3D Printing Automotive Throttle Bodies
Table des matières
Introduction to 3D Printed Automotive Throttle Bodies
The automotive industry is constantly seeking innovative solutions to enhance vehicle performance, improve fuel efficiency, and reduce emissions. One area where significant advancements are being made is in the manufacturing of critical engine components like the throttle body. Traditionally produced through casting or machining, throttle bodies are now benefiting from the transformative capabilities of metal 3D printing, also known as metal additive manufacturing. This cutting-edge technology allows for the creation of complex geometries, optimized designs, and the use of high-performance materials, opening up new possibilities for automotive engineers and procurement managers. At Métal3DP, we are at the forefront of this revolution, providing industry-leading Impression 3D equipment and high-quality metal powders to empower the automotive sector. Our commitment to accuracy and reliability ensures that mission-critical parts like throttle bodies meet the stringent demands of the automotive industry.
What Are 3D Printed Throttle Bodies Used For in Automotive Applications?
The throttle body is a vital component in an internal combustion engine that controls the amount of air entering the engine. By regulating airflow, it directly influences the engine’s power output and responsiveness. In modern vehicles, the throttle body is typically linked to the accelerator pedal, either mechanically or electronically (drive-by-wire systems). Depressing the pedal opens the throttle plate within the throttle body, allowing more air to flow into the intake manifold and subsequently the combustion chambers.
3D printed throttle bodies offer several key applications and benefits within the automotive sector:
- Amélioration des performances : The design freedom offered by metal 3D printing allows for the optimization of the throttle body’s internal channels and venturi shape. This can lead to improved airflow dynamics, resulting in enhanced engine performance, increased horsepower, and better torque delivery.
- Réduction du poids : Metal 3D printing enables the creation of lightweight designs with internal lattices or hollow structures, without compromising structural integrity. Reducing the weight of engine components like the throttle body contributes to overall vehicle weight reduction, leading to improved fuel efficiency and handling.
- Rapid Prototyping and Testing: Additive manufacturing significantly accelerates the prototyping process. Automotive engineers can quickly iterate on different throttle body designs, print functional prototypes in production-grade materials, and conduct rigorous testing to validate performance before committing to mass production.
- Personnalisation et production en faible volume : Metal 3D printing is ideal for producing customized throttle bodies for niche vehicle models, high-performance applications, or aftermarket modifications where traditional manufacturing methods might be cost-prohibitive for low volumes.
- Integration of Features: Complex internal features, such as integrated sensors or cooling channels, can be directly incorporated into the throttle body design during the 3D printing process. This reduces the need for secondary assembly operations and can improve the overall efficiency and functionality of the component.
Metal3DP’s advanced metal 3D printing services and high-performance metal powders are perfectly suited for these demanding automotive applications, providing solutions that meet the highest standards of quality and performance.
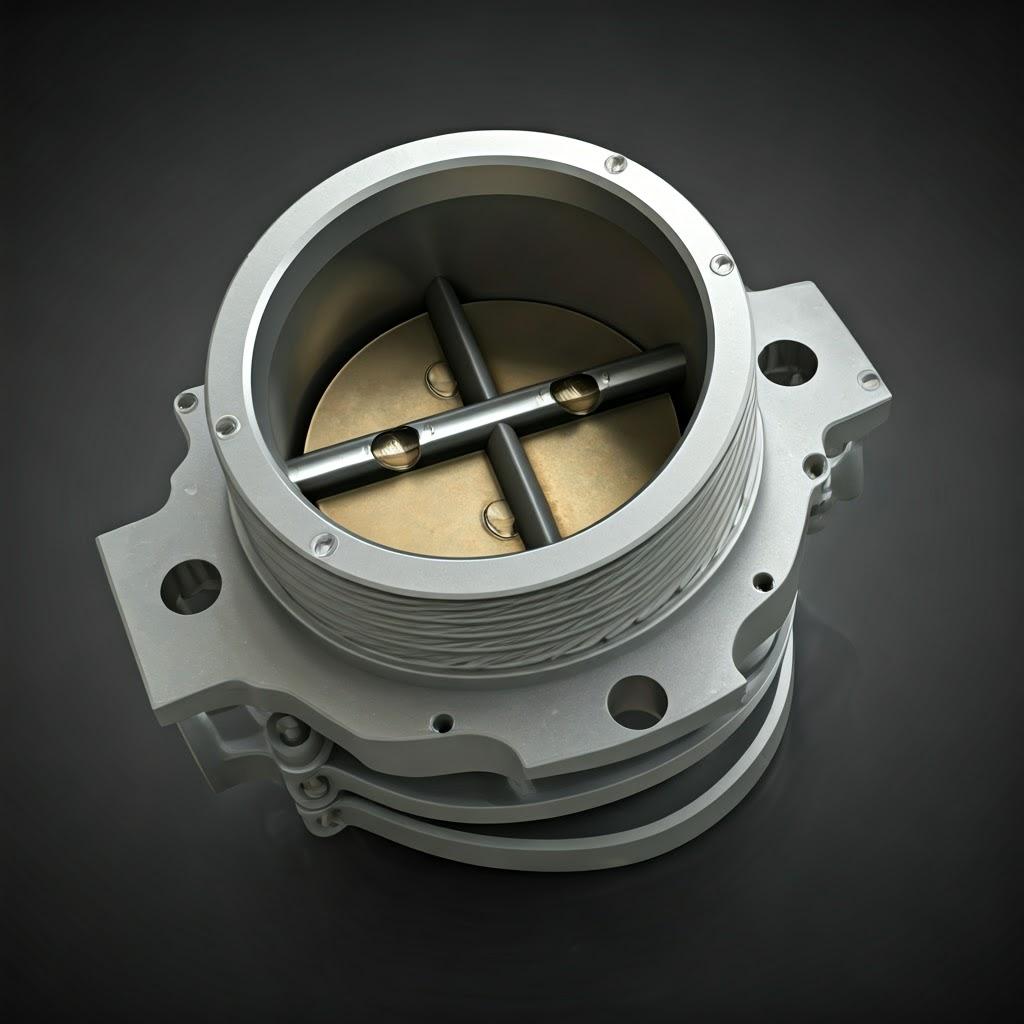
Advantages of Using Metal 3D Printing for Throttle Body Manufacturing
Compared to traditional manufacturing methods like casting and machining, metal 3D printing offers a compelling array of advantages for the production of automotive throttle bodies:
Fonctionnalité | Impression 3D de métaux | Fabrication traditionnelle (moulage/usinage) |
---|---|---|
Complexité de la conception | Enables intricate internal geometries, optimized flow paths, and integrated features. | Limited by mold design and tool accessibility, restricting design freedom. |
Efficacité des matériaux | Produces parts with minimal material waste, using only the necessary material. | Generates significant material waste through sprues, runners, and machining chips. |
Vitesse de prototypage | Rapid iteration and production of functional prototypes in days or weeks. | Longer lead times for tooling and mold creation, delaying the prototyping phase. |
Personnalisation | Cost-effective production of customized or low-volume parts. | High tooling costs make customization and low-volume production expensive. |
Weight Optimization | Allows for lightweight designs with internal lattices and hollow structures. | Achieving significant weight reduction can be challenging and costly. |
Coûts d'outillage | Minimal or no tooling required, reducing upfront investment and lead times. | High costs associated with mold design, fabrication, and maintenance. |
Assembly Reduction | Complex features can be integrated directly, minimizing the need for assembly. | Multiple components often require assembly, increasing complexity and costs. |
Innovation matérielle | Compatible with a wide range of high-performance metal powders tailored for specific applications. | Material selection can be limited by casting or machining processes. |
Exporter vers les feuilles
Our printing methods at Metal3DP leverage these advantages to provide automotive manufacturers with high-quality, performance-driven throttle body solutions.
Recommended Metal Powders for 3D Printed Throttle Bodies and Their Significance
The choice of metal powder is crucial in determining the final properties and performance of a 3D printed automotive throttle body. At Metal3DP, we offer a range of high-quality metal powders optimized for demanding applications. For automotive throttle bodies, two particularly suitable materials are AlSi10Mg and A7075:
1. AlSi10Mg (Aluminum Silicon Magnesium):
- Propriétés : This aluminum alloy offers an excellent combination of lightweight properties, high strength-to-weight ratio, good thermal conductivity, and corrosion resistance. It exhibits good castability and weldability, making it well-suited for complex geometries achievable through 3D printing.
- Significance for Throttle Bodies: The lightweight nature of AlSi10Mg contributes to overall vehicle weight reduction, improving fuel efficiency and handling. Its high strength ensures the throttle body can withstand the mechanical stresses of engine operation. Good thermal conductivity helps dissipate heat effectively, maintaining optimal performance.
- Applications : Widely used in automotive and aerospace industries for components requiring high strength and low weight, such as intake manifolds, cylinder heads, and structural parts.
- Metal3DP Advantage: Our advanced powder making system ensures that our AlSi10Mg powder has high sphericity and good flowability, crucial for achieving dense, high-quality 3D printed parts with superior mechanical properties.
2. A7075 (Aluminum Zinc Magnesium Copper):
- Propriétés : A7075 is a high-strength aluminum alloy known for its exceptional strength-to-weight ratio, even higher than AlSi10Mg. It offers excellent fatigue resistance and is often used in demanding structural applications.
- Significance for Throttle Bodies: For high-performance vehicles or racing applications where maximum strength and durability are critical, A7075 provides superior mechanical properties, ensuring the throttle body can withstand extreme operating conditions.
- Applications : Commonly used in aerospace for highly stressed components, as well as in high-performance automotive and sporting goods.
- Metal3DP Advantage: Metal3DP’s high-quality metal powders, including A7075, are manufactured using industry-leading gas atomization and PREP technologies, guaranteeing consistent quality and optimal performance in 3D printing processes. Our extensive portfolio of innovative alloys allows customers to select the perfect material for their specific application requirements.
By utilizing these recommended metal powders with Metal3DP’s advanced 3D printing equipment and expertise, automotive manufacturers can produce high-performance throttle bodies with optimized designs and superior material properties.
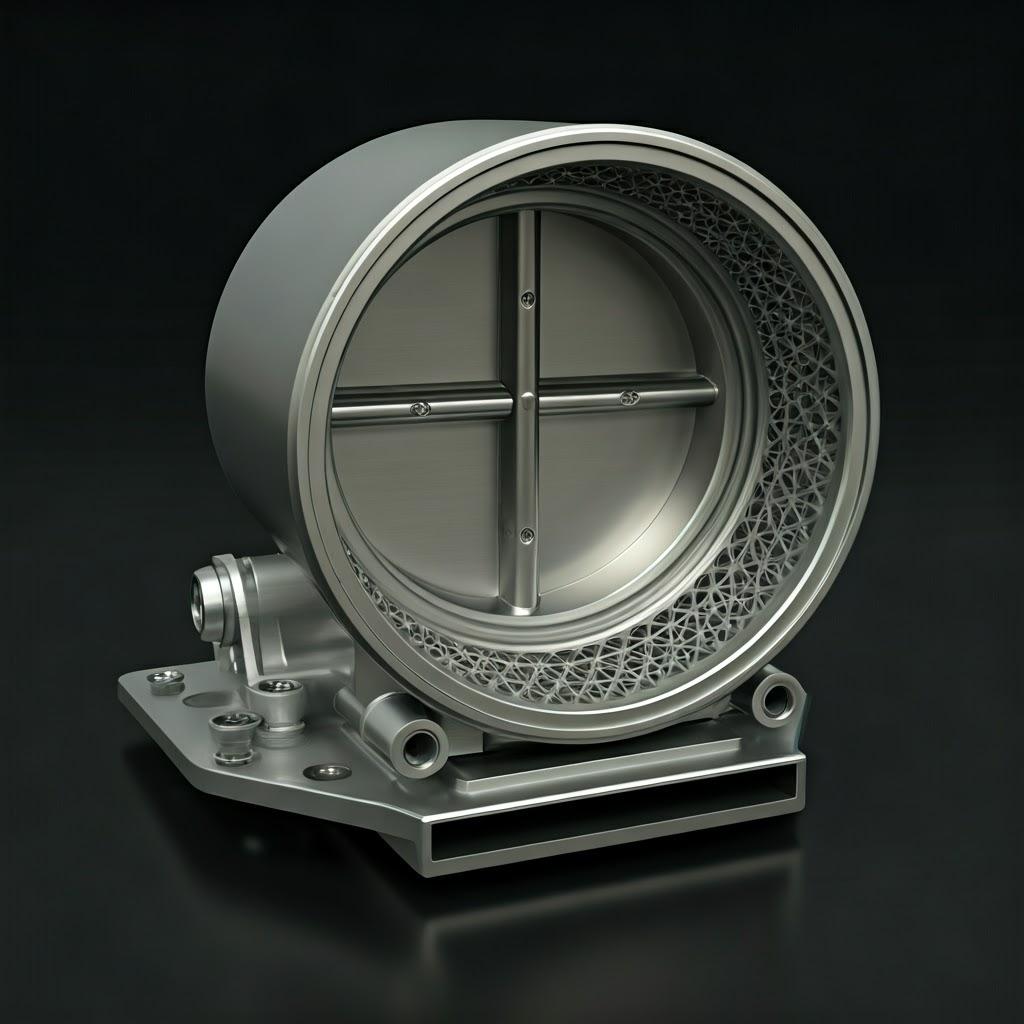
Design Optimization for Additively Manufactured Throttle Bodies
The transition from traditional manufacturing to metal 3D printing unlocks unprecedented design freedom for automotive throttle bodies. Engineers can now move beyond the constraints of casting and machining to create geometries that optimize airflow, reduce weight, and integrate functionalities. Here are key design considerations for additively manufactured throttle bodies:
- Aerodynamic Optimization: Metal 3D printing allows for the creation of complex internal channels with smooth, continuous curves. This can significantly reduce airflow resistance and turbulence compared to conventionally manufactured throttle bodies with abrupt changes in cross-section. By optimizing the venturi shape and inlet/outlet geometries, engineers can enhance engine breathing and improve overall performance. Computational Fluid Dynamics (CFD) analysis plays a crucial role in simulating airflow and guiding design iterations for optimal aerodynamic efficiency.
- Stratégies d'allègement : Additive manufacturing enables the implementation of advanced lightweighting techniques. This includes:
- Structures de treillis internes : Creating intricate internal support structures that provide high strength while significantly reducing material usage and weight. The density and geometry of the lattice can be tailored to specific load-bearing requirements.
- Optimisation de la topologie : Using algorithms to determine the optimal material distribution based on applied loads and constraints. This results in organic-looking designs that use material only where it’s structurally necessary.
- Hollow Features: Designing hollow internal sections with thin walls to reduce weight without compromising stiffness.
- Intégration des fonctionnalités : Metal 3D printing facilitates the integration of multiple components into a single part. For throttle bodies, this could include:
- Integrated Sensor Mounts: Directly incorporating mounting features for throttle position sensors or other relevant sensors, eliminating the need for separate brackets and fasteners.
- Canaux de refroidissement intégrés : Designing internal channels for coolant circulation to manage the temperature of the throttle body, particularly in high-performance applications.
- Integrated Actuation Mechanisms: In some advanced designs, components of the throttle plate actuation system could potentially be integrated into the throttle body itself.
- Considérations relatives à la sélection des matériaux : The choice of material directly influences the design possibilities. For instance, the high strength-to-weight ratio of AlSi10Mg and A7075 allows for thinner walls and more aggressive lightweighting strategies compared to heavier materials. The thermal conductivity of the chosen powder also needs to be considered if heat dissipation is a critical design parameter.
- Design for Additive Manufacturing (DfAM) Principles: Successful metal 3D printing requires adherence to DfAM guidelines. This includes:
- Minimisation des structures de support : Designing parts to reduce the need for support structures, which can impact surface finish and require post-processing.
- Optimisation de l'orientation : Orienting the part within the build chamber to minimize overhangs and improve dimensional accuracy.
- Consideration of Build Volume: Designing within the constraints of the 3D printer’s build volume.
- Gestion thermique pendant l'impression : Understanding how heat will be dissipated during the printing process to avoid warping or other defects.
Au Métal3DP, our team of experienced engineers possesses deep expertise in DfAM and can assist automotive clients in optimizing their throttle body designs for metal 3D printing, ensuring both performance and manufacturability.
Achieving Precision: Tolerance, Surface Finish, and Dimensional Accuracy in 3D Printed Throttle Bodies
For critical automotive components like throttle bodies, achieving tight tolerances, a smooth surface finish, and high dimensional accuracy is paramount to ensure proper fit, sealing, and performance. Metal 3D printing technologies have made significant strides in delivering the required precision:
- Capacités de tolérance : Selective Laser Melting (SLM) and Electron Beam Melting (EBM), the primary metal 3D printing technologies offered by Métal3DP, can achieve dimensional tolerances ranging from ±0.05 mm to ±0.1 mm, depending on the material, part geometry, and build parameters. Critical functional surfaces that require even tighter tolerances can be post-machined.
- Finition de la surface : The as-built surface finish in metal 3D printing is typically rougher than machined surfaces, with Ra (average roughness) values ranging from 5 to 20 µm. The surface finish is influenced by factors such as powder particle size, laser/electron beam parameters, and layer thickness. For throttle body applications where smooth airflow is essential, post-processing techniques like polishing, abrasive blasting, or chemical etching can be employed to achieve smoother surface finishes down to Ra values of 1 µm or better.
- Précision dimensionnelle : Dimensional accuracy refers to the degree to which the printed part matches the intended CAD model. Metal 3D printing processes are capable of achieving high dimensional accuracy, but it’s influenced by factors like material shrinkage during solidification, thermal gradients, and part orientation. Careful process control, optimized build parameters, and experienced operators are crucial for maximizing accuracy. Metal3DP’s industry-leading printers are designed for high accuracy and reliability, ensuring that printed throttle bodies meet stringent dimensional requirements.
Factors Affecting Precision:
Facteur | Impact on Tolerance | Impact on Surface Finish | Impact on Dimensional Accuracy |
---|---|---|---|
Technologie d'impression 3D | SLM generally offers tighter tolerances than EBM | Finer powder and layer thickness in SLM can yield better surface finish | Each technology has its own inherent accuracy limitations |
Matériau | Different materials exhibit varying shrinkage rates | Material properties affect how powder particles fuse | Material properties influence thermal behavior and shrinkage |
Build Parameters | Laser/beam power, scan speed, layer thickness | Laser/beam parameters, layer thickness, powder size distribution | Build orientation, support strategy, thermal control |
Géométrie des pièces | Complex geometries can be more challenging to print accurately | Overhangs and intricate features can result in rougher surfaces | Thin walls and large flat surfaces are prone to distortion |
Post-traitement | Machining can significantly improve tolerances | Polishing, blasting, and coating can enhance surface finish | Can correct minor dimensional inaccuracies |
Exporter vers les feuilles
By carefully controlling these factors and leveraging the capabilities of advanced metal 3D printing technologies, it is possible to produce automotive throttle bodies with the precision required for optimal engine performance and longevity.
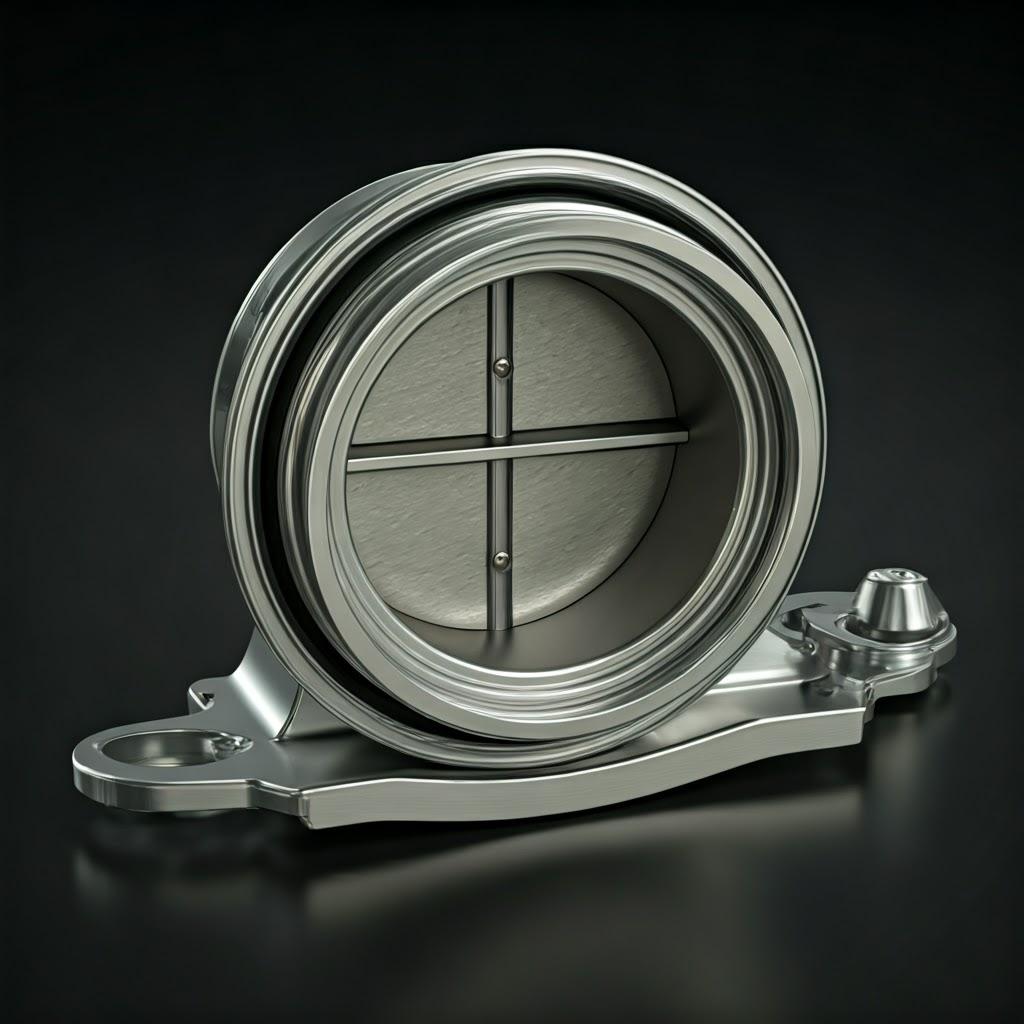
Post-Processing Techniques for 3D Printed Automotive Throttle Bodies
While metal 3D printing offers significant advantages in terms of design freedom and material utilization, post-processing steps are often necessary to achieve the final desired properties, surface finish, and dimensional accuracy for automotive throttle bodies. Common post-processing techniques include:
- Suppression du support : Support structures are often required during the 3D printing process to prevent collapse or distortion of overhanging features. These supports need to be carefully removed after printing. The removal method can vary depending on the material and support geometry, including manual removal, machining, or chemical dissolution.
- Traitement thermique : Heat treatment is a crucial step to relieve internal stresses that may have built up during the rapid heating and cooling cycles of the 3D printing process. It also helps to achieve the desired mechanical properties, such as hardness and tensile strength, for the specific metal alloy. Common heat treatment processes for aluminum alloys like AlSi10Mg and A7075 include solution annealing and aging.
- Finition de la surface : As mentioned earlier, the as-built surface finish of 3D printed metal parts is typically rough. For throttle bodies, smoother internal surfaces are desirable to minimize airflow resistance. Common surface finishing techniques include:
- Media Blasting: Using abrasive media to remove loose powder and reduce surface roughness.
- Polissage : Mechanical or chemical polishing to achieve a smoother, often mirror-like finish.
- Chemical Etching: Selectively removing surface layers to improve smoothness.
- Anodisation (pour l'aluminium) : Creating a protective oxide layer on the surface, which can also improve corrosion resistance and provide a cosmetic finish.
- Usinage CNC : For critical functional surfaces that require very tight tolerances or specific features that are difficult to achieve directly through 3D printing, CNC machining can be used as a secondary operation. This can include machining of mounting surfaces, sealing faces, or threads.
- Revêtement : Depending on the application requirements, coatings may be applied to enhance corrosion resistance, wear resistance, or other surface properties. Examples include hard anodizing for aluminum or specialized coatings for harsh environments.
- Inspection et contrôle qualité : Thorough inspection using techniques like coordinate measuring machines (CMM), laser scanning, and non-destructive testing (NDT) is essential to ensure that the final 3D printed throttle body meets the required dimensional accuracy, surface finish, and material integrity standards.
Métal3DP offers comprehensive post-processing services to ensure that our 3D printed metal parts meet the exact specifications of our automotive clients. Our expertise in heat treatment, surface finishing, and precision machining allows us to deliver functional, high-quality throttle bodies ready for integration into vehicle systems.
Overcoming Common Challenges in Metal 3D Printing of Throttle Bodies
While metal 3D printing offers numerous advantages, there are also potential challenges that need to be addressed to ensure successful production of automotive throttle bodies:
- Déformation et distorsion : Thermal stresses during the printing process can lead to warping or distortion of the part, particularly for large or complex geometries with thin walls. Careful design optimization, proper part orientation, and optimized build parameters are crucial to minimize these effects. Advanced simulation tools can also help predict and mitigate potential distortion.
- Retrait de la structure de soutien : Removing support structures can sometimes be challenging, especially for intricate internal features. Improper support design or removal can lead to surface damage. Soluble support materials or optimized support geometries can help alleviate this issue.
- Porosité : Internal porosity can occur in 3D printed metal parts if the powder particles are not fully melted and fused. This can negatively impact the mechanical properties and fatigue life of the throttle body. Optimizing laser/electron beam parameters, powder quality, and build atmosphere are essential to minimize porosity. Metal3DP’s high-quality metal powders and advanced printing equipment are designed to produce dense, low-porosity parts.
- Rugosité de la surface : Achieving a smooth surface finish directly from the 3D printing process can be challenging. As discussed earlier, post-processing techniques are often required to meet the surface finish requirements for critical airflow surfaces in throttle bodies.
- Residual Stresses: Rapid heating and cooling during the printing process can induce residual stresses within the part. These stresses can lead to cracking or failure under load. Proper heat treatment is essential to relieve residual stresses and ensure the long-term reliability of the component.
- Considérations relatives aux coûts : While metal 3D printing can be cost-effective for prototyping and low-volume production, the cost per part can be higher than traditional methods for very high volumes. Optimizing designs for manufacturability, reducing material usage, and streamlining post-processing can help improve cost-competitiveness.
- Scaling to Mass Production: Transitioning from prototyping to mass production using metal 3D printing requires careful consideration of factors such as build time, equipment capacity, and process repeatability. Strategies like nesting multiple parts within the build volume and utilizing high-throughput printing systems are necessary for scaling production.
By understanding these potential challenges and implementing appropriate design strategies, process controls, and post-processing techniques, automotive manufacturers can effectively leverage metal 3D printing to produce high-performance, reliable throttle bodies. Contactez Metal3DP to explore how our expertise and comprehensive solutions can help you overcome these challenges and achieve your additive manufacturing goals.
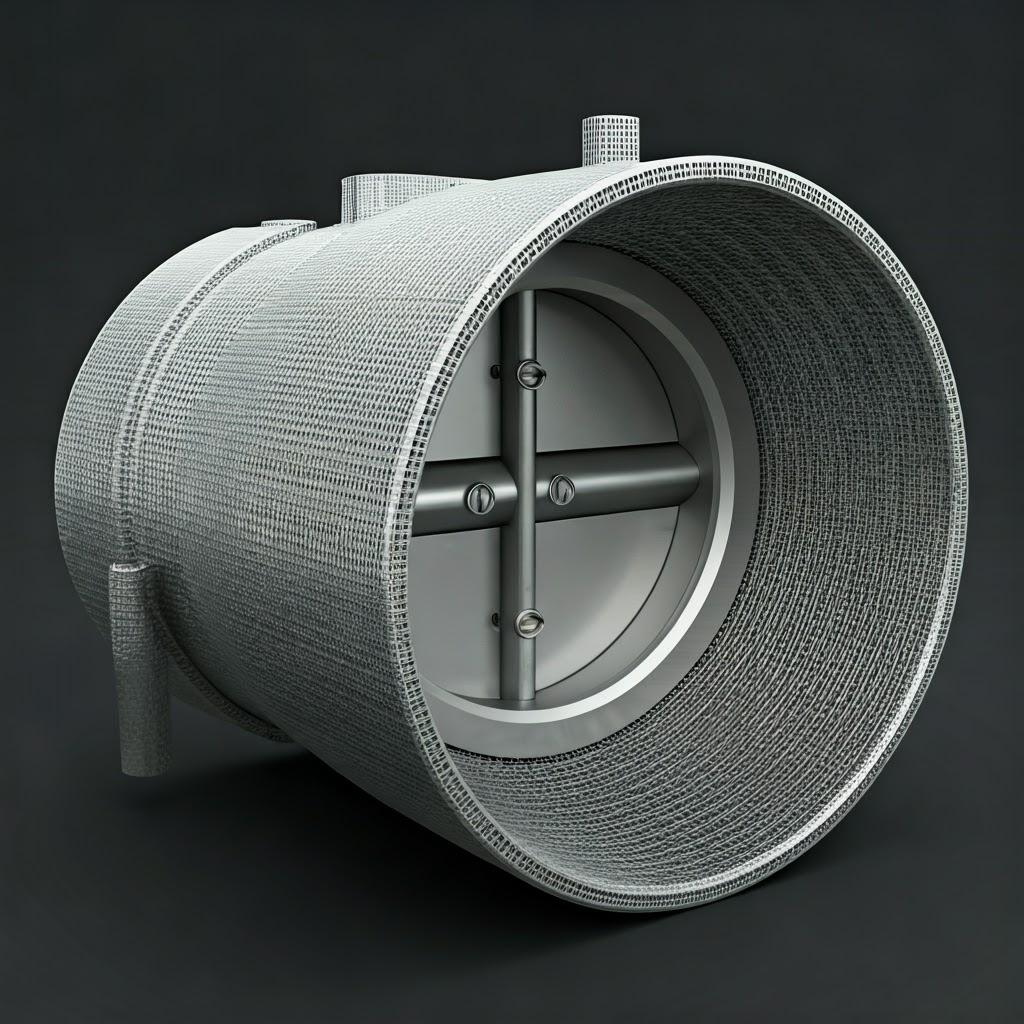
Selecting the Right Metal 3D Printing Service Provider for Automotive Parts
Choosing the right metal 3D printing service provider is a critical decision for automotive manufacturers looking to leverage the benefits of additive manufacturing for components like throttle bodies. A reliable partner will possess the expertise, equipment, and quality control processes necessary to deliver high-performance parts that meet stringent automotive standards. Here are key factors to consider when evaluating potential suppliers:
- Capacités matérielles : Ensure the service provider offers a range of metal powders relevant to automotive applications, including aluminum alloys like AlSi10Mg and A7075, as well as other materials that might be suitable for specific throttle body designs (e.g., titanium alloys for high-performance, lightweight applications). Verify that they have experience processing these materials and can provide material data sheets and testing reports. Métal3DP boasts a comprehensive portfolio of high-quality metal powders optimized for laser and electron beam powder bed fusion.
- Technologie et équipement : Understand the types of metal 3D printing technologies the provider utilizes (e.g., SLM, DMLS, EBM). Each technology has its own strengths and limitations in terms of achievable tolerances, surface finish, and build volume. Ensure they have well-maintained, industry-leading equipment capable of meeting your project requirements. Metal3DP’s printers deliver industry-leading print volume, accuracy, and reliability.
- Quality Assurance and Certifications: Inquire about the service provider’s quality management system and certifications (e.g., ISO 9001, AS9100 for aerospace). Robust quality control processes, including material traceability, in-process monitoring, and post-printing inspection, are essential for ensuring the reliability and consistency of automotive parts.
- Design and Engineering Support: A valuable service provider will offer design and engineering support to help optimize your throttle body design for additive manufacturing. This includes expertise in DfAM principles, topology optimization, and material selection. Our company provides comprehensive solutions spanning SEBM printers, advanced metal powders, and application development services.
- Capacités de post-traitement : Determine if the provider offers the necessary post-processing services to meet your requirements, such as support removal, heat treatment, surface finishing (polishing, anodizing), and CNC machining. An in-house or well-managed network of post-processing capabilities can streamline the production process.
- Lead Times and Production Capacity: Discuss lead times for prototyping and production, as well as the provider’s capacity to handle your anticipated volumes. Ensure their timelines align with your project schedules.
- Cost Structure and Transparency: Obtain a clear understanding of the pricing structure, including printing costs, material costs, and any additional charges for design, post-processing, or quality control. A transparent pricing model is crucial for budget planning.
- Communication and Customer Support: Evaluate the provider’s responsiveness, communication practices, and overall customer support. A strong partner will be proactive in addressing your needs and providing regular updates.
- Expérience dans le secteur : Look for a service provider with a proven track record of working with automotive clients and a deep understanding of the industry’s specific requirements and standards.
By carefully evaluating these factors, you can select a metal 3D printing service provider that is well-equipped to deliver high-quality automotive throttle bodies that meet your performance, cost, and timeline expectations.
Cost Analysis and Lead Time for 3D Printed Throttle Body Production
Understanding the cost factors and lead times associated with metal 3D printing of automotive throttle bodies is essential for effective project planning and budgeting.
Facteurs de coût :
- Coûts des matériaux : The cost of the metal powder is a significant factor. Different alloys have varying prices, and material waste (though generally lower in 3D printing compared to subtractive methods) will also influence the overall material cost per part.
- Temps de construction : The time it takes to print a throttle body depends on its size, complexity, and the chosen printing technology. Longer build times translate to higher machine operating costs.
- Coûts d'exploitation de la machine : These costs include electricity consumption, maintenance, and depreciation of the 3D printing equipment.
- Pre-Processing Costs: This can include design optimization for additive manufacturing, build file preparation, and any necessary simulations.
- Coûts de post-traitement : As discussed earlier, post-processing steps like support removal, heat treatment, surface finishing, and machining add to the overall cost. The complexity and extent of post-processing required will significantly impact the final price.
- Coûts de main-d'œuvre : Skilled technicians are needed for machine operation, pre-processing, post-processing, and quality control. Labor costs will be factored into the overall cost per part.
- Quantity and Volume: The cost per part generally decreases as the production volume increases, especially when optimizing build layouts to maximize the number of parts printed in a single build. However, very high volumes might still be more economically produced using traditional methods.
Délai de mise en œuvre:
- Prototypage : Metal 3D printing offers significantly shorter lead times for prototyping compared to traditional tooling-based methods. Functional prototypes can often be produced within days or weeks, allowing for rapid design iteration and testing.
- Production à faible volume : For low to medium production volumes, metal 3D printing can offer competitive lead times, especially for complex geometries that would require long lead times for tooling.
- Production en grande quantité : Lead times for high-volume production will depend on the number of available printers, build times, and the efficiency of post-processing workflows. Careful production planning and optimization are crucial for meeting high-volume demands.
It’s important to note that both cost and lead time are highly dependent on the specific design of the throttle body, the chosen material, the required quality and tolerances, and the service provider’s capabilities and pricing structure. Obtaining detailed quotes from multiple reputable suppliers like Métal3DP is recommended to get an accurate understanding of the cost and lead time for your specific project.
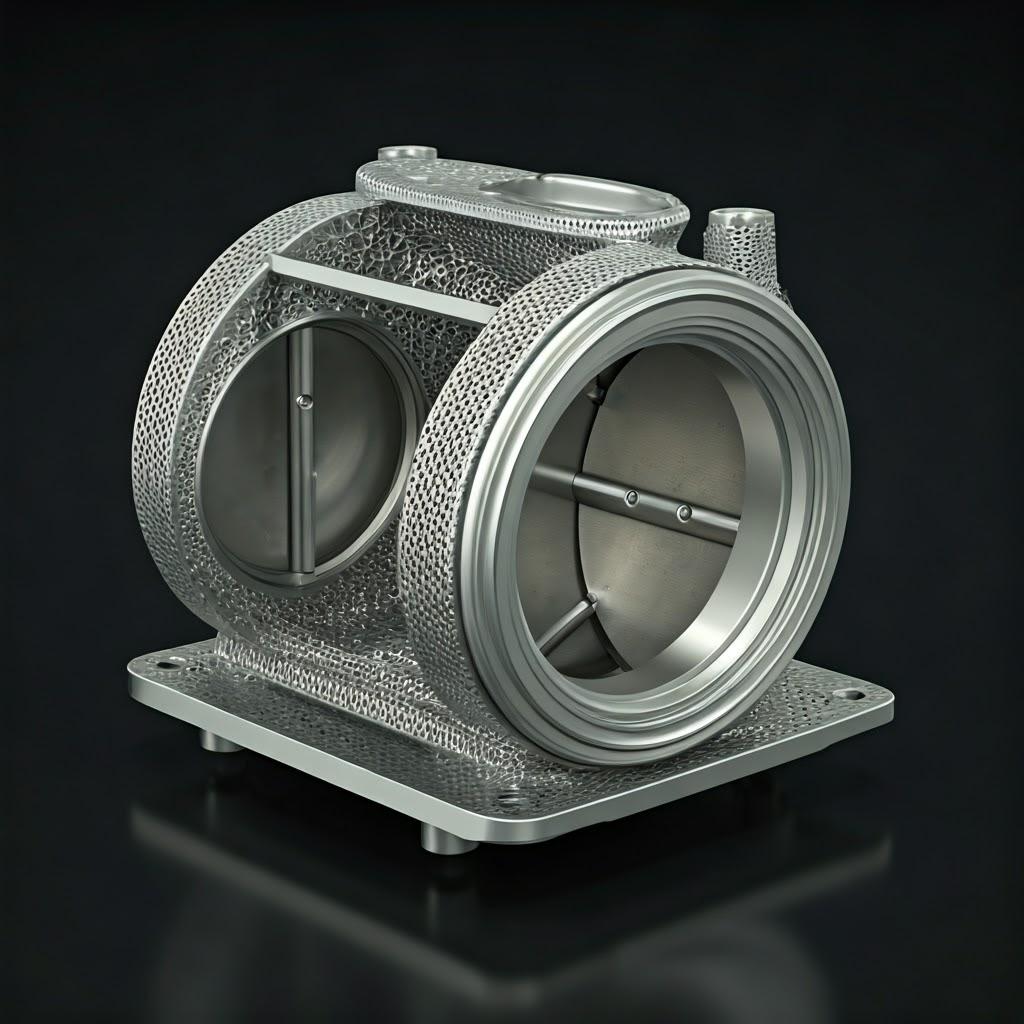
Foire aux questions (FAQ)
- Q: Can metal 3D printed throttle bodies meet the durability requirements of automotive applications?
- A : Yes, when the appropriate high-performance metal powders (such as AlSi10Mg or A7075) are used and proper post-processing techniques (like heat treatment) are applied, 3D printed metal throttle bodies can achieve the required strength, durability, and fatigue resistance for demanding automotive environments. Metal3DP’s expertise in material science and processing ensures the production of robust and reliable parts.
- Q: What are the typical tolerances achievable with metal 3D printing for throttle bodies?
- A : Depending on the printing technology and material, tolerances of ±0.05 mm to ±0.1 mm are achievable. For critical functional surfaces requiring tighter tolerances, post-processing with CNC machining can be employed.
- Q: Is metal 3D printing cost-effective for mass production of automotive throttle bodies?
- A : While metal 3D printing excels in rapid prototyping and low-to-medium volume production of complex parts, the cost-effectiveness for very high-volume production needs to be evaluated on a case-by-case basis, considering factors like design complexity, material costs, and post-processing requirements. For certain intricate designs or specialized applications, it can still be a viable option even at higher volumes.
Conclusion: The Future of Automotive Throttle Body Manufacturing with Metal 3D Printing
Metal 3D printing is rapidly transforming the landscape of automotive component manufacturing, and the production of throttle bodies is no exception. The ability to create complex, optimized designs with lightweight materials like AlSi10Mg and A7075 offers significant advantages in terms of performance, efficiency, and customization. While challenges such as achieving tight tolerances and smooth surface finishes require careful consideration and appropriate post-processing, advancements in metal 3D printing technologies and the expertise of providers like Métal3DP are continuously pushing the boundaries of what’s possible.
As the automotive industry continues to innovate and demand more efficient and high-performing vehicles, metal 3D printing will play an increasingly crucial role in the design and manufacturing of critical engine components like throttle bodies. The technology empowers engineers to break free from the limitations of traditional manufacturing, enabling the creation of next-generation automotive parts that were once considered impossible. Contactez Metal3DP today to explore how our cutting-edge systems and high-quality metal powders can power your organization’s additive manufacturing goals in the automotive sector.
Partager sur
MET3DP Technology Co. est un fournisseur de premier plan de solutions de fabrication additive dont le siège se trouve à Qingdao, en Chine. Notre société est spécialisée dans les équipements d'impression 3D et les poudres métalliques de haute performance pour les applications industrielles.
Articles connexes
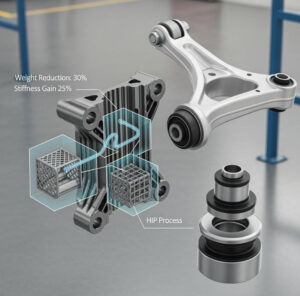
Metal 3D Printed Subframe Connection Mounts and Blocks for EV and Motorsport Chassis
Lire la suite "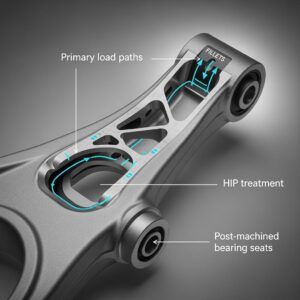
Metal 3D Printing for U.S. Automotive Lightweight Structural Brackets and Suspension Components
Lire la suite "À propos de Met3DP
Mise à jour récente
Notre produit
CONTACTEZ-NOUS
Vous avez des questions ? Envoyez-nous un message dès maintenant ! Nous répondrons à votre demande avec toute une équipe dès réception de votre message.
Obtenir les informations de Metal3DP
Brochure du produit
Obtenir les derniers produits et la liste des prix