Comparaison entre la technologie DED et la technologie WAAM
Table des matières
Introduction
Crochet : Imaginez la fabrication d'objets métalliques complexes, couche par couche, avec du métal en fusion déposé méticuleusement pour construire n'importe quoi, des composants de turbines éoliennes aux implants médicaux complexes. Ce domaine captivant appartient au dépôt d'énergie dirigée (DED) et à la fabrication additive par arc électrique (WAAM), deux techniques révolutionnaires de fabrication additive métallique (AM).
Problème : Choisir entre DED et WAAM peut s'avérer une tâche ardue. Les deux offrent des capacités impressionnantes, mais leurs nuances peuvent avoir un impact significatif sur les résultats du projet.
Solution : Cette exploration en profondeur dissèque le DED et le WAAM, en comparant leurs aspects fondamentaux, leurs applications et leur adéquation à divers scénarios.
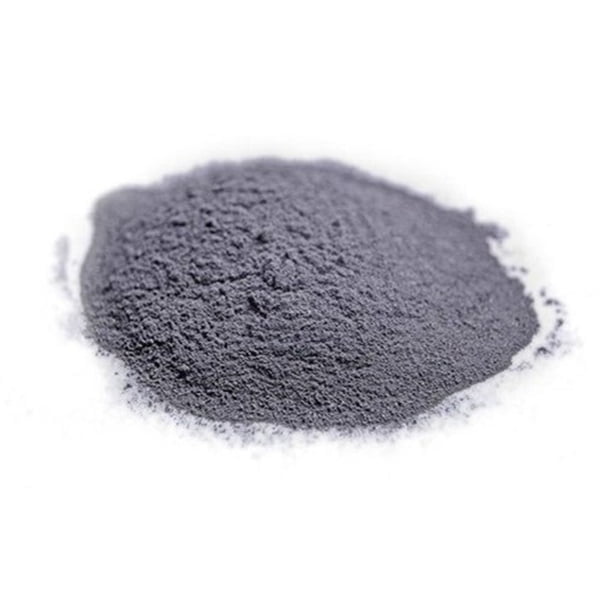
Comprendre la technologie DED
Définition : Le DED est une vaste catégorie de procédés d'AM qui utilisent une source d'énergie concentrée (laser, faisceau d'électrons, arc plasma) pour faire fondre et fusionner un matériau (généralement de la poudre métallique) sur une plateforme de construction, créant ainsi un objet en 3D couche par couche.
Sources de chaleur :
Laser DED : Les lasers haute puissance offrent un contrôle précis et une excellente résolution, ce qui est idéal pour les géométries complexes. Les matériaux les plus courants sont l'acier inoxydable, les alliages de titane et l'Inconel.
Faisceau d'électrons DED : Génère des faisceaux d'énergie très concentrés dans une chambre à vide, permettant une profondeur de fusion supérieure et une compatibilité avec les métaux réactifs tels que le titane.
Arc plasma DED : Utilise une torche à plasma pour faire fondre la matière première, offrant des taux de dépôt plus rapides et un bon rapport coût-efficacité pour les structures plus grandes, en utilisant souvent des fils de soudure courants.
Poudres métalliques pour DED :
Poudre de métal | Description | Avantages | Limites |
---|---|---|---|
Acier inoxydable 316L | Acier austénitique polyvalent connu pour son excellente résistance à la corrosion, sa biocompatibilité et sa grande solidité. | Largement utilisé dans l'aérospatiale, les implants médicaux et le traitement chimique. | Peut nécessiter un post-traitement pour une finition de surface optimale. |
Inconel 625 | Superalliage nickel-chrome réputé pour sa résistance à haute température, sa résistance à l'oxydation et sa résistance au fluage. | Employés dans des applications exigeantes de l'aérospatiale, des turbines à gaz et du nucléaire. | Plus cher que les aciers courants. |
Titane Ti-6Al-4V | Alliage de titane qui offre un bon équilibre entre la solidité, le poids et la résistance à la corrosion. | Populaire dans l'aérospatiale, le biomédical et les articles de sport en raison de sa biocompatibilité. | Susceptible d'être contaminé par l'oxygène pendant l'impression, il doit être manipulé avec précaution. |
Aluminium AlSi10Mg | Alliage combinant une bonne résistance, des propriétés de légèreté et une meilleure coulabilité. | Utilisé dans les applications automobiles, aérospatiales et marines pour réduire le poids. | Hautement réactifs, ils nécessitent des environnements de gaz inertes pour l'impression. |
Acier à outils H13 | Acier à outils pour le travail à chaud, connu pour son excellente résistance à l'usure et à la chaleur. | Employé pour les moules, les matrices et les poinçons utilisés dans les processus de formage et de forgeage des métaux. | Peut être difficile à imprimer en raison de sa forte teneur en carbone. |
Alliage de nickel 718 | Alliage de nickel à haute résistance, durcissant par précipitation, offrant d'excellentes propriétés mécaniques à des températures élevées. | Utilisé dans les composants aérospatiaux pour sa solidité et sa résistance au fluage. | Plus cher que les autres options. |
Cuivre | Métal hautement conducteur avec des applications thermiques et électriques. | Utilisé dans les conducteurs électriques, les échangeurs de chaleur et les composants électroniques. | Sujet à l'oxydation pendant l'impression, nécessitant des mesures de contrôle. |
Chrome cobalt (CoCr) | Alliage biocompatible utilisé pour les implants médicaux résistants à l'usure. | Utilisé dans les prothèses de hanche et de genou en raison de son excellente résistance à l'usure. | Peut nécessiter une manipulation spéciale et un post-traitement pour optimiser la biocompatibilité. |
Inconel 718C | Variation de l'Inconel 625 avec amélioration des caractéristiques de coulée et de soudabilité. | Utilisé dans les aubes de turbines et autres applications à haute température. | Similaire à l'Inconel 625 en termes de propriétés et de limitations. |
Applications du DED : Composants aérospatiaux, implants médicaux, réparation de pièces usées, outillage et structures métalliques à grande échelle.
Démystifier WAAM Technologie
Définition : Le WAAM (Wire Arc Additive Manufacturing) est une variante du DED qui utilise un fil continu et un arc électrique (généralement un soudage à l'arc) pour faire fondre et déposer le matériau.
Avantages :
Rapport coût-efficacité : Le WAAM exploite la technologie de soudage à l'arc existante et les fils facilement disponibles, ce qui en fait une option plus abordable que les procédés DED à base de poudre.
Taux de dépôt élevés : Le WAAM offre des taux de dépôt plus rapides grâce à l'alimentation continue du fil et à la densité d'énergie plus élevée de l'arc, ce qui le rend adapté aux projets de grande envergure.
Compatibilité des matériaux : Le WAAM offre une large compatibilité avec divers fils de soudage courants, notamment :
Acier : Acier doux, acier inoxydable (304L, 316L), acier inoxydable duplex et aciers à outils.
Aluminium : Alliages d'aluminium tels que AlSi10Mg et Al 6061.
Alliages de nickel : Inconel 625 et alliage de nickel 718.
Autres métaux : Cuivre, alliages de titane (utilisation limitée en raison des problèmes d'oxydation).
Applications du WAAM : Construction navale, construction (éléments de ponts, poutres), grands appareils à pression, réparation de machines lourdes et prototypage rapide de grandes structures métalliques.
Considérations clés : DED vs. WAAM
La vitesse d'impression de la technologie DED et WAAM La technologie est différente
- DED : Offre une plus large gamme de vitesses d'impression en fonction de la source de chaleur et du taux d'alimentation en poudre. Le laser DED offre des vitesses plus lentes pour les travaux de haute précision, tandis que l'arc plasma DED permet d'atteindre des vitesses plus élevées pour les constructions plus importantes.
- WAAM : Ce procédé présente généralement les taux de dépôt les plus rapides parmi les procédés DED, grâce à l'alimentation continue du fil et à la densité d'énergie plus élevée de l'arc.
Les coûts des matériaux de la technologie DED et de la technologie WAAM sont différents
- DED : Peut être plus coûteux, en particulier pour les procédés utilisant des poudres métalliques spécialisées comme l'Inconel ou des métaux réactifs comme le titane.
- WAAM : Généralement plus rentable grâce à l'utilisation de fils de soudure facilement disponibles et souvent moins chers.
L'état de surface de la technologie DED et de la technologie WAAM est différent.
- DED : Le DED laser offre les finitions de surface les plus lisses grâce au contrôle précis du faisceau laser. Le DED par faisceau d'électrons permet également d'obtenir de bons états de surface. Le DED par arc plasma, bien que plus rapide, peut nécessiter davantage de post-traitement pour obtenir la qualité de surface souhaitée.
- WAAM : Le WAAM produit généralement des surfaces plus rugueuses que le DED laser en raison des éclaboussures associées au processus de soudage à l'arc. Toutefois, les surfaces WAAM peuvent être usinées ou rectifiées pour obtenir les finitions souhaitées.
Les domaines d'application sont différents
- DED : Il convient parfaitement aux composants complexes et de haute précision nécessitant un excellent état de surface, tels que les pièces aérospatiales, les implants médicaux et les moules.
- WAAM : Il excelle dans les structures métalliques à grande échelle, le prototypage rapide de pièces volumineuses, les composants de construction navale et la réparation de machines massives en raison de ses taux de dépôt élevés et de sa rentabilité.
Coûts d'équipement des technologies DED et WAAM
- DED : Les systèmes DED, en particulier ceux qui utilisent des lasers ou des faisceaux d'électrons, ont tendance à être plus coûteux que les machines WAAM en raison de la complexité de la technologie utilisée.
- WAAM : Les systèmes WAAM tirent souvent parti de la technologie de soudage à l'arc existante, ce qui en fait une option DED plus abordable.
Tableau comparatif des avantages et des limites
Fonctionnalité | DED | WAAM |
---|---|---|
Source de chaleur | Laser, faisceau d'électrons, arc plasma | Arc électrique (soudage à l'arc) |
Matières premières | Poudre de métal | Fil continu |
Taux de dépôt | Variable (Laser DED : lent, Arc Plasma DED : plus rapide) | Haut |
Compatibilité des matériaux | Plus large éventail de matériaux, y compris les métaux réactifs | Principaux matériaux de fil de soudure courants |
Finition de la surface | Peut être très lisse (Laser DED) | Généralement plus rugueux |
Applications | Composants complexes, implants médicaux, moules | Structures à grande échelle, prototypage rapide, réparation |
Coût de l'équipement | Généralement plus élevé | Généralement plus faible |
Coût matériel | Peut être plus élevé pour les poudres spécialisées | Plus faible pour les fils de soudure courants |
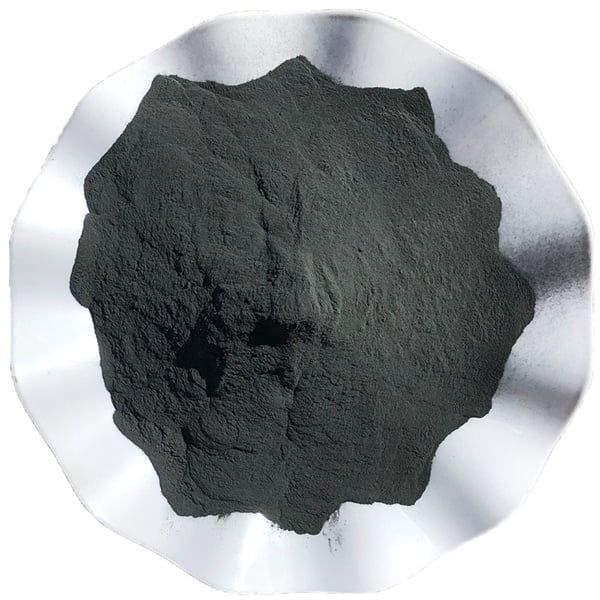
Choisir entre DED et WAAM
Le choix optimal entre DED et WAAM dépend des exigences spécifiques de votre projet :
Pour les pièces complexes avec des finitions de surface critiques et un plus grand choix de matériaux, la DED (en particulier la DED au laser) est probablement le meilleur choix.
Pour les applications à grande échelle, sensibles aux coûts, où la vitesse de dépôt et la disponibilité des matériaux sont des priorités, le WAAM brille.
Autres considérations :
- Complexité du projet : Le DED excelle dans les géométries complexes.
- Exigences matérielles : Le DED offre des options de matériaux plus larges, y compris des métaux réactifs.
- Volume de production : La rapidité du WAAM est un avantage pour les projets de grande envergure.
- Budget : Le WAAM est généralement plus rentable.
L'avenir du DED et du WAAM
Les technologies DED et WAAM évoluent rapidement. On peut s'attendre à des progrès dans les domaines suivants
- Capacités multimatériaux : Le DED et le WAAM peuvent intégrer des fonctionnalités permettant de déposer différents matériaux dans la même construction pour les structures composites.
- Systèmes hybrides DED/WAAM : La combinaison du DED et du WAAM dans une seule machine pourrait offrir une plus grande flexibilité dans la sélection des matériaux et les taux de dépôt.
- Amélioration du contrôle et de l'automatisation : L'amélioration de l'intégration des logiciels et des capteurs permettra un contrôle plus précis du processus d'impression.
FAQ
Q : Quelle est la technologie la plus rapide, DED ou WAAM ?
R : Le WAAM affiche généralement les taux de dépôt les plus rapides parmi les procédés DED. L'alimentation continue du fil et la densité d'énergie plus élevée de l'arc dans le WAAM permettent un dépôt plus rapide du matériau par rapport au DED, en particulier les méthodes DED à base de poudre. Toutefois, le DED laser peut atteindre des vitesses modérées pour les travaux complexes nécessitant une grande précision.
Q : Le DED ou le WAAM sont-ils plus chers ?
R : La WAAM est généralement l'option la plus rentable. Voici un aperçu de la situation :
- Équipement : Les systèmes WAAM tirent parti de la technologie de soudage à l'arc existante, ce qui les rend plus abordables que les machines DED, en particulier celles qui utilisent des lasers ou des faisceaux d'électrons.
- Matériau : Le DED peut être plus coûteux si vous avez besoin de poudres métalliques spécialisées comme l'Inconel ou de métaux réactifs comme le titane. Le WAAM utilise des fils de soudure facilement disponibles et souvent moins chers.
Q : Quelle technologie offre une meilleure finition de surface ?
R : Le DED, en particulier le DED laser, excelle dans la production de finitions de surface lisses en raison du contrôle précis du faisceau laser. Le DED par faisceau d'électrons donne également de bons résultats. Le DED par arc plasma, bien que plus rapide, peut nécessiter davantage de post-traitement pour obtenir la qualité de surface souhaitée. Le WAAM produit généralement des finitions plus rugueuses que le DED par laser en raison des projections associées au processus de soudage à l'arc. Toutefois, les surfaces WAAM peuvent être usinées ou rectifiées pour obtenir une finition plus lisse.
Q : Pour quels types de pièces DED et WAAM conviennent-ils ?
R : Le DED et le WAAM s'adressent à des domaines d'application différents :
- DED : Idéal pour les composants complexes et de haute précision nécessitant un excellent état de surface, tels que.. :
- Pièces pour l'aérospatiale (aubes de turbines, composants de moteurs)
- Implants médicaux (prothèses de hanche, prothèses dentaires)
- Moules et inserts d'outillage
- WAAM : Il excelle dans les structures métalliques à grande échelle et dans les applications où :
- Des taux de dépôt élevés sont essentiels (composants de construction navale, poutres de pont).
- Le prototypage rapide de pièces volumineuses est nécessaire
- Le rapport coût-efficacité est une considération majeure (réparation de machines massives).
Q : Le DED ou le WAAM sont-ils plus respectueux de l'environnement ?
R : Les techniques DED et WAAM peuvent toutes deux être considérées comme respectueuses de l'environnement par rapport aux techniques traditionnelles de fabrication soustractive telles que l'usinage. Voici pourquoi :
- Réduction des déchets matériels : DED et WAAM utilisent des processus additifs, construisant des pièces couche par couche avec un minimum de perte de matière par rapport à l'usinage, qui enlève l'excès de matière.
- Potentiel de recyclage : Les poudres métalliques utilisées dans le DED peuvent potentiellement être recyclées et réutilisées dans des constructions futures, ce qui minimise l'impact sur l'environnement.
En conclusion, Le DED et le WAAM sont des technologies de fabrication additive métallique puissantes qui présentent des atouts et des applications distincts. En comprenant leurs principes fondamentaux, leur compatibilité avec les matériaux et leur adéquation avec les différentes exigences des projets, vous pourrez prendre une décision éclairée sur la technologie qui correspond le mieux à vos besoins. Au fur et à mesure que ces technologies évoluent, nous pouvons nous attendre à des capacités encore plus grandes et à une adoption plus large dans diverses industries.
Partager sur
MET3DP Technology Co. est un fournisseur de premier plan de solutions de fabrication additive dont le siège se trouve à Qingdao, en Chine. Notre société est spécialisée dans les équipements d'impression 3D et les poudres métalliques de haute performance pour les applications industrielles.
Articles connexes
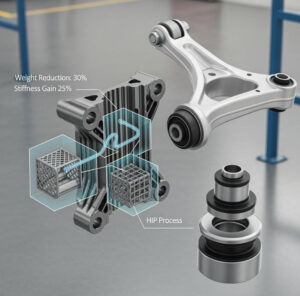
Metal 3D Printed Subframe Connection Mounts and Blocks for EV and Motorsport Chassis
Lire la suite "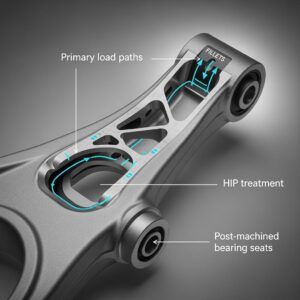
Metal 3D Printing for U.S. Automotive Lightweight Structural Brackets and Suspension Components
Lire la suite "À propos de Met3DP
Mise à jour récente
Notre produit
CONTACTEZ-NOUS
Vous avez des questions ? Envoyez-nous un message dès maintenant ! Nous répondrons à votre demande avec toute une équipe dès réception de votre message.
Obtenir les informations de Metal3DP
Brochure du produit
Obtenir les derniers produits et la liste des prix