Impression 3D de châssis de drone avec de l'aluminium léger
Table des matières
Introduction : Le rôle croissant de la fabrication additive métallique dans la fabrication avancée de châssis de drones
Le véhicule aérien sans pilote (UAV), communément appelé drone, a transcendé ses origines de niche pour devenir une technologie transformatrice dans une multitude de secteurs. De la reconnaissance militaire sophistiquée et de la surveillance de l'agriculture de précision à la livraison rapide de colis et à l'inspection des infrastructures critiques, les UAV remodèlent les capacités opérationnelles dans le monde entier. Au cœur de chaque UAV haute performance se trouve son châssis – l'épine dorsale structurelle qui dicte la capacité de charge utile, la durée de vol, la maniabilité et la résilience globale. À mesure que les exigences des missions deviennent de plus en plus exigeantes, les fabricants sont confrontés au défi de créer des châssis qui sont non seulement exceptionnellement solides et rigides, mais aussi incroyablement légers. C'est là que la synergie entre les matériaux avancés comme les alliages d'aluminium légers et les techniques de fabrication de pointe comme impression 3D de métaux apparaît comme un facteur de changement radical.
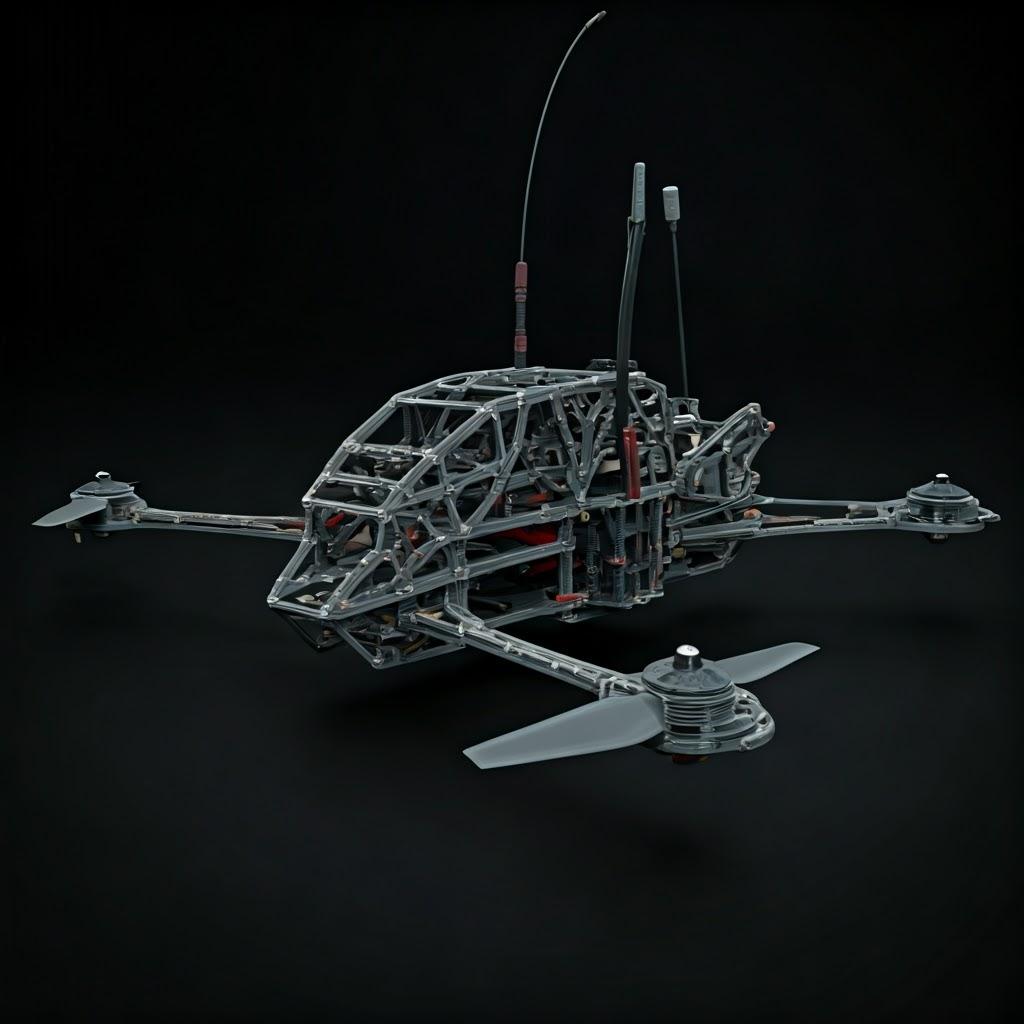
Les méthodes de fabrication traditionnelles, telles que l'usinage CNC à partir de billettes ou la fabrication de structures à partir de tôles et de tubes, imposent souvent des limitations importantes à la complexité géométrique et à l'efficacité des matériaux. Les structures internes complexes, les chemins de charge optimisés et l'intégration transparente des fonctions sont difficiles, longs ou tout simplement impossibles à réaliser de manière conventionnelle. La fabrication additive (FA) métallique, en particulier les technologies de fusion sur lit de poudre comme le Selective Laser Melting (SLM) et l'Electron Beam Melting (EBM), modifie fondamentalement ce paradigme. En construisant des pièces couche par couche directement à partir de poudre métallique fine, la FA libère une liberté de conception sans précédent. Cela permet aux ingénieurs d'employer des techniques telles que l'optimisation topologique et la conception générative, créant des structures de forme organique, très efficaces, qui minimisent le poids tout en maximisant la résistance et la rigidité – des attributs parfaitement adaptés aux châssis de drones avancés.
Les industries aérospatiale et de la défense, qui ont adopté la FA en premier, ont ouvert la voie, démontrant les profonds avantages des composants imprimés dans des applications exigeantes. Aujourd'hui, ces avantages se répandent rapidement sur les marchés commerciaux et industriels des drones. La capacité de consolider plusieurs composants en une seule pièce imprimée réduit le temps d'assemblage, minimise les points de défaillance potentiels associés aux joints et aux fixations, et simplifie les chaînes d'approvisionnement. De plus, la FA facilite le prototypage rapide et l'itération de la conception, ce qui permet d'accélérer les cycles de développement et de créer des plateformes de drones hautement personnalisées, adaptées à des profils de mission ou à des exigences de charge utile spécifiques. Les alliages d'aluminium légers, réputés pour leur excellent rapport résistance/poids, leur résistance à la corrosion et leur rentabilité relative, sont des candidats de choix pour cette révolution technologique. Lorsqu'ils sont combinés à la précision et à la flexibilité de conception de la FA métallique, des matériaux comme l'AlSi10Mg, le Scalmalloy® et les alliages A7075 compatibles avec la FA permettent la production de châssis de drones de nouvelle génération, auparavant inaccessibles.
Pour les responsables des achats et les ingénieurs qui s'approvisionnent en composants ou recherchent des partenaires de fabrication, il est essentiel de comprendre les capacités de la FA métallique pour les châssis de drones. Cela représente un passage à des solutions plus efficaces, plus performantes et potentiellement plus rentables, en particulier pour les productions complexes ou à faible et moyenne volume. Des entreprises comme Met3dp, spécialisées à la fois dans les équipements de FA métallique de pointe et dans la production de poudres métalliques haute performance utilisant des techniques d'atomisation de pointe, sont à l'avant-garde de cette transformation. Notre expertise couvre l'ensemble de l'écosystème de la FA, du développement de paramètres d'impression optimisés à la garantie des caractéristiques de poudre de la plus haute qualité – sphéricité, fluidité et pureté – essentielles pour la production de composants de drones fiables et essentiels à la mission. Alors que l'industrie des drones continue sa croissance exponentielle, la FA métallique jouera sans aucun doute un rôle de plus en plus vital dans l'élaboration de l'avenir de la conception et des performances des plateformes aériennes.
À quoi servent les châssis de drones en aluminium léger ? Principales applications et industries

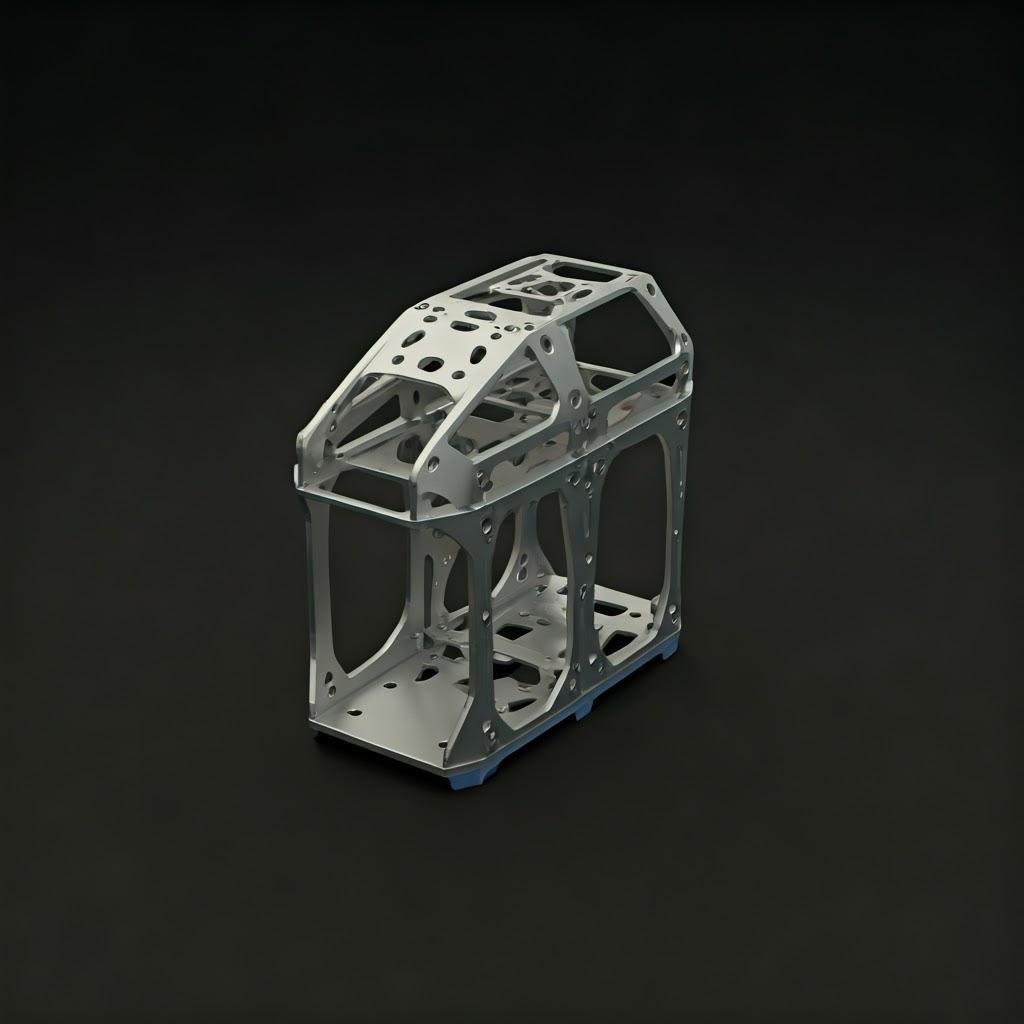
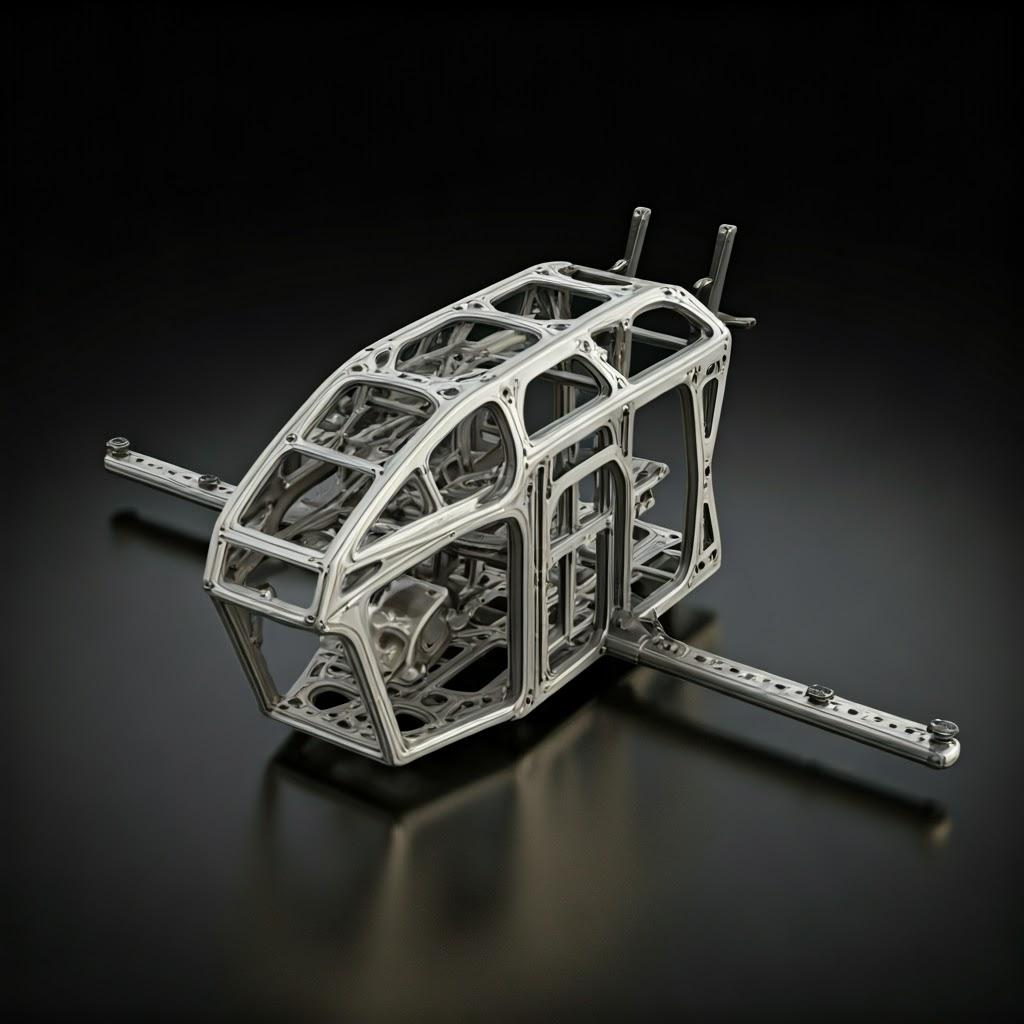
Le châssis du drone est bien plus qu'un simple squelette ; c'est un châssis multifonctionnel conçu pour résister aux forces aérodynamiques, loger et protéger les sous-systèmes critiques, gérer les vibrations et supporter des charges utiles variables dans diverses conditions opérationnelles. La demande de châssis en aluminium léger, en particulier ceux améliorés grâce à la fabrication additive, découle de l'impact direct de la réduction de poids sur des paramètres de performance cruciaux tels que l'endurance de vol, la capacité de charge utile, l'agilité et l'efficacité énergétique. Par conséquent, les châssis en aluminium imprimés en 3D trouvent des applications dans un large éventail d'industries et de cas d'utilisation :
- Aérospatiale et défense : Ce secteur exige les plus hauts niveaux de performance, de fiabilité et, souvent, de furtivité.
- Applications : Plateformes de renseignement, de surveillance et de reconnaissance (ISR) à longue endurance ; drones cibles ; systèmes tactiques sans pilote ; composants d'essaims de drones.
- Exigences du châssis : Réduction de poids extrême pour maximiser le temps de vol ou la portée, intégrité structurelle élevée pour la manœuvrabilité et les environnements difficiles, intégration de supports d'équipement de capteurs ou de communication complexes, caractéristiques potentiellement peu observables. La FA permet des conceptions optimisées et consolidées, souvent à l'aide d'alliages à haute résistance comme le Scalmalloy® ou l'A7075.
- Livraison et logistique commerciales : Le marché florissant de la livraison par drone nécessite des drones efficaces, fiables et sûrs, capables de transporter des colis de différentes tailles et poids.
- Applications : Livraison de colis en dernier kilomètre, transport de fournitures médicales, logistique interne dans les grandes installations.
- Exigences du châssis : Équilibre entre résistance, poids et rentabilité. Durabilité pour une utilisation à haute fréquence, points de montage standardisés pour les conteneurs de charge utile, facilité d'entretien. L'AlSi10Mg est souvent un choix approprié, offrant de bonnes performances à un coût raisonnable.
- Agriculture et surveillance environnementale : Les drones équipés de capteurs spécialisés aident à l'agriculture de précision, à la surveillance des cultures, à l'étude de l'environnement et au suivi de la faune.
- Applications : Pulvérisation des cultures, cartographie des champs (NDVI), analyse des sols, surveillance de l'érosion côtière, conservation de la faune.
- Exigences du châssis : Capacité à transporter des charges utiles de capteurs spécifiques (caméras multispectrales, LiDAR), stabilité pour l'acquisition précise de données, résistance aux facteurs environnementaux (poussière, humidité), endurance suffisante pour couvrir de grandes surfaces. La réduction de poids se traduit directement par des temps d'enquête plus longs.
- Inspection et étude des infrastructures : Les drones offrent un moyen sûr et économique d'inspecter les ponts, les lignes électriques, les éoliennes, les pipelines et les bâtiments, ainsi que d'effectuer des levés et des cartographies terrestres.
- Applications : Inspection visuelle et thermique des infrastructures critiques, cartographie LiDAR, surveillance des chantiers de construction, levés cadastraux.
- Exigences du châssis : Grande stabilité pour le transport de caméras haute résolution ou de scanners LiDAR, amortissement des vibrations, capacité à opérer à proximité des structures, durabilité. La FA permet des caractéristiques d'amortissement intégrées et des montures personnalisées.
- Secteur de l'énergie : Les industries du pétrole et du gaz, des fermes solaires et de l'énergie éolienne utilisent des drones pour les tâches d'inspection et de maintenance, souvent dans des endroits isolés ou dangereux.
- Applications : Inspection des pipelines, inspection des plateformes offshore, analyse thermique des panneaux solaires, inspection des pales d'éoliennes.
- Exigences du châssis : Robustesse, résistance à l'environnement, potentiellement longues durées de vol pour les opérations à distance, capacité à transporter des capteurs spécialisés (par exemple, des détecteurs de méthane).
- Cinématographie et diffusion : Les drones équipés de caméras haut de gamme capturent des images aériennes époustouflantes pour les films, la télévision et les événements en direct.
- Applications : Tournage aérien, diffusion sportive, collecte d'informations.
- Exigences du châssis : Stabilité et amortissement des vibrations exceptionnels pour des images fluides, capacité à transporter des cardans de caméra professionnels, faible signature sonore (influencée par la conception globale, y compris l'aérodynamisme du cadre).
- Sécurité publique et intervention d'urgence : La police, les pompiers et les équipes de recherche et de sauvetage utilisent des drones pour la connaissance de la situation, la surveillance et la localisation des personnes.
- Applications : Opérations de recherche et de sauvetage, surveillance des incendies, reconstitution des scènes d'accident, gestion des foules.
- Exigences du châssis : Capacité de déploiement rapide, robustesse, capacité à transporter des caméras thermiques ou à zoom optique, fiabilité dans diverses conditions météorologiques.
Tableau : Exemples d'applications de drones et considérations clés pour le cadre
Industrie/Application | Principales exigences du cadre | Choix typique d'alliage d'aluminium (FA) | Focus B2B |
---|---|---|---|
Aérospatiale/Défense (ISR) | Réduction maximale du poids, Haute résistance, Haute rigidité, Intégration de la charge utile | Scalmalloy®, A7075 | Fournisseur de composants de haute spécification, Entrepreneur de la Défense |
Livraison commerciale | Durabilité, Rentabilité, Supports standardisés, Poids | AlSi10Mg, potentiellement Scalmalloy® | Intégrateurs logistiques, Vente en gros de pièces de drones |
Agriculture de précision | Capacité de charge utile (capteurs), Stabilité, Endurance | AlSi10Mg | Fournisseurs de technologies agricoles, Sociétés de services |
Inspection des infrastructures | Stabilité, Amortissement des vibrations, Intégration des capteurs, Durabilité | AlSi10Mg, Scalmalloy® | Bureaux d'études, Sociétés de gestion d'actifs |
Secteur de l'énergie (à distance) | Robustesse, Endurance, Résistance environnementale | AlSi10Mg, Scalmalloy® | Entreprises énergétiques, Fournisseurs de services d'inspection |
Cinématographie professionnelle | Stabilité extrême, Amortissement des vibrations, Intégration du cardan | AlSi10Mg, Conceptions optimisées sur mesure | Sociétés de production, Sociétés de location de matériel |
Exporter vers les feuilles
Pour les fabricants de drones et les intégrateurs de systèmes, l'approvisionnement en châssis répondant à ces exigences diverses et exigeantes est primordial. Les alliages d'aluminium légers, en particulier lorsqu'ils sont formés par fabrication additive, offrent les caractéristiques de performance nécessaires. S'associer à un fournisseur de fabrication additive de métaux compétent garantit l'accès aux bons matériaux, à l'expertise en conception et aux capacités de production pour fournir des solutions de châssis optimisées, positionnant ainsi vos produits de manière compétitive sur ces marchés en croissance. Trouver des fournisseurs fiables de composants de drones et fabricants de châssis de drones sur mesure capables de tirer parti de la fabrication additive devient de plus en plus crucial pour le succès.
Pourquoi utiliser l'impression 3D métal pour les châssis de drones ? Avantages par rapport à la fabrication traditionnelle
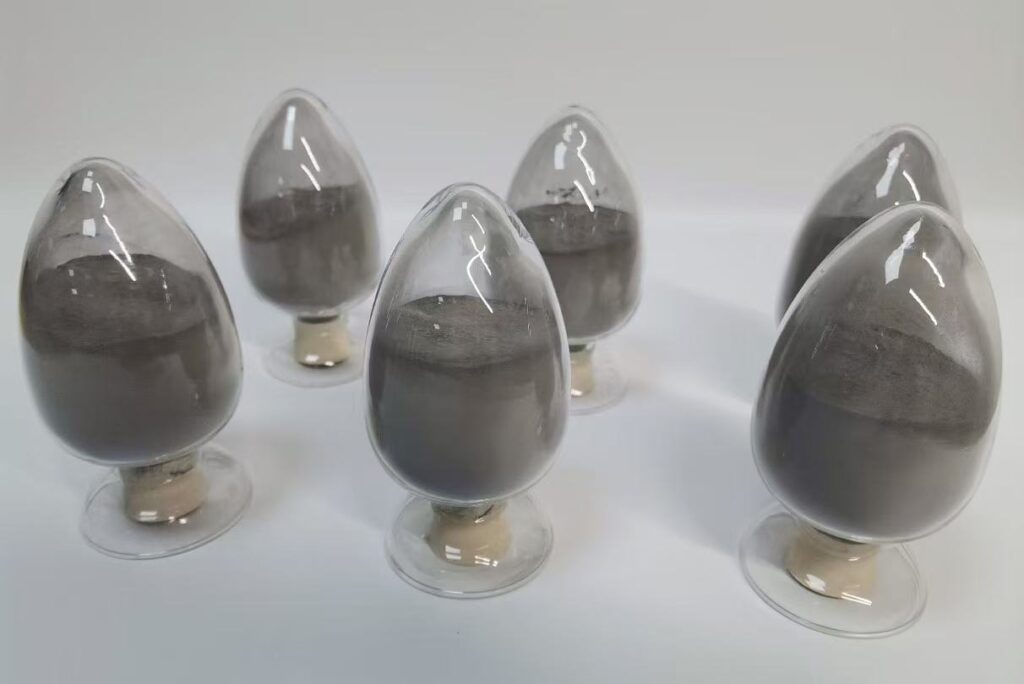
Bien que les méthodes de fabrication traditionnelles aient servi l'industrie des drones pendant des années, la fabrication additive de métaux offre un ensemble d'avantages convaincants, en particulier lors de la conception et de la production de châssis en aluminium légers et performants. Ces avantages se traduisent souvent directement par des performances supérieures des drones, des cycles de développement plus rapides et une production plus efficace, en particulier pour les conceptions complexes ou les lots personnalisés. Examinons les principales raisons pour lesquelles les équipes d'ingénierie et d'approvisionnement se tournent de plus en plus vers la fabrication additive de métaux :
- Liberté de conception et complexité inégalées :
- Défis avec les méthodes traditionnelles : L'usinage CNC est limité par l'accès aux outils, ce qui rend les caractéristiques internes complexes ou les structures creuses difficiles et coûteuses. La fabrication de tôles limite les conceptions aux formes pliées et assemblées.
- Avantage AM : La fabrication additive construit les pièces couche par couche, ce qui permet de créer des géométries complexes impossibles à produire autrement. Cela inclut :
- Optimisation de la topologie : Des algorithmes déterminent la répartition des matériaux la plus efficace pour résister à des charges spécifiques, ce qui donne des structures organiques, semblables à des os, incroyablement légères mais solides.
- Structures de treillis internes : Le remplacement des sections pleines par des treillis internes réduit considérablement le poids tout en conservant l'intégrité structurelle et en ajoutant potentiellement des fonctions telles que l'amortissement des vibrations.
- Caractéristiques intégrées : Les supports pour les moteurs, les capteurs et les batteries, les canaux pour le câblage et les carénages aérodynamiques peuvent être intégrés de manière transparente dans la conception du châssis, ce qui réduit le nombre de pièces et la complexité de l'assemblage.
- Conception conforme : Les composants peuvent être conçus pour suivre des surfaces courbes ou s'adapter précisément à des enveloppes étroites.
- Réduction de poids significative (allègement) :
- Défis avec les méthodes traditionnelles : Obtenir une réduction de poids significative implique souvent un usinage important (gaspillage de matière) ou des assemblages complexes de pièces à parois minces.
- Avantage AM : L'optimisation topologique et les structures en treillis, rendues possibles par la fabrication additive, sont les principaux moteurs de l'allègement. La réduction du poids du châssis améliore directement les paramètres critiques des drones :
- Endurance de vol accrue : Moins de poids nécessite moins d'énergie pour rester en l'air.
- Capacité de charge utile accrue : Le gain de poids du châssis peut être alloué au transport de capteurs, de batteries ou de cargaisons plus lourds.
- Agilité et manœuvrabilité améliorées : Des châssis plus légers permettent une accélération plus rapide et des virages plus serrés.
- Consolidation partielle :
- Défis avec les méthodes traditionnelles : Les assemblages complexes nécessitent souvent de nombreuses pièces individuelles, des fixations (vis, rivets) et des processus d'assemblage (soudure, collage). Chaque interface est un point de défaillance potentiel et ajoute du poids et du temps d'assemblage.
- Avantage AM : De multiples composants fonctionnels peuvent être conçus et imprimés en une seule pièce monolithique. Cela conduit à :
- Réduction du temps et des coûts d'assemblage : Moins de pièces à assembler signifie une production plus rapide et des coûts de main-d'œuvre réduits.
- Intégrité structurelle améliorée : L'élimination des joints et des fixations supprime les points faibles potentiels.
- Chaîne d'approvisionnement simplifiée : Moins de références de pièces individuelles à gérer et à approvisionner.
- Prototypage rapide et itération de la conception :
- Défis avec les méthodes traditionnelles : La création de prototypes par usinage ou outillage pour la fabrication peut prendre du temps et être coûteuse, ce qui ralentit le cycle de conception.
- Avantage AM : Les fichiers de conception numérique peuvent être rapidement transformés en prototypes physiques en métal, souvent en quelques jours. Cela permet aux ingénieurs de :
- Tester les conceptions plus rapidement : Valider rapidement les performances structurelles, l'ajustement et la fonction.
- Itérer rapidement : Apporter des modifications de conception basées sur les résultats des tests et imprimer de nouvelles versions sans avoir besoin de modifications coûteuses de l'outillage.
- Accélérer la mise sur le marché : Mettre sur le marché plus rapidement de nouveaux modèles de drones ou des modèles améliorés.
- Personnalisation et production à la demande :
- Défis avec les méthodes traditionnelles : La production de petites séries ou de versions personnalisées de châssis par des méthodes conventionnelles peut être prohibitive en raison des coûts d'installation et d'outillage.
- Avantage AM : La FA est idéale pour la production à faible et moyenne volume et la personnalisation de masse.
- Conceptions sur mesure : Les châssis peuvent être facilement personnalisés pour des missions, des charges utiles ou des exigences client spécifiques sans frais généraux importants par variation de conception.
- Fabrication à la demande : Les pièces peuvent être produites selon les besoins, ce qui réduit les besoins en inventaire et permet des concepts d'entreposage numérique.
- Efficacité matérielle :
- Défis avec les méthodes traditionnelles : Les méthodes soustractives comme l'usinage CNC partent d'un grand bloc de matériau et enlèvent l'excédent, générant potentiellement des déchets importants (bien que les copeaux puissent être recyclés).
- Avantage AM : Les procédés de fusion sur lit de poudre n'utilisent généralement que le matériau nécessaire à la pièce et aux structures de support. La poudre non fusionnée peut généralement être recyclée et réutilisée, ce qui conduit à des taux d'utilisation des matériaux plus élevés, en particulier pour les géométries complexes. (Remarque : l'enlèvement de la structure de support génère des déchets).
Tableau : Fabrication additive de métaux par rapport à la fabrication traditionnelle pour les châssis de drones
Fonctionnalité | Fabrication additive de métaux (par exemple, SLM/EBM) | Fabrication traditionnelle (par exemple, usinage CNC, fabrication) | Principal avantage pour les châssis de drones |
---|---|---|---|
Complexité géométrique | Très élevé (canaux internes, treillis, formes organiques) | Modéré à faible (limité par l'accès aux outils, les rayons de courbure) | Structures optimisées, fonctionnalités intégrées |
Réduction du poids | Excellent (optimisation topologique, treillis) | Bon (Nécessite un usinage important ou un assemblage complexe) | Endurance, charge utile, agilité accrues |
Consolidation partielle | Excellent (plusieurs pièces imprimables en une seule) | Faible (Nécessite l'assemblage de plusieurs composants) | Réduction du temps/coût d'assemblage, Fiabilité améliorée |
Vitesse de prototypage | Rapide (jours) | Modéré à lent (semaines, selon la complexité/l'outillage) | Validation de la conception plus rapide, Délai de mise sur le marché plus court |
Coût de la personnalisation | Faible par variation (pas d'outillage) | Élevé (nécessite un nouvel outillage ou une reprogrammation complexe) | Conceptions spécifiques à la mission, Solutions sur mesure |
Déchets matériels | Généralement plus faible (recyclage de la poudre) | Peut être élevé (nature soustractive de la CNC) | Plus durable, Coût potentiel des matières premières plus faible (pièces complexes) |
Évolutivité du volume | Idéal pour les faibles à moyens volumes | Idéal pour les volumes importants (une fois l'outillage mis en place) | Production efficace pour les drones spécialisés/personnalisés |
Exporter vers les feuilles
Tirer parti de ces avantages nécessite une expertise à la fois en conception pour la fabrication additive (DfAM) et dans les nuances spécifiques des méthodes d'impression et des matériaux. S'associer à un fournisseur de services comme Met3dp, qui possède une connaissance approfondie de l'impression d'alliages d'aluminium et exploite des équipements de pointe, garantit que ces avantages peuvent être pleinement réalisés, transformant la façon dont les châssis de drones haute performance sont conçus et produits. Pour les responsables des achats, la proposition de valeur réside dans l'obtention de composants plus performants, la simplification potentielle de la logistique et une plus grande flexibilité de conception pour leurs équipes d'ingénierie.
Poudres d'aluminium recommandées pour les châssis de drones : AlSi10Mg, Scalmalloy®, A7075
Le choix du bon matériau est fondamental pour obtenir les caractéristiques de performance souhaitées pour un châssis de drone imprimé en 3D. Les alliages d'aluminium sont privilégiés pour leur légèreté inhérente et leur bonne résistance à la corrosion. Dans le domaine de la fabrication additive, plusieurs poudres d'aluminium se distinguent par leur imprimabilité et les propriétés mécaniques qui en résultent. Le choix implique souvent d'équilibrer la résistance, la ductilité, le poids, les propriétés thermiques, l'imprimabilité, les exigences de post-traitement et le coût. Voici un aperçu plus détaillé des principaux concurrents pour les châssis de drones légers :
1. AlSi10Mg :
- Description : Il s'agit de l'un des alliages d'aluminium les plus courants et les plus connus utilisés dans la fabrication additive métallique, essentiellement un alliage de fonderie aluminium-silicium-magnésium adapté à la fusion sur lit de poudre.
- Propriétés principales :
- Bon rapport résistance/poids.
- Excellente imprimabilité et usinabilité sur diverses plateformes SLM/DMLS.
- Bonne conductivité thermique.
- Ductilité modérée.
- Peut être post-traité (traité thermiquement, usiné, poli).
- Adaptabilité aux châssis de drones : Un excellent choix polyvalent pour un large éventail d'applications de drones, en particulier lorsque la résistance modérée est suffisante et que la rentabilité est un facteur important. Idéal pour les prototypes, les drones commerciaux à usage général et les composants moins exigeants sur le plan structurel. Sa disponibilité généralisée et ses paramètres d'impression établis en font une option fiable pour de nombreux fournisseurs de pièces de drones en gros..
- Considérations : Sa résistance est inférieure à celle des alliages haute performance comme le Scalmalloy® ou l'A7075 optimisé. Un traitement thermique (généralement une relaxation des contraintes ou T6) est souvent nécessaire pour obtenir des propriétés optimales.
2. Scalmalloy® :
- Description : Un alliage aluminium-magnésium-scandium haute performance breveté, spécialement développé pour la fabrication additive par APWORKS. La petite addition de scandium crée des structures de grains extrêmement fines lors de l'impression, ce qui conduit à des propriétés mécaniques exceptionnelles.
- Propriétés principales :
- Très haute résistance spécifique (rapport résistance/poids), dépassant souvent celle des alliages d'aluminium aérospatiaux standard comme l'AlSi10Mg et même certains grades de titane.
- Excellente ductilité et résistance à la fatigue par rapport aux autres alliages d'aluminium AM à haute résistance.
- Bonne soudabilité (pertinent si un assemblage après fabrication est nécessaire).
- Bonne résistance à la corrosion.
- Conserve sa résistance à des températures modérément élevées mieux que l'AlSi10Mg.
- Adaptabilité aux châssis de drones : Le premier choix pour les applications exigeantes nécessitant une économie de poids maximale sans compromettre la résistance et la durabilité. Idéal pour les drones militaires haute performance, les drones de levage lourds, les drones acrobatiques ou de course et les composants structurels critiques où la défaillance n'est pas une option. Ses propriétés permettent des conceptions hautement optimisées et topologiquement complexes.
- Considérations : La poudre de Scalmalloy® est considérablement plus chère que l'AlSi10Mg en raison de la teneur en scandium et des licences. Elle nécessite des paramètres d'impression soigneusement contrôlés et peut avoir des recommandations spécifiques de post-traitement.
3. A7075 (Variantes usinables par procédé AM) :
- Description : Traditionnellement un alliage d'aluminium corroyé à très haute résistance, contenant du zinc, largement utilisé dans les structures aérospatiales (par exemple, 7075-T6). Historiquement, il était considéré comme très difficile à imprimer en utilisant la fusion sur lit de poudre laser en raison de problèmes tels que le fissurage à chaud. Cependant, les progrès de la modification de la composition de la poudre (par exemple, l'ajout d'éléments de nucléation) et des stratégies sophistiquées de contrôle des procédés ont rendu les versions AM viables.
- Principales propriétés (des variantes AM) :
- Résistance extrêmement élevée, pouvant égaler ou dépasser celle du 7075-T6 forgé traditionnel après un traitement thermique approprié.
- Excellent rapport résistance/poids.
- Bonne résistance à la fatigue.
- Adaptabilité aux châssis de drones : Cible les applications exigeant la plus haute résistance, à l'instar des composants traditionnellement fabriqués à partir de 7075 forgé. Convient aux pièces structurelles fortement sollicitées dans l'aérospatiale et les drones de défense où la performance maximale est essentielle et où les complexités de la fabrication peuvent être gérées.
- Considérations : L'impression des variantes A7075 reste difficile et nécessite une expertise importante en matière de procédés et des paramètres rigoureusement contrôlés pour éviter les défauts tels que les fissures et la porosité. Des traitements thermiques spécifiques sont essentiels pour obtenir les propriétés de haute résistance souhaitées. La disponibilité et le coût de la poudre peuvent être plus élevés que pour l'AlSi10Mg, et la connaissance des procédés peut être moins répandue que pour l'AlSi10Mg ou le Scalmalloy®. Nécessite un fournisseur de services AM en métal très compétent. fournisseur de services AM en métal.
Tableau : Comparaison des poudres d'aluminium AM recommandées pour les châssis de drones
Propriété | AlSi10Mg | Scalmalloy® (alliage d'aluminium) | A7075 (Variantes AM) |
---|---|---|---|
Éléments d'alliage primaire | Silicium (Si), Magnésium (Mg) | Magnésium (Mg), Scandium (Sc), Zirconium (Zr) | Zinc (Zn), Magnésium (Mg), Cuivre (Cu) |
Résistance relative | Bon | Très élevé | Extrêmement élevée (avec un traitement thermique approprié) |
Force spécifique | Bon | Excellent | Excellent |
Ductilité/Allongement | Modéré | Bon | Modérée (peut être inférieure à celle du Scalmalloy®) |
Imprimabilité | Excellent | Bonne (Nécessite des paramètres spécifiques) | Difficile (Nécessite un contrôle expert des procédés) |
Résistance à la corrosion | Bon | Bon | Modérée (Peut être sensible à la corrosion sous contrainte) |
Coût relatif | $$ | $$$$ | $$$ |
Cas d'utilisation typiques des drones | Usage général, prototypes, commercial | Haute performance, aérospatiale/défense, levage lourd | Composants Aérospatiaux/Défense à Très Haute Résistance |
Exporter vers les feuilles
Pourquoi la qualité de la poudre est importante :
Indépendamment de l'alliage choisi, la qualité de la poudre métallique elle-même est essentielle pour la réussite de la fabrication additive. Des facteurs tels que :
- Sphéricité : Des particules lisses et sphériques s'écoulent uniformément et se tassent de manière dense, ce qui conduit à des bains de fusion constants et à des pièces sans vide.
- Distribution de la taille des particules (PSD) : Une granulométrie contrôlée assure une bonne densité du lit de poudre et un comportement de fusion prévisible.
- Fluidité : Un écoulement constant de la poudre est essentiel pour un re-revêtement uniforme du lit de poudre pendant l'impression.
- Pureté et faibles satellites : L'absence de contaminants et de particules irrégulières "satellites" empêche les défauts dans la pièce finale.
Met3dp s'appuie sur des technologies avancées de fabrication de poudres telles que l'atomisation au gaz et le procédé à électrode rotative au plasma (PREP) pour produire poudres métalliques de haute qualité, y compris les alliages d'aluminium, optimisés pour la fabrication additive. Notre contrôle qualité rigoureux garantit que les poudres répondent aux spécifications exigeantes requises pour l'aérospatiale et d'autres applications critiques, permettant à nos clients d'imprimer de manière fiable des châssis de drones denses et performants avec des propriétés mécaniques supérieures. Choisir la bonne poudre et garantir sa qualité sont des premières étapes cruciales pour exploiter la fabrication additive métallique pour la conception de drones de nouvelle génération.
Considérations de conception pour les châssis de drones fabriqués par fabrication additive (DfAM)
Exploiter avec succès la fabrication additive métallique pour les châssis de drones exige plus que la simple conversion d'un fichier CAO existant conçu pour les méthodes traditionnelles. Cela exige un changement de philosophie de conception vers la conception pour la fabrication additive (DfAM). Les principes de la DfAM visent à maximiser les avantages de la fabrication additive - tels que la complexité, l'allègement et la consolidation des pièces - tout en atténuant ses contraintes, comme la nécessité de structures de support et les finitions de surface inhérentes. L'application de la DfAM est cruciale pour la production de châssis de drones en aluminium rentables et performants. Voici les principales considérations pour les ingénieurs et les concepteurs :
- Adopter l'optimisation topologique et la conception générative :
- Ces outils logiciels sont essentiels pour l'allègement. En définissant les cas de charge, les contraintes et les espaces de conception, les algorithmes peuvent générer des formes hautement optimisées, souvent d'aspect organique, qui n'utilisent le matériau que là où cela est structurellement nécessaire.
- Application pour les châssis de drones : Idéal pour les principaux éléments structurels, les supports de moteur et les composants du train d'atterrissage, supprimant la masse inutile tout en garantissant le respect des objectifs de résistance et de rigidité. Cela se traduit directement par des temps de vol plus longs ou une capacité de charge utile accrue.
- Concevoir stratégiquement pour l'orientation :
- La façon dont une pièce est orientée sur le plateau de fabrication a un impact significatif sur le temps d'impression, le volume de la structure de support, la qualité de la surface et potentiellement les propriétés mécaniques (en particulier dans la direction de fabrication de l'axe Z).
- Considérations :
- Minimiser les supports : Orienter la pièce pour réduire les surplombs et les surfaces orientées vers le bas qui nécessitent un support. Les angles autoportants (généralement > 45 degrés par rapport à l'horizontale) doivent être utilisés dans la mesure du possible.
- Finition de la surface : Les surfaces critiques nécessitant une qualité supérieure doivent idéalement être orientées comme des parois verticales ou des surfaces orientées vers le haut. Les surfaces orientées vers le bas ont tendance à avoir des finitions plus rugueuses.
- Temps d'impression : Les orientations plus hautes signifient généralement des temps d'impression plus longs.
- Gestion thermique : L'orientation peut influencer la distribution de la chaleur et l'accumulation de contraintes résiduelles.
- Minimiser et optimiser les structures de support :
- Les structures de support sont souvent nécessaires dans la fusion sur lit de poudre métallique pour ancrer la pièce à la plaque de construction, supporter les éléments en surplomb et évacuer la chaleur de la zone de fusion. Cependant, elles augmentent le temps d'impression, consomment du matériau et nécessitent une suppression en post-traitement, ce qui peut être laborieux et potentiellement endommager la surface de la pièce.
- Stratégies de DfAM :
- Concevoir des éléments autoportants (en utilisant des angles > 45 degrés).
- Remplacer les grands surplombs par des chanfreins ou des congés.
- Utiliser des structures en treillis internes au lieu de surplombs pleins, le cas échéant.
- Concevoir des supports pour un accès et un retrait faciles (par exemple, en utilisant des points de perforation, en concevant des éléments détachables).
- Envisager un logiciel spécialisé de génération de supports pour des structures optimisées et facilement amovibles (par exemple, supports en arbre, supports en bloc).
- Respecter les limites de taille des éléments :
- Les procédés de FA ont des tailles minimales d'éléments imprimables, influencées par la taille du point du faisceau laser (SLM) ou les caractéristiques du faisceau d'électrons (EBM), la taille des particules de poudre et l'épaisseur de la couche.
- Lignes directrices :
- Épaisseur minimale de la paroi : S'assurer que les parois sont suffisamment épaisses pour être imprimées de manière fiable et résister aux charges de manipulation/opérationnelles (généralement 0,4 à 1,0 mm, selon la hauteur, le matériau et la machine). Les parois minces et hautes peuvent être sujettes au gauchissement ou à la défaillance lors de l'impression.
- Taille minimale des trous : Les petits trous (généralement < 0,5 mm) peuvent se refermer pendant l'impression ou être difficiles à débarrasser de la poudre. Concevoir des trous suffisamment grands pour une impression fiable et l'élimination de la poudre, ou prévoir de les percer/aléser en post-traitement. Les trous horizontaux sont souvent plus difficiles que les trous verticaux.
- Éléments en relief/gravés : Assurer une profondeur/hauteur et une largeur suffisantes pour une résolution claire.
- Incorporer des congés et des rayons :
- Les angles internes vifs peuvent agir comme des concentrateurs de contraintes, réduisant potentiellement la durée de vie en fatigue. Ils peuvent également être des points difficiles pour l'accumulation de contraintes thermiques pendant l'impression.
- Meilleure pratique : Appliquer généreusement des congés aux angles internes et des rayons aux arêtes externes pour répartir plus uniformément les contraintes et améliorer l'imprimabilité.
- Concevoir pour le post-traitement :
- La plupart des pièces AM en métal nécessitent un post-traitement. Tenir compte de ces étapes lors de la phase de conception :
- Tolérances d'usinage : Si des tolérances serrées ou des états de surface spécifiques sont requis sur certaines caractéristiques (par exemple, les surfaces d'accouplement, les alésages de palier), ajouter du matériau supplémentaire (stock) à ces zones dans le modèle CAO pour permettre l'usinage CNC après l'impression.
- Accès au retrait des supports : S'assurer que les zones où les supports sont fixés sont accessibles aux outils de retrait sans endommager la géométrie finale de la pièce.
- Elimination des poudres : Pour les canaux internes ou les sections creuses, inclure des trous de drainage/accès stratégiquement placés pour faciliter l'élimination de la poudre non fusionnée après l'impression.
- Traitement thermique : Comprendre si le matériau choisi (comme A7075 ou AlSi10Mg T6) nécessite un traitement thermique et s'assurer que la conception peut résister aux cycles thermiques sans déformation excessive.
- La plupart des pièces AM en métal nécessitent un post-traitement. Tenir compte de ces étapes lors de la phase de conception :
- Tirer parti de la consolidation des pièces :
- Rechercher activement les possibilités de combiner plusieurs composants d'un assemblage traditionnel en une seule pièce imprimée. Analyser les interfaces, les fixations et les étapes d'assemblage.
- Avantages revisités : Réduction du nombre de pièces, élimination des joints/fixations (points de défaillance potentiels), simplification de l'assemblage, souvent réduction du poids total et du coût de production pour les assemblages complexes.
La maîtrise de la DfAM nécessite de l'expérience et souvent une collaboration entre les ingénieurs de conception et les spécialistes de la fabrication additive. Travailler avec un expert fournisseur de services AM en métal qui propose des consultations DfAM peut considérablement rationaliser le processus, en veillant à ce que les conceptions de châssis de drones soient optimisées pour la production additive, ce qui se traduit par des composants plus légers, plus résistants et produits plus efficacement.
Atteindre la précision : Tolérance, état de surface et précision dimensionnelle dans les châssis de drones imprimés
Bien que la fabrication additive métallique offre une liberté géométrique incroyable, il est crucial pour les ingénieurs et les responsables des achats d'avoir des attentes réalistes concernant la précision réalisable directement à la sortie de l'imprimante. Les pièces AM en métal telles que construites ne correspondent généralement pas aux tolérances ultra-élevées et aux états de surface fins réalisables avec l'usinage CNC de précision sans opérations secondaires. Cependant, la compréhension des capacités typiques et des facteurs d'influence permet une conception et une planification efficaces pour répondre aux exigences spécifiques des châssis de drones.
Précision dimensionnelle et tolérances :
- Tolérances typiques telles que construites : Pour des procédés comme le SLM/DMLS utilisant des alliages d'aluminium, les tolérances réalisables typiques se situent souvent dans la plage suivante :
- ±0,1 mm à ±0,2 mm pour les petites caractéristiques (par exemple, jusqu'à 20-50 mm).
- ±0,2 % à ±0,5 % de la dimension nominale pour les caractéristiques plus grandes.
- Facteurs d'influence :
- Étalonnage de la machine : Un étalonnage régulier du système laser/faisceau d'électrons, du scanner et du mouvement de l'axe Z est essentiel.
- Propriétés du matériau : Différents alliages présentent des retraits et un comportement thermique variables lors de l'impression.
- Géométrie et taille de la pièce : Les pièces de grande taille ou complexes sont plus susceptibles aux déformations thermiques et aux écarts.
- Orientation : La direction de construction a un impact sur la précision en raison de la construction couche par couche et des gradients thermiques.
- Structures de soutien : La mise en place et le retrait des supports peuvent influencer la précision locale.
- Contraintes thermiques : L'accumulation de contraintes résiduelles pendant l'impression peut provoquer un gauchissement lors du retrait de la plaque de construction si elle n'est pas correctement gérée (par exemple, par le biais d'une relaxation des contraintes).
- Obtenir des tolérances plus strictes : Lorsque des caractéristiques spécifiques sur le châssis du drone nécessitent des tolérances plus strictes que la capacité telle que construite (par exemple, les logements de roulements, les interfaces de montage du moteur, les surfaces d'assemblage), la pratique standard consiste à concevoir la pièce avec des marges d'usinage (matière supplémentaire) sur ces caractéristiques critiques et à utiliser l'usinage CNC en post-traitement pour obtenir la précision requise (souvent jusqu'à ±0,01 mm ou mieux).
Finition de la surface (rugosité) :
- État de surface tel que construit : La rugosité de surface (généralement mesurée en Ra) des pièces AM métalliques telles que construites est significativement plus élevée que celle des surfaces usinées. Elle est influencée par la taille des particules de poudre, l'épaisseur des couches et l'orientation de la surface.
- Parois verticales : Offrent généralement la meilleure finition telle que construite.
- Surfaces orientées vers le haut : Légèrement plus rugueuses en raison de la nature de la fusion de la couche supérieure.
- Surfaces orientées vers le bas (supportées) : Ont tendance à être les plus rugueuses en raison de l'interaction avec les structures de support et de la physique de la fusion sur la poudre ou les supports non consolidés. Les valeurs Ra peuvent varier considérablement, souvent de 6 µm à 25 µm (ou plus pour les surfaces orientées vers le bas) en fonction du procédé, du matériau et des paramètres spécifiques.
- Amélioration de l'état de surface :
- Orientation : Donner la priorité aux surfaces critiques comme les parois verticales lorsque cela est possible.
- Optimisation des paramètres : L'ajustement fin des paramètres tels que l'épaisseur de couche ou la stratégie laser/faisceau peut avoir un certain impact.
- Post-traitement : C'est la principale méthode pour améliorer significativement l'état de surface :
- Sablage et grenaillage : Fournit une finition mate uniforme, élimine les particules non adhérentes et peut améliorer la durée de vie en fatigue (via la contrainte de compression). Les valeurs Ra s'améliorent généralement pour atteindre ~3-10 µm.
- Finition par culbutage et vibration : Lisse les surfaces et les bords, en particulier pour les lots de petites pièces.
- Usinage CNC : Fournit la meilleure finition de surface possible sur des caractéristiques spécifiques, atteignant Ra < 1 µm si nécessaire.
- Polissage : Polissage manuel ou automatisé pour les exigences esthétiques ou les besoins fonctionnels très spécifiques (par exemple, les surfaces aérodynamiques).
Tableau : Capacités de précision typiques pour les châssis de drones en aluminium fabriqués par fabrication additive
Paramètres | Tel que construit (SLM/DMLS typique) | Après usinage CNC (caractéristiques ciblées) | Considérations pour les châssis de drones |
---|---|---|---|
Tolérance (petites caractéristiques) | ±0,1 à ±0,2 mm | ±0,01 à ±0,05 mm (ou mieux) | Concevoir pour l'usinage sur les interfaces critiques (supports moteur, etc.) |
Tolérance (grandes caractéristiques) | ±0,2 % à ±0,5 % | ±0,01 à ±0,05 mm (ou mieux) | Tenir compte du gauchissement potentiel ; utiliser l'usinage pour les ajustements de précision. |
Finition de la surface (Ra) | 6 µm – 25+ µm | < 1 µm à 3 µm | Tel que construit, souvent acceptable pour les surfaces non critiques ; sabler/usiner les autres. |
Résolution de l'article | ~0,4 mm paroi/élément min. | Limité uniquement par la capacité d'usinage | S'assurer que la fabrication additive (FA) peut produire l'élément de base pour l'usinage. |
Exporter vers les feuilles
Pour les transactions B2B, une communication claire entre le concepteur de l'UAV et le fournisseur de services AM en métal concernant les dimensions critiques, les tolérances et les exigences de finition de surface est essentielle. La définition de ces exigences sur les dessins et la spécification des surfaces nécessitant un post-traitement garantissent que le cadre de l'UAV imprimé et fini répond à toutes les exigences fonctionnelles et d'assemblage. Les étapes de contrôle qualité et d'inspection sont essentielles pour vérifier que la précision spécifiée a été atteinte.
Étapes essentielles de post-traitement pour les cadres d'UAV en aluminium imprimés en 3D
L'impression du cadre de l'UAV en aluminium n'est souvent que la première étape majeure du flux de travail de fabrication. Pour transformer la pièce telle que construite en un composant fonctionnel et fiable, prêt pour l'assemblage, une série d'étapes de post-traitement sont généralement nécessaires. Les étapes spécifiques et leur séquence dépendent de l'alliage choisi, de la complexité de la conception et des exigences de l'application (par exemple, tolérance, finition de surface, propriétés mécaniques). La compréhension de ces étapes est essentielle pour la planification du projet, l'établissement des coûts et l'estimation des délais. Les principales étapes de post-traitement comprennent :
- Traitement thermique de relaxation des contraintes (souvent en premier) :
- Objet : Pour réduire les contraintes résiduelles internes accumulées pendant les cycles rapides de chauffage et de refroidissement du processus d'impression couche par couche. Des contraintes résiduelles élevées peuvent provoquer une déformation ou un gauchissement de la pièce, en particulier après le retrait de la plaque de construction, et peuvent avoir un impact négatif sur les propriétés mécaniques.
- Processus : L'ensemble de la plaque de construction avec la ou les pièces imprimées encore attachées est généralement chauffé dans un four à une température spécifique (inférieure à la température de vieillissement pour les alliages traitables thermiquement), maintenu pendant une période, puis refroidi lentement. Les paramètres varient en fonction de l'alliage d'aluminium (par exemple, AlSi10Mg généralement détendu autour de 300°C).
- Importance : Souvent considéré comme obligatoire pour les pièces critiques sur le plan dimensionnel ou les géométries complexes afin d'assurer la stabilité lors des étapes suivantes.
- Retrait de la pièce de la plaque de construction :
- Objet : Pour séparer le(s) cadre(s) de l'UAV imprimé(s) de la plaque de base métallique sur laquelle ils ont été imprimés.
- Méthodes : Couramment effectué en utilisant :
- L'électroérosion à fil (EDM) : Force précise et minimale appliquée à la pièce, idéale pour les structures délicates.
- Sciage à ruban : Plus rapide et moins coûteux, mais moins précis et nécessite une manipulation prudente. Nécessite un jeu suffisant conçu entre la pièce et la plaque.
- Retrait de la structure de soutien :
- Objet : Pour supprimer les structures de support temporaires requises lors de l'impression.
- Méthodes : Peut aller de la rupture/coupe manuelle (pour les supports facilement accessibles et légèrement connectés) à l'usinage CNC ou au meulage pour les supports plus intégraux ou difficiles d'accès.
- Défis : Peut être laborieux et prendre du temps. Il faut veiller à ne pas endommager la surface de la pièce, en particulier aux points de contact des supports. La DfAM joue un rôle important dans la simplification de cette étape.
- Traitement thermique de mise en solution et de vieillissement (le cas échéant) :
- Objet : Pour obtenir les propriétés mécaniques finales souhaitées (résistance, dureté, ductilité) pour les alliages d'aluminium traitables thermiquement comme l'AlSi10Mg (pour la condition T6) ou les variantes A7075. Généralement non requis pour le Scalmalloy® afin d'obtenir sa haute résistance, bien que des traitements de vieillissement spécifiques puissent être utilisés.
- Processus (Exemple : T6 pour AlSi10Mg) :
- Traitement des solutions : Chauffage à une température élevée (par exemple, ~530°C) pour dissoudre les éléments d'alliage dans la matrice d'aluminium.
- Trempe : Refroidissement rapide (généralement dans l'eau) pour piéger les éléments dans une solution solide sursaturée.
- Vieillissement artificiel : Réchauffage à une température inférieure (par exemple, ~160°C) pendant plusieurs heures pour précipiter les phases de renforcement.
- Importance : Crucial pour maximiser les performances des alliages comme l'AlSi10Mg et l'A7075 dans les applications structurelles exigeantes. Nécessite un contrôle précis du four.
- Finition de la surface :
- Objet : Pour améliorer la rugosité de surface, supprimer les imperfections mineures, obtenir un aspect esthétique souhaité ou préparer les surfaces pour le revêtement.
- Méthodes (comme discuté précédemment) :
- Microbillage / Grenaillage : Crée une finition mate uniforme, nettoie les surfaces, peut améliorer la durée de vie à la fatigue.
- Tambourinage / Finition vibratoire : Lisse les surfaces et les bords, bon pour les lots.
- Polissage : Pour les surfaces lisses et réfléchissantes (moins courant pour les cadres structurels, sauf en cas de nécessité aérodynamique).
- Usinage CNC :
- Objet : Pour obtenir des tolérances serrées sur des caractéristiques spécifiques, créer des surfaces d'accouplement précises, percer/tarauder des trous ou améliorer l'état de surface sur des zones critiques.
- Processus : Utilise des centres d'usinage ou de tournage CNC standard. Nécessite une conception de montage soignée pour maintenir la pièce AM potentiellement complexe en toute sécurité sans distorsion. Comme mentionné dans la DfAM, du matériau supplémentaire doit être inclus dans la conception pour ces opérations.
- Importance : Essentiel lorsque les tolérances AM telles que construites sont insuffisantes pour les exigences fonctionnelles (par exemple, ajustements de roulements, interfaces).
- Nettoyage et inspection :
- Objet : Pour éliminer toute poudre résiduelle, les fluides d'usinage ou les débris, et pour vérifier que la pièce répond à toutes les spécifications.
- Méthodes : Nettoyage par ultrasons, inspection visuelle, inspection dimensionnelle (CMM, numérisation 3D), potentiellement des essais non destructifs (END) comme la tomographie par ordinateur ou les essais par ressuage pour les composants aérospatiaux critiques afin de vérifier l'absence de défauts internes ou de fissures de surface.
L'intégration et l'optimisation de ces étapes de post-traitement sont des compétences clés des fabricants à façon de fabrication additive métallique expérimentés. Les entreprises doivent disposer de systèmes de contrôle qualité robustes et potentiellement de certifications (comme l'AS9100 pour l'aérospatiale) couvrant ces opérations secondaires afin de garantir que le châssis de drone final est livré prêt à l'emploi.
Défis courants de l'impression 3D de châssis de drone et stratégies d'atténuation
Bien que l'impression 3D métallique libère un potentiel important pour les châssis de drone, elle n'est pas sans défis. La connaissance des problèmes potentiels et la mise en œuvre de stratégies d'atténuation efficaces, découlant souvent d'une connaissance approfondie des procédés et d'une expertise en science des matériaux, sont cruciales pour un succès constant. Voici quelques défis courants rencontrés lors de l'impression de châssis de drone en aluminium :
- Déformation et distorsion :
- Cause : Des gradients thermiques élevés pendant l'impression entraînent une accumulation de contraintes résiduelles. Lorsque la pièce est libérée de la plaque de fabrication, ces contraintes peuvent la déformer ou la fausser, s'écartant de la géométrie prévue. Les grandes sections plates ou les conceptions asymétriques sont particulièrement sensibles.
- Stratégies d'atténuation :
- Orientation optimisée : Orienter la pièce pour minimiser les grandes surfaces planes parallèles à la plaque de fabrication.
- Stratégie de support robuste : Utiliser des supports bien conçus pour ancrer solidement la pièce et gérer la dissipation de la chaleur.
- Contrôle des paramètres de procédé : Ajuster avec précision la puissance du laser/faisceau, la vitesse de balayage et la stratégie pour minimiser l'accumulation de contraintes.
- Traitement thermique anti-stress : La réalisation de cette étape avant le retrait de la pièce est souvent essentielle.
- Simulation : Utiliser un logiciel de simulation pour prédire les contraintes et la déformation, ce qui permet d'ajuster la conception ou l'orientation avant l'impression.
- Difficultés liées au retrait de la structure de soutien :
- Cause : Les supports sont nécessaires, mais peuvent être denses, situés dans des zones difficiles d'accès ou fortement liés à la pièce, ce qui rend leur retrait long et potentiellement dommageable.
- Stratégies d'atténuation :
- DfAM : L'approche la plus efficace : concevoir pour minimiser le besoin de supports (angles autoportants, optimisation topologique évitant les surplombs).
- Conception optimisée du support : Utiliser un logiciel pour générer des supports suffisamment solides pendant l'impression, mais plus faciles à retirer (par exemple, points de contact réduits, perforation, types de supports spécifiques comme les supports en forme d'arbre).
- Planification du post-traitement : Sélectionner les méthodes de retrait appropriées (manuelles, usinage CNC) en fonction de l'emplacement et de la conception des supports. Prévoir un accès adéquat dans la conception.
- Porosité (gaz ou manque de fusion) :
- Cause : Vides dans le matériau imprimé. La porosité due aux gaz provient des gaz dissous dans la poudre ou le bain de fusion. La porosité due au manque de fusion se produit lorsque les couches ou les pistes de fusion adjacentes ne fusionnent pas complètement, souvent en raison d'un apport d'énergie insuffisant ou d'une mauvaise répartition de la poudre. La porosité dégrade les propriétés mécaniques, en particulier la durée de vie en fatigue.
- Stratégies d'atténuation :
- Poudre de haute qualité : Utilisation d'une poudre à faible teneur en gaz piégés, avec une granulométrie contrôlée et une sphéricité/fluidité élevée. Approvisionnement auprès de fournisseurs réputés. fournisseurs de poudres métalliques est essentiel.
- Paramètres d'impression optimisés : Assurer une densité d'énergie suffisante (puissance du laser/faisceau, vitesse) pour une fusion et une fusion complètes, tout en évitant la surchauffe qui peut augmenter la porosité due aux gaz.
- Environnement machine approprié : Maintenir la pureté de l'atmosphère de gaz inerte (argon/azote) dans la chambre de fabrication afin de minimiser l'oxydation et la captation de gaz.
- Pressage isostatique à chaud (HIP) : Une étape de post-traitement (chauffage sous haute pression) qui peut fermer les pores internes, bien que cela ajoute un coût et soit généralement réservé aux composants très critiques.
- Rugosité de surface et résolution des détails :
- Cause : Nature inhérente de la construction couche par couche avec des particules de poudre fondues, en particulier sur les surfaces inclinées ou orientées vers le bas. La taille minimale des détails est limitée par la taille du point du faisceau et les caractéristiques de la poudre.
- Stratégies d'atténuation :
- Optimisation de l'orientation : Comme discuté, placer les surfaces critiques de manière optimale.
- Réglage des paramètres : L'utilisation de fines épaisseurs de couche (augmente le temps d'impression) ou de stratégies de faisceau spécifiques peut légèrement améliorer la finition.
- Post-traitement : Le grenaillage, le culbutage, l'usinage ou le polissage sont les principales méthodes pour obtenir les finitions de surface souhaitées.
- DfAM : Concevoir des détails bien au-dessus de la taille imprimable minimale pour la robustesse.
- Fissuration (en particulier avec les alliages à haute résistance) :
- Cause : Certains alliages à haute résistance (comme l'A7075 traditionnel avant les modifications spécifiques à la fabrication additive) sont susceptibles de se fissurer par solidification ou de se déchirer à chaud en raison de leur composition et de la solidification rapide inhérente à la fabrication additive.
- Stratégies d'atténuation :
- Sélection/Modification des alliages : Utilisation d'alliages spécialement conçus ou modifiés pour la fabrication additive (par exemple, Scalmalloy®, variantes d'A7075 optimisées pour la fabrication additive avec des affineurs de grain).
- Paramètres optimisés : Contrôle précis des gradients thermiques grâce au réglage des paramètres.
- Chauffage du substrat/plateau de fabrication : Des températures élevées du plateau de fabrication peuvent réduire les gradients thermiques.
- Expertise en matière de processus : S'appuyer sur une connaissance approfondie de la science des matériaux et des procédés.
Surmonter ces défis nécessite une combinaison de bonnes pratiques de conception (DfAM), de matériaux de haute qualité, d'équipements bien entretenus et calibrés, de paramètres de processus optimisés et de capacités de post-traitement robustes. C'est là que le partenariat avec un fournisseur de fabrication additive (AM) expérimenté et compétent comme Met3dp devient inestimable. Nos décennies d'expertise collective en fabrication additive métallique, englobant des imprimantes SEBM avancées, une production sophistiquée de poudres par atomisation au gaz et PREP, ainsi que des services complets de développement d'applications, nous positionnent pour relever ces défis efficacement. Nous travaillons en étroite collaboration avec les clients, de la conception à l'inspection finale, en tirant parti de notre savoir-faire pour fournir des châssis de drones en aluminium de haute qualité et fiables. Vous pouvez en savoir plus sur les fondements et l'expertise de notre entreprise sur notre À propos de nous page. S'engager avec un partenaire qui s'engage à contrôler les processus et à assurer la qualité réduit considérablement les risques liés à l'adoption de la fabrication additive métallique pour des applications exigeantes telles que les composants de drones.
Choisir le bon partenaire d'impression 3D métal pour les composants de drones
Choisir le bon partenaire de fabrication est aussi crucial que d'optimiser la conception et de sélectionner le matériau approprié pour votre châssis de drone. Les capacités, l'expertise et les systèmes de qualité de votre fournisseur de services de fabrication additive métallique choisi auront un impact direct sur la qualité finale, les performances, le coût et la livraison en temps voulu de vos composants. Pour les ingénieurs et les responsables des achats qui s'orientent dans le paysage des fournisseurs de services de fabrication additive métallique, voici les principaux critères à évaluer :
- Expertise technique et expérience :
- Science des matériaux : Compréhension approfondie des alliages d'aluminium spécifiques (AlSi10Mg, Scalmalloy®, variantes A7075), y compris leur métallurgie, leurs caractéristiques d'imprimabilité et le post-traitement requis pour obtenir les propriétés souhaitées.
- Maîtrise du DfAM : Capacité démontrée à fournir des conseils en matière de conception, en aidant à optimiser les pièces pour la fabrication additive afin de maximiser les avantages tels que l'allègement et de minimiser les défis tels que les structures de support.
- Optimisation des processus : Expérience avérée dans le développement et le contrôle de paramètres d'impression robustes pour des résultats constants et de haute qualité.
- Expérience dans le secteur : Recherchez des études de cas ou une expérience spécifique dans les secteurs de l'aérospatiale, de la défense ou des drones. La connaissance des normes et des attentes de l'industrie est cruciale.
- Technologie et équipement :
- Technologie appropriée : Exploitent-ils la meilleure technologie de fabrication additive pour vos besoins ? (par exemple, SLM/DMLS est courant pour l'aluminium).
- Qualité et étalonnage des machines : Utilisation d'équipements de pointe reconnus pour leur précision et leur fiabilité. Renseignez-vous sur les calendriers de maintenance et les protocoles d'étalonnage.
- Volume de construction : Assurez-vous que leurs machines peuvent s'adapter à la taille des composants de votre châssis de drone.
- Manipulation des poudres : Procédures robustes pour le stockage, la manipulation, le tamisage et le recyclage de la poudre afin de maintenir la qualité de la poudre et d'assurer la traçabilité.
- Capacités en matière de matériaux et contrôle qualité :
- Disponibilité des alliages : Confirmation qu'ils peuvent traiter l'alliage d'aluminium spécifique dont vous avez besoin.
- Approvisionnement et tests de la poudre : Contrôle qualité rigoureux des poudres métalliques entrantes (composition chimique, granulométrie, morphologie, aptitude à l'écoulement). Les fournisseurs comme Met3dp, qui fabriquent leurs propres poudres en utilisant des méthodes avancées comme l'atomisation au gaz et le PREP, ont souvent un avantage pour contrôler et vérifier la qualité de la poudre dès la source.
- Traçabilité des matériaux : Capacité à tracer les lots de poudre tout au long du processus de fabrication, essentielle pour l'assurance qualité, en particulier dans l'aérospatiale.
- Système de gestion de la qualité (SGQ) et certifications :
- ISO 9001 : La certification de base pour une opération de fabrication réputée.
- AS9100 : Très souhaitable, souvent obligatoire, pour les fournisseurs de la chaîne d'approvisionnement aérospatiale et de défense. Indique un SGQ mature adapté aux exigences rigoureuses de l'industrie.
- NADCAP : Accréditation pour les procédés spéciaux tels que le traitement thermique, les essais non destructifs (END) ou le soudage, si ceux-ci sont des éléments essentiels du flux de travail et requis par votre application.
- Capacités complètes de post-traitement :
- En interne ou réseau géré : Évaluez leurs capacités pour les étapes de post-traitement nécessaires (détensionnement, traitement thermique, enlèvement des supports, usinage CNC, finition de surface). Effectuent-ils ces opérations en interne ou par l'intermédiaire de partenaires qualifiés ?
- Expertise : Assurez-vous qu'ils possèdent l'expertise nécessaire pour effectuer ou gérer correctement ces étapes critiques, en particulier le traitement thermique spécifique aux alliages d'aluminium AM.
- Capacité, délai de livraison et communication :
- Capacité de production : Peuvent-ils répondre à vos exigences de volume, des prototypes à la production en série potentielle ?
- Délais de livraison transparents : Capacité à fournir des estimations réalistes pour l'ensemble du processus (impression + post-traitement + inspection) et à communiquer de manière proactive sur tout retard potentiel.
- Réactivité : Bonne communication et support client tout au long du cycle de vie du projet.
- Collaboration et support :
- Approche partenariale : Recherchez un fournisseur prêt à agir en tant que partenaire, offrant des conseils techniques et travaillant en collaboration pour résoudre les problèmes.
- Support DfAM : Volonté d'examiner les conceptions et de suggérer des améliorations pour la fabrication additive.
Choisir un partenaire est une décision stratégique. Des entreprises comme Met3dp se distinguent en offrant des solutions complètes qui englobent des imprimantes SEBM de pointe, une production avancée de poudre métallique et des services de développement d'applications. Nos fondations, construites sur des décennies d'expertise collective en fabrication additive métallique, nous permettent de comprendre les subtilités de la production de pièces critiques pour des industries exigeantes comme l'aérospatiale. Nous privilégions le partenariat et tirons parti de nos capacités verticalement intégrées pour fournir des composants fiables et de haute qualité, tels que des châssis de drones en aluminium léger. Prendre le temps de vérifier minutieusement les fournisseurs potentiels par rapport à ces critères augmentera considérablement la probabilité de réussite d'un projet.
Comprendre les facteurs de coût et les délais de livraison pour les châssis de drones imprimés
Bien que la fabrication additive métallique offre des avantages techniques convaincants, il est essentiel de comprendre les coûts et les délais de livraison associés pour la planification et la budgétisation des projets, en particulier pour les achats B2B. Contrairement à la fabrication traditionnelle où l'outillage domine souvent les coûts pour les faibles volumes, les coûts de la fabrication additive sont déterminés par des facteurs différents.
Principaux facteurs de coût pour les châssis de drones en fabrication additive métallique :
- Consommation de matériaux :
- Type de poudre : Le coût par kilogramme de poudre métallique varie considérablement. Les alliages haute performance comme le Scalmalloy® sont considérablement plus chers que l'AlSi10Mg standard en raison des éléments d'alliage (Scandium) et des licences. Les variantes A7075 AM sont également plus chères.
- Volume de la pièce : Le volume réel de la pièce finale influence directement la quantité de poudre fusionnée.
- Structures de soutien : La poudre utilisée pour les supports s'ajoute à la consommation de matériaux. Une DfAM optimisée pour minimiser les supports permet de réduire ce coût.
- Efficacité du recyclage de la poudre : Bien que la poudre non fusionnée soit largement recyclable, certaines pertes surviennent lors de la manipulation et du traitement.
- Temps d'utilisation de la machine :
- Temps d'impression : Il s'agit souvent d'un facteur de coût principal. Il est déterminé par le volume total à scanner (pièce + supports) et la hauteur de la pièce (nombre de couches). Les facteurs qui l'influencent sont les suivants :
- Taille et complexité de la pièce : Les pièces plus grandes et plus complexes prennent plus de temps.
- Épaisseur de la couche : Des couches plus fines améliorent la résolution, mais augmentent considérablement le temps d'impression.
- Stratégie et paramètres de numérisation : Des paramètres optimisés peuvent équilibrer la vitesse et la qualité.
- Coût de la machine : Le coût de fonctionnement horaire des systèmes de fabrication additive métallique coûteux (y compris l'amortissement, la maintenance, l'énergie, le gaz inerte).
- Temps d'impression : Il s'agit souvent d'un facteur de coût principal. Il est déterminé par le volume total à scanner (pièce + supports) et la hauteur de la pièce (nombre de couches). Les facteurs qui l'influencent sont les suivants :
- Main-d'œuvre et ingénierie :
- Pré-traitement : Préparation des fichiers CAO, optimisation DfAM, planification de l'orientation, génération de supports. Nécessite du temps d'ingénierie qualifié.
- Configuration et surveillance de la fabrication : Préparation de la machine, chargement de la poudre, supervision de la fabrication.
- Main-d'œuvre de post-traitement : Cela peut être important, en particulier pour :
- Suppression du support : Souvent manuel et chronophage pour les pièces complexes.
- Finition de la surface : Finition manuelle ou mise en place de processus automatisés.
- Inspection : Contrôles manuels, programmation/fonctionnement CMM.
- Opérations de post-traitement :
- Traitement thermique : Coûts associés au temps de four, à l'énergie et aux connaissances spécialisées (en particulier pour les traitements sous vide ou en atmosphère contrôlée).
- Usinage CNC : Coûts de la programmation FAO, de la configuration de la machine, du temps d'usinage, de l'outillage et de la main-d'œuvre qualifiée de l'opérateur si des tolérances serrées ou des finitions spécifiques sont nécessaires.
- Traitements de surface : Coûts des services de grenaillage, de tribofinition, de polissage ou de revêtement.
- Assurance qualité et inspection :
- Le niveau d'inspection requis (visuelle, dimensionnelle, CND) et la documentation ont un impact sur le coût. Les composants aérospatiaux exigent généralement une AQ plus rigoureuse, ce qui ajoute au prix global.
Tableau : Facteurs de coût et leur impact
Facteur de coût | Niveau d'impact typique | Notes |
---|---|---|
Type de poudre (alliage) | Haut | Scalmalloy®/A7075 beaucoup plus coûteux que AlSi10Mg. |
Volume/Taille de la pièce | Haut | Impact direct sur l'utilisation des matériaux et le temps d'impression. |
Hauteur de la pièce | Haut | Facteur clé du temps d'impression (nombre de couches). |
Complexité/Supports | Moyen à élevé | Augmente le temps d'impression, l'utilisation des matériaux et la main-d'œuvre de post-traitement. |
Besoins en post-traitement | Moyen à élevé | L'usinage, les finitions poussées, les traitements thermiques complexes ajoutent au coût. |
Main-d'œuvre (configuration et post-traitement) | Moyen | En particulier l'enlèvement des supports et la finition. |
Exigences de qualité | Faible à élevé | Dépend de l'industrie ; les CND et une documentation exhaustive augmentent les coûts. |
Volume de production | Faible à moyen | Le coût par pièce diminue modérément avec le volume (amortissement de la configuration). |
Exporter vers les feuilles
Délais d'exécution typiques :
Les délais de fabrication des châssis de drones en FA métallique sont influencés par de nombreux facteurs similaires à ceux des coûts, notamment la disponibilité des machines, le temps d'impression et l'étendue du post-traitement.
- Prototypage : Pour les prototypes plus simples avec un post-traitement minimal, les délais peuvent varier de 5 à 15 jours ouvrables.
- Pièces de production : Pour les châssis nécessitant un post-traitement complexe (par exemple, traitement thermique, usinage intensif, inspection rigoureuse), les délais peuvent s'étendre à 3 à 6 semaines ou plus, selon la complexité et la quantité.
Facteurs influençant les délais :
- Complexité de la conception et temps d'impression.
- Disponibilité des machines et file d'attente de planification.
- Étapes de post-traitement requises (chacune ajoute du temps).
- Exigences d'inspection.
- Quantité commandée.
- Charge de travail actuelle du fournisseur.
Obtenir un devis d'impression 3D en gros nécessite de fournir des informations détaillées au prestataire de services. Une communication claire sur les exigences, y compris les fichiers CAO, les spécifications des matériaux, les tolérances, les besoins de finition et les certifications requises, permettra aux partenaires potentiels de fournir des estimations de coûts et des délais réalistes.
Foire aux questions (FAQ) sur les châssis de drones en aluminium imprimés en 3D
Voici les réponses à certaines questions courantes que se posent les ingénieurs et les responsables des achats concernant l'utilisation de la fabrication additive métallique pour les châssis de drones :
- Q1 : Quelle est la résistance des châssis de drones en aluminium imprimés en 3D par rapport à ceux usinés ?
- A : La résistance dépend fortement de l'alliage d'aluminium spécifique utilisé et du post-traitement (en particulier le traitement thermique). Par exemple, l'AlSi10Mg imprimé et traité thermiquement à l'état T6 offre une bonne résistance, souvent comparable ou supérieure à celle des composants en aluminium moulé standard et se rapprochant des alliages corroyés comme le 6061-T6. Les alliages de fabrication additive haute performance comme le Scalmalloy® peuvent présenter une résistance spécifique (rapport résistance/poids) supérieure à celle de nombreux alliages d'aluminium haute résistance traditionnels et même de certaines nuances de titane. L'A7075 traité par fabrication additive, lorsqu'il est correctement traité thermiquement, vise à égaler la très haute résistance du 7075-T6 corroyé traditionnel. De plus, la liberté de conception de la fabrication additive permet l'optimisation topologique, en plaçant le matériau uniquement là où il est nécessaire, ce qui se traduit par des châssis beaucoup plus légers pour le même niveau de rigidité ou de résistance par rapport aux pièces conçues et fabriquées de manière traditionnelle.
- Q2 : L'impression 3D métal est-elle rentable pour les châssis de drones ?
- A : Cela dépend de plusieurs facteurs, mais souvent, oui, en particulier dans certains cas. La fabrication additive métallique est très rentable pour :
- Géométries complexes : Les pièces avec des structures internes complexes, des formes organiques issues de l'optimisation topologique ou des caractéristiques intégrées qui sont difficiles ou impossibles à usiner de manière conventionnelle.
- Consolidation partielle : L'impression d'une seule pièce complexe au lieu d'assembler plusieurs pièces plus simples peut permettre d'économiser sur la main-d'œuvre d'assemblage, les fixations et les points de défaillance potentiels.
- Prototypage rapide et production à faible volume : La fabrication additive évite les coûts initiaux élevés et les délais associés à l'outillage (par exemple, moules, matrices, montages complexes).
- Personnalisation : La production de châssis uniques ou personnalisés est possible sans encourir de coûts de réoutillage.
- Applications axées sur la performance : Lorsque les gains de poids et de performances permis par les conceptions de fabrication additive offrent une valeur opérationnelle significative (par exemple, une durée de vol plus longue, une charge utile plus élevée) qui l'emporte sur un coût par pièce potentiellement plus élevé par rapport à une alternative simple et fabriquée de manière traditionnelle. Pour les conceptions de châssis très simples produites en très grands volumes, les méthodes traditionnelles comme l'estampage ou l'usinage CNC à grande vitesse pourraient éventuellement devenir plus rentables par pièce, mais la fabrication additive l'emporte souvent lorsque la complexité, la personnalisation ou les délais de livraison des premiers lots sont des facteurs clés.
- A : Cela dépend de plusieurs facteurs, mais souvent, oui, en particulier dans certains cas. La fabrication additive métallique est très rentable pour :
- Q3 : Quelles informations dois-je fournir pour obtenir un devis précis pour un châssis de drone imprimé en 3D ?
- A : Pour recevoir un devis fiable d'un fournisseur de services de fabrication additive métallique, vous devez fournir autant de détails que possible, notamment :
- Fichier CAO 3D : Un modèle de haute qualité dans un format standard (par exemple, STEP, IGES). Assurez-vous que le modèle est étanche et sans erreur.
- Spécification du matériau : Indiquez clairement l'alliage d'aluminium souhaité (par exemple, AlSi10Mg, Scalmalloy®, variante A7075 AM).
- Dessin technique (facultatif mais recommandé) : Un dessin 2D indiquant les dimensions critiques, les tolérances requises (en utilisant GD&T), les exigences spécifiques de finition de surface (valeurs Ra) sur les caractéristiques clés et les emplacements pour tout usinage ultérieur.
- Quantité : Le nombre de cadres requis (pour les prototypes ou la production en série).
- Exigences en matière de post-traitement : Spécifiez les étapes nécessaires telles que le traitement thermique (par exemple, condition T6), la finition de surface souhaitée (par exemple, finition mate par microbillage, usinage spécifique sur les interfaces) et tous les revêtements requis.
- Tests et certification : Mentionnez tous les tests requis (par exemple, END, vérification des propriétés des matériaux) ou les certifications (par exemple, certificats de matériaux, certificat de conformité, conformité AS9100). Fournir des informations complètes permet au fournisseur de fabrication additive d'évaluer avec précision la fabricabilité, d'estimer les coûts (temps d'impression, matériau, post-traitement) et de déterminer un délai de livraison réaliste.
- A : Pour recevoir un devis fiable d'un fournisseur de services de fabrication additive métallique, vous devez fournir autant de détails que possible, notamment :
Conclusion : Élever les performances des UAV avec des cadres en aluminium imprimés en 3D en métal
Le paysage de la conception et de la fabrication des véhicules aériens sans pilote est en train de subir une transformation significative, motivée par la recherche de performances supérieures, d'une plus grande efficacité et de capacités améliorées. La fabrication additive métallique, en particulier en utilisant des alliages d'aluminium légers et à haute résistance comme l'AlSi10Mg, le Scalmalloy® et l'A7075 optimisé pour la fabrication additive, est à l'avant-garde de cette évolution. Comme nous l'avons exploré, les avantages offerts par la fabrication additive métallique – une liberté de conception inégalée permettant l'optimisation topologique et la consolidation des pièces, une réduction de poids significative conduisant à une endurance de vol et une capacité de charge utile améliorées, un prototypage rapide accélérant l'innovation et la capacité de produire des géométries complexes inatteignables par les moyens traditionnels – en font un outil indispensable pour la création de cadres d'UAV de nouvelle génération.
Exploiter avec succès ces avantages nécessite une approche holistique. Cela commence par l'adoption des principes de la conception pour la fabrication additive (DfAM), en repensant la conception des composants pour tirer pleinement parti du processus couche par couche. Cela implique une sélection minutieuse de l'alliage d'aluminium approprié, en équilibrant les exigences de performance avec la capacité d'impression et le coût. Et surtout, cela dépend du choix du bon partenaire de fabrication – un partenaire doté d'une expertise technique approfondie, de systèmes de qualité robustes, d'équipements de pointe et de capacités complètes allant de la poudre à la pièce finie. La compréhension des nuances des tolérances, des finitions de surface, des étapes essentielles de post-traitement et des défis potentiels permet une planification réaliste et une collaboration efficace. Bien que les facteurs de coût et de délai de livraison doivent être soigneusement pris en compte, la proposition de valeur de la fabrication additive s'étend souvent au-delà du simple prix des pièces, englobant des performances améliorées, un délai de mise sur le marché plus rapide pour les conceptions innovantes et une logistique simplifiée grâce à la consolidation des pièces.
Met3dp se consacre à permettre aux organisations de réaliser tout le potentiel de la fabrication additive métallique. Avec nos systèmes d'impression de pointe, notre expertise dans la production poudres métalliques à haute performance grâce à des techniques d'atomisation avancées, et un support applicatif complet, nous fournissons des solutions de bout en bout adaptées aux exigences exigeantes d'industries telles que l'aérospatiale et la fabrication d'UAV. Nous nous associons à nos clients pour naviguer dans les complexités de l'adoption de la fabrication additive, de la consultation de conception initiale à la livraison de composants entièrement qualifiés et prêts pour la mission. Alors que les UAV continuent de jouer un rôle de plus en plus vital dans divers secteurs, l'impression 3D métallique jouera un rôle déterminant pour repousser les limites du possible, en permettant des plateformes aériennes plus légères, plus solides, plus intelligentes et plus performantes pour l'avenir. Contactez Met3dp dès aujourd'hui pour découvrir comment nos capacités peuvent alimenter les objectifs de fabrication additive de votre organisation et améliorer les performances de vos UAV.
Partager sur
MET3DP Technology Co. est un fournisseur de premier plan de solutions de fabrication additive dont le siège se trouve à Qingdao, en Chine. Notre société est spécialisée dans les équipements d'impression 3D et les poudres métalliques de haute performance pour les applications industrielles.
Articles connexes
À propos de Met3DP
Mise à jour récente
Notre produit
CONTACTEZ-NOUS
Vous avez des questions ? Envoyez-nous un message dès maintenant ! Nous répondrons à votre demande avec toute une équipe dès réception de votre message.
Obtenir les informations de Metal3DP
Brochure du produit
Obtenir les derniers produits et la liste des prix
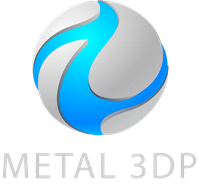
Poudres métalliques pour l'impression 3D et la fabrication additive