Aerospace Fixtures with Stable Properties
Table des matières
Introduction – The Critical Role of Precision in Aerospace Alignment Fixtures
In the demanding realm of aerospace engineering and manufacturing, precision is not merely a goal; it’s a fundamental necessity. Every component, every assembly, and every process must adhere to the strictest tolerances to ensure the safety, reliability, and performance of aircraft. Among the unsung heroes in this pursuit of accuracy are alignment fixtures. These specialized tools play a crucial role in holding, positioning, and verifying the correct orientation of parts during various stages of aircraft construction and maintenance. From assembling intricate wing structures to aligning fuselage sections, the accuracy and stability of these fixtures directly impact the final quality and integrity of the aircraft.
Traditional manufacturing methods for producing these critical alignment fixtures often involve extensive machining, tooling, and assembly processes. While these methods have served the industry for decades, they can be time-consuming, costly, and may present limitations in terms of design complexity and material optimization. This is where the transformative power of metal Impression 3D, also known as metal additive manufacturing, steps in, offering a paradigm shift in how aerospace alignment fixtures are conceived, designed, and manufactured. Companies like Métal3DP are at the forefront of this revolution, providing cutting-edge solutions that address the unique challenges of the aerospace sector. Their expertise in metal 3D printing equipment and high-performance metal powders enables the creation of complex, high-precision fixtures with enhanced functionality and efficiency.
What are Aerospace Alignment Fixtures Used For? – Applications Across Aircraft Manufacturing and Maintenance
Aerospace alignment fixtures are indispensable tools throughout the lifecycle of an aircraft, from initial manufacturing to ongoing maintenance and repair. Their primary function is to ensure that components are accurately positioned and held in place during critical processes. Here are some key applications where these fixtures play a vital role:
- Assembly Operations: During the assembly of major aircraft structures like wings, fuselage sections, and control surfaces, alignment fixtures ensure that individual parts are precisely aligned before fastening. This is crucial for maintaining the overall aerodynamic profile and structural integrity of the aircraft.
- Drilling and Fastening: Fixtures are used to accurately locate and secure parts while holes are drilled for rivets, bolts, and other fasteners. Precise alignment ensures that these connections are strong and correctly positioned.
- Welding and Joining: In welding processes, fixtures hold components in the correct orientation to ensure accurate and strong joints. This is particularly important for materials used in aerospace, where weld quality is paramount.
- Inspection et contrôle qualité : Alignment fixtures are also used as reference points during dimensional inspections, ensuring that manufactured parts meet the required specifications and tolerances.
- Maintenance and Repair: When aircraft undergo maintenance or repairs, specialized fixtures are used to align damaged sections for repair work or to hold replacement parts in the correct position for installation. This can range from aligning engine components to repairing fuselage damage.
- Tooling and Mold Making: In some cases, metal 3D printing can be used to create alignment fixtures that aid in the production of composite tooling or molds used in aerospace manufacturing.
The versatility of metal 3D printing allows for the creation of highly customized alignment fixtures tailored to specific aerospace applications. This can lead to more efficient workflows, reduced errors, and improved overall quality in both manufacturing and maintenance processes. Metal3DP’s metal 3D printing services offer the capability to produce these complex geometries with the precision and material properties required by the aerospace industry.
Why Use Metal 3D Printing for Aerospace Alignment Fixtures? – Advantages Over Traditional Manufacturing
The adoption of metal 3D printing for the production of aerospace alignment fixtures offers several compelling advantages over traditional manufacturing methods:
- Design Flexibility and Complexity: Additive manufacturing allows for the creation of intricate geometries and complex internal features that would be difficult or impossible to achieve with conventional machining. This enables the design of fixtures that are highly optimized for specific tasks, potentially reducing the number of individual components required and simplifying assembly.
- Optimisation des matériaux : Metal 3D printing allows for the precise placement of material only where it is needed, leading to lighter weight fixtures without compromising strength or stiffness. This is particularly beneficial in aerospace applications where weight reduction is a critical factor. Metal3DP’s range of high-quality metal powders includes lightweight yet strong alloys suitable for aerospace fixtures.
- Réduction des délais d'exécution : Traditional manufacturing of complex fixtures often involves lengthy tooling processes and multiple machining steps, leading to extended lead times. 3D printing can significantly reduce the time from design to finished part, allowing for faster iteration and quicker deployment of fixtures.
- Cost Efficiency for Low to Medium Volumes: For small to medium production runs or for highly customized fixtures, metal 3D printing can be more cost-effective than traditional methods that require expensive tooling.
- On-Demand Manufacturing and Customization: 3D printing enables the production of fixtures on demand, eliminating the need for large inventories. It also allows for easy customization of fixtures to accommodate design changes or specific requirements.
- Integration of Features: Functional features such as cooling channels, integrated sensors, or lightweight lattice structures can be directly incorporated into the design of 3D printed fixtures, enhancing their performance and functionality.
- Réduction des déchets matériels : Additive manufacturing processes typically generate less material waste compared to subtractive methods like machining, where significant amounts of material are removed.
By leveraging the capabilities of metal 3D printing, aerospace manufacturers and maintenance providers can achieve greater efficiency, flexibility, and performance in their alignment processes. Metal3DP’s advanced metal powder making system ensures the production of high-quality powders that are essential for achieving the desired properties in 3D printed aerospace fixtures.
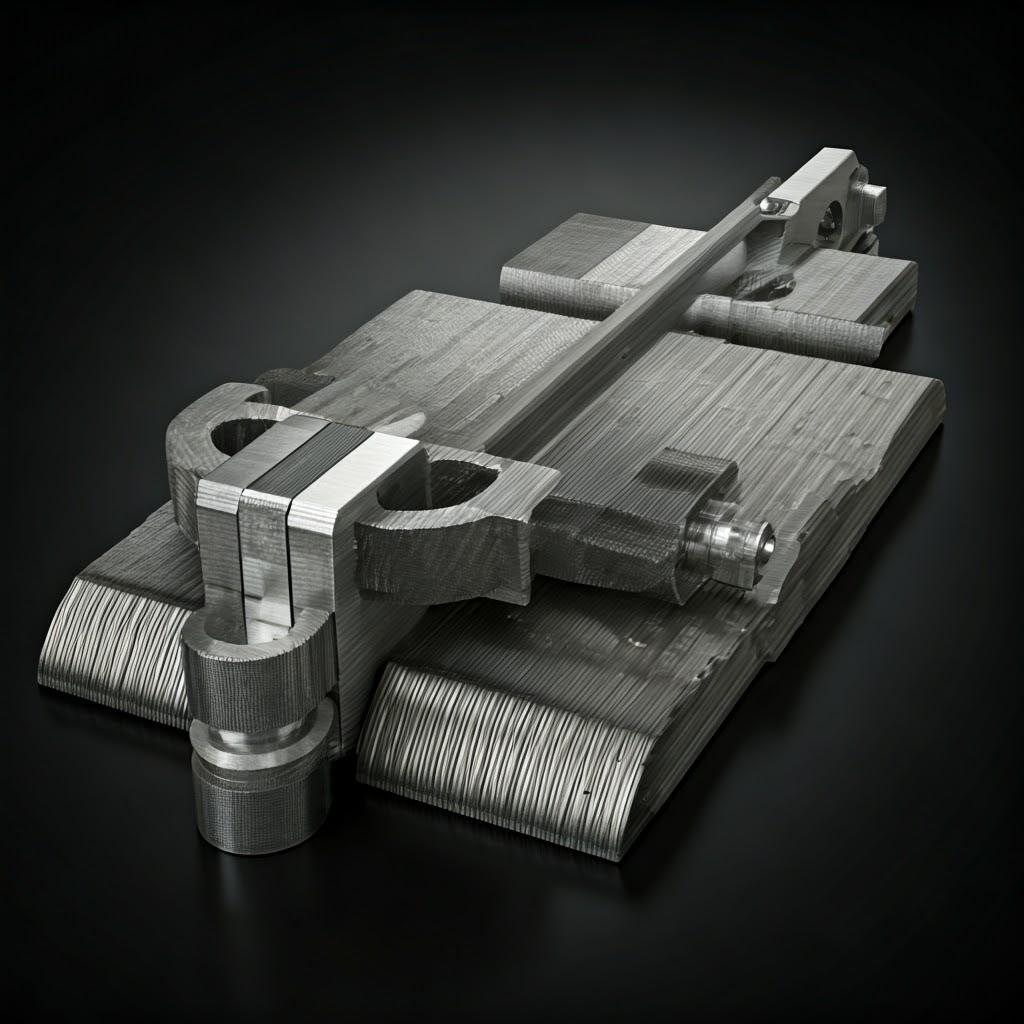
Recommended Materials and Why They Matter – Exploring FeNi36 (Invar) and 316L for Stability and Strength
The choice of material is paramount when it comes to aerospace alignment fixtures, as they must maintain their dimensional stability and structural integrity under various operating conditions. For high-precision aerospace applications, two materials stand out due to their unique properties: FeNi36 (Invar) and 316L stainless steel.
FeNi36 (Invar): Exceptional Dimensional Stability
Invar, an alloy composed primarily of iron (Fe) and nickel (Ni) with approximately 36% nickel, is renowned for its exceptionally low coefficient of thermal expansion (CTE). This means that Invar exhibits minimal changes in size over a wide range of temperatures. This property is crucial for aerospace alignment fixtures, as they may be subjected to temperature fluctuations during manufacturing, assembly, or maintenance processes. The stability of Invar ensures that the fixture maintains its precise dimensions, leading to accurate alignment of the aerospace components.
Propriété | FeNi36 (Invar) | Significance for Aerospace Fixtures |
---|---|---|
Coefficient de dilatation thermique (CTE) | Very Low (around 1.2 × 10⁻⁶ /°C) | Ensures minimal dimensional changes with temperature variations, critical for maintaining alignment accuracy. |
Résistance à la traction | ~485 MPa | Provides sufficient strength to withstand the forces encountered during alignment and assembly processes. |
Limite d'élasticité | ~275 MPa | Indicates the material’s resistance to permanent deformation under load, ensuring the fixture maintains its shape and accuracy over time. |
Résistance à la corrosion | Modéré | Offers adequate resistance to corrosion in typical aerospace environments. Surface treatments can further enhance this property. |
Densité | ~8,1 g/cm³ | A relatively dense material, providing stability and mass to the fixture. Design optimization through 3D printing can help manage overall weight. |
Applications | High-precision alignment tools, metrology instruments | Ideal for fixtures where dimensional stability is paramount, ensuring accurate positioning of critical aerospace components. |
Exporter vers les feuilles
316L Stainless Steel: Excellent Strength and Corrosion Resistance
316L is an austenitic stainless steel alloy known for its excellent corrosion resistance and high strength. The “L” designation indicates a low carbon content, which enhances its resistance to sensitization (chromium carbide precipitation at grain boundaries) during welding or high-temperature exposure, making it suitable for various aerospace applications. While its CTE is higher than Invar, its robust mechanical properties and resistance to harsh environments make it a valuable material for alignment fixtures that may require greater strength and durability.
Propriété | Acier inoxydable 316L | Significance for Aerospace Fixtures |
---|---|---|
Coefficient de dilatation thermique (CTE) | ~16 × 10⁻⁶ /°C | Higher than Invar, but still manageable for many applications, especially with careful design considerations. |
Résistance à la traction | ~550 MPa | Offers high strength, making it suitable for fixtures that need to withstand significant loads. |
Limite d'élasticité | ~290 MPa | Provides good resistance to permanent deformation, ensuring the fixture’s longevity and accuracy. |
Résistance à la corrosion | Excellent | Highly resistant to corrosion in a wide range of environments, crucial for maintaining the integrity and accuracy of the fixture over its service life. |
Densité | ~8,0 g/cm³ | Similar density to Invar, offering good stability. 3D printing can optimize designs for weight reduction without sacrificing strength. |
Applications | Structural alignment fixtures, tooling for corrosive environments | Well-suited for fixtures that require high strength and resistance to corrosion, ensuring reliable performance in demanding aerospace manufacturing and maintenance scenarios. |
Exporter vers les feuilles
Metal3DP’s expertise in metal 3D printing allows for the processing of both FeNi36 and 316L powders to create high-quality aerospace alignment fixtures tailored to specific performance requirements. Their advanced powder making system ensures the consistency and purity of these materials, which are critical for achieving the desired mechanical and thermal properties in the final printed parts.
Design Considerations for Additive Manufacturing of Aerospace Fixtures – Optimizing Geometry and Structure
Designing for metal 3D printing requires a different mindset compared to designing for traditional subtractive manufacturing methods. The layer-by-layer build process offers unique opportunities for optimizing the geometry and internal structure of aerospace alignment fixtures. Here are some key design considerations:
- Optimisation de la topologie : This computational approach can be used to identify the most efficient material distribution for a given set of loads and constraints. By removing unnecessary material, fixtures can be made lighter without sacrificing stiffness or strength. This is particularly valuable in aerospace to reduce overall weight.
- Structures en treillis : Instead of solid infill, internal lattice structures can be incorporated into the design. These intricate, repeating patterns offer a high strength-to-weight ratio and can be tailored to specific load-bearing requirements. Different lattice geometries (e.g., gyroid, cubic, diamond) offer varying mechanical properties.
- Self-Supporting Geometries: Designing parts with overhangs and angles that are self-supporting (typically above 45 degrees) can minimize the need for support structures. Support removal can be a time-consuming post-processing step and can sometimes leave surface imperfections.
- Optimisation de l'orientation : The orientation of the part on the build platform can significantly impact surface finish, support requirements, and mechanical properties. Careful consideration of the loading direction and critical surfaces is essential.
- Wall Thickness and Ribs: Minimum wall thicknesses must be considered based on the chosen material and printing technology. Adding ribs or gussets can enhance the stiffness and strength of thin-walled sections without adding excessive weight.
- Assembly Integration: Metal 3D printing allows for the consolidation of multiple parts into a single component, reducing the need for assembly and potential sources of error. Complex features like integrated clamping mechanisms or locating pins can be directly printed.
- Gestion thermique : For fixtures used in high-temperature environments, internal cooling channels can be designed into the part to dissipate heat effectively. This is a complex feature that is readily achievable with additive manufacturing.
- Caractéristiques du système de référence : Incorporating precise datum features (reference surfaces or points) into the design ensures accurate alignment with the parts being fixtured and with other tooling. These features should be strategically placed and easily accessible for measurement.
By thoughtfully considering these design principles, engineers can leverage the unique capabilities of metal 3D printing to create aerospace alignment fixtures that are lighter, stronger, more functional, and easier to use. Metal3DP’s application development services can assist in optimizing designs for additive manufacturing, ensuring the best possible performance and efficiency.
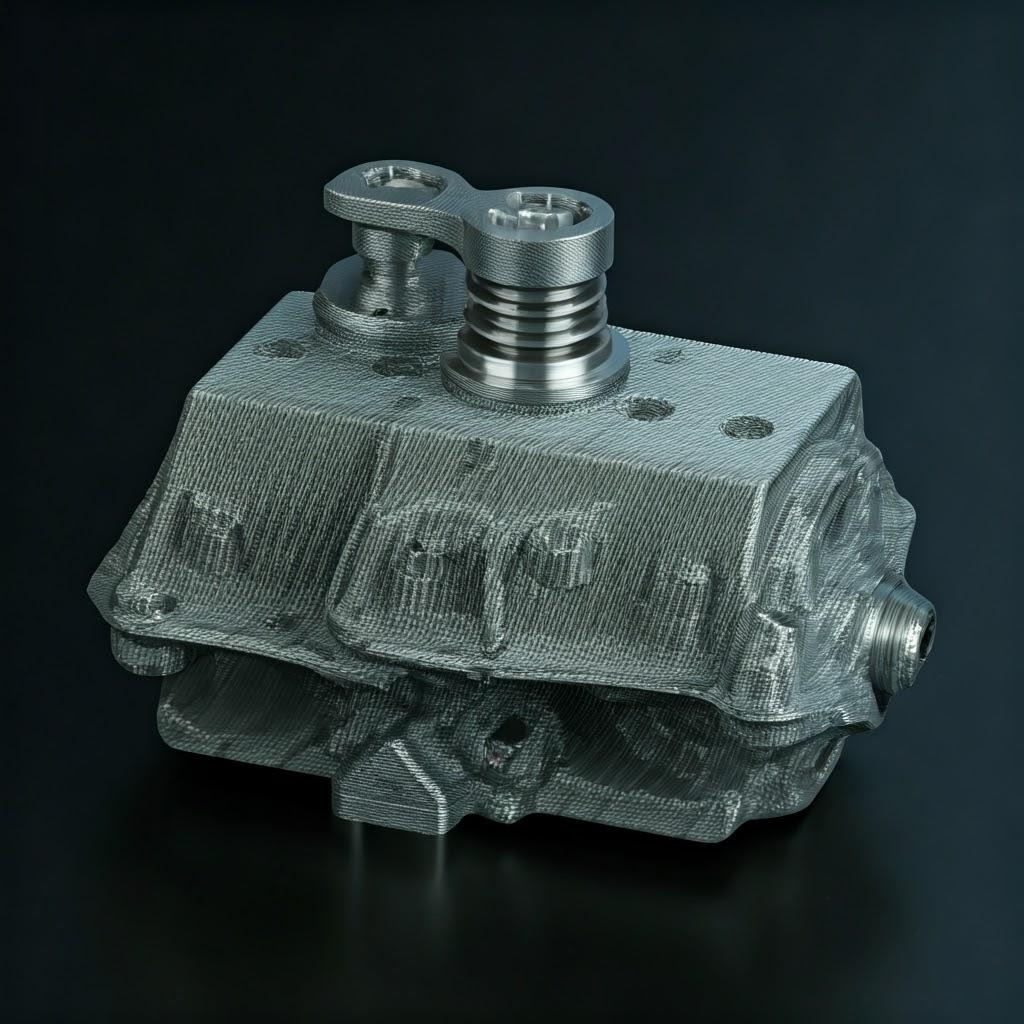
Tolerance, Surface Finish, and Dimensional Accuracy of 3D Printed Aerospace Fixtures – Meeting Stringent Industry Standards
In the aerospace industry, dimensional accuracy and surface finish are critical for the proper fit and function of components. Metal 3D printing technologies have advanced significantly, enabling the production of parts with tight tolerances and good surface finishes. However, achieving the required levels consistently requires careful process control and consideration of several factors:
- Étalonnage et maintenance des machines : Regular calibration and maintenance of the metal 3D printer are essential to ensure accuracy and repeatability. Factors such as laser alignment, powder delivery, and build platform leveling must be precisely controlled.
- Material Properties and Processing Parameters: The specific metal powder used and the printing parameters (laser power, scan speed, layer thickness, etc.) directly influence the final part’s dimensional accuracy and surface finish. Optimized parameter sets are crucial for each material.
- Build Orientation and Support Structures: As mentioned earlier, the orientation of the part during printing and the type and placement of support structures can affect surface finish, particularly on downward-facing surfaces where supports are attached.
- Shrinkage and Distortion: During the solidification process, metal parts can experience shrinkage and distortion due to thermal gradients. Understanding and compensating for these effects through design and process optimization is vital for achieving dimensional accuracy.
- Techniques de post-traitement : While the as-printed surface finish may be sufficient for some applications, others may require post-processing steps like machining, grinding, or polishing to achieve the desired smoothness and dimensional accuracy.
Typical Tolerance and Surface Finish Capabilities:
While specific values can vary depending on the 3D printing technology, material, and part geometry, here are some general guidelines for metal 3D printed aerospace fixtures:
Fonctionnalité | Typical Tolerance | Typical Surface Roughness (Ra) | Notes |
---|---|---|---|
Linear Dimensions | ± 0.1 – 0.2 mm (or ± 0.1-0.2% of dimension) | 5 – ; 20 µm | Tighter tolerances may be achievable with post-processing. |
Flatness | 0.05 – 0.1 mm per 100 mm | N/A | Depends on build orientation and support strategy. |
Circularity | 0.05 – 0.15 mm | N/A | Influenced by build orientation and support structures for internal diameters. |
Surface Finish (As-Built) | 5 – 20 µm Ra | N/A | Varies with layer thickness, powder particle size, and build orientation. |
Exporter vers les feuilles
It’s important to note that achieving tight tolerances and smooth surface finishes often involves a trade-off with build time and cost. Aerospace engineers and procurement managers should work closely with their metal 3D printing service provider, such as Métal3DP, to understand the achievable tolerances and surface finishes for their specific application and material choice. They can provide valuable insights into design optimization and post-processing options to meet stringent aerospace standards.
Post-Processing Requirements for Aerospace Alignment Fixtures – Ensuring Optimal Performance
While metal 3D printing offers near-net-shape manufacturing capabilities, aerospace alignment fixtures often require post-processing steps to achieve the desired functional properties, dimensional accuracy, and surface finish. Common post-processing requirements include:
- Suppression du support : Support structures are often necessary to prevent collapse or distortion during the printing process, especially for complex geometries with overhangs. These supports need to be carefully removed after printing, which can involve manual breaking, cutting, or machining. The design of the supports and their attachment points should minimize surface damage.
- Traitement thermique anti-stress : Metal 3D printed parts can have residual stresses due to the rapid heating and cooling cycles during the printing process. Stress relief heat treatment is often performed to reduce these internal stresses, improving dimensional stability and preventing potential cracking or warping in service.
- Pressage isostatique à chaud (HIP) : HIP is a process that applies high pressure and temperature to the printed part, reducing internal porosity and improving density and mechanical properties. This is particularly important for critical aerospace components that require high performance and reliability.
- Usinage CNC : For applications requiring very tight tolerances or specific surface finishes on critical features, CNC machining may be used as a secondary process. This can ensure precise mating surfaces, accurate hole diameters, and smooth bearing surfaces.
- Finition de la surface : Depending on the application, various surface finishing techniques may be employed, such as grinding, polishing, shot peening, or abrasive flow machining. These processes can improve surface roughness, remove surface defects, and enhance fatigue resistance.
- Chemical Treatments: Processes like passivation (for stainless steels) or anodizing (for aluminum alloys, if used) can enhance corrosion resistance and provide a protective layer.
- Inspection et contrôle qualité : After post-processing, thorough inspection using techniques like coordinate measuring machines (CMM), laser scanning, and non-destructive testing (NDT) is crucial to verify that the fixture meets the required dimensional tolerances and quality standards.
The specific post-processing requirements for an aerospace alignment fixture will depend on the material, the intended application, and the required performance characteristics. Collaborating with an experienced metal 3D printing service provider like Métal3DP is essential to determine the most appropriate post-processing steps to ensure the fixture meets the stringent demands of the aerospace industry. Their expertise in materials science and manufacturing processes can guide the selection and execution of these critical steps.
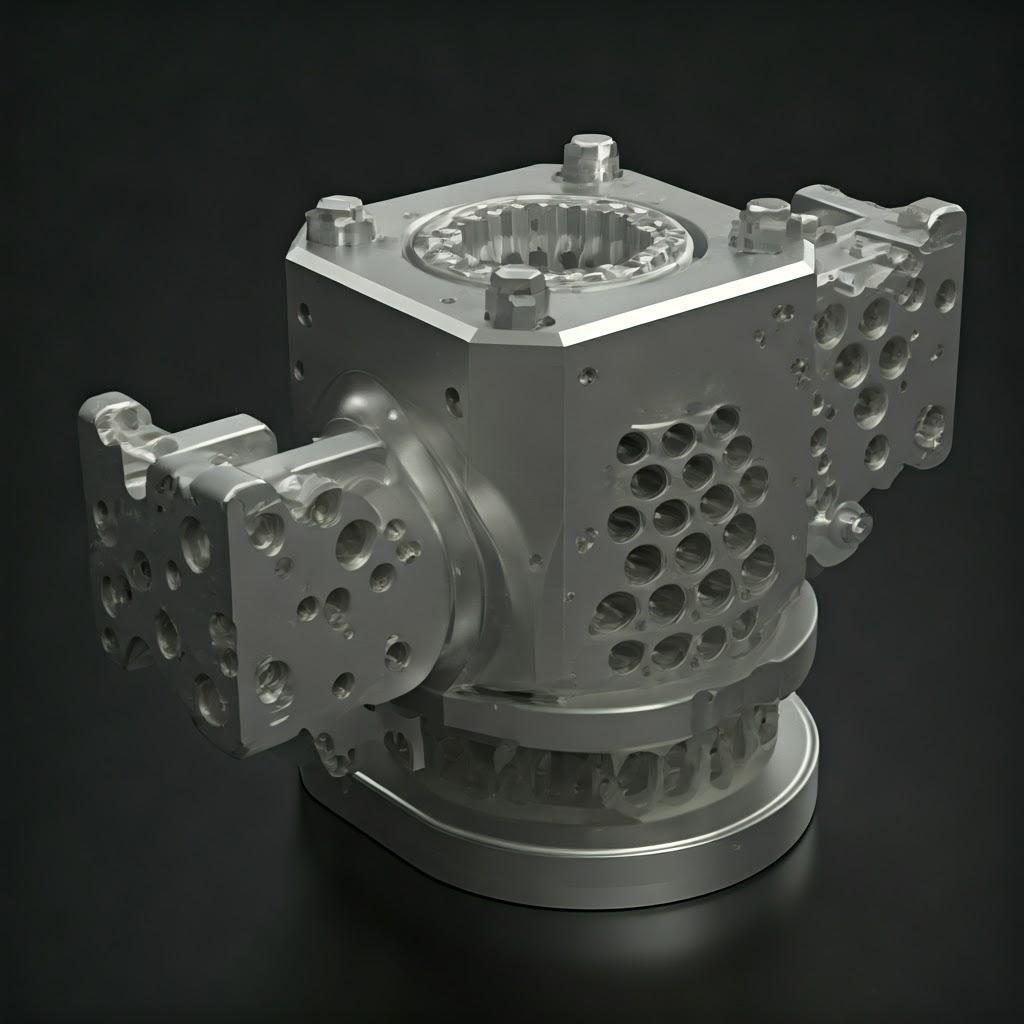
Common Challenges in 3D Printing Aerospace Fixtures and How to Avoid Them – Solutions for Warping and Distortion
While metal 3D printing offers numerous advantages, there are also potential challenges that need to be addressed to ensure the successful production of high-quality aerospace alignment fixtures:
- Déformation et distorsion : Thermal stresses during the printing process can lead to warping or distortion of the part, especially for large or complex geometries.
- Solutions : Optimize part orientation on the build platform, use support structures strategically, employ process parameters that minimize thermal gradients, and consider stress relief heat treatment after printing. Design for additive manufacturing principles, such as incorporating self-supporting angles and avoiding large flat areas.
- Support Removal Issues: Removing support structures can sometimes be challenging and may leave surface imperfections or damage the part.
- Solutions : Design parts to minimize the need for supports, use dissolvable support materials where applicable, optimize support structure design for easier removal, and employ careful post-processing techniques for support removal.
- Porosity and Density: Insufficient density or internal porosity can compromise the mechanical properties of the fixture.
- Solutions : Optimize printing parameters (laser power, scan speed, etc.), ensure high-quality metal powders with good flowability (as provided by Métal3DP), and consider post-processing techniques like Hot Isostatic Pressing (HIP) to densify the material.
- Limites de l'état de surface : The as-printed surface finish may not meet the requirements for all aerospace applications.
- Solutions : Optimize printing parameters (e.g., reduce layer thickness), orient critical surfaces optimally during printing, and employ appropriate post-processing techniques like machining, grinding, or polishing.
- Material Property Variability: Achieving consistent and predictable material properties can be a challenge if the printing process is not well-controlled or if the powder quality is inconsistent.
- Solutions : Work with reputable metal powder suppliers like Métal3DP who have stringent quality control measures, and carefully control and monitor all printing parameters. Perform thorough material testing and qualification.
- Scaling to Production Volumes: While 3D printing is excellent for prototypes and low to medium volumes, scaling to high production volumes can present challenges in terms of build time and cost-effectiveness.
- Solutions : Optimize part design for faster printing, explore multi-part builds where possible, and carefully evaluate the overall economics of 3D printing versus traditional manufacturing for larger volumes.
By understanding these potential challenges and implementing appropriate design strategies, process controls, and post-processing techniques, aerospace manufacturers can effectively leverage metal 3D printing to produce high-quality, reliable alignment fixtures. Collaborating with experienced additive manufacturing partners like Metal3DP is crucial in navigating these complexities and achieving successful outcomes.
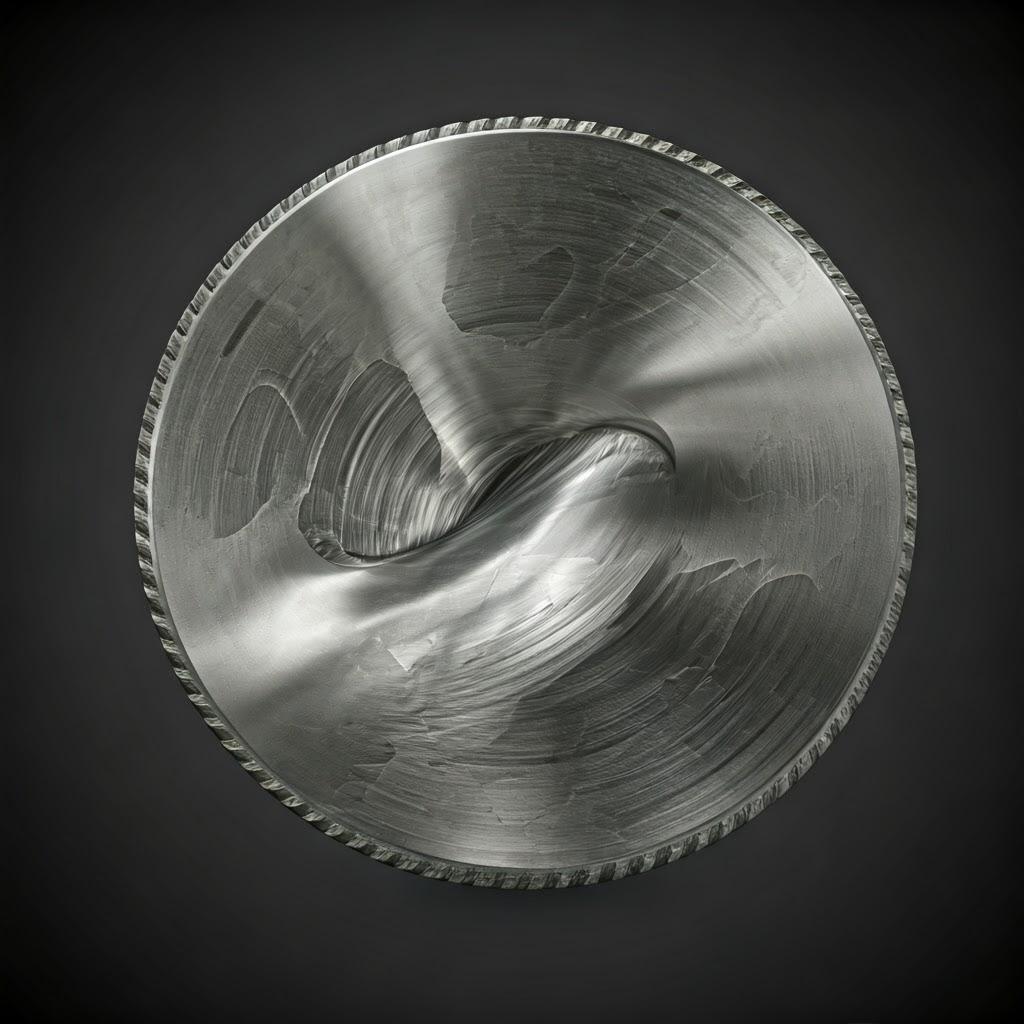
How to Choose the Right Metal 3D Printing Service Provider for Aerospace Applications – Key Evaluation Criteria
Selecting the right metal 3D printing service provider is a critical decision for aerospace companies looking to produce high-quality alignment fixtures. Given the stringent requirements of the aerospace industry, it’s essential to evaluate potential partners based on several key criteria:
- Aerospace Certifications and Standards: Ensure the provider holds relevant aerospace certifications such as AS9100 or Nadcap. These certifications demonstrate a commitment to quality management systems and process control required for aerospace components.
- Material Expertise and Range: The provider should have extensive experience working with the specific metal powders required for your application, such as FeNi36 (Invar) and 316L stainless steel. They should also have a robust understanding of the material properties and processing parameters to achieve the desired performance. Métal3DP offers a wide range of high-quality metal powders optimized for aerospace applications.
- Printing Technology and Equipment: Evaluate the types of metal 3D printing technologies the provider utilizes (e.g., Selective Laser Melting (SLM), Direct Metal Laser Sintering (DMLS), Electron Beam Melting (EBM)). Ensure they have the necessary equipment with the build volume, accuracy, and resolution capabilities to meet your specific fixture requirements.
- Design and Engineering Support: A strong service provider will offer design and engineering support to optimize your fixture designs for additive manufacturing. This includes guidance on topology optimization, lattice structures, and design for manufacturability. Metal3DP’s application development services can provide valuable expertise in this area.
- Capacités de post-traitement : Understand the provider’s in-house post-processing capabilities, including support removal, heat treatment, HIP, machining, and surface finishing. A comprehensive suite of post-processing services can streamline the production process and ensure the final part meets all specifications.
- Contrôle qualité et inspection : Inquire about the provider’s quality control procedures and inspection capabilities. They should have robust processes in place to verify dimensional accuracy, material integrity, and surface finish. This may include CMM inspection, NDT, and material testing.
- Lead Times and Production Capacity: Discuss lead times for both prototyping and production volumes. Ensure the provider has the capacity to meet your project timelines and scale as your needs evolve.
- Communication et gestion de projet : Effective communication and project management are crucial for a successful partnership. The provider should be responsive, transparent, and proactive in keeping you informed throughout the project lifecycle.
- References and Case Studies: Request references from other aerospace clients or review relevant case studies to assess the provider’s experience and track record in delivering high-quality parts for the industry.
By carefully evaluating potential metal 3D printing service providers based on these criteria, aerospace companies can identify a partner that can reliably produce the high-precision alignment fixtures required for their critical applications.
Cost Factors and Lead Time for 3D Printed Aerospace Alignment Fixtures – Understanding the Economics
The cost and lead time for metal 3D printed aerospace alignment fixtures are influenced by several factors. Understanding these elements is essential for budgeting and project planning:
Facteurs de coût :
- Coûts des matériaux : The type and quantity of metal powder used are significant cost drivers. Materials like Invar and high-performance stainless steels can be more expensive than commodity metals.
- Temps de construction : The duration of the printing process directly impacts the cost. Longer build times consume more machine time and energy. Factors influencing build time include part size, complexity, and the number of parts being printed simultaneously.
- Coûts de post-traitement : The extent of post-processing required (support removal, heat treatment, machining, finishing, inspection) will add to the overall cost. Complex post-processing can be time-consuming and require specialized equipment and expertise.
- Design and Engineering Costs: If you require design optimization or engineering support from the service provider, these services will be factored into the cost.
- Machine and Operational Costs: The service provider’s overhead, including machine maintenance, labor, and energy consumption, is part of the pricing structure.
- Quantité : While 3D printing can be cost-effective for low to medium volumes, the unit cost may decrease with larger production runs due to economies of scale.
Facteurs de délai d'exécution :
- Design Complexity and Optimization: If significant design work or optimization for 3D printing is required, this will add to the initial lead time.
- Disponibilité du matériel : The availability of the specific metal powder can impact the start of the printing process. Métal3DP maintains a stock of various high-quality powders to minimize delays.
- Temps d'impression : The actual duration of the 3D printing process depends on the part’s size, complexity, and the number of parts being built concurrently.
- Temps de post-traitement : Each post-processing step (support removal, heat treatment, machining, finishing, inspection) adds to the overall lead time. The complexity and number of these steps will influence the total turnaround time.
- Scheduling and Capacity: The service provider’s current workload and machine availability will affect the lead time. It’s crucial to discuss timelines upfront.
- Shipping and Logistics: The time required for shipping the finished fixtures to your location should also be considered in the overall lead time.
It’s important to request a detailed quotation from potential service providers like Métal3DP that breaks down these cost and lead time factors. Discussing your specific requirements and production volumes will allow them to provide an accurate estimate. Understanding these economics will enable informed decision-making and effective project management.
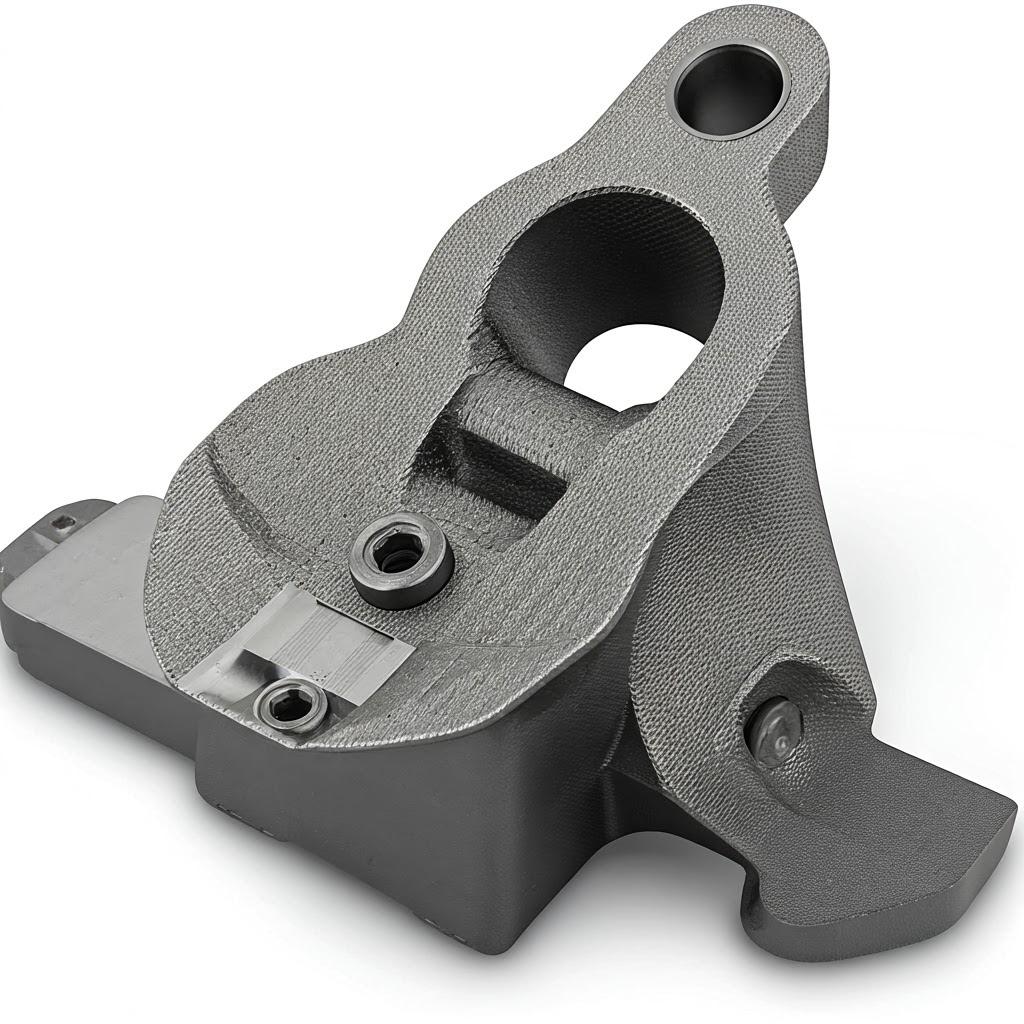
Frequently Asked Questions (FAQ) – Addressing Common Inquiries About Metal 3D Printed Fixtures
Here are some frequently asked questions about using metal 3D printing for aerospace alignment fixtures:
Q: Can metal 3D printed fixtures meet the tight tolerances required in aerospace? A: Yes, with careful design, optimized printing parameters, and appropriate post-processing (such as CNC machining), metal 3D printed fixtures can achieve the tight tolerances demanded by aerospace applications. It’s crucial to work with a provider experienced in aerospace requirements.
Q: What are the advantages of using Invar for aerospace alignment fixtures? A: Invar (FeNi36) offers an exceptionally low coefficient of thermal expansion, making it ideal for applications where dimensional stability over a wide temperature range is critical. This ensures accurate alignment even with temperature fluctuations.
Q: Is metal 3D printing cost-effective for producing aerospace alignment fixtures? A: For low to medium volumes and highly complex or customized fixtures, metal 3D printing can be more cost-effective than traditional manufacturing methods that require extensive tooling. The cost-effectiveness depends on factors like material, build time, and post-processing requirements.
Q: What kind of post-processing is typically required for metal 3D printed aerospace fixtures? A: Common post-processing steps include support removal, stress relief heat treatment, and potentially CNC machining or surface finishing to achieve the desired dimensional accuracy and surface finish. The specific requirements depend on the application.
Q: How do I ensure the quality and reliability of metal 3D printed aerospace fixtures? A: Choose a service provider with relevant aerospace certifications (e.g., AS9100), robust quality control procedures, and experience working with aerospace materials. Ensure thorough inspection and testing are performed to verify the fixtures meet the required specifications.
Q: Can metal 3D printing produce lightweight aerospace alignment fixtures? A: Yes, design optimization techniques like topology optimization and lattice structures, enabled by 3D printing, can significantly reduce the weight of fixtures without compromising their strength or stiffness. This is a major advantage in the aerospace industry.
Conclusion – Embracing Metal 3D Printing for the Future of Aerospace Fixtures
Metal 3D printing is revolutionizing the way aerospace alignment fixtures are designed and manufactured. The ability to create complex geometries, optimize material usage, reduce lead times, and achieve high levels of precision offers significant advantages over traditional methods. Materials like FeNi36 (Invar) and 316L stainless steel, processed through advanced technologies offered by companies like Métal3DP, enable the production of fixtures with exceptional dimensional stability and strength, meeting the demanding requirements of the aerospace industry.
By carefully considering design principles for additive manufacturing, understanding the achievable tolerances and surface finishes, and partnering with experienced service providers who possess the necessary expertise and certifications, aerospace companies can unlock the full potential of metal 3D printing. Embracing this innovative technology will lead to more efficient manufacturing processes, improved accuracy in assembly and maintenance operations, and ultimately contribute to the advancement of aerospace engineering. Contact Métal3DP today to explore how their comprehensive metal additive manufacturing solutions can power your organization’s aerospace goals.
Partager sur
MET3DP Technology Co. est un fournisseur de premier plan de solutions de fabrication additive dont le siège se trouve à Qingdao, en Chine. Notre société est spécialisée dans les équipements d'impression 3D et les poudres métalliques de haute performance pour les applications industrielles.
Articles connexes
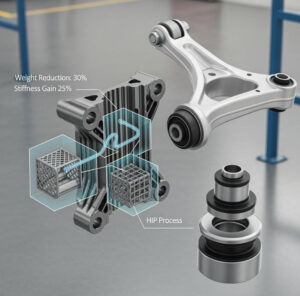
Metal 3D Printed Subframe Connection Mounts and Blocks for EV and Motorsport Chassis
Lire la suite "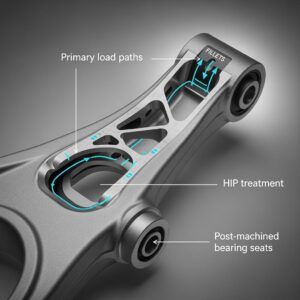
Metal 3D Printing for U.S. Automotive Lightweight Structural Brackets and Suspension Components
Lire la suite "À propos de Met3DP
Mise à jour récente
Notre produit
CONTACTEZ-NOUS
Vous avez des questions ? Envoyez-nous un message dès maintenant ! Nous répondrons à votre demande avec toute une équipe dès réception de votre message.
Obtenir les informations de Metal3DP
Brochure du produit
Obtenir les derniers produits et la liste des prix