La différence entre la technologie EBM et la technologie DMLS
Table des matières
Imaginez que vous construisiez des objets métalliques complexes couche par couche, chaque couche étant méticuleusement fusionnée pour créer un chef-d'œuvre final en trois dimensions. Ce n'est pas de la science-fiction ; c'est la magie de la fabrication additive métallique, également connue sous le nom d'impression 3D. Mais dans ce domaine de la création se trouvent deux titans : la fusion par faisceau d'électrons (EBM) et le frittage laser direct de métaux (DMLS). Bien que toutes deux utilisent des poudres métalliques pour donner vie à des conceptions numériques, elles diffèrent dans leur approche, un peu comme deux artistes habiles maniant des outils différents. Plongeons dans la danse complexe de ces technologies, explorons leurs nuances et identifions le choix idéal pour votre prochain projet.
Les différentes sources d'énergie
EBM exploite la puissance d'un faisceau d'électrons focalisé, agissant comme un accélérateur de particules miniature. Ce faisceau à haute énergie fait fondre les particules de poudre métallique dans une chambre à vide poussé, créant un bain de fusion qui se fond dans les couches environnantes. Imaginez un minuscule pinceau suralimenté en train de fondre méticuleusement de la poudre de métal pour construire votre modèle.
D'autre part, DMLS utilise un puissant laser à fibre comme source de chaleur. Ce faisceau laser balaie le lit de poudre métallique, faisant fondre sélectivement les particules pour former la géométrie souhaitée. Imaginez que vous utilisiez une découpeuse laser sur une feuille de poudre métallique, mais avec une précision incroyable, en construisant l'objet couche par couche.
Voici un tableau résumant les principales différences entre les sources d'énergie :
Fonctionnalité | Fusion par faisceau d'électrons (EBM) | Frittage direct de métaux par laser (DMLS) |
---|---|---|
Source d'énergie | Un faisceau d'électrons | Laser à fibre haute puissance |
Environnement | Chambre à vide poussé | Atmosphère de gaz inerte |
Que signifie cette différence ? L'environnement sous vide poussé de l'EBM minimise l'oxydation, ce qui le rend idéal pour les métaux réactifs tels que le titane et le tantale. À l'inverse, le DMLS utilise une atmosphère de gaz inerte, ce qui offre une plus grande compatibilité avec les poudres métalliques.
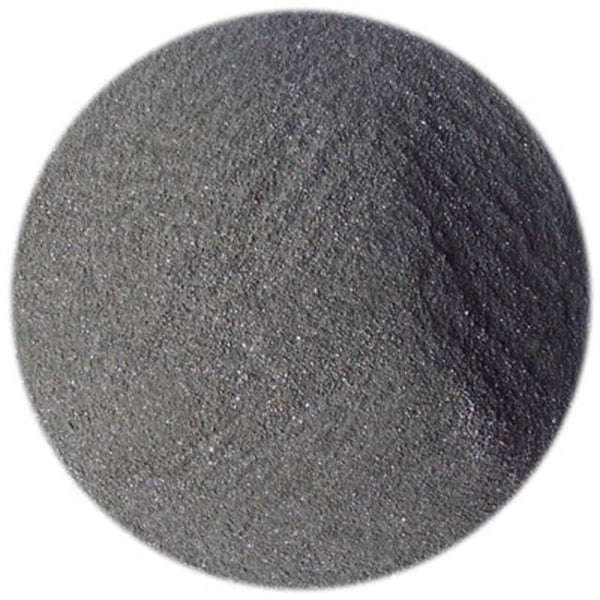
Deux productions ont des vitesses de formage différentes
EBM présente des vitesses de formage impressionnantes grâce à un faisceau d'électrons puissant et hautement focalisé. Cela se traduit par des temps de construction plus courts, en particulier pour les composants de grande taille. Imaginez un artiste compétent travaillant rapidement avec un outil puissant et réalisant son œuvre d'art dans un délai plus court.
DMLSBien que plus lent que l'EBM, il offre un contrôle plus précis du faisceau laser. Cela permet de créer des caractéristiques complexes et des détails plus fins. Imaginez un artiste patient qui sculpte méticuleusement des détails complexes à l'aide d'un outil aiguisé au laser.
Voici un tableau résumant les principales différences en matière de vitesse de formage :
Fonctionnalité | Fusion par faisceau d'électrons (EBM) | Frittage direct de métaux par laser (DMLS) |
---|---|---|
Vitesse de formage | Plus rapide | Plus lent |
Précision des détails | Plus bas | Plus élevé |
Ce qu'il faut en retenir ? Si la vitesse est votre priorité, EBM peut être le meilleur choix. Toutefois, si des détails complexes et des caractéristiques de haute précision sont primordiaux, le DMLS peut être la solution.
La précision du formage est différente
Comme indiqué précédemment, DMLS excelle dans la précision du formage grâce au contrôle précis du faisceau laser. Cela permet de créer des pièces aux caractéristiques plus fines et aux tolérances plus étroites. Imaginez un maître joaillier en train de fabriquer méticuleusement un bijou délicat avec une précision extrême.
EBMBien qu'elle ne soit pas aussi précise que la DMLS, la fusion par faisceau d'électrons peut néanmoins produire des pièces d'une bonne précision dimensionnelle. Toutefois, en raison de la nature du processus de fusion par faisceau d'électrons, l'épaisseur de la couche tend à être légèrement supérieure à celle du DMLS. Imaginez un sculpteur expérimenté travaillant avec des outils un peu plus grands, ce qui donne un produit final un peu moins précis que celui d'un bijoutier délicat.
Voici un tableau résumant les principales différences en matière de précision du formage :
Fonctionnalité | Fusion par faisceau d'électrons (EBM) | Frittage direct de métaux par laser (DMLS) |
---|---|---|
Précision du formage | Bon | Excellent |
Épaisseur de la couche | Légèrement plus épais | Plus mince |
Le résultat ? Si la précision dimensionnelle et les caractéristiques complexes sont cruciales, le DMLS s'impose. Toutefois, l'EBM offre une précision suffisante pour de nombreuses applications, en particulier celles qui privilégient la vitesse à la précision extrême.
Matériaux utilisés de EBM Et les DMLS sont différents
Bien que les deux technologies utilisent des poudres métalliques, les matériaux spécifiques compatibles avec chaque système diffèrent légèrement.
EBM excelle dans le traitement des métaux réactifs tels que :
- Titane (Ti) : Métal léger et résistant couramment utilisé dans l'aérospatiale, les implants médicaux et les composants de haute performance.
- Tantale (Ta) : Métal biocompatible et résistant à la corrosion utilisé dans les implants médicaux et les équipements de traitement chimique.
- Zirconium (Zr) : Métal résistant à la corrosion utilisé dans les réacteurs nucléaires et les équipements de traitement chimique.
DMLS offre une plus large gamme de matériaux compatibles, y compris :
Spécifications, tailles, qualités et normes
En passant d'un ton conversationnel à une approche plus professionnelle, nous allons nous plonger dans le monde critique des poudres métalliques utilisées à la fois dans l'EBM et le DMLS. Ces matériaux finement granuleux constituent les éléments de base des composants métalliques imprimés en 3D, et leurs caractéristiques influencent considérablement les propriétés finales de la pièce. Contrairement à son rôle dans la préparation d'un gâteau, où des variations mineures dans la farine peuvent affecter la texture, des incohérences même légères dans les poudres métalliques peuvent avoir un impact considérable sur la résistance, la finition de surface et la qualité globale de l'objet imprimé. Voici un tableau complet des principales spécifications, tailles, qualités et normes des poudres métalliques utilisées dans la fabrication additive :
Fonctionnalité | Description |
---|---|
Distribution de la taille des particules | Les poudres métalliques sont méticuleusement fabriquées pour obtenir des distributions granulométriques spécifiques, généralement comprises entre 15 et 100 microns. Imaginez un tamis calibré avec précision ; la taille des particules choisie est directement liée à la finition de surface réalisable sur la pièce imprimée. Les poudres plus fines, semblables à de la farine tamisée, produisent des surfaces plus lisses. Cependant, il y a un compromis crucial à faire. Les poudres excessivement fines peuvent présenter une moins bonne fluidité, ce qui empêche leur distribution régulière au cours du processus d'impression. Cela peut entraîner des incohérences et des défauts dans le produit final. À l'inverse, les poudres plus grossières peuvent s'écouler plus facilement, mais risquent d'entraîner une finition de surface plus rugueuse et une porosité potentielle (minuscules trous d'air) dans le composant imprimé. Le choix de la distribution granulométrique optimale nécessite un examen minutieux de l'application spécifique et du résultat souhaité. |
Morphologie des particules | La forme des particules de poudre joue un rôle essentiel dans la densité de l'emballage et la fluidité. Les particules sphériques, semblables à des roulements à billes microscopiques, sont généralement préférées pour des performances d'impression optimales. Elles présentent des caractéristiques d'écoulement supérieures, se tassent étroitement et minimisent les vides dans le lit de poudre. Cela se traduit par une meilleure précision dimensionnelle, de meilleures propriétés mécaniques et une finition de surface plus lisse sur la pièce imprimée. Toutefois, la production de poudres métalliques parfaitement sphériques peut s'avérer difficile et coûteuse. Les particules équiaxes, bien qu'elles ne soient pas des sphères parfaites, offrent un bon équilibre entre la fluidité et la densité de tassement. Les particules de forme irrégulière peuvent poser des problèmes. Elles peuvent mal s'écouler, créer des lacunes dans le lit de poudre et avoir un impact négatif sur l'intégrité structurelle du produit final. |
Chimie des poudres | La composition précise de la poudre, y compris les oligo-éléments et les alliages, influence considérablement les propriétés finales de la pièce imprimée. Tout comme les ingrédients exacts d'une formulation pharmaceutique déterminent son efficacité, la composition chimique de la poudre métallique dicte les caractéristiques du composant imprimé. Par exemple, la poudre de titane pour les applications aérospatiales peut avoir des niveaux d'oxygène et d'azote légèrement différents de la poudre de titane de qualité médicale pour les implants. Ces variations apparemment mineures peuvent influencer des facteurs tels que la solidité, la résistance à la corrosion, la biocompatibilité et les performances globales de la pièce imprimée. Les fabricants de poudres métalliques appliquent des mesures rigoureuses de contrôle de la qualité pour s'assurer que leurs poudres répondent aux normes industrielles spécifiques et aux exigences des applications. |
Fluidité des poudres | La capacité de la poudre à s'écouler librement est cruciale pour une distribution uniforme au cours du processus d'impression. Imaginez que vous versiez du sable dans un sablier : il doit s'écouler de manière fluide et régulière. Une bonne fluidité permet la formation d'un lit de poudre uniforme, une étape critique dans les procédés EBM et DMLS. Les poudres dont la fluidité est médiocre peuvent entraîner un dépôt inégal, ce qui se traduit par des incohérences et des défauts dans la pièce imprimée finale. Les fabricants mesurent la fluidité à l'aide de tests normalisés pour s'assurer que leurs poudres répondent aux exigences spécifiques de chaque technologie d'impression. |
Pureté de la poudre | La pureté de la poudre métallique affecte directement les propriétés mécaniques et les performances de la pièce imprimée. Les impuretés telles que l'oxygène, l'azote et d'autres éléments peuvent entraver le processus de liaison entre les particules métalliques pendant l'impression. Il en résulte des pièces plus fragiles et plus sensibles aux fissures et aux ruptures. Les fabricants de poudres métalliques appliquent des mesures strictes de contrôle de la qualité pour minimiser les impuretés et s'assurer que leurs poudres répondent aux normes de pureté requises pour diverses applications. |
Normes industrielles pour les poudres métalliques dans la fabrication additive :
Plusieurs normes industrielles établies régissent les spécifications et la qualité des poudres métalliques pour la fabrication additive :
- ASTM International (ASTM) : Organisation mondialement reconnue qui développe et publie des normes techniques pour une large gamme de matériaux, y compris les poudres métalliques pour l'AM. Les normes ASTM définissent les exigences relatives à la distribution de la taille des particules, à la composition chimique, à la fluidité et à d'autres paramètres critiques.
- Société américaine pour les matériaux et les essais (AMSTM) : Société basée aux États-Unis qui se consacre à l'avancement des essais, de la science des matériaux et des technologies telles que la fabrication additive. L'AMSTM élabore des spécifications et des normes pour les poudres métalliques utilisées dans les processus de fabrication additive.
- EOS GmbH : Un des principaux fabricants de systèmes d'impression 3D en métal. EOS publie également des fiches techniques spécifiques pour diverses poudres métalliques, décrivant leurs propriétés et les paramètres d'impression recommandés.
- Fabricants de matériaux : Les fournisseurs de poudres métalliques réputés fournissent souvent des fiches techniques détaillées pour leurs produits, y compris la distribution de la taille des particules, la composition chimique, la fluidité et d'autres spécifications pertinentes.
Un monde de poudres métalliques : Découvrir des exemples concrets
Maintenant que nous avons exploré les principales caractéristiques des poudres métalliques pour la fabrication additive, examinons quelques exemples spécifiques couramment utilisés dans les deux types de fabrication. EBM et DMLS. Il s'agira d'une perspective pratique sur les options disponibles et leur adéquation à diverses applications.
Poudres métalliques pour l'EBM :
En raison du vide poussé qui règne dans la chambre EBM, les poudres métalliques choisies doivent présenter des propriétés exceptionnelles de dégazage. Le dégazage correspond à la libération de gaz piégés dans les particules de poudre au cours du processus de fusion. Un dégazage excessif peut perturber l'environnement sous vide et avoir un impact négatif sur la qualité de la pièce imprimée. Voici quelques poudres métalliques couramment utilisées pour l'EBM :
- Poudre de titane atomisée au gaz (Ti-6Al-4V) : Ce matériau de travail est un alliage de titane contenant 6% d'aluminium et 4% de vanadium. Il offre une excellente combinaison de solidité, d'économie de poids et de résistance à la corrosion. Il est largement utilisé dans l'aérospatiale, les implants médicaux et les composants automobiles de haute performance en raison de sa biocompatibilité et de ses propriétés mécaniques favorables lorsqu'il est traité par EBM.
- Inconel 718 atomisé au gaz : Ce superalliage à base de nickel et de chrome présente une résistance exceptionnelle à haute température et aux environnements difficiles. Sa capacité à résister à des températures extrêmes le rend idéal pour les applications dans les moteurs de turbines à gaz, les échangeurs de chaleur et d'autres composants exposés à des charges thermiques élevées. Le traitement EBM offre un risque de contamination minimal, préservant les propriétés souhaitables de l'Inconel 718.
- Cuivre atomisé au gaz (Cu) : La poudre de cuivre pur est utilisée dans des applications nécessitant une conductivité thermique et électrique élevée. L'EBM permet de créer des dissipateurs thermiques et des composants électriques complexes avec une oxydation minimale en raison de l'environnement sous vide.
Poudres métalliques pour DMLS :
La DMLS offre une plus grande compatibilité de matériaux que l'EBM grâce à l'atmosphère de gaz inerte. Voici quelques poudres métalliques couramment utilisées pour le DMLS :
- Acier inoxydable 316L atomisé au gaz : Cette nuance d'acier inoxydable polyvalente offre une excellente résistance à la corrosion et une grande biocompatibilité. Elle est largement utilisée dans les implants médicaux, les équipements de traitement chimique et les applications nécessitant une résistance aux environnements difficiles. Le traitement DMLS permet de créer des géométries complexes avec de bonnes propriétés mécaniques.
- Alliages d'aluminium atomisés au gaz (AlSi10Mg, etc.) : Les alliages d'aluminium offrent un bon équilibre entre résistance, économie de poids et prix abordable. L'ajout de silicium (Si) et de magnésium (Mg) améliore les caractéristiques de moulage et les propriétés mécaniques. Les alliages d'aluminium sont couramment utilisés dans l'aérospatiale, l'automobile et l'électronique grand public en raison de leur légèreté. Le traitement DMLS permet de créer des composants complexes et légers avec une bonne finition de surface.
- Acier à outils atomisé au gaz (H13, etc.) : Les aciers à outils sont connus pour leur résistance à l'usure et leur dureté exceptionnelles. Le H13 est un choix populaire pour les moules et les matrices en raison de sa capacité à résister aux températures élevées et aux contraintes mécaniques. Le traitement DMLS permet de créer des inserts d'outils complexes avec une bonne précision dimensionnelle.
Voici un tableau résumant certaines caractéristiques clés de ces poudres métalliques :
Poudre de métal | Applications typiques (EBM) | Applications typiques (DMLS) | Principales considérations |
---|---|---|---|
Ti-6Al-4V atomisé au gaz | Aérospatiale, Implants médicaux | Aérospatiale, Implants médicaux | Excellent rapport résistance/poids, biocompatible |
Inconel 718 atomisé au gaz | Moteurs à turbine à gaz, échangeurs de chaleur | Moteurs à turbine à gaz, échangeurs de chaleur | Résistance aux températures élevées et aux environnements difficiles |
Cuivre atomisé au gaz (Cu) | Dissipateurs thermiques, composants électriques | Dissipateurs thermiques, composants électriques | Conductivité thermique et électrique élevée |
Acier inoxydable 316L atomisé au gaz | Implants médicaux, Traitement chimique | Implants médicaux, Traitement chimique | Résistance à la corrosion, biocompatible |
Alliages d'aluminium atomisés au gaz (AlSi10Mg) | Aérospatiale, automobile, électronique grand public | Aérospatiale, automobile, électronique grand public | Léger, bon rapport résistance/poids |
Acier à outils atomisé au gaz (H13) | Moules et matrices | Moules et matrices | Résistance à l'usure et dureté exceptionnelles |
N'oubliez pas que cette liste n'est pas exhaustive. Les fabricants proposent une vaste sélection de poudres métalliques pour la fabrication additive, chacune ayant des propriétés et des certifications uniques. Il est essentiel de consulter des fournisseurs de poudres métalliques réputés et de comprendre les exigences spécifiques de votre application pour sélectionner le matériau le mieux adapté à votre projet d'impression 3D.
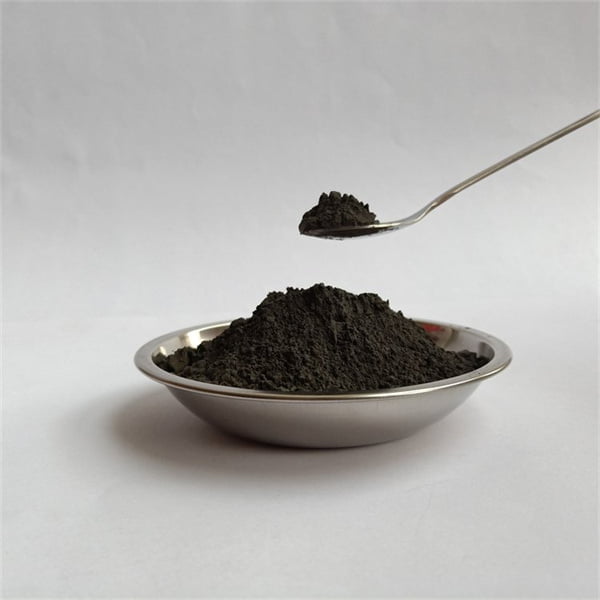
Comparaison entre EBM et DMLS
Après avoir exploré les subtilités des technologies EBM et DMLS, ainsi que le monde des poudres métalliques utilisées dans chaque processus, il est temps de comparer directement ces deux titans de l'impression 3D. Cela vous aidera à prendre une décision éclairée en fonction des besoins spécifiques de votre projet.
Voici un tableau résumant les principales différences entre EBM et DMLS :
Fonctionnalité | Fusion par faisceau d'électrons (EBM) | Frittage direct de métaux par laser (DMLS) |
---|---|---|
Source d'énergie | Un faisceau d'électrons | Laser à fibre haute puissance |
Environnement | Chambre à vide poussé | Atmosphère de gaz inerte |
Vitesse de formage | Plus rapide | Plus lent |
Précision du formage | Bon | Excellent |
Compatibilité des matériaux | Limited (métaux réactifs) | Une plus large gamme de matériaux |
Finition de la surface | Légèrement plus rugueux | Plus lisse |
Porosité | Plus bas | Potentiellement plus élevé |
Pour | Temps de construction plus rapide, bon pour les métaux réactifs, oxydation minimale | Plus grande précision, plus grande compatibilité avec les matériaux, bon état de surface |
Cons | Précision moindre, options de matériaux limitées, consommation d'énergie plus élevée | Temps de construction plus lents, possibilité de porosité plus élevée, peut nécessiter un post-traitement pour certains matériaux. |
Approfondissons ces différences clés pour comprendre quelle technologie pourrait être la mieux adaptée à votre projet :
- Vitesse de construction : Si la vitesse est un facteur critique, l'EBM peut être le meilleur choix. Son faisceau d'électrons très puissant permet une fusion plus rapide et des temps de fabrication plus courts, en particulier pour les composants de grande taille. En revanche, si les détails complexes et la précision dimensionnelle sont primordiaux, le DMLS peut être une meilleure option, même si l'impression prend un peu plus de temps.
- Compatibilité des matériaux : L'EBM excelle dans le traitement des métaux réactifs tels que le titane et le tantale en raison de l'environnement sous vide poussé qui minimise l'oxydation. Le DMLS, quant à lui, offre une plus grande compatibilité de matériaux, y compris l'acier inoxydable, les alliages d'aluminium et les aciers à outils. Ce choix plus large permet une plus grande souplesse de conception en DMLS.
- Précision des pièces et état de surface : La technologie DMLS est la plus performante en termes de précision de formage et de finition de surface. Le contrôle précis du faisceau laser permet de créer des pièces très détaillées avec une finition de surface lisse. L'EBM offre une bonne précision, mais la nature du processus de fusion par faisceau d'électrons peut entraîner une finition de surface légèrement plus rugueuse que celle du DMLS.
- Porosité : La porosité fait référence à de minuscules espaces d'air à l'intérieur du métal imprimé. L'EBM produit généralement des pièces moins poreuses en raison de l'environnement sous vide poussé qui minimise la présence de gaz piégés. Le DMLS, tout en offrant une bonne qualité globale, peut présenter un risque de porosité légèrement plus élevé, en particulier lors de l'utilisation de certains matériaux ou paramètres d'impression. Dans certains cas, les pièces DMLS peuvent nécessiter des techniques de post-traitement telles que le pressage isostatique à chaud (HIP) pour éliminer les vides internes.
- Considérations relatives aux coûts : Le coût de l'impression 3D d'une pièce métallique par EBM ou DMLS dépend de plusieurs facteurs, notamment du matériau choisi, de la complexité de la pièce et du post-traitement requis. Toutefois, en général, l'EBM peut avoir une consommation d'énergie plus élevée en raison de la nécessité d'un environnement à vide poussé. La DMLS peut être une option plus rentable pour certaines applications, en particulier si l'on considère le besoin potentiel de post-traitement avec l'EBM.
Choisir la bonne arme : EBM vs. DMLS - Le verdict final
Il n'y a pas de "vainqueur" unique dans la bataille entre EBM et DMLS. La technologie idéale dépend des besoins spécifiques de votre projet. Voici quelques conclusions pour vous aider à prendre votre décision :
- Pour les projets nécessitant l'impression à grande vitesse de métaux réactifs tels que le titane, et lorsqu'une finition de surface légèrement plus rugueuse est acceptable, l'EBM peut être un bon choix.
- Pour les projets exigeant des détails complexes, une précision dimensionnelle exceptionnelle, une plus grande variété de matériaux et une finition de surface lisse, la DMLS peut être la meilleure option, même si elle prend un peu plus de temps à imprimer.
- Examinez soigneusement les implications financières de chaque technologie, y compris le coût des matériaux, la consommation d'énergie et les besoins éventuels en matière de post-traitement.
Il est toujours conseillé de consulter des professionnels de l'impression 3D expérimentés pour discuter des exigences spécifiques de votre projet et déterminer quelle technologie utiliser, EBM ou DMLS, serait le choix le plus approprié pour obtenir des résultats optimaux.
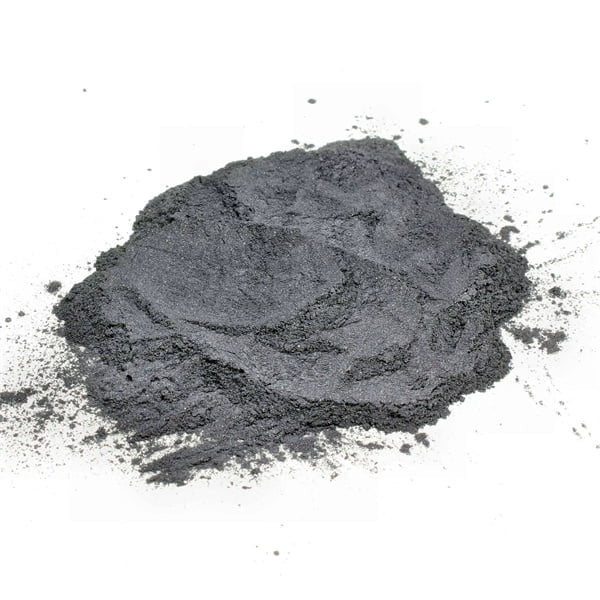
FAQ
Q : Quelle est la technologie la plus performante, EBM ou DMLS ?
R : L'EBM et le DMLS peuvent tous deux produire des pièces métalliques à haute résistance. La résistance réelle dépend de la poudre métallique choisie et des paramètres d'impression spécifiques utilisés. Toutefois, en raison de l'environnement sous vide poussé et d'une porosité potentiellement plus faible, les pièces imprimées par EBM peuvent présenter une résistance légèrement supérieure pour certains métaux réactifs comme le titane.
Q : Puis-je utiliser EBM ou DMLS pour imprimer des pièces métalliques colorées ?
R : Bien que l'EBM et la DMLS se concentrent principalement sur la création de pièces métalliques fonctionnelles, il existe quelques techniques limitées de post-traitement qui permettent d'introduire de la couleur à la surface. Ces techniques impliquent généralement l'application d'une fine couche de revêtement coloré ou l'infiltration d'une résine colorée. Toutefois, il peut être difficile d'obtenir des couleurs vives ou homogènes, et la durabilité à long terme de ces applications colorées peut être limitée. Si la couleur est une exigence essentielle, d'autres technologies d'impression 3D telles que le jet de liant ou la fusion multijet pourraient être plus appropriées, car elles offrent une plus large gamme d'options de couleur directement dans le processus d'impression.
Q : Les pièces imprimées par EBM ou DMLS sont-elles respectueuses de l'environnement ?
R : L'impact environnemental de l'EBM et du DMLS dépend de plusieurs facteurs, notamment de la poudre métallique choisie, de la consommation d'énergie pendant le processus d'impression et de toutes les étapes de post-traitement nécessaires. La production de poudre métallique elle-même peut être énergivore. L'EBM, en raison de son environnement sous vide poussé, peut avoir une empreinte énergétique légèrement supérieure à celle de la DMLS. Cependant, les deux technologies offrent des avantages significatifs en termes de complexité des pièces et d'utilisation des matériaux par rapport aux techniques traditionnelles de fabrication soustractive telles que l'usinage. Cela peut conduire à une réduction des déchets de matériaux et potentiellement à une approche de fabrication plus durable pour certaines applications.
Q : Quelles sont les avancées futures attendues dans les technologies EBM et DMLS ?
R : Le domaine de l'EBM et de la DMLS est en constante évolution. Voici quelques possibilités passionnantes qui se profilent à l'horizon :
- Des vitesses d'impression plus rapides : Les chercheurs développent des techniques pour améliorer la vitesse de l'EBM et du DMLS sans compromettre la qualité des pièces. Il pourrait s'agir de progrès dans la technologie des sources d'énergie ou de mécanismes améliorés de manipulation des poudres.
- Compatibilité élargie avec les matériaux : La gamme des métaux adaptés à l'impression EBM et DMLS devrait s'élargir. Cela offrirait aux concepteurs une plus grande flexibilité dans le choix du matériau optimal pour leurs besoins spécifiques.
- Impression multi-matériaux : Des techniques sont à l'étude pour permettre l'impression de pièces avec différents métaux ou même des combinaisons de métaux et d'autres matériaux en une seule fois. Cela pourrait ouvrir la voie à la création de composants hautement fonctionnels et complexes.
- Amélioration de la finition de la surface : Les progrès de la technologie de contrôle du laser et du faisceau d'électrons pourraient conduire à des finitions de surface encore plus lisses pour les pièces imprimées par DMLS, ce qui pourrait réduire la nécessité d'un post-traitement dans certaines applications.
Au fur et à mesure que ces technologies innovantes se développent, l'EBM et le DMLS sont appelés à jouer un rôle de plus en plus important en révolutionnant la façon dont nous concevons et fabriquons des pièces métalliques dans diverses industries.
Conclusion
La danse complexe entre les technologies EBM et DMLS offre un ensemble d'outils puissants pour créer des objets métalliques complexes et fonctionnels. Comprendre les forces et les faiblesses de chaque approche, ainsi que le vaste monde des poudres métalliques utilisées comme éléments de construction, vous permet de prendre des décisions éclairées pour vos projets d'impression 3D. Qu'il s'agisse de privilégier la vitesse pour les métaux réactifs avec l'EBM ou de rechercher des détails exceptionnels et une plus grande sélection de matériaux avec le DMLS, les deux technologies repoussent les limites de ce qui est possible dans la fabrication des métaux. Au fur et à mesure que ces technologies continuent d'évoluer, l'avenir offre un immense potentiel pour une liberté de conception encore plus grande, l'innovation en matière de matériaux et une approche plus durable de la création de pièces métalliques.
Partager sur
MET3DP Technology Co. est un fournisseur de premier plan de solutions de fabrication additive dont le siège se trouve à Qingdao, en Chine. Notre société est spécialisée dans les équipements d'impression 3D et les poudres métalliques de haute performance pour les applications industrielles.
Articles connexes
À propos de Met3DP
Mise à jour récente
Notre produit
CONTACTEZ-NOUS
Vous avez des questions ? Envoyez-nous un message dès maintenant ! Nous répondrons à votre demande avec toute une équipe dès réception de votre message.
Obtenir les informations de Metal3DP
Brochure du produit
Obtenir les derniers produits et la liste des prix
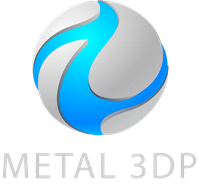
Poudres métalliques pour l'impression 3D et la fabrication additive