Équipement d'atomisation des poudres métalliques
Table des matières
Atomisation de poudres métalliques est une technique de réduction de la taille des particules utilisée pour produire des poudres métalliques fines aux caractéristiques optimisées pour des applications industrielles. Ce procédé consiste à forcer le métal en fusion à travers une buse pour le désintégrer en gouttelettes uniformes qui se solidifient rapidement en particules de poudre.
L'atomisation permet de contrôler la distribution de la taille des particules de poudre, leur morphologie, leur pureté et d'autres propriétés essentielles pour obtenir des performances élevées dans l'impression 3D de métaux, la fabrication de pièces par métallurgie des poudres, les processus de revêtement métallique, etc. Cet article présente une vue d'ensemble des différents types d'équipements d'atomisation, des principes de fonctionnement, des considérations de conception, des applications, des avantages et des limites.
Aperçu du processus d'atomisation des poudres métalliques
L'atomisation des poudres métalliques convertit le métal liquide en vrac en poudres sphériques fines aux caractéristiques contrôlées. Pour ce faire, un flux de métal en fusion est divisé en fines gouttelettes par l'impact d'un jet de gaz ou de liquide. Les gouttelettes se solidifient rapidement en particules de poudre en refroidissant.
Les principales étapes de ce processus sont les suivantes :
- Fusion des métaux - La charge de métal brut est fondue à l'aide d'un four à induction, d'une fusion à l'arc ou d'autres techniques. Les métaux couramment atomisés sont l'aluminium, le titane, le nickel, le fer, le cobalt, le cuivre, etc.
- Approvisionnement en métal fondu - Le métal liquide est maintenu à une température optimale et acheminé vers la zone d'atomisation à l'aide d'un répartiteur, d'un creuset ou d'une pompe.
- Atomisation - Le flux de métal en fusion est désintégré en gouttelettes par interaction avec un gaz ou un liquide à grande vitesse. Différentes méthodes d'atomisation sont utilisées.
- Collection de poudres - La poudre métallique atomisée est refroidie et collectée pour les opérations en aval. Des procédés de tamisage, de séparation magnétique et de recuit peuvent être utilisés.
- Caractérisation des poudres - La distribution de la taille des particules, la morphologie, la densité, la fluidité et la microstructure de la poudre sont analysées.
Un contrôle approprié des paramètres du processus, tels que la composition du métal, la température, la vitesse du fluide d'atomisation et la conception de l'atomiseur, est essentiel pour obtenir les caractéristiques souhaitées de la poudre.
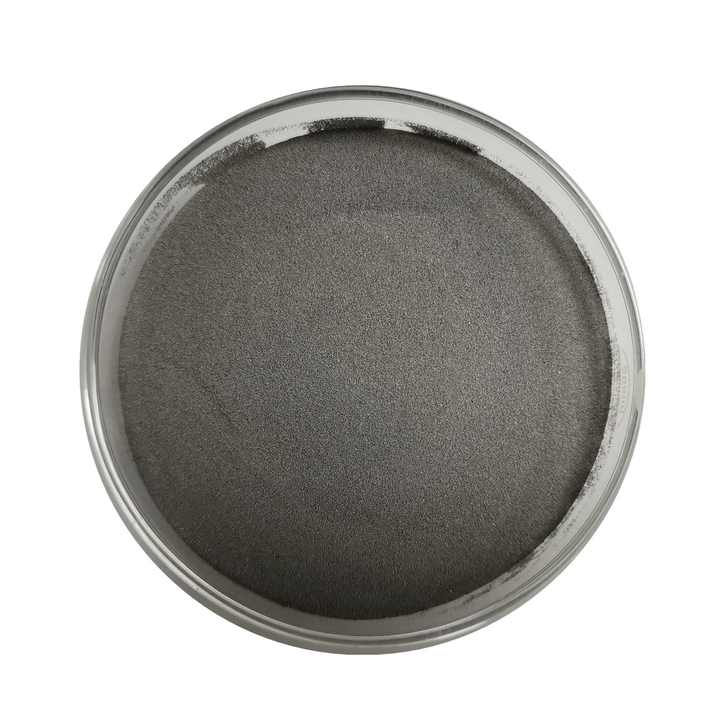
Types d'équipements d'atomisation
Les systèmes d'atomisation peuvent être classés en fonction du support utilisé pour désintégrer le métal en fusion en gouttelettes :
Atomisation des gaz
Dans l'atomisation au gaz, l'énergie cinétique du gaz à haute pression accélère rapidement et disperse le flux de métal liquide en fines gouttelettes. En fonction de la conception de l'alimentation en gaz, il est possible d'établir une classification plus détaillée :
- Atomisation par gaz sous pression - Utilise des buses rapprochées pour envoyer de l'air comprimé ou du gaz inerte latéralement sur le flux de métal liquide.
- Atomisation de gaz par buse à deux fluides - Les buses coaxiales introduisent le gaz d'atomisation à haute vitesse autour d'un tube de distribution métallique interne.
- Atomisation gazeuse à buses multiples - Utilise un ensemble de buses convergentes-divergentes pour délivrer des jets de gaz supersoniques sur le flux de matière fondue.
Les poudres atomisées au gaz ont une taille de particule plus faible, une morphologie plus uniforme et une pureté plus élevée que les poudres atomisées à l'eau. Mais le processus est gourmand en énergie et coûteux.
Atomisation de l'eau
Dans l'atomisation à l'eau, le flux de métal en fusion est désintégré par son impact avec des jets d'eau à haute pression. Des gouttelettes avec une distribution de taille plus large sont formées. L'atomisation à l'eau présente des coûts d'investissement et d'exploitation inférieurs à ceux de l'atomisation au gaz.
Selon la conception, la pulvérisation d'eau peut être utilisée :
- Atomisation de l'eau en circuit fermé - Les jets d'eau frappent directement le métal liquide sortant du répartiteur.
- Atomisation de l'eau en chute libre - Le flux de métal en fusion qui tombe est intercepté par des jets d'eau sous le répartiteur.
Les poudres atomisées à l'eau ont des formes de particules plus irrégulières et une distribution plus large, idéales pour le pressage et le frittage. Mais l'eau introduit une contamination.
Atomisation centrifuge
Dans l'atomisation centrifuge, le métal en fusion est versé ou pompé dans un disque ou une coupelle tournant à grande vitesse. Le métal forme une fine pellicule sur le périmètre qui se désintègre en fines gouttelettes sous l'effet des forces centrifuges.
Parmi les avantages, citons la simplicité de la conception, la faible consommation de gaz et la facilité de mise à l'échelle. Mais la gamme de tailles est relativement plus élevée que celle de l'atomisation au gaz. Utilisé pour produire des poudres sphériques à partir de métaux à faible point de fusion comme l'étain, le plomb, le zinc, etc.
Atomisation ultrasonique de gaz
Combine l'atomisation par gaz avec un générateur d'ultrasons couplé à la buse. Les vibrations à haute fréquence favorisent la désintégration et la dispersion du métal en gouttelettes plus fines, ce qui permet d'obtenir une poudre submicronique.
Très efficace pour générer des morphologies de poudres nanocristallines et amorphes. Mais coûteux et exigeant en termes de maintenance. Utilisé pour des applications spécialisées.
Spark Erosion Atomisation
Dans cette technique d'atomisation électrique, une décharge d'étincelles à courant élevé pulsé est appliquée entre le métal en fusion et une pointe d'électrode, créant un plasma qui désintègre le métal en une poudre sphérique ultrafine.
Permet de produire des poudres métalliques très fines et très sphériques. Mais le taux de production est faible et le coût élevé. Principalement utilisé pour les métaux précieux tels que l'or, le platine et le palladium.
Composants et conception de l'atomiseur
Les atomiseurs sont constitués d'une variété de composants conçus pour fondre, verser, atomiser, refroidir et collecter efficacement la poudre métallique.
Système de fusion et de coulée des métaux
- Four à induction - Le plus souvent utilisé pour la fusion de métaux tels que l'acier. Elle permet un bon contrôle de la température et une faible contamination de la matière fondue.
- Creusets - Pots en céramique réfractaire utilisés pour contenir la charge métallique. Ils peuvent être chauffés dans un four séparé et versés manuellement ou directement incorporés dans le système d'atomisation.
- Tundish - Réservoir intermédiaire de métal en fusion qui contrôle le taux de coulée dans la section d'atomisation.
- Descente d'eau - Dirige avec précision le flux de métal en fusion dans la zone d'atomisation. Fabriqué en métal réfractaire comme le tungstène pour résister aux températures élevées.
- Pompes - Utilisé pour contrôler l'alimentation en métal fondu sous pression dans certaines configurations d'atomiseurs.
Section d'atomisation
- Buse d'atomisation - Buses spécialisées résistantes à la pression et à la température, utilisées pour créer des jets de gaz ou d'eau pour l'atomisation.
- Réseaux de buses - Plusieurs buses spécialisées positionnées stratégiquement pour optimiser la formation des gouttelettes.
- Composants de filature - Les disques et les coupes utilisés dans l'atomisation centrifuge tournent à des vitesses très élevées - de 10 000 à 50 000 tours/minute - sous l'action d'un moteur électrique.
- Générateur d'ultrasons - Convertit le signal électrique en vibrations mécaniques à haute fréquence dans la zone de la buse. Utilisé pour l'atomisation par ultrasons.
- Alimentation électrique - Fournit le courant élevé nécessaire à la génération d'un arc électrique pour l'atomisation par érosion par étincelles.
Système de manutention des poudres
- Cyclones Séparateurs - Séparer la poudre fine des flux de gaz ou d'eau en utilisant les forces centrifuges.
- Filtres à manches - Collecte les poudres très fines qui ne sont pas séparées dans les cyclones. Nécessitent un remplacement fréquent.
- Tamis classificateurs - Classification de la poudre en différentes fractions à l'aide de tamis à mailles.
- Séparateurs magnétiques - Éliminer tout contaminant métallique de la poudre.
- Convoyeurs - Transport de la poudre entre les équipements. Utilisation de convoyeurs à vis, à bande et vibrants.
- Trémies - Stocke la poudre en vue d'un traitement ou d'un conditionnement ultérieur.
- Nettoyage par aspiration - Enlève les poudres répandues sur les équipements et les surfaces.
Instrumentation et contrôles
- Capteurs de température - Il est essentiel de surveiller et de contrôler la température du four/de la matière fondue et de la buse pour une atomisation optimale.
- Capteurs de pression - Contrôler la pression du gaz et de l'eau dans les buses pour maintenir une atomisation correcte.
- Débitmètres - Mesurer et contrôler les débits du fluide d'atomisation et de la matière fondue.
- Tachymètres - Contrôle la vitesse de rotation des disques d'atomisation centrifuge.
- Capteurs de niveau - Maintient des niveaux de fusion optimaux dans les vaisseaux clés. Prévient les débordements.
- Arrêt d'urgence - Nécessaire pour un arrêt rapide et sûr des machines en cas de problème.
- Système de contrôle - La commande automatisée par ordinateur optimise la coordination des paramètres et améliore la répétabilité.
Paramètres du processus d'atomisation des poudres métalliques
La sélection correcte des paramètres du procédé est essentielle pour obtenir des poudres présentant les caractéristiques souhaitées. Le tableau ci-dessous résume les variables clés et leur influence sur les propriétés de la poudre :
Paramètres | Effet sur les propriétés de la poudre |
---|---|
Température du métal en fusion | Une température plus élevée réduit la viscosité et améliore l'atomisation. Mais elle peut augmenter l'oxydation et les pertes par évaporation. |
Pression du gaz d'atomisation | Une pression de gaz plus élevée améliore la distribution de la taille des particules et réduit la taille moyenne. Mais elle augmente la consommation de gaz. |
Débit du gaz d'atomisation | Un débit plus élevé améliore la réduction de la taille des particules. Mais augmente la consommation de gaz. |
Vitesse du fluide d'atomisation | Une vitesse plus élevée améliore la réduction de la taille des particules. Dépend de la conception de la buse. |
Conception de la buse | les buses spécialisées créent des gouttelettes et des poudres plus fines. |
Taux d'écoulement de la matière fondue | Des taux de coulée plus élevés augmentent le rendement pour un fonctionnement continu, mais peuvent réduire la taille des particules. |
Surchauffe de la matière fondue | Augmente lorsque la température de coulée s'élève au-dessus du point de fusion. Améliore la fluidité. |
Filtration de la matière fondue | Élimine les inclusions et les contaminants. Améliore la pureté de la poudre. |
Distance d'atomisation | La distance de chute libre plus longue laisse plus de temps pour la formation de gouttelettes. Réduit la formation de satellites. |
Composition de la matière fondue | Les éléments d'alliage peuvent modifier la viscosité, la tension superficielle, affecter le comportement d'atomisation et les caractéristiques de la poudre. |
Caractérisation des poudres métalliques atomisées
Les propriétés et la qualité de la poudre atomisée déterminent les performances des applications en aval. Les principales caractéristiques évaluées sont les suivantes
Distribution de la taille des particules
La distribution des particules de poudre à travers différentes fractions de taille, communément représentées par les percentiles D10, D50 et D90. L'atomisation au gaz permet d'obtenir des particules de moins de 20 microns, tandis que l'atomisation à l'eau produit une poudre plus grossière.
Forme et morphologie des particules
La poudre atomisée au gaz présente des particules très sphériques, tandis que la poudre atomisée à l'eau est plus irrégulière. Les particules satellites indiquent que l'atomisation n'est pas optimale. La poudre arrondie a un meilleur écoulement et une meilleure densité d'emballage.
Composition chimique
La composition élémentaire et la composition de phase à partir d'analyses. Détermine la qualité de l'alliage. L'atomisation au gaz permet d'obtenir une grande pureté, tandis que l'eau peut contaminer les métaux réactifs tels que le titane et l'aluminium.
Densité apparente et densité à la prise
Indicateur de l'efficacité du conditionnement de la poudre. Une densité plus élevée améliore les propriétés du produit lors du pressage et du frittage. Mais elle peut affecter l'écoulement de la poudre. Les valeurs sont généralement comprises entre 40 et 65% de la densité du matériau.
Caractéristiques du débit
Important pour la manipulation et le traitement en aval. Influencé par des facteurs tels que la forme des particules, la distribution des tailles, la structure de la surface. Amélioré par le recuit, le traitement de surface.
Microstructure
Structure interne de la poudre révélée par microscopie. La poudre atomisée au gaz présente des grains fins et des défauts dus à une solidification rapide, tandis que la poudre atomisée à l'eau est plus grossière. Détermine le comportement au frittage.
Applications de l'atomisation des poudres métalliques
Les poudres métalliques atomisées trouvent un large éventail d'utilisations dans la fabrication de pointe, améliorant la qualité et les performances des produits par rapport au traitement conventionnel des métaux :
Fabrication additive
- Impression 3D - Les poudres sphériques atomisées avec une distribution de taille contrôlée sont idéales pour les techniques de fusion sur lit de poudre. Les superalliages d'aluminium, de titane et de nickel sont couramment utilisés.
- Moulage par injection de métaux - Des poudres plus fines d'acier inoxydable, de titane et d'aluminium améliorent le processus de frittage et la densité des composants.
Métallurgie des poudres
- Pressage et frittage - Poudre ferreuse irrégulière, plus grossière, atomisée à l'eau, utilisée pour une production élevée de pièces P/M présentant de bonnes propriétés mécaniques.
- Aimants doux et durs - Les poudres NdFeB et SmCo finement cristallisées produisent des aimants collés et pressés à chaud très performants.
- Matériaux de friction - La poudre de cuivre atomisée à l'eau améliore les performances des plaquettes de frein et des garnitures d'embrayage.
Revêtements de surface
- Pulvérisation thermique - Poudre sphérique à distribution granulométrique contrôlée, importante pour les revêtements uniformes et denses par pulvérisation plasma ou HVOF. WC-Co, poudre d'alliage de nickel utilisée.
- Dépôt en phase vapeur - Poudre ultrafine de superalliage utilisée dans le dépôt physique en phase vapeur par faisceau d'électrons pour les revêtements de turbines à protection renforcée.
Autres
- Moulage par injection de métaux - Les poudres fines d'acier inoxydable, de titane et d'aluminium permettent de produire des composants complexes de petite taille.
- Pâtes à braser - Alliage d'argent, d'or et de cuivre atomisé utilisé pour la fabrication de joints de brasure à haute température.
- Érosion par étincelage - La poudre sphérique ultrafine utilisée comme milieu diélectrique améliore la précision et la vitesse de l'usinage par électroérosion.

Avantages de l'atomisation des poudres métalliques
Par rapport aux méthodes conventionnelles de traitement des métaux, les principaux avantages de l'utilisation de poudres atomisées sont les suivants :
- Amélioration des propriétés mécaniques - Une microstructure fine et homogène résultant d'une solidification rapide augmente la limite d'élasticité, la résistance à la fatigue et la ductilité.
- Contrôle dimensionnel précis - La poudre constante et sphérique permet une densité élevée et une fabrication précise de la forme du filet. Réduit l'usinage.
- Productivité accrue - Les composants peuvent être produits en masse par le traitement des poudres métalliques plus rapidement que par les méthodes soustractives.
- Une plus grande liberté de conception - Il est possible de fabriquer des géométries complexes impossibles à réaliser par moulage ou usinage.
- Minimise les déchets - La possibilité d'obtenir une forme presque nette réduit la perte de ferraille par rapport à la métallurgie des lingots. La poudre non utilisée peut être recyclée.
- Réduction de la consommation d'énergie - Le processus de fabrication des poudres nécessite une température et une énergie plus faibles que la production à partir de métal en vrac.
- Alliages sur mesure - Il est possible d'atomiser des compositions spécialisées qui sont difficiles à produire en lingots.
- Haute pureté - Les éléments réactifs comme le titane peuvent être atomisés avec une contamination plus faible que les pratiques conventionnelles.
Limites de l'atomisation des poudres métalliques
- L'équipement d'atomisation et les systèmes de manutention des poudres nécessitent des investissements élevés par rapport au traitement des métaux en vrac.
- D'autres processus en aval, tels que le compactage, le frittage, etc. sont nécessaires pour fabriquer des produits à partir de poudres. L'ensemble du processus de production est complexe.
- L'obtention d'une poudre ultrafine à l'échelle nanométrique peut s'avérer difficile et coûteuse, avec des débits moindres.
- Risque de contamination lors de l'utilisation de la pulvérisation d'eau, en particulier pour les métaux réactifs.
- La poudre peut adsorber l'oxygène et l'humidité, ce qui nécessite une protection lors du stockage et de la manipulation.
- Il existe des problèmes de sécurité liés aux explosions de poussières, aux risques d'incendie et à la toxicité de certaines compositions et morphologies de poudres.
- Variabilité des propriétés du composant final par rapport aux produits corroyés. Les défauts liés à la poudre peuvent se manifester après la consolidation.
- Le recyclage et la réutilisation des poudres métalliques sont limités par rapport aux formes métalliques en vrac. Le matériau est mis au rebut après un ou deux cycles de réutilisation.
- L'absence de normes industrielles pour les nouvelles poudres métalliques concernant les caractéristiques, la méthodologie d'essai, le contrôle de la qualité et la certification crée des obstacles à l'adoption.
Sélection d'un système d'atomisation des poudres métalliques
Le choix de l'équipement d'atomisation adapté à une application dépend de facteurs tels que
Volume de production
- Faible production - atomiseurs à l'échelle du laboratoire et du pilote. Systèmes d'atomisation centrifuge ou à gaz sous pression.
- Production moyenne - Atomiseurs continus d'une capacité de production de poudre allant jusqu'à 3 tonnes/heure.
- Production élevée - Systèmes personnalisés à grande échelle d'une capacité supérieure à 10 tonnes/heure.
Matériau de la poudre
- Les métaux non réactifs comme l'acier et les alliages de nickel peuvent être pulvérisés avec de l'eau.
- Les alliages sensibles à l'eau comme l'aluminium et le titane nécessitent une atomisation par gaz inerte.
- Les métaux réfractaires tels que le tungstène nécessitent des moyens d'atomisation et une protection spécialisés.
Propriétés des poudres
- Atomisation au gaz pour des poudres plus fines, inférieures à 30 microns, avec une morphologie sphérique.
- Pulvérisation d'eau pour une poudre plus grossière et irrégulière pour le pressage.
- Atomisation spécialisée pour les poudres métalliques nanocristallines ou amorphes.
Application du produit
- La fabrication additive utilise des poudres très fines, à distribution de particules contrôlée, obtenues par atomisation au gaz.
- Le moulage par injection de poudre nécessite une poudre fine et sphérique avec un bon écoulement.
- Les revêtements par projection thermique nécessitent une poudre dense et sphérique qui se tasse bien.
Coûts d'investissement et de fonctionnement
- L'atomisation à l'eau a un coût d'équipement et un coût d'exploitation plus faibles, mais peut compromettre la qualité de la poudre.
- L'atomisation au gaz a un coût d'investissement 10 fois plus élevé mais produit une poudre supérieure. Les coûts d'exploitation sont également plus élevés.
- L'atomisation centrifuge est économique mais présente des limites de taille et de forme.
Intégration de l'usine
- Nécessite une infrastructure suffisante pour la préparation de la fonte, la manipulation de la poudre, le stockage et le transport.
- Systèmes de protection pour les métaux réactifs comme l'atmosphère de gaz inerte.
- Les contrôles automatisés et la surveillance des données améliorent la stabilité du processus.
Principaux fabricants d'atomiseurs de poudres métalliques
Plusieurs entreprises proposent des systèmes et des composants d'atomisation de poudres métalliques standardisés ou conçus sur mesure :
Systèmes d'atomisation des gaz
- Praxair - leader du marché des équipements de pulvérisation de gaz à haute pression. Propose des systèmes à l'échelle du laboratoire, du pilote et de la production.
- AP&C - Spécialisé dans les atomiseurs de gaz à tuyères rapprochées pour les métaux réactifs et réfractaires. Très utilisés pour les poudres de titane et d'aluminium.
- ALD Vacuum Technologies - Conçoit des atomiseurs de gaz à buses multiples pour une production moyenne à élevée. Propriété d'Oerlikon Metco.
Atomisation de l'eau
- Gasbarre - Propose une atomisation de l'eau par couplage étroit et par chute libre pour des volumes moyens à élevés.
- Sheffield Atomising Systems - Spécialisé dans la technologie d'atomisation de l'eau en chute libre depuis plus de 50 ans.
Atomisation centrifuge
- ABB - Important fournisseur mondial d'équipements. Propose des systèmes d'atomisation centrifuge, du laboratoire à l'échelle de production complète.
- Ferrum AG - Principal fournisseur d'atomiseurs centrifuges horizontaux et verticaux basé en Suisse.
Atomisation par ultrasons
- Tekna - Propose des systèmes d'atomisation de gaz à ultrasons basés sur sa technologie brevetée de guide d'induction à double fil couplé.
- Ultramet - Fournit des équipements d'atomisation ultrasonique spécialisés avec une technologie de liquéfaction à haute température.
Spark Erosion Atomisation
- PyroGenesis - Propose le système d'atomisation par plasma (PAS) pour la production de poudres métalliques sphériques ultrafines.
- Plasma Innovations - Fournit des systèmes d'atomisation par érosion par étincelles à électrodes rotatives (REP).
Analyse des coûts des atomiseurs de poudre métallique
Le coût de l'atomiseur dépend de l'échelle, du taux de production, du niveau d'automatisation et de la poudre traitée. Estimation des coûts d'investissement typiques :
Atomiseur de gaz à grande production | Construction sur mesure | 1000 | 10 millions d'euros |
---|---|---|---|
Atomiseur d'eau de petite production | Système de remorque/conteneur | 100 | 750,000 |
Atomiseur d'eau à moyenne production | Système d'abris | 500 | 2 millions d'euros |
Atomiseur d'eau à grande production | Construction sur mesure | 2000 | 5 millions d'euros |
Atomiseur centrifuge pilote | Monté sur patins | 50 | 400,000 |
Atomiseur centrifuge moyen | Système d'abris | 500 | 1,5 million d'euros |
Atomiseur ultrasonique de laboratoire | Établi | 5 | 250,000 |
Atomiseur ultrasonique Pilot | Monté sur patins | 20 | 1 million d'euros |
Atomiseur d'érosion par étincelles | Système de conteneurs | 10 | 2 millions d'euros |
Coûts de fonctionnement
- Les principaux coûts sont l'énergie, la main-d'œuvre, la maintenance et l'utilisation de gaz inerte.
- La consommation d'énergie pour l'atomisation du gaz est de ~500-800 kWh par tonne de poudre. La consommation de gaz est de 5 à 10 m3 par kg de poudre.
- La consommation d'énergie pour l'atomisation de l'eau est plus faible (~200-400 kWh par tonne de poudre). Mais la main-d'œuvre et l'entretien sont plus élevés.
- Consommation d'énergie de l'atomisation centrifuge ~300-500 kWh par tonne de poudre. Utilisation moindre de gaz inerte.
- Les pièces consommables telles que les buses et les sacs filtrants doivent être remplacées fréquemment.
Possibilités de réduction des coûts
- L'augmentation de l'échelle de production et de la production de poudre réduit le coût d'investissement par kg de poudre.
- Un degré plus élevé d'automatisation et de surveillance améliore la productivité du travail.
- Le recyclage et la réutilisation des gaz de traitement, de l'eau et de la chaleur résiduelle réduisent les frais d'exploitation.
- Les programmes de maintenance préventive réduisent les temps d'arrêt et les coûts de maintenance.
- La fourniture locale d'énergie, de gaz, d'eau et de services auxiliaires réduit les dépenses logistiques.
- L'achat de systèmes d'atomisation reconstruits/utilisés réduit les dépenses d'investissement pour les petits producteurs.
Équipement d'atomisation des poudres métalliques - Questions fréquemment posées
Q : Quelle est la gamme de tailles de particules typiques obtenue par atomisation au gaz ?
R : L'atomisation au gaz peut produire des poudres d'une taille allant de 1 micron à plus de 100 microns. Les valeurs D50 typiques sont de 10 à 45 microns pour la plupart des alliages. Il est possible d'obtenir des poudres plus fines, inférieures à 10 microns, avec des buses optimisées et des vitesses de gaz élevées.
Q : Quelle est la production annuelle d'un petit système d'atomisation de gaz ?
R : Un atomiseur de gaz à échelle pilote d'une capacité de 10 kg/h fonctionnant 5 000 heures par an peut produire environ 50 000 kg de poudre par an. Un petit système de production d'une capacité de 50 kg/h peut produire environ 250 000 kg par an en pleine production.
Q : Quels sont les types de métaux qui peuvent être réduits en poudre par atomisation ?
R : La plupart des systèmes d'alliage commerciaux ont été atomisés, y compris l'acier inoxydable, l'acier à outils, les alliages de nickel, les alliages de titane, les alliages d'aluminium, les superalliages, les alliages de cobalt, etc. Les métaux réfractaires tels que le tungstène et le molybdène posent des problèmes et nécessitent des systèmes d'atomisation spécialisés.
Q : Quelle est la meilleure méthode d'atomisation pour les métaux réactifs comme le titane ?
R : L'atomisation au gaz avec un gaz inerte comme l'argon ou l'azote est préférable pour les métaux réactifs comme le titane et l'aluminium. Cela permet d'éviter l'oxydation et la contamination par rapport à l'atomisation à l'eau.
Q : Quelle est la finesse des particules obtenues par atomisation ultrasonique ?
R : Les atomiseurs de gaz à ultrasons peuvent produire des poudres métalliques submicroniques et nanométriques dont la taille moyenne est inférieure à 100 nanomètres lorsqu'ils sont optimisés. Mais le taux de production de poudre est faible.
Q : La poudre métallique peut-elle être recyclée après avoir été utilisée dans la fabrication additive ?
R : Oui, la poudre non utilisée peut être réutilisée dans les processus AM. Mais la poudre ne peut être recyclée que 1 à 2 fois avant que ses propriétés ne se dégradent. La poudre doit alors être réatomisée pour pouvoir être réutilisée.
Q : Quelle est la meilleure façon de manipuler une fine poudre réactive ?
R : Utiliser des boîtes de gants inertes, sceller les conteneurs de poudre, éviter l'exposition à l'air/l'humidité. Certains matériaux réactifs peuvent nécessiter un traitement de surface. La poudre d'aluminium atomisée à l'eau est généralement recouverte d'un revêtement pour éviter l'oxydation.
Q : Pourquoi un gaz inerte de haute pureté est-il important pour l'atomisation du gaz ?
R : Une pureté élevée minimise la contamination. L'humidité et l'oxygène peuvent oxyder les alliages réactifs pendant l'atomisation. Les gaz résiduels peuvent être piégés dans la poudre, créant des défauts dans les propriétés de la pièce finale.
Q : Est-il facile d'entretenir et de réparer un atomiseur de gaz ?
R : L'entretien courant est simple. En revanche, les réparations importantes, comme le remplacement des buses, peuvent prendre des jours et nécessiter un personnel ayant reçu une formation spécialisée. Des ensembles de buses supplémentaires doivent être conservés comme pièces de rechange pour permettre un changement rapide.
Q : Quels sont les problèmes de sécurité liés à la production de poudres métalliques ?
R : La manipulation de poudres fines présente toujours un risque d'explosion de poussières. Les autres préoccupations sont les risques liés aux gaz sous pression, à l'électricité à haute tension, aux températures élevées et à la manipulation de métaux en fusion, qui nécessitent un équipement de protection et une formation.
Partager sur
MET3DP Technology Co. est un fournisseur de premier plan de solutions de fabrication additive dont le siège se trouve à Qingdao, en Chine. Notre société est spécialisée dans les équipements d'impression 3D et les poudres métalliques de haute performance pour les applications industrielles.
Articles connexes
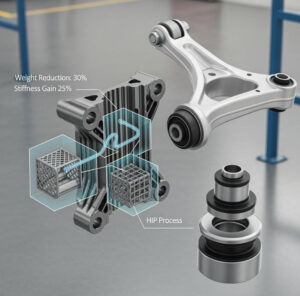
Metal 3D Printed Subframe Connection Mounts and Blocks for EV and Motorsport Chassis
Lire la suite "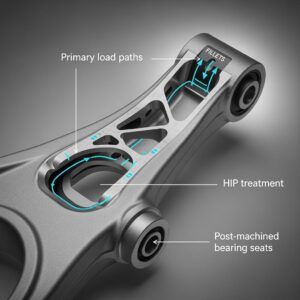
Metal 3D Printing for U.S. Automotive Lightweight Structural Brackets and Suspension Components
Lire la suite "À propos de Met3DP
Mise à jour récente
Notre produit
CONTACTEZ-NOUS
Vous avez des questions ? Envoyez-nous un message dès maintenant ! Nous répondrons à votre demande avec toute une équipe dès réception de votre message.
Obtenir les informations de Metal3DP
Brochure du produit
Obtenir les derniers produits et la liste des prix