3D Printing Injection Mold Inserts with Maraging Steel
Table des matières
Revolutionizing Tooling: An Introduction to 3D Printed Maraging Steel Injection Mold Inserts
Injection molding remains a cornerstone of mass production, enabling the creation of complex plastic parts with remarkable speed and repeatability. However, the efficiency and quality of the injection molding process are heavily reliant on the design and performance of the mold itself, particularly the mold inserts. Traditionally, manufacturing these inserts involves subtractive methods like CNC machining, which, while precise, face limitations in terms of geometric complexity, cooling efficiency, and lead times. The quest for faster cycle times, improved part quality, and greater design freedom has led manufacturers to explore innovative solutions, with impression 3D de métaux (Additive Manufacturing – AM) emerging as a transformative technology for tooling applications.
Specifically, the use of métal Impression 3D for injection mold inserts, especially utilizing high-performance materials like acier maraging, represents a significant leap forward. These inserts are critical components within an injection mold, shaping specific features of the final plastic part and playing a crucial role in the mold’s thermal management. By leveraging AM, manufacturers can create mold inserts with intricate internal structures, most notably conformal cooling channels, which are impossible or prohibitively expensive to produce using traditional methods.
What are Conformal Cooling Channels?
Unlike conventional straight-drilled cooling lines, conformal cooling channels follow the complex contours of the mold cavity or core surface. This proximity allows for more uniform and efficient heat extraction from the molten plastic, leading to several key benefits:
- Reduced Cycle Times: Faster cooling translates directly to shorter overall cycle times, significantly boosting production throughput.
- Amélioration de la qualité des pièces : Uniform cooling minimizes warping, sink marks, and residual stresses in the molded part, leading to higher dimensional accuracy and better surface finish.
- Liberté de conception accrue : Complex part geometries that were previously difficult to cool effectively can now be molded with greater confidence.
Why Maraging Steel?
Maraging steels, such as the widely used 1.2709 (MS1) grade, M300, and even AM-compatible versions of traditional tool steels like H13, are exceptionally well-suited for 3D printing mold inserts. Their key advantages include:
- Résistance et dureté élevées : After appropriate heat treatment, maraging steels achieve excellent hardness and wear resistance, crucial for enduring the rigors of repeated injection cycles.
- Good Weldability and Machinability: This simplifies post-processing steps, allowing for hybrid manufacturing approaches where critical surfaces are finished conventionally.
- Excellente imprimabilité : These alloys generally exhibit good behavior during laser powder bed fusion (LPBF) or electron beam melting (EBM) processes, enabling the creation of dense, high-resolution parts.
- Simple Heat Treatment: Maraging steels typically require a relatively low-temperature aging heat treatment to achieve full hardness, minimizing the risk of distortion compared to the quenching and tempering needed for conventional tool steels.
This convergence of advanced additive manufacturing techniques and high-performance materials like maraging steel is not just an incremental improvement; it’s a paradigm shift in tooling design and manufacturing. It empowers engineers and procurement managers in industries like aerospace, automotive, medical, and industrial manufacturing to rethink mold design, optimize production processes, and gain a competitive edge. Companies specializing in industrial 3D printing solutions and materials, like Met3dp, are at the forefront of this revolution, providing the technology and expertise needed to unlock the full potential of additive manufacturing for tooling. As we delve deeper, we will explore the specific applications, benefits, materials, and considerations involved in successfully implementing 3D printed maraging steel injection mold inserts.
Applications & Industries: Where are 3D Printed Mold Inserts Deployed?
The unique advantages offered by 3D printed injection mold inserts, particularly those featuring conformal cooling and made from robust materials like maraging steel, have led to their adoption across a diverse range of demanding industries. The ability to optimize cooling, handle complex geometries, and shorten lead times makes this technology invaluable where efficiency, precision, and speed are paramount. Procurement managers and engineering leads seeking competitive advantages are increasingly turning to additive manufacturing tooling suppliers for these advanced solutions.
Here’s a breakdown of key application areas and industries benefiting from 3D printed mold inserts:
1. Automotive Industry:
- Applications : Engine components, interior trim parts (dashboards, consoles), exterior lighting lenses, intricate connectors, under-hood components.
- Avantages :
- Cycle Time Reduction: High-volume production demands efficiency. Conformal cooling significantly cuts cycle times for complex parts, boosting throughput for Tier 1 suppliers and OEMs.
- Improved Quality: Uniform cooling reduces warpage in large or complex parts like dashboards, leading to better fit and finish and lower scrap rates.
- Rapid Prototyping & Bridge Tooling: AM allows for faster creation of prototype molds or bridge tooling for low-volume runs or testing phases before committing to expensive hard tooling.
- Réduction du poids : Optimized cooling can sometimes allow for thinner wall sections in plastic parts without compromising quality.
- Focus B2B : Automotive suppliers seek reliable rapid tooling solutions and partners capable of delivering durable automotive mold inserts with consistent quality and performance.
2. Medical Device Industry:
- Applications : Surgical instrument handles, diagnostic device housings, drug delivery system components (e.g., inhalers, auto-injectors), disposable medical consumables, microfluidic devices.
- Avantages :
- Géométries complexes : Medical devices often feature intricate designs and miniaturized components. AM excels at creating inserts for these complex shapes.
- High Precision & Tight Tolerances: Conformal cooling ensures dimensional stability, crucial for functional medical parts and meeting stringent regulatory requirements.
- Compatibilité des matériaux : Inserts can be printed from materials suitable for molding medical-grade polymers.
- Une mise sur le marché plus rapide : Accelerating the tooling phase is critical in the fast-paced medical innovation cycle.
- Focus B2B : Medical device tooling requires suppliers with expertise in precision manufacturing, stringent quality control, and often, material certifications.
3. Consumer Goods & Electronics:
- Applications : Housings for electronics (smartphones, laptops, wearables), appliance components, cosmetic packaging, complex toy parts, power tool casings.
- Avantages :
- Aesthetic Quality: Improved cooling leads to better surface finish and fewer cosmetic defects (like sink marks) on visible parts.
- Complexité de la conception : Enables intricate features, textures, and brand elements to be incorporated directly into the mold.
- Faster Product Cycles: Helps brands bring new designs and products to market more quickly.
- Focus B2B : Manufacturers in this sector look for consumer goods manufacturing tooling solutions that offer both aesthetic quality and production efficiency, often requiring quick turnaround times from tooling suppliers.
4. Industrial Manufacturing & Components:
- Applications : Housings for sensors and control units, connectors, fluid handling components, specialized jigs and fixtures inserts.
- Avantages :
- Durabilité : Maraging steel inserts offer long tool life for demanding industrial applications.
- Amélioration des performances : Optimized cooling can improve the performance and lifespan of molded industrial parts subjected to thermal or mechanical stress.
- Customization & Low Volume: Efficiently produces tooling for specialized or low-volume industrial components.
- Focus B2B : Industrial buyers need robust, reliable tooling solutions and often seek wholesale mold components or partnerships with manufacturers offering comprehensive industrial 3D printing services.
Specific Use Cases Enabled by AM Inserts:
- Conformal Cooling: As discussed, this is the primary driver, enabling faster cycles and better quality across all industries.
- Géométries complexes : Inserts for parts with undercuts, thin walls, sharp corners, or organic shapes that are difficult to machine conventionally.
- Hot Spot Elimination: Targeting specific areas of the mold prone to overheating, improving local cooling efficiency.
- Venting Solutions: Integrating complex venting paths directly into the insert to release trapped gases during injection, preventing defects.
- Hybrid Molds: Combining AM inserts for complex sections with traditionally machined mold bases for cost-effectiveness.
- Rapid Tooling / Bridge Tooling: Creating functional molds quickly for testing, validation, or short production runs while main tooling is being manufactured.
The versatility and proven benefits of 3D printed mold inserts, especially when produced using high-strength maraging steels, make them a critical tool for manufacturers seeking to optimize their injection molding operations. Partnering with an experienced additive manufacturing tooling provider ensures access to the necessary expertise and technology to leverage these advantages effectively.
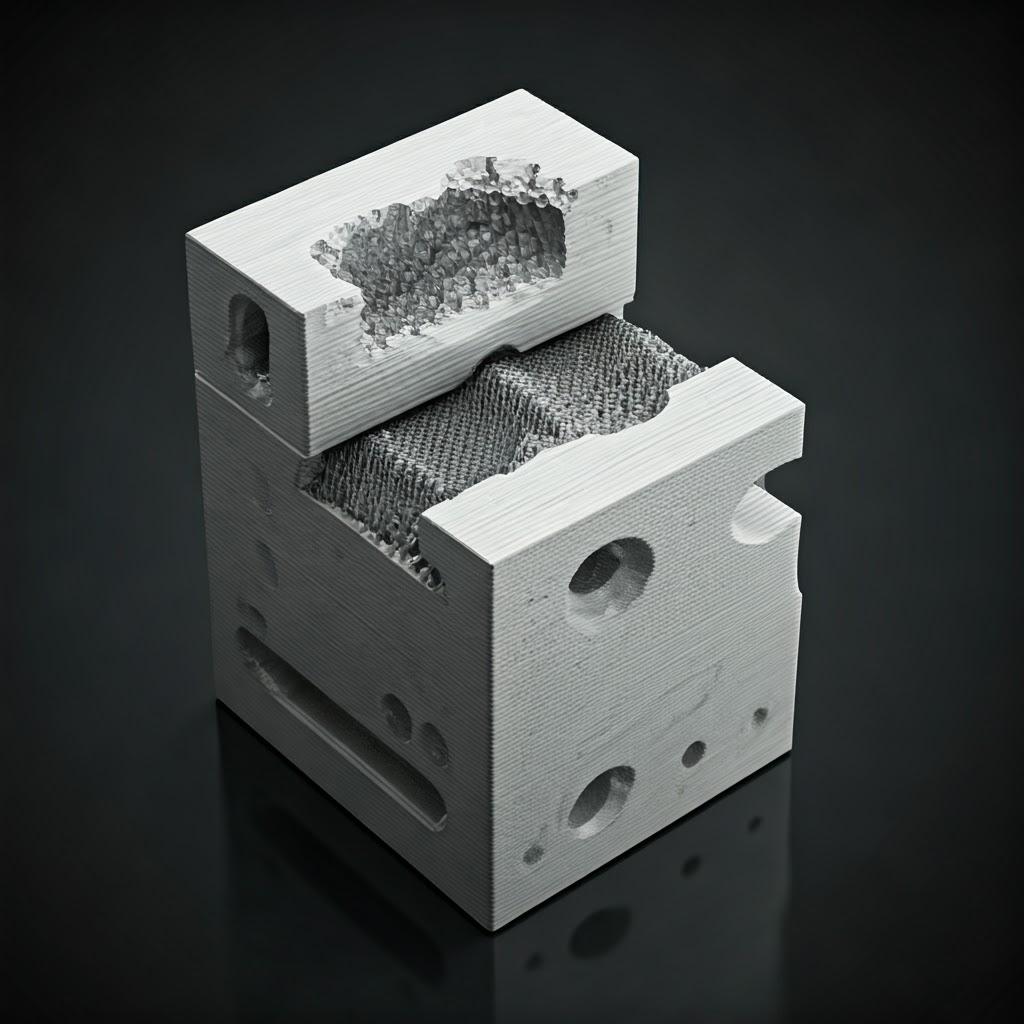
The Additive Advantage: Why Choose Metal 3D Printing for Your Mold Inserts?
While traditional CNC machining has long been the standard for creating injection mold inserts, metal additive manufacturing offers compelling advantages, particularly for complex designs and applications where thermal efficiency is critical. For engineers designing molds and procurement managers sourcing tooling, understanding these benefits is key to making informed decisions and achieving significant improvements in production outcomes. Opting for impression 3D de métaux for mold inserts isn’t just about adopting new technology; it’s about unlocking tangible performance gains and cost efficiencies.
Let’s compare AM with traditional machining across key parameters for mold insert production:
Comparison: Traditional CNC Machining vs. Metal Additive Manufacturing for Mold Inserts
Fonctionnalité | Usinage CNC traditionnel | Metal Additive Manufacturing (e.g., LPBF) | Key Advantage of AM |
---|---|---|---|
Complexité géométrique | Limited by tool access, axis capabilities | High degree of freedom, complex internal channels possible | Permet conformal cooling & intricate part features |
Refroidissement conforme | Very difficult, expensive, often impossible | Relatively easy to integrate during design | Reduced cycle time, improved part quality |
Délai d'exécution | Can be lengthy (weeks/months), esp. complex | Potentially shorter (days/weeks), esp. for complex parts | Faster time-to-market, quicker iterations |
Déchets matériels | Élevée (procédé soustractif) | Low (additive process, supports minimal) | More sustainable, lower raw material cost component |
Design Iteration | Costly and time-consuming to modify tooling | Easier and faster to modify digital file & reprint | Agility in design optimization |
Durée de vie de l'outil | Excellent with proper tool steels & treatment | Excellent with maraging steels & proper treatment | Comparable durability for demanding applications |
Coût initial | Generally lower for simple inserts | Can be higher for simple inserts, cost-effective for complex | Cost optimization for high-complexity tooling |
Setup Time | Requires programming, fixturing, tool setup | Requires file preparation, build setup | Can be faster for unique, complex geometries |
Exporter vers les feuilles
Elaborating on the Key Advantages of AM for Mold Inserts:
- Unmatched Design Freedom & Conformal Cooling: This is the cornerstone benefit. AM liberates designers from the constraints of traditional machining. The ability to design and print conformal cooling channels that precisely follow the contours of the mold cavity surface, just millimeters away, is revolutionary.
- Impact: Drastically improves heat transfer efficiency. Studies and industrial applications consistently show cycle time reductions of 20-50% or even more in some cases. This directly translates to higher machine utilization and lower per-part costs. Furthermore, uniform cooling minimizes differential shrinkage, reducing part warpage, sink marks, and internal stresses, leading to higher yields of quality parts.
- Accelerated Lead Times for Complex Tooling: While simple inserts might be machined quickly, complex inserts requiring multi-axis machining, EDM (Electrical Discharge Machining), and intricate assembly can take weeks or months. AM can often produce highly complex inserts in a matter of days or a couple of weeks (including post-processing).
- Impact: This speed is crucial for l'outillage rapide, bridge production, and industries with short product lifecycles. It allows manufacturers to respond faster to market demands and iterate designs more quickly. Procurement managers benefit from compressed supply chain timelines.
- Efficacité matérielle : Subtractive manufacturing starts with a large block of material and machines away potentially 80-90% of it to get to the final shape. Additive manufacturing builds the part layer by layer, using only the material needed for the part and its support structures.
- Impact: Significant reduction in expensive tool steel waste. While metal powders are costly, the buy-to-fly ratio is much better, contributing to sustainability and potentially lower overall material costs for complex geometries where waste would be substantial in machining.
- Consolidation of Assemblies: Complex inserts might traditionally require multiple machined components to be assembled. AM can often print the entire complex insert as a single piece.
- Impact: Reduces assembly time and potential failure points associated with joints or seams. Simplifies the supply chain by reducing the number of individual components to manage.
- Enabling Complex Part Features: Beyond cooling channels, AM allows for the creation of inserts with fine textures, integrated venting paths, sharp internal corners, and other intricate features that are difficult or impossible to machine directly.
- Impact: Allows for the molding of more sophisticated plastic parts, potentially reducing the need for downstream assembly or finishing operations on the plastic part itself.
While AM might have a higher initial cost for very simple inserts and requires expertise in design (DfAM – Design for Additive Manufacturing) and process control, the benefits of AM tooling – particularly the dramatic reduction in injection molding cycle time and improvement in part quality driven by conformal cooling – provide a compelling return on investment for a vast range of applications. Partnering with knowledgeable fournisseurs de services d'impression 3D métal ensures these advantages are fully realized.
Material Focus: Properties and Benefits of Maraging Steels (1.2709, H13, M300) for Mold Inserts
The success of a 3D printed injection mold insert hinges critically on the material chosen. It must not only be printable but also possess the necessary mechanical and thermal properties to withstand the demanding injection molding environment – high pressures, cyclic thermal loading, and potential abrasive wear from filled plastics. Maraging steels have emerged as front-runners for this application, alongside AM-processed versions of traditional tool steels like H13. Understanding their properties is crucial for selecting the right material for your specific molding needs.
Why Maraging and Tool Steels?
These materials offer a combination of:
- High Strength & Hardness: Essential for durability and resisting deformation under clamping force and injection pressure.
- Résistance à l'usure : Crucial for longevity, especially when molding abrasive glass-filled or mineral-filled polymers.
- La robustesse : Ability to resist cracking under cyclic stress.
- Conductivité thermique : Important for efficient heat removal (though generally lower than copper alloys sometimes used for inserts).
- Temper Resistance: Ability to retain hardness at elevated molding temperatures.
- Imprimabilité : Suitability for processing via common metal AM technologies like Laser Powder Bed Fusion (LPBF).
- Post-Processability: Can be heat-treated, machined, polished, and coated.
Featured Materials for 3D Printed Mold Inserts:
Let’s examine the key characteristics of the recommended powders: 1.2709 (MS1), H13, and M300. It’s important to note that properties can vary slightly based on the specific AM machine, parameters used, and post-processing steps.
Propriété | 1.2709 (MS1 Maraging) | H13 Tool Steel (AM Processed) | M300 Maraging Steel | Significance for Mold Inserts |
---|---|---|---|---|
Typical Hardness (As-Printed) | ~30-35 HRC | ~45-50 HRC | ~33-38 HRC | Indicates initial state before heat treatment. |
Typical Hardness (Heat Treated) | ~50-55 HRC (Age Hardened) | ~48-52 HRC (Tempered) | ~53-58 HRC (Age Hardened) | Crucial for wear resistance and resisting damage. |
Résistance à la traction (traitement thermique) | ~1800-2100 MPa | ~1600-1900 MPa | ~1900-2200 MPa | Resistance to deformation under pressure. |
Conductivité thermique | ~14-20 W/(m·K) | ~24-28 W/(m·K) | ~13-18 W/(m·K) | Affects cooling efficiency (higher is better). |
Traitement thermique | Simple Aging (~480-500°C) | Quench & Temper (~1020°C Q, ~600°C T) | Simple Aging (~480-500°C) | Aging is lower temp, less distortion risk. |
Soudabilité | Bon | Moderate (preheat needed) | Bon | Ease of repair or modification. |
Machinability (Hardened) | Modéré | Difficile | Modéré | Ease of final machining/polishing critical surfaces. |
Exporter vers les feuilles
Deep Dive into Each Material:
- 1.2709 / MS1 Maraging Steel:
- Composition : A low-carbon steel alloyed primarily with nickel, cobalt, and molybdenum.
- Mechanism: Gains hardness through a precipitation hardening process (aging) at relatively low temperatures (~490°C) after printing. Tiny intermetallic compounds form within the metal matrix.
- Avantages :
- Excellente imprimabilité : Widely characterized and relatively easy to print dense parts with good dimensional accuracy.
- Simple Heat Treatment: Low-temperature aging minimizes distortion and residual stress compared to quenching/tempering.
- Good Balance: Offers a great combination of high strength, good toughness, and adequate hardness for many molding applications.
- Good Machinability & Weldability: Simplifies post-processing and potential repairs.
- Considérations : Thermal conductivity is moderate, not as high as H13.
- Ideal For: General purpose inserts, complex geometries benefiting from low-distortion heat treatment, applications requiring good toughness. Often the default starting point.
- H13 Tool Steel (AM Processed):
- Composition : A chromium-molybdenum-vanadium hot-work tool steel.
- Mechanism: Hardened via traditional quenching from high temperature (~1020°C) followed by tempering (~550-620°C).
- Avantages :
- Higher Thermal Conductivity: Compared to maraging steels, facilitating better heat removal.
- Excellent Hot Hardness: Retains hardness well at elevated temperatures encountered in some molding processes.
- Good Wear Resistance: Known for durability in traditional tooling.
- Considérations :
- More Complex Heat Treatment: Quenching introduces higher risk of distortion and residual stress, requiring careful management.
- Défis en matière d'imprimabilité : Can be more prone to cracking during printing than maraging steels if parameters are not optimized.
- Lower Machinability (Hardened): More difficult to machine after hardening.
- Ideal For: Applications where maximum thermal conductivity is needed, high molding temperatures are involved, or direct replacement of traditionally machined H13 inserts is desired.
- M300 Maraging Steel:
- Composition : Similar base to 1.2709 but typically with higher cobalt and titanium content.
- Mechanism: Also hardened via low-temperature aging.
- Avantages :
- Higher Hardness & Strength: Typically achieves slightly higher hardness (~55-58 HRC) and tensile strength than 1.2709 after aging.
- Excellente résistance à l'usure : The increased hardness contributes to better resistance against abrasive fillers.
- Simple Heat Treatment: Benefits from the same low-distortion aging process.
- Considérations : May have slightly lower toughness than 1.2709. Printability is generally good but requires optimized parameters. Thermal conductivity is similar to 1.2709.
- Ideal For: Demanding applications requiring maximum hardness and wear resistance, such as molding highly abrasive plastics, or for achieving longer tool life in high-volume production.
The Importance of Powder Quality:
The final properties of the 3D printed insert are directly linked to the quality of the metal powder used. Factors like:
- Sphéricité : Smooth, spherical particles flow easily and pack densely, minimizing voids.
- Distribution de la taille des particules (PSD) : A controlled PSD ensures consistent melting and layer formation.
- La pureté : Low levels of impurities (like oxygen and nitrogen) prevent defects and ensure desired mechanical properties.
- Fluidité : Consistent powder flow is essential for uniform layers in the printer bed.
This is where specialized powder producers play a vital role. Companies like Met3dp, leveraging advanced powder manufacturing techniques such as industry-leading gas atomization and Plasma Rotating Electrode Process (PREP), focus on delivering poudres métalliques de haute qualité optimized for additive manufacturing. Their expertise ensures powders with high sphericity, controlled PSD, excellent flowability, and high purity, forming the foundation for reliable and high-performance 3D printed mold inserts. Choosing a service provider who uses certified, high-quality powders from reputable manufacturers like Met3dp is essential for achieving consistent and predictable results in your tooling.
Selecting the appropriate material—whether 1.2709 for its balance, H13 for thermal performance, or M300 for maximum hardness—requires careful consideration of the specific injection molding application, the plastic being molded, and the desired tool life and performance characteristics. Consulting with AM tooling experts can help guide this critical decision.

Designing for Additive Success: Key Considerations for 3D Printed Mold Inserts
Successfully leveraging metal additive manufacturing for injection mold inserts goes beyond simply choosing the right material; it demands a fundamental shift in design thinking. Design for Additive Manufacturing (DfAM) principles are paramount to unlocking the full potential of the technology, particularly for creating complex geometries like conformal cooling channels, ensuring manufacturability, and optimizing performance. Engineers and designers must consider the unique opportunities and constraints presented by the layer-by-layer building process. Neglecting DfAM can lead to printing failures, suboptimal performance, or increased post-processing effort and cost.
Here are critical design considerations for AM mold inserts:
1. Conformal Cooling Channel Design:
- Proximity and Path: Channels should follow the mold surface contour closely (typically 3-10mm away, depending on material and application) but maintain a minimum wall thickness to the molding surface and the exterior of the insert for structural integrity and heat transfer. The path should be smooth, avoiding sharp angles (<90°) which can cause pressure drops, turbulent flow, and potential dead zones. Use gradual bends (radius typically >3x channel diameter).
- Diameter and Shape: Channel diameters typically range from 3mm to 10mm. Smaller diameters offer closer conformity but higher pressure drops; larger diameters have lower pressure drop but less precise thermal control. Non-circular shapes (e.g., teardrop, oval) can be beneficial for proximity or self-supporting capabilities during printing but require careful flow analysis.
- Inlets/Outlets: Design standard fittings (e.g., threaded connections) that can be easily machined or integrated post-print for connecting cooling lines. Ensure sufficient landing area for machining sealing surfaces.
- Manufacturability: Consider the minimum printable channel diameter and overhang capabilities of the chosen fabrication additive process (e.g., Laser Powder Bed Fusion – LPBF). While AM can create complex paths, extremely small or tortuous channels might be difficult to print reliably and, crucially, to clear of unfused powder.
- Simulation : Utilize thermal and CFD (Computational Fluid Dynamics) simulation tools to optimize channel layout, predict cooling performance, ensure balanced flow, and identify potential hot spots or pressure issues before committing to print.
2. Minimum Wall Thickness and Feature Size:
- Structural Integrity: Inserts must withstand clamping and injection pressures. Minimum wall thicknesses depend on the material, overall insert size, and operating pressures, but generally range from 0.5mm to 2mm or more for structural walls. Thin walls are prone to distortion during printing and heat treatment.
- Heat Transfer: Wall thickness between the cooling channel and mold surface directly impacts heat transfer efficiency. Thinner is generally better for cooling speed, but structural and manufacturing limits must be respected.
- Printable Features: Understand the resolution limits of the AM process. Minimum printable feature sizes (e.g., ribs, pins, holes) are typically around 0.3-0.5mm, but achieving sharp edges or very fine textures requires careful parameter tuning and often post-processing.
3. Support Structures:
- Objet : Supports anchor the part to the build plate, prevent warping due to thermal stress, and support overhanging features (typically angles below 45° from the horizontal).
- DfAM for Supports:
- Orientation : Orient the part on the build plate to minimize the need for supports, especially on critical or hard-to-reach surfaces.
- Angles autoportants : Design features with angles greater than 45° where possible. Teardrop or diamond shapes for internal channels can make them self-supporting.
- Accessibilité : Ensure supports are placed in areas accessible for removal using manual or machining methods. Avoid trapping supports internally.
- Contact Points: Optimize support contact points to minimize witness marks on the final part surface and ease removal. Perforated or tapered supports can help.
- Gestion thermique : Supports also conduct heat away; their placement can influence thermal stresses and potential distortion.
4. Powder Removal:
- Canaux internes : Design effective entry and exit points for internal conformal cooling channels or other voids to allow unfused powder to be removed after printing (typically via vibration, compressed air, or flushing). Avoid dead-end channels or overly complex networks where powder can become permanently trapped.
- Escape Holes: Strategically place small holes (that can potentially be plugged later if necessary) in enclosed void areas to facilitate powder evacuation.
5. Build Orientation Strategy:
- Finition de la surface : Surfaces facing upwards or downwards typically have different roughness profiles. Critical surfaces might dictate orientation choice, although post-machining is often required anyway. Stepped surfaces (stair-stepping effect) are most pronounced on shallow angles.
- Supports: As mentioned, orientation heavily influences the amount and location of required support structures.
- Build Time & Cost: Orientation affects the height of the build (Z-height), which directly impacts print time and cost.
- Anisotropie : Mechanical properties can sometimes vary slightly depending on the build direction relative to the applied stress in the final application. This is less pronounced in metals compared to polymers but can be a consideration for highly stressed components.
6. Hybrid Manufacturing Approach:
- Design the insert specifically for AM, focusing complexity where needed (e.g., conformal cooling near the cavity). Design simpler base structures or interfaces intended for conventional machining. This hybrid approach optimizes cost and leverages the strengths of both manufacturing methods.
7. Venting Considerations:
- AM allows for the integration of thin, porous sections or complex micro-venting channels directly into the insert in hard-to-reach areas, improving gas evacuation during molding and reducing defects like burn marks or short shots.
By carefully considering these DfAM principles, manufacturers can maximize the benefits of using AM for injection mold inserts, resulting in tools that are not only manufacturable but also perform significantly better than their traditional counterparts. Collaborating with experienced additive manufacturing service providers, who possess deep expertise in DfAM for tooling, is highly recommended to navigate these complexities effectively.
Precision & Quality: Understanding Tolerance, Surface Finish, and Accuracy in AM Mold Inserts
When considering 3D printed mold inserts, particularly for high-precision injection molding applications, questions surrounding achievable tolerance, surface finish, and overall dimensional accuracy are critical for both engineers and procurement managers. While metal AM offers incredible geometric freedom, it’s essential to have realistic expectations about its inherent precision and understand the role of post-processing in achieving final specifications. Quality control throughout the process is vital for ensuring functional, high-performance tooling.
As-Printed vs. Post-Processed State:
It’s crucial to differentiate between the condition of the insert immediately after printing and its state after necessary post-processing steps (like heat treatment, machining, polishing).
- As-Printed: The insert will have certain inherent tolerances and surface roughness characteristic of the layer-wise building process. Internal features like conformal cooling channels will largely retain their as-printed state.
- Post-Processed: Critical functional surfaces (e.g., parting lines, cavity/core surfaces, sealing faces, fitting interfaces) are typically machined and/or polished to achieve the required tight tolerances and smooth finishes demanded by injection molding.
Tolerance Capabilities:
- General Tolerances (As-Printed): For typical metal LPBF processes used for tool steels, general achievable tolerances are often in the range of ±0.1mm to ±0.2mm for smaller dimensions (e.g., up to 100mm), or ±0.1% to ±0.2% for larger dimensions. These values can vary significantly based on:
- Machine calibration and condition
- Part geometry and size
- Build orientation
- Material properties (shrinkage, stress)
- Support strategy
- Obtenir des tolérances plus strictes : For mold inserts, these general AM tolerances are often insufficient for critical interfaces. Post-process machining (CNC milling, grinding, EDM) is almost always required to achieve typical mold-making tolerances, which can be ±0.01mm to ±0.05mm or even tighter, depending on the specific feature and application. Design parts with machining allowances (stock) on critical surfaces.
- Normes : While general AM tolerance standards exist (e.g., ISO/ASTM 52900 series provide terminology and concepts), specific achievable tolerances are highly dependent on the provider’s process control. Reference standards like ISO 2768 (general tolerances) might be used as a baseline, but specific agreements with the metal 3D printing service provider are necessary.
Finition de la surface (rugosité) :
- As-Printed Surface Roughness (Ra): The surface finish of as-printed metal parts is considerably rougher than machined surfaces. Typical Ra values range from 6µm to 20µm, influenced by:
- Épaisseur de la couche : Thicker layers generally lead to rougher surfaces.
- Powder Particle Size: Finer powders can yield smoother finishes.
- Orientation : Top-facing surfaces are often smoother than side walls or down-facing surfaces (which may show support contact points). Sloping surfaces exhibit stair-stepping effects.
- Laser Parameters: Melting parameters influence the surface texture.
- Achieving Smooth Finishes: For mold cavity/core surfaces, a smooth finish is essential for part ejection and achieving the desired plastic part aesthetics. As-printed surfaces are rarely acceptable. Post-processing, primarily polishing (manual or automated), is required to achieve typical mold finishes, often specified using SPI (Society of the Plastics Industry) standards (e.g., A-1 mirror finish <0.012µm Ra, B-2 semi-gloss ~0.1-0.2µm Ra, C-3 matte ~0.35-0.5µm Ra). Extensive polishing is often needed, adding significantly to cost and lead time.
- Canaux internes : Conformal cooling channels generally retain their as-printed surface roughness, which can slightly increase pressure drop compared to smooth drilled channels. Abrasive flow machining or chemical polishing can sometimes be used to improve internal finish if required, but adds complexity.
Dimensional Accuracy & Quality Control:
- Facteurs influençant la précision : Achieving consistent dimensional accuracy requires rigorous process control, including:
- Étalonnage de la machine : Regular calibration of the AM system’s lasers, scanners, and motion systems.
- Gestion thermique : Controlling build chamber temperature and managing thermal stresses during the print.
- Cohérence des matériaux : Using high-quality, consistent poudres métalliques is fundamental. Poor powder quality can lead to defects affecting dimensions.
- Post-Processing Effects: Heat treatment can cause slight distortion (though minimized with maraging steel aging), and machining must be precise.
- Metrology and Inspection: Robust quality control is non-negotiable for tooling.
- Inspection dimensionnelle : Coordinate Measuring Machines (CMMs) are used to verify critical dimensions after post-processing. Optical scanning (3D scanning) can compare the final part to the original CAD model.
- Internal Feature Verification: For conformal cooling channels, Computed Tomography (CT) scanning is often the only way to non-destructively verify the channel path, check for blockages or trapped powder, and measure internal wall thicknesses.
- Material Integrity: Density checks, material testing (hardness), and microstructure analysis may be performed to ensure the material meets specifications.
Partnering for Quality:
Achieving the required precision and quality demands working with a metal 3D printing service provider that has demonstrated expertise specifically in tooling applications. Look for providers like Met3dp and their partners who emphasize:
- Robust Quality Management Systems: (e.g., ISO 9001 certification).
- Advanced Equipment: Well-maintained and calibrated industrial AM systems.
- Contrôle des processus : Defined procedures for printing, handling, and post-processing.
- High-Quality Materials: Sourcing certified powders from reputable manufacturers. Met3dp’s own focus on producing high-sphericity, high-purity powders using advanced atomization is a testament to this commitment to quality at the source.
- Comprehensive Metrology: Capabilities for CMM, potentially CT scanning, and other relevant inspection methods.
By understanding the capabilities and limitations of the technology and engaging in thorough post-processing and quality control, manufacturers can confidently utilize metal AM to produce high-precision, high-performance injection mold inserts.
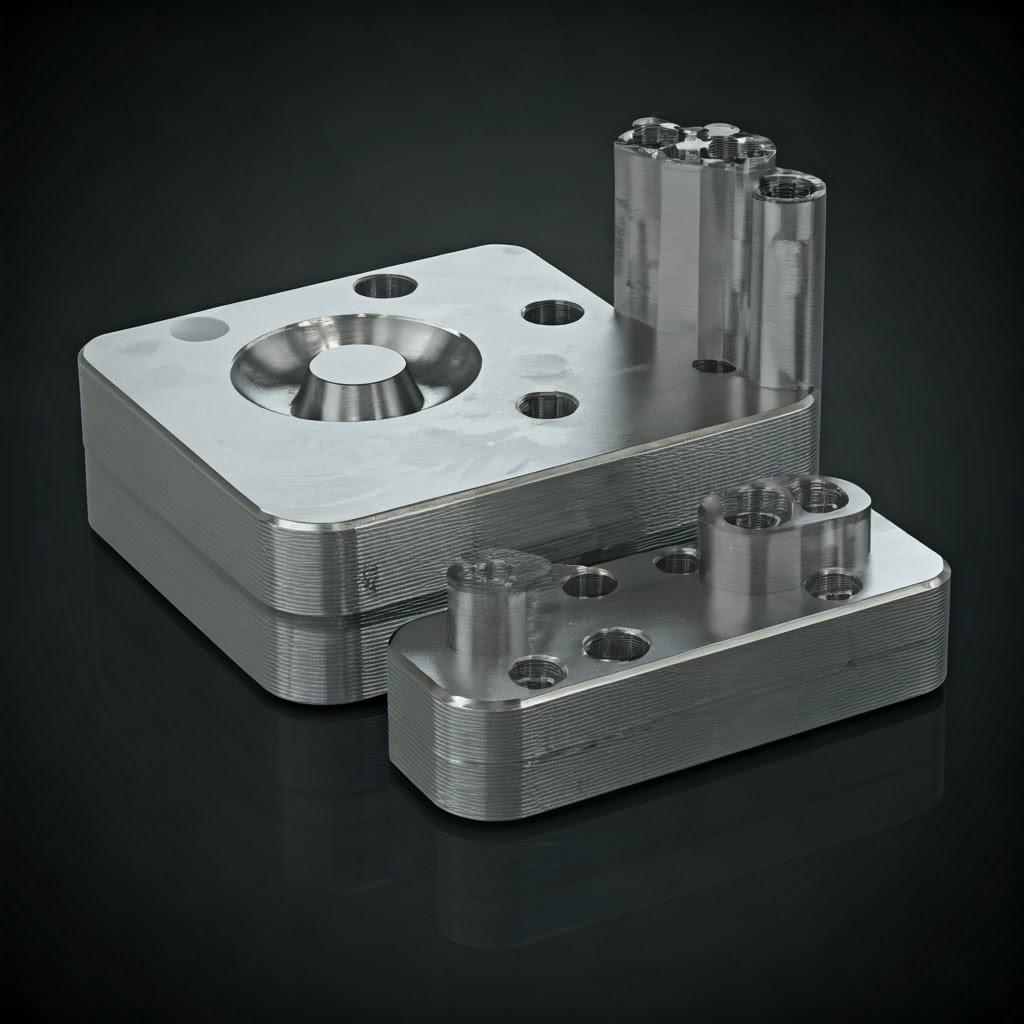
Beyond the Print: Essential Post-Processing Steps for Functional Mold Inserts
Obtaining a 3D printed metal part from the machine is only the midpoint in the journey to a functional injection mold insert. A series of critical post-processing metal AM steps are required to transform the as-printed component into a durable, precise tool ready for the rigors of injection molding. These steps are essential for achieving the required mechanical properties, dimensional accuracy, surface finish, and overall functionality. Understanding this workflow is vital for accurately estimating project timelines and costs.
Here’s a typical sequence of post-processing operations for 3D printed maraging steel (or H13) mold inserts:
1. Stress Relief Heat Treatment (Optional but Recommended):
- Objet : To reduce internal stresses built up during the layer-by-layer printing process due to rapid heating and cooling cycles. This minimizes the risk of distortion or cracking when the part is removed from the build plate.
- Processus : Typically performed while the part is still attached to the build plate in an inert atmosphere furnace at a moderate temperature (below the aging/tempering temperature). For maraging steels, this might be around 300-400°C; for H13, it could be higher.
2. Removal from Build Plate:
- Objet : To separate the printed insert(s) from the metal build plate they were fused onto.
- Méthodes : Commonly done using Wire EDM (Electrical Discharge Machining) or a bandsaw. Precision is required to avoid damaging the parts.
3. Retrait des structures de support :
- Objet : To remove the temporary structures that supported the part during printing.
- Méthodes : This can be a labor-intensive step.
- Suppression manuelle : Supports are often designed with weakened connection points and can sometimes be broken off by hand or with simple tools.
- Usinage : CNC milling or grinding is frequently used to remove support bases and smooth witness marks, especially on critical surfaces.
- Wire EDM: Can be used for intricate or hard-to-reach supports.
- Importance of DfAM: Good design (as discussed previously) focusing on minimizing supports and ensuring accessibility drastically simplifies this step.
4. Heat Treatment (Hardening):
- Objet : This is arguably the most critical step for achieving the final desired mechanical properties (hardness, strength, wear resistance) of the tool steel.
- Processus :
- Maraging Steels (1.2709, M300): Undergo age hardening. This involves heating the parts in a controlled atmosphere or vacuum furnace to a relatively low temperature (typically 480-500°C) and holding them for several hours (e.g., 3-6 hours). This precipitates hardening phases within the metal matrix. The key benefit is minimal distortion due to the low temperature and absence of quenching.
- H13 Tool Steel: Requires a more traditional quench and temper process. Parts are heated to a high austenitizing temperature (~1020°C), rapidly cooled (quenched) in gas or oil, and then tempered at a lower temperature (~550-620°C, often multiple times) to achieve the target hardness and toughness. This process carries a higher risk of distortion and requires careful management.
- Résultat : Transforms the relatively soft as-printed part into a hard, durable tool steel insert.
5. Machining (Critical Dimensions & Features):
- Objet : To achieve the precise final dimensions, tolerances, and features required for the mold assembly and function.
- Méthodes : Utilizes conventional subtractive techniques on the hardened AM part:
- CNC Milling/Turning: To create flat sealing surfaces, parting lines, precise cavity/core dimensions, threads for fittings, pockets, etc.
- Broyage : For achieving very tight tolerances and fine surface finishes on flat or cylindrical surfaces.
- EDM (Sink or Wire): For creating sharp corners, intricate features, or machining very hard materials that are difficult to mill or grind.
- Exigence : As-printed parts must be designed with sufficient machining stock (e.g., 0.5-1.0mm) on surfaces requiring finishing.
6. Polishing:
- Objet : To achieve the required surface finish on the mold cavity and core surfaces for good plastic part release and desired aesthetic appearance.
- Méthodes : Can range from manual polishing using progressively finer abrasive stones and diamond pastes to automated polishing techniques. Achieving high-gloss, mirror finishes (e.g., SPI A-1) requires significant time and skilled labor.
- Impact: Directly affects the quality of the molded plastic part and can influence tool life (smoother surfaces can sometimes reduce wear).
7. Surface Treatments/Coatings (Optional):
- Objet : To further enhance specific properties like wear resistance, corrosion resistance, or lubricity.
- Méthodes :
- Nitriding: A diffusion process to harden the surface.
- PVD (Physical Vapor Deposition) Coatings: Applying thin ceramic coatings like Titanium Nitride (TiN), Chromium Nitride (CrN), or others for significantly increased surface hardness and lower friction.
- Use Case: Often applied for very high-volume runs or when molding highly abrasive (e.g., glass-filled) plastics.
8. Final Cleaning & Inspection:
- Objet : To ensure the insert is clean, free of debris (especially inside cooling channels), and meets all dimensional and surface finish specifications.
- Méthodes : Thorough cleaning, final dimensional checks (CMM), visual inspection, potentially flow testing for cooling channels.
The extent and complexity of post-processing significantly impact the final cost and lead time of 3D printed mold inserts. Engaging with a full-service metal 3D printing service provider that offers integrated post-processing capabilities or manages a qualified network of partners ensures a streamlined workflow and guarantees that the final insert meets the required specifications for demanding injection molding applications.
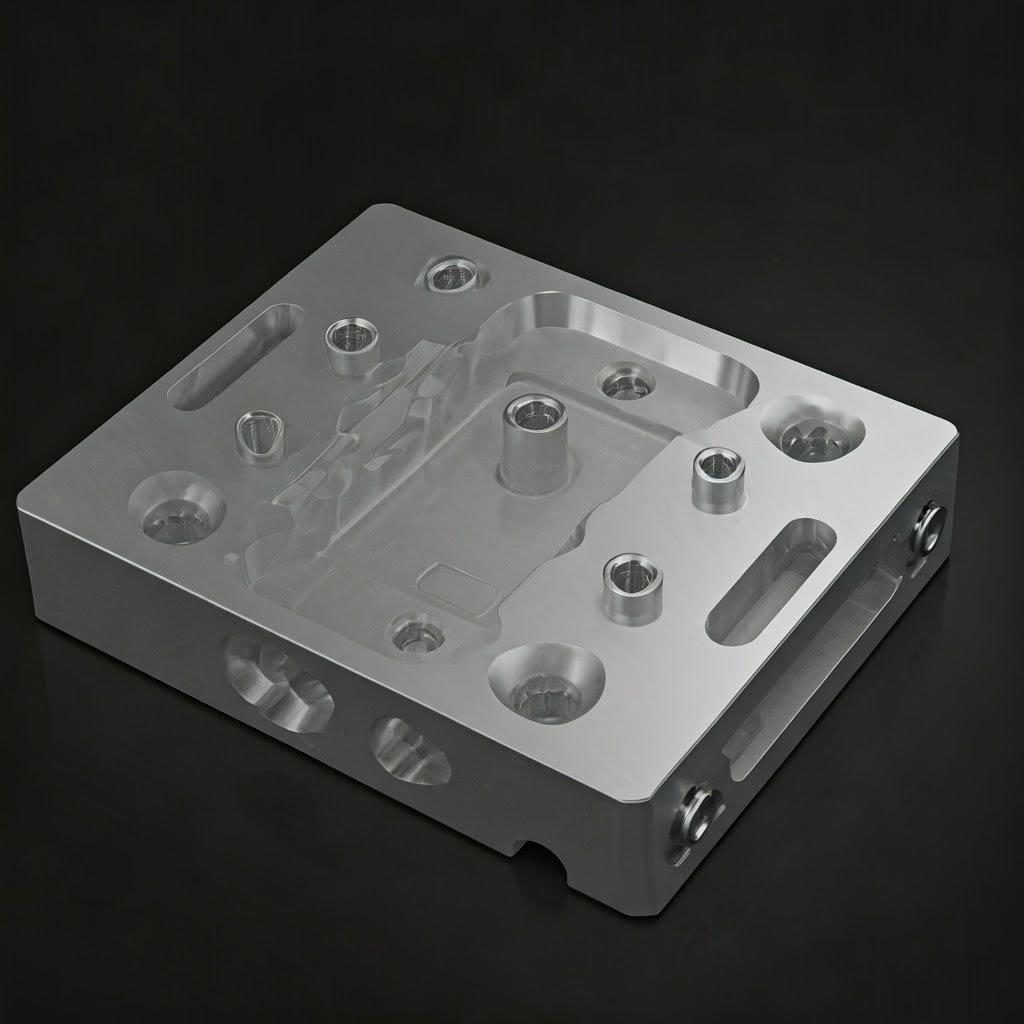
Overcoming Hurdles: Common Challenges and Solutions in Printing Metal Mold Inserts
While metal additive manufacturing offers tremendous advantages for injection mold inserts, it’s not without its challenges. Understanding potential issues and implementing effective mitigation strategies are key to successfully producing reliable and high-performance tooling. Awareness of these hurdles allows engineers and procurement managers to have informed discussions with service providers and set realistic expectations.
Here are some common challenges encountered in 3D printing tooling and how to address them:
1. Warping and Distortion:
- Défi: Significant temperature gradients during the layer-wise melting and solidification process induce internal stresses. These stresses can cause the part to warp during printing or distort after removal from the build plate or during heat treatment (especially quenching).
- Solutions :
- Structures de soutien optimisées : Well-designed supports anchor the part securely and help manage thermal stresses.
- Orientation de la construction : L'orientation stratégique peut minimiser l'accumulation de stress dans les domaines critiques.
- Scan Strategy Optimization: Using techniques like island scanning or chessboard patterns breaks up long melt pools, reducing stress buildup.
- Build Plate Heating: Maintaining an elevated, consistent temperature on the build plate reduces thermal gradients.
- Stress Relief Cycles: Performing intermediate stress relief heat treatments during the build (less common) or immediately after printing (very common) is crucial.
- Simulation : Using process simulation software to predict stress and distortion allows for design and parameter adjustments before impression.
- Material Choice: Maraging steels requiring only low-temperature aging generally exhibit less distortion than steels needing high-temperature quenching (like H13).
2. Cracking (Solidification or Cold Cracking):
- Défi: Cracks can form during solidification of the melt pool or later during cooling due to high residual stresses exceeding the material’s strength, particularly in crack-sensitive alloys or complex geometries.
- Solutions :
- Paramètres d'impression optimisés : Tuning laser power, scan speed, and layer thickness is critical to control the cooling rate and minimize stress.
- Pre-heating: Elevated build plate/chamber temperatures reduce thermal shock.
- Poudre de haute qualité : Using powders with controlled chemistry and low impurities (like those produced by Met3dp using advanced atomization) minimizes crack initiation sites.
- Appropriate Material Selection: Some alloys are inherently more prone to cracking than others.
- Soulagement du stress : Prompt post-print stress relief is vital.
3. Porosity (Gas or Lack-of-Fusion):
- Défi: Voids within the printed material compromise its density, mechanical properties (especially fatigue strength), and potentially its polishability. Porosity can arise from gas trapped within the melt pool or insufficient energy input leading to incomplete fusion between layers or scan tracks.
- Solutions :
- Optimisation des paramètres : Fine-tuning laser power, scan speed, hatch spacing, and focus ensures complete melting and fusion.
- Poudre de haute qualité : Using dry, spherical powder with low internal gas content and good flowability minimizes gas porosity and ensures uniform layer spreading. Protecting powder from moisture is key.
- Shielding Gas: Maintaining a high-purity inert shielding gas atmosphere (Argon or Nitrogen) prevents oxidation and contamination during printing.
- Pressage isostatique à chaud (HIP) : An optional, high-cost post-processing step involving high temperature and pressure to close internal pores. Usually reserved for critical applications requiring maximum density and fatigue life.
4. Support Structure Removal Difficulties:
- Défi: Poorly designed or inaccessible supports can be extremely difficult, time-consuming, and costly to remove, potentially damaging the part surface.
- Solutions :
- Focus DfAM : Design for minimal support need (self-supporting angles, optimized orientation).
- Smart Support Design: Utilize specialized support structures (e.g., thin-walled, perforated, tree supports) with optimized contact points for easier detachment.
- Accessibility Planning: Ensure tools (manual or machine) can reach the support structures.
- Appropriate Removal Techniques: Select the best method (manual, milling, EDM) based on the support type and location.
5. Trapped Powder Removal:
- Défi: Unfused powder can become trapped inside intricate internal channels (like conformal cooling) if escape routes are inadequate. This adds weight, can impede coolant flow, and is a contamination risk.
- Solutions :
- DfAM for Powder Removal: Design channels with sufficient diameter, smooth paths, and dedicated inlet/outlet/drainage ports.
- Escape Holes: Add small, strategically placed holes in enclosed voids.
- Thorough Cleaning Procedures: Utilize vibration tables, compressed air, ultrasonic cleaners, or specialized flushing rigs post-print.
- CT Scanning Inspection: Verify complete powder removal, especially in critical channels.
6. Achieving Fine Details and Surface Finish:
- Défi: The layer-wise nature and melt pool dynamics limit the minimum feature size and inherent surface smoothness achievable directly from the AM process. Achieving sharp edges or mirror finishes requires significant effort.
- Solutions :
- Process Resolution: Select an AM process and parameters (e.g., smaller laser spot size, thinner layers) suited for fine details, accepting potential trade-offs in build speed.
- Orientation : Position critical features optimally relative to the build direction.
- Extensive Post-Processing: Rely on precise CNC machining for sharp edges and features, and meticulous multi-stage polishing for surface finish. Manage expectations – as-printed finish is not mold-ready.
Mitigation Through Expertise and Process Control:
Overcoming these challenges requires a combination of robust DfAM practices, optimized and validated printing parameters, high-quality materials, and meticulous post-processing. Partnering with an experienced metal 3D printing service provider is crucial. Companies with a deep understanding of metallurgy, process physics, tooling requirements, and rigorous quality control systems, often utilizing premium poudres métalliques known for their consistency and purity, are best equipped to navigate these potential pitfalls and deliver successful, high-performance 3D printed mold inserts. Discussing these potential challenges upfront with your provider ensures alignment and effective risk mitigation strategies.
Supplier Selection: Choosing the Right Metal 3D Printing Service Provider for Tooling
Selecting the right manufacturing partner is paramount to successfully implementing 3D printed injection mold inserts. The unique requirements of tooling—demanding materials, tight tolerances, critical surface finishes, and the integration of complex features like conformal cooling—necessitate a provider with specific expertise beyond general metal 3D printing. For procurement managers and engineers evaluating potential suppliers, focusing on capabilities directly relevant to additive manufacturing tooling est essentiel.
Here are essential criteria to consider when performing your AM tooling supplier evaluation:
- Proven Tooling Expertise:
- Does the provider have demonstrable experience producing injection mold inserts or similar tooling components?
- Can they share relevant case studies, examples of past projects, or performance data (e.g., cycle time reduction achieved)?
- Do they understand the nuances of mold design, cooling principles, and the requirements of the injection molding process?
- Material Specialization:
- Are they experienced in printing with the required materials, specifically maraging steels (1.2709, M300) and relevant tool steels (H13)?
- What is their process for material handling and ensuring powder quality? Do they use certified metal powders from reputable sources? High-quality powder, like the spherical powders produced using advanced atomization by specialists such as Met3dp, is fundamental to achieving dense, reliable parts.
- Can they provide material certifications and datasheets for the specific powder batches used?
- Technologie et équipement :
- What type of metal AM technology do they employ (typically LPBF for tooling)?
- What specific machine models do they operate? Are these industrial-grade systems known for reliability and accuracy?
- What is their build envelope size? Can they accommodate the dimensions of your required inserts?
- How frequently are their machines maintained and calibrated?
- Integrated Post-Processing Capabilities:
- This is critical. Does the provider offer comprehensive in-house post-processing, including:
- Stress Relief & Heat Treatment (specifically aging for maraging steels, Q&T for H13) with calibrated furnaces?
- Precision CNC Machining (multi-axis preferred) for critical dimensions and features?
- Wire and/or Sink EDM capabilities?
- Mold Polishing services capable of achieving specified SPI finishes?
- If services are outsourced, how do they manage quality and lead times with their partners? A seamless workflow is essential.
- This is critical. Does the provider offer comprehensive in-house post-processing, including:
- Quality Management and Inspection:
- Do they operate under a robust Quality Management System (e.g., ISO 9001 certification)?
- What are their standard Quality Control (QC) procedures for AM tooling?
- What metrology equipment do they possess (CMM, 3D scanning)?
- Crucially for conformal cooling, do they offer or have access to CT scanning for non-destructive internal inspection and verification of channels?
- Can they provide detailed inspection reports?
- Design for Additive Manufacturing (DfAM) Support:
- Can their engineering team provide expert guidance on optimizing your insert design for AM?
- Can they assist with conformal cooling channel design, support strategy, and feature optimization?
- Do they utilize simulation tools (thermal, CFD, process simulation) to predict performance and manufacturability?
- Lead Time, Capacity, and Communication:
- What are their typical lead times for mold inserts of varying complexity?
- Do they have the capacity to meet your project deadlines?
- How responsive and transparent are they during the quoting and production process? Clear communication is vital.
- Cost Transparency:
- Does their quoting process clearly break down costs associated with design/setup, materials, printing, support removal, different post-processing steps, and inspection?
- Understand precisely what is included in the quote to avoid unexpected charges.
By carefully evaluating AM partners against these criteria, you can identify a provider capable of delivering high-quality, functional mold inserts that leverage the full benefits of additive manufacturing. Companies like Met3dp, which focus on delivering solutions complètes encompassing advanced equipment, high-performance materials, and application expertise, represent the kind of integrated approach needed for success in demanding industrial applications like tooling. They understand that success comes from mastering the entire process chain, from powder to finished part.
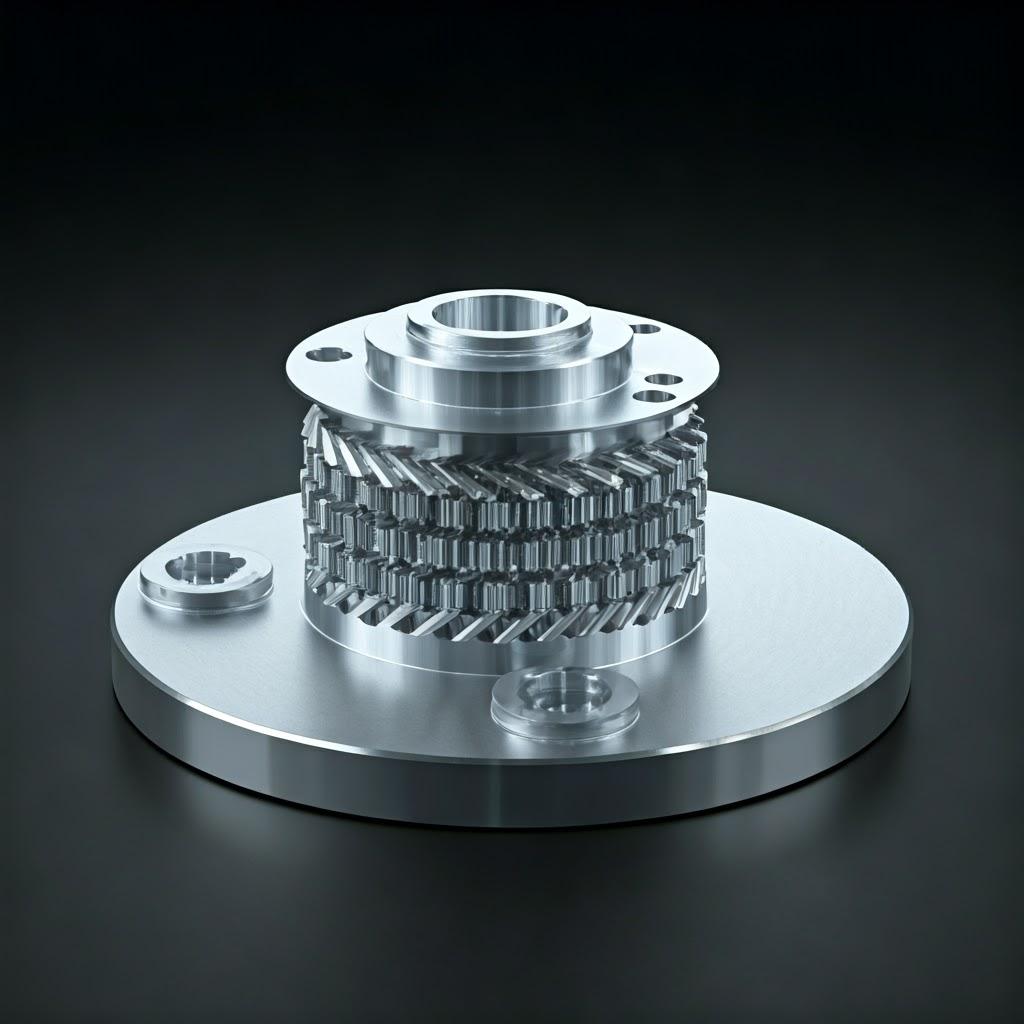
Investment & Timeline: Analyzing Cost Factors and Lead Times for AM Mold Inserts
While the performance benefits of 3D printed mold inserts, particularly those with conformal cooling, are compelling, understanding the associated costs and typical lead times is essential for project planning and ROI calculations. Both factors can vary significantly based on numerous variables, and transparency from the service provider is key.
Key Cost Drivers for 3D Printed Mold Inserts:
Le 3D printing cost for mold inserts is influenced by several factors:
- Consommation de matériaux :
- Volume de la pièce : The amount of expensive maraging or tool steel powder required for the insert itself.
- Support Structure Volume: Supports also consume material and must be factored in. Well-optimized designs minimize support waste.
- Type de poudre : Different alloys have different base costs.
- Machine Time (Print Time):
- Part Volume & Height: Larger and taller parts take longer to print, occupying expensive machine time.
- La complexité : While AM handles complexity well, very intricate features might require slower print parameters.
- Number of Parts per Build: Printing multiple inserts simultaneously can improve machine time efficiency per part, relevant for wholesale AM tooling ordres.
- Labor & Setup:
- File Preparation: Time taken to prepare the CAD file, design supports, and plan the build layout.
- Machine Setup & Teardown: Loading powder, setting up the build, and post-build machine cleaning.
- Manual Intervention: Primarily for support removal and powder evacuation.
- Post-Processing (Often the Most Significant Cost Component):
- Traitement thermique : Furnace time and energy costs.
- Suppression du support : Can be labor-intensive or require dedicated machining time (e.g., Wire EDM).
- Usinage CNC : Programming, setup, and runtime for achieving final tolerances and features on hardened steel. Multi-axis machining adds complexity and cost.
- Polissage : Highly skilled labor is required, especially for high SPI finishes. This can be a major cost driver depending on the surface area and required finish level.
- EDM : Required for specific features, adding process time and cost.
- Assurance qualité et inspection :
- Standard dimensional checks (CMM).
- Advanced inspection like CT scanning adds significant cost but may be necessary for critical internal channels.
- Documentation and reporting requirements.
Return on Investment (ROI) Considerations:
While the initial cost estimation for AM inserts might be higher than simple machined inserts, the ROI analysis must consider the total cost of ownership and operational benefits:
- Reduced Cycle Time: Shortened molding cycles (often 20-50%+) lead to higher throughput, better machine utilization, and lower per-part molding costs. This is often the primary driver for adopting AM inserts.
- Amélioration de la qualité des pièces : Lower scrap rates due to reduced warpage, sink marks, etc., save material and rework costs.
- Tool Longevity: High-hardness maraging steels provide excellent wear resistance.
- Design Enablement: Ability to produce parts previously impossible or requiring complex assemblies.
For complex geometries or high-volume production where cycle time savings are substantial, the ROI for additive manufacturing tooling can be very attractive, quickly offsetting the initial investment.
Typical Lead Times for AM Mold Inserts:
Le additive manufacturing lead time for tooling is also variable but generally follows these stages:
- Design & Simulation (DfAM): 1-5 days (depending on complexity and required analysis).
- Print Queue & Setup: 1-3 days (highly dependent on provider’s backlog).
- Impression : 1-5 days (highly dependent on part size/height/complexity).
- Post-traitement : This is often the longest phase:
- Stress Relief / Build Plate Removal: 1 day.
- Heat Treatment (including furnace cycles): 1-3 days.
- Support Removal & Basic Machining: 2-5 days.
- Precision Machining & EDM: 3-10 days (highly dependent on complexity).
- Polishing: 2-10 days (highly dependent on required finish and surface area).
- Inspection & Shipping: 1-3 days.
Total Estimated Lead Time: La fourchette est généralement comprise entre 2 à 6 semaines, but complex inserts requiring extensive machining and high-level polishing can extend beyond this.
It is crucial to discuss both cost estimates and lead time expectations in detail with potential suppliers, ensuring all necessary steps, particularly post-processing and inspection, are included in their projections. Efficient workflows and the use of high-quality, reliable materials, as emphasized by providers like Met3dp, can contribute to more predictable timelines and cost-effective outcomes.
Frequently Asked Questions (FAQ) about 3D Printed Maraging Steel Mold Inserts
Here are answers to some common questions engineers and procurement managers have about utilizing 3D printed maraging steel for injection mold inserts:
1. Are 3D printed maraging steel inserts as durable as traditional machined tool steel inserts (e.g., P20, H13)?
Yes, in many cases, they offer comparable or even superior durability. When properly printed using high-quality powder and correctly heat treated (aged), maraging steels like 1.2709 and M300 achieve high hardness levels (50-58 HRC), excellent compressive strength, and good wear resistance. This makes them suitable for demanding applications and long production runs, often matching or exceeding the performance of traditional P20 or H13, especially when considering the benefits gained from conformal cooling. The key is proper material selection, process control during printing, and correct post-processing.
2. How does the cost of a 3D printed insert with conformal cooling compare to a traditionally machined insert?
The initial manufacturing cost of a 3D printed insert with conformal cooling can be higher than a simple traditionally machined insert due to material powder costs, machine time, and extensive post-processing. However, the comparison is more favorable for complex inserts where traditional manufacturing would also be expensive (e.g., requiring extensive EDM or multiple assembled components). The true value lies in the Retour sur investissement (ROI). Significant reductions in injection molding cycle times (often 20-50% or more) achieved through conformal cooling can lead to substantial savings in production costs (machine time, labor, energy) that quickly offset the higher initial tooling cost, especially in medium- to high-volume production. Additionally, improved part quality reduces scrap rates. Therefore, a total cost of ownership analysis often favors the AM approach for complex tooling.
3. What level of surface finish can be achieved on the molding surfaces of a 3D printed insert?
Le as-printed surface finish of metal AM parts is relatively rough (typically 6-20 µm Ra) and generally unsuitable for direct molding contact. Post-process polishing is essential. Through meticulous manual or automated polishing after machining, it’s possible to achieve the full range of standard mold finishes, including high-gloss mirror finishes (SPI A-1, A-2 < 0.1 µm Ra) or various textured finishes. Achieving very high finishes requires significant skilled labor and time, adding considerably to the cost and lead time. It’s crucial to specify the required SPI finish level early in the discussion with your service provider.
4. Can we just replace an existing machined insert with a 3D printed copy? Can existing mold designs be easily converted?
Simply replicating an existing conventionally designed insert using 3D printing usually misses the main advantages of the technology. To fully benefit, a redesign leveraging Design for Additive Manufacturing (DfAM) principles is necessary. This involves incorporating conformal cooling channels, optimizing wall thicknesses, planning for support structures and powder removal, and potentially consolidating multiple components into a single printed piece. Converting an existing design requires collaboration with AM experts to re-engineer the insert specifically for the additive process and to maximize thermal performance. It is not typically a direct “drop-in” replacement scenario if you want to achieve the significant cycle time and quality benefits.
Conclusion: Embracing the Future of Injection Molding with Additive Manufacturing
The integration of metal additive manufacturing into the production of injection mold inserts, particularly using high-performance maraging steels like 1.2709 and M300, represents a significant advancement in tooling technology. As we’ve explored, the ability to create inserts with highly complex geometries, most notably optimized conformal cooling channels, offers transformative potential for the injection molding industry.
The key benefits of 3D printed mold inserts are clear and compelling:
- Accelerated Production: Dramatic reductions in molding cycle times (often 20-50%+) directly translate to increased throughput and machine efficiency.
- Enhanced Part Quality: Uniform cooling minimizes defects like warpage, sink marks, and residual stresses, leading to higher yields and improved dimensional stability.
- Liberté de conception sans précédent : Enables the creation of complex mold features and cooling strategies impossible with traditional methods, allowing for more innovative plastic part designs.
- Comparable Durability: Properly processed maraging steel inserts offer excellent hardness, strength, and wear resistance suitable for demanding production environments.
- Faster Tooling Iteration: AM facilitates quicker production of prototype and bridge tooling, speeding up product development cycles.
However, successfully harnessing these advantages requires a holistic approach. It necessitates embracing Conception pour la fabrication additive (DfAM), careful material selection, meticulous post-processing (including heat treatment, machining, and polishing), and robust quality control.
Furthermore, choosing the right manufacturing partner is critical. Collaborating with a metal 3D printing service provider that possesses deep expertise in tooling applications, utilizes high-quality materials, operates state-of-the-art equipment, and offers comprehensive post-processing and inspection capabilities is essential for success.
Des entreprises comme Met3dp are at the forefront of this technological shift, driving innovation through the development of advanced additive manufacturing systems and premium poudres métalliques optimized for demanding applications. Their commitment to providing comprehensive solutions empowers manufacturers across aerospace, automotive, medical, and industrial sectors to leverage the full potential of AM.
Le future of tooling undoubtedly involves a greater integration of additive manufacturing. By overcoming traditional constraints, 3D printed inserts enable manufacturers to achieve new levels of efficiency, quality, and design innovation in injection molding.
Ready to explore how 3D printed maraging steel inserts can revolutionize your injection molding operations? Contact the experts at Met3dp today to discuss your specific tooling challenges and discover how additive manufacturing can provide a competitive edge.
Partager sur
MET3DP Technology Co. est un fournisseur de premier plan de solutions de fabrication additive dont le siège se trouve à Qingdao, en Chine. Notre société est spécialisée dans les équipements d'impression 3D et les poudres métalliques de haute performance pour les applications industrielles.
Articles connexes
À propos de Met3DP
Mise à jour récente
Notre produit
CONTACTEZ-NOUS
Vous avez des questions ? Envoyez-nous un message dès maintenant ! Nous répondrons à votre demande avec toute une équipe dès réception de votre message.
Obtenir les informations de Metal3DP
Brochure du produit
Obtenir les derniers produits et la liste des prix
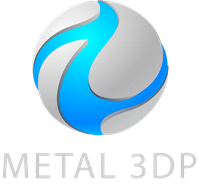
Poudres métalliques pour l'impression 3D et la fabrication additive