Acier inoxydable 316L Poudre
Table des matières
Poudre d'acier inoxydable 316L est un choix de matériau populaire pour de nombreuses applications en raison de son excellente résistance à la corrosion, de ses propriétés mécaniques et de sa biocompatibilité. Ce guide fournit une vue d'ensemble détaillée de la poudre 316L, y compris ses propriétés, ses méthodes de production, ses applications, ses fournisseurs, et plus encore.
Aperçu de la poudre d'acier inoxydable 316L
La poudre d'acier inoxydable 316L est un type d'alliage d'acier inoxydable qui contient du molybdène pour une meilleure résistance à la corrosion. Le "L" fait référence à la faible teneur en carbone, qui améliore la soudabilité.
Les principales propriétés et caractéristiques de la poudre 316L sont les suivantes :
- Excellente résistance à la corrosion, en particulier à la corrosion par piqûres et par crevasses
- Haute résistance et bonne ductilité
- Biocompatibilité exceptionnelle et adaptée aux implants médicaux
- Structure austénitique non magnétique
- Résistance élevée à l'oxydation et au fluage à des températures élevées
- Disponibles en différentes tailles et morphologies de particules
La poudre 316L peut être produite par atomisation au gaz, atomisation à l'eau et autres méthodes. Le processus de production de la poudre influence les caractéristiques de la poudre comme la forme des particules, la distribution des tailles, la fluidité, etc.
Voici une comparaison des différents types de poudre 316L et de leurs applications typiques :
Type de poudre | Taille des particules | Morphologie | Applications |
---|---|---|---|
Gaz atomisé | 15-150 μm | Sphérique | Fabrication additive, MIM |
Eau pulvérisée | 10-300 μm | Irrégulier, dendritique | Moulage par injection de métal |
Plasma atomisé | <100 μm | Sphérique | Fabrication additive |
Électrolytique | <150 μm | Dendritique, hérissé | Fabrication additive, pressage |
Carbonyl | <10 μm | Sphérique | Métallurgie des poudres, pressage |
La poudre 316L est appréciée pour sa combinaison de solidité, de résistance à la corrosion et de biocompatibilité. Parmi les principales applications, on peut citer
- Fabrication additive - Fusion laser sélective, frittage laser direct des métaux, jet de liant
- Moulage par injection de métal - Petites pièces complexes comme les implants orthopédiques
- Presse et frittage - Filtres, structures poreuses, paliers autolubrifiants
- Revêtement de surface - Pour améliorer la résistance à l'usure et à la corrosion
- Brasage et soudage - Comme matériau d'apport
Voici un aperçu de la façon dont la poudre 316L est utilisée dans différents processus de fabrication :
Processus de fabrication | Comment la poudre 316L est-elle utilisée ? |
---|---|
Fabrication additive | Le lit de poudre est sélectivement fondu par laser pour construire des pièces en 3D |
Moulage par injection de métal | Poudre mélangée à un liant, moulée puis frittée |
Pressage et frittage | La poudre est pressée en forme puis frittée |
Revêtement de surface | Pulvérisation ou fusion sur la surface par pulvérisation thermique, revêtement au laser, etc. |
Brasage et soudage | Utilisé comme matériau de remplissage pour l'assemblage |
La structure granulaire ultrafine et la consistance homogène obtenues à partir des poudres font du 316L un matériau idéal pour les applications critiques dans l'aérospatiale, le médical, le traitement chimique, etc.
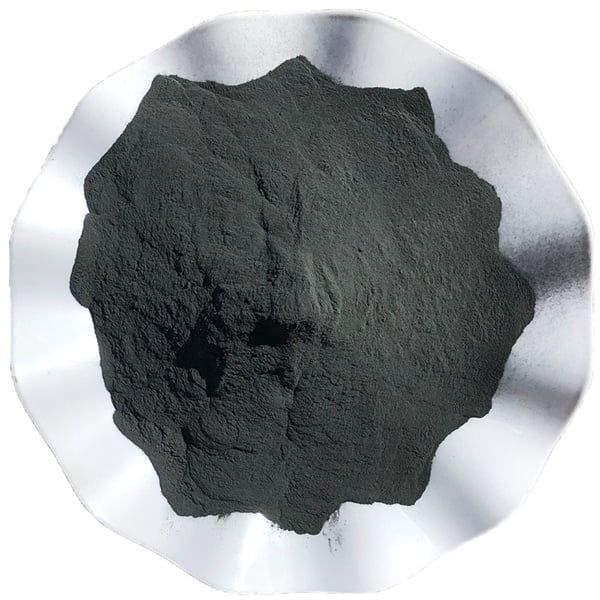
Propriétés de la poudre d'acier inoxydable 316L
Propriété | Description | Impact sur la convivialité |
---|---|---|
Composition chimique | Principalement composé de fer (Fe), de chrome (Cr) (16-18%), de nickel (Ni) (10-12%), de molybdène (Mo) (2-3%), avec des ajouts mineurs de silicium (Si), de manganèse (Mn ), phosphore (P), soufre (S), azote (N). Faible teneur en carbone (moins de 0,03%) | La teneur élevée en chrome confère une excellente résistance à la corrosion, en particulier contre la corrosion par piqûres et fissures. Le nickel améliore la résistance et la ductilité, tandis que le molybdène améliore la résistance aux attaques localisées, notamment celles des chlorures. La faible teneur en carbone minimise le risque de précipitation de carbure pendant le soudage ou les processus à haute température. |
Taille et distribution des particules | Mesuré en micromètres (µm), avec une plage typique de 15 à 50 µm. La répartition des tailles de particules dans cette plage est cruciale. | La taille et la distribution des particules influencent considérablement la fluidité, la densité de tassement et les propriétés mécaniques du produit final. Les particules plus fines offrent généralement un meilleur fini de surface mais peuvent être difficiles à manipuler en raison d'une mauvaise fluidité. Une distribution bien contrôlée avec un mélange de tailles de particules optimise le compactage et minimise les vides dans le produit final. |
Densité apparente et densité au robinet | La densité apparente fait référence à la densité de la poudre versée sans serrer. La densité après tapotement est mesurée après avoir tapoté le récipient de poudre pour obtenir un emballage plus dense. Les unités sont généralement en g/cm³. | La différence entre la densité apparente et la densité après tapotement reflète la fluidité de la poudre. Une densité après tassement plus élevée par rapport à la densité apparente indique de meilleures caractéristiques d'écoulement, essentielles à la création efficace d'un lit de poudre dans les processus de fabrication additive. |
Capacité d'écoulement | La facilité avec laquelle la poudre s'écoule sous son propre poids. Mesuré à l'aide de techniques telles que le débitmètre Hall ou l'indice Carr. | Une bonne fluidité permet un épandage uniforme de la poudre et minimise la ségrégation (séparation de différentes tailles de particules) pendant la manipulation et le dépôt. Cela se traduit par une densité et des propriétés constantes dans le produit final. |
Sphéricité et morphologie | La sphéricité fait référence à la façon dont une particule ressemble à une sphère parfaite. La morphologie décrit la forme globale des particules (sphérique, angulaire, irrégulière). | Les particules sphériques circulent généralement mieux et se regroupent plus densément que les formes irrégulières. Cependant, certaines applications peuvent bénéficier d'une morphologie de particule spécifique pour obtenir la texture de surface ou l'imbrication souhaitée des particules. |
Point et plage de fusion | Environ 1400°C (2552°F). La plage de fusion peut varier légèrement en fonction de la composition spécifique de la poudre. | Le point de fusion est crucial pour déterminer les températures de traitement appropriées dans des techniques telles que le frittage ou la fabrication additive. |
Conductivité thermique | Environ 16 W/mK. | La conductivité thermique influence le transfert de chaleur au sein du lit de poudre pendant le traitement. Cela peut avoir un impact sur des facteurs tels que les vitesses de refroidissement, les contraintes résiduelles et la formation de phases indésirables dans le produit final. |
Comportement au frittage | Capacité des particules de poudre à se lier ensemble lors d’un processus de chauffage à haute température (frittage) pour former un objet solide. | Le comportement du frittage dépend de facteurs tels que la distribution granulométrique, la chimie de la surface de la poudre et les paramètres de frittage. Un frittage bien contrôlé permet de densifier le lit de poudre, obtenant ainsi les propriétés mécaniques souhaitées dans le produit final. |
Résistance à la corrosion | Hérite d'une excellente résistance à la corrosion de son homologue en vrac, l'acier inoxydable 316L. Offre une résistance à un large éventail d’environnements, notamment les acides oxydants, les acides réducteurs et le brouillard salin. | La teneur en molybdène de la poudre 316L offre une résistance supérieure à la corrosion par piqûre, en particulier dans les environnements contenant des chlorures, par rapport à la poudre d'acier inoxydable 304L. Cela le rend adapté aux applications exigeant une résistance élevée à la corrosion. |
Méthodes de production de la poudre 316L
Méthode | Description | Caractéristiques des particules | Avantages | Inconvénients | Applications |
---|---|---|---|---|---|
Atomisation des gaz | L'acier 316L fondu est injecté dans un flux de gaz inerte à haute vitesse, le brisant en fines gouttelettes qui se solidifient rapidement en particules sphériques. | – Forme sphérique – Distribution granulométrique étroite (15-45 microns) – Excellente fluidité – Densité de tassement élevée | – Qualité constante – Idéal pour les processus de fabrication additive (FA) tels que la fusion par faisceau laser (LBM) et la fusion par faisceau d'électrons (EBM) | – Consommation d’énergie élevée – Potentiel de captage d’oxygène et d’azote | – Composants aérospatiaux (aubes de turbines, échangeurs de chaleur) – Implants médicaux (en raison de la biocompatibilité) – Pièces automobiles de haute performance |
Atomisation de l'eau | Semblable à l’atomisation au gaz, mais utilise un jet d’eau à haute pression pour briser le métal en fusion. | – Forme irrégulière avec certains satellites (particules fusionnées) – Distribution de taille plus large (10-100 microns) – Faible fluidité par rapport à l'atomisation au gaz | – Plus rentable que l'atomisation au gaz – Convient aux applications où la forme sphérique est moins critique | – Teneur en oxygène plus élevée en raison de l'interaction avec l'eau – Peut nécessiter un post-traitement supplémentaire pour la fabrication additive | – Réacteurs à lit fluidisé (supports de catalyseur) – Matière première pour moulage par injection de métal (MIM) |
Atomisation par plasma | Utilise une torche plasma à haute température et haute vitesse pour fondre et atomiser la matière première en acier 316L. | – Forme hautement sphérique – Distribution granulométrique étroite avec des particules plus fines possibles (jusqu'à 5 microns) – Excellente fluidité | – Qualité supérieure pour les applications AM exigeantes – Permet d'obtenir des poudres plus fines pour des caractéristiques complexes | – Consommation d’énergie la plus élevée parmi les trois méthodes – Nécessite un équipement spécialisé | – Aubes de turbine hautes performances – Composants microfluidiques – Implants biomédicaux nécessitant un état de surface élevé |
Alliage mécanique | Les poudres élémentaires solides ou préalliées sont mélangées et broyées ensemble dans un broyeur à boulets à haute énergie pour obtenir une composition 316L uniforme. | – Forme irrégulière avec facettes angulaires – Large répartition granulométrique – Faible fluidité | – Hautement personnalisable pour créer des compositions d’alliages uniques impossibles à réaliser avec d’autres méthodes | – Temps de traitement plus long par rapport aux techniques d'atomisation – Peut nécessiter des étapes supplémentaires pour améliorer la fluidité de la FA | – Composants spécialisés nécessitant des propriétés matérielles spécifiques – Développement de nouveaux alliages pour la fabrication additive |
Électrolyse | Un processus aqueux dans lequel une anode 316L se dissout dans la solution électrolytique et les ions métalliques sont déposés sous forme de poudre sur la cathode. | – Formes sphériques ou dendritiques – Large répartition granulométrique – Peut être poreux | – Possibilité d'obtenir des poudres très pures – Potentiel de fabrication de forme quasi nette | – Capacité de production limitée – Processus relativement lent | – Implants biomédicaux nécessitant une grande pureté – Supports catalytiques – Applications spécialisées exigeant des propriétés de poudre spécifiques |
Applications de la poudre d'acier inoxydable 316L
L'industrie | Application | Biens immobiliers financés par effet de levier | Notes complémentaires |
---|---|---|---|
Médical et dentaire | * Implants (genou, hanche, dentaire) * Instruments chirurgicaux * Prothèses | * Biocompatible (sans danger pour le contact avec le corps) * Excellente résistance à la corrosion * Haute résistance * Formabilité pour les conceptions complexes | * Le 316L minimise le risque de rejet et d'infection. * La poudre permet la création de structures poreuses pour la croissance osseuse. * Peut être stérilisé pour une utilisation chirurgicale sûre. |
Transformation des aliments | * Navires * Tubes * Vannes * Raccords * Fixations | * Résistance supérieure à la corrosion aux acides alimentaires et aux saumures * Facile à nettoyer et à entretenir * Répond aux normes d'hygiène et de sécurité | * 316L garantit la qualité des aliments et prévient la contamination. * Les surfaces lisses minimisent les points d'hébergement bactériens. * Résiste aux cycles de nettoyage répétés. |
Marine | * Arbres d'hélice * Pièces de moteur diesel * Équipement de pont | * Résistance exceptionnelle à la corrosion par l'eau salée * Haute résistance mécanique * Durabilité dans les environnements difficiles | * Le 316L prolonge la durée de vie des composants marins critiques. * Maintient l'intégrité structurelle sous contrainte et charges lourdes. * Fonctionne de manière fiable à différentes températures. |
Chimie et pétrochimie | * Récipients de réaction * Systèmes de tuyauterie * Vannes * Pompes | * Imperméable à une large gamme de produits chimiques * Résistance aux hautes températures * Tolérance à la pression | * Le 316L peut gérer des produits chimiques agressifs sans dégradation. * Résiste aux températures de traitement élevées pour des réactions efficaces. * Convient aux environnements à haute pression dans les raffineries et les usines. |
Aérospatiale | * Composants de moteurs d'avion * Systèmes de contrôle des fluides * Pièces structurelles | * Rapport résistance/poids élevé * Excellentes propriétés mécaniques à températures élevées * Résistance à la corrosion dans des environnements difficiles | * Le 316L réduit le poids pour un meilleur rendement énergétique. * Maintient les performances sous une chaleur et une pression extrêmes. * Résiste à la corrosion du carburéacteur et d'autres fluides aérospatiaux. |
Automobile | * Composants d'échappement * Pièces de moteur * Garnitures et éléments décoratifs | * Résistance aux hautes températures * Formabilité pour les formes complexes * Résistance à la corrosion pour une durée de vie prolongée | * Le 316L peut résister aux gaz d'échappement chauds sans se déformer. * Peut être transformé en collecteurs et tuyaux d'échappement complexes. * Résiste à la corrosion causée par les sels de déneigement et les conditions météorologiques difficiles. |
Biens de consommation | * Montres * Bijoux * Couverts * Appareils électroménagers | * Attrait esthétique grâce à la finition polie * Haute résistance et résistance à l'usure * Résistance à la corrosion pour un nettoyage et une hygiène faciles | * Le 316L offre un look élégant et luxueux aux produits haut de gamme. * Les ustensiles et appareils électroménagers conservent leur netteté et leur durabilité. * Facile à entretenir une surface propre et hygiénique. |
Construction | * Revêtement architectural * Fixations * Garde-corps * Quincaillerie | * Résistance à la corrosion pour les applications extérieures * Haute résistance et résistance aux intempéries * Attrait esthétique pour les conceptions modernes | * Le 316L peut résister aux conditions météorologiques difficiles sans rouiller. * Maintient l'intégrité structurelle et la fonctionnalité au fil du temps. * Offre un look élégant et contemporain aux éléments architecturaux. |
Spécifications et normes
La composition, la qualité et les propriétés de la poudre 316L sont régies par diverses spécifications et normes internationales.
Normes ASTM
- ASTM A240 - Norme pour les plaques, feuilles et bandes d'acier inoxydable au chrome et au chrome-nickel pour les appareils à pression et les applications générales. Définit les limites de composition et les propriétés mécaniques de l'alliage 316L.
- ASTM B822 - Méthode de test standard pour la distribution de la taille des particules de poudres métalliques et de composés apparentés par diffusion de lumière. Utilisée pour caractériser la distribution de la taille des poudres.
- ASTM F3055 - Spécification standard pour la fabrication additive de poudre d'alliage de nickel destinée à être utilisée dans les applications de fusion sur lit de poudre. Définit des exigences strictes pour la poudre d'alliage de nickel AM, y compris le 316L.
- ASTM F3049 - Guide pour la caractérisation des propriétés des poudres métalliques utilisées dans les processus de fabrication additive. Fournit des conseils sur la mesure de caractéristiques telles que l'écoulement, la densité, la morphologie, etc.
Autres normes
- ISO 9001 - Gestion de la qualité pour la production de poudres métalliques
- ISO 13485 - Gestion de la qualité des poudres métalliques pour applications médicales
- ASME Boiler and Pressure Vessel Code - Exigences en matière de matériaux pour les appareils à pression
Les fournisseurs de poudre 316L réputés disposent de systèmes de qualité certifiés selon les normes ISO et ASTM. La traçabilité des lots et des tests approfondis sont effectués pour garantir la conformité.
Fournisseurs de poudre 316L
Parmi les principaux fournisseurs mondiaux de poudre d'acier inoxydable 316L, on peut citer
Entreprise | Méthodes de production | Types de poudre | Taille des particules |
---|---|---|---|
Sandvik | Atomisation du gaz | Osprey® 316L | 15-45 μm |
Technologie LPW | Atomisation du gaz | LPW 316L | 15-63 μm |
Charpentier | Atomisation du gaz | Charpentier 316L | 15-150 μm |
Höganäs | Vaporisation de l'eau | 316L | 10-45 μm |
CNPC | Atomisation du gaz et de l'eau | 316L | 10-150 μm |
Pometon | Atomisation du gaz et de l'eau | 316L | 10-150 μm |
ATI | Atomisation du gaz | 316L | 10-63 μm |
Le prix de la poudre 316L dépend de facteurs tels que
- Qualité, composition, taille et morphologie des poudres
- Méthode de production
- Quantité commandée et taille du lot
- Niveau de contrôle de la qualité et d'essais
- Exigences en matière d'emballage et de livraison
Le prix indicatif de la poudre 316L atomisée au gaz est de l'ordre de $50-100 par kg pour les commandes standard. Les commandes personnalisées avec des exigences spéciales peuvent coûter plus cher.
Lors de la sélection d'un fournisseur de poudre 316L, il convient de prendre en compte les éléments suivants :
- Les caractéristiques des poudres - distribution de la taille des particules, morphologie, fluidité, etc. doivent correspondre aux besoins de l'application.
- Qualité constante et composition conforme aux spécifications
- Chaîne d'approvisionnement et logistique fiables
- Conformité aux normes et certifications internationales
- Expertise technique et service à la clientèle
- Prix et quantité minimale de commande
Les principaux fabricants de poudres 316L ont des décennies d'expérience dans la production de poudres adaptées à l'AM, au MIM et à d'autres applications avec un contrôle de qualité rigoureux.
Considérations de conception pour la poudre 316L
Considérations de conception pour la poudre d'acier inoxydable 316L
Aspect | Considération | Impact sur la pièce imprimée | Recommandations |
---|---|---|---|
Épaisseur de la paroi | L'épaisseur minimale doit être de 0,8 à 1 mm | Les pièces aux parois plus minces peuvent être fragiles et sujettes aux fissures. | * Concevoir des murs d'au moins 1 mm d'épaisseur pour une solidité optimale. * Pensez à utiliser des nervures ou des treillis internes pour le renforcement des sections minces. * Pour les pièces nécessitant une épaisseur de paroi minimale, explorez des processus de fabrication additive alternatifs avec une résolution plus élevée. |
Surplombs et angles | Les angles vifs et les surplombs non pris en charge peuvent entraîner une déformation et un délaminage. | * Minimisez les angles vifs en incorporant des congés et des courbes. * Concevoir des surplombs avec des angles compris entre 30 et 45 degrés pour un meilleur support. * Utilisez des structures de support stratégiquement placées pendant l'impression pour éviter l'affaissement. | |
Finition et orientation de la surface | Les caractéristiques de la poudre et l'orientation de la couche peuvent influencer la texture de la surface. | * Comprendre comment la taille et la morphologie de la poudre affectent la rugosité de la surface. * Tenez compte de l'orientation des pièces pour minimiser la visibilité des couches sur les surfaces critiques. * Les techniques de post-traitement comme le polissage ou le sablage aux billes peuvent améliorer la finition de la surface. | |
Porosité | Les poches d'air emprisonnées dans la pièce peuvent compromettre les propriétés mécaniques. | * Optimisez les paramètres d'impression tels que la puissance du laser et la vitesse de numérisation pour obtenir une densité élevée. * Explorez des techniques telles que le pressage isostatique à chaud (HIP) pour minimiser davantage la porosité. * Concevoir des canaux internes ou des trous d'aération pour faciliter l'élimination de la poudre pendant l'impression. | |
La gestion du stress | Les contraintes résiduelles du processus d'impression peuvent entraîner des déformations ou des fissures. | * Utiliser les structures de support de manière stratégique pour minimiser les points de concentration du stress. * Concevez des fonctionnalités telles que des congés et des transitions progressives pour réduire l'accumulation de stress. * Envisagez un traitement thermique après impression pour un recuit de soulagement des contraintes. | |
Précision dimensionnelle | La distribution granulométrique et le retrait pendant le frittage peuvent affecter les dimensions finales. | * Tenez compte des taux de retrait (généralement autour de 20%) lors de la conception du modèle. * Utiliser les principes de conception pour la fabrication additive (DfAM) pour optimiser l'imprimabilité et minimiser les écarts dimensionnels. * Imprimez des pièces de test pour calibrer les paramètres d'impression et garantir la précision dimensionnelle. | |
Structures de soutien | Les structures temporaires nécessaires à des géométries complexes peuvent laisser des traces. | * Concevoir des structures de support avec une zone de contact minimale pour minimiser les marques de retrait. * Explorez les matériaux de support solubles pour un post-traitement plus facile. * Optimisez la conception de la structure de support pour une utilisation efficace des matériaux et un retrait facile. | |
Retrait des poudres | La poudre non retirée emprisonnée dans les cavités peut affecter la fonctionnalité. | * Concevoir des canaux internes ou des trous de drainage pour faciliter l'élimination de la poudre. * Utilisez des caractéristiques inclinées et des stratégies de ventilation pour éviter le piégeage de la poudre. * Optimisez les paramètres d'impression pour minimiser le collage de la poudre et améliorer la fluidité. |
Post-traitement des pièces en 316L
Post-traitement des pièces en acier inoxydable 316L
Processus | Description | Avantages | Considérations |
---|---|---|---|
Suppression du support | Suppression des structures temporaires utilisées lors de l'impression. | * Indispensable pour réaliser la géométrie finale de la pièce. * Permet d'accéder aux fonctionnalités internes. | * Le choix de la méthode de retrait dépend du type de matériau de support (dissolution manuelle, mécanique, chimique). * Une manipulation soigneuse est nécessaire pour éviter d'endommager la pièce. |
Traitement thermique | * Recuit de soulagement des contraintes : Réduit les contraintes résiduelles de l'impression pour améliorer la stabilité dimensionnelle et éviter les fissures. * Recuit de la solution : Affine la microstructure pour des propriétés mécaniques améliorées et une résistance à la corrosion. | * Optimise les performances et la longévité de la pièce. * Permet la conformité aux spécifications matérielles spécifiques. | * Nécessite un contrôle précis de la température et du temps en fonction de la géométrie de la pièce et du résultat souhaité. * Des techniques de refroidissement rapide comme la trempe peuvent être nécessaires pour le recuit en solution. |
Grenaillage | Bombarder la surface avec de petites sphères métalliques pour créer une couche de contrainte de compression. | * Améliore la résistance à la fatigue et à l'usure. * Améliore la résistance à la fissuration par corrosion sous contrainte. | * La sélection du média de projection et des paramètres de sablage dépend de la finition de surface souhaitée et de la profondeur de l'effet. * Un grenaillage excessif peut introduire une rugosité de surface. |
Décapage et passivation | Processus de nettoyage chimique pour éliminer les contaminants de surface et améliorer la résistance à la corrosion. | * Indispensable pour les pièces exposées à des environnements difficiles. * Crée une couche d'oxyde passive pour une protection améliorée contre la corrosion. | * La sélection des solutions de décapage et de passivation dépend de la qualité du matériau et de l'état de la surface. * Une mauvaise manipulation des produits chimiques nécessite des précautions de sécurité appropriées. |
Usinage et finition | Techniques soustractives traditionnelles pour obtenir des dimensions, des tolérances et des états de surface précis. | * Permet la création de fonctionnalités non réalisables avec AM. * Améliore l'esthétique et la fonctionnalité de la surface. | * Nécessite une expertise et un équipement d'usinage supplémentaires. * Peut introduire de la chaleur et du stress qui nécessitent un post-traitement supplémentaire. |
Polissage | Méthodes mécaniques ou chimiques pour obtenir une surface lisse et réfléchissante. | * Améliore l'attrait esthétique pour les applications décoratives. * Améliore l'hygiène des surfaces pour les dispositifs médicaux. * Réduit la rugosité de la surface pour une meilleure résistance à l'usure. | * La sélection de la méthode de polissage dépend du niveau de finition souhaité. * Un polissage excessif peut enlever de la matière et modifier les dimensions des pièces. |
Placage électrolytique | Déposer une fine couche d'un autre métal sur la surface pour des propriétés améliorées. | * Améliore la conductivité électrique, la résistance à l'usure ou la résistance à la corrosion. * Offre des finitions décoratives comme le chrome ou le placage or. | * Nécessite un équipement et une expertise spécialisés pour les bains de galvanoplastie. * L'épaisseur du placage doit être soigneusement contrôlée pour éviter le délaminage. |
Défauts courants dans les pièces en 316L
Défaut | Description | Cause | Impact | Stratégies d'atténuation |
---|---|---|---|---|
Porosité | Poches d'air emprisonnées à l'intérieur de la pièce lors de l'impression. | * Puissance laser ou vitesse de numérisation sous-optimale. * Fluidité insuffisante de la poudre. * Purge de gaz incorrecte. | * Résistance mécanique, durée de vie à la fatigue et résistance à la corrosion réduites. * Peut créer des chemins de fuite dans les applications fluides. | * Optimisez les paramètres d'impression pour une fusion et une densité appropriées. * Préchauffer le lit de poudre pour améliorer l'écoulement. * Utiliser une purge au gaz inerte pour minimiser l'air emprisonné. * Envisagez des techniques de post-traitement telles que le pressage isostatique à chaud (HIP) pour une densification plus poussée. |
Absence de fusion | Fusion incomplète entre les couches de poudre adjacentes. | * Densité de puissance laser insuffisante. * Épaisseur de couche de poudre incohérente. * Contamination à la surface de la poudre. | * Faible liaison intercouche, entraînant des fissures potentielles et une défaillance des pièces. | * Calibrez la puissance du laser et la vitesse de balayage pour une profondeur de fusion appropriée. * Assurer une épaisseur de couche de poudre constante grâce à des mécanismes de recouvrement appropriés. * Maintenir un lit de poudre propre, exempt d'humidité ou de contaminants. |
Ballonnement | Métal en fusion s’accumulant en perles excessives sur la surface supérieure. | * Densité de puissance laser excessive. * Vitesse de numérisation incorrecte. * Répartition incorrecte de la taille de la poudre. | * Finition de surface rugueuse avec une mauvaise esthétique. * Potentiel de projections et d'instabilité du processus. | * Réduisez la puissance du laser ou augmentez la vitesse de numérisation pour éviter la surchauffe. * Optimisez les modèles d'analyse pour éviter un temps de séjour excessif sur une seule zone. * Utiliser une distribution granulométrique plus uniforme pour un comportement de fusion cohérent. |
Fissures | Fractures de la pièce dues à des contraintes résiduelles ou à un choc thermique. | * Refroidissement rapide pendant l'impression. * Post-traitement insuffisant du soulagement du stress. * Coins pointus ou caractéristiques de conception qui concentrent le stress. | * Intégrité structurelle compromise et risque de défaillance des pièces. | * Implémentez des taux de refroidissement plus lents pendant l'impression pour minimiser les gradients thermiques. * Effectuer un recuit de soulagement des contraintes pour réduire les contraintes résiduelles. * Concevez des fonctionnalités avec des transitions douces et évitez les angles vifs. |
L'arrêt de travail | Distorsion de la pièce par rapport à sa géométrie prévue. | * Expansion et contraction thermique inégale pendant l'impression. * Structures de support inadéquates pour les géométries complexes. * Contraintes résiduelles bloquées dans la pièce. | * Imprécisions dimensionnelles et risque de dysfonctionnement des pièces. | * Optimiser les paramètres d'impression pour minimiser les gradients thermiques. * Utilisez des structures de support stratégiquement placées pour un support approprié pendant l'impression. * Mettre en œuvre un recuit de soulagement des contraintes pour réduire les tendances à la déformation. |
Décollement | Séparation des couches au sein de la pièce. | * Faible liaison intercouche due au manque de fusion. * Teneur excessive en humidité dans la poudre. * Contamination sur le lit de poudre. | * Perte d'intégrité structurelle et potentiel de délaminage des pièces. | * Assurer une bonne fusion entre les couches en optimisant les paramètres d'impression. * Maintenir une faible teneur en humidité de la poudre grâce à un stockage et une manipulation appropriés. * Utilisez un lit de poudre propre et exempt de contaminants. |
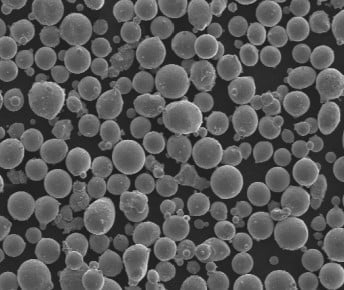
Comment choisir un fournisseur de poudre 316L
Voici un guide étape par étape sur la sélection d'un fournisseur de poudre d'acier inoxydable 316L :
Étape 1 : Déterminer les exigences de la demande
- Déterminer le processus de fabrication qui sera utilisé - AM, MIM, etc.
- Identifier les propriétés critiques de la poudre, telles que la taille des particules, la forme, la pureté, etc.
- Tenez compte des spécifications de la pièce - propriétés mécaniques, précision, finition de la surface, etc.
Étape 2 : Recherche de fournisseurs potentiels
- Recherche des principaux fabricants de poudre 316L avec une longue expérience
- Vérifier les capacités - méthodes de production, variétés de poudres, essais QC, etc.
- Examiner les études de cas et les commentaires des clients en rapport avec votre application
Étape 3 : Évaluer les capacités techniques
- Peut-on personnaliser la poudre 316L en fonction des besoins de l'application ?
- Ont-ils des compétences en matière d'AM, de MIM ou d'autres technologies des poudres ?
- Quel est leur niveau d'intégration verticale et de contrôle de la qualité ?
Étape 4 : Évaluer les offres de services
- Assistance technique lors de la sélection des poudres et du développement des applications
- Tests d'échantillons, services d'essai
- Réactivité aux demandes, flexibilité des délais
Étape 5 : Examen des certifications et de la conformité
- Certifications internationales de qualité - ISO 9001, ISO 13485, etc.
- Conformité aux normes de composition des poudres telles que l'ASTM
- Traçabilité des lots, essais et documentation approfondis
Étape 6 : Comparer les prix
- Prix par kg pour la granulométrie, le niveau de qualité et la quantité requis
- Exigences en matière de quantité minimale de commande et de taille de lot
- Frais d'expédition/logistique
Étape 7 : Vérifier la disponibilité et la fiabilité
- Approvisionnement régulier en stock et capacité à répondre aux fluctuations de la demande
- Suivi et contrôle des commandes, délais transparents
- Des résultats probants en matière de respect des délais
Le choix d'un fournisseur possédant une expertise en matière d'applications, une qualité de produit constante et un service réactif garantit une expérience d'achat sans heurts.
Comment optimiser la poudre 316L pour l'AM
Adapter la taille des particules au processus d'AM
- Utiliser des particules de 10-45 μm pour la fusion sur lit de poudre comme DMLS, SLM.
- Optimiser la distribution des tailles - une distribution trop large peut entraîner des problèmes d'emballage
- Les particules plus fines de 1 à 10 μm conviennent mieux à la projection de liant.
Obtenir une sphéricité et une fluidité élevées
- La fluidité affecte directement l'étalement de la poudre et l'uniformité de la couche.
- L'atomisation au gaz produit des poudres sphériques et fluides.
- Tester l'écoulement de la poudre conformément à la norme ASTM B213
Minimiser les particules des satellites
- Le tamisage et la classification permettent d'éliminer les satellites et les particules fines.
- Les satellites peuvent provoquer des agglomérations et des défauts
Contrôle Composition Tolérance
- Contrôle rigoureux de la composition élémentaire dans la fourchette spécifiée par l'ASTM
- Limiter les impuretés telles que O, N, C qui affectent les propriétés
Réduire la porosité
- Optimiser les paramètres du processus et les modèles de balayage
- Utiliser le pressage isostatique à chaud pour minimiser la porosité
- Maintenir une densité >99% pour des performances élevées
Minimiser les contraintes résiduelles
- Optimiser les gradients thermiques dans le processus de construction
- Utiliser des traitements thermiques appropriés pour réduire les contraintes
Atteindre les propriétés mécaniques souhaitées
- Le recuit de mise en solution et le vieillissement améliorent la résistance
- Maintenir des propriétés uniformes dans toutes les directions de construction
La caractérisation minutieuse des poudres, l'optimisation des paramètres et le post-traitement sont essentiels pour obtenir des pièces en 316L exemptes de défauts grâce à l'AM.
FAQ
Q : À quoi sert généralement la poudre d'acier inoxydable 316L ?
R : La poudre 316L est très largement utilisée pour la fabrication additive, le moulage par injection de métal et les applications de pressage et de frittage en raison de son excellente résistance à la corrosion combinée à de bonnes propriétés mécaniques et à une bonne biocompatibilité. Les applications courantes comprennent les implants, les composants aérospatiaux, les pièces automobiles, les dispositifs biomédicaux et l'outillage.
Q : Quelle est la taille de particule recommandée pour les procédés d'AM basés sur le laser ?
R : Une granulométrie de 10 à 45 microns est généralement recommandée pour les procédés de fusion laser sur lit de poudre tels que le DMLS et le SLM. Les particules plus fines, inférieures à 10 microns, peuvent poser des problèmes d'écoulement et d'étalement. La distribution de la taille des particules doit également être bien contrôlée.
Q : Comment la morphologie des poudres affecte-t-elle leurs propriétés ?
R : Une poudre très sphérique et fluide est souhaitable pour les applications AM. Les poudres irrégulières et hérissées conviennent aux méthodes de pressage et de frittage. Les particules satellites et les fines ont un impact négatif sur l'écoulement de la poudre et peuvent créer des défauts. Le contrôle de la morphologie de la poudre est essentiel pour obtenir des performances optimales.
Q : Quelles sont les principales différences entre la poudre 316L atomisée au gaz et la poudre atomisée à l'eau ?
R : La poudre 316L atomisée au gaz présente une morphologie plus sphérique et une meilleure fluidité. La poudre atomisée à l'eau présente des formes plus irrégulières mais offre une plus grande compressibilité souhaitée pour les applications de pressage et de frittage. La poudre atomisée au gaz a une teneur en oxygène plus faible.
Q : Quelles sont les méthodes de post-traitement utilisées sur les pièces AM en 316L ?
R : Le post-traitement courant comprend le traitement thermique, le pressage isostatique à chaud, la finition de surface par meulage/usinage, le revêtement et les essais de contrôle de la qualité. Cela permet d'obtenir les propriétés souhaitées, la précision dimensionnelle, l'esthétique et la détection des défauts.
Q : Quels sont les défauts courants de la poudre 316L et comment les éviter ?
R : Les défauts potentiels sont la porosité, la fissuration, la mauvaise finition de surface, le manque de fusion et les contraintes résiduelles. L'optimisation minutieuse des paramètres du processus, le contrôle de la qualité de la poudre, l'orientation de la fabrication et le post-traitement peuvent minimiser ces défauts dans les pièces en 316L.
Q : Quelles sont les normes applicables à la poudre 316L pour l'AM et d'autres applications ?
R : Les normes clés sont ASTM F3055 pour les poudres AM, ASTM B822 pour la caractérisation des poudres, ASTM A240 pour la composition des alliages et les normes ISO pour la gestion de la qualité. Les principaux fournisseurs de poudres 316L sont certifiés conformes à ces normes.
Q : Quels sont les facteurs qui déterminent le prix de la poudre 316L ?
R : Les principaux facteurs affectant le prix de la poudre de 316L sont le niveau de qualité, la taille et la distribution des particules, la méthode de production, la quantité commandée, les exigences de l'acheteur en matière d'essais/de contrôle qualité, d'emballage et de livraison. Des exigences plus strictes augmentent le prix.
Q : Comment optimiser la résistance à la corrosion des pièces AM en 316L ?
R : Les solutions comprennent le contrôle des niveaux d'impureté grâce à des tolérances strictes en matière de composition chimique, l'utilisation du pressage isostatique à chaud pour augmenter la densité et réduire la porosité, l'application de traitements de passivation et le recuit de mise en solution pour améliorer la résistance à la corrosion.
Partager sur
MET3DP Technology Co. est un fournisseur de premier plan de solutions de fabrication additive dont le siège se trouve à Qingdao, en Chine. Notre société est spécialisée dans les équipements d'impression 3D et les poudres métalliques de haute performance pour les applications industrielles.
Articles connexes
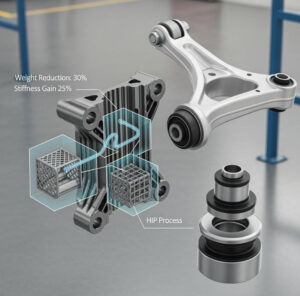
Metal 3D Printed Subframe Connection Mounts and Blocks for EV and Motorsport Chassis
Lire la suite "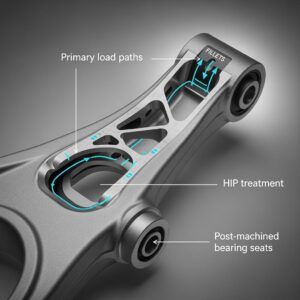
Metal 3D Printing for U.S. Automotive Lightweight Structural Brackets and Suspension Components
Lire la suite "À propos de Met3DP
Mise à jour récente
Notre produit
CONTACTEZ-NOUS
Vous avez des questions ? Envoyez-nous un message dès maintenant ! Nous répondrons à votre demande avec toute une équipe dès réception de votre message.
Obtenir les informations de Metal3DP
Brochure du produit
Obtenir les derniers produits et la liste des prix