Fabrication additive Inconel 625 à Paris 2025
Table des matières
Contour:
- Introduction à l'Inconel 625 dans la fabrication additive
- Le marché en pleine croissance de l'Inconel 625 AM à Paris et en France
- Principaux avantages de l'Inconel 625 pour les applications industrielles
- Principaux fournisseurs de services AM Inconel 625 à Paris
- Études de cas : Mise en œuvre réussie dans les industries parisiennes
- Solutions avancées de poudre Inconel 625 de Met3dp
- Considérations techniques lors de l'utilisation de l'Inconel 625 en fabrication additive
- Analyse des coûts et retour sur investissement pour les projets AM Inconel 625
- FAQ sur la fabrication additive Inconel 625
Permettez-moi de développer ce guide complet en trois parties :
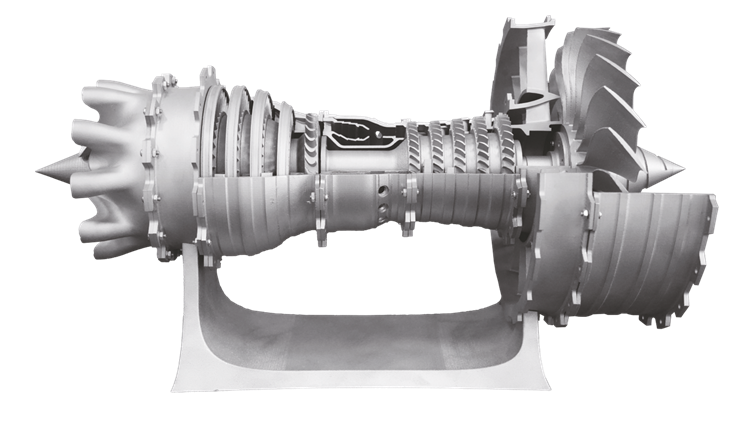
PARTIE 1
1. Introduction à l'Inconel 625 dans la fabrication additive
Le paysage industriel parisien connaît une transformation révolutionnaire grâce à la fabrication additive métallique, l'Inconel 625 s'imposant comme un superalliage de choix dans des secteurs critiques. Alors que la capitale française consolide sa position de pôle européen de fabrication de pointe, les entreprises se tournent de plus en plus vers des matériaux et procédés innovants pour conserver leur avantage concurrentiel.
L'Inconel 625 (UNS N06625) est un superalliage nickel-chrome-molybdène réputé pour sa combinaison exceptionnelle de propriétés :
- Résistance exceptionnelle à la corrosion dans les environnements extrêmes
- Excellente résistance aux hautes températures et à l'oxydation
- Performances mécaniques supérieures dans des conditions de fonctionnement sévères
- Résistance exceptionnelle à la fatigue, au fluage et à la rupture
- Bonne soudabilité et capacités de post-traitement
L’intégration de cet alliage haute performance aux technologies de fabrication additive crée des opportunités sans précédent pour les fabricants parisiens d’innover dans des secteurs allant de l’aérospatiale et de l’énergie aux industries automobile et médicale.
Contexte historique et évolution
L'Inconel 625 a été développé à l'origine dans les années 1960 pour des applications critiques dans les environnements aérospatial et maritime. Sa composition comprend généralement :
Élément | Gamme de composition (%) |
---|---|
Nickel | 58,0 (min) |
Chrome | 20.0-23.0 |
Molybdène | 8.0-10.0 |
Le fer | 5,0 (max) |
Niobium + Tantale | 3.15-4.15 |
Cobalt | 1,0 (max) |
Manganèse | 0,5 (max) |
Silicium | 0,5 (max) |
Aluminium | 0,4 (max) |
Titane | 0,4 (max) |
Carbone | 0,1 (max) |
Bien que traditionnellement fabriqués par des procédés de moulage, de forgeage et d'usinage, l'adoption de impression 3D de métaux a ouvert de nouvelles dimensions pour les applications de l'Inconel 625, en particulier dans la culture d'innovation axée sur le design de Paris.
Technologies de fabrication additive pour l'Inconel 625
Plusieurs technologies AM ont démontré leur succès avec le traitement de l'Inconel 625 :
- Fusion en lit de poudre (PBF)
- Fusion laser sur lit de poudre (L-PBF)
- Fusion par faisceau d'électrons (EBM)
- Dépôt d'énergie dirigée (DED)
- Façonnage des filets au laser (LENS)
- Fabrication additive par faisceau d'électrons (EBAM)
- Jetting de liant
- Avec des opérations de frittage ultérieures
Parmi celles-ci, le L-PBF s'est imposé comme la technologie dominante pour l'Inconel 625 AM à Paris, offrant une haute précision et d'excellentes propriétés mécaniques grâce à des paramètres de traitement soigneusement contrôlés.
Pourquoi Paris adopte l'Inconel 625 AM
L'écosystème industriel parisien est particulièrement bien placé pour capitaliser sur la fabrication additive Inconel 625 en raison de plusieurs facteurs clés :
- Forte présence aérospatiale:Avec les principaux équipementiers et fournisseurs de l'aéronautique concentrés autour de Paris, la demande en superalliages de nickel hautes performances est substantielle.
- Excellence académique et de recherche: Des institutions de classe mondiale comme l'École Polytechnique et Arts et Métiers ParisTech stimulent l'innovation en science des matériaux.
- Soutien gouvernemental:Des initiatives françaises comme le programme « Industrie du Futur » fournissent un financement important pour l’adoption de la fabrication avancée.
- Un riche patrimoine manufacturier:Paris allie l'expertise traditionnelle de fabrication à l'adoption avant-gardiste des technologies numériques.
- Développement durable:L'efficacité matérielle d'AM s'aligne sur l'engagement de Paris visant à réduire l'impact environnemental industriel.
Alors que les fabricants parisiens doivent faire face aux complexités des défis industriels modernes, la fabrication additive Inconel 625 représente une approche transformatrice pour produire des composants complexes à haute valeur ajoutée avec des propriétés améliorées et des délais de livraison réduits.
2. Le marché croissant de l'Inconel 625 AM à Paris et en France
Le secteur parisien de la fabrication additive connaît une croissance sans précédent, le segment de l'Inconel 625 étant en tête dans les domaines d'application à forte valeur ajoutée. Cette trajectoire de croissance reflète les tendances européennes plus générales, mais est accélérée par l'orientation stratégique de la France vers les technologies de fabrication avancées.
Taille du marché et projections de croissance
Le marché français de la fabrication additive métallique a atteint environ 320 millions d'euros en 2022, avec des projections indiquant un taux de croissance annuel composé (TCAC) de 21,81 TP3T jusqu'en 2028. L'Inconel 625 représente environ 181 TP3T du marché total de la fabrication additive métallique en France, Paris représentant près de 401 TP3T de l'activité de fabrication additive métallique du pays.
Année | Projection du marché français des métaux AM (M€) | Segment Inconel 625 estimé (M€) |
---|---|---|
2023 | 389.8 | 70.2 |
2024 | 474.8 | 85.5 |
2025 | 578.3 | 104.1 |
2026 | 704.4 | 126.8 |
2027 | 857.9 | 154.4 |
2028 | 1,044.9 | 188.1 |
Plusieurs facteurs clés alimentent cette croissance remarquable du marché parisien de l’Inconel 625 AM :
- Demande de l'industrie aérospatiale
- Paris-Le Bourget abrite de grands industriels de l'aéronautique nécessitant des composants performants
- Les activités de Safran, Thales et Airbus entraînent une consommation importante de superalliages
- Les nouvelles conceptions d'avions intègrent de plus en plus de pièces Inconel produites par FA
- Transformation du secteur énergétique
- La stratégie d'indépendance énergétique de la France met l'accent sur la fabrication de pointe
- Les applications d'énergie nucléaire exploitent la résistance à la corrosion de l'Inconel 625
- Les systèmes d'énergie renouvelable nécessitent des matériaux haute performance pour des conditions extrêmes
- Régionalisation de la chaîne d'approvisionnement
- L'accent post-pandémique est mis sur les chaînes d'approvisionnement résilientes et localisées
- La fabrication additive permet une production à la demande, réduisant ainsi la dépendance aux fournisseurs internationaux
- Paris sert de plaque tournante industrielle centrale pour l'Europe occidentale
- Accessibilité technologique
- La baisse des coûts d'équipement rend la fabrication additive plus accessible aux PME
- La disponibilité des matériaux s'est améliorée, avec l'arrivée sur le marché de fournisseurs de poudre spécialisés
- Les connaissances techniques se diffusent grâce aux partenariats entre l'industrie et le monde universitaire
Les principaux secteurs industriels parisiens adoptent l'Inconel 625 AM
L’adoption de la fabrication additive Inconel 625 varie selon les secteurs industriels parisiens :
Aérospatiale et Défense (42% de marché) :
- Échangeurs de chaleur et composants de combustion
- Pièces de turbine et carters de moteur
- Composants structurels pour environnements extrêmes
- Composants de satellites et de véhicules spatiaux
Production d'énergie (23% de marché) :
- Composants de turbines à gaz
- Équipement de transfert de chaleur
- Composants de centrales nucléaires
- Équipements offshore et sous-marins
Automobile et course (14% de marché) :
- Formule 1 et composants de véhicules hautes performances
- Systèmes d'échappement
- Composants du turbocompresseur
- Systèmes de gestion de la chaleur
Traitement chimique (12% du marché) :
- Récipients sous pression
- Réacteurs et équipements de traitement
- Échangeurs de chaleur
- Vannes et composants de contrôle de débit
Médical et Recherche (9% de marché) :
- Équipement de recherche spécialisé
- Instruments chirurgicaux sur mesure
- Équipement de test de laboratoire
- Composants de la radiothérapie
Paysage réglementaire et de normalisation
L'écosystème parisien de l'Inconel 625 AM évolue dans un cadre réglementaire complexe qui continue d'évoluer :
- Normes AFNOR:L'organisme français de normalisation a développé des normes spécifiques à la FA adaptables aux superalliages de nickel
- Directive européenne sur les machines:Les exigences de sécurité ont un impact sur le fonctionnement des équipements AM
- Certification des matériaux:Standardisation croissante des spécifications de la poudre Inconel 625
- Assurance qualité:Les certifications ISO 9001, AS9100 et NADCAP deviennent obligatoires pour les fournisseurs de l'aérospatiale
- Réglementation environnementale:Les politiques environnementales strictes de Paris influencent les opérations des installations AM
L'Association Française de Normalisation (AFNOR) participe activement aux efforts de normalisation internationale via l'ISO/TC 261 et l'ASTM F42, garantissant que les fabricants parisiens restent alignés sur les meilleures pratiques mondiales tout en maintenant les normes de fabrication historiquement élevées de la ville.
3. Principaux avantages de l'Inconel 625 pour les applications industrielles
Les industriels parisiens exploitent de plus en plus les propriétés exceptionnelles de l'Inconel 625 grâce à la fabrication additive pour relever des défis industriels complexes. Ce superalliage à base de nickel offre une combinaison convaincante d'avantages qui le rendent idéal pour les applications les plus exigeantes dans de nombreux secteurs.
Propriétés et performances supérieures des matériaux
Les propriétés fondamentales de l'Inconel 625 le rendent particulièrement adapté aux applications de fabrication additive où les performances ne peuvent être compromises :
1. Résistance exceptionnelle à la corrosion
- Résistance exceptionnelle à la corrosion par piqûres et par crevasses
- Excellentes performances dans les environnements contenant du chlorure
- Résistance supérieure à la fissuration par corrosion sous contrainte
- Durabilité exceptionnelle en milieux acides et alcalins
- Résistance à l'eau de mer et aux environnements marins
2. Performance à haute température
- Maintient l'intégrité structurelle à des températures allant jusqu'à 982 °C (1800 °F)
- Excellente résistance au fluage à des températures élevées
- Stabilité thermique tout au long des cycles répétés de chauffage/refroidissement
- Caractéristiques de faible dilatation thermique
- Résistance à l'oxydation dans les environnements à haute température
3. Propriétés mécaniques
- Haute résistance à la traction (655-827 MPa à l'état construit)
- Excellente résistance à la fatigue sous charge cyclique
- Bonnes propriétés d'allongement (généralement 30-50% dans les pièces AM correctement traitées)
- Valeurs de dureté entre 25 et 40 HRC selon le traitement
- Résistance aux chocs et ténacité exceptionnelles
4. Attributs de fabrication et de post-traitement
- Bonne imprimabilité avec des paramètres de processus appropriés
- Soudabilité pour les opérations d'assemblage ou de réparation
- Usinable avec un outillage et des techniques appropriés
- Traitement thermique pour modifier la microstructure et les propriétés
- Compatible avec diverses méthodes de traitement de surface
Propriétés mécaniques typiques de l'Inconel 625 traité par AM
Propriété | Processus L-PBF (tel que construit) | Procédé L-PBF (traitement thermique) | Référence forgée |
---|---|---|---|
Résistance ultime à la traction (MPa) | 827-1030 | 941-1030 | 827-1030 |
Limite d'élasticité (MPa) | 600-770 | 650-770 | 414-655 |
Élongation (%) | 30-40 | 35-45 | 30-60 |
Dureté (HRC) | 25-33 | 28-35 | 20-25 |
Module d'élasticité (GPa) | 175-205 | 175-205 | 205 |
Avantages sectoriels de l'Inconel 625 AM à Paris
Le déploiement stratégique de la fabrication additive Inconel 625 crée des avantages concurrentiels distinctifs dans les industries parisiennes :
Applications aérospatiales et de défense
- Consolidation des composants:Les assemblages complexes nécessitant auparavant plusieurs pièces et opérations d'assemblage peuvent être consolidés en composants imprimés uniques, réduisant ainsi le poids et éliminant les points de défaillance potentiels.
- Gestion thermique:Les composants du moteur et les systèmes d'échappement produits avec des canaux de refroidissement internes optimisés par AM démontrent une gestion thermique améliorée du 15-25% par rapport aux conceptions conventionnelles.
- Structures légères:Les structures Inconel 625 optimisées en termes de topologie permettent une réduction de poids de 30-40% tout en maintenant ou en améliorant les performances mécaniques, essentielles pour l'efficacité énergétique dans les applications aérospatiales.
- Prototypage rapide:Les nouvelles itérations de conception de composants peuvent être testées physiquement en quelques jours plutôt qu'en quelques semaines, accélérant ainsi le cycle d'innovation des fournisseurs aérospatiaux basés à Paris.
Applications dans le secteur de l'énergie
- Durée de vie prolongée:Les composants critiques dans les environnements corrosifs présentent une durée de vie 2 à 3 fois plus longue lorsqu'ils sont produits avec des conceptions Inconel 625 optimisées par AM.
- Efficacité améliorée:Les échangeurs de chaleur à géométries internes complexes impossibles à fabriquer de manière conventionnelle démontrent une efficacité thermique améliorée du 20-30%.
- Temps d'arrêt réduits:La production à la demande de pièces de rechange réduit les temps d'arrêt des usines en éliminant les longs délais de livraison des composants spécialisés.
- Solutions personnalisées:Capacité à produire des solutions sur mesure pour des défis opérationnels uniques dans les infrastructures énergétiques existantes dans toute la France.
Applications automobiles et de course
- Optimisation des performances:Les équipes de Formule 1 et du Mans basées près de Paris utilisent l'Inconel 625 AM pour les composants d'échappement qui résistent aux températures extrêmes tout en minimisant le poids.
- Développement accéléré:Les capacités d'itération de conception rapide réduisent le temps de développement jusqu'à 75% par rapport aux méthodes de fabrication traditionnelles.
- Intégration fonctionnelle:De multiples fonctions combinées dans des composants uniques réduisent la complexité de l'assemblage et améliorent la fiabilité dans les applications hautes performances.
- Personnalisation:Les petites séries de production deviennent économiquement viables, répondant aux exigences de personnalisation du segment automobile haut de gamme.
Avantages économiques et commerciaux
Au-delà des avantages techniques, l’Inconel 625 AM offre des avantages commerciaux convaincants aux industriels parisiens :
- Simplification de la chaîne d'approvisionnement
- Dépendance réduite aux fournisseurs spécialisés
- Diminution des coûts de stockage des stocks
- Risque réduit de ruptures d'approvisionnement
- Protection renforcée de la propriété intellectuelle
- Réduction des délais de livraison
- 40-80% réduction du délai de mise sur le marché des nouvelles conceptions
- Suppression des délais de fabrication des outillages
- Réponse rapide aux modifications des spécifications des clients
- Avantage concurrentiel grâce à l'agilité
- Optimisation des coûts
- Réduction des déchets de matériaux (utilisation de matériaux généralement > 95%)
- Élimination des coûts d'outillage spécialisé
- Diminution des besoins en main-d'œuvre
- Réduction des coûts d'assemblage grâce à la consolidation des pièces
- Avantages en matière de durabilité
- Consommation d'énergie réduite par rapport à la fabrication traditionnelle
- Réduire les émissions liées au transport grâce à une production localisée
- Consommation de matières premières minimisée
- Cycles de vie des produits prolongés grâce à l'optimisation des performances
Grâce à ces multiples avantages, la fabrication additive Inconel 625 s'impose comme une compétence essentielle pour les industriels parisiens avant-gardistes en quête d'avantages concurrentiels sur les marchés mondiaux. Des entreprises comme Met3dp sont à l'avant-garde de cette transformation, fournissant des poudres métalliques avancées et des solutions AM complètes qui permettent aux fabricants de tirer pleinement parti de ces avantages.
PARTIE 2
4. Principaux fournisseurs de services AM Inconel 625 à Paris
Paris s'est imposée comme une plaque tournante des services de fabrication avancée, avec plusieurs prestataires spécialisés proposant des capacités de fabrication additive Inconel 625. Ces entreprises, allant d'acteurs industriels établis à des startups innovantes, apportent chacune leurs atouts uniques à cet écosystème en pleine croissance.
Fournisseurs de services AM Inconel 625 de premier plan
1. AddUp France (Centre d'Innovation de Paris)
AddUp, une joint-venture entre Michelin et Fives, exploite à Paris un centre de fabrication additive de pointe axé sur la fabrication additive métallique haute performance, y compris une expertise spécialisée dans les applications Inconel 625.
Principales capacités :
- Plusieurs systèmes FormUp 350 L-PBF avec volumes de construction étendus
- Systèmes complets de gestion du cycle de vie des poudres
- Contrôle qualité approfondi et certification des matériaux
- Laboratoire métallurgique et installations d'essais avancées
- Capacités complètes de post-traitement, y compris le traitement thermique et l'usinage
Secteur d'activité : Applications aérospatiales, énergétiques et de défense nécessitant une traçabilité élevée et une production certifiée.
2. Initiale (Groupe Prodways)
Initial, l'un des plus grands fournisseurs de services d'impression 3D industrielle en France, maintient des opérations importantes à Paris, offrant des capacités de production complètes d'Inconel 625.
Principales capacités :
- Approche multi-technologie incluant les procédés L-PBF et DED
- Services d'optimisation de conception avec une expertise aérospatiale spécialisée
- Production certifiée ISO 9001 et AS 9100
- Fabrication hybride intégrant la FA aux processus conventionnels
- Capacité de production en série de composants Inconel 625 qualifiés
Secteur d'activité : Applications industrielles mixtes mettant l'accent sur les secteurs aérospatial et énergétique.
3. Spartacus3D (Groupe Farinia)
Situé aux portes de Paris dans le corridor industriel, Spartacus3D est spécialisé dans la fabrication additive métallique haute performance pour des applications exigeantes, avec une expérience significative de l'Inconel 625.
Principales capacités :
- Systèmes L-PBF grand format pour la production de composants surdimensionnés
- Protocoles de traitement thermique spécialisés pour l'Inconel 625
- Systèmes avancés de CND et de vérification de la qualité
- Partenariat de développement de matériaux avec des fournisseurs de poudre
- Installations complètes d'essais mécaniques
Secteur d'activité : Secteur de l'énergie, turbomachines et équipements industriels nécessitant des performances thermiques exceptionnelles.
4. 3D&P (Paris Tech Hub)
Bureau de services spécialisé dans la fabrication additive métallique, axé exclusivement sur les applications de superalliages, 3D&P a développé des procédés exclusifs pour améliorer les propriétés de l'Inconel 625 dans des applications spécifiques.
Principales capacités :
- Développement de paramètres personnalisés pour les exigences spécifiques à l'application
- Techniques de finition de surface spécialisées pour l'Inconel 625
- Caractérisation et validation des poudres en interne
- Surveillance des processus et documentation de la qualité
- Capacités de production en petits lots avec un délai d'exécution rapide
Secteur d'activité : Institutions de recherche, fabricants de dispositifs médicaux et applications industrielles spécialisées.
5. Technologie Metal3DP
Bien que son siège social soit situé à Qingdao, en Chine, Métal3DP a établi une présence significative sur le marché parisien, fournissant à la fois des poudres Inconel 625 avancées et des services complets de fabrication additive aux fabricants français.
Principales capacités :
- Technologie d'atomisation de gaz de pointe pour une poudre Inconel 625 de qualité supérieure
- Capacités d'impression avancées SEBM (Selective Electron Beam Melting)
- Techniques exclusives de traitement des poudres garantissant une fluidité et une densité de tassement exceptionnelles
- Services complets de développement d'applications
- Programme de partenariat technique pour la mise en œuvre industrielle
Secteur d'activité : Applications de pointe dans les secteurs aérospatial, médical et énergétique nécessitant des propriétés de matériaux spécialisées et un support technique.
Analyse comparative des prestataires de services
Fournisseur | Portefeuille technologique | Volume de construction | Certifications | Délai d'exécution | Post-traitement | Soutien à la conception |
---|---|---|---|---|---|---|
AddUp | L-PBF | Jusqu'à 350 × 350 × 350 mm | ISO 9001, AS9100 | 2-4 semaines | Complet | Avancé |
Initial | L-PBF, DED | Jusqu'à 400×400×400mm | ISO 9001, AS9100 | 1-3 semaines | Complet | Avancé |
Spartacus3D | L-PBF | Jusqu'à 500 × 280 × 345 mm | ISO 9001, EN9100 | 3-5 semaines | Complet | Intermédiaire |
3D&P | L-PBF | Jusqu'à 300 × 300 × 300 mm | ISO 9001 | 1-2 semaines | Limitée | De base |
Métal3DP | SEBM, L-PBF | Jusqu'à 350 × 350 × 430 mm | ISO 9001, AS9100 | 2-3 semaines | Avancé | Complet |
Critères de sélection des prestataires de services pour les fabricants parisiens
Lors de l'évaluation des fournisseurs de services Inconel 625 AM à Paris, les fabricants doivent prendre en compte ces facteurs critiques :
Expertise technique et spécialisation
- Expérience approfondie avec l'Inconel 625 en particulier
- Compréhension des exigences spécifiques à l'application
- Connaissances en science des matériaux et expertise métallurgique
- Expérience avérée avec des composants ou des industries similaires
Systèmes de qualité et documentation
- Certifications industrielles pertinentes (AS9100, ISO 13485, etc.)
- Procédures de traçabilité des matériaux
- Méthodologies de validation des processus
- Capacités de contrôle non destructif
- Exhaustivité et conformité de la documentation
Capacités de production
- Type d'équipement et spécifications
- Limitations du volume de construction
- Capacité de débit
- Disponibilité de plusieurs machines pour la mise à l'échelle de la production
- Contrôle de processus cohérent entre les builds
Offre de services complète
- Assistance à l'optimisation de la conception
- Capacités de post-traitement
- Expertise en traitement thermique
- Services d'usinage et de finition
- Services de test et de validation
Considérations commerciales
- Stabilité financière
- Pratiques de protection de la propriété intellectuelle
- Proximité géographique pour la collaboration
- Compétitivité des prix
- Fiabilité des délais de livraison
Modèles de partenariat stratégique
Les industriels parisiens privilégient de plus en plus les partenariats stratégiques avec les prestataires de services de fabrication additive plutôt que de simples relations transactionnelles. Ces partenariats impliquent généralement :
- Programmes de développement collaboratif
- Développement conjoint d'applications
- Investissement partagé dans l'optimisation des processus
- Tests et validation coopératifs
- Initiatives de transfert de connaissances
- Composantes de formation et d'éducation
- Voies de transfert de technologie
- Renforcement progressif des capacités
- Approches de fabrication hybrides
- Intégration de la FA à la fabrication conventionnelle
- Application sélective de la FA pour les fonctionnalités critiques
- Chaînes de processus combinées pour des résultats optimaux
- Intégration de la chaîne d'approvisionnement
- Modèles d'inventaire numériques
- Accords de production à la demande
- Accords de capacité dédiée
En sélectionnant et en développant soigneusement des relations avec des fournisseurs de services AM spécialisés en Inconel 625, les fabricants parisiens peuvent accélérer leur adoption de cette technologie transformatrice tout en minimisant les risques d'investissement et les défis techniques.
5. Études de cas : Mise en œuvre réussie dans les industries parisiennes
La mise en œuvre concrète de la fabrication additive Inconel 625 dans le paysage industriel diversifié de Paris a généré des réussites convaincantes qui démontrent le potentiel transformateur de cette technologie. Ces applications concrètes illustrent comment les entreprises ont surmonté les défis et tiré parti des avantages uniques de la fabrication additive avec ce superalliage polyvalent.
Aéronautique : Refonte des composants de la chambre de combustion des moteurs d'avions Safran
Défi:
Safran Aircraft Engines, leader mondial des systèmes de propulsion aéronautique avec des opérations importantes en région parisienne, souhaitait améliorer l'efficacité thermique et la durabilité des composants de la chemise de chambre de combustion tout en réduisant le poids des moteurs de nouvelle génération.
Solution :
En collaboration avec Metal3DP comme fournisseur de matériaux, Safran a mis en œuvre une refonte innovante des composants de la chemise de chambre de combustion en utilisant la fabrication additive Inconel 625 avec ces éléments clés :
- Les structures en treillis ont remplacé les murs pleins pour optimiser le poids tout en maintenant l'intégrité structurelle
- Des canaux de refroidissement complexes, impossibles à fabriquer de manière conventionnelle, ont été intégrés à la conception
- L'épaisseur de la paroi a été optimisée en fonction des exigences de charge thermique et mécanique
- Plusieurs composants ont été consolidés en un seul assemblage imprimé
Résultats:
- 22% réduction du poids des composants
- 30% amélioration de l'efficacité thermique
- 40% réduction du temps d'assemblage
- Augmentation de 2,5 fois la durée de vie des composants
- Réduction significative de la consommation de carburant et des émissions
Facteurs clés de succès :
- Caractérisation et validation approfondies des matériaux
- Optimisation de la conception itérative grâce à la dynamique des fluides numérique
- Qualification et certification rigoureuses des processus
- Tests et validation post-production complets
Énergie : Échangeur de chaleur spécialisé pour applications nucléaires
Défi:
Un opérateur majeur du secteur de l'énergie nucléaire en France avait besoin d'échangeurs de chaleur spécialisés pour les environnements corrosifs qui ne pouvaient pas être traités de manière adéquate par les méthodes de fabrication conventionnelles en raison d'exigences de géométrie interne complexes.
Solution :
Une société d'ingénierie basée à Paris s'est associée à Metal3DP pour développer une conception d'échangeur de chaleur révolutionnaire exploitant la résistance exceptionnelle à la corrosion de l'Inconel 625 et la liberté de conception de la fabrication additive :
- Les structures internes à surface minimale triplement périodique (TPMS) maximisent la surface tout en minimisant la chute de pression
- L'épaisseur de paroi variable optimise l'utilisation des matériaux tout en garantissant l'intégrité structurelle
- Capteurs intégrés et ports de surveillance pour un contrôle opérationnel amélioré
- La conception modulaire permet une personnalisation en fonction des exigences d'installation spécifiques
Résultats:
- 35% amélioration de l'efficacité du transfert de chaleur
- 45% réduction de l'utilisation de matériaux par rapport aux conceptions conventionnelles
- 60% réduction du délai de livraison des composants spécialisés
- Des capacités de surveillance améliorées auparavant impossibles à mettre en œuvre
- Procédures de maintenance simplifiées grâce à une meilleure accessibilité
Facteurs clés de succès :
- Simulation et modélisation thermique approfondies avant la production
- Protocoles spécialisés de post-traitement et de traitement de surface
- Des tests de qualification rigoureux dans des conditions de fonctionnement réelles
- Documentation détaillée et certification pour les applications nucléaires
Médical : Instrument chirurgical sur mesure pour le CHU de Paris
Défi:
Un important hôpital universitaire parisien avait besoin d'instruments chirurgicaux spécialisés pour des interventions complexes sur la colonne vertébrale qui ne pouvaient pas être traitées de manière adéquate par les méthodes de fabrication conventionnelles.
Solution :
Un fabricant de dispositifs médicaux a utilisé la fabrication additive Inconel 625 pour développer des instruments chirurgicaux personnalisés avec des caractéristiques uniques :
- Conceptions ergonomiques adaptées à des procédures chirurgicales spécifiques
- Canaux de refroidissement intégrés pour la gestion de la température peropératoire
- Géométries personnalisables pour des variations anatomiques spécifiques au patient
- Fonctionnalités de visibilité améliorées pour les procédures mini-invasives
- Caractéristiques de stérilisation améliorées grâce à des conceptions de surface optimisées
Résultats:
- 40% réduction du temps de procédure pour des opérations spécifiques
- Amélioration des résultats chirurgicaux et réduction des complications
- Satisfaction accrue du chirurgien et fatigue réduite
- Capacité à traiter des affections auparavant incurables
- Production rentable en petites séries d'instruments spécialisés
Facteurs clés de succès :
- Une étroite collaboration entre chirurgiens et ingénieurs concepteurs
- Validation rigoureuse de la biocompatibilité et de la stérilisation
- Prototypage itératif et intégration du feedback clinique
- Formation complète et accompagnement à la mise en œuvre
Course automobile : Optimisation des composants du système d'échappement F1
Défi:
Une équipe de Formule 1 basée près de Paris avait besoin de développer un système d'échappement capable de résister à des températures extrêmes tout en minimisant le poids et en optimisant les caractéristiques d'écoulement pour des performances maximales.
Solution :
L'équipe a travaillé avec un fournisseur de services AM spécialisé en métal utilisant la poudre Inconel 625 haute performance de Metal3DP pour créer une conception d'échappement révolutionnaire :
- L'épaisseur de la paroi variait dans tout le composant en fonction de l'analyse de la charge thermique
- Chemin d'écoulement interne complexe optimisé pour une contre-pression réduite
- Les fonctions de bouclier thermique intégrées éliminent les composants séparés
- Texturation de surface appliquée dans des zones stratégiques pour gérer les effets de couche limite
Résultats:
- Réduction de poids du 18% par rapport à la conception précédente
- Gain de 7 chevaux grâce à une meilleure efficacité du flux d'échappement
- 30% amélioration de la gestion thermique
- Élimination des points de défaillance des joints soudés
- Temps de développement réduit de plusieurs mois à quelques semaines
Facteurs clés de succès :
- Simulations numériques approfondies de dynamique des fluides et de thermique
- Protocoles de traitement thermique spécialisés pour les applications de course
- Essais complets sur dynamomètre et sur piste
- Capacité d'itération rapide pour une amélioration continue
Équipement industriel : Corps de vanne sur mesure pour le traitement chimique
Défi:
Une usine de traitement chimique en dehors de Paris avait besoin de corps de vannes spécialisés pour les milieux hautement corrosifs qui présentaient une durabilité exceptionnelle tout en s'adaptant aux contraintes d'espace et aux exigences de débit complexes.
Solution :
En collaboration avec un fournisseur d'équipements industriels, l'usine a mis en œuvre la fabrication additive Inconel 625 pour créer des solutions de vannes personnalisées avec ces caractéristiques :
- Chemins d'écoulement optimisés basés sur la dynamique des fluides numérique
- Caractéristiques intégrées résistantes à l'usure dans les zones à forte érosion
- Assemblage consolidé de 14 composants à 3
- Fonctionnalités de montage et d'interface sur mesure pour les applications de modernisation
- Facilité d'entretien améliorée grâce à des fonctionnalités d'accès améliorées
Résultats:
- 80% réduction des temps d'arrêt dus aux défaillances des vannes
- 25% amélioration de l'efficacité du débit
- 40% réduction des coûts de maintenance
- 50% livraison plus rapide par rapport à la fabrication traditionnelle
- Capacités de surveillance améliorées grâce à des ports de capteurs intégrés
Facteurs clés de succès :
- Analyse détaillée des modes de défaillance dans les conceptions précédentes
- Tests complets de compatibilité des matériaux
- Tests rigoureux de pression et de cycle avant le déploiement
- Documentation détaillée de mise en œuvre et de maintenance
Leçons de mise en œuvre et meilleures pratiques
Au travers de ces diverses applications, plusieurs enseignements cohérents et bonnes pratiques ont émergé pour une mise en œuvre réussie de l'Inconel 625 AM dans les industries parisiennes :
- Reconceptualisation du design
- La plupart des applications réussies ont commencé par reconsidérer complètement les approches de conception plutôt que de simplement reproduire des composants existants
- Une conception qui intègre les capacités uniques de la fabrication additive produit des résultats supérieurs
- Alignement matériau-processus-application
- Les implémentations réussies correspondent soigneusement aux propriétés des matériaux, aux paramètres de traitement et aux exigences de l'application
- Comprendre l’interaction entre ces facteurs est essentiel pour obtenir des résultats optimaux
- Validation complète
- Des tests rigoureux dans des conditions de fonctionnement réelles sont essentiels
- Les propriétés des matériaux et les performances des composants doivent être validées
- Expertise collaborative
- Les équipes interfonctionnelles combinant la conception, la fabrication, la science des matériaux et l'expertise en matière d'application obtiennent des résultats supérieurs
- Les partenariats entre organisations aux capacités complémentaires accélèrent la mise en œuvre
- Cycles d'amélioration continue
- Les implémentations réussies impliquent généralement plusieurs itérations de conception
- La collecte et l'analyse des données favorisent une optimisation continue
Ces études de cas démontrent le potentiel de transformation de la fabrication additive Inconel 625 dans les industries parisiennes lorsqu'elle est mise en œuvre avec une expertise appropriée, des approches méthodiques et des partenariats stratégiques.
6. Solutions avancées en poudre Inconel 625 de Met3dp
Metal3DP Technology s'est imposé comme un fournisseur leader de poudres Inconel 625 spécialisées et de solutions complètes de fabrication additive pour le marché parisien. Grâce à ses capacités avancées de fabrication de poudres et à son expertise technique, Metal3DP propose des matériaux haut de gamme permettant aux fabricants d'obtenir des résultats supérieurs dans des applications exigeantes.
Technologie avancée de fabrication de poudre
Les poudres Inconel 625 de Metal3DP sont produites à l'aide de procédés de fabrication de pointe qui garantissent une qualité constante et des performances exceptionnelles dans les applications de fabrication additive :
1. Technologie de pointe en matière d'atomisation de gaz
Metal3DP utilise des systèmes d'atomisation de gaz exclusifs dotés de plusieurs caractéristiques distinctives :
- Conception de buse unique : Conçu pour produire des particules hautement sphériques avec un minimum de satellites
- Environnement d'atomisation contrôlé : Empêche l'oxydation et la contamination lors de la formation de la poudre
- Contrôle précis du processus : Maintient une distribution granulométrique serrée et une morphologie cohérente
- Systèmes de classification avancés : Assure l'élimination des particules surdimensionnées et des poussières fines
- Surveillance complète de la qualité : Suivi et ajustement des processus en temps réel
2. Technologie PREP (processus d'électrode rotative à plasma)
Pour les applications spécialisées nécessitant une pureté et une sphéricité exceptionnelles, Metal3DP utilise également la technologie PREP avancée :
- Procédé basé sur les électrodes : Commence avec une matière première pré-alliée Inconel 625
- Fusion à l'arc plasma : Crée une formation de gouttelettes contrôlée avec précision
- Séparation par force centrifuge : Produit des particules hautement sphériques
- Environnement sans contamination : Empêche l'absorption d'oxygène et les impuretés
- Caractéristiques de la poudre Premium : Idéal pour les applications aérospatiales et médicales critiques
Caractéristiques distinctives de la poudre
Les poudres Inconel 625 de Metal3DP présentent plusieurs caractéristiques clés qui les distinguent sur le marché :
Propriété | Norme Metal3DP | Moyenne de l'industrie | Bénéfice |
---|---|---|---|
Sphéricité | >95% | 80-90% | Fluidité et densité de tassement améliorées |
Contenu satellite | <2% | 5-10% | Meilleure finition de surface et réduction des défauts |
Fluidité (débit de Hall) | <15 sec/50g | 18-25 sec/50g | Formation de couches plus cohérente |
Densité du robinet | >60% | 50-55% | Densité plus élevée dans les pièces finales |
Pureté chimique | Dépasse la norme ASTM F3056 | Conforme à la norme ASTM F3056 | Propriétés mécaniques supérieures |
Distribution de la taille des particules | D10-D90 : 15-53 µm | Des distributions plus larges | Optimisé pour les procédés L-PBF et SEBM |
Teneur en oxygène | <100 ppm | 150-200 ppm | Meilleures performances à haute température |
Gamme complète de produits
Metal3DP propose une gamme complète de poudres Inconel 625 optimisées pour différents procédés et applications AM :
1. Série MetInconel 625-L
- Optimisé pour les procédés de fusion laser sur lit de poudre (L-PBF)
- Disponible en distributions standard (15-45 µm) et fine (10-30 µm)
- Fluidité améliorée pour un revêtement fiable
- Caractéristiques d'absorption laser optimisées
2. Série MetInconel 625-E
- Spécialement conçu pour les procédés de fusion par faisceau d'électrons (EBM)
- Conductivité électrique optimisée pour l'interaction avec le faisceau d'électrons
- Distribution précise de la taille des particules (45-106 µm)
- Caractéristiques de frittage améliorées dans un lit de poudre
3. Série MetInconel 625-D
- Formulé pour les applications de dépôt d'énergie dirigée (DED)
- Disponible en distributions plus grossières (45-150 µm)
- Excellente fluidité pour les systèmes d'alimentation en poudre
- Optimisé pour des taux de dépôt élevés
4. Série MetInconel 625-SP
- Poudres spécialisées pour des applications industrielles spécifiques
- Compositions personnalisées dans la gamme de spécifications Inconel 625
- Distributions de tailles spécifiques à l'application
- Propriétés améliorées pour des caractéristiques de performance ciblées
Assurance qualité et certification
Metal3DP met en œuvre des mesures de contrôle qualité rigoureuses tout au long du processus de fabrication de la poudre :
Protocoles de test complets :
- Vérification de la composition chimique à l'aide d'ICP-OES et d'autres techniques avancées
- Analyse de la distribution granulométrique par diffraction laser
- Évaluation de la morphologie par microscopie électronique à balayage
- Essais de fluidité utilisant les méthodes Hall Flow et Carney
- Mesures de densité, y compris la densité apparente et la densité tassée
- Détermination de la teneur en oxygène et en azote
- Évaluation de l'étalement et de la formation des couches
Certification et documentation :
- Traçabilité complète des matériaux, de la matière première à la poudre finie
- Certificats de test spécifiques aux lots
- Conformité aux spécifications ASTM F3056 et AMS
- Processus de production certifiés ISO 9001
- Systèmes de gestion de la qualité de niveau aérospatial
Support technique et développement d'applications
Au-delà de la fourniture de poudres Inconel 625 premium, Metal3DP assure un support technique complet aux industriels parisiens :
1. Développement des paramètres du processus
- Optimisation des paramètres d'impression pour des machines et des applications spécifiques
- Ensembles de paramètres personnalisés pour les exigences uniques des composants
- Validation et test de l'efficacité des paramètres
- Documentation et support de mise en œuvre
2. Support d'ingénierie d'application
- Optimisation de la conception pour la fabricabilité AM
- Conseils de sélection de matériaux pour des applications spécifiques
- Recommandations et protocoles de post-traitement
- Assistance aux tests de performance et à la validation
3. Formation et transfert de connaissances
- Formation des opérateurs sur la manipulation et la sécurité des poudres
- Formation en génie des procédés
- Méthodologies de contrôle qualité et de test
- Partage des connaissances spécifiques aux applications
4. Programmes d'amélioration continue
- Optimisation continue des caractéristiques de la poudre
- Mises à jour régulières basées sur les commentaires des clients
- Développement collaboratif pour applications spécialisées
- Partenariats de recherche avec des institutions académiques parisiennes
Témoignages clients avec Metal3DP Inconel 625
Fabricant de composants aérospatiaux :
Un important fournisseur aéronautique de la région parisienne a adopté la poudre Inconel 625-L de Metal3DP pour la production de composants de turbine et a constaté :
- 30% réduction des échecs de construction
- Finition de surface améliorée nécessitant moins de post-traitement
- Propriétés mécaniques plus constantes
- Répétabilité améliorée sur les cycles de production
Spécialiste du secteur de l'énergie :
Un fabricant de composants d'échangeurs de chaleur pour environnements de service sévères a mis en œuvre la poudre Inconel 625-E de Metal3DP et a obtenu :
- Résistance supérieure à la corrosion lors des tests accélérés
- 15% amélioration des performances thermiques
- Variabilité réduite des dimensions critiques
- Exigences de post-traitement simplifiées
Innovateur en matière de dispositifs médicaux :
Une société parisienne de dispositifs médicaux développant des instruments chirurgicaux spécialisés a adopté la poudre Inconel 625-SP de Metal3DP avec ces résultats :
- Performances de biocompatibilité améliorées
- Caractéristiques de surface supérieures après polissage
- Résistance à la fatigue améliorée sous charge cyclique
- Des résultats cohérents pour une production en petits lots
Grâce à ses technologies de poudre avancées, à sa gamme complète de produits et à son support technique exceptionnel, Metal3DP s'est imposé comme un partenaire de confiance pour les industriels parisiens cherchant à maximiser le potentiel de la fabrication additive Inconel 625 pour leurs applications les plus exigeantes. catalogue de produits fournit des informations détaillées sur leur gamme complète de poudres métalliques pour la fabrication additive.
PARTIE 3
7. Considérations techniques lors de l'utilisation de l'Inconel 625 en fabrication additive
La mise en œuvre réussie de la fabrication additive Inconel 625 nécessite une attention particulière à de nombreux aspects techniques tout au long de la chaîne de production. Les fabricants parisiens doivent prendre en compte ces facteurs pour garantir des résultats optimaux et éviter les pièges coûteux.
Caractéristiques et gestion de la poudre
Les propriétés et la manipulation de la poudre Inconel 625 ont un impact significatif sur la qualité d'impression et les performances de la pièce finale :
Propriétés critiques de la poudre :
- Distribution de la taille des particules (PSD)
- Les plages optimales varient selon le processus AM :
- L-PBF : 15-45 μm (D10-D90)
- EBM : 45-106 μm (D10-D90)
- DED : 45-150 μm (D10-D90)
- Des distributions serrées produisent des résultats plus cohérents
- Des fines excessives (<10 μm) peuvent entraîner des problèmes de fluidité et de sécurité
- Les particules surdimensionnées (> D90 spécifié) risquent d'endommager le dispositif de recouvrement et de provoquer des défauts de couche.
- Les plages optimales varient selon le processus AM :
- Morphologie et caractéristiques de l'écoulement
- Les particules sphériques avec un minimum de satellites optimisent la fluidité
- Le débit (Hall Flow) doit être < 15 secondes pour 50 g pour une diffusion optimale
- Densité apparente généralement de 4,2 à 4,6 g/cm³ pour une poudre de qualité
- Le rapport de densité de tassement (rapport de Hausner) < 1,25 indique un bon comportement de tassement.
- Composition chimique
- Teneur en oxygène idéalement <100 ppm pour éviter les défauts d'inclusion d'oxyde
- La teneur en carbone doit être soigneusement contrôlée pour éviter la formation de carbure
- Les oligo-éléments peuvent avoir un impact significatif sur les propriétés mécaniques
- La teneur en humidité doit être minimisée grâce à un stockage et une manipulation appropriés
Gestion du cycle de vie des poudres :
Une gestion efficace de la poudre est essentielle pour des résultats cohérents et une efficacité économique :
- Considérations relatives au stockage :
- Environnement contrôlé avec une humidité relative <40%
- Stabilité de la température entre 15 et 25 °C
- Purge au gaz inerte pour les conteneurs ouverts
- Conteneurs scellés avec déshydratant pour un stockage à long terme
- Protocoles de manipulation :
- Outils et équipements dédiés pour prévenir la contamination croisée
- Mesures antistatiques pour éviter l'agglutination et les dangers
- Équipement de protection individuelle, y compris la protection respiratoire
- Zones de manutention dédiées avec ventilation appropriée
- Recyclage et réutilisation :
- Tamisage pour éliminer les sous-produits et les agglomérations du procédé
- Tests réguliers des propriétés de la poudre recyclée
- Stratégies de mélange de poudre vierge et recyclée
- Nombre maximal d'itérations de recyclage en fonction des exigences de l'application
- Surveillance de l'absorption d'oxygène pendant le recyclage
Optimisation des paramètres de processus
Pour obtenir des résultats optimaux avec l'Inconel 625, il faut un étalonnage minutieux de nombreux paramètres de processus :
Paramètres de la fusion laser sur lit de poudre (L-PBF) :
Paramètres | Gamme typique | Impact sur la construction |
---|---|---|
Puissance du laser | 200-400W | Affecte la taille du bain de fusion et la profondeur de pénétration |
Vitesse de balayage | 600-1200 mm/s | Contrôle l'apport énergétique et la productivité |
Épaisseur de la couche | 20-50μm | Équilibre la résolution et le temps de construction |
Espacement des trappes | 0,08-0,12 mm | Détermine le chevauchement entre les pistes de numérisation |
Stratégie d'analyse | Différents modèles | Influence les contraintes résiduelles et la microstructure |
Température de la plaque de construction | 80-200°C | Réduit les gradients thermiques et la déformation |
Densité énergétique | 50-80 J/mm³ | Paramètre composite affectant la qualité de la fusion |
Paramètres de fusion par faisceau d'électrons (EBM) :
Paramètres | Gamme typique | Impact sur la construction |
---|---|---|
Puissance du faisceau | 300-1500W | Contrôle les caractéristiques du bain de fusion |
Vitesse de balayage | 1000-5000 mm/s | Équilibre l'apport énergétique et la productivité |
Épaisseur de la couche | 50-100 μm | Plus épais que le L-PBF, affecte le taux de construction |
Décalage de la mise au point | 5-20 mA | Ajuste la focalisation du faisceau et la distribution de l'énergie |
Température de préchauffage | 800-1000°C | L'Inconel 625 est essentiel pour éviter les fissures |
Niveau de vide | <10⁻⁵ mbar | Essentiel pour la stabilité du faisceau et la qualité des pièces |
Stratégie d'analyse | Modèles spécialisés | Impact significatif sur les propriétés des matériaux |
Surveillance et contrôle des processus :
Les systèmes de surveillance avancés sont de plus en plus essentiels pour l’assurance qualité :
- Surveillance du bassin de fusion :
- Des caméras à grande vitesse et des photodiodes suivent la dynamique du bain de fusion
- Comparaison en temps réel avec les paramètres établis
- Détection précoce des anomalies de processus
- Documentation pour l'assurance qualité
- Imagerie par couches :
- Les systèmes optiques capturent chaque couche après étalement
- Anomalies du lit de poudre détectées avant la fusion
- Documentation de l'historique de construction pour la traçabilité
- Potentiel de détection automatisée des défauts
- Systèmes de rétroaction de processus :
- Contrôle en boucle fermée ajustant les paramètres en temps réel
- Compensation des variations de processus
- Les systèmes avancés peuvent modifier les paramètres en fonction de l'historique thermique
- Particulièrement précieux pour l'Inconel 625 en raison de sa sensibilité aux conditions thermiques
Exigences en matière de post-traitement
Les pièces en Inconel 625 AM nécessitent généralement plusieurs étapes de post-traitement pour obtenir les propriétés et spécifications finales :
1. Soulagement du stress et traitement thermique
L'Inconel 625 est particulièrement sensible aux contraintes résiduelles lors de la fabrication additive, ce qui rend essentiel un traitement thermique approprié :
- Soulagement du stress :
- Généralement effectué à 800-870°C
- Temps de maintien de 1 à 2 heures
- Refroidissement lent pour éviter d'introduire de nouvelles contraintes
- Souvent réalisée avant le retrait du support
- Recuit de la solution :
- 1080-1150°C pendant 1 à 2 heures
- Trempe à l'eau ou refroidissement rapide à l'air
- Dissout les précipités et homogénéise la microstructure
- Optimise la résistance à la corrosion
- Durcissement par vieillissement (selon l'application) :
- 650-760°C pendant 4 à 16 heures
- Refroidissement par air
- Favorise la précipitation contrôlée pour améliorer la résistance
- Peut réduire légèrement la résistance à la corrosion
2. Traitement de surface et finition
L’obtention de la qualité de surface requise implique souvent plusieurs opérations :
- Suppression du support :
- Découpe mécanique ou électroérosion à fil pour l'enlèvement initial
- Meulage soigneux des points de fixation
- Considérations de conception pour minimiser les besoins de support
- Amélioration de la surface :
- Sablage avec un média en oxyde d'aluminium
- Finition vibratoire pour surfaces accessibles
- Éclaircissement chimique pour les caractéristiques internes complexes
- Polissage électrochimique pour une qualité de surface optimale
- Considérations relatives à l'usinage :
- L'Inconel 625 est difficile à usiner, même lorsqu'il est produit par fabrication additive
- Nécessite des configurations rigides et des outils spécialisés
- Vitesses de coupe inférieures à celles des alliages conventionnels
- Les tolérances sont généralement de 0,5 à 2 mm selon la fonctionnalité
3. Vérification et tests de qualité
Des tests complets valident la qualité et les performances des pièces :
- Vérification dimensionnelle :
- Machines à mesurer tridimensionnelles (MMT) pour géométries externes
- Tomodensitométrie (TDM) pour les caractéristiques internes
- Numérisation 3D pour surfaces complexes de formes libres
- Comparaison avec le modèle CAO et analyse des tolérances
- Essais non destructifs :
- Contrôle par ressuage liquide pour les défauts de surface
- Contrôle par ultrasons des défauts internes
- Inspection par rayons X des composants critiques
- Scanner CT pour une analyse complète des défauts en 3D
- Essais destructifs (échantillonnage) :
- Essais de traction pour les propriétés de résistance
- Essais de dureté pour les propriétés de surface
- Examen métallographique de la microstructure
- Essais de corrosion pour la résistance environnementale
Considérations de conception pour l'Inconel 625 AM
Une mise en œuvre réussie nécessite des approches de conception spécifiquement adaptées au matériau et au processus :
1. Gestion thermique par la conception
Les propriétés thermiques de l'Inconel 625 nécessitent une attention particulière :
- Minimiser les variations de masse thermique :
- Évitez les transitions brusques entre les sections épaisses et fines
- Utiliser des transitions progressives lorsque des changements d'épaisseur sont nécessaires
- Équilibrer l'apport de chaleur à travers la pièce grâce à des sections transversales uniformes
- Envisagez de sectionner les très gros composants pour une meilleure gestion thermique
- Structures de soutien :
- Supports plus substantiels que les autres matériaux en raison des contraintes résiduelles
- Placement stratégique pour gérer la dissipation de la chaleur
- Conception pour l'accessibilité lors du retrait
- Envisagez des fonctionnalités sacrificielles plutôt que des supports traditionnels lorsque cela est possible
- Orientation de la construction :
- Essentiel pour la gestion des gradients thermiques et des contraintes résiduelles
- Prise en compte des propriétés anisotropes dans différentes directions de construction
- Équilibre entre la qualité de surface, les exigences de support et les propriétés mécaniques
- Peut nécessiter plusieurs itérations pour optimiser
2. Optimisation des fonctionnalités pour AM
Certaines caractéristiques de conception nécessitent une attention particulière pour l'Inconel 625 AM :
- Taille minimale des fonctionnalités :
- Parois : épaisseur minimale de 0,4 mm pour une production fiable
- Trous : diamètre minimum de 0,5 mm pour les éléments verticaux
- Broches : diamètre minimum de 0,6 mm pour les éléments autoportants
- Jeux : 0,3 mm minimum pour les ensembles mobiles
- Surplombs et angles autoportants :
- 45° par rapport à l'horizontale est la limite autoportante typique
- Modifications de conception pour éviter les angles < 45° lorsque cela est possible
- Placement de support stratégique où les géométries difficiles sont inévitables
- Prise en compte des exigences de qualité de surface pour les surfaces orientées vers le bas
- Canaux et cavités internes :
- La stratégie d'élimination de la poudre doit être conçue dès le départ
- Diamètre minimum de 2 mm pour une évacuation efficace de la poudre
- Ports d'accès pour réseaux internes complexes
- Construire une planification d'orientation pour minimiser les soutiens internes
3. Conception pour le post-traitement
L'anticipation des exigences de post-traitement lors de la conception améliore les résultats finaux :
- Stock d'usinage :
- Surépaisseur de 0,5 à 2 mm sur les surfaces nécessitant un usinage
- Caractéristiques de référence pour un montage répétable
- Prise en compte de l'accès aux outils et des angles d'approche
- Fonctionnalités d'enregistrement pour les opérations multi-configurations
- Considérations relatives au traitement thermique :
- Conception visant à minimiser la distorsion lors du traitement thermique
- Épaisseur de paroi uniforme dans la mesure du possible pour assurer un chauffage/refroidissement uniforme
- Anticiper les variations dimensionnelles lors du traitement thermique
- Considérez les points de fixation pour les géométries complexes
- Accès à la finition de surface :
- Conception pour l'accessibilité des méthodes de post-traitement
- Tenir compte des chemins d’écoulement des fluides dans les processus vibratoires ou chimiques
- Évitez les volumes piégés qui ne peuvent pas être correctement terminés
- Inclure des fonctionnalités sacrificielles qui peuvent être supprimées après le traitement
En prenant soigneusement en compte ces considérations techniques tout au long de la chaîne de production, les fabricants parisiens peuvent mettre en œuvre avec succès la fabrication additive Inconel 625 pour leurs applications les plus exigeantes. Des entreprises comme Métal3DP fournir un support technique complet pour aider les fabricants à naviguer dans ces considérations complexes et à obtenir des résultats optimaux.
8. Analyse des coûts et retour sur investissement pour les projets AM Inconel 625
La mise en œuvre de la fabrication additive Inconel 625 nécessite une analyse financière rigoureuse pour garantir un retour sur investissement positif. Les fabricants parisiens doivent comprendre l'intégralité de la structure des coûts et de la proposition de valeur pour prendre des décisions éclairées concernant cette approche de fabrication avancée.
Analyse complète de la structure des coûts
Le coût total de la mise en œuvre de l'Inconel 625 AM englobe plusieurs catégories qui doivent être considérées de manière globale :
1. Coûts directs de fabrication
Composante de coût | Gamme typique | Facteurs clés |
---|---|---|
Poudre d'Inconel 625 | 80-150 €/kg | Niveau de qualité, volume d'achat, relation avec les fournisseurs |
Amortissement des machines | 25-75 €/heure | Coût de l'équipement, taux d'utilisation, durée d'amortissement |
Consommation d'énergie | 5-15 €/heure | Type de machine, coûts énergétiques régionaux, paramètres de construction |
Consommation de gaz | 10-25 €/construction | Type de gaz inerte, efficacité du système, durée de construction |
Consommables | 5 à 20 €/construction | Lames de recouvrement, plaques de construction, filtres, produits de nettoyage |
Travail | 30-80 €/heure | Niveau de compétence de l'opérateur, marché du travail, niveau d'automatisation |
Builds échoués | Supplément 5-15% | Maturité des processus, complexité des pièces, systèmes qualité |
2. Coûts de prétraitement
Composante de coût | Gamme typique | Facteurs clés |
---|---|---|
Ingénierie de conception | 70-120 €/heure | Complexité de conception, exigences d'optimisation, expertise |
Ingénierie des procédés | 80-130 €/heure | Développement de paramètres, stratégie de construction, validation de processus |
Préparation des dossiers | 50-90 €/heure | Imbrication de pièces, génération de support, complexité de découpage |
Planification de la qualité | 60-100 €/heure | Exigences en matière de documentation, planification de la vérification, évaluation des risques |
Qualification des matériaux | 500-5 000 €/matériel | Portée des tests, exigences de certification, criticité des applications |
3. Coûts de post-traitement
Composante de coût | Gamme typique | Facteurs clés |
---|---|---|
Suppression du support | 40-80 €/heure | Prise en charge de la complexité, de l'accessibilité et des outils requis |
Traitement thermique | 100-500 €/lot | Exigences du processus, taille des pièces, externalisation ou interne |
Finition de surface | 50-200 €/pièce | Exigences de qualité de surface, complexité géométrique, méthode |
Usinage | 60-120 €/heure | Tolérance des caractéristiques, quantité d'enlèvement de matière, exigences d'outillage |
Vérification de la qualité | 80-150 €/heure | Méthodes d'inspection, exigences en matière de documentation, critères d'acceptation |
4. Coûts indirects et cachés
Ces coûts souvent négligés peuvent avoir un impact significatif sur l’économie globale du projet :
- Exigences relatives aux installations :
- Systèmes de ventilation et de sécurité spécialisés
- Installations de manutention et de stockage de poudre
- Espace équipement de post-traitement
- Systèmes de contrôle environnemental
- Formation et expertise :
- Formation initiale des opérateurs et des ingénieurs
- Développement continu des compétences
- Consultants experts et support technique
- Stratégies de rétention des connaissances
- Développement du système qualité :
- Documentation de validation des processus
- Procédures de test et d'inspection
- Systèmes de traçabilité
- Maintien de la certification
- Intégration commerciale :
- Adaptation du flux de travail
- Intégration de systèmes ERP/MES
- Gestion numérique des stocks
- Éducation des clients sur les capacités de la FA
Comparaison des coûts avec la fabrication conventionnelle
Comprendre les aspects économiques relatifs aux méthodes de fabrication traditionnelles est essentiel pour une application technologique appropriée :
Analyse comparative d'un composant d'échangeur de chaleur complexe :
Élément de coût | Inconel 625 AM | Fabrication conventionnelle | Principales différences |
---|---|---|---|
Coût matériel | €850 | €1,250 | AM réduit le gaspillage de matériaux de 65% |
Fabrication directe | €3,200 | €5,800 | Le conventionnel nécessite un outillage complexe et de multiples configurations |
Post-traitement | €1,300 | €750 | La fabrication additive nécessite généralement plus de post-traitement |
Assurance qualité | €750 | €950 | Avantages conventionnels des protocoles établis |
Délai d'exécution | 2-3 semaines | 8-12 semaines | AM réduit considérablement le délai de mise sur le marché |
Quantité minimale de commande | 1 unité | 5 à 10 unités | AM permet des petits lots économiques |
Flexibilité de la conception | Très élevé | Limitée | La fabrication additive permet une optimisation de la conception impossible de manière conventionnelle |
Coût total (1 unité) | €6,100 | €8,750 | AM offre un avantage de coût 30% |
Coût total (10 unités) | €35,000 | €29,500 | Le conventionnel devient plus économique à des volumes plus élevés |
Analyse du seuil de rentabilité par complexité des composants :
Niveau de complexité | Quantité seuil de rentabilité (AM vs. Conventionnel) | Avantage principal du conducteur |
---|---|---|
Géométrie simple | 5 à 10 unités | Évitement de l'outillage dans la fabrication conventionnelle |
Complexité modérée | 15-25 unités | Économies de matière et fabrication simplifiée |
Haute complexité | 30 à 50 unités | Consolidation de plusieurs pièces et assemblages |
Complexité extrême | 50+ unités ou impossible de manière conventionnelle | Permettre des conceptions auparavant impossibles |
Cadre de calcul du retour sur investissement
Une approche structurée de l'analyse du retour sur investissement permet de justifier les investissements dans l'Inconel 625 AM :
1. Catégories d'investissement de mise en œuvre
Catégorie d'investissement | Description | Gamme typique des entreprises parisiennes |
---|---|---|
Equipement | Machines AM, équipements de post-traitement, systèmes de test | €500,000-2,000,000 |
Préparation de l'installation | Systèmes de sécurité, contrôles environnementaux, services publics | €100,000-300,000 |
Matériaux initiaux | Inventaire des poudres, matériels d'essai, consommables | €30,000-80,000 |
Formation | Formation des opérateurs, enseignement de l'ingénierie, conseil | €50,000-120,000 |
Qualification | Validation des processus, certification des matériaux, documentation | €80,000-200,000 |
Intégration commerciale | Logiciel, adaptation du flux de travail, formation des clients | €40,000-100,000 |
2. Catégories de création de valeur
Catégorie de valeur | Description | Approche de quantification |
---|---|---|
Réduction des coûts directs | Économies de matériaux, efficacité du travail, réduction des stocks | Comparaison des coûts traditionnels et des coûts AM |
Valeur du délai d'exécution | Mise sur le marché plus rapide, coût d'opportunité réduit | Évaluation de la valeur du market timing |
Amélioration des performances | Fonctionnalité, efficacité et durabilité améliorées du produit | Calcul de l'augmentation de la valeur à vie |
Innovation du modèle d'affaires | Capacités de personnalisation, inventaire numérique, production à la demande | Projection de nouvelles sources de revenus |
Atténuation des risques | Résilience de la chaîne d'approvisionnement, gestion de l'obsolescence | Évaluation de la valeur ajustée au risque |
Impact sur la durabilité | Efficacité matérielle, réduction d'énergie, production localisée | Valeur de la tarification du carbone et de la conformité environnementale |
3. Exemple de calcul du retour sur investissement
Pour un équipementier aéronautique parisien de taille moyenne :
Investissement initial :
- Système de fusion sélective par laser : 850 000 €
- Matériel de post-traitement : 150 000 €
- Modifications des installations : 120 000 €
- Formation et qualification : 180 000 €
- Investissement total : 1 300 000 €
Coûts d'exploitation annuels :
- Exploitation et maintenance du système : 180 000 €
- Coûts des matériaux : 240 000 €
- Main d'œuvre (opérateurs et ingénieurs) : 320 000 €
- Qualification et formation continue : 60 000 €
- Coût d'exploitation annuel total : 800 000 €
Avantages annuels :
- Économies sur les coûts de matériel : 380 000 €
- Valeur de réduction du délai de livraison : 250 000 €
- Améliorations des performances : 420 000 €
- Nouvelles opportunités commerciales : 350 000 €
- Bénéfices annuels totaux : 1 400 000 €
Analyse financière :
- Bénéfice annuel net : 600 000 €
- Période de récupération simple : 2,17 ans
- VAN sur 5 ans (taux d'actualisation 8%) : 1 050 000 €
- TRI sur 5 ans : 32%
Considérations sur la valeur stratégique
Au-delà des rendements financiers directs, l’Inconel 625 AM offre une valeur stratégique qui devrait être prise en compte dans les décisions d’investissement :
1. Différenciation concurrentielle
Les industriels parisiens peuvent s'appuyer sur les capacités de l'Inconel 625 AM pour se démarquer :
- Leadership technique :
- Capacité à produire des composants impossibles à produire par des méthodes conventionnelles
- A démontré sa maîtrise des techniques de fabrication avancées
- Réputation d'innovation et de résolution de problèmes
- Positionnement sur le marché :
- Accès à des segments de marché à forte valeur ajoutée nécessitant des capacités avancées
- Concurrence réduite des fabricants conventionnels
- Potentiel de prix premium pour des solutions spécialisées
- Avantage du premier arrivé :
- Établir des normes techniques et des meilleures pratiques
- Développer des connaissances institutionnelles avant les concurrents
- Sécuriser les relations clients clés dans les applications émergentes
2. Valeur d'atténuation des risques
La mise en œuvre de la gestion des actifs offre une réduction des risques précieuse qui mérite d’être prise en compte :
- Résilience de la chaîne d'approvisionnement :
- Dépendance réduite aux fournisseurs de composants spécialisés
- Capacité à produire des pièces de rechange pour les équipements obsolètes
- Réponse plus rapide aux ruptures d'approvisionnement
- Obsolescence technologique :
- Préparation à la transition de l'industrie vers la fabrication numérique
- Adaptabilité aux paradigmes de conception changeants
- Protection contre les pénuries de compétences dans le secteur manufacturier conventionnel
- Réglementation et conformité :
- Préparation à des réglementations environnementales plus strictes
- Capacité à répondre aux certifications industrielles en constante évolution
- Exposition réduite aux perturbations du commerce international
3. Développement des capacités
L’investissement dans l’Inconel 625 AM renforce les capacités organisationnelles :
- Acquisition de connaissances :
- Développement de méthodologies de conception avancées
- Expertise en science des matériaux
- Capacités d'ingénierie des procédés
- Attraction des talents :
- Faire appel à des talents d'ingénierie hautement qualifiés
- Amélioration de la marque employeur en tant que leader technologique
- Création de rôles techniques à haute valeur ajoutée
- Culture de l'innovation :
- Démonstration d'engagement envers les technologies de pointe
- Opportunités de collaboration interfonctionnelle
- Fondation pour les pratiques d'amélioration continue
Stratégies de mise en œuvre et de mise à l'échelle
La mise en œuvre réussie de l'Inconel 625 AM suit généralement une approche par étapes pour optimiser le retour sur investissement :
1. Modèles de mise en œuvre progressive
Les fabricants parisiens adoptent généralement l’une de ces voies de mise en œuvre :
- Partenariat avec les fournisseurs de services d'abord :
- Projets initiaux externalisés auprès de prestataires spécialisés
- Composante de transfert de connaissances dans les accords de service
- Renforcement progressif des capacités avant l'investissement en équipement
- Un investissement initial plus faible mais un développement des capacités plus lent
- Développement d'applications ciblées :
- Identification d'applications spécifiques à haute valeur ajoutée
- Investissement ciblé sur ces cas d'utilisation limités
- Champ d'application élargi à mesure que l'expertise se développe
- Approche équilibrée du risque et du renforcement des capacités
- Investissement à pleine capacité :
- Investissement initial complet en équipement et en expertise
- Développement rapide des capacités
- Risque initial plus élevé mais rendements potentiels plus rapides
- Convient aux organisations disposant déjà d'une expertise en AM
2. Considérations relatives à la mise à l'échelle
À mesure que la mise en œuvre mûrit, les stratégies de mise à l’échelle doivent prendre en compte :
- Extension de l'application :
- Identification systématique de composants supplémentaires appropriés
- Analyse de la valeur pour chaque application potentielle
- Priorisation basée sur des facteurs financiers et stratégiques
- Développement continu de business cases
- Gestion des capacités :
- Optimisation du volume de construction pour une utilisation maximale
- Prise en compte du fonctionnement en plusieurs équipes
- Décisions équilibrées de fabrication et d'achat pour les pics de charge
- Sélection stratégique d'équipements pour une flexibilité de production
- Intégration organisationnelle :
- Développement de capacités de conception spécifiques à la FA
- Intégration avec les flux de fabrication conventionnels
- Élargissement du programme de formation
- Mise en œuvre des systèmes de gestion des connaissances
Grâce à une analyse complète des coûts, un calcul détaillé du retour sur investissement et une prise en compte de la valeur stratégique, les industriels parisiens peuvent prendre des décisions éclairées quant à la mise en œuvre de la fabrication additive Inconel 625. Cette approche méthodique garantit l'alignement des investissements sur les objectifs commerciaux et une rentabilité optimale.
9. FAQ sur la fabrication additive Inconel 625
Informations générales sur l'Inconel 625 AM
Q : Qu'est-ce qui rend l'Inconel 625 particulièrement adapté à la fabrication additive ?
R : L'Inconel 625 est particulièrement bien adapté à la fabrication additive en raison de plusieurs caractéristiques clés :
- Excellente soudabilité, ce qui se traduit par une bonne aptitude au traitement dans les procédés AM par fusion de poudre
- Haute résistance à la fissuration thermique, réduisant les échecs de fabrication
- Propriétés mécaniques exceptionnelles à l'état construit
- Résistance exceptionnelle à la corrosion maintenue grâce au processus AM
- Bonnes caractéristiques de recyclage de la poudre, améliorant la viabilité économique
Ces propriétés en font l’un des superalliages les plus largement adoptés dans la fabrication additive métallique, en particulier pour les applications nécessitant des performances exceptionnelles dans des environnements difficiles.
Q : Comment les propriétés de l’Inconel 625 produit par AM se comparent-elles à celles des versions fabriquées de manière conventionnelle ?
R : L'Inconel 625 produit par AM présente généralement :
- Résistance à la traction : Souvent 5-15% plus élevé que le matériau forgé en raison d'une microstructure plus fine
- Limite d'élasticité : Généralement 10-20% plus élevé dans l'état tel que construit
- Élongation : Généralement comparable ou légèrement inférieur (30-40% contre 40-50% pour le forgé)
- Résistance à la fatigue : Potentiellement inférieur sans post-traitement approprié en raison de la rugosité de la surface
- Microstructure : Structure dendritique plus fine avec des motifs de solidification directionnelle
- Anisotropie : Les propriétés mécaniques peuvent varier de 5-15% selon l'orientation de la construction
- Résistance à la corrosion : Généralement équivalent après un traitement thermique approprié
Avec un post-traitement approprié, l'Inconel 625 produit par AM peut égaler ou dépasser les matériaux conventionnels dans la plupart des applications, tout en offrant des libertés de conception impossibles avec la fabrication traditionnelle.
Q : Quelles sont les applications typiques de l'Inconel 625 AM à Paris ?
A : En région parisienne, l'Inconel 625 AM est fréquemment utilisé dans :
- Aérospatiale :
- Composants de combustion pour moteurs d'avion
- Échangeurs de chaleur et systèmes de gestion thermique
- Composants structurels pour zones à haute température
- Pièces de réparation et de remplacement pour les systèmes existants
- L'énergie :
- Composants de turbines à gaz
- Applications des échangeurs de chaleur
- Composants de l'industrie nucléaire
- Équipement d'extraction de pétrole et de gaz
- Automobile/Course :
- Systèmes d'échappement de Formule 1 et de sport automobile
- Composants du turbocompresseur
- Capteurs haute température spécialisés
- Équipement de test pour conditions extrêmes
- Traitement chimique :
- Composants de réacteur pour environnements corrosifs
- Corps de vannes spécialisés et équipements de contrôle de débit
- Échangeurs de chaleur pour fluides agressifs
- Structures de soutien aux catalyseurs
- Médical :
- Instruments chirurgicaux spécialisés
- Dispositifs médicaux sur mesure
- Équipement de recherche pour conditions extrêmes
- Composants de l'équipement de stérilisation
Questions techniques sur la mise en œuvre
Q : Quels sont les paramètres clés pour une impression réussie avec l’Inconel 625 ?
R : Une impression réussie avec l'Inconel 625 repose généralement sur ces paramètres critiques :
Pour la fusion laser sur lit de poudre (L-PBF) :
- Puissance du laser : 285-350 W optimal pour la plupart des systèmes
- Vitesse de numérisation : 900-1000 mm/s pour un équilibre entre qualité et productivité
- Épaisseur de la couche : Norme 30-40 μm pour la plupart des applications
- Espacement des hachures : 0,10-0,12 mm pour un chevauchement optimal
- Température de la plaque de construction : 150-200°C pour réduire les contraintes résiduelles
- Densité énergétique : Plage optimale de 60 à 75 J/mm³ pour une densité complète
- Stratégie de numérisation : Motif en damier ou rotatif pour réduire les contraintes résiduelles
Pour la fusion par faisceau d'électrons (EBM) :
- Puissance du faisceau : 600-1200 W selon les exigences de fonctionnalités
- Vitesse de numérisation : 2000-4500 mm/s ajusté en fonction du type de fonction
- Épaisseur de la couche : Norme 50-75 μm
- Température de préchauffage : 900-950°C critique pour la prévention des fissures
- Décalage de mise au point : 10-15 mA pour des caractéristiques de faisceau optimales
- Stratégie de numérisation : Approches multifaisceaux spécialisées pour plus d'efficacité
Ces paramètres peuvent nécessiter des ajustements en fonction de l’équipement spécifique, des caractéristiques de la poudre et de la géométrie des composants.
Q : Quels sont les défis les plus courants lors de la mise en œuvre de l’Inconel 625 AM et comment peuvent-ils être résolus ?
A : Les défis courants et leurs solutions incluent :
- Contraintes résiduelles et distorsion
- Solution : Optimiser l'orientation de la construction, mettre en œuvre des structures de support appropriées, utiliser des plates-formes de construction chauffées, effectuer un soulagement des contraintes en cours de processus et développer des cycles de traitement thermique appropriés.
- Rugosité de surface
- Solution : Optimiser les paramètres de processus pour les surfaces en aval, mettre en œuvre des méthodes de post-traitement appropriées (électropolissage, finition vibratoire) et concevoir l'accessibilité des opérations de finition.
- Porosité et défauts
- Solution : Utilisez de la poudre de haute qualité provenant de fournisseurs réputés comme Métal3DP, mettre en œuvre des protocoles rigoureux de gestion des poudres, optimiser les paramètres du processus grâce à des tests de construction et utiliser des systèmes de surveillance en cours de processus.
- Variation des propriétés des matériaux
- Solution : Normaliser les paramètres de processus, mettre en œuvre des systèmes de qualité complets, effectuer des tests de matériaux réguliers et tenir compte de l'anisotropie dans la conception.
- Complexité du post-traitement
- Solution : Concevez des pièces en tenant compte du post-traitement, développez des flux de travail de post-traitement standardisés, investissez dans des équipements spécialisés et collaborez avec des spécialistes du post-traitement.
- Gestion des coûts
- Solution : Mettre en œuvre des protocoles de recyclage de poudre, optimiser l’imbrication pour une efficacité de fabrication optimale, identifier des applications à haute valeur ajoutée et envisager des approches de fabrication hybrides.
Q : Quelles étapes de traitement thermique et de post-traitement sont recommandées pour les pièces Inconel 625 AM ?
R : Le flux de travail de post-traitement recommandé comprend généralement :
- Soulagement du stress (obligatoire)
- 870°C pendant 1 heure
- Refroidissement par four ou par argon
- Effectué avant le retrait du support pour éviter toute distorsion
- Pressage isostatique à chaud (HIP) (pour les applications critiques)
- 1120°C à 100-150 MPa pendant 3-4 heures
- Élimine la porosité interne
- Améliore les performances en fatigue de 30-40%
- Recuit de mise en solution
- 1080°C pendant 1 heure
- Trempe à l'eau
- Homogénéise la microstructure et dissout les phases indésirables
- Traitements de surfaces
- Mécanique : Sablage (oxyde d'aluminium, 100-150 μm)
- Chimie : Électropolissage en solutions spécialisées
- Mécanique + Chimique : Finition vibratoire suivie d'un brillantage chimique
- Usinage : Surfaces critiques avec exigences dimensionnelles
- Vérification de la qualité
- Contrôle dimensionnel : CMM ou numérisation 3D
- CND : Inspection par ressuage, par ultrasons ou par rayons X
- Métallurgie : Évaluation des échantillons pour la microstructure et les propriétés
- Tests de performance : validation spécifique à l'application
Le protocole spécifique doit être adapté aux exigences de l’application et aux normes industrielles pertinentes.
Questions économiques et commerciales
Q : Quelle est la structure de coût typique des pièces Inconel 625 AM à Paris ?
R : La structure des coûts des pièces en Inconel 625 AM à Paris se décompose généralement comme suit :
Composante de coût | Pourcentage du total | Notes |
---|---|---|
Matériau (poudre) | 15-25% | Dépend de la densité de la pièce et de l'efficacité du recyclage de la poudre |
Coûts d'exploitation des machines | 25-35% | Comprend l'amortissement, l'énergie, le gaz et les consommables |
Travail | 15-20% | Comprend le fonctionnement, la configuration et la surveillance de la machine |
Post-traitement | 15-25% | Très variable en fonction des exigences de finition |
Assurance qualité | 5-15% | Cela dépend des exigences de certification et du secteur d'activité |
Conception et ingénierie | 5-10% | Plus élevé pour les conceptions optimisées complexes |
Frais généraux et administration | 10-15% | Comprend les coûts des installations et les opérations commerciales |
Pour un composant aérospatial typique pesant 2 kg, les coûts totaux à Paris varient entre 1 800 et 3 500 € selon la complexité, la quantité et les exigences de certification.
Q : À quoi ressemble généralement le calendrier de retour sur investissement pour la mise en œuvre de l’Inconel 625 AM ?
R : Les délais de retour sur investissement varient considérablement en fonction de l'approche de mise en œuvre et de l'application, mais suivent généralement les modèles suivants :
- Approche Service Bureau (aucun investissement en équipement)
- Retour sur investissement immédiat possible pour les applications à forte valeur ajoutée et à faible volume
- Seuil de rentabilité typique sur les 5 à 10 premiers projets pour les composants complexes
- Limité aux applications présentant des avantages évidents en termes de coût ou de performances
- Mise en œuvre interne ciblée (machine unique)
- 18 à 30 mois pour atteindre le seuil de rentabilité de l'investissement en capital
- Flux de trésorerie positif généralement atteint dans les 12 mois
- Retour sur investissement complet accéléré grâce à l'identification des applications à forte valeur ajoutée
- Mise en œuvre complète de la FA (technologies multiples)
- 24 à 48 mois pour obtenir un retour sur investissement complet
- Rendements positifs progressifs à mesure que les capacités mûrissent
- Les avantages stratégiques dépassent souvent les rendements financiers directs
Les facteurs clés qui accélèrent le retour sur investissement comprennent :
- Se concentrer initialement sur les applications impossibles à fabriquer de manière conventionnelle
- Identifier les cas d'utilisation à forte valeur ajoutée avec des avantages de performance significatifs
- Tirer parti de l'optimisation de la conception pour réduire les matériaux et le poids
- Développer des processus reproductibles qui minimisent l'intervention de l'opérateur
- Créer un portefeuille d'applications sur plusieurs gammes de produits
Q : Quelles sont les considérations de propriété intellectuelle pour l'Inconel 625 AM en France ?
A : Les principales considérations en matière de propriété intellectuelle dans le contexte français comprennent :
- Protection par brevet
- Les paramètres de processus peuvent être brevetables s'ils sont nouveaux et non évidents
- Les conceptions optimisées pour la fabrication additive peuvent bénéficier d'une protection par brevet
- Les compositions de matériaux personnalisées peuvent bénéficier d'une protection par brevet
- Le système de brevets français suit les normes de la Convention sur les brevets européens
- Secrets commerciaux
- Les ensembles de paramètres de processus sont souvent mieux protégés en tant que secrets commerciaux
- Procédures de manutention des matériaux et protocoles de recyclage
- Techniques de post-traitement personnalisées
- La loi française prévoit une forte protection du secret des affaires en vertu de la directive européenne 2016/943
- Droits de conception
- Les droits de conception non enregistrés sont automatiques mais limités à 3 ans
- Les dessins et modèles communautaires enregistrés offrent une protection de 25 ans
- Les données de numérisation 3D des pièces AM peuvent avoir des implications en matière de droits d'auteur
- Protections contractuelles
- Propriété des ensembles de paramètres par le client ou le fabricant
- Délimitation claire de la propriété de la conception dans les accords de service
- Dispositions de confidentialité pour les spécifications des poudres et les détails de traitement
- Exigences de sécurité des données pour les fichiers de conception numérique
- Conformité réglementaire
- Exigences en matière de marquage CE pour les pièces d'utilisation finale
- Exigences en matière de documentation pour les industries réglementées
- Traçabilité des matériaux et enregistrements de validation des processus
- Conformité au RGPD pour les données de fabrication numérique
Travailler avec un conseiller juridique expérimenté et familier avec la législation sur la propriété intellectuelle et le droit français de la propriété intellectuelle est essentiel pour une protection adéquate des actifs intellectuels précieux.
Questions spécifiques à l'industrie
Q : Comment la certification des pièces Inconel 625 AM est-elle gérée dans les applications aérospatiales ?
A : La certification aérospatiale des pièces AM en Inconel 625 en France suit généralement ce cadre :
- Environnement réglementaire
- Les réglementations de l'AESA (Agence européenne de la sécurité aérienne) s'appliquent
- Exigences spécifiques définies dans la partie 21 de l'EASA
- Exigences supplémentaires des maîtres d’œuvre (Airbus, Safran, etc.)
- Certification des processus souvent via Nadcap (National Aerospace and Defense Contractors Accreditation Program)
- Qualification des matériaux
- La poudre doit répondre aux spécifications des matériaux aérospatiaux
- Tests approfondis des propriétés mécaniques et chimiques
- Documentation du contrôle statistique des processus
- Tests et certification par lots
- Qualification des processus
- Validation détaillée des paramètres du processus
- Production d'éprouvettes et de pièces de démonstration
- Documentation des contrôles et de la surveillance des processus
- Établissement de limites de variance acceptables
- Qualification des pièces
- Validation de la conception par des tests et des analyses
- Inspection et approbation du premier article
- Documentation détaillée du post-traitement
- Validation des essais non destructifs
- Exigences du système qualité
- Certification AS9100D généralement requise
- Traçabilité des matériaux de la poudre à la pièce finie
- Surveillance et documentation de la construction
- Méthodologies d'inspection validées
Le processus de certification prend généralement 12 à 18 mois pour une nouvelle demande, avec des coûts allant de 100 000 à 300 000 € selon la complexité.
Q : Comment les industriels parisiens intègrent-ils l'Inconel 625 AM aux procédés de fabrication traditionnels ?
A : Les industriels parisiens mettent en œuvre plusieurs approches de fabrication hybrides :
- Stratégie d'application sélective
- Utiliser la FA uniquement pour les fonctionnalités les plus complexes
- Combinaison avec la fabrication conventionnelle pour des géométries plus simples
- Exemple : composants internes complexes AM joints à des boîtiers fabriqués de manière traditionnelle
- Combinaisons additives-soustractives
- AM pour créer des formes proches du filet
- Usinage de précision pour les interfaces et fonctionnalités critiques
- Intégré dans des cellules de fabrication uniques dans des installations de pointe
- Temps de configuration réduit grâce à des fixations spécialisées pour les pièces AM
- Applications de réparation et d'amélioration
- Composants conventionnels améliorés avec des fonctionnalités fabriquées de manière additive
- Réparation de composants conventionnels par dépôt d'énergie dirigée
- Personnalisation de composants standards avec des fonctionnalités ajoutées par AM
- Particulièrement utile pour le support des équipements existants
- Intégration de la fabrication numérique
- Fil numérique reliant la conception, la simulation, la fabrication additive et les processus traditionnels
- Systèmes de qualité unifiés intégrant plusieurs méthodes de fabrication
- Approches partagées de métrologie et d'inspection
- Cadres communs de spécification et de test des matériaux
- Optimisation du flux de travail
- Traitement parallèle des composants AM et conventionnels
- Planification de la production synchronisée
- Systèmes unifiés d'inventaire et de logistique
- Programmes de formation intégrés couvrant plusieurs technologies de fabrication
Les principaux fabricants parisiens commencent généralement par des applications ciblées tout en développant des stratégies d'intégration complètes pour une mise en œuvre à plus long terme.
Q : Quelles évolutions futures sont attendues pour l'Inconel 625 AM à Paris ?
A : L'écosystème parisien Inconel 625 AM devrait évoluer dans plusieurs directions passionnantes :
- Développements de matériaux avancés
- Compositions d'Inconel 625 modifiées optimisées spécifiquement pour la fabrication additive
- Variantes nano-renforcées pour des propriétés améliorées
- Formulations de poudre spécifiques au processus avec une fluidité améliorée et une teneur en oxygène réduite
- Capacités multi-matériaux combinant l'Inconel 625 avec des alliages compatibles
- Innovations de procédés
- Chambres de construction à température plus élevée pour réduire les contraintes résiduelles
- Systèmes multi-lasers pour une productivité accrue
- Surveillance in situ intégrée avec contrôle en boucle fermée
- Procédés hybrides combinant des approches par lit de poudre et par énergie dirigée
- Extension de l'application
- Adoption accrue dans les applications de l'énergie nucléaire et de l'hydrogène
- Utilisation accrue dans les dispositifs médicaux spécialisés
- Expansion dans les infrastructures civiles pour les environnements extrêmes
- Croissance de l'outillage personnalisé pour les processus de fabrication complexes
- Évolution de la structure de l'industrie
- Intégration plus étroite entre les fournisseurs de poudre et les fabricants de machines
- Prestataires de services de post-traitement spécialisés
- Centres d'excellence AM spécifiques à l'industrie
- Réseaux collaboratifs partageant des équipements et des expertises spécialisés
- Développements en matière d'éducation et de main-d'œuvre
- Programmes d'ingénierie spécialisés en FA dans les universités parisiennes
- Partenariats de recherche industrie-université axés sur l'Inconel 625
- Programmes de certification technique pour les opérateurs AM
- Programmes de formation croisée pour les experts en fabrication conventionnelle
- Progrès en matière de réglementation et de normes
- Protocoles de certification harmonisés dans tous les secteurs
- Spécifications de poudre normalisées pour les applications AM
- Méthodologies de test unifiées pour les superalliages produits par fabrication additive
- Cadres de certification numérique exploitant les données de surveillance des processus
Des entreprises comme Métal3DP sont à l'avant-garde de ces développements, avec leur technologie de poudre avancée et leur gamme complète méthodes d'impression fournissant les bases d’une innovation continue dans la fabrication additive Inconel 625.
Conclusion : Adopter l'avenir de la fabrication avec l'Inconel 625 AM
L'adoption de la fabrication additive Inconel 625 représente une opportunité concurrentielle significative pour les industriels parisiens des secteurs de l'aéronautique, de l'énergie, du médical et de l'industrie. En combinant les propriétés exceptionnelles de ce superalliage polyvalent avec la liberté de conception offerte par les procédés de fabrication additive avancés, les entreprises avant-gardistes peuvent atteindre des performances, une efficacité et une innovation sans précédent.
À mesure que la technologie progresse, sa mise en œuvre réussie nécessitera une attention particulière au choix des matériaux, à l'optimisation des procédés, à la méthodologie de conception et à la stratégie commerciale. Les entreprises qui développeront des compétences complètes en fabrication additive Inconel 625 seront bien placées pour prendre la tête des secteurs manufacturiers à forte valeur ajoutée et relever les défis d'ingénierie les plus exigeants du XXIe siècle.
Pour les fabricants souhaitant explorer les possibilités de la fabrication additive Inconel 625, s'associer à des fournisseurs de matériaux expérimentés comme Metal3DP constitue une voie de réussite éprouvée. Grâce à sa technologie de poudre avancée, son expertise technique et son accompagnement complet, Metal3DP permet aux fabricants parisiens de tirer pleinement parti de cette approche de fabrication transformatrice.
Pour en savoir plus sur la mise en œuvre de la fabrication additive Inconel 625 dans vos opérations, visitez Site Web de Metal3DP pour des informations détaillées sur leurs produits en poudre, leurs services techniques et leur support de développement d'applications.
Partager sur
MET3DP Technology Co. est un fournisseur de premier plan de solutions de fabrication additive dont le siège se trouve à Qingdao, en Chine. Notre société est spécialisée dans les équipements d'impression 3D et les poudres métalliques de haute performance pour les applications industrielles.
Articles connexes
À propos de Met3DP
Mise à jour récente
Notre produit
CONTACTEZ-NOUS
Vous avez des questions ? Envoyez-nous un message dès maintenant ! Nous répondrons à votre demande avec toute une équipe dès réception de votre message.
Obtenir les informations de Metal3DP
Brochure du produit
Obtenir les derniers produits et la liste des prix
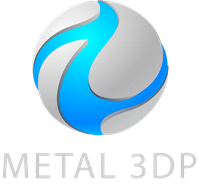
Poudres métalliques pour l'impression 3D et la fabrication additive