Payload Mounts for Satellites and Aircraft via 3D Printing
Table des matières
Introduction: Revolutionizing Aerospace Componentry with 3D Printed Payload Mounts
The aerospace industry operates at the zenith of engineering achievement, demanding components that exhibit extraordinary performance under extreme conditions. From the vacuum of space to the dynamic stresses of atmospheric flight, every part must function flawlessly, often while pushing the boundaries of weight efficiency and structural integrity. Among the myriad of critical components aboard satellites, aircraft, and unmanned aerial vehicles (UAVs), aerospace payload mounts play an indispensable, albeit often overlooked, role. These structures are the vital interface between the primary vehicle structure and the sensitive, high-value payloads they carry – instruments like high-resolution cameras, sophisticated sensors, communication antennas, scientific experiment packages, and more. The primary function of a payload mount is deceptively simple: to securely hold the payload in its designated position, ensuring stability and precise alignment throughout the mission lifecycle, which includes launch, deployment, and operation. However, achieving this requires navigating a complex web of engineering challenges, including managing vibration, withstanding significant G-forces during maneuvers or launch, accommodating thermal expansion and contraction, and, critically, minimizing mass to optimize fuel efficiency or maximize payload capacity.
Traditionally, manufacturing these intricate and highly stressed components involved subtractive methods, predominantly CNC machining from billet materials like aluminum or titanium alloys, or sometimes investment casting for more complex shapes. While reliable, these methods often impose significant limitations. Machining can result in substantial material waste (high buy-to-fly ratio), restrict geometric complexity (making optimally lightweight designs difficult or impossible to produce), and involve long lead times, especially for low-volume, highly customized parts typical in aerospace. Part consolidation, a key strategy for reducing weight and potential failure points, is often hampered by the constraints of machining accessibility and tooling.
Entrer la fabrication additive métallique (AM)plus connu sous le nom de impression 3D de métaux. This transformative technology is rapidly shifting the paradigm for designing and producing high-performance aerospace components, including payload mounts. Unlike subtractive processes that remove material, AM builds parts layer by layer directly from digital models, typically using high-energy sources like lasers or electron beams to fuse fine metal powders. This fundamental difference unlocks unprecedented design freedom, enabling the creation of highly complex, topology-optimized geometries that were previously unmanufacturable. Engineers can now design payload mounts that precisely follow stress paths, incorporating intricate internal lattice structures or smooth, organic shapes to drastically reduce weight while maintaining or even enhancing structural performance (stiffness and strength). Furthermore, AM facilitates the consolidation of multiple sub-components into a single, monolithic part, eliminating fasteners, reducing assembly time, minimizing potential leak paths or points of failure, and further contributing to weight savings. The ability to rapidly iterate designs and produce functional prototypes or final parts directly from CAD data also significantly shortens development cycles, a crucial advantage in the fast-paced aerospace sector.
Companies at the forefront of this technological shift, such as Met3dp, are playing a pivotal role in enabling the adoption of AM for mission-critical applications. Headquartered in Qingdao, China, Met3dp specializes in providing comprehensive additive manufacturing solutions, encompassing both state-of-the-art Impression 3D equipment (utilizing Selective Electron Beam Melting – SEBM and other Powder Bed Fusion technologies) and the development and production of high-performance metal powders specifically optimized for AM processes. With industry-leading capabilities in print volume, accuracy, and reliability, Met3dp empowers aerospace engineers and procurement managers to leverage the full potential of metal AM for components like payload mounts. Their expertise extends beyond just equipment and materials, offering application development services and leveraging decades of collective experience to help organizations integrate AM effectively and accelerate their digital manufacturing transformations. As we delve deeper into the specifics of 3D printed payload mounts, the advantages offered by this technology, driven by expert providers like Met3dp, will become increasingly apparent. The journey involves understanding the applications, the materials, the design principles, and the entire ecosystem required to produce flight-worthy, high-performance components that redefine what’s possible in aerospace engineering.
Critical Applications: Where are 3D Printed Payload Mounts Deployed?
The adoption of metal additive manufacturing for payload mounts isn’t a theoretical exercise; it’s a practical solution being implemented across a diverse range of demanding aerospace platforms. The unique benefits of AM – lightweighting, complex geometries, part consolidation, and rapid production – make it particularly well-suited for applications where every gram saved and every design optimization translates into significant performance gains or cost savings. The deployment environments for these components are among the most challenging imaginable, pushing materials and structures to their limits.
1. Satellite Platforms (LEO, MEO, GEO, CubeSats): Satellites represent a primary application area for 3D printed payload mounts. Launch costs are directly proportional to mass, making weight reduction paramount.
- Instrumentation Mounting: Securely mounting sensitive optical instruments, spectrometers, radiometers, and earth observation sensors requires extreme stability and precise, maintained alignment, often under conditions of thermal cycling as the satellite moves in and out of sunlight. AM allows for mounts with optimized stiffness-to-weight ratios and potentially integrated thermal management features (e.g., complex conduction paths) designed directly into the structure. Topology optimization ensures material is placed only where structurally necessary, shedding significant mass compared to traditionally machined brackets.
- Antenna Brackets: Communication antennas, ranging from small telemetry/command antennas to large deployable reflectors, need robust mounting structures that can withstand launch vibrations and maintain pointing accuracy. Complex curvatures and integration points often required for antenna feeds and reflectors can be more easily realized with AM, sometimes consolidating multiple brackets into a single printed part. Materials like Ti-6Al-4V offer excellent specific strength and stiffness, ideal for these applications.
- Electronics Housing Integration: Payload mounts can be designed to integrate directly with the housings for payload electronics, providing structural support, thermal pathways, and mounting interfaces in a single component. This consolidation simplifies assembly and reduces the overall parts count.
- CubeSats and Small Satellites: For smaller platforms like CubeSats, where volume and mass are severely constrained, AM enables the creation of highly compact, multifunctional structures. A single printed component might serve as a payload mount, part of the satellite bus structure, and incorporate features for cable routing or thermal straps, maximizing utility within the tiny form factor. Scalmalloy®, with its high strength comparable to titanium but lower density, becomes particularly attractive here.
2. Commercial and Military Aircraft: While perhaps less constrained by mass than satellites, weight reduction in aircraft still translates directly to fuel savings or increased payload/range capability. Reliability and fatigue life are critical concerns.
- Sensor and Pod Mounts: Mounting external sensors, reconnaissance pods, targeting systems, or communication equipment onto the airframe requires structures that can handle aerodynamic loads, vibration from engines and airflow, and potentially high G-forces during maneuvers. AM allows for the creation of aerodynamically efficient, conformal mounts that minimize drag while providing the necessary structural integrity. The ability to use high-strength materials like Ti-6Al-4V ensures durability and fatigue resistance.
- Avionics Racks and Brackets: Inside the aircraft, mounting avionics boxes and equipment within designated bays often involves complex brackets designed to fit into tight spaces. AM enables the production of highly customized, lightweight brackets that conform precisely to the available envelope, potentially consolidating multiple simple brackets into a single, more efficient structure.
- Camera Mounts (Internal/External): Mounting cameras for surveillance, reconnaissance, or flight recording demands stability to ensure clear imagery. AM can produce mounts with optimized damping characteristics or specific geometries to isolate the camera from airframe vibrations.
3. Unmanned Aerial Vehicles (UAVs): UAVs, ranging from small tactical drones to large High-Altitude Long-Endurance (HALE) platforms, are highly sensitive to weight and often carry sophisticated, miniaturized payloads.
- Gimbal System Integration: Mounting multi-axis gimbal systems carrying cameras or sensors requires lightweight yet stiff structures to ensure stability and rapid pointing capabilities. Topology-optimized AM mounts are ideal for minimizing the inertia of the gimbal system while providing robust support.
- Custom Payload Integration: UAVs are often adapted for specific missions with unique payload configurations. AM allows for the rapid design and production of custom mounts tailored to specific sensors, antennas, or equipment packages, facilitating faster platform adaptation and mission readiness. Scalmalloy® is frequently considered due to its excellent strength-to-weight ratio, enabling longer flight times or heavier payload capacity.
- Structural Integration: In smaller UAVs, payload mounts can be designed as integral parts of the airframe itself, further reducing weight and complexity. AM’s ability to create complex, load-bearing structures makes this feasible.
Meeting Environmental Challenges: Across all these applications, 3D printed payload mounts must withstand:
- Vibration: From launch acoustics and rocket engine rumble to aerodynamic buffeting and engine vibrations in aircraft. Mounts must be designed to avoid resonance and potentially incorporate damping features.
- Shock Loads: Pyrotechnic separation events, landing impacts, or sudden maneuvers generate significant shock loads.
- Thermal Extremes: Satellites experience wide temperature swings in orbit, while aircraft components can be subjected to high temperatures near engines or frictional heating at high speeds, as well as cryogenic temperatures at altitude or for specific propulsion systems. Material selection (like Ti-6Al-4V’s excellent thermal stability) and design features accommodating thermal expansion are crucial.
- G-Forces: Launch accelerations, high-G maneuvers in fighter jets, and atmospheric re-entry impose substantial inertial loads.
The ability of metal AM, utilizing advanced materials and design techniques, to create payload mounts capable of meeting these diverse and demanding requirements explains its growing adoption in the aerospace sector. Partnering with experienced providers like Met3dp, who understand both the manufacturing process and the nuances of materials like Scalmalloy® and Ti-6Al-4V, is key to successfully implementing these critical components.
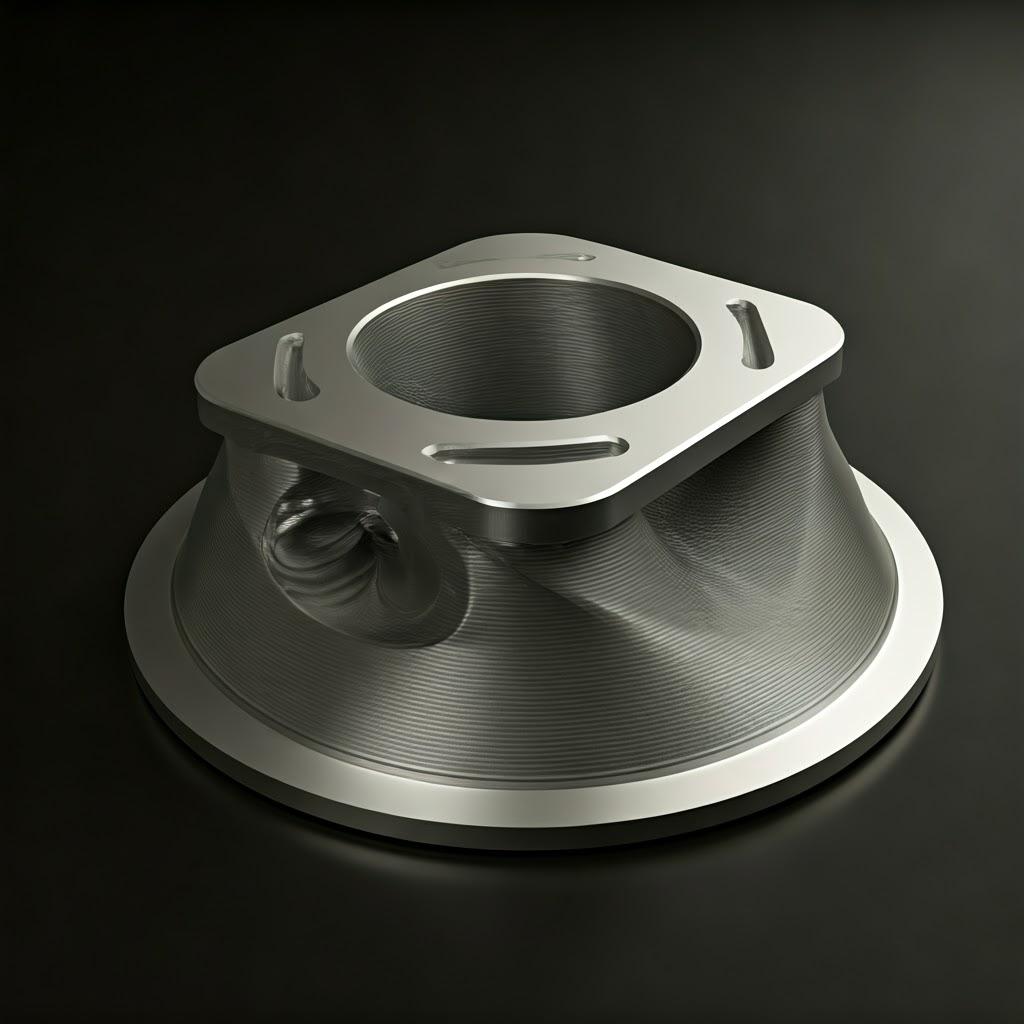
The Additive Advantage: Why Choose Metal 3D Printing for Payload Mounts?
While traditional manufacturing methods like CNC machining and casting have served the aerospace industry well for decades, metal additive manufacturing presents a compelling suite of advantages, particularly for components like payload mounts where performance, weight, and complexity are key drivers. Opting for AM isn’t just about adopting a new technology; it’s about unlocking fundamentally new possibilities in design and production, leading to tangible benefits in performance, cost, and lead time for aerospace procurement managers and engineers.
1. Unprecedented Lightweighting through Design Freedom: This is arguably the most significant advantage of AM for aerospace. Traditional methods are constrained by tool access and the economics of material removal. AM, building layer by layer, liberates designers from these constraints.
- Optimisation de la topologie : Software algorithms can optimize the geometry of a payload mount based on applied loads, boundary conditions, and performance targets (e.g., maximum stiffness, minimum mass). The resulting organic, bone-like structures place material only where it’s needed to carry stress, often yielding weight savings of 30-60% or even more compared to conventionally designed and machined parts, without compromising structural integrity. Producing these complex shapes is often impractical or impossible with CNC machining.
- Structures en treillis : AM enables the integration of internal lattice structures (e.g., honeycombs, gyroids, stochastic foams) within the solid geometry of the mount. These lattices offer exceptional stiffness-to-weight ratios, vibration damping properties, and can facilitate heat dissipation if designed correctly.
- Efficacité matérielle : Unlike subtractive manufacturing, which can waste up to 80-90% of the initial material block (high buy-to-fly ratio), AM is inherently more material-efficient. While some support structures are needed and powder reuse requires management, the overall material consumption is significantly lower, especially for complex parts and expensive materials like titanium alloys or Scalmalloy®.
2. Part Consolidation: Payload mounting systems often consist of multiple individual brackets, fasteners, and interface plates that must be assembled. Each part adds weight, requires manufacturing and inventory management, and introduces potential failure points (e.g., loosening fasteners, stress concentrations at joints).
- Reduced Assembly Time & Cost: AM allows designers to consolidate multiple components into a single, monolithic printed part. A complex mount assembly that previously involved 5, 10, or even 20 distinct pieces can potentially be redesigned and printed as one integrated structure. This drastically reduces assembly labor, simplifies supply chains, and minimizes the need for tooling and fixtures.
- Improved Reliability: Eliminating fasteners and joints removes potential sources of failure due to vibration, fatigue, or improper assembly, leading to a more robust and reliable final component.
- Amélioration des performances : Integrated designs can offer smoother load paths and improved structural efficiency compared to bolted assemblies. Features like fluid channels or integrated heat sinks can also be incorporated directly.
3. Manufacturing Complexity Without Penalty: In traditional manufacturing, complexity directly increases cost and lead time due to intricate machining setups, specialized tooling, or complex casting molds. In AM, complexity is largely “free” once the design is finalized.
- Intricate Geometries: Features like internal cooling channels, hidden voids for weight reduction, conformal shapes that match mating surfaces perfectly, thin walls, and complex curvatures can be produced with relative ease using AM processes like Selective Laser Melting (SLM) or Selective Electron Beam Melting (SEBM) – technologies expertly utilized by providers like Met3dp.
- Personnalisation : AM is ideal for producing highly customized or unique payload mounts, common in satellite manufacturing or for specialized aircraft modifications, without the prohibitive tooling costs associated with traditional methods for low-volume production.
4. Accelerated Development and Prototyping: The aerospace industry demands rigorous testing and validation. AM significantly speeds up the design-build-test cycle.
- Prototypage rapide : Functional prototypes using the final intended metal material can be produced directly from CAD data in days rather than weeks or months. This allows engineers to quickly test and validate designs, perform fit checks, and iterate improvements much faster than traditional prototyping routes.
- Faster Time-to-Flight: By compressing the design and manufacturing phases, AM can shorten the overall lead time for flight-qualified hardware, enabling faster deployment of new satellite capabilities or aircraft upgrades.
5. Metal AM vs. CNC Machining/Casting for Payload Mounts:
Fonctionnalité | Metal AM (e.g., SLM/EBM) | Usinage CNC | Moulage à la cire perdue |
---|---|---|---|
Liberté de conception | Very High (complex geometries, lattices) | Moderate (limited by tool access) | High (but requires tooling) |
Allègement | Excellent (topology optimization feasible) | Limited (difficult complex optimization) | Moderate (near-net shape possible) |
Consolidation partielle | Excellent | Pauvre | Modéré |
Déchets matériels | Low (powder recyclability) | High (high buy-to-fly ratio) | Moderate (gates, risers) |
Lead Time (Proto) | Fast (days/weeks) | Moderate (weeks) | Slow (weeks/months for tooling) |
Lead Time (Prod) | Moderate (depends on build size/quantity) | Fast (for simple parts) / Slow (complex) | Moderate (after tooling is made) |
Coût de l'outillage | Aucun | Low (fixtures) / High (complex jigs) | High (mold/pattern creation) |
Ideal Volume | Low to Medium, High Complexity/Customization | Medium to High, Moderate Complexity | Medium to High, Stable Designs |
Finition de la surface | Moderate (requires post-processing) | Excellent | Good (requires finishing) |
Options de matériaux | Growing (Specific alloys optimized for AM) | Very Wide | Large |
Exporter vers les feuilles
While CNC machining still excels in achieving very high precision and surface finishes on accessible surfaces, and casting can be economical for high-volume production of stable designs, metal AM offers a superior combination of design freedom, lightweighting potential, part consolidation, and speed for complex, low-to-medium volume components like aerospace payload mounts. Leveraging the capabilities of advanced AM systems and high-quality materials from experienced providers is key to realizing these advantages.
Material Focus: Scalmalloy® and Ti-6Al-4V for High-Performance Mounts
The choice of material is paramount in aerospace design, directly impacting the performance, weight, durability, and cost of a component. For 3D printed payload mounts operating in demanding environments, two materials stand out due to their exceptional properties when processed via additive manufacturing: Scalmalloy® (alliage d'aluminium) et Ti-6Al-4V (Grade 5 Titanium). Understanding their characteristics and why they are suitable is crucial for engineers and procurement specialists selecting materials for mission-critical applications. Furthermore, the quality of the raw material – the metal powder – is fundamental to achieving these properties in the final printed part.
1. Scalmalloy® (Al-Mg-Sc Alloy): The High-Performance Aluminum Scalmalloy® is a patented aluminum-magnesium-scandium alloy specifically developed for additive manufacturing. It pushes the boundaries of what’s achievable with aluminum alloys, offering properties that rival some titanium grades but at a significantly lower density.
- Propriétés principales :
- High Specific Strength: This is Scalmalloy®’s defining feature. It boasts a yield strength (( \sigma_y )) typically exceeding 450 MPa and an ultimate tensile strength (( \sigma_{UTS} )) over 500 MPa after appropriate heat treatment, coupled with a low density of approximately 2.67 g/cm³. This results in a specific strength (Strength/Density) significantly higher than traditional high-strength aerospace aluminum alloys (like 7075 or 2024) and comparable to, or even exceeding, that of Ti-6Al-4V in some conditions.
- Excellent Ductility and Toughness: Unlike some very high-strength aluminum alloys which can be brittle, Scalmalloy® maintains good elongation (typically >10%) and fracture toughness, making it resilient to cracking under stress.
- Good Weldability (relevant for AM): Its composition makes it highly suitable for the layer-by-layer fusion process inherent in SLM, resulting in dense, near-net-shape parts.
- Bonne résistance à la corrosion : Offers good resistance to atmospheric corrosion.
- Résistance à la fatigue : Exhibits excellent fatigue life, particularly beneficial for components subjected to cyclic loading, like payload mounts experiencing vibration during launch and operation.
- Microstructure Control: The rapid solidification during AM combined with the scandium addition leads to a very fine-grained microstructure, which is key to its high strength and toughness.
- Why it Matters for Payload Mounts:
- Maximum Weight Savings: Its exceptional specific strength allows for the design of extremely lightweight mounts, directly translating to lower launch costs for satellites or improved fuel efficiency/payload capacity for aircraft and UAVs. It’s often the go-to choice when weight reduction is the absolute primary driver.
- Dynamic Performance: High stiffness-to-weight ratio is advantageous for mounts requiring high natural frequencies to avoid resonance with vehicle vibrations.
- Géométries complexes : Its suitability for AM enables the complex, topology-optimized designs needed to fully leverage its lightweighting potential.
2. Ti-6Al-4V (Grade 5 Titanium): The Aerospace Workhorse Ti-6Al-4V (Titanium alloy with 6% Aluminum and 4% Vanadium) is the most widely used titanium alloy in aerospace, known for its excellent combination of strength, low density, corrosion resistance, and performance at moderately elevated temperatures. It has a long history of successful use in demanding applications.
- Propriétés principales :
- Rapport résistance/poids élevé : While its density (approx. 4.43 g/cm³) is higher than Scalmalloy®, Ti-6Al-4V offers very high strength (( \sigma_y ) typically > 830 MPa, ( \sigma_{UTS} ) > 900 MPa in annealed condition, higher possible with heat treatment). This still results in an excellent specific strength, making it a prime choice for weight-sensitive applications.
- Excellente résistance à la corrosion : Titanium alloys form a stable, passive oxide layer, providing outstanding resistance to corrosion in various environments, including seawater and oxidizing acids – crucial for long-duration space missions or aircraft operating in marine environments.
- Good High-Temperature Performance: Retains significant strength up to temperatures around 300-400°C (approx. 600-750°F), making it suitable for mounts located near engines or experiencing aerodynamic heating.
- Biocompatibilité : While not typically relevant for payload mounts, its biocompatibility highlights its inertness.
- Résistance à la fatigue : Offers good fatigue resistance, essential for components experiencing vibrational loads.
- Established AM Processing: Extensive research and parameter development have been done for processing Ti-6Al-4V via SLM and EBM, leading to well-understood material properties and process controls.
- Why it Matters for Payload Mounts:
- Proven Reliability: Its long track record in aerospace inspires confidence for critical applications.
- Higher Temperature Capability: Preferred over aluminum alloys like Scalmalloy® if the mount operates at elevated temperatures.
- Résistance supérieure à la corrosion : Ideal for missions with very long durations or exposure to corrosive environments.
- Balance of Properties: Offers a robust combination of strength, stiffness, toughness, and environmental resistance suitable for a wide range of payload mounting scenarios.
Material Comparison Summary:
Propriété | Scalmalloy® (alliage d'aluminium) | Ti-6Al-4V (Niveau 5) | Typical Use Case Driver |
---|---|---|---|
Densité | ~2.67 g/cm³ | ~4,43 g/cm³ | Lower Density (Scalmalloy®) |
Limite d'élasticité | > 450 MPa (Heat Treated) | > 830 MPa (Annealed) | Higher Absolute Strength (Ti-6Al-4V) |
Force spécifique | Très élevé | Haut | Max Weight Saving (Scalmalloy®) |
Max Temp Capability | Lower (Generally < 150-200°C) | Higher (~300-400°C) | High Temperature Needs (Ti-6Al-4V) |
Résistance à la corrosion | Bon | Excellent | Harsh Environments (Ti-6Al-4V) |
AM Maturity | High (Specifically designed for AM) | Very High (Extensively studied) | Both well-established |
Coût | High (Scandium content) | High (Titanium base) | Application specific trade-off |
Exporter vers les feuilles
The Importance of High-Quality Metal Powders: Achieving the theoretical properties of Scalmalloy® and Ti-6Al-4V in a 3D printed part fundamentally depends on the quality of the metal powder used as feedstock. Factors like:
- Sphéricité : Highly spherical powder particles ensure good flowability within the AM machine’s recoating system, leading to uniform powder layers and reducing the risk of voids or defects in the final part.
- Distribution de la taille des particules (PSD) : A controlled PSD is crucial for achieving high packing density in the powder bed, contributing to fully dense parts and predictable melting behavior.
- Purity and Chemistry: Strict control over the alloy composition and minimizing impurities (like Oxygen and Nitrogen, especially critical for Titanium) is essential for obtaining the desired mechanical properties and corrosion resistance. Satellite levels must be precisely managed.
- Absence of Satellites: Small, irregular particles attached to larger spherical ones (satellites) can negatively impact flowability and packing density.
Met3dp’s Commitment to Powder Excellence: Recognizing this critical link, Met3dp employs industry-leading powder production technologies, including advanced Atomisation des gaz et Procédé d'électrodes rotatives à plasma (PREP) systems. Their gas atomization equipment utilizes unique nozzle and gas flow designs optimized to produce metallic powders with the high sphericity, controlled PSD, and excellent flowability required for demanding AM applications. This focus ensures that the Scalmalloy®, Ti-6Al-4V, and other innovative alloy powders (like TiNi, TiTa, TiAl, TiNbZr, CoCrMo, stainless steels, superalloys) offered by Met3dp provide a reliable foundation for printing dense, high-quality payload mounts with superior, consistent mechanical properties. Their comprehensive approach, spanning from poudres métalliques avancées to high-performance SEBM printers and application support, makes them a valuable partner for aerospace companies seeking to leverage the full potential of these advanced materials. Choosing the right material is only half the battle; ensuring it’s sourced from a supplier committed to powder quality, like Met3dp, is equally vital for mission success.
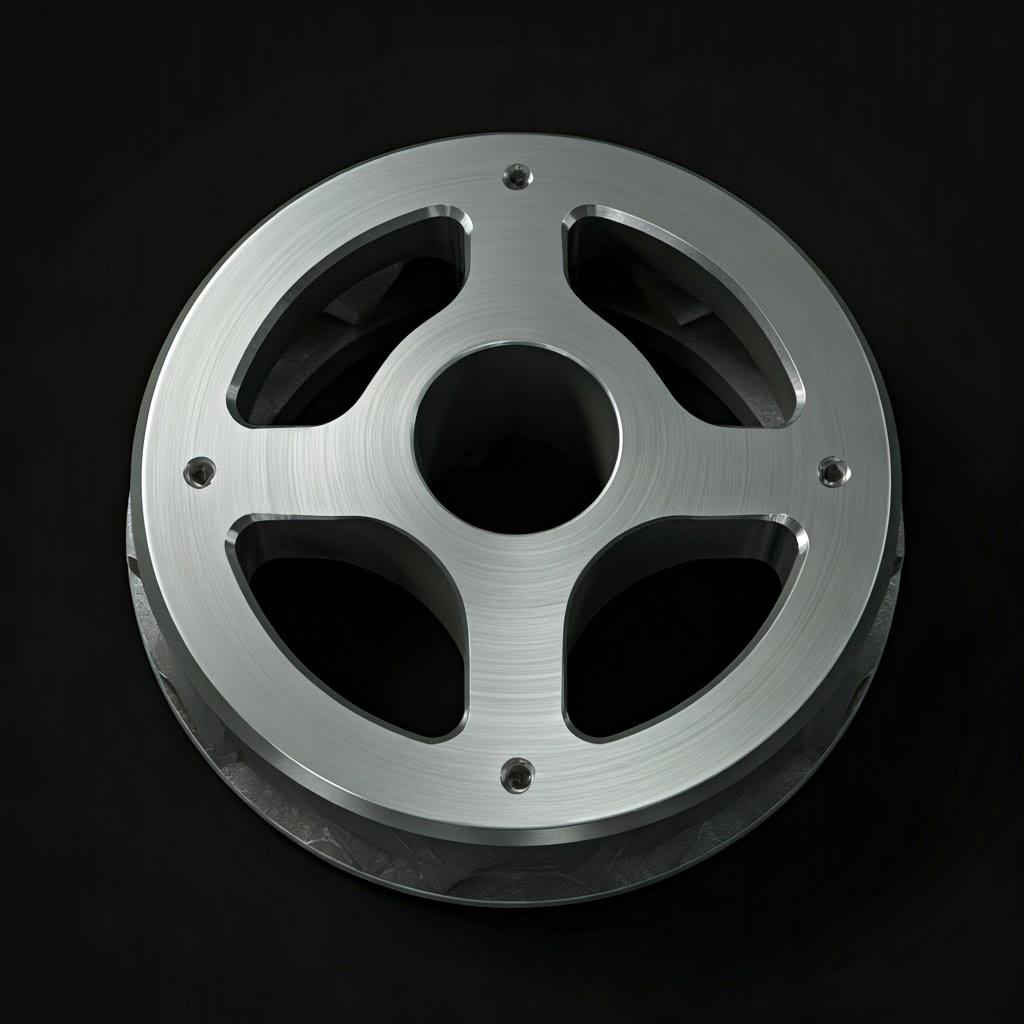
Design for Additive Manufacturing (DfAM): Optimizing Payload Mount Geometry
Moving from the why à la how, designing a payload mount specifically for metal additive manufacturing requires a shift in thinking compared to traditional design-for-machining or casting approaches. Design for Additive Manufacturing (DfAM) is not merely about making existing designs printable; it’s about leveraging the unique capabilities of AM processes like Selective Laser Melting (SLM) or Selective Electron Beam Melting (SEBM) to create components that are fundamentally better – lighter, stronger, more functional, and potentially integrating multiple functions. For aerospace payload mounts, where performance and weight are critical, mastering DfAM principles is essential for unlocking the full potential of materials like Scalmalloy® and Ti-6Al-4V. This involves a detailed consideration of topology optimization, lattice structures, support minimization, feature limitations, and process-specific constraints.
1. Topology Optimization: Designing by Load Path This is perhaps the most powerful DfAM tool for lightweighting aerospace components. Instead of starting with a block of material and carving it away, topology optimization algorithms start with a defined design space (the maximum allowable volume for the mount), apply realistic load cases (e.g., static loads, vibrational loads, thermal loads), define constraints (e.g., fixed mounting points, keep-out zones for payload interfaces), and then iteratively remove material from areas that do not contribute significantly to the structural integrity.
- Workflow: Typically involves Finite Element Analysis (FEA) integrated with optimization software. The engineer defines the problem, the software generates an optimized material layout (often organic and complex), and the engineer then interprets this result, smoothing geometries and making them manufacturable within AM constraints.
- Benefits for Payload Mounts: Leads to highly efficient structures that follow the natural stress paths. This results in significant weight reduction (often 30-60%+) compared to conventional designs, while meeting or exceeding stiffness and strength requirements. The resulting organic shapes are often impossible or prohibitively expensive to produce via machining.
- Considérations : Requires accurate load case definition. The raw output often needs refinement for manufacturability (e.g., ensuring minimum wall thicknesses, smoothing sharp corners to reduce stress concentrations). Vibration analysis (modal analysis) should also be performed on the optimized design to ensure natural frequencies are acceptable.
2. Lattice Structures: Lightweighting and Multifunctionality AM enables the seamless integration of lattice structures – repeating unit cells – within the solid volume of a part. These are not just for show; they offer significant engineering benefits for payload mounts.
- Les types:
- Strut-based lattices: Simple, well-understood (e.g., cubic, octet-truss). Good for stiffness and strength.
- Surface-based lattices (TPMS): Triply Periodic Minimal Surfaces (e.g., Gyroid, Schwarz Diamond). Offer smooth transitions, potentially better stress distribution, and good properties for heat exchange or vibration damping.
- Avantages :
- Further Weight Reduction: Replacing solid internal volumes with lattices drastically reduces mass while maintaining significant structural support and stiffness.
- Vibration Damping: Certain lattice types and configurations can be designed to absorb or damp vibrations, potentially protecting sensitive payloads more effectively.
- Tailored Stiffness: The density and type of lattice can be varied throughout the part to achieve specific stiffness characteristics in different directions.
- Heat Management: Open-cell lattices can facilitate airflow or allow for integrated heat pipes/channels for thermal management of payload electronics.
- Considérations relatives à la conception : Requires specialized software for generation and simulation. Ensuring manufacturability (minimum strut diameter, avoiding trapped powder in closed cells) is crucial. Analyzing the fatigue performance of lattice structures is an active area of research and requires careful consideration.
3. Designing for Minimum Support Structures Metal AM processes typically require support structures for overhanging features and to anchor the part to the build plate, managing thermal stresses. These supports consume material, add print time, require removal in post-processing (which can be labor-intensive and affect surface finish), and can limit design freedom if not considered carefully.
- Angles autoportants : Design features with overhang angles greater than a critical threshold (typically 40-45° from the horizontal, process dependent) to minimize the need for supports. Shallow angles require support.
- Feature Orientation: Orient the part on the build platform strategically to minimize the total area requiring support. This often involves trade-offs with other factors like surface finish on critical faces or build time.
- Designing-Out Supports:
- Use chamfers or fillets instead of sharp horizontal overhangs.
- Employ “tear-drop” or diamond shapes for horizontal holes, making them self-supporting.
- Split complex parts into sub-components that are easier to print without extensive internal supports, though this negates some part consolidation benefits.
- Access for Removal: If supports are unavoidable (especially internal ones), ensure there is clear line-of-sight or access ports designed into the part to facilitate their removal via manual tools, machining, or chemical etching. Trapped powder within internal cavities also needs escape routes.
4. Adhering to Process-Specific Feature Limitations Every AM process and machine has limitations on the minimum feature sizes it can reliably produce. Designing below these thresholds can lead to print failures or parts that don’t meet dimensional specifications.
- Épaisseur minimale de la paroi : Typically around 0.4 – 1.0 mm, depending on the material, wall height, and process (SLM often finer than EBM). Thin walls are prone to warping and may not resolve accurately.
- Minimum Hole Diameter: Small holes (typically < 0.5 – 1.0 mm) may seal over during printing or be difficult to clear of powder. Consider drilling small, critical holes post-print.
- Minimum Pin/Strut Diameter: Fine pins or lattice struts have minimum printable diameters (similar range to wall thickness).
- Maximum Unsupported Span: Horizontal bridges or spans require support if they exceed a certain length (process/material dependent, often a few millimeters).
- Aspect Ratio: Very tall, thin features can be prone to distortion or failure during the build.
- Comprendre Méthodes d'impression: Knowing the specifics of the chosen AM process (e.g., SLM vs. EBM used by providers like Met3dp) is crucial, as laser-based systems (SLM) often offer finer feature resolution but potentially higher residual stress than electron beam systems (EBM), which operate at higher temperatures.
5. Managing Anisotropy Due to the layer-by-layer build process and directional heat flow, AM metal parts often exhibit anisotropic mechanical properties, meaning their strength, stiffness, and fatigue life can vary depending on the direction relative to the build layers (X, Y vs. Z).
- Design Implications: Critical load paths should ideally be aligned with the direction of optimal material properties (often parallel to the build plate, X-Y plane). Avoid orienting primary tensile loads perpendicular to the layers (Z-direction) if possible, as this is often the weakest orientation.
- Simulation and Testing: FEA models should ideally account for anisotropic material properties if high fidelity is required. Coupon testing in different orientations (X, Y, Z) is essential during process qualification to characterize these directional differences.
6. Designing for Post-Processing Consider how the part will be handled, finished, and inspected after printing.
- Tolérances d'usinage : Add extra stock material (e.g., 0.5 – 2.0 mm) to surfaces that require high precision or specific finishes achieved via post-machining.
- Fixturing Points: Incorporate features that aid in holding the part securely during post-machining or inspection (e.g., temporary lugs, flat reference surfaces).
- Accès à l'inspection : Ensure critical features are accessible for measurement tools (CMM probes, scanners) and NDT methods (e.g., CT scanning lines-of-sight are not blocked).
Mastering DfAM for payload mounts requires a collaborative approach between design engineers, manufacturing engineers, and AM service providers like Met3dp, who possess deep knowledge of their machine capabilities, material behaviors, and post-processing requirements. By embracing these principles, aerospace companies can create truly optimized components that push the performance envelope.
Achieving Precision: Tolerance, Surface Finish, and Dimensional Accuracy in AM Mounts
While metal additive manufacturing unlocks incredible design freedom, it’s crucial for engineers and procurement managers to have realistic expectations regarding the achievable precision directly from the printer. Aerospace applications, particularly payload mounts with critical interfaces, demand tight control over dimensions, tolerances, and surface characteristics. Understanding the typical as-built quality of AM parts made from Scalmalloy® or Ti-6Al-4V, the factors influencing it, and the common necessity for post-machining is vital for successful implementation.
1. As-Built Tolerances: The dimensional accuracy achievable directly from metal powder bed fusion processes (SLM, EBM) is influenced by numerous factors, including machine calibration, laser/electron beam spot size, layer thickness, powder characteristics, thermal management, and part geometry/size.
- General Ranges: Typical achievable tolerances for well-controlled processes often fall within the range of ±0,1 mm à ±0,3 mm for smaller dimensions (e.g., up to 100 mm), or ±0.1% to ±0.2% of the nominal dimension for larger parts. Some high-end systems might achieve slightly better results under optimal conditions.
- Met3dp’s Capabilities: Utilizing industry-leading printers known for accuracy and reliability, Met3dp strives to deliver parts within tight as-built tolerances, providing a better starting point for any necessary finishing operations. However, the inherent physics of layer-wise melting and solidification imposes limits.
- Factors Influencing Tolerance:
- Effets thermiques : Residual stresses built up during the print can cause warping or distortion, particularly in large or complex parts.
- Shrinkage: Metal alloys shrink upon solidification and cooling; predicting and compensating for this is complex.
- Structures de soutien : Where supports touch the part, they can leave witness marks or affect local accuracy after removal.
- Part Orientation: The orientation on the build plate can affect dimensional stability and accuracy due to varying thermal conditions and support needs.
2. As-Built Surface Finish (Roughness): The surface finish of as-built AM parts is inherently rougher than that achieved by machining or polishing. This roughness stems from the partially melted powder particles adhering to the surface and the layer-wise construction (stair-stepping effect).
- Typical Values: As-built surface roughness (Ra) for SLM/EBM parts typically ranges from 5 µm to 25 µm (micrometers). EBM processes, often using thicker layers and higher energy, tend to produce rougher surfaces than SLM. Scalmalloy® and Ti-6Al-4V generally fall within this range.
- Stair-Stepping Effect: Angled or curved surfaces exhibit a characteristic “stair-step” texture due to the discrete layers. The severity depends on the layer thickness and the angle of the surface relative to the build direction (surfaces nearly parallel to the build plate are roughest, vertical walls are generally smoother).
- Factors Influencing Roughness:
- Épaisseur de la couche : Thinner layers generally produce smoother surfaces but increase build time.
- Powder Particle Size: Finer powders can lead to smoother finishes.
- Paramètres du processus : Laser/beam power, scan speed, and hatch strategy significantly impact melt pool dynamics and surface texture.
- Orientation: Vertical walls tend to be smoother than top-facing or angled surfaces. Downward-facing surfaces where supports were attached are often the roughest after support removal.
3. The Need for Post-Machining: For many critical features on aerospace payload mounts, the as-built tolerances and surface finish are insufficient to meet stringent engineering requirements. Post-machining is therefore often a planned and essential step.
- Critical Interfaces: Mounting points, mating surfaces connecting to the payload or vehicle structure, bearing or bushing bores, and fastener holes typically require tolerances much tighter than ±0.1 mm (often in the ±0.01 to ±0.05 mm range) and smoother surface finishes (Ra < 1.6 µm or even lower) to ensure proper load transfer, alignment, sealing, or fatigue life.
- Achieving Precision: CNC machining (milling, turning, grinding) is used to bring these specific features into final tolerance and achieve the desired surface finish. Sufficient machining stock must be included in the AM part design on these critical surfaces.
- Fabrication hybride : Some approaches involve printing near-net-shape parts and then using multi-axis CNC machines for finishing, combining the design freedom of AM with the precision of subtractive methods.
- Cost/Time Implication: Incorporating post-machining adds cost and lead time to the overall process but is often non-negotiable for achieving the required quality for aerospace components.
4. Dimensional Verification and Quality Control: Ensuring that the final payload mount meets all dimensional and surface specifications requires rigorous inspection.
- Machines à mesurer tridimensionnelles (MMT) : Used for high-accuracy dimensional verification of critical features after printing and post-machining.
- 3D Scanning: Optical or laser scanners capture the overall geometry of the part, allowing comparison to the original CAD model to assess overall form and identify deviations or warping.
- Surface Profilometry: Measures surface roughness (Ra, Rz, etc.) on critical surfaces to verify compliance with specifications.
In summary, while metal AM provides the geometric complexity needed for optimized payload mounts, achieving the final precision demanded by aerospace standards typically requires a combination of a high-quality AM process (utilizing accurate machines like those at Met3dp and quality powders) and targeted post-machining operations for critical features. Understanding these requirements early in the design phase is crucial for effective planning and costing.
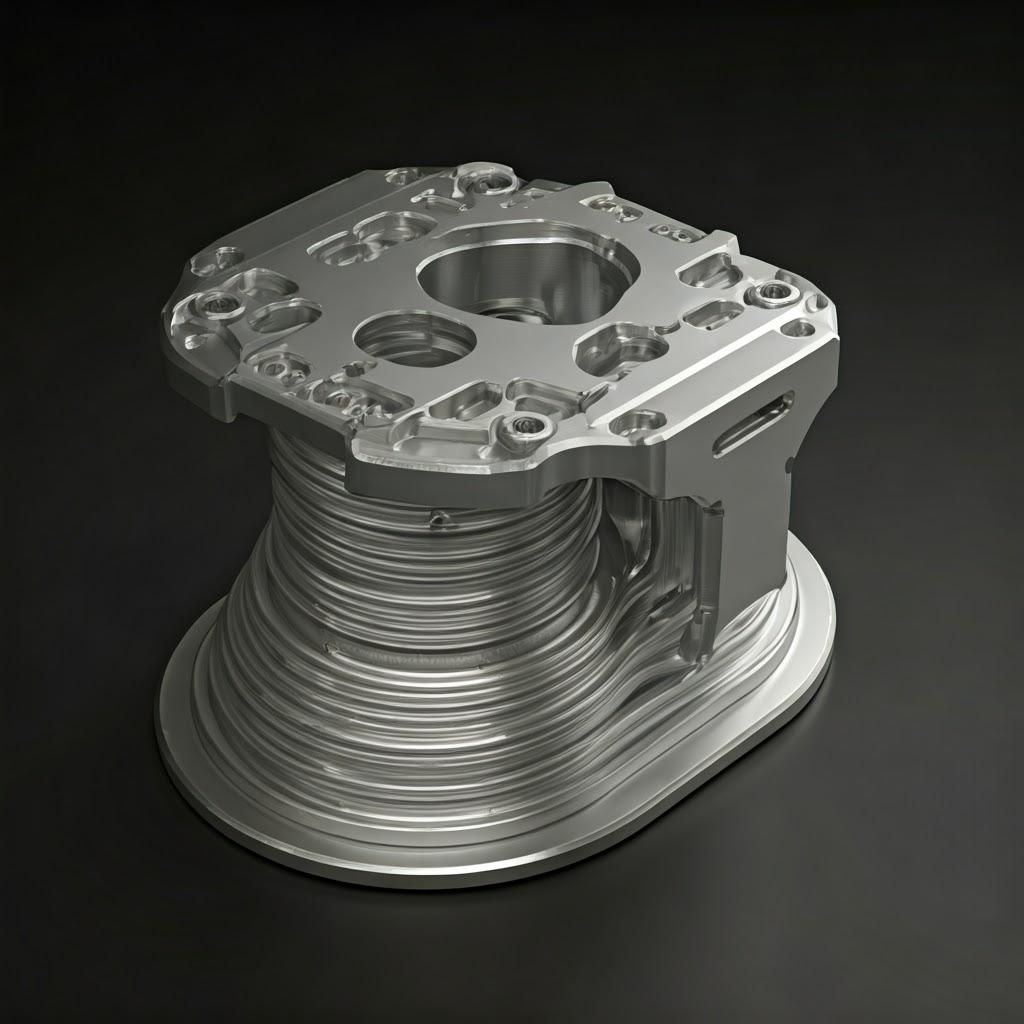
Beyond the Print: Essential Post-Processing for Aerospace Payload Mounts
Producing a dimensionally accurate payload mount via metal additive manufacturing is only the first major step. The “as-built” part, fresh off the printer, requires a series of crucial post-processing steps to transform it into a flight-worthy component that meets the stringent demands of aerospace applications. These steps are essential for relieving internal stresses, achieving the desired material properties (strength, ductility, fatigue life), removing support structures, attaining the required surface finish and tolerances on critical interfaces, and ensuring internal quality. For materials like Scalmalloy® and Ti-6Al-4V, specific thermal treatments are particularly vital.
1. Stress Relief: The rapid heating and cooling cycles inherent in powder bed fusion create significant residual stresses within the printed part. These stresses can cause warping or distortion upon removal from the build plate and can negatively impact the part’s mechanical performance and fatigue life.
- Processus : Typically the first step after printing, often performed while the part is still attached to the build plate. Involves heating the part in a controlled atmosphere (vacuum or inert gas like Argon) furnace to a specific temperature below the material’s transformation or aging temperature, holding it for a defined period, and then slowly cooling it.
- Parameters (Examples):
- Ti-6Al-4V : Common cycles involve heating to 595°C – 800°C (1100°F – 1470°F) for 1-4 hours, followed by furnace cooling or air cooling, depending on the specific goal (stress relief vs. annealing).
- Scalmalloy®: Stress relief parameters are specific to the alloy, often at lower temperatures than titanium, typically around 300-325°C.
- Importance: Critical for dimensional stability during subsequent steps (like removal from build plate and machining) and for improving fatigue performance.
2. Heat Treatment (Solutionizing, Aging): Beyond stress relief, specific heat treatments are often required to achieve the optimal microstructure and mechanical properties (strength, ductility, hardness) for the chosen alloy.
- Ti-6Al-4V :
- Annealing: Often performed concurrently with stress relief, refining the microstructure for improved ductility and toughness.
- Solution Treatment and Aging (STA): A multi-step process to significantly increase strength. Involves heating to a high temperature (solutionizing, e.g., 900-950°C), rapidly cooling (quenching), and then reheating to a lower temperature (aging, e.g., 500-600°C) for several hours. STA parameters are carefully selected to achieve specific strength/ductility targets (higher strength often means lower ductility).
- Scalmalloy®: Requires a specific aging treatment (precipitation hardening) after printing and stress relief to develop its characteristic ultra-high strength. This typically involves heating to around 325-375°C for several hours. The exact cycle is crucial for achieving peak properties.
- Atmosphere Control: These treatments must be performed in vacuum or inert atmospheres to prevent oxidation, especially critical for titanium at high temperatures.
3. Hot Isostatic Pressing (HIP): HIP is a process that subjects parts to high temperature and high isostatic pressure (using an inert gas like Argon) simultaneously.
- Objet : Primarily used to close internal voids or porosity (like gas porosity or lack-of-fusion defects) that may be present after printing. This increases the part’s density closer to 100% theoretical density.
- Avantages : Significantly improves fatigue life, ductility, and fracture toughness, which are critical for aerospace components subjected to cyclic loading and potential impacts. Reduces variability in mechanical properties.
- Processus : Temperatures and pressures are specific to the alloy (e.g., for Ti-6Al-4V, often around 900-950°C and 100-150 MPa). HIP cycles can sometimes be combined with heat treatment steps.
- When Used: Often specified for critical rotating parts or components where fatigue is a primary design driver. Increasingly common for flight-critical AM aerospace parts, including payload mounts.
4. Part Removal and Support Structure Removal: Once heat treatments are complete (or sometimes before, depending on the workflow), the part needs to be separated from the build plate and support structures must be removed.
- Build Plate Removal: Typically done using wire EDM (Electrical Discharge Machining), sawing, or machining.
- Suppression du support : Can be challenging, especially for complex internal geometries. Methods include:
- Suppression manuelle : Breaking or cutting away accessible supports using hand tools (pliers, grinders). Labor-intensive and can damage the part surface if not done carefully.
- Usinage : Milling or grinding away support structures.
- Wire EDM: Precise removal, useful for intricate supports or hard-to-reach areas.
- Chemical Etching: Less common for structural supports but sometimes used for specific materials or surface finishing.
- Surface Impact: Support contact points leave witness marks or rougher areas that usually require further finishing.
5. Surface Finishing: As-built AM surfaces are typically too rough for many aerospace applications, especially mating surfaces or areas prone to fatigue initiation.
- Basic Finishing: Abrasive blasting (bead blasting, sand blasting) provides a uniform matte finish and removes loose powder, but doesn’t significantly improve dimensional tolerance.
- Improved Finishes:
- Tumbling/Mass Finishing: Vibratory finishing or tumbling with media can smooth surfaces and deburr edges, effective for batches of smaller parts.
- Polissage : Manual or automated polishing for achieving very smooth, mirror-like finishes on specific areas.
- Chemical Milling/Etching: Controlled removal of material using chemical baths to improve surface finish or achieve thin walls.
- Électropolissage : Electrochemical process that preferentially removes peaks, resulting in a very smooth and clean surface, often used for improving corrosion resistance or fatigue life.
6. Final Machining: As discussed previously, CNC machining is often required to achieve the final tolerances and surface finish specifications on critical features (mounting holes, interface planes, etc.).
7. Inspection and Quality Assurance: Throughout the post-processing chain, inspection is critical.
- Essais non destructifs (END) :
- Tomodensitométrie (CT) : Essential for detecting internal defects like porosity or inclusions within complex AM parts.
- Contrôle par ressuage fluorescent (FPI) : Used to detect surface-breaking cracks.
- Contrôle par ultrasons (UT) : Can detect internal flaws, though complex geometries can be challenging.
- Inspection dimensionnelle : CMM and 3D scanning verify final dimensions after all processing steps.
- Test des matériaux : Destructive testing of representative samples or witness coupons processed alongside the main part verifies mechanical properties (tensile strength, yield strength, elongation, fatigue life).
Successfully navigating this complex sequence of post-processing steps requires significant expertise, specialized equipment (vacuum furnaces, HIP units, multi-axis CNC machines, NDT systems), and robust process control. Companies like Met3dp, offering comprehensive solutions that consider the entire workflow from powder to finished part, including necessary post-processing partnerships or capabilities, are vital for ensuring that 3D printed payload mounts meet the uncompromising standards of the aerospace industry. Understanding these steps helps procurement managers and engineers accurately scope the time, cost, and technical requirements involved.
Navigating Challenges: Overcoming Hurdles in 3D Printing Payload Mounts
While the advantages of metal additive manufacturing for aerospace payload mounts are compelling, the technology is not without its challenges. Successfully implementing AM for critical flight hardware requires acknowledging potential hurdles and proactively employing strategies to mitigate them. Engineers and procurement managers should be aware of common issues related to residual stress, support structures, porosity, anisotropy, and the overarching challenge of part qualification. Overcoming these requires careful design, rigorous process control, thorough inspection, and collaboration with experienced AM providers.
1. Residual Stress Management: The intense, localized heating and rapid cooling inherent in powder bed fusion processes generate significant thermal gradients, leading to the buildup of internal residual stresses within the part and at the interface with the build plate.
- Consequences:
- Warping/Distortion: Stresses can cause the part to deform during the build, after removal from the build plate, or during post-processing (especially machining).
- Cracking: High tensile stresses can lead to cracks initiating during the build or later in the part’s lifecycle.
- Reduced Performance: Residual stresses can negatively impact fatigue life and dimensional accuracy.
- Mitigation Strategies:
- Stratégies d'analyse optimisées : Using techniques like island scanning, sectoring, or optimized vector patterns helps distribute heat more evenly and reduce peak stresses.
- Build Plate Heating: Preheating the build plate (common in EBM, also used in some SLM systems) reduces thermal gradients.
- Structures de soutien : Well-designed supports help anchor the part and manage stress accumulation during the build.
- Simulation thermique : FEA-based process simulation can predict stress distribution and identify potential problem areas, allowing for design or process adjustments before printing.
- Post-Print Stress Relief: Performing a proper stress relief heat treatment cycle immediately after printing is crucial for reducing internal stresses before further processing.
2. Support Structure Challenges: Supports are often a necessary evil in metal AM, but they bring their own set of difficulties.
- Removal Difficulty: Removing supports, especially dense or internal ones within complex geometries (common in optimized payload mounts), can be extremely difficult, time-consuming, and costly. Incomplete removal can compromise functionality or lead to stress concentrations.
- Atténuation : Prioritize DfAM principles to minimize supports (self-supporting angles, optimized orientation). Design for access – include ports or channels specifically for support removal tools or flushing. Consider dissolvable or chemically removable support materials where available (less common for structural metals).
- Surface Finish Impact: Support contact points leave rough surfaces (“witness marks”) that require significant finishing work if aesthetics or specific surface properties are needed in those areas.
- Atténuation : Use support types and parameter settings that minimize the contact area and are easier to remove cleanly. Plan for post-processing (machining, grinding, polishing) in supported areas if finish is critical.
- Trapped Powder: Complex internal channels or cavities, even if self-supporting, can trap unfused powder that is difficult or impossible to remove completely.
- Atténuation : Design drainage holes or access ports for powder removal. Utilize process simulation to predict powder trapping. Thorough post-print cleaning and inspection (e.g., CT scanning) are essential.
3. Porosity Control: Achieving full density (>99.9%) is critical for the mechanical integrity, particularly fatigue life, of aerospace components. Porosity (internal voids) can arise from several sources.
- Types and Causes:
- Porosité de manque de fusion : Insufficient energy input or improper overlap between scan tracks leaves unmelted powder particles between layers or tracks. Often irregular in shape.
- Porosité du trou de serrure : Excessive energy density creates instability in the melt pool, vaporizing metal and trapping gas bubbles upon solidification. Typically spherical.
- Porosité du gaz : Gas dissolved in the powder (e.g., Argon used in atomization or processing) comes out of solution during melting and gets trapped. Often spherical.
- Consequences: Acts as stress concentrators, significantly reducing ductility, fracture toughness, and especially fatigue life.
- Atténuation :
- Paramètres de processus optimisés : Developing robust parameter sets (laser/beam power, scan speed, layer thickness, hatch spacing) specific to the material and machine is critical.
- Poudre de haute qualité : Using powder with controlled chemistry, low trapped gas content, good sphericity, and appropriate PSD minimizes powder-related defects. Sourcing reliable poudres métalliques from qualified suppliers like Met3dp is essential.
- Surveillance des processus : In-situ monitoring systems can help detect anomalies during the build.
- Pressage isostatique à chaud (HIP) : Highly effective at closing internal pores and achieving near-full density. Often mandated for critical aerospace parts.
4. Anisotropy Management: As mentioned in DfAM, the directional nature of the build process leads to anisotropic material properties.
- Défi: Mechanical properties (strength, stiffness, fatigue) can vary significantly depending on the loading direction relative to the build layers. This must be accounted for in design and analysis.
- Atténuation :
- Strategic Orientation: Orient the part on the build plate so that critical stresses align with the strongest material direction (usually parallel to the build plane).
- Caractérisation : Thorough material testing (tensile, fatigue) on coupons built in different orientations (X, Y, Z) is essential to quantify anisotropy for the specific material, machine, and parameter set.
- Design Allowables: Use design allowables that account for the properties in the weakest expected orientation relevant to the loading conditions.
- Traitement thermique : Appropriate heat treatments can help homogenize the microstructure to some extent, reducing (but typically not eliminating) anisotropy.
5. Part Qualification and Certification: This is often the most significant hurdle for adopting AM parts in flight-critical aerospace applications. Demonstrating that an AM part is equivalent or superior to its traditionally manufactured counterpart requires a rigorous and well-documented process.
- Défis : Establishing process consistency, ensuring material traceability, developing standardized testing protocols, non-destructive evaluation of complex internal geometries, and gaining acceptance from certification authorities (FAA, EASA, NASA, etc.).
- Approach: Requires a robust Quality Management System (QMS), often certified to aerospace standards like AS9100. Involves:
- Process Locking: Defining and strictly controlling all process parameters (machine settings, powder specs, post-processing steps).
- Material Control: Rigorous testing and traceability of incoming powder batches.
- Extensive Testing: Coupon-level testing (tensile, fatigue, fracture toughness) and full part-level testing (static, dynamic, environmental) to validate performance.
- Non-Destructive Inspection (NDI): Utilizing advanced NDI like CT scanning to ensure internal integrity.
- Documentation : Comprehensive records of every step from design to final inspection.
- Partnering for Success: Working with an experienced AM service provider like Met3dp, which understands the intricacies of aerospace qualification, has robust quality systems, and provides comprehensive solutions including material expertise and process control, is invaluable in navigating this complex landscape.
By understanding these challenges and proactively implementing mitigation strategies throughout the design, manufacturing, and post-processing phases, the aerospace industry can confidently leverage the transformative potential of metal AM for high-performance payload mounts and other critical components.
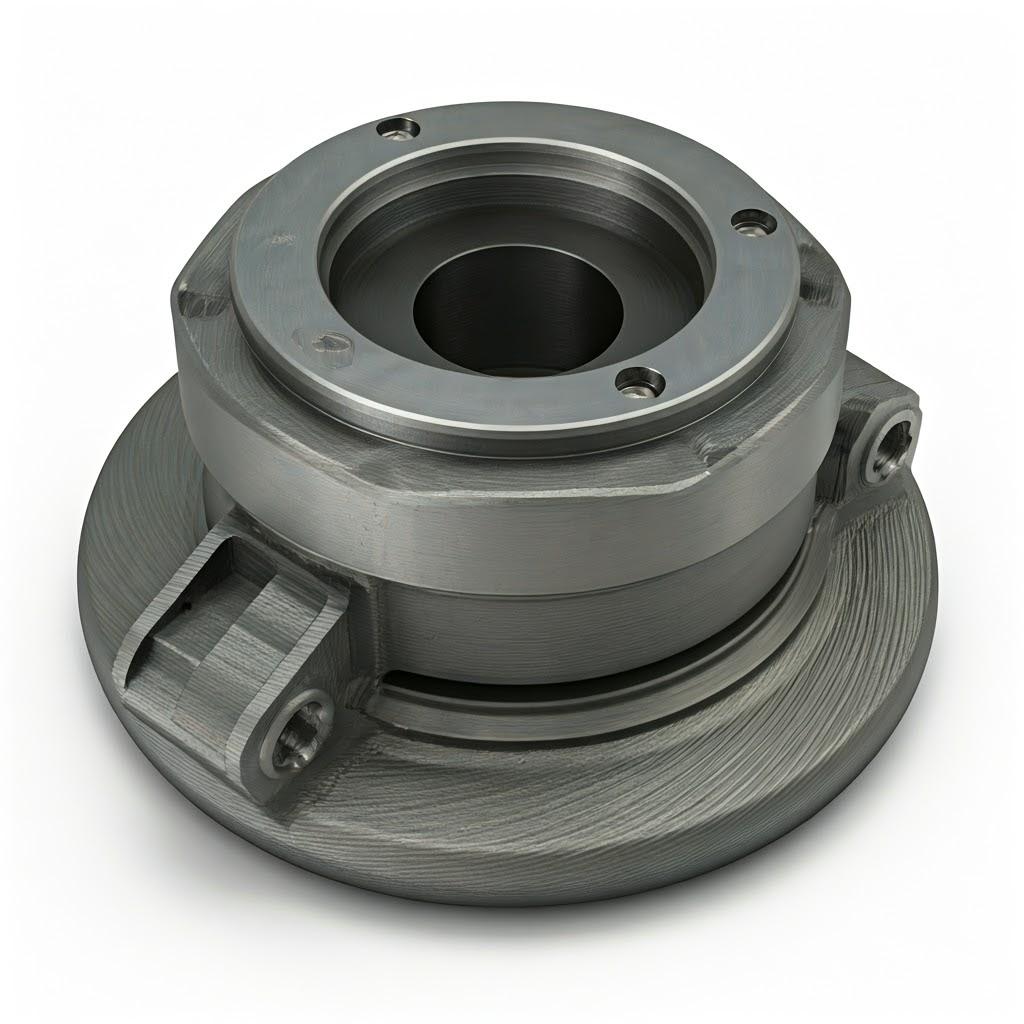
Sélection des fournisseurs : Choisir le bon partenaire pour l'AM des métaux pour les composants aérospatiaux
The decision to utilize metal additive manufacturing for critical components like aerospace payload mounts is only the beginning. Selecting the right manufacturing partner is paramount to ensuring the quality, reliability, and performance required for flight hardware. The stakes are incredibly high in aerospace, and not all AM service providers possess the necessary expertise, equipment, process controls, and quality systems to meet these demands. Procurement managers, engineers, and supply chain professionals must conduct thorough due diligence, evaluating potential suppliers against a stringent set of criteria specifically tailored for aerospace applications. Choosing an inadequate supplier can lead to project delays, cost overruns, subpar component quality, and potentially catastrophic failures.
Critères clés pour l'évaluation des fournisseurs d'AM pour l'aérospatiale :
- Certifications et conformité aérospatiales : This is often a non-negotiable starting point.
- Certification AS9100 : This standard specifies the Quality Management System (QMS) requirements for organizations designing, developing, or producing aviation, space, and defense products. Certification to AS9100 indicates a supplier’s commitment to rigorous process control, traceability, risk management, and continuous improvement aligned with aerospace industry expectations. Lack of AS9100 is often a disqualifier for flight-critical hardware.
- NADCAP Accreditation: The National Aerospace and Defense Contractors Accreditation Program provides specialized accreditation for specific processes. While AM itself is still evolving within NADCAP, accreditations for related crucial post-processing steps like Heat Treating, Non-Destructive Testing (NDT), and Welding (which shares some metallurgical principles with AM fusion) demonstrate a high level of process control and competence recognized industry-wide.
- Conformité ITAR/EAR : For defense-related projects or components subject to U.S. export controls, suppliers must demonstrate compliance with International Traffic in Arms Regulations (ITAR) or Export Administration Regulations (EAR) to handle sensitive technical data and hardware.
- Demonstrated Experience and Expertise: Theoretical knowledge isn’t enough; practical experience is vital.
- Material Specificity: Proven experience successfully printing and post-processing the specific materials required – in this case, Scalmalloy® and Ti-6Al-4V. Ask for evidence of successful projects, material property data generated from their processes, and understanding of the nuances of each alloy in AM.
- Application Relevance: Experience producing components with similar complexity, size, and criticality to aerospace payload mounts is highly desirable. Have they produced flight-qualified hardware previously? Can they share (non-proprietary) case studies or examples?
- Technical Support (DfAM): Evaluate their engineering team’s capability to provide Design for Additive Manufacturing (DfAM) support. Can they assist with topology optimization, lattice structure integration, support strategy development, and ensuring the design is manufacturable and meets performance goals?
- Problem Solving: Assess their ability to troubleshoot potential issues related to printing, post-processing, or quality control based on past experiences.
- Equipment, Technology, and Capacity: The tools matter significantly in AM.
- Machine Type and Quality: Do they operate well-maintained, industrial-grade SLM or EBM machines suitable for Scalmalloy® and Ti-6Al-4V? Are the machines calibrated regularly? What is the manufacturer and model? Providers like Met3dp utilize industry-leading printers known for accuracy and reliability, which is a positive indicator.
- Volume de construction : Can their machines accommodate the size of the required payload mounts? Consider both current needs and potential future requirements.
- Redundancy and Capacity: Do they have multiple machines capable of running the required material to ensure redundancy and handle demand fluctuations or urgent orders? What is their typical utilization rate and available capacity?
- Surveillance des processus : Do their machines incorporate in-situ process monitoring capabilities (e.g., melt pool monitoring, thermal imaging) to help ensure build quality and consistency?
- Material Sourcing, Handling, and Traceability: Powder quality is fundamental.
- Powder Sourcing: Where do they source their Scalmalloy® and Ti-6Al-4V powders? Are the suppliers qualified and reputable? Do they perform incoming powder inspection and testing (chemistry, PSD, morphology, flowability)? Companies like Met3dp, which manufacture their own high-quality spherical powders using advanced Gas Atomization and PREP technologies, offer a distinct advantage in controlling this critical input variable.
- Manipulation des poudres : What are their procedures for storing, handling, sieving, and reusing metal powders to prevent contamination (especially cross-contamination between alloys) and degradation (e.g., oxygen pickup in Titanium)?
- Batch Traceability: Can they ensure full traceability of powder batches from raw material source through to the final printed part? This is essential for aerospace quality control and non-conformance investigation.
- Post-Processing Capabilities (In-House vs. Network): A finished part requires more than just printing.
- Capability Assessment: Evaluate their capabilities (or their network of qualified partners) for all necessary post-processing steps: stress relief, specific heat treatments for Scalmalloy®/Ti-6Al-4V, HIP, precision machining (multi-axis CNC), support removal, surface finishing, and comprehensive NDT (especially CT scanning).
- Integration and Management: If using external partners, how do they manage quality, logistics, and ensure seamless integration of these steps? Are the partners themselves AS9100/NADCAP certified?
- Système de gestion de la qualité (SGQ) robuste : Beyond certification, assess the practical implementation.
- Documentation : Review their procedures for process control, documentation management, revision control, non-conformance reporting, and corrective actions.
- Capacités d'inspection : What are their in-house metrology capabilities (CMM, scanning)? How do they verify part conformance?
- Contrôle des processus : How do they ensure consistent execution of locked-down processes for qualified parts? Statistical Process Control (SPC) data?
- Communication, Project Management, and Cost:
- Responsiveness: How quickly and effectively do they respond to inquiries and technical questions?
- Transparence : Are they open about their processes, capabilities, and potential challenges?
- Project Management: Do they have clear processes for managing projects, providing updates, and meeting deadlines?
- Cost Structure: Is their pricing transparent and competitive? Ensure all costs (printing, material, post-processing, NDT, qualification support) are clearly understood.
Choosing a supplier like Met3dp, with its deep roots in both additive manufacturing equipment and high-performance metal powder production, coupled with decades of collective expertise in metal AM, offers a strong foundation. Their focus on comprehensive solutions—spanning printers, advanced materials, and application development—positions them as a partner invested in customer success. Exploring their capabilities further via their website, particularly the “À propos de nous” section, can provide valuable insights into their philosophy and experience. Ultimately, a thorough audit and open communication are necessary to confirm any supplier meets the demanding requirements for producing aerospace-grade payload mounts.
Understanding Investment: Cost Factors and Lead Times for AM Payload Mounts
Additive manufacturing offers compelling technical advantages for aerospace payload mounts, but understanding the associated costs and timelines is crucial for project planning, budgeting, and evaluating the overall business case. While AM can sometimes offer cost savings over traditional methods for highly complex, low-volume parts (especially when considering total lifecycle costs like assembly), it’s essential to recognize the various factors that influence the final price and delivery schedule. Procurement managers and engineers need a clear picture of these elements to make informed decisions.
Key Cost Drivers for 3D Printed Payload Mounts:
- Coût des matériaux : High-performance aerospace alloys are expensive.
- Alloy Choice: Ti-6Al-4V powder is generally costly due to the titanium base and processing requirements. Scalmalloy®, with its scandium content, is also a premium-priced material. Material cost is often charged per kilogram of powder consumed (including supports).
- Part Volume & Density: Larger and denser parts naturally consume more material, directly impacting cost. Topology optimization and lattice structures, while potentially increasing design/simulation time, significantly reduce material consumption.
- Support Structure Volume: Material used for supports adds to the cost and is essentially waste (though powder from supports can sometimes be reclaimed). Minimizing supports through DfAM reduces this cost.
- AM Machine Time: Industrial metal AM machines represent significant capital investment, and their operating time is a major cost factor.
- Build Height: This is often the primary driver of print time. Taller parts take longer, irrespective of their footprint on the build plate. Orienting parts to minimize height can sometimes reduce print time and cost, but must be balanced against support needs and anisotropic properties.
- Part Volume & Complexity: While less impactful than height, the total volume to be scanned and the complexity of the scan paths (e.g., intricate lattices) influence the time per layer.
- Nesting & Build Plate Utilization: Printing multiple parts simultaneously on a single build plate (nesting) allows amortization of setup/cooldown time and potentially better machine utilization, reducing the cost per part for batch production.
- Machine Taux horaire : Suppliers factor in machine depreciation, maintenance, energy consumption, inert gas usage, and operator time into an hourly rate for build time.
- Coûts de main-d'œuvre : Skilled labor is required throughout the AM workflow.
- Pre-Processing: File preparation, build setup simulation, support generation.
- Machine Operation: Setting up the build, monitoring the process.
- Post-Print Handling: Part removal from build plate, basic cleaning.
- Suppression du support : Often a significant manual labor component, especially for complex parts.
- Basic Finishing: Bead blasting, initial surface cleanup.
- Coûts de post-traitement : These steps add significant cost beyond the initial print.
- Soulagement du stress et traitement par la chaleur : Requires specialized vacuum/inert atmosphere furnaces and energy; costs depend on cycle time and furnace capacity.
- Pressage isostatique à chaud (HIP) : Requires large, high-pressure capital equipment; typically outsourced and charged per cycle, with cost depending on part size/quantity fitting within the HIP unit. Can be a substantial portion of the overall cost.
- Usinage CNC : Billed based on machine time and complexity; required for achieving tight tolerances and fine finishes on critical features.
- Finition de la surface : Costs vary widely depending on the method (tumbling, polishing, etching) and the required finish level.
- CND et inspection : CMM inspection time, CT scanning services (can be costly, especially for high resolution or large parts), FPI, etc.
- Design & Engineering Costs:
- DfAM & Optimization: If significant redesign or topology optimization is required, this upfront engineering investment needs to be factored in.
- Qualification Support: Engineering time spent on developing test plans, analyzing results, and preparing documentation for part qualification.
- Quantité :
- Prototypes/One-Offs: Highest cost per part due to setup time and lack of amortization.
- Batch Production: Lower cost per part as setup, machine time (if nested effectively), and potentially post-processing can be optimized for volume.
Cost Factor Summary Table:
Cost Driver Category | Specific Factors | Impact Level | Notes |
---|---|---|---|
Matériau | Alloy Type (Scalmalloy®/Ti-6Al-4V), Part Volume, Support Volume | Haut | Premium alloys; DfAM critical for minimizing volume. |
AM Machine Time | Build Height, Build Volume/Complexity, Nesting Efficiency, Machine Rate | Haut | Height is key; nesting reduces per-part time for batches. |
Travail | Build Prep, Operation, Part/Support Removal, Basic Finishing | Moyen | Support removal can be labor-intensive. |
Post-traitement | Stress Relief, Heat Treat, HIP, CNC Machining, Surface Finishing, NDT | Haut | HIP & extensive CNC/NDT can significantly increase cost. |
Conception et ingénierie | DfAM Effort, Simulation, Qualification Support | Moyen | Upfront investment, especially for highly optimized/qualified parts. |
Quantité | One-off vs. Batch Production | Moyen | Setup costs amortized over larger quantities. |
Exporter vers les feuilles
Lead Times for AM Payload Mounts:
Lead time is the duration from order placement (or design freeze) to final part delivery. It can vary significantly based on complexity, quantity, required post-processing, and supplier backlog. A typical breakdown might look like this:
- Order Processing & File Prep: 1-3 business days. Reviewing design, generating build files, scheduling machine time.
- Impression : 2 days to 1.5 weeks+. Highly dependent on part height and build volume utilization. A tall, complex mount might take many days of continuous printing.
- Post-traitement : 1 to 4+ weeks. This phase often dominates the lead time.
- Soulagement du stress/traitement thermique : 1-3 jours (y compris le temps de chauffage et de refroidissement).
- HIP: Scheduling can take time; the cycle itself takes ~1 day, but logistics to/from a HIP provider add days/weeks.
- Support Removal & Basic Finishing: 1-5 days, depending on complexity.
- CNC Machining: 2 days to 2+ weeks, depending on complexity, features, and machine shop backlog.
- NDT & Inspection: 1-5 days.
- Expédition: 1 day to 1+ week, depending on location and method.
Total Estimated Lead Time: La fourchette est généralement comprise entre 3 weeks to 8 weeks or more for a complex, fully post-processed and inspected aerospace payload mount. This can still be significantly faster than the months potentially required for traditional manufacturing involving complex tooling (casting) or extensive machining setups for a comparable low-volume, high-complexity part.
Understanding these cost factors and lead time components allows for better project planning, realistic budgeting, and effective communication with AM service providers like Met3dp to optimize the manufacturing process for specific project needs.
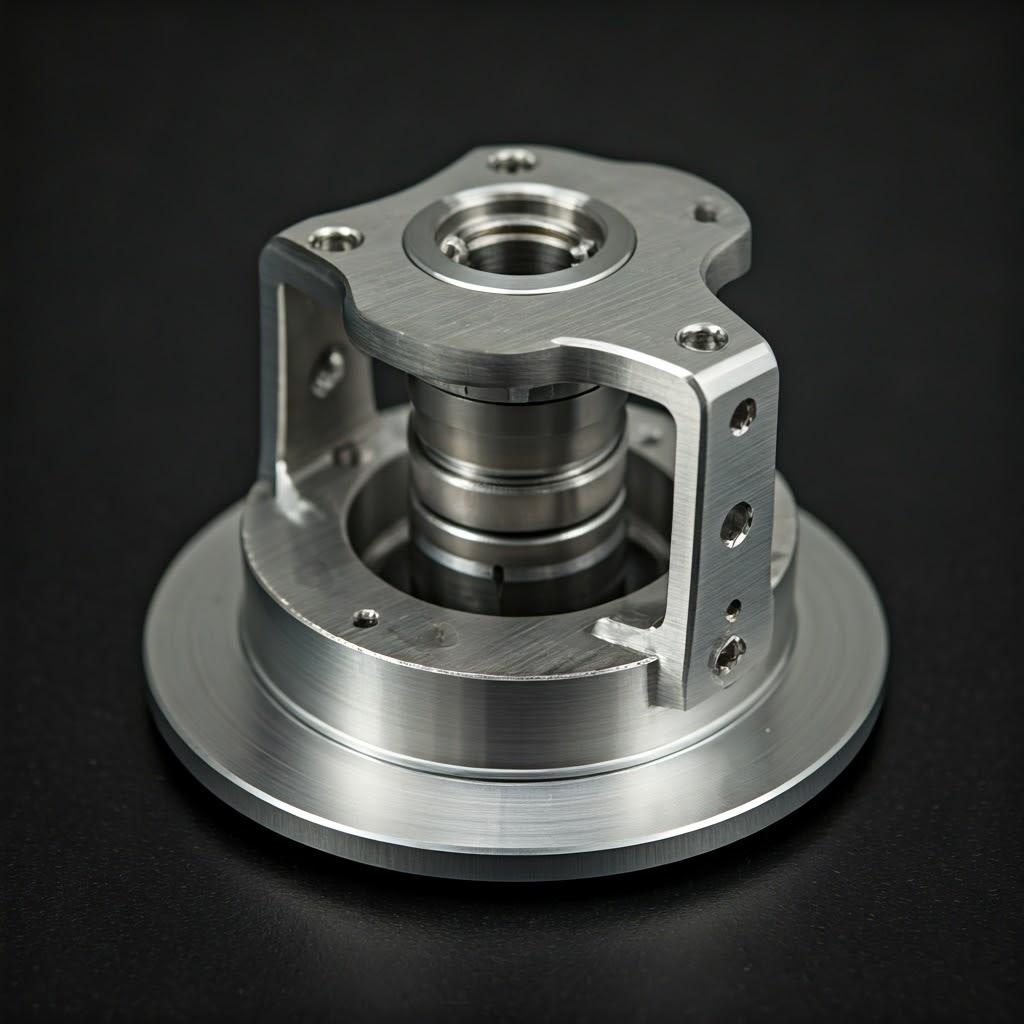
Frequently Asked Questions (FAQ) for 3D Printed Aerospace Payload Mounts
As engineers and procurement managers consider adopting metal additive manufacturing for critical components like payload mounts using advanced materials such as Scalmalloy® and Ti-6Al-4V, several common questions arise. Here are answers to some frequently asked questions:
1. How does the fatigue life of AM payload mounts compare to traditionally machined ones?
- The fatigue life of AM parts is highly dependent on several factors: material choice, process parameters, achieved density, surface finish, and post-processing (especially heat treatment and HIP).
- As-Built Condition: Without post-processing like HIP, AM parts (particularly SLM) can sometimes exhibit lower fatigue life than wrought or machined equivalents due to potential micro-porosity acting as initiation sites and rougher surface finish.
- With HIP & Finishing: When subjected to Hot Isostatic Pressing (HIP) to close internal porosity and appropriate surface finishing (e.g., polishing or machining critical areas), the fatigue performance of AM Ti-6Al-4V and Scalmalloy® can meet or even exceed that of cast or sometimes wrought materials, especially when DfAM allows for optimized load paths that reduce peak stresses.
- Principaux enseignements : Achieving excellent fatigue life comparable or superior to traditional methods is possible but requires meticulous process control, high-quality powder, appropriate post-processing (HIP is often crucial), and thorough testing for validation.
2. What qualification standards (e.g., NASA, ESA, FAA) must AM aerospace parts meet?
- Qualification pathways for AM aerospace components are still evolving but are becoming more standardized. There isn’t one single universal standard, but parts typically need to comply with requirements set by the relevant certification authority (FAA for commercial aircraft, NASA/ESA for space missions, DoD for military) and the prime contractor’s specific standards.
- Processus : Qualification generally involves a rigorous “point design qualification” approach:
- Process Locking: Defining and freezing every parameter: machine type, software versions, material specification (powder chemistry, PSD, supplier), build parameters, thermal post-processing cycles, support strategies, finishing methods, NDT procedures.
- Material Allowables Development: Extensive testing of material coupons built with the locked process in various orientations to establish statistically reliable design properties (e.g., A-Basis or B-Basis allowables), often following guidelines similar to those in MMPDS (Metallic Materials Properties Development and Standardization) or CMH-17 (Composite Materials Handbook).
- Component Testing: Building and testing full components under representative static, dynamic (vibration, shock), fatigue, and environmental conditions.
- Documentation : Comprehensive documentation covering the entire process, testing results, and quality control measures.
- Normes : Relevant documents include NASA-STD-6016, NASA-STD-6030, standards developed by SAE International’s AMS-AM committee, and specific requirements from primes like Boeing, Airbus, Lockheed Martin, etc.
3. Can complex internal cooling channels or wiring paths be integrated into 3D printed payload mounts?
- Yes, this is one of the significant advantages of additive manufacturing. AM allows for the creation of highly complex internal channels, conduits, or cavities directly within the payload mount structure during the printing process.
- Applications : This can be used for:
- Gestion thermique : Integrating channels for liquid cooling or passive heat dissipation paths for sensitive electronics within the payload.
- Réduction du poids : Creating internal voids or lattice structures.
- Integrated Wiring/Fiber Optics: Designing conduits to protect and route cables or optical fibers, reducing clutter and potential snagging hazards.
- Défis : Designing these channels to be self-supporting or ensuring supports and trapped powder can be completely removed after printing is critical. Thorough cleaning and inspection (e.g., CT scanning) are necessary to verify channel integrity and clearance.
4. What is the typical batch-to-batch consistency for critical properties in AM?
- Achieving consistent properties from build-to-build and machine-to-machine is a major focus in maturing AM technology for production. Consistency depends heavily on the rigor of the supplier’s Quality Management System (QMS) and process controls.
- Key Factors for Consistency:
- Strict control and testing of incoming powder batches.
- Regular machine calibration and maintenance.
- Locked and validated process parameters.
- Consistent post-processing execution (e.g., calibrated furnaces, validated cycles).
- Use of process monitoring tools and Statistical Process Control (SPC).
- Résultat : With robust process control, experienced suppliers can achieve high levels of batch-to-batch consistency for mechanical properties (tensile, yield, elongation) and density. However, demonstrating this consistency through ongoing monitoring and testing is part of the qualification and production process.
5. How does Met3dp ensure the quality and traceability of its metal powders and printed parts?
- Met3dp places a strong emphasis on quality throughout the additive manufacturing value chain.
- Qualité de la poudre : By employing advanced Gas Atomization and PREP technologies in-house, Met3dp maintains tight control over powder production, focusing on achieving high sphericity, controlled Particle Size Distribution (PSD), high purity, and good flowability – critical factors for consistent printing. Each batch undergoes rigorous testing and certification.
- Contrôle des processus : Utilizing industry-leading SEBM and other PBF printers known for accuracy and reliability, Met3dp focuses on developing and implementing robust, optimized process parameters for the alloys they offer.
- Traceability: Implementing comprehensive traceability systems allows tracking materials and process data from the raw powder batch through printing and post-processing to the final certified component, which is essential for aerospace requirements.
- Partnership: Met3dp collaborates with clients to understand specific quality requirements and supports the development of testing and qualification plans necessary for critical applications, leveraging their expertise in both materials and AM processes.
6. Are there Minimum Order Quantities (MOQs) for 3D printed payload mounts?
- MOQs can vary significantly between suppliers. AM is well-suited for producing single parts or very small batches (e.g., for prototypes, satellites, or custom modifications), which is one of its advantages over traditional tooling-based methods.
- Pricing Structure: While MOQs might not always be strict, the cost-per-part is typically much higher for single pieces or very small quantities compared to larger batches due to the amortization of setup and fixed costs. Suppliers may offer price breaks at different quantity levels. It’s best to discuss specific project volumes directly with the supplier.
7. How is Intellectual Property (IP) protected when sending sensitive aerospace designs to an AM supplier?
- Protecting sensitive design data is crucial. Reputable AM suppliers serving the aerospace industry should have robust measures in place:
- Non-Disclosure Agreements (NDAs): Standard practice to legally protect confidential information.
- Secure Data Transfer: Using encrypted methods for transferring CAD files and technical data.
- Access Controls: Limiting access to sensitive data within their organization on a need-to-know basis.
- Conformité ITAR/EAR : For controlled data, suppliers must have demonstrated compliance procedures.
- It’s essential to discuss IP protection protocols and sign appropriate NDAs before sharing any proprietary design information.
Conclusion: Elevating Aerospace Missions with Advanced Additive Manufacturing
The journey through the intricacies of designing, manufacturing, and qualifying aerospace payload mounts using metal additive manufacturing reveals a technology poised to redefine component creation for satellites, aircraft, and UAVs. Leveraging advanced materials like the ultra-high-specific-strength Scalmalloy® (alliage d'aluminium) and the proven aerospace workhorse Ti-6Al-4V, AM empowers engineers to break free from the constraints of traditional manufacturing. The ability to produce highly complex, topology-optimized geometries results in significant réduction du poids – a paramount goal in aerospace – leading to lower launch costs, increased payload capacity, or improved fuel efficiency.
Beyond lightweighting, metal AM enables unprecedented liberté de conception, allowing for the creation of functionally superior mounts with integrated features like internal channels, lattice structures for enhanced stiffness or vibration damping, and consolidated assemblies that reduce part count, complexity, and potential failure points. This accelerates development cycles through prototypage rapide and facilitates the production of highly customized components essential for specific mission requirements.
However, realizing these benefits demands a rigorous approach. Success hinges on embracing Conception pour la fabrication additive (DfAM) principles, meticulously planning and executing critical post-traitement steps like stress relief, heat treatment, HIP, and precision machining, and navigating potential challenges such as residual stress, support removal, and porosity control. Above all, ensuring flight-worthiness requires unwavering commitment to quality control, process validation, and thorough inspection, culminating in rigorous part qualification that meets stringent aerospace standards.
Choosing the right manufacturing partner is arguably the most critical step in this journey. Aerospace companies need suppliers who possess not only state-of-the-art equipment but also deep expertise in materials science, proven experience with aerospace applications, robust quality management systems (AS9100 certified), and a comprehensive understanding of the entire process chain from powder to qualified part.
Met3dp embodies these qualities, standing as a leading provider of comprehensive additive manufacturing solutions. With industry-leading capabilities in high-accuracy SEBM printing, in-house production of high-performance spherical metal powders using advanced atomization techniques, and decades of collective expertise, Met3dp is uniquely positioned to support the demanding requirements of the aerospace sector. Their commitment extends from supplying superior materials and equipment to providing application development services and partnering with organizations to navigate the complexities of AM adoption and qualification.
By embracing metal additive manufacturing and collaborating with knowledgeable partners like Met3dp, the aerospace industry can continue to push the boundaries of performance, efficiency, and mission capability. The future of aerospace componentry is being built layer by layer, enabling lighter, stronger, and more capable vehicles to explore the skies and space beyond.
Ready to explore how metal 3D printing can revolutionize your aerospace components? Visite https://met3dp.com/ or contact the Met3dp team today to discuss your specific application and learn how their advanced AM solutions can elevate your next mission.
Partager sur
MET3DP Technology Co. est un fournisseur de premier plan de solutions de fabrication additive dont le siège se trouve à Qingdao, en Chine. Notre société est spécialisée dans les équipements d'impression 3D et les poudres métalliques de haute performance pour les applications industrielles.
Articles connexes
À propos de Met3DP
Mise à jour récente
Notre produit
CONTACTEZ-NOUS
Vous avez des questions ? Envoyez-nous un message dès maintenant ! Nous répondrons à votre demande avec toute une équipe dès réception de votre message.
Obtenir les informations de Metal3DP
Brochure du produit
Obtenir les derniers produits et la liste des prix
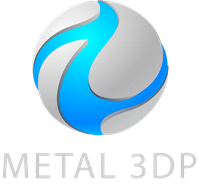
Poudres métalliques pour l'impression 3D et la fabrication additive