Aperçu des poudres d'acier inoxydable
Table des matières
Poudre d'acier inoxydable est un matériau polyvalent avec des applications dans de nombreuses industries. Ce guide fournit un aperçu complet de la poudre d'acier inoxydable, y compris les méthodes de fabrication, les nuances, les propriétés, les applications, et plus encore.
Aperçu des poudres d'acier inoxydable
La poudre d'acier inoxydable fait référence aux particules d'acier inoxydable sous forme de poudre. Elle est fabriquée en atomisant ou en réduisant l'acier inoxydable en une poudre fine à des fins industrielles diverses.
Certaines propriétés et avantages clés de la poudre d'acier inoxydable comprennent :
- Haute résistance et durabilité
- Résistance à la corrosion et à l'usure
- Capacité à être frittée en formes complexes
- Gamme d'éléments d'alliage pour personnaliser les propriétés
- Recyclabilité
- Rapport coût-efficacité
La poudre d'acier inoxydable est utilisée dans des applications telles que l'impression 3D, le revêtement de surface, le brasage, le soudage, les pièces de métallurgie des poudres, et plus encore. La taille du marché mondial de la poudre d'acier inoxydable était de plus d'un milliard de dollars en 2021 et devrait croître à un TCAC de plus de 8 % de 2022 à 2030.
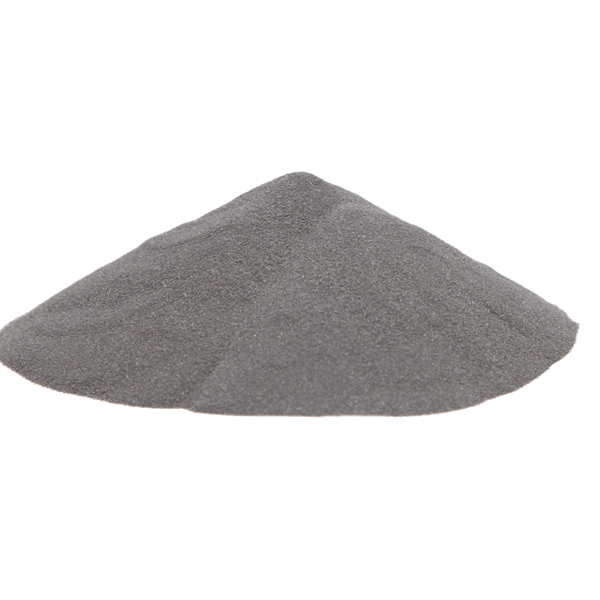
Types de Poudre d'acier inoxydable
Il existe différentes nuances et types de poudre d'acier inoxydable classés par microstructure, éléments d'alliage, propriétés et applications prévues.
Type | Description | Composition | Propriétés | Applications |
---|---|---|---|---|
Austénitique | Non magnétique, résistance à la corrosion plus élevée | Cr, Ni, Mo | Ductile, non durcissable | Automobile, architecture, produits chimiques |
Martensitique | Magnétique, résistance plus élevée | Cr, moins de Ni | Durcissable, moins de résistance à la corrosion | Coutellerie, instruments chirurgicaux, vannes |
Ferritique | Magnétique, moins cher | Cr, pas de Ni | Moins ductile, résistance modérée à la corrosion | Automobile, appareils électroménagers, utilisations industrielles |
Duplex | Équilibre de résistance et de résistance à la corrosion | Cr, Ni, Mo, N | Bonne soudabilité, coût plus élevé | Transformation chimique, pétrole et gaz, marine, papier |
Durcissement par précipitation | Nuance martensitique durcissable | Cr, Ni, Cu, Al | Haute résistance après traitement de vieillissement | Aérospatiale, production d'énergie |
Processus de fabrication de la poudre d'acier inoxydable
La poudre d'acier inoxydable peut être produite par diverses méthodes. Les principaux procédés de fabrication comprennent :
Atomisation – Les alliages d'acier inoxydable fondus sont atomisés en fines gouttelettes qui se solidifient en particules de poudre. Des méthodes d'atomisation à l'eau, au gaz, au plasma ou centrifuges sont utilisées. Cela produit des poudres sphériques et raffinées, idéales pour l'impression 3D.
Électrolyse – Un objet en acier inoxydable est suspendu comme anode dans une cellule électrolytique. L'oxygène généré à l'anode réagit avec l'acier pour former de la poudre d'oxydes de fer et de chrome.
Fraisage – Les déchets d'acier inoxydable sont broyés mécaniquement en une forme de poudre angulaire irrégulière, bien adaptée au pressage en compacts. Coût inférieur, mais granulométrie plus large.
Réduction – Les oxydes d'acier inoxydable sont réduits à l'aide d'hydrogène ou de monoxyde de carbone pour produire une poudre d'acier inoxydable fine.
Moulage par injection de métal – Une matière première de poudre d'acier inoxydable et de liant est moulée par injection, puis frittée pour fabriquer des pièces de forme nette complexes.
Chaque méthode donne des poudres de tailles, de formes, de pureté et de coûts différents. Le procédé de fabrication est adapté en fonction de l'application.
Nuances de poudre d'acier inoxydable
Diverses nuances standard de poudre d'acier inoxydable sont disponibles dans le commerce. Les éléments d'alliage courants comprennent le chrome, le nickel, le molybdène, le manganèse et l'azote. Voici quelques-unes des nuances les plus largement utilisées :
- 304/304L – Nuance la plus populaire, excellente résistance à la corrosion
- 316/316L – Molybdène ajouté pour la résistance à la corrosion par piqûre/crevasse
- 410 – Nuance martensitique de base, usage général
- 420 – Teneur en carbone plus élevée, utilisée pour les outils de coupe
- 17-4PH – Nuance de durcissement par précipitation martensitique, bonne résistance
- 15-5PH – Durcissement par précipitation, résistance et dureté plus élevées
- Nuances personnalisées – Composition optimisée pour le frittage, l'impression 3D, etc.
Propriétés de la poudre d'acier inoxydable
Les principales propriétés de la poudre d'acier inoxydable comprennent :
Taille des particules – Généralement de 5 à 150 microns. Une distribution plus étroite améliore le frittage.
Morphologie – La forme est sphérique pour l'atomisation, irrégulière pour le broyage. Affecte l'écoulement et la densité de tassement.
Densité apparente – Généralement de 40 à 50 % de la densité réelle, ce qui indique la porosité entre les particules.
Capacité d'écoulement – Important pour le remplissage des matrices. Amélioré par les particules sphériques et les additifs.
Compressibilité – Degré de densification lors du compactage. Essentiel pour le frittage.
Fritabilité – Capacité à se lier en une masse dense lors du chauffage. Affecté par la pureté, la taille, la forme.
Composition de l'alliage – Détermine les propriétés telles que la résistance, la résistance à la corrosion, la résistance à l'usure, etc.
En contrôlant les caractéristiques et la composition de la poudre, les propriétés des pièces frittées finies peuvent être adaptées aux besoins de l'application.
Applications de Poudre d'acier inoxydable
Certaines applications majeures de la poudre d'acier inoxydable comprennent :
Impression 3D
Également connue sous le nom de fabrication additive, l'impression 3D construit des pièces couche par couche à partir de poudre d'acier inoxydable en utilisant l'énergie laser ou le faisceau d'électrons. Les avantages incluent la liberté de conception, la réduction des déchets, le prototypage rapide et la personnalisation de masse. Les méthodes courantes incluent le frittage laser direct des métaux (DMLS), la fusion sélective par laser (SLM) et la fusion par faisceau d'électrons (EBM).
Métallurgie des poudres
En métallurgie des poudres, la poudre d'acier inoxydable est compactée puis frittée pour fabriquer des pièces haute performance comme des engrenages, des filtres et des composants automobiles. Permet de produire en série des formes complexes à faible coût avec un minimum de gaspillage de matériaux.
Revêtements de surface
Les revêtements en poudre d'acier inoxydable sont appliqués à l'aide de méthodes de projection thermique ou de revêtement laser. Fournit une résistance à l'usure, une protection contre la corrosion, des barrières thermiques et une conductivité électrique aux surfaces des composants fonctionnant dans des conditions exigeantes.
Brasage et soudure
La pâte de poudre d'acier inoxydable peut être utilisée comme charge pour joindre des composants en acier inoxydable nécessitant des liaisons de matériaux différents ou de grands espaces de joint. Le brasage fournit des joints solides à haute température.
Soudage
Des fils fourrés en poudre d'acier inoxydable spécialisés sont utilisés pour souder des matériaux en acier inoxydable, améliorant la résistance des soudures et la résistance à la corrosion par rapport aux fils pleins. L'âme en poudre fournit des éléments d'alliage.
Charbon actif granulaire
De la poudre d'acier inoxydable est ajoutée pendant la production de charbon actif pour augmenter la résistance mécanique et la résistance à l'abrasion pour les applications de traitement de l'eau.
Autres applications de niche
La poudre d'acier inoxydable est également utilisée dans la fabrication d'outils diamantés, de précurseurs pour les nanomatériaux, de blindage électromagnétique, de fabrication de noyaux de poudre d'acier et de matériaux de friction.
Comment choisir la poudre d'acier inoxydable
La sélection de la poudre d'acier inoxydable appropriée dépend de facteurs tels que :
- Application prévue – Cela détermine les propriétés requises de la poudre et la nuance d'alliage. Par exemple, la poudre 316L pour la résistance à la corrosion ou l'acier maraging pour la résistance.
- Processus de production – Poudre atomisée, broyée ou mélangée adaptée à la FA, au pressage, à la projection thermique, etc.
- Taille et forme des particules – Poudre sphérique et fine d'environ 20 microns pour la FA contre la poudre irrégulière plus grande pour le pressage.
- Niveau de pureté – Une grande pureté supérieure à 99,5 % est nécessaire pour les applications critiques comme les implants médicaux.
- Densité apparente – Une densité plus élevée supérieure à 3 g/cm3 est souhaitable pour un meilleur écoulement et compactage.
- Coût – Les prix varient de 50 à 150 $ par kg en fonction de la nuance, de la pureté, des caractéristiques des particules et du volume d'achat.
Les principaux fournisseurs mondiaux incluent Sandvik, Höganäs, Carpenter Powder Products, Praxair Surface Technologies et CNPC Powder, qui peuvent fournir des poudres optimisées pour des exigences spécifiques. Il est préférable de consulter de près les fournisseurs lors du développement de nouveaux produits.
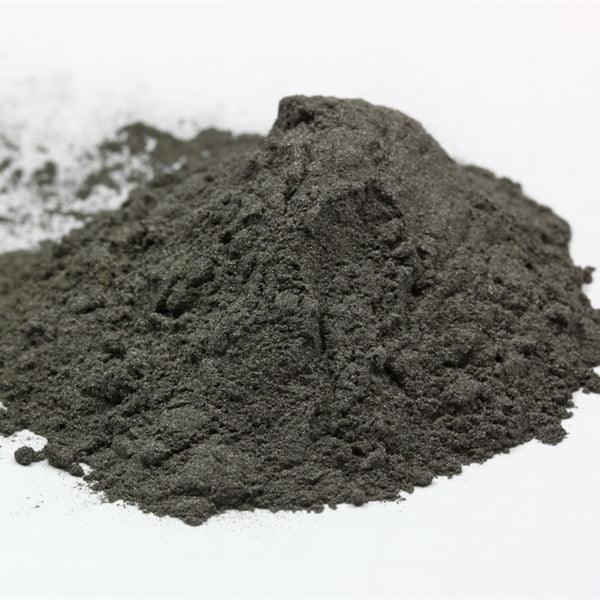
Comparaison des procédés de fabrication de poudre d'acier inoxydable
Processus | Morphologie des particules | Taille des particules | La pureté | Coût | Applications |
---|---|---|---|---|---|
Atomisation du gaz | Sphérique | 5 – 150 μm | Haut | Moyen | Fabrication additive, revêtement de surface |
Vaporisation de l'eau | Irrégulier, sphérique | 20 – 300 μm | Moyen | Faible | Pièces pressées et frittées, revêtements |
Atomisation au plasma d'air | Surtout sphérique | 10 - 150 μm | Moyen | Moyen | Moulage par injection de métal, pressage |
Atomisation centrifuge | Sphérique | 20 - 150 μm | Haut | Haut | Fabrication additive |
Fraisage mécanique | Irrégulier, anguleux | 1 – 350 μm | Faible | Faible | Pièces pressées et frittées |
Électrolyse | Dendritique, irrégulier | 1 – 150 μm | Moyen | Moyen | Revêtement de surface, métallurgie des poudres |
Réduction du métal | Irrégulier, poreux | 10 - 150 μm | Faible | Faible | Pièces pressées et frittées |
Installation d'une usine de production de poudre d'acier inoxydable
L'installation d'une usine de production de poudre d'acier inoxydable nécessite une attention particulière à des facteurs tels que :
- Sélection du site – Espace suffisant pour l'équipement, le stockage des matières premières et des produits, les services publics, le traitement des effluents. Accès facile pour le transport.
- Utilitaires – Alimentation électrique, eau de procédé, conduites d'air comprimé, de gaz inerte.
- Fondation – Fondations en béton armé solides pour les atomiseurs, les broyeurs et les fours de réduction. Supports d'amortissement des vibrations.
- Machines – Installer les principaux équipements tels que les fours à haute température, les boîtes à gants, les atomiseurs, les broyeurs, les cyclones, les tamis selon les instructions du fabricant.
- Systèmes auxiliaires – Manutention des matériaux, dépoussiérage, épuration des gaz, traitement des déchets, commandes et automatisation.
- Sécurité – Équipements électriques antidéflagrants, suppression d'incendie, ventilation adéquate, EPI pour la manipulation de la poudre de métal.
- Mise en service – Essais de production pour vérifier la qualité de la poudre, le taux de production, la manipulation sûre des matériaux, la conformité environnementale.
- Certification – Enregistrement du système qualité ISO 9001. Certifications spécifiques à l'industrie de l'ASME, de l'ASTM, etc.
Une installation et une mise en service appropriées par des spécialistes expérimentés garantissent qu'une usine de poudre d'acier inoxydable dispose d'opérations sûres et optimisées et d'une capacité de production maximale.
Exploitation et maintenance des équipements de poudre d'acier inoxydable
Pour obtenir une qualité et une productivité constantes de la poudre d'acier inoxydable, les principales directives d'exploitation et de maintenance comprennent :
- Suivez les procédures d'exploitation standard pour le démarrage, l'arrêt, la planification des lots, la manutention des matériaux, les systèmes de sécurité et la surveillance environnementale.
- Surveillez les principaux paramètres de processus tels que la température, la pression, les débits, la consommation d'énergie et maintenez-les dans les limites optimisées.
- Prélevez des échantillons représentatifs de lots de poudre et testez-les pour la taille, la forme, la chimie, la densité, l'aptitude à l'écoulement selon les normes ASTM.
- Effectuez une maintenance préventive selon le calendrier pour les fours, les conduites de gaz, les atomiseurs, les cyclones, les broyeurs à mar
- Inspecter les équipements rotatifs tels que les moteurs, les engrenages et les turbines pour détecter les vibrations et le bruit, et lubrifier les roulements.
- Calibrer fréquemment les instruments tels que les manomètres, les sondes RTD et les débitmètres pour garantir leur précision.
- Inspecter les éléments réfractaires et chauffants des fours et les réparer/remplacer si nécessaire pour éviter les pannes imprévues.
- S'assurer que les systèmes d'extraction de poussière fonctionnent efficacement afin de minimiser les risques d'explosion. Suivre les procédures d'exploitation normalisées (SOP) en matière de propreté.
- Auditer périodiquement les systèmes de sécurité des procédés tels que les arrêts d'urgence, la détection des incendies/gaz et la ventilation.
Avec un personnel qualifié et des procédures de maintenance rigoureuses, les installations de production de poudre d'acier inoxydable peuvent fonctionner pendant des années sans problèmes majeurs.
Comment choisir un fournisseur de poudre d'acier inoxydable
Lors du choix d'un fournisseur de poudre d'acier inoxydable, il est essentiel de prendre en compte les facteurs suivants :
- Spécifications de la poudre – Capacité à fournir la nuance, la granulométrie/forme, le niveau de pureté, la densité et les caractéristiques d'écoulement requis.
- Certifications de qualité – Le fournisseur doit être accrédité ISO 9001, AS9100, Nadcap, et disposer de la documentation qualité correspondante.
- Expertise technique – Connaissance de la métallurgie pour personnaliser la poudre en fonction d'applications spécifiques et fournir une assistance à l'application.
- Capacité de fabrication – Utiliser des technologies modernes d'atomisation, de broyage et de criblage pour produire des poudres de manière constante.
- Capacité de test – Laboratoire entièrement équipé pour des tests et une caractérisation complets de la poudre selon les normes internationales.
- Compétence en matière de R&D – S'engager dans la recherche et le développement de nouveaux produits pour les applications émergentes comme la fabrication additive (FA).
- Service à la clientèle – Réponse rapide aux demandes de renseignements, aux commandes et aux requêtes. Conditions claires en matière de prix, de livraison et de retours.
- Conformité réglementaire – Documentation telle que les fiches de données de sécurité (FDS), les certifications de conformité aux réglementations environnementales.
- Réseau logistique – Capacité à expédier le matériau en toute sécurité dans un emballage conforme aux exigences relatives aux marchandises dangereuses.
Les principaux fournisseurs mondiaux de poudre d'acier inoxydable sont Sandvik, Carpenter Powder Products, Hoganas, Praxair Surface Technologies et CNPC Powder.
Avantages et inconvénients de Poudre d'acier inoxydable
Pour | Cons |
---|---|
Excellente résistance et résistance à la corrosion | Coût relativement élevé par rapport à l'acier au carbone |
Peut être formé en formes complexes par frittage et FA | Conductivité thermique inférieure à celle des autres métaux |
Large gamme de nuances pour diverses applications | Nécessite une finition de surface pour une meilleure esthétique |
Propriétés hautement personnalisables grâce à l'alliage | Difficile à usiner dans certaines nuances durcies |
Facile à désinfecter pour l'hygiène dans les utilisations alimentaires/médicales | Peut être sujet à la corrosion par piqûre dans certains environnements |
Bonnes propriétés à haute température | Moins conducteur électriquement/magnétiquement que les autres métaux |
100 % recyclable et respectueux de l'environnement | Manipulation spéciale requise en raison de la réactivité de la poudre fine |
Méthodes de fabrication établies avec une grande disponibilité | Nombre limité de fournisseurs qualifiés dans le monde |
Poudre d'acier inoxydable contre solides d'acier inoxydable
Paramètres | Poudre d'acier inoxydable | Solides d'acier inoxydable |
---|---|---|
État | Forme de poudre fine | Barre pleine, plaque, stock de tuyaux |
Fabrication | Atomisation, électrolyse, broyage | Coulée, laminage, usinage de lingots d'acier inoxydable |
Composition | Alliages souvent personnalisés | Nuances standard des séries 300/400 |
Applications | Fabrication additive, métallurgie des poudres | Fabrication générale de soudures et de composants finis |
Propriétés | Granulométrie fine, sans contrainte | Grains plus grossiers, contraintes possibles |
Traitement | Compactage et frittage | Cintrage, usinage, soudage, traitement thermique |
Coût | $50-150 par kg | 3 à 10 dollars par kg pour les nuances de base |
Disponibilité | Nombre limité de fournisseurs | Facilement disponible dans le monde entier |
Délai d'exécution | Peut être long pour les commandes personnalisées | Délais de livraison plus courts pour les nuances standard |
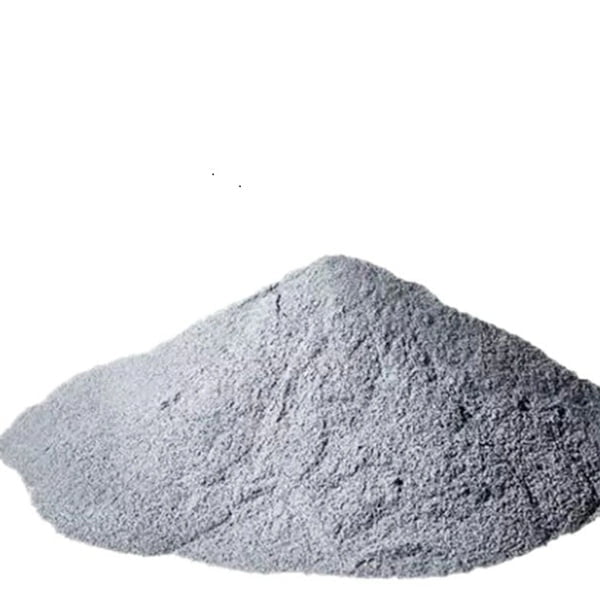
FAQ
Q : Quelles sont les nuances de poudre d'acier inoxydable les plus courantes ?
R : Les nuances austénitiques les plus courantes sont 304, 304L et 316L, tandis que les nuances martensitiques 410 et 17-4PH sont largement utilisées. Des alliages personnalisés optimisés pour les applications de FA ou de frittage sont également disponibles.
Q : Quelle est la granulométrie typique des particules de poudre d'acier inoxydable ?
R : La granulométrie peut varier d'environ 1 micron à plus de 150 microns. Cependant, une granulométrie de 10 à 45 microns est courante pour de nombreuses applications comme le MIM, la FA et le pressage.
Q : Comment la résistance à la corrosion est-elle affectée dans les pièces de métallurgie des poudres en acier inoxydable ?
R : Les pièces de métallurgie des poudres (MP) peuvent présenter une résistance à la corrosion légèrement inférieure à celle des formes corroyées en raison de la porosité résiduelle si elles ne sont pas entièrement densifiées. Un frittage et une finition appropriés minimisent cet effet.
Q : Qu'est-ce qui provoque l'oxydation de surface lors de la manipulation de la poudre d'acier inoxydable ?
R : La poudre fine d'acier inoxydable peut s'oxyder facilement lorsqu'elle est exposée à l'air. L'utilisation d'une atmosphère sous vide ou de gaz inerte est recommandée pour la manipulation afin d'éviter l'oxydation.
Q : Comment la fabricabilité et l'usinabilité des aciers inoxydables MP sont-elles comparées aux formes corroyées ?
R : L'acier inoxydable MP est moins ductile et moins usinable que les formes corroyées en raison de la porosité et de la dureté plus élevée. L'usinage à l'état brut des compacts de poudre avant le frittage améliore la finition.
Q : Quel est le taux de production typique des usines commerciales de poudre d'acier inoxydable ?
R : Le taux de production dépend de la taille de l'équipement et du procédé. Les usines de taille moyenne produisent généralement 100 à 300 kg/heure de poudre d'acier inoxydable.
Q : Quelles sont les précautions de sécurité requises lors de l'utilisation de la poudre d'acier inoxydable ?
R : Évitez d'inhaler la poussière en utilisant des respirateurs. Assurez une ventilation adéquate, une mise à la terre et un éclairage antidéflagrant pour éviter les explosions de poussière. Utilisez l'extraction de poussière et l'équipement de protection individuelle (EPI).
Conclusion
La poudre d'acier inoxydable offre des avantages distincts en termes de résistance, de résistance à la corrosion et de flexibilité de fabrication. Avec des méthodes de fabrication, des nuances d'alliage, des caractéristiques de particules et des applications variées, la poudre d'acier inoxydable offre aux ingénieurs d'études des options améliorées pour développer des composants innovants en utilisant la métallurgie des poudres et les techniques additives. En sélectionnant la poudre, la méthode de production et les paramètres de procédé appropriés, la poudre d'acier inoxydable peut offrir des performances supérieures dans les conditions les plus exigeantes dans tous les secteurs.
Partager sur
MET3DP Technology Co. est un fournisseur de premier plan de solutions de fabrication additive dont le siège se trouve à Qingdao, en Chine. Notre société est spécialisée dans les équipements d'impression 3D et les poudres métalliques de haute performance pour les applications industrielles.
Articles connexes
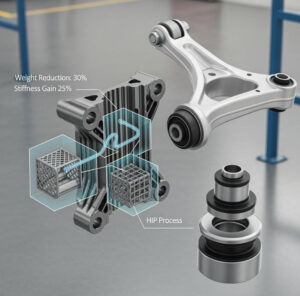
Metal 3D Printed Subframe Connection Mounts and Blocks for EV and Motorsport Chassis
Lire la suite "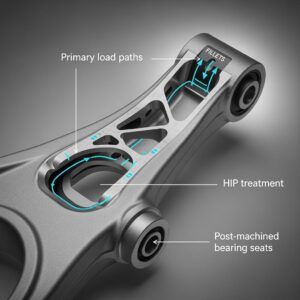
Metal 3D Printing for U.S. Automotive Lightweight Structural Brackets and Suspension Components
Lire la suite "À propos de Met3DP
Mise à jour récente
Notre produit
CONTACTEZ-NOUS
Vous avez des questions ? Envoyez-nous un message dès maintenant ! Nous répondrons à votre demande avec toute une équipe dès réception de votre message.
Obtenir les informations de Metal3DP
Brochure du produit
Obtenir les derniers produits et la liste des prix