Lightweight Radiator Panels for Satellites via Metal AM
Table des matières
Introduction: The Critical Role of Thermal Radiator Panels in Satellite Missions
The unforgiving vacuum of space presents a unique set of engineering challenges, paramount among them being thermal management. Unlike terrestrial applications where heat can be dissipated through convection and conduction to the surrounding atmosphere, spacecraft rely almost entirely on thermal radiation to reject waste heat. Satellites, packed with sophisticated electronics, powerful transmitters, sensitive instruments, and energy-generating systems, continuously produce significant amounts of heat. Without an effective means of shedding this thermal energy, internal temperatures could quickly rise beyond operational limits, leading to component malfunction, degraded performance, and ultimately, mission failure. This makes the Thermal Control System (TCS) one of the most critical subsystems onboard any spacecraft, directly impacting its lifespan, reliability, and overall success.
At the heart of most passive and active thermal control systems lies the satellite radiator panel. These components act as the primary interface between the spacecraft’s internal heat loads and the cold sink of deep space. Their fundamental purpose is to efficiently radiate waste heat, collected from various sources via heat pipes, loop heat pipes (LHPs), or direct conduction, away from the satellite. Achieving optimal thermal performance often involves intricate designs, specialized surface coatings (like Optical Solar Reflectors – OSRs or high-emissivity paints), and careful placement on the satellite body to maximize the view factor to space while minimizing solar and Earth-based thermal inputs.
Traditionally, manufacturing these critical components has relied on conventional methods such as CNC machining of solid metal plates (often aluminum or its alloys), intricate assembly processes involving brazing or bonding face sheets to honeycomb cores, and integrating embedded heat pipes. While effective, these traditional approaches face several inherent limitations, particularly concerning:
- Poids : Launch costs are a primary driver in satellite design, often calculated in tens of thousands of dollars per kilogram sent to orbit. Traditional radiator designs, especially those requiring significant structural integrity or complex internal fluid routing, can contribute substantially to the satellite’s overall mass budget. Every gram saved translates directly to reduced launch costs or increased payload capacity.
- Complexité de la conception : Integrating fluid channels or heat pipes into flat or simply curved panels using conventional methods can be complex, requiring multiple manufacturing steps, specialized joining techniques (like brazing or epoxy bonding), and extensive inspection, which increases cost and lead time. Achieving truly optimized, non-planar, or conformal shapes to fit specific satellite geometries is often impractical or prohibitively expensive.
- Délais d'exécution : The multi-stage processes involved in traditional radiator manufacturing, including machining, surface treatments, joining, and assembly, can result in long lead times, hindering rapid development cycles and delaying satellite deployment schedules. Tooling requirements for specific designs can further extend these timelines.
- Part Count & Reliability: Assemblies involving multiple bonded or brazed components introduce potential failure points at each joint, requiring rigorous quality control and non-destructive testing (NDT) to ensure long-term reliability in the harsh space environment characterized by extreme thermal cycling and vacuum conditions.
Recognizing these challenges, the aerospace industry is increasingly turning towards innovative manufacturing techniques. Fabrication additive métallique (AM), commonly known as metal Impression 3D, has emerged as a disruptive technology offering transformative potential for satellite radiator panel production. By building components layer by layer directly from metal powder feedstock using energy sources like lasers or electron beams, metal AM unlocks unprecedented design freedom, enables significant weight reduction through topology optimization, facilitates part consolidation, and accelerates development timelines. This technology is not just an alternative; it represents a paradigm shift in how we design and manufacture high-performance components for the demanding environment of space. Companies specializing in solutions d'impression 3D de métaux, like Met3dp, are at forefront of this revolution, providing the advanced equipment, high-quality materials, and process expertise needed to realize the full potential of AM for critical applications like satellite thermal management.
Core Functions: What are Satellite Radiator Panels Used For?
Satellite radiator panels are indispensable components of the Thermal Control System (TCS), acting as the spacecraft’s primary mechanism for rejecting waste heat into the cold void of space. To appreciate their importance, one must understand the thermal environment and heat sources inherent to satellite operations. Unlike Earth-bound systems, satellites operate in a near-perfect vacuum, rendering convective cooling impossible. Heat transfer is dominated by conduction within the spacecraft structure and radiation to and from external sources and the satellite’s own surfaces.
Sources of Heat on a Satellite:
- Payload Electronics: Scientific instruments, communication transponders, processors, sensors, and data storage units generate significant heat during operation. The power density of modern electronics continues to increase, intensifying thermal management challenges.
- Power Systems: Solar arrays, batteries (during charge/discharge cycles), and power distribution units generate waste heat as part of the energy conversion and storage process.
- Avionics and Bus Systems: Guidance, navigation, control (GNC) systems, telemetry and command (T&C) modules, reaction wheels, and propulsion systems contribute to the overall thermal load.
- Environmental Loads:
- Direct Solar Radiation: Sunlight directly impinging on the satellite surfaces is a major heat source.
- Albedo Radiation: Sunlight reflected off the Earth’s surface and atmosphere.
- Earth Infrared (IR) Radiation: Heat radiated from the Earth itself.
All this generated and absorbed heat must be carefully managed to maintain components within their specified operating temperature ranges, which can vary widely from cryogenic temperatures for some sensors to moderately high temperatures for power amplifiers. Failure to do so can lead to reduced efficiency, signal distortion, premature aging, and catastrophic failure.
The Role of Radiator Panels in Heat Rejection:
Radiator panels serve as the final stage in the heat rejection pathway. Their operation is governed by the principles of radiative heat transfer, primarily the Stefan-Boltzmann law, which states that the power radiated per unit area is proportional to the fourth power of its absolute temperature 1 and its surface emissivity (ϵ).
Prad/A=ϵσT4
Where:
- Prad is the radiated power
- A is the surface area
- ϵ is the surface emissivity (a value between 0 and 1, indicating how effectively a surface radiates thermal energy)
- σ is the Stefan-Boltzmann constant (5.67×10−8Wm−2K−4)
- T is the absolute temperature in Kelvin
To maximize heat rejection, radiator panels are designed with:
- Large Surface Area (A): Sufficient area is needed to radiate the required amount of heat at the desired operating temperature. This often leads to large, sometimes deployable, panel structures.
- High Emissivity (ϵ): Specialized surface coatings or finishes are applied to achieve high emissivity (typically > 0.85) in the infrared spectrum, maximizing radiative efficiency. Common examples include white paints (like SPU-787, AZ-93), silvered Teflon films, or Optical Solar Reflectors (OSRs), which combine high IR emissivity with low solar absorptivity (α) to minimize heat absorption from the sun.
- Optimal Temperature (T): The TCS aims to transport heat efficiently to the radiator, raising its temperature sufficiently for effective radiation while keeping the source components cool.
Integration with Heat Transport Mechanisms:
Radiators rarely work in isolation. They are typically coupled with heat transport devices that efficiently collect heat from disparate sources across the satellite and deliver it to the radiating surfaces. Common integration methods include:
- Heat Pipes: These passive devices utilize a two-phase cycle (evaporation and condensation) of a working fluid within a sealed tube containing a wick structure. They offer very high effective thermal conductivity, capable of transporting heat over significant distances with minimal temperature drop. Radiators often have heat pipes embedded within or bonded to their structure.
- Loop Heat Pipes (LHPs) & Capillary Pumped Loops (CPLs): More complex passive systems capable of transporting higher heat loads over longer distances and against gravity, suitable for high-power applications. The evaporator is placed at the heat source, and the condenser is integrated with the radiator panel.
- Direct Conduction: Simpler configurations may rely on direct conduction through the satellite structure or dedicated high-conductivity pathways to transfer heat to the radiator surface, often suitable for lower power or less distributed heat sources.
Applications Across Satellite Types:
The specific design and requirements for radiator panels vary depending on the satellite’s mission, orbit, and power levels:
- Low Earth Orbit (LEO): Experience rapidly changing thermal environments, cycling between direct sunlight and Earth’s shadow frequently. Radiators must cope with varying solar and albedo inputs. Weight is often a critical constraint.
- Medium Earth Orbit (MEO): Similar challenges to LEO, often used for navigation constellations (e.g., GPS, Galileo).
- Geostationary Orbit (GEO): Experience relatively stable thermal environments but often have very high power requirements for communications payloads, demanding large and highly efficient radiator panels. One side may continuously face the sun, requiring careful thermal design and surface coatings.
- Deep Space & Scientific Probes: Face extremely cold environments but may have unique thermal challenges related to radioisotope thermoelectric generators (RTGs) or sensitive cryogenic instruments.
Procurement managers and systems engineers seeking reliable satellite component suppliers understand that radiator panels are not off-the-shelf items. They are custom-engineered solutions tailored to the specific thermal demands and mechanical constraints of each unique mission. The ability to manufacture these complex, high-reliability components efficiently and cost-effectively is crucial for the space industry supply chain.
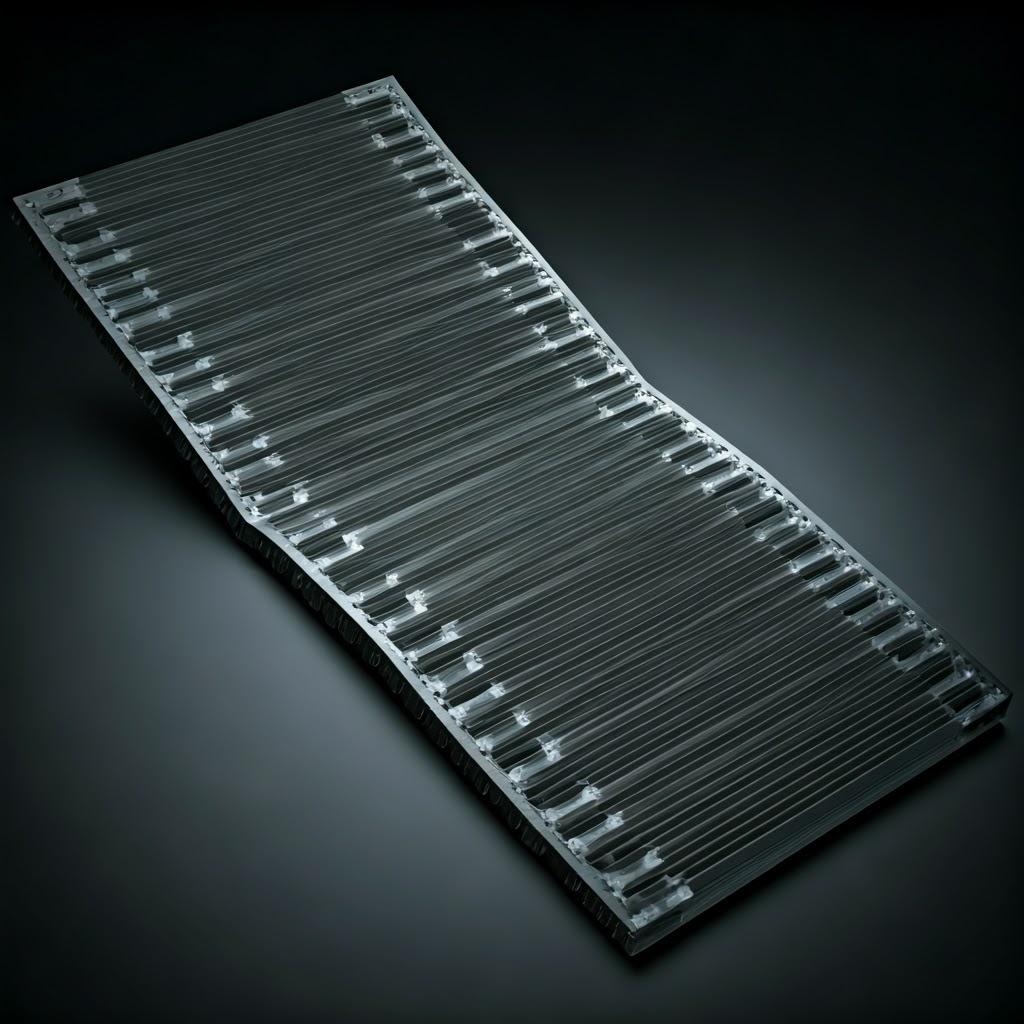
The AM Advantage: Why Use Metal 3D Printing for Satellite Radiator Panels?
The limitations inherent in traditional manufacturing methods for satellite radiator panels—namely weight constraints, design restrictions, long lead times, and assembly complexities—are precisely the areas where Metal Additive Manufacturing (AM) offers significant, often game-changing, advantages. By fundamentally rethinking the design and fabrication process, metal 3D printing enables the creation of next-generation thermal control components that are lighter, more efficient, and faster to produce. For aerospace engineers and procurement specialists focused on optimizing satellite performance and mission cost-effectiveness, understanding these benefits is crucial.
Key Advantages of Metal AM for Radiator Panels:
- Mass Reduction through Optimization: This is arguably the most compelling advantage. Launch costs remain a dominant factor in space missions. Metal AM allows for:
- Optimisation de la topologie : Using specialized software, designers can define loads, constraints, and performance objectives (e.g., stiffness, heat transfer) and allow algorithms to remove material from non-critical areas, resulting in highly efficient, organic-looking structures that meet requirements with minimal mass. Weight savings of 20-50% or even more compared to traditionally machined parts are commonly reported.
- Structures en treillis : Internal lattice or cellular structures can replace solid sections, drastically reducing weight while maintaining necessary structural integrity and potentially enhancing fluid flow characteristics or surface area for heat transfer within internal channels.
- Liberté de conception sans précédent : AM builds parts layer by layer, freeing designers from many constraints imposed by subtractive (machining) or formative (casting, forging) processes. This enables:
- Complex Internal Geometries: Highly optimized, smoothly curved internal channels for fluid coolants or integrated conduits mimicking heat pipe layouts can be printed directly into the panel structure. This eliminates the need for complex embedding, brazing, or bonding processes, improving thermal efficiency and reliability.
- Conformal and Shaped Radiators: Panels can be designed to conform precisely to the available curved surfaces of the satellite body, maximizing radiating area within a given volume envelope, an often impossible feat with traditional flat-panel assemblies.
- Caractéristiques intégrées : Mounting brackets, structural reinforcements, sensor housings, and fluid ports can be built directly into the radiator panel as a single monolithic part.
- Consolidation partielle : By integrating multiple functions and features into a single printed component, AM drastically reduces the number of individual parts required for a radiator assembly. This leads to:
- Reduced Assembly Time and Cost: Fewer parts mean less time spent on joining, fastening, and inspecting interfaces.
- Improved Reliability: Eliminating joints (brazed, bonded, or fastened) removes potential leak paths and failure points, crucial for long-duration missions in the harsh space environment.
- Simplified Supply Chain: Managing fewer part numbers simplifies procurement, inventory, and logistics.
- Prototypage rapide et itération : AM allows for the direct fabrication of functional prototypes from CAD models in days rather than weeks or months. This accelerates the design-build-test cycle significantly, allowing engineers to:
- Quickly validate thermal and structural performance through physical testing.
- Iterate on designs rapidly based on test results to achieve optimal performance before committing to final flight hardware.
- Reduce development risks and overall time-to-launch.
- Enhanced Thermal Performance: The design freedom offered by AM enables novel approaches to improve heat transfer:
- Optimized Internal Channels: Fluid channels can be designed with complex cross-sections, turbulators, or internal finning to enhance convective heat transfer coefficients and minimize pressure drop.
- Increased Surface Area: Micro-features or complex lattice structures can potentially increase the effective radiating surface area or improve heat spreading within the panel substrate.
- Multi-Material Potential (Future): While still developing, future AM processes might allow printing different materials within the same part, enabling functionally graded materials optimized for both structural integrity and thermal conductivity in specific regions.
Comparison: Metal AM vs. Traditional Manufacturing for Radiator Panels
Fonctionnalité | Traditional Manufacturing (e.g., CNC Machining, Brazing) | Metal Additive Manufacturing (e.g., LPBF) | Advantage of AM |
---|---|---|---|
Poids | Often constrained by machinability, standard stock sizes | Highly optimizable via topology/lattices | Significant mass savings (20-50%+) |
Complexité de la conception | Limited internal features, mostly planar/simple curves | Complex internal channels, conformal shapes feasible | Enables highly integrated, performance-optimized designs |
Part Count | Multiple components requiring assembly (face sheets, core, pipes, brackets) | Potential for single monolithic part integration | Reduced assembly time, cost, and improved reliability |
Délai d'exécution | Weeks/Months (machining, tooling, assembly, inspection) | Days/Weeks (for prototypes), potentially faster production | Accelerated development cycles, faster time-to-flight |
Déchets matériels | High (subtractive processes like machining) | Low (additive process, powder recycling) | More sustainable, lower raw material cost impact (though powder is expensive) |
Thermal Perf. | Limited by assembly methods, standard channel shapes | Optimized internal geometries, potentially higher efficiency | Potential for improved heat dissipation |
Coût initial | Can be lower for very simple, high-volume parts | Higher equipment/powder cost, cost-effective for complex/low-vol | Best suited for high-value, complex, or custom components like satellite parts |
Exporter vers les feuilles
Pour procurement managers evaluating aerospace manufacturing suppliers, partnering with a provider skilled in metal 3D printing for aerospace offers a pathway to acquiring components that meet stringent performance requirements while potentially reducing launch costs and accelerating project timelines. The shift towards additive manufacturing for satellite components is not just a trend; it’s a strategic imperative for staying competitive in the demanding space sector.
Material Matters: Recommended Metal Powders (AlSi10Mg, CuCrZr) and Their Aerospace Significance
Choosing the right material is fundamental to the success of any engineering application, and this holds particularly true for satellite radiator panels manufactured via metal Additive Manufacturing (AM). The material must not only possess the required thermal and mechanical properties but also be readily processable using AM techniques like Laser Powder Bed Fusion (LPBF), also known as Selective Laser Melting (SLM). Furthermore, the quality of the metal powder feedstock is paramount, directly influencing the final part’s density, microstructure, and performance – a critical consideration for high-reliability aerospace applications. Two materials stand out for their potential in 3D printed satellite radiators: AlSi10Mg (an aluminum alloy) and CuCrZr (a copper alloy).
AlSi10Mg: The Lightweight Workhorse
AlSi10Mg is one of the most commonly used aluminum alloys in metal AM, particularly LPBF. It’s essentially a casting alloy adapted for additive processes, known for its excellent combination of low density, good mechanical properties, and favorable thermal characteristics for many applications.
- Key Properties and Aerospace Relevance:
- Faible densité : Approximately 2.67 g/cm³. This is a primary driver for its use in aerospace, where minimizing mass is crucial for reducing launch costs. Radiator panels can constitute a significant portion of a satellite’s dry mass, making lightweighting highly beneficial.
- Good Thermal Conductivity: While not as high as pure aluminum or copper alloys, AlSi10Mg offers thermal conductivity typically in the range of 100-130 W/(m·K) after appropriate heat treatment. This is often sufficient for effectively spreading and radiating heat in many satellite applications, especially when combined with embedded heat pipes or optimized internal fluid channels enabled by AM.
- Excellent Processability: AlSi10Mg exhibits good behavior during LPBF processing, with relatively low laser reflectivity and good melt pool stability, allowing for the production of dense (>99.8%) and intricate parts.
- Good Mechanical Properties: It offers a good balance of strength (Yield Strength ~230-280 MPa, Tensile Strength ~350-450 MPa after heat treatment) and ductility, sufficient for handling launch loads and providing structural integrity.
- Résistance à la corrosion : Exhibits good corrosion resistance, suitable for ground handling and pre-launch environments.
- Considérations :
- Its thermal conductivity, while good for an aluminum alloy, may be insufficient for very high heat flux applications without augmentation (e.g., heat pipes).
- Like many aluminum alloys, its strength decreases at elevated temperatures, which must be considered in the thermal design.
AlSi10Mg Properties Summary (Typical values after T6-like heat treatment)
Propriété | Valeur typique | Unité | Significance for Radiators |
---|---|---|---|
Densité | ~2.67 | g/cm³ | Critical for weight reduction / lower launch cost |
Conductivité thermique | ~100 – 130 | W/(m-K) | Good heat spreading capability |
Yield Strength (Rp0.2) | ~230 – 280 | MPa | Structural integrity during launch and operation |
Tensile Strength (Rm) | ~350 – 450 | MPa | Overall strength |
Allongement à la rupture | ~3 – 10 | % | Ductility, resistance to fracture |
Coefficient de dilatation thermique (CTE) | ~20 – 22 | µm/(m·K) | Important for thermal stress analysis & interface matching |
Processability via LPBF | Excellent | – | Enables complex geometries and high-quality builds |
Exporter vers les feuilles
CuCrZr: The High-Conductivity Specialist
When extremely efficient heat removal is paramount, copper alloys become attractive candidates due to their inherently superior thermal conductivity. CuCrZr (Copper-Chromium-Zirconium) is a high-performance precipitation-hardening alloy known for retaining good mechanical strength at elevated temperatures compared to pure copper, while offering excellent thermal and electrical conductivity.
- Key Properties and Aerospace Relevance:
- Very High Thermal Conductivity: Typically in the range of 300-340 W/(m·K), nearly triple that of AlSi10Mg. This makes it ideal for managing high heat fluxes or applications where minimizing temperature gradients is critical. It allows for more compact radiator designs for a given heat load.
- Good High-Temperature Strength: Unlike pure copper, CuCrZr retains significant strength at temperatures up to 400-500°C, making it suitable for components operating under demanding thermal loads.
- Excellent Electrical Conductivity: While less relevant for radiators, this property makes it useful for other AM applications like heat sinks for electronics or induction coils.
- Considérations :
- Higher Density: With a density of approximately 8.9 g/cm³, CuCrZr is significantly heavier than AlSi10Mg. Its use must be justified by thermal performance requirements outweighing the mass penalty. Often used selectively in high-heat flux zones or for internal cooling channels where its conductivity is most needed.
- AM Processing Challenges: Printing copper alloys like CuCrZr via LPBF is more challenging than aluminum due to copper’s high reflectivity to the infrared lasers typically used and its high thermal conductivity, which can lead to melt pool instability and requires higher laser power and specialized process parameters. Oxidation is also a concern, requiring excellent atmospheric control within the printer. Successfully printing dense, high-quality CuCrZr parts requires specialized expertise and optimized equipment.
- Coût plus élevé : Copper alloy powders are generally more expensive than aluminum alloy powders.
CuCrZr Properties Summary (Typical values after aging heat treatment)
Propriété | Valeur typique | Unité | Significance for Radiators |
---|---|---|---|
Densité | ~8.9 | g/cm³ | Significant mass penalty compared to Al; use strategically |
Conductivité thermique | ~300 – 340 | W/(m-K) | Excellent for high heat flux & efficient heat transfer |
Yield Strength (Rp0.2) | ~350 – 450 | MPa | Good strength, especially at elevated temperatures |
Tensile Strength (Rm) | ~450 – 550 | MPa | High overall strength |
Allongement à la rupture | ~10 – 20 | % | Bonne ductilité |
Coefficient de dilatation thermique (CTE) | ~17 – 18 | µm/(m·K) | Lower than Al, important for interface design |
Processability via LPBF | Défi | – | Requires specialized equipment and process control |
Exporter vers les feuilles
The Critical Role of Powder Quality – Met3dp’s Expertise
For demanding aerospace applications like satellite radiators, the quality of the input metal powder is non-negotiable. Powder characteristics directly impact the consistency, density, microstructure, and ultimately, the mechanical and thermal performance of the final AM component. Key powder attributes include:
- Sphéricité : Highly spherical powder particles ensure good flowability, leading to uniform powder bed layers and consistent melting.
- Distribution de la taille des particules (PSD) : A controlled PSD is crucial for achieving high packing density in the powder bed, minimizing porosity in the final part.
- La pureté : Low levels of impurities and contaminants (especially oxygen) are vital for achieving desired material properties and preventing defects.
- Fluidité : Consistent powder flow ensures uniform deposition across the build plate.
This is where specialized powder manufacturers and AM solution providers like Met3dp play a critical role. Met3dp leverages industry-leading powder production technologies, such as Vacuum Induction Melting Gas Atomization (VIGA) et Procédé d'électrodes rotatives à plasma (PREP). These advanced systems, featuring unique nozzle designs and controlled atmospheres, produce high-quality spherical metal powders with high purity, excellent flowability, and controlled PSDs, optimized for demanding AM processes like LPBF and Electron Beam Melting (EBM). Met3dp’s commitment extends to producing a wide range of standard and innovative alloys, including aerospace-grade aluminum alloys and potentially customized copper alloys like CuCrZr, tailored to specific customer requirements. Their extensive portfolio of high-performance metal powders and 3D printing products ensures that engineers and procurement managers have access to materials that meet the stringent quality demands of the space industry. Partnering with a supplier that controls both the powder manufacturing and the printing process can provide significant advantages in consistency and quality assurance.
Material selection for an AM satellite radiator involves a trade-off, primarily between the low weight of AlSi10Mg and the high thermal conductivity of CuCrZr, balanced against processability and cost. Often, the optimal solution might involve using AlSi10Mg for the main structure due to weight constraints and potentially integrating CuCrZr elements in specific high-heat flux areas if feasible through advanced multi-material AM or assembly, or designing highly efficient internal channels within an AlSi10Mg structure using the design freedom of AM.
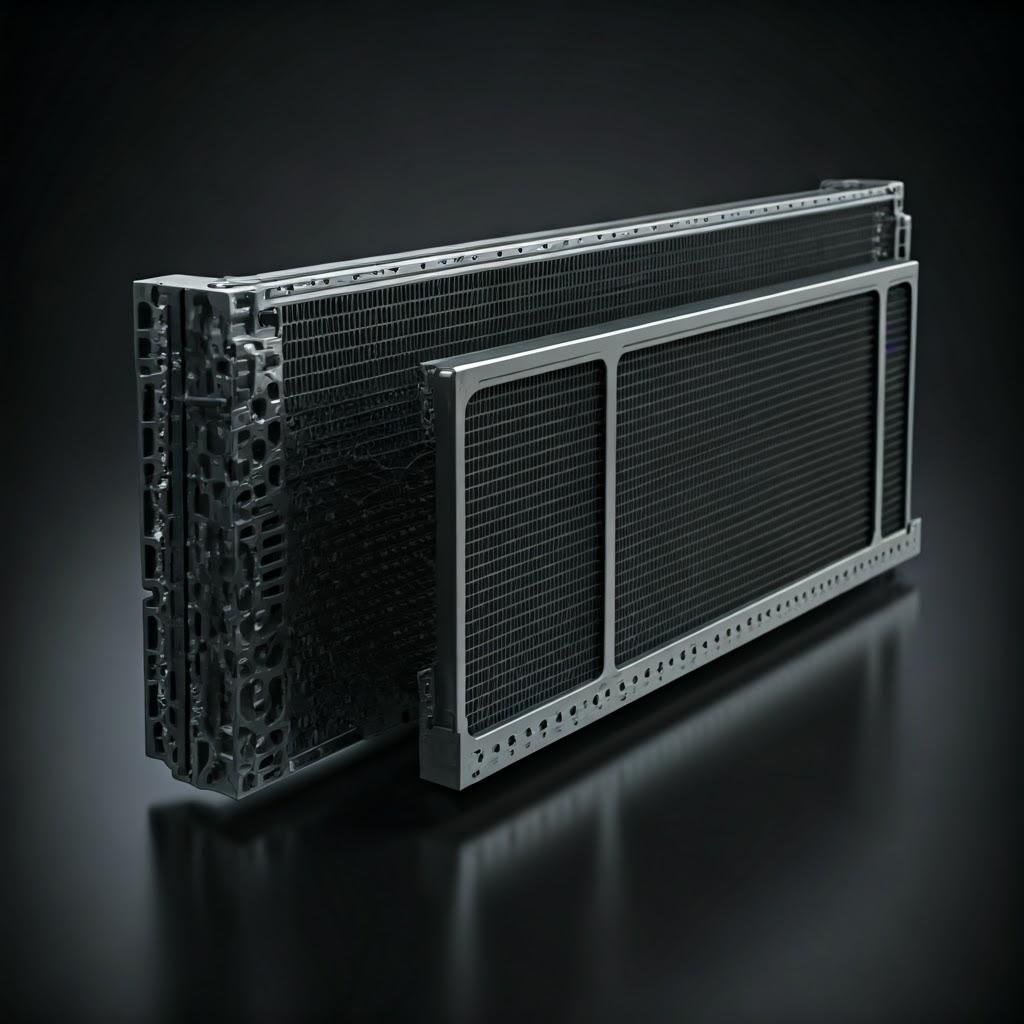
Design for Orbit: Key Design Considerations for AM Radiator Panels
Metal Additive Manufacturing (AM) unlocks tremendous potential for optimizing satellite radiator panels, but realizing these benefits requires a shift in design thinking. Simply transferring a design intended for conventional manufacturing to a 3D printer rarely yields optimal results and can even lead to build failures. Instead, engineers must embrace Conception pour la fabrication additive (DfAM) principles. DfAM involves designing parts specifically to leverage the strengths and accommodate the constraints of the chosen AM process, in this case, primarily Laser Powder Bed Fusion (LPBF) for materials like AlSi10Mg and CuCrZr. Designing “for orbit” using DfAM for radiator panels means focusing on lightweighting, thermal performance, manufacturability, and reliability in the context of the space environment.
Key DfAM Principles for AM Radiator Panels:
- Leverage Topology Optimization and Generative Design:
- These computational tools are essential for achieving significant mass reduction. Engineers define package space, load cases (e.g., launch vibrations, structural loads), material properties, and performance goals (e.g., maximize stiffness, minimize mass).
- The software then generates highly efficient, often organic-looking structures that distribute material only where needed.
- For radiators, this can be applied to the main panel structure, mounting brackets, and support ribs, ensuring structural integrity with minimal weight. It requires careful definition of keep-out zones for heat pipes, fluid channels, and mounting interfaces.
- Optimize Internal Channels and Fluid Paths:
- AM allows the creation of complex, smoothly curved internal channels directly within the panel structure, eliminating the need for assembling separate tubes or manifolds.
- Considérations relatives à la conception :
- Smooth Bends: Avoid sharp corners to minimize pressure drop and ensure smooth fluid flow.
- Self-Supporting Shapes: Design channel cross-sections (e.g., diamond, teardrop) that minimize the need for internal support structures, which are difficult or impossible to remove. Overhang angles typically need to be greater than 45 degrees from the horizontal plane for support-free printing, although this varies with process parameters and feature size.
- Elimination des poudres : Ensure channels have adequate entry/exit points and pathways for efficient removal of unfused powder after the build. Design features like internal chamfers can aid powder drainage. Trapped powder is a critical failure risk.
- Épaisseur de la paroi : Maintain sufficient wall thickness around channels to ensure pressure integrity and prevent leakage, considering the minimum printable feature size of the AM system.
- Thermal Enhancement: Consider incorporating internal fins, turbulators, or complex geometries (like triply periodic minimal surfaces – TPMS) within channels to enhance convective heat transfer from the fluid to the radiator walls.
- Integrate Functionality (Part Consolidation):
- Actively look for opportunities to combine multiple parts into a single printed component.
- Exemples : Integrate mounting flanges, alignment features, structural supports, sensor housings, or fluid connectors directly into the radiator panel design.
- Avantages : Reduces assembly effort, eliminates potential leak paths/failure points at joints, simplifies supply chain management for aerospace procurement teams.
- Manage Overhangs and Support Structures:
- LPBF requires support structures for features overhanging the build plate at angles typically less than 45 degrees. Supports anchor the part, prevent warping, and conduct heat away during printing.
- Stratégies de conception :
- Minimize Supports: Orient the part on the build plate to minimize the number and volume of overhangs requiring support. This reduces material waste, build time, and post-processing effort.
- Design for Removal: Ensure supports are accessible for easy removal without damaging the part surface. Consider sacrificial layers or features that simplify detachment. Support design itself (e.g., perforated, thin contact points) impacts removability.
- Angles autoportants : Where possible, design features with angles greater than 45 degrees. Small holes or horizontal features may require specific design adjustments or supports.
- Thermal Considerations: Supports influence local cooling rates. Dense supports may be needed in critical areas to prevent thermal distortion, especially with high-conductivity materials like CuCrZr.
- Minimum Feature Sizes and Wall Thickness:
- Understand the limitations of the specific LPBF machine and process parameters regarding the smallest features (holes, slots, thin walls, sharp corners) that can be reliably produced.
- Typical minimum wall thickness for structural integrity might be around 0.4 – 1.0 mm, but this depends heavily on the aspect ratio and material.
- Ensure radiator face sheets and internal channel walls meet these minimums while optimizing for weight and thermal performance.
- Design for the Space Environment:
- Consider factors like thermal cycling fatigue (repeated expansion/contraction between sunlight and shadow), potential radiation effects on material properties (though less critical for metals than polymers), and outgassing requirements (ensure no trapped volumes or materials that could release contaminants in vacuum).
- Design interfaces to accommodate Coefficient of Thermal Expansion (CTE) mismatches between the radiator panel (e.g., AlSi10Mg or CuCrZr) and adjoining structures or components (like embedded heat pipes if applicable).
DfAM Considerations Specific to Radiator Materials:
- AlSi10Mg : Generally easier to design for due to good processability. Supports are relatively easy to remove. Thermal conductivity allows for efficient heat spreading, making topology optimization effective.
- CuCrZr: Higher thermal conductivity requires careful management of heat buildup during printing, potentially needing more extensive support structures. Supports can be more challenging to remove due to copper’s ductility. Design should maximize the benefit of high conductivity (e.g., targeted use in high-flux zones, optimized thin-walled channel designs) to justify the mass and processing challenges.
By integrating these DfAM principles early in the design phase, engineers can fully exploit the advantages of metal AM, creating lightweight, high-performance, reliable satellite radiator panels optimized for the demands of orbit. Collaboration with experienced metal AM service providers who possess strong DfAM expertise is often crucial for success.
Precision in Space: Achieving Tight Tolerances, Surface Finish, and Dimensional Accuracy
For satellite components, precision is not optional; it’s a fundamental requirement. Radiator panels must interface correctly with satellite structures, heat pipes, fluid connectors, and potentially deployable mechanisms. Critical dimensions, flatness specifications, and surface characteristics must meet stringent aerospace standards to ensure proper assembly, thermal contact, and reliable operation over the mission lifetime. While metal Additive Manufacturing (AM) offers incredible design freedom, achieving the required levels of precision demands careful control throughout the entire process, from design and simulation to printing and post-processing. Understanding the achievable precision and the factors influencing it is vital for engineers and procurement managers specifying AM components.
Key Definitions:
- Précision dimensionnelle : How closely the final part dimensions conform to the nominal dimensions specified in the CAD model.
- Tolerance: The permissible range of variation for a given dimension. Aerospace components often require tolerances in the range of tens to hundreds of micrometers (µm) for critical features.
- Surface Finish/Roughness (Ra): A measure of the texture of a surface, typically expressed as the arithmetic average of the surface profile deviations from a mean line. Lower Ra values indicate smoother surfaces. As-built AM surfaces are typically rougher than machined surfaces.
Achievable Precision with LPBF:
Laser Powder Bed Fusion (LPBF), the most common process for AlSi10Mg and CuCrZr, can achieve good dimensional accuracy, but it’s crucial to understand the typical ranges and influencing factors.
- Tolérances générales : For well-controlled processes, typical achievable dimensional tolerances for as-built LPBF parts are often cited in the range of ±0.1 mm to ±0.2 mm or ±0.1% to ±0.2% of the dimension, whichever is larger. However, achieving tighter tolerances (e.g., ±0.05 mm or better) usually requires secondary machining operations on critical features.
- Surface Finish (Ra):
- As-Built: LPBF surfaces have a characteristic roughness due to the partially melted powder particles adhering to the surface and the layer-wise construction. As-built Ra typically ranges from 6 µm to 20 µm, depending on material, parameters, build orientation (upward-facing, downward-facing, vertical walls), and feature geometry.
- Post-Processed: Surface finish can be significantly improved through various post-processing techniques like bead blasting, tumbling, chemical polishing, electro-polishing, or CNC machining, potentially achieving Ra values below 1 µm where required.
Factors Influencing Accuracy and Finish:
Achieving consistent precision in metal AM is a complex interplay of multiple factors:
- Machine Calibration and Condition: Regular calibration of the laser system (power, focus, spot size), scanner system (positioning accuracy), and gas flow is essential. Machine stability and build environment control (temperature, oxygen levels) are critical. High-quality, reliable printing equipment, like the systems developed and utilized by experienced providers, forms the foundation for precision.
- Paramètres du processus : Laser power, scan speed, layer thickness, hatch spacing, and scan strategy significantly impact melt pool dynamics, cooling rates, and ultimately, dimensional accuracy and surface finish. Optimized parameter sets, often specific to the material and machine, are crucial.
- Orientation de la construction : The orientation of the part on the build plate affects:
- Support structure requirements (influencing surface quality where supports attach).
- Thermal gradients and potential for warping/distortion.
- Surface finish variation (downward-facing surfaces are typically rougher than upward-facing or vertical walls).
- Dimensional accuracy along different axes (Z-axis accuracy can differ from X-Y accuracy).
- Contraintes thermiques : The rapid heating and cooling cycles inherent in LPBF generate internal stresses that can cause part distortion (warping) during the build or after removal from the plate. Simulation tools can help predict and mitigate this through optimized orientation and support strategies.
- Propriétés du matériau : The material’s thermal conductivity, reflectivity (especially for CuCrZr), and shrinkage characteristics influence process stability and final accuracy.
- Géométrie de la pièce : Complex geometries, thin walls, large flat sections, and sharp corners can be more prone to distortion and accuracy deviations.
- Caractéristiques de la poudre : Consistent powder quality (particle size distribution, morphology, flowability) ensures uniform powder layers and stable melting.
- Post-traitement :
- Soulagement du stress : Heat treatment to relieve internal stresses is crucial before removing parts from the build plate to minimize distortion.
- Suppression du support : Can sometimes affect surface finish or dimensions at contact points if not done carefully.
- Usinage : While used to achieve the tightest tolerances and best finishes on critical features, machining itself must be precise and account for potential part deflection if not fixtured correctly.
- HIP (Hot Isostatic Pressing): Can cause minor, predictable shrinkage that must be accounted for in the initial design.
Meeting Aerospace Quality Requirements:
Ensuring that 3D printed radiator panels meet stringent aerospace quality control standards requires a robust quality management system and thorough verification:
- Métrologie : Precise measurement of critical dimensions using Coordinate Measuring Machines (CMMs) or high-resolution 3D scanners.
- Mesure de la rugosité de surface : Using profilometers to verify surface finish specifications.
- Essais non destructifs (END) : Techniques like X-ray or Computed Tomography (CT) scanning are invaluable for inspecting internal features (like cooling channels for blockages or defects) and verifying overall part integrity without damaging it. CT scanning provides full volumetric data for dimensional analysis of internal geometries.
- Surveillance des processus : In-situ monitoring of the build process (e.g., melt pool monitoring) can provide valuable data for quality assurance and process control.
Achieving the necessary precision for space applications requires not just advanced technology but also deep process knowledge and rigorous quality control. Partnering with an established and reliable metal AM supplier, one with a proven track record in aerospace and robust quality systems, is paramount. Understanding a potential partner’s capabilities, certifications (like AS9100), and approach to quality assurance is a key responsibility for procurement teams. For insights into the commitment required, exploring the background of established companies can be beneficial; learning about Met3dp and their focus on industry-leading accuracy and reliability provides context on what to look for in a supplier dedicated to mission-critical components.
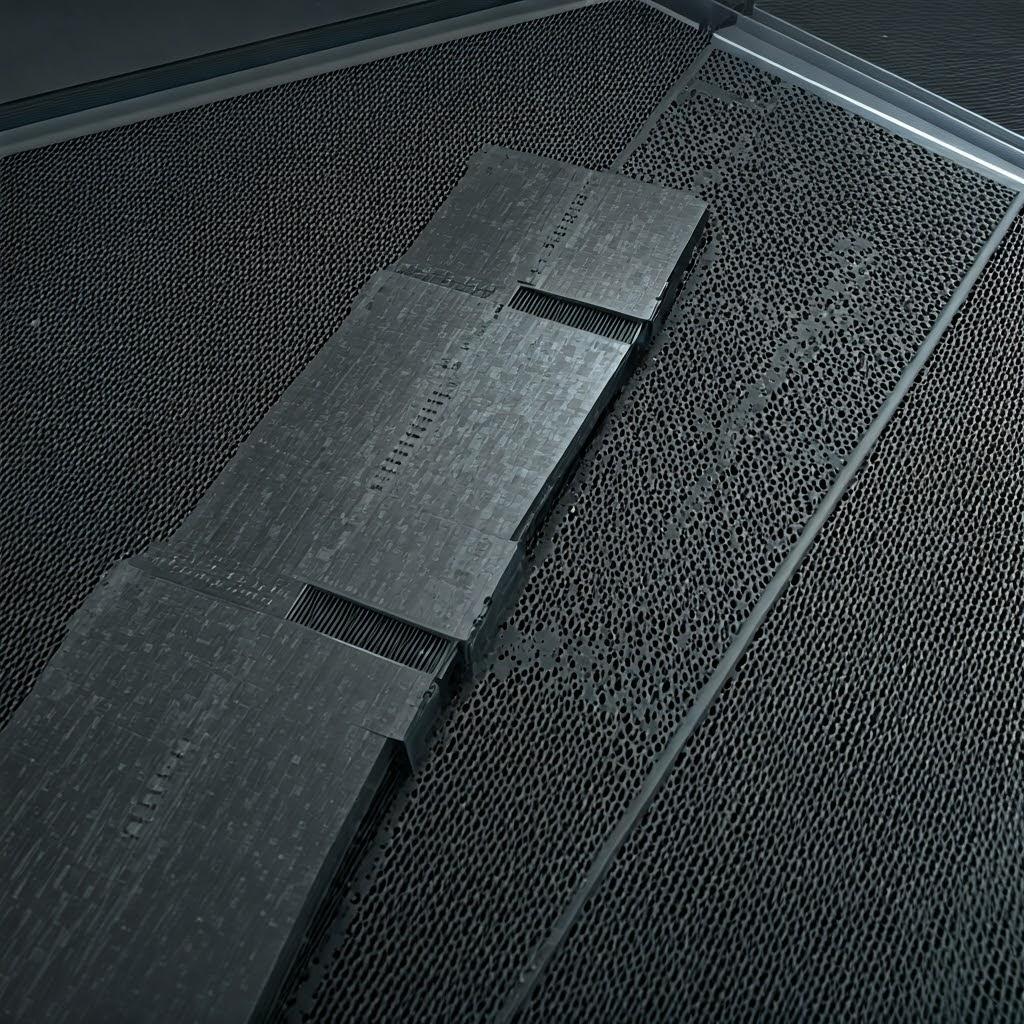
Beyond the Build: Essential Post-Processing for 3D Printed Radiator Panels
A common misconception about metal Additive Manufacturing (AM) is that parts come out of the printer ready for immediate use. While AM creates the near-net shape, a series of crucial post-processing steps are almost always required, especially for demanding applications like satellite radiator panels. These steps are essential to relieve internal stresses, remove support structures, achieve the required dimensional tolerances and surface finish, ensure material properties meet specifications, and prepare the part for integration and its operational environment. Ignoring or improperly executing these steps can compromise the structural integrity, thermal performance, and overall reliability of the component.
Typical Post-Processing Workflow for AM Radiator Panels:
The specific steps and their order can vary based on the material (AlSi10Mg vs. CuCrZr), part complexity, and application requirements, but a typical workflow includes:
- Stress Relief Heat Treatment (In-Situ or Post-Build):
- Objet : To reduce the internal stresses built up during the rapid heating and cooling cycles of the LPBF process. These stresses can cause warping, distortion upon removal from the build plate, and potentially cracking.
- Procédure : Typically involves heating the part (often while still attached to the build plate) in a controlled atmosphere furnace to a specific temperature (below the material’s annealing or aging temperature), holding it for a set duration, and then cooling slowly. Parameters are material-specific (e.g., ~300°C for AlSi10Mg, potentially higher for CuCrZr).
- Importance: Absolutely critical for maintaining dimensional stability and preventing premature failure.
- Retrait de la pièce de la plaque de construction :
- Procédure : Once stress-relieved, the part is separated from the build plate. This is commonly done using electrical discharge machining (EDM) wire cutting, sawing, or machining.
- Considérations : Must be done carefully to avoid damaging the part. The interface layer between the part and plate often requires subsequent finishing.
- Retrait de la structure de soutien :
- Objet : To remove the temporary structures used to anchor the part and support overhanging features during the build.
- Procédure : Can involve manual breaking/cutting (for accessible, well-designed supports), CNC machining, grinding, or sometimes EDM. This can be labor-intensive and requires skill to avoid damaging the part surface.
- Défis : Accessing internal supports (if unavoidable) can be extremely difficult. Support contact points often leave witness marks (“nubs”) that require further finishing. DfAM plays a huge role in simplifying support removal.
- Further Heat Treatment (Optional but Common for Aerospace):
- Pressage isostatique à chaud (HIP) :
- Objet : To eliminate internal porosity (micro-voids) and improve material density, leading to enhanced mechanical properties (especially fatigue strength and ductility) and ensuring vacuum integrity.
- Procédure : Subjects the part to high temperature (below melting point) and high inert gas pressure (e.g., Argon) simultaneously in a specialized HIP vessel.
- Relevance: Often mandatory for critical aerospace components to ensure maximum material integrity and reliability. Can cause slight, predictable shrinkage (~1%) that must be accounted for in the design phase.
- Solution Annealing and Aging (for Precipitation Hardening Alloys):
- Objet : To optimize the microstructure and achieve the desired final mechanical properties (strength, hardness, ductility) for alloys like AlSi10Mg (T6 condition) and CuCrZr.
- Procédure : Involves specific temperature cycles (solutionizing, quenching, aging) tailored to the alloy.
- Pressage isostatique à chaud (HIP) :
- Machining / Surface Finishing:
- Objet : To achieve tight tolerances on critical dimensions (e.g., mounting interfaces, sealing surfaces), improve surface finish for specific functions (e.g., thermal contact, coating adhesion), and remove witness marks from supports or the build plate interface.
- Procédure : CNC machining (milling, turning, grinding) is commonly used for high precision. Other methods like bead blasting, sandblasting, tumbling, or polishing can be used for general surface smoothing or achieving specific textures.
- Importance: Essential for ensuring proper fit, form, and function within the satellite assembly.
- Nettoyage :
- Objet : To remove any remaining unfused powder (especially from internal channels), machining fluids, debris, or contaminants.
- Procédure : May involve compressed air blowing, ultrasonic cleaning in specific solvents, and thorough inspection (sometimes borescope inspection for internal channels).
- Importance: Critical for preventing contamination within the satellite and ensuring clear passages for fluid flow if applicable. Trapped powder is a major concern for flight hardware.
- Inspection and Quality Control:
- Objet : To verify dimensional accuracy, surface finish, internal integrity, and material properties.
- Procédure : Includes dimensional metrology (CMM, 3D scanning), surface roughness testing, NDT (X-ray, CT scanning, potentially penetrant testing), and material testing (e.g., tensile tests on representative samples).
- Importance: Final verification that the part meets all specifications before delivery and integration. Rigorous aerospace quality control n'est pas négociable.
- Surface Coating Application:
- Objet : To apply specialized thermal coatings required for radiator functionality in space.
- Procédure : Application of high-emissivity paints (e.g., white paints like AZ-93, black paints) or bonding of Optical Solar Reflectors (OSRs) or silvered Teflon films. Requires specific surface preparation (cleanliness, sometimes specific roughness) for proper adhesion.
- Importance: Directly impacts the radiator’s thermal performance (heat rejection capability and solar absorption).
Each of these steps requires specialized equipment, expertise, and careful process control. When selecting a metal AM service bureau ou manufacturing partner, procurement managers and engineers must evaluate their in-house post-processing capabilities or their established relationships with qualified subcontractors. A vertically integrated provider or one with strong supply chain management for these critical steps can significantly streamline the production process and ensure consistent quality for custom satellite components.
Navigating Challenges: Overcoming Hurdles in AM Radiator Panel Production
While metal Additive Manufacturing offers compelling advantages for satellite radiator panels, the technology is not without its challenges. Producing high-quality, reliable aerospace components requires a deep understanding of potential issues and robust strategies to mitigate them. Awareness of these hurdles allows engineers and procurement teams to ask the right questions when evaluating suppliers and setting realistic expectations for development and production. Key challenges often revolve around process control, material behavior, and achieving the stringent quality demands of the space industry.
Défis communs et stratégies d'atténuation :
Défi | Common Causes | Stratégies d'atténuation |
---|---|---|
Warping / Distortion | Uneven heating/cooling leading to high residual thermal stresses, insufficient support structure, poor part orientation. | Simulation : Use build simulation software to predict stress and distortion, informing optimal orientation and support strategies. <br> Orientation: Choose orientation to minimize large flat areas parallel to the recoater and manage heat buildup. <br> Supports: Use robust, well-designed support structures and potentially anchors to secure the part. <br> Soulagement du stress : Perform stress relief heat treatment before removing from the build plate. |
Contrainte résiduelle | Inherent rapid solidification characteristic of LPBF, steep thermal gradients between melt pool and surrounding material. | Optimisation des processus : Fine-tune laser parameters (power, speed, scan strategy) to minimize thermal gradients. <br> Traitement thermique : Mandatory stress relief cycle. <br> Conception : Incorporate features that accommodate or minimize stress concentration (e.g., rounded corners). |
Cracking (Solidification/Liquation) | High thermal stresses exceeding material strength, susceptible alloy compositions, impurities, rapid cooling. | Parameter Tuning: Optimize parameters to control cooling rates. <br> Sélection des matériaux : Choose alloys less prone to hot tearing if possible, or ensure high powder purity. <br> Build Strategy: Modify scan patterns or use pre-heating (if available) to reduce thermal shock. <br> Post-traitement : HIP can sometimes close micro-cracks, but preventing them is preferred. |
Porosity (Gas / Keyhole / Lack of Fusion) | Gas: Trapped shielding gas or dissolved gas in powder released during melting. <br> Keyhole: Excessive laser energy density causing melt pool instability and vapor depression collapse. <br> Lack of Fusion: Insufficient energy density leading to incomplete melting between layers or scan tracks. | Qualité de la poudre : Use high-purity powder with low trapped gas content, ensure proper storage and handling to avoid moisture pickup. <br> Optimisation des paramètres : Crucial to find the right balance of laser power, speed, and hatch spacing for full densification without keyholing. Requires extensive process development. <br> Atmosphere Control: Maintain high-purity inert gas environment in the build chamber (<1000 ppm O2, often much lower). <br> HIP: Effective at closing gas and some lack-of-fusion porosity, often required for critical parts. |
Support Removal Difficulty | Poorly designed supports (too dense, strong contact points), difficult-to-access locations, ductile materials (like CuCrZr). | DfAM : Design for support minimization and ease of access. Use optimized support structures (e.g., conical, perforated). <br> Parameter Tuning: Optimize support interface parameters for easier detachment. <br> Techniques de post-traitement : Utilize appropriate tools and potentially multi-axis machining or EDM for removal. |
Surface Finish Variation | Build orientation (down-skins vs. up-skins vs. vertical walls), laser parameters, powder particle adhesion (“spatter”). | Orientation: Optimize part orientation considering critical surfaces. <br> Parameter Refinement: Use specific contour or skin parameters to improve surface quality. <br> Post-traitement : Employ appropriate finishing techniques (blasting, polishing, machining) targeting required Ra values. |
Powder Management & Handling | Contamination (cross-material, debris), moisture absorption, degradation through repeated recycling. | Strict Protocols: Implement rigorous procedures for powder handling, storage (inert atmosphere, controlled temperature/humidity), sieving, and traceability. <br> Contrôle de la qualité : Regularly test recycled powder properties. Limit the number of reuse cycles based on testing and application criticality. <br> Dedicated Equipment: Use dedicated handling equipment for different materials to prevent cross-contamination. |
Consistency & Repeatability | Variations in machine calibration, powder batches, environmental conditions, operator factors. | Un système de gestion de la qualité robuste : Implement a strong Quality Management System (e.g., AS9100) with strict process controls. <br> Surveillance des processus : Utilize available in-situ monitoring tools. <br> Regular Calibration & Maintenance: Maintain equipment rigorously. <br> Normalisation : Standardize operating procedures and operator training. <br> Validation des processus : Thoroughly validate the entire process chain for specific part/material combinations. |
Exporter vers les feuilles
Addressing Challenges with AlSi10Mg and CuCrZr:
- AlSi10Mg : Relatively well-understood and processable. Key challenges often relate to managing residual stress in complex geometries and ensuring consistent properties through heat treatment. Porosity control is crucial but achievable with optimized parameters.
- CuCrZr: More challenging due to high reflectivity and conductivity. Requires higher laser power, careful parameter development to avoid keyholing and ensure fusion, excellent gas shielding to prevent oxidation, and potentially specialized green or blue lasers. Support removal requires care due to ductility. Risk mitigation strategies are particularly important when working with copper alloys.
Successfully navigating these challenges requires significant expertise in materials science, process engineering, and quality control. This underscores the importance of collaborating with experienced manufacturing partners who have invested in the necessary technology, personnel, and quality systems. Companies committed to advancing industrial AM, like those found across the industry landscape, continuously work to refine processes and overcome these hurdles, pushing the boundaries of what’s possible in aerospace manufacturing. Exploring the websites of established providers, such as the homepage https://met3dp.com/, can offer insights into the types of solutions and expertise available in the market.
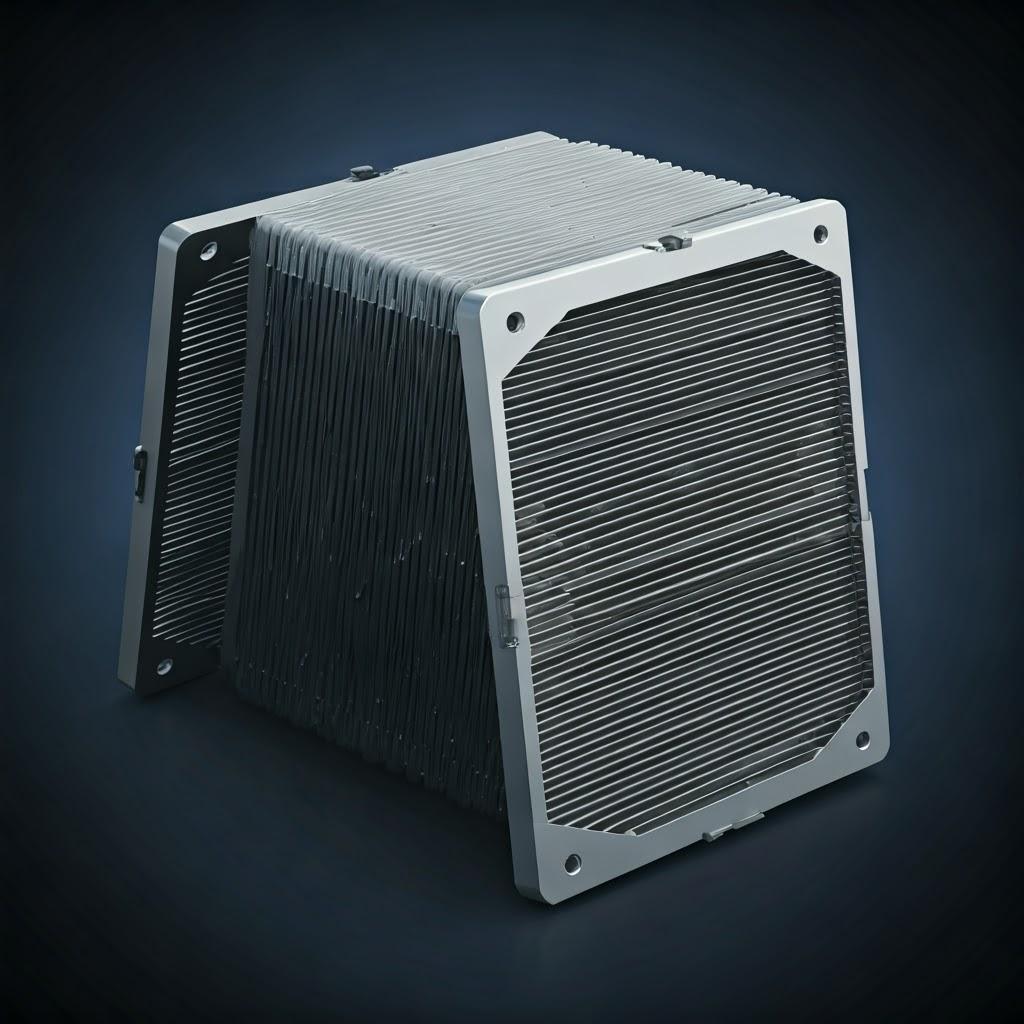
Supplier Selection: Choosing the Right Metal AM Service Provider for Aerospace Components
The success of incorporating additively manufactured (AM) radiator panels into a satellite program hinges significantly on the capabilities and reliability of the chosen manufacturing partner. Selecting the right metal AM service provider is a critical decision for both engineering teams focused on technical execution and procurement managers concerned with quality, cost, and schedule adherence. Given the stringent requirements of the aerospace industry, the selection process must go far beyond simply comparing price quotes. It requires a thorough evaluation of a supplier’s technical expertise, process maturity, quality systems, and experience specifically within the aerospace sector.
Key Criteria for Evaluating Metal AM Suppliers for Satellite Radiators:
- Demonstrated Aerospace Experience:
- Does the supplier have a proven track record of successfully delivering flight-qualified hardware for satellite or other aerospace applications?
- Can they provide relevant case studies or references?
- Do they understand the specific challenges and quality expectations of the space industry (e.g., contamination control, material traceability, rigorous testing)?
- Relevant Certifications:
- Certification AS9100 : This is the standard for Quality Management Systems (QMS) in the aviation, space, and defense industries. It indicates a commitment to rigorous process control, traceability, and continuous improvement. This is often considered a minimum requirement for flight hardware suppliers.
- NADCAP Accreditation: While AS9100 covers the overall QMS, NADCAP (National Aerospace and Defense Contractors Accreditation Program) provides specific accreditation for special processes like heat treatment, non-destructive testing (NDT), welding, and potentially AM itself as standards evolve. Suppliers holding relevant NADCAP accreditations demonstrate a higher level of process control in these critical areas.
- Material Expertise and Qualification:
- Does the supplier have established, qualified processes for the required materials (AlSi10Mg, CuCrZr)? This means they have developed stable parameters, characterized material properties from their process, and can consistently produce parts meeting specifications.
- For challenging materials like CuCrZr, inquire specifically about their experience, equipment capabilities (e.g., laser wavelength, power), atmospheric control, and demonstrated results (density, conductivity, mechanical properties).
- Do they source high-quality aerospace metal powders from reputable suppliers or, like Met3dp, produce their own powders under stringent quality control?
- Technology and Equipment:
- What specific AM technology do they utilize (LPBF/SLM, EBM)? Ensure the technology is suitable for the material and application requirements (LPBF is common for AlSi10Mg and CuCrZr radiators requiring fine features).
- What is the condition, calibration frequency, and capability of their machines? Consistent, well-maintained, industrial-grade equipment is essential for repeatability.
- Do they employ process monitoring capabilities?
- Comprehensive Post-Processing Capabilities:
- Does the supplier offer critical post-processing steps in-house (stress relief, heat treatment, HIP, support removal, CNC machining, surface finishing, cleaning)? In-house capabilities often lead to better integration, shorter lead times, and clearer accountability.
- If certain processes are outsourced (e.g., HIP, coating), do they have strong relationships with qualified, certified subcontractors and manage that supply chain effectively?
- Do they possess the necessary NDT and metrology equipment (CMM, 3D scanning, CT scanning) for thorough inspection and quality verification?
- Système de gestion de la qualité (SGQ) robuste :
- Beyond certification, evaluate the depth and implementation of their QMS. How do they ensure material traceability (powder batch tracking), process documentation, change control, and non-conformance management?
- What are their procedures for process validation and qualification for new parts or revisions?
- Ingénierie et soutien du DfAM :
- Does the supplier offer Design for Additive Manufacturing (DfAM) expertise? Can they collaborate with your engineering team to optimize the radiator design for printability, performance, and cost-effectiveness?
- Do they have capabilities in build simulation to predict and mitigate potential issues like distortion?
- Capacity, Lead Time, and Communication:
- Does the supplier have sufficient capacity to meet your project timelines, from prototyping through potential series production?
- Are their quoted lead times realistic and reliable?
- Is their communication clear, responsive, and transparent? A collaborative partnership approach is often more effective than a purely transactional relationship, especially for complex projects.
- Company Stability and Vision:
- Consider the supplier’s stability, investment in technology, and long-term vision, particularly for multi-year satellite programs.
Choosing a supplier like Met3dp, which offers comprehensive solutions spanning advanced metal AM equipment, high-quality poudres métalliques, and application development services backed by decades of collective expertise, can provide significant advantages. Their focus on industry-leading print volume, accuracy, and reliability, combined with advanced powder manufacturing, positions them as a strong potential partner for demanding aerospace applications. Ultimately, the goal is to find a strategic manufacturing partner who understands the mission-critical nature of satellite components and possesses the technical rigor and quality commitment necessary to deliver flight-worthy hardware reliably.
Cost & Timelines: Understanding Cost Factors and Lead Times for AM Radiator Panels
While Metal Additive Manufacturing (AM) enables the creation of highly optimized and lightweight satellite radiator panels, understanding the cost structure and typical timelines is crucial for project planning, budgeting, and the B2B procurement process. AM costs are driven by different factors compared to traditional manufacturing, and lead times can vary significantly based on complexity, quantity, and qualification requirements.
Key Cost Drivers for AM Radiator Panels:
The final price of a 3D printed metal radiator panel is influenced by a combination of factors:
- Coût des matériaux :
- Type de poudre : The raw material is a significant cost component. High-performance powders like aerospace-grade AlSi10Mg are moderately expensive, while specialized copper alloys like CuCrZr are substantially more costly due to raw material prices and complex atomization processes.
- Volume : The amount of powder consumed, which includes the part volume and the support structure volume. Efficient design (e.g., topology optimization, minimized supports) directly impacts material usage.
- Recyclage : While unfused powder can often be recycled, the costs associated with sieving, testing, and managing recycled powder are factored in. Strict aerospace requirements may limit the number of times powder can be reused.
- Temps machine (temps de construction) :
- Machine Taux horaire : Industrial metal AM systems represent a significant capital investment, and their operating costs (energy, inert gas, maintenance) contribute to an hourly rate charged for build time.
- Build Height & Volume: Build time is primarily driven by the number of layers (height) and the area to be scanned per layer. Taller parts take longer.
- Complexity & Features: Intricate details and thin features may require slower scan speeds, increasing time.
- Nesting Efficiency: Printing multiple parts simultaneously in one build (nesting) can significantly reduce the per-part machine time cost, especially relevant for fabrication en vrac or series production.
- Structures de soutien : The volume and complexity of support structures add to the build time and material consumption.
- Coûts de main-d'œuvre :
- Setup: Preparing the build file, loading the machine, and post-build setup takes skilled operator time.
- Monitoring: While often automated, builds may require some level of monitoring.
- Post-traitement : This can be a very significant labor cost component. Manual support removal, machining operations, surface finishing, cleaning, and inspection all require skilled technician or engineer time. Complex parts with intricate internal channels or extensive support requirements will incur higher labor costs.
- Post-Processing Operations:
- The specific steps required (stress relief, HIP, multi-axis machining, specialized coatings, NDT) add direct costs based on equipment usage, external vendor charges (if outsourced), and associated labor. HIP, extensive machining, and complex coating processes can be particularly costly.
- Assurance qualité et inspection :
- The level of required inspection (CMM, 3D scanning, CT scanning, material testing) adds cost. Rigorous aerospace qualification requirements necessitate more extensive and costly QA procedures compared to industrial applications.
- Non-Recurring Engineering (NRE):
- For new or complex designs, there may be initial costs associated with DfAM consultation, build simulation, process parameter development/validation, and fixture design, especially for the first production run.
Délais d'exécution typiques :
Lead times for AM radiator panels can vary widely:
- Prototypes : For initial form, fit, or functional prototypes (potentially with less stringent QA), lead times can range from 1 to 4 weeks, depending on complexity, size, material availability, and supplier backlog. The ability of AM to produce prototypes quickly from CAD data is a major advantage.
- Pièces de production qualifiées : For flight-qualified hardware requiring full post-processing, rigorous inspection, and documentation, lead times are significantly longer, potentially ranging from 6 weeks to several months. This includes time for potential HIP cycles, specialized machining, coating application, extensive NDT, and final quality verification and documentation package preparation.
- Factors Influencing Lead Time: Part complexity, build time, post-processing intensity, required testing/qualification level, quantity ordered, material availability, and the supplier’s current workload all play a role.
Cost and Lead Time Comparison (Qualitative):
Compared to traditional manufacturing (e.g., complex assembly of machined parts, face sheets, cores, and embedded pipes):
- Low Volume / High Complexity: AM can often be more cost-effective and faster due to the elimination of tooling, reduced assembly labor, and ability to create complex geometries directly. This is highly relevant for custom satellite radiators.
- High Volume / Simple Geometry: Traditional methods may remain more cost-effective for very simple designs produced in large quantities.
Request for Quote (RFQ) Process:
To get accurate pricing and lead times for a specific radiator panel design, procurement managers should engage suppliers through a formal RFQ process. Providing a detailed technical data package (CAD model, material specification, tolerance requirements, surface finish callouts, testing/inspection plan, quantity) is essential for suppliers to provide an accurate quote. Engaging with potential suppliers early in the design phase can also help optimize the part for manufacturability and cost-effectiveness.
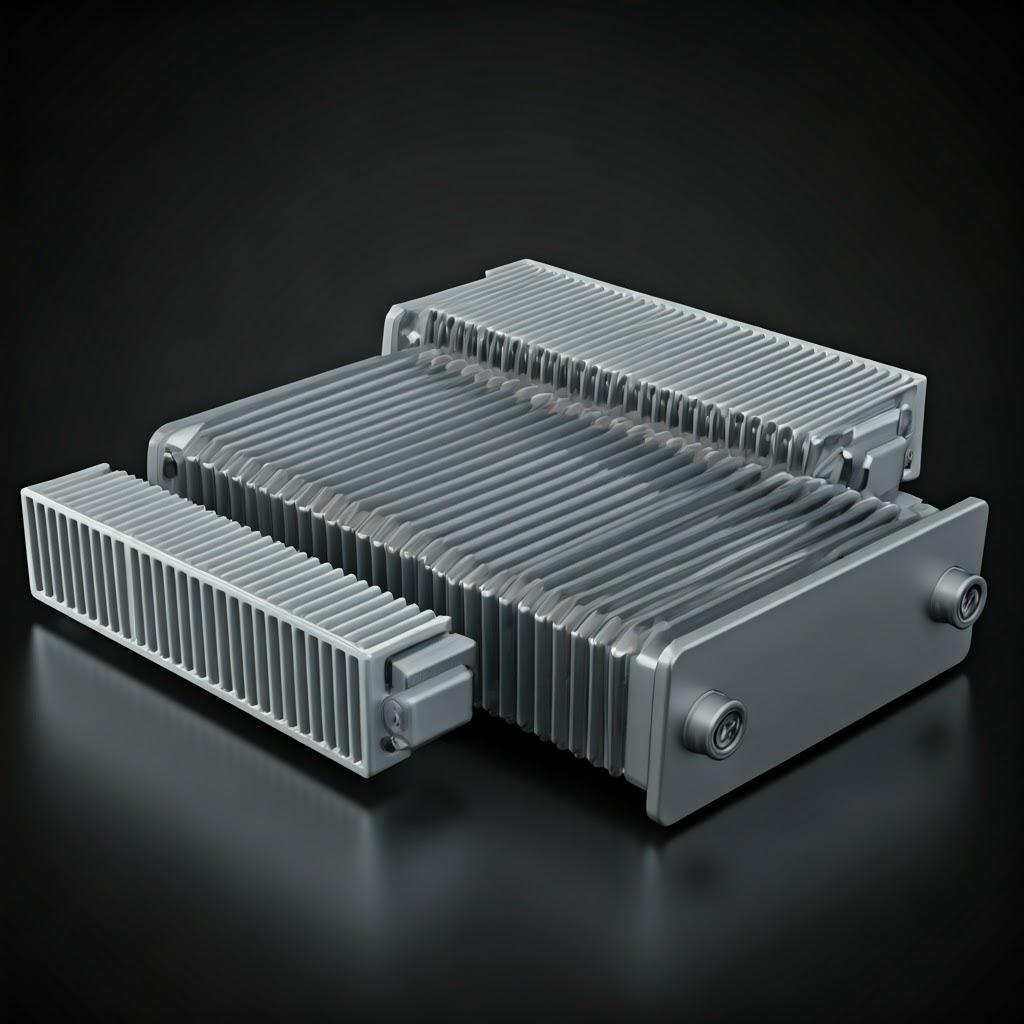
Frequently Asked Questions (FAQ) about 3D Printed Satellite Radiator Panels
Here are answers to some common questions engineers and procurement managers have about using metal Additive Manufacturing for satellite radiator panels:
Q1: How much weight saving can realistically be achieved with AM radiator panels compared to traditional ones?
- Répondre: Significant weight savings are a primary driver for using AM. Through topology optimization and the use of internal lattice structures, weight reductions typically range from 20% to 50% compared to radiator panels manufactured using conventional methods like CNC machining or brazed assemblies, while maintaining or even improving structural and thermal performance. The exact savings depend heavily on the initial design, load requirements, and how effectively DfAM principles are applied. For cost-sensitive satellite missions, this mass reduction translates directly into lower launch costs or increased payload capacity.
Q2: Are 3D printed metal radiators space-qualified? What kind of testing is required?
- Répondre: Yes, 3D printed metal components, including radiators and heat exchangers, have successfully flown on numerous space missions. However, achieving “space qualification” is a rigorous process specific to each part, mission, and set of requirements. It involves more than just successful printing. Qualification typically requires:
- Material & Process Validation: Demonstrating consistent material properties (tensile, fatigue, thermal) from the specific AM process and powder batch.
- Functional Testing: Verifying thermal performance under relevant conditions (e.g., thermal vacuum testing).
- Environmental Testing: Subjecting the part to simulated launch loads (vibration testing, acoustic testing) and space environment conditions (thermal cycling).
- CND et inspection : Thorough non-destructive testing (CT scanning is often crucial for internal channels) and dimensional verification.
- Traceability & Documentation: Comprehensive records of materials, processes, testing, and inspections. Partnering with an experienced aerospace AM supplier familiar with qualification requirements is essential.
Q3: Can complex internal cooling channels be reliably printed and verified? How do you ensure they are clean?
- Répondre: Yes, one of the key advantages of AM (specifically LPBF) is the ability to print complex, optimized internal channels directly into the radiator panel. DfAM principles are used to design these channels with self-supporting shapes and smooth pathways to facilitate printing and powder removal.
- Verification: Ensuring the channels are printed correctly and are free from defects or blockages typically involves Computed Tomography (CT) scanning. CT scanning provides a full 3D volumetric view of the part’s interior, allowing for detailed dimensional analysis of the channels and detection of any trapped powder or anomalies.
- Nettoyage : Thorough cleaning procedures involving pressurized gas blow-outs, potentially solvent flushing (if compatible), and ultrasonic cleaning are used. Verification of cleanliness might involve visual inspection with borescopes where possible, or confirmation via CT scanning that loose powder has been removed. Designing channels for effective powder removal is critical.
Q4: What level of thermal performance improvement can be expected from AM radiator designs?
- Répondre: Performance improvements stem primarily from the design freedom AM offers. While the base material conductivity is fixed (e.g., AlSi10Mg or CuCrZr), AM allows:
- Optimized Channel Geometry: Designing internal fluid channels with features like internal fins, turbulators, or complex cross-sections can enhance convective heat transfer coefficients, leading to more efficient heat removal from the fluid to the panel.
- Conformal Designs: Fitting radiators perfectly to curved surfaces maximizes radiating area in constrained volumes.
- Integrated Heat Spreaders: Using topology optimization or functionally graded materials (in the future) could potentially improve heat spreading across the radiator face. The exact improvement depends on the specific design optimization undertaken compared to the traditional baseline, but enhanced thermal efficiency (allowing for smaller/lighter radiators for the same heat load) is a key goal.
Q5: For radiator panels, when should AlSi10Mg be chosen versus CuCrZr?
- Répondre: The choice depends on a trade-off between weight, thermal performance requirements, and cost/manufacturability:
- Choose AlSi10Mg when:
- Weight reduction is the absolute top priority.
- Thermal loads are moderate and can be managed by its good (but not exceptional) thermal conductivity, potentially augmented by optimized fluid channels or heat pipes.
- Cost and manufacturing lead time are significant constraints (AlSi10Mg is generally easier and cheaper to print than CuCrZr).
- Choose CuCrZr when:
- Extremely high thermal conductivity is required to manage very high heat fluxes or minimize temperature gradients in specific areas.
- The superior thermal performance justifies the significant increase in mass (density is ~3.3x higher than AlSi10Mg) and higher manufacturing cost/complexity.
- Good mechanical strength at elevated temperatures is also needed. Often, the best solution might involve using AlSi10Mg for the main structure and strategically employing CuCrZr only in critical high-heat zones if feasible, or relying heavily on DfAM to maximize thermal performance within an AlSi10Mg design.
- Choose AlSi10Mg when:
Conclusion: Elevating Satellite Performance with Additively Manufactured Radiator Panels
The journey to space is demanding, and ensuring the survival and optimal performance of satellites hinges on effective thermal management. Traditional manufacturing methods for critical components like radiator panels, while established, often impose limitations in terms of weight, design complexity, and production speed. Metal Additive Manufacturing has decisively broken through these barriers, offering a transformative approach to designing and fabricating satellite thermal control hardware.
As we’ve explored, utilizing metal AM technologies like Laser Powder Bed Fusion enables the creation of lightweight radiator panels through advanced topology optimization and lattice structures, directly addressing the critical need to reduce launch mass. The unparalleled liberté de conception allows engineers to integrate complex internal cooling channels, create conformal shapes maximizing radiating area, and consolidate multiple components into single, monolithic parts, thereby enhancing both thermal efficiency and system reliability. Furthermore, the ability to rapidly prototype and iterate designs accelerates development cycles, enabling faster deployment of advanced satellite systems.
The selection of appropriate matériaux de qualité aérospatiale, such as the lightweight workhorse AlSi10Mg or the high-conductivity specialist CuCrZr, combined with rigorous process control and meticulous post-processing, ensures that 3D printed radiators meet the demanding mechanical, thermal, and quality requirements of the space environment. Overcoming challenges related to precision, surface finish, internal stresses, and defect mitigation requires deep expertise and a commitment to quality, underscoring the importance of choosing the right manufacturing partner.
For engineers designing next-generation satellites and procurement managers seeking innovative, high-performance solutions, metal AM offers a clear pathway to enhanced capabilities. The benefits – reduced weight, improved thermal performance, increased design complexity, part consolidation, and potentially faster development – collectively contribute to more capable, reliable, and cost-effective satellite missions.
The future of space manufacturing is increasingly intertwined with additive technologies. As processes mature, new materials emerge, and designs become ever more sophisticated, AM will continue to play a pivotal role in pushing the boundaries of satellite performance.
Ready to explore how metal additive manufacturing can revolutionize your satellite thermal management systems? Partnering with a leader in the field is key. We encourage you to reach out to Met3dp, a company dedicated to providing cutting-edge metal AM systems, high-quality powders, and comprehensive application support for the aerospace industry. Discover how their expertise can help you achieve your mission objectives. Visit https://met3dp.com/ to learn more or contact their team to discuss your specific project needs.
Partager sur
MET3DP Technology Co. est un fournisseur de premier plan de solutions de fabrication additive dont le siège se trouve à Qingdao, en Chine. Notre société est spécialisée dans les équipements d'impression 3D et les poudres métalliques de haute performance pour les applications industrielles.
Articles connexes
À propos de Met3DP
Mise à jour récente
Notre produit
CONTACTEZ-NOUS
Vous avez des questions ? Envoyez-nous un message dès maintenant ! Nous répondrons à votre demande avec toute une équipe dès réception de votre message.
Obtenir les informations de Metal3DP
Brochure du produit
Obtenir les derniers produits et la liste des prix
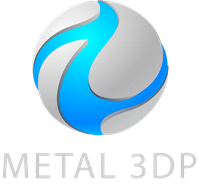
Poudres métalliques pour l'impression 3D et la fabrication additive