Lightweight Satellite Solar Panel Mounts: Revolutionizing Aerospace Engineering with Metal 3D Printing
Table des matières
Introduction – The Critical Role of Lightweighting in Satellite Technology
In the demanding realm of satellite technology, every gram counts. The relentless pursuit of lightweighting drives innovation across all satellite components, and solar panel mounts are no exception. These critical structures must securely deploy and orient solar arrays, the lifeline of any satellite, while enduring extreme environmental conditions. Metal Impression 3D, also known as metal additive manufacturing, is emerging as a transformative technology, offering unprecedented design freedom and material efficiency for creating high-performance, lightweight satellite solar panel mounts. At Métal3DP, we understand the intricate demands of the aerospace industry and are at the forefront of providing advanced metal AM solutions for such mission-critical applications.
What are Lightweight Satellite Solar Panel Mounts Used For? – Applications Across Space Missions
Lightweight satellite solar panel mounts serve a fundamental purpose: to provide a stable and reliable platform for deploying and positioning solar arrays. These arrays are the primary power source for satellites, converting sunlight into the electricity needed to operate onboard systems, including communication payloads, scientific instruments, and propulsion mechanisms. The mounts must withstand significant mechanical stresses during launch and deployment, as well as the harsh thermal cycling and radiation exposure encountered in orbit. Their applications span a wide array of space missions, including:
- Earth Observation Satellites: Providing power for high-resolution imaging and environmental monitoring.
- Communication Satellites: Ensuring continuous power for telecommunications, broadcasting, and internet services.
- Navigation Satellites: Supplying energy for precise positioning and timing systems.
- Scientific Research Satellites: Powering instruments for astrophysics, planetary science, and space weather studies.
- Small Satellites and CubeSats: Enabling efficient power generation for these increasingly popular and cost-effective platforms.
The need for lightweighting in these applications is paramount. Lower mass translates directly to reduced launch costs, increased payload capacity, and improved satellite maneuverability and longevity. By employing advanced metal 3D printing techniques, Métal3DP enables the creation of complex geometries that optimize structural integrity while minimizing weight, directly addressing these critical needs.
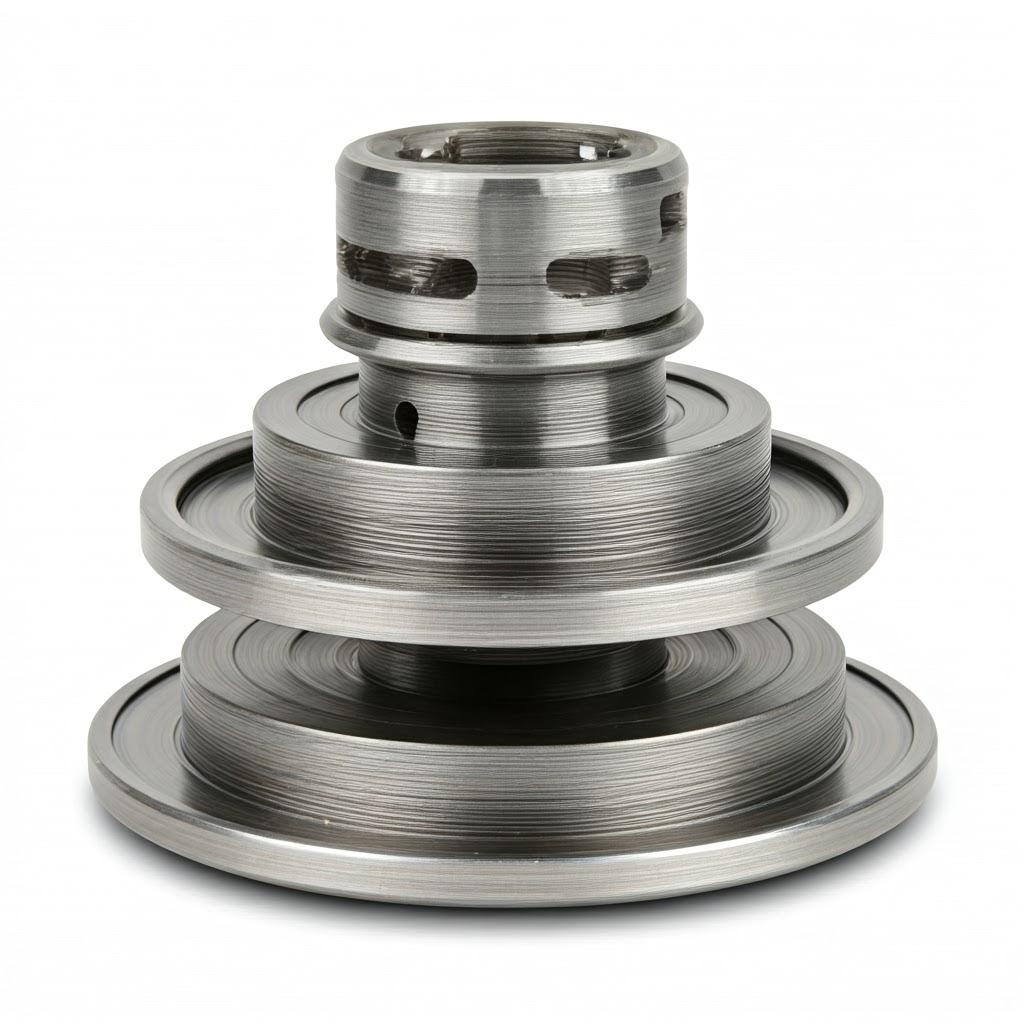
Why Use Metal 3D Printing for Satellite Solar Panel Mounts? – Advantages Over Traditional Manufacturing
Traditional manufacturing methods for satellite components, such as machining and casting, often involve subtractive processes that can lead to significant material waste and limitations in design complexity. Metal 3D printing offers a compelling alternative with numerous advantages for the production of lightweight satellite solar panel mounts:
- Design Freedom and Topology Optimization: Additive manufacturing allows for the creation of intricate lattice structures and organic shapes that are impossible or cost-prohibitive to produce using conventional methods. This enables engineers to optimize the mount’s design for maximum strength-to-weight ratio, removing unnecessary material and significantly reducing mass. Métal3DP excels in leveraging these design flexibilities through its advanced printing technologies.
- Efficacité matérielle : Unlike subtractive methods, 3D printing builds parts layer by layer, using only the material required for the component. This drastically reduces material waste, a significant cost saving, especially when working with expensive aerospace-grade alloys.
- Consolidation partielle : Metal 3D printing allows for the integration of multiple components into a single printed part. This reduces the number of fasteners and assembly steps, leading to lower overall weight, increased reliability, and simplified supply chains.
- Customization and Rapid Prototyping: Additive manufacturing facilitates rapid iteration and customization of designs. This is crucial in the aerospace industry, where requirements can be highly specific and development cycles demanding. Métal3DP provides rapid prototyping services, allowing for quick design validation and optimization.
- Amélioration des performances : By enabling the use of advanced materials and optimized geometries, metal 3D printing can lead to solar panel mounts with superior stiffness, strength, and thermal management properties compared to traditionally manufactured parts.
Recommended Materials and Why They Matter – Scalmalloy® and AlSi10Mg for Optimal Performance
The choice of material is critical for satellite components that must withstand extreme conditions. For lightweight satellite solar panel mounts, Métal3DP recommends and utilizes high-performance metal powders such as Scalmalloy® and AlSi10Mg:
- Scalmalloy® : This high-strength aluminum-magnesium-scandium alloy is specifically designed for lightweight applications in demanding industries like aerospace. Its key properties include:
- Rapport force/poids exceptionnel : Scalmalloy® offers significantly higher strength than conventional aluminum alloys while maintaining low density, making it ideal for mass-critical components.
- Excellente résistance à la fatigue : This is crucial for components subjected to repeated stress cycles during launch and orbital maneuvers.
- Good Weldability and Corrosion Resistance: Important for long-term reliability in the harsh space environment.
- Microstructure fine : Achieved through advanced powder metallurgy and 3D printing processes, ensuring consistent and predictable mechanical properties.
- AlSi10Mg : This aluminum-silicon-magnesium alloy is a widely used material in metal 3D printing due to its excellent balance of properties and processability. Its advantages for satellite solar panel mounts include:
- Bonne résistance et ductilité : Providing sufficient structural integrity for the application.
- Léger : Aluminum alloys are inherently less dense than many other metals, contributing to overall weight reduction.
- Excellente conductivité thermique : Important for dissipating heat generated by the solar panels.
- Bonne résistance à la corrosion : Ensuring longevity in the space environment.
- Rentable : Compared to some other aerospace-grade alloys, AlSi10Mg can offer a more economical solution for certain applications.
Au Métal3DP, our advanced powder making systems ensure the production of high-quality metal powders with high sphericity and good flowability, critical for achieving dense, high-performance 3D-printed parts. Our expertise in materials science and additive manufacturing processes allows us to guide our clients in selecting the optimal material for their specific satellite solar panel mount requirements, ensuring mission success.
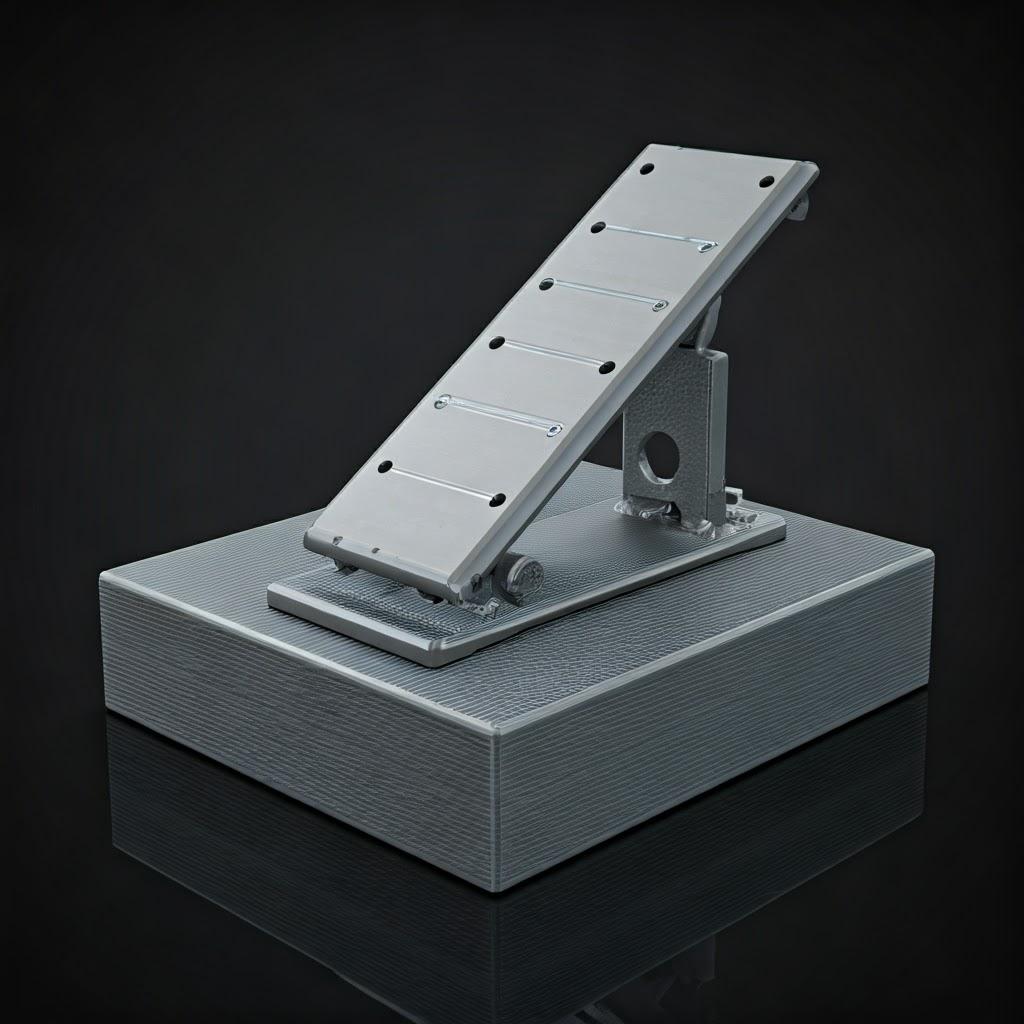
Design Considerations for Additive Manufacturing – Optimizing Geometry for Performance and Weight
Designing for metal additive manufacturing requires a different mindset compared to traditional methods. To fully leverage the capabilities of 3D printing and achieve optimal lightweighting and performance for satellite solar panel mounts, several key design considerations must be taken into account:
- Optimisation de la topologie : This computational method allows engineers to define the functional requirements and constraints of a part and then algorithmically generate an optimized geometry that minimizes weight while maximizing stiffness and strength. Metal 3D printing excels at producing these complex, organic shapes that often result from topology optimization. Métal3DP utilizes advanced software and design expertise to assist clients in implementing topology optimization for their specific applications.
- Structures en treillis : Incorporating lattice structures within the design is a highly effective way to reduce weight without significantly compromising structural integrity. These intricate, repeating cellular patterns can be tailored to provide specific stiffness and energy absorption characteristics. Additive manufacturing is uniquely suited for creating these complex internal geometries.
- Wall Thickness and Ribbing: Careful consideration of wall thickness and the strategic placement of ribs and stiffeners can enhance the structural rigidity of the mount while minimizing material usage. 3D printing allows for the creation of thin-walled structures with internal reinforcement that would be challenging or impossible to produce conventionally.
- Integration of Features: Metal 3D printing enables the integration of multiple functional features directly into the part design. For example, mounting interfaces, cable routing channels, and thermal management features can be incorporated into a single printed component, reducing the need for additional hardware and assembly.
- Orientation and Support Structures: The orientation of the part during the printing process can significantly impact its strength, surface finish, and the amount of support material required. Thoughtful orientation and the design of efficient support structures are crucial for minimizing material waste and post-processing effort. Our team at Métal3DP possesses extensive experience in optimizing part orientation for various metal 3D printing technologies.
- Gestion thermique : Satellite components are subjected to extreme temperature variations in space. Designing features that facilitate heat dissipation, such as internal cooling channels or optimized surface areas for radiative cooling, can be crucial for the long-term performance and reliability of the solar panel mounts. Metal 3D printing offers the flexibility to incorporate these complex thermal management solutions directly into the design.
By considering these design principles and leveraging the unique capabilities of metal additive manufacturing, engineers can create satellite solar panel mounts that are significantly lighter, stronger, and more functional than those produced using traditional methods.
Tolerance, Surface Finish, and Dimensional Accuracy – Achieving Precision in 3D-Printed Mounts
In the aerospace industry, precision is paramount. Satellite components, including solar panel mounts, often have stringent requirements for dimensional accuracy, tolerance, and surface finish to ensure proper fit, functionality, and long-term reliability. Metal 3D printing technologies have made significant advancements in achieving these critical parameters:
- Précision dimensionnelle : The dimensional accuracy achievable with metal 3D printing depends on several factors, including the printing technology used (e.g., Selective Laser Melting (SLM), Electron Beam Melting (EBM)), the material, the part geometry, and the process parameters. Modern metal 3D printers, such as those offered by Métal3DP, can achieve tolerances in the range of ±0.05 mm to ±0.1 mm for critical dimensions.
- Tolérance : Tolerances define the allowable variation in a dimension. Achieving tight tolerances with metal 3D printing often requires careful process control and optimization. Post-processing steps, such as precision machining, can be employed to achieve even tighter tolerances when necessary.
- Finition de la surface : The as-printed surface finish of metal 3D-printed parts is typically rougher than that achieved by machining. The surface roughness depends on the powder particle size, layer thickness, and printing parameters. Common surface roughness values (Ra) for SLM parts range from 5 to 20 μm. For applications requiring smoother surfaces, various post-processing techniques, such as polishing, blasting, and coating, can be applied.
- Facteurs influençant la précision : Several factors can influence the dimensional accuracy and surface finish of metal 3D-printed parts:
- Printer Calibration and Maintenance: Regular calibration and maintenance of the 3D printer are essential for ensuring consistent and accurate results.
- Propriétés du matériau : The flowability, particle size distribution, and thermal conductivity of the metal powder can affect the printing process and the final part accuracy. Métal3DP employs advanced powder making systems to ensure the high quality and consistency of its metal powders.
- Build Orientation and Support Structures: As mentioned earlier, the orientation of the part during printing and the design of support structures can impact dimensional accuracy and surface finish.
- Slicing Parameters: The parameters used to slice the 3D model into layers, such as layer height, scan strategy, and laser power, play a crucial role in the final part quality.
By carefully controlling these factors and employing appropriate post-processing techniques, metal 3D printing can meet the demanding tolerance and surface finish requirements for lightweight satellite solar panel mounts.
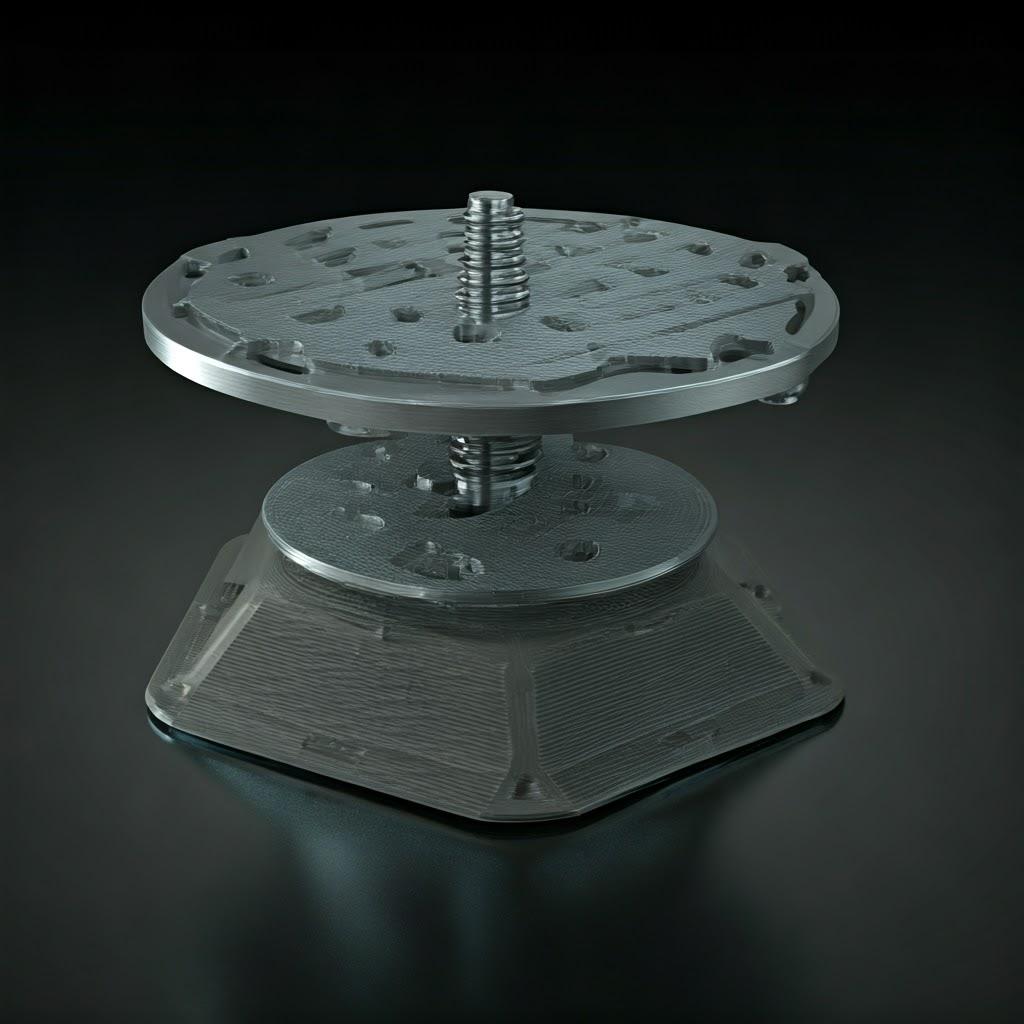
Post-Processing Requirements – Enhancing Functionality and Surface Quality
While metal 3D printing offers significant advantages in terms of design freedom and material efficiency, post-processing steps are often necessary to achieve the final desired properties and surface quality of satellite solar panel mounts:
- Suppression du support : Support structures are often required during the printing process to prevent warping and ensure the stability of overhanging features. These supports need to be carefully removed after printing, which can be a manual or automated process depending on the geometry and the type of support used.
- Traitement thermique : Heat treatment is a crucial post-processing step for many metal 3D-printed parts. It helps to relieve internal stresses that may have built up during the printing process and can also improve the mechanical properties, such as strength and ductility, of the material. The specific heat treatment cycle depends on the material and the desired properties.
- Finition de la surface : As mentioned earlier, the as-printed surface finish may not be suitable for all applications. Techniques such as polishing, sandblasting, shot peening, and chemical etching can be used to achieve smoother surfaces, improve fatigue resistance, and prepare the parts for further processing or coating.
- Usinage CNC : For critical dimensions and tolerances that cannot be achieved directly through 3D printing, CNC machining can be used as a secondary process to achieve the required precision. This hybrid approach combines the design flexibility of 3D printing with the accuracy of traditional machining.
- Coating and Surface Treatments: Depending on the specific application and environmental conditions, coatings or surface treatments may be applied to enhance corrosion resistance, wear resistance, or thermal properties. Examples include anodizing, painting, and specialized aerospace coatings.
- Contrôle de la qualité : Thorough quality inspection is essential to ensure that the 3D-printed and post-processed parts meet the required specifications for dimensional accuracy, surface finish, and material properties. Techniques such as coordinate measuring machines (CMM), non-destructive testing (NDT), and material testing are employed for this purpose.
Métal3DP offers comprehensive post-processing services to ensure that our 3D-printed metal parts meet the highest quality standards required by the aerospace industry. Our expertise in material science and manufacturing processes allows us to tailor the post-processing steps to the specific requirements of each application.
Common Challenges and How to Avoid Them – Ensuring Successful 3D Printing Outcomes
While metal 3D printing offers numerous benefits, there are also potential challenges that need to be addressed to ensure successful outcomes in the production of lightweight satellite solar panel mounts:
- Déformation et distorsion : Thermal stresses during the printing process can lead to warping and distortion of the part, especially for complex geometries or large parts. Careful optimization of the build orientation, support structures, and process parameters can help to minimize these issues.
- Porosité : Porosity, or the presence of voids within the printed part, can negatively impact its mechanical properties. Optimizing the laser or electron beam power, scan speed, and powder bed density are crucial for minimizing porosity. Métal3DP utilizes advanced printing technologies and rigorously controlled processes to produce dense, high-quality parts.
- Difficultés liées au retrait de l'aide : Complex support structures can be challenging to remove without damaging the part. Designing self-supporting geometries or using optimized support designs can mitigate this issue.
- Rugosité de la surface : Achieving the desired surface finish may require significant post-processing effort. Optimizing printing parameters and selecting appropriate post-processing techniques early in the design phase can help to streamline the overall process.
- Material Property Variability: Inconsistent material properties can arise from variations in the powder feedstock or the printing process. Using high-quality metal powders, such as those produced by Métal3DP, and carefully controlling the printing parameters are essential for ensuring consistent and reliable material properties.
- Considérations relatives aux coûts : While metal 3D printing can be cost-effective for certain applications, the initial investment in equipment and materials can be significant. Understanding the cost drivers and optimizing the design for manufacturability can help to control costs.
By understanding these potential challenges and implementing appropriate design strategies, process controls, and post-processing techniques, manufacturers can successfully leverage metal 3D printing to produce high-performance, lightweight satellite solar panel mounts.
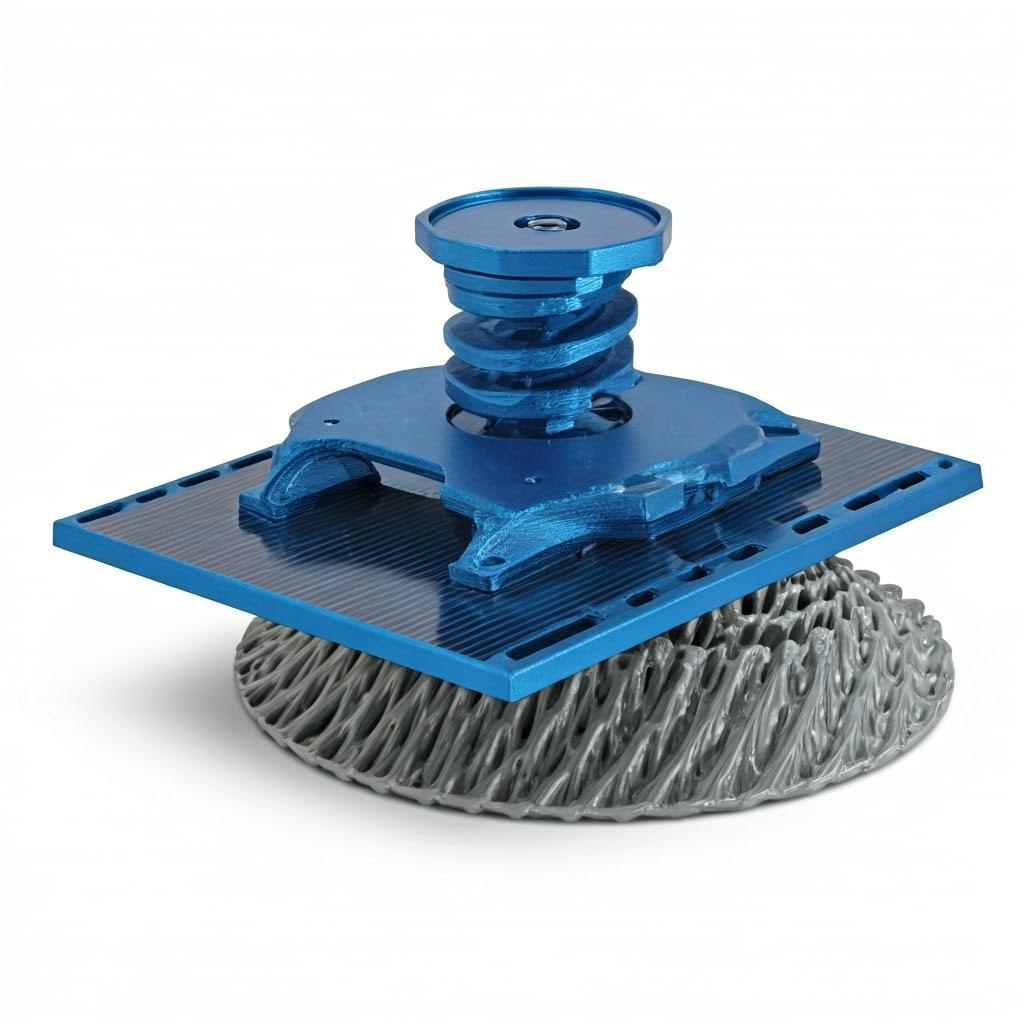
How to Choose the Right Metal 3D Printing Service Provider – Key Considerations for Aerospace Applications
Selecting the right metal 3D printing service provider is a critical decision, especially for demanding applications like satellite components. Here are key factors to consider when evaluating potential partners:
- Capacités matérielles : Ensure the provider has experience working with the specific aerospace-grade alloys required for your application, such as Scalmalloy® and AlSi10Mg. They should also have a robust understanding of the material properties and the optimal printing parameters for these materials. Métal3DP boasts extensive experience with a wide range of high-performance metal powders tailored for aerospace applications.
- Printing Technology and Equipment: Different metal 3D printing technologies (e.g., SLM, EBM) offer varying capabilities in terms of build volume, accuracy, and surface finish. Understand the provider’s technology portfolio and ensure they have the right equipment to meet your specific requirements. Our industry-leading SEBM printers at Métal3DP deliver exceptional print volume, accuracy, and reliability.
- Gestion de la qualité et certifications : For aerospace applications, stringent quality control is paramount. The service provider should have robust quality management systems in place and relevant certifications, such as AS9100 or ISO 9001. This demonstrates their commitment to quality and traceability.
- Design and Engineering Support: An experienced service provider should offer design and engineering support to help optimize your parts for additive manufacturing. This includes guidance on topology optimization, lattice structures, support design, and material selection. Our team at Métal3DP provides comprehensive application development services, leveraging decades of collective expertise in metal additive manufacturing.
- Capacités de post-traitement : Understand the provider’s in-house post-processing capabilities, including support removal, heat treatment, surface finishing, and machining. A comprehensive suite of post-processing services can streamline the production process and ensure the final parts meet your specifications.
- Experience and Expertise: Look for a provider with a proven track record in the aerospace industry and a deep understanding of the unique challenges and requirements of satellite component manufacturing. Case studies and testimonials can provide valuable insights into their experience.
- Communication and Collaboration: Effective communication and a collaborative approach are essential for a successful partnership. 1 The provider should be responsive, transparent, and willing to work closely with your team throughout the project lifecycle. 1. medium.com medium.com
- Lead Times and Scalability: Inquire about the provider’s typical lead times for similar projects and their ability to scale production to meet your future needs.
- Cost Structure: Understand the provider’s pricing model and ensure it aligns with your budget. Consider the total cost of ownership, including design optimization, printing, post-processing, and quality control.
By carefully evaluating these factors, you can select a metal 3D printing service provider like Métal3DP that can deliver high-quality, lightweight satellite solar panel mounts that meet the demanding requirements of your aerospace applications.
Cost Factors and Lead Time – Understanding the Economics of 3D-Printed Mounts
The cost and lead time for producing lightweight satellite solar panel mounts using metal 3D printing are influenced by several factors:
- Coûts des matériaux : The cost of the metal powder (e.g., Scalmalloy®, AlSi10Mg) is a significant factor. Specialized aerospace-grade alloys can be more expensive than standard metals. The quantity of material used, which is directly related to the part’s weight and design optimization, also impacts the overall material cost.
- Temps d'impression : The build time depends on the part’s size, complexity, and the chosen printing technology. Longer print times translate to higher machine utilization costs.
- Coûts de la machine : The cost of operating and maintaining the metal 3D printer is factored into the overall production cost. This includes energy consumption, consumables, and maintenance.
- Coûts de post-traitement : The extent of post-processing required (e.g., support removal, heat treatment, surface finishing, machining) significantly impacts the final cost. Complex geometries that require extensive support removal or tight tolerances necessitating CNC machining will incur higher post-processing costs.
- Design and Engineering Costs: The cost of design optimization for additive manufacturing, including topology optimization and lattice design, as well as engineering analysis and simulation, can be a factor.
- Quality Control Costs: Rigorous quality inspection and testing, which are essential for aerospace applications, contribute to the overall cost.
- Volume de production : The cost per part generally decreases as the production volume increases, due to economies of scale. However, metal 3D printing can still be cost-effective for low to medium volumes, especially for complex, customized parts.
Délai de mise en œuvre: The lead time for metal 3D-printed satellite solar panel mounts is influenced by:
- Design Complexity and Optimization: Intricate designs and extensive optimization processes may require more time upfront.
- Temps d'impression : As mentioned earlier, the build time is a key factor in the overall lead time.
- Durée du post-traitement : The time required for post-processing steps can vary depending on the complexity and the number of processes involved.
- Disponibilité de l'équipement : The availability of the specific metal 3D printer and post-processing equipment at the service provider’s facility can impact lead times.
- Procédures de contrôle de la qualité : Thorough quality inspection can add to the overall lead time.
- Shipping and Logistics: The time required for shipping the final parts to the customer needs to be considered.
Métal3DP is committed to providing transparent and competitive pricing while optimizing lead times through efficient processes and advanced manufacturing capabilities. We work closely with our clients to understand their specific requirements and provide accurate cost and lead time estimates.
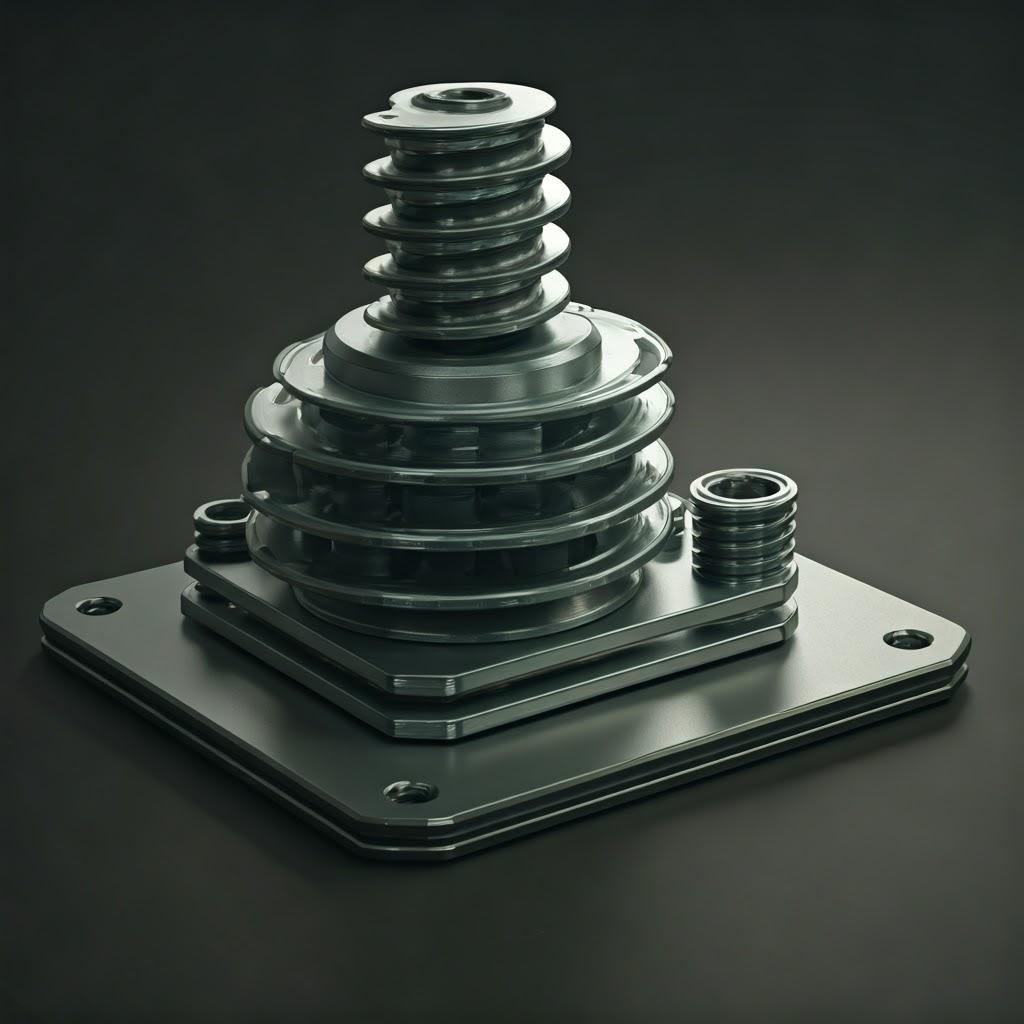
Foire aux questions (FAQ)
- What are the typical weight savings achievable with metal 3D-printed satellite solar panel mounts compared to traditionally manufactured ones? Weight savings can vary significantly depending on the design and the specific application, but reductions of 20% to 50% or even more are often achievable through topology optimization and the use of lattice structures enabled by metal 3D printing.
- Are metal 3D-printed parts strong enough for the harsh environment of space? Yes, when the appropriate materials and printing parameters are used, and proper post-processing is performed, metal 3D-printed parts can meet or exceed the strength and durability requirements for space applications. Alloys like Scalmalloy® offer exceptional strength-to-weight ratios and excellent fatigue resistance.
- Can metal 3D printing be used for large satellite solar panel mounts? Yes, while the build volume of individual printers has limitations, large parts can be produced in sections and then joined using techniques like welding or mechanical fastening. Métal3DP offers printers with industry-leading print volumes to accommodate larger components.
- What is the typical lifespan of a metal 3D-printed satellite solar panel mount in orbit? The lifespan depends on the material used, the design, and the specific orbital environment. However, with proper material selection and design considerations for radiation resistance and thermal cycling, metal 3D-printed mounts can achieve the same lifespan as traditionally manufactured components.
Conclusion – Embracing the Future of Satellite Technology with Metal 3D Printing
Metal 3D printing is revolutionizing the design and manufacturing of lightweight satellite solar panel mounts, offering unprecedented opportunities for weight reduction, performance enhancement, and design innovation. By leveraging advanced materials like Scalmalloy® and AlSi10Mg and embracing the design freedom offered by additive manufacturing, companies can achieve significant cost savings, increased payload capacity, and improved satellite longevity.
Métal3DP stands at the forefront of this technological revolution, providing cutting-edge metal AM equipment, high-quality metal powders, and comprehensive application development services. Our expertise and commitment to quality make us a trusted partner for organizations looking to implement 3D printing and accelerate their digital manufacturing transformations in the aerospace industry. Contact Métal3DP today to explore how our capabilities can power your organization’s additive manufacturing goals and help you achieve the next generation of lightweight satellite technology.
Nuremberg-West, Germany • Update location
Partager sur
MET3DP Technology Co. est un fournisseur de premier plan de solutions de fabrication additive dont le siège se trouve à Qingdao, en Chine. Notre société est spécialisée dans les équipements d'impression 3D et les poudres métalliques de haute performance pour les applications industrielles.
Articles connexes
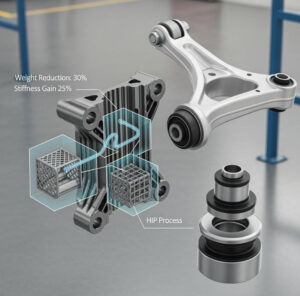
Metal 3D Printed Subframe Connection Mounts and Blocks for EV and Motorsport Chassis
Lire la suite "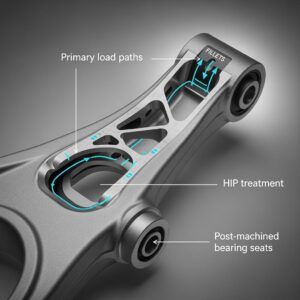
Metal 3D Printing for U.S. Automotive Lightweight Structural Brackets and Suspension Components
Lire la suite "À propos de Met3DP
Mise à jour récente
Notre produit
CONTACTEZ-NOUS
Vous avez des questions ? Envoyez-nous un message dès maintenant ! Nous répondrons à votre demande avec toute une équipe dès réception de votre message.
Obtenir les informations de Metal3DP
Brochure du produit
Obtenir les derniers produits et la liste des prix