Poudre moulable par injection
Table des matières
Poudre moulable par injection désigne un type de matériau d'alimentation utilisé dans le moulage par injection de poudre, un procédé de fabrication industrielle permettant de produire des pièces métalliques complexes et de haute précision. Cette poudre est un mélange de poudres métalliques fines et de liants polymères qui peuvent être moulés par injection dans des pièces complexes de forme nette en grande quantité.
Avantages de l'utilisation de poudre moulable par injection
Avantage | Description | Bénéfice |
---|---|---|
Géométries complexes : L'IMP permet de créer des formes complexes avec des caractéristiques fines qui sont difficiles, voire impossibles à réaliser avec les techniques traditionnelles de moulage par injection. Cette liberté de conception ouvre la voie à des composants innovants dans diverses industries. | Contrairement aux matériaux de moulage traditionnels tels que les plastiques fondus, l'IMP utilise un système de liant qui maintient les particules de poudre ensemble pendant le processus de moulage. Cela permet de créer des pièces avec des canaux internes, des contre-dépouilles et d'autres géométries complexes. | |
Efficacité matérielle : L'IMP favorise une fabrication proche de la forme nette, ce qui minimise les pertes de matériaux par rapport aux techniques soustractives telles que l'usinage. Ceci est particulièrement bénéfique pour les matériaux coûteux ou à haute performance. | Le contrôle précis de la distribution de la poudre pendant le moulage par injection minimise l'utilisation de matériaux excédentaires. En outre, contrairement aux procédés traditionnels qui génèrent des pièces de rebut lors des essais, le moulage par injection permet des itérations de conception plus rapides avec un minimum de perte de matière. | |
Large choix de matériaux : L'IMP offre une plus grande variété de matériaux que le moulage par injection traditionnel. Cette polyvalence permet de créer des pièces aux propriétés spécifiques adaptées à l'application. | Au-delà des polymères standard utilisés dans le moulage par injection, l'IMP peut utiliser des poudres métalliques, des céramiques et même des matériaux composites. Cela ouvre la voie à la création de pièces présentant des combinaisons uniques de résistance, de conductivité ou de biocompatibilité. | |
Pièces haute performance : La possibilité d'utiliser des poudres métalliques et céramiques dans l'IMP permet de produire des pièces de haute performance présentant une solidité, une résistance à la chaleur ou des propriétés d'usure exceptionnelles. | Les composants métalliques moulés par injection (MIM) peuvent atteindre des propriétés mécaniques comparables à celles des métaux corroyés (en vrac), ce qui les rend adaptés à des applications exigeantes. De même, les pièces moulées par injection de céramique offrent une excellente résistance à l'usure et des performances à haute température. | |
Potentiel de production de masse : Initialement utilisée pour le prototypage, la technologie IMP a évolué pour permettre une production de masse rentable de pièces complexes. | Le haut degré d'automatisation des procédés IMP permet de produire efficacement de grandes quantités de pièces avec une qualité constante. Il s'agit donc d'une option viable pour les applications à grand volume. | |
Amélioration de l'état de surface : Par rapport aux techniques traditionnelles de moulage des métaux, l'IMP permet parfois d'obtenir une finition de surface plus lisse sur les pièces finales. | L'utilisation de poudres fines et le processus de moulage contrôlé permettent de minimiser les imperfections de surface, ce qui peut réduire la nécessité d'étapes de post-traitement approfondies telles que le polissage. |
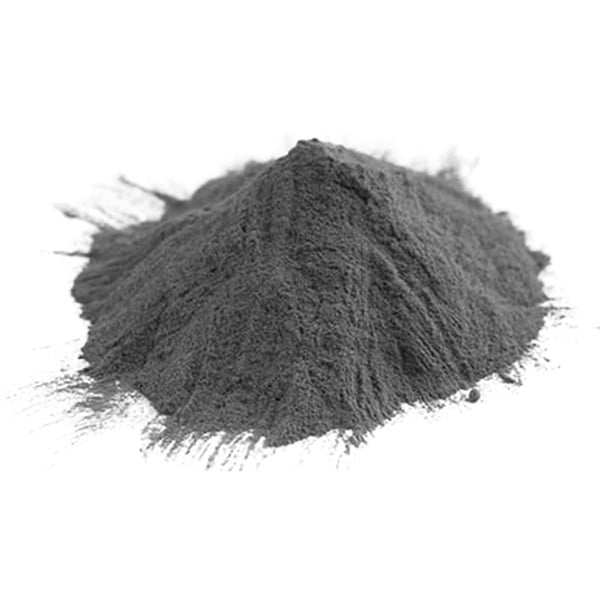
Composition de la poudre moulable par injection
Composant | Description | Fonction |
---|---|---|
Poudres de base | Ils constituent le principal matériau fonctionnel de la pièce finale et peuvent être classés en trois catégories principales : Poudres métalliques : Particules métalliques finement divisées de divers alliages, tels que l'acier inoxydable, l'acier à outils ou les superalliages. Poudres céramiques : Matériaux céramiques tels que l'alumine, la zircone ou le nitrure de silicium sous forme de poudre. Poudres de polymères : Polymères thermoplastiques couramment utilisés dans le moulage par injection, tels que le nylon ou le polypropylène. | Le choix de la poudre de base détermine les propriétés finales de la pièce moulée, telles que la solidité, la résistance à l'usure ou les performances thermiques. |
Système de reliure | Il s'agit d'un composant essentiel qui agit comme une colle temporaire, maintenant les particules de poudre de base ensemble pendant le processus de moulage. Le système de liant se compose généralement des éléments suivants Polymère thermoplastique : Résine thermoplastique qui fond pendant l'étape du moulage par injection, permettant la fluidité et l'adhérence avec la poudre de base. * Cires ou additifs : Ceux-ci peuvent améliorer les propriétés d'écoulement, l'efficacité du déliant ou la dispersion des poudres dans le liant. | Le système de liant garantit que la poudre se comporte comme une matière première moulable lors de l'injection et permet la création de formes complexes. |
Formateurs de pores | Il s'agit d'additifs facultatifs qui créent des pores temporaires dans la pièce moulée. Ils peuvent être : * Matériaux organiques : Ceux-ci se consument lors du déliantage, laissant derrière eux un réseau de pores qui facilite l'élimination du système de liant. * Agents de lixiviation chimique : Ceux-ci se dissolvent dans un solvant spécifique au cours d'une étape de post-traitement, créant ainsi une structure poreuse contrôlée. | Les formateurs de pores permettent de créer des structures poreuses dans la pièce finale, ce qui peut être bénéfique pour des applications telles que les filtres ou les implants osseux. |
Caractéristiques des poudres métalliques utilisées
Caractéristique | Description | Importance dans la MIM |
---|---|---|
Taille et distribution des particules | La taille et la distribution des particules de poudre métallique ont un impact significatif sur les aspects suivants du MIM : Remplissage des moules et résistance au vert : Les poudres plus fines offrent généralement une meilleure densité d'emballage et peuvent améliorer le remplissage des moules lors de l'injection. Toutefois, des particules trop fines peuvent nuire à la fluidité et poser des problèmes lors de la transformation. Une distribution étroite de la taille des particules garantit un compactage cohérent et minimise les vides dans la pièce moulée, ce qui contribue à une bonne résistance à l'état vert (résistance de la pièce avant le frittage). Comportement au frittage et propriétés finales : La taille des particules influence le processus de frittage, au cours duquel les particules s'assemblent pour former une structure solide. Les poudres ayant une distribution granulométrique plus large peuvent conduire à un frittage inhomogène et potentiellement affecter les propriétés mécaniques finales de la pièce. | Une sélection minutieuse de la taille et de la distribution des particules est cruciale pour obtenir un bon remplissage du moule, une bonne résistance à l'état vert et des performances optimales dans le composant fritté final. |
Morphologie des particules | Il s'agit de la forme des particules de poudre métallique. Idéalement, les procédés MIM favorisent les poudres de morphologie sphérique ou quasi-sphérique. | Les particules sphériques s'écoulent plus facilement, ce qui améliore le remplissage du moule et la densité de l'emballage. Les particules de forme irrégulière peuvent créer des vides et entraver l'écoulement, ce qui peut entraîner des défauts dans la pièce moulée. |
Densité apparente et densité à la prise | Ces propriétés représentent la densité apparente de la poudre dans différentes conditions. Densité apparente : Il s'agit de la densité de la poudre au repos, compte tenu des espaces entre les particules. Densité du robinet : Cela reflète un état plus dense obtenu grâce à un processus de taraudage standardisé. | Une densité de piquage plus élevée est généralement souhaitable dans le MIM pour une utilisation efficace des matériaux et une bonne précision dimensionnelle de la pièce finale. Elle contribue également à améliorer l'emballage pendant le moulage et à minimiser le retrait pendant le frittage. |
Composition chimique | Les éléments ou alliages spécifiques utilisés dans la poudre métallique déterminent les propriétés finales de la pièce frittée. | Le choix de la composition de la poudre métallique permet d'adapter les propriétés telles que la solidité, la résistance à la corrosion ou la résistance à l'usure pour répondre aux exigences spécifiques de l'application. Le MIM peut utiliser divers alliages métalliques, notamment l'acier inoxydable, l'acier à outils et même des alliages à haute performance comme l'Inconel. |
Capacité d'écoulement | Il s'agit de la facilité avec laquelle la poudre s'écoule sous l'effet de la gravité ou des forces appliquées. | Une bonne fluidité est essentielle pour une distribution uniforme de la poudre pendant le moulage par injection. Les poudres ayant une mauvaise fluidité peuvent entraîner des incohérences dans la densité de tassement et des défauts potentiels dans la pièce finale. |
Normes pour les poudres métalliques
Les poudres métalliques utilisées doivent répondre à des normes de composition et de granulométrie :
Corps standard | Standard | Description | Importance dans la PMI |
---|---|---|---|
ASTM International (ASTM) | ASTM B930 - Guide standard pour la caractérisation des poudres des matières premières pour le moulage par injection de métaux (MIM) | Cette norme décrit diverses méthodes d'essai pour caractériser les propriétés des poudres métalliques utilisées dans le MIM. | Il fournit un cadre pour l'évaluation de facteurs tels que la distribution de la taille des particules, la morphologie, la fluidité et la densité apparente. Cela garantit la cohérence et le contrôle de la qualité des poudres métalliques utilisées pour les applications de l'IMP. |
** | ** | * ASTM B783 - Spécification standard pour les poudres d'acier inoxydable pour les applications de moulage par injection de métal (MIM) | Cette norme définit les exigences spécifiques relatives à la composition chimique, à la distribution granulométrique et à la fluidité des poudres d'acier inoxydable utilisées dans le MIM. |
** | ** | * ASTM D4000 - Système de classification standard pour la spécification des matériaux plastiques | Bien qu'elle ne s'applique pas exclusivement à la PMI, cette norme fournit un système de classification pour divers types de matières plastiques, y compris celles potentiellement utilisées comme liants dans les matières premières de la PMI. |
Organisation internationale de normalisation (ISO) | * ISO 3095 - Poudres métalliques - Détermination du débit au moyen d'un débitmètre à effet Hall | Cette norme spécifie une méthode de mesure de l'écoulement des poudres métalliques à l'aide d'un débitmètre à effet Hall. | Fournit une approche normalisée de l'évaluation de la fluidité, une caractéristique essentielle pour obtenir un bon remplissage des moules et une qualité constante des pièces en IMP. |
** | ** | * ISO 4497 - Plastiques - Détermination du débit à l'état fondu (MFR) et du débit-volume à l'état fondu (MVR) des thermoplastiques | La présente norme décrit une méthode de mesure de la vitesse d'écoulement à l'état fondu (MFR) des matières thermoplastiques, qui peut s'appliquer au liant contenu dans les matières premières des IMP. |
Étapes du processus de fabrication
Le processus de fabrication comprend les étapes clés suivantes :
Étape | Description | Importance |
---|---|---|
1. Préparation et mélange des poudres | La poudre de base (métal, céramique ou polymère) est soigneusement sélectionnée et prétraitée en fonction des propriétés finales souhaitées. Des additifs tels que des agents de formation des pores ou des lubrifiants peuvent être ajoutés. La poudre est ensuite pesée avec précision et mélangée au système de liant pour former un produit de départ homogène. | Cette étape jette les bases des propriétés de la pièce finale. Une sélection minutieuse et un mélange précis garantissent un comportement cohérent du matériau au cours du traitement. |
2. Moulage par injection | La matière première IMP préparée est chauffée jusqu'à un état semi-fondu et injectée dans une cavité de moule fermée sous haute pression. Le moule reproduit la forme souhaitée de la pièce finale. | Cette étape définit la géométrie de la pièce. Un débit et une pression constants pendant l'injection sont essentiels pour obtenir des dimensions précises et un minimum de défauts. |
3. Débouclage | La pièce moulée, également appelée "pièce verte", est soumise à un processus de déliantage afin d'éliminer le système de liant. Ce processus peut être réalisé de la manière suivante * Débouclage par solvant : La pièce est immergée dans un solvant qui dissout le liant, laissant derrière lui la structure de la poudre. * Débouclage thermique : La pièce est exposée à un cycle de chauffage contrôlé, au cours duquel le liant se décompose thermiquement et s'échappe sous forme de gaz. | Un déliantage efficace est essentiel pour obtenir la forme et la porosité souhaitées sans endommager la structure délicate de la poudre. |
4. Frittage | La pièce ébarbée est soumise à des températures élevées dans une atmosphère contrôlée (souvent sous vide ou sous gaz inerte). Ce processus favorise la diffusion et la liaison entre les particules de poudre, ce qui permet d'obtenir un composant solide et de forme presque nette. | Le frittage détermine les propriétés mécaniques finales de la pièce, telles que la résistance, la densité et la stabilité dimensionnelle. Un contrôle précis de la température et de l'atmosphère est essentiel. |
5. Post-traitement | En fonction des exigences de l'application, la pièce frittée peut subir des étapes de finition supplémentaires telles que * Usinage ou rectification : Pour obtenir des tolérances dimensionnelles ou des finitions de surface précises. * Traitement thermique : Pour améliorer les propriétés mécaniques spécifiques telles que la résistance ou la dureté. * Revêtement ou infiltration : Améliorer les propriétés de la surface comme la résistance à l'usure ou à la corrosion. | Les traitements de post-traitement peuvent encore améliorer la fonctionnalité et l'esthétique de la pièce finale de l'IMP. |
Applications des pièces moulées par injection
Poudre moulable par injection peut être utilisé pour fabriquer diverses pièces complexes et de haute précision dans tous les secteurs d'activité :
L'industrie | Exemples d'application | Avantages du moulage par injection |
---|---|---|
Automobile | Composants intérieurs (tableaux de bord, panneaux de porte, consoles) Pièces sous le capot (carénages de ventilateurs, collecteurs d'admission) Composants fonctionnels (engrenages, pignons) | Production en grande quantité de formes complexes avec des caractéristiques précises. Pièces légères pour un meilleur rendement énergétique. Large gamme d'options de matériaux pour des besoins de performance variés (durabilité, résistance à la chaleur). |
Électronique grand public | Boîtiers électroniques (téléphones, ordinateurs portables, tablettes) Connecteurs et boutons Composants internes (supports, engrenages) | Production en masse de pièces complexes avec une grande précision dimensionnelle. Finitions de surface lisses pour l'esthétique et le confort de l'utilisateur. Variété de couleurs et de textures possibles grâce au choix des matériaux et aux techniques de moulage. |
Dispositifs médicaux | Instruments chirurgicaux (manches, poignées) Composants prothétiques (articulations du genou, implants dentaires) Composants médicaux à usage unique (seringues, flacons) | Matériaux stérilisables pour l'hygiène et la sécurité. Matériaux biocompatibles destinés à être utilisés dans le corps humain (certains polymères et alliages métalliques). Géométries complexes pour une fonctionnalité précise dans les applications médicales. |
Aérospatiale et défense | Composants d'aéronefs (conduits, pièces de trains d'atterrissage) Composants du satellite (supports, boîtiers) Équipement de défense (casques, composants d'armes) | Matériaux légers et à haute résistance pour la réduction du poids dans les applications aérospatiales. Matériaux ignifuges ou résistants à la chaleur pour des besoins spécifiques. Pièces durables pour les environnements difficiles et les conditions opérationnelles exigeantes. |
Biens de consommation | Jouets et jeux Appareils (boîtiers, boutons, cadrans) Articles de sport (casques, pièces de vélo) | Production rentable de produits de consommation en grande quantité. Grande variété de couleurs et de finitions pour l'attrait visuel. Pièces durables et fonctionnelles pour une utilisation quotidienne. |
Avantages du moulage par injection pour la fabrication de pièces
Avantage | Description | Bénéfice |
---|---|---|
Production en grande quantité : Le moulage par injection permet de produire efficacement de grandes quantités de pièces identiques. Les capacités d'automatisation et les temps de cycle rapides permettent une production de masse rentable. | Ceci est particulièrement avantageux pour les produits nécessitant des millions d'unités, tels que l'électronique grand public ou les composants automobiles. La qualité constante et la répétabilité sont assurées tout au long du cycle de production. | |
Flexibilité de la conception : Le moulage par injection peut s'adapter à un large éventail de complexités géométriques, y compris des formes complexes, des parois minces et des caractéristiques internes. Cette liberté de conception permet de créer des pièces fonctionnelles et innovantes. | Contrairement à certaines méthodes de fabrication soustractive, le moulage par injection n'est pas limité par la géométrie de l'outil. Des contre-dépouilles, des canaux et d'autres caractéristiques complexes peuvent être directement moulés dans la pièce. | |
Précision dimensionnelle et répétabilité : Le contrôle précis de la conception du moule et des paramètres d'injection permet d'obtenir des dimensions de pièces cohérentes et précises pour des volumes de production élevés. | Cela minimise le besoin d'étapes de post-traitement pour la correction dimensionnelle et garantit l'interchangeabilité des pièces lors de l'assemblage. La répétabilité est essentielle au maintien d'une qualité et d'une fonctionnalité constantes des produits. | |
Large choix de matériaux : Une vaste gamme de matériaux peut être utilisée dans le moulage par injection, notamment les thermoplastiques, les thermodurcissables, les élastomères et même certains alliages métalliques (par le biais du moulage par injection de métal - MIM). | Cette polyvalence permet de sélectionner le matériau optimal en fonction des propriétés souhaitées telles que la solidité, la résistance à la chaleur, la résistance chimique ou la flexibilité. | |
Finition de la surface et esthétique : Le moulage par injection permet de produire des pièces avec des finitions de surface lisses et de haute qualité, ce qui élimine souvent la nécessité d'étapes de post-traitement approfondies telles que le polissage. En outre, divers colorants et textures peuvent être incorporés pendant le moulage. | Cela contribue à l'attrait visuel et à la fonctionnalité du produit final. Les surfaces lisses peuvent être essentielles pour l'hygiène dans les dispositifs médicaux ou pour faciliter le nettoyage dans les biens de consommation. | |
Efficacité matérielle : Le moulage par injection favorise une fabrication proche de la forme nette, ce qui minimise le gaspillage de matériaux par rapport aux techniques soustractives telles que l'usinage. Les matériaux excédentaires, appelés carottes et canaux, peuvent souvent être recyclés et réutilisés dans des séries de production ultérieures. | Cela est bénéfique du point de vue des coûts et de la durabilité. La réduction des déchets permet également de diminuer l'impact environnemental du processus de fabrication. | |
Potentiel d'automatisation : Le processus de moulage par injection peut être fortement automatisé, avec une intervention humaine minimale. Cela permet d'obtenir une qualité de production constante et de réduire les coûts de main-d'œuvre. | L'automatisation est particulièrement avantageuse pour les productions en grande quantité et garantit une qualité constante du produit, quel que soit le niveau de compétence de l'opérateur. |
Limites du processus de fabrication
Il existe également certaines limites :
- Poids des pièces limité à < 400 g
- Épaisseur de la paroi > 0,4 mm
- Assemblages nécessaires pour les géométries complexes
- Outillage coûteux pour les moules
- Changements dimensionnels pendant le frittage
Fournisseurs mondiaux de matières premières
De nombreuses entreprises internationales fournissent des matières premières prêtes à l'emploi pour le moulage par injection :
Entreprise | Localisation | Matériaux |
---|---|---|
BASF | Allemagne | Acier inoxydable 316L, alliages de titane |
Sandvik | Suède | Aciers inoxydables, aciers à outils |
GKN | ROYAUME-UNI | Alliages d'aluminium et de magnésium |
Rio Tinto | Australie | Mélanges injectés de métal et de céramique |
Prix indicatifs
Matériau | Fourchette de prix |
---|---|
Acier inoxydable | $50-70 par kg |
Acier à outils | $45-65 par kg |
Alliage lourd de tungstène | $130-170 par kg |
Les prix dépendent du volume des commandes, des besoins de personnalisation et des facteurs économiques.
Avantages et inconvénients de l'utilisation Poudres moulables par injection
Avantages | Inconvénients |
---|---|
Formes compliquées et complexes | Taille et poids limités |
Tolérances plus étroites | Outils et équipements coûteux |
Finition fine de la surface | Changements dimensionnels pendant le frittage |
Gamme de matériaux | Le post-traitement est souvent nécessaire |
Production élevée, faible coût par pièce | Les matériaux fragiles ont tendance à se fissurer |
Réduction des déchets | Restreint le choix des matériaux |
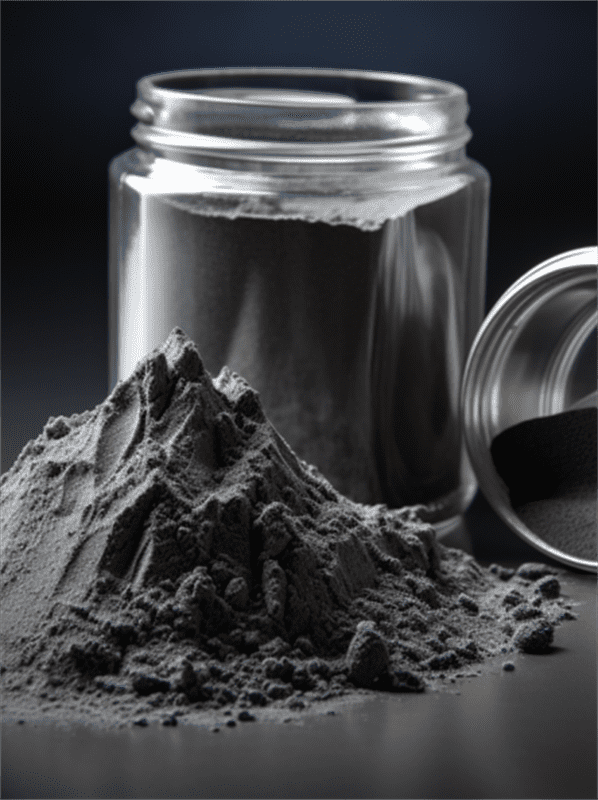
FAQ
Q : Quelle est la composition typique des poudres moulables par injection ?
R : Ils contiennent 80-90% de poudre métallique, 8-20% de liant et 1-2% de lubrifiant en poids. Les liants courants sont la cire, le PP, le PE et le PEG.
Q : Quelle est la gamme de tailles des poudres utilisées ?
R : Les poudres utilisées se situent entre 1 et 20 microns. Les poudres plus fines améliorent la densité mais peuvent être sujettes à l'agglomération.
Q : Quelle est l'ampleur du retrait lors du frittage ?
R : Jusqu'à 20%, le retrait linéaire des pièces se produit pendant le frittage en phase liquide. Des tolérances doivent être prévues dans la conception de l'outil.
Q : Quelles sont les causes des fissures dans les pièces moulées par injection en métal fritté ?
R : Chauffage non uniforme dans les fours, utilisation d'un refroidissement rapide après le frittage, mauvais mélange des poudres et choix d'alliages fragiles.
Q : Quelles sont les options de matériaux disponibles pour les poudres moulables par injection ?
R : Aciers inoxydables, aciers à outils, alliages lourds de tungstène, alliages de cuivre, titane et alliages de titane, entre autres.
Partager sur
MET3DP Technology Co. est un fournisseur de premier plan de solutions de fabrication additive dont le siège se trouve à Qingdao, en Chine. Notre société est spécialisée dans les équipements d'impression 3D et les poudres métalliques de haute performance pour les applications industrielles.
Articles connexes
À propos de Met3DP
Mise à jour récente
Notre produit
CONTACTEZ-NOUS
Vous avez des questions ? Envoyez-nous un message dès maintenant ! Nous répondrons à votre demande avec toute une équipe dès réception de votre message.
Obtenir les informations de Metal3DP
Brochure du produit
Obtenir les derniers produits et la liste des prix
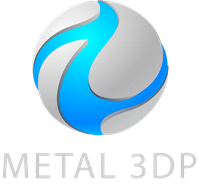
Poudres métalliques pour l'impression 3D et la fabrication additive