Guide Rails for Aerospace Assemblies
Table des matières
Revolutionizing Aerospace Assemblies: The Power of Metal 3D Printed Guide Rails
The aerospace industry perpetually seeks innovation – lighter components, stronger materials, faster production cycles, and enhanced performance under extreme conditions. Every gram saved translates to fuel efficiency or increased payload capacity. Every improvement in component reliability enhances safety and mission success. Within the complex ecosystem of aircraft and spacecraft, seemingly simple components like guide rails play a surprisingly critical role. These are not mere tracks; they are precision-engineered systems enabling vital functions, from the deployment of landing gear and flight control surfaces to the smooth operation of cargo handling systems and interior mechanisms. Traditionally manufactured through subtractive methods like CNC machining or complex casting and assembly processes, the production of high-performance guide rails often faces limitations in design complexity, material waste, and lead times.
Enter Metal Additive Manufacturing (AM), more commonly known as metal Impression 3D. This transformative technology is rapidly shifting paradigms across industries, and aerospace is at the forefront of its adoption. Instead of carving parts from solid blocks, metal AM builds components layer by intricate layer directly from digital designs using high-performance metal powders. This fundamental difference unlocks unprecedented possibilities for designing and manufacturing aerospace guide rails, offering advantages previously unattainable. Imagine guide rails with internal cooling channels, complex geometries perfectly optimized for specific load paths, or multiple functional components consolidated into a single, lighter, stronger part. This is the reality metal AM delivers.
At the vanguard of this technological evolution is Met3dp. Headquartered in Qingdao, China, Met3dp is a leading provider of comprehensive additive manufacturing solutions, specializing in state-of-the-art 3D printing equipment and a wide range of high-performance metal powders tailored for demanding industrial applications. With decades of collective expertise, Met3dp empowers aerospace manufacturers, suppliers, and procurement managers to leverage the full potential of metal AM. Our industry-leading printers boast exceptional print volume, accuracy, and reliability, crucial for producing mission-critical parts like guide rails. Coupled with our advanced powder manufacturing capabilities, employing Gas Atomization and Plasma Rotating Electrode Process (PREP) technologies, we ensure the foundational material quality necessary for superior final part properties. This blog post delves into the specifics of using metal AM for aerospace guide rails, exploring applications, benefits, materials, design considerations, and how partnering with an expert like Met3dp can elevate your aerospace assemblies. For fournisseurs de composants aérospatiaux, aircraft manufacturerset procurement managers seeking advanced manufacturing solutions, understanding the potential of metal 3D printed guide rails is no longer optional – it’s essential for staying competitive.
Critical Applications: Where Are Metal 3D Printed Guide Rails Deployed?
The term “guide rail” encompasses a variety of components designed to direct, support, and enable linear or controlled motion within a larger assembly. In the demanding environment of aerospace, these components must perform flawlessly under significant stress, vibration, and temperature fluctuations. Metal 3D printing allows for the creation of highly optimized guide rails for a diverse range of critical applications:
- Systèmes de trains d'atterrissage : Guide rails are essential for the precise deployment and retraction sequences of landing gear. They guide struts, actuators, and locking mechanisms, requiring high strength, wear resistance, and dimensional stability. Metal AM enables complex internal features for hydraulic fluid or sensor integration, along with optimized shapes for weight reduction without compromising structural integrity.
- Cargo Handling Systems: Modern aircraft feature sophisticated cargo systems using rollers, tracks, and locking mechanisms guided by rails. These systems handle heavy loads repeatedly. AM allows for durable, lightweight rail designs, potentially integrating features like specific locking points or sensor mounts directly into the rail structure, reducing part count and assembly complexity. B2B aerospace component distributors can benefit from the consolidated and potentially customized nature of AM parts.
- Flight Control Surface Actuation: Rails guide the movement of actuators controlling flaps, slats, ailerons, and rudders. Precision and reliability are paramount. AM can produce rails with complex curvatures or variable cross-sections tailored to specific aerodynamic requirements and space constraints, often impossible or prohibitively expensive with traditional methods.
- Passenger Seating and Interior Modules: Seat adjustment mechanisms rely on guide rails for smooth, reliable operation. Galley components, overhead bins, and cabin dividers often utilize guide tracks. While seemingly less critical, weight savings here accumulate significantly across an entire aircraft. AM allows for lightweight designs using materials like Scalmalloy® and potentially integrates features like cable routing or attachment points. Aircraft interior suppliers can leverage AM for customized, lightweight solutions.
- Deployable Systems: Spacecraft, satellites, and UAVs utilize guide rails for deploying solar arrays, antennas, booms, and scientific instruments. These deployments must be precise and reliable after potentially long periods of stowage. AM facilitates intricate, lightweight, and strong deployment mechanisms and guide structures optimized for minimal mass and volume.
- Composants du moteur : Within jet engines or rocket motors, guide rails might direct the movement of variable geometry components (like nozzle vanes) or support internal structures. These applications demand materials like Ti-6Al-4V capable of withstanding extreme temperatures and stresses.
- Assembly Jigs and Fixtures: While not part of the final aircraft, custom guide rails are often used in jigs and fixtures during the assembly process. Metal AM allows for the rapid production of bespoke, complex fixtures that improve assembly accuracy and speed, representing a key benefit for aerospace assembly operations.
Table: Key Aerospace Guide Rail Applications & AM Benefits
Domaine d'application | Traditional Challenges | Avantages de l'AM des métaux | B2B Focus Keywords |
---|---|---|---|
Train d'atterrissage | Weight, complex machining, assembly steps | Lightweighting (Topology Optimization), Integrated Features, High Strength Materials | Aerospace landing gear suppliers |
Cargo Handling | Wear, load capacity, part count | Durability, Part Consolidation, Customized Locking Features, Weight Reduction | Aircraft cargo system manufacturers |
Flight Controls | Precision, space constraints, complex paths | Complex Geometries, High Stiffness, Tailored Performance, Reduced Assembly | Flight control actuation systems |
Interiors/Seating | Weight accumulation, standard parts | Significant Weight Savings, Customization, Feature Integration (e.g., wiring) | Aircraft interior component wholesale |
Deployable Systems | Weight, volume, deployment reliability | Extreme Lightweighting, Complex Mechanisms, High Reliability, Compact Designs | Spacecraft mechanism suppliers |
Composants du moteur | High temperature, stress, complex shapes | High-Temperature Materials (Ti-6Al-4V), Optimized Cooling/Flow Paths, Durability | Aerospace engine parts manufacturers |
Assembly Jigs/Fixtures | Customization time, complexity, cost | Rapid Production of Custom Tools, Complex Geometries, Improved Assembly Efficiency | Aerospace tooling solutions |
Exporter vers les feuilles
The ability to tailor guide rails precisely to their function using advanced materials and manufacturing techniques makes metal AM a compelling choice for aerospace parts manufacturers seeking performance enhancements and competitive advantages.
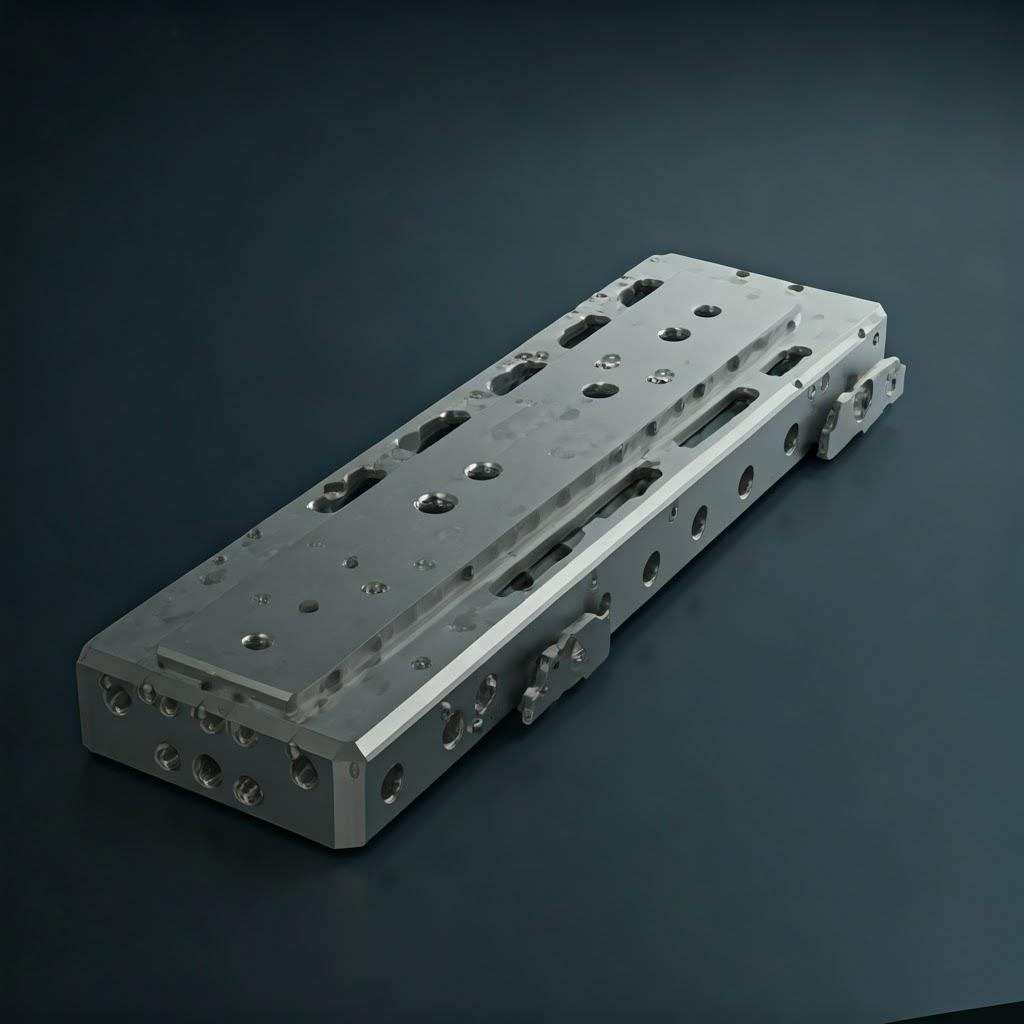
Unlocking Performance: Why Choose Metal AM for Aerospace Guide Rails?
While traditional manufacturing methods like CNC machining from billet, casting, or extrusion have served the aerospace industry well, they come with inherent limitations, particularly when designing for optimal performance and minimal weight. Metal additive manufacturing offers a suite of compelling advantages specifically suited for producing next-generation aerospace guide rails:
- Unmatched Design Freedom & Complexity: AM liberates engineers from many constraints of traditional manufacturing. Guide rails can feature:
- Canaux internes : For cooling, lubrication, hydraulic lines, or sensor wiring, integrated directly without complex drilling or assembly.
- Complex Curvatures & Non-Linear Paths: Enabling movement along paths previously difficult or impossible to achieve.
- Coupes transversales variables : Tailoring the rail’s profile along its length to match specific load requirements, adding material only where needed.
- This complexity is achieved without the typical cost increases associated with intricate machining setups.
- Potentiel d'allègement important : Aerospace lives by the mantra “lighter is better.” Metal AM enables:
- Optimisation de la topologie : Using software algorithms to remove material from non-critical areas, leaving behind an organic-looking, highly efficient load-bearing structure. Weight savings of 30-50% or more are often achievable compared to traditionally designed parts.
- Structures en treillis : Incorporating internal lattice or honeycomb structures provides high stiffness and strength at a fraction of the weight of solid material.
- For guide rails, this means reduced overall aircraft weight, leading to fuel savings or increased payload capacity – a critical factor for aerospace procurement specialists.
- Consolidation partielle : Complex assemblies often require multiple individual components (brackets, fasteners, rail segments) to be manufactured and then assembled. Metal AM allows engineers to redesign these assemblies as a single, monolithic printed part. This offers numerous benefits:
- Reduced Part Count: Simplifies inventory, logistics, and supply chain management.
- Faster Assembly: Less time and labor required on the final assembly line.
- Improved Reliability: Eliminates potential failure points associated with joints and fasteners.
- Réduction du poids : Fewer fasteners and interfaces often lead to lighter overall systems.
- Improved Material Efficiency (Buy-to-Fly Ratio): Traditional subtractive manufacturing, especially CNC machining, can be incredibly wasteful. Starting with a large block of expensive aerospace-grade material (like Titanium) and carving away up to 80-90% of it results in a poor “buy-to-fly” ratio. Metal AM is an additive process, using primarily only the material needed for the part and its support structures. While powder recycling isn’t 100% efficient, the material waste is significantly lower, making it more cost-effective for expensive alloys like Scalmalloy® and Ti-6Al-4V, a key consideration in additive manufacturing cost-benefit analysis.
- Accelerated Prototyping and Production: Metal AM allows for rapid iteration of designs. A new guide rail concept can be designed, printed, and tested in a matter of days or weeks, compared to potentially months for traditional tooling and machining setups. For low-to-medium volume production runs, AM can often be faster than setting up traditional manufacturing lines, enabling quicker deployment of new aircraft features or faster MRO (Maintenance, Repair, Overhaul) operations. This speed offers a significant advantage in on-demand aerospace part manufacturing.
- Enhanced Supply Chain Resilience: Metal AM supports the concept of a digital inventory. Designs can be stored digitally and printed on demand, closer to the point of need. This reduces reliance on complex global supply chains, minimizes warehousing costs, and provides flexibility in sourcing, a crucial factor for aerospace supply chain managers.
Table: Metal AM vs. Traditional Manufacturing for Aerospace Guide Rails
Fonctionnalité | Traditional Methods (CNC, Casting, Extrusion) | Fabrication additive métallique (PBF) | Key Benefit for Guide Rails |
---|---|---|---|
Complexité de la conception | Limited by tooling, machining access, assembly | High geometric freedom, internal features, lattices | Optimized performance, integrated functions |
Allègement | Limited; material removal only | Excellent; Topology Optimization, lattice structures | Reduced aircraft weight, fuel efficiency |
Consolidation partielle | Difficult; requires assembly | Excellent; monolithic parts possible | Reduced assembly time, weight, failure points |
Déchets matériels | High (especially CNC – poor Buy-to-Fly) | Low (Near-Net Shape) | Cost savings on expensive materials |
Lead Time (Proto) | Weeks to Months (tooling, setup) | Jours à semaines | Faster design iteration, testing |
Lead Time (Prod) | Efficient for high volume, slow setup for low volume | Competitive for low-medium volume, on-demand capable | Flexible production, MRO speed |
Personnalisation | Costly, requires new tooling/programming | Easy, digitally driven | Bespoke solutions, rapid design updates |
Exporter vers les feuilles
By leveraging these advantages, aerospace companies working with knowledgeable partners like Met3dp can produce guide rails that are not just replacements for traditionally made parts, but fundamentally superior components contributing to the next generation of aircraft and spacecraft.
Material Matters: Selecting Scalmalloy® and Ti-6Al-4V for Optimal Performance
The performance of any aerospace component, especially a load-bearing or motion-enabling one like a guide rail, is intrinsically linked to the material from which it’s made. Metal additive manufacturing processes, such as Powder Bed Fusion (PBF), require specialized metal powders engineered for optimal melting, solidification, and final part properties. For demanding aerospace guide rail applications, two materials stand out: Scalmalloy® and Ti-6Al-4V. The choice between them depends heavily on the specific operational requirements – load, temperature, environment, and weight priority.
Scalmalloy®: The High-Performance Aluminum Alloy
Scalmalloy® is a patented high-performance aluminum-magnesium-scandium alloy specifically developed for additive manufacturing. It bridges the gap between traditional high-strength aluminum alloys and titanium alloys, offering compelling properties for aerospace:
- Rapport résistance/poids élevé : This is Scalmalloy®’s defining characteristic. It delivers mechanical strength (yield and ultimate tensile strength) comparable to some stronger traditional aluminum alloys (like 7000 series) and even approaching that of Ti-6Al-4V, but at a significantly lower density (approx. 2.67 g/cm³). This makes it ideal for lightweight structural components where reducing mass is paramount.
- Excellent Processability in AM: Scalmalloy® was designed with Laser Powder Bed Fusion (L-PBF) in mind. It exhibits good weldability and resistance to hot cracking during the rapid melting and solidification cycles inherent in the process, allowing for the production of dense, reliable parts.
- Good Ductility and Fatigue Life: Unlike some high-strength aluminum alloys which can be brittle, Scalmalloy® retains good ductility and exhibits excellent fatigue performance, crucial for components subjected to cyclic loading, like guide rails in actuation systems.
- Résistance à la corrosion : Offers good general corrosion resistance suitable for typical aerospace operating environments.
- Applications for Guide Rails: Ideal for guide rails where weight saving is the primary driver, such as in interior modules, seating systems, deployable structures, cargo handling (where loads allow), and certain flight control surface applications not exposed to extreme heat.
Ti-6Al-4V (Grade 5): The Aerospace Workhorse Titanium Alloy
Ti-6Al-4V, often referred to as Ti64 or Grade 5 Titanium, is arguably the most widely used titanium alloy in aerospace, and for good reason. It translates well to additive manufacturing processes like L-PBF and Electron Beam Melting (EBM), including the Selective Electron Beam Melting (SEBM) technology utilized in some of Met3dp’s advanced printers.
- Excellent rapport résistance/poids : While denser than Scalmalloy® (approx. 4.43 g/cm³), Ti-6Al-4V offers exceptionally high strength, maintaining its properties at elevated temperatures where aluminum alloys falter.
- High-Temperature Capability: Can operate effectively at temperatures up to 300-400°C (or higher for short durations), making it suitable for guide rails near engines or in high-speed aircraft applications experiencing significant aerodynamic heating.
- Superb Corrosion Resistance: Exhibits outstanding resistance to corrosion in a wide range of aggressive environments, including saltwater and various aerospace fluids.
- Biocompatibilité : While not relevant for guide rails, its biocompatibility makes it a primary choice for medical implants, highlighting its inert nature.
- Proven Aerospace Pedigree: Decades of use in critical aircraft structures and engine components provide extensive data and confidence in its performance and reliability.
- Applications for Guide Rails: The default choice for guide rails requiring high strength, stiffness, fatigue resistance, and/or high-temperature performance. Common in landing gear, engine components, flight control surface actuation (especially near heat sources), and demanding structural applications.
Table: Comparison of Scalmalloy® and Ti-6Al-4V for AM Guide Rails
Propriété | Scalmalloy® (alliage d'aluminium) | Ti-6Al-4V (Niveau 5) | Significance for Guide Rails |
---|---|---|---|
Densité | ~2.67 g/cm³ | ~4,43 g/cm³ | Scalmalloy® offers greater lightweighting potential. |
Limite d'élasticité | High (e.g., 450-500+ MPa, process dependent) | Very High (e.g., 830+ MPa, process dependent) | Both provide excellent strength for load-bearing. |
Force spécifique | Excellent | Excellent | Both materials are highly efficient structurally. |
Max Service Temp. | Moderate (~150-200°C) | High (~300-400°C+) | Ti-6Al-4V required for high-temperature applications. |
Résistance à la corrosion | Bon | Remarquable | Ti-6Al-4V preferred for highly corrosive environments. |
AM Processability | Excellent (esp. L-PBF) | Excellent (L-PBF, EBM/SEBM) | Both are well-suited for producing complex AM parts. |
Coût relatif | High (Scandium content) | Very High (Titanium base) | Material cost is a significant factor in project economics. |
Typical AM Process | Laser Powder Bed Fusion (L-PBF/SLM) | L-PBF, Electron Beam Melting (EBM/SEBM) | Process selection can influence microstructure and properties. |
Exporter vers les feuilles
Met3dp’s Commitment to Material Quality:
The successful printing of high-performance materials like Scalmalloy® and Ti-6Al-4V hinges critically on the quality of the metal powder used. Met3dp understands this fundamental requirement. Our company leverages industry-leading powder production technologies:
- Gas Atomization (GA): This process uses high-pressure inert gas jets to break up a stream of molten metal into fine droplets, which solidify into spherical powders. Met3dp employs unique nozzle and gas flow designs to achieve high sphericity and excellent flowability – crucial for uniform powder bed spreading and consistent melting in PBF processes.
- Procédé d'électrodes rotatives à plasma (PREP) : PREP involves rotating a consumable electrode rod at high speed while melting its tip with a plasma torch. Centrifugal force disperses the molten metal into droplets that solidify in flight within an inert atmosphere. This method is known for producing highly spherical powders with very high purity and minimal satellite particles, ideal for the most demanding applications.
Met3dp manufactures a wide range of poudres métalliques à haute performance, including Titanium alloys (like Ti-6Al-4V, TiNi, TiTa, TiAl, TiNbZr), superalloys, stainless steels, CoCrMo, and more, optimized for laser and electron beam powder bed fusion. Our rigorous quality control ensures powders meet stringent specifications for particle size distribution (PSD), morphology (sphericity), flowability, chemical composition, and purity. This commitment to powder excellence provides aerospace parts suppliers et fabricants with the confidence that the materials used in their critical guide rails will deliver the expected performance and reliability. Choosing the right material, processed from high-quality powder supplied by experts like Met3dp, is the foundation for successful metal AM implementation in aerospace.
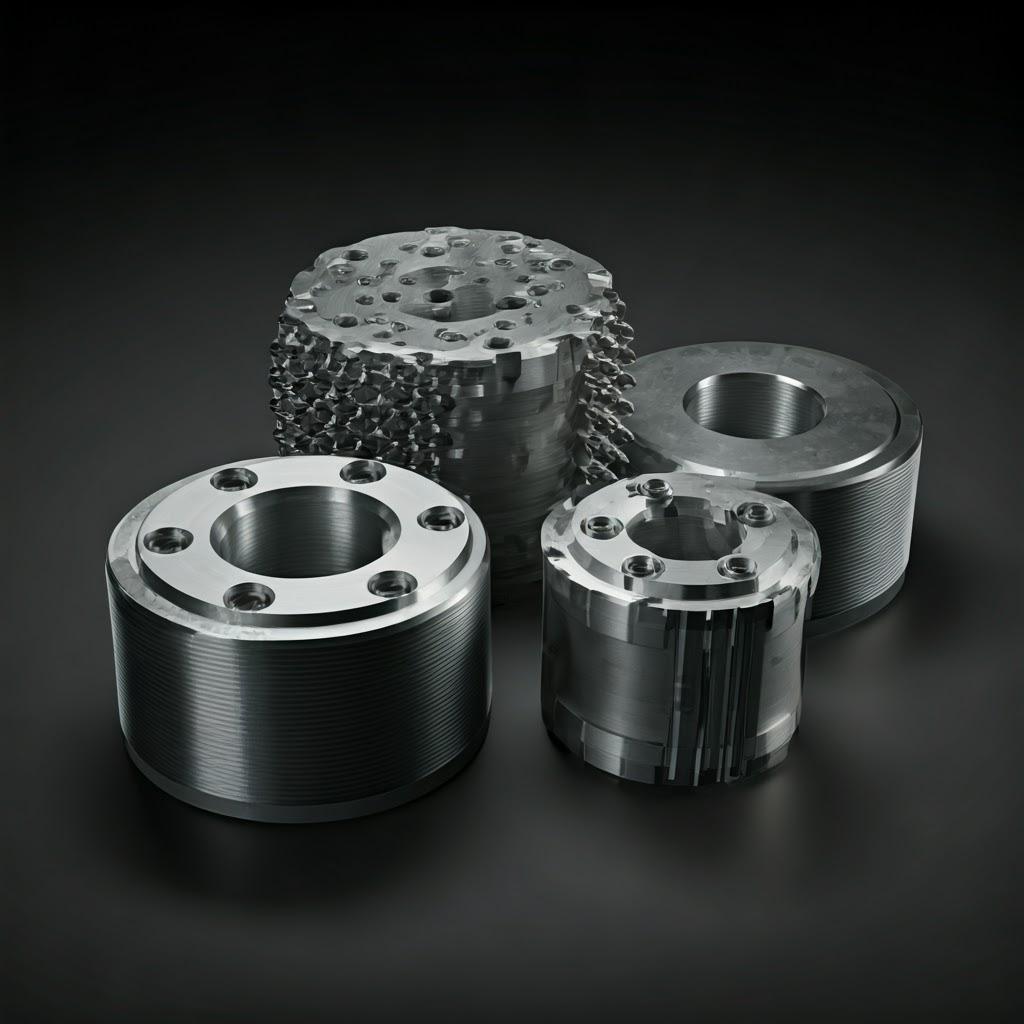
Design for Additive Manufacturing (DfAM): Optimizing Guide Rails for Printing Success
Simply taking a design intended for CNC machining and sending it to a metal 3D printer rarely yields optimal results. To truly harness the power of additive manufacturing for aerospace guide rails, engineers and designers must embrace Conception pour la fabrication additive (DfAM). DfAM is not just a suggestion; it’s a fundamental shift in thinking that considers the unique capabilities and constraints of the layer-by-layer building process from the earliest stages of design. Applying DfAM principles is crucial for achieving lightweighting goals, ensuring printability, minimizing post-processing, reducing costs, and ultimately producing a superior guide rail component. For additive manufacturing engineering teams and aerospace design bureaus, mastering DfAM is key to innovation.
Here are critical DfAM considerations when designing aerospace guide rails for metal AM processes like Powder Bed Fusion (PBF):
- Optimisation de la topologie : This is often the starting point for significant lightweighting.
- What it is: Using specialized software, engineers define load cases, constraints, and design spaces. The software then iteratively removes material from areas that don’t contribute significantly to structural integrity, leaving an optimized, often organic-looking geometry.
- Benefit for Guide Rails: Creates highly efficient structures that meet or exceed stiffness and strength requirements with minimal mass. Ideal for reducing the weight of mounting features, support structures, and non-critical sections of the rail itself.
- Considération : Optimized designs can be complex and may require smoothing or minor adjustments for printability or functional interfaces.
- Lattice Structures and Infill:
- What it is: Replacing solid internal volumes with engineered lattice structures (e.g., honeycomb, gyroid, strut-based lattices) or patterned infill.
- Benefit for Guide Rails: Dramatically reduces weight and material consumption while maintaining significant structural support and stiffness. Can also be designed to absorb energy or dampen vibrations.
- Considération : Requires careful selection of lattice type, cell size, and strut diameter based on load requirements. Ensuring powder can be removed from internal lattices is critical (see Powder Escape Holes).
- Managing Overhangs and Support Structures:
- What it is: PBF processes build upon layers below. Steep overhangs (typically beyond 45 degrees from vertical, though process/material dependent) require support structures to prevent collapse during printing and anchor the part to the build plate.
- Benefit of DfAM: Designing with self-supporting angles where possible, orienting the part strategically on the build plate to minimize the volume of supports needed, and designing features that inherently act as supports.
- Considération : Supports consume material, add print time, require removal (adding labor and potentially damaging surfaces), and can impact surface finish. Support structure minimization is a primary DfAM goal. Designing accessible supports is crucial.
- Épaisseur minimale de la paroi et dimensions de l'élément :
- What it is: Every AM process has limitations on the minimum thickness of walls and the smallest features (e.g., pins, holes) it can reliably produce due to laser/electron beam spot size, powder particle size, and thermal effects.
- Benefit of DfAM: Designing walls, ribs, and features above the minimum threshold (typically 0.4-1.0 mm, consult your AM provider) ensures they print successfully and have sufficient structural integrity.
- Considération : Thin walls are prone to warping and may be fragile. Overly thick sections can accumulate thermal stress.
- Fillets and Radii:
- What it is: Avoiding sharp internal corners and edges by incorporating fillets (rounded internal edges) and radii (rounded external edges).
- Benefit for Guide Rails: Reduces stress concentrations, which improves fatigue life – critical for cyclically loaded components. Smoother transitions can also improve powder flow during printing and fluid flow if internal channels are present.
- Considération : While AM can produce sharp edges, incorporating radii is generally good engineering practice, especially for fatigue-sensitive aerospace parts.
- Powder Escape Holes:
- What it is: Strategically placed holes that allow unfused metal powder to be removed from internal cavities, channels, or complex lattice structures after printing.
- Benefit for Guide Rails: Ensures internal features are clear and reduces the final part weight by removing trapped powder. Critical for hollow designs or those using extensive internal lattices.
- Considération : Holes must be large enough for powder to escape easily (often > 2-5 mm diameter, depending on powder and complexity). Placement should consider accessibility during post-processing (shaking, blowing).
- Part Orientation:
- What it is: Deciding how the guide rail will be positioned on the build plate.
- Benefit of DfAM: Orientation significantly impacts support needs, surface finish (up-facing vs. down-facing surfaces), print time (part height), and potentially mechanical properties (anisotropy). Strategic orientation optimizes these factors.
- Considération : Often involves trade-offs. Optimizing for minimal support might compromise surface finish on critical faces, requiring careful evaluation based on part requirements. Simulation tools can help predict outcomes.
- Concevoir pour le post-traitement :
- What it is: Considering how the part will be handled after printing.
- Benefit of DfAM: Adding machining allowances on critical surfaces that require tight tolerances, ensuring access for support removal tools, designing features robust enough to withstand handling and finishing processes.
- Considération : Thinking about the entire process chain, from print to finished part, during the initial design phase saves time and cost later.
Met3dp works closely with its clients, offering application development services and DfAM expertise. Our engineers can help review designs, suggest optimizations, and run simulations to ensure your aerospace guide rail design is perfectly suited for additive manufacturing, maximizing performance while minimizing production challenges. Following metal 3D printing design guidelines is not just about making a part printable; it’s about unlocking the true potential of the technology.
Achieving Precision: Tolerances, Surface Finish, and Dimensional Accuracy in AM Guide Rails
For components like aerospace guide rails, where precise movement, mating interfaces, and reliable operation are critical, understanding the achievable levels of precision with metal additive manufacturing is essential. Engineers and procurement managers need realistic expectations regarding tolerances, surface finish, and overall dimensional accuracy. While metal AM technology, such as the impression 3D de métaux processes offered by Met3dp, delivers remarkable capabilities, it differs from the precision typically associated with multi-axis CNC machining in its as-built state.
Tolerances:
- Définition : Tolerances define the allowable variation in a dimension.
- Typical AM Capabilities: Metal Powder Bed Fusion (PBF) processes like Laser PBF (L-PBF/SLM) and Electron Beam Melting (EBM/SEBM) typically achieve tolerances in the range of:
- ±0.1 mm to ±0.3 mm for smaller features (e.g., up to 20-50 mm).
- ±0.2% to ±0.5% of the nominal dimension for larger features.
- Influencing Factors: Process type (EBM often has slightly looser tolerances than L-PBF due to higher temperatures and powder interactions), machine calibration, material properties (thermal expansion/contraction), part geometry and orientation, support strategy, and thermal stresses during the build.
- For Guide Rails: While these tolerances are suitable for many features, critical interfaces, bearing surfaces, or mounting points often require tighter control, necessitating post-process machining.
Finition de la surface (rugosité) :
- Définition : Surface roughness (commonly measured as Ra – arithmetic average roughness) describes the texture of a surface.
- Typical As-Built Values:
- L-PBF: Ra values typically range from 6 µm to 15 µm, depending on material, parameters, and surface orientation (up-facing surfaces are generally smoother than down-facing or side-facing surfaces).
- EBM/SEBM: Generally produces rougher surfaces than L-PBF, often in the Ra 20 µm to 35 µm range, due to larger powder particles and higher process temperatures causing some particle sintering.
- Influencing Factors: Layer thickness (thinner layers = smoother finish), powder particle size distribution (finer powder = smoother finish), energy input (laser/beam parameters), part orientation relative to the recoater blade and build direction.
- For Guide Rails: As-built surfaces are often too rough for smooth sliding contact or precise sealing. Surfaces requiring low friction, high wear resistance, or specific mating characteristics typically need secondary finishing operations like polishing, grinding, or coating.
Précision dimensionnelle :
- Définition : How closely the final printed part conforms to the original CAD model dimensions.
- Influencing Factors: This is a complex interplay of:
- Thermal Stress and Distortion: The rapid heating and cooling cycles can cause internal stresses leading to warping or deviation from the intended shape, especially in large or complex parts.
- Shrinkage: Materials contract upon cooling from melting point to room temperature. This is compensated for in process planning, but variations can occur.
- Structures de soutien : Effective supports are crucial to prevent distortion and anchor the part, but their removal can sometimes affect dimensions.
- Étalonnage de la machine : Accurate laser/beam positioning, Z-axis movement, and thermal management are vital.
- Qualité de la poudre : Consistent powder characteristics ensure predictable melting behavior.
- For Guide Rails: Achieving high dimensional accuracy across the entire length of a potentially long guide rail requires careful process control, simulation (to predict and compensate for distortion), robust support strategies, and often, final machining of key dimensions.
Met3dp’s Approach to Precision:
Met3dp recognizes the critical importance of precision in aerospace applications. Our commitment includes:
- Advanced Equipment: Utilizing printers with industry-leading accuracy and reliability, including SEBM systems known for good thermal management which can help reduce residual stress.
- Contrôle des processus : Implementing rigorous process monitoring and control protocols.
- High-Quality Materials: Ensuring consistent, high-quality metal powders with optimized characteristics produced via our advanced GA and PREP systems.
- Expertise : Employing experienced engineers and technicians who understand the nuances of achieving accuracy in metal AM.
- Métrologie : Utilizing advanced metrology for AM techniques for quality assurance and part validation.
While AM provides incredible geometric freedom, achieving micron-level tolerances requires integrating post-processing steps like CNC machining. Understanding the inherent capabilities and limitations of PBF precision allows for effective design and planning, ensuring the final aerospace guide rail meets all functional and dimensional accuracy aerospace parts exigences.
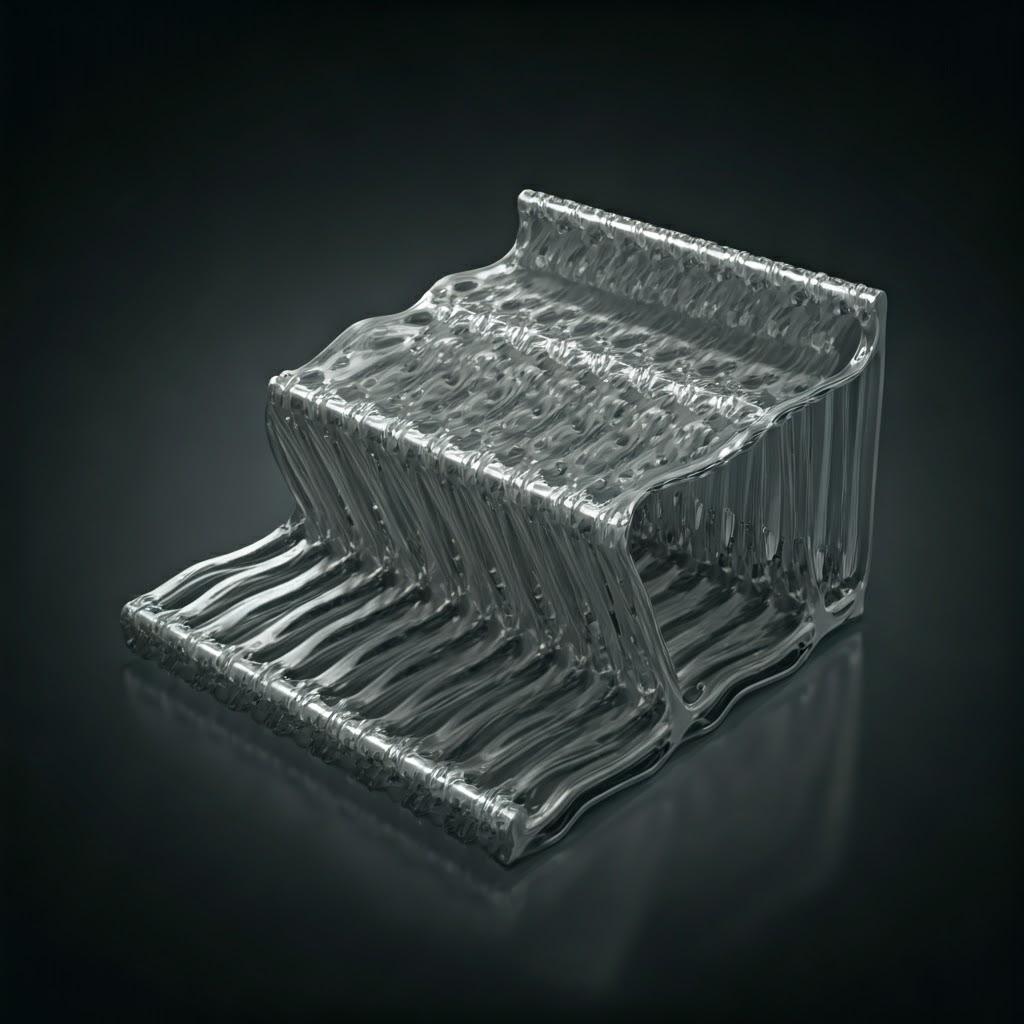
Beyond the Build: Essential Post-Processing for Aerospace-Grade Guide Rails
Printing a metal guide rail is often just the first manufacturing step. Achieving the demanding performance, reliability, and safety standards required for aerospace applications necessitates a series of critical post-processing steps. These operations transform the as-built part, which may contain residual stresses, suboptimal surface finish, and porosity, into a finished component ready for assembly and flight. Understanding these metal AM post-processing requirements is essential for planning production workflows and estimating final costs and lead times.
Key post-processing steps for aerospace guide rails produced via PBF include:
- Traitement thermique anti-stress :
- Objet : To reduce the internal stresses built up during the rapid heating and cooling cycles of the AM process. These stresses can cause distortion or premature failure if not relieved.
- Processus : Heating the part in a controlled furnace environment (often under vacuum or inert atmosphere) to a specific temperature (below the material’s transformation temperature), holding it for a defined period, and then cooling it slowly. Parameters are material-specific (e.g., different cycles for Ti-6Al-4V vs. Scalmalloy®).
- Nécessité : Generally considered mandatory for almost all metal AM aerospace components to ensure dimensional stability and prevent cracking. Often performed while the part is still attached to the build plate to minimize distortion during the treatment itself.
- Pressage isostatique à chaud (HIP) :
- Objet : To eliminate internal porosity (voids) within the printed material and further improve mechanical properties like fatigue strength and ductility.
- Processus : Subjecting the component to high temperature (below melting point) and high inert gas pressure (typically Argon) simultaneously within a specialized HIP vessel. The high pressure effectively collapses internal voids, diffusion bonding the material across the void interface.
- Nécessité : Increasingly standard for critical aerospace components, especially those made from Titanium alloys or subject to high fatigue loading. HIP treatment aerospace significantly enhances component reliability and longevity, making it crucial for safety-critical parts like guide rails in landing gear or flight controls.
- Part Removal and Support Structure Removal:
- Objet : Separating the printed guide rail(s) from the build plate and removing the support structures required during the build process.
- Processus : Typically involves cutting the part from the plate (e.g., using wire EDM or a bandsaw). Support removal can be manual (breaking or prying), use hand tools, or require machining (milling, grinding) or EDM, depending on the support design, material, and accessibility.
- Considération : Support removal can be labor-intensive and risks damaging the part surface if not done carefully. DfAM plays a role here by designing supports for easier removal.
- Usinage CNC :
- Objet : To achieve tight tolerances, specific surface finishes, and precise features on critical surfaces that cannot be met by the as-built AM process.
- Processus : Using traditional CNC milling or turning machines to finish specific areas of the guide rail.
- Nécessité : Almost always required for aerospace guide rails on surfaces such as:
- Sliding/mating faces requiring specific flatness, parallelism, or low roughness.
- Bearing interfaces or mounting holes requiring precise diameters and positions.
- Threaded holes.
- Sealing surfaces.
- CNC finishing 3D prints bridges the gap between AM’s geometric freedom and the precision requirements of aerospace assemblies.
- Surface Finishing and Coating:
- Objet : To improve surface characteristics like smoothness (reducing friction), wear resistance, corrosion protection, or fatigue life.
- Processus : Can include various methods:
- Abrasive Blasting (Bead/Sand Blasting): Creates a uniform matte finish, cleans surfaces.
- Finition par culbutage et vibration : Smoothes surfaces and deburrs edges using media in a rotating or vibrating drum.
- Polissage : Achieves very smooth, low-Ra surfaces for low-friction applications.
- Anodizing (for Titanium): Improves wear resistance and provides corrosion protection.
- Specialized Coatings (e.g., DLC – Diamond-Like Carbon): Applied for extreme wear resistance or low friction properties on sliding surfaces. Aerospace coatings for additive manufacturing are a specialized field.
- Nécessité : Dependent on the specific application requirements of the guide rail’s interacting surfaces.
- Inspection and Non-Destructive Testing (NDT):
- Objet : To verify dimensional accuracy and ensure the absence of critical internal or external defects.
- Processus :
- Inspection dimensionnelle : Using Coordinate Measuring Machines (CMM), 3D scanners, or traditional metrology tools.
- Surface Defect Inspection: Visual inspection, Dye Penetrant Inspection (DPI).
- Internal Defect Inspection: X-ray radiography or Computed Tomography (CT) scanning to detect porosity, inclusions, or cracks.
- Nécessité : Mandatory for quality assurance in aerospace. NDT inspection of AM parts provides crucial verification of part integrity before flight.
Met3dp understands that additive manufacturing is often just one part of the production chain. We work with a network of trusted partners or can integrate with a client’s existing supply chain to manage these essential post-processing steps, delivering finished, certified aerospace guide rails that meet all specifications.
Navigating Challenges: Avoiding Pitfalls in Metal AM for Guide Rails
While metal additive manufacturing offers transformative potential for aerospace guide rails, the technology is not without its challenges. Successfully implementing metal AM requires a deep understanding of the process nuances, material behaviors, and potential pitfalls. Partnering with an experienced provider like Met3dp, equipped with robust process controls and deep expertise, is crucial for navigating these complexities. Awareness of these common metal 3D printing problems and solutions allows engineers and procurement teams to plan effectively and mitigate risks.
Here are some key challenges in producing metal AM guide rails and strategies to overcome them:
- Déformation et distorsion :
- Défi: Intense localized heating from the laser or electron beam followed by rapid cooling creates significant thermal gradients and internal stresses. These stresses can cause the part to warp during the build, lift from the build plate, or distort after removal. This is particularly challenging for long, thin parts like some guide rails.
- Mitigation Strategies:
- Simulation de processus : Using software to predict thermal behavior and distortion patterns before printing, allowing for adjustments to orientation or support strategy.
- Structures de soutien optimisées : Robust supports anchor the part and help dissipate heat.
- Build Plate Heating: Maintaining an elevated temperature reduces thermal gradients (especially effective in EBM/SEBM).
- Stratégies d'analyse optimisées : Controlling the laser/beam path and parameters to manage heat input.
- DfAM : Designing features to minimize stress accumulation (e.g., avoiding large flat areas parallel to the plate).
- Traitement thermique anti-stress : Essential post-processing step.
- Contrainte résiduelle :
- Défi: Even if a part doesn’t visibly warp, significant internal stresses can remain locked within the material after printing. These stresses can negatively impact fatigue life, strength, and dimensional stability over time.
- Mitigation Strategies: Primarily addressed through effective Stress Relief Heat Treatment et HIP. Process simulation and optimized build parameters also play a role in minimizing stress build-up during the print itself. Understanding controlling distortion in AM est essentiel.
- Porosité :
- Défi: The presence of small voids or pores within the printed material. Porosity can act as stress concentrators, significantly reducing fatigue strength and ductility – unacceptable for critical aerospace components. Causes include trapped gas within the powder or melt pool (gas porosity) or insufficient melting leading to gaps between layers or particles (lack-of-fusion porosity).
- Mitigation Strategies:
- Poudre de haute qualité : Using powder with high sphericity, good flowability, low internal gas content, and controlled particle size distribution (a strength of Met3dp’s GA and PREP powders).
- Paramètres de processus optimisés : Ensuring sufficient energy input (laser/beam power, speed) for complete melting and fusion, managed within an inert atmosphere (Argon or Nitrogen).
- Pressage isostatique à chaud (HIP) : The most effective method for closing internal porosity post-build. Essential for controlling porosity in additive manufacturing pour l'aérospatiale.
- Support Removal Difficulty and Surface Quality:
- Défi: Support structures are necessary but can be difficult and time-consuming to remove, especially from complex internal channels or delicate features. Removal processes can leave undesirable marks (‘witness marks’) on the part surface, impacting finish and potentially requiring further remediation.
- Mitigation Strategies:
- DfAM for Supports: Designing parts to be self-supporting where possible, optimizing orientation, using support types designed for easier removal (e.g., conical or thin-walled supports).
- Advanced Software: Utilizing software that generates optimized, easily removable support structures.
- Appropriate Removal Techniques: Employing careful manual removal, specialized tools, or precise machining/EDM where needed.
- Powder Handling and Safety:
- Défi: Many metal powders used in AM, particularly fine Titanium and Aluminum alloys like Ti-6Al-4V and Scalmalloy®, are reactive and potentially flammable or explosive when dispersed in air as a dust cloud, especially in the presence of an ignition source (like static discharge). Handling requires stringent safety protocols. Inhalation is also a health concern.
- Mitigation Strategies:
- Inert Atmospheres: Processing (printing, powder handling, sieving) under Argon or Nitrogen gas.
- Grounding and Bonding: Preventing static electricity build-up.
- Proper Personal Protective Equipment (PPE): Respirators, gloves, protective clothing.
- Facility Design: Explosion-proof vacuum systems, appropriate ventilation, designated powder handling areas.
- Formation : Ensuring personnel are fully trained on metal powder handling safety procedures. Met3dp adheres to strict safety protocols in its operations.
- Anisotropie :
- Défi: Due to the layer-by-layer build process and directional heat flow, the mechanical properties (e.g., strength, ductility) of AM parts can sometimes vary depending on the direction of testing relative to the build direction (X, Y vs. Z).
- Mitigation Strategies: Understanding the specific anisotropic behavior of the material and process (data often available from material suppliers or through testing), optimizing part orientation to align critical load paths with the strongest direction, performing HIP (which can help homogenize microstructure), and incorporating design safety factors.
- Cost Management:
- Défi: Metal AM can be expensive due to powder costs, machine time, and extensive post-processing. Achieving cost-effectiveness requires careful planning.
- Mitigation Strategies: Leveraging DfAM for lightweighting and part consolidation, optimizing build layouts (nesting multiple parts), minimizing support structures, streamlining post-processing workflows, and selecting the most appropriate material and process for the application. Achieving cost reduction in additive manufacturing requires a holistic approach.
By proactively addressing these challenges through careful design, meticulous process control, appropriate post-processing, and leveraging the expertise of partners like Met3dp, manufacturers can confidently utilize metal AM to produce high-performance, reliable aerospace guide rails. Understanding the available additive manufacturing printing methods and their associated challenges is the first step towards successful implementation.
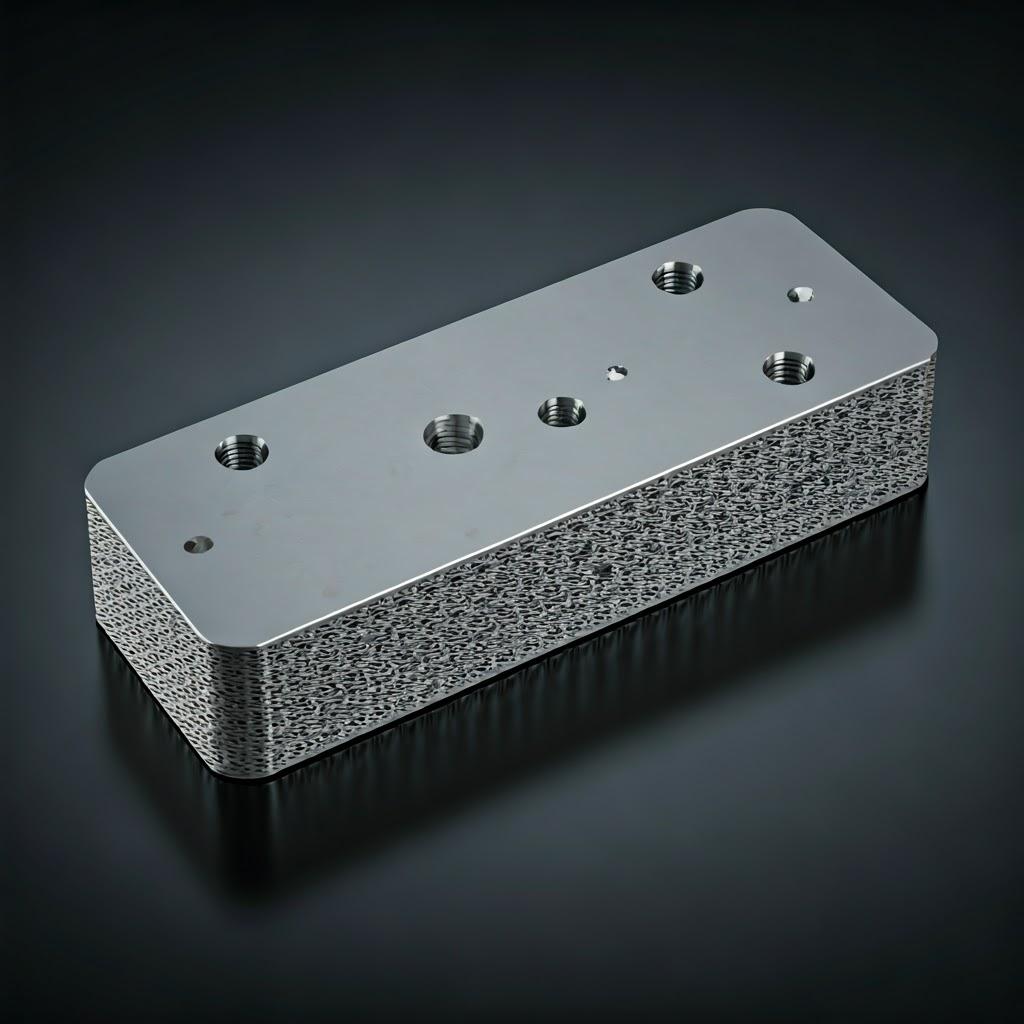
Partner Selection: Choosing the Right Metal AM Service Provider for Aerospace
The decision of which metal additive manufacturing service provider to partner with is critically important, especially within the aerospace sector where quality, reliability, and traceability are non-negotiable. Not all AM providers possess the specific expertise, equipment, quality systems, and material controls necessary to produce flight-worthy components like guide rails. Making the right choice ensures access to the full benefits of AM while mitigating risks associated with subpar manufacturing. For B2B procurement specialists et engineering leads in aerospace, evaluating potential metal AM service bureau partners requires a rigorous approach focusing on several key criteria:
- Certifications et conformité aérospatiales :
- AS9100 : This is the standard Quality Management System (QMS) requirement for the Aviation, Space, and Defense industries. Certification to AS9100 demonstrates a provider’s commitment to meeting the stringent quality, traceability, and process control demands of the sector. While ISO 9001 is a good baseline, AS9100 is often considered essential.
- Nadcap: Accreditations for special processes like heat treatment, non-destructive testing (NDT), and welding may be required, depending on the scope of services needed.
- ITAR Compliance: If working on defense-related projects, ensure the provider complies with International Traffic in Arms Regulations.
- Expérience confirmée dans le domaine de l'aérospatiale :
- Look for providers with a demonstrated track record of successfully producing parts for aerospace applications. Ask for case studies, examples of similar components (like guide rails, brackets, actuators), and references if possible. An understanding of aerospace requirements, materials, and challenges is invaluable.
- Technical Expertise and Support:
- The provider should employ experienced engineers and metallurgists who understand DfAM principles, material science (especially for alloys like Scalmalloy® and Ti-6Al-4V), process simulation, and post-processing requirements. Access to DfAM support can significantly enhance part performance and reduce costs.
- Machine Capability and Technology:
- Assess the provider’s fleet of metal AM machines. Do they utilize state-of-the-art equipment? Do they offer the appropriate technology (e.g., L-PBF, EBM/SEBM) for your material and application? Consider build volume capabilities for larger guide rails and machine redundancy for managing production schedules and mitigating downtime risks. Met3dp, for instance, leverages advanced systems, including potentially SEBM technology known for excellent thermal control beneficial for materials like Ti-6Al-4V.
- Material Portfolio and Quality Control:
- Verify the provider has experience with the specific materials needed (Scalmalloy®, Ti-6Al-4V) and, crucially, has robust procedures for powder handling, storage, testing, recycling, and traceability. Ask about their powder sourcing or in-house production capabilities. A focus on high-quality, consistent powder, like that produced by Met3dp’s advanced Gas Atomization and PREP systems, is fundamental to achieving reliable part properties.
- Système de gestion de la qualité (SGQ) robuste :
- Beyond certifications, delve into their QMS details. How do they ensure powder lot traceability to the final part? What process monitoring and controls are in place? What are their calibration procedures for machines and inspection equipment? Evaluating additive manufacturing partners requires scrutiny of their quality infrastructure.
- Comprehensive Post-Processing Capabilities:
- Determine if the provider offers necessary post-processing steps (stress relief, HIP, machining, finishing, NDT) in-house or through a network of qualified, preferably Nadcap-accredited, partners. A single point of contact managing the entire workflow can streamline the process significantly.
- Capacity, Lead Time, and Communication:
- Ensure the provider has the capacity to meet your project timelines for both prototypes and potential production runs. Evaluate their communication practices, project management approach, and responsiveness. Clear, consistent communication is vital for complex aerospace projects.
Why Consider Met3dp?
While rigorous evaluation is always recommended, Met3dp positions itself as a strong contender for aerospace applications based on several key strengths:
- Deep Expertise: Decades of collective experience in metal additive manufacturing.
- Technologie avancée : Utilization of industry-leading printing equipment (including SEBM) and powder production technologies (GA, PREP).
- Material Focus: Specialization in high-performance metal powders optimized for AM, including critical aerospace alloys.
- Quality Commitment: Emphasis on accuracy, reliability, and rigorous process controls essential for demanding sectors.
- Des solutions globales : Offering support across the AM lifecycle, from material supply and printing to application development.
Choisir le bon aerospace AM supplier is a strategic decision. Look for a partner, not just a vendor – one who understands the unique demands of aerospace and possesses the capabilities and commitment to deliver flight-ready components like high-performance guide rails.
Understanding Investment: Cost Factors and Lead Times for AM Guide Rails
Implementing metal additive manufacturing for aerospace guide rails involves understanding the associated costs and typical production timelines. While AM offers significant performance benefits, it’s crucial for aerospace parts procurement teams and project managers to have a clear picture of the investment required. Both cost and lead time are influenced by a complex interplay of factors.
Key Cost Drivers for Metal AM Guide Rails:
- Coût des matériaux :
- Powder Price: High-performance aerospace alloys like Scalmalloy® (due to Scandium) and Ti-6Al-4V are inherently expensive raw materials, significantly impacting the overall cost. Prices are typically quoted per kilogram.
- Material Consumption: This includes the volume of the final part plus the volume of support structures needed during the build. DfAM optimization to reduce part volume and support needs directly lowers material cost.
- Powder Reuse/Recycling: While unfused powder can often be sieved and reused, there are limits and quality control processes involved. Some powder loss is inevitable, contributing to the effective material cost.
- Le temps des machines :
- Temps de construction : This is often the largest contributor to AM costs. It’s primarily driven by the height of the part(s) in the build chamber (more layers = more time) and the volume of material being fused per layer. Factors like required laser/beam power, scan speed, and layer thickness influence this.
- Machine Rate: The hourly operational cost of the sophisticated metal AM printer, including depreciation, maintenance, energy, and inert gas consumption.
- Setup/Cooldown/Cleaning: Time required before and after the print cycle adds to the overall machine utilization cost. Nesting multiple guide rails (or other parts) efficiently within a single build can significantly improve machine time economics per part.
- Coûts de main-d'œuvre :
- Pre-Processing: Engineering time for DfAM, simulation, build preparation, and slicing.
- Machine Operation: Skilled technicians monitoring the build process.
- Post-traitement : Significant labor is often involved in part removal from the build plate, support structure removal (can be very time-consuming), heat treatment setup, CNC machining programming and operation, manual finishing/polishing, and inspection.
- Coûts de post-traitement :
- Heat Treatment (Stress Relief/HIP): Requires specialized furnaces/HIP units and associated energy/gas costs. HIP, in particular, can be a substantial cost component but is often essential for aerospace performance.
- Usinage CNC : Costs depend on the complexity of the features being machined, the number of setups required, and the machining time.
- Surface Finishing/Coating: Costs vary widely depending on the process (blasting, polishing, specialized aerospace coatings).
- NDT Inspection: Costs associated with equipment (CT scanners, CMMs) and certified personnel time.
- Design Complexity and Part Size:
- More intricate designs may require more complex support structures, longer print times, and more involved post-processing, increasing costs. Larger parts consume more material and machine time.
- Quality Assurance Requirements:
- The stringent documentation, testing, and certification requirements typical of aerospace add overhead compared to industrial applications. This includes material certifications, process documentation, detailed inspection reports, and potentially destructive testing coupons built alongside the parts.
Typical Lead Times for AM Guide Rails:
Lead time is the total duration from order placement (or design finalization) to delivery of the finished part. It’s highly variable but generally includes:
- Design Review & Preparation: 1-5 days (includes DfAM checks, simulation, build layout).
- Machine Queue: 0 days to 2+ weeks (dependent on provider’s backlog).
- Temps d'impression : 1 day to 1+ week (highly dependent on part height/volume and nesting).
- Post-traitement : 1 week to 4+ weeks (can be the longest phase due to sequential steps like stress relief -> HIP -> machining -> finishing -> NDT, each requiring scheduling and processing time).
- Inspection & Shipping: 1-5 days.
Therefore, a simple prototype might be available in 1-2 weeks, while a fully post-processed and certified aerospace guide rail could take 4 to 8 weeks or longer. Understanding these aerospace component lead time factors is crucial for project planning.
To get an accurate metal additive manufacturing cost breakdown and lead time estimate for your specific guide rail project, you’ll typically need to provide potential suppliers like Met3dp with detailed information, including CAD models, material specifications, tolerance requirements, post-processing needs, and desired quantities when you request a quote for metal AM.
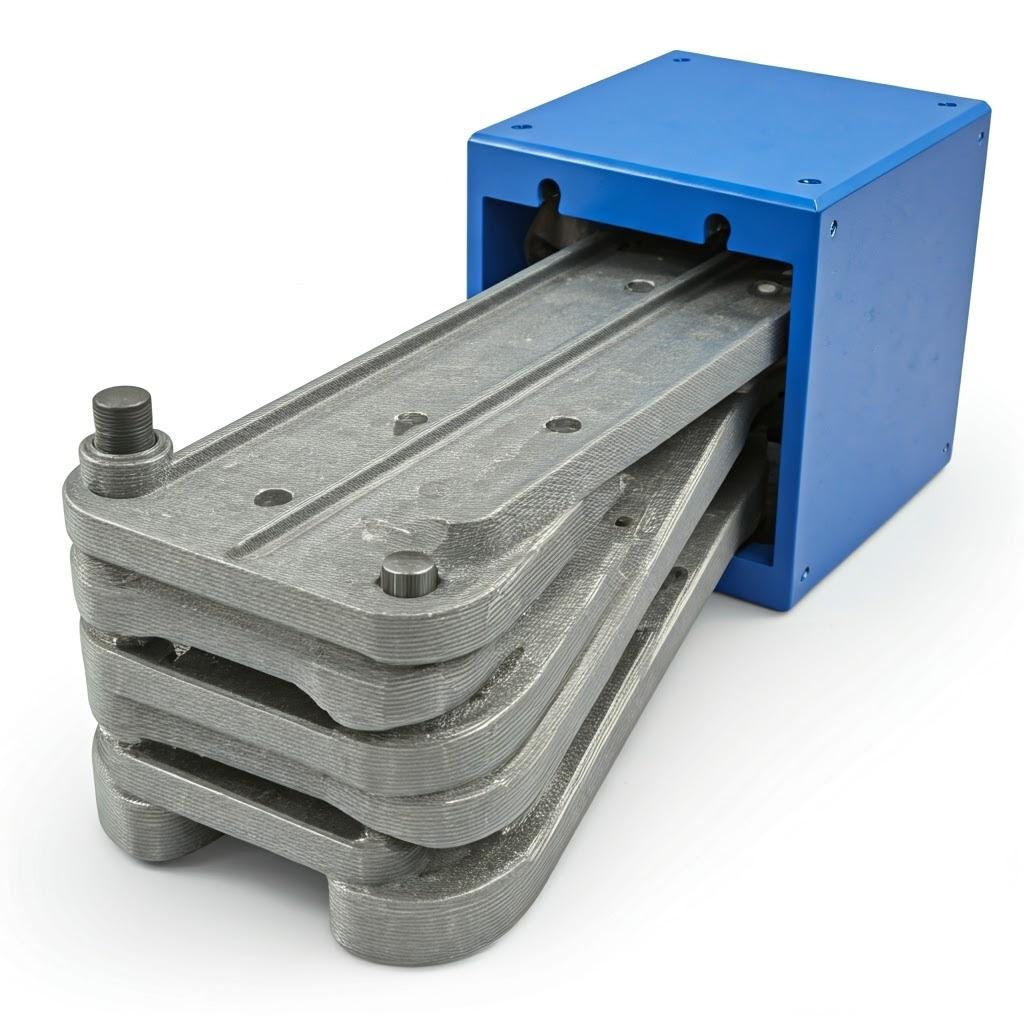
Frequently Asked Questions (FAQ) about Metal 3D Printed Aerospace Guide Rails
As engineers, designers, and procurement specialists explore the use of metal AM for aerospace guide rails, several common questions arise. Here are answers to some frequently asked questions:
Q1: How do the mechanical properties of AM Scalmalloy® or Ti-6Al-4V compare to traditional wrought or forged equivalents?
- A : When produced using optimized parameters and subjected to appropriate post-processing, particularly Hot Isostatic Pressing (HIP), the static mechanical properties (like yield strength and ultimate tensile strength) of AM Scalmalloy® and Ti-6Al-4V can be highly comparable, and sometimes even superior in certain aspects, to their traditional counterparts. However, properties like fatigue strength and ductility can be more sensitive to the AM process specifics (e.g., build orientation, surface finish, defect population). Anisotropy (directional property variation) can exist in AM parts, though HIP helps homogenize the microstructure. It’s crucial to work with experienced providers who understand metal AM vs wrought properties and can perform the necessary testing and qualification for aerospace applications.
Q2: What is the typical surface finish achievable on a guide rail’s critical sliding or mating surface?
- A : The as-built surface finish of metal AM parts (typically Ra 6-15 µm for L-PBF, Ra 20-35 µm for EBM/SEBM) is generally too rough for high-performance sliding surfaces or precise mating interfaces in guide rails. To achieve the smooth, low-friction surfaces required (often needing Ra < 1 µm, sometimes much lower), post-processing is essential. This typically involves CNC machining (milling, grinding) and potentially subsequent polishing or application-specific coatings (like DLC). The final achievable 3D printing surface finish Ra depends entirely on the post-processing applied.
Q3: Can metal AM be used for serial production of aerospace guide rails, not just prototypes?
- A : Absolutely. While initially known for prototyping, metal AM is increasingly used for the additive manufacturing serial production of aerospace components, including guide rails. It is particularly cost-effective and advantageous for:
- Géométries complexes : Parts difficult or impossible to machine traditionally.
- Consolidation partielle : Replacing multi-part assemblies with a single printed component.
- High-Value Materials: Where the improved buy-to-fly ratio of AM offers significant cost savings on expensive alloys.
- Low-to-Medium Volume Production: Where the cost of traditional tooling (e.g., for casting) is prohibitive.
- Fabrication à la demande : Reducing inventory and enabling rapid MRO. The business case depends on comparing the total lifecycle cost, including performance benefits like lightweighting, against traditional methods.
Q4: What information does Met3dp need to provide an accurate quote for printing my aerospace guide rail design?
- A : To provide a comprehensive quote, Met3dp typically requires the following:
- 3D CAD File: In a standard format (e.g., STEP, IGES).
- Material Specification: Clearly state Scalmalloy®, Ti-6Al-4V, or other required alloy.
- Technical Drawings (if available): Highlighting critical dimensions, tolerances, and surface finish requirements on specific features.
- Besoins en post-traitement : Specify required heat treatments (stress relief, HIP), machining operations, surface finishes, or coatings.
- Quantity Required: Number of parts needed (for prototypes or production runs).
- Testing & Certification: Any specific NDT, destructive testing, or certification requirements (e.g., material certs, certificate of conformance). Providing detailed information upfront helps ensure an accurate metal AM quote requirement response.
Q5: Does Met3dp hold aerospace-specific certifications like AS9100?
- A : Met3dp operates with a strong commitment to quality, utilizing rigorous process controls, advanced equipment, and high-quality materials essential for demanding industries like aerospace. Our focus on industry-leading powder production and reliable printing systems forms the foundation of this commitment. For specific inquiries regarding certifications like AS9100 or Nadcap relevant to your project’s unique requirements, we encourage you to contact our team directly to discuss how we can meet your quality needs. We are dedicated to providing the necessary documentation and compliance support for aerospace 3D printing certification as required by our partners.
Conclusion: Elevating Aerospace Assemblies with Met3dp’s Additive Manufacturing Expertise
The landscape of aerospace manufacturing is undergoing a profound transformation, driven by the relentless pursuit of higher performance, reduced weight, and increased efficiency. Metal additive manufacturing stands at the forefront of this revolution, offering unprecedented capabilities for creating complex, lightweight, and highly optimized components. As we’ve explored, aerospace guide rails – critical elements enabling motion and ensuring structural integrity – represent a prime application where metal AM, utilizing advanced materials like Scalmalloy® and Ti-6Al-4V, delivers tangible benefits over traditional methods.
From enabling intricate designs and topology optimization for significant weight savings to consolidating multi-part assemblies into monolithic structures, metal AM empowers engineers to rethink what’s possible. The journey from digital design to flight-ready component, however, requires navigating considerations of DfAM, precision tolerances, essential post-processing, and potential manufacturing challenges. Success hinges on leveraging the right materials, processes, and, crucially, the right expert partner.
Met3dp is more than just a supplier; we are a dedicated partner in your additive manufacturing journey. Our foundation rests on industry-leading metal powder production using advanced Gas Atomization and PREP technologies, ensuring the highest quality starting materials for your critical components. This is complemented by our state-of-the-art printing capabilities, including advanced SEBM systems, delivering industry-leading accuracy and reliability. We provide solutions complètes, offering expertise that spans material science, DfAM support, printing services, and guidance through post-processing pathways.
En s'associant avec Met3dp, aerospace manufacturers, suppliers, and innovators gain access to the technology, materials, and expertise needed to fully exploit the advantages of metal AM. Whether you are looking to lightweight existing guide rail designs, consolidate complex assemblies, or develop entirely new high-performance components, our team is ready to collaborate.
Ready to elevate your aerospace assemblies? Discover how Met3dp’s cutting-edge additive manufacturing solutions can revolutionize your components. Contactez Met3dp aujourd'hui to discuss your specific guide rail project or other aerospace application needs with our team of experts and take the next step towards the future of aerospace manufacturing.
Partager sur
MET3DP Technology Co. est un fournisseur de premier plan de solutions de fabrication additive dont le siège se trouve à Qingdao, en Chine. Notre société est spécialisée dans les équipements d'impression 3D et les poudres métalliques de haute performance pour les applications industrielles.
Articles connexes
À propos de Met3DP
Mise à jour récente
Notre produit
CONTACTEZ-NOUS
Vous avez des questions ? Envoyez-nous un message dès maintenant ! Nous répondrons à votre demande avec toute une équipe dès réception de votre message.
Obtenir les informations de Metal3DP
Brochure du produit
Obtenir les derniers produits et la liste des prix
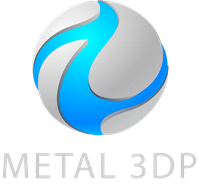
Poudres métalliques pour l'impression 3D et la fabrication additive