Introduction à l'alliage mécanique pour l'impression 3D de poudre métallique
Table des matières
Le monde de Poudre métallique pour l'impression 3D continue d'évoluer à un rythme étonnant, repoussant les limites de ce qui est possible en termes de conception, de complexité et de sélection des matériaux. La fabrication additive de métaux, en particulier, a ouvert les portes à la création d'objets complexes et fonctionnels directement à partir de modèles numériques. Mais vous êtes-vous déjà demandé comment la poudre métallique utilisée dans ces imprimantes est même produite ? Entrez dans l'alliage mécanique, une technologie fascinante qui joue un rôle crucial dans la création de hautes performances Poudre métallique pour l'impression 3D.
les principes de base de l'alliage mécanique
Imaginez que vous avez un shaker à cocktails rempli de bonbons de différentes couleurs. Secouer vigoureusement mélange les bonbons, créant un mélange apparemment uniforme. C'est, en substance, le principe de base de l'alliage mécanique. Il s'agit d'une technique de traitement des poudres à l'état solide qui utilise le broyage à boulets à haute énergie pour mélanger et mélanger intimement plusieurs poudres métalliques ensemble au niveau atomique.
Voici une ventilation plus détaillée du processus :
- Sélection des poudres : La première étape consiste à choisir soigneusement les poudres métalliques souhaitées en fonction des propriétés matérielles finales et des exigences d'application. Cela pourrait impliquer des éléments individuels, des poudres pré-alliées ou même des combinaisons des deux.
- Processus de broyage : Les poudres sélectionnées sont ensuite chargées dans un broyeur à boulets à haute énergie, qui agit essentiellement comme un shaker géant. À l'intérieur du broyeur, de nombreuses billes faites d'un matériau plus dur (souvent de l'acier ou de la céramique) entrent en collision avec les particules de poudre à grande vitesse. Cette force mécanique intense fracture, déforme et soude les particules de poudre ensemble, favorisant un mélange intime et créant un nouveau, matériau en poudre homogénéisée avec des propriétés uniques.
- Collecte et traitement de la poudre : Après un temps de broyage prédéterminé, la poudre résultante est collectée et subit d'autres étapes de traitement comme le tamisage et la classification pour obtenir la distribution granulométrique et la morphologie souhaitées.
Pensez-y de la manière suivante : Imaginez que vous essayez de mélanger des pépites de chocolat et de la farine à la main. Vous pourriez vous retrouver avec un mélange quelque peu mél
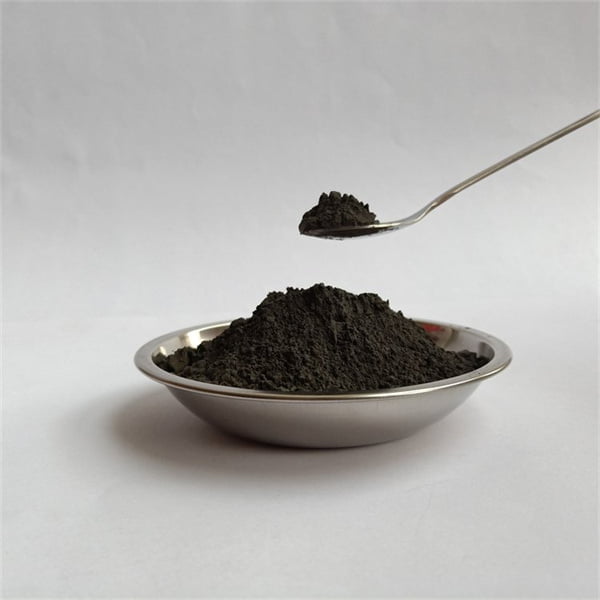
Comment appliquer le mélange mécanique à la production de poudres métalliques imprimées en 3D
Le mélange mécanique offre une approche polyvalente pour produire des poudres métalliques spécialement conçues pour les applications d'impression 3D. Voici comment il joue un rôle clé :
- Création de nouveaux alliages : En mélangeant différentes poudres élémentaires, le mélange mécanique permet de créer de nouveaux alliages avec des propriétés spécifiques qui ne sont pas facilement disponibles sous des formes conventionnelles. Cela ouvre la voie à la personnalisation des propriétés des matériaux, telles que la résistance, la résistance à la corrosion et le comportement thermique, pour des applications spécifiques d'impression 3D.
- Amélioration des propriétés des poudres : Le mélange mécanique peut également améliorer l'aptitude à l'écoulement, la densité de tassement et l'imprimabilité globale des poudres métalliques existantes. En affinant la taille et la morphologie des particules, la poudre devient plus adaptée à divers procédés d'impression 3D, tels que la fusion sur lit de poudre laser (LPBF) et la fusion par faisceau d'électrons (EBM).
- Activation des poudres composites : Cette technique ouvre également la voie au développement de composites à matrice métallique (CMM) pour l'impression 3D. En incorporant des particules de céramique ou d'autres particules de renforcement dans la matrice métallique par mélange mécanique, la poudre résultante offre des propriétés mécaniques améliorées, telles que la résistance à l'usure et les performances à haute température.
Essentiellement, le mélange mécanique agit comme un outil puissant pour libérer le potentiel des métaux d'impression 3D en permettant la création de nouveaux matériaux avec des propriétés précisément adaptées pour répondre aux exigences de diverses applications.
Les avantages du mélange mécanique dans Poudres métalliques pour l'impression 3D
Par rapport aux méthodes traditionnelles de production de poudre, telles que l'atomisation, le mélange mécanique offre plusieurs avantages distincts pour l'impression 3D :
- Un meilleur contrôle de la composition : Il permet la création d'alliages précis et uniformes avec des compositions spécifiques, sans se limiter aux poudres pré-alliées facilement disponibles.
- Des propriétés de poudre améliorées : Le procédé affine les particules de poudre, améliorant ainsi leur aptitude à l'écoulement, leur densité de tassement et leur imprimabilité, ce qui conduit à de meilleures performances dans les procédés d'impression 3D.
- Développement de nouveaux matériaux : Il ouvre la voie à la création d'alliages uniques et de composites à matrice métallique avec des propriétés impossibles à obtenir par des méthodes conventionnelles, élargissant ainsi les possibilités pour les applications d'impression 3D.
- Évolutivité : Le mélange mécanique peut être adapté pour produire de petits ou de grands lots de poudre, ce qui le rend adapté à la recherche et à la production à l'échelle industrielle.
Cependant, il est important de reconnaître que le mélange mécanique présente également certaines limites :
- Délai de traitement : Le procédé de broyage peut prendre du temps et consommer beaucoup d'énergie, en particulier pour les combinaisons de matériaux plus durs ou plus complexes.
- Potentiel de contamination : Une sélection minutieuse des milieux de broyage et un contrôle du procédé sont essentiels pour minimiser la contamination par les billes de broyage ou l'environnement.
- Considérations relatives aux coûts : La mise en place et la maintenance d'un équipement de broyage à haute
Modèles spécifiques de poudres métalliques pour l'impression 3D utilisant le mélange mécanique
Bien que les fonctionnalités de base restent cohérentes, les modèles spécifiques de poudres métalliques produits par mélange mécanique répondent à diverses applications d'impression 3D et aux exigences de performance. Voici 10 exemples notables :
1. Inconel 625 : Cette poudre de superalliage à base de nickel-chrome possède une résistance exceptionnelle à haute température, une résistance à l'oxydation et une résistance au fluage. Elle est particulièrement adaptée aux applications exigeantes telles que les composants aérospatiaux, les pièces de turbines à gaz et les échangeurs de chaleur dans le domaine de l'impression 3D.
2. Ti-6Al-4V : Cette poudre d'alliage de titane très performante offre un excellent équilibre entre résistance, poids et biocompatibilité. Elle est largement utilisée dans les industries médicale et aérospatiale pour des applications telles que les implants orthopédiques, les composants d'avions et les prothèses personnalisées en raison de ses propriétés favorables lorsqu'elle est produite par mélange mécanique.
3. AlSi10Mg : Cette poudre d'alliage d'aluminium-silicium-magnésium est connue pour sa bonne coulabilité, sa soudabilité et sa résistance à la corrosion. Elle trouve des applications dans divers secteurs, notamment l'automobile, l'aérospatiale et les biens de consommation, en raison de sa combinaison d'imprimabilité et de propriétés mécaniques réalisables grâce au mélange mécanique.
4. Cu-Sn10 : Cette poudre d'alliage cuivre-étain offre une conductivité électrique et une résistance à l'usure supérieures. Elle est souvent utilisée dans la production de composants électriques tels que les dissipateurs thermiques, les barres omnibus et les connecteurs, où ses propriétés, améliorées par le mélange mécanique, sont cruciales pour les performances.
5. CoCrMo : Cette poudre d'alliage cobalt-chrome-molybdène est réputée pour sa biocompatibilité, sa résistance à l'usure et sa résistance à la corrosion élevées. C'est un choix populaire pour l'impression 3D d'implants médicaux tels que les prothèses de hanche et de genou, où la biocompatibilité et les propriétés mécaniques obtenues grâce au mélange mécanique sont primordiales.
7. Inconel 718 : Cette poudre de superalliage à base de nickel-chrome est connue pour sa résistance exceptionnelle à haute température, sa bonne résistance à l'oxydation et son excellente résistance au fluage. Elle est souvent utilisée dans des applications exigeantes telles que les aubes de turbine, les composants de moteurs-fusées et d'autres pièces haute performance, où les propriétés réalisables grâce au mélange mécanique sont essentielles.
8. Acier maraging 300 : Cette poudre d'acier à haute résistance et à faible teneur en carbone offre une résistance et une ténacité supérieures après traitement thermique. Elle est utilisée dans diverses applications nécessitant un rapport résistance/poids élevé, comme les composants aérospatiaux, l'outillage et l'équipement de défense, où les propriétés obtenues grâce à l'alliage mécanique sont cruciales.
9. Bronze nickel-aluminium (NAB) : Cette poudre d'alliage cuivre-aluminium-nickel offre une excellente résistance à la corrosion et à l'usure, ainsi que de bonnes propriétés mécaniques. Il trouve des applications dans les composants marins, les roulements et les pièces d'usure, où son imprimabilité et ses propriétés, améliorées par l'alliage mécanique, sont avantageuses.
10. Hastelloy C-276 : Cette poudre d'alliage de nickel-chrome-molybdène est connue pour sa résistance exceptionnelle à la corrosion dans un large éventail d'environnements agressifs. Il est utilisé dans les équipements de traitement chimique, les systèmes de contrôle de la pollution et d'autres applications nécessitant une résistance supérieure aux produits chimiques agressifs, où les propriétés obtenues grâce à l'alliage mécanique sont vitales.
Il est important de se rappeler qu'il ne s'agit que de quelques exemples et que les possibilités offertes par les poudres d'alliage mécanique sont en constante expansion. Au fur et à mesure que la technologie progresse, nous pouvons nous attendre à voir apparaître des poudres métalliques encore plus innovantes et spécialisées, conçues pour répondre aux besoins spécifiques de diverses applications d'impression 3D.
Comparaison des modèles de poudres métalliques pour l'impression 3D
Lorsque vous choisissez un modèle de poudre métallique pour votre projet d'impression 3D, plusieurs facteurs doivent être pris en compte :
- Propriétés souhaitées : Identifiez les propriétés essentielles dont votre pièce finie a besoin, telles que la solidité, le poids, la résistance à la corrosion, la biocompatibilité ou la conductivité électrique.
- Conditions de candidature : Tenez compte de l'application spécifique et des conditions environnementales auxquelles la pièce sera soumise.
- Processus d'impression 3D : Adaptez les caractéristiques de la poudre, telles que la taille des particules et la fluidité, au processus d'impression 3D spécifique que vous utiliserez (par exemple, LPBF, EBM).
Voici une brève comparaison de certaines propriétés clés des modèles de poudres métalliques mentionnés :
Modèle de poudre métallique | Résistance (MPa) | Densité (g/cm³) | Point de fusion (°C) | Applications |
---|---|---|---|---|
Inconel 625 | Il présente une résistance exceptionnelle à haute température, ce qui le rend idéal pour les applications exigeantes telles que les composants aérospatiaux et les échangeurs de chaleur. | Sa densité élevée de 8,44 g/cm³ contribue à sa robustesse. | Son point de fusion est de 1455°C, ce qui lui permet de résister à des températures extrêmes. | Largement utilisé dans l'aérospatiale, les turbines à gaz et les échangeurs de chaleur en raison de sa combinaison de solidité, de résistance aux températures élevées et de bonne imprimabilité. |
Ti-6Al-4V | Il présente un excellent équilibre entre résistance, poids et biocompatibilité, ce qui le rend adapté à des applications telles que les implants orthopédiques et les prothèses. | Densité modérée de 4,43 g/cm³, offrant un bon équilibre entre poids et résistance. | Fond à une température d'environ 1600°C, ce qui démontre sa capacité à résister à des températures élevées. | Un choix populaire dans les industries médicales et aérospatiales en raison de sa biocompatibilité, de son rapport résistance/poids favorable et de sa bonne imprimabilité. |
AlSi10Mg | Connu pour sa bonne coulabilité, sa soudabilité et sa résistance à la corrosion, ce qui le rend polyvalent pour diverses applications. | Possède une densité plus faible d'environ 2,7 g/cm³, ce qui contribue à ses propriétés de légèreté. | Fond à une température relativement plus basse que les autres, environ 577°C, ce qui permet une transformation plus aisée dans certains cas. | Couramment utilisé dans les secteurs de l'automobile, de l'aérospatiale et des biens de consommation en raison de son imprimabilité, de ses propriétés mécaniques favorables et de sa bonne coulabilité. |
Cu-Sn10 | Il offre une conductivité électrique et une résistance à l'usure supérieures, ce qui le rend précieux pour des applications telles que les composants électriques et les dissipateurs thermiques. | Il présente une densité modérée d'environ 8,9 g/cm³, ce qui permet d'équilibrer la conductivité électrique et les considérations de poids. | Fond à une température d'environ 830°C, offrant une bonne maniabilité et une bonne imprimabilité. | Fréquemment utilisé dans la production de composants électriques tels que les dissipateurs thermiques et les barres omnibus en raison de sa conductivité électrique exceptionnelle et de sa résistance à l'usure. |
CoCrMo | Réputé pour sa grande biocompatibilité, sa résistance à l'usure et à la corrosion, ce qui en fait un choix de premier ordre pour les implants médicaux. | Possède une densité élevée d'environ 8,3 g/cm³, ce qui contribue à sa durabilité et à sa résistance à l'usure. | Fond à une température d'environ 1350°C, ce qui démontre sa capacité à résister à des températures élevées au cours de divers processus. | Largement utilisé dans le domaine médical pour des applications telles que les prothèses de hanche et de genou en raison de son excellente biocompatibilité, de sa bonne imprimabilité et de sa résistance à l'usure. |
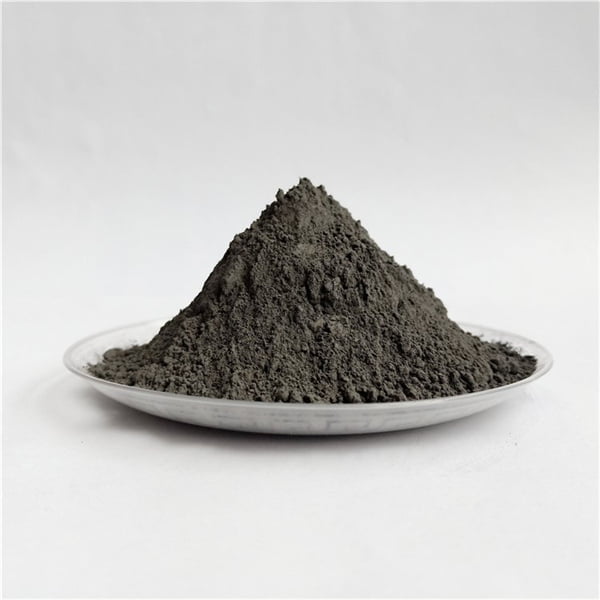
Considérations supplémentaires et perspectives d'avenir de l'alliage mécanique dans l'impression 3D
Si l'alliage mécanique présente de nombreux avantages pour Poudres métalliques pour l'impression 3DIl est donc essentiel de prendre en compte certains facteurs supplémentaires :
- Coût : Le processus peut être plus cher par rapport aux méthodes traditionnelles de production de poudres telles que l'atomisation, en particulier pour les grandes quantités.
- Contrôle des processus : Contrôle strict L'optimisation des paramètres et de l'équipement de broyage est essentielle pour garantir une qualité de poudre constante et minimiser les risques de contamination.
- Impact sur l'environnement : La consommation d'énergie associée au processus de broyage nécessite la prise en compte de la durabilité et de l'impact potentiel sur l'environnement.
Malgré ces considérations, l'avenir de l'alliage mécanique dans l'impression 3D semble prometteur. Voici quelques possibilités passionnantes qui s'offrent à nous :
- Développement de nouveaux alliages : La technologie continuera à ouvrir la voie à la création de nouveaux alliages aux propriétés uniques, repoussant les limites de ce qui est réalisable en impression 3D.
- Amélioration de l'efficacité des processus : Les progrès de la technologie de broyage et l'optimisation des processus peuvent entraîner une augmentation de l'efficacité et une réduction des coûts, ce qui rend le broyage plus accessible pour diverses applications.
- Poudres nanocomposites : L'avenir pourrait voir le développement de poudres nanocomposites aux propriétés exceptionnelles, élargissant encore le potentiel de l'impression 3D pour des applications avancées.
En conclusion, le mélange mécanique est un outil puissant pour libérer le potentiel des métaux d'impression 3D. En permettant la création de nouveaux matériaux avec des propriétés sur mesure et en favorisant les progrès dans ce domaine, cette technologie ouvre la voie à la création d'objets innovants, performants et fonctionnels dans divers secteurs. Au fur et à mesure que la recherche et le développement se poursuivent, nous pouvons nous attendre à voir apparaître des possibilités encore plus intéressantes, façonnant l'avenir de l'impression 3D des métaux.
FAQ
Q : Quels sont les avantages de l'utilisation de poudres mécaniquement alliées dans l'impression 3D ?
R : Plusieurs avantages existent, notamment :
- Un meilleur contrôle de la composition : Permet la création d'alliages précis et uniformes avec des compositions spécifiques.
- Des propriétés de poudre améliorées : Améliore l'aptitude à l'écoulement, la densité de tassement et l'imprimabilité pour de meilleures performances dans les procédés d'impression 3D.
- Développement de nouveaux matériaux : Permet la création d'alliages uniques et de composites à matrice métallique avec des propriétés impossibles à obtenir par des méthodes conventionnelles.
- Évolutivité : Adaptable pour produire de petits ou de grands lots de poudre pour la recherche et la production à l'échelle industrielle.
Q : Quelles sont certaines des limites de l'utilisation de poudres mélangées mécaniquement ?
R : Les limites potentielles incluent :
- Délai de traitement : Le procédé de broyage peut prendre du temps et consommer beaucoup d'énergie, en particulier pour les combinaisons de matériaux complexes.
- Potentiel de contamination : Une sélection minutieuse des milieux de broyage et un contrôle du procédé sont essentiels pour minimiser la contamination.
- Considérations relatives aux coûts : La mise en place et la maintenance d'un équipement de broyage à haute énergie peuvent être coûteuses.
Q : Quels sont certains des facteurs à prendre en compte lors du choix d'un modèle de poudre métallique pour l'impression 3D ?
R : Les facteurs clés incluent :
- Propriétés souhaitées : Identifier les propriétés cruciales dont votre pièce finie a besoin (résistance, poids, résistance à la corrosion, etc.).
- Conditions de candidature : Tenir compte de l'application spécifique et des conditions environnementales auxquelles la pièce sera confrontée.
- Processus d'impression 3D : Faire correspondre les caractéristiques de la poudre (taille des particules, aptitude à l'écoulement) au procédé d'impression 3D spécifique que vous utiliserez.
Q : Quelles sont les perspectives d'avenir du mélange mécanique dans l'impression 3D ?
R : L'avenir semble prometteur, avec le potentiel de :
- Développement de nouveaux alliages : Création de nouveaux alliages avec des propriétés uniques, élargissant les possibilités de l'impression 3D.
- Amélioration de l'efficacité des processus : Les progrès de la technologie de broyage et l'optimisation des procédés peuvent conduire à une efficacité accrue et à une réduction des coûts.
- Poudres nanocomposites : Développement de poudres nanocomposites avec des propriétés exceptionnelles, élargissant encore le potentiel de l'impression 3D pour les applications avancées.
En comprenant le potentiel et les limites du mélange mécanique, nous pouvons exploiter cette technologie pour créer des objets imprimés en 3D innovants et fonctionnels, façonnant l'avenir de divers secteurs.
Partager sur
MET3DP Technology Co. est un fournisseur de premier plan de solutions de fabrication additive dont le siège se trouve à Qingdao, en Chine. Notre société est spécialisée dans les équipements d'impression 3D et les poudres métalliques de haute performance pour les applications industrielles.
Articles connexes
À propos de Met3DP
Mise à jour récente
Notre produit
CONTACTEZ-NOUS
Vous avez des questions ? Envoyez-nous un message dès maintenant ! Nous répondrons à votre demande avec toute une équipe dès réception de votre message.
Obtenir les informations de Metal3DP
Brochure du produit
Obtenir les derniers produits et la liste des prix
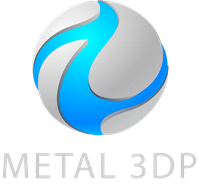
Poudres métalliques pour l'impression 3D et la fabrication additive