3D Printed Housings for Satellite Cameras
Table des matières
Introduction: The Critical Role of Housings for Satellite Cameras in Modern Aerospace
In the demanding environment of space, every component matters. Satellites, our eyes and ears beyond the atmosphere, rely on intricate systems operating flawlessly under extreme conditions – vast temperature swings, vacuum, radiation, and significant launch vibrations. Among the most critical systems are the optical payloads, particularly the cameras that enable Earth observation, astronomical research, communication relays, and reconnaissance. Protecting these sensitive optical instruments is the satellite camera housing, a component whose design and manufacture directly impact mission success.
Traditionally, manufacturing these housings involved subtractive methods, primarily CNC machining complex geometries from solid blocks of metal like aluminum or titanium. While effective, this approach often results in significant material waste, lengthy lead times, and limitations in design complexity, especially when striving for optimal lightweighting – a paramount concern in aerospace where every gram saved translates to reduced launch costs and increased payload capacity.
Entrer la fabrication additive métallique (AM), commonly known as metal Impression 3D. This transformative technology offers a paradigm shift in producing high-performance composants aérospatiaux. Instead of removing material, AM builds parts layer by layer directly from digital designs using specialized metal powders. This process unlocks unprecedented design freedom, enabling the creation of highly complex, topology-optimized, and lightweight structures that were previously impossible or prohibitively expensive to manufacture.
Pour satellite camera housings, metal AM presents a compelling value proposition. It allows engineers to:
- Dramatically reduce weight: By incorporating complex internal lattice structures and optimizing material placement only where structurally needed.
- Integrate functionality: Combining multiple components into a single printed part, reducing assembly complexity, potential failure points, and overall mass.
- Optimize thermal management: Designing intricate internal cooling channels or features to dissipate heat generated by camera electronics, crucial for maintaining optical stability.
- Accelerate development cycles: Rapidly iterating designs and producing prototypes or final parts much faster than traditional methods allow.
- Utilize advanced materials: Employing high-performance alloys specifically designed for the rigors of space, such as high-strength aluminum alloys like Scalmalloy® or space-proven titanium alloys like Ti-6Al-4V.
The shift towards AM for critical space exploration technology like camera housings is not merely about adopting a novel manufacturing technique; it’s about enhancing satellite performance, capability, and mission longevity. Companies specializing in fabrication de précision for aerospace are increasingly leveraging AM to meet the stringent demands of the sector. As a leader in metal additive manufacturing solutions, Met3dp provides both the advanced printing systems and high-quality metal powders necessary to produce these mission-critical components. Our expertise in technologies like Selective Electron Beam Melting (SEBM) and gas atomized powders ensures the reliability and performance required for the most demanding aerospace applications. Explore Met3dp’s comprehensive metal 3D printing services to understand how we empower aerospace innovation.
This article delves into the specifics of using metal 3D printing for satellite camera housings, covering applications, material choices, design considerations, quality assurance, and supplier selection, providing engineers and procurement managers with the insights needed to leverage this powerful technology.
Applications & Demands: Where are 3D Printed Satellite Camera Housings Utilized?
The utility of satellites spans a vast range of applications, each placing unique demands on its components, including the camera housings. Metal 3D printing is proving instrumental in meeting these diverse requirements across various satellite types and missions. Procurement managers and engineers sourcing satellite component suppliers are increasingly turning to AM providers capable of delivering parts for these critical systems.
Principaux domaines d'application :
- Earth Observation (EO) Satellites:
- Fonction : These satellites monitor our planet’s surface, capturing data for weather forecasting, climate change monitoring, agricultural management, urban planning, disaster response, and environmental studies.
- Housing Requirements: High stability is paramount to ensure precise imaging geometry. Housings must maintain optical alignment despite thermal fluctuations and micro-vibrations. Lightweighting is critical for constellations (large numbers of smaller satellites). Materials need good thermal conductivity and low coefficient of thermal expansion (CTE). AM allows for integrated thermal straps or channels and complex mounting features for sensors and electronics within a lightweight, stiff structure.
- B2B Relevance: Suppliers offering AM solutions for Earth observation satellites need to demonstrate capabilities in producing dimensionally stable, lightweight structures with integrated thermal features using materials like Ti-6Al-4V or specialized aluminum alloys.
- Communication Satellites:
- Fonction : Relaying communication signals (television, internet, radio, telephony) across vast distances, often from geostationary orbits.
- Housing Requirements: While the primary payload is transponders, cameras are used for deployment monitoring, station-keeping verification, and potentially optical communication links. Housings need extreme reliability for long mission durations (15+ years), radiation shielding, and thermal stability. Part consolidation through AM can reduce assembly complexity and potential outgassing points.
- B2B Relevance: Manufacturers require communication satellite components with proven long-term reliability. AM providers must demonstrate robust quality control, material traceability, and experience with space-grade materials suitable for extended missions.
- Space Telescopes & Scientific Missions:
- Fonction : Observing distant stars, galaxies, planets, and cosmic phenomena (e.g., Hubble, James Webb Space Telescope) or conducting specific scientific experiments in orbit.
- Housing Requirements: These represent the pinnacle of precision. Housings for instruments on space telescopes demand exceptional dimensional stability ($\mu$m level), ultra-low CTE, minimal outgassing, and often cryogenic temperature compatibility. Complex baffling features to control stray light are often needed, which are ideally suited for AM. Lightweighting is crucial due to high launch costs for these flagship missions.
- B2B Relevance: Suppliers for scientific missions must offer state-of-the-art precision AM, potentially including specialized materials (like TiAl or TiNbZr offered by Met3dp) and meticulous post-processing and inspection capabilities. Collaboration between instrument scientists and the satellite component supplier est essentiel.
- Reconnaissance & Surveillance Satellites:
- Fonction : Gathering intelligence for military or security purposes.
- Housing Requirements: High resolution imaging demands extreme stability and pointing accuracy. Rapid deployment and potentially maneuverability favor lightweight designs. Housings may require specific structural characteristics to withstand demanding operational environments. Fast iteration using AM allows for rapid updates to sensor packages.
- B2B Relevance: Achats dans le secteur aérospatial for defense applications often involves strict security protocols and requires suppliers with robust quality management systems and potentially specific certifications. The ability to rapidly prototype and produce tailored designs via AM is a significant advantage.
- Navigation Satellites (e.g., GPS, Galileo):
- Fonction : Providing positioning, navigation, and timing (PNT) signals globally.
- Housing Requirements: While primary payloads are atomic clocks and signal generators, monitoring cameras might be included. Housings require high reliability and longevity within the constellation architecture.
- B2B Relevance: Cost-effective production for constellations is important. AM can offer advantages if designs allow for significant lightweighting or part consolidation across numerous satellites.
Common Demands Across Applications:
Regardless of the specific mission, several demands are universal for satellite camera housings, driving the adoption of metal AM:
- Mass Reduction: Launch costs are often estimated in tens of thousands of dollars per kilogram. Reducing housing mass directly saves costs or allows for more fuel/payload.
- Structural Integrity: Housings must survive the intense vibrations and acoustic loads during launch and maintain structural integrity throughout the mission.
- Stabilité thermique : Temperature fluctuations in orbit can cause expansion or contraction, misaligning sensitive optics. Housings need appropriate CTE and often integrated thermal management features.
- Vacuum Compatibility: Materials must exhibit low outgassing properties to avoid contaminating sensitive optical surfaces or electronics.
- Radiation Hardness: Components must withstand the space radiation environment without degradation.
- Reliability & Longevity: Satellites are typically designed for long operational lifetimes without the possibility of repair.
Metal 3D printing, particularly with advanced materials like Scalmalloy® and Ti-6Al-4V processed by expert providers like Met3dp using optimized equipment, directly addresses these demanding requirements, making it an increasingly indispensable tool for manufacturing next-generation satellite imaging systems.
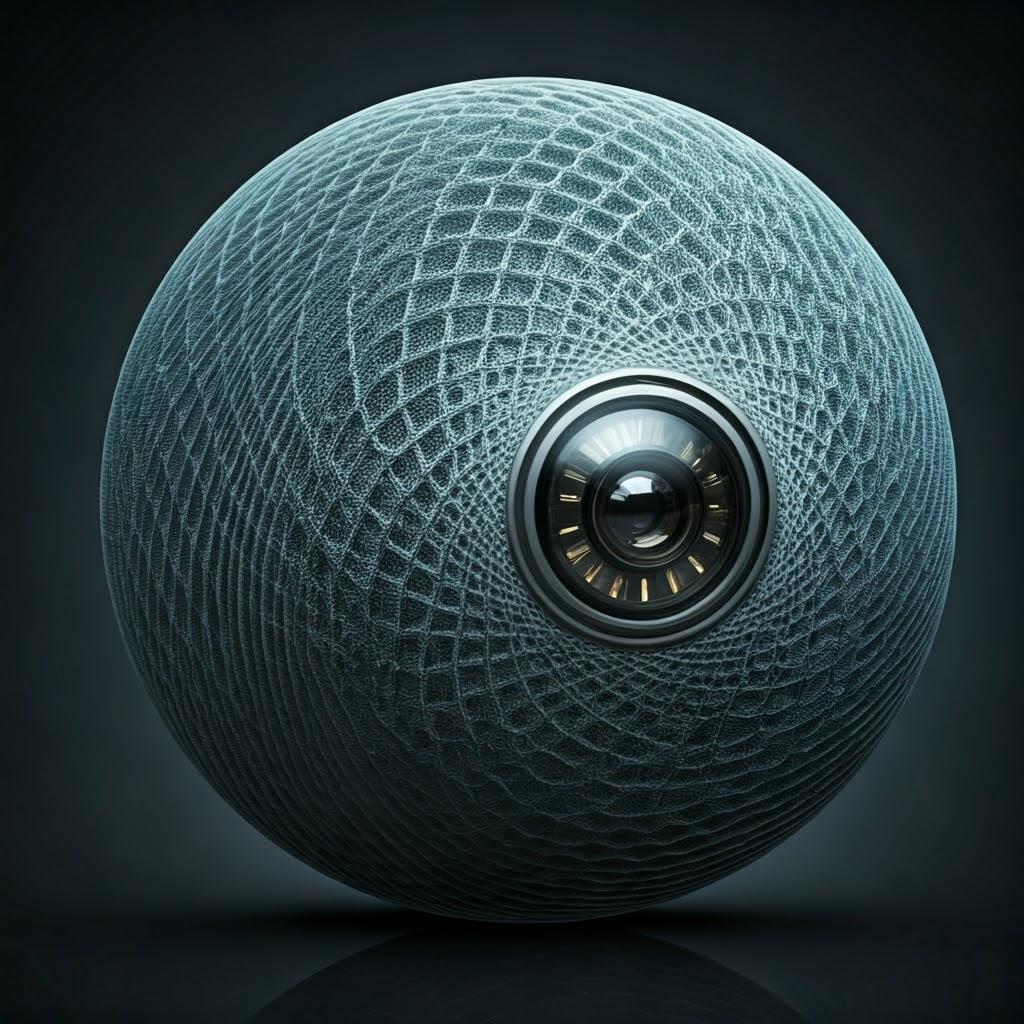
Why Choose Metal 3D Printing for Satellite Camera Housings? Unlocking Performance Gains
The decision to move from traditional manufacturing methods, like CNC machining, to metal additive manufacturing for satellite camera housings is driven by a compelling set of advantages that directly translate to enhanced performance, reduced costs, and accelerated timelines in the demanding aerospace sector. While CNC machining remains a vital technology, particularly for achieving final tolerances on critical surfaces, AM offers unique capabilities for the initial part geometry creation, especially for complex components like camera housings. Let’s compare additive manufacturing vs CNC and highlight the specific benefits of AM:
Comparison: Metal AM vs. Traditional Machining for Satellite Camera Housings
Fonctionnalité | Metal Additive Manufacturing (e.g., LPBF/SEBM) | Usinage CNC traditionnel | Advantage for AM Housings |
---|---|---|---|
Liberté de conception | High: Enables complex internal/external geometries, lattices, topology optimization. | Moderate: Limited by tool access, fixturing, and material block shape. | Major: Allows for highly optimized, lightweight designs with integrated features (e.g., cooling channels, mounting). |
Allègement | Excellent: Material placed only where needed. Topology optimization and lattice structures easily integrated. | Limited: Often constrained by subtractive nature; internal pockets difficult/impossible. | Major: Significant mass reduction possible, lowering launch costs and improving satellite agility. |
Consolidation partielle | High: Multiple components can often be combined into a single printed part. | Low: Requires assembly of multiple machined parts. | Significant: Reduces fastener count, assembly time, potential failure points, and overall mass. |
Déchets matériels | Low: Uses only the material needed for the part and supports (powder is recyclable). | High: Significant material (swarf) removed from initial billet. | Significant: More sustainable and cost-effective, especially with expensive aerospace alloys like titanium. |
Lead Time (Complex Parts) | Potentially Faster: Especially for highly complex, one-off, or low-volume parts. Rapid prototyping. | Potentially Slower: Requires complex programming, multiple setups, specialized tooling. | Significant: Accelerates development cycles and enables faster deployment of new satellite capabilities. |
Coûts d'outillage | None: Direct digital manufacturing. | Required: Fixtures, specialized cutting tools. | Significant: Eliminates tooling costs and lead times, beneficial for custom or low-volume production. |
Gestion thermique | High Integration: Complex internal cooling channels or heat sinks can be designed directly into the part. | Limited Integration: Channels often require drilling, brazing, or assembly. | Major: Enables superior thermal control for sensitive optics and electronics within a compact design. |
Options de matériaux | Growing range of specialized AM powders (e.g., Scalmalloy®, Ti-6Al-4V, custom alloys). | Wide range of well-established machinable metals. | Comparable/Advantageous: Access to high-performance AM-specific alloys optimized for strength-to-weight. |
Surface Finish (As-Built) | Rougher: Typically requires post-processing for smooth or critical surfaces. | Smoother: Can achieve fine finishes directly. | Disadvantage (Requires Post-Processing): AM parts need secondary finishing for optical mounts, seals etc. |
Tolerances (As-Built) | Less Precise: Requires post-machining for tight tolerances. | More Precise: Capable of achieving tight tolerances directly. | Disadvantage (Requires Post-Processing): Critical dimensions usually require final machining after printing. |
Exporter vers les feuilles
Key Advantages of Metal AM for Housings Summarized:
- Unmatched Lightweighting: This is arguably the most significant driver for AM in aerospace. Techniques like topology optimization (using software to remove material from non-critical areas while maintaining structural integrity) and the incorporation of internal lattice structures can reduce housing weight by 30-60% or even more compared to traditionally machined counterparts. This directly impacts launch cost and satellite maneuverability.
- Complex Geometry & Part Consolidation: Satellite camera housings often require intricate internal features for mounting optics, electronics, sensors, and baffling to control stray light. They also need complex external shapes for mounting to the satellite structure and interfacing with other components. AM excels at producing these geometries in a single piece. Consolidating, for example, a housing body, mounting brackets, and thermal straps into one printed part drastically simplifies assembly, reduces part count, minimizes potential leak paths or failure points (like fasteners), and further contributes to weight reduction.
- Optimized Thermal Management: Maintaining the precise operating temperature of satellite cameras is crucial for image quality and sensor longevity. AM allows designers to embed conformal cooling channels directly within the housing walls, following the contours of heat-generating components. These channels can be designed with complex internal structures (like turbulators) to enhance heat transfer efficiency far beyond what’s possible with simple drilled holes in a machined block. This integration leads to more effective and compact thermal management solutions for satellites.
- Accelerated Development & Prototyping: Need to test a new camera configuration or mounting interface? AM allows engineers to go from a digital design to a physical metal prototype in days or weeks, compared to potentially months for traditional methods involving tooling and complex machining setups. This rapid iteration capability significantly speeds up the development and qualification process for new satellite imaging systems.
- Efficacité matérielle : Especially when using expensive aerospace-grade materials like titanium alloys or specialized aluminum like Scalmalloy®, the subtractive nature of CNC machining generates substantial costly waste. AM uses powder bed fusion, where unfused powder can be recycled and reused, leading to much higher material utilization rates and reduced raw material costs, a key consideration for aerospace procurement.
- Résilience de la chaîne d'approvisionnement : Additive manufacturing allows for decentralized production. A housing designed in one location can be printed by a qualified AM service provider, like Met3dp, closer to the point of integration, potentially simplifying logistics and reducing supply chain risks.
While post-processing steps like heat treatment, HIP (Hot Isostatic Pressing), support removal, and final machining of critical interfaces are necessary to achieve the required properties and tolerances, the fundamental advantages offered by AM in creating the near-net shape part make it a transformative technology for producing high-performance satellite camera housings. Companies like Met3dp, with their advanced powder manufacturing and printing capabilities, are key enablers in realizing these benefits of metal AM for the aerospace industry.
Material Focus: Scalmalloy® and Ti-6Al-4V for Space-Grade Performance
The choice of material is paramount for any aerospace component, especially one as critical as a satellite camera housing operating in the harsh environment of space. The material must provide the right combination of strength, stiffness, low density, thermal stability, and processability via additive manufacturing. Two materials stand out for this application: Scalmalloy® and Ti-6Al-4V. As a leading fournisseur de poudre métallique with advanced gas atomization and PREP technology, Met3dp understands the critical link between powder quality and final part performance, offering high-quality powders suitable for demanding applications.
1. Scalmalloy® (Al-Mg-Sc-Zr Alloy): The High-Performance Aluminum
Scalmalloy® is a patented high-strength aluminum alloy specifically designed for additive manufacturing. Developed by APWORKS (an Airbus subsidiary), it has rapidly gained traction in aerospace due to its exceptional properties compared to traditional cast or wrought aluminum alloys.
- Key Properties & Advantages for Satellite Housings:
- Rapport force/poids exceptionnel : Scalmalloy® offers specific strength comparable to, or even exceeding, that of some titanium alloys, but at a much lower density (approx. 2.67 g/cm³ vs. ~4.43 g/cm³ for Ti-6Al-4V). This makes it ideal for aggressive lightweighting strategies.
- High Ductility & Toughness: Unlike many other high-strength aluminum alloys, Scalmalloy® retains good ductility and toughness, making it more resistant to fracture, which is crucial for components experiencing launch vibrations.
- Excellent Processability via AM: It was designed specifically for Laser Powder Bed Fusion (LPBF), exhibiting good weldability and allowing for the creation of fine features and complex geometries.
- Bonne résistance à la corrosion : Offers adequate resistance for typical aerospace applications.
- Propriétés thermiques : Possesses good thermal conductivity, beneficial for dissipating heat from camera electronics.
- Considérations :
- Coût : Typically more expensive than standard aluminum alloys and sometimes even Ti-6Al-4V powder.
- Lower High-Temperature Strength: Compared to titanium, its strength diminishes more significantly at elevated temperatures (though generally sufficient for most satellite operating ranges).
- CTE: Higher Coefficient of Thermal Expansion than titanium, which needs careful consideration for optical stability if significant temperature gradients are expected across the housing.
- Why Use Scalmalloy® for Housings? It’s the go-to choice when maximum lightweighting is the primary driver, combined with the need for high strength and stiffness. Its excellent AM processability allows designers to fully leverage topology optimization and lattice structures. Ideal for Earth observation constellations, agile satellites, and applications where minimizing mass is paramount.
2. Ti-6Al-4V (Grade 5 Titanium): The Proven Workhorse
Ti-6Al-4V (Titanium-6% Aluminum-4% Vanadium) is the most widely used titanium alloy, with decades of proven performance in demanding aerospace, medical, and industrial applications. Its transition into additive manufacturing has been highly successful.
- Key Properties & Advantages for Satellite Housings:
- Excellent rapport résistance/poids : While denser than Scalmalloy®, Ti-6Al-4V still offers a very competitive strength-to-weight ratio, significantly better than steels or nickel alloys.
- High Strength & Fatigue Resistance: Maintains good strength at moderately elevated temperatures (up to ~300-400°C) and exhibits excellent fatigue life, important for launch survival and long mission durations.
- Superb Corrosion Resistance: Highly resistant to corrosion in various environments, including residual atmospheric traces or potential propellant exposure.
- Low Coefficient of Thermal Expansion (CTE): Significantly lower CTE than aluminum alloys. This is a major advantage for optical instrument housings, as it minimizes dimensional changes with temperature fluctuations, helping to maintain precise alignment.
- Biocompatibilité : While not relevant for camera housings, its biocompatibility highlights its inert nature.
- Well-Understood AM Processing: Extensive research and established process parameters exist for printing Ti-6Al-4V via LPBF and EBM (Electron Beam Melting). Met3dp’s expertise extends to processing titanium alloys effectively.
- Considérations :
- Higher Density: Compared to Scalmalloy®.
- Lower Thermal Conductivity: Compared to aluminum alloys, which might require more sophisticated thermal management design if heat dissipation is a primary concern.
- Réactivité : Titanium can be reactive at high temperatures during processing, requiring careful atmosphere control (inert gas or vacuum).
- Why Use Ti-6Al-4V for Housings? It’s the preferred choice when thermal stability (low CTE) is critical for optical alignment, when operating temperatures might be slightly higher, or when leveraging existing extensive aerospace qualification data for titanium is advantageous. It remains an excellent option for achieving significant lightweighting compared to traditional designs and offers superior corrosion resistance. Ideal for high-precision optical payloads, space telescopes, and long-duration missions.
Material Property Comparison (Typical Values for AM):
Propriété | Scalmalloy® (traité thermiquement) | Ti-6Al-4V (Heat Treated/HIPed) | Unité | Importance for Housings |
---|---|---|---|---|
Densité | ~2.67 | ~4.43 | g/cm³ | Lower is better for lightweighting. |
Résistance ultime à la traction (UTS) | ~520 – 580 | ~950 – 1150 | MPa | Higher indicates greater load-bearing capacity. |
Yield Strength (YS) | ~480 – 540 | ~850 – 1050 | MPa | Stress at which permanent deformation begins. |
Module d'élasticité | ~70 – 75 | ~110 – 120 | GPa | Material stiffness; higher resists deflection. |
Allongement à la rupture | ~8 – 16 | ~10 – 18 | % | Ductility; higher indicates less brittle behavior. |
Specific Strength (UTS/Density) | ~195 – 217 | ~214 – 260 | MPa/(g/cm³) | Strength relative to weight. Higher is better. |
Specific Stiffness (E/Density) | ~26 – 28 | ~25 – 27 | GPa/(g/cm³) | Stiffness relative to weight. Higher is better. |
Conductivité thermique | ~110 – 130 | ~7 – 8 | W/(m-K) | Ability to conduct heat. Higher aids dissipation. |
Coeff. of Thermal Expansion (CTE) | ~21 – 23 | ~8.5 – 9.5 | µm/(m·K) | Dimensional change with temperature. Lower is better for stability. |
Exporter vers les feuilles
(Note: Exact properties depend heavily on AM process parameters, build orientation, heat treatment, and testing conditions. These are representative values.)
Choosing the Right Material & Supplier:
The selection between Scalmalloy® 3D printing et Ti-6Al-4V aerospace applications depends on a careful analysis of the specific mission requirements:
- Prioritize maximum weight saving? Scalmalloy® is likely superior.
- Prioritize thermal stability (low CTE) for optical alignment? Ti-6Al-4V is often preferred.
- Besoin higher temperature performance? Ti-6Al-4V has the edge.
- Need efficient dissipation de la chaleur? Scalmalloy® has better thermal conductivity.
Working with an experienced additive manufacturing provider like Met3dp is crucial. Met3dp not only manufactures high-quality Met3dp powders like Ti-6Al-4V using advanced atomization techniques but also possesses the expertise in process optimization for various materials on their industry-leading printing equipment. This ensures that the chosen material achieves its maximum potential performance in the final printed housing, meeting the stringent demands of space applications. Their comprehensive approach, from powder production to final part qualification, provides the reliability needed for mission-critical titanium satellite components and advanced aluminum parts. Sources and related content
Design for Additive Manufacturing (DfAM): Optimizing Satellite Camera Housings
Simply recreating a design intended for CNC machining using additive manufacturing rarely unlocks the full potential of the technology. To truly leverage the benefits of metal 3D printing – particularly lightweighting, part consolidation, and enhanced thermal performance – engineers must embrace Conception pour la fabrication additive (DfAM) principles right from the conceptual stage. DfAM is not just a set of rules but a mindset shift, focusing on function-driven design optimized for the layer-by-layer building process. For satellite camera housings, applying DfAM is critical to achieving mission objectives and maximizing performance gains.
Key DfAM Principles for Satellite Camera Housings:
- Optimisation de la topologie :
- What it is: Using specialized software (e.g., Altair Inspire, ANSYS Discovery, nTopology) to algorithmically remove material from a design space based on applied loads, constraints, and performance targets (like stiffness or natural frequency). The software essentially “carves away” unnecessary material, leaving behind an organic, load-bearing structure.
- Why it matters for housings: This is the primary tool for achieving significant lightweighting in satellite parts. Camera housings often have complex load paths (launch vibrations, mounting points) and stiffness requirements (maintaining optical alignment). Topology optimization ensures material is placed precisely where needed to meet these demands, resulting in highly efficient, often bio-inspired structures that can be significantly lighter (30-60%+) than conventionally designed counterparts.
- Considérations : Optimized shapes can be complex and non-intuitive, requiring careful validation through FEA (Finite Element Analysis). Manufacturing constraints (minimum feature size, overhang angles) must be incorporated into the optimization setup.
- Lattice Structures & Infill:
- What they are: Replacing solid volumes within a part with internal lattice structures (e.g., cubic, octet-truss, gyroid) or variable density infill. These structures are composed of interconnected beams or surfaces.
- Why they matter for housings: Lattices offer an excellent stiffness-to-weight ratio, further contributing to mass reduction beyond topology optimization of the main load paths. They can also be designed to absorb energy (vibration damping), enhance thermal dissipation (increased surface area), or allow for powder removal from internal cavities. Different lattice types offer varying properties (e.g., stiffness bias, energy absorption).
- Considérations : Requires specialized software for generation and analysis. Manufacturability (minimum strut diameter, node connections, powder removal) is crucial. Ensuring complete powder removal from complex internal lattices can be challenging and requires careful design and post-processing planning.
- Consolidation partielle :
- What it is: Redesigning an assembly of multiple components to be printed as a single, monolithic part.
- Why it matters for housings: Camera housings often interface with brackets, thermal straps, optical mounts, and electronic enclosures. AM allows designers to integrate many of these features directly into the housing structure. This eliminates fasteners (reducing weight, failure points, assembly time), improves structural integrity, potentially reduces leak paths, and simplifies the supply chain.
- Considérations : Increases the complexity of the single part. Repairability might be reduced (though often not feasible in space anyway). Requires careful consideration of tolerances at integrated interfaces.
- Feature Integration for Functionality:
- What it is: Designing functional features directly into the part geometry, such as conformal cooling channels, integrated waveguides, embedded sensor mounts, or complex baffling for stray light control.
- Why it matters for housings: Pour thermal management in satellites, AM enables the creation of highly efficient conformal cooling channels that follow the exact shape of heat-generating components (like the camera sensor or processing electronics), far surpassing the efficiency of simple drilled passages. Complex internal baffles, crucial for high-contrast imaging, can be printed with intricate geometries impossible to machine.
- Considérations : Requires careful CFD (Computational Fluid Dynamics) analysis for cooling channels. Internal features necessitate robust powder removal strategies.
- Designing for Support Minimization:
- What they are: Temporary structures printed alongside the main part to support overhanging features (typically surfaces angled less than 45 degrees from the horizontal build plate) and anchor the part during printing.
- Why it matters: Supports consume extra material and time, require removal in post-processing (which can damage surfaces or be difficult in internal areas), and can affect surface finish. DfAM encourages designing parts with self-supporting angles (>= 45 degrees) where possible, orienting the part strategically on the build plate, and using chamfers or fillets instead of sharp horizontal overhangs.
- Considérations : Complete elimination of supports is often impossible for complex geometries. Designing for minimal et accessible supports is key. Support strategy heavily influences residual stress and potential distortion.
- Orientation Strategy:
- What it is: Deciding how the part will be positioned and oriented on the AM machine’s build plate.
- Why it matters: Orientation impacts:
- Structures de soutien : Where supports are needed.
- Finition de la surface : Up-facing, down-facing, and vertical surfaces have different roughness characteristics.
- Précision dimensionnelle : Anisotropy (direction-dependent properties) can affect accuracy.
- Temps de construction : Taller builds generally take longer.
- Contrainte résiduelle : Orientation influences thermal gradients during the build.
- Post-traitement : Affects accessibility for support removal and machining.
- Considérations : Often involves trade-offs. Critical features might dictate orientation (e.g., orienting a critical bore vertically for better roundness). Collaboration with the AM service provider (like Met3dp) is crucial for determining the optimal orientation.
- Wall Thickness and Feature Size:
- What it is: Defining appropriate minimum and maximum wall thicknesses and feature sizes based on the chosen AM process and material.
- Why it matters: Thin walls might warp or not resolve properly; overly thick sections can accumulate residual stress. Minimum hole diameters and feature sizes are limited by the laser/electron beam spot size and powder characteristics.
- Considérations : Consult the AM provider’s design guidelines. Typical minimum wall thicknesses for LPBF/SEBM might be around 0.4-0.8 mm, but this varies.
- Designing for Powder Removal:
- What it is: Ensuring that unfused metal powder trapped within internal channels, cavities, or lattice structures can be easily removed after printing.
- Why it matters: Trapped powder adds weight, can interfere with functionality (e.g., blocking cooling channels), and may pose contamination risks.
- Considérations : Design escape holes/ports at strategic locations. Avoid complex, dead-end internal passages. Use smooth internal transitions. Consider lattice types known for better powder drain-out.
By applying these DfAM aérospatiale principles, engineers can transform a standard satellite camera housing into a highly optimized, lightweight, and functionally superior component. Tools like conception générative et topology optimization for satellites are becoming standard practice, enabled by the capabilities of advanced satellite housing design guidelines tailored for AM. This requires a collaborative approach between the design engineers and the AM experts, such as the team at Met3dp, who understand the nuances of the printing process and material behavior.
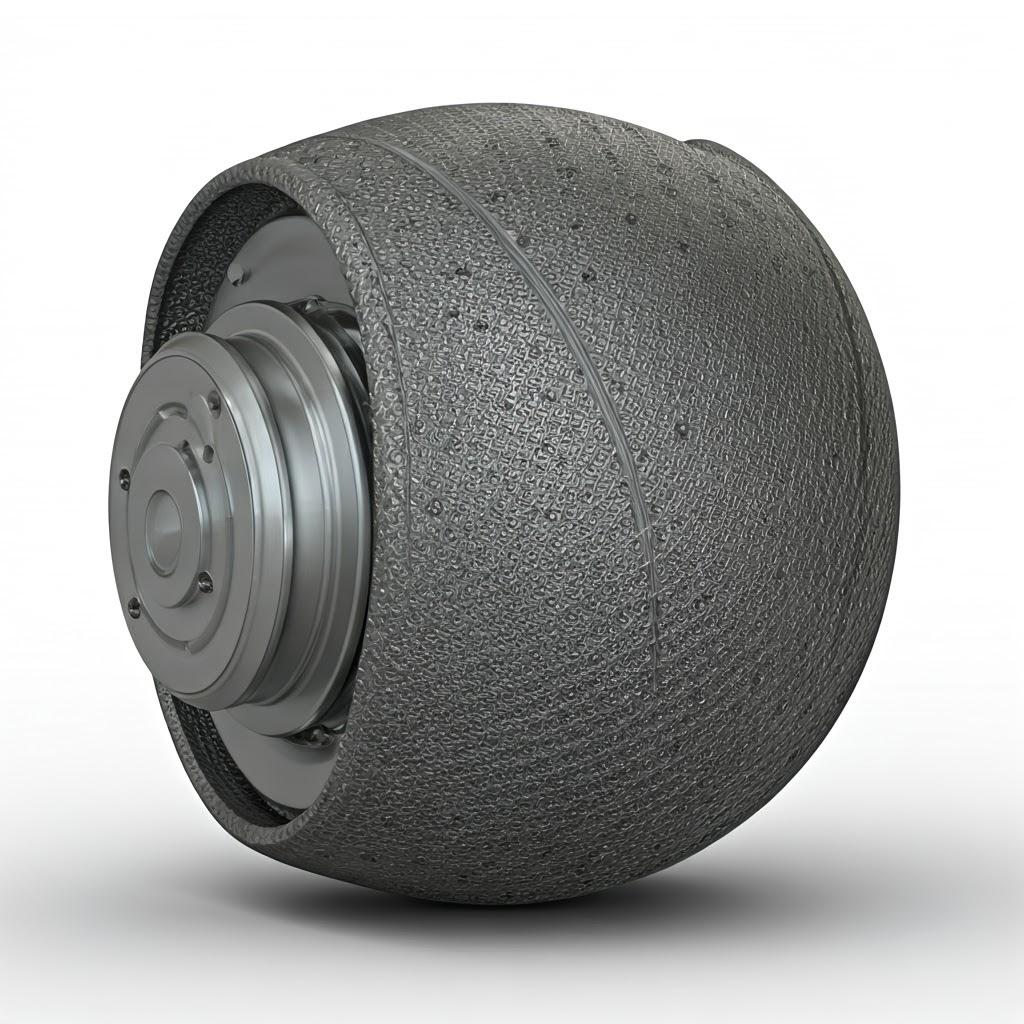
Achieving Mission Success: Tolerance, Surface Finish, and Dimensional Accuracy in AM Housings
While metal additive manufacturing unlocks incredible design freedom, achieving the stringent precision required for satellite camera housings necessitates a clear understanding of the achievable tolerances, surface finishes, and overall dimensional accuracy. These factors are critical for ensuring proper optical alignment, sealing, interfacing with other components, and ultimately, mission success. Unlike CNC machining, where tolerances are primarily dictated by the machine tool and cutting strategy, AM involves complex thermal processes that influence the final part’s dimensional characteristics.
Understanding As-Built vs. Post-Processed States:
It’s crucial to differentiate between the part characteristics directly after printing (‘as-built’) and after necessary post-processing steps (like heat treatment and machining).
- As-Built: Parts directly off the AM machine typically have:
- Looser Tolerances: Influenced by factors like thermal shrinkage, warping, layer resolution, and support structure interaction. General tolerances might be in the range of ±0.1 mm to ±0.5 mm or +/- 0.2% of dimension, depending on size, geometry, material, and process control.
- Rougher Surface Finish: Characterized by partially melted powder particles and layer lines. Ra (average roughness) values can range from 5 µm to 25 µm or more, depending on orientation and process. Down-facing surfaces (supported) are generally rougher than up-facing or vertical surfaces.
- Post-Processed: Through steps like CNC machining, grinding, or polishing:
- Tighter Tolerances: Critical features (e.g., optical mounts, interface flanges, sealing surfaces) can be machined to achieve tolerances comparable to traditional manufacturing (e.g., ISO 2768-m/f or tighter, potentially down to microns for specific features).
- Amélioration de l'état de surface : Machining, polishing, or other surface treatments can achieve very smooth finishes (Ra < 1 µm or even lower) required for sealing, optical interfaces, or specific thermal/optical coatings.
Key Considerations for Housings:
- Tolerances:
- Tolérances générales : For non-critical features, the as-built tolerances of AM might be sufficient. Define these realistically on drawings (e.g., using general tolerance standards like ISO 2768-c/v for as-built).
- Critical Tolerances: Features essential for optical alignment (e.g., lens/sensor mounting seats, alignment pins/holes), mating flanges, and dynamic seals usually require post-machining. Specify these tight tolerances only where necessary to control costs.
- Geometric Dimensioning and Tolerancing (GD&T): Essential for defining complex tolerance requirements (e.g., flatness of mounting surfaces, perpendicularity, coaxiality of bores) unambiguously. Crucial for ensuring proper assembly and alignment.
- Finition de la surface (rugosité) :
- As-Built Surfaces: Acceptable for internal, non-functional surfaces or where roughness aids thermal emissivity (though this needs characterization).
- Down-Facing Surfaces: Tend to be the roughest due to support contact points. Avoid locating critical surfaces here if possible, or plan for significant machining allowance.
- Up-Facing & Vertical Surfaces: Generally smoother than down-facing but still rougher than machined surfaces.
- Required Finishes: Specify required Ra values for sealing surfaces, optical interfaces, and areas receiving specific coatings. These almost always require post-processing.
Surface Roughness Expectations (Typical Ra values for LPBF):
Surface Orientation | Typical As-Built Ra (µm) | Notes |
---|---|---|
Horizontal Up-Facing (Top) | 8 – 15 | Relatively smooth, defined by layer thickness & melt pool. |
Vertical Walls | 10 – 20 | Shows layer lines, influenced by contour scanning. |
Sloped Up-Facing (>45°) | 8 – 18 | Stair-stepping effect visible. |
Sloped Down-Facing (<45°) | 15 – 30+ | Requires support, surface marred by support contact points. |
Horizontal Down-Facing (Bottom) | 20 – 35+ | Fully supported, generally roughest surface. |
Exporter vers les feuilles
(Note: Values are indicative and depend heavily on material, machine, parameters, and layer thickness. SEBM often produces slightly rougher surfaces than LPBF).
- Dimensional Accuracy & Verification:
- Controlling Accuracy: Achieving good as-built accuracy relies on optimized process parameters, robust support strategies, controlled thermal management during the build, and high-quality, reliable AM systems like those used by Met3dp.
- Verification Methods: Garantir dimensional accuracy for satellite parts requires rigorous inspection:
- Machines à mesurer tridimensionnelles (MMT) : For precise measurement of critical features, tolerances, and GD&T callouts, typically after post-machining.
- 3D Scanning (Laser or Structured Light): Provides a full-field comparison of the printed part against the original CAD model, useful for verifying complex geometries and overall form accuracy, often used on as-built parts.
- Tomodensitométrie (CT) : For non-destructive internal inspection, verifying internal channel integrity, detecting internal defects (porosity), and measuring internal features that are otherwise inaccessible.
- Met3dp’s Commitment: Achieving industry-leading accuracy and reliability is a cornerstone of Met3dp’s approach. Their focus on advanced méthodes d'impression 3D en métal and stringent process control contributes significantly to producing parts that meet the demanding geometrical requirements of aerospace components.
Ultimately, a hybrid approach is standard practice for high-precision AM components like satellite camera housings. AM is used to create the complex near-net shape with optimized geometry and internal features, while targeted post-machining and finishing achieve the final critical tolerances and surface finishes. Careful planning during the design phase, accounting for machining allowances and inspection requirements, is essential for mission success.
Beyond the Print: Essential Post-Processing for Satellite Camera Housings
The journey of a metal 3D printed satellite camera housing doesn’t end when the printing process finishes. A series of crucial post-processing steps are required to transform the as-built component into a mission-ready part, ensuring it possesses the necessary mechanical properties, dimensional accuracy, surface characteristics, and overall integrity demanded by the aerospace industry. Neglecting or improperly executing these steps can compromise the entire component. For procurement managers and engineers, understanding these requirements is vital when evaluating AM service providers.
Standard Post-Processing Workflow for AM Aerospace Components:
- Stress Relief (Thermal):
- Why: The rapid heating and cooling cycles inherent in powder bed fusion processes (LPBF/SEBM) create significant internal residual stresses within the printed part. These stresses can cause distortion or cracking during removal from the build plate or later in the part’s life.
- How: Parts are typically heat-treated while still attached to the build plate in a controlled atmosphere furnace (inert gas like argon, or vacuum). The specific temperature and duration depend on the material (e.g., ~300-650°C for Ti-6Al-4V, lower for Scalmalloy®) and geometry but are sufficient to relax internal stresses without significantly altering the microstructure (this is not a full heat treatment).
- Importance: Absolutely critical first step before any mechanical removal.
- Retrait de la pièce de la plaque de construction :
- Why: The part is metallurgically bonded to the metal build plate during printing.
- How: Typically done using Wire Electrical Discharge Machining (Wire EDM) or sometimes a bandsaw. Wire EDM is precise and induces minimal stress.
- Importance: Careful removal prevents damage to the part.
- Retrait de la structure de soutien :
- Why: The temporary support structures needed during printing must be removed.
- How: Can involve manual breaking/cutting (for easily accessible supports), CNC machining, or specialized tools. Access to internal supports can be challenging and must be planned during DfAM.
- Importance: Thorough removal is necessary for functionality, weight targets, and aesthetics. Incomplete removal can trap powder or act as stress concentrators. This step often requires significant manual labor and skill.
- Heat Treatment (Solution Annealing, Aging, HIP):
- Why: To optimize mechanical properties (strength, ductility, fatigue life), relieve residual stresses further, and achieve near-full density. As-built AM materials often have fine-grained, non-equilibrium microstructures.
- How:
- Solution Annealing & Aging: Standard heat treatments used to modify the microstructure and precipitation phases, tailoring properties (e.g., for Ti-6Al-4V or Scalmalloy® to achieve specific strength/ductility targets). Performed in vacuum or inert atmosphere furnaces.
- Pressage isostatique à chaud (HIP) : A crucial step for many critical pièces pour l'aérospatiale. The component is subjected to high temperature (below melting point) and high isostatic pressure (using an inert gas like Argon) simultaneously. This process effectively closes internal microporosity (e.g., from gas entrapment or lack-of-fusion) leading to near 100% density, significantly improving fatigue life, fracture toughness, and property consistency.
- Importance: Essential for achieving the required mechanical performance and reliability for space applications. HIP metal AM is often a mandatory requirement for fatigue-critical or fracture-critical components.
- CNC Machining / Finishing:
- Why: To achieve tight tolerances on critical features, obtain required surface finishes, and create features not feasible during printing (e.g., very fine threads).
- How: Using standard CNC milling, turning, grinding, or polishing techniques. Requires careful fixturing of the potentially complex AM part geometry. Machining allowances must be included in the DfAM phase.
- Importance: Bridges the gap between AM’s geometric freedom and the precision requirements for interfaces, seals, and optical mounts. CNC machining 3D prints is standard practice.
- Surface Treatment & Cleaning:
- Why: To achieve final surface properties (e.g., roughness, cleanliness, optical/thermal properties) and remove contaminants.
- How: Methods include:
- Décapage par billes / Décapage au sable : Provides a uniform matte finish, removes loose powder, can provide minor peening effect.
- Tambourinage / Finition vibratoire : Smoothes surfaces and deburrs edges using media.
- Polishing / Lapping: For achieving very smooth, mirror-like finishes on critical surfaces.
- Électropolissage : Electrochemical process to smooth and passivate surfaces (common for stainless steels, can work for Ti).
- Anodizing (for Aluminum/Scalmalloy®): Improves corrosion resistance and provides a surface suitable for priming/painting.
- Chemical Cleaning: To remove oils, residues, and ensure cleanliness standards (critical for optical systems to prevent outgassing).
- Revêtement : Application of specialized coatings for thermal control (e.g., white paint, black paint, VDA – Vapor Deposited Aluminum), corrosion protection, or optical filtering.
- Importance: Tailors the housing surface for its specific function within the satellite environment and ensures compatibility with sensitive optical instruments. Surface treatment for satellite components est essentielle.
- Inspection and Quality Assurance:
- Why: To verify that all previous steps have been performed correctly and the part meets all specifications.
- How: Includes dimensional inspection (CMM, scanning), non-destructive testing (NDT) like CT scanning or FPI (Fluorescent Penetrant Inspection) for surface defects, material testing (tensile tests on witness coupons), and final visual inspection.
- Importance: Final gate check before delivery, ensuring quality assurance in aerospace.
The complexity and criticality of these post-processing steps underscore the need to partner with a knowledgeable and well-equipped AM service provider. Companies like Met3dp, with their comprehensive understanding of the entire additive manufacturing workflow from powder to finished part, including necessary secondary operations, provide end-to-end solutions ensuring that components meet the rigorous standards of the aerospace industry.
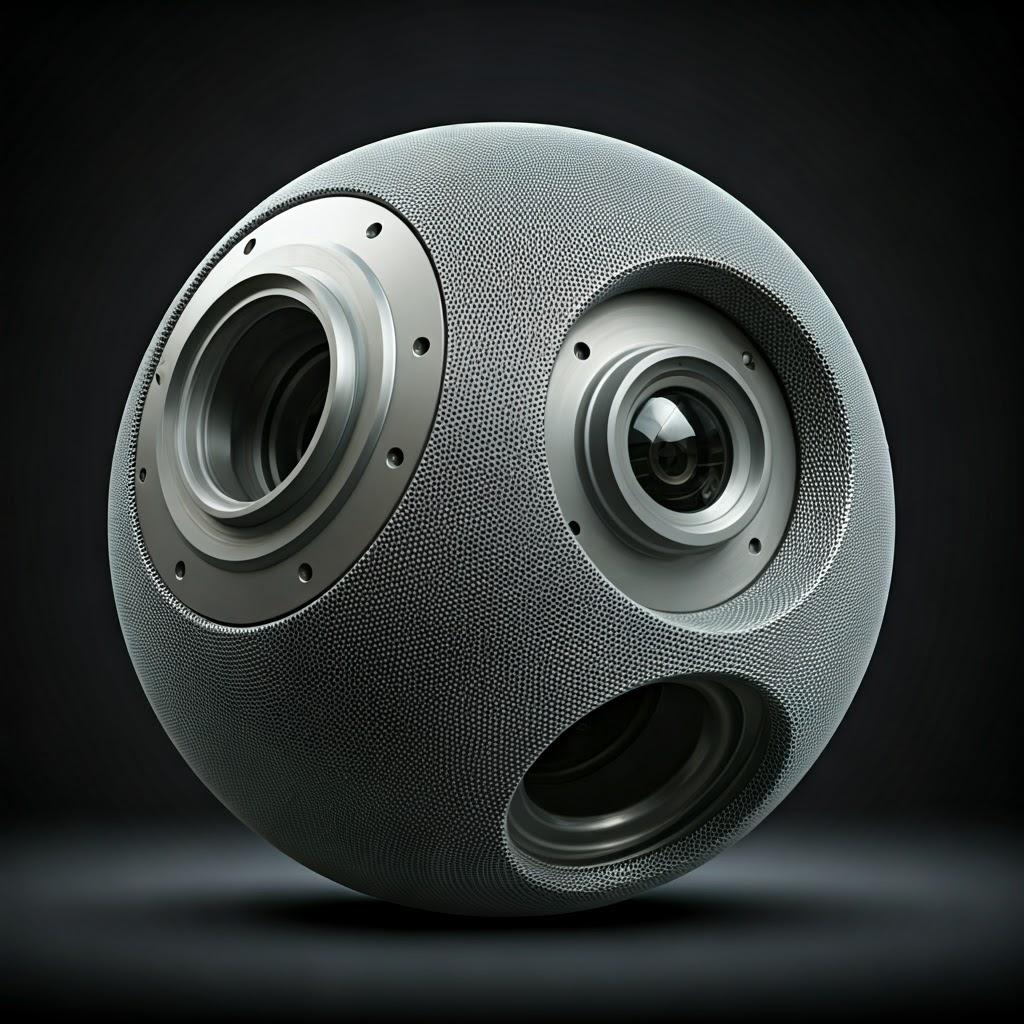
Navigating Challenges: Overcoming Hurdles in 3D Printing Satellite Housings
While metal additive manufacturing offers significant advantages, it’s not without its challenges, particularly when producing complex, high-stakes components like satellite camera housings. Understanding these potential hurdles and the strategies employed by experienced providers like Met3dp to mitigate them is crucial for successful project outcomes. Engineers and procurement managers should be aware of these common issues:
- Contraintes résiduelles et déformation :
- Le défi : The rapid, localized heating and cooling during layer-wise melting and solidification generate significant internal stresses. These stresses can exceed the material’s yield strength, causing the part to warp or distort during the build, upon removal from the build plate, or during post-processing. This is particularly problematic for large, flat structures or parts with varying thicknesses.
- Mitigation Strategies:
- Optimized Build Orientation: Orienting the part to minimize large flat surfaces parallel to the build plate and manage thermal gradients.
- Structures de soutien robustes : Well-designed supports anchor the part securely to the build plate, resisting warping forces and helping to conduct heat away.
- Stratégies d'analyse optimisées : Using specific laser/electron beam scan patterns (e.g., island scanning, sectoring) to distribute heat more evenly and reduce localized stress buildup.
- Optimisation des paramètres du processus : Fine-tuning laser power, scan speed, layer thickness, and pre-heating (especially in EBM) to minimize thermal gradients.
- Thermal Stress Relief: Performing stress relief heat treatment immediately after printing and before part removal is essential.
- Simulation : Using process simulation software to predict stress distribution and potential distortion, allowing for adjustments to orientation and supports before printing.
- Porosité :
- Le défi : Small voids or pores can form within the printed material due to trapped gas (e.g., Argon used in the build chamber) or incomplete melting (lack-of-fusion between layers or scan tracks). Porosity degrades mechanical properties, particularly fatigue strength and fracture toughness, and is unacceptable for critical aerospace components.
- Mitigation Strategies:
- Poudre de haute qualité : Using powder with controlled particle size distribution, high sphericity, good flowability, and low internal gas content (Met3dp’s focus on advanced powder production is key here). Proper powder handling and storage are also vital.
- Paramètres de processus optimisés : Ensuring sufficient energy density (laser/beam power, speed, hatching) to fully melt the powder particles and allow dissolved gases to escape the melt pool.
- Controlled Atmosphere: Maintaining a high-purity inert gas atmosphere (LPBF) or high vacuum (SEBM) to minimize contamination and gas pickup.
- Pressage isostatique à chaud (HIP) : The most effective method for eliminating residual porosity. HIP effectively closes internal voids through high temperature and pressure, leading to near-fully dense parts. Often mandatory for critical applications.
- Surveillance des processus : Using in-situ monitoring tools (melt pool monitoring, thermal imaging) to detect potential anomalies during the build.
- Difficultés liées au retrait de l'aide :
- Le défi : While necessary, support structures must be removed. Accessing and removing supports from complex internal channels, lattice structures, or delicate features can be extremely difficult, time-consuming, and risks damaging the part.
- Mitigation Strategies:
- DfAM for Support Minimization: Designing parts with self-supporting angles, using fillets, and orienting strategically to reduce the need for supports in inaccessible areas.
- Conception optimisée du support : Using support types that are strong enough during the build but easier to remove (e.g., conical supports, thin connection points, specialized lattice supports).
- Soluble Supports (Emerging): Research is ongoing into materials or designs allowing for chemical dissolution of supports, though not yet standard for structural aerospace metals.
- Designing for Access: Ensuring tools or hands can reach internal supports, or designing features that can be machined away later to grant access.
- Techniciens qualifiés : Relying on experienced technicians for careful manual removal.
- Powder Removal from Internal Geometries:
- Le défi : Unfused powder within complex internal channels (like cooling passages or lattice structures) must be completely removed. Trapped powder adds weight and can compromise functionality. Complete removal can be hard to verify.
- Mitigation Strategies:
- DfAM for Powder Flow: Designing channels with sufficient diameter, smooth bends, and escape holes at low points. Avoiding complex, dead-end cavities.
- Orientation optimisée : Orienting the part to facilitate powder drainage during build chamber clean-out.
- Post-Processing Cleaning: Using vibration tables, compressed air jets, ultrasonic cleaning baths, and sometimes micro-abrasive flow to dislodge and flush out trapped powder.
- Inspection : Using borescope inspection or CT scanning to verify complete powder removal from critical internal passages.
- Ensuring Quality, Repeatability, and Traceability:
- Le défi : Guaranteeing that every part produced meets the same stringent quality standards, especially for aerospace applications requiring high reliability and full traceability from raw material to final component.
- Mitigation Strategies:
- Système de gestion de la qualité (SGQ) robuste : Implementing rigorous procedures aligned with aerospace standards (like AS9100, though confirmation needed for specific providers). About Met3dp – Find out more about Met3dp’s commitment to quality and innovation.
- Material Control & Traceability: Strict control over powder batch management, recycling protocols, and maintaining full traceability records.
- Process Monitoring & Control: Utilizing machine sensors, melt pool monitoring, and data logging to track build consistency. Regular machine calibration and maintenance are essential.
- Procédures normalisées : Documenting and adhering to qualified process parameters and post-processing steps.
- Comprehensive Testing & Inspection: Implementing thorough NDT, dimensional inspection, and mechanical testing (using witness coupons printed alongside parts).
Successfully navigating these challenges requires deep expertise in materials science, process physics, DfAM, and quality control. Partnering with a vertically integrated and experienced provider like Met3dp, who controls aspects from powder creation to advanced printing and understands the full process chain, significantly mitigates risks and ensures the production of high-quality, reliable satellite camera housings ready for the demands of space.
Supplier Selection: Choosing the Right Metal Additive Manufacturing Partner for Aerospace
Selecting the right manufacturing partner is always critical, but for mission-critical components like satellite camera housings produced via additive manufacturing, the stakes are exceptionally high. The unique complexities of metal AM, combined with the stringent requirements of the aerospace industry, demand a supplier with specialized expertise, robust processes, and a proven track record. Engineers and procurement managers evaluating potential aerospace AM service providers should consider a comprehensive set of criteria beyond just price.
Key Evaluation Criteria for AM Suppliers:
- Aerospace Experience & Proven Track Record:
- Why it Matters: The aerospace sector has unique demands regarding materials, quality, documentation, and performance under extreme conditions. A supplier familiar with these nuances is better equipped to deliver conforming parts.
- What to Look For: Case studies involving similar components (housings, brackets, optical benches), experience with relevant aerospace materials (Scalmalloy®, Ti-6Al-4V, Inconel), understanding of space environment effects (outgassing, radiation, thermal cycling), and potentially non-disclosure agreements (NDAs) demonstrating work with aerospace primes or subsystem suppliers.
- Quality Management System (QMS) & Certifications:
- Why it Matters: A robust QMS ensures consistency, repeatability, and traceability throughout the manufacturing process. While formal AS9100 certification (specific to Aviation, Space, and Defense) is ideal, a strong commitment to quality evidenced by ISO 9001 certification coupled with rigorous internal aerospace-focused procedures is essential.
- What to Look For: Certification status (AS9100 preferred, ISO 9001 minimum), documented procedures for process control, material handling, traceability, calibration, inspection, and non-conformance management. Evidence of continuous improvement practices. Met3dp, for instance, emphasizes industry-leading quality control from powder production through final part inspection.
- Material Expertise & Control:
- Why it Matters: The quality of the final part is intrinsically linked to the quality and handling of the metal powder. Expertise in specific aerospace alloys is crucial.
- What to Look For:
- Gamme de matériaux : Capability to process the required alloys (Scalmalloy®, Ti-6Al-4V, etc.).
- Powder Sourcing & Quality: Use of high-quality, aerospace-grade powders with controlled particle size distribution and chemistry. Providers like Met3dp, who manufacture their own high-performance powders using advanced atomization techniques (Gas Atomization, PREP), offer an advantage in quality control and material science expertise.
- Powder Handling & Management: Strict procedures for powder storage, handling, sieving, recycling (including tracking reuse cycles), and preventing cross-contamination.
- Traçabilité des matériaux : Ability to trace powder batches back to their source and link them directly to specific parts and builds.
- Test des matériaux : In-house or certified third-party labs for powder characterization and witness coupon testing (tensile, chemistry, microstructure).
- Technology & Equipment Capabilities:
- Why it Matters: The specific AM technology (e.g., Laser Powder Bed Fusion – LPBF, Electron Beam Melting – SEBM) and the quality/features of the machines impact resolution, accuracy, surface finish, and material properties.
- What to Look For: Appropriate machine technology for the material and application (LPBF common for Scalmalloy® and Ti-6Al-4V, SEBM also excellent for Ti-6Al-4V), well-maintained and calibrated machines from reputable manufacturers, adequate build volume capacity, and advanced features like in-situ process monitoring (melt pool monitoring, thermal imaging) for enhanced quality assurance. Met3dp utilizes industry-leading printing equipment known for accuracy and reliability.
- Post-Processing Capabilities:
- Why it Matters: As discussed previously, post-processing is integral. A supplier’s ability to manage these steps efficiently and correctly is critical.
- What to Look For: In-house capabilities for stress relief, heat treatment (including vacuum/inert atmosphere furnaces), HIP (or a strong relationship with a certified HIP provider), support removal, CNC machining (5-axis capabilities often needed for complex AM parts), surface finishing, cleaning, and relevant NDT methods (CT scanning, FPI, etc.). A single point of contact managing the entire process chain simplifies project management.
- Design for Additive Manufacturing (DfAM) Support:
- Why it Matters: Suppliers with strong DfAM expertise can collaborate with your design team to optimize the housing for AM, maximizing benefits like lightweighting and performance while ensuring manufacturability.
- What to Look For: Application engineers with experience in topology optimization, lattice structures, support strategy, and AM constraints. Willingness to engage early in the design process and provide feedback.
- Project Management & Communication:
- Why it Matters: Clear communication, transparent processes, and responsive project management are vital for complex aerospace projects.
- What to Look For: Dedicated points of contact, clear quoting process, regular progress updates, documented procedures, responsiveness to queries and design changes.
- Capacity & Lead Time:
- Why it Matters: Ensure the supplier has the available machine capacity and resources to meet your project timelines.
- What to Look For: Realistic lead time estimates based on current workload and project complexity. Ability to potentially scale production if needed.
Choisir un metal 3D printing B2B supplier for aerospace components is a strategic decision. Thoroughly vetting potential partners against these criteria will significantly increase the likelihood of receiving high-quality, reliable satellite camera housings that meet all mission requirements. Look for partners like Met3dp who offer comprehensive solutions, combining materials science, advanced manufacturing technology, and rigorous quality control.
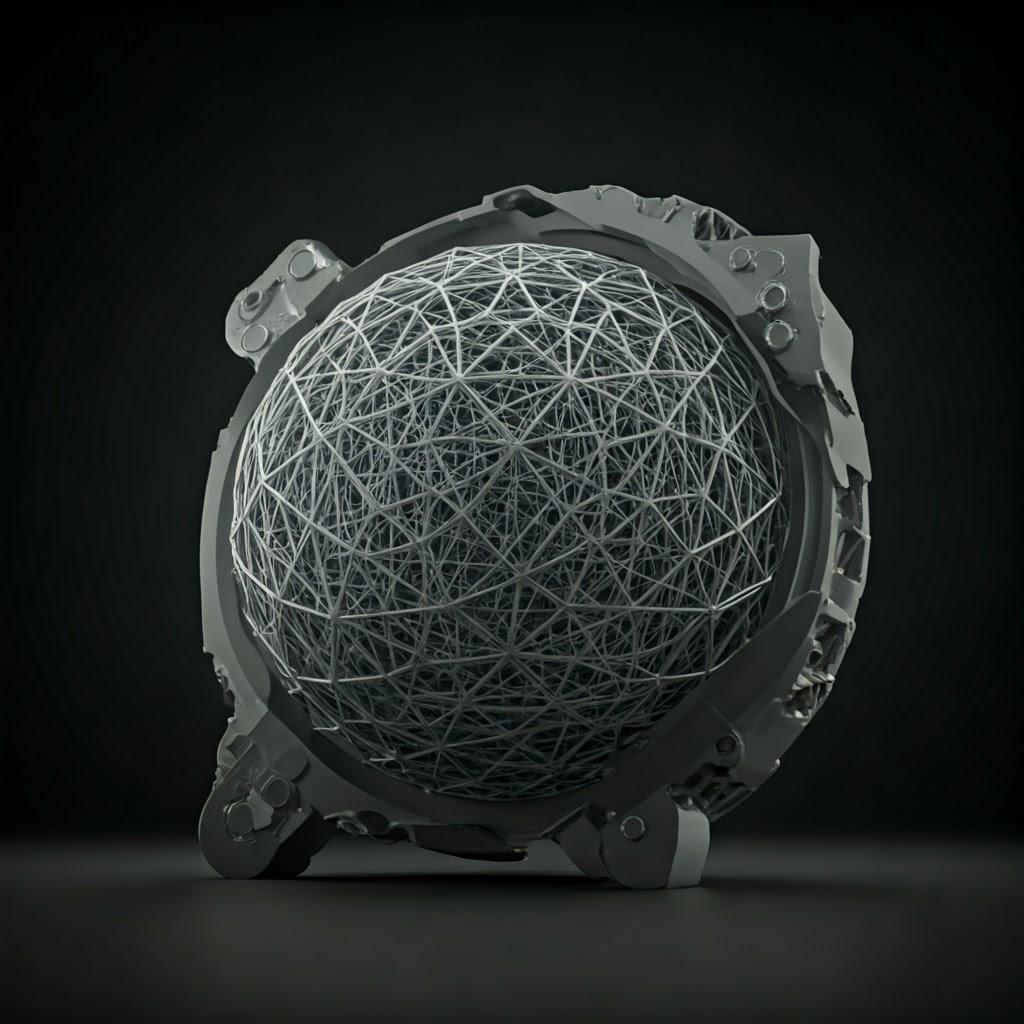
Budgeting and Timelines: Understanding Cost Factors and Lead Times for AM Housings
While metal additive manufacturing offers significant long-term value through performance gains and potential assembly simplification, understanding the cost structure and typical lead times is crucial for effective project planning and budgeting. The metal 3D printing cost for aerospace components like satellite camera housings is influenced by a complex interplay of factors, as are the associated timelines.
Principaux facteurs de coûts :
- Material Type & Consumption:
- Coût de la poudre : High-performance aerospace alloys like Scalmalloy® and Ti-6Al-4V are inherently more expensive than standard engineering metals. Cost is typically calculated per kilogram of powder consumed (including supports).
- Part Volume/Mass: Larger, denser parts naturally consume more material, directly impacting cost.
- Structures de soutien : Material used for supports adds to consumption and requires time/labor for removal. Efficient DfAM minimizes this.
- Temps machine (temps de construction) :
- Build Height: Primarily determines print duration. Taller parts take longer. Optimized orientation can sometimes reduce height at the expense of a larger footprint.
- Part Volume & Density: More material to melt per layer increases layer time. Complex geometries or extensive lattice structures can increase scan path complexity and time.
- Machine Rate: AM machines represent significant capital investment, and their operating costs (power, gas, maintenance) contribute to hourly rates.
- Complexité de la conception :
- Manufacturability: Highly complex designs may require more intricate support structures, have a higher risk of build failure (requiring reprints), and necessitate more complex post-processing, all adding to cost.
- Fine Features: Very small features or thin walls can slow down print speeds or require specialized parameters.
- Post-Processing Intensity:
- Traitement thermique/HIP : Required steps adding furnace time and operational costs. HIP is a significant cost adder but often mandatory for critical parts.
- Suppression du support : Labor-intensive, especially for complex internal supports.
- Usinage CNC : Required for tight tolerances and specific finishes. Cost depends on the number of features, complexity of setups, and required precision.
- Finition de la surface : Polishing, blasting, coating steps add labor and material costs.
- Nettoyage : Specialized cleaning procedures for aerospace/optical applications add time and cost.
- Inspection & Quality Assurance:
- NDT : Costs associated with CT scanning, FPI, X-ray, etc., depending on requirements.
- Inspection dimensionnelle : CMM programming and measurement time.
- Documentation : Generating required quality documents, material certifications, and inspection reports adds overhead.
- Quantity & Setup:
- Setup Costs: Programming, build preparation, and initial parameter qualification costs are amortized over the number of parts produced. Per-part cost decreases with larger volumes (though AM is often most competitive at lower volumes compared to tooling-based methods).
- Nesting: Printing multiple parts together in a single build can improve machine utilization and reduce cost per part.
Typical Lead Time Factors:
Lead time for an AM satellite camera housing can vary significantly, from a few weeks for a simpler prototype to several months for a complex, fully qualified production part.
- Design & Optimization Phase: Initial DfAM, analysis (FEA, CFD), and design finalization can take days to weeks, depending on complexity and iterations.
- Quoting & Scheduling: Obtaining quotes and securing a slot in the AM provider’s production schedule.
- Préparation de la construction : Preparing the build file, planning orientation and supports.
- Temps d'impression : Can range from 1-2 days for smaller parts to over a week for large, complex housings filling a build chamber.
- Post-traitement : This often constitutes a significant portion of the total lead time:
- Stress Relief: ~1 day (including furnace cycle and cooling).
- Part/Support Removal: 1-3 days (highly variable).
- Heat Treatment/HIP: 2-5 days (including furnace cycles, shipping to/from HIP provider if external).
- CNC Machining: 3 days to 2+ weeks (depending on complexity, shop loading).
- Finishing/Cleaning: 1-5 days.
- Inspection : 1-5 days (depending on requirements).
- Expédition: Depends on location and method.
Overall Estimated Lead Time:
- Rapid Prototype (basic finishing): 2-4 semaines
- Functional Prototype (some machining/heat treat): 4-8 semaines
- Fully Qualified Production Part (full post-processing & inspection): 8-16+ weeks
Remarque : These are rough estimates. Complex geometries, stringent qualification requirements, supply chain issues (e.g., HIP availability), and high machine utilization at the provider can extend these timelines. Clear communication with the supplier is essential for establishing realistic additive manufacturing lead times. While the initial satellite component pricing via AM might seem higher than a simple machined block, considering the value from lightweighting (reduced launch costs), part consolidation (reduced assembly), and accelerated development often reveals a favorable total cost of ownership for complex aerospace components.
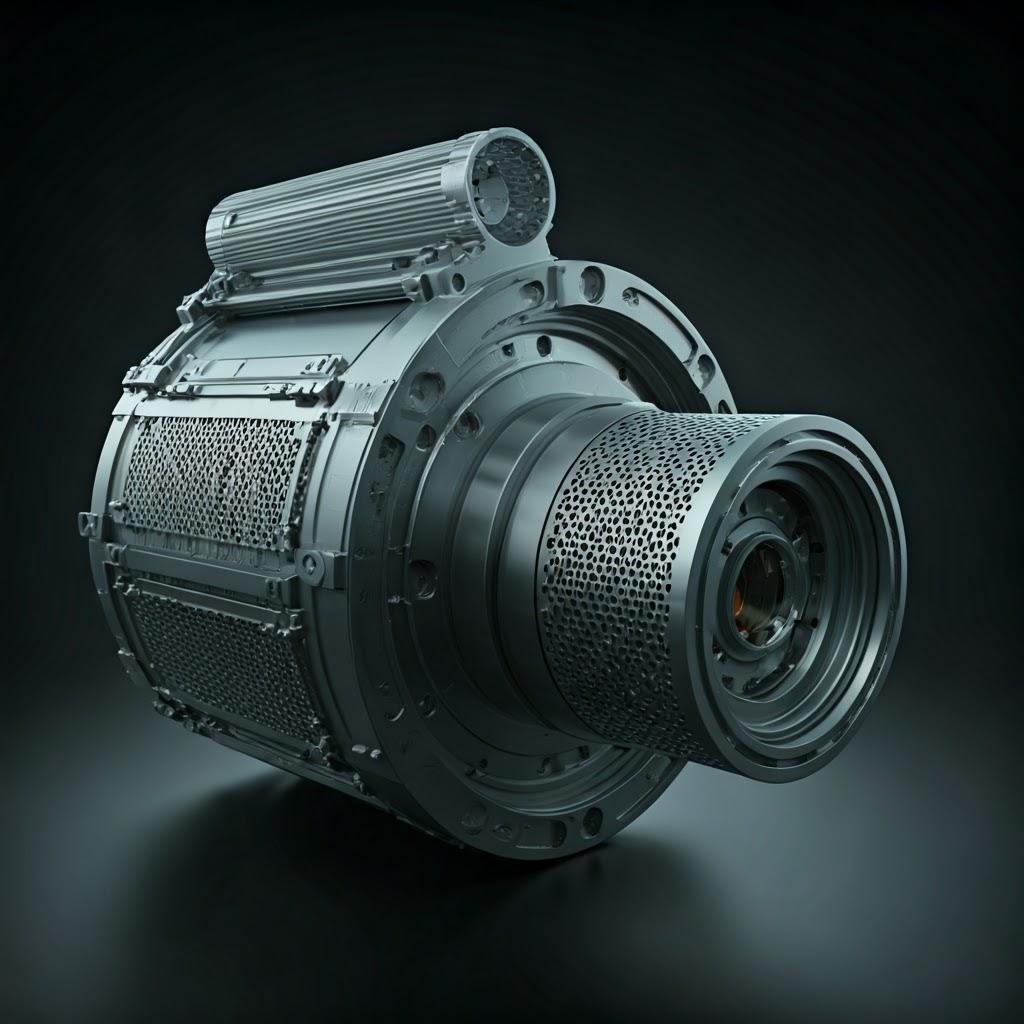
Frequently Asked Questions (FAQ) about 3D Printed Satellite Camera Housings
Here are answers to some common questions engineers and procurement managers have about using metal additive manufacturing for satellite camera housings:
1. How does the cost of AM satellite camera housings compare to traditionally CNC machined ones?
- The comparison depends heavily on part complexity, material, and production volume.
- For highly complex geometries, significant lightweighting (using topology optimization/lattices), or parts requiring consolidation: AM can be more cost-effective, even at low volumes. While the per-part print cost might be high, savings come from reduced material waste (especially with expensive alloys), eliminated tooling costs, drastically reduced assembly labor (due to part consolidation), and significant launch cost savings from lightweighting.
- For simpler geometries easily machined from block: Traditional CNC machining is often cheaper, especially at higher volumes where machining setups are amortized.
- Hybrid Approach: Often, the most cost-effective solution involves printing the complex near-net shape via AM and then using CNC machining for critical interfaces and tolerances.
- Overall: AM’s value proposition often lies in enabling performance enhancements (weight, thermal management) that are impossible or prohibitively expensive with traditional methods, rather than direct piece-price reduction for simple designs.
2. What level of qualification and testing is typically required for 3D printed components used in space missions?
- Qualification is rigorous and often mission-specific, but generally involves a multi-faceted approach:
- Qualification des matériaux : Extensive testing of the specific powder batch (chemistry, particle size) and mechanical properties of printed material (using witness coupons built alongside parts) under relevant conditions (e.g., tensile strength, fatigue life, fracture toughness at operational temperatures). Low outgassing properties must be verified.
- Validation des processus : Demonstrating that the AM process (machine, parameters, post-processing) consistently produces parts meeting specified requirements (density, microstructure, dimensional accuracy). This often involves extensive parameter development and statistical analysis.
- Part-Specific Testing: The final housing design typically undergoes functional and environmental testing, which may include:
- Vibration Testing: Simulating launch loads.
- Thermal Cycling: Testing performance across expected orbital temperature swings.
- Thermal Vacuum (TVAC) Testing: Operating the component in a simulated space environment (vacuum and temperature extremes).
- Vérification dimensionnelle : Full inspection using CMM and potentially CT scanning.
- Essais non destructifs (END) : To ensure internal integrity (e.g., check for cracks or porosity).
- Normes : While universal AM space standards are still evolving, organizations like NASA and ESA have internal standards, and industry bodies (ASTM, ISO) are developing relevant guidelines. Requirements are typically defined at the mission or prime contractor level.
3. Can we simply take our existing housing design (made for machining) and print it using AM?
- While technically possible, it’s generally not recommended as it fails to leverage the key advantages of additive manufacturing. A direct conversion (“build-to-print”) of a design optimized for subtractive methods often results in:
- Minimal or no weight savings.
- Potentially longer print times and higher costs than necessary.
- Missed opportunities for part consolidation and functional integration (like conformal cooling).
- Possible manufacturability issues (e.g., unsupported features, difficult powder removal).
- Best Practice: Re-designing the housing using Conception pour la fabrication additive (DfAM) principles is crucial. This involves thinking about function first and leveraging topology optimization, lattice structures, and feature integration to create a part truly optimized for the layer-by-layer process and the performance requirements of the application. Collaboration with AM experts during this redesign phase is highly beneficial.
4. For a satellite camera housing, which material is generally better: Scalmalloy® or Ti-6Al-4V?
- Neither material is universally “better”; the optimal choice depends on the specific priorities for the housing:
- Choisissez Scalmalloy® si :
- Maximum lightweighting is the absolute top priority (its lower density is a significant advantage).
- Bonne conductivité thermique is needed for heat dissipation.
- Operating temperatures remain moderate.
- Choose Ti-6Al-4V if:
- Low thermal expansion (CTE) is critical for maintaining precise optical alignment over temperature fluctuations.
- Higher operating temperatures are expected.
- Proven space heritage and extensive qualification data are highly valued.
- Résistance supérieure à la corrosion is required (though Scalmalloy® is generally adequate).
- Choisissez Scalmalloy® si :
- Trade-off Analysis: A decision matrix weighing factors like mass budget, thermal stability requirements, operating environment, structural loads, and program maturity/risk tolerance helps determine the best fit for each specific mission. Consulting with materials and AM experts is recommended.
Conclusion: Elevating Satellite Performance with Advanced Metal 3D Printed Housings
The journey into space demands components that push the boundaries of performance, reliability, and efficiency. For satellite camera housings – the critical guardians of sensitive optical payloads – metal additive manufacturing has emerged as a transformative technology, moving beyond prototyping to become a key enabler of next-generation satellite capabilities.
As we’ve explored, the advantages are compelling. The unparalleled design freedom offered by AM allows engineers to leverage powerful tools like optimisation de la topologie et lattice structures, ce qui donne dramatically lighter housings that reduce launch costs and enhance satellite agility. The ability to consolidate multiple parts into a single, complex component simplifies assembly, reduces potential failure points, and further minimizes mass. Furthermore, AM enables the integration of highly efficient thermal management features, such as conformal cooling channels, vital for maintaining the stability and longevity of sophisticated camera systems. Utilizing advanced, space-grade materials like the high-strength, lightweight Scalmalloy® (alliage d'aluminium) or the proven, thermally stable Ti-6Al-4V ensures performance under the extreme conditions of orbit.
However, realizing these benefits requires a deep understanding of the entire process chain – from employing Conception pour la fabrication additive (DfAM) principles and selecting the right materials, to meticulously controlling the printing process and executing essential post-processing steps like heat treatment, HIP, and precision machining. Navigating potential challenges such as residual stress, porosity, and achieving stringent tolerances necessitates expertise and robust quality control.
This underscores the importance of choosing the right manufacturing partner. An ideal partner possesses not only state-of-the-art equipment but also profound expertise in materials science, process optimization, quality assurance, and the specific demands of the aerospace sector.
Met3dp stands at the forefront of this technological wave, offering comprehensive solutions de fabrication additive métallique. With industry-leading capabilities spanning the development and production of high-quality metal powders using advanced atomization techniques, to operating cutting-edge SEBM printers renowned for their accuracy and reliability, Met3dp provides an end-to-end ecosystem for demanding industrial applications. Our decades of collective expertise in metal AM enable us to partner with organizations in aerospace, medical, automotive, and other sectors to accelerate their adoption of additive manufacturing and realize its full potential.
By embracing metal 3D printing and partnering with experienced providers like Met3dp, aerospace companies can develop satellite camera housings and other critical components that are lighter, more capable, and delivered faster, paving the way for the future of satellite technology and unlocking new possibilities in Earth observation, communication, and scientific discovery.
Contactez Met3dp aujourd'hui to explore how our advanced metal AM systems, high-performance powders, and expert application development services can power your organization’s most ambitious projects.
Partager sur
MET3DP Technology Co. est un fournisseur de premier plan de solutions de fabrication additive dont le siège se trouve à Qingdao, en Chine. Notre société est spécialisée dans les équipements d'impression 3D et les poudres métalliques de haute performance pour les applications industrielles.
Articles connexes
À propos de Met3DP
Mise à jour récente
Notre produit
CONTACTEZ-NOUS
Vous avez des questions ? Envoyez-nous un message dès maintenant ! Nous répondrons à votre demande avec toute une équipe dès réception de votre message.
Obtenir les informations de Metal3DP
Brochure du produit
Obtenir les derniers produits et la liste des prix
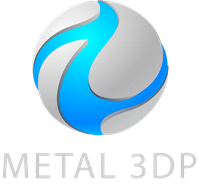
Poudres métalliques pour l'impression 3D et la fabrication additive