Technologie SLM : un guide complet
Table des matières
SLM (fusion sélective au laser) est une technologie avancée de fabrication additive pour les pièces métalliques. Ce guide fournit un examen approfondi des systèmes, processus, matériaux, applications, avantages et considérations SLM lors de l'adoption de cette technologie.
Introduction à la fusion laser sélective
La fusion sélective au laser (SLM) est un processus de fabrication additive par fusion sur lit de poudre qui utilise un laser haute puissance pour fondre et fusionner sélectivement des particules de poudre métallique couche par couche afin de créer des pièces métalliques entièrement denses directement à partir de données de CAO 3D.
Principales caractéristiques de Technologie SLM:
- Utilise le laser pour faire fondre sélectivement les métaux en poudre
- Ajoute du matériel uniquement lorsque cela est nécessaire
- Permet des géométries complexes impossibles à réaliser par moulage ou usinage
- Crée des composants métalliques denses et sans vide
- Les matériaux courants comprennent l'aluminium, le titane, l'acier et les alliages de nickel.
- Capable de pièces de petites et moyennes tailles
- Idéal pour les pièces complexes à faible volume
- Élimine le besoin d'outillage dur comme les moules et les matrices
- Réduit les déchets par rapport aux méthodes soustractives
- Permet d'améliorer les performances des structures d'ingénierie
SLM offre des capacités révolutionnaires pour la conception de produits innovants et la production allégée. Cependant, la maîtrise du processus nécessite une expertise spécialisée.
Comment fonctionne la fusion laser sélective
Le processus SLM implique :
- Étaler une fine couche de poudre métallique sur une plaque de construction
- Balayage d'un faisceau laser focalisé pour faire fondre sélectivement la poudre
- Abaisser la plaque de construction et répéter la superposition et la fusion
- Retrait des pièces finies du lit de poudre
- Post-traitement des pièces selon les besoins
Il est essentiel de contrôler avec précision l’apport d’énergie, les modèles de numérisation, la température et les conditions atmosphériques pour obtenir des pièces denses et sans défauts.
Les systèmes SLM comprennent un laser, une optique, une distribution de poudre, une chambre de fabrication, une manipulation de gaz inerte et des commandes. Les performances dépendent fortement de la conception du système et des paramètres de construction.
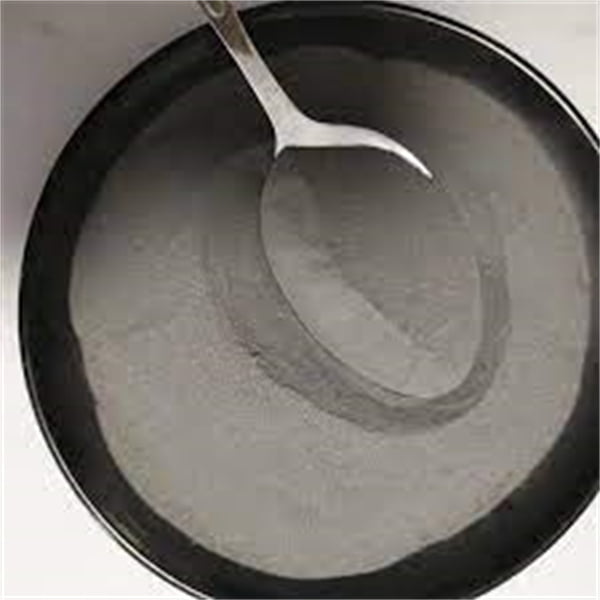
Technologie SLM Fournisseurs
Les principaux fabricants de systèmes SLM comprennent :
Entreprise | Modèles | Plage de taille de construction | Matériaux | Fourchette de prix |
---|---|---|---|---|
Solutions SLM | Nouvelle génération, NXG XII | 250x250x300mm <br> 800x400x500mm | Ti, Al, Ni, Aciers | $400,000 – $1,500,000 |
EOS | M300, M400 | 250x250x325mm <br> 340x340x600mm | Ti, Al, Ni, Cu, Aciers, CoCr | $500,000 – $1,500,000 |
Trumpf | TruPrint3000 | 250x250x300mm <br> 500x280x365mm | Ti, Al, Ni, Cu, Aciers | $400,000 – $1,000,000 |
ConceptLaser | Ligne X 2000R | 800x400x500mm | Ti, Al, Ni, Aciers, CoCr | $1,000,000+ |
Renishaw | AM400, AM500 | 250 x 250 x 350 mm <br> 395x195x375mm | Ti, Al, Aciers, CoCr, Cu | $500,000 – $800,000 |
Le choix du système dépend des besoins en matière de taille de construction, des matériaux, de la qualité, du coût et du service. Un partenariat avec un fournisseur de solutions SLM expérimenté est recommandé pour évaluer correctement les options.
Caractéristiques du processus SLM
La SLM implique des interactions complexes entre divers paramètres de processus. Voici les caractéristiques clés :
Laser – Puissance, longueur d’onde, mode, vitesse de balayage, distance des trappes, stratégie
Poudre – Matériau, granulométrie, forme, débit d’alimentation, densité, coulabilité, réutilisation
Température – Préchauffage, fusion, refroidissement, contraintes thermiques
Atmosphère – Type de gaz inerte, teneur en oxygène, débits
Plaque de construction – Matériau, température, revêtement
Stratégie d'analyse – Motif de hachures, rotation, contours des bordures
Soutien – Minimiser le besoin, l’interface, la suppression
Post-traitement – Traitement thermique, HIP, usinage, finition
Comprendre les relations entre ces paramètres est essentiel pour obtenir des pièces sans défauts et des propriétés mécaniques optimales.
Lignes directrices de conception SLM
Une conception appropriée des pièces est essentielle au succès de la SLM :
- Concevoir en pensant à la fabrication additive par rapport aux méthodes conventionnelles
- Optimiser les géométries pour réduire le poids, les matériaux et améliorer les performances
- Minimisez le besoin de supports en utilisant des angles autoportants
- Autoriser la prise en charge des régions d'interface dans la conception
- Orienter les pièces pour réduire les contraintes et éviter les défauts
- Autoriser le retrait thermique des éléments
- Concevoir des canaux intérieurs pour l'élimination de la poudre non fondue
- Tenir compte du gauchissement potentiel dans les surplombs ou les sections minces
- Finitions de surface conçues en tenant compte de la rugosité telle que construite
- Considérer les effets des lignes de couches sur les performances en fatigue
- Interface de montage de conception pour pièces brutes
- Minimiser les volumes piégés de poudre non frittée
Un logiciel de simulation permet d'évaluer les contraintes et les déformations dans les pièces SLM complexes.
Options de matériaux SLM
Une gamme d'alliages peut être traitée par SLM, les propriétés des matériaux dépendant des paramètres utilisés.
Catégorie | Alliages courants |
---|---|
Titane | Ti-6Al-4V, Ti 6242, TiAl, Ti-5553 |
Aluminium | AlSi10Mg, AlSi12, Scalmalloy |
Acier inoxydable | 316L, 17-4PH, 304L, 4140 |
Acier à outils | H13, acier Maraging, acier à outils en cuivre |
Alliages de nickel | Inconel 625, 718, Haynes 282 |
Chrome cobalt | CoCrMo, MP1, CoCrW |
Métaux précieux | Or, argent |
Le choix d’alliages compatibles et la définition de paramètres qualifiés sont essentiels pour obtenir les performances matérielles requises.
Applications clés de la GDT
SLM permet des capacités de transformation dans tous les secteurs :
L'industrie | Applications typiques |
---|---|
Aérospatiale | Aubes de turbine, roues à aubes, composants de satellite et d'UAV |
Médical | Implants orthopédiques, outils chirurgicaux, dispositifs spécifiques au patient |
Automobile | Composants allégés, outillage personnalisé |
L'énergie | Vannes fioul/gaz complexes, échangeurs de chaleur |
Industriel | Inserts de refroidissement conformes, gabarits, fixations, guides |
Défense | Drones, composants d'armement, de véhicules et de gilets pare-balles |
Les avantages par rapport à la fabrication conventionnelle comprennent :
- Capacité de personnalisation de masse
- Temps de développement plus court
- Liberté de conception pour des gains de performances
- Consolidation et allégement des pièces
- Éliminer l’utilisation excessive de matériaux
- Consolidation de la chaîne d'approvisionnement
Une validation minutieuse des performances mécaniques est nécessaire lors de l'application de pièces SLM dans des applications critiques.
Avantages et inconvénients de Technologie SLM
Avantages :
- Liberté de conception rendue possible grâce à la fabrication additive
- Complexité obtenue sans coût supplémentaire
- Élimine le besoin d'outillage dur
- Consolide les sous-ensembles en pièces uniques
- Allègement à partir de structures topologiquement optimisées
- Personnalisation et production en faible volume
- Temps de développement réduit lors du moulage/usinage
- Rapport résistance/poids élevé grâce à des microstructures fines
- Minimise le gaspillage de matériaux par rapport aux processus soustractifs
- Production juste à temps et décentralisée
- Délais de livraison et stocks de pièces réduits
Limites :
- Des volumes de fabrication plus petits que les autres processus de fabrication additive métallique
- Précision dimensionnelle et état de surface inférieurs à ceux de l'usinage
- Choix limité d’alliages qualifiés par rapport au moulage
- Essais et erreurs importants pour optimiser les paramètres de construction
- Propriétés des matériaux anisotropes issues de la stratification
- Potentiel de contrainte résiduelle et de fissuration
- Les défis de l'élimination de la poudre des géométries complexes
- Un post-traitement est souvent nécessaire
- Coût d’équipement plus élevé que l’impression 3D polymère
- Installations spéciales et manipulation de gaz inerte nécessaires
Lorsqu'il est appliqué de manière appropriée, le SLM permet des performances révolutionnaires impossibles par d'autres moyens.
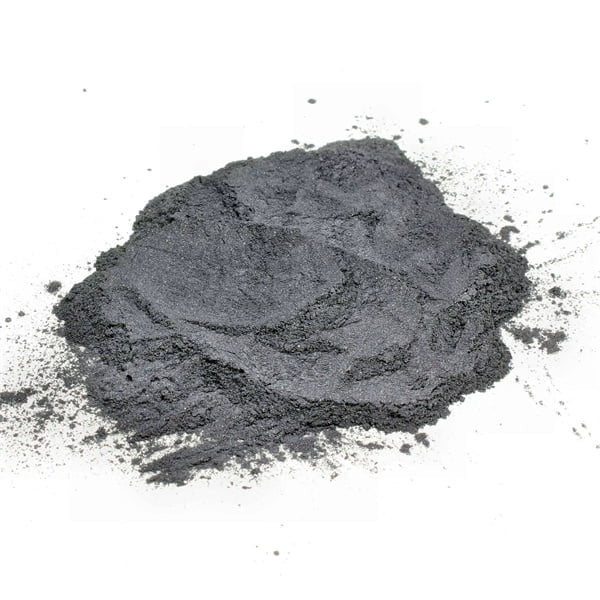
Adopter la technologie SLM
La mise en œuvre de la GDT implique des défis, notamment :
- Identifier les applications adaptées en fonction des besoins
- Confirmation de la faisabilité SLM pour les conceptions choisies
- Développer des protocoles rigoureux de qualification des processus
- Investir dans des équipements SLM adaptés
- Sécuriser l’expertise dans les procédés sur lit de poudre métallique
- Établir des procédures et des normes de qualité des matériaux
- Maîtriser le développement et l'optimisation des paramètres de build
- Implémenter des méthodes de post-traitement robustes
- Propriétés mécaniques qualifiantes des composants finis
Un plan d’introduction méthodique axé sur les applications à faible risque minimise les pièges. Le partenariat avec des bureaux de services SLM ou des OEM de systèmes expérimentés donne accès à une expertise.
Analyse des coûts de production SLM
L’économie de la production SLM implique :
- Coût élevé de l'équipement de la machine
- Main-d'œuvre pour la configuration de la construction, le post-traitement et le contrôle qualité
- Coûts des matériaux de la matière première en poudre métallique
- Finition des pièces – usinage, perçage, ébavurage, etc.
- Frais généraux – installations, gaz inerte, services publics, maintenance
- Temps de développement initial par essais et erreurs
- Les coûts diminuent grâce à l’optimisation de la conception et à l’expérience en production
- Devient économique à partir de faibles volumes de 1 à 500 unités
- Offre le plus grand avantage en termes de coût pour les géométries complexes
Il est recommandé de choisir des alliages qualifiés auprès de fournisseurs réputés pour éviter les défauts. Un partenariat avec un fournisseur de services peut offrir une voie d’adoption plus rapide et moins risquée.
SLM comparé à d'autres processus
Processus | Comparaison avec SLM |
---|---|
Usinage CNC | SLM permet d'obtenir des formes complexes non usinables par processus soustractif. Aucun outillage dur requis. |
Moulage par injection de métal | SLM élimine les coûts d’outillage élevés. Meilleures propriétés matérielles que MIM. Des volumes inférieurs sont réalisables. |
Moulage sous pression | SLM a des coûts d’outillage inférieurs. Aucune limitation de taille. Géométries très complexes réalisables. |
Lamination de feuilles | SLM crée un matériau entièrement dense et isotrope par rapport aux composites stratifiés. |
Jetting de liant | SLM fournit des pièces vertes entièrement denses par rapport aux pièces poreuses projetées par liant nécessitant un frittage. |
DMLS | Le SLM offre une plus grande précision et de meilleures propriétés matérielles que les systèmes polymères DMLS. |
EBM | La fusion par faisceau d'électrons a des taux de construction plus élevés mais une résolution inférieure à celle du SLM. |
Chaque processus présente des avantages basés sur des applications spécifiques, des tailles de lots, des matériaux, des objectifs de coûts et des exigences de performances.
Perspectives d'avenir pour la fabrication additive SLM
SLM est sur le point de connaître une croissance significative dans les années à venir, portée par :
- Expansion continue des matériaux avec une plus grande disponibilité des alliages
- Des volumes de construction plus importants permettant une production à l’échelle industrielle
- Finitions de surface et tolérances améliorées
- Fiabilité et productivité accrues du système
- Nouveaux systèmes hybrides intégrant l’usinage
- Diminution des coûts améliorant la mise à l'échelle de l'analyse de rentabilisation
- Autres algorithmes d'optimisation et simulation
- Intégration automatisée du post-traitement
- Croissance des pièces qualifiées pour les industries réglementées
- Avancement continu des conceptions complexes
SLM deviendra courant pour une gamme croissante d'applications où ses capacités offrent un avantage concurrentiel distinct.
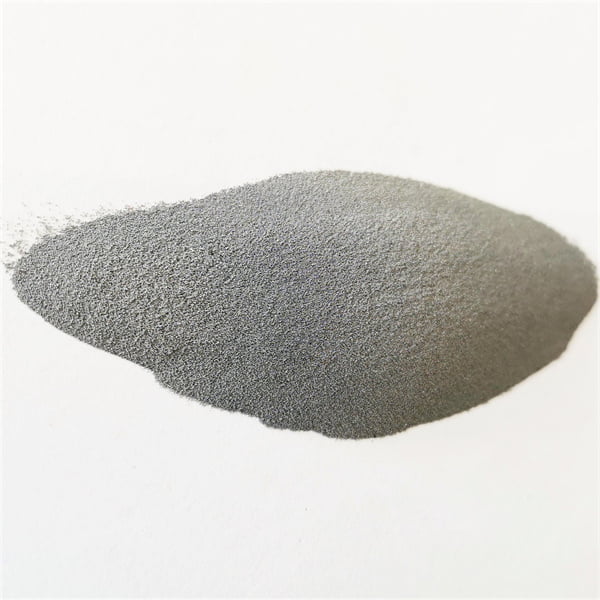
FAQ
Quels matériaux pouvez-vous traiter avec SLM ?
Les alliages de titane et d'aluminium sont les plus courants. Les aciers à outils, l'acier inoxydable, les alliages de nickel et le chrome-cobalt sont également traités.
Quelle est la précision du SLM ?
Une précision d'environ ±0,1-0,2% est typique, avec une résolution minimale d'environ 100 microns.
Quel est le coût des équipements SLM ?
Les systèmes SLM vont de $300 000 à $1 000 000+ en fonction de la taille, des capacités et des options.
Quels types de post-traitement sont nécessaires ?
Des post-processus tels que le traitement thermique, le HIP, la finition de surface et l'usinage peuvent être nécessaires.
Quelles industries utilisent la SLM ?
Les secteurs de l’aérospatiale, du médical, de l’automobile, de l’industrie et de la défense sont les premiers à adopter la SLM.
Pour quels matériaux le SLM ne fonctionne-t-il pas bien ?
Les métaux hautement réfléchissants comme le cuivre ou l’or restent un défi. Certaines propriétés des matériaux sont encore émergentes.
Quelles sont les finitions de surface typiques ?
La rugosité de la surface SLM telle que construite varie de 5 à 15 microns Ra. La finition peut améliorer cela.
Quelle taille de pièces pouvez-vous fabriquer avec SLM ?
Des volumes allant jusqu'à 500 mm x 500 mm x 500 mm sont typiques. Les machines plus grandes peuvent accueillir des pièces plus grandes.
Le SLM est-il adapté à la fabrication en production ?
Oui, le SLM est de plus en plus utilisé pour les pièces de production finales, avec des exemples dans les industries aérospatiale et médicale.
Comment le SLM se compare-t-il à l’EBM ?
SLM peut obtenir des détails plus fins tandis qu'EBM a des vitesses de construction plus rapides. Les deux fournissent des pièces métalliques entièrement denses.
Partager sur
MET3DP Technology Co. est un fournisseur de premier plan de solutions de fabrication additive dont le siège se trouve à Qingdao, en Chine. Notre société est spécialisée dans les équipements d'impression 3D et les poudres métalliques de haute performance pour les applications industrielles.
Articles connexes
À propos de Met3DP
Mise à jour récente
Notre produit
CONTACTEZ-NOUS
Vous avez des questions ? Envoyez-nous un message dès maintenant ! Nous répondrons à votre demande avec toute une équipe dès réception de votre message.
Obtenir les informations de Metal3DP
Brochure du produit
Obtenir les derniers produits et la liste des prix