Comprendre le moulage par injection de métal (MIM)
Table des matières
Moulage par injection de métal (MIM) est un procédé de fabrication utilisé pour produire de petites pièces métalliques complexes avec des tolérances serrées. Le MIM combine la polyvalence du moulage par injection plastique avec la résistance et l'intégrité des métaux usinés. Cet article fournit une vue d'ensemble détaillée de la technologie MIM, des applications, de l'équipement, du processus, des considérations de conception, etc.
Aperçu du moulage par injection de métal
Le moulage par injection de métal est un procédé de métallurgie des poudres qui permet de produire en grande quantité de petits composants métalliques de précision à l'aide de techniques de moulage par injection.
Comment fonctionne le MIM
Le processus MIM consiste à mélanger une fine poudre de métal avec un liant pour créer une matière première qui peut être injectée dans des moules. Les pièces moulées, appelées pièces vertes, sont ensuite frittées pour éliminer le liant et consolider la poudre de métal en une structure solide. Les étapes de base sont les suivantes :
- Mélange - Une fine poudre métallique est mélangée à des liants pour créer un produit de départ homogène.
- Moulage par injection - La matière première est fondue et injectée dans le moule pour former des pièces vertes.
- Débouclage - Le liant est éliminé par solvant, par voie thermique ou par catalyse.
- Frittage - Les pièces débitées sont frittées pour densifier et renforcer la structure métallique.
- Opérations secondaires - Les étapes de finition supplémentaires telles que l'usinage, le perçage, le taraudage, etc.
Avantages du MIM
Le MIM offre plusieurs avantages par rapport aux autres techniques de fabrication :
- Production en grande quantité avec un faible coût par pièce
- Géométries complexes avec des tolérances serrées
- Variété de matériaux tels que l'acier inoxydable, le titane, le tungstène, le chrome-cobalt, etc.
- Pertes de ferraille et déchets de matériaux réduits au minimum
- Fabrication d'une forme de filet proche réduisant l'usinage
- Petites pièces de 0,005 lb à 0,5 lb
- Consolidation des pièces en combinant les assemblages
- Surfaces lisses et bonne finition
Limites de la MIM
Les limites du moulage par injection de métal sont les suivantes :
- Coûts de démarrage et d'outillage élevés
- Gamme de tailles limitée pour les pièces
- Équipement spécialisé requis
- Processus en plusieurs étapes avec une production plus lente
- Limitations dimensionnelles basées sur les caractéristiques de la poudre
- Restrictions sur la géométrie des pièces en fonction du flux de poudre
Applications du MIM
Le MIM est largement utilisé pour fabriquer de petites pièces complexes avec des tolérances serrées dans des secteurs tels que l'industrie :
- Médical - implants orthopédiques, implants dentaires, instruments chirurgicaux
- Automobile - composants de moteurs, valves, engrenages
- Aérospatiale - aubes de turbines, roues, buses
- Électronique - connecteurs, micro-engrenages, blindage
- Armes à feu - gâchettes, marteaux, sécurités
- Montres - boîtiers, bracelets, couronnes
- Industrie - boutons, attaches, outils de coupe
Le MIM est en concurrence avec d'autres procédés tels que le moulage à la cire perdue, l'usinage et l'emboutissage pour la production de pièces métalliques.
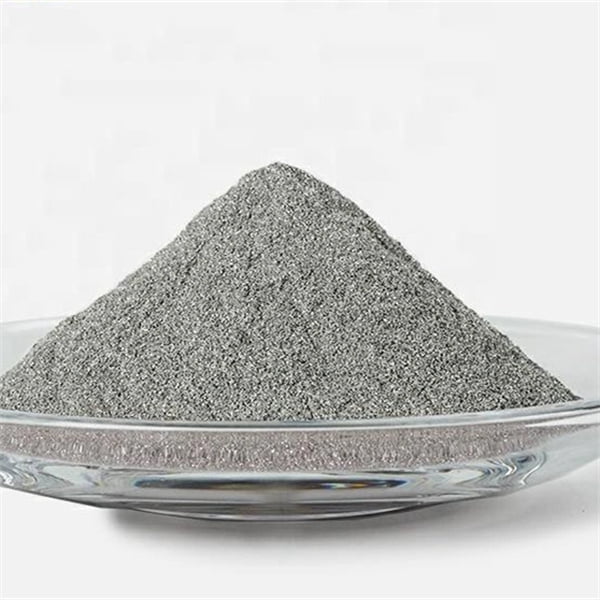
moulage par injection de métaux Guide de l'équipement
Chaque étape du processus de MIM nécessite un équipement spécialisé. Voici les principaux types d'équipement MIM :
Equipement | Fonction |
---|---|
Alimentateurs de poudre | Mesure précise des poudres fines |
Mélangeurs | Mélange homogène de la poudre et du liant |
Granulateurs | Transformer les matières premières en granulés pour le moulage |
Machines de moulage par injection | Mouler les matières premières dans les formes requises |
Fours de débridage | Retirer le liant des pièces moulées |
Fours de frittage | Densifier et renforcer la structure métallique |
Machines à meuler | Enlever les barrières, les patins et les surfaces lisses |
Centres d'usinage | Percer, tourner, fraiser des éléments pour en faire des pièces frittées |
L'automatisation avancée, les systèmes de manutention et les contrôles sont utilisés pour intégrer le processus et maximiser la productivité. L'équipement doit être soigneusement sélectionné en fonction de facteurs tels que le matériau, la taille des pièces, le volume de production et les exigences de qualité.
Moulage par injection de métal Processus étape par étape
Le traitement MIM comprend plusieurs étapes pour transformer une fine poudre de métal en composants finaux entièrement denses.
Étape 1 - Mélange
- La poudre de métal et le liant sont soigneusement mélangés dans un mélangeur pour produire un produit de départ homogène.
- La taille, la forme et la distribution des particules de poudre ont un impact sur la moulabilité et le frittage.
- Les liants assurent l'écoulement et l'adhérence lors du moulage par injection.
- Cires, thermoplastiques tels que PP, PE, PVC et polymères utilisés comme liants
- Mélange effectué à l'aide de pales sigma, de pales Z et de mélangeurs planétaires doubles.
Étape 2 - Granulation
- Le mélange de matières premières est granulé en petites pastilles pour le moulage par injection.
- Améliore le flux des matériaux et évite la ségrégation dans le tonneau
- Les broyeurs utilisent des lames rotatives pour couper la matière première en granulés uniformes.
- La forme et la taille des granulés affectent la densité de l'emballage et la moulabilité.
Étape 3 - Moulage par injection
- Les granulés de matière première sont moulés dans la forme et la taille requises pour la pièce.
- Utilise des machines de moulage par injection modifiées dont la température et la pression sont contrôlées.
- Il est important d'optimiser les paramètres de moulage pour minimiser les défauts
- Les pièces moulées, appelées "pièces vertes", ont une forme mais ne sont pas résistantes.
Étape 4 - Débouclage
- Le liant est extrait des parties vertes par solvant, par voie thermique ou par catalyse.
- Le déliantage par solvant utilise l'action capillaire pour dissoudre le liant.
- Le déliantage thermique décompose le liant dans un four.
- Le déliantage catalytique accélère l'élimination du liant à l'aide d'un catalyseur
- Le déliantage permet de créer des pièces brunes avec une structure poreuse de particules métalliques.
Étape 5 - Frittage
- Les pièces brunes sont frittées dans un four à atmosphère contrôlée.
- Les liaisons entre les particules métalliques sont formées par diffusion et transport de masse.
- Densité presque totale jusqu'à 96-99% obtenue lors du frittage
- Atmosphère, température, durée optimisées pour éviter les défauts
- Retrait du frittage pris en compte lors du moulage
Étape 6 - Opérations secondaires
- Autres étapes du travail des métaux telles que le recuit, l'usinage, le perçage, le placage
- Le recuit soulage les contraintes internes dues au frittage.
- L'usinage CNC enlève les carottes, lisse les surfaces et ajoute des caractéristiques.
- Placage et peinture appliqués à des fins d'amélioration ou de protection contre la corrosion
Le processus MIM permet d'obtenir des pièces métalliques complexes et de haute précision en combinant les avantages du moulage par injection de plastique et de la métallurgie des poudres.
Considérations relatives à la conception des pièces MIM
Le MIM permet des libertés géométriques qui ne sont pas possibles avec l'usinage, mais il faut tenir compte de certaines considérations en matière de conception :
- Epaisseur de la paroi - Gamme typique de 0,3 à 4,0 mm, certaines poudres supportant des parois allant jusqu'à 6 mm.
- Finition de la surface - Finition plus lisse que le moulage mais pas aussi fine que l'usinage ; la valeur Ra de 1 à 4 μm est typique pour le MIM.
- Tolérances dimensionnelles - ±0,1% à ±0,5% en fonction de la géométrie de la pièce, avec une précision de l'ordre du micron possible
- Densité - Une densité maximale de 99% peut être atteinte grâce à un frittage optimisé.
- Géométrie - Il est essentiel d'éviter de piéger les poudres et de permettre aux liants de s'échapper.
- Angles de dépouille - Parois coniques avec des angles de dépouille de 1 à 3° pour faciliter l'éjection des pièces
- Rayons et filets - Les transitions graduelles sont préférables aux angles aigus
- Trous et cavités - Diamètres minimaux de 0,25 à 0,5 mm pour les trous débouchants
- Fils - Peut être moulé mais est souvent usiné après le frittage pour une meilleure précision.
- Détails de la surface - Limiter les détails fins pour réduire l'usure des moules ; les processus de post-moulage peuvent améliorer la qualité des produits.
La conception MIM doit se concentrer sur une géométrie qui maximise les performances plutôt que sur la facilité de fabrication. Le processus permet de consolider des assemblages de plusieurs pièces en une seule, avec des économies significatives en termes de coûts et de poids.
Matériaux utilisés dans le moulage par injection de métal
Le MIM permet de produire des pièces à partir d'une large gamme de métaux, d'alliages et de céramiques dans diverses industries.
Matériau | Applications | Propriétés |
---|---|---|
Acier inoxydable | Médical, armes à feu, marine | Résistance à la corrosion, solidité |
Acier faiblement allié | Automobile, industrie | Réponse magnétique, usinabilité |
Alliages magnétiques doux | Capteurs, actionneurs | Perméabilité élevée |
Alliages de métaux durs | Outils de coupe | Résistance à l'usure, dureté |
Alliages de cuivre | Électronique, thermique | Conductivité électrique |
Alliages d'aluminium | Électrique, thermique | Légèreté, conductivité |
Alliages de titane | Aérospatiale, automobile | Résistance, biocompatibilité |
Alliages de tungstène | Protection contre les rayonnements | Haute densité |
Cermets | Électronique, optique | Résistance à l'oxydation |
Des facteurs tels que la fonction de la pièce, le coût, les étapes de post-traitement et la compatibilité des alliages déterminent le choix idéal du matériau MIM.
Fournisseurs de MIM et fabricants d'équipements
De nombreuses entreprises proposent des matériaux, des services, une production et des équipements de MIM à l'échelle mondiale. Voici quelques-uns des principaux fournisseurs de MIM tout au long de la chaîne de valeur :
Entreprise | Produits/Services |
---|---|
BASF | Matières premières, liants |
Sandvik Osprey | Poudres métalliques |
Höganäs | Poudres métalliques |
Poudre CNPC | Poudres métalliques |
Indo-Mim | Produits et services MIM |
PPM | Produits et services MIM |
Groupe ARC | Produits et services MIM |
Atlas Pressed Metals | Production de pièces MIM |
Epson Atmix | Équipement MIM |
Milacron | Machines de moulage par injection |
Elnik | Fours de frittage |
TCN | Fours de débobinage et de frittage |
Il existe également de nombreux petits acteurs régionaux impliqués dans la chaîne d'approvisionnement du MIM. Les utilisateurs finaux qui souhaitent adopter le MIM peuvent s'associer à des fournisseurs de matériaux et à des fabricants sous contrat en fonction des capacités requises.
Analyse des coûts des pièces MIM par rapport à d'autres solutions
Voici une comparaison des coûts estimés pour la production de 1000 pièces à l'aide de différents procédés de fabrication :
Processus | Coûts de mise en place | Coûts des machines | Coûts d'outillage | Coût partiel | Total (1000 pièces) |
---|---|---|---|---|---|
Usinage CNC | Faible | $100,000 | $2,000 | $50 | $52,000 |
Moulage à la cire perdue | Haut | $500,000 | $40,000 | $20 | $60,000 |
Moulage par injection de métal | Haut | $750,000 | $100,000 | $15 | $115,000 |
Estampillage | Haut | $1,000,000 | $150,000 | $10 | $160,000 |
- L'usinage CNC présente de faibles volumes, des coûts de pièces élevés et une complexité limitée.
- Le moulage à la cire perdue est préférable pour les volumes allant jusqu'à 10 000 unités.
- Le MIM présente des avantages pour les volumes moyens à élevés et les géométries complexes.
- L'emboutissage a des coûts d'outillage très élevés, mais le prix des pièces est le plus bas pour des volumes importants, supérieurs à 100 000 pièces.
Le point de passage où le MIM devient plus économique que les autres procédés dépend des volumes, de la complexité et de la taille.
Choisir un fournisseur ou un partenaire MIM
Le choix d'un fournisseur ou d'un partenaire de production MIM compétent est crucial pour une production de pièces rentable. Voici quelques éléments clés à prendre en compte :
- Expertise technique - Expérience préalable avec des pièces, des matériaux et des secteurs d'activité similaires dans le domaine du MIM
- Systèmes de qualité - Certification ISO 9001, pratiques de contrôle de la qualité
- Capacité de production - Capacité à répondre aux besoins actuels et futurs en termes de volume
- Processus secondaires - Capacités d'usinage, d'emboutissage, de placage et de peinture
- Optimisation des pièces - Concevoir un support MIM pour maximiser les avantages
- Prototypage - Services de prototypage rapide pour valider les conceptions
- Capacités d'outillage - Conception et fabrication d'outils en interne de préférence
- Accès aux matières premières - Canaux d'approvisionnement établis pour les matières premières
- Capacités de R&D - Recherche et développement continus dans le domaine des matériaux et des techniques de fabrication avancés
- L'orientation client - Réactivité aux besoins et approche de la collaboration
- Structure des coûts - Modèle de tarification et compétitivité pour les volumes prévus
- Logistique - Capacité à livrer des pièces de manière fiable tout en respectant les délais de livraison.
La hiérarchisation de ces facteurs permettra d'identifier le partenaire stratégique MIM le mieux adapté à une application particulière.
Installation de l'équipement MIM
Pour les entreprises qui installent des capacités de MIM en interne, il est essentiel de procéder à une installation correcte de l'équipement. Voici quelques éléments clés à prendre en compte :
- Espace au sol d'environ 2 000 à 5 000 pieds carrés nécessaire pour la ligne MIM
- Alimentation électrique stable d'une capacité de 200 à 600 kVA requise
- Conduites d'air comprimé conçues pour une pression de 100 psi
- Ventilation par aspiration pour la chaleur, les émissions et le dépoussiérage
- Services publics tels que l'azote, l'eau de traitement et l'approvisionnement en gaz
- Contrôle de la température et de l'humidité d'environ 20±3 °C, 50±20%
- Mezzanines, plates-formes pour l'installation d'équipements auxiliaires
- Systèmes de manutention tels que les palans, les chariots élévateurs à fourche, les bacs
- Salle de contrôle, systèmes informatiques de surveillance
- Formation du personnel à la sécurité des processus et au fonctionnement des équipements
- Simulations de processus, essais pour valider l'installation
- Calendriers d'étalonnage et de maintenance préventive
Un espace adéquat, des services publics et des conditions contrôlées sont essentiels au bon fonctionnement de l'équipement MIM. Des essais et une formation approfondis préparent à la production réelle.
MIM Maintenance des équipements
Une maintenance régulière améliore le temps de fonctionnement et les performances des équipements de production de MIM. Aspects clés :
- Programme de maintenance préventive documenté pour chaque machine
- Nettoyage quotidien des déversements de matériaux, des fuites, de la poussière et des débris
- Vérification des niveaux de liquide, des fuites, des bruits inhabituels, des vibrations
- Surveillance des pressions, des températures et de la consommation d'énergie
- Essai des systèmes de chauffage, de refroidissement et de contrôle
- Remplacement des pièces d'usure telles que les tamis, les vis, les barils
- Inspections de la fatigue des composants, des dommages, de l'alignement
- Reconstructions et révisions régulières en fonction du nombre d'heures de fonctionnement
- Suivi des journaux de maintenance pour analyse
- Stockage des pièces de rechange pour les composants critiques
- Formation à l'utilisation correcte des équipements et à la sécurité
- Service et soutien opportuns de la part des fournisseurs d'équipement
Un personnel bien formé et une collaboration avec les fournisseurs d'équipement permettent de maximiser la productivité de l'équipement MIM tout en minimisant les temps d'arrêt.
Logiciel de simulation de moulage par injection de métal
Un logiciel de simulation est utilisé pour modéliser numériquement le processus MIM avant la production réelle. Les avantages sont les suivants
- Prévision des schémas de remplissage des moules et optimisation de l'emplacement des portes
- Identifier les lignes de soudure et les pièges à air pour éviter les défauts
- Étude des gradients thermiques et de la solidification dans des géométries complexes
- Simulation des effets du profil de déliantage et de frittage sur la forme finale
- Valider les conceptions d'outillage avant la fabrication
- Réduire les coûts des essais grâce au prototypage virtuel
- Former le personnel à l'aide de représentations visuelles
Parmi les logiciels commerciaux de simulation de MIM, on peut citer
- MIMSIM - Simulation intégrée pour le moulage par frittage
- Sigma Soft - Analyse FEM 3D du remplissage et de la distorsion des moules
- Netzsch MIMPre - Modélisation des propriétés rhéologiques des matières premières du MIM
- Simufact Additive - Simulation multiphysique des processus d'AM
- EOS PSW - Simulation axée sur le frittage et le traitement thermique
L'utilisation d'un logiciel de MIM améliore la cohérence du processus, optimise la qualité des pièces et réduit les coûts de prototypage physique. Un flux de travail intégré de la simulation à la production est préférable.
Dépannage des défauts courants du MIM
Voici quelques défauts typiques des pièces MIM et leurs causes potentielles :
Défaut | Causes |
---|---|
Coups courts | Faible pression d'injection, solidification prématurée |
Flash | Moules surchargés, dégâts causés par les moisissures |
L'arrêt de travail | Refroidissement non uniforme, problèmes de liant |
Fissures | Frittage rapide, teneur élevée en liant |
Porosité | Mauvaise homogénéisation, gaz piégés |
Contamination | Contamination croisée, atmosphère du four |
Variations dimensionnelles | Problèmes liés aux matières premières, à l'usure des moules, au rétrécissement |
Défauts de surface | Porosité des gaz, fragilisation des métaux liquides |
Inclusions | Matières premières contaminées, obstruction des buses |
Une méthodologie systématique d'analyse des défauts doit être utilisée pour isoler les paramètres du processus à l'origine des défauts et entreprendre des actions correctives telles que l'ajustement de la formulation des matières premières, des paramètres de moulage, des profils de déliantage et de frittage.
Avantages de la technologie MIM
Le MIM offre des avantages significatifs par rapport aux autres méthodes de production de pièces métalliques :
- Complexité - Possibilité de géométries 3D complexes, consolidation des assemblages
- Cohérence - Processus hautement reproductible avec une faible variance des pièces
- Efficacité - Fabrication de formes presque nettes avec moins de déchets de matières premières
- Automatisation - Le processus hautement automatisé réduit la main d'œuvre
- Flexibilité - Large éventail de matériaux tels que les métaux, les céramiques et les composites
- Qualité - Bonne finition de surface et bonnes propriétés mécaniques
- Productivité - Production en grande quantité avec un faible coût par pièce
- Miniaturisation - Micro-composants avec des détails allant jusqu'à 10 μm.
- Durabilité - Efficacité énergétique par rapport à l'usinage
- Coût - Coût total inférieur pour les volumes de production moyens à élevés
Les capacités uniques du MIM favorisent son adoption dans des secteurs aussi divers que l'automobile, l'aérospatiale, la médecine et l'électronique.
Limites du moulage par injection de métal
Malgré ses nombreux avantages, le MIM présente certaines limites :
- Investissement initial élevé en outillage
- Gamme de tailles limitée, généralement inférieure à 65 grammes
- Précision inférieure à celle de l'usinage CNC
- Risques de porosité nécessitant des contrôles de processus
- Choix restreint de matériaux en fonction des caractéristiques de la poudre
- Risques liés à la sécurité des poudres fines
- Contraintes de géométrie des pièces liées à la moulabilité
- Variabilité potentielle d'un lot à l'autre
- Propriétés mécaniques inférieures à celles des matériaux corroyés
- Production limitée de prototypes dans des volumes moindres
- Nécessité d'un usinage secondaire dans de nombreuses applications
- Équipement spécialisé et opérateurs formés nécessaires
Pour les pièces métalliques de très haute précision ou de grande taille produites en faibles volumes, d'autres procédés peuvent être mieux adaptés que le MIM.
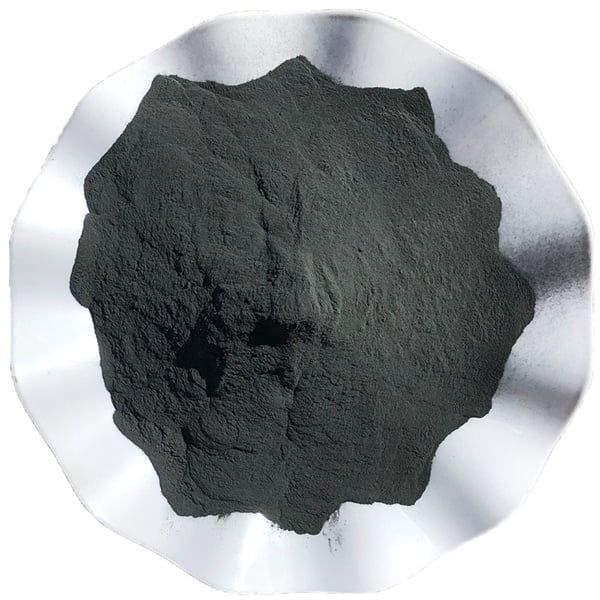
L'avenir du moulage par injection de métal
Le MIM devrait connaître une forte croissance continue grâce à l'amélioration constante de la technologie et des matériaux :
- Nouveaux systèmes de liants pour améliorer la moulabilité et la résistance à l'état vert
- Nouvelles formulations de matières premières utilisant des nanocomposites
- Pièces de grande taille dépassant les limites de courant
- Adoption accrue des céramiques et des alliages de tungstène
- Forte croissance de la demande dans les secteurs médical et électronique
- Utilisation de la fabrication additive pour fabriquer des outils MIM
- Automatisation à l'aide de la robotique et de l'intégration de l'industrie 4.0
- Plus d'applications dans des environnements extrêmes
- Convergence avec l'impression 3D de métaux par dépôt de métal lié
Grâce à l'intensification de la R&D et à une adoption plus facile, l'utilisation de la MIM augmentera rapidement dans diverses applications au cours des prochaines années.
Partager sur
MET3DP Technology Co. est un fournisseur de premier plan de solutions de fabrication additive dont le siège se trouve à Qingdao, en Chine. Notre société est spécialisée dans les équipements d'impression 3D et les poudres métalliques de haute performance pour les applications industrielles.
Articles connexes
À propos de Met3DP
Mise à jour récente
Notre produit
CONTACTEZ-NOUS
Vous avez des questions ? Envoyez-nous un message dès maintenant ! Nous répondrons à votre demande avec toute une équipe dès réception de votre message.
Obtenir les informations de Metal3DP
Brochure du produit
Obtenir les derniers produits et la liste des prix