poudres métalliques pour l'impression 3D
Table des matières
Poudres métalliques Les poudres métalliques sont des matières premières essentielles pour la fabrication additive utilisant la technologie de fusion sur lit de poudre. Ce guide donne un aperçu des différentes poudres métalliques utilisées dans les processus d'impression 3D tels que la fusion sélective par laser (SLM) et la fusion par faisceau d'électrons (EBM).
Introduction aux poudres métalliques pour l'AM
Les poudres métalliques permettent d'imprimer des pièces métalliques complexes et performantes grâce à la fabrication additive.
Matériaux utilisés :
- Aciers inoxydables
- Aciers à outils
- Alliages cobalt-chrome
- Titane et alliages de titane
- Alliages d'aluminium
- Superalliages de nickel
- Alliages de cuivre
Principales propriétés de la poudre :
- Chimie - Pureté et composition
- Forme et morphologie des particules
- Distribution de la taille des particules
- Densité apparente et densité de prise
- Capacité d'écoulement
- Réutilisation de la poudre
Méthodes de production des poudres :
- Atomisation du gaz
- Vaporisation de l'eau
- Atomisation par plasma
- Fusion par induction des électrodes
- Processus de carbonylation
- Alliage mécanique
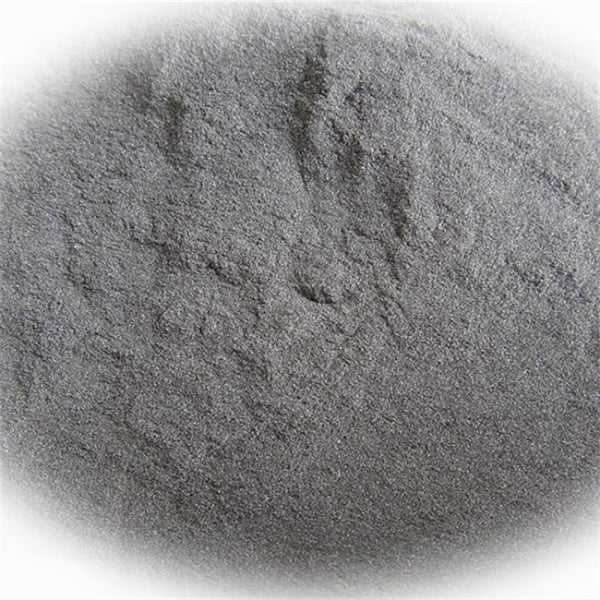
Poudres d'acier inoxydable
Les poudres d'acier inoxydable sont couramment utilisées pour imprimer des pièces résistantes à la corrosion :
Types d'alliages :
- Aciers austénitiques tels que 316L, 304L
- Aciers martensitiques comme le 17-4PH
- Aciers duplex comme le 2205
- Durcissement par précipitation comme 17-4PH, 15-5PH
Caractéristiques :
- Haute résistance à la corrosion et à l'oxydation
- Bonne résistance et ductilité
- Moins sujet à la fissuration que les aciers fortement alliés
- Paramètres tels que l'atmosphère de construction critique
Applications :
- Pièces pour l'industrie chimique et de transformation
- Composants marins
- Implants et dispositifs médicaux
- Pièces de l'industrie alimentaire/pharmaceutique nécessitant une hygiène
Fournisseurs : Carpenter, Sandvik, Praxair, Höganäs, LPW Technology
Poudres d'acier à outils
Les aciers à outils comme le H13 sont idéaux pour l'impression de pièces d'usure et de haute dureté :
Types d'alliages :
- Aciers résistants aux chocs comme le S7
- Aciers pour travail à froid comme D2
- Aciers pour travail à chaud tels que H13, H11
- Aciers rapides comme le M2
Caractéristiques :
- Excellente dureté jusqu'à 60 HRC
- Haute résistance à l'usure
- Bonne ténacité et résistance à la fatigue thermique
- Nécessite un recuit de mise en solution à haute température
Applications :
- Matrices et moules pour le formage des métaux
- Outils de coupe et forets
- Pièces d'usure et roulements
- Outillage haute température
Fournisseurs : Sandvik, Erasteel, LPW Technology, Tekna Plasma Systems
Alliages de cobalt et de chrome
Les poudres de cobalt-chrome impriment des implants et des restaurations dentaires biocompatibles :
Types d'alliages :
- CoCrMo comme Co-28Cr-6Mo
- CoNiCrMo comme Co-35Ni-20Cr-10Mo
- CoCr comme Co-67Cr-28Fe
Caractéristiques :
- Excellente biocompatibilité et résistance à la corrosion
- Résistance et dureté élevées
- Résistance à l'usure des articulations
- Impression difficile et tendance à la fissuration
Applications :
- Chapes, bridges et couronnes dentaires
- Implants orthopédiques du genou et de la hanche
- Dispositifs de fixation tels que les plaques crâniennes
- Matériel de fusion vertébrale
Fournisseurs : SLM Solutions, Carpenter, Arcam EBM
Poudres de titane
Les poudres de titane permettent de créer des pièces imprimées solides et légères :
Types d'alliages :
- Titane non allié comme Ti Grade 1-4
- Alliage Ti-6Al-4V
- Alliage Ti-6Al-7Nb
- Autres alliages alpha + bêta
Caractéristiques :
- Rapport résistance/poids élevé
- Excellente résistance à la corrosion
- Bonnes propriétés à haute température
- Faible densité - 4,5 g/cc
- Réactif et nécessite une atmosphère inerte
Applications :
- Composants pour l'aérospatiale et les sports mécaniques
- Implants médicaux et prothèses
- Pièces pour l'industrie alimentaire/chimique
- Pièces détachées automobiles
Fournisseurs : AP&C, Tekna, Additif Carpenter
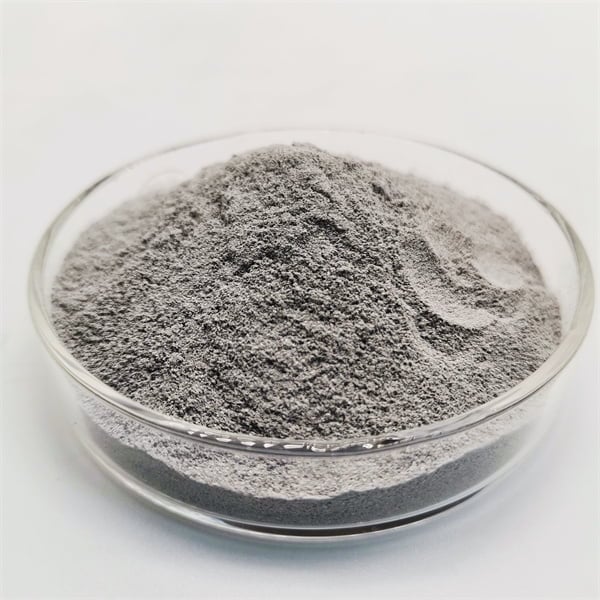
Alliages d'aluminium
Les poudres d'aluminium impriment des pièces structurelles ou fonctionnelles légères :
Types d'alliages :
- AlSi10Mg
- AlSi7Mg
- AlSi12
- Scalmalloy® et autres alliages d'aluminium
Caractéristiques :
- Faible densité - 2,7 g/cc
- Bonne résistance et rigidité
- Excellente conductivité thermique
- Sujet à la fissuration et aux contraintes résiduelles
Applications :
- Composants pour l'automobile et les sports motorisés
- Applications aérospatiales et spatiales
- Échangeurs de chaleur
- Matériel médical comme les plâtres
Fournisseurs: AP&C, Sandvik, LPW Technology, ECKA Granules
Superalliages de nickel
Les superalliages de nickel comme l'Inconel 718 permettent d'imprimer des pièces à haute température :
Types d'alliages :
- Inconel 718
- Inconel 625
- Waspaloy
- Hastelloy X
Caractéristiques :
- Excellente résistance à haute température
- Bonne résistance à la corrosion et au fluage
- Capacité à travailler dans des conditions de stress et à des températures élevées
- Difficulté de mise en œuvre et risque de fissuration
Applications :
- Aubes de turbine
- Pièces de la chambre de combustion
- Composants de l'engin spatial
- Pièces pour l'industrie nucléaire/chimique
Fournisseurs : Praxair, Carpenter Additive, GE Additive
Alliages de cuivre
Les alliages de cuivre comme le CuCrZr permettent d'imprimer des pièces hautement conductrices :
Types d'alliages :
- Cuivre-chrome comme CuCr1Zr
- Cuivre-nickel comme CuNi2SiCr
- Les bronzes comme CuSn10
Caractéristiques :
- Excellente conductivité thermique et électrique
- Bonne résistance à la corrosion
- Propriété antibactérienne
- Résistance inférieure à celle des aciers et des alliages de nickel
Applications :
- Composants électriques tels que les barres omnibus
- Échangeurs de chaleur et puits de chaleur
- Guides d'ondes et composants RF
- Instruments médicaux et fixations
Fournisseurs : Sandvik, LPW Technology, Metalysis
Spécifications techniques
Spécifications typiques des poudres métalliques utilisées en AM :
Paramètres | Valeurs typiques | Normes de test |
---|---|---|
Taille des particules | 10 - 45 μm | ASTM B214 |
Forme des particules | Sphérique | ISO 13322-2 |
Débit | 25 - 35 s/50g | ASTM B213 |
Densité apparente | 2 - 5 g/cc | ASTM B212 |
Densité du robinet | 4 - 8 g/cc | ASTM B527 |
Oxygène résiduel | < 300 ppm | Méthode interne |
Azote résiduel | < 50 ppm | Méthode interne |
Carbone résiduel | < 30 ppm | ASTM E1019 |
Méthodes de production des poudres
1. Atomisation des gaz
- Poudre hautement sphérique
- Petites particules de 5 à 100 μm
- Utilisé pour les alliages réactifs comme le titane
2. Atomisation de l'eau
- Forme irrégulière de la poudre
- Particules plus grosses jusqu'à 300 μm
- Processus moins coûteux
3. Atomisation par plasma
- Formes de particules contrôlées
- Tailles submicroniques à 150 μm
- Poudre de haute pureté
4. Alliage mécanique
- Mélange et broyage d'éléments
- Rentable pour les alliages sur mesure
- Particules de grande taille
Fournisseurs et prix
Fournisseur | Matériaux | Fourchette de prix |
---|---|---|
Technologie LPW | Aciers à outils, aciers inoxydables | $50 - $120/kg |
AP&C | Alliages de titane, alliages d'aluminium | $70 - $450/kg |
Sandvik | Aciers inoxydables, alliages de nickel | $45 - $250/kg |
Praxair | Superalliages, titane | $150 - $600/kg |
Additif pour charpentier | Aciers à outils, CoCr, inoxydables | $80 - $300/kg |
- Coût des poudres d'acier inoxydable $45-$120 par kg
- Coût des poudres d'alliage de titane $150-$450 par kg
- Les superalliages et les aciers à outils coûtent $250-$600 par kg
Les prix dépendent de l'alliage, de la qualité, de la taille du lot et des accords d'achat.
Manipulation et stockage des poudres
Pour éviter toute contamination, il est essentiel de manipuler correctement les poudres :
- Utiliser des zones dédiées au tamisage des poudres
- Assurer l'atmosphère inerte des boîtes à gants et des trémies
- Utiliser des récipients conducteurs pour dissiper les charges statiques.
- Mise à la terre de tous les équipements et conteneurs de transport
- Éviter le contact avec l'huile, l'eau ou l'oxygène
- Stocker la poudre dans des récipients scellés sous gaz inerte
- Contrôle de la température et de l'humidité pendant le stockage
- Respecter les mesures de sécurité telles que l'EPI lors de la manipulation
Un stockage adéquat prolonge la durée de réutilisation des poudres.
Tamisage des poudres
Le tamisage permet d'obtenir des particules de taille homogène :
Avantages :
- Élimine les particules satellites à l'origine des défauts
- Casse les agglomérats
- Améliore l'écoulement et la densité de l'emballage
- Réduit les problèmes de recyclabilité
- Élimine les contaminants étrangers
Procédure :
- Tamiser la poudre en utilisant des mailles d'environ 20-63 μm.
- Tamisage par rotation ou vibration
- Effectuer le tamisage sous atmosphère inerte
- Document pourcentage de poids de poudre restant
Le tamisage améliore la qualité des pièces en assurant une répartition idéale de la poudre.
Installation et mise en service
L'installation d'une imprimante AM métal avec un système de poudre implique :
- Nettoyer les surfaces des équipements pour éviter toute contamination
- Essai d'étanchéité des raccords de gaz inertes
- Vérification de la puissance du laser ou du faisceau d'électrons
- Chargement et test du système de revêtement par poudre
- Intégration du refroidisseur, de l'échappement et des raccords de service
- Installation de capteurs de surveillance et de sécurité
- Vérification des systèmes de tamisage et de manutention des poudres
- Etalonnage de la mise à niveau de la plaque de construction
- Test d'impression des échantillons et validation de la qualité
Les vendeurs fournissent une assistance à l'installation et à la mise en service.
Fonctionnement et bonnes pratiques
Directives d'utilisation de l'imprimante :
- Effectuer régulièrement des contrôles d'étanchéité et des tests de pureté des gaz inertes
- Préconditionner la poudre pour garantir une texture homogène
- Ajuster l'épaisseur de la couche et les paramètres du laser pour les nouveaux matériaux
- Surveillance étroite du bain de fusion et contrôle de la température des pièces
- Valider les dimensions critiques à l'aide de tirages d'essai
- Contrôler l'état de la poudre et ne la réutiliser que dans les limites des recommandations
- Effectuer une maintenance régulière des optiques, du système d'émission de faisceaux et du mécanisme de recouvrement des poudres.
Sécurité du personnel :
- Utiliser des EPI appropriés tels que des respirateurs et des gants
- Éviter le contact avec les poudres métalliques fines réactives
- Manipuler correctement les déchets de poudre sous atmosphère inerte
Partie post-traitement :
- Utiliser des températures de traitement thermique et de vieillissement adaptées à l'alliage et à l'application.
- Contrôler les taux de rampe pendant le traitement thermique pour soulager les contraintes
- Utiliser le pressage isostatique à chaud pour les pièces complexes, si nécessaire, afin d'améliorer les densités.
- Appliquer des étapes de finition telles que l'usinage CNC et le polissage
Entretien et inspection
Activités de maintenance régulières :
Tous les jours :
- Inspecter les optiques comme les miroirs, les lentilles et les fenêtres pour vérifier qu'ils ne sont pas endommagés.
- Nettoyer la chambre de construction et le système de manutention des poudres
- Vérifier les niveaux de gaz inerte et les recharger si nécessaire
- Tester le mécanisme de tamisage et la machine à recouvrir les poudres
Hebdomadaire :
- Étalonner les capteurs et les instruments
- Vérifier les fixations, les bornes électriques et la mise à la terre.
- Lubrifier et inspecter les pièces mobiles telles que les moteurs et les entraînements
- Contrôler le remplacement des filtres
Mensuel :
- Essai d'étanchéité du système de gaz inerte à l'hélium
- Inspecter les dispositifs de sécurité tels que les détecteurs d'incendie
- Vérifier l'état de santé du système de cogénération
Tous les ans :
- Programmer la maintenance préventive avec le fournisseur de l'équipement
- Étalonnage de l'appareil de mesure de la puissance du laser
- Remplacer les filtres et les consommables
La maintenance, conformément aux directives du fournisseur, est nécessaire pour maintenir la qualité des pièces et l'état de l'équipement.
Choisir le bon système d'impression sur métal
Facteurs à prendre en compte lors de la sélection d'une machine d'AM des métaux :
1. Exigences en matière de production
- Type de composants à produire
- Matériau nécessaire en fonction des propriétés de la pièce
- Exigences en matière de volume de production
- Précision et état de surface requis
2. Spécifications de l'imprimante
- Matériaux et paramètres pris en charge
- Taille et vitesse de construction
- Précision et répétabilité
- Gestion de l'atmosphère inerte
- Fonctions d'automatisation et contrôles
3. Système de manutention des poudres
- Système intégré ou autonome
- Capacités de tamisage, d'alimentation, de stockage et de réutilisation
- Confinement des matériaux réactifs tels que le titane
- Des dispositifs de surveillance pour éviter la contamination
4. Respect des normes
- Normes industrielles telles que ASTM F3301
- Certifications de qualité du fabricant
- Respect des normes de sécurité
5. Références du fournisseur
- Expérience confirmée dans le secteur de l'AM
- Capacités locales de vente et d'assistance technique
- Contrats de maintenance et services proposés
- Plans de formation des opérateurs
- Coût global de possession
Une analyse approfondie des besoins et une comparaison des machines proposées sur la base de ces critères permettent de sélectionner le système d'impression 3D métal idéal, adapté aux besoins de production.
Avantages et inconvénients de l'AM des métaux
Avantages :
- Complexité géométrique élevée imprimée facilement
- Délai plus court pour obtenir des pièces fonctionnelles
- Réduction des déchets par rapport aux procédés soustractifs
- Production en une seule étape directement à partir de la CAO
- Potentiel d'allègement et de consolidation des pièces
- Amélioration des performances grâce aux alliages spéciaux
- Capacités de personnalisation et de personnalisation de masse
Inconvénients :
- Coûts élevés des machines et des matériaux
- Des étapes supplémentaires de post-traitement sont nécessaires
- Taille limitée en fonction de la chambre de construction
- Le contrôle des défauts internes peut s'avérer difficile
- Les propriétés des matériaux peuvent varier par rapport au corroyage
- Les limites de l'état de surface peuvent nécessiter une finition
- Exigences en matière de formation et d'expertise
Dépannage des problèmes courants liés à l'AM des métaux
Défaut | Causes possibles | Actions correctives |
---|---|---|
Porosité | Paramètres de processus inappropriés | Optimiser la puissance, la vitesse et l'espacement des éclosions du laser |
Contamination de la poudre | Utiliser de la poudre fraîchement tamisée, améliorer la manipulation de la poudre | |
Chevauchement insuffisant entre les pistes de balayage | Régler la taille de la focalisation du faisceau et le chevauchement | |
Craquage | Contraintes thermiques excessives | Optimiser le préchauffage, contrôler la vitesse de refroidissement à l'aide d'appareils de chauffage |
Matériau susceptible de se fissurer | Changer d'orientation pour réduire le stress | |
Contamination de l'atmosphère de la construction | Garantir une atmosphère inerte de haute pureté | |
Déformation | Chauffage ou refroidissement inégal | Optimisation des modèles de balayage et immobilisation de la pièce sur la plaque de construction |
Mauvais état de surface | Température de la pièce trop basse | Augmenter la température de préchauffage |
Mauvaise fluidité du bain de fusion | Régler la puissance et les autres paramètres | |
Poudre contaminée | Utiliser de la poudre fraîche et améliorer la maniabilité |
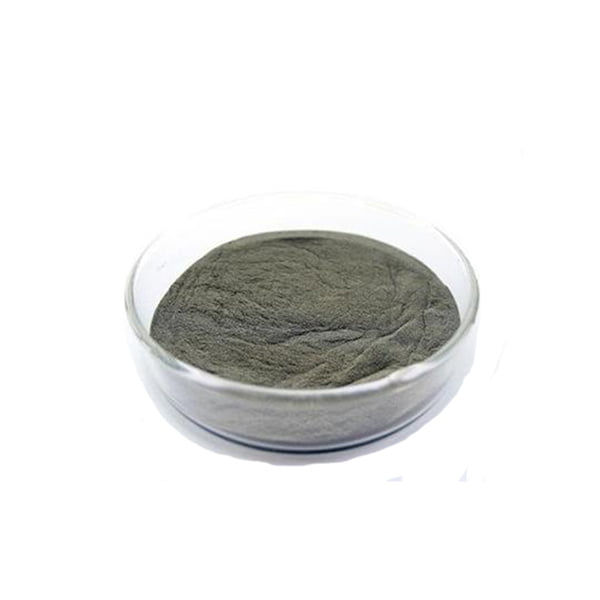
FAQ
Q : Quelles poudres d'alliage métallique peuvent être utilisées pour l'AM ?
R : Les aciers inoxydables, les aciers à outils, les alliages de titane, les superalliages de nickel, les alliages d'aluminium, le cobalt-chrome et les alliages de cuivre sont courants.
Q : Quelle est la gamme typique de tailles de particules de poudre utilisées ?
R : Pour les procédés PBF-LB/M, il est courant d'avoir une épaisseur de 10 à 45 microns, avec une distribution plus serrée autour de 20 à 45 μm.
Q : Quelle est la durée de vie des poudres métalliques ?
R : Avec un stockage idéal de l'argon, de nombreux alliages ont une durée de vie de 1 à 2 ans. La durée de réutilisation est plus courte - 20 à 100 tirages en fonction de l'alliage.
Q : Quelles sont les étapes de post-traitement nécessaires pour les pièces obtenues par AM métal ?
R : L'enlèvement du support, le traitement thermique, la finition de la surface comme l'usinage CNC, le polissage et le revêtement sont souvent nécessaires.
Q : Comment les poudres métalliques réactives telles que le titane et l'aluminium sont-elles traitées ?
R : Une manipulation spécialisée de la poudre sous atmosphère inerte d'argon est nécessaire pour éviter le captage d'oxygène.
Q : Quels sont les risques courants de contamination par les poudres ?
A : Exposition à une atmosphère conduisant à une accumulation d'oxygène ou d'azote. Particules métalliques provenant de l'usinage ou de l'usure. Huile et humidité.
Q : Quelles sont les normes utilisées pour qualifier les poudres métalliques ?
A : ASTM B214, ASTM B812, ASTM F3049, ASTM F3301 et normes MPIF.
Q : Pourquoi le tamisage des poudres est-il important ?
R : Il brise les agglomérats, élimine les satellites et permet d'obtenir une taille de poudre optimale et constante pour une densité et une finition de surface élevées.
Conclusion
Les poudres métalliques permettent la fabrication additive de composants avancés et très performants dont les propriétés sont, dans certains cas, supérieures à celles des matériaux corroyés. Une large gamme d'alliages, allant des aciers inoxydables aux superalliages et au titane, est disponible sous forme de poudre, adaptée aux applications exigeantes dans les secteurs de l'aérospatiale, de la médecine, de l'automobile et de l'industrie en général. Grâce aux améliorations constantes apportées aux alliages, aux normes de qualité, aux processus de production, aux machines et aux propriétés des pièces, l'AM des métaux est en train de devenir une technologie de production de base à l'échelle mondiale. Toutefois, il est essentiel de disposer d'une expertise en matière de processus et de matériaux, ainsi que d'un contrôle de qualité rigoureux, pour en tirer tous les avantages. Au fur et à mesure que l'on acquiert de l'expérience, l'AM des métaux offre des capacités sans précédent pour fabriquer des pièces complexes et personnalisées avec une plus grande liberté de conception et des délais d'exécution plus courts.
Partager sur
MET3DP Technology Co. est un fournisseur de premier plan de solutions de fabrication additive dont le siège se trouve à Qingdao, en Chine. Notre société est spécialisée dans les équipements d'impression 3D et les poudres métalliques de haute performance pour les applications industrielles.
Articles connexes
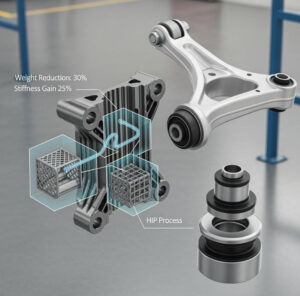
Metal 3D Printed Subframe Connection Mounts and Blocks for EV and Motorsport Chassis
Lire la suite "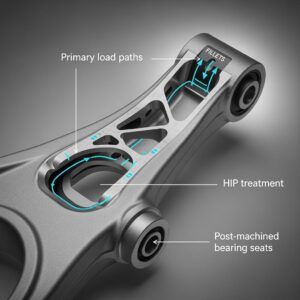
Metal 3D Printing for U.S. Automotive Lightweight Structural Brackets and Suspension Components
Lire la suite "À propos de Met3DP
Mise à jour récente
Notre produit
CONTACTEZ-NOUS
Vous avez des questions ? Envoyez-nous un message dès maintenant ! Nous répondrons à votre demande avec toute une équipe dès réception de votre message.
Obtenir les informations de Metal3DP
Brochure du produit
Obtenir les derniers produits et la liste des prix