3D Printed Aluminum Electrical Connector Housings
Table des matières
Introduction – The Imperative of High-Performance Electrical Connector Housings
In today’s rapidly evolving technological landscape, the demand for robust, reliable, and high-performance electrical connector housings is paramount across a multitude of industries. From the intricate wiring systems in aerospace and automotive to the critical connections in medical devices and the heavy-duty applications in industrial machinery, these seemingly small components play an indispensable role in ensuring seamless and secure electrical signal and power transmission. The integrity of an electrical system hinges on the quality and durability of its connectors, making the selection and manufacturing process of their housings a critical consideration for engineers and procurement managers alike. As businesses strive for greater efficiency, customization, and faster turnaround times, innovative manufacturing solutions are gaining prominence. Among these, metal Impression 3D, also known as metal additive manufacturing, stands out as a transformative technology offering unprecedented design freedom, material versatility, and the potential for significant operational advantages. This blog post delves into the application of metal 3D printing, specifically using aluminum alloys like AlSi10Mg and A6061, for the production of high-quality electrical connector housings, exploring its benefits, design considerations, and practical implications for various industries. At the forefront of this innovation is Métal3DP, a leading provider of additive manufacturing solutions committed to delivering industry-leading print volume, accuracy, and reliability. Their expertise in both 3D printing equipment and high-performance metal powders positions them as a trusted partner for organizations looking to leverage the power of metal AM.
What are 3D Printed Aluminum Electrical Connector Housings Used For? – Applications Across Industries
3D printed aluminum electrical connector housings serve as critical components in a diverse range of applications, providing protection, insulation, and secure mounting for electrical connections. Their adaptability and the ability to customize designs make them invaluable across numerous sectors:
- Aérospatiale : In the aerospace industry, where weight reduction and high reliability are crucial, 3D printed aluminum housings are used for connectors in avionics systems, satellite communication modules, and aircraft wiring harnesses. The ability to create complex geometries allows for optimized designs that meet stringent performance requirements while minimizing weight.
- Automobile : The automotive sector benefits from the lightweight and corrosion-resistant properties of aluminum 3D printed housings in various electrical systems, including sensor housings, control unit enclosures, and wiring connectors for electric vehicles. The rapid prototyping capabilities also accelerate the development of new vehicle models.
- Dispositifs médicaux : For medical applications, the biocompatibility and sterilizability of certain aluminum alloys make 3D printed connector housings suitable for diagnostic equipment, surgical instruments, and implantable devices. Customization allows for housings that fit specific device designs and patient needs.
- Fabrication industrielle : In industrial settings, these housings protect critical electrical connections in machinery, automation systems, and control panels. The durability of aluminum ensures longevity in harsh environments, contributing to reduced downtime and increased operational efficiency.
- Electronics and Telecommunications: From consumer electronics to telecommunications infrastructure, 3D printed aluminum housings provide shielding and structural support for connectors in various devices and systems. The ability to produce intricate designs enables miniaturization and improved performance.
- Robotique : The robotics industry utilizes custom-designed aluminum connector housings for power and signal transmission in robotic arms, control systems, and sensor integrations. The lightweight nature of aluminum is particularly advantageous for mobile robots.
The versatility of aluminum and the design flexibility offered by metal 3D printing enable the creation of connector housings tailored to the specific demands of each industry, often outperforming traditionally manufactured components in terms of weight, complexity, and performance. Métal3DP‘s advanced metal powders and printing technology empower businesses to explore these diverse applications with confidence. You can learn more about the possibilities on their impression 3D de métaux page.
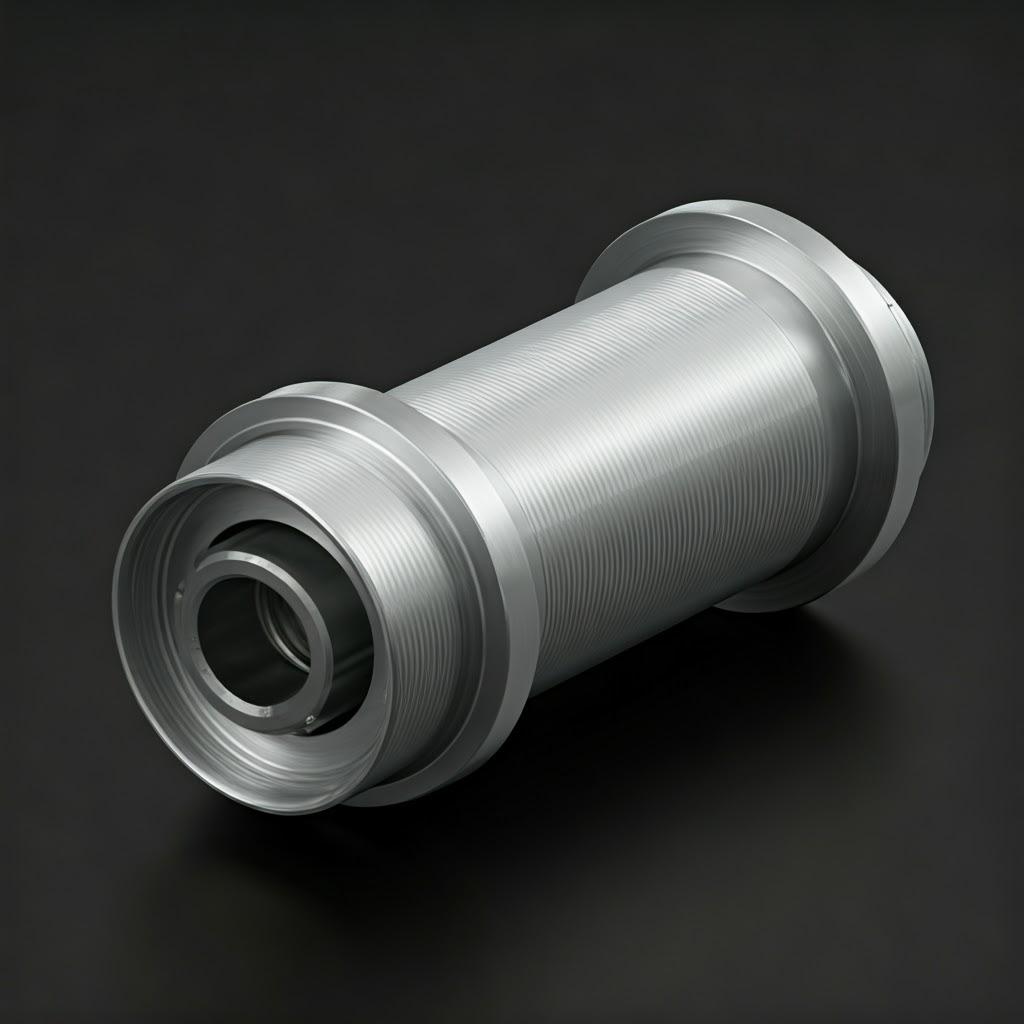
Why Choose Metal 3D Printing for Aluminum Electrical Connector Housing Manufacturing? – Advantages for Suppliers and Wholesale Buyers
Opting for metal 3D printing for the manufacturing of aluminum electrical connector housings presents a compelling array of advantages for suppliers and wholesale buyers compared to traditional manufacturing methods such as machining or die casting:
- Liberté de conception et complexité : Additive manufacturing allows for the creation of intricate geometries and internal features that are often impossible or cost-prohibitive to produce using conventional techniques. This design freedom enables the optimization of housings for specific functional requirements, such as integrated cooling channels or lightweight lattice structures.
- Customization and Rapid Prototyping: Metal 3D printing facilitates the rapid production of custom-designed connector housings in small to medium volumes without the need for expensive tooling. This is particularly beneficial for prototyping, low-volume production runs, or the creation of housings for specialized applications.
- Efficacité des matériaux et réduction des déchets : Unlike subtractive methods like machining, which remove material to create a part, 3D printing adds material layer by layer, significantly reducing material waste. This can lead to substantial cost savings, especially when working with expensive materials like aluminum alloys.
- Potentiel d'allègement : Aluminum alloys are inherently lightweight, and 3D printing allows for further weight optimization through design features like thin walls and internal voids, without compromising structural integrity. This is crucial in industries like aerospace and automotive where weight reduction translates directly to improved performance and fuel efficiency.
- On-Demand Manufacturing and Reduced Lead Times: Metal 3D printing enables on-demand production, eliminating the need for large inventories and reducing lead times associated with traditional manufacturing processes. This agility allows suppliers and buyers to respond quickly to changing demands and shorten product development cycles.
- Enhanced Functionality and Integration: 3D printing allows for the integration of multiple components into a single part, reducing assembly time and potential failure points. For electrical connector housings, this could mean incorporating features like mounting brackets or shielding directly into the design.
- Cost-Effectiveness for Low to Medium Volumes: While traditional methods may be more cost-effective for very high volumes, metal 3D printing offers a competitive edge for low to medium production runs and highly customized parts, eliminating the significant upfront costs associated with tooling.
Métal3DP‘s comprehensive solutions, including their advanced Imprimantes SEBM and high-quality aluminum powders, empower businesses to harness these advantages and revolutionize their electrical connector housing supply chain.
Recommended Aluminum Powders for Electrical Connector Housings: AlSi10Mg and A6061 – Material Properties and Benefits
When it comes to metal 3D printing electrical connector housings using aluminum, two alloys stand out for their excellent combination of properties and processability: AlSi10Mg and A6061. Métal3DP offers high-quality powders of both these materials, ensuring optimal performance for demanding applications.
AlSi10Mg :
- Composition : Aluminum alloy with approximately 10% silicon and 0.5% magnesium.
- Key Properties and Benefits:
- Excellent rapport résistance/poids : Offers high strength and hardness while remaining lightweight, crucial for aerospace and automotive applications.
- Bonne conductivité thermique : Effectively dissipates heat, important for electrical components that may generate thermal energy.
- Résistance élevée à la corrosion : Provides excellent resistance to environmental factors, ensuring long-term reliability in various operating conditions.
- Bonne soudabilité : Allows for post-processing joining if required.
- Good Processability in Laser Powder Bed Fusion (LPBF): Well-suited for LPBF processes, yielding dense and accurate parts.
- Applications : Widely used for structural components, heat sinks, and complex geometries requiring high strength and good thermal management.
A6061 :
- Composition : Aluminum alloy with magnesium and silicon as the major alloying elements.
- Key Properties and Benefits:
- Haute résistance : Exhibits excellent mechanical properties, making it suitable for demanding structural applications.
- Bonne résistance à la corrosion : Offers good resistance to corrosion in various environments.
- Excellente usinabilité : Can be easily machined for tight tolerances and fine surface finishes after 3D printing.
- Bonne soudabilité : Can be readily welded using various techniques.
- Applications polyvalentes : A widely used alloy known for its versatility and good overall performance.
- Applications : Commonly used in aerospace, automotive, and industrial applications requiring high strength and good machinability.
The choice between AlSi10Mg and A6061 depends on the specific requirements of the electrical connector housing. AlSi10Mg is often preferred for its superior printability and good balance of strength and thermal properties, while A6061 is a strong contender when high strength and excellent machinability are paramount. Métal3DP‘s expertise in des systèmes avancés de fabrication de poudres ensures that their AlSi10Mg and A6061 powders exhibit high sphericity and good flowability, leading to consistent and high-quality 3D printed parts.
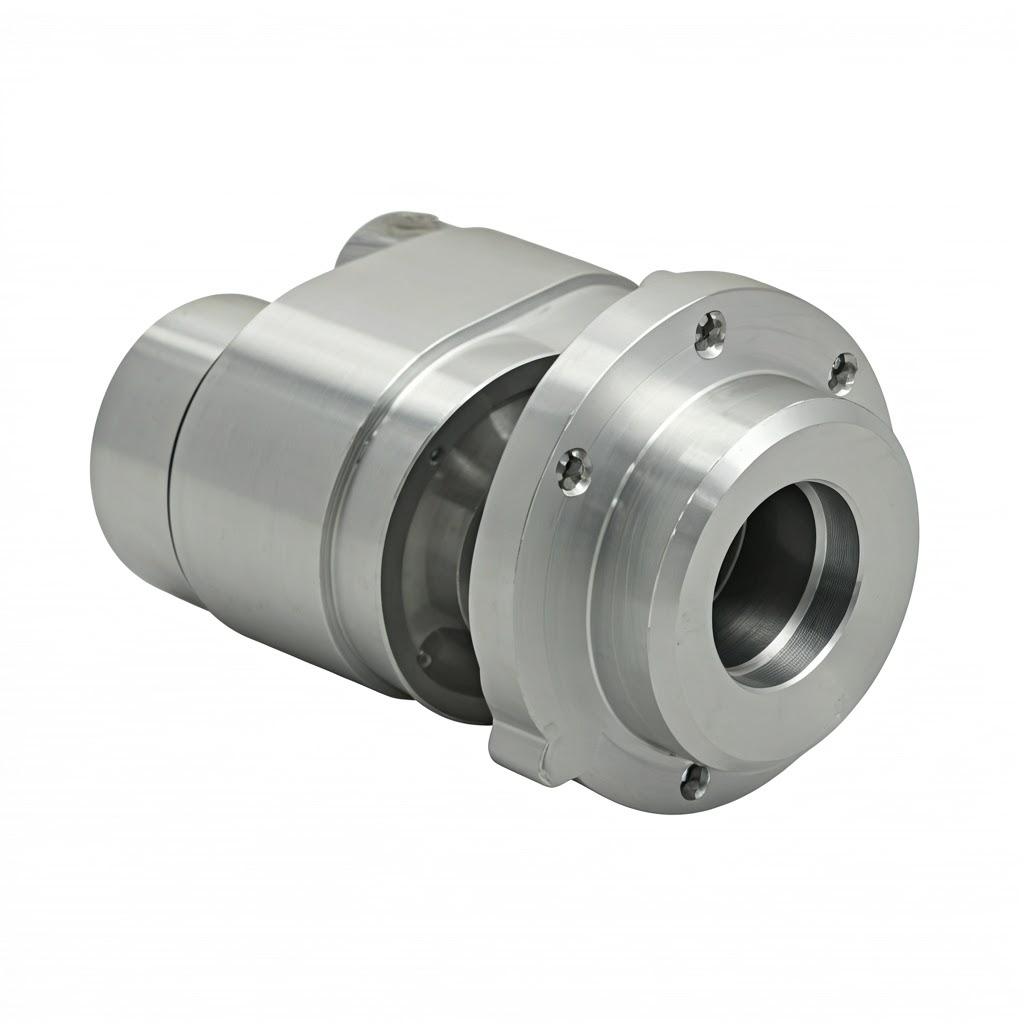
Design Optimization for Additive Manufacturing of Electrical Connector Housings – Key Considerations for Engineers
Designing for metal 3D printing differs significantly from designing for traditional manufacturing methods. To fully leverage the capabilities of additive manufacturing for aluminum electrical connector housings, engineers must consider several key factors:
- Optimisation de la topologie : This computational approach allows for the creation of designs that maximize structural performance while minimizing material usage. By defining load cases and constraints, engineers can generate lightweight yet strong housings with optimized material distribution.
- Structures en treillis : Incorporating lattice structures within the housing design can significantly reduce weight without compromising stiffness. These intricate internal networks provide support and can be tailored to meet specific mechanical requirements.
- Wall Thickness and Ribs: Careful consideration of wall thickness is crucial to balance weight, strength, and printability. Adding ribs or gussets can enhance stiffness and prevent deformation in thin-walled sections.
- Structures de soutien : Metal 3D printing often requires support structures to prevent overhangs from collapsing during the build process. Designing parts with self-supporting angles or strategically planning support placement is essential for minimizing material waste and post-processing effort.
- Orientation : The orientation of the part on the build platform can significantly impact surface finish, support requirements, and mechanical properties. Optimizing the orientation can lead to improved print quality and reduced build time.
- Tolerances and Fit: Designing for the specific tolerances achievable with metal 3D printing is crucial for ensuring proper fit and function when the housing is integrated with other components. Understanding the dimensional accuracy of the chosen printing process and material is key.
- Internal Channels and Features: Additive manufacturing allows for the creation of complex internal features, such as cooling channels or wire pathways, which can be integrated directly into the housing design, enhancing functionality and reducing assembly steps.
- Considérations relatives à l'état de surface : The as-printed surface finish of metal 3D printed parts can vary depending on the material and printing process. Designing with the intended surface finish in mind can minimize the need for extensive post-processing.
By embracing these design considerations, engineers can unlock the full potential of metal 3D printing to create highly optimized, functional, and efficient aluminum electrical connector housings. Métal3DP‘s application development services provide expert guidance to help organizations optimize their designs for additive manufacturing. You can explore different méthodes d'impression to understand their design implications.
Achieving Precision: Tolerance, Surface Finish, and Dimensional Accuracy in 3D Printed Connectors
The precision achievable in metal 3D printed aluminum electrical connector housings is a critical factor for their functionality and integration within larger systems. Understanding the typical tolerances, surface finishes, and dimensional accuracy that can be expected is essential for engineers and procurement managers:
- Précision dimensionnelle : Metal 3D printing processes, especially Laser Powder Bed Fusion (LPBF) and Electron Beam Melting (EBM), can achieve relatively high dimensional accuracy. Typical tolerances range from ±0.1 to ±0.5 mm, depending on the part size, geometry, and printing parameters. Precision can be further enhanced through optimized design and careful process control.
- Tolérance : Tolerances in 3D printed metal parts are influenced by factors such as material shrinkage during solidification, thermal gradients, and the layer-by-layer build process. Specifying appropriate tolerances in the design phase is crucial to ensure proper fit and assembly. Feature-specific tolerances should be considered based on their functional requirements.
- Finition de la surface : The as-printed surface finish of metal 3D printed parts is generally rougher compared to machined surfaces. Typical surface roughness (Ra) values can range from 5 to 20 µm, depending on the powder size, layer thickness, and build orientation. For applications requiring smoother surfaces, post-processing steps like polishing or machining are often employed.
- Facteurs influençant la précision : Several factors can affect the final precision of 3D printed metal parts, including:
- Étalonnage et maintenance des machines : Properly calibrated and maintained 3D printers are essential for consistent accuracy.
- Propriétés du matériau : The inherent properties of the aluminum alloy, such as thermal expansion and shrinkage, can influence dimensional accuracy.
- Paramètres d'impression : Layer thickness, laser power, scan speed, and other process parameters play a significant role in the final part quality and accuracy.
- Orientation de la construction : The orientation of the part on the build platform can affect dimensional accuracy and surface finish in different areas of the part.
- Post-traitement : Heat treatment can relieve internal stresses and improve dimensional stability, while machining can achieve tighter tolerances and smoother surfaces.
Métal3DP‘s state-of-the-art printing equipment and expertise in process optimization enable the production of aluminum electrical connector housings with industry-leading accuracy and repeatability. They understand the critical importance of precision for demanding applications.
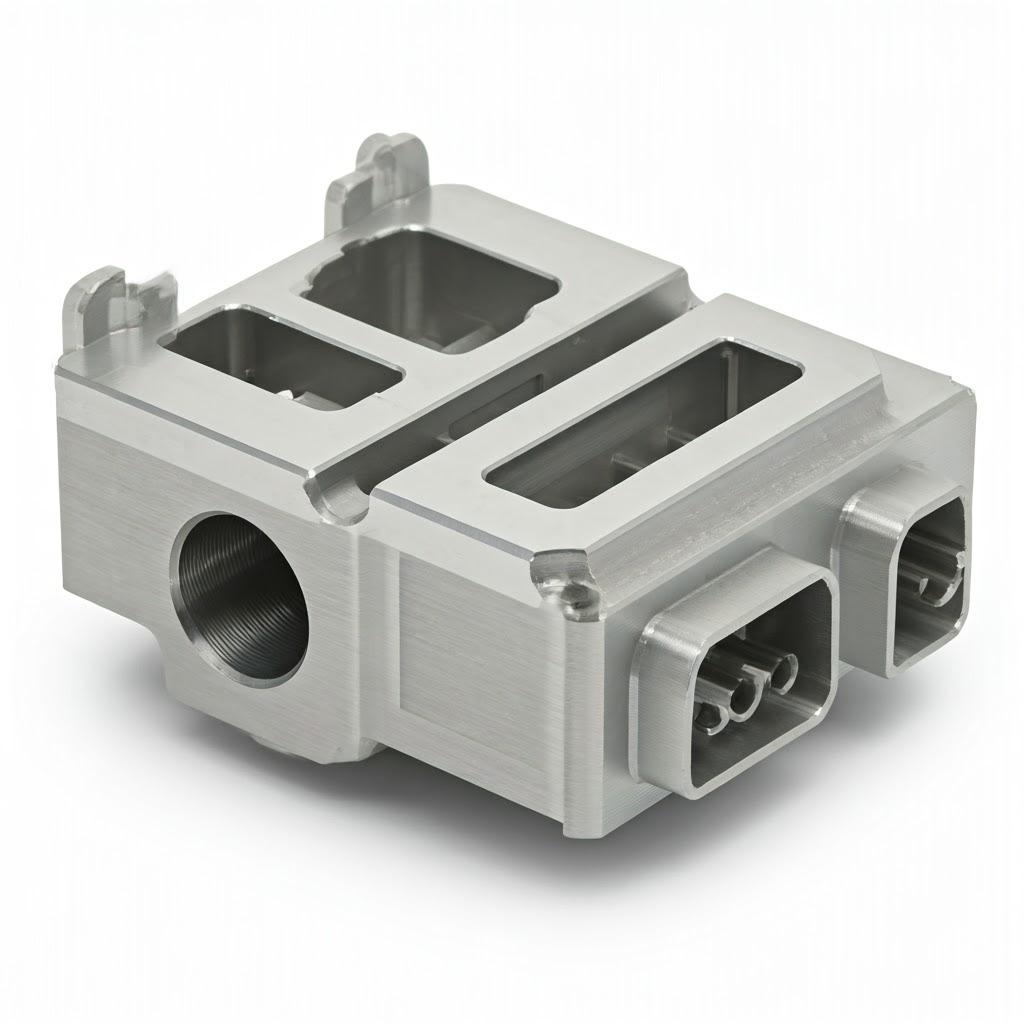
Streamlining Production: Post-Processing Requirements for Aluminum Connector Housings
While metal 3D printing offers significant advantages in terms of design freedom and customization, post-processing steps are often necessary to achieve the final desired properties, surface finish, and dimensional accuracy of aluminum electrical connector housings. Common post-processing requirements include:
- Suppression du support : Support structures, which are often required during the printing process, need to be carefully removed. This can be done manually using tools or through automated processes like machining or chemical dissolution, depending on the support material and part geometry.
- Traitement thermique : Heat treatment is often performed to relieve internal stresses that may have built up during the rapid solidification process of 3D printing. This can improve the mechanical properties and dimensional stability of the aluminum housings. Common heat treatment processes for aluminum alloys include annealing, solution treating, and aging.
- Finition de la surface : To achieve smoother surfaces or specific aesthetic requirements, various surface finishing techniques can be employed. These include:
- Media Blasting: Used to remove loose powder and improve surface uniformity.
- Polissage : Can achieve very smooth, mirror-like finishes.
- Finition par vibration : A cost-effective method for smoothing and deburring multiple parts simultaneously.
- Usinage CNC : For critical features requiring very tight tolerances or specific geometries that are difficult to achieve directly through 3D printing, CNC machining can be used as a secondary process. This allows for high-precision finishing of key interfaces and mounting surfaces.
- Coating and Plating: Depending on the application environment, coatings or plating may be applied to enhance corrosion resistance, wear resistance, or electrical conductivity of the aluminum housings. Common options include anodizing, chromate conversion coating, and electroless nickel plating.
- Inspection et contrôle qualité : Thorough inspection using techniques like coordinate measuring machines (CMM), optical scanners, and non-destructive testing (NDT) is crucial to ensure that the final parts meet the required dimensional accuracy, material integrity, and performance specifications.
The specific post-processing requirements for 3D printed aluminum electrical connector housings will depend on the application, the desired properties, and the capabilities of the chosen manufacturing service provider. Métal3DP offers comprehensive post-processing services to ensure that their 3D printed parts meet the highest quality standards.
Overcoming Challenges in Metal 3D Printing of Electrical Connectors – Solutions for Consistent Quality
While metal 3D printing offers numerous benefits, several challenges can arise during the process of manufacturing aluminum electrical connectors. Understanding these potential issues and implementing appropriate solutions is crucial for achieving consistent quality and reliable parts:
- Déformation et distorsion : Thermal stresses during the printing process can lead to warping or distortion, especially in parts with large flat areas or thin walls.
- Solutions : Optimizing part orientation, using support structures effectively, and employing build platform heating can minimize thermal gradients and reduce warping. Stress relief heat treatment after printing is also essential.
- Porosité : Internal voids or porosity can compromise the mechanical strength and electrical conductivity of the housings.
- Solutions : Optimizing printing parameters such as laser power, scan speed, and powder flow rate is crucial for achieving high density. Using high-quality, spherical powders with good flowability, like those offered by Métal3DP, also helps minimize porosity.
- Rugosité de la surface : The as-printed surface finish may be too rough for certain applications, affecting fit and performance.
- Solutions : Optimizing build orientation, reducing layer thickness, and employing post-processing techniques like media blasting, polishing, or machining can achieve the desired surface finish.
- Support Removal Issues: Removing support structures can sometimes be challenging, especially for complex geometries, and may leave surface marks.
- Solutions : Designing parts with self-supporting angles, strategically placing supports, and using dissolvable support materials can simplify removal and minimize surface damage.
- Material Property Variations: Inconsistent material properties throughout the printed part can occur due to variations in the printing process.
- Solutions : Utilizing well-calibrated and controlled 3D printing equipment, along with consistent powder quality from a reputable supplier like Métal3DP, helps ensure uniform material properties.
- Cost Management: The cost of metal 3D printing can be a concern, especially for larger production volumes.
- Solutions : Optimizing part design for efficient printing, minimizing material usage through topology optimization and lattice structures, and selecting the most cost-effective printing process and materials are key to managing costs.
By proactively addressing these potential challenges through careful design, process optimization, and collaboration with experienced metal 3D printing service providers like Métal3DP, manufacturers can ensure the consistent production of high-quality aluminum electrical connector housings.
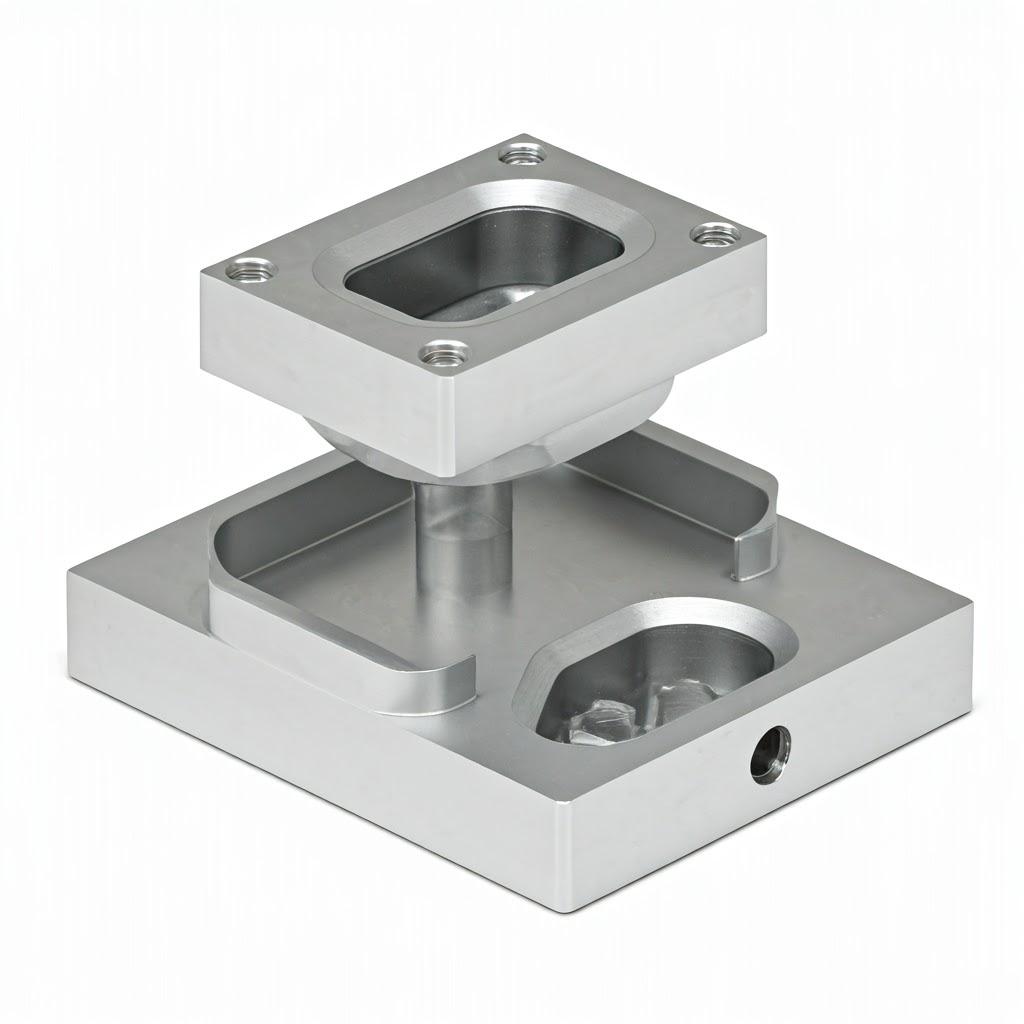
Selecting a Reliable Metal 3D Printing Service for Electrical Connector Housings – A Guide for Procurement Managers
Choosing the right metal 3D printing service provider is a critical decision for procurement managers seeking high-quality aluminum electrical connector housings. A reliable partner can significantly impact the success of a project, ensuring timely delivery, adherence to specifications, and cost-effectiveness. Here are key factors to consider when evaluating potential suppliers:
- Capacités matérielles : Ensure the service provider has experience working with the specific aluminum alloys required for your application, such as AlSi10Mg and A6061. Verify they source high-quality powders from reputable suppliers like Métal3DP.
- Printing Technology and Equipment: Understand the types of metal 3D printing technologies they utilize (e.g., LPBF, DED, Binder Jetting). The choice of technology can impact the achievable tolerances, surface finish, and mechanical properties. Inquire about the quality and maintenance of their printing equipment.
- Quality Assurance and Certifications: Look for providers with robust quality management systems and relevant certifications (e.g., ISO 9001, AS9100 for aerospace). This demonstrates their commitment to quality control and process adherence.
- Design and Engineering Support: A valuable service provider will offer design optimization expertise for additive manufacturing. They should be able to provide guidance on material selection, design for printability, and post-processing requirements. Métal3DP offers comprehensive application development services to support your design needs.
- Capacités de post-traitement : Determine if the provider offers the necessary post-processing services, such as support removal, heat treatment, surface finishing, and machining, to meet your specific requirements. An in-house capability can streamline the production process and ensure quality control.
- Experience and Expertise: Evaluate the provider’s track record and experience in producing similar components for your industry. Case studies and testimonials can provide valuable insights into their capabilities and customer satisfaction.
- Lead Times and Production Capacity: Understand their typical lead times for projects of your scale and their production capacity to ensure they can meet your delivery requirements.
- Cost Structure and Transparency: Obtain a clear breakdown of their pricing, including printing costs, material costs, and post-processing charges. A transparent pricing structure will help you accurately assess the overall cost-effectiveness.
- Communication and Customer Support: Effective communication and responsive customer support are crucial for a smooth and successful collaboration. Assess their responsiveness and willingness to address your questions and concerns.
By carefully evaluating these factors, procurement managers can select a metal 3D printing service provider that aligns with their project requirements and ensures the delivery of high-quality aluminum electrical connector housings. Consider reaching out to Métal3DP to explore their comprehensive range of services and expertise.
Understanding Cost Drivers and Lead Times for 3D Printed Aluminum Connectors – Factors for Wholesale Orders
The cost and lead time associated with 3D printed aluminum electrical connectors are influenced by several factors, which are important considerations for wholesale buyers and suppliers:
Facteurs de coûts :
- Coûts des matériaux : The price of the aluminum powder (e.g., AlSi10Mg, A6061) is a significant cost component. Specialty alloys or certified materials for specific industries (like aerospace or medical) may have higher costs. Suppliers like Métal3DP focus on providing high-quality powders at competitive prices.
- Temps de construction : The duration of the printing process directly impacts the machine utilization cost. Factors affecting build time include part size, complexity, build volume, and layer thickness. Optimizing part orientation and nesting multiple parts in a single build can help reduce build time per part.
- Coûts de post-traitement : The extent of post-processing required (support removal, heat treatment, surface finishing, machining, coatings) significantly affects the overall cost. Complex geometries requiring extensive support removal or tight tolerances necessitating CNC machining will incur higher post-processing costs.
- Machine and Labor Costs: The operational costs of the 3D printing equipment (maintenance, energy consumption) and the labor involved in design, setup, printing, and post-processing are factored into the final price.
- Volume de commande : While 3D printing can be cost-effective for low to medium volumes, economies of scale may apply for larger wholesale orders, potentially leading to per-unit cost reductions. Discussing volume discounts with your service provider is advisable.
- Complexité de la conception : Intricate designs requiring extensive support structures or complex internal features may increase printing time and material usage, thus impacting the cost. Designing for manufacturability in 3D printing can help mitigate these costs.
Délais d'exécution :
- Temps de construction : As mentioned above, the printing duration is a key component of the lead time.
- Pre-Processing Time: This includes design optimization, build preparation, material loading, and machine setup.
- Temps de post-traitement : The time required for support removal, heat treatment cycles, surface finishing, and any secondary operations like machining can significantly extend the overall lead time.
- Contrôle qualité et inspection : Thorough inspection processes add to the lead time but are essential for ensuring quality.
- Shipping and Logistics: The time taken for packaging and transportation to the final destination must also be considered.
Understanding these cost drivers and lead time factors will enable wholesale buyers to make informed decisions and effectively plan their procurement of 3D printed aluminum electrical connector housings. Transparent communication with a reliable supplier like Métal3DP regarding these aspects is crucial for a successful partnership.
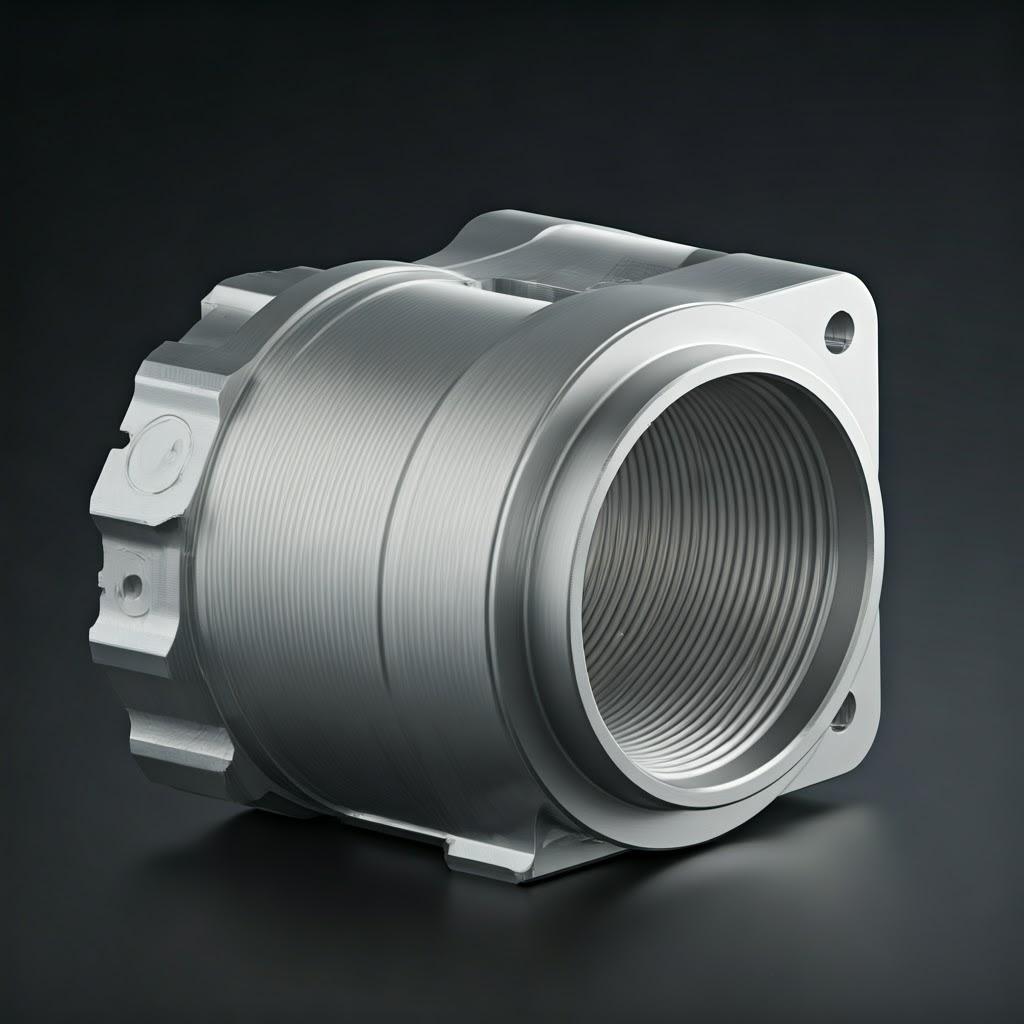
Foire aux questions (FAQ)
- What are the typical applications for 3D printed aluminum electrical connector housings?
- 3D printed aluminum housings are used in aerospace (avionics, satellites), automotive (sensor housings, EV connectors), medical devices (diagnostic equipment), industrial machinery (control panels), electronics, and robotics for protecting and mounting electrical connections.
- Can metal 3D printing achieve the same strength as traditionally manufactured aluminum housings?
- Yes, with proper material selection (like AlSi10Mg or A6061 from Métal3DP), optimized printing parameters, and appropriate post-processing (like heat treatment), 3D printed aluminum parts can achieve comparable or even superior strength-to-weight ratios compared to traditionally manufactured components.
- What are the limitations of using metal 3D printing for electrical connector housings?
- Potential limitations include higher costs for very high production volumes compared to traditional methods, the need for post-processing to achieve smooth surfaces and tight tolerances, and the learning curve associated with designing for additive manufacturing. However, these limitations are continuously being addressed through advancements in technology and materials.
Conclusion – Embracing the Future of Electrical Connector Housing Manufacturing with Metal 3D Printing
Metal 3D printing, particularly with high-performance aluminum alloys like AlSi10Mg and A6061 offered by Métal3DP, represents a paradigm shift in the manufacturing of electrical connector housings. Its ability to facilitate complex designs, enable rapid customization, reduce material waste, and offer lightweighting potential provides significant advantages across diverse industries, including aerospace, automotive, medical, and industrial manufacturing.
By understanding the design considerations, achievable precision, post-processing requirements, and potential challenges, engineers and procurement managers can effectively leverage this innovative technology. Choosing a reliable partner like Métal3DP, with their expertise in advanced metal powders and printing solutions, ensures the production of high-quality, application-specific electrical connector housings that meet stringent performance and reliability standards. As technology continues to advance, metal 3D printing will undoubtedly play an increasingly vital role in shaping the future of electrical component manufacturing, offering unparalleled design freedom and efficiency. Contact Métal3DP today to explore how their capabilities can power your organization’s additive manufacturing goals. You can find more information on their site web.
Partager sur
MET3DP Technology Co. est un fournisseur de premier plan de solutions de fabrication additive dont le siège se trouve à Qingdao, en Chine. Notre société est spécialisée dans les équipements d'impression 3D et les poudres métalliques de haute performance pour les applications industrielles.
Articles connexes
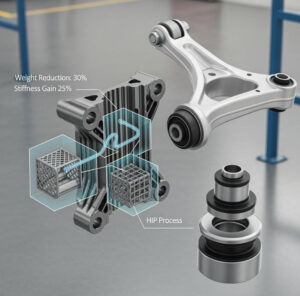
Metal 3D Printed Subframe Connection Mounts and Blocks for EV and Motorsport Chassis
Lire la suite "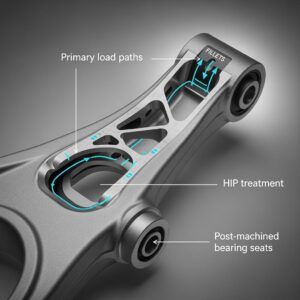
Metal 3D Printing for U.S. Automotive Lightweight Structural Brackets and Suspension Components
Lire la suite "À propos de Met3DP
Mise à jour récente
Notre produit
CONTACTEZ-NOUS
Vous avez des questions ? Envoyez-nous un message dès maintenant ! Nous répondrons à votre demande avec toute une équipe dès réception de votre message.
Obtenir les informations de Metal3DP
Brochure du produit
Obtenir les derniers produits et la liste des prix