3D Printed Heat Exchangers for Automotive and Aerospace
Table des matières
Revolutionizing Thermal Management: 3D Printed Heat Exchangers for Automotive and Aerospace
The relentless pursuit of higher performance, increased efficiency, and reduced weight in the automotive and aerospace sectors places immense demands on thermal management systems. Heat exchangers, the unsung heroes responsible for transferring thermal energy between fluids or between a solid surface and a fluid, are critical components in engines, power electronics, environmental control systems, and auxiliary power units. Traditionally, manufacturing these intricate devices involved complex processes like brazing, welding, and assembling multiple parts, often limiting design possibilities and adding weight. However, the advent of impression 3D de métaux, also known as additive manufacturing (AM), is fundamentally changing how heat exchangers are designed, produced, and optimized. By building parts layer by layer directly from metal powder, AM unlocks unprecedented design freedom, enabling the creation of highly complex, lightweight, and efficient heat exchangers that were previously impossible to manufacture. This technological shift offers significant advantages for engineers and procurement managers looking for innovative solutions to demanding thermal challenges in high-stakes industries like automotive and aerospace, paving the way for next-generation vehicle and aircraft designs. Companies specializing in advanced metal powders and printing systems, like Met3dp, are at the forefront, providing the materials and expertise needed to harness the full potential of AM for thermal management applications.
The Critical Role of Heat Exchangers in Automotive and Aerospace Systems
Heat exchangers are indispensable components, playing a vital role in maintaining optimal operating temperatures for a wide array of systems within vehicles and aircraft. Their primary function is to facilitate efficient heat transfer, either removing excess heat to prevent overheating or transferring heat to where it’s needed for optimal performance. The failure or inefficiency of a heat exchanger can lead to reduced performance, component damage, safety risks, and even catastrophic system failure. Understanding their specific roles highlights their importance:
Applications automobiles :
- Engine Cooling (Radiators): Perhaps the most familiar application, radiators dissipate heat from the engine coolant into the surrounding air, preventing the engine from overheating.
- Oil Coolers: Maintain optimal engine or transmission oil viscosity by cooling the oil, ensuring proper lubrication and component longevity.
- Charge Air Coolers (Intercoolers): Cool the compressed air coming from a turbocharger or supercharger before it enters the engine cylinders. Cooler, denser air allows for more fuel to be burned, increasing power output and efficiency.
- Exhaust Gas Recirculation (EGR) Coolers: Cool exhaust gases before they are recirculated back into the engine cylinders to reduce NOx emissions.
- HVAC Systems (Evaporators & Condensers): Facilitate the heat exchange necessary for air conditioning (cooling cabin air) and heating systems.
- Battery Thermal Management (Electric & Hybrid Vehicles): Crucial for maintaining optimal battery temperature ranges for performance, safety, and lifespan. This includes cooling batteries during fast charging or high discharge and potentially heating them in cold conditions.
- Power Electronics Cooling: Dissipate heat generated by inverters, converters, and onboard chargers, which are critical for EV/HEV operation.
Aerospace Applications:
- Engine Bleed Air Cooling (Precoolers): Cool hot air bled from engine compressor stages before it’s used for cabin pressurization, anti-icing, and other onboard systems.
- Environmental Control Systems (ECS Packs): Complex systems involving multiple heat exchangers (condensers, evaporators, reheaters) to provide conditioned air (temperature, pressure, humidity) for the cabin and cockpit.
- Fuel Cooled Oil Coolers (FCOC): Use cold fuel to cool engine or gearbox lubricating oil, simultaneously pre-heating the fuel for better combustion efficiency.
- Hydraulic Fluid Cooling: Maintain the optimal operating temperature of hydraulic systems, essential for flight controls, landing gear, and other actuators.
- Avionics and Electronics Cooling: Dissipate heat generated by sensitive electronic equipment (radar, communication systems, flight computers) often housed in confined spaces, ensuring reliability.
- Auxiliary Power Unit (APU) Cooling: Manage heat generated by the APU, which provides power on the ground and backup power in flight.
- Thermal Management for Hypersonic Flight: Extreme temperatures require highly advanced heat exchangers integrated into the vehicle structure or propulsion system.
Common Requirements Across Both Industries:
- High Thermal Efficiency: Maximum heat transfer within given volume/weight constraints.
- Low Weight: Especially critical in aerospace, but increasingly important in automotive for fuel economy and performance.
- Compact Size: Fitting complex thermal solutions into tightly packed engine bays or aircraft structures.
- Durability & Reliability: Withstanding vibration, thermal cycling, pressure variations, and potentially corrosive fluids.
- Leak-Proof Operation: Essential for containing coolants, fuels, oils, or refrigerants.
The increasing complexity and power density of modern automotive and aerospace systems continually push the boundaries of traditional heat exchanger design and manufacturing. This is precisely where metal additive manufacturing offers transformative potential.
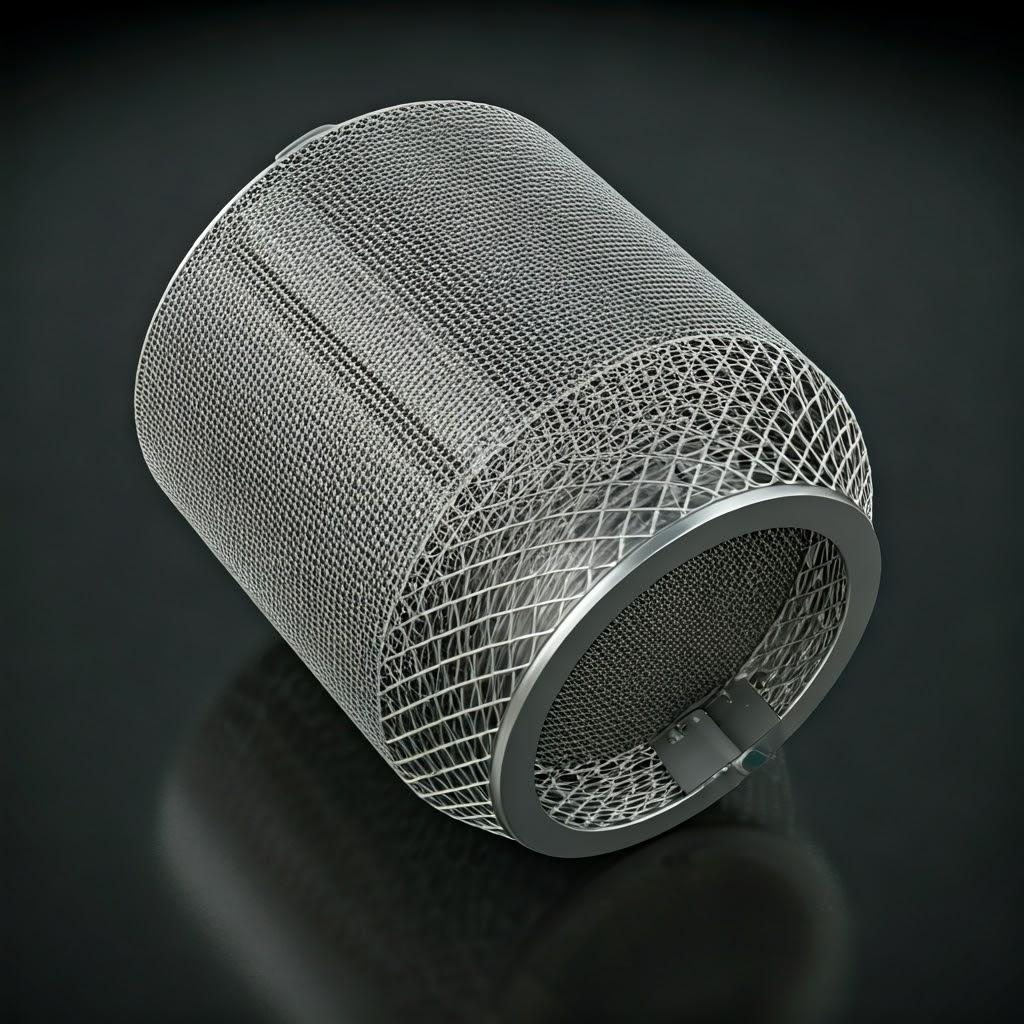
Why Choose Metal Additive Manufacturing for Heat Exchanger Production?
While traditional manufacturing methods like forming, brazing, casting, and machining have served the industry well, they inherently limit the geometric complexity and integration achievable in heat exchanger design. Metal additive manufacturing overcomes many of these limitations, offering compelling advantages for producing next-generation thermal management solutions:
- Une liberté de conception inégalée : AM allows for the creation of highly complex internal and external geometries that are impossible or prohibitively expensive to make conventionally. This includes:
- Optimized Flow Paths: Designing intricate, non-linear channels that minimize pressure drop while maximizing fluid turbulence and surface area contact for enhanced heat transfer.
- Caractéristiques intégrées : Combining multiple components (e.g., manifolds, mounting brackets, sensors ports) into a single printed part, reducing assembly steps, potential leak points, and overall weight.
- Canaux de refroidissement conformes : Channels that precisely follow the contours of the heat source for more effective cooling.
- Advanced Surface Structures: Incorporating internal features like triply periodic minimal surfaces (TPMS), lattice structures, or complex fin geometries directly into the design to dramatically increase the surface area-to-volume ratio, boosting thermal performance within a compact footprint.
- Allègement : AM enables the creation of topologically optimized structures and the use of internal lattices, significantly reducing material usage and component weight without compromising structural integrity or thermal performance. This is a paramount advantage in aerospace, where every gram saved translates to fuel efficiency or increased payload, and increasingly vital in automotive for improving fuel economy, vehicle dynamics, and EV range.
- Consolidation partielle : By printing complex assemblies as a single monolithic part, AM eliminates the need for multiple manufacturing steps (machining, brazing, welding) and associated tooling. This simplifies the supply chain, reduces assembly time and labor costs, and minimizes potential points of failure (e.g., brazed joints).
- Prototypage rapide et itération : AM allows designers to quickly produce and test functional heat exchanger prototypes. Design modifications can be implemented digitally and reprinted in days rather than weeks or months, accelerating the development cycle and enabling faster optimization.
- Variété de matériaux : AM processes can work with a growing range of high-performance metal alloys specifically suited for demanding thermal and structural requirements in automotive and aerospace, including lightweight aluminum alloys, high-conductivity copper alloys, and high-strength, temperature-resistant superalloys.
- Customization and Low-Volume Production: AM is economically viable for producing customized heat exchangers or small batch runs without the high tooling costs associated with traditional methods. This is ideal for specialized vehicles, motorsport applications, aerospace development programs, or replacement parts for legacy systems.
Comparison: Traditional vs. Additive Manufacturing for Heat Exchangers
Fonctionnalité | Traditional Manufacturing (e.g., Brazed Plate-Fin) | Metal Additive Manufacturing (e.g., LPBF) |
---|---|---|
Liberté de conception | Limited by forming, stamping, brazing constraints | High; complex channels, TPMS, integrated features |
Géométrie | Primarily linear channels, stacked plates/fins | Complex, conformal, bio-inspired geometries possible |
Poids | Often heavier due to assembly, less optimization | Potential for significant weight reduction via topology optimization, lattices |
Part Count | High (multiple plates, fins, headers, tanks) | Low (often printed as a single monolithic part) |
Assemblée | Complex brazing/welding required | Minimal or no assembly required |
Potential Leaks | Joints (brazed/welded seams) are weak points | Reduced leak paths (monolithic structure) |
Coûts d'outillage | High (dies, jigs, fixtures) | Low/None (digital manufacturing) |
Lead Time (Proto) | Weeks/Months | Days/Weeks |
Ideal Volume | High volume production | Prototypes, low-to-medium volume, customization |
Utilisation des matériaux | Potentially less efficient | Optimized material distribution |
Exporter vers les feuilles
While AM offers significant advantages, it’s important to note that traditional methods remain cost-effective for very high-volume production of simpler designs. However, for applications demanding maximum performance, minimal weight, and compact packaging – characteristics highly sought after in automotive and aerospace – metal Impression 3D presents a superior and often enabling technology.
Recommended Metal Powders for 3D Printed Heat Exchangers: AlSi10Mg, CuCrZr, IN625
The choice of material is fundamental to the performance and reliability of a 3D printed heat exchanger. The operating environment (temperature, pressure, fluid type) and performance requirements (thermal conductivity, strength, corrosion resistance) dictate the optimal metal powder. For automotive and aerospace applications, several alloys stand out, each offered with high quality and consistency by specialized powder manufacturers like Met3dp, leveraging advanced atomization techniques.
1. Aluminum Alloy (AlSi10Mg): The Lightweight Workhorse
- Propriétés principales :
- Excellent thermal conductivity (relative to its weight)
- Low density (lightweight)
- Bon rapport résistance/poids
- Bonne résistance à la corrosion
- Excellent printability via Laser Powder Bed Fusion (LPBF)
- Why it Matters for Heat Exchangers: AlSi10Mg is often the go-to choice when weight saving is a primary driver, without compromising too much on thermal performance. Its good printability allows for the creation of very complex and thin-walled structures common in advanced heat exchanger designs.
- Applications typiques : Automotive radiators, intercoolers, oil coolers, HVAC components, electronics cooling, aerospace ECS components where operating temperatures are moderate.
- Considérations : Lower melting point and strength compared to steel or superalloys, limiting its use in very high-temperature applications.
2. Copper Alloy (CuCrZr): The Thermal Conductivity Champion
- Propriétés principales :
- Excellent electrical and thermal conductivity (approaching pure copper)
- Good strength and hardness (precipitation hardenable)
- Good high-temperature strength retention (compared to pure copper)
- Bonne résistance à l'usure
- Why it Matters for Heat Exchangers: When maximum thermal performance is paramount, copper alloys are often preferred due to their superior ability to transfer heat. CuCrZr offers a good balance of high conductivity and improved mechanical properties compared to pure copper, making it suitable for demanding applications.
- Applications typiques : High-performance heat sinks, electronics cooling requiring maximum heat dissipation, induction coils, components for aerospace thermal management systems where extreme heat fluxes occur, performance automotive cooling solutions.
- Considérations : Higher density than aluminum, more challenging to print reliably via LPBF due to high reflectivity and conductivity (requires optimized process parameters), higher material cost.
3. Nickel Superalloy (IN625): The High-Temperature High-Strength Performer
- Propriétés principales :
- Excellente résistance aux températures élevées et au fluage
- Outstanding corrosion and oxidation resistance (even in harsh environments)
- Haute résistance à la fatigue
- Good printability via LPBF and Electron Beam Melting (EBM)
- Why it Matters for Heat Exchangers: IN625 is the material of choice for heat exchangers operating in extreme temperature and/or corrosive environments. Its ability to maintain structural integrity at high temperatures makes it ideal for applications close to engines or handling hot gases.
- Applications typiques : Aerospace engine components (bleed air coolers, exhaust heat exchangers), high-performance automotive exhaust system components, chemical processing heat exchangers, marine applications.
- Considérations : Lower thermal conductivity compared to aluminum and copper alloys, higher density, higher material cost.
Material Selection Guide Summary:
Matériau | Primary Advantage | Avantage clé | Typical Max Temp (°C) | Coût relatif | Densité (g/cm³) | Conductivité thermique (W/m-K) |
---|---|---|---|---|---|---|
AlSi10Mg | Léger | Good balance of properties, cost | ~150-200 | Faible | ~2.67 | ~130-150 |
CuCrZr | Conductivité thermique | Maximum heat transfer | ~400-500 | Haut | ~8.89 | ~300-320 |
IN625 | High-Temp Strength | Durability in extreme environments | ~800-1000+ | Très élevé | ~8.44 | ~10-15 |
Exporter vers les feuilles
Rôle de Met3dp : Choosing the right powder is only part of the equation. Ensuring the powder meets stringent quality standards – particle size distribution, sphericity, flowability, and chemical purity – is critical for successful printing. Met3dp utilizes industry-leading gas atomization and Plasma Rotating Electrode Process (PREP) technologies to produce high-quality metal powders, including variants of these essential alloys. Our expertise ensures that the powders used in manufacturing your heat exchangers possess the optimal characteristics for achieving dense, reliable, high-performance parts, meeting the demanding specifications of the automotive and aerospace industries.
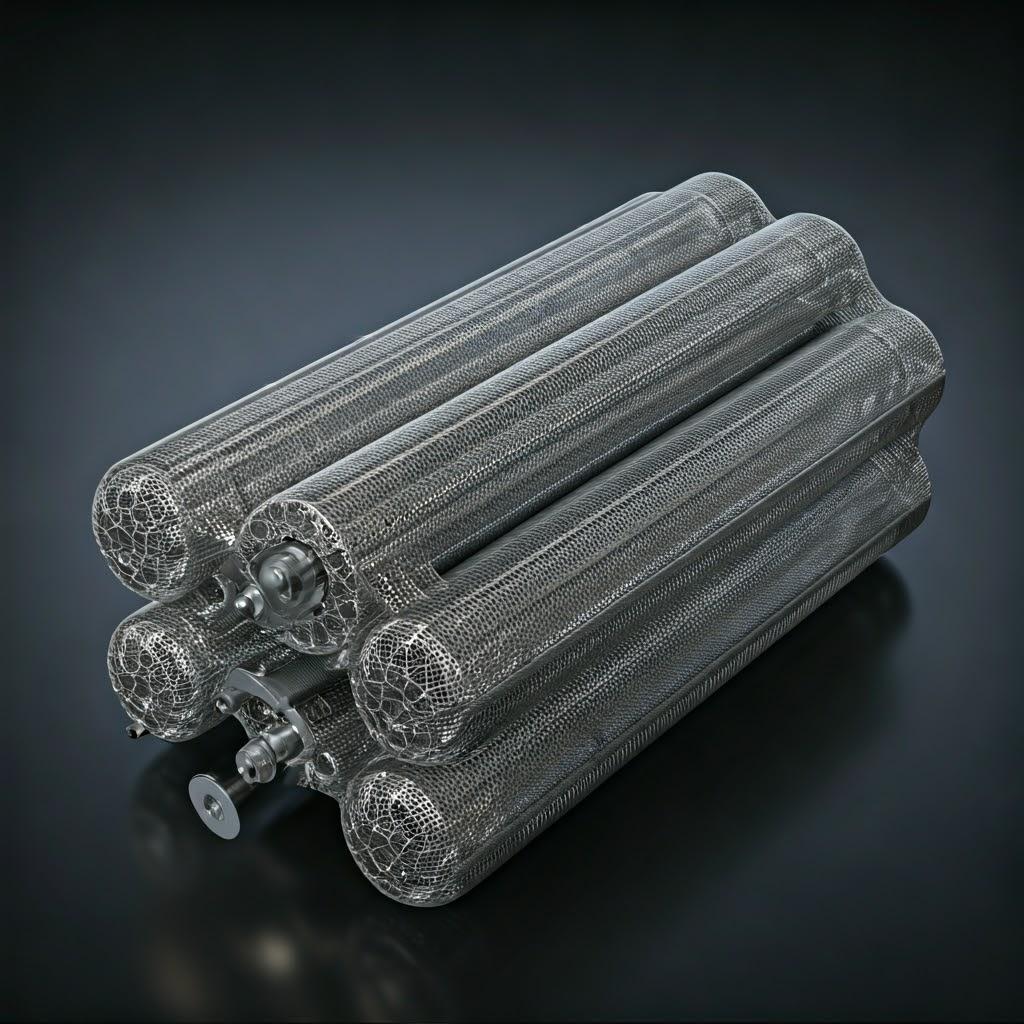
Design for Additive Manufacturing (DfAM) Principles for Optimal Heat Exchanger Performance
Simply replicating a conventionally designed heat exchanger using additive manufacturing often fails to capture the technology’s true potential and can even lead to suboptimal results or manufacturing challenges. To fully leverage the benefits of metal 3D printing – complexity, lightweighting, consolidation – engineers must embrace Design for Additive Manufacturing (DfAM) principles specifically tailored for thermal management applications. DfAM is not just about making a part printable; it’s about designing it to maximize performance and manufacturability because it’s being printed.
Key DfAM Considerations for 3D Printed Heat Exchangers:
- Leveraging Geometric Complexity for Thermal Efficiency:
- Optimized Channel Shapes: Move beyond simple circular or rectangular channels. Design curved, variable cross-section, or bio-inspired pathways (like vascular networks) to enhance fluid mixing (turbulence) and maximize heat transfer coefficients while managing pressure drop.
- Triply Periodic Minimal Surfaces (TPMS) and Lattices: Integrate TPMS structures (e.g., Gyroid, Schwarz-P) or complex lattice geometries within the heat exchanger core. These structures offer incredibly high surface area-to-volume ratios, significantly boosting thermal performance within a compact design envelope. They can also be self-supporting to a degree, reducing print challenges.
- Conception conforme : Design channels and fins that conform precisely to the shape of the component being cooled or the available space envelope, ensuring the most direct and efficient thermal path.
- Thin Walls and Feature Sizes:
- Balancing Thermal Resistance and Printability: Thinner walls reduce thermal resistance, improving heat transfer. However, AM processes have minimum printable feature sizes (dependent on machine, material, parameters). Design walls thick enough to be reliably printed and handle operating pressures, but as thin as feasible for thermal performance. Typical minimum wall thicknesses for LPBF might range from 0.3mm to 0.8mm.
- Aspect Ratios: Very tall, thin walls can be prone to distortion during printing due to thermal stresses. Consider incorporating ribbing or designing walls with appropriate aspect ratios for stability.
- Managing Supports and Overhangs:
- Angles autoportants : Design internal channels and external features with overhang angles typically greater than 45 degrees from the horizontal build plane to minimize the need for support structures. Supports within complex internal channels can be extremely difficult or impossible to remove.
- Stratégie de soutien : Where supports are unavoidable (e.g., horizontal surfaces, low-angle overhangs), design them strategically for easy removal without damaging critical surfaces. Consider accessibility for tools or post-processing steps like electrochemical machining for support removal. Sometimes, redesigning the part orientation or geometry slightly can eliminate problematic supports.
- Elimination des poudres :
- Designing for Evacuation: Ensure complex internal channels have adequate inlet/outlet ports and smooth internal transitions to facilitate the complete removal of unfused metal powder after printing. Trapped powder can impede flow, reduce thermal performance, add weight, and become loose during operation. Include drainage holes in strategic locations if necessary, which can be plugged later.
- Consolidation partielle :
- Integrating Functionality: Look for opportunities to combine manifolds, inlets, outlets, mounting features, and sensor bosses directly into the main heat exchanger body. This reduces assembly complexity, weight, and potential leak paths.
- Fluid Flow Considerations:
- Smooth Transitions: Avoid sharp corners or abrupt changes in flow path cross-section, which can create stagnant zones or high pressure drops. Use fillets and smooth transitions.
- Flow Balancing: In multi-channel designs, ensure the geometry promotes balanced flow distribution across all channels for uniform heat transfer. Computational Fluid Dynamics (CFD) simulation is invaluable here.
- Simulation-Driven Design:
- Thermal & Fluid Simulation (CFD): Use CFD early and often in the design process to simulate fluid flow and heat transfer, evaluating the performance of different geometries (channels, TPMS, fins) before printing.
- Structural Simulation (FEA): Analyze the design for mechanical stresses (due to pressure and thermal gradients) and optimize the structure for strength and durability, especially important when lightweighting.
- Build Process Simulation: Simulate the printing process itself to predict thermal stresses, potential distortion, and optimize build orientation and support strategies, minimizing print failures.
Applying these DfAM principles requires a shift in thinking and often involves close collaboration between design engineers and AM specialists. Companies like Met3dp, with deep expertise in various méthodes d'impression like Selective Electron Beam Melting (SEBM) and Laser Powder Bed Fusion (LPBF), can provide crucial guidance during the design phase, ensuring the final heat exchanger design is not only high-performing but also optimized for successful and efficient additive manufacturing.
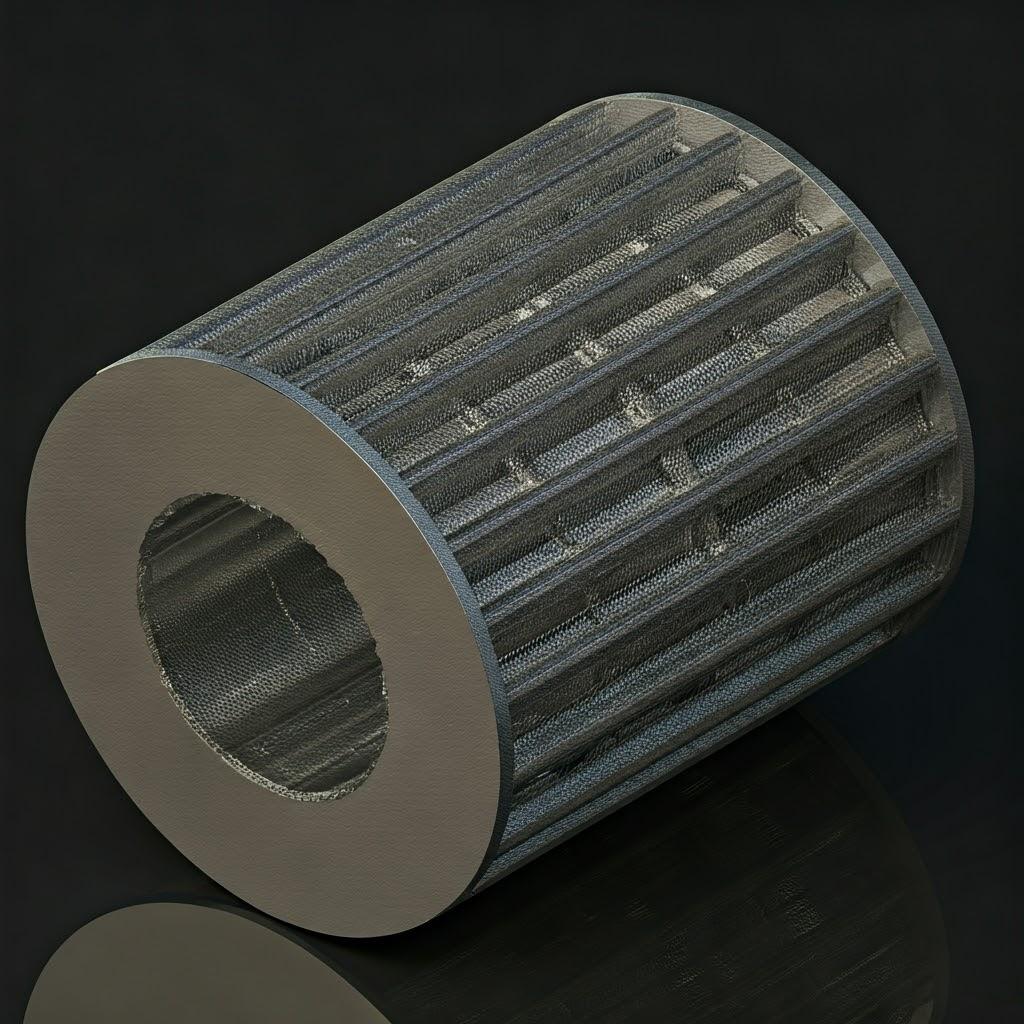
Achieving Precision: Tolerance, Surface Finish, and Dimensional Accuracy in 3D Printed Heat Exchangers
While AM enables complex geometries, understanding the achievable levels of precision is crucial for ensuring the functionality and integration of 3D printed heat exchangers, particularly for sealing surfaces, interfaces, and fluid connectors. Tolerance, surface finish, and overall dimensional accuracy are influenced by the chosen AM process, material, design complexity, build orientation, and post-processing steps.
Tolérances typiques :
- Fusion laser sur lit de poudre (LPBF) : Generally offers higher accuracy and finer feature resolution. Typical achievable tolerances for smaller parts (<100mm) can be in the range of ±0.1mm to ±0.2mm, with larger parts potentially seeing tolerances closer to ±0.1% to ±0.2% of the dimension.
- Fusion par faisceau d'électrons (EBM) : Often used for materials like titanium alloys and IN625, EBM typically operates at higher temperatures, which helps reduce residual stress but can result in slightly lower dimensional accuracy compared to LPBF. Tolerances might range from ±0.2mm to ±0.4mm or higher for large components.
- Factors Influencing Tolerance:
- Étalonnage de la machine : Regular calibration and maintenance of the AM system are critical.
- Paramètres du processus : Laser power, scan speed, layer thickness, etc., significantly impact accuracy.
- Propriétés du matériau : Different materials shrink and warp differently during heating and cooling.
- Contraintes thermiques : Uneven cooling can cause part distortion.
- Géométrie et orientation des pièces : Large flat surfaces or tall thin features can be more prone to warping. Build orientation affects support needs and thermal behavior.
- Post-traitement : Stress relief and machining steps can affect final dimensions.
Finition de la surface (rugosité) :
- As-Built Condition: Metal AM parts typically have a rougher surface finish compared to machined parts. The roughness (measured as Ra – arithmetic average roughness) depends on layer thickness, powder particle size, build angle, and process parameters.
- LPBF : Ra values often range from 6 µm to 20 µm. Vertical walls tend to be smoother than angled or horizontal surfaces (especially downward-facing ones influenced by support structures).
- EBM : Generally produces rougher surfaces than LPBF, potentially Ra 20 µm to 40 µm or higher.
- Impact on Heat Exchangers:
- Fluid Dynamics: Rough internal channel surfaces can increase turbulence (potentially enhancing heat transfer slightly) but also increase pressure drop significantly.
- Fouling: Rougher surfaces may be more prone to deposit buildup (fouling) over time, reducing thermal efficiency.
- Sealing: As-built surfaces are usually unsuitable for critical sealing; post-processing is required.
- Amélioration de l'état de surface : Post-processing steps like abrasive flow machining (AFM), electrochemical polishing, micro-machining, or standard CNC machining are used to achieve smoother finishes where required (e.g., sealing faces, critical flow paths).
Dimensional Accuracy & Metrology:
- Verification: Ensuring the final part meets dimensional specifications is crucial. This requires robust metrology techniques.
- Méthodes :
- Machines à mesurer tridimensionnelles (MMT) : Provide high-accuracy point measurements for critical features.
- 3D Laser/Structured Light Scanning: Capture the full geometry of the part, allowing comparison to the original CAD model and generating deviation maps (heat maps) to visualize inaccuracies.
- CT Scanning: Can be used, particularly for complex internal channels, to verify geometry and detect internal defects like porosity or trapped powder.
Achieving the required precision often involves designing with post-processing in mind. Critical interfaces, sealing surfaces, or bearing bores should be designed with extra material (machining allowance) to be finished via CNC machining after printing and stress relief. Partnering with an AM provider like Met3dp, equipped with high-precision printers and robust quality control processes including advanced metrology, ensures that your heat exchangers meet the stringent dimensional requirements of automotive and aerospace applications.
Essential Post-Processing Steps for Functional Metal Heat Exchangers
A metal 3D printed part, as it comes off the build plate, is rarely ready for end-use, especially for demanding applications like heat exchangers. Post-processing is a critical phase that transforms the near-net-shape printed part into a functional, reliable component meeting all performance and quality specifications.
Common Post-Processing Steps for AM Heat Exchangers:
- Soulagement du stress / Traitement thermique :
- Objet : The rapid heating and cooling cycles inherent in powder bed fusion processes create significant internal stresses within the printed part. These stresses can cause distortion, cracking, and reduced mechanical performance (especially fatigue life). Heat treatment in a controlled atmosphere furnace relieves these stresses, stabilizes the microstructure, and achieves the desired material properties (hardness, strength, ductility) specified for the alloy (e.g., precipitation hardening for CuCrZr, solution annealing/aging for IN625).
- Importance : This is arguably the most critical post-processing step for ensuring dimensional stability and long-term reliability. It’s typically performed before removing the part from the build plate to minimize distortion.
- Part Removal:
- Méthode : Cutting the part(s) off the build plate, usually using wire EDM (Electrical Discharge Machining) or a bandsaw. Care must be taken not to damage the part.
- Retrait de la structure de soutien :
- Méthode : Supports printed to anchor the part during the build must be removed. This can involve manual breaking/cutting for accessible supports or CNC machining for more integrated supports or critical surfaces. For complex internal channel supports, specialized techniques like electrochemical machining (ECM) might be considered, although designing for support-less printing is preferred.
- Défis : Can be labor-intensive and risks damaging the part surface if not done carefully. Accessing internal supports is a major challenge.
- Powder Removal / Cleaning:
- Objet : Removing all unfused metal powder, especially from intricate internal channels and complex features like TPMS structures. Trapped powder is detrimental to performance and safety.
- Méthodes : Manual brushing, compressed air blowing, ultrasonic cleaning baths, abrasive flow machining (AFM). Designing for powder removal (drainage holes, smooth channels) is crucial during the DfAM phase. Verification (e.g., weighing the part, visual inspection with borescopes, CT scanning) may be required.
- Usinage :
- Objet : Achieving tight tolerances, specific surface finishes, and critical features that cannot be accurately produced by the AM process alone.
- Applications : Creating flat sealing surfaces, machining threads for fluid connectors, finishing bearing bores, achieving precise interface dimensions for assembly. Parts are often designed with machining stock (+ allowance) on these critical features.
- Finition de la surface :
- Objet : Improving surface roughness for enhanced fluid dynamics, reduced fouling, improved fatigue life, or aesthetic requirements.
- Méthodes :
- Shot Peening/Blasting: Improves fatigue life and can provide a uniform matte finish.
- Finition par culbutage et vibration : Smooths surfaces and deburrs edges, particularly for batches of smaller parts.
- Polishing (Manual, Electrochemical, AFM): Achieves very smooth surfaces for specific applications (e.g., reducing friction, improving cleanability).
- Revêtement : Applying specialized coatings for enhanced corrosion resistance, wear resistance, or thermal barrier properties.
- Leak Testing:
- Objet : Absolutely essential for heat exchangers to ensure containment of fluids under operating pressure.
- Méthodes : Pressure testing (hydrostatic or pneumatic) while submerging the part or using leak detection fluids/gases (e.g., helium leak testing for high-sensitivity requirements). Test parameters (pressure, duration, fluid) should reflect the end-use application.
- Inspection and Quality Assurance:
- Objet : Final verification that the part meets all dimensional, material, and functional specifications.
- Méthodes : Dimensional inspection (CMM, scanning), material property testing (if required on test coupons printed alongside the part), visual inspection, NDT (Non-Destructive Testing) like CT scanning or FPI (Fluorescent Penetrant Inspection) to check for cracks or porosity if specified.
The specific sequence and combination of these steps depend heavily on the material, design complexity, and application requirements. Integrating post-processing considerations into the initial design phase (DfAM) is key to achieving a cost-effective and efficient overall manufacturing process.

Overcoming Common Challenges in Metal 3D Printing for Heat Exchangers
While metal AM offers tremendous advantages for heat exchangers, engineers and procurement managers should be aware of potential challenges inherent to the technology. Understanding these challenges and collaborating with experienced AM providers who have robust processes in place is key to successful implementation.
Key Challenges and Mitigation Strategies:
- Residual Stress and Warpage:
- Défi: The rapid, localized heating and cooling during printing induces internal stresses. These can cause the part to warp or distort during or after the build, or even lead to cracking, especially in large or complex geometries.
- Atténuation :
- Simulation : Use build process simulation to predict stress concentrations and distortion.
- Optimized Build Strategy: Careful selection of build orientation, laser scan patterns, and potentially pre-heating the build plate (common in EBM).
- Structures de soutien : Well-designed supports anchor the part and help dissipate heat.
- Soulagement du stress : Prompt and appropriate heat treatment after printing is crucial.
- Sélection des matériaux : Some alloys are more prone to cracking than others.
- Porosité :
- Défi: Small voids or pores can form within the printed material due to trapped gas, incomplete fusion, or powder inconsistencies. Porosity can reduce mechanical strength, fatigue life, and critically for heat exchangers, can create potential leak paths.
- Atténuation :
- Paramètres de processus optimisés : Developing and strictly controlling parameters (laser power, speed, layer thickness, gas flow) specific to the material and machine. Met3dp leverages extensive research to define optimal parameters for its produit range, including printers and powders.
- Poudre de haute qualité : Using powder with consistent spherical shape, particle size distribution, and low internal porosity/gas content. Met3dp’s advanced atomization techniques ensure high powder quality.
- Controlled Build Atmosphere: Maintaining a high-purity inert gas environment (Argon or Nitrogen) to minimize oxidation and gas pickup.
- Pressage isostatique à chaud (HIP) : A post-processing step involving high pressure and temperature to close internal pores (adds cost but can significantly improve density and properties).
- Support Removal Complexity:
- Défi: Removing support structures, especially from intricate internal channels or delicate features, can be time-consuming, costly, and risks damaging the part. Inaccessible internal supports may be impossible to remove completely.
- Atténuation :
- DfAM : Designing for self-supporting angles (>45°) wherever possible.
- Orientation optimisée : Choosing a build orientation that minimizes the need for critical supports.
- Accessible Support Design: Designing supports that are easier to access and remove (e.g., using specific support types, optimizing contact points).
- Techniques avancées de suppression : Considering methods like ECM or AFM for challenging internal supports, although prevention through design is better.
- Élimination des poudres dans les canaux internes :
- Défi: Ensuring all unfused powder is removed from complex, tortuous internal pathways is critical for flow and thermal performance. Partially clogged channels lead to reduced efficiency and potential contamination.
- Atténuation :
- DfAM : Designing channels with smooth transitions, sufficient diameters, and access ports/drainage holes. Avoiding dead-end pockets.
- Thorough Cleaning Procedures: Implementing rigorous cleaning protocols using compressed air, vibration, ultrasonic baths, or flow-through systems.
- Verification: Using methods like weighing, borescopic inspection, or CT scanning to confirm complete powder removal.
- Achieving Leak Tightness:
- Défi: Ensuring the final heat exchanger is completely leak-proof under operating pressures, given the potential for micro-porosity or defects in thin-walled structures.
- Atténuation :
- Contrôle de processus robuste : Minimizing porosity during printing through optimized parameters and quality powder.
- Appropriate Design: Ensuring sufficient wall thickness for pressure containment.
- Rigorous Testing: Implementing stringent leak testing protocols (e.g., pressure decay, helium leak testing) as part of the quality assurance process.
- Potential Impregnation: In some cases, sealing micro-porosity using specialized impregnation resins might be considered (though generally avoided if possible through better process control).
Successfully navigating these challenges requires deep expertise in materials science, process engineering, and quality control. Partnering with an established AM provider like Met3dp, which combines advanced equipment with rigorous process validation and quality management systems, significantly de-risks the adoption of additive manufacturing for critical components like automotive and aerospace heat exchangers.
Selecting the Ideal Metal 3D Printing Service Provider for Your Heat Exchanger Needs
Choosing the right additive manufacturing partner is as critical as the design and material selection for ensuring the success of your 3D printed heat exchanger project. Not all service providers have the same capabilities, expertise, or quality standards, especially when dealing with the demanding requirements of the automotive and aerospace industries. Procurement managers and engineers should carefully evaluate potential suppliers based on a range of technical and operational criteria.
Key Factors for Evaluating Metal AM Service Providers:
- Technical Expertise and DfAM Support:
- Does the provider have engineers experienced specifically with thermal applications and heat exchanger design?
- Can they offer valuable DfAM consultation to optimize your design for performance, manufacturability, and cost-effectiveness?
- Do they understand the nuances of fluid dynamics and heat transfer principles as applied to AM?
- Equipment and Technology:
- What specific AM technologies do they offer (e.g., LPBF, EBM)? Does the technology align with your chosen material and design requirements?
- What is the build volume capacity of their machines? Can they accommodate the size of your heat exchanger?
- What is the age, condition, and calibration frequency of their equipment? State-of-the-art, well-maintained machines generally produce more consistent and accurate parts.
- Material Capabilities and Quality:
- Do they offer the specific alloys you require (e.g., AlSi10Mg, CuCrZr, IN625)?
- Crucially, what is their process for qualifying and controlling metal powder quality? Do they source from reputable suppliers or, ideally, manufacture their own high-quality powders like Met3dp? Consistent powder characteristics (sphericity, particle size distribution, purity) are fundamental to part quality.
- Do they have experience printing with your chosen material and understand its specific processing requirements?
- Quality Management Systems and Certifications:
- Do they operate under a robust Quality Management System (QMS)? ISO 9001 certification is a baseline requirement.
- For aerospace applications, AS9100 certification (or equivalent) is often mandatory, indicating adherence to stringent aerospace quality standards.
- For automotive, IATF 16949 awareness or certification might be relevant depending on the application tier.
- What are their traceability procedures for materials and processes?
- Capacités internes de post-traitement :
- Can they perform necessary post-processing steps like stress relief/heat treatment, CNC machining, surface finishing, and leak testing in-house? Managing these processes internally often leads to better quality control and shorter lead times compared to outsourcing.
- Do they have the appropriate equipment and expertise for these critical steps?
- Inspection and Metrology:
- What metrology equipment do they possess (CMM, 3D scanners, CT scanning)?
- What are their standard inspection procedures, and can they accommodate specific NDT requirements?
- Experience and Track Record:
- Have they successfully produced parts similar to your heat exchanger in terms of complexity, material, and industry application?
- Can they provide case studies or references?
- Capacité, délai de livraison et communication :
- Do they have the capacity to meet your volume requirements and delivery timelines?
- What are their typical lead times for quoting, production, and post-processing?
- How responsive and transparent is their communication throughout the project lifecycle?
Pourquoi s'associer à Met3dp ?
Met3dp stands out as a comprehensive solutions provider, uniquely positioned to support demanding heat exchanger projects. As detailed further on our À propos de nous page, we offer:
- Integrated Expertise: Decades of collective experience spanning advanced metal powder production (using industry-leading gas atomization and PREP technologies), development of high-performance SEBM and LPBF printers, and extensive application engineering support.
- Excellence matérielle : We manufacture a wide range of high-quality spherical metal powders optimized for AM, including Aluminum, Copper, and Nickel alloys, ensuring optimal material properties for your heat exchangers.
- Advanced Equipment: Our printers deliver industry-leading print volume, accuracy, and reliability, suitable for mission-critical automotive and aerospace components.
- End-to-End Solutions: From DfAM consultation and material selection through printing, post-processing, and quality assurance, we provide a seamless path to functional parts.
- Secteur d'activité : We understand the stringent requirements of the aerospace, automotive, medical, and industrial sectors.
Choosing a partner like Met3dp, with control over both materials and machines, provides a significant advantage in ensuring the quality, reliability, and performance of your 3D printed heat exchangers.
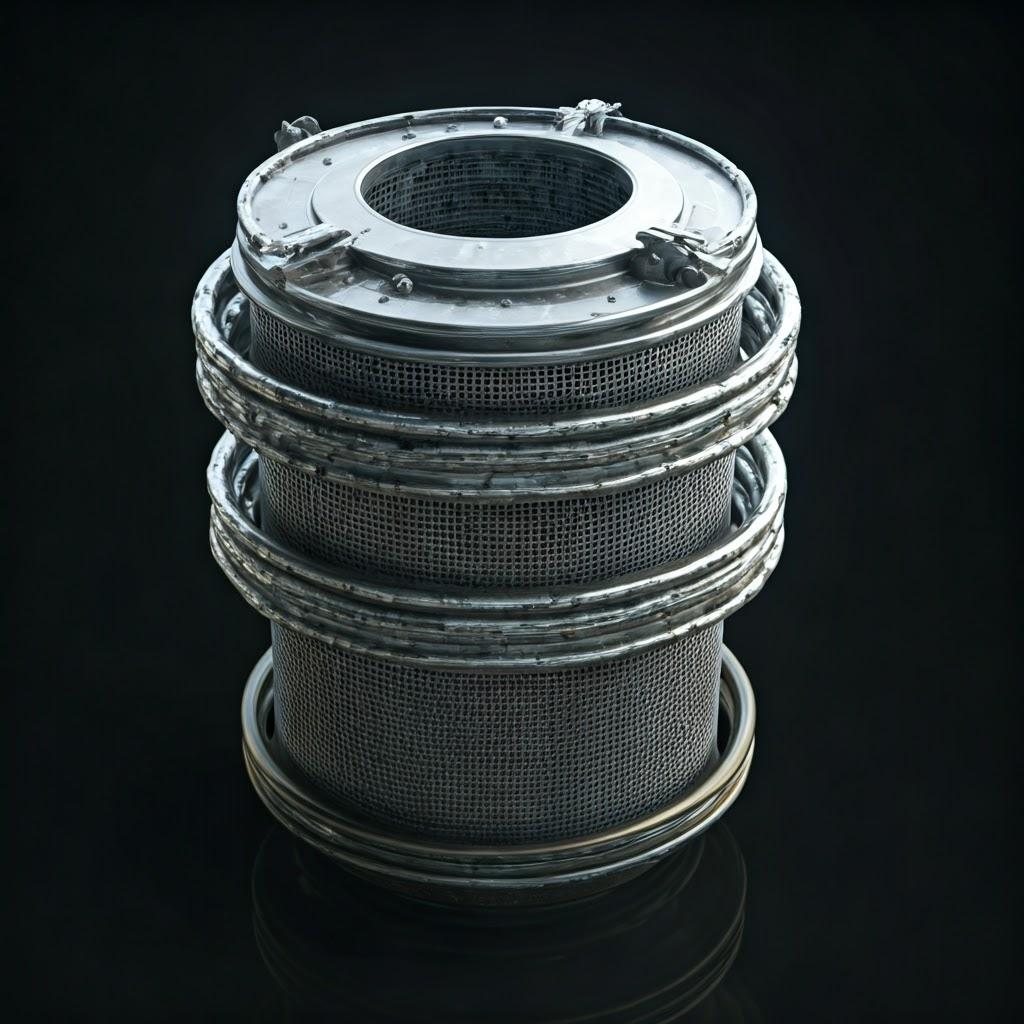
Understanding Cost Drivers and Lead Times for 3D Printed Heat Exchangers
While offering significant performance benefits, it’s important to understand the factors influencing the cost and production time for metal additive manufacturing. Unlike traditional mass production where tooling dominates initial costs, AM costs are more closely tied to material consumption and machine time per part.
Primary Cost Drivers:
- Material Type and Consumption:
- Coût de la poudre : High-performance alloys like IN625 or CuCrZr are significantly more expensive than AlSi10Mg or stainless steels.
- Part Volume & Weight: The amount of powder directly consumed to build the part is a major cost factor. Larger or denser parts cost more.
- Structures de soutien : Material used for supports also adds to the cost, reinforcing the benefit of DfAM for support minimization.
- Le temps des machines :
- Build Height: The primary driver of print time. Taller parts take longer, regardless of how many parts are nested on the build plate (within limits).
- Part Volume/Complexity: While height is dominant, the total volume scanned by the laser/electron beam also influences time. Very complex geometries with extensive scanning increase time.
- Machine Taux horaire : Varies depending on the AM technology, machine size, and provider’s overheads.
- Labor and Setup:
- File Preparation: Preparing the build file, generating supports, and slicing the model.
- Machine Setup & Teardown: Loading powder, setting up the build, and cleaning the machine afterwards.
- Post-traitement : This can be a significant cost component, involving labor for stress relief, part removal, support removal, powder evacuation, machining, finishing, and inspection. Complex internal geometries requiring extensive cleaning or manual support removal increase labor costs substantially.
- Quality Assurance and Testing:
- Standard Inspection: Dimensional checks, visual inspection.
- Advanced NDT: Requirements like CT scanning or FPI add cost.
- Leak Testing: Essential for heat exchangers, adding process time and cost.
- Certifications : Meeting specific industry certifications (e.g., AS9100) involves more rigorous process control, documentation, and testing, impacting cost.
- Volume de commande :
- Economies d'échelle : While AM avoids tooling costs, some economies of scale exist. Setting up a build and performing post-processing steps often becomes more efficient per part when producing batches rather than single prototypes. However, the cost reduction per part is generally less dramatic than in traditional mass production.
Délais d'exécution typiques :
Lead time depends heavily on part complexity, size, material, required post-processing, and the service provider’s current capacity.
- Quoting: 1-3 business days (assuming a print-ready CAD file).
- Impression :
- Small/Simple Prototypes: 2-5 days
- Medium Complexity/Size Parts: 5-10 days
- Large/Very Complex Parts or Batches: 1-3+ weeks
- Post-traitement : Highly variable.
- Basic (Stress Relief, Support Removal): 2-5 days
- Extensive (Machining, Polishing, Complex Cleaning, Testing): 1-3+ weeks
- Total Lead Time (Door-to-Door):
- Simple Prototypes: 1-2 weeks
- Production Parts (Moderate Complexity): 3-6 weeks
- Complex Parts/Batches with Extensive Post-Processing: 6+ weeks
It’s crucial to discuss specific requirements and timelines with your chosen AM provider early in the project. Providing a clear technical data package (CAD model, material specification, tolerances, testing requirements) will facilitate accurate quoting and realistic lead time estimation.
Frequently Asked Questions (FAQ) about 3D Printed Heat Exchangers
Here are answers to some common questions engineers and procurement managers have about using metal AM for heat exchangers:
- Q1: How does the thermal efficiency of 3D printed heat exchangers compare to traditional ones (e.g., brazed plate-fin)?
- A : When designed effectively using DfAM principles, 3D printed heat exchangers can significantly outperform traditional designs. AM allows for much higher surface area density (using TPMS or complex fins), optimized flow paths reducing stagnation and improving turbulence, and conformal designs for better thermal contact. This often results in higher thermal efficiency within the same volume/weight, or similar efficiency in a much more compact and lighter package. However, simply printing a traditional design may not yield significant benefits.
- Q2: Are 3D printed metal heat exchangers durable and reliable enough for demanding automotive and aerospace environments?
- A : Yes, provided the correct material is chosen, the part is designed appropriately (considering pressure, vibration, thermal cycling), printed using optimized parameters to ensure high density and low porosity, and properly post-processed (especially stress relief). Metal AM parts made from alloys like IN625, Ti6Al4V, or specialized steels can exhibit mechanical properties comparable or even superior to cast or wrought materials, making them suitable for harsh operating conditions after thorough validation and testing. Rigorous quality control and testing (like leak testing and fatigue analysis) are crucial.
- Q3: What is the typical cost difference between producing a heat exchanger via AM versus traditional methods?
- A : It depends heavily on complexity, volume, and design. For simple designs produced in very high volumes (thousands+), traditional methods like brazing are often more cost-effective due to economies of scale. However, for highly complex designs, low-to-medium production volumes, customized parts, or applications where performance, weight, and part consolidation are critical drivers, AM can be cost-competitive or even cheaper when considering the total cost of ownership (reduced assembly, improved performance, simplified supply chain). AM excels where traditional methods struggle or are impossible.
- Q4: Can you print heat exchangers in materials other than AlSi10Mg, CuCrZr, and IN625?
- A : Absolutely. While these three are common choices balancing different needs (lightweight, conductivity, high-temp strength), metal AM can utilize various other alloys suitable for heat exchangers depending on specific requirements. This includes other aluminum alloys, various grades of stainless steel (e.g., 316L for corrosion resistance), titanium alloys (Ti6Al4V for excellent strength-to-weight and corrosion resistance, often used in aerospace), and other nickel superalloys (e.g., Hastelloy X). The material portfolio is constantly expanding. Discussing your specific operating environment and requirements with an expert provider like Met3dp will help identify the optimal material choice.
Conclusion: The Future of Thermal Management is Additive
The challenges of managing heat in increasingly powerful, compact, and efficient automotive and aerospace systems demand innovative solutions. Metal additive manufacturing has decisively moved beyond prototyping to become a viable and often superior production method for critical components like heat exchangers.
By unshackling designers from the constraints of traditional manufacturing, metal 3D printing enables the creation of heat exchangers with:
- Unprecedented Geometric Complexity: Leading to enhanced thermal performance through optimized flow paths and maximized surface area (TPMS, lattices).
- Significant Lightweighting: Reducing component mass through topology optimization and material efficiency, crucial for vehicle dynamics and fuel economy.
- Consolidation partielle : Simplifying assemblies, reducing potential leak points, and streamlining supply chains.
- Accelerated Development: Enabling rapid iteration and functional testing.
Materials like the lightweight AlSi10Mg, highly conductive CuCrZr, and robust IN625 provide tailored solutions for diverse operating conditions. While challenges in design, process control, and post-processing exist, partnering with an experienced and capable AM provider mitigates these risks.
Companies like Met3dp, with integrated expertise in high-performance metal powders, advanced printing systems, and application engineering, are empowering industries to harness the full potential of AM. We provide the cutting-edge materials and technology needed to manufacture the next generation of high-performance thermal management systems.
The future of efficient, lightweight, and high-performance thermal management in automotive and aerospace lies in embracing the design freedom and manufacturing capabilities of metal additive manufacturing.
Ready to explore how 3D printed heat exchangers can revolutionize your thermal management challenges? Contact Met3dp today to discuss your application with our additive manufacturing experts and discover how our comprehensive solutions can power your innovation.
Partager sur
MET3DP Technology Co. est un fournisseur de premier plan de solutions de fabrication additive dont le siège se trouve à Qingdao, en Chine. Notre société est spécialisée dans les équipements d'impression 3D et les poudres métalliques de haute performance pour les applications industrielles.
Articles connexes
À propos de Met3DP
Mise à jour récente
Notre produit
CONTACTEZ-NOUS
Vous avez des questions ? Envoyez-nous un message dès maintenant ! Nous répondrons à votre demande avec toute une équipe dès réception de votre message.
Obtenir les informations de Metal3DP
Brochure du produit
Obtenir les derniers produits et la liste des prix
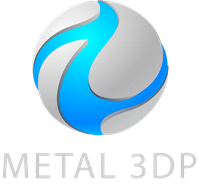
Poudres métalliques pour l'impression 3D et la fabrication additive