Impression 3D d'aubes de turbines avec des superalliages
Table des matières
Introduction : Révolutionner la fabrication des aubes de turbines grâce à la fabrication additive métallique
Les aubes de turbines sont au cœur des performances de nombreuses industries critiques, depuis les hauteurs de l'aérospatiale jusqu'aux environnements exigeants de la production d'énergie. Ces composants méticuleusement conçus fonctionnent dans des conditions extrêmes, supportant une chaleur intense, des pressions élevées et des contraintes mécaniques importantes. Traditionnellement, la fabrication des pales de turbines fait appel à des processus complexes en plusieurs étapes, tels que le moulage à la cire perdue et le forgeage de précision, suivis d'un usinage poussé. Bien qu'efficaces, ces méthodes se heurtent souvent à des limites liées à la complexité de la conception, au gaspillage de matériaux (en particulier avec les superalliages coûteux) et à de longs délais d'exécution, ce qui a un impact sur les cycles d'innovation et la réactivité de la chaîne d'approvisionnement.
La fabrication additive métallique (AM), plus communément connue sous le nom de fabrication additive métallique, a fait son apparition L'impression 3D. Cette technologie transformatrice modifie rapidement le paysage de la production de composants de haute performance. Au lieu de soustraire de la matière d'un bloc solide ou de la couler dans un moule, l'AM construit des pièces couche par couche directement à partir de dessins numériques en utilisant des poudres métalliques de haute qualité. Pour les aubes de turbine, cela ouvre des possibilités sans précédent. Imaginez des aubes dotées de canaux de refroidissement internes complexes optimisés pour une dissipation maximale de la chaleur, des conceptions offrant une efficacité aérodynamique inégalée ou la possibilité de produire des pièces de rechange à la demande, réduisant ainsi considérablement les temps d'arrêt.
La synergie entre les superalliages avancés - matériaux spécialement conçus pour résister aux températures élevées et au fluage - et la liberté géométrique offerte par le système de gestion de l'énergie de l'Union européenne (UE) a permis d'améliorer la qualité de l'air impression 3D de métaux est particulièrement efficace pour les applications de pales de turbines. Les superalliages à base de nickel tels que l'IN738LC, l'IN718 et le Rene 41 possèdent les propriétés exceptionnelles requises pour résister aux environnements de fonctionnement difficiles à l'intérieur des moteurs à réaction et des turbines à gaz industrielles. L'AM des métaux permet aux ingénieurs d'exploiter pleinement ces matériaux et de créer des composants dont la fabrication était auparavant impossible ou d'un coût prohibitif.
Pour les ingénieurs et les responsables des achats dans les secteurs de l'aérospatiale, de l'énergie et de l'industrie, comprendre les capacités de l'AM des métaux pour la production d'aubes de turbines n'est plus facultatif ; c'est un impératif stratégique. Cette technologie offre des possibilités de :
- Amélioration des performances : Optimiser les conceptions pour améliorer l'efficacité, la durabilité et la gestion thermique.
- Réduction des délais d'exécution : Accélérer le prototypage et la production, ce qui permet d'accélérer les cycles de développement et les opérations de maintenance, de réparation et de révision (MRO).
- Utilisation améliorée des matériaux : Minimiser le gaspillage de superalliages coûteux grâce à une fabrication proche de la forme du filet.
- Agilité de la chaîne d'approvisionnement : Permettre une production à la demande, réduire les coûts d'inventaire et atténuer les risques associés aux chaînes d'approvisionnement traditionnelles.
- Consolidation partielle : Combinez plusieurs composants en une seule pièce imprimée, réduisant ainsi le temps d'assemblage et les points de défaillance potentiels.
Des entreprises comme Metal3DP Technology Co. LTD (Met3dp) sont à l'avant-garde de cette révolution. Basée à Qingdao, en Chine, Met3dp est spécialisée dans la fourniture de solutions complètes de fabrication additive, comprenant des équipements d'impression 3D à la pointe de l'industrie et des poudres métalliques de première qualité et de haute performance adaptées à des applications exigeantes. Notre expertise dans le traitement de matériaux difficiles tels que les superalliages, associée à des techniques avancées de production de poudres telles que l'atomisation au gaz, garantit la qualité et la fiabilité requises pour les pièces critiques. Cet article traite des spécificités de l'utilisation de l'AM des métaux, en particulier des superalliages tels que l'IN738LC, l'IN718 et le Rene 41, pour la fabrication d'aubes de turbine de pointe, en vous guidant à travers les applications, les avantages, les considérations relatives aux matériaux, et plus encore. Que vous envisagiez le prototypage, la production en série ou l'optimisation de votre chaîne d'approvisionnement pour les composants critiques, la compréhension de cette technologie est essentielle pour conserver un avantage concurrentiel.
Applications principales : Où sont déployées les aubes de turbine imprimées en 3D ?
Les capacités uniques de la fabrication additive métallique, en particulier lorsqu'elle est associée à des superalliages haute performance, en font une solution de plus en plus attrayante pour la production d'aubes de turbine dans toute une série d'industries exigeantes. La capacité de créer des géométries complexes, d'optimiser les performances et de répondre rapidement aux besoins de MRO favorise son adoption dans des applications critiques où la défaillance n'est pas une option. Les principaux domaines d'application sont les suivants
1. Moteurs à turbine à gaz pour l'aérospatiale : Il s'agit sans doute de l'application la plus importante et la plus exigeante. Les aubes des turbines des moteurs à réaction fonctionnent à des températures extrêmes (dépassant souvent le point de fusion de l'alliage lui-même, ce qui nécessite un refroidissement sophistiqué) et à des vitesses de rotation élevées.
- Lames de turbine à haute pression (HPT) : Ces pales sont soumises au flux de gaz le plus chaud directement après la chambre de combustion. L'AM permet de créer des canaux de refroidissement internes très complexes (passages en serpentin, micro-canaux, trous de refroidissement de film) qu'il est extrêmement difficile, voire impossible, de réaliser avec le moulage traditionnel. Ce refroidissement amélioré permet aux moteurs de fonctionner à plus haute température, ce qui augmente l'efficacité et la poussée. Les superalliages tels que l'IN738LC et les alliages monocristallins spécialisés (souvent développés en propre) sont courants ici.
- Lames de turbine à basse pression (LPT) : Bien qu'elles fonctionnent à des températures plus basses que les aubes HPT, les aubes LPT sont plus grandes et soumises à des forces centrifuges importantes. L'AM permet de réduire le poids grâce à l'optimisation des structures internes et de la topologie, ce qui améliore l'efficacité globale du moteur et réduit potentiellement les contraintes sur les composants en aval. Des matériaux tels que l'IN718 sont fréquemment utilisés.
- Lames de compresseur : Bien qu'ils fonctionnent généralement à des températures plus basses que les aubes de turbine, certains étages de compresseurs avancés bénéficient également de la liberté de conception et des options de matériaux offertes par l'AM, en particulier pour l'allègement ou les profils aérodynamiques complexes.
- MRO et systèmes existants : L'AM offre une solution vitale pour la production de pales de remplacement pour les flottes d'avions vieillissantes, lorsque l'outillage d'origine n'existe plus ou que les quantités minimales de commande pour le moulage sont prohibitives. Cette solution garantit le maintien de la navigabilité et de la disponibilité opérationnelle, une préoccupation majeure pour les équipes chargées des achats dans les secteurs de la défense et de l'aviation commerciale.
2. Turbines à gaz industrielles (IGT) pour la production d'électricité : Semblables à des moteurs à réaction, mais généralement plus grands et conçus pour durer et être plus efficaces que la simple poussée, les IGT sont essentiels à la production d'électricité.
- Pales et aubes de turbines : L'AM permet de produire de grandes pales complexes dotées d'un système de refroidissement avancé afin d'améliorer l'efficacité et le rendement des turbines. La capacité de produire rapidement des conceptions de pales personnalisées ou améliorées permet aux exploitants de centrales électriques d'améliorer les performances pendant les cycles de maintenance. Les superalliages tels que l'IN738LC et l'IN718 sont des outils de travail dans ce secteur en raison de leur excellent équilibre entre résistance mécanique, résistance au fluage et résistance à la corrosion dans les environnements de combustion.
- Composants du brûleur et buses de combustible : Bien qu'il ne s'agisse pas de pales, les composants de la section chaude bénéficient également de la capacité de l'AM à créer des passages internes complexes pour un mélange air-carburant et un refroidissement optimaux, améliorant ainsi l'efficacité de la combustion et réduisant les émissions.
- Réparation et remise à neuf : Les techniques d'AM telles que le dépôt direct d'énergie (DED) ou le dépôt de métal au laser (LMD) sont de plus en plus utilisées pour réparer les pales d'IGT usées ou endommagées, souvent en ajoutant du matériau aux pointes ou aux bords d'attaque usés, ce qui prolonge considérablement la durée de vie des composants et réduit les coûts de MRO pour les fournisseurs de production d'énergie.
3. Turbines à vapeur : Utilisées pour la production d'électricité (souvent en association avec des sources de chaleur nucléaire ou fossile) et pour l'entraînement industriel à grande échelle, les turbines à vapeur fonctionnent dans des conditions différentes (haute pression, humidité) de celles des turbines à gaz.
- Optimisation des lames : Bien que les superalliages soient moins courants ici (les aciers inoxydables et les alliages de titane sont plus typiques), l'AM peut encore offrir des avantages en optimisant les profils des pales pour des conditions de vapeur spécifiques, améliorant ainsi l'efficacité, en particulier dans les dernières étapes où les pales sont très longues et complexes.
- Prototypage rapide : L'essai de nouvelles conceptions aérodynamiques est plus rapide et plus rentable avec l'AM qu'avec les méthodes traditionnelles.
4. Turbocompresseurs haute performance : Utilisés dans les applications automobiles et marines, les turbocompresseurs utilisent une petite turbine pour entraîner un compresseur, augmentant ainsi la puissance et l'efficacité du moteur.
- Roues à turbines : La roue de la turbine fonctionne à des températures et des vitesses élevées. Bien qu'elle soit souvent fabriquée à partir de matériaux tels que l'Inconel (par exemple, IN713C par moulage), l'AM offre la possibilité de créer des roues plus légères avec des géométries d'aubes optimisées en utilisant des matériaux tels que l'IN718 ou même des aluminiures de titane (TiAl) pour des applications de performances extrêmes, améliorant la réponse transitoire.
Répondre aux besoins des entreprises : Pour les responsables des achats et les spécialistes de la chaîne d'approvisionnement, l'AM des métaux offre une proposition de valeur convaincante dans ces applications :
- Réduction des coûts d'outillage : Élimine le besoin de moules de coulée ou de matrices de forgeage coûteux, ce qui est particulièrement avantageux pour les séries de production de faible à moyen volume ou pour les pièces anciennes.
- Disponibilité à la demande : Facilite l'inventaire numérique et la production locale, réduisant ainsi la dépendance à l'égard de fournisseurs éloignés et les longs délais d'approvisionnement en pièces de rechange essentielles.
- Personnalisation et mises à jour : Permet des conceptions sur mesure pour des exigences de performance spécifiques ou l'intégration d'améliorations de la conception sans investissements majeurs de réoutillage.
- Consolidation des fournisseurs : Un partenariat avec un fournisseur d'AM compétent comme Met3dp, qui offre à la fois des services d'impression avancés et un approvisionnement en poudre de haute qualité, peut rationaliser le processus d'approvisionnement pour les composants complexes.
Le déploiement d'aubes de turbine imprimées en 3D s'étend rapidement à mesure que la technologie mûrit, démontrant des avantages tangibles en termes de performance, de coût et de résilience de la chaîne d'approvisionnement dans ces secteurs industriels vitaux.
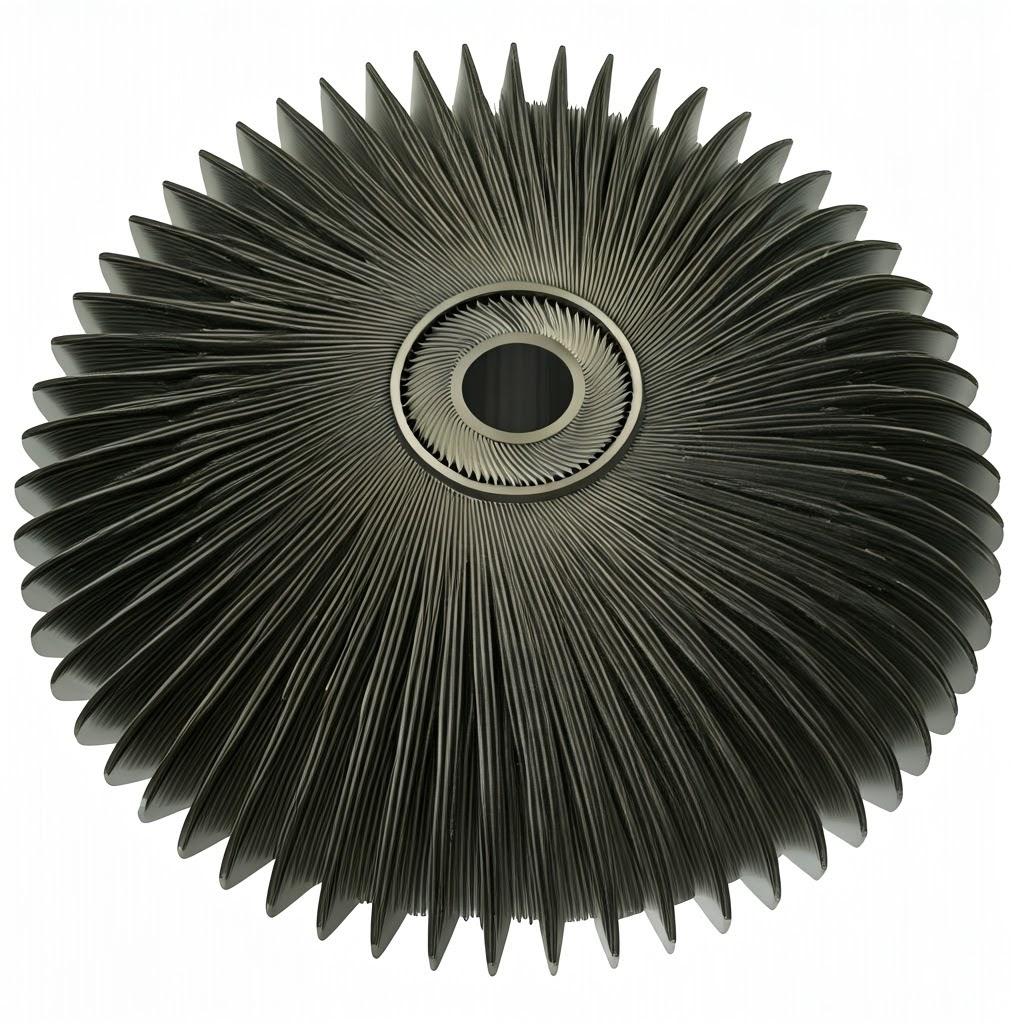
L'avantage AM : Pourquoi choisir l'impression 3D de métaux pour la production d'aubes de turbines ?
Alors que les méthodes de fabrication traditionnelles telles que le moulage à la cire perdue et l'usinage CNC multi-axes ont bien servi l'industrie pendant des décennies, la fabrication additive métallique représente un changement de paradigme, offrant des avantages distincts cruciaux pour les besoins exigeants de la production d'aubes de turbine. Ces avantages permettent de relever les principaux défis auxquels sont confrontés les ingénieurs et les professionnels de l'approvisionnement, en influant sur la conception, les délais, les coûts et l'efficacité globale de la chaîne d'approvisionnement.
1. Une liberté de conception sans précédent : C'est peut-être l'avantage le plus important. Les méthodes traditionnelles sont limitées par les exigences en matière d'outillage (par exemple, les angles de dépouille pour le moulage, l'accès à l'outil pour l'usinage). L'AM fabrique les pièces couche par couche, libérant ainsi les concepteurs d'un grand nombre de ces contraintes.
- Géométries internes complexes : Permet la création de canaux de refroidissement internes très sophistiqués à l'intérieur des pales (par exemple, passages en serpentin, structures en treillis, refroidissement conforme) qui sont impossibles ou peu pratiques à réaliser autrement. Un meilleur refroidissement permet d'augmenter les températures à l'entrée de la turbine, ce qui se traduit directement par une augmentation de l'efficacité du moteur/de la turbine et de la puissance produite.
- Optimisation de la topologie : Le logiciel peut optimiser la structure de la pale, en retirant de la matière des zones à faible contrainte tout en renforçant les régions critiques. Cela permet d'alléger les pales sans compromettre leur résistance, de réduire la masse en rotation et d'améliorer la réponse du moteur et le rendement énergétique.
- Consolidation partielle : Plusieurs composants (par exemple, une pale et ses éléments de plate-forme ou de carénage) peuvent potentiellement être imprimés en une seule unité, ce qui réduit les étapes d'assemblage, le poids, le nombre de pièces et les points de défaillance potentiels.
- Biomimicry & ; Novel Designs : L'AM permet d'explorer des formes aérodynamiques et des structures internes entièrement nouvelles, inspirées de la nature ou de simulations avancées de la dynamique des fluides numérique (CFD).
2. Développement accéléré et réduction des délais : La fabrication traditionnelle implique de longs délais pour la création de l'outillage (plusieurs mois pour les moules de coulée complexes) et la mise en place. L'AM raccourcit considérablement le chemin entre la conception et la pièce physique.
- Prototypage rapide : Les ingénieurs peuvent concevoir, imprimer et tester des prototypes fonctionnels en quelques jours ou semaines, au lieu de plusieurs mois. Cela permet de multiplier les itérations de conception et d'accélérer les cycles d'optimisation.
- Élimination de l'outillage : L'AM est un processus sans outil. Cela permet de réduire considérablement le délai initial et les coûts associés à la production de moules ou de matrices, ce qui est particulièrement avantageux pour la production de faibles volumes ou de pièces personnalisées.
- Production à la demande et MRO : Les lames de rechange ou de remplacement peuvent être imprimées en fonction des besoins, ce qui minimise les coûts de stockage et réduit le temps d'immobilisation de l'avion au sol ou de la centrale électrique. Cette souplesse est essentielle pour assurer l'efficacité des opérations de maintenance et de réparation et la résilience des chaînes d'approvisionnement.
3. Amélioration de l'efficacité des matériaux : Les superalliages utilisés pour les aubes de turbine (Inconels, alliages de René) sont notoirement chers. La fabrication soustractive traditionnelle peut gaspiller une quantité importante de ce matériau précieux (rapport achat-vol élevé).
- Fabrication de formes quasi-nettes : Les procédés AM tels que la fusion sélective par laser (SLM) ou la fusion par faisceau d'électrons (EBM) permettent de fabriquer des pièces couche par couche, en n'utilisant que le matériau nécessaire à la pièce et à ses structures de support. Cela permet de réduire considérablement les pertes de matériaux par rapport à l'usinage à partir d'une pièce massive.
- Utilisation optimisée des matériaux : L'optimisation de la topologie permet de concevoir des pièces en n'utilisant le matériau que là où il est structurellement nécessaire, ce qui améliore encore l'efficacité du matériau.
4. Potentiel de rentabilité (en fonction du contexte) : Si le coût par pièce de l'AM peut parfois être plus élevé que celui des pièces moulées produites en série, la proposition de valeur globale est souvent convaincante :
- Réduction de l'investissement dans l'outillage : Il élimine les coûts d'outillage initiaux élevés, ce qui le rend économique pour les prototypes, les séries de faible volume et les pièces personnalisées.
- Réduction des coûts d'assemblage : Réalisé grâce à la consolidation partielle.
- Réduction des coûts liés aux déchets de matériaux : Économies significatives, en particulier avec les superalliages coûteux.
- Diminution des coûts des stocks : La production à la demande permet d'atteindre cet objectif.
- Valeur des gains de performance : L'efficacité ou la longévité accrues obtenues grâce à des conceptions AM supérieures peuvent compenser les coûts initiaux plus élevés des pièces au cours de leur cycle de vie (coût total de possession).
5. Simplification et résilience de la chaîne d'approvisionnement : L'AM permet de passer à la fabrication numérique.
- Inventaire Numérique : Les dessins sont stockés sous forme numérique et peuvent être imprimés n'importe où avec l'équipement adéquat et des processus/matériaux certifiés.
- Production localisée : Réduction de la dépendance à l'égard des chaînes d'approvisionnement mondiales complexes, atténuation des risques géopolitiques et des coûts/retards de transport.
- Réduction de la dépendance à l'égard des fournisseurs : Moins de dépendance à l'égard des fonderies spécialisées dans le moulage, ce qui pourrait élargir la base des fournisseurs.
Résumé de la comparaison : méthodes AM et méthodes traditionnelles pour les pales de turbines
Fonctionnalité | Fabrication additive métallique (SLM/EBM) | Moulage à la cire perdue | Usinage CNC (à partir de billettes/forges) |
---|---|---|---|
Complexité de la conception | Très élevé (possibilité de caractéristiques internes complexes) | Modérée (limitée par la conception du moule) | Modéré (limité par l'accès aux outils) |
Refroidissement interne | Excellent (chaînes très complexes réalisables) | Bon (il existe des techniques établies) | Médiocre (très difficile/impossible) |
Délai d'exécution (initial) | Court (jours/semaines – ; pas d'outillage dur) | Longue (mois – ; production de moules) | Modéré (semaines – ; installation/programmation) |
Délai d'exécution (répétition) | Modéré | Courte et modérée (en utilisant le moule existant) | Modéré |
Déchets matériels | Faible (forme proche du filet) | Modéré (portes, coureurs) | Élevé (enlèvement important de copeaux) |
Coût de l'outillage | Aucune/Minimale (soutiens) | Élevé (conception du moule & ; production) | Faible-modéré (accessoires, outils) |
Coût (faible volume) | Potentiellement inférieur (pas d'amortissement de l'outillage) | Élevé (le coût de l'outillage domine) | Élevée (déchets de matériaux, temps machine) |
Coût (volume élevé) | Potentiellement plus élevé (rythme de construction plus lent) | Plus faible (amortissement de l'outillage, cycle plus rapide) | Modéré-élevé |
Consolidation partielle | Potentiel élevé | Faible potentiel | Faible potentiel |
Options de matériaux | Croissance (nécessite le développement de la poudre & ; paramètres du processus) | Large (bien établi) | Large (nécessite des pièces usinables) |
Exporter vers les feuilles
Le choix de l'AM des métaux, soutenu par des fournisseurs experts tels que Met3dp, qui comprennent à la fois les techniques avancées de l'AM des métaux et les techniques de l'AM des métaux méthodes d'impression et la science des matériaux, permet aux entreprises de dépasser les limites traditionnelles et d'atteindre de nouveaux niveaux de performance et d'efficacité dans la production d'aubes de turbines. Les équipes chargées des achats bénéficient de délais réduits, d'une plus grande souplesse de la chaîne d'approvisionnement et d'un potentiel de réduction des coûts à long terme grâce à une conception et à un cycle de vie supérieurs des composants.
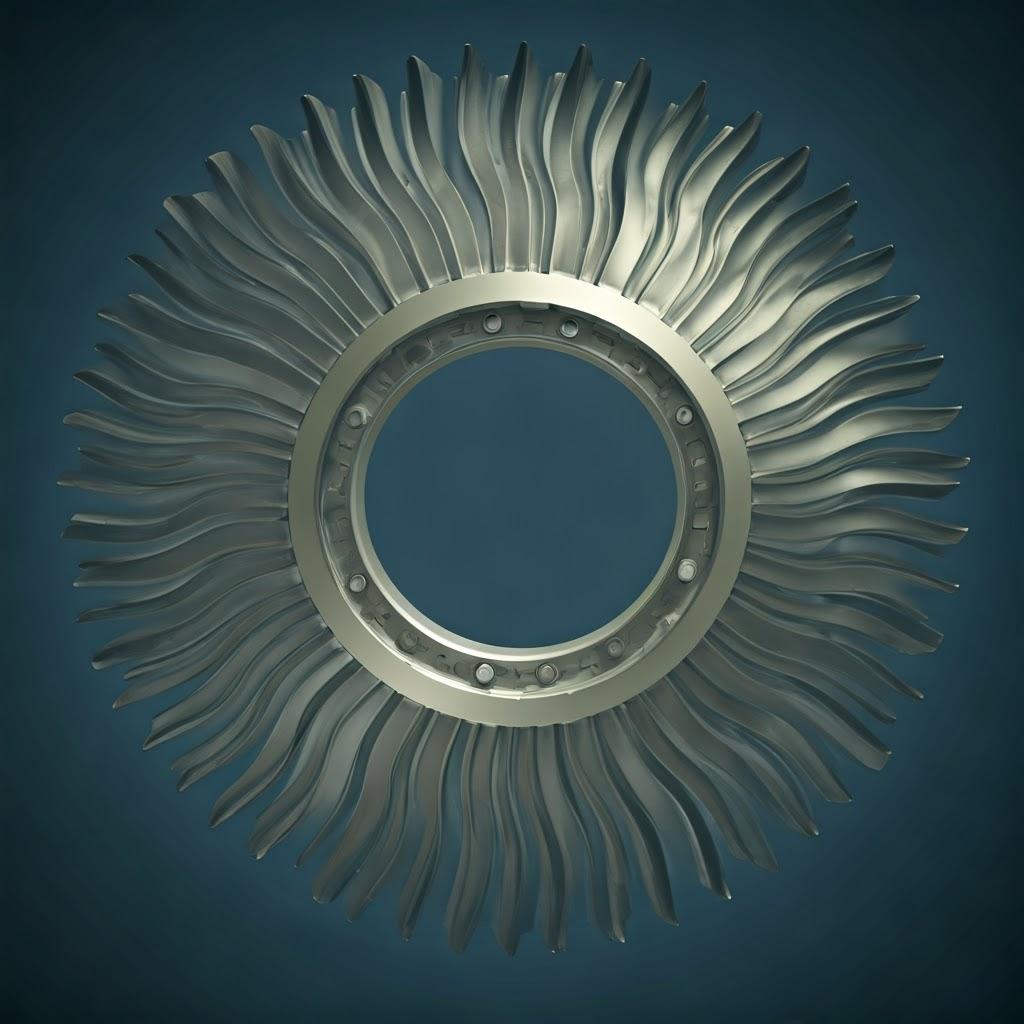
Focus matériaux : Superalliages IN738LC, IN718, Rene 41 pour des lames de haute performance
Les conditions de fonctionnement extrêmes des turbines à gaz nécessitent l'utilisation de matériaux aux propriétés exceptionnelles. Les superalliages, généralement à base de nickel, sont les matériaux de choix pour les aubes de turbine en raison de leur capacité à maintenir une résistance élevée, une résistance au fluage, une durée de vie en fatigue et une stabilité de surface (résistance à l'oxydation et à la corrosion) à des températures élevées proches de leur point de fusion. Il est primordial de sélectionner le bon superalliage et d'assurer sa qualité sous forme de poudre pour réussir la fabrication additive de composants de turbine fiables. Parmi les superalliages les plus pertinents et les plus fréquemment utilisés, imprimables par AM pour ces applications, figurent l'IN738LC, l'IN718 et le Rene 41.
Pourquoi les superalliages ? Avant d'entrer dans les détails, il est essentiel de comprendre ce qui suit pourquoi ces matériaux sont essentiels :
- Résistance à haute température : Ils conservent une résistance à la traction et une limite d'élasticité significatives même lorsqu'ils sont exposés à des températures supérieures à 800°C (1472°F), et souvent beaucoup plus élevées pour de courtes durées ou avec un refroidissement.
- Résistance au fluage : Ils résistent à une déformation lente sous une contrainte constante à des températures élevées, ce qui est essentiel pour les lames soumises à une charge centrifuge dans une trajectoire de gaz chauds.
- Résistance à la fatigue : Ils résistent aux charges cycliques (thermiques et mécaniques) subies lors du démarrage, du fonctionnement et de l'arrêt de la turbine.
- Résistance à la corrosion et à l'oxydation : Ils forment des couches d'oxyde protectrices (généralement de la chromie ou de l'alumine) pour résister à la dégradation due aux gaz de combustion chauds et aux facteurs environnementaux.
Superalliages recommandés pour les aubes de turbines AM :
1. Inconel 738 à faible teneur en carbone (IN738LC) :
- Vue d'ensemble : Superalliage à base de nickel durcissable par précipitation, connu pour son excellente résistance à haute température, sa résistance au fluage et sa résistance à la corrosion à chaud, en particulier dans les environnements contenant du soufre, typiques des turbines à gaz industrielles. La variante “LC” ; a une teneur en carbone plus faible pour une meilleure soudabilité et, par conséquent, une meilleure imprimabilité par rapport à l’IN738 standard.
- Propriétés principales : Excellente résistance au fluage jusqu'à ~980°C (1800°F), bonne coulabilité (historiquement), et bonne résistance à la corrosion à chaud. Nécessite des traitements thermiques spécifiques après l'impression pour obtenir une microstructure et des propriétés optimales.
- Considérations relatives à la FA : Peut être difficile à imprimer en raison de sa susceptibilité à la fissuration par solidification si les paramètres ne sont pas soigneusement contrôlés. Nécessite une gestion thermique précise pendant le processus de fabrication et bénéficie souvent d'un post-traitement par pressage isostatique à chaud (HIP) pour fermer la porosité interne.
- Applications typiques : Principalement utilisé pour les aubes de turbine du premier étage et les aubes des turbines à gaz industrielles (IGT) en raison de sa résistance supérieure à la corrosion à chaud et de sa grande résistance au fluage.
2. Inconel 718 (IN718) :
- Vue d'ensemble : L'un des superalliages à base de nickel les plus utilisés en raison de son bon équilibre de propriétés, de son excellente aptitude à la fabrication (y compris à l'impression) et de son coût relativement plus faible que celui d'autres superalliages haut de gamme. Il est renforcé par précipitation en ajoutant du niobium et du molybdène.
- Propriétés principales : Haute résistance jusqu'à ~700°C (1300°F), bonne résistance au fluage jusqu'à cette température, excellente soudabilité/impression, bonne résistance à la fatigue et bonne résistance à la corrosion. Facilement disponible et bien caractérisé pour les processus AM.
- Considérations relatives à la FA : Généralement considéré comme l'un des superalliages les plus faciles à imprimer par fusion laser sur lit de poudre (L-PBF/SLM) et par fusion par faisceau d'électrons (EBM). Les traitements thermiques standard (recuit de mise en solution et vieillissement) sont bien établis pour développer les propriétés souhaitées.
- Applications typiques : Largement utilisé dans l'aérospatiale pour les disques et les aubes de compresseurs, les carters de moteurs, les aubes de turbines à basse pression (LPT) et divers composants structurels. Également utilisé dans les IGT pour les composants fonctionnant à des températures légèrement inférieures, ainsi que dans les turbocompresseurs, les applications nucléaires et le traitement chimique.
3. Rene 41 (Haynes® R-41) :
- Vue d'ensemble : Superalliage à base de nickel, durcissable par vieillissement, connu pour sa très grande résistance à des températures élevées. Il contient des quantités importantes de chrome, de cobalt et de molybdène, qui contribuent à sa solidité et à sa résistance à la corrosion.
- Propriétés principales : Résistance exceptionnellement élevée jusqu'à ~870°C (1600°F). Bonne résistance à l'oxydation.
- Considérations relatives à la FA : Peut être très difficile à traiter par AM en raison de sa forte susceptibilité à la fissuration par déformation lors des traitements thermiques post-soudure ou post-impression s'il n'est pas manipulé avec soin. Il nécessite des paramètres d'impression méticuleusement développés et des cycles de traitement thermique souvent spécialisés. Son imprimabilité est généralement considérée comme inférieure à celle de l'IN718.
- Applications typiques : Utilisé dans des applications aérospatiales exigeantes nécessitant un rapport résistance/poids élevé à haute température, telles que les composants de postcombustion, les carters de turbines, les boulons et certaines applications d'aubes de turbines où son profil de résistance spécifique est avantageux, malgré les difficultés de mise en œuvre.
Aperçu comparatif :
Fonctionnalité | IN738LC | IN718 | Rene 41 (Haynes® R-41) |
---|---|---|---|
Principaux points forts | Résistance à la corrosion à chaud, haute résistance au fluage. | Imprimabilité, propriétés équilibrées, coût | Très haute température Résistance |
Température maximale d'utilisation (approx.) | ~980°C (1800°F) – ; Fluage limité | ~700°C (1300°F) – ; Résistance limitée | ~870°C (1600°F) – ; Résistance limitée |
Imprimabilité | Modéré (sensible aux fissures) | Excellent | Difficile (sensible aux fissures liées à l'âge et à la déformation) |
Post-traitement | Traitement thermique, souvent HIP | Traitement thermique standard, HIP en option | Traitement thermique spécialisé, HIP souvent nécessaire. |
Utilisation typique de l'AM | Lames/Vanes IGT | Composants aérospatiaux, Lames LPT, Pièces IGT | Profilés à chaud pour l'aérospatiale, pièces soumises à des contraintes élevées |
Exporter vers les feuilles
Le rôle essentiel de la qualité de la poudre : La réussite de la fabrication additive d'aubes de turbine dépend non seulement du choix du bon alliage, mais aussi de la qualité de la poudre métallique utilisée comme matière première. Les principales caractéristiques des poudres ayant un impact sur l'imprimabilité et les propriétés des pièces finales sont les suivantes :
- Sphéricité : Les particules hautement sphériques assurent une bonne fluidité de la poudre et une densité uniforme du lit de poudre, ce qui permet d'obtenir une fusion constante et une porosité réduite.
- Distribution de la taille des particules (PSD) : Un DSP contrôlé est essentiel pour obtenir une densité d'empaquetage élevée et un comportement de fusion prévisible. Les particules fines peuvent affecter la fluidité et présenter des risques pour la sécurité, tandis que les particules trop grosses risquent de ne pas fondre complètement.
- Fluidité : Assure l'étalement uniforme des couches de poudre par le mécanisme de recouvrement de l'imprimante, évitant ainsi les vides et les défauts.
- La pureté : De faibles niveaux d'impuretés (comme l'oxygène, l'azote) et l'absence de contaminants sont essentiels pour prévenir les défauts et garantir les propriétés mécaniques et la résistance à la corrosion souhaitées pour la pièce finale. Les particules satellites (particules plus petites attachées à des particules plus grandes) doivent être réduites au minimum.
- Composition chimique : Il faut respecter strictement les spécifications de l'alliage pour garantir les performances.
L'engagement de Met3dp pour l'excellence des poudres : Conscient de l'importance cruciale de la qualité des poudres, Met3dp utilise des technologies de fabrication de pointe pour produire des poudres métalliques de qualité supérieure pour la fabrication additive.
- Atomisation avancée : En utilisant les systèmes de pointe VIGA (Vacuum Induction Melting Gas Atomization) et PREP (Plasma Rotating Electrode Process), Met3dp produit des poudres d'une sphéricité exceptionnelle, d'une faible teneur en satellites et d'une grande pureté. Nos conceptions uniques de buses et de flux de gaz dans l'atomisation gazeuse garantissent une morphologie optimisée des particules.
- Un contrôle de qualité rigoureux : Chaque lot de poudre est soumis à des tests rigoureux de composition chimique, de PSD, de fluidité, de densité et de morphologie afin de s'assurer qu'il répond aux spécifications exigeantes requises pour les applications critiques telles que les aubes de turbines.
- Large portefeuille : Outre l'IN738LC, l'IN718 et le Rene 41 (la disponibilité peut varier, veuillez vous renseigner), Met3dp propose une large gamme de poudres métalliques de haute performance, notamment des alliages de titane, du cobalt-chrome, des aciers inoxydables et des alliages innovants, qui répondent à divers besoins industriels. Vous pouvez explorer notre gamme de produits en poudre métallique ici.
Choisir la bonne poudre de superalliage et s'assurer de sa qualité est une étape fondamentale pour les responsables des achats et les ingénieurs qui souhaitent tirer parti de l'AM pour fabriquer des pales de turbine à haute performance. Le partenariat avec un fournisseur compétent comme Met3dp, qui possède une expertise avérée dans la production de poudres et les processus d'AM, apporte la confiance nécessaire à la fabrication de composants critiques.
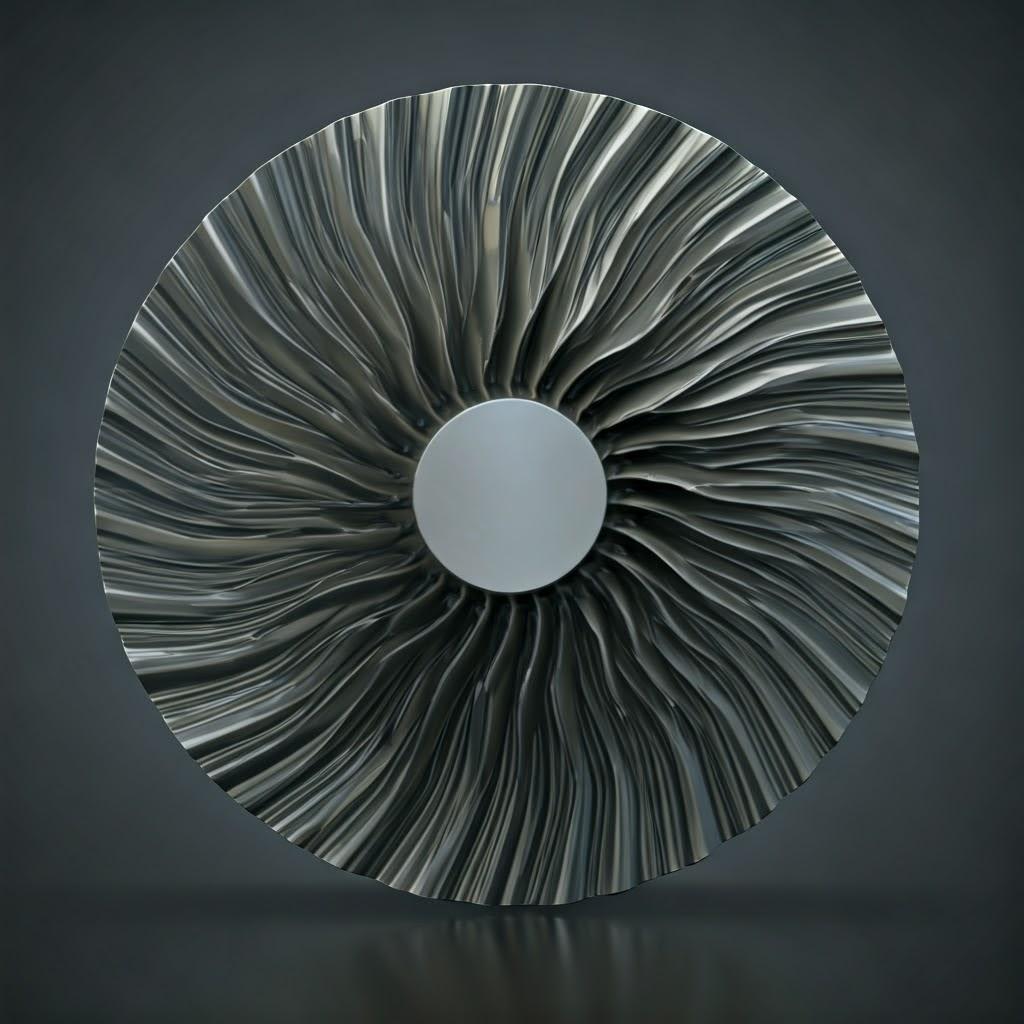
Conception pour la fabrication additive (DfAM) : Optimisation de la géométrie des aubes de turbines</h2>
La simple reproduction d'un modèle d'aube de turbine initialement prévu pour le moulage ou l'usinage à l'aide de la fabrication additive ne permet souvent pas d'exploiter le véritable potentiel de cette technologie. Pour exploiter pleinement les avantages de l'impression 3D de métaux - amélioration des performances, réduction du poids et amélioration de la fabricabilité - les ingénieurs doivent adopter la conception pour la fabrication additive (DfAM). La conception pour la fabrication additive n'est pas seulement un ensemble de règles, mais un changement d'état d'esprit qui consiste à concevoir des pièces spécifiquement pour le processus d'AM couche par couche, en tenant compte de ses capacités et contraintes uniques, en particulier lorsqu'il s'agit de superalliages à hautes performances.
Pourquoi la DfAM est cruciale pour les pales de turbines : Les aubes de turbines sont des composants très complexes dont les performances sont critiques. L'application des principes DfAM permet aux ingénieurs de :
- Maximiser les performances : La liberté géométrique permet de créer des canaux de refroidissement et des surfaces aérodynamiques optimisés au-delà des limites traditionnelles.
- Réduire le poids : Utiliser l'optimisation de la topologie et les structures internes en treillis pour minimiser la masse tout en maintenant l'intégrité structurelle, ce qui est crucial pour les composants rotatifs.
- Améliorer la réussite de l'impression : Des caractéristiques de conception qui minimisent les contraintes résiduelles, réduisent le besoin de supports difficiles à retirer et tiennent compte du retrait et de l'anisotropie des matériaux.
- Rationaliser le post-traitement : La conception tient compte des opérations de finition et garantit l'accès pour l'usinage des surfaces critiques ou l'enlèvement des supports internes.
- Accélérer l'innovation : Répéter rapidement des conceptions optimisées pour l'AM, en testant de nouveaux concepts rapidement et efficacement.
Principes clés du DfAM pour les pales de turbines AM :
- Conception avancée des canaux de refroidissement internes :
- Refroidissement Conforme : Concevoir des canaux de refroidissement qui suivent le contour complexe en 3D de la surface de la pale, ce qui permet une évacuation plus uniforme et plus efficace de la chaleur par rapport aux trous droits percés.
- Géométries complexes : Incorporer des caractéristiques telles que des bandes de déclenchement, des piédestaux et des réseaux de ramification complexes dans les canaux pour améliorer le transfert de chaleur (turbulence) avec une perte de charge minimale.
- Structures en treillis : Utiliser des structures internes en treillis ou gyroïdes dans les grandes cavités pour alléger le poids tout en fournissant un support structurel et en facilitant éventuellement la dissipation de la chaleur.
- Transitions Douces : Éviter les angles vifs dans les canaux internes, qui peuvent provoquer des concentrations de contraintes et entraver l'élimination de la poudre après l'impression. Il est préférable d'opter pour des courbes graduelles.
- Taille minimale des fonctionnalités : Il faut tenir compte des limites du processus d'AM en ce qui concerne le plus petit diamètre de canal ou la plus petite épaisseur de paroi qui peuvent être produits de manière fiable. Ces limites varient en fonction de la machine et du matériau.
- Optimisation de la topologie et allègement :
- Utiliser un logiciel spécialisé pour définir les cas de charge, les contraintes et les espaces de conception (par exemple, la plate-forme des pales, les fixations des haubans). Le logiciel élimine ensuite de manière itérative les matériaux des zones non critiques, ce qui permet d'obtenir une structure organique optimisée pour le passage des charges.
- Ceci est particulièrement efficace pour réduire le poids de la section d'emplanture de la pale ou de la plate-forme, diminuant ainsi la charge centrifuge sur le disque de la turbine.
- Combinez l'optimisation de la topologie avec des structures en treillis pour réduire davantage le poids dans les zones moins critiques.
- Stratégie de structure de soutien et conception autoportante :
- Les procédés AM nécessitent généralement des structures de support pour les éléments en surplomb (généralement inférieurs à 45 degrés par rapport à l'horizontale) afin de les ancrer à la plaque de construction ou aux couches inférieures et de dissiper la chaleur.
- Minimiser les supports : Les caractéristiques de conception doivent être autoportantes (angles plus raides, chanfreins au lieu de surplombs prononcés) dans la mesure du possible, en particulier sur les surfaces aérodynamiques critiques ou les zones internes difficiles d'accès.
- Optimiser le placement des supports : Placer les supports de manière stratégique afin de minimiser les points de contact (“marques témoins” ;) sur les surfaces fonctionnelles. Utiliser des types de supports facilement amovibles (par exemple, coniques, perforés).
- Conception pour l'accès : S'assurer qu'il existe un accès physique aux outils ou processus nécessaires pour retirer les supports, en particulier les supports internes complexes.
- Consolidation partielle :
- Étudier les possibilités de combiner le profil aérodynamique de la pale avec sa plate-forme, les éléments du carénage ou les caractéristiques d'amortissement en un seul composant imprimé.
- Les avantages sont notamment la réduction du nombre de pièces, l'élimination des processus d'assemblage (comme le soudage ou le brasage), un poids potentiellement plus faible et la suppression des interfaces susceptibles de constituer des points de défaillance.
- Nécessite un examen attentif de l'imprimabilité, de la gestion des contraintes résiduelles dans la pièce plus grande et plus complexe, et de l'accessibilité au post-traitement.
- Considérations relatives à l'orientation et à l'anisotropie :
- L'orientation dans laquelle la lame est imprimée sur la plaque de construction a un impact significatif :
- Finition de la surface : Différentes finitions sur les surfaces verticales, verticales et orientées vers le haut et vers le bas.
- Exigences en matière de support : Affecte la quantité et l'emplacement des soutiens.
- Propriétés mécaniques : En raison de la croissance colonnaire des grains typique de nombreux procédés AM, les propriétés (telles que la résistance à la fatigue ou le fluage) peuvent différer légèrement le long de la direction de construction (axe Z) par rapport à la perpendiculaire (plan X-Y).
- La DfAM consiste à sélectionner l'orientation optimale de la construction dès le début du processus de conception afin d'équilibrer la finition de la surface, les besoins de support, le temps d'impression et les effets des propriétés anisotropes pour les exigences spécifiques de l'application.
- L'orientation dans laquelle la lame est imprimée sur la plaque de construction a un impact significatif :
- Caractéristiques de gestion thermique :
- Intégrer des éléments de conception qui contribuent à atténuer l'accumulation de contraintes thermiques résiduelles pendant l'impression.
- Utilisez des transitions graduelles entre les sections épaisses et minces. Éviter les grands blocs de matériau solides où la chaleur peut se concentrer.
- Envisager des caractéristiques sacrificielles ou des stratégies de soutien optimisées spécifiquement conçues pour évacuer efficacement la chaleur.
S'engager avec un partenaire expérimenté dans la fabrication additive est inestimable pour mettre en œuvre la DfAM de manière efficace. Des entreprises comme Met3dp apportent non seulement une technologie d'impression avancée, mais aussi une expertise cruciale en matière de développement d'applications. Comprendre les nuances de l'interaction entre les choix de conception et les superalliages spécifiques (comme IN738LC, IN718, Rene 41) et les matériaux sélectionnés pour la fabrication des pièces de rechange, c'est faire preuve d'un grand sens de l'innovation et de la créativité méthodes d'impression est la clé du succès. En intégrant les principes de la DfAM dès le départ, les équipes d'ingénierie et d'approvisionnement peuvent s'assurer qu'elles tirent véritablement parti du pouvoir de transformation de l'AM pour produire les pales de turbine de la prochaine génération.
Atteindre la précision : Tolérance, état de surface et précision des aubes de turbines AM
Si la fabrication additive métallique offre une liberté de conception inégalée, il est essentiel que les ingénieurs et les responsables des achats aient des attentes réalistes quant à la précision dimensionnelle, aux tolérances et à la finition de surface réalisables directement à partir du processus d'impression, en particulier pour les composants de précision tels que les pales de turbines fabriquées à partir de superalliages. Il est essentiel de comprendre ces aspects pour définir les exigences, planifier les étapes de post-traitement et s'assurer que la pièce finale répond à des critères de performance et d'assemblage rigoureux.
Précision dimensionnelle telle que construite : La précision d'une pièce sortant de la machine d'AM dépend de plusieurs facteurs, notamment l'étalonnage de la machine, la taille du spot du faisceau laser/électronique, l'épaisseur de la couche, les propriétés du matériau (retrait, conductivité thermique), la stratégie de balayage et l'efficacité des structures de support dans la gestion des contraintes thermiques.
- Plages typiques : Pour des procédés tels que la fusion laser sur lit de poudre (L-PBF/SLM), la précision dimensionnelle typique peut aller de ±0,05 mm à ±0,2 mm (±0,002″ ; à ±0,008″ ;) pour les petites caractéristiques, et peut augmenter légèrement pour les pièces de plus grandes dimensions. La fusion par faisceau d'électrons (EBM) présente souvent des tolérances légèrement plus faibles en raison des températures de traitement plus élevées et des effets de frittage des poudres, mais elle excelle dans la réduction des contraintes résiduelles.
- Facteurs d'influence : Le gauchissement thermique pendant la construction est un défi majeur. Une orientation soignée, des structures de support robustes et des paramètres de processus optimisés sont essentiels pour minimiser les écarts par rapport à la géométrie prévue. La réduction des contraintes après l'impression et le HIP peuvent également entraîner des modifications dimensionnelles mineures et prévisibles.
Finition de surface (rugosité de surface – ; Ra) : La finition de surface des pièces obtenues par AM est intrinsèquement plus rugueuse que celle obtenue par usinage ou polissage traditionnel. Cela est dû à la nature couche par couche du processus et à la présence de particules de poudre partiellement fondues qui adhèrent à la surface.
- Valeurs Ra typiques :
- L-PBF (SLM) : Le Ra tel qu'il est construit varie généralement de 6µm à 20µm (240µin à 800µin), ce qui dépend fortement de l'orientation de la surface par rapport à la direction de construction.
- EBM : Produit généralement des surfaces plus rugueuses que le L-PBF, souvent dans la gamme Ra 20µm à 40µm (800µin à 1600µin), en raison des particules de poudre plus grosses et des températures plus élevées qui provoquent un certain frittage de la poudre.
- Dépendance à l'égard de l'orientation :
- Surfaces en contact avec la peau : Les surfaces orientées vers le haut pendant la construction ont tendance à être plus lisses.
- Surfaces de la peau du bas : Les surfaces orientées vers le bas, soutenues par des structures, sont généralement les plus rugueuses en raison des points de contact avec le support et des effets de la chaleur.
- Parois verticales : Elles présentent des lignes de couche distinctes, qui contribuent à la rugosité. Les surfaces inclinées présentent des effets de marches d'escalier.
- Impact: La rugosité des surfaces a un impact significatif sur les performances aérodynamiques (traînée) et peut être le point de départ de fissures de fatigue. Par conséquent, les surfaces critiques des profils aérodynamiques nécessitent presque toujours une finition après le processus. Les canaux de refroidissement internes ont également besoin d'une rugosité contrôlée pour un transfert de chaleur et un écoulement optimaux.
Tolérancement (GD&T – ; Geometric Dimensioning and Tolerancing) : Pour les pales de turbines, certaines caractéristiques exigent des tolérances très serrées qui dépassent souvent les capacités des processus d'AM tels qu'ils sont construits.
- Caractéristiques critiques : Il s'agit généralement des éléments suivants
- Forme de la racine (par exemple, sapin) : Doit s'adapter précisément à la fente du disque de la turbine. Les tolérances requises sont de l'ordre du micron.
- Interfaces de linceul : Le cas échéant, pour l'étanchéité et l'amortissement.
- Dégagement de l'astuce : L'espace entre la pointe de la lame et le carter est essentiel pour l'efficacité et la prévention des frottements.
- Bords avant/arrière : La précision du profil a une incidence sur l'aérodynamique et les concentrations de contraintes.
- Tolérances AM et tolérances finales : Il est essentiel de faire la distinction entre ce qui est réalisable et ce qui ne l'est pas brut de fabrication et l'utilisation de la final requis les tolérances. Les concepteurs doivent clairement indiquer quelles caractéristiques nécessitent des tolérances plus strictes qui seront obtenues par post-usinage.
- Spécification pour AM : Lors de la spécification des dessins pour les pièces AM, utilisez les repères GD&T de manière réaliste. Indiquez les tolérances d'exécution lorsqu'elles sont acceptables et définissez clairement les surfaces/caractéristiques nécessitant des opérations de finition avec leurs tolérances finales.
Inspection et contrôle qualité : Il est essentiel de vérifier la précision dimensionnelle et l'intégrité des pales de turbines AM.
- Machines à mesurer tridimensionnelles (MMT) : Utilisé pour mesurer avec précision les dimensions critiques et les caractéristiques géométriques, souvent après l'usinage.
- numérisation 3D (laser/lumière structurée) : Permet une comparaison plein champ de la pièce imprimée avec le modèle CAO d'origine, utile pour vérifier la forme générale, détecter le gauchissement et vérifier les formes complexes des profils aérodynamiques. Peut être utilisé sur des pièces finies ou en cours de fabrication.
- Scannage CT : Bien qu'il serve principalement à la détection des défauts internes (voir Post-traitement), il peut également fournir des données dimensionnelles, en particulier pour les canaux internes.
Implications pour l'approvisionnement et l'ingénierie :
- Exigences claires : Définir sans ambiguïté les dimensions critiques, les tolérances et les exigences en matière de finition de surface dans les appels d'offres et les spécifications techniques. Faire la différence entre l'état d'avancement des travaux et l'état final de finition.
- Planification du post-traitement : Reconnaître que l'obtention de tolérances serrées et de finitions lisses sur les surfaces critiques nécessitera des opérations secondaires telles que l'usinage CNC et la finition des surfaces. Il faut en tenir compte dans l'estimation des délais et des coûts.
- Capacité du fournisseur : Assurez-vous que le fournisseur de services d'AM choisi dispose non seulement de capacités d'impression précises, mais aussi de systèmes de contrôle de la qualité robustes et, idéalement, de capacités de post-traitement intégrées ou de partenariats solides pour les opérations de finition. Il est essentiel de comprendre la capacité de processus validée d'un fournisseur pour des matériaux et des caractéristiques spécifiques.
L'obtention de la précision nécessaire pour les pales de turbine AM est un processus en plusieurs étapes. Alors que l'AM fournit la géométrie complexe initiale, un post-traitement ciblé est essentiel pour répondre aux exigences rigoureuses en matière de tolérance et de finition de surface de ces composants critiques.
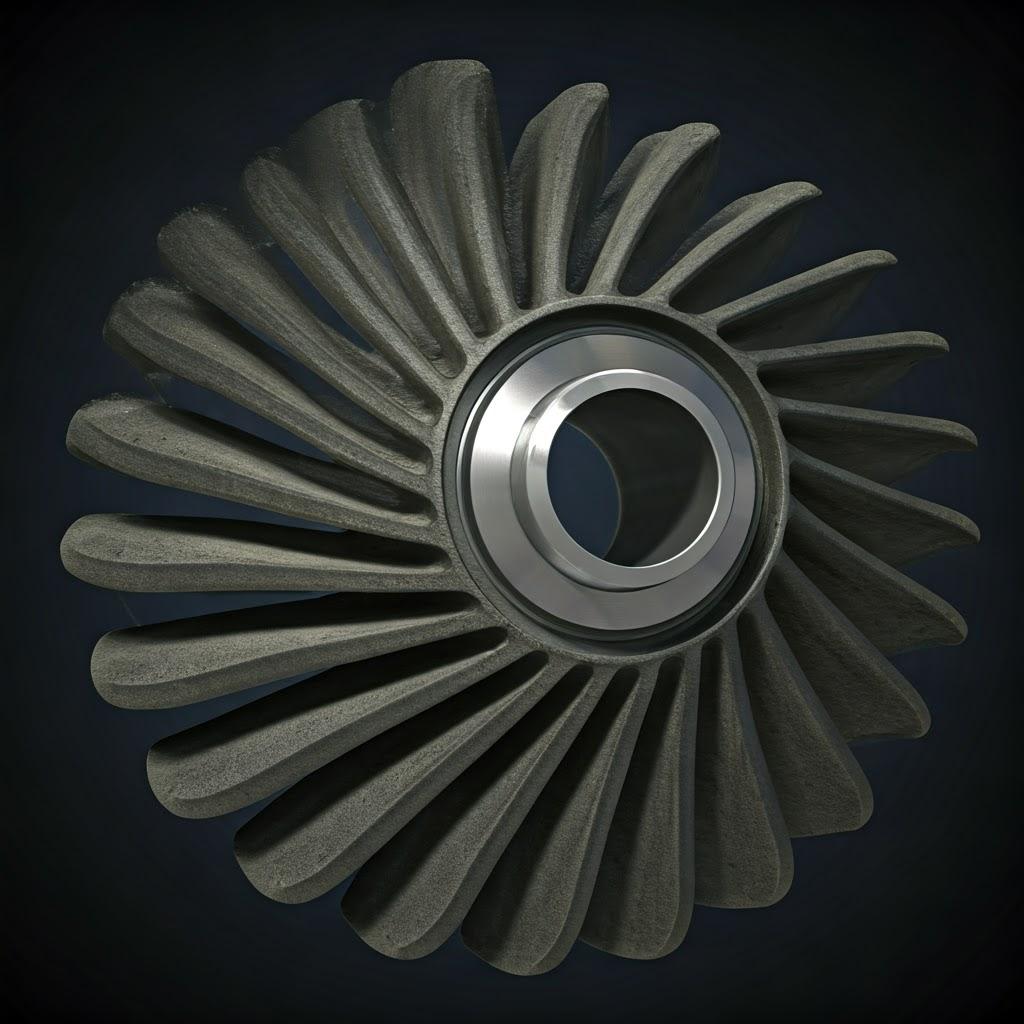
Au-delà de l'impression : Post-traitement essentiel pour les aubes de turbines en superalliage
La production d'une aube de turbine géométriquement précise à l'aide de la fabrication additive est une réalisation importante, mais le voyage de l'imprimante à un composant en état de vol ou opérationnel est loin d'être terminé, en particulier lorsqu'il s'agit de superalliages à hautes performances. Une série d'étapes critiques de post-traitement est nécessaire pour réduire les contraintes internes, affiner la microstructure, obtenir les propriétés mécaniques nécessaires, respecter les tolérances dimensionnelles, assurer l'intégrité de la surface et vérifier la qualité globale. Négliger ou mal exécuter ces étapes peut compromettre les performances de la lame et potentiellement conduire à une défaillance prématurée.
Obligatoire & ; Étapes communes de post-traitement :
- Traitement thermique anti-stress :
- Objet : Réduire les contraintes résiduelles élevées accumulées au cours des cycles de chauffage et de refroidissement rapides inhérents au processus AM. Ces contraintes peuvent entraîner des déformations lors du retrait de la plaque de construction, voire des fissures.
- Procédure : Généralement effectué pendant que la pièce est encore attachée à la plaque de construction, souvent dans un four à atmosphère inerte. La température et la durée spécifiques dépendent de l'alliage (par exemple, IN718 par rapport à IN738LC) et de la géométrie de la pièce, mais sont généralement inférieures à la température de vieillissement.
- Retrait de la pièce de la plaque de construction :
- Méthodes : Cette opération est généralement réalisée à l'aide d'un fil d'électroérosion (EDM) ou d'une scie à ruban. Il faut veiller à ne pas endommager la pièce.
- Retrait de la structure de soutien :
- Objet : Enlever les structures temporaires nécessaires à la construction.
- Méthodes : Elle peut aller de la simple rupture manuelle (pour les supports bien conçus) à l'usinage, au meulage ou à l'électroérosion pour les supports plus tenaces ou difficiles à atteindre. Les supports de canaux internes posent souvent le plus grand défi. Des techniques avancées telles que la gravure chimique ou l'usinage par flux abrasif peuvent être nécessaires pour les passages internes complexes. Le DfAM joue ici un rôle crucial.
- Recuit de mise en solution et traitement thermique de vieillissement :
- Objet : Absolument critique pour les superalliages durcissables par précipitation tels que IN718, IN738LC et Rene 41. Ces traitements dissolvent les incohérences dues à la solidification rapide pendant l'AM et précipitent ensuite avec précision les phases de renforcement (comme le gamma prime et le gamma double prime) dans la structure du grain pour obtenir la résistance à haute température, la résistance au fluage et la durée de vie en fatigue souhaitées.
- Procédure : Il s'agit d'un chauffage à une température élevée de mise en solution, suivi d'un refroidissement contrôlé, puis d'un ou plusieurs traitements de vieillissement ultérieurs à des températures intermédiaires spécifiques pendant des durées déterminées. Les cycles sont spécifiques à chaque alliage et doivent être étroitement contrôlés (uniformité de la température, taux de rampe, atmosphère). Un traitement thermique inadéquat peut gravement dégrader les propriétés mécaniques.
- Pressage isostatique à chaud (HIP) :
- Objet : Éliminer la microporosité interne (pores de gaz ou vides de fusion) inhérente au processus d'AM et améliorer l'homogénéité du matériau.
- Procédure : La pièce est soumise simultanément à une température élevée (inférieure au point de fusion, mais souvent proche de la température de mise en solution) et à un gaz inerte à haute pression (généralement de l'argon) dans une cuve HIP spécialisée. La pression fait s'effondrer les vides internes, la diffusion liant le matériau à travers les interfaces des vides.
- Avantages : Améliore considérablement la résistance à la fatigue, la ductilité et la ténacité. Augmente la densité du matériau pour se rapprocher des limites théoriques. Souvent obligatoire pour les pièces rotatives critiques dans l'aérospatiale et les applications IGT (considéré comme un processus de densification). Généralement effectué après le détensionnement mais avant les traitements de vieillissement finaux.
- Usinage :
- Objet : Pour obtenir des tolérances dimensionnelles serrées et des finitions de surface spécifiques sur des caractéristiques critiques qui ne peuvent pas être obtenues par le processus d'AM tel qu'il a été conçu.
- Domaines : Il s'agit généralement du pied de pale (sapin), des faces de contact du carénage, des surfaces d'extrémité et, parfois, des bords d'attaque et de fuite ou de sections spécifiques du profil aérodynamique.
- Considérations : La géométrie complexe de l'AM nécessite une conception minutieuse de l'outillage. L'usinage des superalliages est difficile en raison de leur résistance élevée et de leurs caractéristiques d'écrouissage.
- Finition de la surface :
- Objet : Améliorer les performances aérodynamiques en réduisant la traînée et améliorer la résistance à la fatigue en supprimant les imperfections de surface qui peuvent servir de sites d'initiation de fissures.
- Méthodes : Varie en fonction de la valeur Ra requise et de l'accessibilité :
- Finition en masse : Tambour vibrant, finition par centrifugation (à l'aide d'abrasifs).
- Usinage par flux abrasif (AFM) : Force la pâte abrasive à travers les canaux internes et sur les surfaces externes - idéal pour les géométries complexes.
- Polissage électrochimique (ECM) : Enlève le matériau par voie électrochimique, produisant une finition très lisse.
- Meulage/polissage manuel : Pour les zones spécifiques et accessibles nécessitant une grande précision.
- Application du revêtement :
- Objet : Pour protéger la pale des températures extrêmes et de l'environnement corrosif à l'intérieur de la turbine.
- Les types:
- Revêtements de Barrière Thermique (RBT) : Revêtements céramiques (souvent de la zircone stabilisée à l'yttrium – ; YSZ) appliqués sur une couche de liaison métallique. Ils isolent le superalliage de base, ce qui permet d'obtenir des températures de gaz plus élevées.
- Revêtements de protection de l'environnement (EBC) : Protéger contre l'oxydation et la corrosion.
- Procédure : Généralement appliqué par pulvérisation plasma ou par dépôt physique en phase vapeur par faisceau d'électrons (EB-PVD) après l'usinage final et la préparation de la surface.
- Essais non destructifs (END) :
- Objet : S'assurer que la pièce finale est exempte de défauts internes et externes critiques après toutes les étapes de la fabrication et de la transformation.
- Méthodes :
- Tomographie informatisée aux rayons X (CT) : Fournit une vue en 3D de la structure interne, détectant les vides, les inclusions et les fissures. Indispensable pour valider l'intégrité interne.
- Contrôle par ressuage fluorescent (FPI) : Détecte les fissures superficielles.
- Contrôle par ultrasons (UT) : Peut détecter des défauts sous la surface.
Approche intégrée : Un post-traitement efficace nécessite une vision globale, intégrant des considérations dès l'étape DfAM. Les responsables des achats doivent s'assurer que les fournisseurs potentiels d'AM disposent de procédures établies et certifiées pour ces étapes critiques, soit en interne, soit par l'intermédiaire de partenaires qualifiés. Les coûts et les délais associés au post-traitement sont importants et doivent être pris en compte dans tout plan de projet visant à produire des pales de turbine en superalliage AM fiables et de haute qualité. Un partenariat avec un fournisseur de services complets comme Met3dp, qui comprend l'ensemble du flux de travail, de la poudre à la pièce finie, peut considérablement rationaliser ce processus complexe. Pour en savoir plus sur notre approche globale, consultez notre site Web À propos de nous page.
Surmonter les obstacles : Défis communs et solutions dans l'impression de lames en superalliage
La fabrication additive d'aubes de turbine à l'aide de superalliages tels que IN738LC, IN718 et Rene 41 est une technologie puissante, mais elle n'est pas sans poser de problèmes. La combinaison de géométries complexes, de matériaux exigeants sujets à des phénomènes de haute température et du processus de fusion par couches peut entraîner des défauts ou des problèmes spécifiques s'ils ne sont pas correctement gérés. Il est essentiel de reconnaître ces obstacles potentiels et de mettre en œuvre des solutions efficaces pour produire régulièrement des composants fiables et de haute qualité.
1. Contraintes résiduelles, distorsion et gauchissement :
- Défi: Les cycles de chauffage et de refroidissement rapides et localisés pendant le L-PBF ou l'EBM créent des gradients thermiques importants à l'intérieur de la pièce et entre la pièce et la plaque de construction. Cela génère des contraintes résiduelles internes qui peuvent entraîner une déformation de la pièce, un gauchissement (en particulier des sections minces) ou même un détachement de la plaque de construction pendant l'impression.
- Solutions :
- Stratégies d'analyse optimisées : L'utilisation de techniques telles que le balayage d'îlots, le balayage de secteurs ou la variation des vecteurs de balayage entre les couches permet de répartir la chaleur de manière plus uniforme et de réduire l'accumulation de contraintes localisées.
- Structures de soutien robustes : Des supports bien conçus ancrent solidement la pièce et agissent comme des puits de chaleur, évacuant plus efficacement l'énergie thermique.
- Construire une plaque chauffante : Le préchauffage de la plaque de construction (courant en EBM, de plus en plus utilisé en L-PBF pour les alliages sensibles aux fissures) réduit le gradient thermique entre le matériau solidifié et la plaque/le lit de poudre.
- Simulation de processus : L'utilisation d'un logiciel pour prévoir les gradients thermiques et l'accumulation de contraintes permet d'optimiser l'orientation, les supports et les stratégies de numérisation avant l'impression.
- Soulagement du stress en cours de traitement : Certains systèmes avancés intègrent des méthodes de gestion du stress pendant la construction.
- Soulagement du stress après la construction : Effectuer un traitement thermique de soulagement du stress avant le retrait de la pièce de la plaque est une pratique courante.
2. Craquement :
- Défi: Certains superalliages, en particulier les superalliages durcissables par précipitation avec de larges plages de congélation ou ceux susceptibles de liquéfier les joints de grains (comme IN738LC, Rene 41, et parfois IN718 dans des conditions non optimales), sont sujets à diverses formes de fissuration, soit pendant la solidification, soit pendant les traitements thermiques ultérieurs.
- Fissuration de solidification : Se produit dans le bassin de fusion pendant la solidification en raison des contraintes thermiques qui séparent les dendrites avant que la fusion ne soit terminée.
- Fissuration de liquation : Se produit dans la zone affectée thermiquement (ZAT) adjacente au bain de fusion, où les phases à bas point de fusion aux joints de grains peuvent refondre et se fissurer sous l'effet de la contrainte.
- Fissures dues à l'âge et à la déformation : Se produit pendant le traitement thermique post-impression (vieillissement) dans certains alliages (notamment le René 41) lorsque les contraintes résiduelles provoquent un durcissement par précipitation aux joints de grains, ce qui entraîne une fragilisation et une fissuration.
- Solutions :
- Élaboration minutieuse des paramètres : Le contrôle précis de la puissance du laser/du faisceau, de la vitesse de balayage, de l'épaisseur de la couche et de l'espacement des hachures est essentiel pour gérer la taille de la piscine de fusion et la vitesse de refroidissement. Il est souvent nécessaire d'effectuer des plans d'expériences (DoE) approfondis.
- Sélection/Modification des alliages : Utilisation de variantes conçues pour une meilleure soudabilité/impression (par exemple, IN738LC par rapport à l'IN738 standard).
- Traitements thermiques optimisés : Cycles spécifiques de détente et de recuit conçus pour minimiser la susceptibilité à la fissuration lors des traitements de vieillissement ultérieurs. Le HIP peut parfois aider à guérir les microfissures.
- Matériau du substrat & ; Chauffage : Adaptation des propriétés thermiques du substrat et utilisation d'un préchauffage suffisant.
3. Porosité :
- Défi: De petits vides dans le matériau imprimé peuvent agir comme des concentrateurs de contraintes, réduisant de manière significative la durée de vie en fatigue et les propriétés mécaniques. La porosité peut être due à
- Porosité du gaz : Gaz piégés (par exemple, gaz de protection à l'argon, gaz dissous dans la poudre) formant des bulles dans la piscine de fusion qui se figent sur place.
- Porosité de manque de fusion : Apport d'énergie insuffisant ou mauvaise densité de la couche de poudre entraînant une fusion incomplète entre les couches ou les pistes de balayage adjacentes.
- Solutions :
- Poudre de haute qualité : Il est fondamental d'utiliser des poudres ayant une sphéricité élevée, une bonne fluidité, un PSD contrôlé et une faible teneur en gaz interne (comme celles produites par l'atomisation avancée de Met3dp). Une manipulation et un stockage corrects de la poudre sont également essentiels.
- Paramètres de processus optimisés : Assurer une densité d'énergie suffisante (puissance/vitesse* espacement des hachures) pour faire fondre complètement le matériau sans vaporisation excessive ou keyholing (qui peut piéger le gaz).
- Atmosphère contrôlée : Maintenir une atmosphère de gaz inerte pur dans la chambre de construction afin de minimiser la contamination et le captage de gaz.
- Pressage isostatique à chaud (HIP) : Très efficace pour fermer les pores de gaz et les pores d'absence de fusion, ce qui permet d'obtenir des pièces presque entièrement denses. Souvent considéré comme obligatoire pour les pales de turbine soumises à des contraintes de fatigue.
4. Soutien Suppression Difficulté :
- Défi: Le retrait des structures de support, en particulier les structures denses ou complexes situées dans les canaux de refroidissement internes ou sur des éléments délicats, peut prendre du temps, coûter cher et risquer d'endommager la pièce.
- Solutions :
- Focus DfAM : Concevoir pour l'autoportance, optimiser l'orientation, utiliser des types de support facilement amovibles (faible densité, pointes coniques) et assurer l'accès aux outils d'enlèvement.
- Techniques avancées de suppression : Utilisation de l'électroérosion à fil, de l'usinage électrochimique, de l'usinage par flux abrasif ou de la gravure chimique pour les zones difficiles d'accès.
- Optimisation des paramètres du processus : Réglage fin des paramètres de soutien pour faciliter le détachement sans compromettre la stabilité de la construction.
5. Anisotropie et contrôle de la microstructure :
- Défi: La solidification directionnelle inhérente à l'AM entraîne souvent une croissance du grain en colonne alignée sur la direction de construction (axe Z). Il en résulte des propriétés mécaniques anisotropes (résistance/ductilité différentes dans les directions Z et X/Y). Il peut être difficile de contrôler la structure des grains (par exemple, obtenir des grains équiaxes pour de meilleures propriétés isotropes).
- Solutions :
- Comprendre le comportement des matériaux : Caractérisation des propriétés anisotropes et conception en conséquence (par exemple, orientation de la lame de manière à ce que les contraintes critiques s'alignent sur la direction du grain le plus fort).
- Modifications du processus : Des techniques telles que l'oscillation du faisceau, les faisceaux pulsés ou des stratégies de balayage variables peuvent parfois influencer la structure du grain. L'EBM tend à produire une texture moins prononcée que le L-PBF en raison des températures de masse plus élevées.
- Post-traitement : Le HIP et les traitements thermiques spécifiques peuvent contribuer à homogénéiser la microstructure dans une certaine mesure, mais une anisotropie significative peut subsister.
Pour relever ces défis avec succès, il faut une expertise approfondie en science des matériaux, en physique des procédés, en DfAM et un contrôle rigoureux des procédés. La collaboration avec un fournisseur de services d'AM expérimenté comme Met3dp, équipé de machines fiables, de matériaux de haute qualité et d'une équipe qui comprend les subtilités de l'impression de superalliages pour des applications exigeantes comme les pales de turbines, est essentielle pour atténuer les risques et obtenir des résultats reproductibles et de haute qualité.
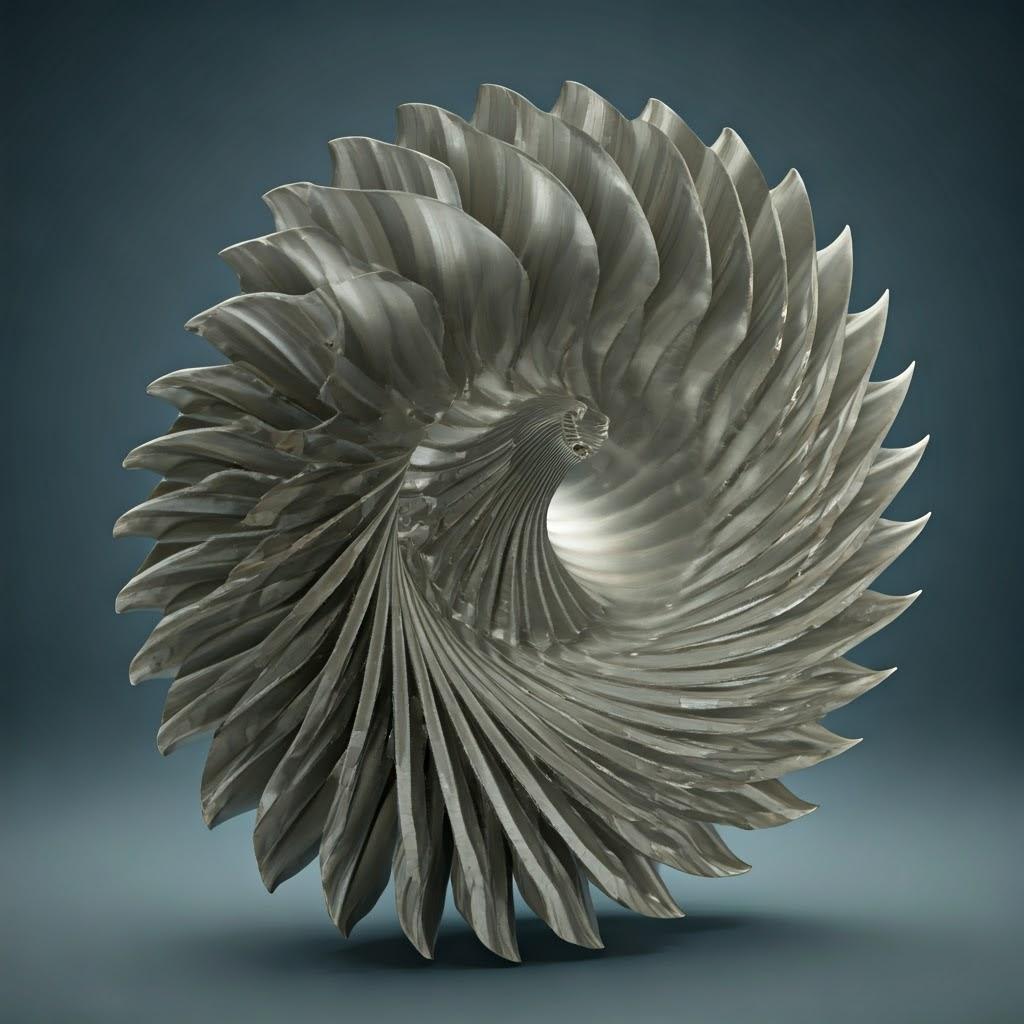
Sélectionnez votre partenaire : Choisir un fournisseur fiable pour l'impression 3D de pales de turbines en métal
Le choix du prestataire de services de fabrication additive avec lequel s'associer est particulièrement critique lorsqu'il s'agit de produire des composants soumis à de fortes contraintes et à des températures élevées, comme les aubes de turbine, à partir de superalliages. Tous les fournisseurs ne possèdent pas l'expertise, l'équipement et le contrôle rigoureux des processus nécessaires à ces applications exigeantes. Le choix du bon partenaire est primordial pour garantir la qualité des pièces, leur fiabilité et le respect des normes industrielles rigoureuses - une considération essentielle pour les achats interentreprises dans l'aérospatiale, la production d'énergie et d'autres secteurs critiques.
Lors de l'évaluation des fournisseurs potentiels d'AM des métaux pour les projets d'aubes de turbines, il convient de prendre en compte les critères essentiels suivants :
- Expertise approfondie des matériaux :
- Le fournisseur a-t-il une expérience démontrable de l'impression du superalliage spécifique requis (par exemple, IN738LC, IN718, Rene 41) ? Il doit notamment posséder des paramètres de processus validés et optimisés.
- Comprennent-ils les défis uniques associés à ces matériaux (par exemple, la susceptibilité à la fissuration, la réaction au traitement thermique) ?
- Quelles sont les procédures de manipulation, de stockage, d'essai et de traçabilité des poudres pour garantir l'intégrité des matériaux ?
- Technologie et équipement appropriés :
- Utilisent-ils le bon type de technologie d'AM (L-PBF, EBM) en fonction du matériau et de l'application ?
- Leur équipement est-il bien entretenu, calibré et capable de produire des pièces de la taille et de la complexité requises ?
- Disposent-ils d'une capacité de production suffisante pour répondre aux exigences potentielles en matière de volume de production et de délais d'exécution ? Une bonne compréhension des différentes méthodes d'impression et leurs compromis est bénéfique.
- Système de gestion de la qualité (SGQ) robuste & ; Certifications :
- Le fournisseur est-il certifié selon les normes de qualité en vigueur ? La norme ISO 9001 est une référence ; la norme AS9100 est souvent exigée pour les composants aérospatiaux.
- Disposent-ils de procédures documentées pour le contrôle des processus, l'inspection des pièces, la traçabilité (du lot de poudre à la pièce finale) et le traitement des non-conformités ?
- Peuvent-ils fournir la documentation nécessaire, comme les certificats de conformité et les rapports d'essai des matériaux ?
- Capacités complètes de post-traitement :
- Les aubes de turbines nécessitent un post-traitement important. Le fournisseur offre-t-il ces services en interne (de préférence pour des raisons de contrôle et de délai) ou par l'intermédiaire d'un réseau de partenaires qualifiés et étroitement gérés ?
- Cela comprend la réduction des contraintes, le traitement thermique (avec un contrôle précis de l'atmosphère et de la température), le HIP, l'usinage CNC de haute précision, la finition de surface, le CND (scanographie, FPI) et la préparation du revêtement.
- Ingénierie et soutien du DfAM :
- Le fournisseur dispose-t-il d'ingénieurs d'application capables de collaborer à l'optimisation de la conception (DfAM) afin de maximiser l'imprimabilité, les performances et la rentabilité ?
- Peuvent-ils fournir des conseils sur les stratégies de soutien, l'orientation et les limites de la conception des caractéristiques ?
- Antécédents avérés et expérience du secteur :
- Le fournisseur peut-il fournir des études de cas ou des exemples de projets menés à bien avec des matériaux, des complexités et des exigences industrielles similaires ?
- Ont-ils de l'expérience dans le domaine de l'aérospatiale, de la production d'énergie ou des marchés industriels concernés ?
- Capacité, évolutivité et gestion de projet :
- Peuvent-ils gérer le volume requis, depuis les prototypes initiaux jusqu'à la production potentielle de petites et moyennes séries ?
- Disposent-ils de processus de gestion de projet efficaces pour garantir le respect des délais et une communication claire ?
- Confidentialité et protection de la propriété intellectuelle (PI) :
- Quelles sont les mesures mises en place pour protéger les données de conception sensibles et la propriété intellectuelle des clients ? Garantir des accords de confidentialité solides et des pratiques de traitement des données sûres.
Le choix d'un fournisseur ne se résume pas au prix ; il s'agit de trouver un véritable partenaire disposant de la profondeur technique et de l'attention portée à la qualité requises pour les composants critiques. Des entreprises telles que Met3dp, qui proposent des solutions intégrées verticalement comprenant des équipements AM avancés, des poudres métalliques de haute qualité spécialement conçues pour l’AM et des services de développement d’applications experts, sont positionnées pour être de tels partenaires. Notre engagement en faveur de la qualité et notre compréhension de l'ensemble du processus de fabrication additive offrent la fiabilité que les clients industriels B2B exigent.
Comprendre l'investissement : Facteurs de coût et délais de livraison pour les commandes d'aubes de turbines industrielles
La fabrication additive offre des avantages significatifs pour la production d'aubes de turbines, mais il est essentiel de comprendre les coûts et les délais associés pour une planification et un approvisionnement efficaces du projet. Contrairement à la fabrication traditionnelle en grande série, où l'amortissement de l'outillage influe fortement sur le prix des pièces, les coûts de la fabrication additive sont déterminés par un ensemble différent de facteurs, et les délais d'exécution dépendent fortement de l'ensemble de la chaîne de processus, et pas seulement de la durée de l'impression.
Principaux facteurs de coût des aubes de turbine en superalliage AM :
- Coût des matériaux :
- Les superalliages à base de nickel (IN738LC, IN718, Rene 41) sont des matières premières intrinsèquement coûteuses. Le coût par kilogramme d'une poudre de haute qualité atomisée au gaz et adaptée à l'AM est considérable.
- Si l'AM minimise les déchets par rapport aux méthodes soustractives, le volume de matériau dans la pièce finale et les structures de soutien nécessaires ont un impact direct sur le coût.
- Les pratiques de réutilisation/recyclage des poudres du fournisseur influencent également le coût effectif des matériaux.
- Le temps des machines :
- Il s'agit souvent de l'élément de coût le plus important. Il est principalement déterminé par :
- Volume de la pièce : La taille globale (boîte de délimitation) de la pièce détermine l'espace qu'elle occupe dans la chambre de construction.
- Hauteur de la pièce : Détermine le nombre de couches nécessaires, ce qui a un impact direct sur la durée de l'impression.
- Complexité & ; Densité : Les structures internes très complexes ou les sections denses et solides nécessitent plus de temps de balayage par couche.
- L'amortissement de la machine, l'entretien, la consommation d'énergie et l'utilisation de gaz inerte sont pris en compte dans le taux horaire de la machine.
- Il s'agit souvent de l'élément de coût le plus important. Il est principalement déterminé par :
- Travail :
- Une main-d'œuvre qualifiée est nécessaire pour l'installation de la machine, la préparation de la fabrication (chargement de la poudre, découpage des données), le contrôle de la fabrication, le retrait des pièces, le retrait du support et les nombreuses opérations de post-traitement.
- Coûts de post-traitement :
- Ces étapes augmentent considérablement le coût total et ne peuvent être négligées :
- Traitements thermiques (réduction des contraintes, solutions, vieillissement) : Temps de cuisson, énergie, atmosphères contrôlées.
- Pressage isostatique à chaud (HIP) : Un procédé par lots spécialisé, souvent coûteux, nécessaire à la densification et à l'amélioration des propriétés.
- Suppression du support : Peut nécessiter beaucoup de travail, en particulier pour les supports internes complexes.
- Usinage CNC : Nécessaire pour les tolérances critiques ; l'usinage des superalliages est lent et nécessite beaucoup d'outillage.
- Finition de la surface : Les coûts varient considérablement en fonction de la méthode (par exemple, AFM, polissage) et de la valeur Ra requise.
- CND et inspection : Coûts liés à la tomodensitométrie, au FPI, au CMM, etc.
- Ces étapes augmentent considérablement le coût total et ne peuvent être négligées :
- Assurance qualité & ; Documentation :
- Les frais généraux liés au maintien d'un système de gestion de la qualité solide, à la réalisation d'inspections, d'essais de matériaux (coupons témoins) et à la production de documents de certification contribuent à ce coût.
- Volume de commande :
- Bien que l’AM n’ait pas l’amortissement des coûts d’outillage de la fonderie, il existe des économies d’échelle. Des volumes plus importants permettent une meilleure imbrication des pièces au sein d'une fabrication, ce qui peut réduire le temps machine par pièce et amortir le travail de préparation sur un plus grand nombre d'unités. Les fournisseurs peuvent offrir des remises sur les commandes en gros. Toutefois, la courbe des coûts de l'AM a tendance à être plus plate que celle des méthodes traditionnelles de production de masse.
Considérations relatives aux délais de livraison :
Le délai de fabrication d'une aube de turbine AM finie est la somme de plusieurs étapes :
- Devis et Traitement des Commandes : Le délai peut varier de quelques jours à quelques semaines en fonction de la complexité et de la charge de travail du fournisseur.
- Préparation de la construction : Préparation des données, programmation des machines, mise en place (heures à jours).
- Temps d'impression : Très variable en fonction de la taille/complexité ; peut aller de quelques heures pour les petits prototypes à plusieurs jours pour les grandes lames complexes ou les plaques de construction complètes.
- Cool Down & ; Démontage de la pièce : Heures.
- Post-traitement :C'est souvent ce qui détermine le délai d'exécution global.
- Soulagement du stress/traitements thermiques : Jours (y compris les cycles du four).
- HIP : il est souvent nécessaire de regrouper les pièces et de les expédier à un établissement spécialisé, ce qui peut prendre de 1 à 3 semaines.
- Usinage/finition : de quelques jours à quelques semaines en fonction de la complexité et de la charge de l'atelier.
- Contrôle non destructif (CND) et inspection : Jours.
- Expédition: Variable en fonction du lieu et de la méthode.
Délais typiques (estimations très variables) :
- Prototypes (post-traitement de base) : 1-4 semaines
- Pièces de production entièrement traitées (y compris HIP, traitement thermique complet, usinage, CND) : 6 à 12 semaines, voire plus, en fonction de la complexité et de la programmation des processus externes (comme HIP).
Pour les marchés publics : Il est essentiel de demander des devis détaillés qui ventilent les coûts entre l'impression et les différentes étapes de post-traitement. De même, il faut demander des estimations réalistes des délais d'exécution, qui tiennent compte de l'ensemble des étapes de l'impression entière il s'agit d'une question de flux de travail, et pas seulement de temps d'impression. Une communication claire et une planification en amont avec le fournisseur sont essentielles.
Foire aux questions (FAQ) sur l'impression 3D d'aubes de turbines
Alors que la fabrication additive métallique est de plus en plus adoptée pour des composants critiques tels que les pales de turbines, les ingénieurs et les responsables des achats se posent souvent des questions sur ses capacités, ses limites et sa comparaison avec les méthodes traditionnelles. Voici les réponses aux questions les plus fréquentes :
Q1 : Comment les propriétés mécaniques des lames en superalliage imprimées en 3D se comparent-elles à celles des lames coulées ou corroyées ? A : En utilisant des poudres de haute qualité (comme IN738LC, IN718, Rene 41) et des procédés optimisés et certifiés comprenant des traitements thermiques appropriés et le pressage isostatique à chaud (HIP), les propriétés mécaniques (résistance à la traction, limite d'élasticité, allongement, résistance au fluage, durée de vie en fatigue) des pièces en superalliage AM peuvent être très comparables, et parfois même supérieures aux équivalents coulés à la cire perdue. Le HIP est essentiel pour fermer la porosité interne, ce qui améliore considérablement les propriétés de résistance à la fatigue. La microstructure à grain fin souvent obtenue par AM peut offrir des avantages en termes de résistance. Toutefois, les propriétés peuvent présenter une certaine anisotropie (directionnalité) liée à la direction de fabrication, qui doit être prise en compte dans la conception et la qualification. Il est plus difficile d'obtenir des propriétés équivalentes à celles des matériaux corroyés, car les alliages corroyés bénéficient d'un traitement thermomécanique important, mais les pièces obtenues par AM répondent souvent, voire dépassent, les exigences auxquelles répondaient auparavant les pièces moulées. Des essais rigoureux et une qualification conforme aux normes industrielles (par exemple, AMS, directives MMPDS) sont essentiels.
Q2 : Le coût de l'impression 3D métallique est-il compétitif par rapport à celui du moulage à la cire perdue pour les pales de turbines ? A : La compétitivité des coûts dépend fortement de plusieurs facteurs :
- Volume : Pour les très gros volumes de production (des milliers de pièces identiques), le moulage à la cire perdue reste souvent plus économique en raison des coûts d'outillage bien amortis et des temps de cycle plus courts par pièce.
- La complexité : Pour les lames dotées de canaux de refroidissement internes très complexes ou de caractéristiques difficiles/impossibles à mouler, l'AM peut s'avérer plus rentable, même à faible volume, en permettant des conceptions qui améliorent considérablement les performances ou éliminent les étapes d'assemblage.
- Délai de mise en œuvre: L'AM permet de réduire considérablement les délais de production des pièces initiales (pas d'outillage nécessaire), ce qui la rend idéale pour le prototypage, l'itération rapide et les besoins urgents en matière d'entretien et de réparation. Cette rapidité peut apporter une valeur économique significative.
- Pièces de l'héritage : Pour les systèmes plus anciens pour lesquels il n'existe plus d'outillage de fonderie, l'AM est souvent la seule option viable pour la production de pièces de rechange.
- Coût total de possession : Prenez en compte l'ensemble du cycle de vie. Si l'AM permet de concevoir une lame plus légère, plus efficace ou plus durable, le prix initial plus élevé de la pièce peut être compensé par des économies opérationnelles. En résumé : L'AM excelle dans la compétitivité des coûts pour les volumes faibles à moyens, la grande complexité, le développement rapide et les pièces de rechange à la demande.
Q3 : Quelle est la limite de taille typique pour l'impression des pales de turbine ? A : La taille maximale imprimable est dictée par le volume de construction de la machine d'AM spécifique utilisée. Les machines L-PBF et EBM actuelles, à la pointe de la technologie, ont des enveloppes de construction qui peuvent accueillir une large gamme d'aubes de turbine, y compris la plupart des aubes que l'on trouve dans les moteurs aéronautiques et dans de nombreuses turbines à gaz industrielles (IGT). Les volumes de construction peuvent aller de 250x250x300 mm à 800x400x500 mm, voire plus dans certains systèmes spécialisés. Si la plupart des pales entrent dans ces limites, les pales les plus grandes des plus grandes turbines à gaz industrielles peuvent encore dépasser les capacités actuelles d'impression unique et nécessiter une fabrication traditionnelle, voire une impression en sections et un assemblage. Vérifiez toujours les capacités spécifiques des machines du fournisseur que vous avez choisi.
Q4 : Comment se déroule la certification des matériaux pour les pales de turbine AM ? A : La certification des matériaux pour les pièces AM critiques est un processus rigoureux qui implique :
- Contrôle des poudres : Contrôle strict et traçabilité des lots de poudres, y compris la vérification de la chimie, l'analyse PSD et les contrôles morphologiques. Les stratégies de réutilisation doivent être validées.
- Contrôle des processus : Verrouiller les paramètres validés du processus (puissance du laser, vitesse, etc.) et assurer l'étalonnage de la machine et le contrôle de l'environnement.
- Coupons témoins : Impression de spécimens d'essai normalisés (barres de traction, échantillons de fluage/fatigue) en même temps que les pièces réelles dans le même travail de construction.
- Essais mécaniques : Essais approfondis de ces coupons (après un post-traitement identique à celui des pièces) pour vérifier que les propriétés mécaniques sont conformes aux spécifications requises pour les matériaux (par exemple, les normes AMS).
- CND et inspection : Effectuer les contrôles non destructifs requis (par exemple, tomodensitométrie) et le contrôle dimensionnel des pièces finales.
- Documentation : Fournir un certificat de conformité (CoC) complet comprenant les informations sur les lots de poudre, les détails du traitement (confirmation du respect du processus qualifié), les enregistrements de traitement thermique/HIP, les résultats des essais non destructifs (END) et les rapports d'essais mécaniques des coupons témoins.
Q5 : Quelle est la durée de vie ou la durabilité attendue d'une pale de turbine imprimée en 3D ? A : L'objectif de l'utilisation de l'AM pour les pales de turbine est de produire des pièces dont la durée de vie et la durabilité sont supérieures à celles des pales de turbine atteindre ou dépasser celles de leurs homologues fabriquées traditionnellement et conçues pour les mêmes conditions d'exploitation. Lorsqu'elles sont produites à l'aide de matériaux qualifiés, de processus validés, d'un post-traitement complet (en particulier le traitement HIP et les traitements thermiques corrects) et d'un contrôle de qualité rigoureux, les aubes de turbine AM sont conçues pour atteindre la durée de vie requise et sont censées y parvenir. La capacité à créer des canaux de refroidissement optimisés et des caractéristiques microstructurales potentiellement supérieures peut même, dans certains cas, conduire à une durabilité ou à des performances accrues. Toutefois, comme pour tout composant critique, des essais et une certification approfondis du moteur sont nécessaires pour valider la durée de vie dans l'environnement d'application spécifique avant le déploiement à grande échelle.
Conclusion : L'avenir des chaînes d'approvisionnement en aubes de turbines grâce à l'impression 3D de métaux
La fabrication d'aubes de turbine est un témoignage de la précision de l'ingénierie, opérant à la dure confluence de températures extrêmes, de contraintes élevées et d'exigences de performance élevées. Alors que les méthodes traditionnelles telles que le moulage et le forgeage ont longtemps été la norme, la fabrication additive métallique, alimentée par des superalliages avancés tels que IN738LC, IN718 et Rene 41, représente un changement profond, offrant des capacités jusqu'alors inaccessibles.
Comme nous l’avons exploré, l’impression 3D de métaux permet d’obtenir des résultats inégalés liberté de conceptionil permet de créer des géométries complexes de refroidissement interne et des structures topologiquement optimisées qui augmentent l'efficacité et les performances des turbines. Il permet de créer des géométries réduit les délais d'exécution pour les prototypes et les pièces de production, ce qui accélère les cycles d'innovation et permet de mettre en place des stratégies de maintenance et de réparation réactives. En outre, l'AM offre un potentiel important pour une meilleure utilisation des matériaux et la création de des chaînes d'approvisionnement souples et flexibles grâce à l'inventaire numérique et à la production à la demande.
Toutefois, pour tirer parti de ces avantages, il faut savoir naviguer dans les méandres de la technologie. Le succès dépend d'une Conception pour la fabrication additive (DfAM), prudent sélection des matériaux couplé à poudre de haute qualitédes processus d'impression contrôlés avec précision, et étapes critiques du post-traitement le traitement thermique, le HIP et l'usinage permettent d'obtenir les propriétés et les tolérances requises. Relever des défis tels que les contraintes résiduelles, les fissures potentielles et garantir la précision dimensionnelle exige une expertise approfondie et un contrôle de qualité rigoureux.
Pour les ingénieurs et les responsables des achats des secteurs de l'aérospatiale, de la production d'énergie et des industries connexes, l'adoption de l'AM des métaux pour la production d'aubes de turbines devient une nécessité stratégique. Cela nécessite une planification minutieuse, une spécification claire des exigences et, surtout, la sélection du bon partenaire de fabrication.
Met3dp est prêt à être ce partenaire. Avec nos racines dans la fourniture de solutions de fabrication additive à la pointe de l'industrie, englobant à la fois des systèmes d'impression 3D avancés et la production de poudres métalliques sphériques de haute performance via des techniques d'atomisation de pointe, nous offrons une approche complète. Notre expertise couvre l'ensemble du flux de travail de la fabrication additive, garantissant la qualité et la fiabilité de la charge de poudre jusqu'à la vérification des composants finis. Nous collaborons avec des organisations pour mettre en œuvre l'impression 3D de manière efficace, en les aidant à transformer leurs capacités de fabrication et à accélérer leur parcours vers la production numérique.
L'intégration de la fabrication additive métallique dans la production de composants critiques tels que les pales de turbines n'est pas seulement une tendance, c'est l'avenir qui se dessine. Elle promet des turbines plus efficaces et plus performantes, ainsi que des chaînes d'approvisionnement plus réactives et plus robustes. En s'associant à des fournisseurs compétents et qualifiés tels que Met3dpgrâce à la fabrication additive, les entreprises peuvent en toute confiance tirer parti de cette technologie transformatrice pour acquérir un avantage concurrentiel et alimenter la prochaine génération d'innovations dans les domaines de l'aviation et de l'énergie. Contactez Met3dp dès aujourd'hui pour découvrir comment nos capacités peuvent alimenter les ambitions de votre organisation en matière de fabrication additive.
Partager sur
MET3DP Technology Co. est un fournisseur de premier plan de solutions de fabrication additive dont le siège se trouve à Qingdao, en Chine. Notre société est spécialisée dans les équipements d'impression 3D et les poudres métalliques de haute performance pour les applications industrielles.
Articles connexes
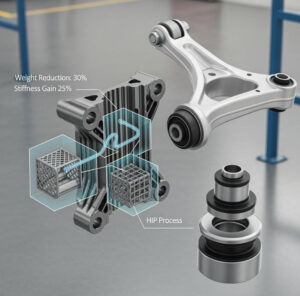
Metal 3D Printed Subframe Connection Mounts and Blocks for EV and Motorsport Chassis
Lire la suite "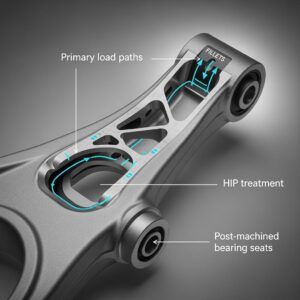
Metal 3D Printing for U.S. Automotive Lightweight Structural Brackets and Suspension Components
Lire la suite "À propos de Met3DP
Mise à jour récente
Notre produit
CONTACTEZ-NOUS
Vous avez des questions ? Envoyez-nous un message dès maintenant ! Nous répondrons à votre demande avec toute une équipe dès réception de votre message.
Obtenir les informations de Metal3DP
Brochure du produit
Obtenir les derniers produits et la liste des prix