Quelle poudre d'alliage à base de nickel imprimée en 3D peut être utilisée dans l'aérospatiale ?
Table des matières
Imaginez un oiseau s'élevant sans effort dans le ciel. Imaginez maintenant un moteur à réaction, le cœur battant d'un avion moderne, qui le propulse à travers les continents à des vitesses phénoménales. Ces deux merveilles de l'ingénierie partagent un besoin crucial : des matériaux légers et incroyablement solides, capables de résister à des températures extrêmes et à des environnements difficiles. Entrez dans le monde fascinant des matériaux imprimés en 3D poudres d'alliages à base de nickelL'industrie aérospatiale joue un rôle de premier plan dans sa quête incessante d'innovation.
Les alliages à base de nickel sont une classe de superstars métalliques. Ils présentent une résistance exceptionnelle à haute température, une résistance à la corrosion et une excellente résistance au fluage, c'est-à-dire la capacité de résister à la déformation sous une contrainte constante à des températures élevées. Ces propriétés les rendent idéaux pour les conditions de fonctionnement brutales auxquelles sont soumis les composants des moteurs d'avion. Mais qu'est-ce qui rend l'impression 3D de ces alliages vraiment révolutionnaire ?
Plongeons dans l'univers des poudres d'alliages à base de nickel imprimées en 3D, en explorant les types spécifiques utilisés dans les applications aérospatiales, leurs propriétés uniques et les avantages qu'elles offrent par rapport aux méthodes de fabrication traditionnelles.
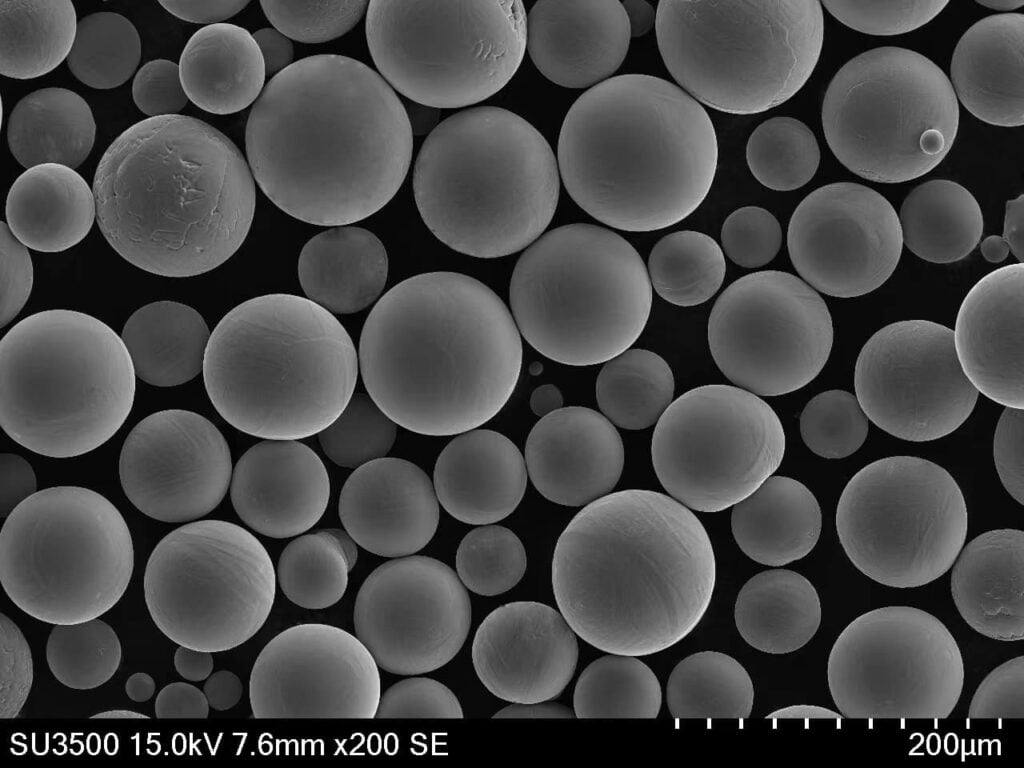
Communs Poudres d'alliages à base de nickel pour l'aérospatiale
Le monde des poudres d'alliages à base de nickel imprimées en 3D n'est pas une affaire à taille unique. Différents alliages offrent des avantages distincts en fonction de l'application spécifique. Nous allons ici mettre en lumière trois des principaux concurrents :
- Inconel 718 : Cet alliage puissant est le champion incontesté pour de nombreuses applications aérospatiales. Son rapport résistance/poids exceptionnel, ses excellentes performances à haute température (jusqu'à 700°C) et sa bonne soudabilité en font un choix polyvalent pour une large gamme de composants. Considéré comme le "couteau suisse" des poudres d'alliage à base de nickel, il est parfait pour tout ce qui concerne les disques et les pales de turbines, ainsi que les composants de trains d'atterrissage.
- Inconel 625 : Offrant une résistance à la corrosion supérieure à celle de l'Inconel 718, cet alliage est d'une grande utilité dans les environnements exposés à des produits chimiques agressifs et à l'oxydation. Pensez aux systèmes d'échappement brûlants et aux pièces exposées à l'eau salée pendant de longues périodes. Bien qu'il ne soit pas aussi résistant que l'Inconel 718 à haute température, l'Inconel 625 brille dans les applications où la lutte contre la corrosion est primordiale.
- Hastelloy X : Imaginez un matériau qui prospère dans des environnements si hostiles que même les autres superalliages vacillent. L'Hastelloy X monte sur le ring. Ce champion affiche une résistance phénoménale à une large gamme de milieux corrosifs, y compris les acides chlorhydriques et sulfuriques chauds. Considéré comme le "guerrier de la corrosion" par excellence, il est parfait pour les systèmes d'alimentation en carburant, les échangeurs de chaleur et d'autres composants exposés à des produits chimiques agressifs.
Tableau 1 : Comparaison des propriétés clés des poudres d'alliages communs à base de nickel
Propriété | Inconel 718 | Inconel 625 | Hastelloy X |
---|---|---|---|
Résistance à haute température | Excellent (jusqu'à 700°C) | Bonne (jusqu'à 675°C) | Modéré |
Résistance à la corrosion | Bon | Excellent | Exceptionnel |
Soudabilité | Bon | Bon | Juste |
Applications typiques | Disques et aubes de turbines, Composants de trains d'atterrissage | Systèmes d'échappement, composants exposés à l'eau de mer | Systèmes de carburant, Échangeurs de chaleur |
Applications des poudres d'alliages à base de nickel dans l'aérospatiale
La possibilité de créer des composants complexes, légers et incroyablement résistants à l'aide de poudres d'alliage à base de nickel imprimées en 3D révolutionne la façon dont les avions sont conçus et fabriqués. Explorons quelques-unes des applications les plus passionnantes :
- Disques et aubes de turbines : Ces bêtes de somme constituent le cœur d'un moteur à réaction, tournant à des vitesses vertigineuses et supportant des températures extrêmes. L'Inconel 718 imprimé en 3D offre le mélange parfait de résistance et de performance à haute température pour ces composants critiques, permettant des conceptions plus légères qui améliorent l'efficacité énergétique.
- Pièces de rechange et réparation : Imaginez que vous puissiez remplacer rapidement et efficacement une aube de turbine endommagée. L'impression 3D avec des poudres d'alliage à base de nickel fait de cette idée une réalité. Les composants peuvent être imprimés sur mesure à la demande, ce qui réduit les temps d'arrêt et les coûts de maintenance pour les compagnies aériennes.
- Échangeurs de chaleur : Ces composants vitaux transfèrent la chaleur dans tout le moteur. L'exceptionnelle résistance à la corrosion de l'Hastelloy X le rend idéal pour cette application, garantissant un fonctionnement parfait de l'échangeur dans des environnements difficiles.
- Conception de moteurs de nouvelle génération : La liberté de conception offerte par l'impression 3D permet aux ingénieurs de créer des canaux de refroidissement internes complexes dans les composants du moteur. Cela permet non seulement d'améliorer l'efficacité, mais aussi d'explorer des architectures de moteur entièrement nouvelles, repoussant ainsi les limites de la performance.
Avantages de l'impression 3D Poudres d'alliages à base de nickel
L'impression 3D avec des poudres d'alliage à base de nickel offre un ensemble d'avantages distincts par rapport aux techniques de fabrication traditionnelles telles que le moulage et le forgeage :
- Liberté de conception : Les limites des méthodes traditionnelles telles que le moulage et le forgeage ont disparu. L'impression 3D permet de créer des géométries complexes avec des caractéristiques internes complexes, auparavant impossibles à réaliser. Cela ouvre la voie à des conceptions de moteurs plus légères et plus efficaces qui optimisent le flux d'air et le transfert de chaleur. Imaginez une aube de turbine avec des canaux de refroidissement internes qui serpentent à travers son cœur, maximisant la dissipation de la chaleur sans ajouter d'encombrement.
- Réduction des délais d'exécution : Les processus de fabrication traditionnels peuvent prendre beaucoup de temps, avec de longs délais pour les composants complexes. L'impression 3D permet de réduire considérablement ces délais. Les composants peuvent être imprimés à la demande, ce qui accélère considérablement les cycles de conception, de prototypage et de production. Cette souplesse est cruciale dans l'industrie aérospatiale, qui évolue rapidement, car elle permet de répondre plus rapidement aux nouvelles demandes du marché et aux avancées technologiques.
- Efficacité matérielle : Les techniques de fabrication traditionnelles entraînent souvent d'importantes pertes de matériaux au cours des processus d'usinage et de façonnage. L'impression 3D utilise un laser pour faire fondre sélectivement la poudre uniquement là où c'est nécessaire, ce qui minimise les déchets et en fait une option de fabrication plus durable. Dans un secteur qui s'efforce de réduire son empreinte écologique, cet avantage devient de plus en plus important.
- Amélioration du ratio achat/vol : Le "buy-to-fly ratio" fait référence à la quantité de matière première nécessaire pour produire un composant fini prêt à voler. La fabrication traditionnelle peut entraîner un ratio achat-vol élevé en raison du gaspillage de matériaux. L'efficacité inhérente à l'impression 3D réduit considérablement ce ratio, ce qui permet d'alléger les avions et d'améliorer le rendement énergétique - un facteur essentiel dans un secteur obsédé par la réduction des coûts d'exploitation et de l'impact sur l'environnement.
Défis et considérations
Si les poudres d'alliage à base de nickel imprimées en 3D offrent un potentiel énorme, il y a aussi des défis à relever :
- Coût : Actuellement, le coût de l'impression 3D poudres d'alliages à base de nickel reste plus élevé que les techniques de fabrication traditionnelles pour certaines applications. Toutefois, à mesure que la technologie progresse et que les taux d'adoption augmentent, ces coûts devraient diminuer.
- Qualité de la poudre : La qualité et la consistance de la poudre jouent un rôle crucial dans les propriétés finales du composant imprimé. Des mesures strictes de contrôle de la qualité sont essentielles pour garantir que les pièces répondent aux exigences rigoureuses des applications aérospatiales.
- Post-traitement : Les composants imprimés en 3D peuvent nécessiter des étapes de post-traitement supplémentaires, comme le traitement thermique ou l'usinage, pour obtenir les propriétés finales souhaitées. L'optimisation de ces étapes de post-traitement est cruciale pour garantir la performance et l'efficacité des composants.
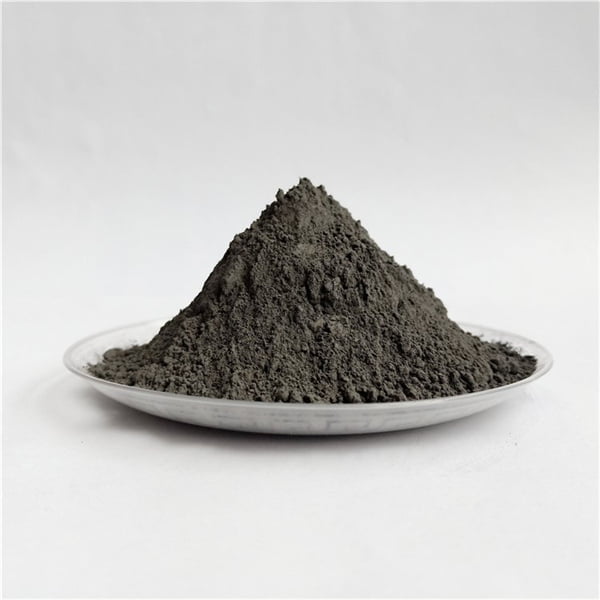
FAQ
Voici quelques-unes des questions les plus fréquentes concernant les poudres d'alliage à base de nickel imprimées en 3D dans l'industrie aérospatiale :
Q : Quels sont les avantages de l'utilisation de poudres d'alliages à base de nickel imprimées en 3D par rapport aux méthodes de fabrication traditionnelles ?
A : L'impression 3D offre des avantages tels que la liberté de conception, la réduction des délais d'exécution, l'amélioration de l'efficacité des matériaux et un meilleur rapport entre l'achat et le vol.
Q : Quelles sont les poudres d'alliage à base de nickel les plus couramment utilisées dans les applications aérospatiales ?
A : L'Inconel 718, l'Inconel 625 et l'Hastelloy X figurent parmi les choix les plus populaires en raison de leurs propriétés uniques telles que la résistance aux températures élevées, la résistance à la corrosion et la soudabilité.
Q : Quels sont les défis associés à l'utilisation de poudres d'alliages à base de nickel imprimées en 3D ?
A : Le coût, la qualité de la poudre et la nécessité d'un post-traitement sont quelques-uns des principaux défis qui sont relevés grâce aux progrès constants de la technologie et des processus de fabrication.
Q : Quel est l'avenir des poudres d'alliages à base de nickel imprimées en 3D dans l'industrie aérospatiale ?
A : L'avenir s'annonce radieux. Avec les progrès technologiques, la baisse des coûts et l'amélioration de la qualité des poudres, l'impression 3D est appelée à jouer un rôle de plus en plus important dans la conception et la production des avions de nouvelle génération, en repoussant les limites de la performance et de l'efficacité.
Conclusion
Le mariage de la technologie d'impression 3D et des poudres d'alliage à base de nickel change la donne pour l'industrie aérospatiale. Il ouvre de nouvelles possibilités d'innovation en matière de conception, d'avions plus légers et plus efficaces, et de cycles de production plus rapides. Bien que des défis subsistent, les avantages potentiels sont indéniables. Alors que nous nous tournons vers l'avenir, les poudres d'alliage à base de nickel imprimées en 3D joueront certainement un rôle essentiel en nous propulsant vers une nouvelle ère d'exploration et d'accomplissement aérospatial.
Partager sur
MET3DP Technology Co. est un fournisseur de premier plan de solutions de fabrication additive dont le siège se trouve à Qingdao, en Chine. Notre société est spécialisée dans les équipements d'impression 3D et les poudres métalliques de haute performance pour les applications industrielles.
Articles connexes
À propos de Met3DP
Mise à jour récente
Notre produit
CONTACTEZ-NOUS
Vous avez des questions ? Envoyez-nous un message dès maintenant ! Nous répondrons à votre demande avec toute une équipe dès réception de votre message.
Obtenir les informations de Metal3DP
Brochure du produit
Obtenir les derniers produits et la liste des prix
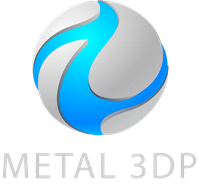
Poudres métalliques pour l'impression 3D et la fabrication additive