Corrosion-Resistant Heat Transfer Fins for Marine Systems
Table des matières
Introduction: Enhancing Marine Thermal Management with Additively Manufactured Heat Transfer Fins
The marine environment presents a unique and formidable set of challenges for engineering materials and components. Constant exposure to saltwater, fluctuating temperatures, high pressures, and demanding operational cycles necessitate robust, reliable, and efficient systems. Central to the operation of countless marine vessels and offshore structures is effective thermal management. Heat exchangers, cooling systems, and HVAC units are critical for maintaining optimal operating temperatures for engines, electronics, and personnel comfort. Within these systems, the humble heat transfer fin plays a pivotal role. Its primary function is to maximize the surface area available for heat exchange between a fluid and a solid surface, or between two fluids. The more efficient the fin, the more compact and effective the overall thermal management system can be. However, traditional manufacturing methods often limit the complexity and, consequently, the performance of these crucial components, especially when dealing with materials resilient enough for harsh marine conditions.
Enter metal additive manufacturing (AM), more commonly known as metal Impression 3D. This transformative technology is rapidly moving beyond prototyping into the realm of functional part production, offering unprecedented design freedom and material capabilities. For marine heat transfer fins, AM unlocks the potential to create highly complex geometries, such as triply periodic minimal surfaces (TPMS) or intricate lattice structures, which dramatically increase surface area-to-volume ratios far beyond what casting, machining, or extrusion can typically achieve. This geometric freedom translates directly into enhanced thermal performance, allowing for smaller, lighter, and more efficient heat exchange systems – a critical advantage in space- and weight-constrained marine applications.
Furthermore, metal AM excels in processing advanced materials specifically chosen for their suitability in corrosive saltwater environments. Alloys like Copper-Nickel (CuNi) and Copper-Chromium-Zirconium (CuCrZr) offer an exceptional blend of high thermal conductivity and outstanding resistance to biofouling and corrosion, making them ideal candidates for marine heat transfer applications. Additive manufacturing allows these high-performance alloys to be formed into optimized fin designs with near-net shapes, reducing material waste and potentially shortening lead times compared to traditional fabrication routes involving multiple complex steps. Companies specializing in advanced metal powder production and AM processes, such as Met3dp, are instrumental in providing the high-quality materials and manufacturing expertise needed to leverage these benefits. Their focus on developing and atomizing specialized powders, including copper alloys, using state-of-the-art techniques like gas atomization, ensures the feedstock quality necessary for producing dense, reliable, high-performance marine components. This convergence of advanced materials, design freedom, and precise manufacturing control positions metal AM as a key enabler for the next generation of high-performance, corrosion-resistant marine thermal management solutions. Procurement managers and design engineers in the maritime sector seeking enhanced efficiency, reduced maintenance, and improved system longevity should closely examine the potential of additively manufactured heat transfer fins.
Critical Applications: Where are Corrosion-Resistant Heat Transfer Fins Deployed in Marine Systems?
The need for efficient and corrosion-resistant heat transfer is ubiquitous across the marine industry. Heat transfer fins fabricated from durable alloys like CuNi30Mn1Fe and CuCrZr, particularly when optimized through additive manufacturing, find critical applications in a wide array of systems onboard ships, submarines, offshore platforms, and other maritime installations. Understanding these specific use cases highlights the operational demands and the value proposition of advanced materials and manufacturing techniques.
Principaux domaines d'application :
- Main Engine Cooling Systems:
- Fonction : Large marine diesel engines and gas turbines generate immense heat during operation. Efficient cooling is paramount to prevent overheating, ensure optimal combustion, maintain performance, and extend engine life.
- Fin Deployment: Heat transfer fins are core components in shell-and-tube or plate-fin heat exchangers used for jacket water cooling, lubricating oil cooling, and charge air cooling (intercoolers/aftercoolers).
- Avantage AM : 3D printed fins made from CuNi or CuCrZr offer superior corrosion resistance against seawater (used as the cooling medium in many systems) and high thermal conductivity for efficient heat dissipation. Complex AM designs can enhance turbulence and heat transfer coefficients within compact footprints.
- Auxiliary Machinery Cooling:
- Fonction : Generators, hydraulic power units, gearboxes, thrusters, and other auxiliary machinery also require effective cooling.
- Fin Deployment: Smaller heat exchangers, often using seawater or a central freshwater cooling loop, employ fins to manage thermal loads from these systems.
- Avantage AM : The ability to produce custom fin designs via AM allows for optimized thermal solutions tailored to the specific heat loads and space constraints of diverse auxiliary equipment. Corrosion resistance remains critical, especially in direct seawater cooling circuits.
- HVAC and Refrigeration Systems:
- Fonction : Maintaining climate control for personnel comfort and preserving perishable goods requires robust heating, ventilation, air conditioning (HVAC), and refrigeration systems.
- Fin Deployment: Condensers and evaporators within these systems rely heavily on fins to facilitate heat exchange between refrigerants and the cooling medium (air or water). Seawater-cooled condensers are common in marine HVAC.
- Avantage AM : AM enables the creation of highly compact and efficient condenser/evaporator coils with optimized fin patterns. CuNi alloys are particularly valued here for their resistance to both seawater corrosion and biofouling, which can significantly degrade HVAC performance over time.
- Electronics Cooling:
- Fonction : Sensitive electronic equipment, including navigation systems, communication arrays, control consoles, and power electronics, generate heat that must be effectively removed to ensure reliability and prevent failure.
- Fin Deployment: Heat sinks, often integrated into enclosures or employing liquid cooling loops with heat exchangers, utilize fins to dissipate heat into the surrounding air or a liquid coolant.
- Avantage AM : Metal AM allows for the creation of highly customized heat sinks with complex fin structures perfectly matched to the contours of electronic components or integrated into compact cooling modules. The high thermal conductivity of CuCrZr is particularly beneficial for demanding electronics cooling applications.
- Offshore Oil and Gas Platform Systems:
- Fonction : Platforms require extensive thermal management for hydrocarbon processing, power generation, utility systems, and living quarters. Seawater is the primary cooling utility.
- Fin Deployment: Large-scale heat exchangers using corrosion-resistant fins are essential for various process cooling duties, seawater lift cooling, and platform HVAC.
- Avantage AM : For specialized or critical heat exchangers, AM offers the potential for enhanced performance through complex fin designs and superior material properties (corrosion/erosion resistance) offered by alloys like CuNi30Mn1Fe, reducing maintenance downtime and improving operational safety. The ability to rapidly prototype or produce replacement parts can also be valuable in remote offshore locations.
- Naval and Submarine Applications:
- Fonction : Military vessels have stringent requirements for stealth, reliability, power density, and shock resistance. Thermal management systems are critical for propulsion, combat systems, and life support.
- Fin Deployment: Heat exchangers in submarines and surface combatants often require highly compact, efficient, and durable designs capable of withstanding harsh conditions.
- Avantage AM : AM enables the production of fins and heat exchanger components with optimized geometries for maximum performance within minimal space and weight envelopes. The specific material properties of AM CuNi and CuCrZr (strength, conductivity, corrosion resistance) meet demanding naval specifications. Topology optimization can be used to design fins that are both thermally efficient and structurally robust against shock and vibration.
Table: Application Summary and Material Relevance
Domaine d'application | Typical System | Principaux défis | Relevance of AM CuNi/CuCrZr Fins |
---|---|---|---|
Main Engine Cooling | Jacket Water, Lube Oil Coolers | High Heat Load, Seawater Corrosion | High Conductivity, Excellent Corrosion/Biofouling Resistance (CuNi) |
Auxiliary Machinery Cooling | Generator, Gearbox Coolers | Space Constraints, Corrosion | Custom Designs, High Performance Materials |
HVAC & Refrigeration | Condensers, Evaporators | Biofouling, Seawater Corrosion | Enhanced Efficiency, Anti-Fouling (CuNi), Compactness |
Electronics Cooling | Heat Sinks, Liquid Cooling Units | High Heat Flux, Reliability | High Conductivity (CuCrZr), Custom Geometries, Integration |
Offshore Platforms | Process Coolers, Utility Cooling | Large Scale, Harsh Environment | Durability, Corrosion/Erosion Resistance, Performance Longevity |
Naval/Submarine Systems | Propulsion, Combat System Cooling | Stealth, Compactness, Shock | Optimized Design, High Performance/Weight Ratio, Durability |
Exporter vers les feuilles
The widespread use of heat transfer fins across these critical marine systems underscores the need for materials and manufacturing methods that can deliver both high thermal performance and exceptional durability in corrosive environments. Metal AM, combined with advanced copper alloys like CuNi30Mn1Fe and CuCrZr, provides a powerful solution to meet these demanding requirements, offering significant advantages for designers, manufacturers, and operators of marine equipment.
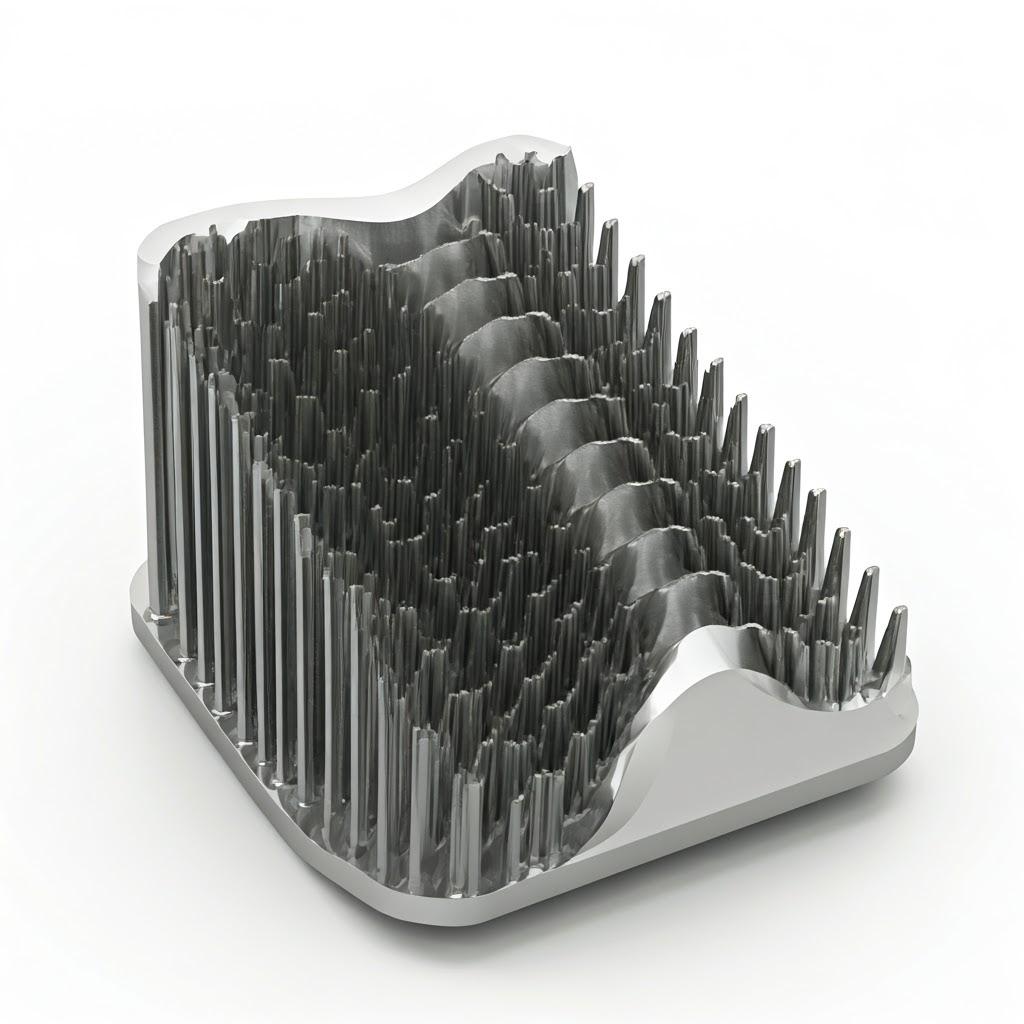
The Additive Advantage: Why Metal 3D Printing Excels for Marine Heat Transfer Fin Production
While traditional manufacturing methods like casting, extrusion, stamping, and machining have long been used to produce heat transfer fins, they often impose significant limitations, particularly when dealing with complex designs or challenging materials like high-strength copper alloys. Metal additive manufacturing fundamentally changes the paradigm, offering distinct advantages that are especially relevant for demanding marine applications. These advantages stem from the layer-by-layer fabrication process, enabling geometric complexity, material efficiency, and design possibilities previously unattainable.
Key Advantages of Metal AM for Marine Fins:
- Unparalleled Geometric Complexity:
- Challenge with Traditional Methods: Casting struggles with very thin walls or intricate internal channels. Extrusion limits designs to constant cross-sections. Machining complex surfaces from a solid block is time-consuming and generates significant waste. Assembling complex fins from multiple stamped or machined pieces introduces potential leak paths and thermal contact resistance.
- AM Solution: AM builds parts layer by layer directly from a 3D CAD model. This allows for the creation of incredibly complex and highly optimized geometries:
- Thin Walls and High Aspect Ratios: AM can produce very thin fins (sub-millimeter) with high aspect ratios (height-to-thickness), maximizing surface area within a given volume.
- Canaux internes : Complex internal cooling channels can be directly integrated into the fin structure for liquid-cooled applications.
- Lattice Structures & TPMS: Lightweight, high-surface-area structures like lattices or Triply Periodic Minimal Surfaces (TPMS) can be fabricated. These biomimetic designs significantly enhance turbulence and heat transfer coefficients while minimizing material usage and weight.
- Conformal Designs: Fins can be designed to perfectly conform to curved or irregular surfaces, improving thermal contact and overall system integration.
- Impact: This design freedom directly translates to significantly improved thermal performance (higher heat transfer rates) and allows for more compact and lightweight heat exchanger designs – crucial for marine vessels where space and weight are at a premium.
- Enhanced Heat Transfer Efficiency:
- Mechanism: The complex geometries enabled by AM (e.g., TPMS, optimized fin shapes, boundary layer disruptors) enhance fluid mixing and turbulence near the heat transfer surface. This disrupts the insulating boundary layer that typically forms, leading to higher convective heat transfer coefficients (h).
- Bénéfice : For a given temperature difference (ΔT) and surface area (A), the heat transfer rate (Q) is governed by Q=hAΔT. By significantly increasing both the effective surface area (A) through complex designs and the heat transfer coefficient (h) through enhanced turbulence, AM fins can achieve much higher heat transfer rates compared to simpler, traditionally manufactured fins of similar volume or weight. This means heat exchangers can be made smaller and lighter for the same thermal duty, or existing systems can be upgraded for higher capacity.
- Material Optimization and Alloy Suitability:
- Challenge with Traditional Methods: Some high-performance alloys, particularly certain copper alloys needed for marine corrosion resistance and thermal conductivity, can be difficult to cast or machine effectively. Casting may lead to segregation or porosity issues, while machining work-hardens the material, leading to tool wear.
- AM Solution: Powder Bed Fusion (PBF) processes like Selective Laser Melting (SLM) or Electron Beam Melting (EBM) are well-suited for processing a wide range of advanced metal powders, including CuNi30Mn1Fe and CuCrZr. The rapid melting and solidification inherent in AM can lead to fine microstructures with excellent material properties. Specialized providers like Met3dp leverage advanced powder manufacturing techniques (e.g., Gas Atomization, Plasma Rotating Electrode Process – PREP) to produce spherical, high-purity metal powders optimized for AM, ensuring the creation of dense, high-integrity parts.
- Impact: AM allows designers to select the best material for the application (like corrosion-resistant CuNi) and fabricate it into the optimal geometry, without being overly constrained by traditional manufacturing limitations.
- Prototypage rapide et itération de la conception :
- Challenge with Traditional Methods: Creating tooling (e.g., molds for casting, dies for extrusion) is expensive and time-consuming. This makes iterating on fin designs to find the optimal configuration a slow and costly process.
- AM Solution: AM is a tool-less process. Designs can be modified in CAD software and a new prototype printed relatively quickly (hours or days, depending on size and complexity).
- Impact: Engineers can rapidly test multiple fin designs, perform computational fluid dynamics (CFD) simulations, print prototypes for physical testing (thermal performance, fluid flow, corrosion resistance), and quickly iterate towards an optimized solution before committing to larger production runs. This accelerates the development cycle significantly.
- Part Consolidation and Reduced Assembly:
- Challenge with Traditional Methods: Complex heat exchanger components often require assembling multiple individual fins, plates, tubes, and headers, involving brazing, welding, or mechanical fastening. Each joint represents a potential failure point (leakage, corrosion) and adds thermal resistance.
- AM Solution: AM allows for the consolidation of multiple parts into a single, monolithic component. For instance, fins can be directly printed onto a base plate or tube sheet, eliminating assembly steps and joints.
- Impact: This reduces assembly time and cost, improves structural integrity, eliminates potential leak paths, and can enhance thermal performance by removing interfacial thermal resistance.
- Customization and On-Demand Production:
- Challenge with Traditional Methods: Producing small batches or highly customized fin designs using traditional methods is often economically unviable due to high setup and tooling costs.
- AM Solution: Since AM is tool-less, it is economically feasible to produce small batches, one-off custom designs, or replacement parts on demand without incurring massive tooling expenses.
- Impact: This enables tailored solutions for specific marine applications, retrofitting older systems with performance-enhancing components, or providing rapid replacements for obsolete or damaged parts, minimizing downtime for critical marine assets. This is particularly relevant for wholesale marine parts suppliers and maintenance providers looking for agile manufacturing solutions.
- Supply Chain Optimization and Reduced Lead Times:
- Challenge with Traditional Methods: Complex supply chains involving casting foundries, machining shops, and assembly lines can lead to long lead times for specialized components.
- AM Solution: AM can potentially shorten lead times, especially for complex or low-volume parts, by consolidating manufacturing steps and enabling localized or distributed manufacturing closer to the point of need.
- Impact: Faster access to critical components like high-performance heat transfer fins can reduce vessel downtime during maintenance or repair, improving operational readiness.
Table: Comparing AM vs. Traditional Manufacturing for Marine Fins
Fonctionnalité | Traditional Manufacturing (Casting, Extrusion, Machining) | Fabrication additive métallique (PBF) | Marine Application Benefit |
---|---|---|---|
Complexité géométrique | Limited (Simple shapes, constant cross-sections) | Very High (Lattices, TPMS, thin walls, internal channels) | Enhanced thermal performance, Compactness, Lightweighting |
Heat Transfer | Moderate Efficiency | High to Very High Efficiency | Smaller/Lighter Systems, Increased Capacity |
Utilisation des matériaux | Can be high waste (machining); constraints (casting) | Near-Net Shape, Efficient Powder Use | Reduced material cost, Sustainable manufacturing |
Alloy Processing | Can be challenging for some alloys (e.g., Cu alloys) | Well-suited for many advanced/difficult alloys | Optimal material selection (Corrosion resistance, Conductivity) |
Outillage | Required (Molds, Dies); High Cost & Time | Tool-less | Rapid prototyping, Cost-effective low-volume production |
Design Iteration | Slow, Expensive | Fast, Relatively Inexpensive | Accelerated development, Optimized designs |
Consolidation partielle | Limited; Assembly Required | High Potential; Monolithic Parts Possible | Reduced assembly cost, Improved reliability, Better thermal path |
Personnalisation | Difficult / Expensive for low volumes | Economically Viable | Tailored solutions, On-demand spares, Retrofitting |
Délai d'exécution | Can be long, dependent on tooling & supply chain | Potentially shorter for complex/low-volume parts | Reduced downtime, Improved operational readiness |
Exporter vers les feuilles
In summary, metal additive manufacturing offers a compelling suite of advantages for producing corrosion-resistant heat transfer fins for marine systems. By overcoming the limitations of traditional methods, AM enables the creation of components with superior thermal performance, optimized material properties, and enhanced reliability, paving the way for more efficient and durable marine thermal management solutions.
Material Focus: CuNi30Mn1Fe and CuCrZr Powders for Optimal Marine Performance
The selection of the right material is arguably the most critical factor in ensuring the longevity and performance of components operating in harsh marine environments. For heat transfer fins, the material must possess a challenging combination of properties: high thermal conductivity for efficient heat exchange, excellent resistance to various forms of corrosion (especially saltwater), good mechanical strength, and resistance to biofouling. Additive manufacturing processes require these materials in a specific powder form, optimized for consistent melting, solidification, and densification. Two copper alloys stand out as exceptional candidates for 3D printed marine heat transfer fins: CuNi30Mn1Fe (Copper-Nickel) et CuCrZr (Copper-Chromium-Zirconium).
Understanding Material Requirements for Marine Heat Transfer Fins:
Before delving into the specific alloys, let’s establish the key properties required:
- Conductivité thermique élevée : Essential for the primary function – transferring heat efficiently. Copper and its alloys generally excel in this regard.
- Excellente résistance à la corrosion : Must withstand continuous exposure to saline water, potentially polluted harbor water, and resist galvanic corrosion when in contact with other metals.
- Résistance aux salissures biologiques : Marine organisms (algae, barnacles) readily colonize surfaces, impeding heat transfer and fluid flow. Some copper alloys exhibit natural resistance.
- Good Mechanical Strength: Fins must withstand fluid pressure, vibration, and potential impacts during operation and maintenance.
- Weldability/Brazability (if applicable): While AM allows part consolidation, integration with existing systems might still require joining.
- Manufacturability (AM Powder Suitability): The alloy must be processable via AM technologies like SLM or EBM, requiring high-quality, spherical powder with good flowability and consistent characteristics.
1. CuNi30Mn1Fe (C71500 / CN107): The Marine Workhorse
- Composition : Primarily Copper (approx. 70%) and Nickel (approx. 30%), with small but important additions of Iron (Fe) and Manganese (Mn).
- Key Properties & Marine Relevance:
- Exceptional Seawater Corrosion Resistance: This is the defining characteristic of CuNi alloys. The 70/30 composition (like CuNi30Mn1Fe) offers superior resistance compared to 90/10 CuNi, especially in high-velocity seawater conditions. It forms a stable, adherent protective oxide film that resists chloride attack, erosion-corrosion, and crevice corrosion.
- Excellent Biofouling Resistance: Copper ions that slowly leach from the surface are toxic to many marine organisms, significantly reducing the attachment of algae, mussels, and barnacles. This maintains thermal efficiency and reduces cleaning requirements for heat exchangers.
- Good Strength and Ductility: Offers sufficient mechanical strength for fin structures while retaining good ductility, making it resilient to vibration and thermal cycling.
- Moderate Thermal Conductivity: While lower than pure copper or CuCrZr, its thermal conductivity (around 29 W/m·K at room temperature) is still significantly better than stainless steels or titanium alloys often considered for corrosion resistance, making it a good compromise for heat transfer applications where corrosion is the primary concern.
- AM Processability: CuNi alloys can be successfully processed using Laser Powder Bed Fusion (L-PBF / SLM). Achieving high density requires careful parameter optimization due to copper’s high reflectivity and thermal conductivity, but specialized AM providers have developed robust parameters. High-quality, gas-atomized CuNi30Mn1Fe powder with controlled particle size distribution and sphericity is crucial.
- Ideal Applications: Seawater coolers (main engine, auxiliary), condensers in marine HVAC/refrigeration, piping systems, desalination components – anywhere direct contact with seawater necessitates maximum corrosion and biofouling resistance.
2. CuCrZr (C18150): High Conductivity and Strength
- Composition : Primarily Copper, with small additions of Chromium (Cr) and Zirconium (Zr). It’s a precipitation-strengthened alloy.
- Key Properties & Marine Relevance:
- Very High Thermal Conductivity: Approaches that of pure copper (around 300-320 W/m·K after proper heat treatment), making it extremely efficient for heat transfer. This is significantly higher than CuNi alloys.
- Résistance et dureté élevées : Through precipitation hardening (achieved via solution annealing and aging heat treatments post-printing), CuCrZr develops mechanical strength considerably higher than pure copper or CuNi alloys, especially at elevated temperatures. This allows for thinner, more delicate fin designs or applications requiring greater structural integrity.
- Bonne résistance à la corrosion : While not as inherently resistant to saltwater corrosion and biofouling as CuNi alloys, CuCrZr still offers good general corrosion resistance, superior to many steels. Its performance can be adequate in less aggressive marine environments or closed-loop cooling systems using treated water. Protective coatings can be considered if extreme saltwater exposure is expected.
- Excellent AM Processability: CuCrZr is generally considered easier to process via L-PBF than pure copper due to the alloy additions slightly reducing reflectivity and conductivity in the molten state. It responds well to standard heat treatment procedures after printing to achieve desired strength and conductivity levels. High-quality powder feedstock is again essential.
- Ideal Applications: High-performance heat sinks for electronics cooling, components where maximum thermal efficiency is paramount (e.g., compact heat exchangers with high heat flux), structural components requiring good thermal conductivity, resistance welding electrodes (a common traditional application showcasing its strength/conductivity blend). In marine systems, it’s best suited for applications where the extreme corrosion/biofouling resistance of CuNi is not the absolute top priority, but maximum heat transfer and strength are needed, potentially in closed-loop or freshwater circuits, or specialized electronics cooling modules.
Table: Comparison of Recommended Copper Alloys for AM Marine Fins
Propriété | CuNi30Mn1Fe (C71500 / CN107) | CuCrZr (C18150) | Importance for Marine Fins |
---|---|---|---|
Primary Elements | Cu (~70%), Ni (~30%), Fe, Mn | Cu (~99%), Cr (~0.5-1.2%), Zr (~0.03-0.3%) | Dictates core properties |
Conductivité thermique | Moderate (~29 W/m·K) | Very High (~300-320 W/m·K post-HT) | Critical for heat transfer efficiency |
Seawater Corrosion | Excellent | Good (Less than CuNi) | Essential for longevity in marine environments |
Résistance à l'encrassement | Excellent | Moderate/Poor | Maintains thermal performance, reduces cleaning needs |
Résistance mécanique | Bon | Very Good (Post-Heat Treatment) | Structural integrity, resistance to pressure/vibration |
Elevated Temp. Strength | Modéré | Bon | Relevant for high-temperature engine/exhaust cooling |
AM Processability (L-PBF) | Feasible (Requires Optimization) | Bon | Enables complex fin geometries |
Post-Processing (Heat Treat) | Generally not required for properties | Required (Solution Anneal + Age) | Develops optimal strength and conductivity in CuCrZr |
Typical Marine Use Case | Seawater Heat Exchangers, Condensers | High-Efficiency Coolers, Electronics | Matching material to the specific operational demands |
Exporter vers les feuilles
The Role of Powder Quality:
Regardless of the chosen alloy, the success of manufacturing marine heat transfer fins via AM heavily relies on the quality of the metal powder feedstock. Key powder characteristics include:
- Sphéricité : Smooth, spherical particles flow easily and pack densely in the powder bed, leading to more uniform layers and higher final part density.
- Distribution de la taille des particules (PSD) : A controlled PSD ensures good flowability and resolution, enabling the creation of fine features common in fin designs.
- Purity/Low Impurities: Low oxygen and other contaminants are crucial for achieving desired material properties and preventing defects like porosity.
- Batch Consistency: Reliable powder suppliers ensure minimal variation between powder batches, leading to consistent printing results.
Des entreprises comme Met3dp, specializing in metal powder production using advanced methods like Vacuum Induction Melting Gas Atomization (VIGA) et le Procédé d'électrodes rotatives à plasma (PREP), play a critical role. These processes are designed to produce powders with high sphericity, low satellite content, controlled PSD, and high purity, tailored specifically for demanding AM applications. Procuring high-quality CuNi30Mn1Fe or CuCrZr powders from reputable suppliers is a prerequisite for successfully manufacturing reliable, high-performance 3D printed marine heat transfer fins. Engineers and procurement managers should verify a supplier’s powder production capabilities and quality control measures when sourcing materials for critical marine components.
In conclusion, both CuNi30Mn1Fe and CuCrZr offer compelling properties for additively manufactured marine heat transfer fins, but they cater to slightly different priorities. CuNi30Mn1Fe is the undisputed champion for direct seawater contact requiring maximum corrosion and biofouling resistance, while CuCrZr shines where the absolute highest thermal conductivity and mechanical strength are needed, often in less corrosive environments or where protective measures can be employed. The ability of metal AM to process both alloys into complex, optimized geometries unlocks new possibilities for enhancing marine thermal management systems.
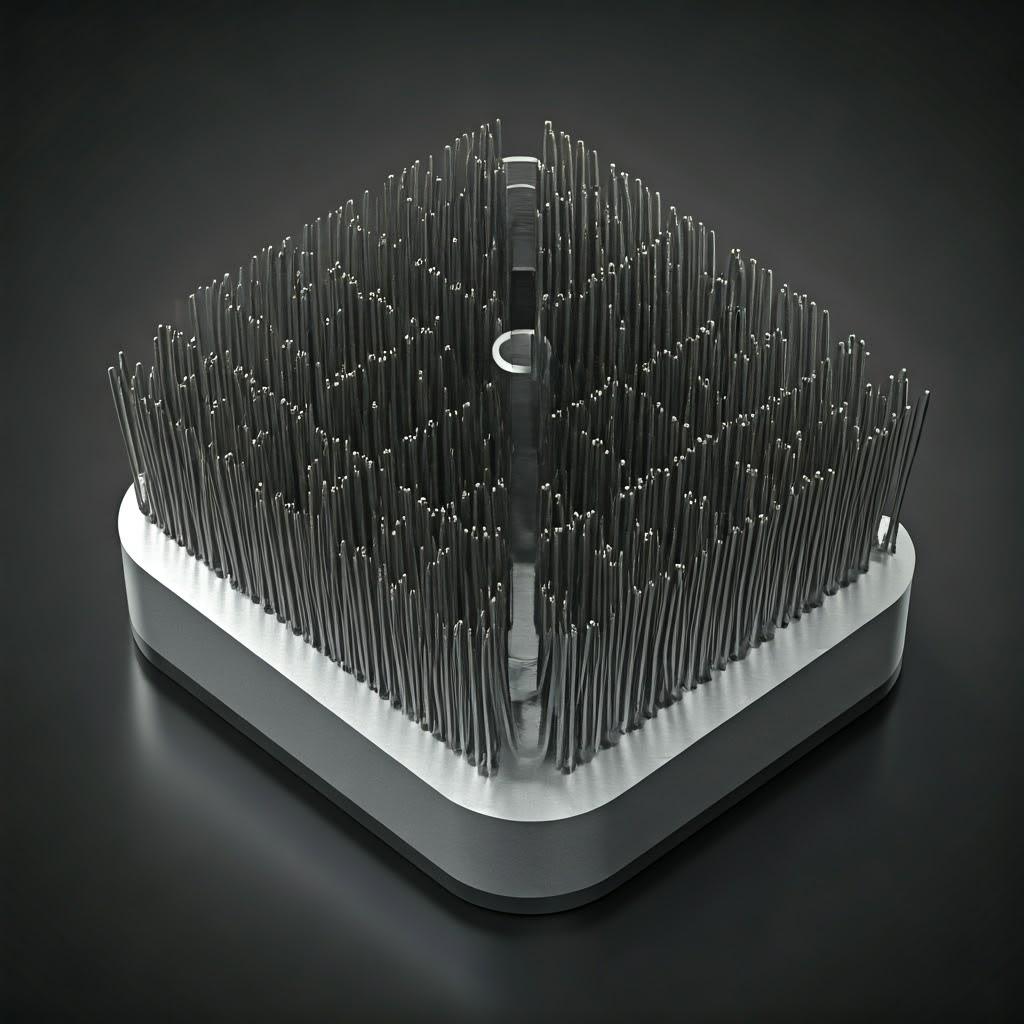
Design for Additive Manufacturability (DfAM): Optimizing Fin Geometry for Performance and Printability
The true power of using metal additive manufacturing for marine heat transfer fins lies in the ability to break free from the constraints of traditional manufacturing and create truly optimized geometries. However, this design freedom is not absolute; it must be guided by the principles of Design for Additive Manufacturability (DfAM). DfAM involves designing parts specifically to leverage the strengths and accommodate the limitations of the chosen AM process, in this case, likely Laser Powder Bed Fusion (L-PBF or SLM) for CuNi and CuCrZr alloys. Applying DfAM principles is crucial not only for ensuring the part can be successfully printed but also for maximizing its performance, minimizing post-processing efforts, and controlling costs. For engineers and designers developing marine components, mastering DfAM is key to unlocking the full potential of 3D printed heat transfer fins.
Key DfAM Considerations for Marine Heat Transfer Fins:
- Leveraging Geometric Complexity for Thermal Performance:
- Thin Walls and High Aspect Ratios: L-PBF can create very thin walls (down to approx. 0.3-0.5 mm, depending on material and machine). Design fins with minimal thickness necessary for structural integrity to maximize surface area per unit volume. High aspect ratios (height/thickness) increase the heat transfer area significantly. DfAM Tip: Ensure wall thickness is consistent and above the minimum printable size for the chosen machine and material combination. Consult with your AM service provider, like Met3dp, on achievable minimum feature sizes with their equipment.
- Lattice Structures and TPMS: Instead of solid fins, consider replacing the volume with intricate lattice structures or Triply Periodic Minimal Surfaces (e.g., Gyroid, Schwarz P). These mathematically defined structures offer extremely high surface area-to-volume ratios and inherently promote fluid mixing and turbulence, dramatically boosting heat transfer coefficients. They are virtually impossible to create with traditional methods but are a key strength of AM. DfAM Tip: Select lattice/TPMS unit cell types and densities based on desired thermal performance, pressure drop constraints, and structural requirements. Utilize CFD simulation tools to optimize these complex geometries before printing.
- Optimized Fin Profiles: Move beyond simple rectangular or trapezoidal fin profiles. AM allows for curved, variable-thickness, or aerodynamically shaped profiles designed to manipulate fluid flow, minimize pressure drop, or enhance heat transfer in specific regions. DfAM Tip: Use topology optimization software to identify where material is most needed for heat transfer and structural support, leading to organic, highly efficient designs.
- Support Structure Strategy:
- Understanding Supports: In PBF processes, downward-facing surfaces and overhangs beyond a certain angle (typically <45° from the horizontal) require support structures. These structures anchor the part to the build plate, prevent warping, and conduct heat away from the melt pool during printing. For copper alloys with high thermal conductivity, effective heat dissipation via supports is critical.
- Minimizing Supports: Support structures consume extra material, add print time, and require removal during post-processing (which can be difficult and time-consuming, especially for internal features). Design parts to be self-supporting whenever possible. DfAM Tips:
- Orientation: Carefully select the build orientation. Orienting the part to minimize the area of steep overhangs is often the first step. For fins, printing them vertically might seem intuitive but could require extensive supports along their length. Printing them horizontally or at an angle might be more effective, depending on the overall part geometry.
- Angles autoportants : Design overhangs to be above the critical self-supporting angle (often 45° or steeper).
- Chamfers and Fillets: Replace sharp horizontal overhangs with chamfered or filleted edges that gradually transition, reducing the need for supports.
- Sacrificial Features: Incorporate features designed to be machined away later, which can serve as supports during the build.
- Designing for Support Removal: When supports are unavoidable, design them for easy access and removal. Avoid placing them on critical surfaces or within intricate internal channels where removal is impossible. Consider break-off points or features that facilitate cutting or machining.
- Minimum Feature Size and Resolution:
- Laser Spot Size and Layer Thickness: The L-PBF process has inherent limitations on the smallest features it can accurately produce, dictated by the laser spot size, powder particle size, and layer thickness used.
- Design Constraints: Ensure all critical features (e.g., fin thickness, channel widths, hole diameters) are designed above the minimum achievable size. Tiny gaps or holes may fuse shut during printing. DfAM Tip: Consult the specifications of the AM machine and the chosen process parameters. Typical minimum feature sizes are often in the range of 0.3 mm to 0.5 mm, but this varies.
- Thermal Management During Printing:
- Heat Accumulation: Large solid sections or densely packed thin features can lead to localized heat buildup during the printing process. This is particularly relevant for highly conductive copper alloys. Excessive heat can cause dimensional inaccuracies, increased residual stress, or even print failures.
- DfAM Strategies:
- Hollowing/Lattices: Replace solid volumes with hollow sections or internal lattice structures to reduce material volume and facilitate heat dissipation.
- Thermal Bridges: Intentionally design features that act as thermal bridges to conduct heat away from critical areas towards the build plate or support structures.
- Build Layout: Strategically place parts on the build plate to manage overall heat distribution within the build chamber.
- Residual Stress and Warping Mitigation:
- Cause : The rapid heating and cooling cycles inherent in L-PBF create internal stresses within the printed part. If these stresses exceed the material’s yield strength, they can cause warping or distortion, especially in thin, flat, or cantilevered structures common in fins.
- DfAM Strategies:
- Orientation: Orienting long, thin parts vertically can sometimes reduce warping compared to printing them flat on the build plate.
- Robust Anchoring: Ensure sufficient support structures anchor the part securely to the build plate.
- Stress Relief Features: Incorporate design features that allow for some compliance or distribute stress more evenly.
- Material Reduction: Minimize large solid volumes where stress can accumulate. Lattice structures can help distribute stress more effectively.
- Concevoir pour le post-traitement :
- Tolérances d'usinage : If certain surfaces require very tight tolerances or specific finishes achievable only through machining, add extra stock material (machining allowance) to those features in the CAD model.
- Access for Inspection/Cleaning: Ensure internal channels or complex features are designed with access points for cleaning (powder removal) and inspection (e.g., NDT methods).
- Handling Features: For delicate fin structures, consider adding temporary handling features that can be easily removed after post-processing.
Table: DfAM Checklist for AM Marine Fins
Principe du DfAM | Key Action / Consideration | Bénéfice |
---|---|---|
Leverage Complexity | Use thin walls, high aspect ratios, lattices, TPMS, optimized profiles | Maximize thermal performance, reduce weight/volume |
Support Minimization | Optimize orientation, use self-supporting angles, chamfers/fillets | Reduce print time, material cost, post-processing effort |
Support Removability | Design for access, use easily breakable/machinable supports | Ensure part integrity, feasibility of complex internal designs |
Taille minimale de l'objet | Ensure features > machine/process limits (e.g., >0.3-0.5 mm) | Prevent feature loss, ensure printability |
Thermal Management Design | Hollow sections, lattices, thermal bridges | Reduce stress, improve accuracy, prevent print failures |
Warping Mitigation | Optimize orientation, robust anchoring, stress relief features | Maintain dimensional accuracy, prevent build failures |
Design for Post-Processing | Add machining stock, ensure access for cleaning/inspection | Achieve final tolerances/finish, ensure part quality & cleanability |
Consult AM Provider | Discuss design with experts (e.g., Met3dp) early | Leverage expertise, ensure feasibility, optimize for specific equipment |
Exporter vers les feuilles
By thoughtfully applying these DfAM principles, engineers can design marine heat transfer fins that are not only highly efficient and corrosion-resistant but also manufacturable, reliable, and cost-effective using metal additive manufacturing. Collaborating closely with experienced AM service providers during the design phase is highly recommended to leverage their process-specific knowledge and ensure optimal outcomes. Understanding the nuances of the specific AM printing methods like L-PBF is crucial for effective DfAM implementation.
Achieving Precision: Tolerances, Surface Finish, and Dimensional Accuracy in 3D Printed Fins
While metal additive manufacturing unlocks unprecedented geometric freedom, potential users, particularly engineers and procurement managers focused on functional marine components, need realistic expectations regarding the precision achievable. Tolerances, surface finish, and overall dimensional accuracy are critical parameters that influence a part’s fit, function, and performance. Understanding the typical capabilities and limitations of L-PBF for copper alloys like CuNi and CuCrZr is essential for design, specification, and quality control.
Typical Tolerances and Dimensional Accuracy:
- Tolérances générales : For L-PBF processes, typical dimensional tolerances for metal parts, including copper alloys, often fall within the range of ±0.1 mm to ±0.2 mm for smaller features (e.g., up to 50-100 mm), or ±0.1% to ±0.2% of the nominal dimension for larger parts. However, this is a general guideline and can vary significantly.
- Facteurs influençant la précision :
- Étalonnage de la machine : The accuracy and calibration of the specific AM machine (laser positioning system, scanner accuracy, layer thickness control) play a fundamental role. Reputable service providers like Met3dp invest in high-precision equipment and maintain rigorous calibration schedules.
- Paramètres du processus : Laser power, scan speed, hatch spacing, and layer thickness directly impact the melt pool size and stability, influencing dimensional accuracy. Optimized parameters specific to the alloy (CuNi, CuCrZr) are crucial.
- Effets thermiques : The high temperatures involved and the significant thermal conductivity of copper alloys can lead to thermal expansion, contraction, and residual stress accumulation during the build. This can cause warping or distortion, affecting final dimensions. Effective thermal management during the build and post-build stress relief are vital.
- Part Geometry and Size: Larger parts and complex geometries with thin walls or overhangs are generally more susceptible to distortion and deviation from the intended dimensions.
- Orientation de la construction : The orientation of the part on the build plate affects heat distribution, support requirements, and stress patterns, all of which can influence accuracy.
- Qualité de la poudre : Consistent powder characteristics (PSD, morphology, flowability) contribute to stable melting and solidification, leading to better dimensional control.
- Obtenir des tolérances plus strictes : While the general tolerances mentioned above are typical for as-built parts, tighter tolerances (e.g., down to ±0.05 mm or better) can often be achieved on critical features through post-process machining (CNC milling, turning, grinding). DfAM principles should incorporate machining allowances on surfaces requiring such high precision.
Finition de la surface (rugosité) :
- As-Built Surface Finish: The surface finish of parts produced by L-PBF is inherently rougher than machined surfaces. This is due to the layer-by-layer process and the partially melted powder particles adhering to the surface.
- Typical Values: As-built surface roughness (Ra – arithmetic average roughness) typically ranges from 6 µm to 20 µm (micrometers), depending on the material, process parameters, build orientation (upward-facing, downward-facing/supported, and vertical walls have different roughness characteristics), and machine type. Downward-facing surfaces relying on supports tend to be rougher.
- Impact on Fins: For heat transfer fins, surface roughness can have a mixed effect. Increased roughness slightly increases the total surface area but can also increase pressure drop and potentially provide more nucleation sites for corrosion or biofouling if not properly managed (though the inherent properties of CuNi help mitigate this).
- Amélioration de l'état de surface : If a smoother surface is required for fluid dynamic reasons, sealing surfaces, or aesthetics, various post-processing techniques can be employed:
- Abrasive Blasting (Sandblasting, Bead Blasting): Common method to remove loose powder, slightly smooth surfaces, and provide a uniform matte finish. Can achieve Ra values typically in the 3-10 µm range.
- Finition par culbutage et vibration : Parts are tumbled with abrasive media to deburr edges and smooth surfaces. Effective for batches of smaller parts.
- Micro-Machining/Polishing: Can achieve very smooth finishes (Ra < 1 µm) on accessible surfaces but adds significant cost and time.
- Électropolissage : An electrochemical process that preferentially removes material from peaks, resulting in a very smooth, bright, and clean surface. Can be effective for complex shapes but requires specific electrolytes compatible with copper alloys.
Specification and Quality Control:
- Clear Drawings and Specifications: Engineering drawings must clearly define critical dimensions, required tolerances (using GD&T – Geometric Dimensioning and Tolerancing), and surface finish requirements for specific features. Distinguish between as-built acceptable tolerances and those requiring post-machining.
- Consultation with AM Provider: Discuss tolerance and surface finish requirements early in the design phase with the chosen AM service provider. They can advise on achievable limits for their specific equipment and processes for CuNi/CuCrZr and suggest DfAM adjustments if needed.
- Inspection Methods: Quality control typically involves:
- Inspection dimensionnelle : Using calipers, micrometers, coordinate measuring machines (CMMs), or 3D scanners to verify dimensions against the CAD model and drawing specifications.
- Mesure de la rugosité de surface : Using a profilometer to measure Ra or other relevant roughness parameters on specified surfaces.
- Essais non destructifs (END) : Methods like X-ray or CT scanning can be used to detect internal defects like porosity or inclusions that might affect structural integrity, although less common for fins unless critically loaded.
Table: Precision Parameters for AM Copper Alloy Fins
Paramètres | Typical As-Built (L-PBF) Range | Factors Influencing | Post-Processing Options for Improvement | Considerations for Marine Fins |
---|---|---|---|---|
Tolérance dimensionnelle | ±0.1 to ±0.2 mm or ±0.1% to ±0.2% | Machine, Parameters, Thermal, Geometry | CNC Machining (for critical features, <±0.05 mm) | Ensure fit within heat exchanger assemblies, alignment. |
Rugosité de la surface (Ra) | 6 µm to 20 µm | Orientation, Supports, Parameters | Blasting (3-10 µm), Tumbling, Polishing (<1 µm), EP | Impact on heat transfer vs. pressure drop, biofouling potential. |
Taille minimale de l'objet | ~0.3 mm to 0.5 mm | Laser Spot, Powder Size, Layer Height | None (Design limited) | Ensure thin fins, small channels are printable. |
Déformation/distorsion | Can occur, especially in large/thin parts | Thermal Stress, Geometry, Anchoring | Stress Relief HT, Optimized Design/Orientation/Supports | Critical for maintaining flatness and overall shape integrity. |
Exporter vers les feuilles
In conclusion, while metal 3D printing might not inherently match the ultra-high precision of CNC machining across an entire complex part in its as-built state, it offers very respectable dimensional accuracy and tolerances suitable for many functional marine components, including heat transfer fins. By understanding the achievable precision, applying DfAM principles, specifying requirements clearly, and utilizing targeted post-processing where necessary, engineers and procurement teams can confidently leverage AM to produce high-performance, dimensionally accurate marine parts from advanced copper alloys like CuNi30Mn1Fe and CuCrZr.
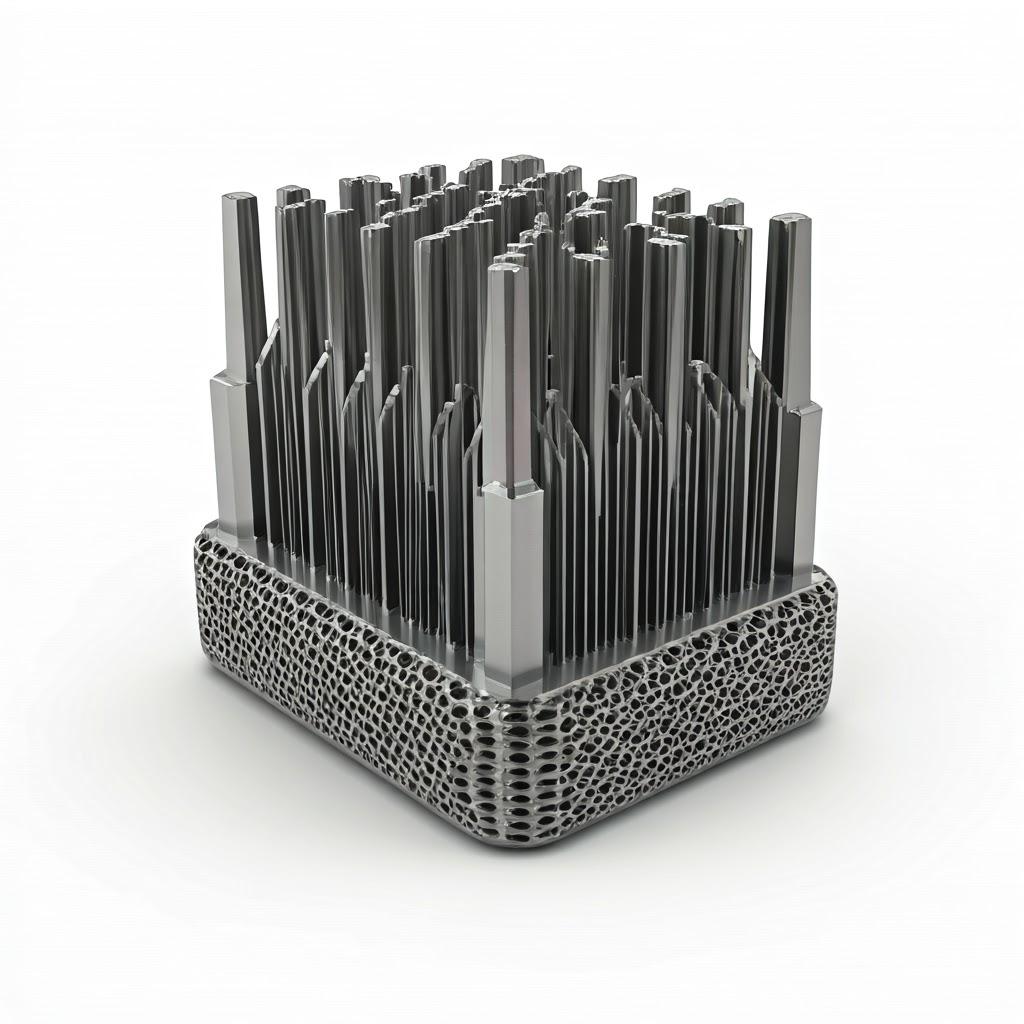
Beyond the Print: Essential Post-Processing Steps for Marine Heat Transfer Fins
Completing the 3D printing process is a significant milestone, but it’s rarely the final step in producing functional, high-performance marine heat transfer fins. Parts emerging from the L-PBF machine require a series of post-processing steps to transform them from a raw build into a finished component ready for integration and service. These steps are crucial for achieving the desired material properties, dimensional accuracy, surface finish, and overall quality required for demanding maritime applications. Understanding these common post-processing requirements is vital for project planning, cost estimation, and ensuring the final fins meet all specifications.
Common Post-Processing Steps for AM Copper Alloy Fins:
- Elimination des poudres :
- Processus : Immediately after the build finishes and the build chamber cools, the component, still attached to the build plate and potentially surrounded by unsintered powder, is removed. Excess powder must be carefully removed from all surfaces, including intricate internal channels or lattice structures.
- Méthodes : Compressed air/inert gas blow-off, gentle brushing, vibration, and sometimes specialized powder handling stations are used. For complex internal geometries, thorough cleaning is critical to prevent blockages or contamination.
- Importance: Ensures part cleanliness, allows for powder recovery and recycling (important for valuable copper alloy powders), and prepares the part for subsequent steps.
- Traitement thermique anti-stress :
- Objet : The rapid heating and cooling cycles during L-PBF build up significant internal residual stresses within the part. These stresses can lead to distortion over time or during subsequent machining, and potentially reduce fatigue life. A stress relief heat treatment aims to relax these internal stresses without significantly altering the core microstructure or hardness (especially important for CuNi).
- Processus : Parts (often while still attached to the build plate to provide restraint against warping during heating) are heated to a specific temperature below the alloy’s aging or recrystallization temperature, held for a period, and then slowly cooled. Parameters depend on the alloy (CuNi vs. CuCrZr) and part geometry.
- Importance: Improves dimensional stability, reduces risk of cracking, and makes the part safer to handle and machine. Often considered mandatory for functional parts.
- Retrait de la pièce de la plaque de construction :
- Processus : The part, now stress-relieved, needs to be separated from the metal build plate it was printed on.
- Méthodes : Commonly done using wire EDM (Electrical Discharge Machining), band sawing, or manual cutting, depending on the part size, geometry, and support structure interface.
- Importance: Frees the individual component for further processing. Requires care to avoid damaging the part.
- Retrait de la structure de soutien :
- Objet : The support structures necessary during the build must be removed.
- Méthodes : Can range from simple manual breaking or prying for easily accessible supports, to more involved methods like hand grinding, milling, or EDM for supports in complex locations or those strongly bonded to the part. The difficulty depends heavily on the DfAM considerations applied during the design phase.
- Importance: Essential for achieving the final part geometry and function. Can be one of the most labor-intensive and potentially damaging post-processing steps if not planned carefully.
- Solution Annealing and Aging Heat Treatment (Primarily for CuCrZr):
- Objet : CuCrZr is a precipitation-hardening alloy. To achieve its characteristic high strength and high thermal conductivity, it requires a specific two-stage heat treatment après printing and stress relief:
- Recuit de la solution : Heating to a high temperature (e.g., ~950-1000 °C) to dissolve the Chromium and Zirconium into the copper matrix, followed by rapid quenching (usually in water).
- Aging (Precipitation Hardening): Reheating to a lower temperature (e.g., ~450-500 °C) and holding for a specific time to allow fine precipitates of Cr and Zr to form within the copper matrix. These precipitates impede dislocation movement, significantly increasing strength and hardness, while minimally impacting electrical/thermal conductivity compared to keeping the elements in solution.
- Importance: Absolutely critical for developing the target mechanical and thermal properties of CuCrZr. Skipping or improperly performing this step will result in a component with suboptimal performance. CuNi alloys generally do not require this type of hardening treatment.
- Objet : CuCrZr is a precipitation-hardening alloy. To achieve its characteristic high strength and high thermal conductivity, it requires a specific two-stage heat treatment après printing and stress relief:
- Finition de la surface :
- Objet : To improve the as-built surface roughness, remove support witness marks, achieve a desired aesthetic, or prepare the surface for coating.
- Methods (as described previously):
- Abrasive Blasting (Bead/Sand): Common for a uniform matte finish and cleaning.
- Finition par culbutage et vibration : For smoothing and deburring batches of parts.
- Manual Grinding/Polishing: For specific areas requiring high smoothness.
- Électropolissage : For overall smoothing and brightening, potentially enhancing corrosion resistance.
- Importance: Affects fluid dynamics (pressure drop), cleanability, potentially corrosion/biofouling initiation, and final appearance. Requirement depends on the specific application.
- Usinage CNC :
- Objet : To achieve tighter tolerances, specific flatness, or required surface finishes on critical interfacing features (e.g., mounting surfaces, sealing faces, connection points) that cannot be reliably achieved by the AM process alone.
- Processus : Utilizes traditional CNC milling, turning, or grinding machines. Requires careful fixture design to hold the complex AM part securely without distortion. Machining allowances must have been included in the DfAM phase.
- Importance: Ensures proper fit and function when the fin or finned component integrates into a larger marine assembly.
- Nettoyage et inspection :
- Objet : Final cleaning to remove any machining fluids, debris, or residual contaminants. Followed by final quality inspection to verify all dimensional, surface finish, and material property requirements are met.
- Méthodes : Ultrasonic cleaning, solvent wiping. Inspection methods include visual checks, dimensional measurements (CMM, scanning), surface roughness tests, and potentially NDT or material testing (e.g., hardness check for CuCrZr post-heat treatment).
- Importance: Ensures the delivered component meets all engineering specifications and quality standards before deployment in a critical marine system.
Table: Post-Processing Sequence and Purpose
Étape | Typical Order | Objectif | Alloy Relevance | Principales considérations |
---|---|---|---|---|
1. Powder Removal | 1 | Clean part, recover powder | Les deux | Thoroughness, especially internal channels |
2. Stress Relief HT | 2 | Reduce internal stress, improve stability | Both (Mandatory) | Proper parameters, often done on build plate |
3. Part Removal from Plate | 3 | Separate part from build plate | Les deux | Method (Wire EDM, saw), avoid part damage |
4. Support Removal | 4 | Remove temporary build supports | Les deux | Access, method (manual, machine), DfAM impact |
5. Solution Anneal + Age HT | 5 | Develop high strength & conductivity | CuCrZr (Mandatory) | Precise temperature/time control, quench rate |
6. Surface Finishing | 6 (Optional) | Improve roughness, aesthetics, prepare for coating | Les deux | Method (Blast, tumble, polish, EP), required Ra |
7. CNC Machining | 7 (Optional) | Achieve tight tolerances/finish on specific features | Les deux | Machining allowance in design, fixturing |
8. Final Cleaning & Inspection | 8 | Ensure cleanliness, verify specs | Les deux | Methods, adherence to drawing requirements |
Exporter vers les feuilles
The extent and specific nature of post-processing can significantly impact the final cost and lead time of 3D printed marine fins. Procurement managers and engineers must factor these steps into their project planning. Working with a full-service AM provider experienced in handling copper alloys and the associated post-processing requirements is crucial for obtaining finished components that meet the rigorous demands of the marine industry.
Navigating Challenges: Overcoming Potential Issues in 3D Printing Marine Fins
While metal additive manufacturing, particularly L-PBF, offers tremendous potential for creating advanced marine heat transfer fins from CuNi and CuCrZr alloys, the process is not without its challenges. Copper alloys, in particular, present unique difficulties due to their inherent physical properties. Awareness of these potential issues allows engineers, designers, and manufacturers to implement strategies to mitigate them, ensuring successful builds and high-quality final parts. Partnering with experienced AM service providers who understand these challenges is key.
Common Challenges in Printing Copper Alloy Fins:
- High Reflectivity and Thermal Conductivity:
- Enjeu : Copper alloys strongly reflect the infrared wavelengths typically used by fiber lasers in L-PBF machines. They also conduct heat away from the melt pool extremely rapidly.
- Consequences:
- Low Absorption: Requires higher laser power to initiate melting compared to steels or titanium.
- Process Instability: Small variations in absorptivity (due to surface condition or slight compositional changes) can lead to inconsistent melt pool size and depth.
- Porosité de manque de fusion : Insufficient energy density due to reflection or rapid heat loss can prevent complete melting and fusion between layers or scan tracks, leading to voids.
- Ball-Up Effect: Surface tension can cause the unstable melt pool to form balls instead of spreading evenly.
- Mitigation Strategies:
- High-Power Lasers: Using machines equipped with higher power lasers (e.g., 1kW or more) provides sufficient energy input.
- Optimized Parameters: Developing specific process parameters (laser power, scan speed, hatch strategy) tailored for the high reflectivity/conductivity of CuNi or CuCrZr is crucial. This often involves slower scan speeds and specific energy density targets.
- Laser Wavelength: Green lasers (~515 nm) have significantly higher absorption in copper compared to infrared lasers (~1070 nm), leading to a more stable process. Machines with green lasers are becoming more common but are still less widespread than IR systems.
- Qualité de la poudre : Using powders with appropriate morphology and surface characteristics can slightly influence absorption. Met3dp’s focus on high-quality, spherical powders produced via advanced atomization helps ensure consistent melting behavior.
- Residual Stress, Warping, and Distortion:
- Enjeu : As discussed under DfAM and Precision, the large temperature gradients during L-PBF generate significant residual stresses. Highly conductive copper alloys exacerbate this by cooling very quickly. Thin fin structures are particularly susceptible to warping.
- Mitigation Strategies:
- Stratégies d'analyse optimisées : Using techniques like island scanning or chessboard patterns can help distribute heat more evenly and reduce localized stress buildup.
- Structures de soutien robustes : Well-designed supports are critical for anchoring the part and conducting heat away, minimizing distortion during the build.
- Build Plate Heating: Pre-heating the build plate reduces the temperature gradient between the molten material and the surrounding environment, lowering residual stress.
- Traitement thermique anti-stress : Performing this step immediately after printing (ideally before removing from the build plate) is essential.
- DfAM : Designing features to minimize stress concentration and avoiding large, solid blocks of material.
- Retrait de la structure de soutien :
- Enjeu : Copper alloys, being relatively ductile and strong (especially CuCrZr after HT), can make support removal challenging. Supports in intricate internal channels or within fine lattice structures designed for heat transfer can be particularly difficult or impossible to remove completely.
- Mitigation Strategies:
- DfAM for Support Minimization: The primary strategy is to design the part to be self-supporting as much as possible through orientation and feature design (chamfers, fillets).
- Conception optimisée du support : Using support types (e.g., conical, thin-walled, perforated) designed for easier removal. Reducing the contact area between the support and the part.
- Accessible Design: Ensuring physical access for tools (manual or automated) to reach the support structures.
- Material Choice: If internal supports are unavoidable and irremovable, assess if the slight performance degradation is acceptable or if a design modification is required.
- Contrôle de la porosité :
- Enjeu : Voids or pores within the final part compromise its mechanical integrity, can act as corrosion initiation sites, and may slightly reduce thermal conductivity. Porosity can arise from:
- Porosité du gaz : Trapped gas (e.g., Argon process gas, dissolved gases in the powder) within the melt pool during solidification.
- Porosité de manque de fusion : Insufficient energy density leads to incomplete melting between layers or scan tracks.
- Mitigation Strategies:
- Poudre de haute qualité : Using powders with low internal gas content and controlled morphology (like those from Met3dp’s VIGA or PREP processes) minimizes the risk of gas porosity. Proper powder handling and storage are also critical to prevent moisture pickup.
- Paramètres de processus optimisés : Ensuring sufficient energy density to achieve full melting and fusion while avoiding excessive energy that could vaporize material or trap process gas.
- Stable Melt Pool Dynamics: Process parameters and scan strategies aimed at creating a stable, well-behaved melt pool.
- Pressage isostatique à chaud (HIP) : A post-processing step involving high temperature and high pressure inert gas. HIP can effectively close internal pores (both gas and lack-of-fusion), leading to near-fully dense parts. It adds cost but may be specified for critical applications demanding maximum material integrity.
- Enjeu : Voids or pores within the final part compromise its mechanical integrity, can act as corrosion initiation sites, and may slightly reduce thermal conductivity. Porosity can arise from:
- Powder Handling and Safety:
- Enjeu : Fine metal powders, including copper alloys, can be reactive and pose inhalation risks. Copper powder is also relatively dense, requiring robust handling systems. Cross-contamination with other metal powders must be avoided.
- Mitigation Strategies:
- Dedicated Equipment: Ideally, using AM machines dedicated solely to copper alloys prevents cross-contamination.
- Inert Atmosphere Handling: Using glove boxes or closed-loop powder handling systems filled with inert gas (Argon) minimizes oxidation and operator exposure.
- Équipement de protection individuelle (EPI) : Operators must use appropriate respirators, gloves, and protective clothing.
- Grounding and Spark Prevention: Copper powder is conductive; measures must be taken to prevent static discharge and potential ignition sources (though copper is less of a fire risk than Ti or Al).
Table: Challenge Mitigation Summary
Défi | Primary Cause | Principales stratégies d'atténuation | Role of Supplier/Expertise |
---|---|---|---|
Reflectivity/Conductivity | Inherent material properties of Cu | High power / Green lasers, Optimized parameters, Quality powder | Parameter development, Machine capability, Powder quality (Met3dp) |
Residual Stress / Warping | Thermal gradients, Rapid cooling | Optimized scan strategy, Supports, Build plate heat, Stress relief HT, DfAM | Process control, DfAM guidance, HT expertise |
Support Removal Difficulty | Ductile material, Complex geometry | DfAM (minimization/accessibility), Optimized support design, Appropriate removal tools | DfAM consultation, Post-processing capabilities |
Porosity (Gas / LoF) | Trapped gas, Insufficient energy density | Quality powder, Optimized parameters, Stable melt pool, HIP (optional) | Powder quality control (Met3dp), Process optimization, NDT/HIP |
Powder Handling / Safety | Reactivity, Inhalation risk, Cross-contamination | Dedicated equipment, Inert handling, PPE, Grounding | Strict safety protocols, Cleanliness, Material traceability |
Exporter vers les feuilles
Successfully navigating these challenges requires a combination of careful design (DfAM), selection of high-quality materials, precise process control during printing, appropriate post-processing, and often, collaboration with an experienced additive manufacturing partner like Met3dp. Their expertise in both advanced powder manufacturing and metal AM processes can significantly de-risk the production of complex, high-performance copper alloy components like marine heat transfer fins.
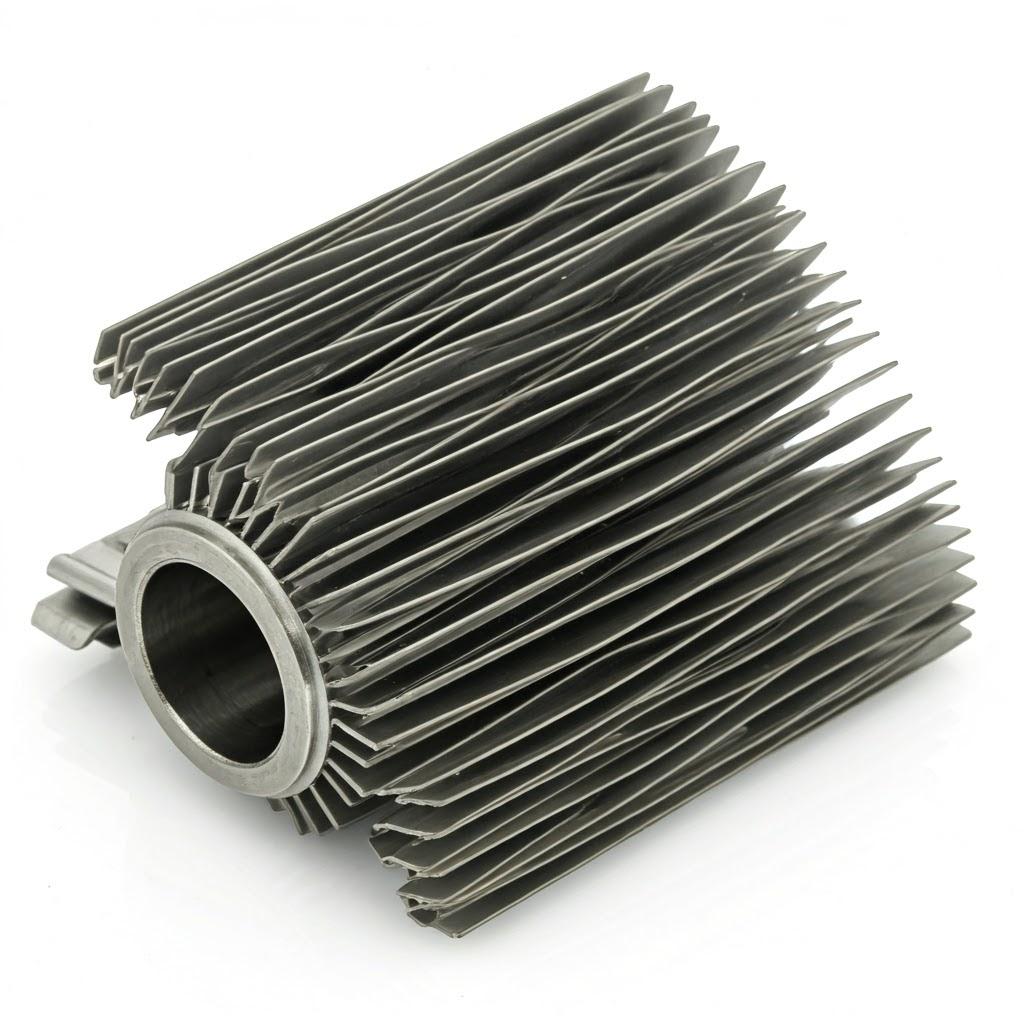
Supplier Selection: Choosing the Right Metal AM Partner for Marine Component Manufacturing
The successful adoption of additively manufactured marine heat transfer fins hinges not only on optimized design and appropriate material selection but also crucially on the capabilities and expertise of the chosen manufacturing partner. Selecting the right metal additive manufacturing service provider or strategic partner is a critical decision for engineers and procurement managers, especially when dealing with high-value components destined for demanding maritime environments. The ideal supplier goes beyond simply printing a part; they act as a collaborative partner, offering expertise throughout the product lifecycle, from design consultation to final quality assurance.
Key Criteria for Evaluating Metal AM Suppliers for Marine Fins:
- Proven Expertise with Copper Alloys (CuNi, CuCrZr):
- Why it Matters: As highlighted previously, printing copper alloys like CuNi30Mn1Fe and CuCrZr presents unique challenges due to their high reflectivity and thermal conductivity. A supplier must have demonstrable experience and success in processing these specific materials.
- Evaluation Points: Ask for case studies, sample parts, or data related to copper alloy projects. Inquire about their specific parameter sets, process controls, and techniques for managing issues like porosity and residual stress in these alloys. Do they possess machines optimized for copper (e.g., high power or green lasers)?
- Advanced AM Equipment and Technology:
- Why it Matters: The quality, accuracy, and capabilities of the L-PBF machines directly impact the final part quality.
- Evaluation Points: What specific machine models do they operate? What are the build volumes, laser power options, and achievable accuracy/resolution? Do they maintain their equipment rigorously? Companies like Met3dp, who not only provide services but also manufacture their own advanced SEBM (Selective Electron Beam Melting) printers and utilize leading L-PBF technology, often possess deep technical knowledge of the hardware.
- Robust Powder Quality Control and Management:
- Why it Matters: Feedstock quality is paramount for successful AM. The supplier’s procedures for sourcing, testing, handling, storing, and recycling metal powders are critical, especially for sensitive and expensive copper alloys.
- Evaluation Points: What are their powder sourcing policies? Do they perform incoming quality checks (e.g., chemistry, PSD, morphology)? How do they ensure traceability and prevent cross-contamination between different metal powders? How is powder rejuvenated or recycled? Suppliers like Met3dp, with in-house powder production capabilities using Gas Atomization and PREP technologies, often have a distinct advantage in understanding and controlling powder quality from start to finish. Look for suppliers who can provide powder specification sheets and certificates of conformity.
- Comprehensive In-House Post-Processing Capabilities:
- Why it Matters: As detailed earlier, extensive post-processing is required for AM fins. A supplier with integrated, in-house capabilities (stress relief, heat treatment specific to CuCrZr aging, support removal, CNC machining, surface finishing, inspection) can offer better control, shorter lead times, and potentially lower costs compared to outsourcing multiple steps.
- Evaluation Points: What post-processing steps can they perform in-house? What equipment do they have (furnaces, CNC machines, blasting cabinets, CMMs)? Do they have experience with the specific heat treatment cycles required for CuCrZr?
- Quality Management Systems and Certifications:
- Why it Matters: Formal quality systems ensure consistency, traceability, and adherence to procedures. This is vital for critical marine components.
- Evaluation Points: Does the supplier hold relevant certifications, such as ISO 9001 (Quality Management)? Are they working towards or do they hold industry-specific certifications (e.g., AS9100 for aerospace, which indicates a high level of quality control relevant to demanding applications)? Do they have documented quality control procedures for each stage of the manufacturing process?
- Design for Additive Manufacturability (DfAM) Support:
- Why it Matters: Optimizing a design for AM requires specialized knowledge. A good partner will offer DfAM consultation to help clients leverage the benefits of AM while ensuring printability and cost-effectiveness.
- Evaluation Points: Do they offer design review services? Can their engineers provide feedback on feature sizes, support strategies, orientation, and topology optimization possibilities? Early collaboration can prevent costly redesigns later.
- Gestion de projet et communication :
- Why it Matters: Clear communication, responsive project management, and transparency are essential for a smooth manufacturing process, especially for custom or complex parts.
- Evaluation Points: Is there a dedicated point of contact for your project? How responsive are they to inquiries? Do they provide clear quotes, timelines, and progress updates?
- Capacity and Lead Time:
- Why it Matters: The supplier needs adequate machine capacity and efficient workflow to meet required project timelines.
- Evaluation Points: What are their typical lead times for copper alloy parts of similar complexity? How do they manage their build queues? Can they accommodate urgent requests or scale production if needed?
- Cost Transparency and Value:
- Why it Matters: While cost is always a factor, the focus should be on overall value (quality, reliability, expertise, service) rather than just the lowest price.
- Evaluation Points: Do they provide detailed quotes outlining all cost components (material, print time, post-processing, NDT, etc.)? Are they transparent about factors that influence cost?
Table: Supplier Evaluation Checklist
Critères | Key Questions to Ask | Ideal Partner Attributes |
---|---|---|
Copper Alloy Expertise | Experience with CuNi/CuCrZr? Case studies? Parameter control? | Proven track record, specialized knowledge, optimized equipment |
AM Equipment | Machine types? Build volume? Accuracy? Maintenance? | State-of-the-art, well-maintained L-PBF machines suitable for copper |
Powder Quality Control | Sourcing? Testing? Handling? Traceability? Recycling? | Rigorous QC, traceability, contamination control, preferably in-house powder expertise (e.g., Met3dp) |
Post-traitement interne | What capabilities? Stress relief, HT (CuCrZr), CNC, finishing, inspection? | Comprehensive suite of relevant in-house capabilities |
Quality Systems/Certs | ISO 9001? Other relevant certs? Documented procedures? | Certified QMS, strong focus on quality control and documentation |
DfAM Support | Offer design reviews? Provide optimization feedback? | Collaborative DfAM expertise, proactive suggestions |
Project Management/Comm. | Dedicated contact? Responsiveness? Transparency? Updates? | Clear, consistent communication, professional project management |
Capacity & Lead Time | Typical lead times? Ability to scale? Urgent request handling? | Realistic lead time estimates, sufficient capacity, reliable delivery |
Coût et valeur | Detailed quotes? Transparency? Focus on value vs. just price? | Clear pricing structure, focus on delivering high-quality, reliable parts |
Company Stability & Reputation | Years in business? Customer testimonials? Financial stability? (À propos de nous) | Established, reputable company with positive client feedback (Consider exploring Met3dp’s background) |
Exporter vers les feuilles
Choosing the right supplier is an investment in the success of your project. For procurement managers sourcing wholesale marine parts or engineers developing cutting-edge thermal systems, partnering with a knowledgeable and capable metal AM provider like Met3dp, with deep roots in both material science and additive manufacturing technology, can significantly mitigate risks and ensure the delivery of high-performance, reliable corrosion-resistant heat transfer fins.
Understanding Investment: Cost Drivers and Typical Lead Times for AM Marine Fins
While the technical advantages of additively manufactured marine fins are compelling, understanding the associated costs and production timelines is crucial for project planning, budgeting, and evaluating the overall value proposition compared to traditional methods. Metal AM, particularly with specialized materials like copper alloys, represents a significant investment, and several factors influence the final price and delivery schedule.
Key Cost Drivers for AM Marine Fins:
- Coût des matériaux :
- Poudres d'alliage de cuivre : CuNi and CuCrZr powders are significantly more expensive than common materials like stainless steel or aluminum alloys. Copper itself is a valuable commodity, and the specialized atomization processes required to produce high-quality, spherical AM powders add further cost. Powder recyclability and buy-back programs from the supplier can influence the effective material cost.
- Powder Consumption: The total volume of the part, including any necessary support structures, directly dictates the amount of powder consumed. Designs optimized using DfAM (e.g., lattices, thin walls) can reduce material consumption compared to solid designs.
- AM Machine Time (Printing Cost):
- Temps de construction : This is often the largest cost component. It’s influenced by:
- Part Volume: Larger parts naturally take longer to print.
- Part Height: Print time is directly proportional to the number of layers, hence the height in the build orientation.
- La complexité : Intricate features and complex scan strategies required for stability can increase print time.
- Structures de soutien : Printing supports adds to the overall build time.
- Nesting: Printing multiple parts simultaneously in one build (nesting) can improve machine utilization but requires careful thermal management.
- Machine Depreciation and Operating Costs: The high capital cost of industrial metal AM machines, maintenance, inert gas consumption, energy usage, and skilled labor required to operate them are factored into the hourly machine rate.
- Temps de construction : This is often the largest cost component. It’s influenced by:
- Coûts de post-traitement :
- Labor Intensity: Many post-processing steps (support removal, manual finishing) are labor-intensive and require skilled technicians. The complexity of the part and the difficulty of support removal significantly impact this cost.
- Traitement thermique : Stress relief is standard. For CuCrZr, the mandatory solution annealing and aging cycles require furnace time and energy, adding cost.
- Usinage : If CNC machining is required for tight tolerances or specific finishes, this adds significant cost based on machine time, programming, and fixturing complexity.
- Finition de la surface : Costs vary depending on the method (blasting is relatively low-cost; extensive polishing or electropolishing is more expensive).
- Inspection : Time required for dimensional checks (CMM, scanning) and any NDT adds to the cost.
- Setup and Programming:
- Préparation de la construction : Time taken by engineers/technicians to orient the part, generate support structures, define scan parameters, and prepare the build file. This cost is often amortized over the number of parts in a build.
- CNC Programming: If machining is needed, programming the toolpaths requires skilled labor.
- Volume de commande :
- Economies d'échelle : While AM is cost-effective for prototypes and low volumes compared to tooling-intensive traditional methods, some economies of scale exist. Setup costs are spread over more parts, and full build plates utilize machine time more efficiently. However, AM generally doesn’t achieve the same per-part cost reduction at very high volumes as mass production techniques like stamping or casting.
Délais d'exécution typiques :
Lead time refers to the total time from order placement to component delivery. For AM marine fins, this can range widely:
- Simple Prototypes: For small, relatively simple fin designs requiring minimal post-processing, lead times might be a few days to 1-2 weeks, depending heavily on machine availability.
- Complex Parts / Small Batches: For larger, more complex fins involving intricate geometries, extensive supports, mandatory heat treatments (CuCrZr), and potentially CNC machining, lead times are typically longer, ranging from 3 à 8 semaines, or potentially more.
- Factors Influencing Lead Time:
- Machine Availability: Current workload and scheduling queues at the AM service provider.
- Temps de construction : The actual time spent printing the part(s).
- Post-Processing Complexity: The number and duration of required post-processing steps (especially multi-stage heat treatments or extensive machining).
- Inspection Requirements: Rigorous inspection protocols add time.
- Expédition: Time required for transportation to the final destination.
Table: Cost & Lead Time Factors
Facteur | Primary Influence | Impact sur les coûts | Impact sur le délai d'exécution | Mitigation / Optimization |
---|---|---|---|---|
Matériau | Alloy type (CuNi/CuCrZr), Part Volume, Supports | Haut | Faible | DfAM (reduce volume), Efficient nesting, Powder recycling |
AM Print Time | Volume, Height, Complexity, Supports, Machine Rate | Haut | Haut | DfAM (optimize orientation/complexity), Efficient nesting |
Post-traitement | Labor, Heat Treatment, Machining, Finishing, Inspection | Moyen à élevé | Moyen à élevé | DfAM (minimize supports/machining), In-house capabilities |
Setup/Programming | Build prep time, CNC programming | Faible à moyen | Faible | Standardized workflows, Experience |
Volume des commandes | Amortization of setup, Machine utilization | Moyen | Moyen | Optimize build layout, Larger batches (where applicable) |
Exporter vers les feuilles
Cost Comparison Note: While the direct per-part cost of AM fins might sometimes be higher than traditionally manufactured fins (especially simple designs at high volumes), a total cost of ownership analysis is crucial. AM fins can offer benefits like improved thermal performance (leading to smaller systems or lower energy consumption), enhanced corrosion resistance (reducing maintenance and replacement costs), design consolidation (reducing assembly), and rapid availability of custom/spare parts, which can provide significant long-term value and operational advantages in the demanding marine sector. Procurement teams should consider this broader lifecycle value when comparing manufacturing methods.
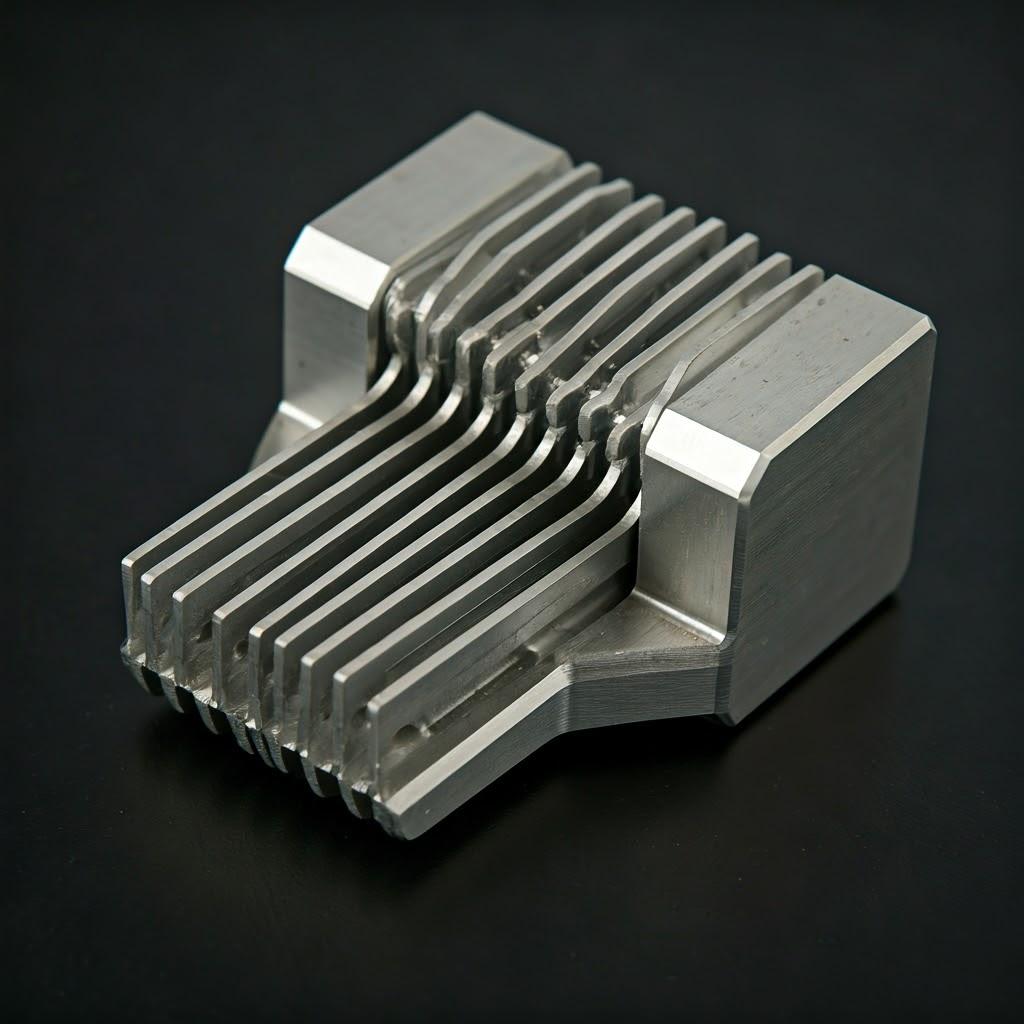
Frequently Asked Questions (FAQ) about 3D Printed Marine Heat Transfer Fins
Here are answers to some common questions engineers and procurement managers might have when considering metal additive manufacturing for marine heat transfer fins using CuNi or CuCrZr alloys:
- How does the cost of 3D printed copper alloy fins compare to traditionally manufactured ones?
- Répondre: It depends heavily on complexity, volume, and the specific traditional method.
- Prototypes & Low Volumes: AM is often more cost-effective for prototypes or small batches due to the avoidance of high tooling costs (e.g., casting molds, stamping dies).
- Haute complexité : For fins with highly complex geometries (lattices, TPMS, internal channels) that are difficult or impossible to make traditionally, AM can be the only viable option, making direct cost comparison less relevant than performance gains.
- Simple Designs / High Volumes: For very simple fin designs produced in large quantities, traditional methods like stamping or extrusion are typically cheaper on a per-part basis.
- Total Cost of Ownership: Consider lifecycle benefits: AM fins might offer superior performance (allowing smaller systems), longer life due to corrosion resistance (reducing maintenance/replacement), and faster availability for spares, which can offset a potentially higher initial part cost.
- Répondre: It depends heavily on complexity, volume, and the specific traditional method.
- What is the expected lifespan and durability of 3D printed CuNi30Mn1Fe or CuCrZr fins in seawater?
- Répondre: Properly manufactured and processed AM fins made from these alloys should exhibit durability comparable to, or potentially even better than, their wrought or cast counterparts, assuming similar density and defect levels.
- CuNi30Mn1Fe: This alloy is renowned for its excellent seawater corrosion and biofouling resistance. AM parts achieving full density (>99.5%) should offer long service life, similar to traditionally manufactured C71500 components used extensively in marine environments for decades. The fine microstructure sometimes achieved in AM might even offer slight improvements in certain corrosion modes.
- CuCrZr: While offering good corrosion resistance, it’s not as inherently resistant to aggressive seawater and biofouling as CuNi. Its lifespan in direct seawater contact might be shorter unless protective coatings are applied or it’s used in less aggressive conditions (e.g., treated water, closed loops). Its primary advantage is high thermal conductivity and strength.
- Quality is Key: Lifespan depends critically on achieving high density during printing and proper post-processing to minimize defects and residual stress. Partnering with a quality-focused supplier is essential.
- Répondre: Properly manufactured and processed AM fins made from these alloys should exhibit durability comparable to, or potentially even better than, their wrought or cast counterparts, assuming similar density and defect levels.
- Can we just print our existing fin design, or does it need to be redesigned for additive manufacturing?
- Répondre: While it might be possible to print an existing design, it’s rarely optimal. To fully leverage the benefits of AM and ensure successful, cost-effective printing, designs should ideally be reviewed and potentially modified using Design for Additive Manufacturability (DfAM) principles.
- Optimization Potential: Existing designs are often constrained by traditional manufacturing limitations. DfAM allows for incorporating features like thinner walls, complex lattices, or optimized profiles that enhance thermal performance significantly. Simply printing the old design misses these opportunities.
- Printability Issues: Designs intended for casting or machining may have features (e.g., unsupported overhangs, large solid sections, features below minimum printable size) that are problematic for AM. Orientation and support strategies need careful consideration, which might necessitate minor design tweaks.
- Recommendation: Engage with your AM service provider early. Provide them with your existing design and performance requirements. They can perform a DfAM review and suggest modifications to improve printability, enhance performance, and potentially reduce cost.
- Répondre: While it might be possible to print an existing design, it’s rarely optimal. To fully leverage the benefits of AM and ensure successful, cost-effective printing, designs should ideally be reviewed and potentially modified using Design for Additive Manufacturability (DfAM) principles.
Conclusion: The Future of Marine Thermal Systems is Additive
The relentless demands of the marine environment – combating corrosion, maximizing efficiency within tight space constraints, and ensuring unwavering reliability – constantly push the boundaries of engineering materials and manufacturing processes. For critical components like heat transfer fins, metal additive manufacturing represents a paradigm shift, offering solutions that directly address these challenges in ways previously unimaginable.
By harnessing the power of AM processes like Laser Powder Bed Fusion, engineers can now design and produce marine fins with unparalleled geometric complexity. Intricate lattice structures, TPMS geometries, and ultra-thin walls, fabricated from advanced copper alloys like the exceptionally corrosion-resistant CuNi30Mn1Fe or the high-strength, high-conductivity CuCrZr, translate directly into tangible benefits: significantly enhanced thermal performance, leading to more compact and lightweight heat exchange systems; superior resistance to saltwater corrosion and biofouling, reducing maintenance and extending component lifespan; and the ability to consolidate parts, improving reliability and streamlining assembly.
The journey involves navigating specific challenges related to processing copper alloys and requires careful attention to Design for Additive Manufacturability (DfAM), precision control, and thorough post-processing. Success hinges on selecting the right manufacturing partner – one with proven expertise in copper alloys, robust quality systems, comprehensive capabilities, and a collaborative approach. Companies like Met3dp, with their deep expertise spanning from advanced metal powder production using Gas Atomization and PREP to providing comprehensive solutions d'impression 3D de métaux, are at the forefront of enabling this technological advancement.
While considerations around cost drivers and lead times remain important, the potential for performance breakthroughs and improved total cost of ownership makes a compelling case for adopting AM for marine heat transfer fins. From main engine coolers and HVAC condensers to sophisticated electronics cooling modules, the ability to create optimized, durable components tailored to specific needs offers a distinct competitive advantage.
The future of high-performance marine thermal management is increasingly pointing towards additive manufacturing. As the technology matures, costs decrease, and more engineers embrace DfAM principles, we can expect to see even wider adoption of 3D printed components enhancing the efficiency, reliability, and capability of marine systems worldwide. Exploring the potential of AM for your specific marine application is no longer just an option for the future – it’s a strategic imperative for staying ahead today.
Ready to explore how additive manufacturing can revolutionize your marine thermal management systems? Contact Met3dp today to discuss your project requirements and learn how our expertise in advanced copper alloy powders and metal 3D printing can deliver superior performance and durability for your critical components.
Partager sur
MET3DP Technology Co. est un fournisseur de premier plan de solutions de fabrication additive dont le siège se trouve à Qingdao, en Chine. Notre société est spécialisée dans les équipements d'impression 3D et les poudres métalliques de haute performance pour les applications industrielles.
Articles connexes
À propos de Met3DP
Mise à jour récente
Notre produit
CONTACTEZ-NOUS
Vous avez des questions ? Envoyez-nous un message dès maintenant ! Nous répondrons à votre demande avec toute une équipe dès réception de votre message.
Obtenir les informations de Metal3DP
Brochure du produit
Obtenir les derniers produits et la liste des prix
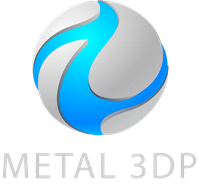
Poudres métalliques pour l'impression 3D et la fabrication additive