High-Temp Turbine Combustion Liners: Revolutionizing Performance with Metal 3D Printing
Table des matières
Introduction – The Critical Role of Combustion Liners in High-Temperature Applications
In the demanding world of aerospace, power generation, and advanced industrial machinery, the turbine combustion liner stands as a critical component. It forms the heart of the combustion chamber, where fuel and air are mixed and ignited under immense pressure and extreme temperatures. The efficiency and longevity of these systems hinge significantly on the performance and durability of the combustion liner. Traditionally manufactured through casting and machining of high-temperature alloys, these liners often face limitations in design complexity and material optimization. However, the advent of metal 3D printing, also known as metal additive manufacturing, is ushering in a new era of possibilities for creating high-performance turbine combustion liners with intricate geometries and tailored material properties. This blog post delves into the transformative potential of metal Impression 3D for manufacturing high-temperature turbine combustion liners, exploring its advantages, material considerations, design aspects, and the crucial factors for selecting a reliable service provider like Métal3DP.
What is a Turbine Combustion Liner Used For? – Industries and Key Functions
The turbine combustion liner is the central component within a gas turbine’s combustion system. Its primary function is to contain and manage the high-energy combustion process that generates the hot gas stream to drive the turbine blades. Understanding its applications across various industries highlights its significance:
- Aérospatiale : In jet engines, combustion liners are crucial for the propulsion system. They must withstand rapid temperature fluctuations and extreme heat while maintaining structural integrity. Advanced designs contribute to improved fuel efficiency and reduced emissions.
- Production d'électricité : Gas turbines are widely used in power plants to generate electricity. The combustion liners in these turbines operate continuously under high temperatures and pressures, demanding exceptional durability and thermal resistance for reliable and efficient power output.
- Fabrication industrielle : Various industrial processes utilize gas turbines for power and heat generation. Combustion liners in these applications need to be robust and reliable to ensure uninterrupted operation and process efficiency.
- Applications émergentes : As technology advances, turbine-based systems are finding new applications, such as in advanced propulsion systems and distributed power generation, further emphasizing the importance of high-performance combustion liners.
The key functions of a turbine combustion liner include:
- Containing Combustion: Providing a controlled volume for the combustion of fuel and air.
- Directing Gas Flow: Ensuring a uniform and high-velocity flow of hot gases towards the turbine stages.
- Managing Temperature: Withstanding and dissipating the intense heat generated during combustion, often through sophisticated cooling mechanisms integrated into the liner design.
- Ensuring Durability: Maintaining structural integrity under extreme thermal and mechanical stresses for extended operational life.
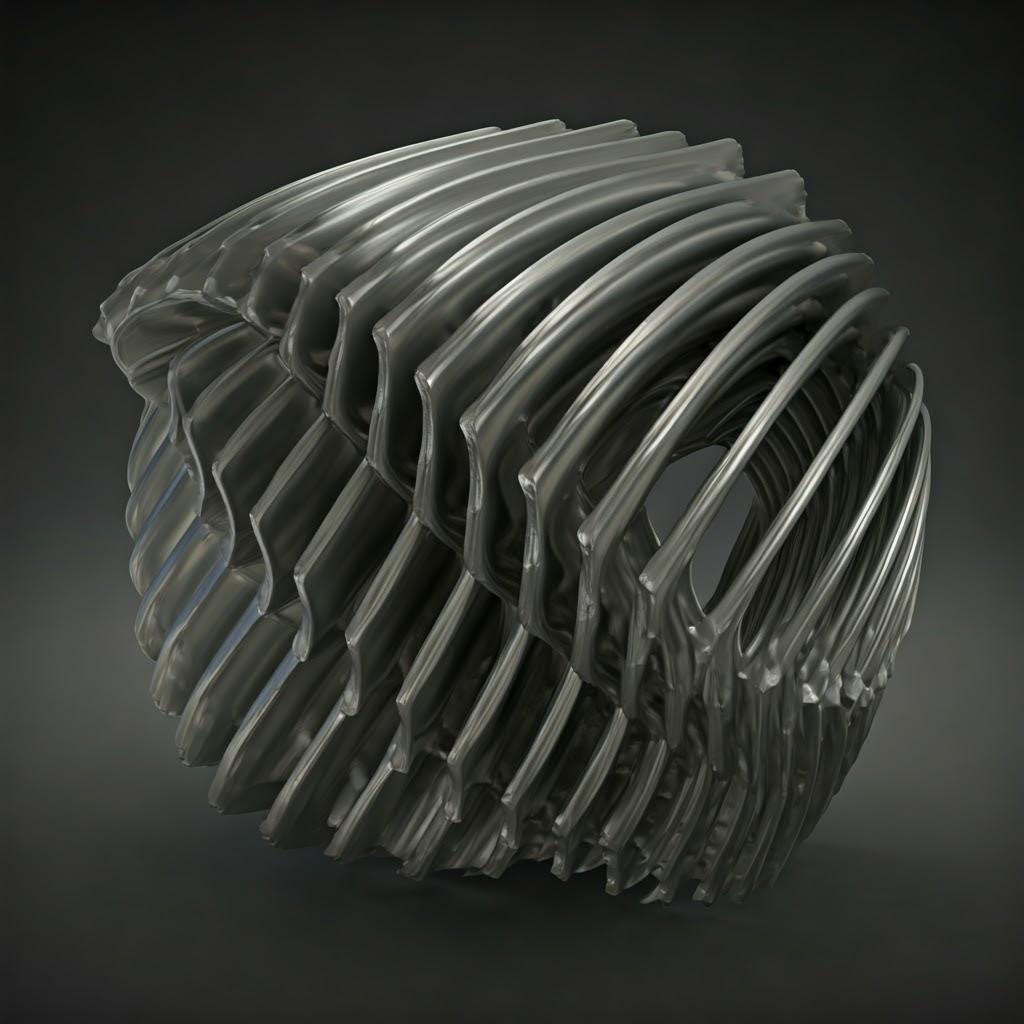
Why Use Metal 3D Printing for Turbine Combustion Liners? – Advantages Over Traditional Methods
Opting for metal 3D printing to manufacture turbine combustion liners offers a compelling array of advantages over traditional manufacturing methods like casting and machining:
- Liberté de conception et complexité : Additive manufacturing allows for the creation of intricate geometries that are virtually impossible or cost-prohibitive to achieve with traditional methods. This includes:
- Optimized Cooling Channels: Complex internal cooling channels can be designed and built directly into the liner, improving heat dissipation and extending component life. This can lead to enhanced engine efficiency and reduced fuel consumption.
- Allègement : Lattice structures and topology optimization can be employed to reduce the weight of the liner without compromising structural integrity, which is particularly crucial in aerospace applications.
- Caractéristiques intégrées : Features like mounting brackets, stiffening ribs, and sensor housings can be integrated directly into the design, reducing the need for secondary assembly processes.
- Material Optimization and Performance Enhancement: Metal 3D printing enables the use of advanced high-temperature alloys, such as IN718 and Haynes 282, in powder form, allowing for tailored microstructures and improved material properties. Métal3DP offers a range of high-quality metal powders optimized for laser and electron beam powder bed fusion, ensuring dense, high-performance parts. Their advanced powder making system, utilizing gas atomization and PREP technologies, produces spherical powders with high sphericity and good flowability, critical for consistent 3D printing.
- Reduced Lead Times and Costs: For complex geometries and low to medium production volumes, metal 3D printing can significantly reduce lead times compared to the tooling and setup required for casting or extensive machining. This agility can be particularly beneficial for rapid prototyping, design iterations, and the production of customized or legacy parts.
- Efficacité matérielle : Additive manufacturing processes typically generate less material waste compared to subtractive methods, as material is only deposited where needed. This can lead to significant cost savings, especially when working with expensive high-performance alloys.
- Customization and Small Batch Production: Metal 3D printing is ideal for producing customized combustion liners for specific turbine designs or for small batch production runs, without the high upfront costs associated with traditional tooling. This is particularly valuable for specialized applications or for the development of new turbine technologies.
Recommended Materials and Why They Matter – High-Performance Metal Powders
The extreme operating conditions within a turbine combustion chamber necessitate the use of high-performance materials capable of withstanding high temperatures, significant thermal cycling, and corrosive environments. Metal 3D printing offers the flexibility to process advanced alloys tailored for these demands. Two key recommended powders for high-temperature turbine combustion liners are IN718 and Haynes 282:
IN718 (Inconel 718)
IN718 is a nickel-chromium-based superalloy renowned for its excellent high-temperature strength, creep and rupture resistance, and corrosion resistance up to around 700°C (1290°F). Its key properties make it a workhorse material for demanding applications:
- Haute résistance à des températures élevées : IN718 maintains significant tensile and yield strength even at high operating temperatures, crucial for withstanding the mechanical stresses within a running turbine.
- Exceptional Creep and Rupture Strength: This alloy resists deformation under prolonged stress at high temperatures, ensuring the dimensional stability and long-term performance of the combustion liner.
- Good Corrosion and Oxidation Resistance: IN718 offers excellent resistance to oxidation and corrosion in the harsh environments within the combustion chamber, contributing to the liner’s durability.
- Weldability and Fabricability: While offering high performance, IN718 also exhibits relatively good weldability and fabricability compared to some other superalloys, making it suitable for complex 3D printed designs and potential post-processing.
- Wide Availability and Cost-Effectiveness: IN718 is a widely used superalloy, making its powder form relatively accessible and cost-effective compared to some more specialized alloys.
Chemical Composition of IN718 (Nominal)
Élément | Poids % |
---|---|
Nickel (Ni) | 50-55 |
Chrome (Cr) | 17-21 |
Fer (Fe) | Équilibre |
Niobium (Nb) | 4.75-5.5 |
Molybdène (Mo) | 2.8-3.3 |
Titane (Ti) | 0.65-1.15 |
Aluminium (Al) | 0.2-0.8 |
Cobalt (Co) | 1,0 max |
Cuivre (Cu) | 0,3 max |
Manganèse (Mn) | 0.35 max |
Silicium (Si) | 0.35 max |
Carbone (C) | 0,08 max |
Exporter vers les feuilles
Métal3DP offers high-quality IN718 powder specifically optimized for metal 3D printing, ensuring the production of dense parts with superior mechanical properties.
Haynes 282
Haynes 282 is a more advanced nickel-chromium-cobalt-molybdenum alloy developed for superior creep strength, thermal stability, and oxidation resistance at even higher temperatures, typically in the range of 650-930°C (1200-1700°F). This makes it an excellent choice for next-generation, high-efficiency turbines:
- Résistance exceptionnelle au fluage : Haynes 282 exhibits significantly higher creep resistance than many other superalloys in its operating temperature range, allowing for longer component life and improved performance under high stress and temperature.
- Résistance supérieure à l'oxydation : This alloy offers excellent resistance to oxidation at elevated temperatures, crucial for maintaining the integrity of the combustion liner in aggressive combustion environments.
- Good Thermal Stability: Haynes 282 maintains its mechanical properties and microstructure stability over extended periods at high temperatures, ensuring consistent performance.
- Weldability and Fabricability: Unlike some other high-performance superalloys, Haynes 282 offers good weldability and fabricability, making it suitable for complex 3D printed designs and repair processes.
Chemical Composition of Haynes 282 (Nominal)
Élément | Poids % |
---|---|
Nickel (Ni) | Équilibre |
Chrome (Cr) | 18.5-20.5 |
Cobalt (Co) | 9.0-11.0 |
Molybdène (Mo) | 8.0-9.0 |
Titane (Ti) | 1.9-2.3 |
Aluminium (Al) | 1.38-1.65 |
Carbone (C) | 0.04-0.08 |
Bore (B) | 0.003-0.010 |
Fer (Fe) | 1,5 max |
Exporter vers les feuilles
Métal3DP can provide high-quality Haynes 282 powder, enabling the 3D printing of combustion liners that can withstand the most demanding high-temperature environments. Choosing the right powder, like those offered by Métal3DP, is crucial for achieving the desired performance and longevity of the 3D printed turbine combustion liner. Their expertise in advanced metal powders ensures that customers can select the optimal material for their specific application requirements.
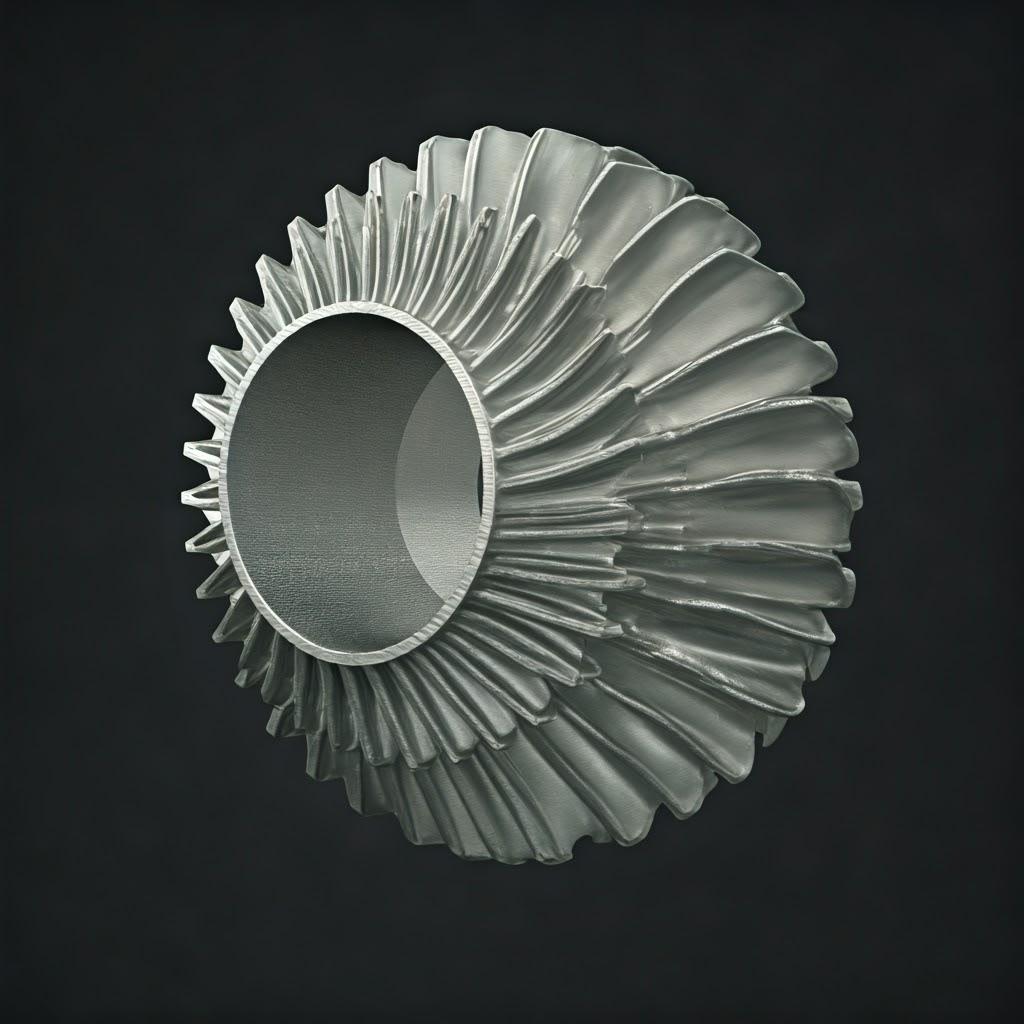
Design Considerations for Additive Manufacturing of Turbine Combustion Liners
Designing turbine combustion liners for metal 3D printing requires a shift in mindset compared to traditional manufacturing. The unique capabilities and limitations of additive manufacturing processes open up new possibilities while also necessitating careful consideration of specific design parameters:
- Optimisation de la topologie et allègement : Metal 3D printing excels at creating complex, organic shapes. Topology optimization algorithms can be used to identify areas of low stress within the liner design, allowing for material removal and the creation of lightweight yet structurally sound components. Lattice structures can further reduce weight while maintaining stiffness and potentially enhancing heat transfer through increased surface area.
- Canaux de refroidissement internes : One of the most significant advantages of metal 3D printing for combustion liners is the ability to integrate intricate internal cooling channels directly into the design. These channels can be tailored to the specific heat flux distribution on the liner walls, enabling more efficient cooling with less cooling air. This can lead to improved engine efficiency and reduced emissions. Considerations for cooling channel design include:
- Channel Geometry: Optimizing the shape and size of the channels for effective heat transfer and minimal pressure drop.
- Channel Network Complexity: Designing complex networks of channels that conform to the liner’s contours and hot spots.
- Caractéristiques de surface : Incorporating features like turbulators or fins within the channels to enhance convective heat transfer.
- Wall Thickness and Structural Integrity: While lightweighting is desirable, maintaining sufficient wall thickness is crucial for structural integrity under high pressure and thermal stresses. Finite element analysis (FEA) plays a vital role in determining the optimal wall thickness distribution across the liner, considering both mechanical and thermal loads.
- Structures de soutien : During the metal 3D printing process, support structures are often required to anchor overhanging features, prevent warping due to thermal stresses, and dissipate heat. Careful design of support structures is essential to:
- Minimize Material Usage: Optimizing support structure geometry to reduce material waste and printing time.
- Facilitate Removal: Designing supports that can be easily and cleanly removed after printing without damaging the part’s surface.
- Consider Surface Finish: Strategically placing supports in areas where surface finish requirements are less critical.
- Intégration des fonctionnalités : Metal 3D printing allows for the integration of multiple features into a single component, reducing the need for assembly and potential weak points. This can include:
- Mounting Features: Directly printing flanges, tabs, or other mounting interfaces.
- Stiffening Ribs and Gussets: Incorporating structural elements to enhance rigidity and prevent deformation.
- Sensor Integration: Designing pockets or channels for the integration of temperature or pressure sensors.
- Considérations relatives à l'état de surface : The as-printed surface finish of metal 3D printed parts can vary depending on the printing process and parameters. For combustion liners, surface roughness can affect airflow and potentially create nucleation sites for deposits. Design considerations may include:
- Optimisation de l'orientation : Orienting the part during printing to minimize the need for support structures on critical surfaces and improve surface finish.
- Allowance for Post-Processing: Designing the part with sufficient material allowance for subsequent surface finishing processes like polishing or machining if required.
By carefully considering these design aspects, engineers can leverage the unique capabilities of metal 3D printing to create high-performance turbine combustion liners with enhanced functionality, reduced weight, and improved durability. Métal3DP possesses the expertise and technology to guide customers through these design considerations and optimize their parts for additive manufacturing.
Tolerance, Surface Finish, and Dimensional Accuracy in 3D Printed Combustion Liners
Achieving the required tolerance, surface finish, and dimensional accuracy is paramount for the functional performance and longevity of turbine combustion liners. Metal 3D printing technologies have advanced significantly in their ability to produce precise parts, but understanding the achievable levels and influencing factors is crucial:
- Capacités de tolérance : The dimensional tolerance achievable with metal 3D printing depends on several factors, including the printing technology (e.g., Laser Powder Bed Fusion (LPBF), Electron Beam Powder Bed Fusion (EBPBF)), the material being used, the part geometry, and the build parameters. Generally, tolerances in the range of ±0.1 to ±0.05 mm (or ±0.004 to ±0.002 inches) are achievable for critical features. However, tighter tolerances may require post-processing. Métal3DP utilizes advanced printing equipment known for its accuracy and reliability, contributing to the production of parts with tight tolerances.
- Surface Finish Characteristics: The as-printed surface finish in metal 3D printing is typically rougher compared to machined surfaces. The surface roughness (Ra) can range from 5 to 20 μm (200 to 800 μin) depending on the process and powder particle size. Factors influencing surface finish include:
- Powder Particle Size and Morphology: Finer, more spherical powders generally result in smoother surfaces. [Metal3DP]’s advanced powder making system ensures high sphericity and good flowability, which can contribute to improved surface finish.
- Épaisseur de la couche : Thinner layers can produce smoother surfaces but may increase build time.
- Orientation de la construction : The orientation of the part during printing can significantly impact the surface finish of upward-facing and downward-facing surfaces.
- Structures de soutien : The points where support structures contact the part can leave surface marks that may require post-processing.
- Dimensional Accuracy Factors: Achieving high dimensional accuracy requires careful control over the entire 3D printing process. Key factors influencing accuracy include:
- Machine Calibration and Stability: Properly calibrated and stable 3D printers are essential for consistent and accurate results.
- Material Properties and Shrinkage: Different metal alloys exhibit varying degrees of shrinkage during the solidification process. Understanding and compensating for this shrinkage in the design and process parameters is crucial.
- Gestion thermique : Controlling the temperature within the build chamber and the thermal gradients within the part is vital to minimize warping and ensure dimensional accuracy.
- Complexité et taille des pièces : Larger and more complex parts can be more challenging to print with high accuracy due to increased thermal stresses and potential for distortion.
- Strategies for Enhancing Accuracy and Finish: Several strategies can be employed to improve the tolerance, surface finish, and dimensional accuracy of 3D printed combustion liners:
- Paramètres de construction optimisés : Fine-tuning printing parameters such as laser power, scan speed, and layer thickness can improve both accuracy and surface finish.
- Orientation stratégique des pièces : Orienting the part to minimize the build height and the number of support structures on critical surfaces can enhance accuracy and reduce the need for extensive post-processing.
- Allowance for Post-Processing: Designing critical features with a slight material overbuild to allow for precise finishing through machining, grinding, or polishing.
- Hybrid Manufacturing Approaches: Combining the design freedom of 3D printing with the precision of traditional manufacturing processes for critical features. For example, a near-net-shape liner can be 3D printed, followed by precision machining of key interfaces or cooling channel outlets.
By understanding the capabilities and limitations of metal 3D printing in terms of tolerance, surface finish, and dimensional accuracy, and by employing appropriate design and post-processing strategies, it is possible to produce high-quality turbine combustion liners that meet stringent performance requirements. [Metal3DP]’s expertise in metal additive manufacturing and their commitment to quality ensure that customers can achieve the necessary precision for their critical applications.
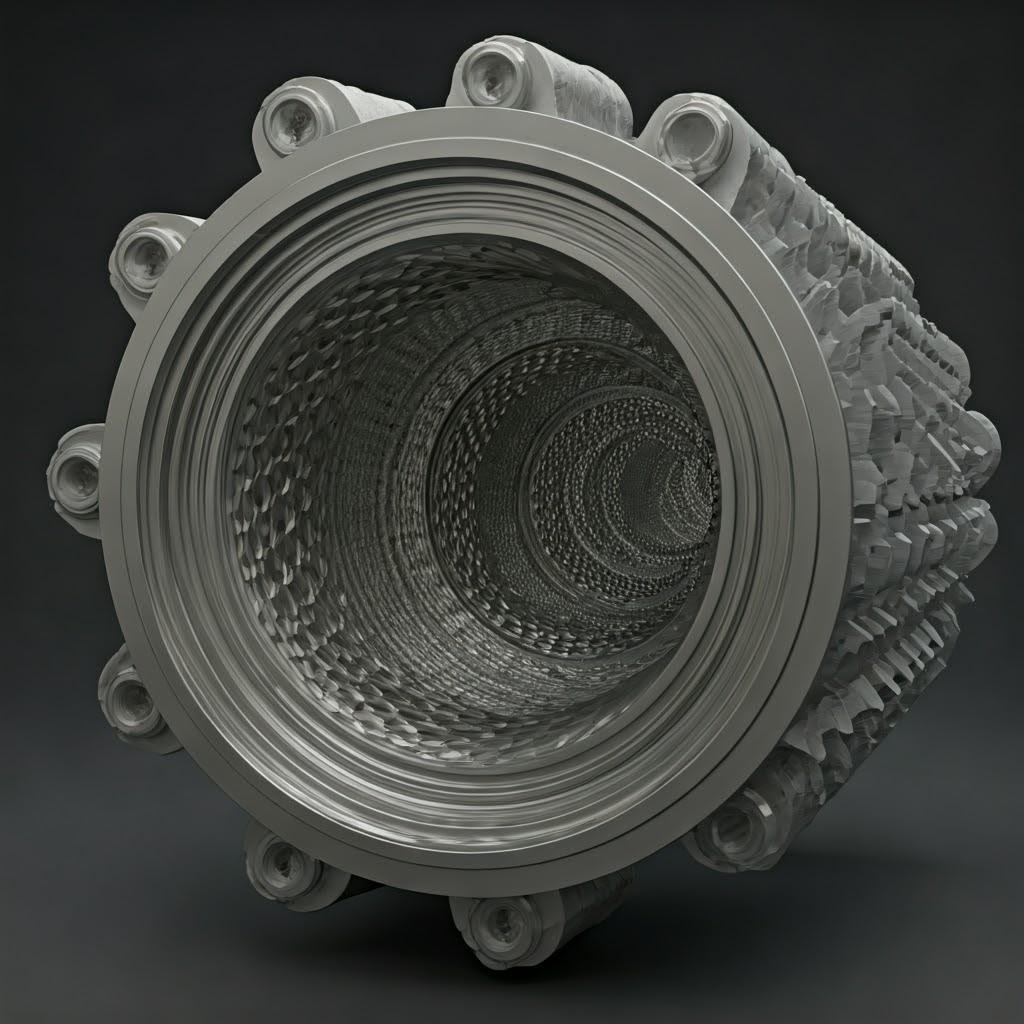
Post-Processing Requirements for 3D Printed Turbine Combustion Liners
While metal 3D printing offers significant advantages in creating complex geometries, post-processing steps are often necessary to achieve the final desired properties, surface finish, and dimensional accuracy for turbine combustion liners:
- Retrait de la structure de soutien : As mentioned earlier, support structures are often required during the printing process. Their removal is a crucial first step in post-processing. This can be done manually using tools like pliers and cutters, or through automated methods like machining or chemical dissolution, depending on the support material and geometry. Care must be taken to avoid damaging the part’s surface during support removal.
- Traitement thermique anti-stress : Metal 3D printing processes can introduce residual stresses within the part due to rapid heating and cooling cycles. Stress relief heat treatment is often performed to reduce these internal stresses, which can improve the part’s dimensional stability and prevent cracking or distortion in service. The specific temperature and duration of the heat treatment depend on the alloy being used.
- Pressage isostatique à chaud (HIP) : HIP is a process that involves subjecting the 3D printed part to high pressure and temperature in an inert gas environment. This process helps to eliminate internal porosity, increase the density of the material, and improve its mechanical properties, particularly fatigue strength and ductility, which are critical for highly stressed components like combustion liners.
- Finition de la surface : Depending on the application requirements, further surface finishing may be necessary to achieve the desired smoothness and remove any surface imperfections from the printing process or support removal. Common surface finishing techniques include:
- Media Blasting: Using abrasive media to remove surface oxides and improve surface uniformity.
- Grinding and Polishing: Employing abrasive tools to achieve smoother surface finishes and tighter tolerances on critical surfaces.
- Électropolissage : Using an electrochemical process to smooth and brighten the surface of metallic parts.
- Usinage CNC : For features requiring very tight tolerances or specific surface finishes that are difficult to achieve directly through 3D printing, CNC machining may be employed as a secondary process. This can include machining of mounting surfaces, cooling channel outlets, or other critical interfaces. Hybrid manufacturing approaches, combining the strengths of 3D printing and CNC machining, are becoming increasingly common.
- Revêtement : In some cases, coatings may be applied to the 3D printed combustion liners to enhance their resistance to oxidation, corrosion, or wear at high temperatures. These coatings can include thermal barrier coatings (TBCs) to protect the base metal from extreme heat. Coating processes can include thermal spraying, chemical vapor deposition (CVD), or physical vapor deposition (PVD).
- Inspection et contrôle qualité : After post-processing, thorough inspection and quality control are essential to ensure that the combustion liner meets the required dimensional accuracy, surface finish, and material integrity standards. This can involve visual inspection, dimensional measurements using coordinate measuring machines (CMMs), non-destructive testing (NDT) methods like ultrasonic testing or dye penetrant inspection to detect internal flaws, and material analysis to verify the microstructure and properties.
The specific post-processing requirements for a 3D printed turbine combustion liner will depend on the material, the printing process used, the design complexity, and the final application requirements. Collaborating with an experienced metal 3D printing service provider like Métal3DP ensures access to the necessary post-processing capabilities and expertise to achieve high-quality, готовые к эксплуатации компоненты.
Common Challenges and How to Avoid Them in 3D Printing Combustion Liners
While metal 3D printing offers numerous advantages, several challenges can arise during the manufacturing of turbine combustion liners. Understanding these potential issues and implementing preventative measures is crucial for successful outcomes:
- Déformation et distorsion : Thermal gradients during the printing process can lead to internal stresses that cause warping or distortion of the part, especially for large or complex geometries.
- How to Avoid: Optimize part orientation to minimize build height and overhanging features. Employ effective support structures to anchor the part and dissipate heat. Carefully control build chamber temperature and laser/electron beam parameters. Consider design modifications to reduce sharp corners and large flat areas.
- Support Structure Removal Damage: Improper removal of support structures can leave surface marks or even damage delicate features of the combustion liner.
- How to Avoid: Design support structures with easy removal in mind. Utilize appropriate removal tools and techniques. Consider using soluble support materials where applicable. Optimize part orientation to minimize the need for supports on critical surfaces.
- Porosity and Lack of Fusion: Insufficient melting and fusion of the metal powder layers can result in internal porosity or weak spots within the printed part, compromising its mechanical properties.
- How to Avoid: Optimize printing parameters such as laser/electron beam power, scan speed, and layer thickness for the specific material. Ensure the use of high-quality metal powders with good flowability, such as those offered by Métal3DP. Maintain a clean and controlled build environment.
- Rugosité de la surface : As-printed surfaces can be too rough for certain applications, affecting airflow or creating nucleation sites for deposits.
- How to Avoid: Optimize build orientation and layer thickness. Utilize finer powder particles. Plan for post-processing steps like media blasting, polishing, or machining for critical surfaces.
- Dimensional Inaccuracy: Deviations from the intended dimensions can occur due to material shrinkage, thermal distortion, or machine calibration issues.
- How to Avoid: Calibrate and maintain the 3D printer regularly. Accurately account for material shrinkage in the design phase. Optimize build parameters and part orientation. Consider using fiducial markers on the part for in-process monitoring and post-print inspection.
- Material Property Variability: Inconsistent melting and solidification can lead to variations in the microstructure and mechanical properties throughout the printed part.
- How to Avoid: Employ optimized and consistent printing parameters. Ensure a stable build environment. Utilize high-quality metal powders from reputable suppliers like [Metal3DP], which have consistent particle size distribution and chemistry. Consider post-processing treatments like HIP to homogenize the microstructure.
- High Costs for Complex Geometries: While 3D printing can create complex shapes, highly intricate designs with extensive support structures or requiring significant post-processing can be expensive.
- How to Avoid: Optimize designs for manufacturability using additive manufacturing principles. Minimize the need for excessive support structures. Consider design trade-offs between complexity and cost. Explore different printing technologies and materials to find the most cost-effective solution.
By proactively addressing these potential challenges through careful design, optimized process parameters, and collaboration with experienced metal 3D printing service providers like Métal3DP, manufacturers can successfully leverage the benefits of additive manufacturing for high-performance turbine combustion liners.
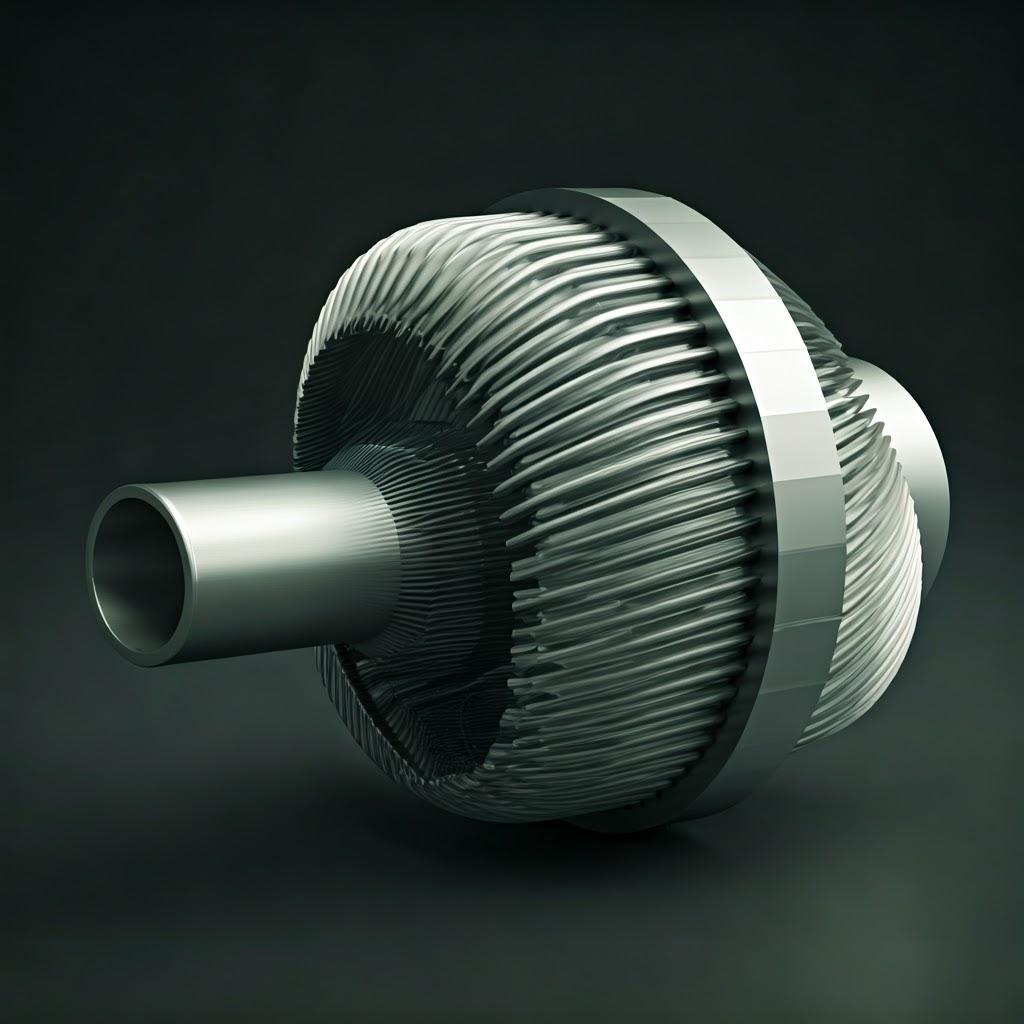
How to Choose the Right Metal 3D Printing Service Provider for Turbine Combustion Liners
Selecting the right metal 3D printing service provider is a critical decision that can significantly impact the quality, cost, and lead time of your turbine combustion liners. Here are key factors to consider when evaluating potential suppliers:
- Capacités matérielles : Ensure the service provider has experience processing the specific high-temperature alloys required for your application, such as IN718 and Haynes 282. Verify their expertise in handling these materials and their ability to achieve the desired material properties. Métal3DP offers a wide range of high-quality metal powders, including those ideal for high-temperature applications, and possesses deep expertise in processing them.
- Printing Technology and Equipment: Understand the types of metal 3D printing technologies the provider utilizes (e.g., LPBF, EBPBF). Different technologies offer varying levels of precision, surface finish, and build volume. Ensure their equipment is well-maintained and capable of producing parts that meet your dimensional and quality requirements. [Metal3DP]’s industry-leading printers deliver high accuracy and reliability for mission-critical parts. You can learn more about their printing methods at https://met3dp.com/printing-methods/.
- Design Optimization Expertise: A good service provider should offer support in optimizing your combustion liner design for additive manufacturing. This includes guidance on topology optimization, lightweighting strategies, internal cooling channel design, and minimizing the need for support structures. Their expertise can help you leverage the full potential of metal 3D printing and avoid potential manufacturing challenges.
- Capacités de post-traitement : Inquire about the in-house or partnered post-processing services offered, such as support removal, heat treatment (including stress relief and HIP), surface finishing (e.g., polishing, coating), and CNC machining. A comprehensive suite of post-processing capabilities ensures a streamlined manufacturing process and a готовый к эксплуатации компонент.
- Assurance qualité et inspection : Verify the provider’s quality management system and their inspection procedures. Do they have certifications like ISO 9001 or AS9100 (for aerospace applications)? What non-destructive testing methods do they employ to ensure the integrity of the printed parts? Robust quality assurance processes are essential for critical components like turbine combustion liners.
- Experience and Industry Focus: Look for a service provider with a proven track record in manufacturing parts for demanding industries such as aerospace, automotive, medical, or industrial manufacturing. Experience with high-temperature applications and an understanding of the specific requirements of turbine components are highly valuable. Métal3DP has decades of collective expertise in metal additive manufacturing and partners with organizations in these key industries.
- Lead Times and Production Capacity: Discuss your project timelines and production volume requirements. Ensure the service provider has the capacity to meet your needs within your desired timeframe. Understand their typical lead times for similar projects and their ability to scale production if required.
- Cost Structure and Transparency: Obtain a clear and detailed quotation that outlines all costs, including printing, materials, support removal, post-processing, and inspection. Understand their pricing model and any potential factors that could affect the final cost. Transparency in pricing is crucial for budget planning.
- Communication and Customer Support: Evaluate the provider’s responsiveness, communication style, and technical support capabilities. A collaborative partner who is readily available to answer your questions and provide updates throughout the project is essential for a smooth and successful engagement.
- References and Case Studies: Request references or case studies of similar projects they have undertaken. Speaking with previous clients can provide valuable insights into their capabilities, quality, and customer service.
By carefully considering these factors, you can select a metal 3D printing service provider that aligns with your specific needs and ensures the successful manufacturing of high-performance turbine combustion liners. Contacting Métal3DP to discuss your project requirements is a great first step in exploring how their comprehensive solutions can power your organization’s additive manufacturing goals.
Cost Factors and Lead Time for 3D Printed Combustion Liners
Understanding the factors that influence the cost and lead time for 3D printed turbine combustion liners is crucial for project planning and budgeting:
Facteurs de coût :
- Coûts des matériaux : The cost of the metal powder is a significant factor. High-performance alloys like IN718 and Haynes 282 can be expensive. The quantity of material used, which is influenced by the part’s volume and the amount of support material required, directly impacts the cost. Optimizing the design for material efficiency is key to cost reduction.
- Temps de construction : The duration of the printing process directly affects the machine time cost. Longer build times, often associated with larger parts, finer layer resolutions, and complex geometries, increase the overall cost. Part orientation and support structure design can influence build time.
- Coûts de post-traitement : The extent of post-processing required significantly impacts the final cost. Support removal, heat treatment (including HIP), surface finishing (e.g., polishing, coating), and CNC machining all add to the overall expense. Minimizing the need for extensive post-processing through design optimization and process control can help reduce costs.
- Coûts de main-d'œuvre : The expertise required for design optimization, print setup, machine operation, post-processing, and quality control contributes to the overall cost. Engaging with experienced service providers like [Metal3DP] ensures skilled handling of the entire process.
- Machine and Overhead Costs: The cost of operating and maintaining the sophisticated metal 3D printing equipment, along with general overhead expenses of the service provider, are factored into the pricing.
- Quantity and Scale: While 3D printing is often advantageous for low to medium volumes, the cost per part can decrease with larger production runs due to economies of scale in material procurement and process optimization.
Facteurs de délai d'exécution :
- Complexité et taille des pièces : More intricate designs and larger parts typically require longer printing times, extending the lead time.
- Disponibilité du matériel : The availability of the specific metal powder required can impact the start of the printing process. [Metal3DP]’s wide range of in-house metal powders can help mitigate potential delays.
- Machine Availability and Scheduling: The lead time is also influenced by the service provider’s current workload and the availability of their 3D printing equipment.
- Durée du post-traitement : The time required for various post-processing steps, such as heat treatment cycles, surface finishing, and inspections, adds to the overall lead time. Complex post-processing requirements will naturally extend the delivery timeline.
- Shipping and Logistics: The time for final inspection, packaging, and shipping the completed combustion liners to the customer also needs to be considered in the overall lead time.
By carefully considering these cost and lead time factors and discussing them transparently with potential service providers like [Metal3DP], you can establish realistic expectations and make informed decisions for your metal 3D printed turbine combustion liner projects.
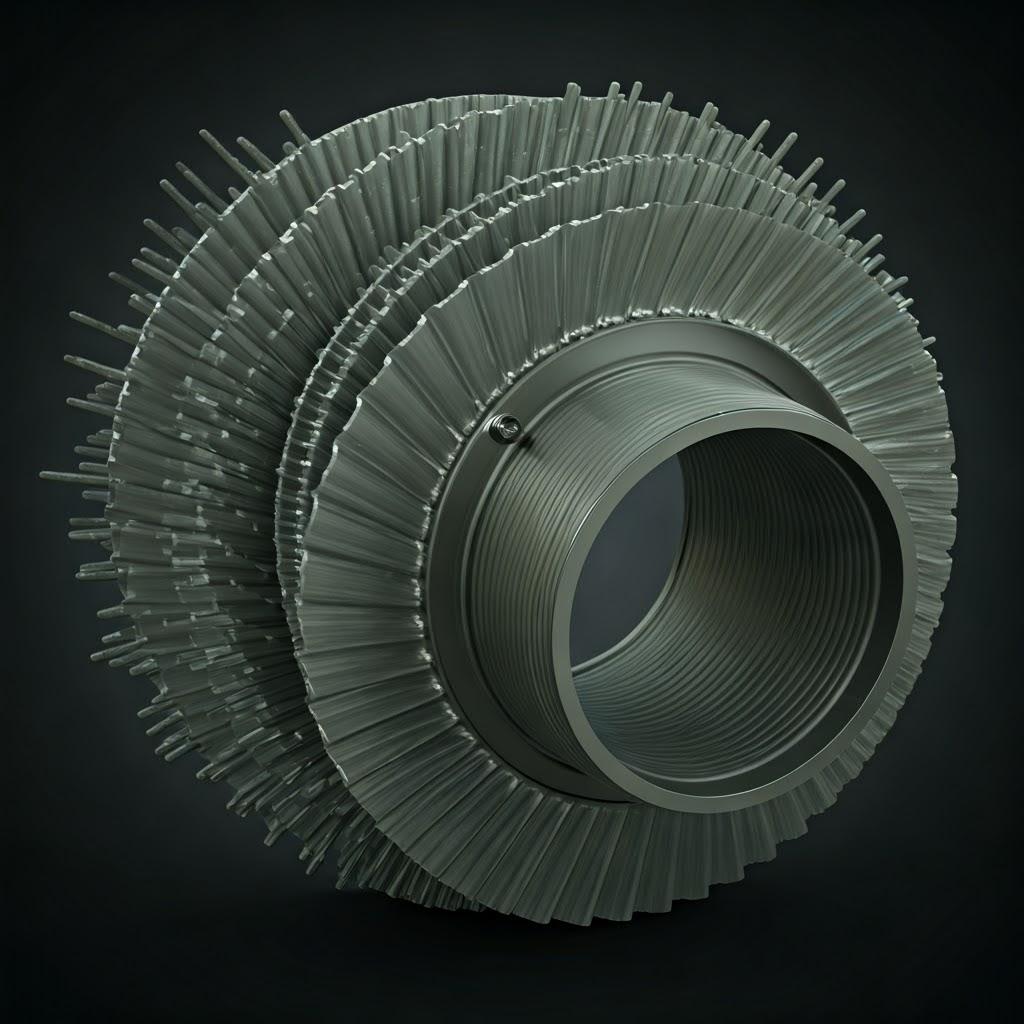
Foire aux questions (FAQ)
- What are the typical applications of metal 3D printed turbine combustion liners? Metal 3D printed turbine combustion liners are used in aerospace engines, power generation turbines, industrial gas turbines, and emerging applications requiring high-performance, high-temperature components with complex geometries and optimized cooling features.
- Can metal 3D printing reduce the weight of turbine combustion liners? Yes, through design optimization techniques like topology optimization and the use of lattice structures, metal 3D printing can significantly reduce the weight of turbine combustion liners compared to traditionally manufactured parts without compromising structural integrity.
- What kind of post-processing is typically required for 3D printed combustion liners? Common post-processing steps include support structure removal, stress relief heat treatment, Hot Isostatic Pressing (HIP) to improve density, surface finishing (media blasting, polishing), and potentially CNC machining for critical features or coating for enhanced performance.
- How does the cost of metal 3D printed combustion liners compare to traditional methods? The cost-effectiveness of metal 3D printing depends on factors like part complexity, production volume, and material used. For complex geometries and low to medium volumes, it can be more cost-effective due to reduced tooling costs and material waste. For very high volumes, traditional methods may still be more economical.
- What are the key advantages of using IN718 and Haynes 282 for combustion liners? IN718 offers excellent high-temperature strength, creep and rupture resistance, and good corrosion resistance at moderate high temperatures. Haynes 282 provides superior creep strength, thermal stability, and oxidation resistance at even higher temperatures, making it suitable for more demanding applications. [Metal3DP] offers both of these high-performance powders.
Conclusion – Embracing the Future of Turbine Technology with Metal 3D Printing
Metal 3D printing is revolutionizing the design and manufacturing of high-temperature turbine combustion liners. Its ability to create intricate geometries, optimize material usage, reduce lead times for complex parts, and enable the use of advanced alloys like IN718 and Haynes 282 opens up new possibilities for enhancing turbine performance, efficiency, and durability. By partnering with a knowledgeable and experienced metal 3D printing service provider like Métal3DP, engineers and procurement managers in aerospace, power generation, and industrial manufacturing can unlock the full potential of additive manufacturing to create next-generation turbine components. [Metal3DP]’s comprehensive solutions, spanning advanced metal powders, industry-leading printing technology, and application development services, make them a trusted partner in accelerating digital manufacturing transformations and powering the future of turbine technology. Contact Métal3DP today to explore how their capabilities can support your organization’s additive manufacturing goals.
Partager sur
MET3DP Technology Co. est un fournisseur de premier plan de solutions de fabrication additive dont le siège se trouve à Qingdao, en Chine. Notre société est spécialisée dans les équipements d'impression 3D et les poudres métalliques de haute performance pour les applications industrielles.
Articles connexes
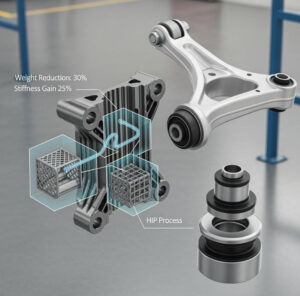
Metal 3D Printed Subframe Connection Mounts and Blocks for EV and Motorsport Chassis
Lire la suite "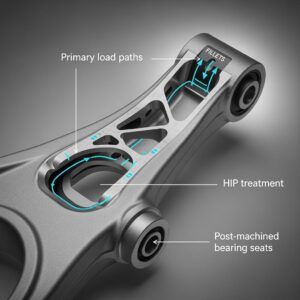
Metal 3D Printing for U.S. Automotive Lightweight Structural Brackets and Suspension Components
Lire la suite "À propos de Met3DP
Mise à jour récente
Notre produit
CONTACTEZ-NOUS
Vous avez des questions ? Envoyez-nous un message dès maintenant ! Nous répondrons à votre demande avec toute une équipe dès réception de votre message.
Obtenir les informations de Metal3DP
Brochure du produit
Obtenir les derniers produits et la liste des prix