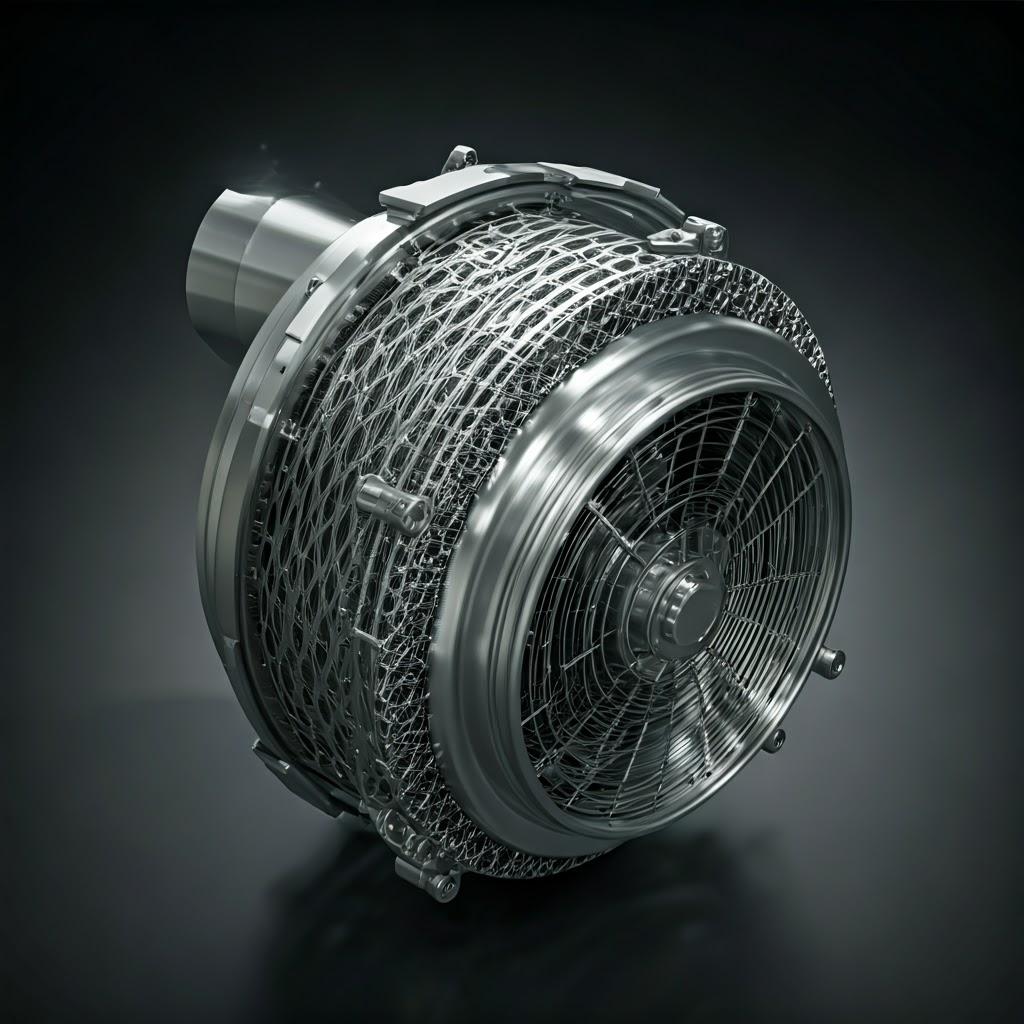
Foire aux questions (FAQ)
Here are answers to some common questions regarding 3D printed metal turbo cooling ducts:
- Q1: How does the performance of a 3D printed duct compare to a traditionally made one?
- A 3D printed duct peut offer superior performance, but it’s not automatic. The key advantage lies in the design freedom offered by additive manufacturing. If DfAM principles are used effectively (e.g., optimizing internal flow paths via CFD, achieving significant lightweighting through topology optimization, consolidating parts), the resulting AM duct can provide better cooling efficiency, reduced weight, and improved system packaging compared to a conventionally manufactured counterpart limited by traditional constraints. However, simply printing an old design without optimization may yield similar or even inferior performance due to factors like surface roughness if not managed. Performance gains are directly tied to leveraging AM’s design potential.
- Q2: Can metal 3D printed ducts handle the high temperatures and vibrations in an engine bay?
- Absolutely, provided the correct material and design considerations are employed. For extreme heat near the turbine housing (often >800°C), a nickel superalloy like IN625 is essential due to its excellent high-temperature strength and creep resistance. For moderate temperature zones (<200°C), lightweight AlSi10Mg is often suitable. Proper design using FEA to account for thermal stresses and vibrational loads, combined with appropriate post-processing (especially stress relief), ensures the duct possesses the necessary fatigue strength and durability to survive the harsh engine bay environment. Validation testing (bench testing, vehicle testing) is always recommended for critical components.
- Q3: What is the typical cost difference between printing in AlSi10Mg vs. IN625?
- There is a significant cost difference. IN625 is substantially more expensive than AlSi10Mg primarily due to:
- Raw Powder Cost: IN625 powder typically costs 5 to 10 times more (or even higher) per kilogram than AlSi10Mg powder.
- Printability & Speed: IN625 can sometimes require slower printing parameters for optimal results and stress management.
- Post-traitement : IN625 generally requires more intensive and critical post-processing, including mandatory stress relief/annealing cycles, potentially HIP, and more difficult support removal and machining due to its toughness and work-hardening characteristics.
- Overall, the final cost of an IN625 duct could easily be 5 to 15 times higher than an identical geometry printed in AlSi10Mg. The choice depends entirely on whether the extreme temperature capability of IN625 is required by the application.
- There is a significant cost difference. IN625 is substantially more expensive than AlSi10Mg primarily due to:
- Q4: Is metal 3D printing suitable for mass production of turbo cooling ducts?
- “Mass production” in the automotive sense (hundreds of thousands or millions per year) is generally still challenging for metal AM from a cost-per-part perspective compared to established methods like casting or stamping for simple geometries. However, AM is increasingly viable and advantageous for:
- Volumes faibles à moyens : Performance aftermarket, motorsport, specialty vehicles, heavy-duty trucks (tens to thousands per year).
- Highly Complex Geometries: Where AM enables designs that offer significant performance benefits (e.g., optimized flow, consolidation) unattainable otherwise.
- Consolidation partielle : Replacing a complex, multi-part fabricated assembly with a single printed part can be cost-effective even at moderate volumes when considering total system cost (assembly labor, reduced inventory, improved reliability).
- The economics of series production additive manufacturing are continually improving with faster machines, automation, and optimized workflows. While not yet replacing traditional methods for simple high-volume ducts, AM is a powerful tool for specific applications and is finding its place in niche and performance-driven series production today.
- “Mass production” in the automotive sense (hundreds of thousands or millions per year) is generally still challenging for metal AM from a cost-per-part perspective compared to established methods like casting or stamping for simple geometries. However, AM is increasingly viable and advantageous for:
Conclusion: The Future of Turbo Cooling is Additive
The demanding environment of modern turbocharged engines requires sophisticated thermal management solutions, and metal additive manufacturing has emerged as a powerful enabler for creating next-generation turbo cooling ducts. By unshackling designers from the constraints of traditional manufacturing, metal AM facilitates the creation of highly optimized, complex geometries that were previously impossible to produce. This translates directly into tangible benefits: enhanced cooling efficiency through superior fluid dynamics, significant lightweighting via topology optimization and thin-walled structures, accelerated development cycles through rapid prototyping, and improved system reliability via part consolidation.
We’ve explored how materials like lightweight AlSi10Mg are ideal for moderate temperature applications where weight saving is key, while robust IN625 provides the exceptional high-temperature strength and durability required for components enduring the extreme heat near the turbine. However, unlocking these benefits hinges on embracing Design for Additive Manufacturing (DfAM) principles, understanding the nuances of achievable tolerances and surface finishes, implementing critical post-processing steps like heat treatment and machining, and proactively mitigating potential challenges through expertise and process control.
Choosing the right manufacturing partner is paramount. A provider like Métal3DP, with deep expertise spanning advanced metal powders, sophisticated printing systems, and comprehensive application development services, can be instrumental in navigating the complexities of metal AM and ensuring project success. Their integrated approach and commitment to quality provide the foundation needed for producing reliable, high-performance automotive components.
The journey of metal AM in the automotive sector is rapidly accelerating. Driven by ongoing advancements in printing speed, material science, software tools, and automation, the technology is becoming increasingly competitive for a wider range of applications. For engineers and manufacturers grappling with complex thermal management challenges, seeking performance breakthroughs, or aiming to streamline component production, metal additive manufacturing offers compelling solutions. The future of high-performance turbo cooling, and indeed many other advanced automotive components, is increasingly additive.
Ready to explore how metal 3D printing can revolutionize your turbo cooling solutions? Contact Met3dp today to discuss your specific application, leverage their expertise, and discover the potential of Met3dp additive manufacturing solutions for your next project. Let’s shape the future of automotive manufacturing together.
Partager sur
MET3DP Technology Co. est un fournisseur de premier plan de solutions de fabrication additive dont le siège se trouve à Qingdao, en Chine. Notre société est spécialisée dans les équipements d'impression 3D et les poudres métalliques de haute performance pour les applications industrielles.
Articles connexes
À propos de Met3DP
Mise à jour récente
Notre produit
CONTACTEZ-NOUS
Vous avez des questions ? Envoyez-nous un message dès maintenant ! Nous répondrons à votre demande avec toute une équipe dès réception de votre message.
Obtenir les informations de Metal3DP
Brochure du produit
Obtenir les derniers produits et la liste des prix
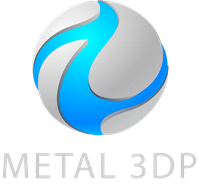
Poudres métalliques pour l'impression 3D et la fabrication additive