Fabrication additive EBM
Table des matières
Aperçu de la fabrication additive EBM
La fusion par faisceau d'électrons (EBM) est un type de fabrication additive par fusion sur lit de poudre qui utilise un faisceau d'électrons pour fondre et fusionner sélectivement des particules de poudre métallique, couche par couche, afin de construire des pièces complexes en 3D.
Les principales caractéristiques du processus EBM sont les suivantes
- Construction de pièces entièrement denses à partir de poudres métalliques
- Utilise un faisceau d'électrons comme source d'énergie
- Fonctionne sous vide et à haute température
- Obtention d'excellentes propriétés mécaniques
- Idéal pour les métaux réactifs tels que le titane et le tantale
- Permet de réaliser des géométries complexes impossibles à usiner
- Un post-traitement peut être nécessaire pour obtenir la finition de la pièce.
L'EBM offre des avantages en termes de liberté de conception, de consolidation des pièces, de réduction du poids et d'amélioration des performances dans les domaines de l'aérospatiale, du médical, du dentaire, de l'automobile et de l'industrie.
Comment Fabrication additive EBM Travaux
Le processus de fabrication additive EBM fonctionne comme suit :
- Un modèle CAO 3D est découpé en fines couches transversales.
- La poudre métallique est répartie uniformément sur une plaque de construction dans la chambre à vide.
- Un faisceau d'électrons balaie sélectivement la poudre et la fait fondre en fonction des données de la tranche.
- La plaque de construction s'abaisse et une autre couche de poudre est étalée dessus.
- Les étapes 3-4 sont répétées jusqu'à ce que la pièce soit complète.
- L'excès de poudre est éliminé et la pièce est traitée thermiquement.
- Un post-traitement tel que l'usinage ou le perçage peut être effectué si nécessaire.
La machine EBM contrôle précisément le faisceau d'électrons à l'aide de lentilles électromagnétiques et de bobines de déviation. Le processus se déroule sous vide poussé, ce qui permet d'atteindre des températures de fusion très élevées.
Types de systèmes de fabrication additive EBM
Il existe deux types principaux de machines EBM :
Type de machine | Description | Taille du bâtiment | Matériaux | Applications |
---|---|---|---|---|
Petits systèmes | Coût moins élevé, adapté aux petites pièces | 150 x 150 x 150 mm | Titane, chrome cobalt, acier inoxydable, acier à outils | Dentaire, médical, recherche |
Grands systèmes | Pour les applications de production en grande quantité | 500 x 400 x 400 mm | Titane, inconel, tantale | Aérospatiale, automobile, industrie |
Arcam EBM et GE Additive sont les principaux fabricants de systèmes EBM qui proposent des machines de petite et de grande taille.
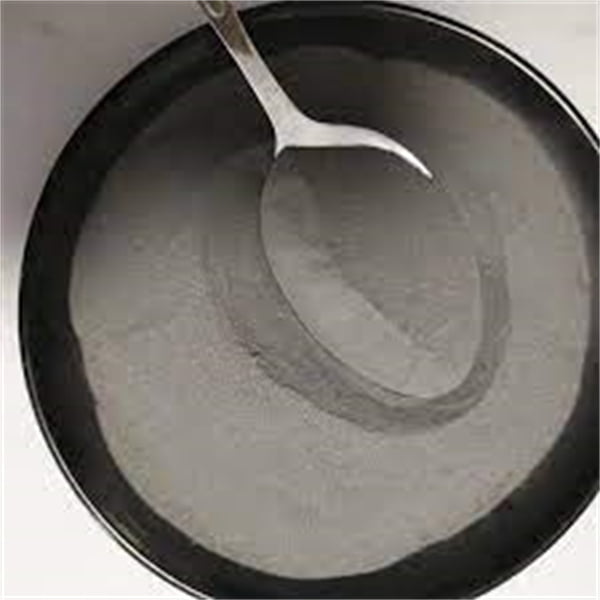
Matériaux pour la fabrication additive EBM
La technologie EBM permet de traiter toute une série de métaux :
- Alliages de titane: Ti6Al4V, Ti6Al4V ELI, TiAl
- Alliages de nickel: Inconel 718, Inconel 625
- Alliages cobalt-chrome: CoCrMo
- Aciers: Aciers inoxydables, aciers à outils, acier maraging
- Métaux réfractaires: Tantale, tungstène
- Métaux précieux: Argent, or, platine
- Alliages d'aluminium: AlSi10Mg
Le titane est particulièrement adapté à l'EBM en raison de sa réactivité. Mais ce procédé permet également de fabriquer des pièces très résistantes à la corrosion à partir d'autres alliages avancés.
Applications de la fabrication additive EBM
Les principales applications sont les suivantes
Aérospatiale: Aubes de turbines, composants de moteurs, cellules et pièces structurelles
Implants médicaux: Implants orthopédiques, dispositifs de fixation, instruments chirurgicaux
Automobile: Roues de turbocompresseurs, corps de soupapes, pièces du système d'alimentation en carburant
Industriel: Échangeurs de chaleur, récipients sous pression, corps de pompe, gabarits et montages
Pétrole et gaz: Outils de fond de puits, corps de vanne, collecteurs
Défense: Composants de satellites et d'UAV, blindage
L'EBM permet d'obtenir des composants plus légers, plus résistants et plus performants grâce à des conceptions optimisées dans l'ensemble de ces secteurs.
Bénéfices de Fabrication additive EBM
Les avantages de la technologie EBM sont les suivants
- Faible porosité - Une densité proche de 100% permet d'obtenir d'excellentes propriétés mécaniques.
- Haute résistance - Les alliages de titane égalent et même dépassent les propriétés des matériaux corroyés.
- Liberté de conception - Possibilité de fabriquer des géométries complexes
- Prototypage rapide - Accélérer les cycles de développement des produits
- Consolidation partielle - Réduit les assemblages en intégrant de multiples composants
- Réduction du poids - L'allègement des composants permet d'économiser du carburant dans l'automobile et l'aérospatiale
- Production en flux tendu - Réduit les longs délais de livraison des pièces moulées et forgées
- Produits personnalisés - Dispositifs médicaux spécifiques au patient et biens de consommation personnalisés
- Production durable - Réduction des déchets par rapport aux méthodes soustractives
Ces avantages favorisent l'adoption de l'EBM dans tous les secteurs d'activité afin d'améliorer les performances, de réduire les coûts et de permettre l'innovation de nouveaux produits.
Limites de la fabrication additive EBM
L'EBM présente certaines limites :
- Coût élevé de l'équipement - Les machines EBM ont un coût d'investissement initial élevé, de l'ordre de $500.000-$1,5 million.
- Contraintes liées à la taille des pièces - Les enveloppes de construction limitent les dimensions maximales des pièces
- Précision dimensionnelle - Le post-traitement est souvent nécessaire pour obtenir des tolérances serrées
- Finition de la surface - L'effet de marches d'escalier entraîne des surfaces rugueuses nécessitant une finition.
- Taux de construction - Plus lent que les procédés de fusion sur lit de poudre utilisant des faisceaux laser ou d'électrons
- Métaux réactifs - Limité aux métaux inertes ou aux métaux comme le titane et le tantale
- Élimination de la poudre - La poudre métallique non utilisée doit être enlevée et recyclée
- Contraintes thermiques - Peut provoquer un gauchissement des pièces et des fissures
Les développements continus de la technologie EBM visent à améliorer la vitesse, la qualité, la flexibilité des matériaux et la rentabilité.
Principes de conception pour la fabrication additive EBM
Le respect des directives de conception est essentiel pour une utilisation réussie de la technologie EBM :
- Minimiser les surplombs et les géométries non soutenues
- Inclure de petits trous (1-2 mm) pour l'élimination de l'excès de poudre.
- Utiliser des structures en treillis pour réduire le poids
- Maintenir des épaisseurs de paroi supérieures à 1 mm
- Inclure des angles ≥ 30° pour éviter les concentrations de contraintes
- Tenir compte du facteur d'échelle linéaire de 0,2%
- Tolérance de 0,2 mm sur les détails fins
- Conception de canaux internes ≥ 2 mm pour le dégagement des poudres.
- Minimiser les zones d'accumulation de poudre
- Positionner la pièce sur la plaque de manière à minimiser la surface de la section transversale
Les outils de simulation permettent d'évaluer les performances de la conception dès le début du processus de conception. Les conceptions peuvent être optimisées en fonction des capacités de l'AM.
Paramètres du processus pour l'EBM
Les paramètres critiques du processus EBM sont les suivants
- Puissance du faisceau - Affecte le taux de construction, la porosité, la microstructure
- Vitesse du faisceau - Des vitesses plus élevées augmentent le taux de construction mais peuvent compromettre la densité
- Mise au point du faisceau - Fusion du contrôle de la mise au point et de la déviation
- Stratégie de balayage - L'alternance de la direction de la trame entre les couches réduit les contraintes résiduelles
- Épaisseur de la couche - Des couches plus fines améliorent la résolution mais réduisent la vitesse de construction
- Température de construction - Des températures plus élevées réduisent les contraintes résiduelles mais compromettent la précision
- Taille du bassin de fusion - Affecte la microstructure et les propriétés locales
- Matières premières - La distribution de la taille et la morphologie des poudres influencent la densité et l'état de surface.
Le contrôle de ces paramètres permet de régler les propriétés et la qualité pour des applications spécifiques.
Post-traitement des pièces EBM
Les étapes courantes de post-traitement des pièces EBM sont les suivantes :
- Élimination de la poudre - Décapage par billes pour éliminer l'excès de poudre dans les cavités internes
- Soulagement du stress - Le pressage isostatique à chaud peut contribuer à réduire les contraintes résiduelles
- Coupure - L'électroérosion à fil pour retirer les pièces de la plaque de construction
- Usinage - Fraisage, tournage et perçage CNC pour obtenir une précision dimensionnelle et des finitions de surface
- Polissage - Pour une finition de surface brillante sur les pièces visuelles telles que les bijoux et les implants médicaux.
- Revêtements - Application de revêtements résistants à l'usure, à faible friction ou esthétiques
- Tests de qualité - Mesure des propriétés mécaniques, des défauts internes, de la microstructure
Minimiser le post-traitement permet de réduire le coût global des pièces. Mais les applications critiques peuvent nécessiter une finition poussée pour répondre aux spécifications.
Contrôle qualité pour EBM
Les procédures rigoureuses de contrôle de la qualité pour la production d'EBM impliquent :
- Inspection des matières premières - Analyse par tamisage, test de débit et microscopie de la poudre d'alimentation
- Surveillance en cours de processus - Taille du bain de fusion, température du lit de poudre, niveau de vide
- Contrôles dimensionnels - CMM et autres contrôles métrologiques des dimensions critiques
- Essais mécaniques - traction, compression, microdureté, résistance à la rupture, fatigue
- Évaluation non destructive - tomographie par rayons X pour vérifier les défauts internes
- Métallographie - Caractérisation microstructurale par microscopie optique et électronique
- Analyse de la densité - Méthode d'Archimède ou pycnométrie à l'hélium pour vérifier la densité ≥ 99,5%
- Mesure de la rugosité des surfaces - Profilométrie optique pour quantifier la texture des surfaces
- Analyse chimique - ICP et spectroscopie de masse pour vérifier la composition
- Constructions de validation - Constructions d'essai pour vérifier les paramètres du processus pour les nouvelles pièces.
Ce test complet permet de vérifier la qualité des produits EBM pour des applications industrielles strictes.
Modélisation des coûts pour Fabrication additive EBM
Les coûts totaux dépendent de
- Coût de la machine - Investissement élevé en biens d'équipement
- Coût des matériaux - Coût de la matière première en poudre/kg
- Coût de fonctionnement - Main-d'œuvre, énergie, entretien, gaz inerte
- Post-traitement - Usinage et finition supplémentaires
- Vitesse de construction - Des constructions plus rapides réduisent les coûts
- Taux d'utilisation - Une utilisation plus importante de la machine permet de répartir les coûts sur un plus grand nombre de pièces
- Taux d'achat par vol - La poudre non utilisée doit être recyclée, ce qui augmente les coûts
- Géométrie de la pièce - Les pièces compactes maximisent l'utilisation du volume de construction
- Construire du volume - Des machines plus grandes pour un meilleur rendement
- Économies d'échelle - La production en grande quantité réduit les coûts par pièce
Les coûts diminuent considérablement à mesure que les volumes de production augmentent et que la poudre excédentaire peut être réutilisée.
Sélection d'un fournisseur de fabrication additive EBM
Critères de sélection d'un prestataire de services EBM :
- Installations de systèmes éprouvées et références de clients
- Expérience diversifiée et certifiée dans les domaines de l'aérospatiale, de la médecine et des applications industrielles
- Gamme de matériaux qualifiés comme le titane, l'inconel, le chrome cobalt
- Certification du système de gestion de la qualité - ISO 9001, AS9100
- Procédures rigoureuses de contrôle de la qualité
- Inventaire des poudres standard et des poudres spéciales
- Capacités secondaires d'usinage et de finition en interne
- Soutien à la conception et services de simulation de construction
- Ingénieurs professionnels disposant d'une expertise en métallurgie
- Grandes enveloppes de construction pour un débit élevé
- Une structure de prix compétitive communiquée de manière transparente
- Capacité à gérer des projets ITAR et d'autres projets réglementés
- Situé à proximité, il permet des réunions et une collaboration en personne
Les fournisseurs de services bien établis, ayant fait leurs preuves dans des secteurs réglementés, ont tendance à mieux répondre aux attentes rigoureuses en matière de qualité.
Avantages et inconvénients de l'EBM par rapport à d'autres méthodes de gestion de l'information
Avantages de l'EBM :
- Pièces métalliques entièrement denses rivalisant avec les propriétés forgées
- Bon état de surface sur les surfaces orientées vers le haut
- Taux de fabrication élevé par rapport aux procédés laser
- Faibles contraintes résiduelles par rapport à la fusion laser sur lit de poudre
- Excellentes propriétés mécaniques des composants finis
- Le contrôle du bain de fusion permet d'affiner la microstructure
- Conditions de construction inertes idéales pour les métaux réactifs comme le titane
- Rentabilité pour les volumes de production moyens à élevés
Inconvénients de l'EBM :
- Coût d'équipement plus élevé que les systèmes à base de polymères
- Options de matériaux limitées par rapport au PBF laser
- Processus contrôlé nécessitant des opérateurs formés
- Un post-traitement important est souvent requis
- Consomme de grandes quantités d'énergie électrique
- Taille maximale de la pièce limitée par l'enveloppe de construction
- Manipulation et recyclage des poudres métalliques réactives
- Précision du profil inférieure à celle des pièces usinées ou forgées
Pour la production de pièces métalliques en volume moyen à élevé, EBM excelle à fournir une résistance et une qualité élevées à des coûts raisonnables. Mais il faut de l'expérience pour maîtriser le processus.
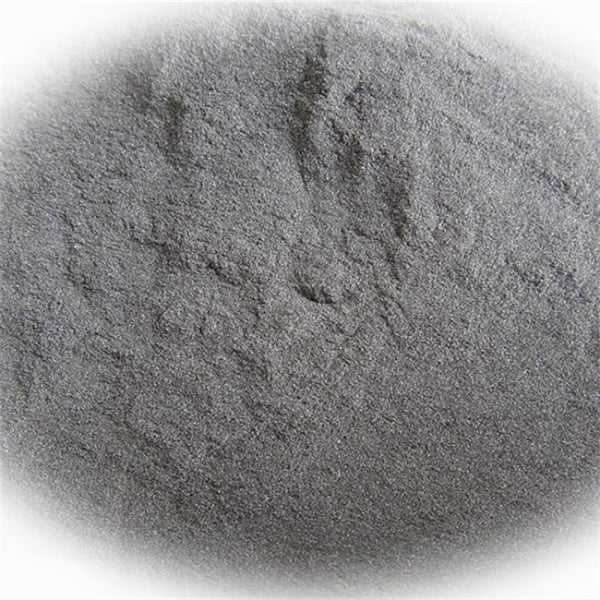
Comparaison de l'EBM avec la DMLS et la SLM
EBM vs DMLS :
Paramètres | EBM | DMLS |
---|---|---|
Source du faisceau | Faisceau d'électrons | Laser à fibre |
Atomsphère | Vide | Gaz inerte |
Matériaux typiques | Alliages de titane, tantale, inconel | Acier inoxydable, chrome cobalt, aluminium |
Taux de construction | Haut | Moyen |
Finition de la surface | Modéré | Très élevé |
Coût par pièce | Modéré | Haut |
Taille maximale des pièces | Grandes dimensions | Moyen |
EBM contre SLM :
Paramètres | EBM | SLM |
---|---|---|
Source du faisceau | Faisceau d'électrons | Laser à fibre |
Atmosphère | Vide | Gaz inerte |
Matériaux typiques | Titane, tantale, inconel | Alliages d'aluminium, aciers, alliages de nickel |
Stress résiduel | Faible | Haut |
Propriétés mécaniques | Excellent | Très bon |
Coût par pièce | Modéré | Faible |
Précision | Modéré | Haut |
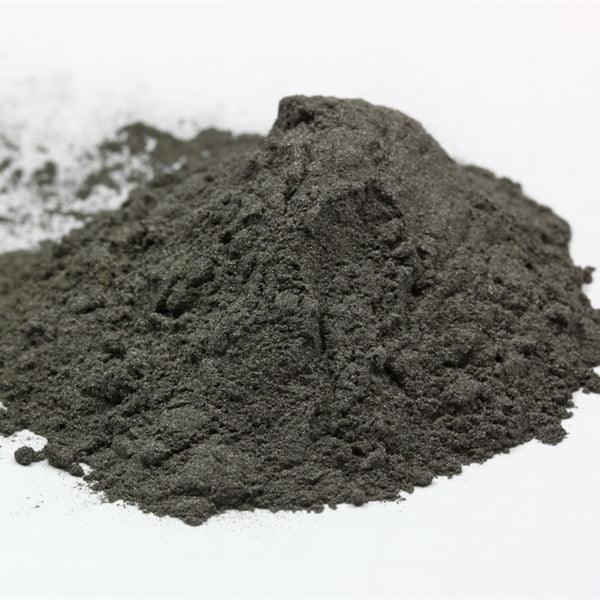
FAQ
Quels matériaux peuvent être traités à l'aide de la technologie EBM ?
Les matériaux EBM les plus courants sont les alliages de titane, les alliages de nickel comme l'Inconel, le chrome-cobalt et certains aciers à outils. Plus récemment, les métaux réfractaires et les alliages d'aluminium ont également été adoptés.
Quelle épaisseur de couche peut-on obtenir avec les systèmes EBM ?
Les machines EBM peuvent déposer des couches d'une épaisseur allant jusqu'à 50 microns. Les couches plus fines de 25 à 35 microns sont typiques pour les petites pièces complexes, tandis que les couches de 70 à 100 microns sont utilisées pour les pièces plus grandes et plus grossières.
Quelles sont les méthodes de post-traitement utilisées pour les composants EBM ?
Le post-traitement typique comprend l'enlèvement de la poudre, le détensionnement, le découpage de la plaque, l'usinage, les traitements de surface tels que le meulage ou le polissage, ainsi que l'inspection et les essais.
Quelle précision et quel état de surface peut-on obtenir avec des pièces EBM ?
Une précision dimensionnelle d'environ ±0,2% (±0,5 mm par 25 cm) est réalisable, mais les tolérances peuvent être encore améliorées grâce au post-usinage. La rugosité de surface telle que construite varie de 10 à 50 μm Ra.
Comment l'EBM se compare-t-il au DMLS pour les applications aérospatiales ?
L'EBM permet d'obtenir les mêmes propriétés matérielles que les composants en titane forgés traditionnellement pour les applications structurelles. Elle offre des taux de fabrication plus élevés que la DMLS, mais nécessite généralement un post-traitement plus important.
Partager sur
MET3DP Technology Co. est un fournisseur de premier plan de solutions de fabrication additive dont le siège se trouve à Qingdao, en Chine. Notre société est spécialisée dans les équipements d'impression 3D et les poudres métalliques de haute performance pour les applications industrielles.
Articles connexes
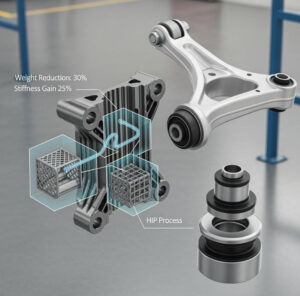
Metal 3D Printed Subframe Connection Mounts and Blocks for EV and Motorsport Chassis
Lire la suite "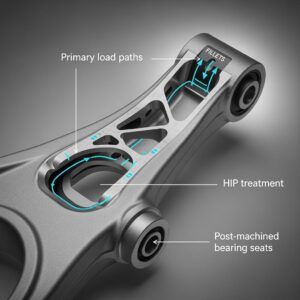
Metal 3D Printing for U.S. Automotive Lightweight Structural Brackets and Suspension Components
Lire la suite "À propos de Met3DP
Mise à jour récente
Notre produit
CONTACTEZ-NOUS
Vous avez des questions ? Envoyez-nous un message dès maintenant ! Nous répondrons à votre demande avec toute une équipe dès réception de votre message.
Obtenir les informations de Metal3DP
Brochure du produit
Obtenir les derniers produits et la liste des prix