atomisation par plasma
Table des matières
Imagine having the ability to transform solid metal into a cloud of perfectly spherical particles, each one microscopic yet immensely powerful. That’s the magic of atomisation par plasma, a revolutionary technology that’s reshaping the world of metal powders. But what exactly is it, and how does it work? Buckle up, because we’re about to delve into the fascinating world of this high-tech process.
Du métal en fusion aux merveilles microscopiques
Plasma atomization takes metal feedstock, typically in the form of wire, and blasts it with an intensely hot plasma stream – think temperatures exceeding 10,000°C (18,000°F)! This intense heat instantly melts the metal, transforming it into a molten droplet. But the story doesn’t end there. The process then utilizes a variety of atomization techniques, like gas or centrifugal force, to break this molten droplet into a fine mist of tiny metal particles. These particles rapidly solidify as they cool in mid-air, resulting in a collection of near-perfect spheres – the coveted metal powder.
Le pouvoir de la atomisation par plasma
Plasma atomization stands out from other metal powder production methods like water or gas atomization due to its ability to create exceptionally high-quality powders. Here’s why:
- Purity Powerhouse: The high temperatures achieved in plasma atomization minimize the risk of contamination from the surrounding environment, leading to exceptionally pure metal powders. This is crucial for applications where even a trace amount of impurity can significantly impact performance.
- Spherical Supremacy: Thanks to the surface tension forces acting on the molten droplets during solidification, plasma atomization produces highly spherical particles. This consistent shape translates to superior flowability and packing density, making the powder ideal for additive manufacturing processes like 3D printing.
- Fine-Tuning the Force: The precise control over the plasma torch and atomization parameters allows for the creation of powders with a narrow size distribution. This consistency is essential for many applications where uniform particle size is critical for optimal performance.
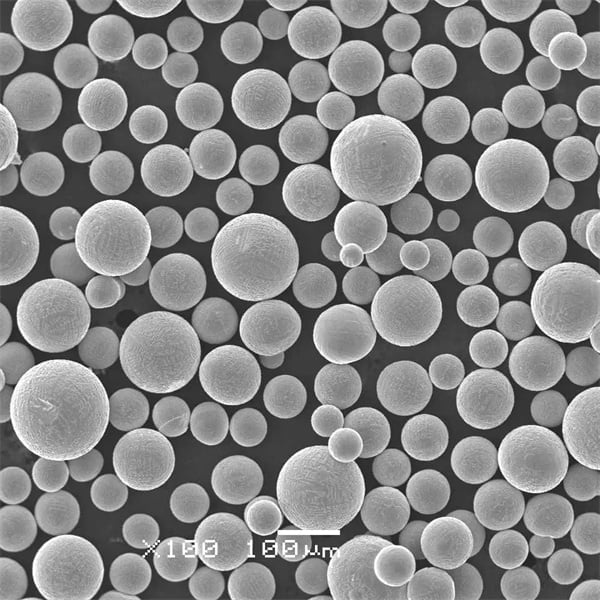
Poudres métalliques spécifiques
Now, let’s delve deeper and explore some of the metal powder champions crafted through plasma atomization:
1. Poudres de titane : Renowned for their exceptional strength-to-weight ratio and excellent corrosion resistance, titanium powders are the go-to choice for aerospace, medical implants, and high-performance sporting goods. Plasma-atomized titanium powders boast superior purity and consistent spherical morphology, making them perfect for additive manufacturing applications where these qualities are paramount.
2. Poudres de nickel : A versatile metal, nickel finds its way into countless applications, from coinage and batteries to superalloys used in jet engines. Plasma-atomized nickel powders offer exceptional flowability and packing density, crucial for processes like powder metallurgy where precise control over material properties is essential.
3. Poudres d'aluminium : Lightweight and readily formable, aluminum powders are finding increasing use in the automotive and aerospace industries for weight reduction. Plasma atomization ensures high purity and a narrow size distribution in aluminum powders, leading to components with predictable mechanical properties.
4. Cobalt Powders: A key ingredient in superalloys and hard-wearing cutting tools, cobalt powders benefit tremendously from plasma atomization. This process delivers high-purity powders with excellent flowability, allowing for the creation of robust and wear-resistant components.
5. Poudres de cuivre : A highly conductive metal, copper is a mainstay in electrical applications. Plasma-atomized copper powders offer superior flowability and packing density, making them ideal for processes like metal injection molding (MIM) used to create intricate electronic components.
6. Stainless Steel Powders: Offering a combination of strength, corrosion resistance, and affordability, stainless steel powders are widely used in various industries. Plasma atomization ensures consistent particle size and morphology in these powders, leading to predictable mechanical properties in the final product.
7. Inconel Powders: A family of high-performance nickel-chromium superalloys, Inconel powders are vital for applications demanding exceptional strength and heat resistance, such as jet engine components. Plasma atomization ensures these powders possess the high purity and precise grain structure needed to withstand extreme conditions.
8. Poudres de tungstène : Dense and incredibly hard, tungsten powders are used for applications like armor plating and high-performance cutting tools. Plasma atomization yields tungsten powders with minimal impurities and a controlled particle size distribution, crucial for achieving the desired hardness and wear resistance.
9. Poudres de molybdène : Another high-melting point metal, molybdenum finds use in heating elements and other high-temperature applications. Plasma atomization ensures exceptional purity and controlled particle size in molybdenum powders, leading to components with predictable thermal and mechanical properties.
10. Tantalum Powders: Highly corrosion-resistant and biocompatible, tantalum powders are finding increasing use in medical implants and capacitors. Plasma atomization delivers high-purity tantalum powders with a controlled grain structure, essential for ensuring the long-term performance and biocompatibility of medical devices.
Beyond the Big 10: A Universe of Metal Powders
The beauty of plasma atomization lies in its versatility. This process can be used to create powders from a vast array of metals, including:
- Zirconium: Used in nuclear reactors due to its exceptional neutron absorption properties. Plasma atomization ensures high purity in zirconium powders, crucial for safe and efficient reactor operation.
- Niobium : A valuable alloying element known for its strength and superconductivity at low temperatures. Plasma-atomized niobium powders offer precise control over particle size and morphology, leading to superior performance in superconducting applications.
- Magnésium : The lightest structural metal, magnesium is gaining traction in weight-sensitive applications like aerospace. Plasma atomization ensures high purity and controlled porosity in magnesium powders, optimizing their strength-to-weight ratio.
Unveiling the Nuances of Metal Powders
When it comes to metal powders, the devil is in the details. Here’s a breakdown of some key parameters to consider:
Paramètres | Description | Importance for Plasma-Atomized Powders |
---|---|---|
Distribution de la taille des particules | The range of sizes present in the powder | Plasma atomization offers precise control, leading to consistent and predictable properties in the final product. |
Sphéricité | How closely the particles resemble perfect spheres | High sphericity in plasma-atomized powders ensures excellent flowability and packing density. |
Surface | The total surface area of the powder particles | Plasma atomization can influence surface area, impacting factors like reactivity and sintering behavior. |
Densité apparente | Le poids de la poudre par unité de volume | High apparent density in plasma-atomized powders translates to efficient use of material and reduced production costs. |
Capacité d'écoulement | La facilité avec laquelle la poudre s'écoule | Excellent flowability in plasma-atomized powders enables efficient handling and processing in various applications. |
Composition chimique | The elemental makeup of the powder | Plasma atomization minimizes contamination, leading to high-purity powders with predictable properties. |
Supplier and Pricing Landscape
With the growing demand for high-quality metal powders, the number of atomisation par plasma suppliers is steadily increasing. Here’s a glimpse into the landscape:
- Principaux fournisseurs : Some of the prominent names in the plasma atomization industry include AP&C, Höganäs, and PyroGenesis. These companies offer a wide range of metal powders catering to diverse applications.
- Pricing Dynamics: Pricing for plasma-atomized powders varies depending on the specific metal, powder grade, and quantity. Generally, high-purity and finely sized powders command a premium price.
Peser le pour et le contre
While plasma atomization offers numerous advantages, it’s important to consider its limitations:
Avantages :
- Pureté exceptionnelle : Minimized contamination leads to predictable and reliable material properties.
- Superior Sphericity: Consistent particle shape ensures excellent flowability and packing density.
- Contrôle précis : Tailored process parameters allow for control over particle size and morphology.
- Large gamme de matériaux : Applicable to a vast array of metals for diverse applications.
Inconvénients :
- Consommation d'énergie élevée : The intense plasma torches require significant energy input, impacting production costs.
- Complex Equipment: The plasma atomization setup involves sophisticated equipment, leading to higher capital investment.
- Taux de production limités : Compared to some other methods, plasma atomization may have slower production rates for certain metals.
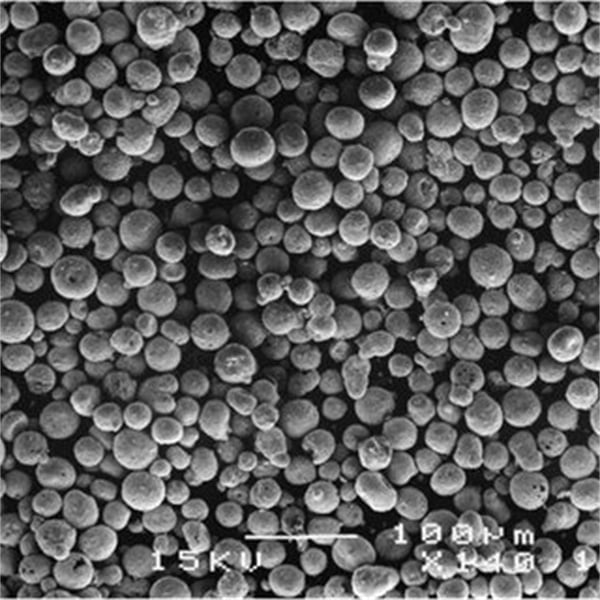
FAQ
Here are some commonly asked questions about atomisation par plasmaLes réponses aux questions posées sont claires et concises :
Question | Répondre |
---|---|
What are the advantages of plasma atomization over other powder production methods? | Plasma atomization offers superior purity, consistent sphericity, and precise control over particle size, leading to high-performance powders. |
What are some of the applications of plasma-atomized metal powders? | These powders are used in additive manufacturing, powder metallurgy, metal injection molding, and various other industrial processes. |
What factors influence the cost of plasma-atomized powders? | The specific metal, powder grade, and quantity all play a role in pricing. |
Is plasma atomization an environmentally friendly process? | While the energy consumption of plasma atomization can be significant, advancements are being made to improve energy efficiency. Additionally, the minimal waste generated and the potential for recycling unused powder contribute to a more sustainable approach. |
What are the future prospects of plasma atomization? | As the demand for high-performance metal powders increases, plasma atomization is expected to see continued growth. Advancements in automation, process optimization, and material science are likely to further enhance the capabilities and efficiency of this technology. |
Partager sur
MET3DP Technology Co. est un fournisseur de premier plan de solutions de fabrication additive dont le siège se trouve à Qingdao, en Chine. Notre société est spécialisée dans les équipements d'impression 3D et les poudres métalliques de haute performance pour les applications industrielles.
Articles connexes
À propos de Met3DP
Mise à jour récente
Notre produit
CONTACTEZ-NOUS
Vous avez des questions ? Envoyez-nous un message dès maintenant ! Nous répondrons à votre demande avec toute une équipe dès réception de votre message.
Obtenir les informations de Metal3DP
Brochure du produit
Obtenir les derniers produits et la liste des prix
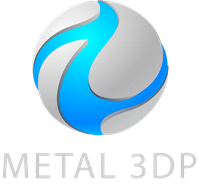
Poudres métalliques pour l'impression 3D et la fabrication additive
PRODUIT
cONTACT INFO
- Ville de Qingdao, Shandong, Chine
- [email protected]
- [email protected]
- +86 19116340731