La transformation de la SLM dans l'aérospatiale
Table des matières
L'industrie aérospatiale a toujours été pionnière en repoussant les limites de la conception et de la technologie. Imaginez un monde où les avions seraient plus légers, plus résistants et plus économes en carburant. Ce rêve est en train de devenir réalité grâce à la fusion sélective par laser (SLM), une technique d'impression 3D révolutionnaire qui fait des vagues dans ce domaine. Le SLM transforme la façon dont les composants aérospatiaux sont fabriqués, ouvrant la voie à des conceptions innovantes et à l'optimisation des performances. Mais comment la technologie SLM prend-elle son envol dans le monde des avions, des fusées et au-delà ? Approfondissons la question et explorons les applications spécifiques de la technologie SLM dans l'industrie aérospatiale.
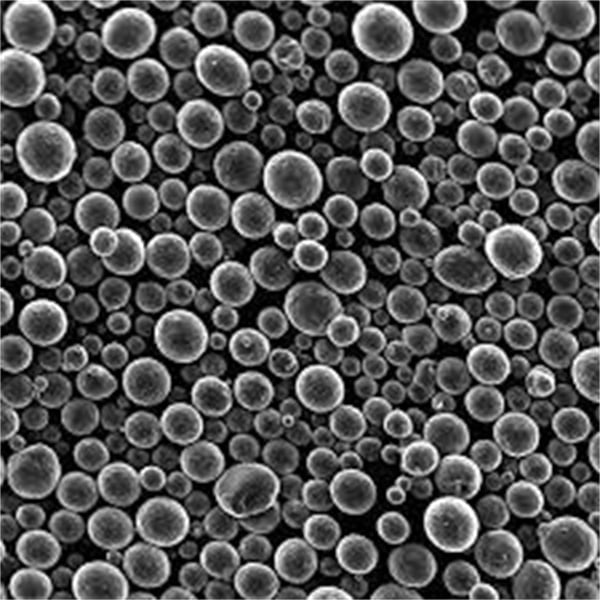
Poudres métalliques pour l'aérospatiale SLM
La magie des poudres métalliques est au cœur de la technique SLM. Ces fines particules métalliques sont méticuleusement superposées et fusionnées à l'aide d'un laser puissant, créant ainsi des structures 3D complexes à la demande. La poudre métallique utilisée joue un rôle crucial dans la détermination des propriétés et des performances du composant final. Voici un aperçu de quelques-unes des principales poudres métalliques utilisées dans la technique SLM pour les applications aérospatiales :
Poudres métalliques pour l'aérospatiale SLM
Poudre de métal | Composition | Propriétés | Caractéristiques | Applications dans l'aérospatiale |
---|---|---|---|---|
Alliages de titane (Ti-6Al-4V, Ti-6Al-4V ELI) | Titane (Ti), Aluminium (Al), Vanadium (V) | Rapport résistance/poids élevé, excellente résistance à la corrosion, biocompatible | Les particules de poudre sont sphériques pour un écoulement optimal et une fusion au laser. | Aubes de turbines, composants de trains d'atterrissage, composants structurels des cellules d'avion, |
Superalliages à base de nickel (Inconel 625, Inconel 718) | Nickel (Ni), chrome (Cr), cobalt (Co), molybdène (Mo) et autres éléments | Résistance aux températures élevées, résistance à l'oxydation | Plus difficile à mettre en œuvre que les alliages de titane | Disques de turbine, revêtements de chambre de combustion, composants de postcombustion |
Alliages d'aluminium (AlSi10Mg, Scalmalloy) | Aluminium (Al), Silicium (Si), Magnésium (Mg) | Légèreté, bonne résistance, soudabilité | Conductivité thermique élevée par rapport à d'autres alliages | Échangeurs de chaleur, composants de l'aile, composants du fuselage |
Chrome cobalt (CoCr) | Cobalt (Co), Chrome (Cr) | Haute résistance à l'usure, biocompatible | Souvent utilisés dans les applications médicales, ils gagnent en popularité dans l'aérospatiale pour des pièces d'usure spécifiques. | Roulements, engrenages, composants de trains d'atterrissage |
Acier inoxydable (316L, 17-4 PH) | Fer (Fe), Chrome (Cr), Nickel (Ni), Molybdène (Mo) | Résistance à la corrosion, bonne résistance | Relativement abordable par rapport à d'autres poudres métalliques | Composants des systèmes de fluides, composants structurels nécessitant une bonne résistance à la corrosion |
Alliages de cuivre (CuNi) | Cuivre (Cu), Nickel (Ni) | Conductivité thermique élevée, bonne conductivité électrique | Utilisé pour les applications nécessitant un transfert de chaleur efficace | Dissipateurs de chaleur, barres omnibus pour systèmes électriques |
Tantale (Ta) | Tantale (Ta) | Point de fusion élevé, excellente résistance à la corrosion | Poudre métallique relativement coûteuse | Revêtements de creusets pour applications à haute température, boucliers thermiques |
Molybdène (Mo) | Molybdène (Mo) | Point de fusion élevé, bonne conductivité thermique | Utilisé en combinaison avec d'autres métaux dans les superalliages | Composants à haute température dans les moteurs de fusée |
Tungstène (W) | Tungstène (W) | Point de fusion très élevé, excellente résistance à l'usure | Difficile à traiter en raison du point de fusion élevé | Tuyères pour moteurs de fusées, boucliers thermiques pour véhicules de rentrée dans l'atmosphère |
Inconel fabriqué de manière additive (AM) | Nickel (Ni), chrome (Cr), cobalt (Co), molybdène (Mo) et autres éléments | Propriétés sur mesure grâce au processus AM | Permet de créer des microstructures uniques aux propriétés spécifiques | Aubes de turbine haute performance avec canaux de refroidissement optimisés |
Comme vous pouvez le constater, la sélection de poudres métalliques pour le SLM dans l'aérospatiale est vaste et soigneusement choisie en fonction des exigences de l'application spécifique. De la robustesse des alliages de titane pour les pales de turbine à la légèreté de l'aluminium pour les composants des cellules d'avion, la technique SLM permet de créer des pièces aux propriétés exceptionnelles qui n'auraient pas pu être obtenues avec les méthodes de fabrication traditionnelles.
Applications de SLM dans l'aérospatiale
L'impact de la technologie SLM dans l'aérospatiale va bien au-delà des matériaux utilisés. Cette technologie révolutionne la façon dont les composants des avions sont conçus et fabriqués, ouvrant la voie à une nouvelle ère d'innovation. Voici quelques-unes des principales applications de la technologie SLM dans le domaine aérospatial :
Applications SLM dans l'aérospatiale
Application | Avantages | Exemples |
---|---|---|
Aubes de turbine | Canaux de refroidissement internes complexes pour une meilleure efficacité, un poids réduit et la possibilité de créer des géométries de pales complexes pour de meilleures performances. | Aubes de turbine haute pression, aubes de turbine basse pression, blisks (aubes de turbine et disque intégrés) |
Composants du train d'atterrissage | Poids plus léger pour une meilleure efficacité énergétique, liberté de conception pour des structures en treillis complexes pour une meilleure absorption des chocs | Supports de train d'atterrissage, jambes de force, composants structurels |
Composants structurels de la cellule | Optimisation de la topologie pour réduire le poids, capacité à fabriquer des formes complexes difficiles à réaliser avec les méthodes traditionnelles | Côtes, lisses, longerons (éléments structurels) |
Chemises de combustion | Canaux de refroidissement conformes pour une meilleure gestion thermique, capacité à créer des caractéristiques de surface complexes pour un meilleur mélange air-carburant | Revêtements de chambre de combustion pour une meilleure efficacité et une réduction des émissions |
Échangeurs de chaleur | Conception légère avec une surface élevée pour un transfert de chaleur efficace | Échangeurs de chaleur air-air, refroidisseurs d'huile |
Composants du satellite | Réduction du poids pour une capacité de charge accrue, possibilité de fabriquer des structures complexes pour des fonctionnalités spécifiques | Supports, antennes, composants structurels |
Composants du moteur-fusée | Matériaux résistants aux hautes températures pour les environnements extrêmes, capacité à créer des canaux de refroidissement complexes pour la gestion de la chaleur | Tuyères, chambres de combustion, chambres de poussée |
Les avantages de l'utilisation du procédé SLM dans ces applications sont nombreux. Par exemple, la capacité de créer des canaux de refroidissement internes complexes dans les aubes de turbine permet une gestion plus efficace de la chaleur, ce qui se traduit par une augmentation des performances du moteur et de l'efficacité énergétique. De même, la technologie SLM permet de concevoir et de fabriquer des composants légers pour les cellules et les trains d'atterrissage, ce qui contribue directement à la réduction de la consommation de carburant et à l'augmentation de l'autonomie des avions. En outre, la technologie SLM permet aux ingénieurs de créer des géométries complexes qui étaient auparavant impossibles à réaliser avec les techniques de fabrication traditionnelles, ce qui ouvre de nouvelles possibilités d'optimisation de la conception et d'amélioration des performances.
Défis et considérations pour les SLM dans l'aérospatiale
Bien que la technique SLM offre un potentiel énorme pour l'industrie aérospatiale, il reste encore des défis à relever. Voici quelques éléments clés à prendre en compte pour l'utilisation de la technique SLM dans les applications aérospatiales :
- Coûts des machines et des poudres : Le prix des machines SLM est actuellement élevé et les poudres métalliques spécialement conçues pour les applications aérospatiales peuvent être coûteuses.
- Contrôle des processus et qualification : Le procédé SLM est un processus complexe qui exige un contrôle strict des paramètres pour garantir une qualité constante et fiable des pièces. La qualification du processus SLM pour les composants aérospatiaux exige des procédures d'essai et de certification rigoureuses.
- Rugosité de la surface : Les pièces fabriquées par SLM peuvent présenter un état de surface plus rugueux que les pièces fabriquées traditionnellement. Des techniques de post-traitement telles que l'usinage ou le polissage peuvent être nécessaires en fonction de l'application.
- Limitations de la taille des pièces : Les machines SLM actuelles ont des limites quant à la taille des pièces qu'elles peuvent produire. La fabrication de composants aérospatiaux plus grands pourrait nécessiter la segmentation et l'assemblage de plusieurs pièces imprimées par SLM.
Malgré ces difficultés, les avantages potentiels de la technique SLM sont indéniables. À mesure que la technologie mûrit et que les coûts de production diminuent, la technique SLM est en passe de devenir une méthode de fabrication courante pour l'industrie aérospatiale. Les efforts de recherche et de développement améliorent continuellement les capacités des machines, la qualité des poudres et le contrôle des processus, ouvrant la voie à une adoption plus large de la technologie SLM. SLM dans les années à venir.
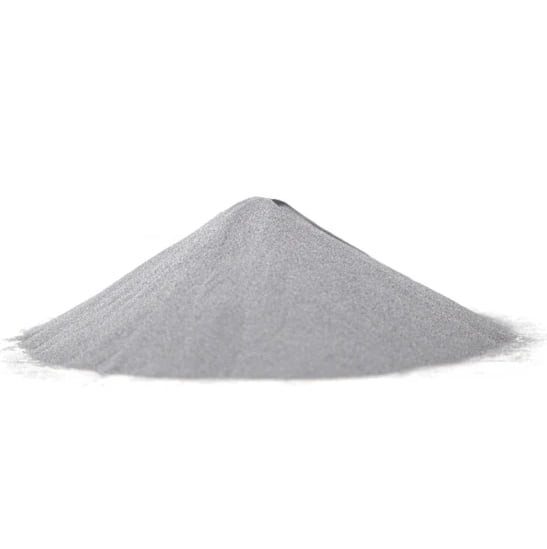
FAQ
Q : Quels sont les avantages de l'utilisation du procédé SLM pour les composants aérospatiaux ?
R : La méthode SLM présente plusieurs avantages, notamment
- Pièces légères : La technologie SLM permet de créer des composants plus légers que les méthodes de fabrication traditionnelles, ce qui se traduit par une amélioration du rendement énergétique et une augmentation de l'autonomie des aéronefs.
- Liberté de conception : Le SLM permet de concevoir et de fabriquer des géométries complexes qui n'étaient pas réalisables avec les techniques traditionnelles, ce qui ouvre de nouvelles perspectives en matière d'optimisation des performances.
- Propriétés du matériau : Les pièces SLM peuvent être fabriquées à partir de matériaux de haute performance présentant des propriétés exceptionnelles telles qu'un rapport poids/résistance élevé et une résistance aux températures élevées.
- Réduction des déchets : Le SLM est un processus plus efficace que les méthodes traditionnelles, qui génère moins de déchets matériels.
Q : Quelles sont les limites de l'utilisation du procédé SLM pour les composants aérospatiaux ?
R : Les limites de la technique SLM dans l'aérospatiale sont les suivantes :
- Coûts des machines et des poudres : Les machines SLM et les poudres métalliques peuvent être coûteuses, ce qui a un impact sur les coûts de production.
- Contrôle des processus et qualification : La technique SLM exige un contrôle strict des paramètres et des procédures de qualification rigoureuses pour les applications aérospatiales.
- Rugosité de la surface : Les pièces obtenues par SLM peuvent nécessiter un post-traitement pour obtenir des finitions de surface plus lisses, en fonction de l'application.
- Limitations de la taille des pièces : Les machines SLM actuelles ont des limites quant à la taille des pièces qu'elles peuvent produire.
Q : Quelles sont les avancées futures attendues dans le domaine de la technologie SLM pour les applications aérospatiales ?
R : L'avenir de la technique SLM dans l'aérospatiale est prometteur et plusieurs avancées sont attendues :
- Réduction des coûts des machines et des poudres : Au fur et à mesure que la technologie mûrit, les coûts de production des machines SLM et des poudres métalliques devraient diminuer, ce qui rendra la SLM plus accessible pour une adoption plus large.
- Des volumes de construction plus importants : Le développement de machines SLM plus grandes avec des volumes de fabrication accrus permettra la production de composants aérospatiaux plus grands, éliminant ainsi le besoin de segmentation et d'assemblage.
- SLM multi-matériaux : Les progrès de la technologie SLM pourraient permettre l'impression de pièces utilisant plusieurs matériaux en une seule fois, créant ainsi des composants aux propriétés variées pour des performances optimales.
- Surveillance et contrôle des processus in situ : La surveillance et le contrôle en temps réel du processus SLM garantissent une qualité constante des pièces et réduisent le risque de défauts.
- Automatisation et intégration : L'automatisation accrue et l'intégration de la gestion du cycle de vie à d'autres processus de fabrication permettront de rationaliser les flux de production et d'améliorer l'efficacité.
Q : Le SLM est-il l'avenir de la fabrication aérospatiale ?
R : S'il est peu probable que la technologie SLM remplace toutes les méthodes de fabrication traditionnelles dans l'aérospatiale, elle révolutionne incontestablement le secteur. La capacité de la technologie SLM à créer des composants légers, performants et de conception complexe la rend idéale pour un large éventail d'applications aérospatiales. Au fur et à mesure que la technologie continue à se développer et à surmonter ses limites, le SLM est en passe de devenir une force dominante qui façonnera l'avenir de la fabrication aérospatiale.
Conclusion
La fusion sélective par laser (SLM) transforme la façon dont les avions sont conçus et fabriqués. Cette technologie d'impression 3D innovante offre une combinaison unique de liberté de conception, de propriétés des matériaux et de capacités de réduction du poids, repoussant ainsi les limites du possible dans l'industrie aérospatiale. Qu'il s'agisse d'avions plus légers et plus économes en carburant ou de fusées capables d'atteindre de nouveaux sommets, la technologie SLM joue un rôle crucial dans le façonnement de l'avenir du vol. Au fur et à mesure que la technologie mûrit et surmonte ses difficultés, le pouvoir de transformation de la technologie SLM dans l'aérospatiale n'a plus de limites.
Partager sur
MET3DP Technology Co. est un fournisseur de premier plan de solutions de fabrication additive dont le siège se trouve à Qingdao, en Chine. Notre société est spécialisée dans les équipements d'impression 3D et les poudres métalliques de haute performance pour les applications industrielles.
Articles connexes
À propos de Met3DP
Mise à jour récente
Notre produit
CONTACTEZ-NOUS
Vous avez des questions ? Envoyez-nous un message dès maintenant ! Nous répondrons à votre demande avec toute une équipe dès réception de votre message.
Obtenir les informations de Metal3DP
Brochure du produit
Obtenir les derniers produits et la liste des prix
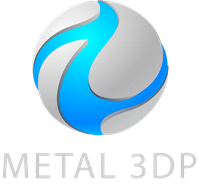
Poudres métalliques pour l'impression 3D et la fabrication additive