3D Printed Rib Structures for Aerospace Weight Reduction
Table des matières
Introduction: The Critical Role of Rib Structures and the Quest for Lighter Aerospace Components
In the intricate dance of physics and engineering that allows massive aircraft to defy gravity, structural components play a paramount role. Among the most fundamental of these are rib structures. Found within wings, fuselages, and control surfaces, ribs are the unsung heroes that maintain the aerodynamic shape, distribute operational loads, and ensure the overall integrity of the airframe. They act like the skeletal framework, transferring stresses from the skin and spars, preventing buckling, and providing attachment points for other critical systems. The design and manufacture of these components have always been central to aircraft development, balancing the non-negotiable demands of safety and strength with the ever-present drive for efficiency.
This drive for efficiency in the aerospace industry is relentless, and its primary focus is often réduction du poids. Every kilogram saved on an aircraft’s structural weight translates directly into tangible benefits over its operational lifespan. Lighter aircraft consume less fuel, leading to significant cost savings for operators and a reduced environmental footprint – a critical consideration in today’s eco-conscious world. Furthermore, reduced weight can mean increased payload capacity (more passengers or cargo), extended range, or enhanced maneuverability and performance, particularly vital in defense and space applications. This relentless pursuit of lightness, often referred to as “lightweighting,” permeates every aspect of aerospace design, from material selection to component geometry. Procurement managers and engineers within aerospace OEMs and their fournisseurs de composants aérospatiaux are constantly seeking innovative materials and manufacturing processes that can shave off precious grams without compromising safety or performance.
Traditionally, aerospace ribs have been manufactured using subtractive methods, primarily CNC machining from solid blocks or plates of high-strength aluminum or titanium alloys. While effective and well-understood, this approach often involves carving away vast amounts of expensive raw material, resulting in poor “buy-to-fly” ratios (the ratio of the weight of the raw material purchased to the weight of the final part). Complex rib geometries can require intricate multi-axis machining operations, extensive programming, specialized tooling, and long machining times, contributing significantly to lead times and costs, especially for low-volume production runs or prototyping.
Entrer Fabrication additive métallique (AM), commonly known as metal Impression 3D. This transformative technology is rapidly moving beyond prototyping and into the realm of serial production for demanding industries like aerospace. Instead of removing material, AM builds parts layer by layer directly from a digital model, typically using high-energy sources like lasers or electron beams to fuse fine metal powders. This fundamental difference unlocks a paradigm shift in how aerospace components, including rib structures, can be designed and produced.
Metal AM offers aerospace engineers unprecedented design freedom. Complex, organic shapes optimized for specific load paths, previously impossible or prohibitively expensive to manufacture, become feasible. Internal lattice structures can be incorporated to provide stiffness while drastically reducing mass. Multiple components of a rib assembly can potentially be consolidated into a single printed part, reducing fastener count, assembly time, and potential points of failure. Furthermore, AM processes are inherently more material-efficient than traditional subtractive methods, significantly improving the buy-to-fly ratio and reducing waste of high-value aerospace alloys.
Pour aerospace procurement managers et acheteurs B2B seeking cutting-edge manufacturing solutions, metal AM represents a powerful tool to achieve strategic objectives: reducing component weight, shortening lead times for complex parts, enabling design innovation, and potentially simplifying supply chains through part consolidation. Companies like Met3dp, headquartered in Qingdao, China, are at the forefront of this revolution, providing not only advanced metal 3D printing equipment, like their Selective Electron Beam Melting (SEBM) systems known for industry-leading accuracy and reliability but also specializing in the research and manufacture of the high-performance, poudres métalliques de qualité aérospatiale essential for producing mission-critical parts. This blog post will delve into the specifics of using metal AM for aerospace rib structures, exploring applications, the compelling advantages over traditional methods, recommended materials like Scalmalloy® and AlSi10Mg, crucial design considerations, and what to look for in an AM service provider.
Applications and Functions: Where are 3D Printed Rib Structures Deployed in Aerospace?
Aerospace rib structures, regardless of manufacturing method, are integral to maintaining the form and function of various airframe sections. Their primary roles include maintaining the aerodynamic profile (especially in wings and control surfaces), transferring loads between the skin, spars, and stringers, preventing buckling under compressive and shear forces, and providing rigid attachment points for other systems. The advent of metal additive manufacturing hasn’t changed these fundamental functions, but it a expanded the possibilities for how these functions are achieved and where optimized, lightweight ribs can provide the most significant benefits. The ability to create complex, topology-optimized designs makes AM particularly attractive for applications where structural efficiency is paramount.
Let’s explore the key areas where 3D printed rib structures are finding increasing application:
- Wing Ribs: This is perhaps the most classic application. Wing ribs define the airfoil shape crucial for generating lift. They transfer aerodynamic loads from the wing skin to the main spars and distribute loads from fuel tanks, engines, and landing gear housed within or attached to the wing. Using AM allows for highly optimized wing rib designs that follow the precise stress paths, removing material where it isn’t needed. This can lead to significant weight savings across the entire wingset, directly impacting fuel efficiency. Furthermore, internal channels for wiring, fuel lines, or even thermal management systems can be integrated directly into the rib structure during the printing process, consolidating parts and simplifying assembly. AM enables the creation of variable-density lattice structures within the rib, providing tailored stiffness and strength exactly where required.
- Fuselage Frames/Ribs: Similar to wing ribs, fuselage frames or ribs maintain the cross-sectional shape of the aircraft body, supporting the skin against buckling and distributing pressurization loads (in commercial aircraft) and aerodynamic forces. They also serve as mounting points for cabin interiors, cargo systems, and various equipment. AM enables the design of lightweight frames that integrate attachment brackets and system interfaces, reducing part count and assembly complexity. For unpressurized sections or in space applications, topology optimization can yield highly efficient, skeletal frame structures.
- Empennage Structures (Tail Sections): Ribs within the horizontal stabilizer, vertical stabilizer (fin), elevators, and rudder perform similar functions to wing ribs – maintaining aerodynamic profiles and transferring loads to spars. Given the location at the rear of the aircraft, weight savings in the empennage can also have a positive impact on overall aircraft balance and stability, potentially reducing the required size and weight of counterbalance systems. AM allows for the production of highly integrated ribs for control surfaces, potentially combining hinge points or actuator attachments into a single printed component.
- Engine Component Supports & Nacelle Structures: Ribs and brackets within engine nacelles provide structural support, maintain aerodynamic shape, and route essential services. They often operate in high-temperature or high-vibration environments. AM, utilizing materials like high-temperature alloys or optimized aluminum/titanium designs, can create lightweight, stiff support structures capable of withstanding these demanding conditions. Part consolidation is again a key driver here, reducing the number of fabricated sheet metal parts and fasteners typical in nacelle assemblies.
- Landing Gear Assemblies: Ribs and support structures within landing gear bays and the gear itself must withstand enormous impact loads during landing. While some ultra-high-strength steel components might remain traditionally manufactured, AM offers opportunities for lightweighting associated support structures, brackets, and fairing ribs using high-strength aluminum (like Scalmalloy®) or titanium alloys.
- Control Surface Ribs: Ailerons, flaps, elevators, and rudders rely on internal ribs for shape and stiffness. AM allows for intricate, thin-walled rib designs optimized for aerodynamic efficiency and minimal weight, enhancing control responsiveness.
- Satellite and Launch Vehicle Structures: In space applications, every gram is critical. AM is used extensively to create ultra-lightweight ribs and isogrid structures for satellite buses, solar panel deployments, antenna supports, and propellant tank interfacing structures within launch vehicles. The ability to rapidly iterate designs and produce highly complex geometries makes AM ideal for the often unique and low-volume demands of the space industry.
Intégration fonctionnelle : Beyond just structural support, AM enables the integration of additional functionality directly into the rib design:
- Gestion thermique : Internal channels can be designed into ribs located near heat sources (like engines or electronics) to allow for air or liquid cooling, creating multifunctional components.
- System Routing: Conduits for electrical wiring harnesses or hydraulic lines can be incorporated, protecting them and simplifying aircraft assembly.
- Integrated Mounts/Brackets: Attachment points for other components can be grown as part of the rib, eliminating the need for separate brackets and fasteners.
Pour aerospace procurement managers et supply chain specialists, sourcing these advanced, often complex AM rib structures requires partnering with capable fournisseurs de services de fabrication additive métallique. These suppliers must not only possess the right printing technology but also demonstrate expertise in aerospace materials, process control, quality assurance, and post-processing necessary to meet the stringent demands of the industry. The ability of AM to consolidate assemblies also presents an opportunity to streamline the supply chain, reducing the number of individual part numbers that need to be tracked, sourced, and managed.
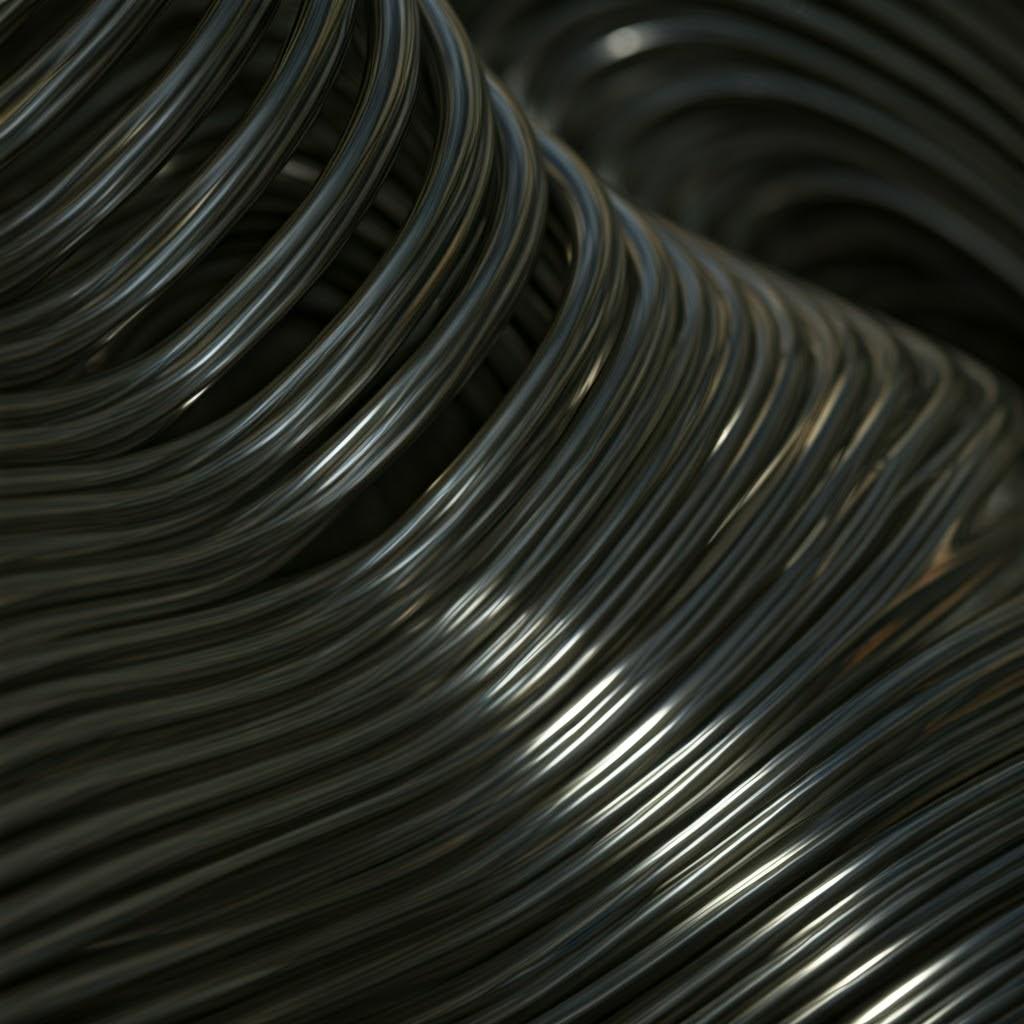
Why Metal 3D Printing for Aerospace Ribs? Unlocking Performance and Efficiency Gains
The aerospace industry has relied on subtractive manufacturing, particularly CNC machining, for decades to produce high-precision structural components like ribs. This method involves starting with a solid block, plate, or forging of material (often aluminum or titanium) and meticulously carving away the excess until the final shape is achieved. While capable of producing high-quality parts, this traditional approach faces inherent limitations, especially when applied to complex aerospace structures optimized for minimum weight. Metal Additive Manufacturing offers compelling solutions to overcome these limitations, unlocking significant performance and efficiency gains.
Let’s dissect the key advantages of using metal AM (specifically powder bed fusion techniques like Laser Powder Bed Fusion – LPBF, also known as Selective Laser Melting – SLM, and Selective Electron Beam Melting – SEBM) for producing aerospace ribs:
- Revolutionary Lightweighting through Topology Optimization: This is arguably the most significant advantage. Traditional manufacturing constraints often force designers into prismatic shapes or designs easily achievable with cutting tools. AM removes many of these constraints. Using optimisation de la topologie software, engineers can define the load cases, boundary conditions, and design space for a rib, and the software algorithm iteratively removes material from areas experiencing low stress, leaving behind an organic, often bone-like structure that represents the most efficient load path.
- Bénéfice : This results in components that are significantly lighter (weight reductions of 30-60% or even more compared to traditionally designed counterparts are common) while meeting or exceeding the required strength and stiffness criteria. This directly translates to the fuel savings and performance gains discussed earlier.
- Contrast: Achieving such complex, optimized shapes with CNC machining would be incredibly difficult, time-consuming, and potentially impossible due to tool access limitations.
- Massive Improvement in Buy-to-Fly Ratio: Aerospace alloys are expensive. CNC machining ribs from solid billets often results in buy-to-fly ratios exceeding 10:1, meaning over 90% of the costly raw material is machined away into chips (scrap). This represents significant wasted cost and resources.
- Bénéfice : AM builds parts layer by layer, using only the material needed for the part and its support structures. While some support material is used and unfused powder needs recycling, the overall material utilization is vastly superior. Buy-to-fly ratios closer to 1.5:1 or 2:1 are achievable, drastically reducing raw material costs and waste.
- Impact: This makes the economics of production more favorable, especially for high-value materials like titanium or specialized alloys like Scalmalloy®.
- Part Consolidation for Reduced Complexity and Weight: Rib structures in assemblies often involve multiple machined components, brackets, fasteners (rivets, bolts), and sealing elements. Each joint and fastener adds weight, introduces potential failure points, and increases assembly time and complexity.
- Bénéfice : AM allows engineers to redesign assemblies, consolidating multiple components into a single, monolithic printed part. A complex rib assembly with numerous attached brackets could potentially become one integrated structure.
- Impact: This reduces part count, eliminates fasteners, lowers overall weight, simplifies assembly processes, reduces inventory management for procurement departments, and potentially improves structural integrity by removing joints.
- Manufacturing of Complex Geometries: AM excels at creating intricate internal features and complex external shapes that are difficult or impossible to achieve with traditional methods.
- Bénéfice : This includes internal cooling channels, optimized lattice structures for tailored stiffness-to-weight ratios, hidden voids for further weight reduction, and complex conformal shapes that perfectly match aerodynamic profiles or mating components.
- Application : For ribs needing integrated thermal management or requiring highly optimized internal structures, AM is often the only viable manufacturing method.
- Accelerated Prototyping and Design Iteration: Setting up for traditional manufacturing of a complex rib often involves creating specialized fixtures and complex CNC programming. Design changes can necessitate significant rework of these elements.
- Bénéfice : AM is digitally driven. Designs can be modified in CAD and sent directly to the printer, allowing for much faster iteration cycles during the development phase. Multiple design variants can potentially be printed simultaneously in a single build for comparative testing.
- Impact: This accelerates the product development lifecycle, allowing engineers to test and validate optimized designs more quickly and efficiently before committing to serial production.
- Potential for Reduced Lead Times (Especially for Complex/Low-Volume Parts): While the actual printing process can take hours or days, the overall lead time from final design to finished part can often be shorter with AM compared to traditional methods for highly complex or low-volume components.
- Reasoning: AM eliminates the need for tool design and fabrication, reduces complex programming and setup times associated with multi-axis machining, and simplifies the supply chain through part consolidation.
- Considération : This is highly dependent on part complexity, material, required post-processing, and the AM service provider’s capacity and backlog. However, for urgent needs or parts with long traditional lead times, AM offers a valuable alternative.
While AM offers these substantial advantages, it’s crucial to partner with experienced providers like Met3dp. Their focus on industry-leading print volume, accuracy, and reliability, backed by deep expertise in both machine technology (SEBM) and powder metallurgy (Gas Atomization, PREP), ensures that the theoretical benefits of AM are translated into tangible, high-quality aerospace components. Choosing the right metal AM aerospace partner is key to successfully leveraging these benefits for demanding applications like rib structures.
Recommended Materials for 3D Printed Ribs: Scalmalloy® and AlSi10Mg Deep Dive
Selecting the appropriate material is fundamental to the success of any engineering application, and this holds particularly true for aerospace components where performance, safety, and weight are critical. While metal additive manufacturing can process a wide range of alloys (including titaniums, nickel superalloys, and steels), aluminum alloys are frequently chosen for rib structures due to their inherent low density and good mechanical properties. Within the AM aluminum family, two materials stand out for aerospace rib applications, albeit with different strengths and ideal use cases: Scalmalloy® (alliage d'aluminium) et AlSi10Mg.
Understanding the characteristics of these materials is crucial for both design engineers specifying the part and procurement managers sourcing the manufacturing service and metal powder suppliers aerospace besoins.
Scalmalloy® (Al-Mg-Sc Alloy): The High-Performance Champion
Scalmalloy® is a patented high-performance aluminum-magnesium-scandium alloy specifically developed for the demanding requirements of additive manufacturing. Its unique composition results in a fine-grained microstructure after printing and appropriate heat treatment, delivering mechanical properties that significantly surpass those of traditional cast or wrought aluminum alloys commonly used in AM.
- Key Properties & Advantages:
- Exceptional Specific Strength: This is Scalmalloy®’s defining characteristic. It boasts a very high yield and ultimate tensile strength relative to its low density, making it one of the strongest AM-processable aluminum alloys available. This high strength-to-weight ratio allows for significant lightweighting potential beyond what’s achievable with standard alloys, even after topology optimization.
- Excellente ductilité et durée de vie à la fatigue : Unlike some high-strength materials that can be brittle, Scalmalloy® maintains good elongation (ductility), allowing it to deform significantly before fracture. Crucially for aerospace components subjected to cyclic loading (like wing ribs), it exhibits superior fatigue strength compared to other AM aluminum alloys like AlSi10Mg.
- Good Weldability & Processability: It generally processes well in Laser Powder Bed Fusion (LPBF) systems and can be welded if necessary for larger assemblies or repairs (though part consolidation often negates this need).
- Résistance à la corrosion : Offers good resistance to corrosion, suitable for typical aerospace operating environments.
- Microstructural Stability: The scandium addition helps stabilize the microstructure, contributing to its consistent high performance.
- Ideal Applications:
- Highly loaded structural components where maximum weight saving is the primary driver.
- Fatigue-critical parts (wing ribs, fuselage frames, landing gear components).
- Performance-driven applications in motorsport, defense, and space.
- Direct replacement/upgrade for components traditionally made from high-strength 7xxx series aluminum alloys.
- Considérations :
- Coût : Scalmalloy® powder is significantly more expensive than standard aluminum alloys due to the scandium content and licensing. This higher material cost needs to be justified by the performance gains and weight savings achieved.
- Traitement thermique : Requires specific, optimized heat treatment cycles to achieve its peak properties. Partnering with an AM provider experienced with Scalmalloy®’s post-processing is essential.
AlSi10Mg: The Established Workhorse
AlSi10Mg is one of the most widely used and well-characterized aluminum alloys in metal additive manufacturing. It’s essentially an aluminum casting alloy adapted for AM processes, known for its excellent printability and balanced properties.
- Key Properties & Advantages:
- Excellente imprimabilité : The silicon content provides good fluidity in the melt pool, making it relatively easy to process across various LPBF machines with good density and surface finish. This leads to reliable and repeatable manufacturing.
- Good Strength & Hardness: Offers respectable mechanical properties suitable for many structural applications, especially after appropriate heat treatment (e.g., T6 condition). While not reaching Scalmalloy® levels, its strength is sufficient for moderately loaded components.
- Good Thermal Properties: Possesses good thermal conductivity, making it suitable for applications where heat dissipation is a factor (e.g., ribs integrated with heat exchangers or near electronics).
- Cost-Effective & Widely Available: AlSi10Mg powder is significantly less expensive than Scalmalloy® and is offered by numerous powder suppliers and AM service providers.
- Well-Understood: Extensive research and application data are available for AlSi10Mg, providing a high degree of confidence in its performance characteristics.
- Ideal Applications:
- General-purpose structural components where cost is a major driver alongside weight reduction.
- Prototypes and components requiring rapid iteration.
- Structures with integrated thermal management features.
- Components where the absolute maximum strength-to-weight ratio is not the primary requirement, but good overall performance is needed.
- Replacing traditional cast aluminum components.
- Considérations :
- Lower Strength & Fatigue Life: Its ultimate tensile strength, yield strength, and particularly its fatigue strength are lower than Scalmalloy®. This limits its use in highly stressed or fatigue-critical applications compared to its high-performance counterpart.
- Ductilité : Can exhibit lower ductility compared to Scalmalloy®, especially in the as-built state.
Material Comparison:
Propriété | Scalmalloy® (traité thermiquement) | AlSi10Mg (Heat Treated – T6 typical) | Unités | Notes |
---|---|---|---|---|
Densité | ~2.67 | ~2.67 | g/cm³ | Very similar, both offer inherent lightweight advantages. |
Résistance ultime à la traction (UTS) | > 520 | ~300 – 350 | MPa | Scalmalloy® significantly stronger. |
Yield Strength (YS) | > 480 | ~230 – 280 | MPa | Scalmalloy® significantly stronger. |
Allongement à la rupture | > 12 | ~6 – 10 | % | Scalmalloy® generally offers better ductility. |
Résistance à la fatigue | Significantly Higher | Modéré | (Relative) | Crucial advantage for Scalmalloy® in cyclic loading applications. |
Imprimabilité | Bon | Excellent | (Relative) | AlSi10Mg is generally considered easier to print reliably. |
Coût relatif | Haut | Low – Moderate | (Relative) | Scalmalloy® powder is notably more expensive. |
Avantage clé | Highest Strength-to-Weight, Fatigue Life | Cost-Effectiveness, Printability, Thermal | Choose based on primary application requirements. |
Exporter vers les feuilles
The Importance of Powder Quality:
Regardless of the chosen alloy, the quality of the metal powder used in the AM process is paramount for achieving the desired mechanical properties and part integrity, especially in aerospace. Powder characteristics like:
- Sphéricité : Affects powder flowability and packing density in the build chamber.
- Distribution de la taille des particules (PSD) : Influences melt pool dynamics and final part resolution/surface finish.
- Purity & Low Oxygen Content: Contaminants and excessive oxygen can lead to porosity and embrittlement, compromising mechanical properties.
- Fluidité : Ensures consistent powder deposition across the build plate.
This is where partnering with a company like Met3dp provides a distinct advantage. Met3dp employs industry-leading powder production technologies, including advanced Gas Atomization and Plasma Rotating Electrode Process (PREP) systems. These methods are specifically designed to produce highly spherical metal powders with controlled particle sizes, excellent flowability, and high purity – essential characteristics for printing dense, high-quality metal parts with superior and repeatable mechanical properties demanded by the aerospace sector. Their expertise extends beyond common alloys to innovative materials like TiNi, TiTa, and superalloys, showcasing a deep understanding of powder metallurgy. When sourcing AM services, inquiring about the provider’s powder sourcing, quality control, and handling procedures is crucial. Met3dp’s commitment to providing poudres métalliques de haute qualité ensures a solid foundation for producing reliable, high-performance aerospace components like rib structures.
Choosing between Scalmalloy® and AlSi10Mg depends heavily on the specific requirements of the rib structure – balancing the need for ultimate performance and weight saving against budget constraints and manufacturing considerations.
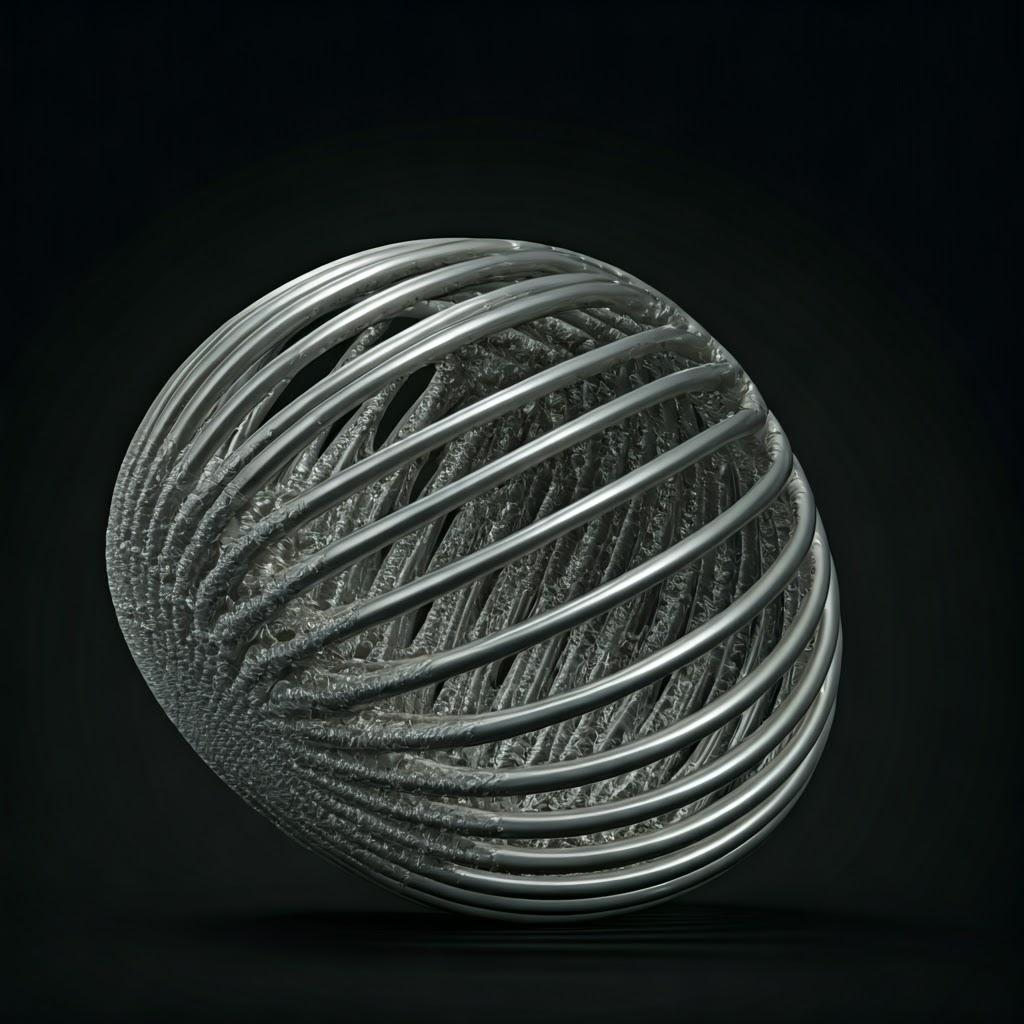
Design for Additive Manufacturing (DfAM): Optimizing Rib Structures for Printing Success
Simply taking a rib structure designed for CNC machining and sending it to a metal 3D printer rarely yields optimal results, either in terms of performance or cost-effectiveness. To truly unlock the potential of additive manufacturing for aerospace components, engineers must embrace Conception pour la fabrication additive (DfAM). This is more than just a set of rules; it’s a fundamental shift in mindset, moving away from the constraints of subtractive methods and leveraging the unique capabilities of layer-by-layer fabrication. For aerospace ribs, DfAM focuses on maximizing structural efficiency (strength-to-weight ratio), integrating functionality, and ensuring manufacturability and ease of post-processing.
Here are key DfAM principles crucial for designing effective 3D printed aerospace ribs:
- Leveraging Topology Optimization and Generative Design: As introduced earlier, these computational tools are foundational to lightweighting with AM.
- Optimisation de la topologie : Starts with a defined design space and load conditions, then algorithmically removes material from low-stress regions, revealing the most efficient load path. This often results in organic, freeform shapes optimized purely for mechanical performance. Engineers need to carefully define load cases, constraints (keep-out zones, manufacturing constraints like minimum thickness), and optimization goals (e.g., maximize stiffness, minimize mass).
- Conception générative : Often explores a wider range of solutions by generating multiple design alternatives based on functional requirements, material choices, and manufacturing constraints (including AM). This can provide engineers with novel design concepts they might not have conceived otherwise.
- Résultat : These tools enable the creation of rib structures that are significantly lighter than their traditionally designed counterparts while maintaining or even exceeding performance requirements.
- Intégration de structures en treillis : AM makes it possible to design parts with complex internal structures, such as lattices.
- Les types: These can range from uniform strut-based lattices (like octet truss) to more complex, mathematically defined structures like Triply Periodic Minimal Surfaces (TPMS) (e.g., Gyroid).
- Avantages : Lattices offer exceptionally high stiffness and strength relative to their density, enabling further weight reduction beyond what solid topology optimization might achieve. They can also be designed for specific energy absorption characteristics or to facilitate heat transfer if integrated with thermal management functions. Variable-density lattices allow engineers to tailor stiffness locally within the rib.
- Considérations : Designing effective lattices requires specialized software modules. Ensuring powder removal from complex internal lattices is critical and must be planned for (requiring escape holes). Support requirements à l'intérieur lattice structures also need consideration.
- Adhering to Minimum Feature Sizes and Thickness: AM processes have limitations on the smallest features they can reliably produce.
- Épaisseur de la paroi : There’s a minimum printable wall thickness (typically 0.3mm – 1.0mm depending on the machine, material, and orientation) below which features may not form properly or may warp excessively. Rib designs must respect these limits.
- Holes and Channels: Small holes (especially horizontal ones) may require specific design adjustments or support. Minimum diameter is often linked to wall thickness capabilities. Escape holes (typically >3-5mm diameter) are essential for removing unfused powder from internal cavities and lattice structures.
- Unsupported Features: Overhanging features require support structures beyond a certain angle (typically >45 degrees from the vertical is considered self-supporting, but this varies). Designing ribs with chamfers or fillets instead of sharp horizontal overhangs can significantly reduce support needs. Maximum unsupported bridge lengths also need consideration.
- Strategic Support Structure Planning: Support structures are often necessary in metal AM, particularly for complex geometries like optimized ribs with overhangs. They serve several purposes: anchoring the part to the build plate, preventing warping due to thermal stress, supporting overhanging features, and conducting heat away from the melt zone.
- DfAM Goal: Minimize the besoin for supports and design for ease of removal.
- Techniques:
- Orientation : Choosing the optimal build orientation is the first step. This involves balancing surface finish requirements, minimizing overhang angles, managing residual stress, and considering mechanical property anisotropy. Simulation tools can help predict stress and deformation for different orientations.
- Designing for Self-Support: Incorporating chamfers (e.g., 45-degree angles) or tear-drop shapes for horizontal holes can eliminate the need for internal supports.
- Accessibilité : Ensuring that support structures, especially internal ones, are physically accessible for removal tools (manual or automated).
- Support Type: Utilizing advanced support generation software allows for different types (solid block, thin web/fin, tree/cone supports) that can be easier to remove and minimize contact points (‘witness marks’) on the final part surface. Perforated or fragmented supports can also ease removal.
- Accounting for Anisotropy: Due to the layer-by-layer build process and directional heat flow, metal AM parts can exhibit anisotropic mechanical properties, meaning their strength and ductility may differ depending on the direction of loading relative to the build direction (X, Y vs. Z).
- Considération : Engineers must be aware of this potential anisotropy (especially relevant for fatigue life) and consider it during the design and orientation selection phase. Critical load paths should ideally be aligned with the direction of optimal material properties (often parallel to the build plate in the X-Y plane). Material data sheets from reputable providers often specify properties in different orientations.
- Concevoir pour le post-traitement : The as-built AM part is rarely the final product for aerospace applications. DfAM must consider downstream processes.
- Tolérances d'usinage : If surfaces require tight tolerances, specific surface finishes, or critical interface geometries (e.g., mounting holes, mating faces), extra material (‘machining stock’ or ‘offset’) should be added to those features in the CAD model (typically 0.5mm – 2.0mm).
- Fixturing: Consider how the complex AM part will be held (fixtured) for post-machining or inspection. Adding temporary locating features or datums that are later removed can be beneficial.
- Traitement thermique : Ensure the design can withstand the thermal cycles of stress relief and heat treatment without excessive distortion.
Effective DfAM requires collaboration between design engineers and AM specialists. Partnering with a service provider like Met3dp, who possesses deep expertise in AM processes (including SEBM and LPBF considerations) and materials, ensures that designs are not only innovative but also manufacturable, cost-effective, and meet the rigorous demands of aerospace applications.
Achievable Tolerance, Surface Finish, and Dimensional Accuracy in Metal AM Ribs
Engineers and procurement managers accustomed to the high precision of CNC machining need to understand the typical capabilities and limitations of metal additive manufacturing regarding dimensional accuracy, tolerances, and surface finish. While metal AM can produce highly complex parts, achieving the extremely tight tolerances often found in aerospace drawings usually requires post-processing steps. Setting realistic expectations for the as-built condition is crucial for effective project planning and cost estimation.
Précision dimensionnelle et tolérances :
- Tolérances typiques telles que construites : For most industrial Laser Powder Bed Fusion (LPBF) and Selective Electron Beam Melting (SEBM) systems, typical achievable tolerances for well-designed and properly processed parts fall in the range of:
- +/- 0.1 mm to +/- 0.2 mm for smaller dimensions (e.g., up to 50-100 mm).
- +/- 0.1% to +/- 0.2% of the nominal dimension for larger features.
- These values can often align with general tolerance standards like ISO 2768-m (medium) or sometimes ISO 2768-f (fine) for certain features, but this is not guaranteed across the entire part geometry without specific validation.
- Facteurs influençant la précision : Achieving consistent dimensional accuracy depends on numerous factors:
- Effets thermiques : The repeated heating and cooling cycles inherent in AM cause expansion and contraction, leading to internal stresses, potential shrinkage, and warping, especially in large or complex geometries like ribs. Advanced process simulation can help predict and compensate for some distortion.
- Étalonnage de la machine : Regular and precise calibration of the printer’s scanners, energy source, and powder deposition system is critical.
- Paramètres du processus : Laser/electron beam power, scan speed, layer thickness, and hatching strategy significantly impact the melt pool stability and resulting part accuracy. Optimized parameters developed by experienced providers are essential.
- Qualité de la poudre : Consistent powder characteristics (PSD, morphology, flowability) ensure uniform melting and solidification.
- Géométrie et orientation des pièces : Complex shapes with large overhangs or varying cross-sections are more prone to distortion. Build orientation affects thermal history and stress accumulation.
- Structures de soutien : Adequately designed supports help anchor the part and manage thermal stresses, improving dimensional stability during the build.
- Obtenir des tolérances plus strictes : For features requiring tolerances tighter than the general AM process capability (e.g., critical mounting interfaces, bearing bores, precise alignment features on a rib), l'usinage CNC post-processus is typically required. This involves machining specific surfaces of the as-built AM part to achieve the necessary precision. DfAM principles dictate adding machining stock to these features in the original design.
Finition de la surface (rugosité) :
- As-Built Surface Roughness (Ra): The surface finish of as-built metal AM parts is inherently rougher than machined surfaces. Typical Ra values can vary significantly:
- Top Surfaces: Generally smoother (Ra 5 – 15 µm).
- Vertical Walls (Z-axis): Moderate roughness, influenced by layer thickness and particle adhesion (Ra 8 – 20 µm).
- Up-facing/Down-facing Angled Surfaces: Exhibit characteristic “stair-stepping” due to the layered build process. Down-facing surfaces supported by structures are typically rougher due to support contact points (Ra 15 – 30 µm or higher).
- Factors Influencing Surface Finish:
- Épaisseur de la couche : Thinner layers generally produce smoother surfaces but increase build time.
- Powder Particle Size: Finer powders can lead to better surface finish but may pose challenges for flowability or require different process parameters.
- Energy Input & Scan Strategy: Affect melt pool dynamics and surface solidification.
- Orientation : Steeply angled surfaces will show more pronounced stair-stepping than surfaces built parallel or perpendicular to the build plate.
- Amélioration de l'état de surface : If the as-built roughness is unacceptable for functional (e.g., fluid flow, fatigue) or aesthetic reasons, various post-processing methods can be employed:
- Décapage par billes / Décapage au sable : Creates a uniform, matte finish, removes partially melted particles, and can slightly improve Ra (e.g., down to Ra 5-10 µm).
- Tambourinage / Finition vibratoire : Uses abrasive media to smooth surfaces and edges, particularly effective for batches of smaller parts.
- Usinage CNC : Provides the best possible surface finish on specific features.
- Polissage (manuel ou automatisé) : Can achieve very smooth, mirror-like finishes if required, but is often labor-intensive.
- Electropolishing / Chemical Polishing: Can smooth complex surfaces but may not be suitable for all geometries or alloys.
Metrology and Verification:
Given the geometric complexity often enabled by AM and the critical nature of aerospace components, robust metrology is essential.
- Techniques: Coordinate Measuring Machines (CMMs) are used for precise dimensional measurements of critical features. Non-contact methods like 3D laser scanning or structured light scanning are invaluable for comparing the entire printed part geometry against the original CAD model, identifying deviations, and verifying complex surfaces.
- Importance : Verification ensures that the final rib structure meets all design specifications for fit, form, and function. This data is crucial for quality assurance documentation required by aerospace standards.
Companies like Met3dp understand the importance of precision in aerospace. Their focus on industry-leading accuracy and reliability in their méthodes d'impression combined with rigorous quality control ensures that parts meet demanding specifications, whether in the as-built state or after necessary post-processing. Clear communication between the design team and the AM service provider regarding critical dimensions, tolerances, and surface finish requirements is paramount from the outset.
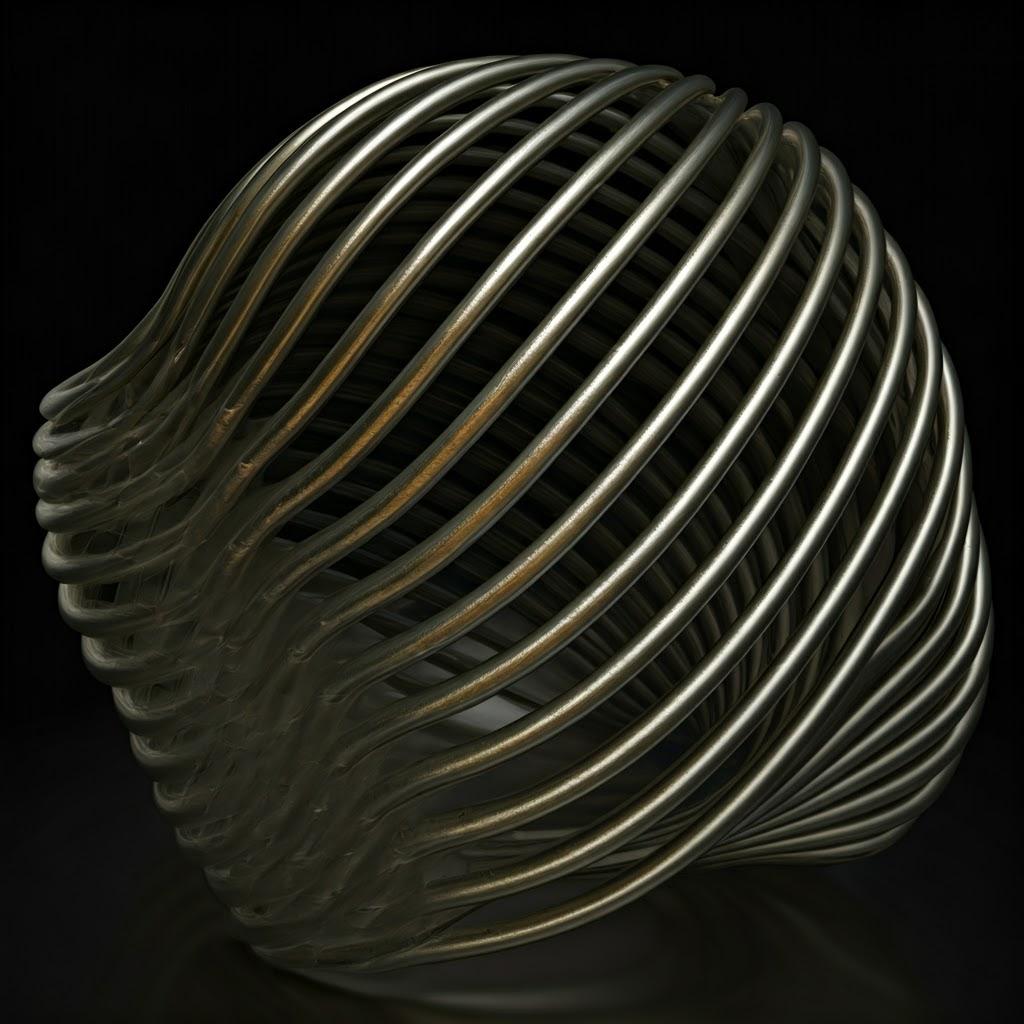
Essential Post-Processing Steps for Aerospace-Grade Rib Structures
Obtaining a finished, flight-ready aerospace rib structure involves significantly more than just the additive manufacturing build process itself. Post-processing steps are critical to relieve internal stresses, achieve the desired material properties, remove support structures, attain required tolerances and surface finishes, and verify the integrity of the component. These steps are often mandatory to meet stringent aerospace certification requirements and ensure the safety and reliability of the final part.
Here’s an overview of the essential post-processing sequence typically applied to metal AM aerospace ribs:
- Soulagement du stress :
- Objet : The rapid heating and cooling cycles during the PBF process induce significant residual stresses within the printed part. These stresses can cause distortion (especially after removal from the build plate) and negatively impact mechanical properties, particularly fatigue life. Stress relief is a thermal cycle designed to reduce these internal stresses without significantly altering the microstructure.
- Processus : Typically performed while the part is still attached to the build plate (though sometimes done after removal), involving heating the part to a specific temperature below the aging or solutionizing temperature, holding it for a defined period, and then slowly cooling it. This is usually done in a vacuum or inert atmosphere furnace (e.g., Argon) to prevent oxidation.
- Importance : Considered a mandatory first step for most critical metal AM parts to ensure dimensional stability and predictable performance.
- Retrait de la plaque de construction :
- Processus : Once stress relief is complete and the part has cooled, it needs to be separated from the build plate. This is commonly done using wire EDM (Electrical Discharge Machining), band sawing, or sometimes CNC machining.
- Considérations : Care must be taken to avoid damaging the part during removal. The chosen method depends on the part geometry, material, and required precision of the base surface.
- Traitement thermique (recuit de mise en solution, vieillissement, etc.) :
- Objet : To achieve the final desired microstructure and mechanical properties (strength, hardness, ductility) for the chosen alloy. For aluminum alloys like Scalmalloy® and AlSi10Mg, this often involves solution treatment followed by artificial aging (precipitation hardening), commonly referred to as a T6 or similar temper condition.
- Processus : Involves heating the part to a higher temperature (solutionizing temperature) to dissolve alloy elements into a solid solution, quenching (rapidly cooling) to lock this structure in place, and then aging (re-heating to a lower temperature for a specific time) to precipitate fine hardening particles within the grain structure. These cycles are precisely defined for each alloy and desired temper. Again, controlled atmosphere furnaces are crucial.
- Importance : Absolutely critical for developing the full strength potential of heat-treatable alloys like Scalmalloy® and AlSi10Mg, ensuring the rib meets its design performance targets.
- Pressage isostatique à chaud (HIP) :
- Objet : To eliminate internal microporosity that may be present even in well-processed AM parts. Porosity acts as stress concentrators and can significantly degrade fatigue life and fracture toughness.
- Processus : Involves subjecting the component to high temperature (below melting point) and high isostatic pressure (typically 100-200 MPa) using an inert gas (like Argon) within a specialized HIP vessel. The combination of heat and pressure causes internal voids to collapse and diffusion bond shut.
- Importance : Often mandated by aerospace standards (e.g., for Class A / flight-critical components) as it significantly improves fatigue strength, ductility, and overall material integrity, leading to more reliable and predictable parts. It adds cost but is frequently a non-negotiable step for demanding applications.
- Retrait de la structure de soutien :
- Objet : To remove the temporary support structures used during the build process.
- Processus : Can be one of the most labor-intensive steps, especially for complex rib geometries with internal supports. Methods include:
- Suppression manuelle : Casser ou découper les supports facilement accessibles.
- Usinage CNC : Milling or grinding away support structures, often used for block supports or to achieve a clean surface finish at the support interface.
- Wire EDM / Plunge EDM: Used for precise removal or in difficult-to-reach areas.
- Considérations : Requires careful execution to avoid damaging the part surface. DfAM plays a huge role here – designing for support accessibility is key. Witness marks (small blemishes where supports were attached) may need further finishing.
- Surface Finishing & Machining:
- Objet : To achieve the final required surface roughness, dimensional tolerances on critical features, and cosmetic appearance.
- Processes (as required):
- Usinage CNC : Essential for creating precise mating surfaces, bearing bores, mounting holes, and achieving tight tolerances specified on the drawing that exceed as-built AM capabilities.
- Microbillage / Grenaillage : Provides a uniform matte finish, cleans surfaces, and shot peening induces beneficial compressive stresses to improve fatigue life.
- Tumbling / Polishing: For general surface smoothing or specific aerodynamic/aesthetic requirements.
- Deburring: Removing any sharp edges or burrs left from machining or support removal.
- Non-Destructive Testing (NDT) and Inspection:
- Objet : To verify the internal and external integrity of the finished rib structure without damaging it, ensuring it is free from critical defects and meets all dimensional specifications.
- Common NDT Methods for AM Aerospace Parts:
- Computed Tomography (CT Scanning): X-ray based method providing detailed 3D visualization of internal structures, highly effective for detecting porosity, inclusions, cracks, and performing internal dimensional analysis. Increasingly common for critical AM parts.
- Contrôle par ultrasons (UT) : Uses sound waves to detect internal flaws.
- Dye Penetrant Inspection (DPI) / Liquid Penetrant Inspection (LPI): Détecte les fissures superficielles.
- Radiographic Testing (RT): Traditional X-ray imaging.
- Inspection dimensionnelle : Using CMMs and 3D scanners to verify all critical dimensions and overall geometry against the design specifications.
- Importance : Final quality gate before the component is certified for use. Mandatory for ensuring flight safety.
Successfully navigating this complex post-processing chain requires significant expertise and specialized equipment. Aerospace manufacturers et procurement specialists should seek fournisseurs de services de fabrication additive métallique who offer comprehensive, integrated solutions, either in-house or through qualified partners, covering the entire workflow from printing through final inspection, ensuring traceability and quality control at every stage.
Common Challenges in 3D Printing Aerospace Ribs and Mitigation Strategies
While metal additive manufacturing offers transformative potential for aerospace rib structures, realizing these benefits requires navigating several inherent challenges. Understanding these potential hurdles and implementing effective mitigation strategies is crucial for successful adoption, particularly for engineers designing the parts and procurement managers selecting AM quality control aerospace partners.
Here are some common challenges encountered when 3D printing complex aerospace ribs:
- Contraintes résiduelles et déformation :
- Défi: The intense, localized heating and rapid cooling during the PBF process create significant temperature gradients within the part. This leads to differential expansion and contraction, resulting in built-in residual stresses. If these stresses exceed the material’s yield strength, they can cause distortion (warping) during the build, after removal from the build plate, or even during post-processing. Complex rib geometries with varying thicknesses and large flat sections can be particularly susceptible.
- Stratégies d'atténuation :
- Simulation de processus : Using thermal simulation software during the design phase to predict stress concentration areas and potential distortion based on geometry and proposed orientation.
- Orientation optimisée : Selecting a build orientation that minimizes large cross-sectional areas parallel to the build plate and reduces thermal gradients.
- Structures de soutien robustes : Designing effective supports that not only anchor the part but also act as heat sinks, drawing heat away more uniformly.
- Stratégies d'analyse optimisées : Using specific laser/beam scanning patterns (e.g., island scanning, sector hatching) designed to distribute heat more evenly and reduce stress build-up.
- Immediate Stress Relief: Performing a stress relief heat treatment cycle immediately after the build, ideally before removing the part from the build plate, is critical.
- Support Structure Removal Difficulty:
- Défi: Topology-optimized ribs often feature complex overhangs and internal cavities requiring extensive support structures. Removing these supports, especially from internal or difficult-to-reach areas, can be extremely challenging, time-consuming, and costly. Improper removal can also damage the part surface.
- Stratégies d'atténuation :
- Focus DfAM : Designing for support minimization (using self-supporting angles, avoiding internal overhangs where possible) and ease of access is paramount. Design features that allow tools or hands to reach internal supports.
- Advanced Support Software: Utilizing software that generates easily removable support types (e.g., thin webs, conical/tree supports with small contact points, perforated structures).
- Appropriate Removal Techniques: Selecting the right method (manual, CNC machining, wire/sinker EDM) based on support type, location, and material.
- Orientation de la construction : Orienting the part to minimize the volume and complexity of required supports.
- Contrôle de la porosité :
- Défi: Achieving full density (>99.5% or often >99.9% for aerospace) is critical. Internal pores (gas porosity from trapped Argon/powder contaminants or keyhole porosity from unstable melt pools) act as defects, significantly degrading mechanical properties, especially fatigue strength.
- Stratégies d'atténuation :
- Poudre de haute qualité : Using powder with controlled sphericity, PSD, low internal gas content, and strict handling procedures to prevent moisture absorption and contamination. This highlights the importance of providers like Met3dp with advanced powder manufacturing capabilities (learn more about Met3dp).
- Paramètres de processus optimisés : Rigorous development and validation of printing parameters (laser/beam power, speed, focus, layer thickness, atmosphere control) specific to the material and machine to ensure stable melting.
- Surveillance des processus : Utilizing in-situ monitoring tools (e.g., melt pool monitoring) to detect potential instabilities during the build.
- Pressage isostatique à chaud (HIP) : As discussed, HIP is highly effective at closing residual microporosity and is often mandatory for critical aerospace parts to guarantee density and enhance fatigue performance.
- Achieving Consistent Mechanical Properties:
- Défi: Ensuring that the specified mechanical properties (strength, ductility, fatigue life) are consistently achieved throughout the entire complex rib structure and are repeatable from build to build. Variations can arise from minor inconsistencies in powder, machine calibration, or process parameters. Anisotropy also plays a role.
- Stratégies d'atténuation :
- Strict Powder Management: Rigorous quality control of incoming powder, defined powder recycling strategies (limiting reuse cycles, regular testing), and proper storage/handling.
- Robust Machine Calibration & Maintenance: Regular preventative maintenance and calibration schedules for AM systems.
- Standardized Processes: Implementing and adhering to qualified, standardized printing and post-processing procedures (including heat treat and HIP).
- Process Monitoring & Quality Assurance: Utilizing process monitoring data and implementing rigorous quality assurance protocols, including witness coupons (test specimens built alongside the part) for destructive testing to verify batch properties.
- Understanding Anisotropy: Characterizing material properties in different build orientations and accounting for this in design and qualification.
- Surface Finish Limitations:
- Défi: The as-built surface finish of AM parts may not meet the requirements for certain aerodynamic surfaces or fatigue-critical areas. Achieving very smooth finishes requires additional post-processing effort and cost. Managing expectations regarding as-built vs. finished surfaces is important.
- Stratégies d'atténuation :
- Optimisation de l'orientation : Orienting critical surfaces vertically or horizontally where possible to achieve the best native finish.
- Paramètres optimisés : Fine-tuning contour parameters can sometimes improve sidewall finish.
- Targeted Post-Processing: Applying appropriate finishing methods (blasting, machining, polishing) specifically to the surfaces where improved finish is required, rather than the entire part.
- Clear Specification: Clearly defining surface finish requirements on drawings for specific features.
- Cost Management:
- Défi: While AM enables incredible designs, extreme complexity can increase build times (more layers, intricate scan paths), support material volume, and post-processing time (especially support removal and finishing), driving up costs. The high cost of materials like Scalmalloy® is also a factor.
- Stratégies d'atténuation :
- Holistic DfAM: Balancing performance optimization with manufacturability. Sometimes slightly less optimized designs are significantly easier and cheaper to print and process.
- Efficient Nesting: Maximizing the number of parts built simultaneously on the build plate reduces setup/cooldown time per part.
- Sélection des matériaux : Choosing the most cost-effective material that meets performance requirements (e.g., AlSi10Mg instead of Scalmalloy® if feasible).
- Experienced Partners: Working with AM service providers who can offer guidance on cost-effective design and processing strategies.
Successfully overcoming these challenges requires a combination of sophisticated design tools, advanced process control, rigorous quality management, and deep expertise in materials science and additive manufacturing processes. Partnering with a vertically integrated or highly experienced metal 3D printing service provider is often the most effective mitigation strategy for aerospace companies venturing into AM for critical structures like ribs.
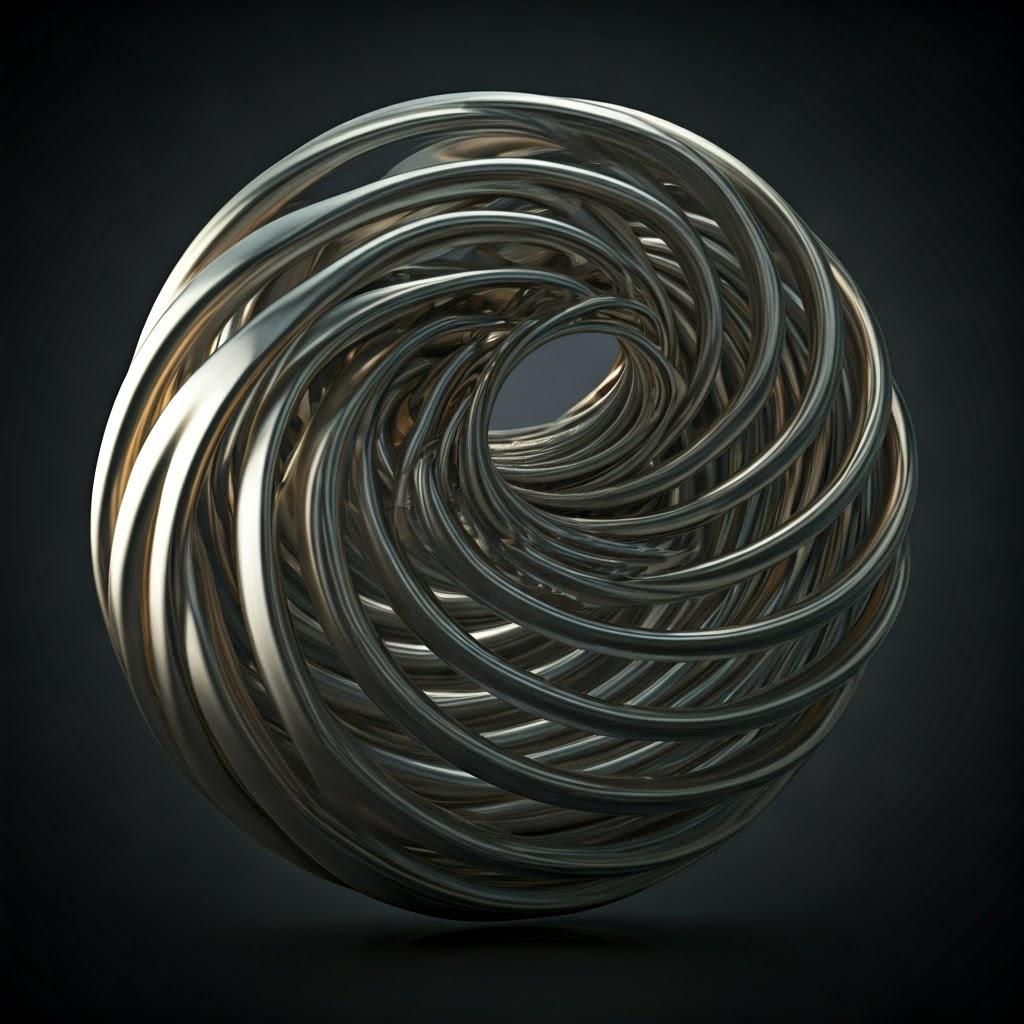
Choisir le bon fournisseur de services d'impression 3D de métaux pour les composants aérospatiaux
Choosing a manufacturing partner for critical aerospace components like 3D printed ribs is a decision that carries significant weight. The quality, reliability, and airworthiness of the final part depend heavily on the capabilities, processes, and expertise of your chosen fournisseur de services AM en métal. For engineers and aerospace procurement managers, evaluating potential aerospace additive manufacturing suppliers requires a thorough due diligence process focusing on specific criteria crucial to the aerospace industry. Simply selecting based on the lowest quote can introduce unacceptable risks.
Here’s a comprehensive guide to evaluating and selecting the right partner for your metal 3D printing aerospace needs:
- Aerospace Experience and Certification (AS9100):
- Certification AS9100 : This is the internationally recognized Quality Management System (QMS) standard for the aviation, space, and defense industries. Non-negotiable for manufacturing flight-critical components. Verify that the provider holds a current AS9100 certification and, importantly, that the scope of their certification covers the specific processes (e.g., LPBF/SEBM printing, heat treatment, NDT) and materials relevant to your project.
- Proven Track Record: Look for evidence of successful projects with other aerospace OEMs or reputable tier suppliers. Case studies, references (if available), and demonstrated experience with similar components (e.g., structural parts, lightweight designs) are valuable indicators.
- ITAR Compliance: If working on defense-related projects subject to US International Traffic in Arms Regulations, ensure the provider meets ITAR registration and compliance requirements.
- Material Expertise and Traceability:
- Specific Alloy Capabilities: Confirm the provider has proven, qualified processes for the specific aerospace alloys you require (e.g., Scalmalloy®, AlSi10Mg, Ti-6Al-4V, IN718). Ask about their experience level with these materials.
- Contrôle de la qualité des poudres : Inquire about their procedures for sourcing, testing (e.g., chemistry, Particle Size Distribution (PSD), morphology, flowability), handling, storing, and recycling metal powders. Providers like Met3dp, who manufacture their own high-quality powders using advanced atomization techniques, can offer greater control over this critical input material.
- Full Material Traceability: Robust systems must be in place to track powder batches from sourcing through processing, printing (linking specific batches to specific builds/parts), and final component release. This is essential for quality assurance and certification.
- Technological Capabilities and Capacity:
- Appropriate AM Technology: Do they offer the best-suited technology (e.g., LPBF for fine features, SEBM for certain materials or productivity benefits) for your specific rib design and material? Met3dp, for instance, specializes in SEBM systems known for accuracy and reliability.
- Machine Fleet & Build Volume: Assess their specific printer models, build envelope sizes (can they accommodate your rib dimensions?), and the number of machines available. Sufficient capacity is needed to meet project lead times and potentially scale to production volumes.
- Surveillance des processus : What in-situ process monitoring capabilities do their machines have (e.g., melt pool monitoring, thermal imaging)? This data can be valuable for quality assurance and process consistency.
- Integrated Post-Processing Capabilities:
- Comprehensive Services: Evaluate whether they offer the required post-processing steps (stress relief, heat treatment, HIP, support removal, CNC machining, surface finishing, NDT) in-house or through a tightly controlled network of qualified partners.
- Expertise : Ensure they (or their partners) have specific expertise in post-processing AM parts, which can behave differently than wrought or cast materials. Heat treatment cycles, machining strategies, and NDT interpretation may need adaptation for AM components.
- Quality Management: If using external partners, how does the primary provider manage the quality and traceability throughout the entire supply chain? An integrated approach often simplifies logistics and quality oversight.
- Système de gestion de la qualité (SGQ) robuste :
- Beyond Certification: While AS9100 is essential, delve deeper into their day-to-day quality practices. Ask about process validation procedures, operator training programs, equipment calibration schedules, non-conformance reporting and corrective action processes, and documentation control.
- Capacités d'inspection : Do they have the necessary metrology equipment (CMM, 3D scanners) and NDT capabilities (or certified partners) to thoroughly inspect parts against demanding aerospace specifications?
- Ingénierie et soutien du DfAM :
- Collaborative Partnership: Does the provider act as just a print bureau, or do they offer value-added engineering support? Look for DfAM expertise to help optimize your rib design for printability, performance, and cost-effectiveness.
- Simulation Capabilities: Can they perform process simulation to predict thermal stresses and distortion, helping to optimize orientation and support strategies upfront?
- Problem Solving: Assess their willingness and ability to collaborate on resolving technical challenges that may arise during development or production.
- Gestion de projet et communication :
- Clear Quoting: Is their quoting process transparent and detailed, clearly outlining all included steps and associated costs?
- Communication: Will you have a dedicated point of contact? How frequently will they provide project updates? Clear, proactive communication is vital for managing complex aerospace projects.
- Reporting: What level of documentation (material certs, build logs, inspection reports, certificates of conformance) will be provided with the finished parts?
- Facility, Security, and Stability:
- Cleanliness & Controls: A clean, well-organized facility with appropriate environmental controls is indicative of a professional operation.
- Data Security: Ensure they have adequate measures to protect your sensitive design data (IP).
- Stabilité financière : Assess the provider’s stability, especially if considering them for long-term production partnerships.
Selecting the right provider is about finding a true partner who understands the high stakes of aerospace manufacturing. Companies like Met3dp, offering comprehensive solutions that span advanced SEBM printers, specialized poudres métalliques de haute qualité developed through industry-leading techniques, and application development services, exemplify the kind of integrated expertise beneficial for demanding projects. Visiting facilities, conducting audits, and having detailed technical discussions are recommended steps in the metal 3D printing partner evaluation process. You can learn more About Met3dp and their commitment to advancing additive manufacturing.
Cost Factors and Lead Time Estimation for 3D Printed Aerospace Ribs
Pour aerospace component procurement AM strategies to be effective, a clear understanding of the factors driving cost and lead time for 3D printed ribs is essential. Unlike traditional manufacturing where tooling can be a major upfront cost, AM costs are more closely tied to material consumption, machine time, and the complexity of post-processing. Lead times are influenced by various stages, from design review to final inspection.
Key Cost Drivers for Metal AM Rib Structures:
- Consommation de matériaux :
- Type de poudre : This is often a primary driver. High-performance alloys like Scalmalloy® printing cost significantly more per kilogram than standard alloys like AlSi10Mg printing cost.
- Volume de la pièce : The actual geometric volume of the final rib structure directly impacts the amount of powder fused.
- Support Structure Volume: Support structures also consume powder, and complex designs requiring extensive supports will incur higher material costs. Efficient DfAM aims to minimize this.
- Nesting Efficiency: How effectively multiple parts can be arranged on the build plate impacts the ratio of part volume to potentially wasted powder in the surrounding bed (though unfused powder is typically recycled).
- Le temps des machines :
- Build Height: The primary factor determining the number of layers required. Taller parts take longer.
- Part Cross-Sectional Area & Complexity: Influences the scanning time required for each layer. Highly complex internal structures or extensive hatching increase time.
- Number of Parts per Build: Nesting multiple ribs efficiently utilizes machine time better than printing single parts.
- Machine Taux horaire : Varies depending on the specific AM system (LPBF vs. SEBM), its capabilities, and the service provider’s pricing structure.
- Travail :
- Setup & Teardown: Time required for preparing the machine, loading powder, removing the completed build, and cleaning the system.
- Main-d'œuvre de post-traitement : Manual support removal, finishing, inspection, and handling can be significant contributors, especially for complex parts.
- Coûts de post-traitement :
- Soulagement du stress / Traitement thermique : Furnace time, energy consumption, controlled atmosphere costs.
- Pressage isostatique à chaud (HIP) : Often a substantial cost adder due to specialized equipment and long cycle times. Typically priced per cycle or by volume/weight.
- Suppression du support : Can be manual labor-intensive or require machine time (CNC, EDM).
- Usinage CNC : Costs associated with programming, setup, fixture design (if needed), machine time, and tooling for finishing critical features.
- Finition de la surface : Costs for blasting, tumbling, polishing, etc.
- CND et inspection : Costs for specialized equipment (CT scanners, CMMs) and qualified technician time.
- Engineering & Quality Assurance:
- DfAM Consultation: If requiring significant design support from the provider.
- Qualification du processus : Costs associated with first article inspection (FAI), developing qualified process parameters, and potentially destructive testing for initial batches.
- Documentation : Time spent preparing comprehensive quality documentation packages.
- Quantité :
- Economies d'échelle : While AM is often cost-effective for low volumes, some economies of scale exist. Setup, qualification, and programming costs can be amortized over larger batches. Powder costs may decrease slightly with bulk purchases. However, the primary cost drivers (material, machine time) scale fairly linearly.
Typical Lead Time Components:
Estimating the délai de fabrication additive requires considering all stages involved:
- Quoting & Design Review: 1-5 business days (depending on complexity and provider responsiveness).
- Print Queue & Scheduling: Highly variable, from a few days to several weeks, depending on the provider’s backlog and machine availability.
- Impression : Hours to multiple days (e.g., 12 hours to 72+ hours) depending primarily on build height and volume.
- Cooldown: Several hours.
- Soulagement du stress / Traitement thermique : 1-3 days (including furnace time and controlled cooling).
- HIP: 2-5 days (HIP cycles are long, and parts are often batched; may involve shipping to a specialized HIP provider).
- Support Removal / Machining / Finishing: Highly variable, from 1 day for simple removal to 1-2+ weeks for complex machining and finishing.
- CND et inspection : 1-3 days (depending on methods required and reporting).
- Expédition: 1-5 days (domestic/international).
Overall Estimated Lead Time:
- Simple Prototypes (AlSi10Mg, minimal post-processing): 1-3 weeks.
- Complex Ribs (Scalmalloy®, full heat treatment, HIP, machining, NDT): 6-12 weeks or potentially longer, depending on all factors.
Cost Optimization Strategies:
- Optimize the design using DfAM to minimize volume and support structures.
- Select the most cost-effective material that meets all performance requirements.
- Clearly define only necessary tolerances and surface finishes to avoid excessive machining.
- Consolidate parts into single builds where possible.
- Work closely with your AM provider to understand cost trade-offs during the design phase.
Understanding these cost and lead time dynamics is crucial for budgeting, project planning, and integrating Impression 3D de métaux effectively into the aerospace supply chain.
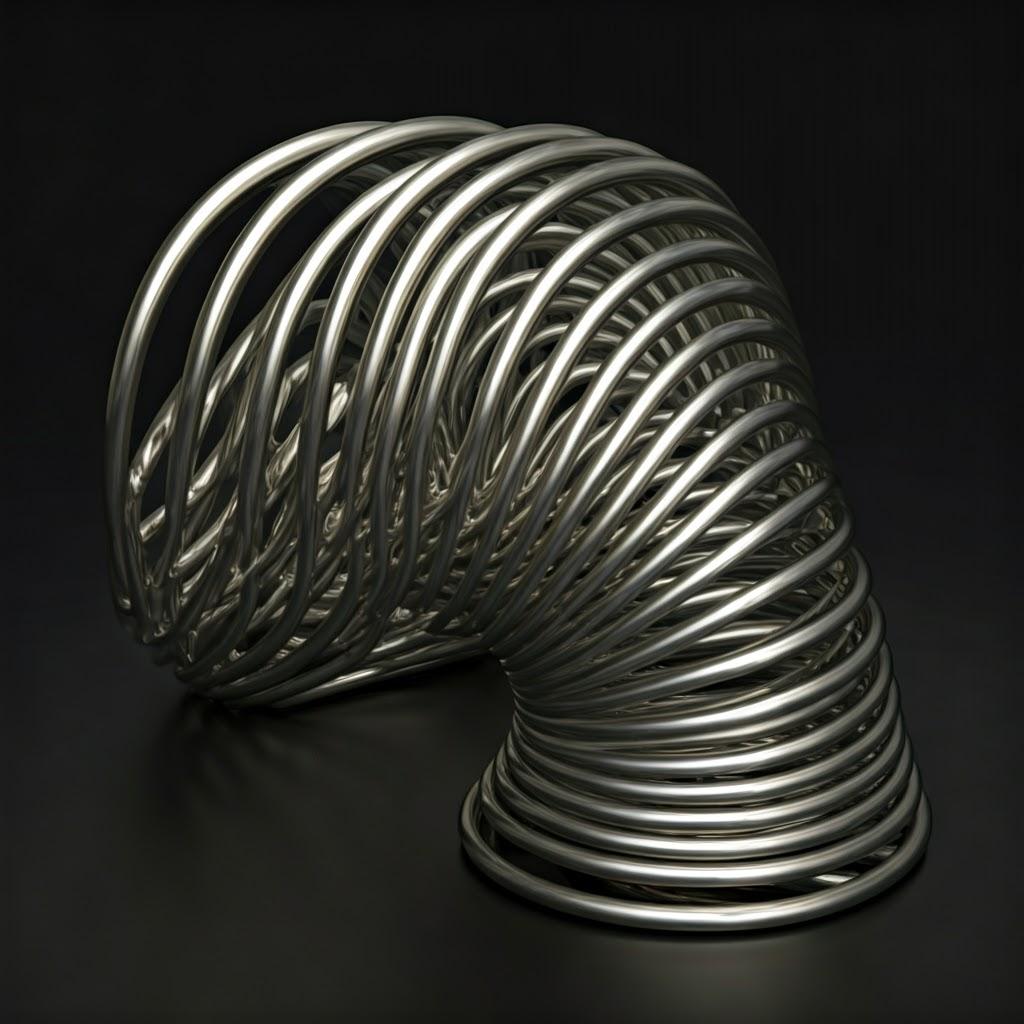
Frequently Asked Questions (FAQ) about 3D Printed Aerospace Ribs
Here are answers to some common questions engineers and procurement specialists have about using metal additive manufacturing for aerospace rib structures:
- How does the strength of 3D printed Scalmalloy® or AlSi10Mg compare to traditional wrought aluminum alloys like 7075-T6?
- Scalmalloy® (Heat Treated): Its strength properties (UTS > 520 MPa, YS > 480 MPa) are highly competitive and often exceed those of many traditional high-strength aluminum alloys like 7075-T6 (typical UTS ~570 MPa, YS ~500 MPa) when considering specific strength (strength-to-weight). Critically, Scalmalloy® often demonstrates superior fatigue performance compared to many wrought alloys, especially in the presence of notches or typical AM surface features.
- AlSi10Mg (Heat Treated – T6): Is significantly less strong than 7075-T6. Its properties (UTS ~300-350 MPa, YS ~230-280 MPa) are more comparable to mid-strength wrought alloys like 6061-T6.
- Principaux enseignements : Scalmalloy® enables direct competition with high-strength wrought alloys on a performance basis, especially when lightweighting and fatigue are key. AlSi10Mg is suitable for less demanding structural applications. Proper heat treatment is crucial for both AM alloys.
- Can 3D printed ribs meet the stringent certification requirements for flight-critical components?
- Yes, absolutely. Metal AM components are increasingly being certified for flight-critical (Class A) applications. However, achieving certification requires a highly rigorous and controlled approach encompassing:
- Mature & Stable AM Process: Using qualified machines with locked-down, validated process parameters.
- Qualified Material: Strict control and testing of incoming powder feedstock and recycling procedures. Material properties must meet established allowables (often developed through extensive testing programs similar to MMPDS for traditional materials, or via specific part qualification).
- Robust Quality Management System: AS9100 certification is a prerequisite, along with detailed process controls, traceability, and documentation.
- Comprehensive Post-Processing: Standardized and qualified procedures for stress relief, heat treatment, HIP (often required), machining, and finishing.
- Rigorous NDT & Inspection: Employing validated NDT techniques (like CT scanning) and dimensional inspection to verify part integrity and conformance.
- Collaboration : Close collaboration between the designer, AM service provider, and certification authorities.
- Yes, absolutely. Metal AM components are increasingly being certified for flight-critical (Class A) applications. However, achieving certification requires a highly rigorous and controlled approach encompassing:
- What is the typical weight saving achieved by redesigning a rib structure for AM?
- Weight savings typically range from 20% to 60% or even higher compared to traditionally manufactured (e.g., machined billet) counterparts designed for the same load cases. The actual saving depends heavily on:
- The complexity and efficiency of the original design.
- The freedom available for topology optimization (design space, load cases).
- The chosen AM material (e.g., using high specific strength Scalmalloy® allows for greater savings).
- Whether part consolidation is achieved.
- Weight savings typically range from 20% to 60% or even higher compared to traditionally manufactured (e.g., machined billet) counterparts designed for the same load cases. The actual saving depends heavily on:
- Is Hot Isostatic Pressing (HIP) always necessary for 3D printed aluminum aerospace parts?
- Not always, but it is highly recommended and often mandatory for fatigue-critical or fracture-critical aerospace components. HIP significantly improves material integrity by closing internal microporosity, which enhances ductility, fracture toughness, and most importantly, fatigue life. For primary structural elements like ribs, where fatigue performance is crucial, regulatory authorities and prime contractors typically require HIP treatment as part of the qualification process to ensure maximum reliability and safety. For less critical (e.g., secondary structure) or non-load-bearing parts, it might be omitted if justified by analysis and testing.
- What information is needed to get an accurate quote from a metal AM service provider like Met3dp?
- To provide an accurate quote and assess manufacturability, providers typically need:
- Modèle CAO 3D : Native CAD or preferably STEP (.stp/.step) format.
- Spécification du matériau : Clearly defined alloy (e.g., Scalmalloy®, AlSi10Mg) and any required temper/heat treatment condition (e.g., T6).
- 2D Drawings (if available): Specifying critical dimensions, tolerances (using GD&T), required surface finishes for specific features, and any other key requirements.
- Quantité : Number of parts required (for prototype vs. production run).
- Required Certifications: Specify if AS9100 compliance, material certs, Certificates of Conformance (CoC), or First Article Inspection (FAI) reports are needed.
- NDT Requirements: Detail any required non-destructive testing (e.g., CT scan acceptance criteria, LPI).
- Besoins en post-traitement : Specify required machining, surface finishes, coatings, etc.
- Desired Lead Time: Indicate your target delivery date.
- To provide an accurate quote and assess manufacturability, providers typically need:
Conclusion: Elevating Aerospace Structures with Metal Additive Manufacturing
The journey through the intricacies of 3D printed aerospace rib structures reveals a compelling narrative of innovation meeting necessity. Metal additive manufacturing is no longer a futuristic concept but a tangible, powerful tool enabling aerospace engineers and manufacturers to push the boundaries of performance and efficiency. For components like ribs, where structural integrity must coexist with the relentless pursuit of weight reduction, AM offers a transformative pathway.
En tirant parti optimisation de la topologie and the design freedom inherent in AM, engineers can craft rib structures that are radically lighter yet meet demanding strength and stiffness requirements. The ability to consolidate multiple components into a single printed part simplifies assembly, reduces potential failure points, and further contributes to weight savings. High-performance materials tailored for AM, such as the exceptional strength-to-weight ratio of Scalmalloy® (alliage d'aluminium) or the reliable processability of AlSi10Mg, provide tailored solutions for diverse aerospace applications.
However, realizing these benefits demands a holistic approach. Effective Conception pour la fabrication additive (DfAM) principles must guide the initial concept, considering not just optimization but also manufacturability, support strategies, and downstream processing. Achieving the necessary dimensional accuracy and surface finish often relies on meticulous post-traitement, including critical steps like stress relief, heat treatment, Hot Isostatic Pressing (HIP), precision machining, and rigorous Non-Destructive Testing (NDT). Navigating the common challenges of residual stress, support removal, and porosity control requires deep process expertise and robust quality management.
Successfully implementing metal AM for critical aerospace components hinges significantly on choosing the right manufacturing partner. Expertise in aerospace requirements, AS9100 certification, proven material capabilities, advanced technological infrastructure, integrated post-processing, and unwavering commitment to quality are paramount.
Met3dp stands as a knowledgeable partner in this advanced manufacturing landscape. With comprehensive solutions encompassing cutting-edge SEBM printing technology renowned for accuracy and reliability, the in-house capability to produce high-purity, spherical metal powders optimized for AM using advanced atomization, and dedicated application development support, Met3dp empowers organizations to leverage the full potential of metal additive manufacturing.
The future of aerospace structures is undeniably linked to the capabilities of additive manufacturing. For your next project involving complex, lightweight structural components like ribs, consider the transformative possibilities. Explore how metal AM can help you achieve unprecedented weight savings, enhance performance, and accelerate your innovation cycles.
Ready to explore how metal additive manufacturing can elevate your aerospace components? Contact Met3dp today to discuss your project requirements and learn how our expertise can power your organization’s additive manufacturing goals.
Visite Met3dp pour en savoir plus.
Partager sur
MET3DP Technology Co. est un fournisseur de premier plan de solutions de fabrication additive dont le siège se trouve à Qingdao, en Chine. Notre société est spécialisée dans les équipements d'impression 3D et les poudres métalliques de haute performance pour les applications industrielles.
Articles connexes
À propos de Met3DP
Mise à jour récente
Notre produit
CONTACTEZ-NOUS
Vous avez des questions ? Envoyez-nous un message dès maintenant ! Nous répondrons à votre demande avec toute une équipe dès réception de votre message.
Obtenir les informations de Metal3DP
Brochure du produit
Obtenir les derniers produits et la liste des prix
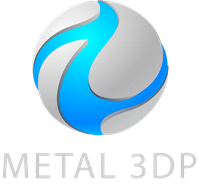
Poudres métalliques pour l'impression 3D et la fabrication additive