Impression 3D par laser à poudre pour l'aérospatiale
Table des matières
Poudre Laser Impression 3Dégalement connu sous le nom de Laser Powder Bed Fusion (LPBF), joue un rôle essentiel dans le domaine aérospatial, offrant plusieurs avantages par rapport aux techniques de fabrication traditionnelles.
1. Composants légers et complexes :
1. Fabrication de pièces d'avion
Les imprimantes laser 3D Powder peuvent-elles être utilisées pour fabriquer des composants de moteur d'avion ?
Absolument ! Les imprimantes 3D à laser à poudre jouent un rôle de plus en plus important dans la fabrication de composants de moteurs d'avion. Voici pourquoi :
Avantages :
Conceptions complexes et légères : L'impression 3D permet des conceptions complexes avec des canaux internes et des treillis, impossibles à réaliser avec les techniques traditionnelles. Cela peut conduire à des composants plus légers et plus résistants, améliorant ainsi le rendement énergétique et les performances.
Matériaux de haute performance : Les imprimantes LPBF peuvent traiter des alliages métalliques avancés tels que le titane et l'Inconel, essentiels pour résister aux températures et pressions élevées des moteurs à réaction.
Réduction des déchets et des délais : L'impression 3D utilise souvent moins de matériaux que la fabrication soustractive traditionnelle, ce qui minimise les déchets. En outre, elle permet de rationaliser la production et de réduire les délais par rapport au moulage ou au forgeage.
Exemples :
Rolls-Royce : L'entreprise utilise le LPBF pour les tuiles de combustion complexes de son moteur Pearl 10X, revendiquant une augmentation de l'efficacité de 5%.
GE Aviation : Ils construisent la plus grande imprimante LPBF du monde pour produire des composants structurels de moteurs à réaction pour les avions monocouloirs.
Honeywell : Ils utilisent l'impression 3D pour les injecteurs de carburant et d'autres composants du moteur, dans le but de réduire le poids et les émissions.
Défis :
Coût : Les imprimantes LPBF sont actuellement coûteuses, mais les coûts diminuent.
Qualification : Des essais et une certification approfondis sont nécessaires pour les pièces critiques en termes de sécurité, comme les composants de moteur.
Taille de construction limitée : Certaines imprimantes ont des limites de taille, mais des systèmes plus grands sont en cours de développement.
LPBF excelle dans la création de pièces complexes et légères avec des canaux internes et des treillis, ce qui est impossible avec les méthodes conventionnelles. Cela permet de réduire le poids sans compromettre la résistance, qui est cruciale pour l'efficacité énergétique et les performances. Voici quelques exemples :
Injecteurs de carburant : Géométries internes complexes pour un mélange et une combustion optimaux du carburant.
Supports de satellite : Léger et solide pour réduire le poids de la charge utile.
Échangeurs de chaleur : Canaux internes complexes pour un transfert de chaleur efficace.
2. exemples de composants d'aéronefs
Composants du système d'alimentation en carburant : Les buses, les injecteurs et les échangeurs de chaleur peuvent être imprimés en 3D avec des canaux internes complexes pour améliorer le flux de carburant et le transfert de chaleur.
Composants intérieurs : Des supports, des clips et d'autres pièces non critiques peuvent être imprimés en 3D pour réduire le poids et personnaliser le produit.
Composants du moteur : Certaines entreprises expérimentent l'impression 3D de certains composants de moteurs, tels que les chambres de combustion et les aubes de turbines.
Véhicules aériens sans pilote (UAV) : En raison de leur légèreté et de leur complexité, les drones sont des candidats de choix pour les composants imprimés en 3D.
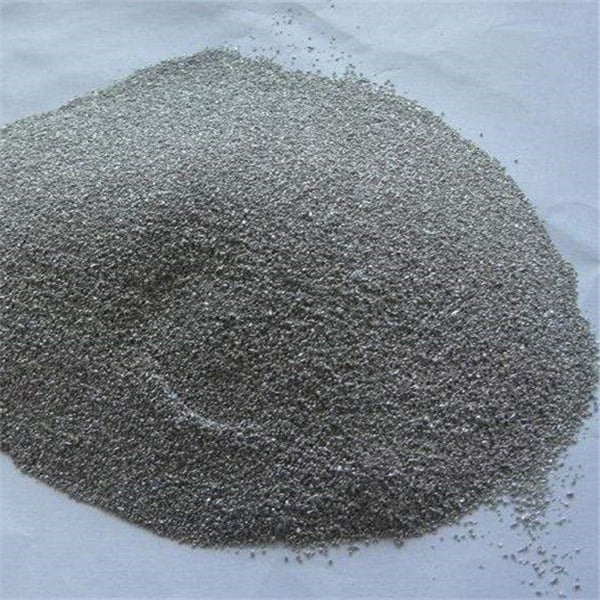
2. Pièces sur mesure et fabrication à la demande :
Le LPBF permet une production rapide de pièces personnalisées, essentielles pour les réparations, les prototypes et les applications à faible volume. Cela réduit la dépendance à l'égard de la fabrication à grande échelle et permet des délais d'exécution plus courts. Voici quelques exemples :
1. Vitesse et personnalisation :
Des délais d'exécution plus courts : Le LPBF élimine l'outillage traditionnel, ce qui réduit considérablement les délais d'exécution des pièces personnalisées. Imaginez que vous ayez besoin d'un support unique pour votre avion ; au lieu d'attendre des mois, il peut être imprimé en quelques jours.
Une personnalisation inégalée : Les géométries complexes et les conceptions compliquées sont un jeu d'enfant pour LPBF. Pensez à des panneaux légers avec des structures internes en treillis pour les avions, ou à des accessoires sur mesure pour les expériences dans les vaisseaux spatiaux - les possibilités sont infinies.
2. Avantages pour des applications spécifiques :
Composants intérieurs d'aéronefs : Imaginez des panneaux personnalisés avec un éclairage intégré ou des supports s'adaptant parfaitement à des espaces non standard. Cela permet de gagner du poids, de réduire le temps d'assemblage et d'améliorer l'esthétique.
Composants de l'engin spatial : Le LPBF est idéal pour les pièces uniques et spécifiques à une mission, telles que les antennes, les supports ou même les petits composants de moteur. Imaginez l'impression d'un échangeur de chaleur personnalisé pour une mission lunaire spécifique, adapté à l'environnement et aux exigences de la mission.
Pièces de rechange : Plus besoin d'attendre des pièces obsolètes ou endommagées ! Le LPBF permet l'impression à la demande, ce qui minimise les temps d'arrêt et garantit le bon déroulement des opérations. Imaginez l'impression d'un engrenage rare pour un avion ancien ou d'un boîtier de capteur critique pour un vaisseau spatial en orbite.
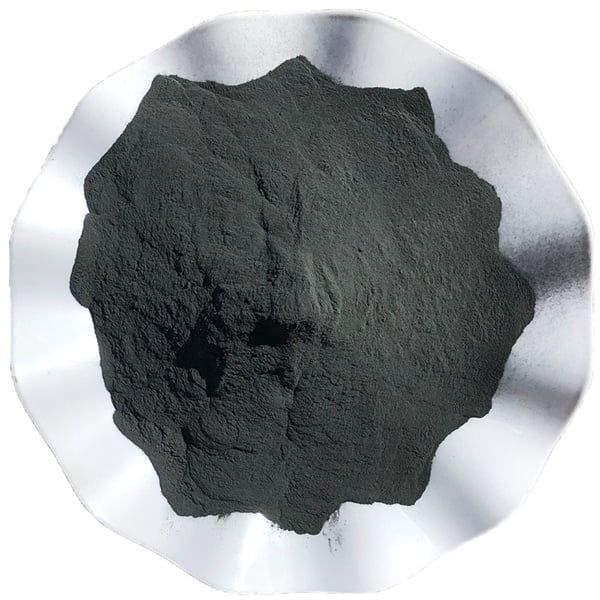
3. Matériaux avancés et performances de Poudre Laser Impression 3D
Le LPBF (Laser Powder Bed Fusion) ne se limite pas à la création de pièces personnalisées ; il libère le potentiel de la technologie de l'aluminium. matériaux haute performance qui étaient auparavant difficiles ou impossibles à utiliser dans la fabrication traditionnelle. Voyons plus en détail comment LPBF permet à des industries telles que l'aérospatiale, la fusée et la technologie des turbines:
1. Merveilles matérielles :
Alliages de titane : Imaginez des pales de turbine qui résistent à des températures brûlantes et à une pression intense. Le LPBF permet d'imprimer des canaux de refroidissement complexes à l'intérieur de ces pales en utilisant des alliages de titane très résistants, maximisant ainsi les performances et l'efficacité.
Inconel : Cet alliage de nickel et de chrome présente une résistance à la chaleur et une solidité exceptionnelles, ce qui le rend idéal pour les composants des moteurs de fusée. Le LPBF permet des conceptions complexes telles que les chambres de combustion et les injecteurs, optimisant ainsi la poussée et l'efficacité du carburant.
Aluminium-lithium : Cette merveille de légèreté permet de réduire le poids précieux des structures aérospatiales. Le LPBF permet d'imprimer des nervures, des poutrelles et des structures en nid d'abeille complexes, créant ainsi des composants solides mais légers pour les avions et les engins spatiaux.
2. Au-delà des exemples :
Implants médicaux : Les alliages de titane biocompatibles imprimés avec le LPBF créent des implants durables et légers qui s'adaptent parfaitement à l'anatomie du patient.
Prothèses dentaires : Des matériaux solides et biocompatibles tels que le cobalt-chrome sont utilisés pour les prothèses et les couronnes imprimées LPBF, offrant une adaptation et une fonction supérieures.
Des outils de pointe : Imaginez des instruments chirurgicaux ou des moules aux caractéristiques complexes, imprimés à partir de matériaux résistants à l'usure comme le carbure de tungstène - LPBF rend cela possible.
3. Débloquer la performance :
Rapport résistance/poids : Le LPBF permet d'imprimer des structures légères et complexes qui sont incroyablement solides, ce qui est essentiel pour maximiser les performances dans l'aérospatiale et d'autres applications sensibles au poids.
Résistance aux hautes températures : Les matériaux tels que l'Inconel peuvent résister à une chaleur extrême, ce qui permet à LPBF de créer des composants pour les moteurs à réaction, les moteurs de fusée et d'autres environnements à haute température.
Propriétés de fatigue : Les pièces imprimées en LPBF présentent une excellente résistance à la fatigue, essentielle pour les composants soumis à des contraintes répétées dans des applications telles que les turbines et les structures aéronautiques.
Matériau | Propriétés principales | Applications | Avantages | Inconvénients | Coût | Post-traitement | Certification |
---|---|---|---|---|---|---|---|
Alliages de titane | Rapport résistance/poids élevé, résistance aux températures élevées, résistance à la corrosion | Aérospatiale, médecine, automobile | Excellentes propriétés mécaniques, biocompatibilité, légèreté | Coût élevé des matériaux, post-traitement complexe | Haut | Traitement thermique, usinage | Des réglementations strictes |
Inconel | Résistance aux hautes températures, solidité, résistance à la corrosion | Aérospatiale, énergie, traitement chimique | Excellentes performances à haute température, résistance aux environnements difficiles | Coût élevé des matériaux, post-traitement complexe | Haut | Traitement thermique, usinage | Des réglementations strictes |
Aluminium-Lithium | Légèreté, résistance élevée, bonne rigidité | Aérospatiale, automobile, défense | Réduction du poids, amélioration du rendement énergétique | Résistance inférieure à celle des alliages de titane, plus grande vulnérabilité à la corrosion | Moyen | Traitement thermique, usinage | Des réglementations moins strictes |
Acier inoxydable | Grande solidité, résistance à la corrosion, biocompatibilité | Médical, automobile, industriel | Bonne combinaison de propriétés, bon rapport qualité-prix | Rapport résistance/poids inférieur à celui des alliages de titane, moins résistant à la corrosion que l'Inconel | Faible | Traitement thermique, usinage | Varie en fonction de l'application |
Acier à outils | Dureté élevée, résistance à l'usure, ténacité | Outillage, fabrication, automobile | Excellente résistance à l'usure, longue durée de vie de l'outil | Coût élevé des matériaux, post-traitement complexe | Moyen | Traitement thermique, usinage | Varie en fonction de l'application |
Nylon | Léger, solide, flexible | Automobile, biens de consommation, médical | Léger, économique, biocompatible | Solidité et résistance à la température inférieures à celles des métaux | Faible | Post-traitement minimal | Varie en fonction de l'application |
Polypropylène | Légèreté, résistance aux produits chimiques, faible coût | Biens de consommation, emballage, médical | Léger, économique, bonne résistance aux produits chimiques | Solidité et résistance à la température inférieures à celles des métaux | Faible | Post-traitement minimal | Varie en fonction de l'application |
4. Liberté de conception et optimisation :
Le LPBF (Laser Powder Bed Fusion) ne se limite pas à l'impression de formes complexes. concevoir des pièces qui repoussent les limites du possible. Contrairement à la fabrication traditionnelle, qui présente des limites, le procédé LPBF offre des avantages inégalés. liberté de conception et optimisationLes composants sont donc plus légers, plus résistants et plus efficaces. Explorons les possibilités passionnantes qui s'offrent à nous :
1. Libérer la créativité :
Structures en nid d'abeille : Imaginez des ailes d'avion ou des panneaux de vaisseau spatial à la fois légers et incroyablement résistants, obtenus grâce à des structures en nid d'abeille complexes imprimées en LPBF. Ces conceptions minimisent l'utilisation de matériaux tout en maximisant la résistance et la rigidité, ce qui permet de réduire considérablement le poids et d'améliorer le rendement énergétique.
Pièces optimisées sur le plan topologique : Dites adieu aux conceptions encombrantes et inefficaces ! Le LPBF permet d'imprimer des pièces optimisées en fonction d'exigences spécifiques en matière de charge et de contrainte. Imaginez un composant de suspension de voiture conçu à l'aide de l'optimisation topologique, atteignant une résistance optimale avec un minimum de matériau, ce qui permet d'économiser du poids et d'améliorer les performances.
Conceptions biomimétiques : Inspirez-vous de la nature ! LPBF permet d'imprimer des composants inspirés de structures biologiques, comme les os d'oiseaux ou les toiles d'araignée. Imaginez une pale de turbine dont les canaux internes imitent l'aile d'un oiseau, ce qui permet d'obtenir un transfert de chaleur et une efficacité supérieurs.
2. Au-delà des exemples :
Implants médicaux : Le LPBF permet d'imprimer des implants avec des structures complexes et poreuses imitant l'os naturel, favorisant la croissance osseuse et l'ostéo-intégration.
Biens de consommation : Imaginez des vélos ou des équipements sportifs légers et ergonomiques, imprimés avec des structures internes complexes pour des performances et un confort optimaux.
Architecture : Le LPBF ouvre la voie à l'impression d'éléments de construction complexes avec une utilisation réduite de matériaux et une résistance accrue, ouvrant ainsi la voie à une architecture durable et innovante.
3. Libérer le potentiel :
Réduction du poids : En créant des structures légères avec un minimum de matériau, le LPBF permet de réaliser des économies de poids significatives dans des applications critiques telles que l'aérospatiale, l'automobile et le secteur médical.
Amélioration des performances : Des conceptions optimisées et une inspiration biomimétique peuvent permettre d'améliorer les performances dans des domaines tels que le transfert de chaleur, l'écoulement des fluides et la résistance structurelle.
Durabilité : La réduction de l'utilisation des matériaux et l'allègement des composants se traduisent par une diminution de l'impact sur l'environnement tout au long du cycle de vie du produit.
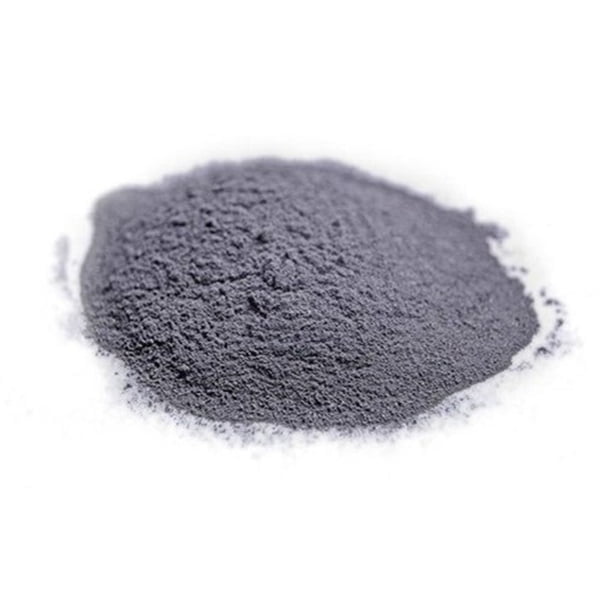
5. Défis et considérations :
Si le LPBF offre des possibilités passionnantes, il est essentiel de reconnaître les défis qui accompagnent cette technologie :
1. Coût :
Coût de la machine : Par rapport aux équipements de fabrication traditionnels, les machines LPBF peuvent être nettement plus coûteuses, en particulier pour les imprimantes à haute performance. Cela limite l'accessibilité et augmente le coût par pièce.
Coût des matériaux : Les matériaux à haute performance tels que les alliages de titane et l'Inconel sont intrinsèquement coûteux, et la forme de poudre utilisée dans les IAA ajoute un coût supplémentaire par rapport aux matériaux en vrac.
2. Post-traitement :
Suppression du support : L'IAA nécessite souvent l'impression de structures de support pour les géométries complexes. Le retrait de ces supports peut prendre du temps et nécessiter des techniques spécialisées, ce qui augmente le coût global et la complexité.
Finition : Selon l'application, les pièces peuvent nécessiter un traitement thermique, un usinage ou d'autres étapes de finition pour obtenir les propriétés souhaitées, ce qui augmente encore le temps et le coût de traitement.
3. Certification :
Des réglementations strictes : Pour les applications dans les industries critiques telles que l'aérospatiale ou la médecine, les pièces doivent être conformes à des réglementations strictes et à des normes de sécurité. Cela implique souvent des tests et des processus de qualification approfondis, qui peuvent être longs et coûteux.
Normes limitées : Bien que les normes relatives aux IAA évoluent, elles ne sont pas aussi mûres que celles des méthodes de fabrication traditionnelles. Cela peut créer des incertitudes et des obstacles supplémentaires à la certification.
4. Autres considérations :
Expertise en matière de conception : L'utilisation efficace des IAA nécessite des connaissances spécialisées sur les capacités et les limites de la technologie, ce qui ajoute à la complexité globale du projet.
Contrôle de la qualité : Garantir une qualité et une répétabilité constantes des pièces peut s'avérer difficile en raison de facteurs tels que les caractéristiques de la poudre, les paramètres du laser et l'étalonnage de la machine.
Impact sur l'environnement : Si les IAA permettent de réaliser des économies de matériaux par rapport aux méthodes traditionnelles, la consommation d'énergie et la gestion des déchets de poudre doivent être prises en compte pour une adoption durable.
Partager sur
MET3DP Technology Co. est un fournisseur de premier plan de solutions de fabrication additive dont le siège se trouve à Qingdao, en Chine. Notre société est spécialisée dans les équipements d'impression 3D et les poudres métalliques de haute performance pour les applications industrielles.
Articles connexes
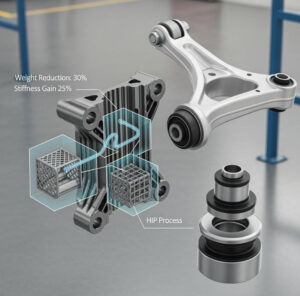
Metal 3D Printed Subframe Connection Mounts and Blocks for EV and Motorsport Chassis
Lire la suite "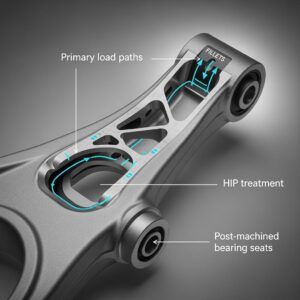
Metal 3D Printing for U.S. Automotive Lightweight Structural Brackets and Suspension Components
Lire la suite "À propos de Met3DP
Mise à jour récente
Notre produit
CONTACTEZ-NOUS
Vous avez des questions ? Envoyez-nous un message dès maintenant ! Nous répondrons à votre demande avec toute une équipe dès réception de votre message.
Obtenir les informations de Metal3DP
Brochure du produit
Obtenir les derniers produits et la liste des prix