High-Temperature Exhaust System Components via 3D Printing
Table des matières
Introduction – The Critical Role of High-Temperature Materials in Exhaust Systems
In demanding industries like aerospace, automotive, medical, and industrial manufacturing, exhaust systems face extreme operating conditions. These systems must efficiently expel combustion byproducts while enduring high temperatures, corrosive environments, and significant mechanical stresses. Traditionally, manufacturing these intricate components has involved complex and often costly processes. However, the advent of metal 3D printing, also known as additive manufacturing, presents a revolutionary approach to producing high-temperature exhaust system components with enhanced performance and design flexibility. At https://met3dp.com/, we understand these critical demands and offer advanced metal Impression 3D solutions tailored to meet the rigorous specifications of high-temperature applications.
What are High-Temperature Exhaust System Components Used For?
High-temperature exhaust system components play a crucial role in a variety of applications across diverse industries. In the secteur aérospatial, these components are integral to jet engines, rocket propulsion systems, and auxiliary power units, where they manage extremely hot gases generated during combustion. Le l'industrie automobile relies on these parts for exhaust manifolds, turbocharger housings, and catalytic converter casings, which must withstand high thermal cycling and corrosive exhaust gases to ensure optimal engine performance and emissions control. In fabrication industrielle, these components are found in gas turbines, power generation equipment, and chemical processing plants, handling hot and often corrosive process streams. Even in the domaine médical, specialized exhaust systems in sterilization equipment and certain diagnostic tools require materials capable of withstanding elevated temperatures. The functionality of these components is paramount for the overall efficiency, safety, and longevity of the systems they serve.
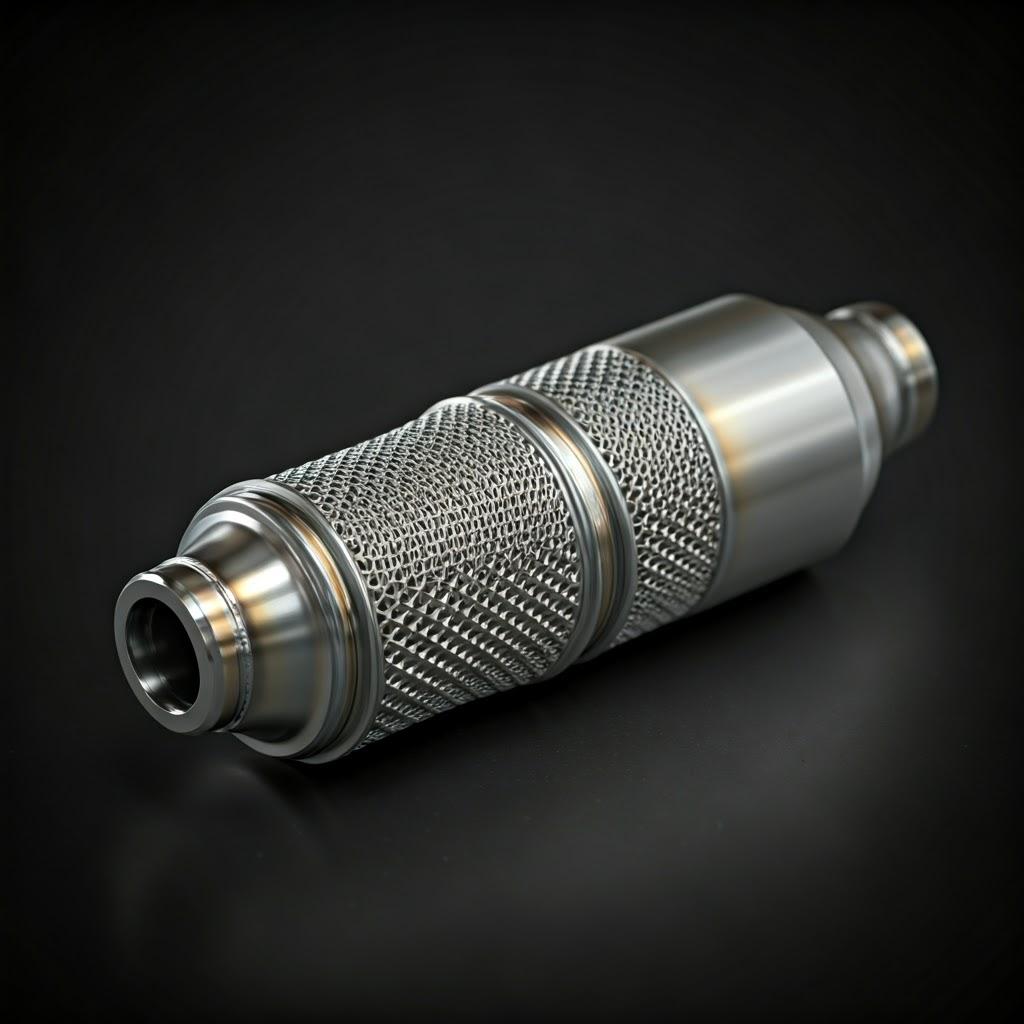
Why Use Metal 3D Printing for High-Temperature Exhaust System Components?
Opting for metal 3D printing for the fabrication of high-temperature exhaust system components offers a multitude of advantages over traditional manufacturing methods.
- Liberté de conception : Additive manufacturing allows for the creation of complex geometries and internal features that are difficult or impossible to achieve with conventional techniques like casting or machining. This enables engineers to optimize component designs for improved flow dynamics, reduced weight, and enhanced heat dissipation.
- Efficacité matérielle : 3D printing uses material only where it’s needed, significantly reducing waste compared to subtractive methods. This is particularly beneficial when working with expensive, high-performance alloys.
- Prototypage rapide et itération : Metal 3D printing accelerates the design and development cycle. Prototypes can be produced quickly, allowing for rapid testing and design iterations to optimize performance before mass production.
- Customization and Complexity: Each component can be tailored to specific application requirements without the need for new tooling, making it ideal for low-volume production or highly specialized parts.
- Amélioration des performances : By utilizing advanced metal powders and optimized designs, 3D-printed exhaust components can exhibit superior strength-to-weight ratios, improved thermal management, and enhanced resistance to corrosion and wear.
- Fabrication à la demande : 3D printing facilitates on-demand production, reducing the need for large inventories and enabling quicker response to changing demands.
Metal 3D printing services provided by Met3dp leverage these advantages to deliver high-quality, custom exhaust system components tailored to the most demanding applications.
Recommended Materials and Why They Matter
For high-temperature exhaust system components, the choice of material is critical to ensure performance and longevity. Met3dp recommends IN625 et IN718 for these demanding applications due to their exceptional high-temperature properties and corrosion resistance.
IN625
IN625 is a nickel-chromium-molybdenum alloy renowned for its:
- Excellente résistance à la corrosion : It exhibits superior resistance to a wide range of corrosive environments, including oxidation, pitting, and crevice corrosion, making it ideal for harsh exhaust gas conditions.
- High strength at elevated temperatures: IN625 maintains significant strength and creep resistance at high temperatures, crucial for withstanding the thermal stresses in exhaust systems.
- Good fatigue strength: This alloy offers excellent resistance to fatigue failure caused by thermal cycling and mechanical vibrations.
- Soudabilité : IN625 can be readily welded, a significant advantage for complex exhaust system assemblies.
Typical Applications of IN625 in Exhaust Systems:
- Collecteurs d'échappement
- Composants du turbocompresseur
- Bellows and expansion joints
- High-temperature ducting
IN718
IN718 is a nickel-chromium alloy strengthened by precipitation hardening, offering:
- Exceptional high-temperature strength: It exhibits outstanding tensile, creep, and rupture strength at temperatures up to 700°C (1300°F).
- Excellente résistance à la corrosion : IN718 provides good resistance to oxidation and many corrosive environments encountered in exhaust systems.
- Bonne soudabilité : Compared to other high-strength nickel-based superalloys, IN718 offers relatively good welding characteristics.
Typical Applications of IN718 in Exhaust Systems:
- Jet engine exhaust components
- Composants de turbines à gaz
- Pièces de moteur-fusée
- High-performance automotive exhaust systems
The advanced poudres métalliques offered by Met3dp, including IN625 and IN718, are meticulously processed using industry-leading gas atomization and PREP technologies. This ensures high sphericity and excellent flowability, critical for producing dense, high-quality 3D-printed components with superior mechanical properties.
Table 1: Comparison of IN625 and IN718 for High-Temperature Exhaust Systems
Propriété | IN625 | IN718 | Importance for Exhaust Systems |
---|---|---|---|
Résistance à haute température | Good strength and creep resistance up to 980°C (1800°F) | Exceptional strength up to 700°C (1300°F) | Critical for withstanding thermal stresses and maintaining structural integrity. |
Résistance à la corrosion | Excellent resistance to a wide range of corrosive environments | Good resistance to oxidation and many corrosive environments | Essential for preventing degradation from exhaust gases and environmental factors. |
Résistance à la fatigue | Good resistance to thermal and mechanical fatigue | Good fatigue strength | Important for components subjected to cyclical loading and vibrations. |
Soudabilité | Bonne soudabilité | Relatively good weldability compared to other high-strength superalloys | Facilitates the fabrication of complex assemblies. |
Applications typiques | Manifolds, turbocharger parts, bellows, high-temperature ducting | Jet engine exhausts, gas turbine components, rocket parts, auto exhausts | Demonstrates the versatility of these alloys in demanding high-temperature environments. |
Exporter vers les feuilles
By carefully selecting the appropriate material based on the specific operating conditions and performance requirements, engineers can leverage metal 3D printing to create high-temperature exhaust system components with optimized durability and efficiency. Contact Met3dp today to discuss your specific material and application needs and explore how our advanced additive manufacturing solutions can benefit your organization.
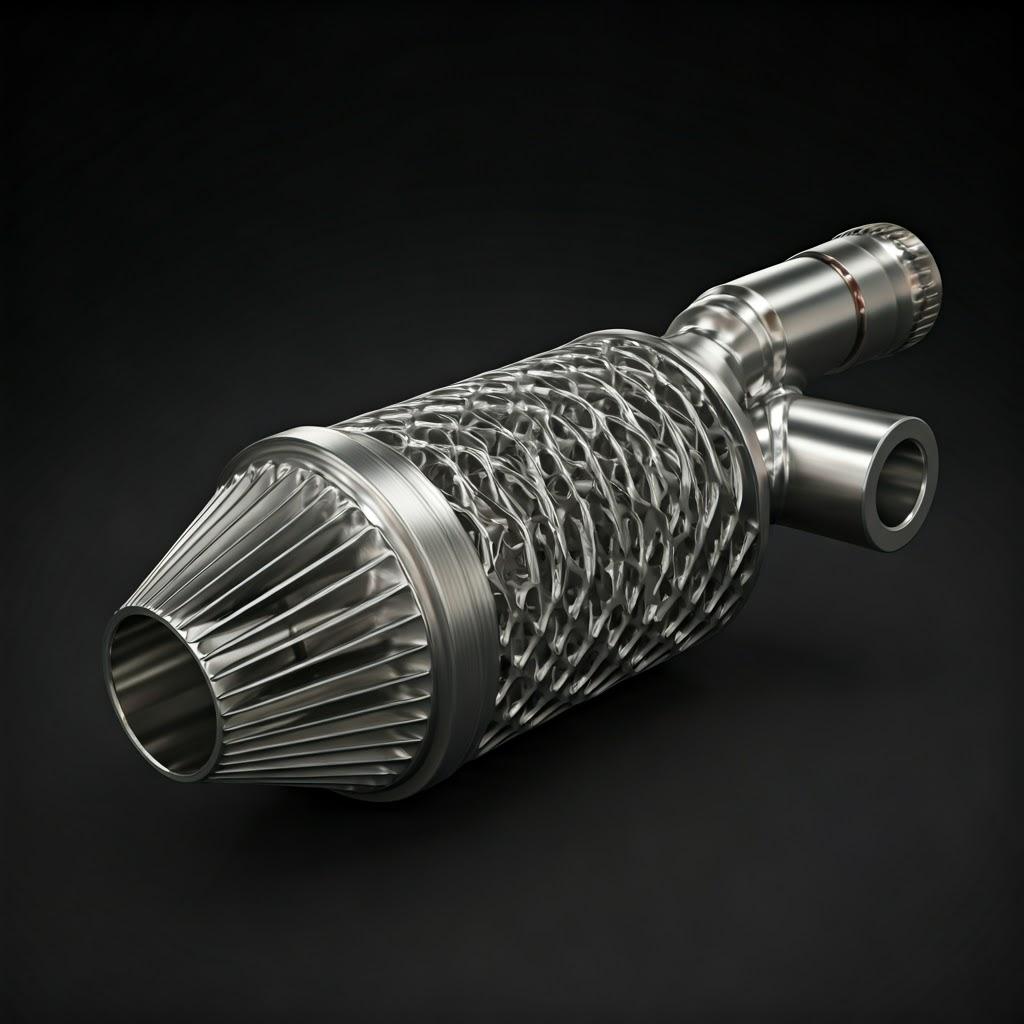
Design Considerations for Additive Manufacturing of Exhaust System Components
Designing for metal 3D printing requires a different mindset compared to traditional manufacturing. To fully leverage the capabilities of additive manufacturing for high-temperature exhaust system components, engineers should consider the following design principles:
- Optimisation de la topologie : This computational method can identify and remove material from low-stress areas, resulting in lightweight yet structurally sound components. For exhaust systems, this can lead to reduced weight, improving overall system efficiency.
- Structures en treillis : Incorporating lattice structures within the design can provide significant weight reduction while maintaining or even enhancing stiffness and strength. These intricate internal geometries are only achievable through 3D printing. In exhaust systems, lattice structures can also be designed to enhance heat transfer.
- Consolidation des pièces : Additive manufacturing allows for the integration of multiple components into a single, complex part. This reduces the need for assembly, lowers the risk of failure at joints, and can improve overall system reliability. For example, flanges, brackets, and sensor housings can be directly incorporated into the main exhaust duct.
- Customized Cooling Channels: Internal cooling channels with complex geometries can be designed and printed directly within the exhaust component. This enables efficient heat dissipation, protecting the material from extreme temperatures and extending the component’s lifespan.
- Surface Texture Optimization: The surface finish of 3D-printed parts can be tailored to specific functional requirements. For exhaust systems, controlled surface roughness can influence fluid flow and heat transfer characteristics.
- Minimisation des structures de support : While support structures are often necessary during the printing process, careful design can minimize their use, reducing post-processing time and material waste. Features like self-supporting angles and strategic part orientation can help achieve this.
- Wall Thickness and Ribbing: Optimizing wall thickness and incorporating ribs can enhance the structural integrity of the component without adding excessive weight. This is crucial for withstanding the pressure and vibrations within exhaust systems.
- Intégration des fonctionnalités : Features such as mounting points, sensor ports, and flow directors can be directly integrated into the 3D model, eliminating the need for secondary operations.
By embracing these design considerations, engineers can unlock the full potential of metal 3D printing to create high-performance, lightweight, and highly functional exhaust system components. Met3dp’s expertise in méthodes d'impression ensures that your designs are optimized for manufacturability and performance.
Tolerance, Surface Finish, and Dimensional Accuracy of 3D-Printed Exhaust Components
Achieving the required tolerance, surface finish, and dimensional accuracy is paramount for the proper functioning and integration of exhaust system components. Metal 3D printing technologies have made significant advancements in these areas.
- Tolérance : Depending on the specific 3D printing technology and material, tolerances of ±0.1 mm or even tighter can be achieved. Factors influencing tolerance include the printer’s accuracy, material shrinkage during solidification, and post-processing techniques. At Met3dp, our state-of-the-art Selective Electron Beam Melting (SEBM) printers are known for their high accuracy and ability to produce parts with tight tolerances, crucial for ensuring proper fit and sealing in exhaust systems.
- Finition de la surface : The as-printed surface finish typically depends on the powder particle size and layer thickness used during the printing process. While it may be rougher than machined surfaces, various post-processing techniques like polishing, blasting, and machining can be employed to achieve smoother finishes as required by the application. For exhaust systems, a smooth internal surface can be beneficial for reducing flow resistance.
- Précision dimensionnelle : Dimensional accuracy refers to the degree to which the printed part matches the intended design dimensions. This is influenced by factors such as printer calibration, material properties, and part orientation during printing. Careful process control and optimization are essential to achieve high dimensional accuracy. Met3dp’s commitment to quality and precision ensures that our 3D-printed exhaust components meet stringent dimensional requirements.
Table 2: Typical Tolerance and Surface Finish Capabilities in Metal 3D Printing
Propriété | Selective Laser Melting (SLM) / Direct Metal Laser Sintering (DMLS) | Fusion sélective par faisceau d'électrons (SEBM) | Jetting de liant |
---|---|---|---|
Tolérance | ±0.05 – ±0.2 mm | ±0.1 – ±0.3 mm | ±0.2 – ±0.5 mm (before sintering and infiltration) |
Finition de la surface (Ra) | 5 – ; 20 µm | 10 – 30 µm | 10 – 40 µm (after sintering) |
Exporter vers les feuilles
Note: These values are typical ranges and can vary depending on the specific machine, material, and process parameters. Post-processing can significantly improve surface finish and dimensional accuracy.
For critical exhaust system interfaces, post-processing steps like CNC machining can be employed to achieve very tight tolerances and smooth surface finishes on specific areas. Met3dp offers comprehensive post-processing services to meet the exact specifications of your application.
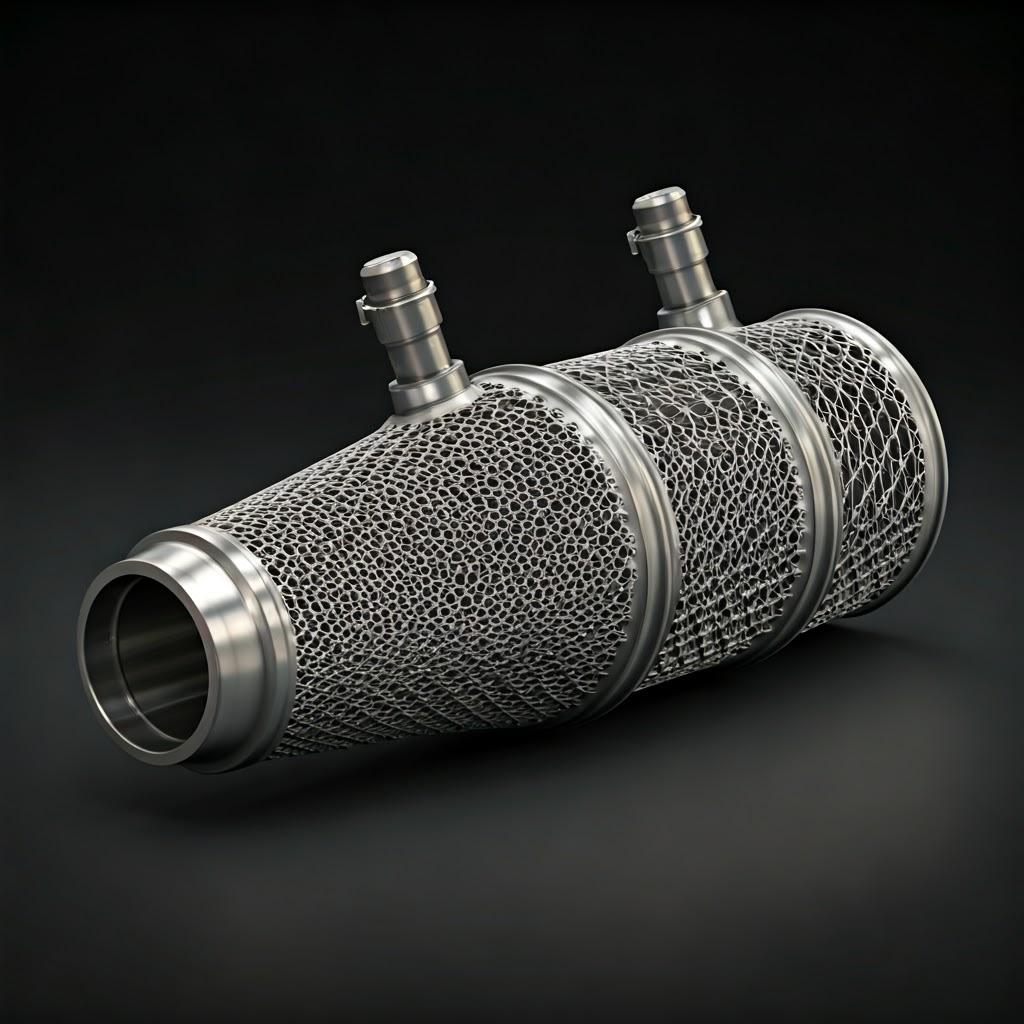
Post-Processing Requirements for Metal 3D-Printed Exhaust Components
While metal 3D printing offers significant advantages, post-processing is often required to achieve the final desired properties and dimensions of exhaust system components. Common post-processing steps include:
- Suppression du support : Support structures, necessary during printing to prevent collapse or distortion, must be removed. This can be done manually, mechanically, or through chemical dissolution, depending on the material and support type.
- Traitement thermique : Heat treatment is crucial for relieving internal stresses, optimizing the microstructure, and achieving the desired mechanical properties of the 3D-printed metal. This may involve processes like annealing, stress relieving, or hot isostatic pressing (HIP). For high-temperature alloys like IN625 and IN718, specific heat treatment cycles are essential to maximize their high-temperature strength and creep resistance.
- Finition de la surface : As mentioned earlier, various surface finishing techniques can be applied to improve the surface roughness, aesthetics, or corrosion resistance of the components. These include polishing, grinding, shot peening, and sandblasting.
- Usinage CNC : For critical features requiring very tight tolerances or specific surface finishes, CNC machining can be used as a secondary operation. This is often applied to mating surfaces, threads, or other functional areas.
- Revêtement : Coatings can be applied to enhance the corrosion resistance, wear resistance, or thermal barrier properties of the exhaust components, especially in harsh operating environments. Examples include ceramic coatings or specialized metallic coatings.
- Inspection et contrôle qualité : Thorough inspection using techniques like coordinate measuring machines (CMM), non-destructive testing (NDT), and material analysis is essential to ensure the quality and integrity of the final components.
Met3dp provides a comprehensive suite of post-processing services, ensuring that your 3D-printed exhaust system components meet the highest standards of quality and performance. Our expertise in material science and manufacturing processes allows us to tailor the post-processing steps to the specific requirements of your application and chosen material.
Common Challenges and How to Avoid Them in 3D Printing Exhaust Components
While metal 3D printing offers numerous benefits, certain challenges can arise during the fabrication of exhaust system components. Understanding these potential issues and implementing preventive measures is crucial for successful outcomes.
- Déformation et distorsion : High thermal gradients during the printing process can lead to warping or distortion, especially in large or complex parts.
- How to Avoid: Optimize part orientation, use appropriate support structures, and carefully control the printing parameters. Simulation tools can help predict and mitigate potential distortion.
- Porosité : Internal voids or pores can compromise the mechanical strength and fatigue resistance of the component.
- How to Avoid: Optimize printing parameters such as laser power, scan speed, and powder bed density. High-quality metal powders with good flowability, like those offered by Metal3DP Technology Co. LTD, are also crucial.
- Support Structure Removal Marks: Removing support structures can sometimes leave surface marks that may require additional finishing.
- How to Avoid: Design parts with self-supporting features, optimize support placement, and use appropriate support removal techniques.
- Residual Stresses: The rapid heating and cooling cycles in 3D printing can induce residual stresses, potentially leading to cracking or reduced fatigue life.
- How to Avoid: Implement appropriate heat treatment processes to relieve residual stresses.
- Material Property Variations: Inconsistent material properties throughout the printed part can occur if the printing process is not well-controlled.
- How to Avoid: Work with experienced 3D printing service providers like Met3dp who have robust process control and quality assurance procedures.
- Considérations relatives aux coûts : While cost-effective for certain applications, the initial investment in metal 3D printing and the cost of metal powders can be significant.
- How to Avoid: Carefully evaluate the total cost of ownership, considering factors like design optimization for material efficiency and reduced post-processing. For complex, low-volume parts, 3D printing often presents a cost-effective alternative to traditional methods.
By being aware of these potential challenges and partnering with a knowledgeable and experienced metal 3D printing service provider like Met3dp, you can effectively mitigate these risks and achieve high-quality, reliable exhaust system components.
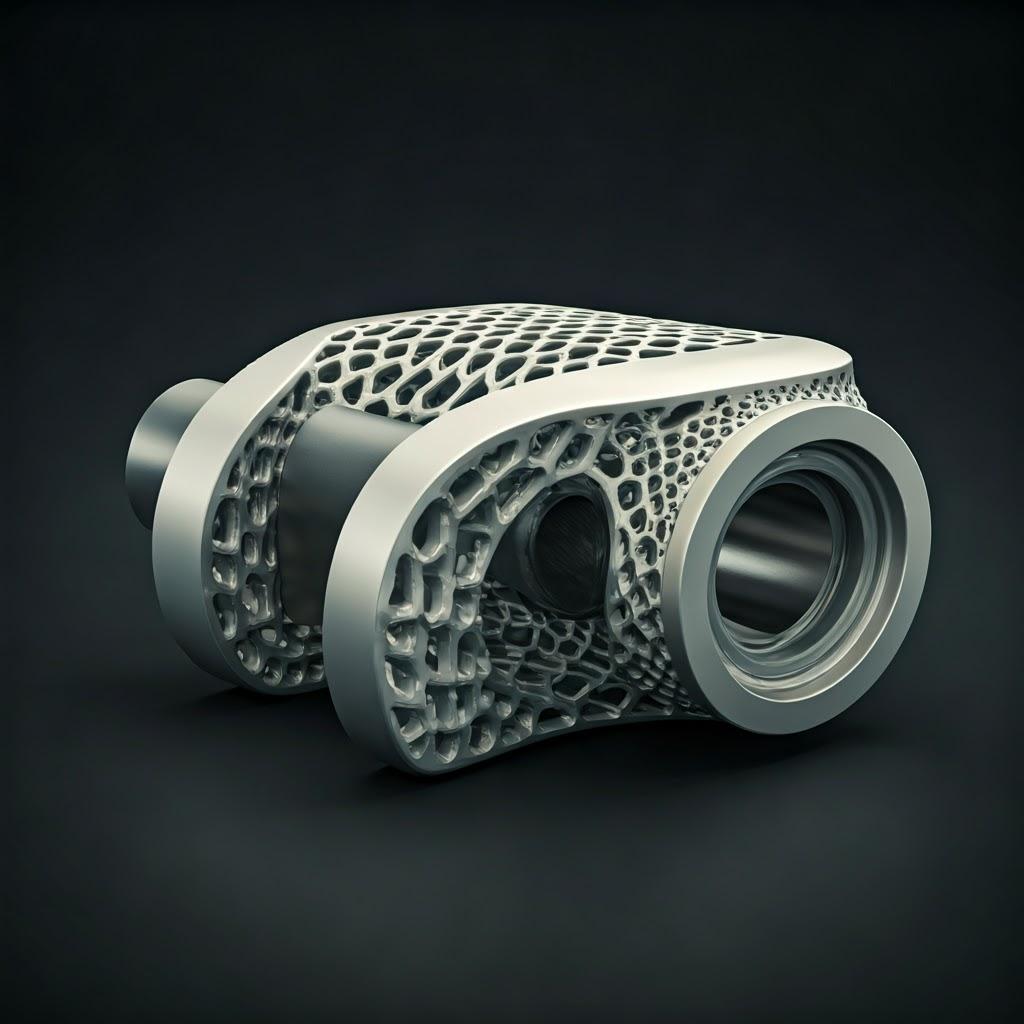
How to Choose the Right Metal 3D Printing Service Provider for Exhaust Components
Selecting the right metal 3D printing service provider is crucial for the successful fabrication of high-performance exhaust system components. Consider the following factors when making your decision:
- Capacités matérielles : Ensure the provider has experience working with high-temperature alloys like IN625 and IN718, and possesses the necessary expertise in optimizing printing parameters for these materials. Met3dp specializes in a wide range of high-quality metal powders, including those ideal for high-temperature applications.
- Technologie et équipement : Inquire about the types of metal 3D printing technologies they employ. Selective Electron Beam Melting (SEBM) and Direct Metal Laser Sintering (DMLS) are commonly used for high-performance metal parts. Evaluate their equipment capabilities in terms of build volume, accuracy, and surface finish. Met3dp’s industry-leading SEBM printers offer exceptional accuracy and reliability for mission-critical parts.
- Quality Assurance and Certifications: Verify if the provider has robust quality control procedures and relevant certifications (e.g., ISO 9001, AS9100 for aerospace). This ensures that the manufactured components meet stringent quality standards.
- Design and Engineering Support: A good service provider should offer design consultation and engineering support to optimize your parts for additive manufacturing, considering factors like topology optimization, support structure minimization, and material selection. Met3dp provides comprehensive solutions spanning advanced metal powders and application development services.
- Post-Processing Services: Determine if the provider offers the necessary post-processing services, such as heat treatment, surface finishing, and CNC machining, to meet the specific requirements of your exhaust components.
- Experience and Expertise: Look for a provider with a proven track record in manufacturing similar components for your industry. Their experience can be invaluable in avoiding potential pitfalls and ensuring a successful outcome. With decades of collective expertise in metal additive manufacturing, Met3dp has a strong history of partnering with organizations across various sectors.
- Lead Times and Production Capacity: Understand their lead times for prototyping and production, as well as their capacity to handle your required volumes.
- Cost Structure: Obtain a clear breakdown of the costs involved, including printing, materials, and post-processing. Compare quotes from different providers while considering the overall value and quality offered.
By carefully evaluating these factors, you can choose a metal 3D printing service provider that aligns with your specific needs and ensures the successful production of your high-temperature exhaust system components.
Cost Factors and Lead Time for 3D-Printed Exhaust Components
The cost and lead time for manufacturing exhaust system components using metal 3D printing are influenced by several factors:
Facteurs de coût :
- Coûts des matériaux : The cost of metal powders, especially high-performance alloys like IN625 and IN718, is a significant factor. Material prices can vary depending on the alloy, quantity, and supplier.
- Build Volume and Part Size: Larger parts that occupy more build volume and require longer print times will generally be more expensive.
- Complexity of Design: Intricate geometries and the need for extensive support structures can increase both printing time and material consumption, thus affecting the cost.
- Exigences en matière de post-traitement : The extent and complexity of post-processing steps, such as heat treatment, surface finishing, and machining, will add to the overall cost.
- Volume de production : While 3D printing can be cost-effective for low to medium volumes and customized parts, higher production volumes might benefit from economies of scale with traditional manufacturing methods in some cases.
- Service Provider’s Pricing Structure: Different service providers have varying pricing models based on machine time, material usage, and labor costs.
Délai de mise en œuvre:
- Design and Optimization: The initial design phase, including optimization for 3D printing, can take time depending on the complexity of the component.
- Temps d'impression : The duration of the printing process depends on the part size, complexity, and the chosen 3D printing technology. Larger and more intricate parts will require longer build times.
- Temps de post-traitement : Each post-processing step (support removal, heat treatment, finishing, etc.) adds to the overall lead time. The complexity of these steps will influence the duration.
- Contrôle qualité et inspection : Thorough inspection processes can also contribute to the lead time.
- Supplier’s Capacity and Scheduling: The service provider’s current workload and scheduling can impact the turnaround time.
It’s essential to discuss these factors with your chosen metal 3D printing service provider to get an accurate estimate of both the cost and lead time for your specific exhaust system components. Met3dp is committed to providing transparent and competitive pricing along with efficient lead times tailored to your project requirements.
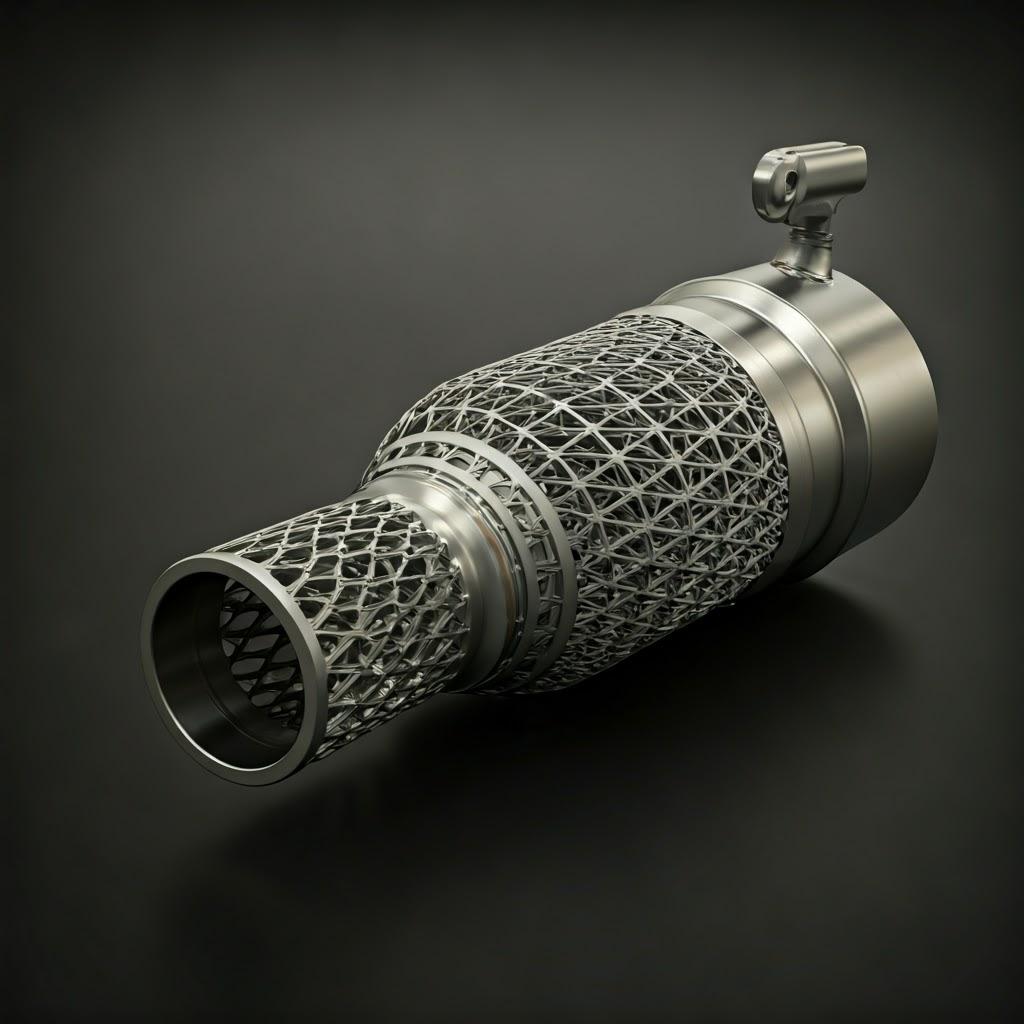
Foire aux questions (FAQ)
- Can metal 3D-printed exhaust components withstand extreme temperatures? Yes, with the selection of appropriate high-temperature alloys like IN625 and IN718, and proper post-processing including optimized heat treatment, metal 3D-printed exhaust components can effectively withstand the extreme temperatures encountered in demanding applications such as aerospace and automotive exhaust systems.
- What level of precision can be achieved with metal 3D-printed exhaust components? Metal 3D printing technologies like SEBM and DMLS can achieve tolerances down to ±0.1 mm or even tighter in some cases. Post-processing techniques like CNC machining can further enhance the dimensional accuracy of critical features. Met3dp’s advanced printing equipment ensures high precision for functional exhaust system components.
- Is metal 3D printing cost-effective for producing exhaust system components? Metal 3D printing can be highly cost-effective, especially for complex geometries, low to medium production volumes, and customized designs where traditional manufacturing methods may involve extensive tooling and machining. The material efficiency and design flexibility offered by 3D printing can also lead to overall cost savings.
Conclusion – Embracing the Future of High-Temperature Exhaust System Manufacturing with Metal 3D Printing
Metal 3D printing offers a transformative approach to the design and manufacturing of high-temperature exhaust system components across various industries. The ability to create complex geometries, optimize designs for performance, utilize advanced materials like IN625 and IN718, and achieve customized solutions provides significant advantages over traditional methods. Companies like Met3dp are at the forefront of this revolution, offering cutting-edge SEBM technology, high-quality metal powders, and comprehensive application development services to empower organizations in aerospace, automotive, medical, and industrial manufacturing. By embracing metal 3D printing, businesses can achieve enhanced performance, reduced weight, faster development cycles, and ultimately, a competitive edge in their respective fields. Contact https://met3dp.com/ today to explore how our capabilities can power your organization’s additive manufacturing goals for high-temperature exhaust system components.
Partager sur
MET3DP Technology Co. est un fournisseur de premier plan de solutions de fabrication additive dont le siège se trouve à Qingdao, en Chine. Notre société est spécialisée dans les équipements d'impression 3D et les poudres métalliques de haute performance pour les applications industrielles.
Articles connexes
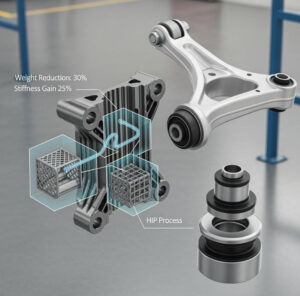
Metal 3D Printed Subframe Connection Mounts and Blocks for EV and Motorsport Chassis
Lire la suite "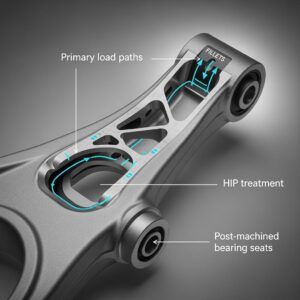
Metal 3D Printing for U.S. Automotive Lightweight Structural Brackets and Suspension Components
Lire la suite "À propos de Met3DP
Mise à jour récente
Notre produit
CONTACTEZ-NOUS
Vous avez des questions ? Envoyez-nous un message dès maintenant ! Nous répondrons à votre demande avec toute une équipe dès réception de votre message.
Obtenir les informations de Metal3DP
Brochure du produit
Obtenir les derniers produits et la liste des prix