Moulage par injection de métal (MIM)
Table des matières
Imaginez un processus de fabrication qui associe les détails complexes et la liberté de conception du moulage par injection de plastique à la solidité et à la durabilité inégalées du métal. C'est la magie de Moulage par injection de métal (MIM), qui change la donne dans le monde de l'usinage des métaux.
Qu'est-ce que le moulage par injection de métal (MIM) ?
Le MIM est une technique de fabrication proche de la forme nette qui utilise un mélange unique de poudre métallique et d'un liant polymère. Cette combinaison, connue sous le nom de "feedstock", se comporte comme une pâte moulable. Le processus MIM injecte stratégiquement cette matière première dans une cavité de moule sous haute pression, reproduisant ainsi la géométrie complexe souhaitée. Voici la décomposition du processus MIM en ses principales étapes :
- Préparation des matières premières : Le métal finement pulvérisé, généralement de l'acier inoxydable, des alliages d'acier ou même des matériaux exotiques comme le carbure de tungstène, est méticuleusement mélangé à un système de liant. Ce liant assure la fluidité du mélange lors du moulage par injection.
- Moulage : La matière première préparée est injectée sous haute pression dans une cavité de moule conçue avec précision. Cela permet de reproduire la forme complexe, proche du filet, du composant métallique souhaité.
- Débouclage : Après le moulage, le liant doit être retiré de la pièce moulée. Ce processus délicat, souvent appelé déliantage, peut faire appel à des techniques thermiques (chauffage) ou à un déliantage par solvant, en fonction du système de liant choisi.
- Frittage : La pièce ébarbée, devenue une structure fragile de poudre métallique, est soumise à un processus de frittage à haute température dans une atmosphère contrôlée. Cette étape cruciale permet de fusionner les particules de métal et d'obtenir la résistance et la densité souhaitées pour le composant final.
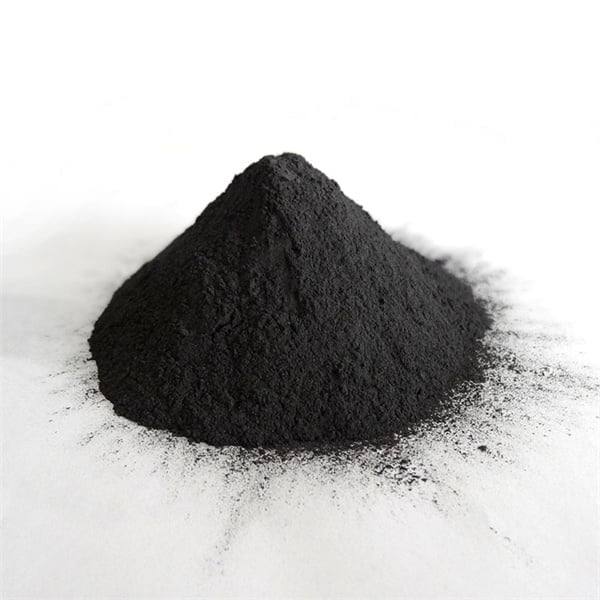
Les avantages de la Moulage par injection de métal (MIM)
Le MIM offre un ensemble d'avantages convaincants qui en font un processus très recherché par diverses industries :
- Géométries complexes : Contrairement aux techniques d'usinage traditionnelles qui peuvent se heurter à des formes complexes, le MIM excelle dans la production de composants aux caractéristiques complexes, aux tolérances serrées et aux parois minces. Cela ouvre la voie à des conceptions innovantes qui étaient auparavant difficiles, voire impossibles, à réaliser avec les méthodes conventionnelles.
- Haute précision et répétabilité : Le MIM tire parti de la précision du moulage par injection, ce qui permet d'obtenir des pièces très cohérentes avec des variations dimensionnelles minimales. Cela se traduit par des performances fiables et des besoins de post-traitement réduits.
- Production de masse : Le MIM est un procédé bien adapté à la production de gros volumes. Une fois le moule mis en place, le MIM peut produire efficacement un grand nombre de pièces identiques, ce qui le rend idéal pour les applications exigeant une qualité constante et de grandes quantités.
- Polyvalence des matériaux : Le MIM s'enorgueillit d'une large gamme de matériaux compatibles, des aciers inoxydables et aciers à outils courants aux options exotiques telles que le titane et l'inconel. Cela permet de sélectionner le matériau optimal en fonction de la résistance spécifique, de la résistance à la corrosion ou d'autres exigences de performance de l'application.
- Rapport coût-efficacité : Par rapport aux techniques d'usinage traditionnelles, en particulier pour les géométries complexes, le MIM permet de réaliser d'importantes économies. La possibilité d'obtenir des formes presque nettes minimise les pertes de matériaux et réduit la nécessité d'opérations d'usinage approfondies.
Applications du moulage par injection de métal (MIM)
Les divers avantages du MIM en ont fait un choix populaire dans un large éventail d'industries. Voici quelques exemples marquants :
- Automobile : Le MIM se distingue dans l'industrie automobile, où il produit des composants complexes tels que des engrenages, des pignons, des composants de soupapes et des pièces de systèmes d'alimentation en carburant, réputés pour leur durabilité et leur précision dimensionnelle.
- Dispositifs médicaux : La nature biocompatible de certains matériaux MIM les rend parfaits pour les applications médicales. Le MIM est utilisé pour créer des instruments chirurgicaux complexes, des implants et des composants pour divers appareils médicaux.
- Électronique grand public : La capacité de produire de petites pièces complexes avec une grande précision fait du MIM un outil idéal pour l'industrie de l'électronique grand public. Le MIM trouve des applications dans les connecteurs, les boîtiers et les composants internes de divers appareils électroniques.
- Aérospatiale et défense : Les exigences élevées des secteurs de l'aérospatiale et de la défense conviennent parfaitement au MIM. Le MIM produit des composants légers et très résistants pour les avions, les engins spatiaux et les systèmes d'armement.
Au-delà des avantages : Considérations relatives à la MIM
Bien que le MIM offre une multitude d'avantages, il est essentiel de prendre en compte certains facteurs avant de le choisir pour votre application spécifique :
- Limitations de la taille des pièces : Le MIM a actuellement des limites quant à la taille maximale des pièces qu'il peut produire. Les pièces dépassant un certain volume pourraient être mieux adaptées aux techniques traditionnelles d'usinage des métaux.
- Limites matérielles : Bien que le MIM offre une large gamme de matériaux, certains alliages exotiques ou spéciaux peuvent ne pas être facilement disponibles ou rentables grâce au MIM.
- Coûts de développement : La mise en place du processus MIM pour un nouveau composant nécessite un investissement initial dans le développement du moule et l'optimisation du processus. Ce facteur de coût doit être mis en balance avec le volume de production potentiel et les avantages à long terme.
Comprendre la MIM : une plongée technique
Pour ceux qui s'intéressent aux subtilités techniques du MIM, voici un examen plus approfondi de certains aspects clés :
Sélection des matières premières : La sélection de la bonne matière première est cruciale pour la réussite du MIM. Voici quelques aspects clés à prendre en considération :
- Poudre métallique :
- Taille et distribution des particules : La taille et la distribution de la poudre métallique ont un impact significatif sur les propriétés de la pièce finale. Les poudres plus fines permettent généralement des tolérances plus serrées et des finitions plus lisses, mais elles peuvent aussi être plus difficiles à traiter en raison de problèmes de fluidité. Une répartition équilibrée de la taille des particules est souvent préférable.
- Morphologie des poudres : La forme des particules métalliques joue également un rôle. Les poudres sphériques ont tendance à mieux s'écouler et à se tasser plus densément, ce qui améliore la résistance et la précision dimensionnelle.
- Système de reliure : Le système de liant agit comme une colle temporaire, maintenant la poudre métallique ensemble pendant le moulage et le déliantage. Les différents systèmes de liants présentent des caractéristiques variées, telles que la stabilité thermique, le comportement au déliantage et la compatibilité avec le processus de déliantage choisi.
Conception de moules pour la MIM :
Les moules MIM présentent des similitudes avec les moules de moulage par injection de plastique, mais nécessitent des considérations spécifiques pour le comportement des poudres métalliques :
- Conception de la porte : La conception des vannes, qui sont les points d'entrée de la matière première dans la cavité du moule, doit garantir un écoulement correct et minimiser les turbulences susceptibles d'entraîner des défauts.
- Ventilation : Les canaux d'aération sont essentiels pour permettre à l'air emprisonné de s'échapper pendant l'injection, afin d'éviter les vides et d'assurer le remplissage complet des pièces.
- Angles d'ébauche : Les angles de dépouille sur les parois du moule sont essentiels pour faciliter le démoulage de la pièce moulée après refroidissement.
Techniques de déliantage en MIM :
Comme nous l'avons déjà mentionné, le déliantage est l'étape critique qui consiste à retirer le liant de la pièce moulée. Voici une présentation des deux principales techniques de déliantage :
- Débouclage thermique : Cette méthode consiste à chauffer progressivement la pièce moulée dans une atmosphère contrôlée. À mesure que la température augmente, le liant se dégrade et se décompose, laissant derrière lui la structure de la poudre métallique. Le profil de chauffage doit être soigneusement conçu pour garantir l'élimination complète du liant sans endommager la structure métallique délicate.
- Débouclage par solvant : Cette technique utilise un solvant qui dissout sélectivement le système de liant. La pièce moulée est immergée dans le solvant, ce qui permet au liant d'être lessivé tandis que la poudre de métal reste intacte. Le déliantage par solvant peut être plus rapide que le déliantage thermique, mais il peut nécessiter une manipulation spéciale et des considérations d'élimination du solvant utilisé.
Frittage en MIM :
Le frittage est l'étape finale du processus MIM, au cours de laquelle la poudre métallique ébarbée se transforme en un composant solide et fonctionnel. Pendant le frittage, la pièce est exposée à des températures élevées (généralement entre 1/2 et 2/3 du point de fusion du métal) dans une atmosphère contrôlée. Cette température élevée favorise la liaison par diffusion entre les particules de métal, ce qui entraîne une densification et une amélioration significative de la résistance et d'autres propriétés mécaniques.
Contrôle de la qualité en MIM :
Le maintien d'une qualité constante est primordial dans la production de MIM. Voici quelques mesures essentielles de contrôle de la qualité :
- Caractérisation des matières premières : Des tests réguliers des propriétés de la matière première, tels que la distribution de la taille des poudres métalliques et la teneur en liant, garantissent un comportement cohérent du matériau au cours du traitement.
- Inspection dimensionnelle : Les dimensions des pièces moulées sont minutieusement contrôlées afin de s'assurer qu'elles répondent aux spécifications de conception et qu'elles conservent des tolérances étroites.
- Mesure de la densité : La densité des pièces frittées est un indicateur essentiel de leur résistance et de leurs performances. Diverses techniques, telles que le principe d'Archimède ou la pycnométrie, peuvent être utilisées pour mesurer la densité.
- Analyse de la microstructure : L'examen microscopique de la microstructure de la pièce frittée révèle des informations sur la taille des grains, la porosité et les défauts potentiels.
L'avenir de la Moulage par injection de métal
La MIM est une technologie en constante évolution et les efforts de recherche et de développement se concentrent sur les points suivants :
- Extension de la gamme de matériaux : L'exploration de nouveaux matériaux et systèmes de liants compatibles avec le MIM élargit les possibilités d'application de ce procédé polyvalent.
- Amélioration de l'efficacité des processus : La recherche vise à optimiser les étapes de déliantage et de frittage afin de réduire les temps de cycle et d'améliorer l'efficacité globale de la production.
- Complexité avancée des pièces : Les progrès réalisés dans la conception des moules et la science des matériaux repoussent les limites de la complexité des pièces réalisables grâce à la MIM.
Moulage par injection de métal offre un mélange unique de liberté de conception, de polyvalence des matériaux et de rentabilité pour un large éventail d'industries. Au fur et à mesure que la technologie évolue, nous pouvons nous attendre à des applications encore plus innovantes et à des avancées dans le monde passionnant du MIM.
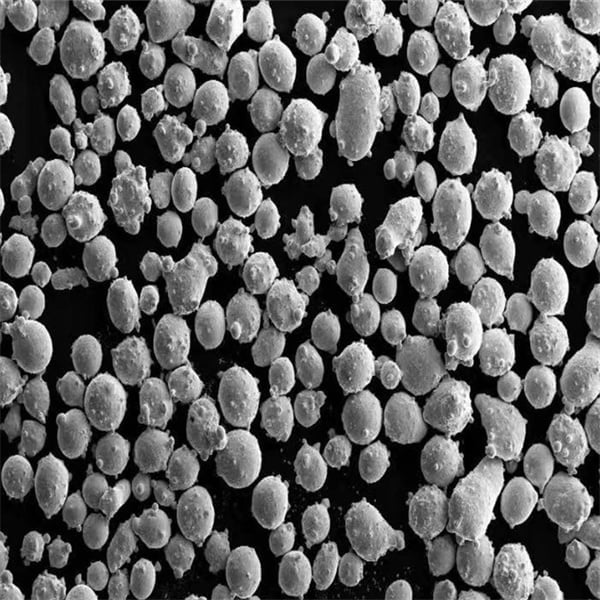
FAQ
Tableau 1 : Questions fréquemment posées sur le moulage par injection de métal (MIM)
Question | Répondre |
---|---|
Quelles sont les limites de taille typiques pour les pièces MIM ? | La taille maximale des pièces MIM est généralement limitée à quelques centimètres cubes. Cette limitation est due aux difficultés liées au flux de matières premières et à la garantie d'un ébarbage uniforme dans les pièces de grande taille. |
La MIM peut-elle être utilisée pour le prototypage ? | Oui, le MIM peut être une option viable pour le prototypage de pièces métalliques complexes, en particulier lorsqu'un degré élevé de précision et de fidélité à la conception finale est requis. Toutefois, le coût initial du développement du moule doit être pris en compte. |
Quels sont les avantages du MIM par rapport à l'usinage traditionnel ? | Le MIM offre plusieurs avantages par rapport à l'usinage traditionnel, notamment Capacité à produire des géométries complexes avec des tolérances serrées Une plus grande liberté de conception pour les caractéristiques complexes Haute précision et répétabilité pour des pièces homogènes Efficacité de la production de masse pour les grandes quantités Réduction des déchets de matière par rapport aux techniques soustractives |
Quels sont les inconvénients du MIM par rapport à l'usinage traditionnel ? | La MIM présente également certaines limites : Limitation de la taille des pièces par rapport à des techniques telles que le moulage ou le forgeage Limitations des matériaux pour certains alliages exotiques ou spéciaux Coûts initiaux plus élevés en raison du développement des moules La finition de la surface peut ne pas correspondre aux finitions exceptionnellement lisses que l'on peut obtenir par polissage ou meulage. |
Quels sont les facteurs à prendre en compte pour choisir entre le MIM et l'usinage traditionnel des métaux ? | Le choix idéal dépend de votre application spécifique. Voici quelques facteurs clés à prendre en compte : Complexité de la géométrie des pièces Exigences en matière de volume de production Besoins en matière de sélection des matériaux Considérations relatives aux coûts, y compris l'investissement initial et les économies potentielles Exigences de finition de surface |
Quelles sont les tendances futures de la technologie MIM ? | Les efforts de recherche et de développement dans le domaine du MIM sont axés sur l'élargissement de la gamme de matériaux, l'amélioration de l'efficacité des processus pour des temps de cycle plus courts et le repoussement des limites de la complexité des pièces réalisables. |
Quelles sont les applications typiques de la MIM ? | Le MIM trouve des applications dans un large éventail d'industries, notamment : Automobile (engrenages, pignons, composants de soupapes) Dispositifs médicaux (instruments chirurgicaux, implants) Électronique grand public (connecteurs, boîtiers) Aérospatiale et défense (composants légers et à haute résistance) |
Quels sont les différents types de matières premières utilisées dans le MIM ? | La matière première du MIM se compose généralement d'une poudre métallique (par exemple, acier inoxydable, alliages d'acier, titane) mélangée à un système de liant polymère. Le type spécifique de poudre métallique et de liant dépend des propriétés finales souhaitées pour la pièce. |
Quelles sont les différentes techniques de déliantage utilisées en MIM ? | Il existe deux techniques principales de déliantage : Déliantage thermique : Chauffage progressif pour éliminer le liant. Déliantage par solvant : Utilisation d'un solvant pour dissoudre sélectivement le liant. |
Choisir le bon processus : MIM et travail des métaux traditionnel
Le choix entre le MIM et les techniques traditionnelles d'usinage des métaux dépend de divers facteurs spécifiques à votre application. Voici quelques considérations clés pour vous guider dans votre choix :
- Géométrie de la pièce : Si votre composant présente des caractéristiques complexes, des tolérances serrées et des détails compliqués, le MIM offre un avantage significatif.
- Volume de production : Pour les productions en grande série, l'efficacité et la répétabilité du MIM en font une option convaincante.
- Sélection des matériaux : Assurez-vous que le matériau dont vous avez besoin est compatible avec le MIM. Si vous avez besoin d'un alliage exotique qui n'est pas facilement disponible dans le MIM, la métallurgie traditionnelle peut être la solution.
- Considérations relatives aux coûts : Il faut tenir compte des coûts initiaux de développement des moules pour le MIM par rapport au gaspillage potentiel de matériaux et aux délais de production plus longs des techniques traditionnelles pour les pièces complexes.
- Exigences en matière de finition de surface : Si une finition de surface impeccable est primordiale, des techniques traditionnelles telles que le polissage peuvent s'avérer nécessaires.
Conclusion
Le moulage par injection de métal (MIM) est un processus de fabrication puissant et polyvalent, qui offre une combinaison unique de liberté de conception, d'options de matériaux et de rentabilité pour une large gamme d'applications. En comprenant ses avantages, ses limites et sa comparaison avec les techniques traditionnelles d'usinage des métaux, vous pouvez prendre des décisions éclairées pour exploiter le MIM en fonction de vos besoins spécifiques et libérer le potentiel de composants métalliques innovants et performants.
Partager sur
MET3DP Technology Co. est un fournisseur de premier plan de solutions de fabrication additive dont le siège se trouve à Qingdao, en Chine. Notre société est spécialisée dans les équipements d'impression 3D et les poudres métalliques de haute performance pour les applications industrielles.
Articles connexes
À propos de Met3DP
Mise à jour récente
Notre produit
CONTACTEZ-NOUS
Vous avez des questions ? Envoyez-nous un message dès maintenant ! Nous répondrons à votre demande avec toute une équipe dès réception de votre message.
Obtenir les informations de Metal3DP
Brochure du produit
Obtenir les derniers produits et la liste des prix
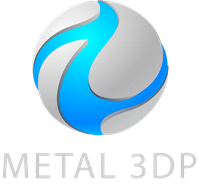
Poudres métalliques pour l'impression 3D et la fabrication additive