L'application de la technologie MIM aux dispositifs médicaux
Table des matières
Imaginez un monde où des dispositifs médicaux complexes, dotés de géométries complexes et d'une résistance exceptionnelle, peuvent être produits en série avec une précision inégalée. Ce n'est pas de la science-fiction ; c'est la réalité inaugurée par le moulage par injection de métal (MIM).
Le MIM révolutionne l'industrie des dispositifs médicaux en offrant un mélange unique de flexibilité de conception, de matériaux de haute performance et de rentabilité. Cet article se penche sur les merveilles du MIM, en explorant ses applications, les options de matériaux et l'impact profond qu'il a sur divers instruments médicaux.
MIM Technologie : Le mariage du métal et du plastique
À la base, le MIM comble le fossé entre l'usinage traditionnel des métaux et le moulage par injection de plastique. Voici un aperçu du processus :
- Préparation de la poudre : Les poudres métalliques, méticuleusement choisies pour leurs propriétés, sont mélangées à un liant pour créer une matière première dont la consistance est similaire à celle du sable mouillé.
- Moulage : La matière première est injectée sous haute pression dans une cavité de moule conçue avec précision, imitant ainsi le processus utilisé pour le moulage par injection de plastique.
- Débouclage : Le liant est soigneusement éliminé par un processus thermique ou chimique, laissant derrière lui une pièce métallique fragile.
- Frittage : La structure métallique restante est soumise à un frittage à haute température, ce qui entraîne la fusion des particules métalliques et permet d'obtenir un produit final robuste et de forme proche de celle d'un filet.
Cette technique innovante offre un trésor d'avantages aux fabricants de dispositifs médicaux :
- Liberté de conception : Le MIM permet de créer des géométries complexes avec des canaux internes, des contre-dépouilles et des parois minces, caractéristiques qui sont souvent difficiles, voire impossibles à réaliser avec des méthodes traditionnelles telles que l'usinage ou le moulage.
- Polyvalence des matériaux : Une large gamme de poudres métalliques peut être utilisée, chacune offrant des propriétés uniques adaptées à des applications spécifiques.
- Production de masse : Le MIM facilite la production rentable de pièces complexes en grandes quantités, ce qui le rend idéal pour les dispositifs médicaux très demandés.
- Une précision exceptionnelle : Le MIM permet d'obtenir des composants de forme presque nette avec des tolérances serrées, ce qui minimise le besoin de post-traitement et garantit une qualité constante.
- Biocompatibilité : Certaines poudres métalliques utilisées dans le MIM sont biocompatibles, ce qui les rend adaptées aux dispositifs médicaux implantables.
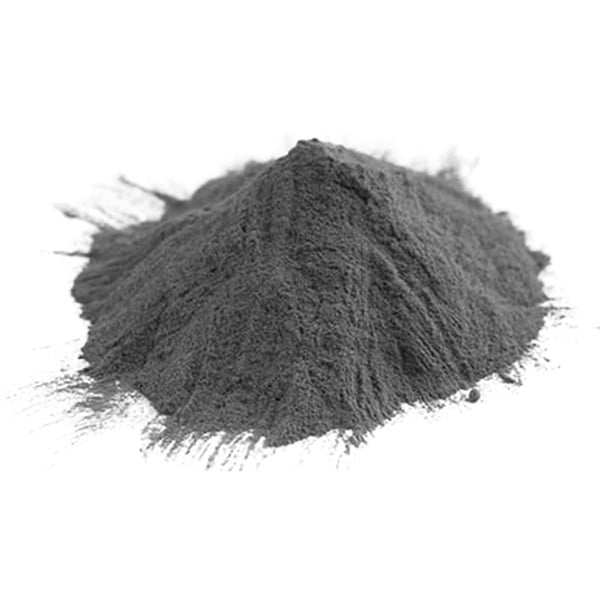
10+ poudres métalliques pour MIM
Le succès du MIM dépend de la sélection minutieuse des poudres métalliques. Chaque poudre possède des caractéristiques uniques qui la rendent idéale pour des applications spécifiques. Voici un aperçu de l'arsenal de poudres métalliques disponibles pour le MIM :
1. Acier inoxydable 316L : Polyvalent, l'acier inoxydable 316L offre une excellente résistance à la corrosion, une biocompatibilité et une bonne résistance mécanique. Il est largement utilisé pour les vis à os, les implants dentaires et les instruments chirurgicaux.
2. Acier inoxydable 17-4 PH : Cet acier inoxydable à haute résistance, durcissant par précipitation, offre une solidité et une résistance à l'usure exceptionnelles, ce qui en fait un candidat de choix pour les implants orthopédiques, les composants articulaires et l'instrumentation rachidienne.
3. Cobalt-Chrome (CoCr) : Réputé pour sa biocompatibilité et sa grande résistance à l'usure, le CoCr est un choix populaire pour les prothèses de la hanche et du genou, les implants dentaires et les fils-guides.
4. Titane (Ti) : Léger mais remarquablement solide, le titane est un métal biocompatible apprécié pour ses excellentes propriétés d'ostéointégration (liaison osseuse). Il est largement utilisé pour les implants dentaires, les implants maxillo-faciaux et les dispositifs de réparation des fractures.
5. MP35N : Ce superalliage à base de nickel durcissant par précipitation présente une solidité exceptionnelle, des performances à haute température et une résistance à la corrosion. Il trouve des applications dans les instruments chirurgicaux exigeants et les outils de chirurgie mini-invasive (MIS).
6. Inconel 625 : Autre superalliage haute performance à base de nickel, l'Inconel 625 offre une solidité, une résistance au fluage et une résistance aux environnements difficiles supérieures. Il est utilisé pour les instruments chirurgicaux spécialisés et les composants exposés à des températures élevées.
7. Tantale (Ta) : Ce métal biocompatible et résistant à la corrosion est particulièrement précieux pour son excellente radiotransparence, qui permet une imagerie radiographique claire. Il est utilisé dans les implants dentaires, les implants crâniens et d'autres applications où la visibilité des rayons X est cruciale.
8. Molybdène (Mo) : Le point de fusion élevé du molybdène et son excellente conductivité thermique en font un ajout précieux à certaines poudres MIM, améliorant la dissipation de la chaleur dans les instruments utilisés pour l'électrochirurgie et les applications laser.
9. Tungstène (W) : La densité exceptionnelle du tungstène et son point de fusion élevé en font un matériau idéal pour les applications nécessitant un blindage contre les radiations ou des poids de lestage dans les appareils médicaux.
10. Kovar : Cet alliage fer-nickel-cobalt présente un coefficient de dilatation thermique proche de celui du verre, ce qui le rend idéal pour créer des joints verre-métal dans les dispositifs médicaux intégrant des composants en verre.
La technologie MIM en action : Transformer les dispositifs médicaux
La polyvalence du MIM s'étend à un large éventail de dispositifs médicaux, chacun bénéficiant de ses avantages uniques. Examinons quelques applications clés :
MIM pour les dispositifs implantables :
- Stents cardiaques, stents vasculaires et autres stents implantables : Le MIM permet de créer des endoprothèses complexes avec des parois minces et des géométries d'entretoise précises, ce qui est essentiel pour une circulation sanguine optimale et une obstruction minimale des vaisseaux. Des matériaux biocompatibles tels que l'acier inoxydable 316L et le CoCr garantissent des performances à long terme dans l'organisme.
- Articulations artificielles, vis orthopédiques, implants dentaires et autres implants : Le MIM facilite la production d'implants orthopédiques complexes avec des formes presque nettes, ce qui élimine la nécessité d'un traitement ultérieur approfondi. Les matériaux tels que l'acier inoxydable 17-4 PH et le titane offrent une solidité, une résistance à l'usure et une ostéointégration exceptionnelles pour une fonctionnalité durable.
MIM pour les instruments chirurgicaux :
- Couteaux, pinces, ciseaux et autres instruments chirurgicaux : Le MIM permet de créer des instruments chirurgicaux pointus et complexes d'une précision et d'une durabilité exceptionnelles. Des matériaux de haute performance tels que le MP35N et l'Inconel 625 garantissent que ces instruments peuvent résister à des procédures chirurgicales exigeantes.
MIM pour les autres dispositifs médicaux :
- Dispositifs d'administration de médicaments : La capacité du MIM à produire des composants complexes avec des canaux internes le rend idéal pour les dispositifs complexes d'administration de médicaments tels que les micro-aiguilles et les stents à élution de médicaments.
- Composants microscopiques : Le MIM excelle dans la création de dispositifs médicaux miniatures aux tolérances étroites, tels que les composants utilisés dans les outils chirurgicaux peu invasifs et les équipements de diagnostic.
- Boîtiers biocompatibles : Le MIM permet de produire des boîtiers biocompatibles pour les dispositifs implantables tels que les stimulateurs cardiaques et les défibrillateurs, offrant une combinaison de résistance, de biocompatibilité et de liberté de conception.
Avantages de la MIM pour les dispositifs médicaux :
- Fonctionnalité améliorée : Le MIM permet de créer des géométries complexes qui améliorent les performances et les fonctionnalités des appareils par rapport aux méthodes de fabrication traditionnelles.
- Biocompatibilité améliorée : La sélection de poudres métalliques biocompatibles permet de créer des dispositifs implantables qui minimisent le risque de rejet par l'organisme.
- Rapport coût-efficacité : Pour la production en grande quantité de dispositifs médicaux complexes, le MIM offre une alternative rentable aux méthodes traditionnelles telles que l'usinage ou le moulage.
- Réduction des déchets matériels : Le MIM minimise les déchets de matériaux par rapport aux techniques de fabrication soustractives telles que l'usinage, ce qui en fait une option plus durable.
Considérations relatives à l'utilisation de la MIM dans les dispositifs médicaux :
- Complexité des pièces : Le MIM est le mieux adapté aux pièces présentant des géométries complexes et des caractéristiques internes difficiles à produire avec d'autres méthodes.
- Sélection des matériaux : Le choix de la poudre métallique appropriée est crucial pour s'assurer que le dispositif final possède les propriétés souhaitées pour l'application à laquelle il est destiné.
- Finition de la surface : Bien que le MIM permette d'obtenir des pièces de forme presque nette, un post-traitement peut être nécessaire pour obtenir l'état de surface souhaité pour des applications spécifiques.
MIM vs. les méthodes de fabrication traditionnelles
Le MIM n'est pas sans concurrence. Les méthodes de fabrication traditionnelles telles que l'usinage, le moulage et le forgeage ont longtemps dominé le paysage des dispositifs médicaux. Voici un aperçu de la façon dont le MIM se positionne par rapport à ces techniques établies :
MIM vs. usinage :
- La complexité : Le MIM excelle dans la production de géométries complexes, alors que l'usinage peut s'avérer long et coûteux pour les pièces complexes.
- Déchets de matériaux : Le MIM génère un minimum de déchets de matériaux par rapport à l'usinage, qui enlève l'excès de matière pour créer la forme souhaitée.
- Coût : Pour la production en grande série de pièces complexes, le MIM peut être plus rentable que l'usinage.
MIM contre moulage :
- Précision : Le MIM offre une plus grande précision dimensionnelle et des tolérances plus serrées que le moulage, qui peut être sujet à des variations.
- Finition de la surface : Les pièces MIM nécessitent généralement moins de post-traitement pour obtenir la finition de surface souhaitée que les pièces moulées.
- Options de matériaux : Le MIM offre une plus grande variété de choix de poudres métalliques par rapport aux limites des alliages de fonderie.
MIM et forgeage :
- La force : Le forgeage excelle dans la production de composants à haute résistance, mais le MIM peut atteindre une résistance suffisante pour de nombreuses applications de dispositifs médicaux.
- La complexité : Le MIM permet de créer des géométries complexes, alors que le forgeage est limité à des formes plus simples.
- Coût : Pour la production en grande série de pièces complexes, le MIM peut être une option plus compétitive en termes de coûts que le forgeage.
L'avenir de la MIM dans les dispositifs médicaux
L'avenir de la MIM dans les dispositifs médicaux est plein de promesses. Voici quelques tendances intéressantes à observer :
- Conceptions hybrides : Imaginez un dispositif dont la structure de base est fabriquée efficacement par MIM et dont les détails complexes ou les réseaux internes sont créés par AM. Cela pourrait permettre de créer des implants ou des instruments plus légers et plus résistants, dotés d'une meilleure fonctionnalité.
- Pièces multi-matériaux : Le MIM excelle avec les métaux, tandis que l'AM permet d'utiliser une plus large gamme de matériaux. La combinaison de ces techniques pourrait permettre de créer des dispositifs dont les sections seraient constituées de différents matériaux, chacun étant choisi pour ses propriétés idéales dans un endroit spécifique.
- Prototypage et développement plus rapides : La combinaison du MIM pour les structures de base et de l'AM pour les caractéristiques complexes pourrait rationaliser le processus de prototypage des dispositifs médicaux, en accélérant le développement et la mise sur le marché.
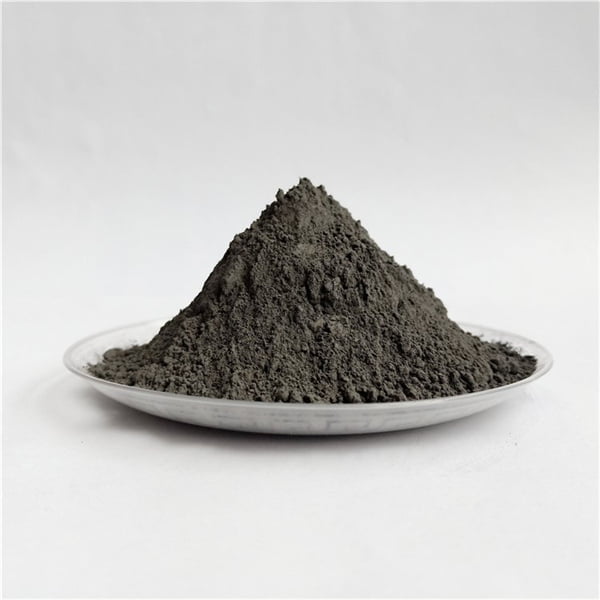
FAQ
Voici quelques questions fréquemment posées sur la technologie MIM et ses applications dans les dispositifs médicaux :
Q : Quelles sont les limites de la MIM pour les dispositifs médicaux ?
Si le MIM offre de nombreux avantages, il est essentiel de tenir compte de ses limites :
- Taille de la pièce : Il existe des limites à la taille des pièces qui peuvent être produites efficacement à l'aide du MIM. Les pièces très grandes ou volumineuses peuvent ne pas convenir au MIM en raison des problèmes potentiels liés à l'écoulement de la poudre et à l'uniformité du frittage.
- Finition de la surface : Alors que le MIM permet d'obtenir des pièces de forme presque nette, l'obtention d'une finition de surface hautement polie ou ultra lisse peut nécessiter des étapes de post-traitement supplémentaires.
- Conception pour la fabrication (DFM) : Il est essentiel de concevoir des pièces spécifiquement pour le MIM afin d'optimiser le processus et de minimiser les problèmes potentiels. Les angles internes aigus ou les parois extrêmement fines peuvent être difficiles à produire avec le MIM.
- Disponibilité du matériel : Bien qu'une large gamme de poudres métalliques soit disponible pour le MIM, certains matériaux spécialisés ou exotiques peuvent ne pas être facilement disponibles ou rentables pour ce processus.
Q : Quel est le coût du MIM par rapport aux autres méthodes de fabrication ?
Le coût de l'utilisation du MIM dépend de plusieurs facteurs, notamment
- Complexité des pièces : Les pièces complexes avec des caractéristiques compliquées coûteront généralement plus cher à produire avec le MIM qu'avec des conceptions plus simples.
- Sélection des matériaux : La poudre métallique choisie peut avoir un impact significatif sur le coût, certaines poudres exotiques ou à haute performance étant plus chères.
- Volume de production : Le MIM est plus rentable pour les gros volumes de production. Pour les applications à faible volume, d'autres méthodes, comme l'usinage, peuvent être plus appropriées.
Dans l'ensemble, le MIM peut être une option très compétitive en termes de coûts pour la production en grande quantité de dispositifs médicaux complexes par rapport aux méthodes traditionnelles telles que l'usinage ou le moulage.
Q : Quelles sont les considérations réglementaires relatives à l'utilisation de la MIM dans les dispositifs médicaux ?
Les dispositifs médicaux sont soumis à des exigences réglementaires strictes en fonction de leur classification et de l'usage auquel ils sont destinés. Les fabricants de MIM et les concepteurs de dispositifs doivent s'assurer que le processus de MIM respecte les réglementations en vigueur, ce qui peut impliquer :
- Caractérisation des matériaux : Les propriétés et la biocompatibilité de la poudre métallique choisie doivent être soigneusement caractérisées et documentées.
- Validation des processus : Le processus de MIM lui-même doit être validé pour garantir une production constante de pièces de haute qualité répondant aux spécifications requises.
- Contrôle de la qualité : Des procédures rigoureuses de contrôle de la qualité doivent être mises en œuvre tout au long du processus de MIM afin de garantir la sécurité et l'efficacité du dispositif médical final.
Q : La MIM est-elle un processus de fabrication durable ?
Le MIM offre plusieurs avantages du point de vue de la durabilité :
- Réduction des déchets matériels : Le MIM utilise une approche de fabrication proche de la forme nette, ce qui minimise le gaspillage de matériaux par rapport aux techniques soustractives telles que l'usinage.
- Recyclage des matériaux : Les poudres métalliques utilisées dans le MIM peuvent souvent être recyclées et réutilisées, ce qui réduit encore l'impact sur l'environnement.
- Efficacité énergétique : Par rapport à certaines méthodes traditionnelles comme le moulage, le MIM peut être plus économe en énergie, en particulier pour la production en grande quantité.
Toutefois, l'empreinte environnementale du MIM dépend également de facteurs tels que la poudre métallique choisie et la source d'énergie utilisée au cours du processus.
Partager sur
MET3DP Technology Co. est un fournisseur de premier plan de solutions de fabrication additive dont le siège se trouve à Qingdao, en Chine. Notre société est spécialisée dans les équipements d'impression 3D et les poudres métalliques de haute performance pour les applications industrielles.
Articles connexes
À propos de Met3DP
Mise à jour récente
Notre produit
CONTACTEZ-NOUS
Vous avez des questions ? Envoyez-nous un message dès maintenant ! Nous répondrons à votre demande avec toute une équipe dès réception de votre message.
Obtenir les informations de Metal3DP
Brochure du produit
Obtenir les derniers produits et la liste des prix
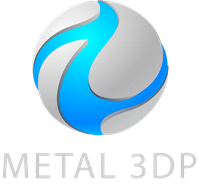
Poudres métalliques pour l'impression 3D et la fabrication additive