Aperçu de la technologie de fusion par faisceau d'électrons
Table des matières
Fusion par faisceau d'électrons (EBM) est une technologie de fabrication additive couramment utilisée pour l'impression 3D de métaux. L'EBM utilise un puissant faisceau d'électrons comme source de chaleur pour fondre et fusionner sélectivement des poudres métalliques, couche par couche, afin de construire des pièces entièrement denses directement à partir de données de CAO.
Comparée à d'autres méthodes d'impression 3D de métaux, comme les procédés laser, l'EBM offre des avantages uniques en termes de vitesse de fabrication, de propriétés des matériaux, de qualité et de rentabilité. Cependant, elle présente également certaines limites en termes de résolution, de finition de surface et d'options de matériaux.
Ce guide fournit une vue d'ensemble détaillée de la technologie de fusion par faisceau d'électrons :
- Comment fonctionne l'EBM
- Types d'équipements et principaux composants
- Matériaux et applications
- Considérations relatives à la conception
- Paramètres du processus
- Avantages et limites
- Comparaison des fournisseurs
- Guide d'utilisation
- Analyse des coûts
- Choisir le bon système EBM
Comment fonctionne la fusion par faisceau d'électrons
Le processus EBM se déroule dans une chambre à vide poussé remplie de gaz argon inerte. La poudre métallique est étalée en fines couches sur une plate-forme de construction à l'aide de râteaux. Un faisceau d'électrons provenant d'un canon à électrons est utilisé pour faire fondre et fusionner sélectivement des régions de chaque couche de poudre en fonction des données de coupe d'un modèle CAO.
La plate-forme de construction s'abaisse progressivement à chaque nouvelle couche. Les pièces sont construites directement sur la plateforme sans nécessiter de structures de support, en raison de la nature indépendante de la géométrie de la fusion sur lit de poudre. Une fois la construction terminée, l'excès de poudre est éliminé pour révéler la pièce solide imprimée en 3D.
La densité d'énergie élevée du faisceau d'électrons entraîne une fusion et une solidification rapides, ce qui permet des taux de fabrication élevés. Le processus EBM se déroule à des températures élevées, jusqu'à 1000°C, ce qui réduit les contraintes résiduelles et les distorsions.
Les pièces imprimées avec EBM atteignent une densité de plus de 99%, avec des propriétés de matériaux comparables ou supérieures à celles de la fabrication traditionnelle.
Types d'équipements et composants EBM
Les systèmes EBM contiennent les principaux éléments suivants :
Pistolet à électrons - génère un faisceau focalisé d'électrons à haute énergie
Contrôle du faisceau - des électro-aimants guident et dévient le faisceau d'électrons
Alimentation haute tension - accélère les électrons jusqu'à 60kV
Chambre à vide - fournit un environnement à vide poussé
Distribution de poudre - dépose et étale des couches de poudre métallique
Cassettes à poudre/hottes - stocker et distribuer la poudre
Construire une plateforme - s'abaisse progressivement au fur et à mesure que les couches sont construites
Serpentins de chauffage - préchauffe le lit de poudre jusqu'à 1000°C
Pupitre de commande - ordinateur et logiciel pour faire fonctionner le système
Il existe plusieurs variantes de machines EBM commerciales :
Système EBM | Construire l'enveloppe | Puissance du faisceau | Épaisseur de la couche |
---|---|---|---|
Arcam A2X | 200 x 200 x 380 mm | 3kW | 50-200 microns |
Arcam Q10plus | 350 x 350 x 380 mm | 5,4 kW | 50-200 microns |
Arcam Q20plus | 500 x 500 x 400 mm | 7kW | 50-200 microns |
Arcam Spectra L | 275 x 275 x 380 mm | 1kW | 50-200 microns |
Sciaky EBAM | 1500 x 1500 x 1200 mm | 15-60kW | 200 microns |
Des enveloppes de construction plus grandes et une puissance de faisceau plus élevée permettent des constructions plus rapides, des pièces plus grandes et une productivité plus élevée. Les machines plus petites ont tendance à avoir une résolution et des finitions de surface plus fines.
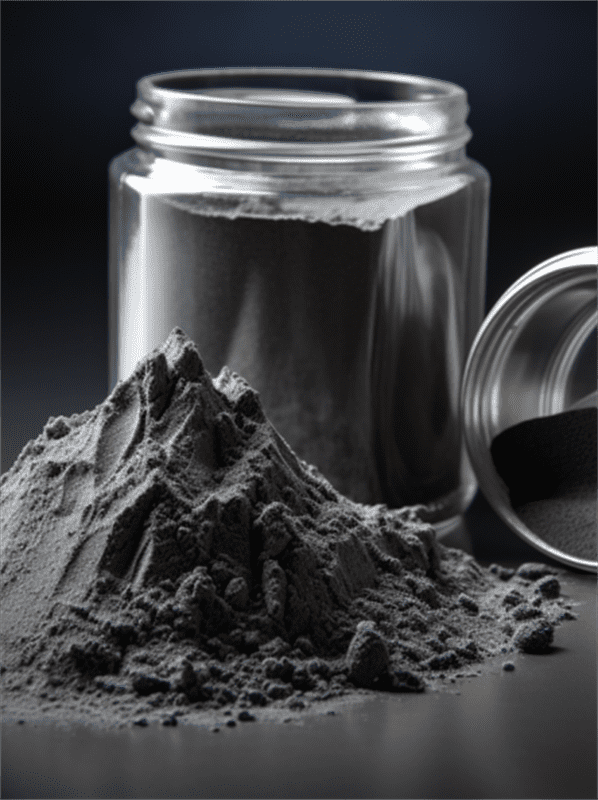
Matériaux et applications EBM
Les matériaux les plus couramment utilisés dans l'EBM sont les suivants :
- Alliages de titane comme le Ti-6Al-4V
- Superalliages à base de nickel comme l'Inconel 718, l'Inconel 625
- Alliages cobalt-chrome
- Aciers à outils comme le H13, l'acier maraging
- Alliages d'aluminium
- Alliages de cuivre
- Aciers inoxydables tels que 17-4PH, 316L
Les principales applications de l'EBM sont les suivantes
- Aérospatiale - aubes de turbines, roues, supports structurels
- Médical - implants orthopédiques, prothèses
- Automobile - composants pour les sports mécaniques, outillage
- Industrie - pièces pour le traitement des fluides, échangeurs de chaleur
- Outillage - moules d'injection, moulage sous pression, matrices d'extrusion
Les avantages de l'EBM pour ces applications sont les suivants
- Grande solidité et résistance à la fatigue
- Géométries complexes avec treillis et canaux internes
- Délais courts pour les pièces métalliques
- Consolidation des assemblages en une seule pièce
- Allègement et optimisation de la conception
- Adaptation et personnalisation des pièces
Considérations relatives à la conception de l'EBM
L'EBM impose certaines restrictions en matière de conception :
- Épaisseur minimale des parois de 0,8 à 1 mm pour éviter l'effondrement
- Pas de contre-dépouilles ni de surplombs horizontaux
- Porte-à-faux max. de 45° sans support
- Canaux internes ouverts d'un diamètre minimum de 1 mm
- Caractéristiques fines limitées à une résolution de 0,5-1 mm
Les conceptions doivent éviter les gradients thermiques importants afin de minimiser les contraintes résiduelles :
- Epaisseur de paroi uniforme
- Transitions graduelles dans l'épaisseur de la section
- Supports intérieurs et treillis pour les grands volumes
Le post-traitement, comme l'usinage, le perçage et le polissage, peut améliorer l'état de surface.
Paramètres du processus EBM
Paramètres clés du processus EBM :
- Faisceau d'électrons - Intensité du faisceau, mise au point, vitesse, modèle
- Poudre - Matériau, épaisseur de la couche, taille des particules
- Température - Préchauffage, température de construction, stratégie de balayage
- Vitesse - Distance entre les points, vitesse des contours, vitesse des hachures
Ces paramètres contrôlent des propriétés telles que la densité, la précision, l'état de surface et la microstructure :
Paramètres | Gamme typique | Effet sur les propriétés des pièces |
---|---|---|
Courant du faisceau | 5-40mA | Apport d'énergie, taille du bassin de fusion |
Vitesse du faisceau | 104-107 mm/s | Densité énergétique, taux de refroidissement |
Épaisseur de la couche | 50-200μm | Résolution, rugosité de la surface |
Température de construction | 650-1000°C | Contrainte résiduelle, distorsion |
Vitesse de balayage | 500-10 000 mm/s | Etat de surface, porosité |
Modèle de balayage | Échiquier, unidirectionnel | Anisotropie, densité |
Un réglage précis de ces paramètres est nécessaire pour obtenir des propriétés matérielles et une précision optimales pour chaque alliage.
Avantages de la fusion par faisceau d'électrons
Les principaux avantages de l'EBM sont les suivants
- Taux de production élevé - jusqu'à 80 cm3/hr possible
- Pièces entièrement denses - plus de 99% de densité atteinte
- Excellentes propriétés mécaniques - solidité, dureté, résistance à la fatigue
- Haute précision et répétabilité - précision de ±0,2 mm
- Supports minimaux nécessaires - réduit le post-traitement
- Construction à haute température - réduit les contraintes résiduelles
- Faible contamination - environnement sous vide de haute pureté
Les vitesses de balayage élevées entraînent des cycles de fusion et de solidification rapides, créant des microstructures à grain fin. La méthode de construction par couches permet d'obtenir des pièces comparables aux propriétés du corroyage.
Limites de la fusion par faisceau d'électrons
Les inconvénients de l'EBM sont les suivants :
- Résolution limitée - taille minimale des caractéristiques ~0,8 mm
- Finition de surface rugueuse - effet de marche d'escalier, nécessite une finition.
- Matériaux restreints - principalement alliages de Ti, alliages de Ni, CoCr actuellement
- Coût élevé de l'équipement - $350.000 à $1 million+ pour une machine
- Temps de préchauffage lent - 1 à 2 heures pour atteindre la température de construction
- Risque de contamination - le zirconium peut contaminer les alliages réactifs
- Gestion des poudres - recyclage, manipulation des poudres fines
- Exigences en matière de ligne de vue - les surplombs horizontaux ne sont pas possibles
Le modèle de construction en couches anisotropes et l'effet de "marche d'escalier" des couches de poudre frittée créent des stries visibles sur les surfaces orientées vers le haut. Le faisceau d'électrons ne peut fusionner des matériaux qu'en ligne de mire directe.
Fournisseurs de machines EBM
Les principaux fabricants d'équipements EBM sont les suivants
Fournisseur | Modèles | Matériaux | Puissance du faisceau | Fourchette de prix |
---|---|---|---|---|
Arcam EBM (GE) | A2X, Q10plus, Q20plus | Alliages de Ti, Ni, CoCr | 3-7kW | $350,000-$800,000 |
Sciaky | Série EBAM 300, 500 | Ti, Al, Inconel, aciers | 15-60kW | $500 000-$1,5 million |
slaM | slm280 | Al, Ti, CoCr, aciers à outils | 5kW | $500,000-800,000 |
JEOL | JEM-ARM200F | Alliages de nickel, aciers, Ti | 3kW | $700,000-900,000 |
Les systèmes EBM d'Arcam ont les capacités les plus étendues en matière de matériaux, tandis que Sciaky propose des solutions de production à grande échelle. SLM Solutions et JEOL proposent également une technologie EBM axée sur les métaux.
Exploitation des systèmes EBM
Faire fonctionner une machine EBM :
- Installer l'équipement EBM avec l'alimentation électrique, le refroidissement, le gaz inerte et la ventilation d'échappement appropriés.
- Chargement des données CAO et saisie des paramètres de construction dans le logiciel EBM
- Tamiser et charger la poudre métallique dans des cassettes
- Préchauffage du lit de poudre à la température de traitement
- Étalonnage de la focalisation et de la puissance du faisceau d'électrons
- Commencer la construction en couches pendant que le faisceau balaie et fait fondre la poudre.
- Laisser les pièces refroidir lentement avant de les retirer de la machine
- Éliminer l'excès de poudre à l'aide d'un aspirateur
- Découper des pièces à partir de la plaque de construction et procéder à un post-traitement
Une manipulation et un stockage corrects de la poudre sont essentiels pour éviter toute contamination susceptible de provoquer des défauts. Il est également essentiel d'entretenir régulièrement le filament du faisceau, les filtres à poudre et le système d'aspiration.
Analyse des coûts de traitement des EBM
Facteurs de coût pour la production d'EBM :
- Amortissement des machines - ~15-20% du coût total de la pièce
- Travail - fonctionnement de la machine, post-traitement
- Poudre - $100-500/kg pour les alliages de titane
- Puissance - une forte consommation d'électricité pendant la construction
- Argon - consommation journalière de gaz de purge
- Maintenance - source de faisceau, système de vide, râteaux
- Post-traitement - enlèvement du support, finition de la surface
Des économies d'échelle peuvent être réalisées en regroupant des pièces plus petites en une seule fabrication. Des machines plus grandes produisent des pièces plus rapidement et de manière plus rentable. Le coût initial élevé du système est réparti sur un plus grand nombre de pièces.
Pour la production de faibles volumes, l'externalisation vers un bureau de services permet de minimiser les frais généraux liés à l'équipement.
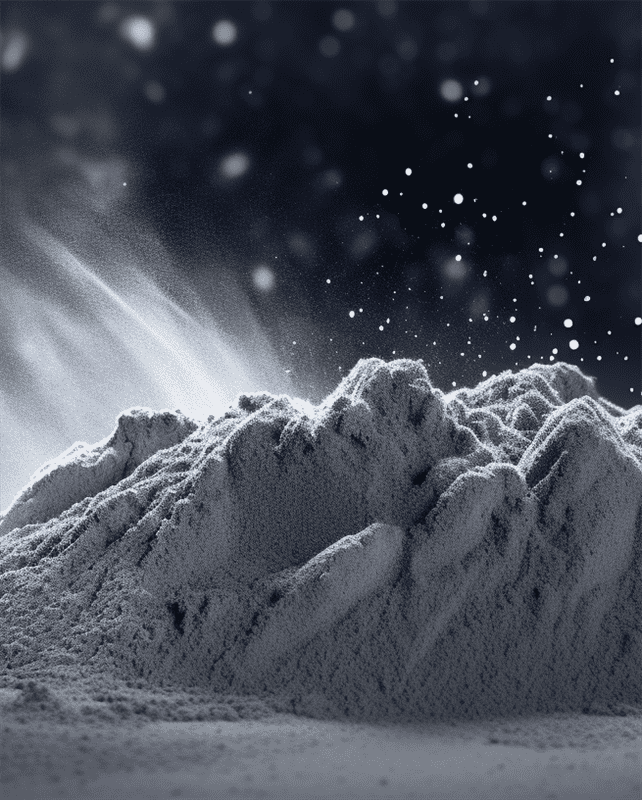
Comment choisir un système EBM
Considérations clés pour la sélection d'une machine EBM :
- Construire une enveloppe - correspondre aux exigences en matière de taille des pièces
- Précision - la taille minimale des caractéristiques et les exigences en matière de finition de surface
- Matériaux - alliages requis pour les applications
- Débit - objectifs de volume de production quotidiens/mensuels
- Exigences en matière d'alimentation - la capacité d'alimentation électrique disponible
- Logiciel - facilité d'utilisation, flexibilité, formats de données
- Post-traitement - le temps et les coûts de finition
- Formation et soutien - installation, fonctionnement, entretien
- Coût total - prix du système, frais d'exploitation, poudre
Effectuer des essais de fabrication d'échantillons de pièces sur différents systèmes EBM afin d'évaluer la qualité réelle des pièces et les aspects économiques.
Investissez dans l'enveloppe de construction la plus large possible en fonction du budget et des contraintes d'espace, afin de permettre une expansion future. S'associer à un fournisseur réputé qui peut fournir une assistance technique continue.
FAQ
Q : Quelle est la précision de l'EBM ?
R : La précision dimensionnelle et les tolérances de ±0,2 mm sont typiques pour les pièces EBM. Des caractéristiques fines jusqu'à 0,3 mm sont possibles.
Q : Quels sont les matériaux qui peuvent être utilisés dans l'EBM en dehors des métaux ?
R : L'EBM est limité aux alliages métalliques conducteurs. Les photopolymères et les céramiques ne peuvent actuellement pas être traités en raison de la source d'énergie du faisceau d'électrons.
Q : L'EBM nécessite-t-elle des supports ?
R : L'EBM ne nécessite pas de structures de soutien pour les surplombs inférieurs à 45° en raison de la nature indépendante de la géométrie de la fusion en lit de poudre. Des supports internes minimaux peuvent être utiles pour les grandes sections creuses.
Q : Quel est l'état de surface ?
R : Les pièces EBM telles qu'elles sont fabriquées présentent des surfaces relativement rugueuses en raison des couches de poudre et des traces de balayage. Diverses opérations d'usinage, de rectification ou de polissage sont nécessaires pour améliorer l'état de surface.
Q : Quel est le coût de l'EBM par rapport aux autres procédés d'impression 3D ?
R : L'équipement EBM a un coût initial plus élevé, de 1T4T350 000 à plus de 1T4T1 million. Mais la vitesse de fabrication élevée peut compenser ce coût en réduisant les coûts des pièces à l'échelle. Le coût du processus par pièce est compétitif par rapport aux autres méthodes d'impression 3D de métaux.
Q : Les pièces EBM nécessitent-elles un post-traitement ?
R : La plupart des pièces EBM nécessitent un post-traitement tel que le découpage de la plaque de construction, le détensionnement, l'usinage de surface, le perçage de trous, le meulage ou le polissage afin d'obtenir la finition, la tolérance et l'aspect final de la pièce. Des retouches manuelles minimales peuvent être nécessaires pour casser les arêtes vives ou réduire la rugosité.
Partager sur
MET3DP Technology Co. est un fournisseur de premier plan de solutions de fabrication additive dont le siège se trouve à Qingdao, en Chine. Notre société est spécialisée dans les équipements d'impression 3D et les poudres métalliques de haute performance pour les applications industrielles.
Articles connexes
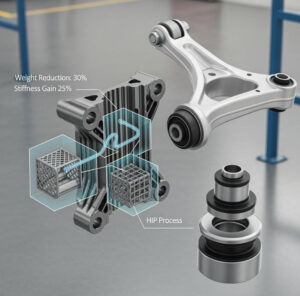
Metal 3D Printed Subframe Connection Mounts and Blocks for EV and Motorsport Chassis
Lire la suite "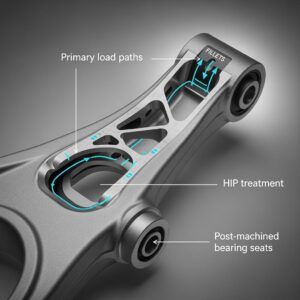
Metal 3D Printing for U.S. Automotive Lightweight Structural Brackets and Suspension Components
Lire la suite "À propos de Met3DP
Mise à jour récente
Notre produit
CONTACTEZ-NOUS
Vous avez des questions ? Envoyez-nous un message dès maintenant ! Nous répondrons à votre demande avec toute une équipe dès réception de votre message.
Obtenir les informations de Metal3DP
Brochure du produit
Obtenir les derniers produits et la liste des prix